氧化铝陶瓷烧成缺陷:斑点、色斑及色差的成因和预防解决方法的探讨
Al2O3陶瓷制品烧结工艺的影响因素探讨

Al2O3陶瓷制品烧结工艺的影响因素探讨作者:周益平来源:《江苏陶瓷》2015年第02期摘要阐述了Al2O3制品的烧结机理,分析了烧成气氛,添加剂对Al2O3制品烧结的影响,探讨理想的升温制度、保温时间。
关键词氧化铝陶瓷制品;烧结机理;影响因素;烧成制度0 前言工业特种陶瓷中, Al2O3制品以其优良的耐酸碱性、耐磨性、耐电性、机械强度高等,在化工磷复肥和有色金属行业以及其他行业得到了广泛的应用。
在氧化铝陶瓷生产过程中,坯体烧结后的制品显微结构及其内在性能会发生根本变化,也很难通过其他途径补救。
所以研究氧化铝陶瓷的烧结工艺,选择合理的烧成制度,确保氧化铝陶瓷制品的性能和产品质量是十分必要的。
本文对烧结机理、影响烧结性能的因素、添加烧结助剂进行了探讨。
1 烧结机理和影响烧结性能的因素1.1烧结机理烧结是坯体由于温度变化发生的物理化学反应,得到了致密、坚硬的陶瓷制品的过程。
其物理化学变化包括坯体中残余拌料水分的排除、物料中化合物结合水和有机物分解的排除、氧化铝同质异晶的晶型转变以及固态物质颗粒间的固相反应等。
固相反应在氧化铝陶瓷的烧结技术中占有重要的位置,它是通过物质质点的迁移扩散作用进行的,随着温度的升高,晶体的热缺陷不断增加,质点的迁移扩散由内扩散形式到外扩散,从而发生反应产生新的物质。
1.2影响Al2O3陶瓷烧结的因素较多,主要表现如下:1.2.1晶体的结构化学键强的化合物(晶体)具有较高的晶格能量,晶格结构牢固,即使在较高温度下,质点的振动迁移也较弱,只有在接近熔点温度时,才会产生显著的物理化学反应。
所以,由这类化合物组成的坯体不易烧结。
而由微细晶体组成的多晶体相比于单晶体而言,由于前者内部晶界面很多,而晶界是缺位缺陷相对集中和易消除的地方,也是原子和离子扩散迁移的快速通道,所以远比后者易于烧结。
1.2.2物料的分散度物料分散度越高,表面能就越高,所以具有促进迁移扩散的强大作用,有利于烧结。
铝板氧化斑点机理

铝板氧化斑点机理
铝板表面出现氧化斑点的机理主要涉及铝与氧气在空气中发生氧化反应。
铝是一种活泼的金属,在空气中容易与氧气发生反应生成氧化铝,这种氧化反应通常被称为铝的氧化。
氧化铝是一种无机化合物,具有不溶于水、耐热、耐腐蚀等性质。
铝板表面出现氧化斑点的机理可以总结如下:
1.铝表面暴露于空气中:铝板在使用或储存过程中,表面通常会暴露于空气中。
2.氧气氧化反应:暴露于空气中的铝表面与氧气发生氧化反应,生成氧化铝。
这一反应通常可以描述为:4Al+3O2→2Al2O3
3.氧化铝形成斑点:氧化反应在铝表面不均匀地进行,导致氧化铝在铝表面形成不均匀的斑点。
这些斑点通常呈现为灰色、白色或者深色,严重时可能会对铝板表面造成质量缺陷。
4.其他因素的影响:氧化反应的速率受到环境中湿度、温度、氧气浓度等因素的影响。
湿润的环境有助于加速铝的氧化反应,导致斑点的形成速率增加。
综上所述,铝板表面出现氧化斑点的机理主要是铝与空气中的氧气发生氧化反应,生成氧化铝,由于反应不均匀而在铝表面形成不规则的斑点。
因此,在储存和使用铝板时,需要注意避免其暴露于潮湿的环境中,以减缓氧化反应的发生。
1。
95氧化铝瓷斑点的形成原因及解决措施

技术交流广东建设报/2003年/04月/28日/第D03版/95氧化铝瓷斑点的形成原因及解决措施 95氧化铝瓷斑点的形成原因主要有下几点:1、原料方面造成的;2、备料工序和成形工序中造成的。
煅烧过的Al-2O-3粉需要进行细磨,采用的球磨工艺有干磨和水磨。
工艺过程为:水磨→烘房→配方→干磨→烘箱→制蜡板→化蜡→热压铸成形。
备料是95瓷的准备过程,经过跟踪调查,该工艺过程容易给瓷件带来杂质的因素有三方面,一是振动筛,干磨振动筛经常与铁架磨擦,铁架框边被磨掉厚厚一层(3~5mm);二是制蜡板,尽管搅浆杆和盖板都是不锈钢的,在室内一般不会生锈,但搅浆杆和盖板经常磨擦易掉入不锈钢粉。
观察发现操作工在上卸盖板时,经常无意识使盖板与搅拌浆杆磨擦,事实上,搅浆杆与盖板磨擦已有一条大缝和几条小缝。
三是化蜡板,由于真空泵几年没有大修,同时发现搅浆工在打扫卫生时一般没有注意到,搅浆杆和盖板的接缝处易掉下杂质。
根据具体情况,解决措施如下:1、搅浆制蜡,先将不锈钢换成铝板,搅浆杆与盖板接触处包一层铝皮。
同时,尽可能将搅拌机改为升降式。
2、真空泵的搅浆桶是不锈钢的,将钢刀换成环氧树脂玻璃纤维板,可以避免钢刀与桶磨擦而掉入不锈钢粉。
3、真空机中,搅浆杆与盖板缝隙处易掉下铁锈,因此,在搅浆杆上安装一个盒子,使它随杆一起转,这样杂质只掉在盒中可以定期打扫而不会影响浆料质量。
4、振动筛边框与筛子磨擦,边框是铁质的,经常磨擦容易掉下铁粉。
因而,给筛子底部和侧面贴补橡胶片,避免直接与边框磨擦。
© 1994-2007 China Academic Journal Electronic Publishing House. All rights reserved. 。
氧化铝陶瓷升温使用过程中变黑的原因

氧化铝陶瓷是一种常见的陶瓷材料,具有优异的耐高温、耐腐蚀、绝缘等特点,在工业生产中得到了广泛的应用。
然而,在氧化铝陶瓷升温使用过程中,很多情况下会发现其表面会出现黑色或灰色的变化,这引起了广泛的关注和研究。
本文将从多个角度分析氧化铝陶瓷升温过程中变黑的原因,以期为相关领域的研究和开发提供一定的参考和帮助。
一、氧化铝陶瓷的化学成分氧化铝陶瓷的主要成分为氧化铝(Al2O3),通常还会掺杂一些稀土元素或其他金属氧化物,用以提高其性能。
在高温下,氧化铝陶瓷会发生氧化还原反应,尤其是在氧气存在的环境中,氧化铝可能被还原成金属铝,从而导致陶瓷的颜色发生变化。
二、氧化铝陶瓷的热解和氧化过程在升温过程中,氧化铝陶瓷会经历热解和氧化过程。
在一定的温度范围内,氧化铝陶瓷会发生热解反应,释放出氧气分子,进而使得材料发生氧化反应。
这些化学反应可能会导致氧化铝陶瓷的表面颜色发生变化,出现黑色或灰色的现象。
三、氧化铝陶瓷的结构变化在高温下,氧化铝陶瓷的结构也会发生变化。
其晶体结构可能会发生相变或者形态变化,这会导致材料的光学性能发生变化,从而使得表面颜色产生变化。
在长时间的高温作用下,氧化铝陶瓷的晶粒可能会长大,从而使得表面变得不均匀,出现黑色斑点或条纹。
四、氧化铝陶瓷与外界环境的作用氧化铝陶瓷与外界环境的作用也会导致其表面颜色的变化。
在高温下,氧化铝陶瓷可能会吸附氧气、水汽和其他气体,从而使得其表面发生化学反应或腐蚀,导致表面变黑。
氧化铝陶瓷升温使用过程中变黑的原因可能是多方面的。
除了材料本身的化学成分和结构特性外,外界环境的影响也是一个重要因素。
针对氧化铝陶瓷变黑的现象,需要综合考虑材料本身的特性、外界环境和使用条件等多个因素,进行系统的分析和研究,以期找到有效的解决方案,提高氧化铝陶瓷的稳定性和可靠性。
五、氧化铝陶瓷的改性和防护措施针对氧化铝陶瓷升温使用过程中变黑的问题,人们也积极探索了多种改性和防护措施。
一种常见的方法是添加一定的稀土元素或其他金属氧化物来改善氧化铝陶瓷的稳定性。
陶瓷烧成缺陷及原因分析

陶瓷烧成缺陷及原因分析发布时间:2008-8-4 15:07:14 阅读:52 次新闻来源:作者:(一)变形:产品烧成变形是陶瓷行业最常见、最严重的缺陷,如口径歪扭不圆,几何形状有不规则的改变等。
主要原因是装窑方法不当。
如匣钵柱行不正,匣钵底或垫片不平,使窑车运行发生震动,影响到产品的变形。
另外,产品在烧成中坯体预热与升温快时,温差大易发生变形。
烧成温度过高或保温时间太长也会造成大量的变形缺陷。
使用的匣钵高温强度差、或涂料抹不平时也会造成烧成品的变形。
(二)开裂:开裂指制品上有大小不同的裂纹。
其原因是坯体入窑水分太高(大于2%以上),预热升温和冷却太快,导致制品内外收缩不匀。
有的是坯体在装钵前已受到碰撞有内伤。
坯体厚薄不匀,配件(如壶把、咀等)重量过大或粘结不良也会造成制品开裂。
防止的办法是:(1)入窑坯体水分小于2%,车速适当减少冷却量。
(2)装窑时套装操作谨慎,垫片与坯体配方一致。
配件大小、重量与粘接位置恰当。
有的在粘接泥浆中加入10-15%的釉料,可以使咀、把与主体牢固熔接一体,如此可克服开裂缺陷。
(三)起泡:烧制品起泡有"坯泡"与"釉泡"两种。
坯泡分为"氧化泡"与"还原泡"两种。
氧化泡指坯泡外面覆盖釉层,断面呈灰黑色,多形成于窑内低温部位。
主要是瓷胎与釉料中的分解物未能充分氧化,烧失物未完全排除所致。
予热升温快,氧化分解阶段时间短、氧化结束时窑内温度过低,上下温度差过大。
在坯釉料中,碳酸盐。
硫酸盐及有机杂质含量较多等都是造成产品起泡的主因。
此外时装车密度不当、入窑水份高等原因亦须注意。
还原泡又称过火泡,断而发黄,多发生于高温近喷火口处的制品。
主要由于坯体内硫酸盐与高价铁还原不足,强还原气氛不足及烧成温度过高造成。
釉泡系沉积炭及分解物在釉熔前未能烧尽挥发,气体被阻于釉面层中形成。
若延长釉熔时间或适当平烧即可解决。
改善氧化铝陶瓷的缺点

改善氧化铝陶瓷的缺点
氧化铝陶瓷的缺陷应该是产品发黑,但是这并不会对其正常的使用造成影响,我们应该及时将发黑的因素找出,并针对性的对其进行相关的解决措施,保证其在性能上不会出现变化。
在选用氧化铝陶瓷中陶瓷釉面的时候,其原料的选择是非常重要的,尽量使用的是比较不容易吸烟的原料,因为这种材料可以将气氛在敏感的程度上适当降低,但是还需要对陶瓷釉在温度上进行有效的控制。
想要保证氧化铝陶瓷可以达到光亮的状态,需要将釉烧的温度和金属的温度控制在10℃,这样便能尽可能的将釉面出现发黑的现象降低,而且还能将氧化
铝陶瓷在使用的性能上得到有效的提升,所以这种方式还是比较有效的。
而且,将氧化铝陶瓷黑色的粗糙面进行改善之后,还能适当的将设备的气氛进行改善,主要的是对于抑制黑色氧化铝陶瓷出现发黑具备比较明显的作用和效果,上面所提到的降低黑色出现的方式,大家还是应该引起重视。
传统的氧化铝陶瓷制造粉末的方式因为在煅烧的过程中会比较容易出现结
块的现象,所以一次性是获取不到粉末的,而且颗粒会因为煅烧的温度而不断的增加,这也是生产人员头痛的问题,但是却没有实质性的解决方式。
氧化铝陶瓷在进行研磨的时候,还会受到二次的污染,这是为何不能制造出性能较高的粉末的主要因素,即便是能获取粉末,也不可以直接将其制造成陶瓷件,因为在烧结的密度上不能达到要求,会导致产品在性能上受到严重的影响。
氧化铝陶瓷变黄的原因

氧化铝陶瓷变黄的原因
氧化铝陶瓷变黄的原因主要有以下几点:
1. 阳光照射:氧化铝陶瓷在长时间阳光照射下,其内部结构成分发生改变,这种变化是不可逆的,导致颜色发生改变,从白色变为淡黄色。
2. 潮解现象:氧化铝陶瓷具有一定的吸湿性,长时间暴露在潮湿环境中,容易吸收水分,形成水合物氧化铝,从而使陶瓷表面变黄。
3. 杂质影响:氧化铝陶瓷在生产过程中,如果原料中含有杂质,如铁、钛等金属离子,这些杂质会在陶瓷表面形成黄色或灰色斑点。
4. 生产工艺不当:氧化铝陶瓷的生产过程中,如果洗涤工艺不当,如清洗不彻底、残留物吸附等,也会导致陶瓷产品变黄。
5. 环境因素:氧化铝陶瓷在运输、储存过程中,受到有害气体的侵蚀,如二氧化碳、硫化氢等,会使陶瓷表面发生化学反应,从而导致颜色变化。
要避免氧化铝陶瓷变黄,可以采取以下措施:
1. 选择优质原料,确保氧化铝陶瓷的纯度和稳定性。
2. 控制生产工艺,如洗涤、烘干、烧结等环节,确保陶瓷制品表面干净无瑕。
3. 储存和运输过程中,避免暴露在恶劣环境中,确保陶瓷制品不受有害气体侵蚀。
4. 针对氧化铝陶瓷的吸湿性,可在储存时采取防潮措施,避免陶瓷吸收过多水分。
5. 避免长时间阳光直射,可选择遮阳材料进行遮盖。
陶瓷砖产品表面缺陷产生原因及解决方法的探讨
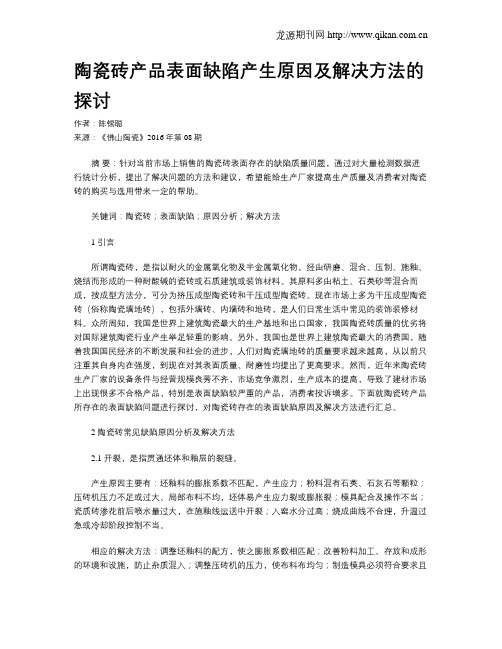
陶瓷砖产品表面缺陷产生原因及解决方法的探讨作者:陈锡聪来源:《佛山陶瓷》2016年第08期摘要:针对当前市场上销售的陶瓷砖表面存在的缺陷质量问题,通过对大量检测数据进行统计分析,提出了解决问题的方法和建议,希望能给生产厂家提高生产质量及消费者对陶瓷砖的购买与选用带来一定的帮助。
关键词:陶瓷砖;表面缺陷;原因分析;解决方法1 引言所谓陶瓷砖,是指以耐火的金属氧化物及半金属氧化物,经由研磨、混合、压制、施釉、烧结而形成的一种耐酸碱的瓷砖或石质建筑或装饰材料。
其原料多由粘土、石英砂等混合而成,按成型方法分,可分为挤压成型陶瓷砖和干压成型陶瓷砖。
现在市场上多为干压成型陶瓷砖(俗称陶瓷墙地砖),包括外墙砖、内墙砖和地砖,是人们日常生活中常见的装饰装修材料。
众所周知,我国是世界上建筑陶瓷最大的生产基地和出口国家,我国陶瓷砖质量的优劣将对国际建筑陶瓷行业产生举足轻重的影响。
另外,我国也是世界上建筑陶瓷最大的消费国,随着我国国民经济的不断发展和社会的进步,人们对陶瓷墙地砖的质量要求越来越高,从以前只注重其自身内在强度,到现在对其表面质量、耐磨性均提出了更高要求。
然而,近年来陶瓷砖生产厂家的设备条件与经营规模良莠不齐,市场竞争激烈,生产成本的提高,导致了建材市场上出现很多不合格产品,特别是表面缺陷较严重的产品,消费者投诉增多。
下面就陶瓷砖产品所存在的表面缺陷问题进行探讨,对陶瓷砖存在的表面缺陷原因及解决方法进行汇总。
2 陶瓷砖常见缺陷原因分析及解决方法2.1 开裂,是指贯通坯体和釉层的裂缝。
产生原因主要有:坯釉料的膨胀系数不匹配,产生应力;粉料混有石英、石灰石等颗粒;压砖机压力不足或过大、局部布料不均,坯体易产生应力裂或膨胀裂;模具配合及操作不当;瓷质砖渗花前后喷水量过大,在施釉线运送中开裂;入窑水分过高;烧成曲线不合理,升温过急或冷却阶段控制不当。
相应的解决方法:调整坯釉料的配方,使之膨胀系数相匹配;改善粉料加工、存放和成形的环境和设施,防止杂质混入;调整压砖机的压力,使布料布均匀;制造模具必须符合要求且安装合理,严格执行脱模的操作规程;控制好喷水量,或采取一定的补救措施来降低干燥速度;严格控制入窑水分(一般在2%以下);调整并控制好烧成曲线。
铝合金型材表面氧化处理工艺缺陷及解决方法探究与探讨
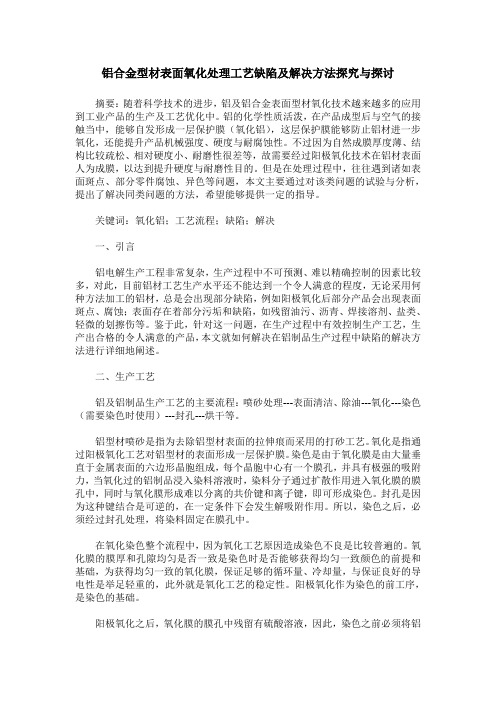
铝合金型材表面氧化处理工艺缺陷及解决方法探究与探讨摘要:随着科学技术的进步,铝及铝合金表面型材氧化技术越来越多的应用到工业产品的生产及工艺优化中。
铝的化学性质活泼,在产品成型后与空气的接触当中,能够自发形成一层保护膜(氧化铝),这层保护膜能够防止铝材进一步氧化,还能提升产品机械强度、硬度与耐腐蚀性。
不过因为自然成膜厚度薄、结构比较疏松、相对硬度小、耐磨性很差等,故需要经过阳极氧化技术在铝材表面人为成膜,以达到提升硬度与耐磨性目的。
但是在处理过程中,往往遇到诸如表面斑点、部分零件腐蚀、异色等问题,本文主要通过对该类问题的试验与分析,提出了解决同类问题的方法,希望能够提供一定的指导。
关键词:氧化铝;工艺流程;缺陷;解决一、引言铝电解生产工程非常复杂,生产过程中不可预测、难以精确控制的因素比较多,对此,目前铝材工艺生产水平还不能达到一个令人满意的程度,无论采用何种方法加工的铝材,总是会出现部分缺陷,例如阳极氧化后部分产品会出现表面斑点、腐蚀;表面存在着部分污垢和缺陷,如残留油污、沥青、焊接溶剂、盐类、轻微的划擦伤等。
鉴于此,针对这一问题,在生产过程中有效控制生产工艺,生产出合格的令人满意的产品,本文就如何解决在铝制品生产过程中缺陷的解决方法进行详细地阐述。
二、生产工艺铝及铝制品生产工艺的主要流程:喷砂处理---表面清洁、除油---氧化---染色(需要染色时使用)---封孔---烘干等。
铝型材喷砂是指为去除铝型材表面的拉伸痕而采用的打砂工艺。
氧化是指通过阳极氧化工艺对铝型材的表面形成一层保护膜。
染色是由于氧化膜是由大量垂直于金属表面的六边形晶胞组成,每个晶胞中心有一个膜孔,并具有极强的吸附力,当氧化过的铝制品浸入染料溶液时,染料分子通过扩散作用进入氧化膜的膜孔中,同时与氧化膜形成难以分离的共价键和离子键,即可形成染色。
封孔是因为这种键结合是可逆的,在一定条件下会发生解吸附作用。
所以,染色之后,必须经过封孔处理,将染料固定在膜孔中。
氧化铝陶瓷烧结常见问题

氧化铝陶瓷烧结常见问题
氧化铝陶瓷烧结过程中可能会遇到的问题包括:
1. 烧结温度高:由于氧化铝的熔点高达2020℃,因此其烧结难度极大。
降低烧结温度是氧化铝陶瓷行业所关心和必需解决的问题。
2. 晶粒尺寸控制:烧结温度对晶粒生长的影响较大,而烧结时间与烧结压力的影响相对来说就比较小一些。
3. 颜色质量问题:在氧化铝陶瓷烧成后,可能会出现瓷件表面有斑点,如黑点、棕点、红点;瓷件表面产生斑块,如暗斑(阴斑),黑色云斑、亮斑等;瓷件有色差现象,如整体发黄或发灰等问题。
解决这些问题的方法包括采用热压烧结技术,即在烧结的同时施加一定的压力,使得原子的扩散速率增大,从而提高了烧结驱动力,使得烧结过程所需的时间大大减短。
此外,还可以通过获得分散均匀、无团聚,并具有良好烧结活性的超细粉体以降低陶瓷的烧结温度。
陶瓷烧制中常见的釉面缺陷及处理方法

陶瓷烧制中常见的釉面缺陷及处理方法陶瓷作为一种古老而又广泛应用的材料,其独特的质感和美观的外观使其在建筑、餐具、装饰等领域得到了广泛的应用。
然而,在陶瓷的烧制过程中,常常会出现一些釉面缺陷,影响了其质量和美观度。
本文将介绍几种常见的釉面缺陷及其处理方法。
首先,我们来讨论一下釉面开裂这一常见的缺陷。
釉面开裂可能是由于釉料与胎体的热胀冷缩系数不匹配所引起的。
在烧制过程中,釉料和胎体会因为温度变化而产生不同程度的膨胀和收缩,如果两者之间的差异过大,就会导致釉面开裂。
为了解决这个问题,可以采取一些措施,如调整釉料的成分,增加胎体的强度等。
此外,适当控制烧制温度和速度也是防止釉面开裂的有效方法。
另一个常见的釉面缺陷是釉面流挂。
釉面流挂是指在烧制过程中,釉料在陶瓷表面形成一层厚重的流挂,影响了陶瓷的外观和质感。
釉面流挂的原因有很多,例如釉料的粘度过高、烧制温度过高等。
为了解决这个问题,可以通过调整釉料的成分和粘度来控制釉面的流动性,同时适当降低烧制温度,避免釉面流挂的发生。
除了釉面开裂和釉面流挂,还有一种常见的釉面缺陷是釉面气泡。
釉面气泡是指在烧制过程中,釉料中的气体无法完全排出,形成的气泡在釉面上留下了不美观的痕迹。
釉面气泡的形成与釉料的成分、烧制温度等因素有关。
为了避免釉面气泡的产生,可以采取一些措施,如调整釉料的成分、控制烧制温度和时间等。
此外,还可以在釉料中添加一些消泡剂来减少气泡的形成。
此外,在陶瓷烧制过程中,还会出现一些其他的釉面缺陷,如釉面色斑、釉面剥落等。
这些缺陷的产生原因各不相同,处理方法也各有不同。
对于釉面色斑,可以通过调整釉料的成分和配比来解决。
对于釉面剥落,可以采取一些措施,如增加釉料的附着力、增加胎体的强度等。
总之,陶瓷烧制中常见的釉面缺陷给陶瓷的质量和美观度带来了一定的影响。
通过对釉面缺陷的原因进行分析,我们可以采取相应的处理方法来解决这些问题。
调整釉料的成分、控制烧制温度和时间、增加胎体的强度等都是有效的方法。
陶瓷色差分析及预防解决措施

陶瓷色差分析及预防解决措施査武华杨涛江健黄焱墉方晓凯李清莲摘要:随着社会经济和人文文化的快速发展,人类欣赏水平的提升,陶瓷行业从“一片黄”发展到如今的“一片灰”,从玉石到大理石,从一石一面到一石多面,现代的装修讲究多元化铺贴的整体效果,而不是四四方方一模一样的呆板老气。
色彩的喜爱和铺贴风格的变化,对于陶瓷行业生产来说,却带来了一个技术难题:色差/阴阳色。
关键词:色差/阴阳色;一石多面;铺贴效果;大理石1 引言陶瓷色差是指一片砖与另一片砖的颜色差异,或同一片砖的不同部分之间的颜色差异。
在光线均匀空间的空地上铺贴9—12件砖,目测整体效果颜色均匀,则可视为无色差,反之则视为色差降级。
其中也有些一石多面的大理石产品,设计纹理落差大,深受一些消费者喜欢,也可视为无色差。
造成陶瓷产品出现色差的主要原因有设计色差、淋釉色差、喷墨机色差、窑炉色差、抛光色差和其它色差等等。
本文结合作者自身陶瓷生产经验以及向同行业了解到相关的信息与大家探讨如何判断色差原因以及采取对应的解决措施。
2 色差分析和预防解决措施解决问题的首要条件是找到问题,要想解决陶瓷色差带来的降级损失就必须先清楚造成色差的因素。
造成色差的原因主要为设计色差、淋釉色差、喷墨机色差、窑炉色差、抛光色差和其它色差等等。
正确的铺贴摆砖方向有助于分析和判定导致色差的因素。
最常用的摆砖方向,如图1,可以清晰的对比出几个因素有没有问题。
2.1 设计色差当摆砖对板发现色差,第一步就要确定设计有没有色差,因为设计图是诸多导致色差唯一固定不变的因素,首先取窑尾同花色中间代号两件砖按图2摆好。
当靠在一起的两个B边和A边无色差,才能证明设计正常;反之则需要修改设计。
修改设计的技巧很多,拉深各颜色通道图层检查差异,圈选调整。
推荐一个修图片上下边色差的方法:选择【滤镜】—【其它】—【位移】。
2.2 淋釉色差在生产白色产品或玉石类产品的时候,都会忽视釉量不均导致的色差降级风险,因为这两种产品几乎不会出现窑炉色差、抛光色差、设计色差、喷墨机色差等等。
陶瓷烧制工艺中常见问题的解决方法与经验总结
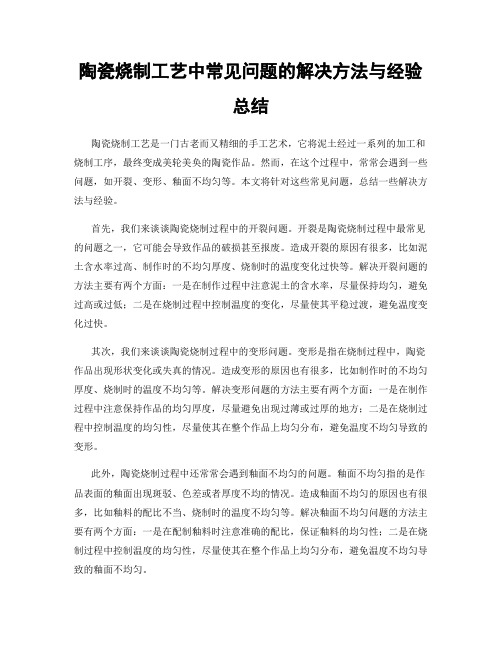
陶瓷烧制工艺中常见问题的解决方法与经验总结陶瓷烧制工艺是一门古老而又精细的手工艺术,它将泥土经过一系列的加工和烧制工序,最终变成美轮美奂的陶瓷作品。
然而,在这个过程中,常常会遇到一些问题,如开裂、变形、釉面不均匀等。
本文将针对这些常见问题,总结一些解决方法与经验。
首先,我们来谈谈陶瓷烧制过程中的开裂问题。
开裂是陶瓷烧制过程中最常见的问题之一,它可能会导致作品的破损甚至报废。
造成开裂的原因有很多,比如泥土含水率过高、制作时的不均匀厚度、烧制时的温度变化过快等。
解决开裂问题的方法主要有两个方面:一是在制作过程中注意泥土的含水率,尽量保持均匀,避免过高或过低;二是在烧制过程中控制温度的变化,尽量使其平稳过渡,避免温度变化过快。
其次,我们来谈谈陶瓷烧制过程中的变形问题。
变形是指在烧制过程中,陶瓷作品出现形状变化或失真的情况。
造成变形的原因也有很多,比如制作时的不均匀厚度、烧制时的温度不均匀等。
解决变形问题的方法主要有两个方面:一是在制作过程中注意保持作品的均匀厚度,尽量避免出现过薄或过厚的地方;二是在烧制过程中控制温度的均匀性,尽量使其在整个作品上均匀分布,避免温度不均匀导致的变形。
此外,陶瓷烧制过程中还常常会遇到釉面不均匀的问题。
釉面不均匀指的是作品表面的釉面出现斑驳、色差或者厚度不均的情况。
造成釉面不均匀的原因也有很多,比如釉料的配比不当、烧制时的温度不均匀等。
解决釉面不均匀问题的方法主要有两个方面:一是在配制釉料时注意准确的配比,保证釉料的均匀性;二是在烧制过程中控制温度的均匀性,尽量使其在整个作品上均匀分布,避免温度不均匀导致的釉面不均匀。
除了以上常见问题的解决方法,还有一些经验值得总结。
首先,制作陶瓷作品时要注意保持作品的均匀性,避免出现过薄或过厚的地方,这样可以减少开裂和变形的可能性。
其次,烧制陶瓷作品时要注意温度的控制,尽量使其平稳过渡,避免温度变化过快导致的开裂和变形。
最后,配制釉料时要注意准确的配比,保证釉料的均匀性,避免釉面出现不均匀的情况。
氧化铝陶瓷的缺点-概念解析以及定义
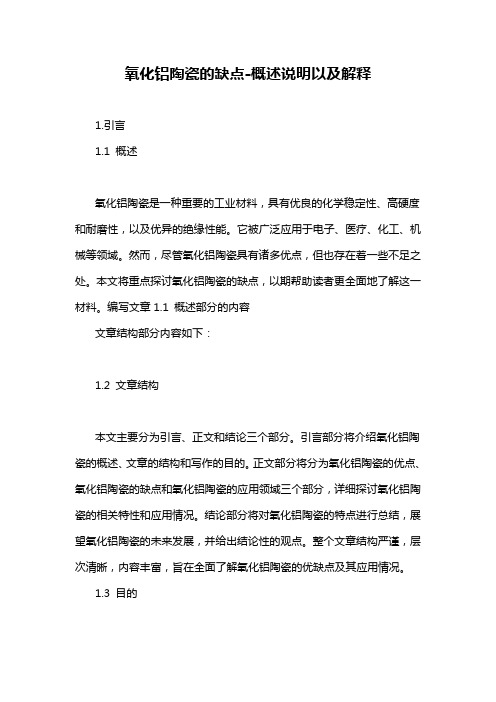
氧化铝陶瓷的缺点-概述说明以及解释1.引言1.1 概述氧化铝陶瓷是一种重要的工业材料,具有优良的化学稳定性、高硬度和耐磨性,以及优异的绝缘性能。
它被广泛应用于电子、医疗、化工、机械等领域。
然而,尽管氧化铝陶瓷具有诸多优点,但也存在着一些不足之处。
本文将重点探讨氧化铝陶瓷的缺点,以期帮助读者更全面地了解这一材料。
编写文章1.1 概述部分的内容文章结构部分内容如下:1.2 文章结构本文主要分为引言、正文和结论三个部分。
引言部分将介绍氧化铝陶瓷的概述、文章的结构和写作的目的。
正文部分将分为氧化铝陶瓷的优点、氧化铝陶瓷的缺点和氧化铝陶瓷的应用领域三个部分,详细探讨氧化铝陶瓷的相关特性和应用情况。
结论部分将对氧化铝陶瓷的特点进行总结,展望氧化铝陶瓷的未来发展,并给出结论性的观点。
整个文章结构严谨,层次清晰,内容丰富,旨在全面了解氧化铝陶瓷的优缺点及其应用情况。
1.3 目的本文旨在探讨氧化铝陶瓷在工业生产和实际应用中存在的一些缺点。
通过对氧化铝陶瓷的缺点进行分析和总结,我们可以更全面地了解该材料的特性,并为未来在材料研究和工程应用中的改进提供一定的参考和指导。
同时,本文也旨在引起人们对氧化铝陶瓷材料的重视,促进氧化铝陶瓷在工业生产和其他领域的更加广泛的应用和发展。
2.正文2.1 氧化铝陶瓷的优点氧化铝陶瓷作为一种常见的工业材料,在许多方面都具有优异的性能,其优点主要包括以下几个方面:1. 耐高温性能:氧化铝陶瓷具有优异的耐高温性能,可以在高温环境下保持稳定的物理和化学性质。
这使得氧化铝陶瓷在高温工艺和耐火材料领域有着广泛的应用。
2. 耐磨损性能:由于氧化铝陶瓷具有高硬度和优异的耐磨损性能,因此被广泛用于制造耐磨零件,如轴承、瓦刀和研磨介质等。
3. 良好的化学稳定性:氧化铝陶瓷在常见的酸碱介质中具有良好的化学稳定性,不易受腐蚀,因此被广泛应用于化工和医药领域。
4. 绝缘性能:氧化铝陶瓷具有良好的绝缘性能,能够有效阻止电流的传导,因此常被用于制造绝缘零件和电子器件的外壳。
常见陶瓷烧制问题解决办法汇总

常见陶瓷烧制问题解决办法汇总陶瓷是一种古老而又美丽的艺术形式,它的烧制过程是非常重要的。
然而,烧制陶瓷时常常会遇到一些问题,比如开裂、变形、釉面不均匀等等。
在本文中,我们将汇总一些常见的陶瓷烧制问题,并提供相应的解决办法。
1. 开裂问题开裂是陶瓷烧制过程中最常见的问题之一。
它通常是由于烧制过程中的温度变化过快引起的。
为了避免开裂,我们可以采取以下措施:- 控制烧制速度:将烧制过程中的温度变化控制在一个合理的范围内,避免温度变化过快。
- 使用合适的烧制工艺:根据陶瓷的种类和形状选择合适的烧制工艺,避免过度收缩或不均匀收缩导致开裂。
2. 变形问题陶瓷在烧制过程中也容易发生变形,特别是对于大型或复杂形状的陶瓷作品来说。
为了解决变形问题,我们可以采取以下方法:- 控制烧制温度:根据陶瓷的种类和形状,控制烧制温度,避免过高温度导致变形。
- 使用支撑物:对于大型或复杂形状的陶瓷作品,可以使用支撑物来支持其结构,减少变形的可能性。
3. 釉面不均匀问题釉面不均匀是指陶瓷作品在烧制过程中釉面出现斑点或颜色不均匀的情况。
为了解决这个问题,我们可以尝试以下方法:- 均匀涂釉:在涂釉过程中,要确保釉料均匀地覆盖在陶瓷表面,避免出现厚薄不均的情况。
- 控制烧制温度:烧制温度过高或过低都可能导致釉面不均匀,因此需要根据釉料的特性选择合适的烧制温度。
4. 烧结不完全问题烧结不完全是指陶瓷作品在烧制过程中未能完全烧结,导致其强度不够或存在孔隙。
为了解决这个问题,我们可以采取以下方法:- 控制烧制温度和时间:根据陶瓷的种类和形状,控制烧制温度和时间,确保陶瓷作品能够充分烧结。
- 添加助烧剂:对于一些特殊的陶瓷材料,可以添加一些助烧剂来促进烧结过程,提高陶瓷的强度。
总结:烧制陶瓷是一门复杂的工艺,常常会遇到各种问题。
然而,通过掌握一些基本的解决办法,我们可以解决大部分常见的烧制问题。
在实践中,我们还应该不断积累经验,提高自己的技术水平。
氧化铝流延生瓷片正反色差大的原因

一、氧化铝流延生瓷片的特点氧化铝流延生瓷片是一种使用氧化铝粉末和其他添加剂制成的陶瓷材料。
由于其硬度高、耐磨损、耐腐蚀等优点,氧化铝流延生瓷片被广泛应用于电子、机械、化工等领域。
然而,一些生产厂家在生产过程中发现,氧化铝流延生瓷片的正反色差较大,给产品的外观质量带来了一定的影响。
二、可能导致正反色差的原因1.原料选择不当在氧化铝流延生瓷片的生产过程中,原料的选择对产品的质量有着至关重要的影响。
如果所选用的氧化铝粉末和添加剂质量不稳定,可能会导致生瓷片的成分不均匀,从而出现正反色差较大的问题。
2.生产工艺不当生产工艺是影响产品质量的重要因素之一。
如果在氧化铝流延生瓷片的生产过程中,温度、压力、时间等参数控制不当,也会导致产品的正反色差较大。
3.材料成分不均匀在氧化铝流延生瓷片的生产过程中,材料成分的均匀度直接影响产品的质量。
如果混合过程中氧化铝粉末与其他添加剂的混合不均匀,会导致产品的成分不均匀,进而造成正反色差较大的问题。
4.流延过程控制不当流延是制备氧化铝流延生瓷片的关键工艺之一。
如果在流延过程中,温度、压力、速度等参数控制不当,会导致产品厚度不均匀,从而出现正反色差较大的问题。
5.烧结工艺不良烧结是氧化铝流延生瓷片在成型过程中的重要环节。
如果烧结温度、时间控制不当,会导致产品晶粒长大不均匀,进而影响产品的正反色差。
三、解决正反色差较大的问题的方法为了解决氧化铝流延生瓷片正反色差较大的问题,生产厂家可以从以下几个方面进行改进:1. 提高原料的质量稳定性,选择稳定可靠的原料供应商,并加强对原料的质量控制。
2. 优化生产工艺,确保在生产过程中参数控制的稳定性,降低产品的成本差异。
3. 完善产品检测体系,加强对产品质量的监控,及时发现并解决产品的质量问题。
4. 加强员工的技术培训,提高员工的质量意识,增强全员质量管理。
四、结语在氧化铝流延生瓷片的生产过程中,正反色差较大的问题是一个比较常见的质量问题。
陶瓷产品常见质量缺陷检测及形成原因

破坏强度:S=F L ∕b
S——破坏强度,N; F——破坏载荷,N;
L——支撑棒之间跨距,mm ;
b—— 试样的宽度,mm .
断裂模数:R=3FL/2bh2
h——实验后沿断边测得试样断裂的最小厚
度。
★吸水率
吸水率是在指陶瓷产品最基本的指标, 它是以陶瓷砖开口气孔吸入饱和的水分 占干砖质量的百分比来表示。通常情况 下,吸水率的大小决定了产品性能的高 低。
★吸水率计算公式:
吸水率计算公式:
E=(m2-m1)/m1*100%
其中:E—砖的吸水率 m1—干砖的质量 m2—湿砖的质量
★产品的放射性
由于建筑材料含天然放射性(镭-226、 钍-232、钾-40),具有一定的放射性,因 此必须对其放射性比活度进行限量、以减 少对人体的影响。
国家标准 GB6566-2001 规定了产品内照 射指数与外指数的量,我公司的陶瓷通过 中国强制认证(3C认证)和环保产品认证, 放射性水平为A类,使用范围不受限制。
★边直度、直角度
边直度:在砖的平面内边的中央偏离直线 的偏差(这种测量只适用于砖的直边)。
直角度:将砖的一个角紧靠着放在标准板 校正过的直尺上,测量它与标准直角度的 偏差
★边直度、直角度的测量方法:
★平整度的分类
☆平整度包括:边弯曲度、中心弯曲度、翘曲度
边弯曲度:砖的一条边的中心偏离由该边两角为直线的 距离;
★光泽度
光泽度表征砖面上镜面反射光的强弱。我 国国家标准GB3295—1996中规定,测量 砖面的光泽度时用黑色玻璃板作为标准板, 用硒光电池测量照射在砖面反射光的反光 量,被测砖在的反光能力与黑玻璃的反光 能力相比较得出砖的光泽主度。通常用光 泽度仪器来测其光泽度,国家标准中规定 抛光砖的光泽度>55度。内控标准规定: 超洁亮产品的光泽度要求在90度以上。
氧化铝粉体黑点 国标
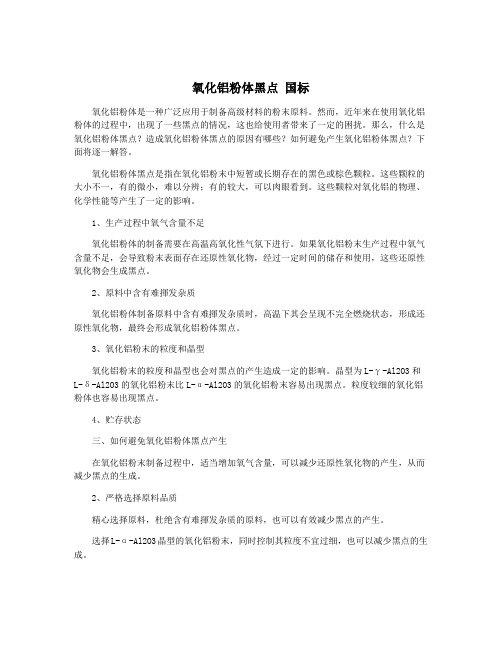
氧化铝粉体黑点国标氧化铝粉体是一种广泛应用于制备高级材料的粉末原料。
然而,近年来在使用氧化铝粉体的过程中,出现了一些黑点的情况,这也给使用者带来了一定的困扰。
那么,什么是氧化铝粉体黑点?造成氧化铝粉体黑点的原因有哪些?如何避免产生氧化铝粉体黑点?下面将逐一解答。
氧化铝粉体黑点是指在氧化铝粉末中短暂或长期存在的黑色或棕色颗粒。
这些颗粒的大小不一,有的微小,难以分辨;有的较大,可以肉眼看到。
这些颗粒对氧化铝的物理、化学性能等产生了一定的影响。
1、生产过程中氧气含量不足氧化铝粉体的制备需要在高温高氧化性气氛下进行。
如果氧化铝粉末生产过程中氧气含量不足,会导致粉末表面存在还原性氧化物,经过一定时间的储存和使用,这些还原性氧化物会生成黑点。
2、原料中含有难揮发杂质氧化铝粉体制备原料中含有难揮发杂质时,高温下其会呈现不完全燃烧状态,形成还原性氧化物,最终会形成氧化铝粉体黑点。
3、氧化铝粉末的粒度和晶型氧化铝粉末的粒度和晶型也会对黑点的产生造成一定的影响。
晶型为L-γ-Al2O3和L-δ-Al2O3的氧化铝粉末比L-α-Al2O3的氧化铝粉末容易出现黑点。
粒度较细的氧化铝粉体也容易出现黑点。
4、贮存状态三、如何避免氧化铝粉体黑点产生在氧化铝粉末制备过程中,适当增加氧气含量,可以减少还原性氧化物的产生,从而减少黑点的生成。
2、严格选择原料品质精心选择原料,杜绝含有难揮发杂质的原料,也可以有效减少黑点的产生。
选择L-α-Al2O3晶型的氧化铝粉末,同时控制其粒度不宜过细,也可以减少黑点的生成。
在氧化铝粉末的贮存过程中,应该采取密封、干燥的贮存方式,避免吸潮、受潮,从而减少黑点的产生。
总之,氧化铝粉体黑点的产生与氧气含量、原料品质、氧化铝粉体的晶型和粒度以及储存状态都有一定的关系,只有在生产和储存过程中严格控制,才能够有效减少氧化铝粉体黑点的产生,为粉末原料的应用提供更好的品质保证。
- 1、下载文档前请自行甄别文档内容的完整性,平台不提供额外的编辑、内容补充、找答案等附加服务。
- 2、"仅部分预览"的文档,不可在线预览部分如存在完整性等问题,可反馈申请退款(可完整预览的文档不适用该条件!)。
- 3、如文档侵犯您的权益,请联系客服反馈,我们会尽快为您处理(人工客服工作时间:9:00-18:30)。
95,99氧化铝 陶瓷一般常 用的生产工艺有热 压铸工 艺和模压成型工艺(干压和等静压)。不蚓生 产工 艺 、成型方法,可能的污 泄 : ,下面分别论述。
第 23卷 第 2期 2016年 4月
Байду номын сангаас
中 国 陶 瓷 工 业
CHIN A CERA M IC IN DU STRY
DOI:1 0.1 39 58/J.cnki.Ztcg.2 01 6.02.009
Vo1.23,No.2 Apr.2016
氧化铝 陶瓷烧成缺 陷 :斑点 、色斑及色差 的成 因和预 防解 决方法的探讨
解决办法 ,与业内人士进行探讨 ,希望对提高氧化 铝 陶 瓷 的产 品质量 有所 帮助 。
1 氧 化 铝瓷 (95、99瓷)瓷件 斑 点
1.1 常见 现象 在氧化铝瓷生产过程 中,经常在瓷件表面会有
黑色 、褐色 、棕色和粉红色斑点 ,仔细观察内部也 有(见图1,2,3),此斑点是造成氧化铝 瓷制 品产
从斑 点 的形状 、大小 也可 以看 出 ,上述 斑 点 的 产生主要是由颗粒状金属杂质 引入所致。通过分析 斑 点 成分 和追 踪 生产工 艺 和生 产过 程 ,可 以初 步 判 定 黑色 、棕 色 、褐色斑 点 主要 在原 料及 陶 瓷生 产过 程 中 混入机 械 铁粒 子造 成 。而 粉红 色斑 点 从成 份分 析 可 以判 断是 由不锈钢 材 料 的细小 颗粒 造 成 。
图 1 氧 化铝 瓷件 的黑 色斑 点
Fig.1 Black spot in alum ina ceram ic specimen
收稿 日期 :2015一l1—20。
修订 日期 :2015—11—25
通信联 系人 :孙志昂 , ,高级工程师 。
Received date:2015—11-20.
作 者在 从事 三 十 多年的 氧化铝 陶 瓷工 作经 历 中 总结 出遇 到 的氧 化铝 陶瓷 烧成 后常 见 的有关 颜 色 的 质量问题有 :①瓷件表面有斑点 ,如黑点 、棕点 、 红点 ;②瓷件表面产生斑块 ,如暗斑(阴斑),黑色 云斑 、亮斑等 ;③瓷件有色差现象,如整体发黄或
发灰 ;④瓷件经 日光照射后变黄 。 本 文 主要 针对 上述 现象 的成 因进 行分 析 并探索
孙 志 昂,蒋晓辉
(中闰长城铝业公司 ,河南长兴实业有限公 司 ,河 南 郑州 450041)
摘 要:对 氧化舒{陶瓷产品缺陷中的色点 、色斑及色差等质量问题产生 的原 因进行了分析 ,并研究和探索了预防和解决措施 。 关键词 :氧化 铝 ;陶瓷 ;斑点 ;色斑 ;产品缺陷 中 图分 类号 :TQ174.75 文 献 标 志 码 :A 文 章编 号 : 1006—2874(2016)02-0043—07
·45 ·
表 2 氧化铝 瓷 件(图8),-v常部 位能 谱微 量 元素表 Tab.2 Trace element detection table of thc normal position of alumina specimen(Fig.3)
本 可 确 定 为 :产 生 黑 色 、棕 色 和 褐 色 斑 点 的 主 要 杂质 成 分为Fe,粉红 色斑 点 的主 要 杂质 为Fe,Cr、 Ni。郑 州海赛 高 技术 陶瓷 有 限公 一J的孟德 安 曾对 氧 化 铝 陶 瓷瓷件 上 的红 色 ,黑 色斑 点进 行 了谱扫 描 电 镜 和 能谱 分析 证 明主 要成 分 为铁 。
Firing Defects of Alumina Ceram ics:Causes,Prevention M easures and Solutions of Spots,Stains and Color Aberration
SUN Zhi'ang,JIAN G X iaohui (Henan Changxing Industrial Co.,Ltd.,China Great W all Aluminum Corporation,Zhengzhou 450041,Henan,China)
A bstract:This paper analyzes the causes of alumina ceramic defects including color spots,color stains,color aberration,etc.and explores w ays to prevent and resolve these problem s. K ey w ords:alum ina;ceram ics;spot; stain;product defect
0 引 言
氧化铝瓷 由于具有 耐高温 、耐磨 、耐酸碱腐 蚀 、抗 氧化 、耐 烧蚀 、高温 下蠕 变小 以及 优异 绝缘 性能 和 电性 能 ,被 广 泛应 用 于能 源 、航天 航空 、机 械 、汽车 、冶金 、化工 、电力 、电子等领域 。成为 发 展极为迅速 的陶瓷材料 ,特 别是氧化铝 瓷95瓷 和99瓷 ,无 论在 结 构 陶 瓷或 是 电子 陶 瓷 均 是 应 用 范 围最 广 ,用 量 最 大 的 陶瓷 材 料之 一 。 氧 化 铝 陶 瓷(95瓷 、99瓷)目前常用 的成型方法不外乎热压铸 成型 、模压 、等静压成型和流延法成型 ,上述几种 成型工艺在陶瓷烧成前都经历较 多生产工序 ,在过 程 中物 料 与机械 、设 备 、工 具 、器皿 、环 境接 触机 会较 多。 因此 ,出现 污染 及 瓷件 质量 问题 的 因素也 较 多 。
Revised date:2015—11—25
Correspondent author:SUN Zhi’ang m ale,Senior engineer ,
E—mail:sza61@126.com
第23卷第2期 孙 志昂 等 :氧化铝 陶瓷烧成缺 陷 :斑点、色斑及色差的成 因和预 防解 决方 法的探讨