催化裂化装置滑阀设计技术规定
催化裂化装置各岗位安全技术操作规程
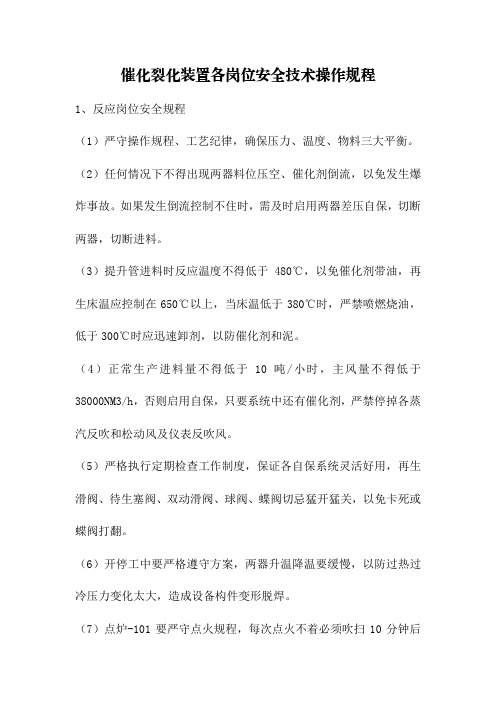
催化裂化装置各岗位安全技术操作规程1、反应岗位安全规程(1)严守操作规程、工艺纪律,确保压力、温度、物料三大平衡。
(2)任何情况下不得出现两器料位压空、催化剂倒流,以免发生爆炸事故。
如果发生倒流控制不住时,需及时启用两器差压自保,切断两器,切断进料。
(3)提升管进料时反应温度不得低于480℃,以免催化剂带油,再生床温应控制在650℃以上,当床温低于380℃时,严禁喷燃烧油,低于300℃时应迅速卸剂,以防催化剂和泥。
(4)正常生产进料量不得低于10吨/小时,主风量不得低于38000NM3/h,否则启用自保,只要系统中还有催化剂,严禁停掉各蒸汽反吹和松动风及仪表反吹风。
(5)严格执行定期检查工作制度,保证各自保系统灵活好用,再生滑阀、待生塞阀、双动滑阀、球阀、蝶阀切忌猛开猛关,以免卡死或蝶阀打翻。
(6)开停工中要严格遵守方案,两器升温降温要缓慢,以防过热过冷压力变化太大,造成设备构件变形脱焊。
(7)点炉-101要严守点火规程,每次点火不着必须吹扫10分钟后再点。
(8)严格遵守交接班和巡回检查制度,发生任何设备和操作事故一定要及时查清原因,坚持操作平稳、事情不明不交班。
(9)催化剂罐抽真空的蒸汽系统停用后,要将蒸汽放空阀打开,以防蒸汽串入催化剂罐使催化剂和泥。
(10)事故状态下,一般情况应先联系后处理,特殊情况下按事故处理原则进行处理,以免扩大事故。
同时操作员一定要沉着、冷静、周密分析,正确判断和处理,要服从命令,听指挥、严禁惊慌失措、高声喊叫。
2、分馏岗位安全规程(1)严格执行操作规程和工艺指标,集中精力细心操作,保证产品质量和收率。
(2)认真执行交接班制度和巡回检查制度,发现问题及时汇报处理。
(3)控制住塔顶温度和压力,严防冲塔和反应憋压。
(4)始终保证油浆循环、控制好塔底液面,严禁泵抽空和反应憋压。
(5)控制好V202液面不高于70%,以免反应憋压和气压机抽液体。
(6)分馏副操保证本岗位热油备用泵的预热。
滑阀使用说明书

冷壁式滑阀使用说明书荆门炼化机械有限公司目录1、概述2、技术参数3、结构简介4、安装说明5、维护说明6、易损件明细表一、概述滑阀用于催化裂化装置反-再系统,按阀板作用形式可分为单动滑阀和双动滑阀两种,按隔热形式又可分为外保温的热壁滑阀和内设隔热耐磨衬里的冷壁滑阀。
目前在催化裂化装置中使用的基本都是冷壁滑阀。
二、技术参数DN 冷壁式动滑阀三、结构简介冷壁式单动滑阀采用等径或异径三通结构。
冷壁式双动滑阀采用异径四通结构。
阀门壳体为20R或16MnR钢板铆焊件。
阀体内部衬有100~150mm的有龟甲网双层衬里。
耐磨衬里采用TA-218高强度耐火浇注料,隔热衬里采用QA-212浇注料。
衬里采用柱型保温钉加龟甲网锚固连接,使双层衬里成为完整的一体。
操作温度下,阀体外壁温度一般不超过200℃。
阀体与相邻接管的连接采用同类材料焊接方式,质量容易保证,而且衬里后两者的内径相同,介质流动平稳,避免了变径处的局部磨损。
阀体与阀盖采用标准圆形法兰结构连接,其受力均匀,密封面加工质量容易保证,配用不锈钢内加强环缠绕垫片,确保密封可靠。
另外,圆形法兰开口大,便于现场安装和维修。
阀盖采用组焊结构,内衬有龟甲网双层衬里。
阀盖两侧和填料函上分别设有导轨和阀杆吹扫接口。
阀盖上的填料函采用串联填料密封结构,填料函内安装了工作和备用两种不同的填料。
当工作填料失效发生泄漏时,可向备用填料的注浇口注入油脂二硫化钼及石墨料的稠状混合物,挤紧内侧的备用填料,使该填料起密封作用,这样即可及时更换外侧的工作填料,保证装置正常运行。
节流锥是高温受力部件,它承受介质压差即阀座圈、导轨、阀板的全部重量。
节流锥由高温合金钢铸造而成,其上端阀壳体采用螺栓或焊接连接,下端悬挂直接与阀座圈连接,在开、停工温度骤变时可自由伸缩。
各种合金螺栓与螺母之间装配时均涂有高温防咬剂,防止高温咬死。
所有高温螺母均点焊防松。
阀座圈采用高温合金钢铸件,表面衬单层TA-218耐磨衬里。
滑阀
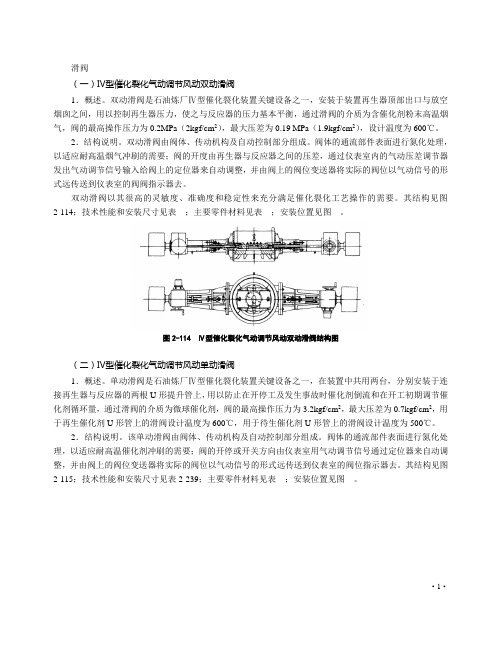
滑阀(一)Ⅳ型催化裂化气动调节风动双动滑阀1.概述。
双动滑阀是石油炼厂Ⅳ型催化裂化装置关键设备之一,安装于装置再生器顶部出口与放空烟囱之间,用以控制再生器压力,使之与反应器的压力基本平衡,通过滑阀的介质为含催化剂粉末高温烟气,阀的最高操作压力为0.2MPa(2kgf/cm2),最大压差为0.19 MPa(1.9kgf/cm2),设计温度为600℃。
2.结构说明。
双动滑阀由阀体、传动机构及自动控制部分组成。
阀体的通流部件表面进行氮化处理,以适应耐高温烟气冲刷的需要;阀的开度由再生器与反应器之间的压差,通过仪表室内的气动压差调节器发出气动调节信号输入给阀上的定位器来自动调整,并由阀上的阀位变送器将实际的阀位以气动信号的形式远传送到仪表室的阀阀指示器去。
双动滑阀以其很高的灵敏度、准确度和稳定性来充分满足催化裂化工艺操作的需要。
其结构见图2-114;技术性能和安装尺寸见表;主要零件材料见表;安装位置见图。
图2-114 Ⅳ型催化裂化气动调节风动双动滑阀结构图(二)Ⅳ型催化裂化气动调节风动单动滑阀1.概述。
单动滑阀是石油炼厂Ⅳ型催化裂化装置关键设备之一,在装置中共用两台,分别安装于连接再生器与反应器的两根U形提升管上,用以防止在开停工及发生事故时催化剂倒流和在开工初期调节催化剂循环量,通过滑阀的介质为微球催化剂,阀的最高操作压力为3.2kgf/cm2,最大压差为0.7kgf/cm2,用于再生催化剂U形管上的滑阀设计温度为600℃,用于待生催化剂U形管上的滑阀设计温度为500℃。
2.结构说明。
该单动滑阀由阀体、传动机构及自动控制部分组成。
阀体的通流部件表面进行氮化处理,以适应耐高温催化剂冲刷的需要;阀的开停或开关方向由仪表室用气动调节信号通过定位器来自动调整,并由阀上的阀位变送器将实际的阀位以气动信号的形式远传送到仪表室的阀位指示器去。
其结构见图2-115;技术性能和安装尺寸见表2-239;主要零件材料见表;安装位置见图。
催化裂化装置烟气轮机入口阀门的配置
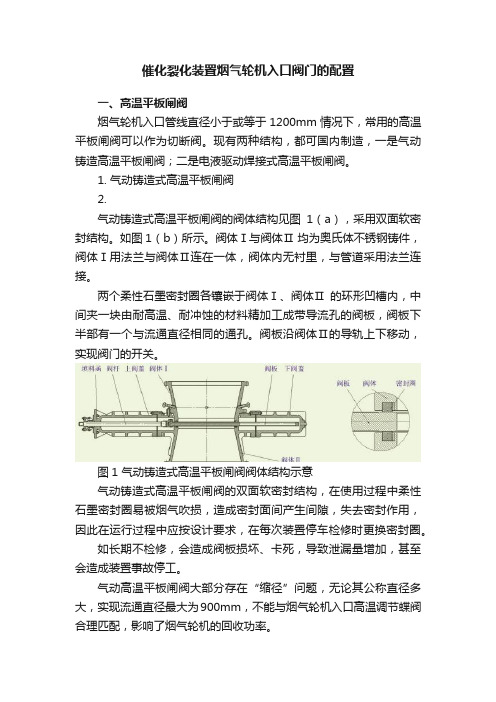
催化裂化装置烟气轮机入口阀门的配置一、高温平板闸阀烟气轮机入口管线直径小于或等于1200mm情况下,常用的高温平板闸阀可以作为切断阀。
现有两种结构,都可国内制造,一是气动铸造高温平板闸阀;二是电液驱动焊接式高温平板闸阀。
1.气动铸造式高温平板闸阀2.气动铸造式高温平板闸阀的阀体结构见图1(a),采用双面软密封结构。
如图1(b)所示。
阀体Ⅰ与阀体Ⅱ 均为奥氏体不锈钢铸件,阀体Ⅰ用法兰与阀体Ⅱ连在一体,阀体内无衬里,与管道采用法兰连接。
两个柔性石墨密封圈各镶嵌于阀体Ⅰ、阀体Ⅱ 的环形凹槽内,中间夹一块由耐高温、耐冲蚀的材料精加工成带导流孔的阀板,阀板下半部有一个与流通直径相同的通孔。
阀板沿阀体Ⅱ的导轨上下移动,实现阀门的开关。
图1 气动铸造式高温平板闸阀阀体结构示意气动铸造式高温平板闸阀的双面软密封结构,在使用过程中柔性石墨密封圈易被烟气吹损,造成密封面间产生间隙,失去密封作用,因此在运行过程中应按设计要求,在每次装置停车检修时更换密封圈。
如长期不检修,会造成阀板损坏、卡死,导致泄漏量增加,甚至会造成装置事故停工。
气动高温平板闸阀大部分存在“缩径”问题,无论其公称直径多大,实现流通直径最大为900mm,不能与烟气轮机入口高温调节蝶阀合理匹配,影响了烟气轮机的回收功率。
气动高温平板闸阀的上述缺点也促进了对单面金属硬密封电液高温闸阀的研发。
2. 电液高温平板闸阀电液高温平板闸阀为电液单面金属硬密封焊接式高温平板闸阀的阀体结构见图2(a),阀板和阀座圈采用单面金属硬密封加蒸汽辅助密封结构,如图2(b)所示。
阀体、阀盖均为大型厚壁奥氏体不锈钢板组焊结构,阀体内无衬里,其公称直径与流通直径一致,与管道采用焊接方式连接,现已实现工业应用的最大公称直径为1200mm。
图2 电液单面金属硬密封焊接式高温平板闸阀阀体结构示意阀体和阀盖采用方法兰联接,唇型密封。
阀座圈用高温合金螺栓固定在阀体上,两条“L”形导轨用高温合金螺栓固定在阀座圈上。
重油催化裂化装置主要技术方案

重油催化裂化装置主要技术方案1.1 工艺技术路线①采用多产丙烯技术采用多产丙烯技术,在降低汽油中的烯烃含量的同时,增加液化石油气特别是丙烯的产率。
②采用增产丙烯专用催化剂为满足本装置生产低烯烃汽油的要求,设计考虑采用增产丙烯专用催化剂。
③重油原料雾化采用CS型高效喷嘴CS型喷嘴具有雾化效果好、焦炭产率低、轻质油收率高、操作平稳等特点,可以充分满足工艺过程的要求,且在一定程度上可降低蒸汽消耗。
④反应再生系统采用PLY型高效旋风分离器从维持反-再系统平稳操作,减少催化剂自然跑损的角度出发,反应再生系统中旋风分离器均采用分离效率高的PLY型旋风分离器。
⑤采用高效汽提技术提高汽提效果对降低再生器烧焦负荷有很大好处。
本设计重油沉降器及汽油沉降器采用了高效汽提技术并对汽提段进行特殊设计,以改善汽提蒸汽与待生催化剂的接触,提高汽提效果。
1.2 工艺技术特点1.2.1采用同轴式两器型式本设计重油沉降器与再生器采用同轴式两器布置。
该两器型式具有技术先进、操作简单、抗事故能力强、能耗低及占地少等特点。
1.2.2再生工艺方案再生方案的选择以满足降低再生催化剂的定碳、使催化剂性能得以充分恢复,同时避免采用过于苛刻的再生条件,有利于保护催化剂活性为前提。
本装置采用单段逆流再生,催化剂定碳<0.1%。
该技术由以下几种单项技术组成:⑴采取加CO助燃剂的完全再生方案采用该方案后,平均氧浓度的提高可使再生剂含碳明显降低,特别对于单段再生其效果更加明显。
⑵采用较低的再生温度较低的再生温度有利于提高剂油比并保护催化剂活性,为反应原料提供更多的活性中心。
⑶采用逆流再生通过加高待生套筒使待生催化剂进入密相床上部,并良好分配,然后向下流动与主风形成气固逆流接触,有利于提高总的烧焦强度并减轻催化剂的水热失活。
⑷采用待生催化剂分配技术在待生套筒出口配置特殊设计的待生催化剂分配器,使待生剂均匀分布于再生密相床上部,为单段逆流高效再生提供基本的保证。
催化裂化装置操作规程确定版

第一章概述第一节装置加工能力及组成装置设计加工能力为10×104吨/年,以原料油为混合原油的蜡油(设计比重0.9183g/cm3,残炭0.363m%)并掺炼30%的减压渣油或常压重油(设计比重0. 9839g/cm3,残炭19.208m%)为原料,多产液化石油气及高辛烷值汽油。
装置由反应再生、分馏、吸收稳定(精制)、主风、气压、司泵等部分组成,产品有汽油、轻柴油、液化气、干气等。
原料及产品性质见表达式1、2、3:第二节主要工艺技术,控制方案及特点第一条目的产品收率高,富产液化石油气,石油气中富含烯烃(尢其是丙烯、丁烯)可提供更多的化工原料。
第二条反应温度略高,在490-520℃之间,采用较低的反应压力和较长的反应停留时间一般为3~4秒,其操作灵活性大,可采用油浆全回炼和部分回炼的操作方式,以得到更多的液化石油气和汽油;采用较大的注气量,一般占总进料的~10w%,以降低油气分压;采用较大的剂油比操作,可达6~8。
第三条本装置设有回炼油系统和轻污油回炼系统。
第四条两器采用同轴式布置:两器采用沉降器在上,再生器在下的同轴式布置,这种布置型式允许的两器差压大,很好地兼顾了反应和再生对操作压力的不同要求。
另外,同轴布置具有结构简单,操作控制灵活方便,压力平衡适用范围大,抗事故干扰,尤其是抗催化剂倒流能力强、占地面积小等优点。
1、采用中CO助燃剂的完全再生方案采用该方案后,由于平均氧浓度的提高可使再生剂含碳明显降低,特别对于本装置单段再生效果更好。
2、采用单段逆流高效完全再生通过加高待生套筒使待生催化剂进入密相床上部并良好分配,然后向下流动与主风形成气固逆流接触烧焦的良好条件,由于高含氧的气体仅和低含炭的催化剂相遇,低含氧气体则同高含炭的催化剂接触。
因此,整个烧焦过程化学动力学速度比较均一,有利于提高总的烧焦强度。
3、采用待生催化剂分配技术在待生套筒出口配置特殊设计的待生催化剂分配器,使待生催化剂均匀分布于再生密相床上部,为形成单段逆流高效再生提供基本的保证。
催化裂化装置区工艺管道施工技术要求

催化裂化装置区改造工程施工技术要求1.1施工技术准备1.1.1开工之前由设计代表对施工单位技术人员进行施工图纸交底并由施工单位技术人员对所有参加施工人员进行技术交底,以便施工人员了解工程概况、工期、质量及安全要求,施工难点及技术要求。
1.1.2机具检查,对施工所需要的机具进行清点核实,查看施工机具是否完好,是否满足施工的要求。
1.1.3材料检验,主要检查材料的外观质量,质量保证书和合格证。
管材、管件表面不得有裂纹、缩孔、折皱、重皮以及严重锈蚀和过大的机械损伤。
所有阀门都必须按要求进行水压强度和严密性试验。
1.1.4特殊工种作业人员资格需检查是否符合要求并办理上岗证,焊接工艺评定需报检。
1.2管道预制1.2.1材料的领用:根据设计图纸的要求,领用所需的材料,核对其规格、型号、数量、材质,以免误领,而用于预制的材料需经过喷沙除锈和底漆防腐处理。
1.2.2管道组对1. 道用火焰切割,要清除管口附近的毛刺、熔渣、氧化物、铁屑等。
2. 管壁厚度为3--9mm 时,坡口形式按下图3. 管道组对时应检查组对的平直度。
1. 管子、管件组对应对坡口及其内外表面50mm 范围内的油、漆、锈、毛刺等污物进行清理,清理合格后及时焊接。
5.部分大口径管道因条件限制可采用火焰加工坡口,坡口示意图然后用角向磨光机将火焰切割的热影响区打磨干净,相邻的两道焊缝之间的最小距离不得小于100mm。
对于SHA级管道应采用机械加工破口。
6. 法兰连接时应保持平行,其偏差不得大于法兰外径的1.5‰且不大于2mm。
法兰连接应保持与管道同心,并应保证螺栓自由穿入。
1.2.3管道预制1. 工艺管道的预制在指定预制场完成,在进行预制时应按单线图(进行,若设计未给出单线图的则需先按平面布置图绘制出单线图用于施工。
2. 在管道预制前,应对单线图进行焊口编号并报项目组审核,在经确认后用于施工。
3. 所有预制焊口的详细信息(包括焊口号、焊工号、焊接日期及管线号等)需被及时记录并在输入到计算机上相关焊接数据库以便追踪检查。
抗氢致开裂阀门技术要求

中国石油玉门油田分公司炼油化工总厂40万吨/年催化汽油加氢脱硫装置及外围配套工程40万吨/年催化汽油加氢脱硫装置抗氢致开裂(ANTI-HIC)阀门技术要求编制张军校对孙明菊审核付仁超3210 张军孙明菊付仁超2013.05.06 修改编制校对审核审定日期目录1总则 (3)2供货范围 (3)3标准与规范 (3)4一般技术要求 (4)5料检验与试验 (5)6阀门检验与试验 (7)7适用文件及优先级 (7)8质量保证 (8)9标志和包装 (8)10制造商和原产地 (9)11资料交付和要求 (9)1总则1.1本技术要求适用于中国石油玉门油田分公司炼油化工总厂40万吨/年催化汽油加氢脱硫装置及外围配套工程40万吨/年催化汽油加氢脱硫装置用国产抗氢致开裂(ANTI-HIC)阀门。
1.2投标方应遵守第3章所列规范和本技术要求的要求。
1.3本技术要求目的在于明确投标方的供货及工作范围。
1.4除非有其他说明,本技术要求与本项目的其他文件一起使用,这些文件内容如果有冲突,以要求严格者为准。
1.5投标方应仔细阅读本技术要求,如有偏离,应在投标书中明确。
提出的偏离将会在技术澄清会上讨论,用户和设计方保留接受或驳回这些偏离请求的权利,如果没有偏离,将认为报价文件与技术要求完全一致。
2供货范围2.1本技术要求所包括的产品供货范围、数量等见阀门规格书和设材表。
2.2阀门的设计参数、结构要求、材料要求等见阀门规格书。
3标准与规范API 598 V alves Inspection and TestingAPI 600 Bolted Bonnet Steel Gate V alves for Petroleum and Natural GasIndustriesAPI 602 Steel Gate, Globe and Check V alves for Sizes DN100 and Smaller-forthe Petroleum and Natural Gas IndustriesAPI 609 Butterfly V alves: Double Flanged Lug and Wafer-typeASME B16.5 Pipe Flanges and Flanged FittingsASME B16.10 Face-to-Face and End-to-End Dimensions of ValvesASME B16.11 Forged Fittings, Socked-Welding and ThreadedASME B16.34 V alves-Flanged, Threaded and Welding EndASME B1.20.1 NACE MR0103NACE MR0175NACE TM0284 Pipe Threads, General PurposeMaterials Resistant to Sulfide Stress Cracking in Corrosive Petroleum Refining EnvironmentsPetroleum and Natural Gas Industries-Materials for Use H S-containing Environments in oil and gas productionEvaluation of Pipeline and Pressure Vessel Steels for Resistance to Hydrogen-Induced Cracking4一般技术要求4.1投标方发到现场的阀门是装配完整、性能良好的阀门,用户原则上不需要再进行其它工作就可直接使用。
滑阀作为催化剂循环流程中的关键设备之一,在反应

滑阀作为催化剂循环流程中的关键设备之一,在反应再生生产中,对催化裂化反应温度控制、物料调节以及压力控制起到关键作用。
在紧急情况下,再生和待生滑阀还起到自保切断两器的安全作用。
在同轴式催化裂化装置中,滑阀也作为催化剂外循环的调节阀和安保切断阀。
此外,在催化裂化装置的再生气压力控制中,烟气流程上的双动滑阀也同样是起到两器安全和烟机安全的保护作用。
文中对滑阀生产运行中的典型故障情况进行了分析。
1 滑阀简介滑阀按照隔热形式分为冷壁式和热壁式。
热壁式是早期的技术,而冷壁式是20世纪90年代发展起来的,其应用更加具有代表性。
1.1 滑阀主要参数及结构阀体材质为20g或16MnR,内壁采用100~150mm厚的耐磨隔热双层衬里,使阀体外壁工作温度较低。
对单动的再生、待生滑阀,其外表实测壁温能够控制在150~180℃。
对双动滑阀,阀体内操作温度高达700℃时,其外壁温度也不超过200℃。
所以,冷壁滑阀的阀体材质大多采用16MnR低合金钢,相对热壁式滑阀,在材料应用和制造上降低了要求。
阀体与管道的连接采用同类材料焊接方式,现场组对焊接方便。
滑阀的出入口多采用等径焊接结构,大盖多采用圆形或矩形箱体结构。
双动滑阀则采用了类似单动滑阀的结构,只是对称设置了2个箱体及大盖。
双动滑阀的大盖密封均采用了先进的唇型密封结构。
冷壁单动滑阀阀体设计上主要采用等径三通型焊接结构,双动滑阀阀体采用异径四通型焊接结构。
催化裂化装置中典型滑阀结构示意图见图1。
1.阀杆2.填料函组件3.阀大盖4.唇形密封5.节流挡板组件6.阀体7.耐磨衬里8.阀板9.导轨图1 典型单动滑阀结构简图1.2 滑阀内件构成滑阀内件主要由节流锥、阀座圈、导轨及阀板等几部分组成。
节流锥在滑阀内部,属于高温受力部件,承受着介质压差及阀座圈、导轨、阀板的全部重量。
节流锥为悬挂式,大端焊在阀体上,节流锥下部通过螺栓固定有阀座圈和导轨,阀板与导轨相对滑动,节流锥和阀座圈等可随阀体内温度变化而自由膨胀和收缩。
催化裂化装置立管-阀门系统设计及运行分析
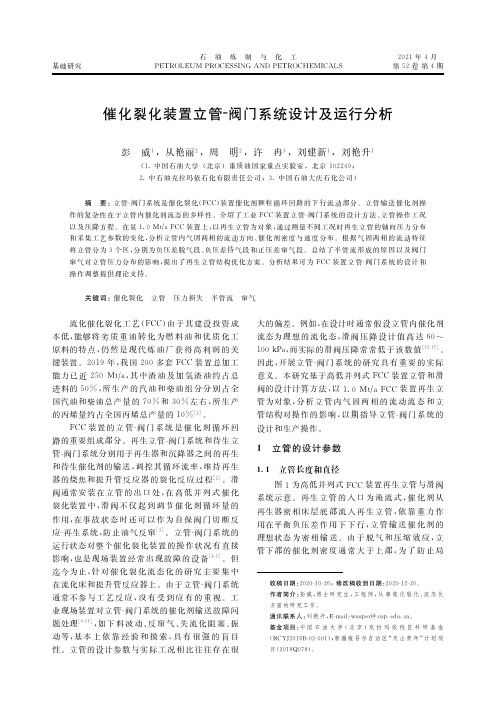
基础研究石 油 炼 制 与 化 工PETROLEUMPROCESSINGANDPETROCHEMICALS2021年4月 第52卷第4期 收稿日期:2020 10 26;修改稿收到日期:2020 12 20。
作者简介:彭威,博士研究生,工程师,从事催化裂化、流态化方面的研究工作。
通讯联系人:刘艳升,E mail:wsuper@cup.edu.cn。
基金项目:中国石油大学(北京)克拉玛依校区科研基金(RCYJ2016B 02 001);新疆维吾尔自治区“天山青年”计划项目(2018Q078)。
56q6jk«¬ ®¯°)*d§¨F±彭 威1,从艳丽2,周 明2,许 冉3,刘建新1,刘艳升1(1.中国石油大学(北京)重质油国家重点实验室,北京102249;2.中石油克拉玛依石化有限责任公司;3.中国石油大庆石化公司)摘 要:立管 阀门系统是催化裂化(FCC)装置催化剂颗粒循环回路的下行流动部分。
立管输送催化剂操作的复杂性在于立管内催化剂流态的多样性。
介绍了工业FCC装置立管 阀门系统的设计方法、立管操作工况以及压降方程。
在某1.0Mt?aFCC装置上,以再生立管为对象,通过测量不同工况时再生立管的轴向压力分布和采集工艺参数的变化,分析立管内气固两相的流动方向、催化剂密度与速度分布。
根据气固两相的流动特征将立管分为3个区,分别为负压差脱气段、负压差持气段和正压差窜气段。
总结了半管流形成的原因以及阀门窜气对立管压力分布的影响,提出了再生立管结构优化方案。
分析结果可为FCC装置立管 阀门系统的设计和操作调整提供理论支持。
关键词:催化裂化 立管 压力损失 半管流 窜气流化催化裂化工艺(FCC)由于其建设投资成本低,能够将劣质重油转化为燃料油和优质化工原料的特点,仍然是现代炼油厂获得高利润的关键装置。
2019年,我国200多套FCC装置总加工能力已近250Mt?a,其中渣油及加氢渣油约占总进料的50%,所生产的汽油和柴油组分分别占全国汽油和柴油总产量的70%和30%左右,所生产的丙烯量约占全国丙烯总产量的10%[1]。
第三章催化裂化装置(I)

第三章催化裂化装置(I)第三章催化裂化装置(Ⅰ)第⼀节装置概况及特点⼀、装置概况催化裂化装置(Ⅰ)为⾼低并列式提升管催化裂化装置,由洛阳炼油设计院|设计。
原设计处理200万吨/年蜡油催化裂化装置,装置⼀九七七年动⼯兴建,⼀九⼋○年被列为缓建项⽬,⼀九⼋⼀年底⼜经国家有关部门批准暂按100万吨/年渣油催化裂化缓建维护⽅案建设,于⼀九⼋四年底建成,同年⼗⽉试运投产⼀次成功。
⼀九⼋七年装置⼜进⾏了扩⼤处理量120万吨/年直馏蜡油减压渣油催化裂化改造,并于⼀九⼋⼋年⼆⽉正式喷油成功。
由于原油加⼯量不⾜,溶剂脱沥青装置未建成,常减压装置减压部分未开,装置根据重油催化裂化的特点陆续进⾏了技术改造。
2000年~2001年,装置经引进UOP的VSS快分、⾼效汽提、Optimix喷嘴等技术改造后达到140万吨/年重油加⼯能⼒,其它配套加⼯设备相继进⾏了扩能改造。
2002年,随着加⼯原料的劣质化,恢复了回炼油系统,并随着国家汽油质量的升级、减压蒸馏装置的开⼯,增上了MGD、顶循环油补柴油技术和进料。
| ⼆、装置规模及组成催化裂化装置(Ⅰ)原设计处理能⼒200万吨/年蜡油,由于减压蒸馏装置多年未开⼯,催化裂化装置(Ⅰ)先后扩能改为120万吨/年、140万吨/年重油加⼯装置。
并根据重油催化裂化的特点先后进⾏了⼀系列的技术改造:完善了再⽣器取热系统,采⽤⾼效旋风分离器、⾼效喷嘴、⾼效汽提、VSS快分、引进了美国D-L公司MGA-1512轴流式主风机组(3#主风机)、滑阀由⽓动执⾏机构改为电液执⾏机构、催化剂采⽤⾃动⼩型加料器、停开催化加热炉、吸收塔改为填料塔、稳定塔15层以上改为填料塔盘、再吸收塔塔板改为梯形⽴式喷射塔板、液化⽓脱硫增上了⽔洗系统,按计划、根据原料性质、市场需求及综合效益选⽤过多种催化剂、多功能⾦属钝化剂、催化裂化助剂、油浆阻垢剂,⽣产操作由电⽓⾃动化控制改为“DCS、DES、PLC”计算机控制。
催化裂化装置(Ⅰ)主要由反应再⽣、分馏、吸收稳定、⽓压机组、主风机组、烟⽓能量回收系统、⽓体脱硫等部分组成。
催化裂化装置仪表及自动控制设计规定
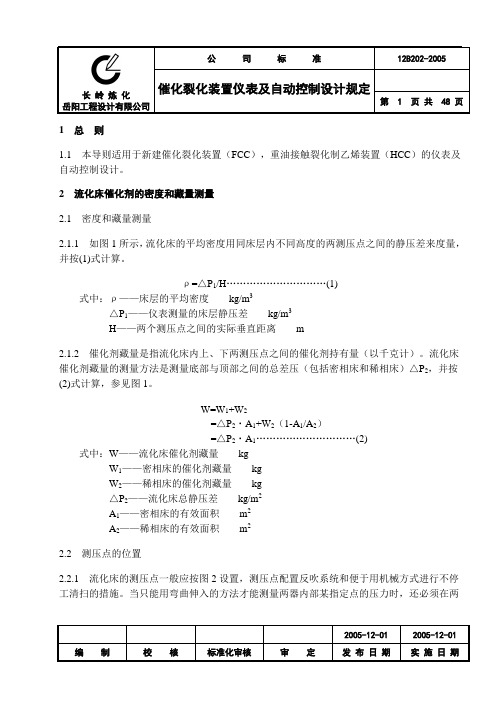
长岭炼化岳阳工程设计有限公司公司标准12B202-2005 催化裂化装置仪表及自动控制设计规定第 1 页共 48 页1 总则1.1 本导则适用于新建催化裂化装置(FCC),重油接触裂化制乙烯装置(HCC)的仪表及自动控制设计。
2 流化床催化剂的密度和藏量测量2.1 密度和藏量测量2.1.1 如图1所示,流化床的平均密度用同床层内不同高度的两测压点之间的静压差来度量,并按(1)式计算。
ρ=△P1/H (1)式中:ρ——床层的平均密度kg/m3△P1——仪表测量的床层静压差kg/m3H——两个测压点之间的实际垂直距离m2.1.2 催化剂藏量是指流化床内上、下两测压点之间的催化剂持有量(以千克计)。
流化床催化剂藏量的测量方法是测量底部与顶部之间的总差压(包括密相床和稀相床)△P2,并按(2)式计算,参见图1。
W=W1+W2=△P2·A1+W2(1-A1/A2)=△P2.A1 (2)式中:W——流化床催化剂藏量kgW1——密相床的催化剂藏量kgW2——稀相床的催化剂藏量kg△P2——流化床总静压差kg/m2A1——密相床的有效面积m2A2——稀相床的有效面积m22.2 测压点的位置2.2.1 流化床的测压点一般应按图2设置,测压点配置反吹系统和便于用机械方式进行不停工清扫的措施。
当只能用弯曲伸入的方法才能测量两器内部某指定点的压力时,还必须在两2005-12-012005-12-01编制校核标准化审核审定发布日期实施日期器内部设置导压管。
设置器内导压管时,要考虑热补偿以防止在升温时导压管被拉裂或拉断,器内导压管只能依靠反吹气保持通畅,不能用机械方式进行不停工清扫;同时要注意在运行中有被流化床内的局部高速气流冲蚀穿孔的可能。
2.2.2 测压点管嘴采用DN20mm承插焊接管嘴或3/4”锥管螺纹管嘴,内部引起管采用φ32×4.5无缝钢管,其材质根据最高操作温度确定。
2.2.3 测压点应向内下斜45°;当两器外部空间受限制时,也可以是水平取压方式,以方便安装和清扫为原则。
催化裂化装置滑阀液压系统及操作

3 液压执行机构的原理 普通单向阀
(b)
正向导通 反向不通
普通单向阀
3 液压执行机构的原理 液控单向阀
3 液压执行机构的原理 液控锁 利用两个液控 单向阀,既不影响 缸的正常动作,又 可完成缸的双向闭 锁。锁紧缸的办法 虽有多种,用液控 单向阀的方法是最 可靠的一种。
1
2
3 液压执行机构的原理 换向阀“通”和“位”
4.3操作方式之机械手轮操作
1.操作手 柄指针置 于锁定位 置 2.离合器 手柄置于 “手动” 4.手摇手 轮至所需 要位置
3.操作手 柄指针置 于锁定位 置 手动切换 杠杆
4.4滑阀常用操作方式日常检查维护
电液执行机构用于控制炼油化工催化裂化设备中,因处 在长年累月的连续工作状况,环境极其恶劣. 操作人员日常检查主要内容 1、检查系统压力、泄漏情况、液位高度和油液温度。 2、检查阀位显示、输入显示是否一致。 3、出现报警提示,现场确认并及时处理。 4、在冬季前,应放尽盘管内冷却水。 5、在油箱低液位报警时,应及时补油,以免造成油泵吸空。 补充的油液型号应与原来的工作油液相同,并且经过严格的过 滤。
四
BDY9-B电液执行机构液压原理动画
阀停
停
射流管伺服阀 单向阀 YM2
关
关
关
失电
四
BDY9-B电液执行机构液压原理动画
阀关
射流管伺服阀 单向阀 YM2
关
四
BDY9-B电液执行机构液压原理动画
液压手操
开
射流管伺服阀 单向阀
YM2
四
目录
主要内容
待生滑阀反复自锁事件
待生滑阀先后五次自锁的情况及处理措施
2、正确熟练操作滑阀 仪表室点动操作 机械手轮操作 液压手动操作 了解滑阀的相关知识,灵活处理滑阀故障 3、做好日常维护,确保平稳操作
催化裂化操作规程
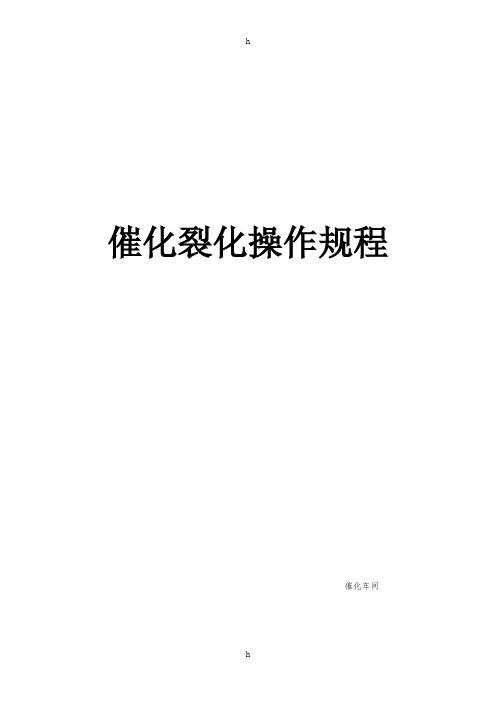
催化裂化操作规程催化车间第一章 装置概况第一节 概况一、本装置设计能力为41014 吨/年(年开工时为8000小时),由反应、分馏、吸收稳定、主风机、气压机等部分组成。
原料由大庆管道原油的常压渣油、通过催化裂化,生产93#汽油,轻柴油、液化汽等目的产品。
二、本装置工艺和设备的主要特点1、两器采用同轴式组合,具有操作弹性大、两端再生。
再生催化剂含碳低。
2、 抗金属污染好、生氢及生焦率较低轻质油收率较高,气体收率较低的系统列分子筛催化剂(具体使用的催化剂类型,根据生产需要选择)。
3、为降低装置能耗采用内取热器,回收才生余热付产蒸汽。
4、由于设计原料为大庆管道原油的常压渣油,其残炭和胶质的含量较高,所以裂化后的油浆比重较大,故在生产采用油浆,不回炼或部分回炼的方案以维持再生器的热量平衡和分馏塔底油浆的比重不超标准。
5、由于同常减压装置可以联合操作,以常压热渣油为原料,所以在开工后可以甩掉加热炉。
6、吸收稳定系统采用双塔流程。
第二节设计数据一、原料性质二、汽油馏分性质三、轻柴油馏分性质四、装置物料平衡表五、反应再生部分工艺计算汇总六、装置能耗汇总表设计进料量70000吨/年装置组成:反应再生部分,分馏部分,吸收稳定部分,碱洗部分第三节装置流程简介一、反应再生部分原料油自罐区的原料罐来经泵(P201/1.2)加压后送到至原料一—轻柴油换热器(E205/1.),再进入原料—油浆换热器(E201/1.2.)换热后,进入闪蒸罐(V203/1),经过加热炉后的原料沿管排进入闪蒸(V203/1),进入闪蒸罐内的原料汽相沿顶部汽返线进入分馏塔(T201)第二层塔盘上部,液相自罐底部抽经泵(P201/2.3)加压后进入提升管反应器。
回炼油自分馏塔第一层塔盘自流入回炼油罐(V202),经回炼油泵(P206/1.2)加压后,送到提升管反应器下部与分馏塔底油浆经泵(P207/1.2)加压后送至提升管下部的回炼油浆混合一并进入提升管反应器(R101)。
催化裂化装置滑阀_安装及验收条件

1 总则l.0.l 本规定适用于提升管流化催化裂化装置及催化裂解装置用的单动滑阀和双动滑阀的安装和验收。
本规定不包括上述滑阀的检修技术要求。
l.0.2 滑阀的安装和验收除执行本规定要求外,尚应符合国家劳动部颁发的《压力容器安全技术监察规程》和GBl50-89《钢制压力容器》以及其他现行有关标准规范的规定。
图样或技术文件中有关安装的要求,不得低于本规定相应的要求。
l.0.3 滑阀安装工程中的安全技术、劳动保护的要求应符合SHJ505-87《炼油化工施工安全规程》和其他现行有关标准规范的规定。
1.0.4 本标准代替《提升管流化催化裂化滑阀安装及验收条件》(BA10-11-4-89)。
2 引用规范及标准GB150-89 钢制压力容器;JB4730-94 压力容器无损检测;JB16l4-83 锅炉受压元件焊接接头机械性能检验方法;JB/T4709-92 钢制压力容器焊接规程;JB4708-92 钢制压力容器焊接工艺评定;(90)劳总锅字8号压力容器安全技术监察规程;SHJ505-87 炼油化工施工安全规程;SHJ509-88 石油化工工程焊接工艺评定;GBJ235-82 工业管道工程施工及验收规范(金属管道篇);GBJ93-86 工业自动化仪表工程施工及验收规范;GBJ232-82 电气装置安装工程施工及验收规范(电缆线路篇);炼化建703-77 隔热耐磨衬里工程施工及验收技术规范;BA10-11-5-95 滑阀、蝶阀隔热耐磨衬里施工技术条件;BA10-11-3-96 滑阀外部保温施工技术条件;重设B-2680 保温钉、端板、龟甲网;3 安装前的准备工作3.0.1 滑阀安装前应具备下列技术文件a) 产品合格证;b) 主要零部件材料的化学成分和机械性能;c) 隔热和耐磨衬里的化学成分,机械性能和热处理升温曲线;d) 焊接质量的检查结果(包括超过两次的返修记录);e) 硬质合金喷焊或堆焊质量的检查结果;f) 无损探伤结果;g) 压力试验结果;h) 与本条件和图样不符的项目;3.0.2 制造厂提供的阀板与导轨、阀座圈之间间隙实测记录以及风动马达和指挥阀的测试记录、电液伺服阀和位置传感器等测试记录;3.0.3 滑阀出厂前的冷态空负荷的调试记录,包括:滑阀的灵敏度、位置精度、开阀和关阀时间的实测记录以及电液控制与驱动装置的各项报警和锁定的调试记录;3.0.4 滑阀的安装使用说明书内容包括:滑阀的特性:(设计压力、设计温度、设计压差、全开面积、阀杆行程及试验压力等。
- 1、下载文档前请自行甄别文档内容的完整性,平台不提供额外的编辑、内容补充、找答案等附加服务。
- 2、"仅部分预览"的文档,不可在线预览部分如存在完整性等问题,可反馈申请退款(可完整预览的文档不适用该条件!)。
- 3、如文档侵犯您的权益,请联系客服反馈,我们会尽快为您处理(人工客服工作时间:9:00-18:30)。
中国石化北京设计院共25 页第 1 页目次1 总则1.1 适用范围1.2 引用标准1.3 术语2 设计原则2.1 一般要求2.2 设计参数要求2.3 控制要求2.4 动力风压2.5 阀板移动速度2.6 反馈凸轮3 技术资料和数据3.1 设计条件3.2 滑阀的名称3.3 滑阀的技术数据4 设计4.1 控制和驱动装置的选择4.2 阀体和阀盖4.3 垫片4.4 阀板4.5 阀座圈4.6 导轨4.7 间隙要求4.8 阀杆4.9 螺栓中国石化北京设计院共25 页第 2 页4.10 平衡吊挂5 材料5.1 阀体部分所用的主要材料及用途5.2 材料的化学成分和机械性能应符合有关标准的规定5.3 奥氏体不锈钢材料的含碳量不低于0.04%6 制造技术要求6.1 焊接6.2 喷焊或堆焊6.3 衬里6.4 水压试验6.5 操作性能试验7 附图附录A 编制说明1 总则1.1 适用范围本规定适用于提升管流化催化裂化装置及催化裂解装置的催化剂再生单动滑阀、待生单动滑阀、循环单动滑阀、切断单动滑阀和烟气双动滑阀的结构设计。
1.2 引用标准GB150-1998《钢制压力容器》GB699-88《优质碳素结构钢技术条件》GB/T983-1995《不锈钢焊条》GB984-85《堆焊焊条》GB1220-92《不锈钢棒》GB1221-92《耐热钢棒》GB2100-80《不锈耐酸钢铸件技术条件》GB3077-88《合金结构钢技术条件》GB4238-92《耐热钢板》GB/T5117-1995《碳钢焊条》中国石化北京设计院共25 页第 3 页GB/T5118-1995《低合金钢焊条》GB6654-1996《压力容器用钢板》GB7659-87《焊接结构用碳素钢铸件》JB2536-80《压力容器油漆、包装和运输》JB4703-92《长颈对焊法兰》JB/T4709-92《钢制压力容器焊接规程》JB4708-92《钢制压力容器焊接工艺评定》JB4730-94《压力容器无损检测》SH3074-95《石油化工钢制压力容器》SH3075-95《石油化工钢制压力容器材料选用标准》BA10-11-3-96《滑阀外部保温施工技术条件》BA10-11-5-95《滑阀、蝶阀隔热耐磨衬里施工技术条件》1.3 术语1.3.1 输入信号来自变送器的控制信号(气动信号-压力范围0.02~0.1MPa或电动信号—电流范围4~20mA),根据工艺参数的变化,控制滑阀的动作。
1.3.2 输出信号来自变送器的反馈信号(气动的或电动的),用于指示滑阀的阀位开度。
1.3.3 气开式(正比)当输入信号达到最大值时(气信号为0.1Mpa,电信号为20mA),滑阀处于全开位置,最小值(气信号为0.02MPa,电信号为4mA)时处于关闭位置。
1.3.4 气关式(反比)当输入信号达到最大值时,滑阀处于关闭位置,最小值时处于全开位置。
1.3.5 灵敏度阀杆在任意位置开始动作所需最小的输入信号变动量,以输入信号全量程的百分比表示。
1.3.6 准确度阀杆在任意位置只要输入信号有变化,阀杆都要移动到与新的输入信号相对应的位置上,实际的位置与对应的位置之差称滑阀的准确度或非线性偏差,用全行程的百分比表示。
1.3.7 稳定性输入信号经反馈达到平衡后,阀杆应保持不动,以单程振荡次数表示之。
1.3.8 最高操作压力滑阀在正常工作过程中可能产生的最高压力。
1.3.9 设计压力在相应设计温度下,用以确定阀体计算壁厚的压力。
1.3.10 设计压差滑阀上游与下游设计的压力差,用于确定内部元件的尺寸。
1.3.11 最高操作温度滑阀在正常工作过程中可能产生的最高温度,由不正常操作引起滑阀中国石化北京设计院共25 页第 4 页短时超温不属本范畴之内。
1.3.12 设计温度滑阀在正常操作过程中,在相应的设计压力下,规定阀体壁和内部元件可能达到的最高温度。
2 设计原则2.1 一般要求2.1.1 滑阀的设计必须符合工艺操作的要求。
2.1.2 阀体内部的结构设计必须保证其内部元件拆卸方便。
2.1.3 阀体内部元件的设计必须最大限度地抗催化剂的冲刷与磨损,以提高其使用寿命。
2.1.4 阀体的零部件设计必须考虑工作状态时的热膨胀变形。
2.1.5 阀座圈、阀板和导轨等内部零件应布置在阀口的下游,以避免催化剂的直接冲刷。
2.1.6 驱动装置必须备有手动操纵机构。
2.1.7 滑阀必须设有机械限位装置。
2.1.8 在阀体、阀盖和驱动装置上应设置吊耳、供吊装用。
2.2 设计参数要求2.2.1 设计压力滑阀的设计压力通常取1.1倍的最高操作压力,但不低于0.5MPa。
2.2.2 操作压差和设计压差a) 滑阀的操作压差包括催化剂的料柱,按工艺要求定,但不宜过大,否则会加剧滑阀内部零件的磨损。
一般按操作压差的1.2~1.5倍选取。
b) 对调节用单动滑阀,滑阀的设计压差最大不应超过0.2MPa;双动滑阀最大不应超过0.12MPa;对切断单动滑阀最大不应超过滑阀的操作压力。
2.2.3 设计温度滑阀的设计温度按最高操作温度加50℃选取,对冷壁滑阀阀体壁设计温度取350℃2.3 控制要求2.3.1 控制方式a) 单动滑阀的控制方式根据工艺的要求决定,一般气动采用气开式,电液采用正比式。
b) 双动滑阀的控制方式气动采用气关式;电液采用反比式。
中国石化北京设计院共25 页第 5 页2.3.2 灵敏度a) 气动单动滑阀的灵敏度要求达到1/200,电液的要求达到1/1000。
b) 气动双动滑阀的灵敏度要求达到1/400,电液的要求达到1/1000。
2.3.3 准确度气动滑阀的准确度要求达到1/100;电液的要求达到1/600。
2.3.4 稳定性单程振荡次数气动的不大于3次,电液的不大于1次。
2.4 动力风压对于风动马达驱动的滑阀来说,进入滑阀的动力风压力为0.4-0.6MPa。
2.5 阀板移动速度2.5.1 气动调节风动驱动的滑阀,动力风为0.5MPa时,一般不小于15mm/s。
2.5.2 电液控制和驱动的滑阀不小于25mm/s。
2.6 反馈凸轮气动调节的定位器和阀位变送器用反馈凸轮的设计转角应不大于254°。
3 技术资料和数据3.1 设计条件滑阀的设计条件由工艺专业提供,其中应包括:3.1.1 滑阀的接管直径(衬里内的和衬里外的直径);3.1.2 开口面积和余隙(双动滑阀);3.1.3 最高操作压力和操作温度;3.1.4 滑阀的操作压差;3.1.5 滑阀的安装方位及介质流向;3.1.6 滑阀的控制方式;3.1.7 滑阀的名称(再生、待生和循环等)及其作用(调节的或切断的)。
3.2 滑阀的名称在图中表示的滑阀名称应简单明了,即要反映驱动与控制方式,又要反映滑阀的规格和结构特点,举例如下:中国石化北京设计院共25 页第 6 页3.2.1 GO2.0-φ585/φ660单动滑阀(用于待生斜管)安装位置衬里(上游/下游)内直径风动马达功率(KW)滚珠丝杠传动箱3.2.2 FⅡQ7.5-φ800切断单向滑阀(用于外取热上斜管)安装位置衬里内直径风动马达功率(KW)Ⅱ型梯形螺纹传动箱3.2.3 BDY9A-φ700冷壁式单动滑阀(用于再生斜管)安装位置衬里内直径改型序号液压系统压力(Mpa)分离式电液传动控制装置隔爆型注:制造图不注安装位置,凡是没有标出冷壁式的滑阀都是热壁式结构。
3.3 滑阀的技术数据滑阀的说明书和图纸中应表示如下内容的技术数据。
3.3.1 气动调节风动滑阀a) 阀体部分1) 设计压力Mpa2) 设计温度℃3) 设计压差Mpa4) 全开口径mm5) 全开面积cm26) 关闭余隙面积cm2中国石化北京设计院共25 页第7 页7) 阀杆行程mm8) 通过介质9) 试验压力Mpab) 风动马达1) 空气压力Mpa2) 空气耗量Nm3/min3) 出轴转速r/min4) 相应主轴功率KWc) 传动部分1) 总减速比2)出轴转速r/mind) 阀位变送及定位部分1) 传动速比2) 凸轮实际转角度e) 滑阀特性1) 灵敏度2) 准确度3) 开或关时间S4) 稳定性f) 控制方式g) 设备衬里1) 耐磨层2) 厚度mm3) 隔热层4) 厚度mm3.3.2 电液控制和驱动滑阀a) 阀体部分1) 设计压力Mpa2) 设计温度℃3) 设计压差Mpa中国石化北京设计院共25 页第8 页4) 全开口径mm5) 全开面积cm26) 关闭余隙面积cm27) 阀杆行程mm8) 通过介质9) 试验压力Mpab) 电液执行机构1) 油缸油缸内径mm活塞杆直径mm最大行程mm最大/运行推力N2) 轴向柱塞油泵型号额定流量L/min环境温度℃额定压力Mpa3) 电动机型号功率KW转速r/min防爆等级dⅡBT44) 蓄能器容量L操作容量L5) 油箱容量L6) 系统压力Mpa7) 液压油牌号8) 滑阀特性灵敏度1/1000中国石化北京设计院共25 页第9 页准确度1/600稳定性≤1开、关时间S9) 控制要求输入信号4~20mA 250Ω输出信号4~20mA 250Ω仪表电源220V/1/50电磁阀电源24VDC控制方式正比或反比c) 设备衬里1) 耐磨层mm2) 厚度mm3) 隔热层4) 厚度mm4 设计4.1 控制和驱动装置的选择滑阀的控制和驱动装置根据用户的需要,选择可采用:4.1.1 气动调节风动驱动装置;4.1.2 电液控制和驱动装置。
电液执行机构推力大,精度高应优先采用。
4.2 阀体和阀盖4.2.1 阀体和阀盖的最小设计壁厚应考虑内部所承受的压力和驱动装置的推拉力以及管道所施加的外部载荷。
4.2.2 从制造角度考虑,阀体与阀盖有铸造与焊接两种结构形式,应尽量采用焊接结构,以避免铸造易产生的缺陷。
4.2.3 阀体与管道的连接,一般应采用焊接连接,对于口径在350mm以下的滑阀,为了便于检修阀体内部的零部件,可采用法兰与管道连接。
4.2.4 阀体和阀盖的连接法兰有圆形和矩形两种,其大小必须保证阀体内部零件(阀板、阀中国石化北京设计院共25 页第10 页座圈和导轨)从此法兰连接口中取出,并有足够的空间来除去导轨和阀座圈螺栓的焊点。
4.2.5 法兰的设计a) 法兰的计算应考虑内部的压力和驱动装置的推拉力或管道所施加的外部载荷。
b) 对热壁阀体的圆形法兰采用PN6.4(6.4Mpa)级的JB4703-92长颈对焊法兰。
c) 对冷壁阀体的圆形法兰采用PN2.5(2.5Mpa)级的JB4703-92长颈对焊法兰。
d) 法兰密封面选用凹凸面型式。
e) 矩形法兰按特殊要求设计。
4.2.6 阀体和阀盖的隔热型式。
a) 热壁式在阀体外(法兰除外)按BA10-11-3-96《滑阀外部保温施工技术条件》的要求铺设隔热层见“图4.2.6-1”,阀体壁温与内部零件的温度基本相同。