精益生产-连续流13
精益生产之连续流

3
为什么要创建连续流
减少WIP Reduce work-in-process inventory 缩短工序间的距离,减少走动的浪费 Shorten the distance between work stations and minimize non-value added movement 缩短Lead Time Shorten lead time 增加人均生产率 Increase productivity
3
如何执行连续流-1
4
如何执行连续流-1
如何选择产品系列? Do you have the right end items?
4
如何执行连续流-1
如何选择产品系列? Do you have the right end items? 什么是节拍时间? What is the takt time?
8
执行连续流的挑战 Challenges
工作平衡 Line Balance 标准工序 Standard Work 产品均衡 Product Mix 快速换模 Frequent Change Over 解决问题 Problem Solving 持续改善 Continuous Improvement 纪律 Discipline 物料补给 Material Replenishment
7
什么样的工艺适用连续流 Applications
手工制造 Manual production 半自动制造 Semi automated manufacturing 冲压、注塑成型、油漆以及全自动生产不适用 Not applicable at stamping, injection molding, and complete automated processes
精益生产之连续流

4
如何执行连续流-1
如何选择产品系列? Do you have the right end items? 什么是节拍时间? What is the takt time? 贵工厂生产一件产品有哪些工作步骤? What are the work elements necessary to make one piece?
4
如何执行连续流-1
如何选择产品系列? Do you have the right end items? 什么是节拍时间? What is the takt time? 贵工厂生产一件产品有哪些工作步骤? What are the work elements necessary to make one piece? 如何测定工作步骤的工时? What is the actual time required for each work element?
8
执行连续流的挑战 Challenges
工作平衡 Line Balance 标准工序 Standard Work 产品均衡 Product Mix 快速换模 Frequent Change Over
8
执行连续流的挑战 Challenges
工作平衡 Line Balance 标准工序 Standard Work 产品均衡 Product Mix 快速换模 Frequent Change Over 解决问题 Problem Solving
9
总 结 Summary
什么样的工艺适用连续流 Applications
7
什么样的工艺适用连续流 Applications
精益生产之“连续流”提高生产效率
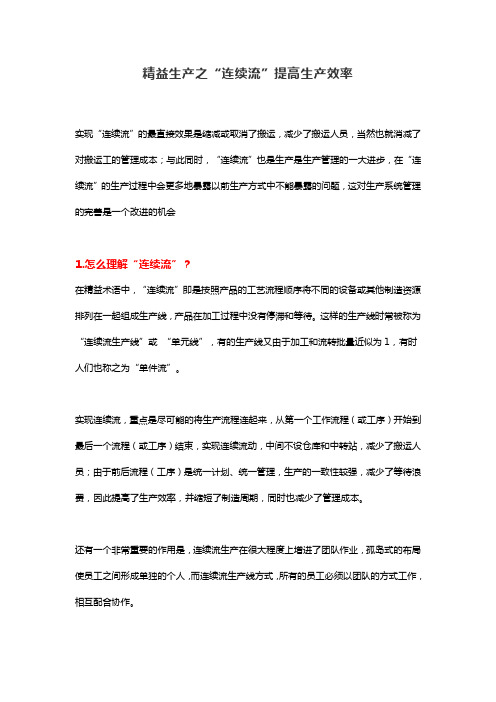
精益生产之“连续流”提高生产效率实现“连续流”的最直接效果是缩减或取消了搬运,减少了搬运人员,当然也就消减了对搬运工的管理成本;与此同时,“连续流”也是生产是生产管理的一大进步,在“连续流”的生产过程中会更多地暴露以前生产方式中不能暴露的问题,这对生产系统管理的完善是一个改进的机会1.怎么理解“连续流”?在精益术语中,“连续流”即是按照产品的工艺流程顺序将不同的设备或其他制造资源排列在一起组成生产线,产品在加工过程中没有停滞和等待。
这样的生产线时常被称为“连续流生产线”或“单元线”,有的生产线又由于加工和流转批量近似为1,有时人们也称之为“单件流”。
实现连续流,重点是尽可能的将生产流程连起来,从第一个工作流程(或工序)开始到最后一个流程(或工序)结束,实现连续流动,中间不设仓库和中转站,减少了搬运人员;由于前后流程(工序)是统一计划、统一管理,生产的一致性较强,减少了等待浪费,因此提高了生产效率,并缩短了制造周期,同时也减少了管理成本。
还有一个非常重要的作用是,连续流生产在很大程度上增进了团队作业,孤岛式的布局使员工之间形成单独的个人,而连续流生产线方式,所有的员工必须以团队的方式工作,相互配合协作。
2.如何实现“连续流”?实现连续流,可以从一下几个方面开展改善活动:1)按加工顺序排列设备在一些工厂中经常可以看到,不同工序的加工设备之间的距离非常远,加工过程中产生的中间产品需要花费较多时间和人力才能搬运到下一道工序,这样的现象被称为孤岛式布局。
“连续流”生产要求放弃按设备类型排列的布局,而是按照加工顺序来排列生产设备,避免孤岛现象的出现,尽可能使设备的布置流水线化。
2)按节拍进行生产“连续流”生产还要求各道工序严格按照一定的节拍进行生产。
如果各道工序的生产节拍不一致,将会出现产品积压或停滞,无法形成“连续流”。
因此,应该合理安排作业内容,根ECRS原则,让大家的工作均衡,每一道工序都按节拍进行生产,从而使整个生产过程顺畅。
精益系列之连续流生产

精益系列之连续流生产引言在现代制造业中,精益生产已经成为一种非常流行的管理方法。
其中的连续流生产是精益生产中非常重要的一环。
本文将介绍连续流生产的概念、原则以及在实施过程中需要注意的事项。
连续流生产的概念连续流生产是一种生产方式,它的目标是通过尽可能减少浪费、提高生产效率和质量,实现产品的持续快速流动。
其核心思想是对生产过程进行流程优化,将分散的生产工序整合为一个连续的流水线,从而达到降低生产周期、提高产品质量和迅速响应市场需求的目的。
连续流生产的原则1. 一次加工连续流生产的核心原则是一次加工,即在产品生产过程中,产品在整个生产流程中只经历一次加工。
这样可以避免由于重复加工而引起的浪费和质量问题,提高生产效率和产品一致性。
2. 拉动生产拉动生产是指根据市场需求实际情况,按需生产,而不是按计划或按库存生产。
这样可以避免产生过多的库存和待产品,减少库存成本,并且可以根据市场需求及时调整生产速度。
3. 小批量生产连续流生产中,生产产品的批量应尽量保持小。
小批量生产可以降低生产周期和库存量,减少对不良品的产出,提高生产灵活性和响应速度。
4. 稳定生产稳定生产是指在连续流生产过程中,要尽量避免产生不稳定因素,如停机、故障、压力等,以确保生产过程的连续性和稳定性。
只有在生产稳定的前提下,才能实现高效连续流生产。
实施连续流生产的注意事项1. 流程分析在实施连续流生产前,首先需要进行流程分析,了解当前的生产流程并找出其中的瓶颈和浪费点。
只有深入了解当前问题,才能有针对性地进行改进。
2. 设计生产线根据流程分析的结果,设计一个合理的生产线。
生产线应该尽量简化,减少不必要的工序,并且要考虑到合理的工作安排、人机配合和物料流动等因素。
3. 优化物料供应物料供应是连续流生产中非常重要的一环。
为了确保连续流生产的顺利进行,物料供应要及时、准确、稳定。
可以采用合理的物料采购计划和供应链管理方法,确保每个环节的物料供应充足。
精益生产之“连续流”提高生产效率

精益生产之“连续流”提高生产效率实现“连续流”的最直接效果是缩减或取消了搬运,减少了搬运人员,当然也就消减了对搬运工的管理成本;与此同时,“连续流”也是生产是生产管理的一大进步,在“连续流”的生产过程中会更多地暴露以前生产方式中不能暴露的问题,这对生产系统管理的完善是一个改进的机会1.怎么理解“连续流”?在精益术语中,“连续流”即是按照产品的工艺流程顺序将不同的设备或其他制造资源排列在一起组成生产线,产品在加工过程中没有停滞和等待。
这样的生产线时常被称为“连续流生产线”或“单元线”,有的生产线又由于加工和流转批量近似为1,有时人们也称之为“单件流”。
实现连续流,重点是尽可能的将生产流程连起来,从第一个工作流程(或工序)开始到最后一个流程(或工序)结束,实现连续流动,中间不设仓库和中转站,减少了搬运人员;由于前后流程(工序)是统一计划、统一管理,生产的一致性较强,减少了等待浪费,因此提高了生产效率,并缩短了制造周期,同时也减少了管理成本。
还有一个非常重要的作用是,连续流生产在很大程度上增进了团队作业,孤岛式的布局使员工之间形成单独的个人,而连续流生产线方式,所有的员工必须以团队的方式工作,相互配合协作。
2.如何实现“连续流”?实现连续流,可以从一下几个方面开展改善活动:1)按加工顺序排列设备在一些工厂中经常可以看到,不同工序的加工设备之间的距离非常远,加工过程中产生的中间产品需要花费较多时间和人力才能搬运到下一道工序,这样的现象被称为孤岛式布局。
“连续流”生产要求放弃按设备类型排列的布局,而是按照加工顺序来排列生产设备,避免孤岛现象的出现,尽可能使设备的布置流水线化。
2)按节拍进行生产“连续流”生产还要求各道工序严格按照一定的节拍进行生产。
如果各道工序的生产节拍不一致,将会出现产品积压或停滞,无法形成“连续流”。
因此,应该合理安排作业内容,根ECRS原则,让大家的工作均衡,每一道工序都按节拍进行生产,从而使整个生产过程顺畅。
无间断的流程,精益生产中的流水线作业

无间断的流程,精益生产中的流水线作业这是为俄国女沙皇叶卡特琳娜二世量身定制的一个瓷碟,雍雍华贵,极尽繁复。
制作这个瓷器的公司就是WEDGWOOD(韦奇伍德)。
韦奇伍德创建于18世纪,问世之初,就是全世界极品瓷器的代名词,没有之一。
1793年英国使团出使中国,进献给乾隆皇帝的礼物之中就有韦奇伍德瓷器。
这个公司现在还在,但遗憾的是已经于2009年宣告破产。
200余年品牌,终究难逃一劫。
当然,我对瓷器外行,所以今天这里不可能谈瓷器。
那为什么要谈韦奇伍德呢?主要是因为其创始人乔赛亚·韦奇伍德。
稍微科普一下乔赛亚·韦奇伍德。
乔赛亚·韦奇伍德(JOSIAH WEDGWOOD),英国瓷器之父,在制瓷的技术上当时无人出其右。
当然他还有另外一个身份,他是达尔文的外公。
没错,就是那个搞出《进化论》的达尔文。
当然达尔文同时还是他的孙女婿。
有点乱,是不是?今天,在这里提到他,不是因为这些八卦,而是因为他当时的另外一项了不起的成就,尽管他自己当时并没有意识到,那就是创建了历史上第一条有史可查的流水线。
公元1769年,英国人乔赛亚·韦奇伍德开办埃特鲁利亚陶瓷工厂,在工厂内实行精细的劳动分工,他把原来由一个人从头到尾完成的制陶流程分成几十道专门工序,分别由专人完成。
这样一来,原来意义上的“制陶工”就不复存在了,存在的只是挖泥工、运泥工、扮土工、制坯工等等制陶工匠变成了制陶工场的工人,他们必须按固定的工作节奏劳动,服从统一的劳动管理。
1从本质上看,韦奇伍德的这种工作方法已经完全可以定义成为“流水线”,虽然当时没有这样说。
当然,业界普遍认可的是亨利·福特(HENRY FORD)在20世纪初发明了流水线装配工艺。
无论如何,流水线操作存世久矣!而一旦谈及精益生产,TPS,流水线作业一定是一个不得不提的话题。
流水线作业是精益生产部不可或缺的基础之一。
我个人的习惯是正本清源,所以先从基础开始。
精益生产第十三章 价 值 流 图

2.产品路径(PR)分析
表13-1 产品路径分析
2.产品路径(PR)分析
B1302.TIF
二、价值流图常用符号
图13-6 价值流图符号
三、绘制当前状态图
1.收集相关信息 2.绘制步骤
1.收集相关信息
在正式绘制现状图之前,必须深入到基层单位先 收集相关信息,一般从最下游的作业(即发货)开 始,收集实际的过程数据,例如发货频率、订 货量、工艺流程图、各工序作业时间、换模时 间、操作工人数、班次、周期时间等,并在收 集数据的过程中,将信息流和物流的情况记录 下来,作为绘制现状图的依据
2.绘制步骤
(1)绘制客户、供应商生产控制部门。 (2)绘制客户需求信息。 (3)绘制发货与收货信息。 (4)绘制各工序信息 (5)绘制信息流 (6)绘制在制品库存和物料流动
(1)绘制客户、供应商和生产控制部门。
图13-7 绘制客户、供应商和生产控制部门
(2)绘制客户需求信息。
图13-8 绘制客户需求信息
图13-11 绘制信息流
(6)绘制在制品库存和物料流动
1)在各工序之间在制品或成品的位置画上库存图标,并在库存图标的下面 标注库存的数量。 2)计算各工序间库存储存的天数,并将计算结果填写在该工序方框下方的 时间线上。 3)在价值流图上画出有推动、拉动和先进先出通道的地方。
图13-12 绘制在制品库存和物料流动
1.绘制客户、供应商和生产控制部门
图13-14 绘制客户、供应商和生产控制部门
2.填写发货信息
图13-15 填写发货信息
二、客户需求阶段
1.确定生产节拍和装箱节拍 2.确定目前的生产方法是否能满足需求 3.确定并绘制缓冲库存、安全库存或周转库存
1.确定生产节拍和装箱节拍
精益生产物流第三章 连续流生产

四、计算生产节拍
1.运行效率
运行效率
=
实际运行时间 计划运行时间
100
实际运行时间 = 计划运行时间 - (DT + LT + C/O)
LT = 损失时间 (非计划停顿时间:非设 备原因造成的时间损失 )
DT = 停顿时间 (非计划停顿时间:仅由 于设备原因造成的时间 损失)
C/O = 换产调整时间
三、生产作业流程分析 1.生产作业流程 生产作业流程分析,对每项作业要素进行识别、分类、
细化和排序。 (1)生产作业流程用图表表示,可以直观地发现浪费和
消除浪费。 (2)通过每个作业的分析,找出浪费产生的原因。 (3)每项作业是生产系统设计的依据。 (4)生产作业流程分析是制定生产管理文件的依据。
2.方案设计
(1)价值流图指导工 作场地改善。
(2)工作场地有效支 持连续流生产。
(3)按价值流分析编 制生产工艺。
(4)节拍控制流水线 生产速度。
(5)生产工序尽可能 相互临近,实施多品 种、小批量(或一个 流)生产,减少在制 品数量。
3.方案实施
(1)连续流生产能有 效消除浪费,为客户 创造价值。
④时间:计算增值或非增值时间,通常以小时为单位,小数 点保留两位。在填写数据时,注意不得混淆计量单位,如以秒计 算加工过程,而以天计算存储时间。
⑤零件移动距离:从一个加工地点到另一个加工地点的零件 移动距离,以米为单位。
⑥零件移动数量:从一个加工地点移动到另一个加工地点零 件的数量。除非中间发生变化,第一个加工地点移出的数量就是 整个生产过程中移动的数量。
§3.1连续流生产概述 §3.2连续流生产组织实施 §3.3单元生产
§3.1连续流生产概述
精益生产要素之连续流培训课件

一、连续流的目标和内容
1、连续的定义与目标
1.1 连续流的定义 连续流指的是把人与机器按照一定次序联系起来的方法,它会创造一个可视化的流程 ,让人们较容易的发现任何异常情况并且最小化生产流程中的停滞。 连续流的核心是价值的流动。 连续流的目的是减少交付期、消除在制品、实现单件流。 1.2 连续流的目标
Batch production 批量生产
Continuous flow production 连续流生产
6
一、连续流的目标和内容
2、连续流支持灵活的人力安排
Stage 1 1 3 5 1 Stage 2 3 5 TT Stage 1
1 2 A
3 4 B
5 6 C
TT Volume drop 2 A 4 B 6 C 2 A 4 B 6 Stage 2 C
1
2 A
3 4 B
5 6 C
Reduced demand (volume drop) will increase the takt time resulting in idle time or over production市场需求的下降会增加节拍时间, 从而导致机器闲置或者过度生产。 In case of process improvement, idle time or over production will occur if demand does not rise流程改善后,如果市场需求不增加,同样 会导致机器闲置或者过度生产。
5
一、连续流的目标和内容 2.2 连续流资料介绍
1、理想状态下的连续流
•Continuous flow processing is established when removing the work-in-progress (WIP) between processes and producing one piece at a time, with each item passed immediately from one process step to the next without stagnation in between. •当工序之间的在制品被消除,仅允许每次将一个产品从此工序流到下一工序,两工序之间没有停滞时,一个连 续流便建立了。 •Continuous flow processing reduces: transportation, movement and space by bringing the process steps closer 连续流减少了:运输、动作、空间(通过流程之间的距离减少) lead time by minimizing in process stock in the loop 交期-- 通过降低工序循环中库存。
创建连续流——实现精益生产的有效方式

创建连续流——实现精益生产的有效方式精益生产是一种以持续改进和高效运作为目标的生产方式。
在这种方式下,企业通过优化流程、消除浪费和提高质量来增加价值创造,以满足客户需求并提高竞争力。
创建连续流是实现精益生产的一种有效方式。
连续流是精益生产的核心概念之一,它强调无浪费的生产环境,每一项工作都要顺畅进行,没有停滞或阻塞。
连续流的目标是实现流程的顺畅和高效运作,从而提高产品和服务的交付效率和质量。
要创建连续流,以下是一些有效的方法和步骤:1.明确价值:首先,企业需要明确自己产品或服务的价值,了解客户需要什么以及他们对产品质量和效率有什么要求。
2.流程分析:对生产流程进行仔细分析,找出其中的浪费和瓶颈点。
浪费是指任何不增加价值的活动或资源的使用。
排除浪费可以提高生产效率和质量。
3.价值流图:创建价值流图以可视化整个生产流程。
价值流图是一个细致的流程图,显示了所有生产步骤和原材料、信息和劳动力在流程中的流动。
它帮助识别瓶颈、延误和浪费,并揭示改善的机会。
4.消除浪费:基于价值流图,集中精力消除浪费。
包括以下几类浪费:-运输:减少物料在不同工作站之间的运输次数和距离。
-库存:降低原材料和成品的库存,避免过多的库存造成的积压和浪费。
-动作:简化生产过程中的动作,减少不必要的步骤和移动。
-等待:减少等待时间,确保流程持续运转,不出现停滞。
-过度加工:避免对产品进行多余的加工或修饰,保持产品质量在客户要求范围内即可。
5.平衡流程:根据价值流图和消除浪费的目标,重新设计流程以平衡工作负载。
确保每个工作站的工作量相对平衡,避免出现瓶颈和过度负荷。
6.一次性制造:精益生产强调一次性制造,即在一个连续流上只生产所需数量的产品,以避免过度生产导致的浪费和库存积压。
7.持续改进:连续流的创建不是一次性的过程,而是一个持续改进的过程。
企业需要不断评估和改进生产流程,寻找更多的优化机会。
总之,创建连续流是实现精益生产的有效方式。
精益生产的两大支柱自働化和连续流

精益生产的两大支柱自働化和连续流
丰田精益屋,一边是准时生产(just in time),另一边是自働化。
准时生产就是连续流的化身,同理不在累述。
另一边就是自动化。
自働化不同于自动化:自动化就是单纯的自动作业,出了故障是需要人工操作停止机器作业。
自働化是发生异常时机器本身能作判断自动停止作业。
自働化是为了质量百分之百,为连续流(准时生产)扫清障碍,和连续流相辅相成。
包括内建质检,自己检查(逐步取消事后检验),可视化,安灯停线,防错。
精益屋从5S和标准化这些基础屋基开始,我们最好有人管,大家管,专人管。
精益屋就是精益系统,一步一步建起来吧!
当然从基础5S和标准化开始,不能急。
改善小书虫:李保章:
自働化(质量)和连续流(准时制),是精益生产的两大支柱。
相辅相成
改善小书虫:李保章:
批量大(不是单件流),质量问题被掩盖。
防错也发挥不了作用,(防错100%)是为了连续流不停线。
防错不好,靠事后检验,仍然会有不良品流出,更没有品质可言。
当然,精益屋顶,屋基,和支柱中间的核心是人。
人的智慧和行动,一边发现并解决问题防错,另一边换模换代加连续流。
抽调骨干,成立编外人员,干改善的事,大野耐一是这么干的。
精益生产之连续流讲解
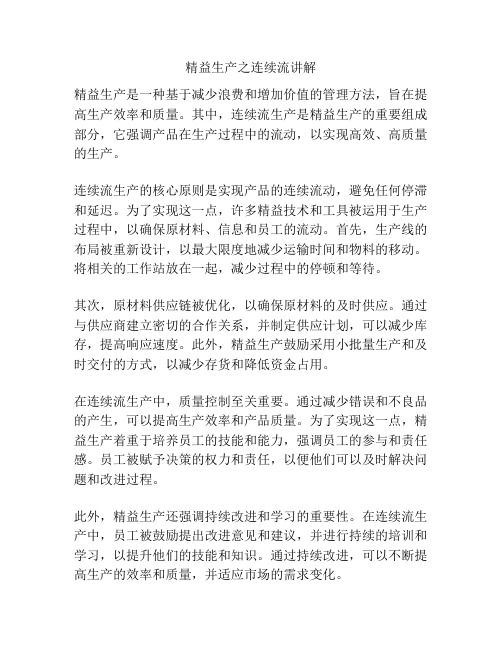
精益生产之连续流讲解精益生产是一种基于减少浪费和增加价值的管理方法,旨在提高生产效率和质量。
其中,连续流生产是精益生产的重要组成部分,它强调产品在生产过程中的流动,以实现高效、高质量的生产。
连续流生产的核心原则是实现产品的连续流动,避免任何停滞和延迟。
为了实现这一点,许多精益技术和工具被运用于生产过程中,以确保原材料、信息和员工的流动。
首先,生产线的布局被重新设计,以最大限度地减少运输时间和物料的移动。
将相关的工作站放在一起,减少过程中的停顿和等待。
其次,原材料供应链被优化,以确保原材料的及时供应。
通过与供应商建立密切的合作关系,并制定供应计划,可以减少库存,提高响应速度。
此外,精益生产鼓励采用小批量生产和及时交付的方式,以减少存货和降低资金占用。
在连续流生产中,质量控制至关重要。
通过减少错误和不良品的产生,可以提高生产效率和产品质量。
为了实现这一点,精益生产着重于培养员工的技能和能力,强调员工的参与和责任感。
员工被赋予决策的权力和责任,以便他们可以及时解决问题和改进过程。
此外,精益生产还强调持续改进和学习的重要性。
在连续流生产中,员工被鼓励提出改进意见和建议,并进行持续的培训和学习,以提升他们的技能和知识。
通过持续改进,可以不断提高生产的效率和质量,并适应市场的需求变化。
总之,连续流生产是精益生产的核心概念之一,它通过实现产品的连续流动,以提高生产效率和质量。
通过优化生产线布局、供应链管理和质量控制,可以减少浪费和提高产品的价值。
同时,精益生产还强调员工的参与和持续改进,在不断学习和创新中实现持续的增长和提升。
如前文所述,连续流生产是精益生产中至关重要的一部分。
下面将继续探讨连续流生产的关键要素和核心原则,以及实施连续流生产所面临的挑战和应对策略。
在连续流生产中,突破批量生产的束缚是至关重要的。
传统上,大部分企业都倾向于进行大批量的生产,以获得规模经济。
然而,这种大批量生产往往导致生产过程中的停滞和延迟,浪费了时间和资源。
精益生产-创建连续流
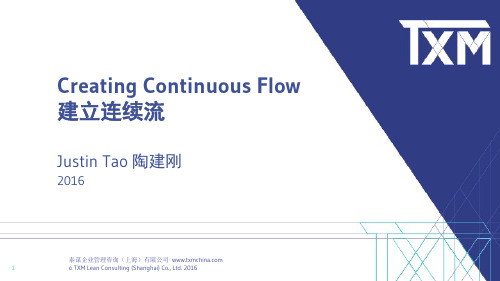
5
© TXM Lean Consulting (Shanghai) Co., Ltd. 2016
Eliminating the Non Value Added Operations 消除非增值操作
P1
P2
• Transfer lot size = Production lot size 搬运批量=生产批量
11
© TXM Lean Consulting (Shanghai) Co., Ltd. 2016
Continuous Flow Main Advantages 创建连续流的好处
• Increase in productivity; 提高生产率 • WIP reduction; 降低在制品 • Shorten lead time;缩短交货周期 • Reduce movement of parts; 减少部件搬运 • Reduce manufacturing required area; 减少制造所需空间 • Avoid overproduction;避免过量生产 • Avoid batch defects; 避免大批量质量问题 • Increase flexibility;增加弹性 • Visualize the problem; 将问题暴露出来
7
© TXM Lean Consulting (Shanghai) Co., Ltd. 2016
Reducing Batches to Pull 减少批量来拉动
P1 P2
P10
• Production Lot: 50 pieces (Fast Setup) 生产批量:50件(快速换型)
• Transfer Lot = Unitary (Single Piece Flow) 搬运批量=单一的(单件流)
创建连续流(精益生产)
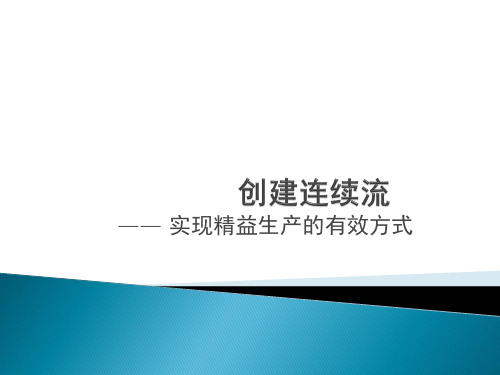
第三章
执行连续流的挑战及未来发展方向
连续流不是流水线更不是输送带,而是一种减少产 品等待时间的高柔性生产组织方式
实现连续流生产方式,增加了生产系统的脆弱和敏 感程度,对管理水平提出了更高的要求
大规模定制化生产 模块化设计、模块化生产和组装
基于计算机网络的团队协作方式 与电子商务的深度结合
2、对选定的产品系列做VSM分析
通过对选定的产品系列做价值流分析,我们可以 系统的找出生产运营流程中的各种浪费,从而对 生产运营流程的流畅性进行调整,从而实现连续 流生产。
绘制现状VSM
绘制未来VSM
识别出哪些工序内(间)可以创建连续流,进行改善
选择产品群的代表产品进行工作要素识别
工作要素指产品的加工步骤。加工步骤需要分割成 精细的动作组合,以便获取准确的观测数据
计算时可能出现小数点后几位, 当<0.3时,不增加操作员,进一步减少浪费和附带工作; 当0.3~0.5时,仍不增加操作员,经过两周的练习和改善,仔细分析 可消除的浪费及附带工作; 当>0.5时,如必要可增加一名操作员。通过减少浪费和附带工作,最 终取消该名操作员。
经过以上步骤,确定出人的工作步骤,下面将对场
工作要素的划分需遵循如下原则:
1. 容易看出动作的起点和终点 2. 有利于提高观测精度 3. 要由同一目标的一系列动作构成 4. 人操作时间和机器操作时间要分开 5. 规则要素和不规则要素划分清楚 6. 可变要素和不可变要素必须分开
观测时要注意将显而易见的浪费排除在工作要素之 外:
1. 不要把操作员的走动当成工作要素 2. 不要把周期操作计划外的工作视为工作要素 3. 不要把等待列为工作要素
—— 实现精益生产的有效方式
课程说明 课程目录
精益生产的核心思想

精益生产的核心思想引言精益生产(Lean Production)是一种由日本丰田汽车公司发展起来的生产管理方法,旨在通过消除浪费,提高效率和质量,从而实现生产流程的优化和精简。
精益生产的核心思想是通过持续改善和增加价值的方式来提高生产效率,同时注重员工参与和团队合作,以实现组织的长期成功和可持续发展。
核心原则精益生产的核心原则包括以下几个方面:1.价值流思维:精益生产强调以价值流为中心的思考方式。
通过对生产流程进行价值流分析,识别出无效的环节和冗余的活动,从而消除浪费,提高生产效率。
2.浪费的消除:精益生产强调消除各种形式的浪费,包括运输浪费、库存浪费、过程浪费等。
通过减少不必要的等待、传输和运动等环节,实现生产过程的优化和简化。
3.持续改进:精益生产的核心就是持续改进。
通过建立改进文化和鼓励员工提出改进建议,不断完善生产过程和工作环境,提高质量和效率,从而不断推动组织的发展。
4.员工参与:精益生产强调员工的参与和团队合作。
通过培养员工的技能和意识,激发员工的创造力和工作热情,实现员工与组织的共同发展。
核心工具和方法精益生产使用了一系列工具和方法来实现生产过程的优化和改进。
以下是其中几个常用的工具和方法:1.5S整理法:通过整理、排序、清洁、清扫和坚守纪律的方式,营造整洁和有序的工作环境,提高效率和工作品质。
2.Kanban看板:通过使用看板作为信息传递和控制的工具,实现对生产过程的可视化管理和控制。
3.精益流程改善:采用PDCA循环(Plan-Do-Check-Act)的方法,持续地进行流程改善和问题解决,以提高效率和质量。
4.持续流:通过建立具有一体化功能的生产线,通过物料的连续流动和“单出品”生产,实现生产过程的平衡和优化。
5.质量控制圈:采用QC(Quality Control)圈的方式,组织员工参与质量改进和问题解决,通过小组合作和系统化的方法,提高质量和效率。
精益生产的优势精益生产方法的应用可以带来以下几个优势:1.提高效率:通过消除浪费和优化生产流程,大大提高了生产效率和产能。
精益产品开发的13条原则

精益产品开发的13条原则作者:John Teresko 来源:《世界经理人》杂志发表时间:2008-09-17精益生产模式的开拓者丰田所采用的产品开发方针有如下13条:1.确定顾客界定的价值是什么,以区分哪些可以为顾客增值,哪些纯属浪费。
2.提前评估产品开发流程,以便在在具备最大设计空间的情况下,深入探索不同的解决方案。
3.创造连续、顺畅的产品开发流程。
4.遵照严格的标准,以减少变异,创造灵活性和可预见的结果。
5.开发首席工程师系统来实现开发集成。
6.平衡各职能部门内的专业知识,并促成不同职能部门间的整合。
7.培养所有工程师的能力。
8.将供应商全面整合到产品开发系统中。
9.在不断地学习与持续改进中成长。
10.建立执着追求卓越与持续改进的文化。
11.调整技术,以适应人员与流程。
12.通过简单的视觉交流团结整个组织。
13.使用功能强大的工具,以实现标准化和组织学习。
下面是诗情画意的句子欣赏,不需要的朋友可以编辑删除!!谢谢1. 染火枫林,琼壶歌月,长歌倚楼。
岁岁年年,花前月下,一尊芳酒。
水落红莲,唯闻玉磬,但此情依旧。
2. 玉竹曾记凤凰游,人不见,水空流。
3. 他微笑着,在岁月的流失中毁掉自己。
4. 还能不动声色饮茶,踏碎这一场,盛世烟花。
5. 红尘嚣浮华一世转瞬空。
6. 我不是我你转身一走苏州里的不是我。
7. 几段唏嘘几世悲欢可笑我命由我不由天。
8. 经流年梦回曲水边看烟花绽出月圆。
9. 人生在世,恍若白驹过膝,忽然而已。
然,我长活一世,却能记住你说的每一话。
10. 雾散,梦醒,我终于看见真实,那是千帆过尽的沉寂。
11. 纸张有些破旧,有些模糊。
可每一笔勾勒,每一抹痕迹,似乎都记载着跨越千年万载的思念。
12. 生生的两端,我们彼此站成了岸。
13. 缘聚缘散缘如水,背负万丈尘寰,只为一句,等待下一次相逢。
14. 握住苍老,禁锢了时空,一下子到了地老天荒15. 人永远看不破的镜花水月,不过我指间烟云世间千年,如我一瞬。
精益生产要素之连续流培训课件

Batch production 来自量生产Continuous flow production 连续流生产
6
一、连续流的目标和内容
2、连续流支持灵活的人力安排
Stage 1 1 3 5 1 Stage 2 3 5 TT Stage 1
1 2 A
3 4 B
5 6 C
TT Volume drop 2 A 4 B 6 C 2 A 4 B 6 Stage 2 C
2.3 专项练习
2.3.1 生产流程 2.3.2 布局改进
2.4 模板
4
一、连续流的目标和内容 2.1 连续流的简介
准时化生产分为五部分,它以最低的资源消耗,只在客户需要的时候生产客户需要的数 Flexible manpower 量。Material 物料 Flow 流程 Takt 节拍 Pull 拉动
WIP = Work-in-progress
12
一、连续流的目标和内容
3、连续流实施的阻力(有时批量生产是不可避免的) 单件流实施阻力
1、换模时间长 2、设备共享 3、过程周期时间是远 远长于节拍时间 4、流程之间距离较长 5、流程不稳定 6、健康和安全
举例
– 流程之间的周转时间非常快(周期时间很短),需要根据产品不同更换不同 的模具。
11
一、连续流的目标和内容
2、批量生产与单件流生产对比 与批量生产不同,单件流降低了在制品,消除了次品,并且缩短了交期。 传统的批量生产 单件流生产
A
在制品 在制品 在制品 时间
B
在制品 = 32 min
C
A
成品 在制品
B
时间 = 13 min
C
成品
10件订单,三道工序,23分钟之内产出1件产品
- 1、下载文档前请自行甄别文档内容的完整性,平台不提供额外的编辑、内容补充、找答案等附加服务。
- 2、"仅部分预览"的文档,不可在线预览部分如存在完整性等问题,可反馈申请退款(可完整预览的文档不适用该条件!)。
- 3、如文档侵犯您的权益,请联系客服反馈,我们会尽快为您处理(人工客服工作时间:9:00-18:30)。
课程目录
精益从心开始 改善从我做起
第一章
连续流的基本概念
精益从心开始 改善从我做起
什么是连续流?
1.连续流又称单件流,是按照客户需求的节 拍顺畅、连续、均衡的提供给客户需求的产 品和服务 2.连续流包含作业流、信息流、物流三个方 面
目的
精益从心开始 改善从我做起
目的:打造连续、稳定、周期短、易暴露问题的生产流程,流动中创造价值
间的关系进行分析,以进行产品分族
例子:高速路上车辆分道行驶
精益从心开始 改善从我做起
1.定义产品群组
举例:
产品名称 工序1 产品1 V 产品2 产品3 V 产品4 产品5 V 产品6 V 产品7 产品8 产品9 产品10 V 产品11 产品12 V 产品13 产品14 V 产品15 产品16 产品17 V 产品18 V 产品19 V 产品20
绘制价值流图(例如)
壳体车间产品价值流分析_现状图
壳体生产科
制造处计划科
月调变指令每月发送2次
组合电器
发运次数:2次/天 发运数量:10件/次
焊接工段
完成产出
1
1234
2
1234
3
1234
4
1234
1234
生产周期
20分钟 44分钟 66分钟 94分钟
加工周期 20分钟 24分钟
22分钟 28分钟
精益从心开始 改善从我做起
连续流生产与批量生产对比
二、连续流生产
序号
第一工序 5分钟/个
第二工序 6分钟/个
第三工序 第四工序 5.5分钟/个 7分钟/个
优化增值的环节:这是指优化增值环节本身,尽管这些环节在流程中是增值的,但仍然有提升的空 间 ,所以在精益的过程中,进一步挖掘增值环节的潜力提高增值环节的效率,会大大提高流程效率
增值环节的整合:这是指对所有增值环节整体上的优化,增值环节如果可以并行,经过整合后, 也可以大大提高流程的效率。
目的
精益从心开始 改善从我做起
工艺路线 必须相似, 且易于弹 性调配设 备、作业 人员和作 业时间。
精益从心开始 改善从我做起
1.定义产品群组
举例:
对分族后的产品群进行数量分析
产品群
A类 B类 C类 D类 E类
销售数量 (设计产能)
1200 600 350 246 50
备注:数据根据实际考虑选用 过去的销售数据,或未来产能 设计数据。
工序2
V
V
V V V V V
V
V V
V
V
工序3 V V
V V
工序4 V V V V V V
V V V V V
V V V V V V V
工序5
V V V V V
V
工序6 V V V V
V V
V V
V
V V V
V
工序7 V
V V V V V
V
V V V V
V V V
通过对生产的 所有产品进行 工艺路线分析, 划分产品族
人的动作
除去
不产生附加本可以无限下降 (改善无止境)
支柱
精益从心开始 改善从我做起
准创造价值 消除浪费自
时 在正确的时间提供
正确数量的需求
化
连续流生产
动 即时暴露问题,
解决问题
化
目视化、防错等
精益从心开始 改善从我做起
连续流生产与批量生产对比
一、批量生产
序号
第一工序 第二工序 第三工序 第四工序 5分钟/个 6分钟/个 5.5分钟/个 7分钟/个
完成产出 生产周期
1 2 3 4
加工周期
1 2 3 4
5分钟
1 2 3 4
6分钟
1
2
1
3
2
4
3
4
5.5分钟 7分钟
1 2 3 4
5分钟 11分钟 16.5分钟 23.5分钟 30.5分钟 37.5分钟 44.5分钟
精益从心开始 改善从我做起
第二章
实现连续流的基本步骤
精益从心开始 改善从我做起
主要步骤
资源输入
加工过程(流程)
客户需求量
资源输入
加工过程(流程)
客户需求量
精益从心开始 改善从我做起
目的
等待时间 不增值
精益之前
工作时间
增值
精益之后
流程时间
1 流程优化前的环节 2
3
1 23
4 5 流程优化后的环节
4
5
去除或减少不增值的环节:把流程中冗长的环节进行简化,提高流程增值环节的比例,缩短整个流 程 的时间,从而提高了流程的效率。
工序2
V V
V V V V
V V V V V V
工序6 V V V V
V V V
V V V V V V
工序7 V V V V V V V V V V V V V V
工序1 V V V
V V V
V V V V
工序5
V V V V V V
工序3 V V V V
A类 B类 C类 D类
E类
产品分族 时注意:
精益从心开始 改善从我做起
2.价值流( VSM)分析
精益从心开始 改善从我做起
2.价值流( VSM)分析
绘制价值流图
要点:数据根据现场实际写实得出,同时测量时尽量保证所测对象为中等熟练程度且 在正常作业条件下按照正常的速度以标准的作业方法作业。
精益从心开始 改善从我做起
2.价值流( VSM)分析
精益从心开始 改善从我做起
1.定义产品群组
举例:
产品名称 工序4 产品1 V 产品14 V 产品17 V 产品4 V 产品5 V 产品10 V 产品19 V 产品15 V 产品7 产品13 产品18 V 产品3 V 产品12 V 产品6 V 产品2 V 产品8 V 产品9 V 产品11 V 产品16 V 产品20 V
传统的制造 (分批排队)
现金-现金转换
流程 3
成品
流程 1
在制品
流程 2
在制品
原材料
总成本
基于时间的制造 (单件流)
时间 现金-现金转换
流
原材 程
料
1
流 成品 流 程3
程
2
总成本
时间
总成本随着跨度时间的缩短而降低!
精益从心开始 改善从我做起
核心:消除浪费
需要
产生附加价 值的部分
不产生附加 价值的部分
1.定义产品群组 2.价值流( VSM)分析 3.确定生产节拍 4.工序均衡 5. 精益布局 6.标准作业 7.多技能工培养 8.成果保持
精益从心开始 改善从我做起
1.定义产品群组
目的:有助于把握和利用产品的共性,把握重点, 由点向面进行扩展
原理:成组技术、20/80原则 方法:PQ/PR分析(即对产品与数量及工艺路线之
通过分析,可以建立针对A类产品和 B类产品的连续流生产专线。 对C类、D类、E类产品考虑建立一 条通用生产线或3个生产单元。
精益从心开始 改善从我做起
2.价值流( VSM)分析
通过对选定的产品系列做价值流分析,我们可以 系统的找出生产运营流程中的各种浪费,从而对 生产运营流程的流畅性进行调整,从而实现连续 流生产。