高分子材料成型设备第六章挤出机挤出辅机8
高分子材料成型加工设备教学设计
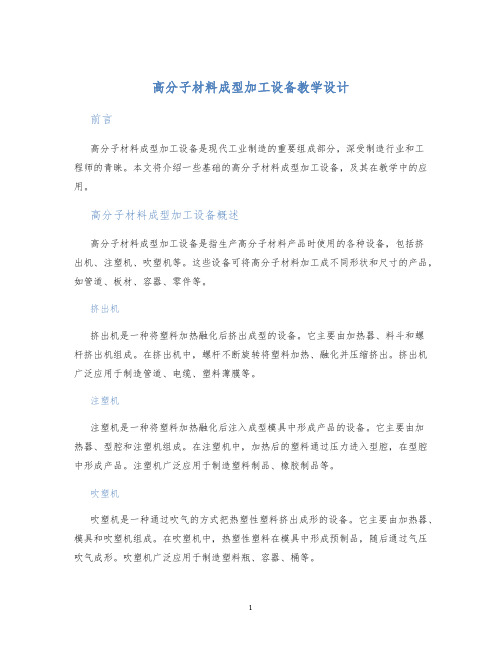
高分子材料成型加工设备教学设计前言高分子材料成型加工设备是现代工业制造的重要组成部分,深受制造行业和工程师的青睐。
本文将介绍一些基础的高分子材料成型加工设备,及其在教学中的应用。
高分子材料成型加工设备概述高分子材料成型加工设备是指生产高分子材料产品时使用的各种设备,包括挤出机、注塑机、吹塑机等。
这些设备可将高分子材料加工成不同形状和尺寸的产品,如管道、板材、容器、零件等。
挤出机挤出机是一种将塑料加热融化后挤出成型的设备。
它主要由加热器、料斗和螺杆挤出机组成。
在挤出机中,螺杆不断旋转将塑料加热、融化并压缩挤出。
挤出机广泛应用于制造管道、电缆、塑料薄膜等。
注塑机注塑机是一种将塑料加热融化后注入成型模具中形成产品的设备。
它主要由加热器、型腔和注塑机组成。
在注塑机中,加热后的塑料通过压力进入型腔,在型腔中形成产品。
注塑机广泛应用于制造塑料制品、橡胶制品等。
吹塑机吹塑机是一种通过吹气的方式把热塑性塑料挤出成形的设备。
它主要由加热器、模具和吹塑机组成。
在吹塑机中,热塑性塑料在模具中形成预制品,随后通过气压吹气成形。
吹塑机广泛应用于制造塑料瓶、容器、桶等。
高分子材料成型加工设备教学设计在高分子材料成型加工设备教学中,实验教学是非常重要的一部分。
通过实践,能够加深学生对设备的理解和操作方法,从而提高学生实际操作能力。
下面是一个针对高分子材料成型加工设备的实验教学设计:实验名称基本高分子材料成型加工设备的操作和维护实验目的1.掌握高分子材料成型加工设备的操作流程和操作技能;2.理解设备的结构原理和安全操作规程;3.掌握设备的日常维护方法。
实验材料注塑机、挤出机、吹塑机、高分子材料实验步骤操作和维护部分1.学生随机抽取设备,了解设备的基本结构和使用方法;2.学生对设备进行操作演练,操作时应注意设备的安全使用规程;3.学生学习不同设备的日常维护方法。
成型操作部分1.学生可以根据自己的兴趣选择不同的设备进行操作,如挤出机、注塑机、吹塑机等;2.学生需要根据设备的工作原理,选择不同的高分子材料进行加工操作。
《高分子材料成型加工基础》课件——项目三-挤出成型

三.辅助设备:
• 前处理设备:预热. 干燥 • 控制生产的设备:各种控制仪表
四. 挤出机的一般操作法:
• 处理挤出物的设备:冷却定型. 牵引.切割.卷取
① 开机前准备: ② 料最好先干燥、必要时须预热 ③ 换上新的多孔板及滤网,检查并装上机头 ④ 检查电器及机械,在传动部分加足润滑油
⑤ 开电热预热:先预热机头、后机身,同时料 斗座通水冷却
● 3.螺杆: ● 挤出机的改进主要在螺杆上 ● (1)螺杆直径(D)与长径比(L/D): ● D↑:挤出机大,产量高(产量∝D2) ● L/D: L为有效长度 ● L/D↑:利于塑化, ↑产量,适应性强
(2)螺杆各段的作用:
• ①加料段: • 加料口(2~10D) • 使塑料受热前移、
压实物料
使塑料密实、排气 ● 热:外加热、 内摩擦热,物料由固体→熔体 ● 完全塑化后经机头挤出成型、冷却定型或拉、吹胀为最终制品
二.塑料在挤出成型中的受热:
● 热量来源:外加热与摩擦热 ● 加料段:
固体物料,螺槽深,温差大,外加热为主 ● 均化段:
熔体,螺槽浅,温差小,摩擦热为主 ● 压缩段:
介于以上两段之间 ● 故挤出机必须分段控温
一.挤出成型的塑料
● 几乎所有热塑性料和某些热固性料:如PVC、PE、PP、PS、PA、ABS、PC等及 PF、UF(脲醛树脂)等
二.挤出成型的制品
● 管、板、单丝、膜、电线、棒、异型材、中空制品(瓶等)等
三.挤出成型特点
生产连续化 生产效率高:挤出制品单机产
量比注塑制品大一倍以上
适应范围广 经济效益好:设备成本低、投资收效快
一.挤出成型设备(挤出生产线或挤出机组) ● ——以塑料异型材为例
6.5挤出成型工艺详解

问题 挤出成型原理
牵引速度略大于挤出速度 不同的塑件,牵引速度不同。
挤出成型工艺
挤出成型设备
产品工艺过程
思考与练习
2024年8月2日
第六章 塑料成型技术
四、挤出成型工艺条件
问题 挤出成型原理 挤出成型工艺 挤出成型设备 产品工艺过程 思考与练习
温度 压力
挤出速度 牵引速度
2024年8月2日
第六章 塑料成型技术
1、掌握挤出成型的特点; 2、熟悉挤出机的结构和主要部件的作用; 3、掌握挤出理论中影响生产和产品质量的因素; 4、熟悉管材、薄膜、板与片、拉伸膜的工艺。
第六章 塑料成型技术
6.3 挤出成型
一、概述
2024年8月2日
问题 挤出成型原理
1.挤出成型原理:将塑料塑化后使其在一定压力下通过某种 模具而形成截面形状与此模具相仿的连续体,并在固化后保 持该形状的成型方法。
•
与金属管相比,塑料管材有以下优点:相对密
度小,仅为金属的1/5、1/8,耐化学腐蚀性好,
电器绝缘性优良。耐磨性好。塑料管广泛用作各种
液体、气体输送管,尤其是某些腐蚀性掖体和气体,
如自来水管、排行管、农业排灌用管、化工管道、
石油管、煤气管等。
思考与练习
第六章 塑料成型技术
问题 挤出成型原理 挤出成型工艺 挤出成型设备 产品工艺过程 思考与练习
减小压力波动。
第六章 塑料成型技术
2024年8月2日
问题 挤出成型原理 挤出成型工艺 挤出成型设备 产品工艺过程 思考与练习
3.挤出速度 单位时间内由挤出机头和口模中挤出的塑化好
的物料量或塑件长度。它表示挤出能力的高低。 影响因素:机头、螺杆和料筒的结构、螺杆转速、 加热冷却系统的结构和塑料的性能 4.牵引速度 牵引速度与挤出速度相当,可略大于挤出速度。
挤出成型设备介绍(PPT 88页)

气式(常规式)挤出机。 ⑷按用途分:制品成型挤出机、混炼造
粒挤出机和压延机喂料挤出机。 ⑸按螺杆转速分:常规挤出机(100~
300r/min)、高速挤出机(300~900r/min
)和超高速挤出机(900~1500r/min)。
①机头
俗称口模,是挤出成型的模具,是制品 成型的主要部件。熔料通过它获得一定的 几何截面和尺寸。
7
②定型装置 稳定从机头挤出的制品的形状,并对其
进行精整,从而得到尺寸更为精确的截面 形状及更为光亮的制品表面。定型过程通
常采用冷却和加压的方法来实现。 ③冷却装置
对经定型后的制品实施进一步冷却,以 获得最终制品的形状和尺寸。 ④牵引装置
表层得到不断的更新,具有很好的脱挥排气
性能。 ②啮合型异向旋转双螺杆挤出机
29
工作原理: ⅰ由于两根螺杆的旋转方向不同,一根螺 杆中物料旋转前进的道路被另一根螺杆堵死, 故不能形成”∞”运动。在啮合处,一根螺杆 的螺纹插入另一根螺杆的螺槽中,使连续的 螺槽被分割成互相隔离的C形小室。螺杆旋 转时,随着啮合部分的轴向移动, C形小室 也沿着轴向前移,螺杆每转一圈, C形小室
④发泡挤出机。在机筒上开设有发泡剂加 入装置,可成型发泡的挤出制品。
16
⑤喂料挤出机。机筒可以摆动一个角 度,主要用于给压延机均匀喂料。
⑥阶式挤出机。由两台(以上)挤出 机串联而成,主要用来回收造粒、脱挥或 发泡成型加工。
⑦电磁动态挤出机。是近年中国首创
发明的利用电磁动态作用进行塑化的挤出 机,特点是结构紧凑和节省电能。
⑧可视化挤出机。是近年开发的在机
高分子材料成型设备第六章挤出机排气式和双螺杆挤出机7
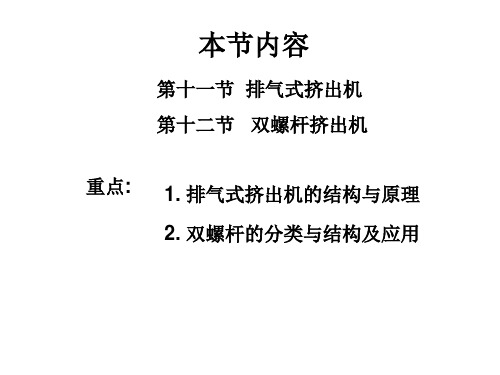
六、排气机的主要参数
第一阶螺杆长占螺杆全长53—58%,其它各段比例 与普通螺杆相似。
泵比:第二均化段的螺槽深度与第一均化段的螺槽深度 之 比。
泵比x=hⅡ/hⅠ(⒈5—⒉0) 排气段的长度:(2~6)D
第十二节 双螺杆挤出机
一、概述
1、单螺杆机的缺陷:加料性能不好,粉料、 玻纤等较难加入;表面更新小,排气差; 自洁性差;物料停留时间长,颜料易变色, 排出产量低。 2、双螺杆机的优点:①加料容易,无回流, 粉尘的加工更好②物料停留时间短③排气 好④混合塑化优异⑤功耗低,可减少50% ⑥螺杆特性硬
三、不同双螺杆挤出机的应用
• 封闭式反向(转动)全啮合型(CICT)双螺杆挤出机 类型不同用途不同,选用时要 – 可用于异型材挤出(低的最大螺杆速度20~40r/min); 根据所用原料的特性(如软硬、 – 可用于配料、连续的化学反应(高的最大螺杆速度 100~200r/min); 粘度、热敏性、温度、形状(粉、 粒料、填充物)和加工目的 • 同向、啮合型(CICO)双螺杆挤出机 (成型产品及特点、混合、塑 – 封闭式啮合型双螺杆挤出机 炼等)选用相适应的双螺杆挤 • 应在低速下运转,主要应用于异型材挤出 出机。 – 自洁式双螺杆挤出机( CSCO ) • 用于混合 • 非啮合型双螺杆挤出机 – 主要用于混合、排气、连续的化学反应。
二、双螺杆的分类与结构
按两根螺杆啮合与否
啮合型:自洁好,走“∞”。 非啮合型:自洁差,物料运动复杂。
按螺杆旋转的方向分
同向啮合:齿顶与齿根间隙小物料走“∞”路线, 混料好,多用混料造粒,自洁好。 异向啮合:齿顶与齿根间隙大,物料走“○”路 线,剪切强烈,塑化好,自洁差。
按两根螺杆轴线的相对位置分 平行双螺杆挤出机
高分子材料成型加工挤出
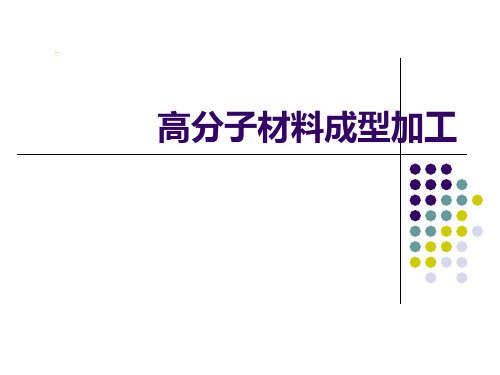
螺杆形式和分段
1-渐变型(等距不等深) 2-渐变型(等深不等距) 3-突变型 4-鱼雷头螺杆 Ⅰ-加料段(固体输送段) Ⅱ-压缩段(熔融段) Ⅲ-计量段(均化段)
加料段 压缩段 计量段
将料斗供给的物料送往压缩段 压缩物料、排除空气
将熔融的物料定量定压送入机头
固态、部分熔融 熔融态 熔融态
螺杆的几何结构参数
工艺示例
以聚丙烯薄膜为例:薄膜厚度10~60μm,挤出温度250~270℃,流 延温度30~40℃,纵向拉伸温度125~145℃、拉伸比4.5~6.0,横向拉 伸温度160~170℃,拉伸比9.0~10.0,热处理温度170~180℃, 陈化处 理2~3天,释放拉伸应力和薄膜表面和起作用的添加剂迁移到表面。
挤出成型设备
螺杆式挤出机:连续成型,用途最多; 柱塞式挤出机:间歇成型,一般不用;
单螺杆式挤出机
螺杆式挤出机 双螺杆式挤出机
多螺杆式挤出机
以单螺杆和双螺杆式挤出机最为常见。
螺杆式挤出机
螺杆式挤出机主要构成
传动装置 加料装置 料筒 螺杆 机头
传动装置
由电机、减速箱、轴承等部分组成 主要作用是带动螺杆转动
感谢阅读
塑化
在挤出机内将固体塑料加热并依靠塑料之间的内摩擦热使其成为 粘流态熔体物料。
固体态聚合 物或混合物
熔融态聚合 物或混合物
成型
在挤出机螺杆的旋转推挤作用之下,通过具有一定形状的口模, 使粘流态的物料成为连续的型材。
1-转动机构;2-止推轴承;3-料斗;4-冷却系统; 5-加热器; 6- 螺杆;7-机筒;8-滤板;9-机头孔型
加热或引发剂
冷却 聚合
(3)物理化学变化兼有:热固性塑料、橡胶
挤出成型工艺—挤出造粒操作(塑料成型加工课件)
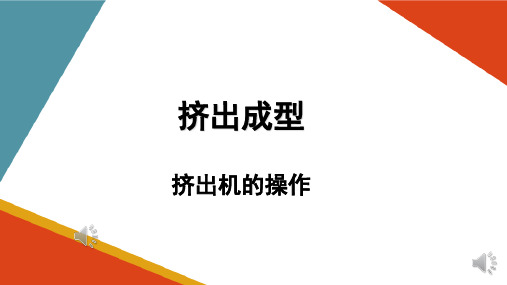
三、操作注意事项
1. 未经培训人员不能单独操作。 2. 操作前应先检查好电源、设备和急停装置。 3. 不能将刮刀、铁丝等工具伸入到料筒中。 4. 进行实训操作时要戴隔热手套,不能触碰料 筒和机头等加热区域。 5. 操作结束后要及时清理辊筒和现场卫生。
挤出成型
挤出机的操作
一、操作设备
挤出机主要用于塑料的挤出成型,生产具有恒定截面连 续的塑料制品。根据不同类型的螺杆和辅机设备,可制得的 塑料制品也不同,其主要关键的操作在于挤出设备的操作。
二、操作过程
1.检查清理 设备
检查喂料口和排气口是否通畅,冷却水槽的水量是 否足够;将挤出螺杆和喂料螺杆的转速调节回零;接通 电源,检查电箱风机是否正常,并接通所有开关。
注意:喂料转速要比挤出转速略低一些。
料斗
口模
吹风口
4.造粒
将挤出物料牵引至造粒机切粒口,启动开关,调节切刀 转速直至与挤出速度相符;将切出的粒料用料斗车接住,观 察粒料。
开关
切粒口
切刀转速
出料口
5.停机
当料斗内的物料喂完后,将喂料螺杆缓慢调节回零,关 闭喂料螺杆;然后等料筒内物料挤完,将挤出螺杆缓慢调节 回零,关闭挤出螺杆和风机;最后关闭钥匙开关和电源,清 理干净后完成实训。
注意:喂料口和排气孔如果堵住必须在断电状态下 用软质的铜棒清理,不可使用硬质铁器。
喂料口 排气口
机箱开关
2.预热
启动加热,将六个加热区和机头的温度设置到所需 温度,当温度达到设置值后再恒温一段时间。
温度控制
挤出转速控制 钥匙开关 风冷、水冷
喂料转速控制
挤出启停
喂料启停
3.挤出启动风冷,将物料倒源自料斗中,启动挤出螺杆和喂料螺 杆,缓慢调节螺杆转速;物料从口模挤出后,牵引至水槽过 水冷却,再由吹风口通过干燥。
高分子材料成型加工基础 第六章注塑成型

第六章注塑成型一、简答题1.简单描述一个完整的注塑过程。
塑化物料,注塑,保压冷却,开模,脱模,合模2.注塑制品有何特点。
壁厚均匀;制品上有凸起时,要对称,这样容易加工;为加强凸台的强度.要设筋,并在拐角处加工出圆角;倾斜的凸台或外形会使模具复杂化,而且体积变大,应该设计为和分型面垂直的形状;深的凹进部分.尽可能的集中在制品的同一侧;对于较薄的壁.为避免出现侧凹,可将制品上的凹孔设计成v形槽;所有的拐角处都应有较大的圆角。
3.注塑机有几种类型,包括哪些组成部分。
按传动方式:机械式注塑机,液压式注塑机,机械液压式注塑机按操纵方式:手动注塑机、半自动注塑机、全自动注塑机按塑化方式:柱塞式注塑机、预塑式注塑机、橡胶注塑机包括以下:注射装置、合模装置、液压电气控制系统4.柱塞在柱塞式注塑机中的作用。
柱塞将注塑力传递至聚合物,并将一定的熔料快速注射入模腔。
5.挤出机和注塑机的螺杆有何异同。
注塑机的螺杆存在前进、后退运动,多为尖头,压缩比较小6.为了防止“流涎”现象,喷嘴可采用哪几种形式,描述每种形式的工作原理。
小孔型:孔径小而射程长。
料压闭锁型:利用预塑时熔料的压力,推动喷嘴芯达到防止“流涎”弹簧锁闭式:用弹簧侧向压合顶针。
可控锁闭式:用液(或电、气)动控制顶针开闭7.锁模系统有哪几种型式,描述每种型式的工作原理。
液压式,轴杆式8.注塑机料筒清洗要注意哪些问题。
1.首先使用上要注意操作的问题。
2.如果加工的物料有腐蚀性,且停机后需要一定时间才开机,则要及时对料筒进行清洗。
清洗工作应在料筒加热情况下进行,一般用聚苯乙烯作为清洗料。
在清洗结束后,立即关闭加热开关,并做结束工作。
3.如果是一般物料,清洗时一定要升温到上次实验物料的熔点之上进行清洗,否则螺杆会扭断。
后在降温到所需温度进行实验。
4.清洗时可采用高低不同转速进行清洗,容易洗净。
最后在所需转速清洗,后进行实验。
9.嵌件预热有何意义。
为了装配和使用强度的要求,理解塑件内常常嵌入金属嵌件。
挤出成型工艺
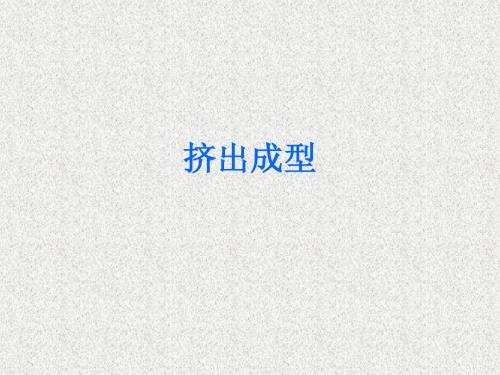
法易于进行机械加工,故多采用。
螺槽深度(h):
h↓,剪切速率↑,传热效率
↑,混合及塑化效率↑,生产率↓ 。故热敏性塑料(如PVC)宜用深 螺槽,而熔体粘度低且热稳定性好 的塑料(如聚酰胺等)宜用浅螺槽 。
螺旋升角θ
θ↑,出料快,生产能力↑,
但停留时间短,塑化↓。
实验证明,物料形状不同,对加
料段的螺纹升角要求也不一样。 1)θ=30 °左右适于粉料, 2)θ=l7°左右适于圆柱料, 3)θ=15°左右适于方块料。 出于机械加工的方便,一般取D=S ,θ=17°40’。
• a螺杆特性曲线
• 它是一组相互平行的直线族,随螺杆转速n的改变而改变。 螺杆的特性线是挤出机的重要特性之一,它表示螺杆均化 段熔体的流率与压力的关系。随着机头压力的升高,挤出 量降低,而降低的快慢决定于螺杆特性线的斜率。
b.口模特性曲线 挤出机机头是挤出机的重要组成部分, 是物料流经并获得一定几何形状、 必要尺寸精度和表面光洁度的部件。 假定熔体为牛顿流体,当其通过机 头时,其流率方程为:
实际上螺槽中熔体的总的流动是这几种流动的总 和。
挤出机的生产能力:
Q=Qd (正流)- Qp (逆流)- QL (漏流)
(4)挤出机的工作状态
要想了解整个挤出过程的特性,还必须将螺杆和机 头联合起来讨论,为此我们引入了以下几个概念: • 螺杆特性线---挤出机产量与挤出压力的关系; • 口模特性线---机头产量与机头压力的关系; • 挤出机的综合工作点---螺杆特性线与口模特性线 的交点
b、逆流方向 流动,流量为QP
c. 漏流: 由口型阻力引起,沿螺棱顶部与料筒
内表面之间的间隙中反向流动。 方向沿螺杆轴线方向,并由机头向后, 不利于产量的提高。流量用QL表示。
第6章挤出成型工艺

第六章挤出成型工艺第一节热塑性塑料工艺特性(一)收缩率热塑性塑料加工成型中产生的热收缩产生原因:宏观:材料的热胀冷缩行为-微观:分子间自由体积发生变化。
通常高分子材料的热膨胀系数远大于金属材料、陶瓷材料。
影响热塑性塑料成形收缩的因素如下:第六章挤出成型工艺第六章挤出成型工艺1、塑料品种热塑性塑料成形过程中由于还存在结晶化形起的体积变化,内应力强,冻结在塑件内的残余应力大,分子取向性强等因素,因此与热固性塑料相比则收缩率较大,收缩率范围宽、方向性明显。
另外成形后的收缩、退火或调湿处理后的收缩一般也都比热固性塑料大。
第六章挤出成型工艺2、塑件特性成形时融料与型腔表面接触外层立即冷却形成低密度的固态外壳。
由于塑料的导热性差,使塑件内层缓慢冷却而形成收缩大的高密度固态层。
所以壁厚、冷却慢、高密度层厚的则收缩大。
另外,有无嵌件及嵌件布局,数量都直接影响物料流动方向,密度分布及收缩阻力大小等,所以塑件的特性对收缩大小,方向性影响较大。
第六章挤出成型工艺3、进料口形式、尺寸、分布这些因素直接影响物料流动方向、密度分布、及成形时间。
直接进料口、进料口截面大(尤其截面较厚的)则收缩小但方向性大,进料口宽及长度短的则方向性小。
距进料口近的或与物料流动方向平行的则收缩大。
4、成形条件模具温度高,融料冷却慢、密度高、收缩大,尤其对结晶料则因结晶度高,体积变化大,故收缩更大。
另外,保持压力及时间对收缩也影响较大,压力大、时间长的则收缩小但方向性大。
第六章挤出成型工艺(二)流动性1、热塑性塑料流动性大小,一般可从分子量大小、熔融指数、表现粘度及流动比(流程长度/塑件壁厚)等一系列指数进行分析。
分子量小,分子量分布宽,分子结构规整性差,熔融指数高、表现粘度小;流动比大的则流动性就好。
按模具设计要求我们大致可将常用塑料的流动性分为三类:第六章挤出成型工艺(1)流动性好:尼龙、聚乙烯、聚苯乙烯、聚丙烯、醋酸纤维素;(2)流动性中等改性:聚苯乙烯(例ABS·AS)、PMMA、聚甲醛、聚氯醚;(3)流动性差:聚碳酸酯、硬聚氯乙烯、聚苯醚、聚砜、聚芳砜、氟塑料。
第6章 塑料挤出模具(机头)设计 6.4~6.5(第24讲)

第 24 讲 6.4 吹塑薄膜机头设计 一、吹膜机头的分类及特点 二、吹膜机头的结构设计
6.5 板材挤出机头设计 一、板片材挤出机头类型及特点 二、平缝式机头的设计要点
《塑料成型工艺与模具设计》 第6章 塑料挤出模具(机头)设计
6.4 吹塑薄膜机头设计
《塑料成型工艺与模具设计》 第6章 塑料挤出模具(机头)设计
1、芯棒式吹膜机头
(2)芯棒式机头设计要点 物料均匀分配问题 • 方法一:在芯棒上设置平衡流道, 方法一:在芯棒上设置平衡流道 设置平衡流道, 槽宽a等于机头进料口直径 等于机头进料口直径, 槽宽 等于机头进料口直径,深度为芯 棒侧原有间隙的1~1.5倍。 棒侧原有间隙的 倍
《塑料成型工艺与模具设计》
第6章 塑料挤出模具(机头)设计
3、螺旋式吹膜机头
螺旋槽数与芯棒直径关系
螺旋槽数与径向孔数相等;径向孔径取决于树脂种类、 螺旋槽数与径向孔数相等;径向孔径取决于树脂种类、温 度和挤出量,通常为φ8 φ16mm,螺槽起始深度16 20mm, φ8~φ16mm 16~20mm 度和挤出量,通常为φ8 φ16mm,螺槽起始深度16 20mm, 螺距16 22mm,口模平直段长度20 25mm,环隙0.8 1.2mm。 16~22mm 20~25mm 0.8~1.2mm 螺距16 22mm,口模平直段长度20 25mm,环隙0.8 1.2mm。 机头中心进料孔直径:过小阻力大, 机头中心进料孔直径:过小阻力大,过大则会在孔壁处滞 流引起熔体分解。 流引起熔体分解。
《塑料成型工艺与模具设计》
第6章 塑料挤出模具(机头)设计
3、螺旋式吹膜机头
结构: 结构:中心进料后沿径向பைடு நூலகம்成 3~6股料流,到达芯棒表面后, 6股料流,到达芯棒表面后, 进入各自的螺旋槽, 进入各自的螺旋槽,螺槽由深变 最终消失; 浅,最终消失;物料流动过程中 逐渐熔合,可有效消除熔接痕。 逐渐熔合,可有效消除熔接痕。
挤出成型机组包括什么设备

挤出成型机组包括什么设备挤出成型机组是一种常见的生产设备,广泛应用于塑料制品、橡胶制品、金属材料等行业。
挤出成型机组通常由多个不同设备组成,各个设备共同协作完成材料挤出成型的过程。
下面将介绍挤出成型机组包括的主要设备及其功能。
1. 挤出机挤出机是挤出成型机组的核心设备之一。
挤出机通常由螺杆和筒组成,通过螺杆的旋转将材料从进料口输送到出料口,并且在过程中通过加热和挤压形成所需的产品形状。
挤出机的性能直接影响到挤出成型的效果和产品质量。
2. 模具模具是用来成型产品形状的重要设备。
挤出成型机组通常需要根据产品的形状来选择合适的模具,通过模具的设计和制造可以实现不同形状和尺寸的产品生产。
模具的设计精准度和制造质量对产品的成型效果和质量有着重要影响。
3. 冷却系统冷却系统通常包括水冷却系统和风冷却系统。
在挤出成型过程中,通过冷却系统对产品进行及时降温,以防止产品变形或产生缺陷。
冷却系统的设计和运行稳定性能直接影响产品的成型速度和质量。
4. 牵引机牵引机是用来将挤出的产品持续牵引和拉伸,以确保产品的形状和尺寸保持稳定。
牵引机通常具有不同牵引速度和力度的调节功能,可以根据产品的要求进行灵活调整。
牵引机的性能对产品的表面光滑度和尺寸一致性有着重要影响。
5. 切割机切割机是将挤出的产品按照要求的尺寸进行切割和定型的设备。
切割机通常具有高速、精确的切割功能,可以实现对产品尺寸的精确控制。
切割机的性能对产品的最终成型质量和外观效果有着决定性影响。
结语挤出成型机组是一个由多个不同设备组成的生产系统,在实际生产中各个设备之间需要密切协作,以确保产品的高效率生产和优质成型。
以上介绍的挤出成型机组包括的设备主要包括挤出机、模具、冷却系统、牵引机和切割机,它们各自担负着重要的功能,共同组成一个完整的挤出成型生产线。
挤出成型技术在现代工业生产中具有重要地位和应用前景,随着科技的不断发展和进步,挤出成型机组的设备和技术也在不断创新和完善,为各行各业的生产提供了更多可能性和选择。
挤出成型原理

挤出成型设备1、主机挤出系统:由螺杆与料筒组成,是挤出机关键部分。
其作用是塑化物料,定量、定压、定温挤出熔体传动系统:驱动螺杆,提高所需的扭矩和转矩加热和冷却系统:保证塑料和挤出系统在成型过程中温度达工艺要求2、辅机由机头、定型装置、冷却装置、牵引装置、卷取装置或切割组成3、控制系统由电器、仪表和执行机构组成。
作用:控制主、辅机电动机、以满足所需转速和功率;控制主辅机温度、压力、流量,保证制品质量;实现挤出机组的自动控制,保证主、辅机协调运行。
挤出成型原理料自料斗进入料筒,在螺杆旋转作用下,通过料筒内壁和螺杆表面摩擦剪切作用向前输送到加料段(玻璃态),在此松散固体向前输送同时被压实;压缩段(高弹态),螺槽深度变浅,进一步压实,同时在料筒外加热和螺杆与料筒内壁摩擦剪切作用,料温升高开始熔融,压缩段结束;均化段=计量段(黏流态)使物料均匀,定温、定量、定压挤出熔体,到机头后成型,经定型得到制品。
对于非晶聚物,对它施加恒定的力,观察它发生的形变与温度的关系,通常特称为温度形变曲线或热机械曲线。
非晶聚物有三种力学状态,它们是玻璃态、高弹态和粘流态。
在温度较低时,材料为刚性固体状,与玻璃相似,在外力作用下只会发生非常小的形变,此状态即为玻璃态:当温度继续升高到一定范围后,材料的形变明显地增加,并在随后的一定温度区间形变相对稳定,此状态即为高弹态,温度继续升高形变量又逐渐增大,材料逐渐变成粘性的流体,此时形变不可能恢复,此状态即为粘流态。
我们通常把玻璃态与高弹态之间的转变,称为玻璃化转变,它所对应的转变温度即是玻璃化转变温度,或是玻璃化温度。
高弹态(rubbery state):链段运动但整个分子链不产生移动。
此时受较小的力就可发生很大的形变(100~1000%),外力除去后形变可完全恢复,称为高弹形变。
高弹态是高分子所特有的力学状态。
相对分子质量很大的晶态聚合物达到后还不能流动,而是先进入高弹态,在升温到后才会进入黏流态,于是有两个转变。
塑料成型工艺第六章-挤出成型

适用的树脂材料: 绝大部分热塑性塑料及部分热固性塑料,如
PVC、PS、ABS、PC、PE、PP、PA、丙烯酸 树脂、环氧树脂、酚醛树脂及密胺树脂等 应用:
塑料薄膜、网材、带包覆层的产品、截面一定、 长度连续的管材、板材、片材、棒材、打包带、 单丝和异型材等等,还可用于粉末造粒、染色、 树脂掺和等。
面灰暗无光泽等。
努力方向是尽可能减少或消除这种波动和温差。
产生这种波动和温差的原因:
如加热冷却系统不稳定,螺杆转数的变化等, 但 以螺杆设计的好坏影响最大。
普通三段螺杆存在的问题
1.熔融效率低 熔融段熔体与固体床共同存在于一个螺槽中,减
小了料筒壁与固体床的接触面积;固体床随着熔融 解体,部分碎片进入熔体中,很难从剪切获得热量, 这样,固体床不能彻底熔融;另外,已熔物料与料 筒壁接触,从料筒壁和熔膜处获取热量,温度继续 升高过热。 2.压力、温度和产量波动大
的物料量或塑件长度。它表示挤出能力的高低。 4.牵引速度
牵引速度与挤出速度相当,可略大于挤出速度。 牵引— 比— 牵引速度与挤出速度的比值,其值 等于或大于1。
§6.3 挤出管材成型工艺
一、挤出管材工艺控制要点
1.温度的控制
挤出成型温度是促使成型物料塑化和塑料熔体流动的 必要条件。对物料的塑化及制品的质量和产量有着十分 重要的影响。
分离型(屏障型)螺杆
原理:在螺杆熔融段再附加一条螺纹,将原来一 个螺纹所形成的螺槽分为两个,将已熔物料和未 熔物料尽早分离,促进未熔料尽快熔融。
销钉型螺杆 物料流经过销钉时,销钉将固体料或未彻底熔 融的料分成许多细小料流,这些料流在两排销钉 间较宽位置又汇合,经过多次汇合分离,物料塑 化质量得以提高。
料筒外部加热器提供的热量。
《高分子成型加工》第六章1-挤出成型
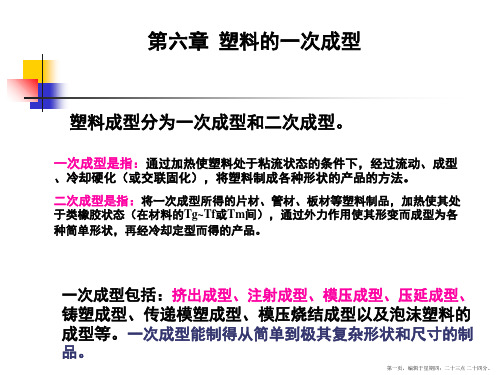
6.2.1 螺杆挤出机
由于塑料品种很多、性质各异,因此为适应加工不 同塑料的需要,螺杆的种类很多,结构上也有差异 ,以便能对塑料产生较大的输送、挤压、混合和塑 化作用。
表示螺杆结构特征的基本参数有:直径、长径比
、压缩比、螺距、螺槽深度、螺旋角、螺杆与料筒的 间隙等。
第十八页,编辑于星期四:二十三点 二十四分。
6.2.1 螺杆挤出机
② 长径比(L/D)
螺杆工作部分有效长度与直径之比。
通常为18~25。
L/D大,能改善物料温度分布,有利于塑料的混合和 塑化,并能减少漏流和逆流,提高挤出机的生产能 力。 L/D大,螺杆适应能力强,能用于多种塑料的挤出。
第十九页,编辑于星期四:二十三点 二十四分。
(3)螺杆是圆柱形还是锥形;
(4)压缩比的实现是靠:螺纹高度或导程; 根径由小变大或外
径由大变小; 螺纹头数变化。
(5)螺杆是整体的还是组合的。
第四十页,编辑于星期四:二十三点 二十四分。
6.2.1 螺杆挤出机
螺杆类型: (1)Colombo螺杆: 螺杆分为三段,每一段有一混合室。 加料段的外径和螺距最大;
压缩段次之;
均化段为最小。
同一段中,螺杆是等径等距的。
第四十一页,编辑于星期四:二十三点 二十四 分。
6.2.1 螺杆挤出机 (2)锥形双螺杆
向外反向转动。
从加料段到计量段,螺杆的外径和根径均匀地由 大到小变化。 螺杆各部分的长度、螺纹头数、螺槽数、螺棱 宽度、螺棱形状等均有变化。
第四十二页,编辑于星期四:二十三点 二十四 分。
6.2.1 螺杆挤出机
5.机头和口模
机头的作用是将处于旋转运动的塑料熔体转变为 平行直线运动,使塑料进一步塑化均匀,并将熔 体均匀而平稳地导入口模,赋予必要的成型压力 ,使塑料易于成型和取得制品密实度。
第六章 高分子材料挤出成型
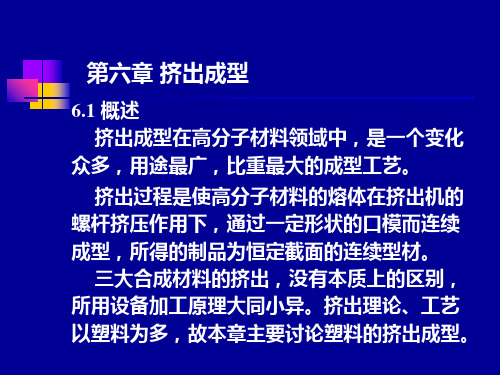
在满足强度的条件下,结构应紧凑。
辅助设备
辅助装备
原料输送干燥 定型冷却 牵引装置 切割装置 其它辅助装备
第二节 挤出成型原理
热塑性塑料在挤出过程中的变化:
熔体输送理论
均化段物料是均一的粘流状态,它关系到挤出 产量和质量,对该段主要研究物料的流动—是一 种拖曳流动。
均化段螺槽:图8-17。 螺杆旋转时,由于推挤作用,塑料沿Z方向移 动,但由于机头回压,塑料又有反压流动,使均 化段料流复杂,一般认为,物料在均化段有四种 流动:正流、逆流、横流、漏流,挤出流量是这 四种流动的总和。
螺槽深度(H)
影响塑料的塑化及挤出效率。H小,产生的 剪切速率大,塑化效果好,但生产率低。
H1一般是一个定值, H1 >0.1Ds; H2是一 个变化的值; H3=01.40.712~0.06 Ds,Ds较小者取大 值,反之,取小值。 螺旋角( )
螺旋角大,出料快,生产率高,但停留时间 短,塑化效果差。当螺杆在Ls=Ds时,最容易加
几种新型螺杆
屏障型螺杆 屏障型螺杆就是在螺杆的某部位设置屏障段,
使未熔的固态物料不能通过,并促使固态物料 熔融的一种螺杆。
通常情况下,屏障段设在均化段与压缩相交 处。
几种新型螺杆
分流型螺杆 螺杆的某一部分设置许多突起部分、沟槽或
孔道,将螺槽内的料流分割,以改变物料的流 动状态,熔融状态,增强混炼和均化作用。
两组曲线的交战是 操作点。
利用这种图,可以 求出指定挤出机,配 合不同的机头口模时 的挤出量。
○ 挤出流率的影响因素
高分子材料成型设备第六章挤出机料筒等6
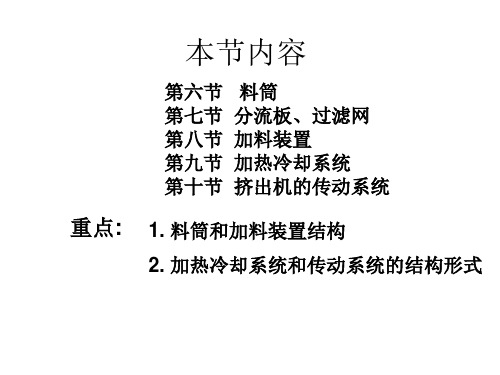
传动系统的设计
• 2、挤出机的工作特性 • 所谓挤出机的工作特性,是指螺杆的转速和驱动 功率与扭矩之间的关系。 • 工作特性分两种: 恒功率特性和恒扭矩特性。 • 挤出机的工作特性是恒扭矩特性。即:随螺杆转 速的增加,而其扭矩基本保持不变。 • 因此,为适应挤出机的这种特性,传动系统设计 时,应尽可能符合挤出机的这种工作特性。
滤胶:K=3.65×10-3 带旁压辊的挤出机,功率增加10% • 冷喂料:N=D3×L/D×N×K×10-5 KW K—系数,一般取5.52-6.73
• 3)类比统计法
对照国内外已有的相近规格的机台所使用的功率来 确定所设计的挤出机的功率。
传动系统的设计
• • 4、确定转速范围 根据挤出的工艺要求,螺杆转速在一定范围内应 可调,并且尽可能实现无级调速。 • 对于大多数挤出机来说,其调速范围在1-10之间。 橡胶挤出机多在1-3之间,塑料挤出机要求的范 围要大一些。
传动系统的设计
• 5、选择调速方式
• 1)调速方式的选择,应考虑以下几个方面:
a、其工作特性是否符合挤出机的恒扭矩工作特性
b、是否满足调速范围
c、是否有足够的传动功率 d、制造成本是否合适——经济性要求。 • 2)常用的调速方式 a、齿轮箱有级调速
多用于普通的橡胶热喂料挤出机,成本低。
传动系统的设计
N总=KN=9.81×10-5Nη千瓦 • 其中: N总—挤出机的驱动功率 N—螺杆挤出段(均化段)的功率消耗(可由熔体输 送理论的有关公式计算) K—系数,随物料不同而异 η—有效系数,由经验确定,一般取2-2.5
传动系统的设计
• 2)经验公式 • 热喂料 N=KD2n
K—由实际测定的常数,压型:K=2.95×10-3
- 1、下载文档前请自行甄别文档内容的完整性,平台不提供额外的编辑、内容补充、找答案等附加服务。
- 2、"仅部分预览"的文档,不可在线预览部分如存在完整性等问题,可反馈申请退款(可完整预览的文档不适用该条件!)。
- 3、如文档侵犯您的权益,请联系客服反馈,我们会尽快为您处理(人工客服工作时间:9:00-18:30)。
(1)吹膜辅机
1、薄膜吹塑法的分类及组成
①薄膜上吹法Flash ②薄膜下吹法Flash ③薄膜平吹法Flash 2、吹胀比及牵伸比 是选择模头口模尺寸的依据,根据吹胀比和牵引比计算
p ①吹胀比 D
2W W 0.64 D D
P-吹胀后膜管的直径 D-环形口模的直径 w-膜折径 口模直径 芯模直径 ②牵伸比
6、收卷装置
表面卷取 中心卷取
(2)、挤管机组
1、管材挤出过程及设备
①挤出过程 挤硬管Flash 挤软管 挤波纹管 挤管示频 挤出→冷却定型→冷却→牵引→切割→堆放 ②挤管机组:包括主机、机头、定型装置、冷却装置、牵引装 置、切割装置和堆放装置
2、定型装置
①外定径:是靠管子外壁与定径套内壁相接触来进行管材外径 定型冷却的 内压充气示意图Flash 加大型真空定径箱
D 0.64
v牵 v挤
W
d D 2t
v挤 Q Dt v牵
口模间隙
t
Q 2W
---膜的米重
2W Dt
2W D t
注意: ①吹胀比和牵引比对膜的强度、宽度和厚度的影响; ②牵引比对冷却速度的影响; ③冷却速度对产量的影响; ④冷却速度对透明性的影响。
2、阶梯挤出机
主要用于大 流量挤出和 排气。第一 级主要是送 料和塑炼, 螺杆大螺槽 深;第二级 主要是均化 挤出,转速 高。
3、立式挤出机 4、螺杆的改进 5、控制上的改进
作业:P178: 第 10 题:橡胶、塑料及纺丝挤出联 动线各包括哪些主要设备?各自的职能是什么?
Go to chapter7
2、压力控制
压力测试:液压式测压表,电气式测压表 压力调节:径向调节,轴向调节
3、安全保护:电流过载保护和扭矩过载保护
主机机械保护装置(安全销) 传动箱润滑系统报警、自动停机系统 机头熔体压力超压报警、自动停机系统 主电动机和主电动机冷却风机、油泵电机顺序联锁保护系统 主电动机和喂料电动机联锁保护系统
第十四节 挤出辅机(挤出联动线) 及新产品介绍
一、挤出成型辅机的种类与组成 挤出联动线是指与挤出机配套联合生产某一特定产 品的附属装置,称为联动线。也称为机组。根据不同的 产品有不同的联动线。 1、分类 (一)塑料挤出联动线 ①挤管机组;②挤板机组;③挤膜机组;④吹塑膜 机组;⑤吹塑中空制品机组;⑥涂层机组;⑦电线电缆 包层机组;⑧拉丝机组;⑨薄膜双轴拉伸机组;⑩造粒 机组。
(四)新品介绍 1、新产品 ① BOPP、BOPET双向拉伸膜联动线
双向拉伸聚酯薄膜(BOPET) 双向拉伸聚丙烯薄膜(BOPP)
②复合膜(多功能膜)
④管:波纹管
挤波纹管Flash
⑤丝:单丝、扁丝挤丝Flash ⑥板:发泡板、波浪板
第十五节 挤出机的发展
1、行星齿轮挤出机: 塑化快,易于粉料加工
塑料挤出机组的组成
• • • • • • • • • • • 用来完成挤出成型的后续加工,如定型、冷却、切割、收卷等。随 产品的不同有不同,其组成有所区别。主要由以下几大部分组成: 机头:(模头)作用:成型制品形状。 定型装置:固定、精整成型后的制品。 冷却装置:使成型后的制品充分冷却。 牵引装置:引出成型后的制品离开模头,并送至下步工序。 切割装置:将挤出的连续体硬制品按一定规格要求载切成段。 卷取装置:将连续体软制品收成卷,以便储运和使用。 堆放装置:将一定规格的硬制品堆放整齐,便于储运。 拉伸装置:将挤出物拉长,提高其强度。 其它装置:如测宽、测厚、计长、电晕等 教材P172-173画出了十一种塑料产品的挤出联动线
GC t1 t 2 E L KD外 t m KD外 t m
水进出口平均温差; G i △i-----管坯热焓
根据冷却时间设计:
• 以管坯壁厚中心层达到软化点温度为基准 所需冷却时间:
2 4t m t w T 2 ln k t s t w
(二)橡胶挤出压延机组
即用于生产橡胶产品或半成品的机组。由于橡 胶产品的多样性,有多种多样的机组。主要也是挤出 辅机和压延辅机。大体上主要由压片装置、输送装 置;称量装置;裁切装置;冷却装置;干燥装置;打 毛装置;粘接、贴合装置;蓄料装置;硫化装置、牵 引装置等等。书中P171介绍了橡胶胎面挤出联动线, 它主要由12种装置组成 (三)纺丝联合机组 由挤出机和喷丝头、计量加压泵、加热、冷却装置、纺 丝甬道、上油装置长度计算,原则是使管坯离开 套时管壁的硬化程度达到能自撑,不至变形或 破裂。 G---管坯质量; • 有经验法和热平衡设计计算法 Cp---管坯比热容; t1---管坯进套温度; 热平衡设计法: t2---管坯出套温度; 传热面积F=LπD外 则套长L=F/πD外 E---管坯潜热; F=Q/KΔtm Q=G△i K---总传热系数; △i=Cp (t1-t2)+E 故: Δtm----管坯与冷却
本节内容
第十三节 挤出机的控制 第十四节 挤出辅机(挤出联动线)及新产品介绍 第十五节 挤出机的发展
重点:
1.挤出联动线的类型及组成 2.挤管定径套的设计
第十三节 挤出机的控制
1、温度控制
温度控制原理:测量 调节操作 目标控制 温度的测量:热电偶,测温电阻,热敏电阻(使测温装 置直接和物料接触) 温度调节:位式调节器, 时间比例控制器 电脑控制
(二)橡胶生产联动线
即用于生产橡胶产品或半成品的挤出机组。 由于挤出产品的多样性,有多种多样的机组,比 塑料机组复杂,大体上主要由输送装置;称量装 置;裁切装置;冷却装置;干燥装置;打毛装 置;粘接、贴合装置;蓄料装置;硫化装置、压 片装置等等。书中P171介绍了橡胶胎面挤出联动 线,它是主要由12种装置组成。
再根据牵引速度求长度L:
Tv L 60
k---热扩散系数;ts ---软化点温度;tw ---冷却水温; tm ---管坯温度;v----牵引速度 定径套的内径:D= D外+S
S---塑料的收缩率
(3)、挤板辅机
1、挤板过程及机组组成 挤板Flash ①挤板过程 ②挤板机组的组成:挤出机、挤板(狭缝)机头、三棍压光机、 导辊、切边装置、牵引装置、切割装置和堆放装置 2、挤板辅机的主要部件 ①三辊压光机:压光机头送来的板坯、对板坯实施冷却、可调整 板材多点速度,以保证板材的平直,起到一定的牵引作用 ②牵引装置:由一个主动钢辊(在下方)和外面包着橡胶的被动钢 辊组成 ③切割装置:切边,裁断 ④其它装置:冷却输送辊,自动测厚仪,自动卸(板)料装置
3、冷却定型装置
要求: ①要有与挤出机生产能力相适应的冷却效率,使薄膜充 分冷却,避 免薄膜在牵引和卷曲过程中产生粘连和打褶的现象; ②膜管稳定,能对薄膜厚度进行调整; ③为适应多种幅宽的薄膜的生产,其安装高度应能有一 定的调节范围; ④易于操作和调整,以保证薄膜的透明度、外观质量和 物理力学性能良好。
真空定径示意图FLASH
大型 定径套实物图
②内定径:是一种在具有很小锥度的芯棒延长轴 内通冷却水,靠芯棒延长轴的外径确定管材内 经的方法 内径定径示意图
3、冷却装置:①浸浴式冷却水槽 ②喷淋式冷却 水箱 4、牵引装置:①滚轮式牵引机构Flash ②履带式 牵引机构Flash 5、切割装置:电动圆盘锯切割装置,行星锯切 割装置
分类: ①风冷装置:普通风环;双风口减压风环;内外双面风 冷系统 ②水冷装置
4、人字板
作用:折叠膜泡成平面;稳定膜泡; 分类:导辊式;硬木夹板式;不锈钢夹板
5、牵引装置,分上牵引和下牵引。由一个衬胶辊
和一个钢辊加传动装置组成。作用是将膜片引离 模口并送至下步工序。上牵引不有夹紧膜泡使泡 内气体封闭在冷却定型段不漏出。