熟料硫碱比对水泥浆流变性的影响
碱对熟料强度的影响及碱含量的合理控制
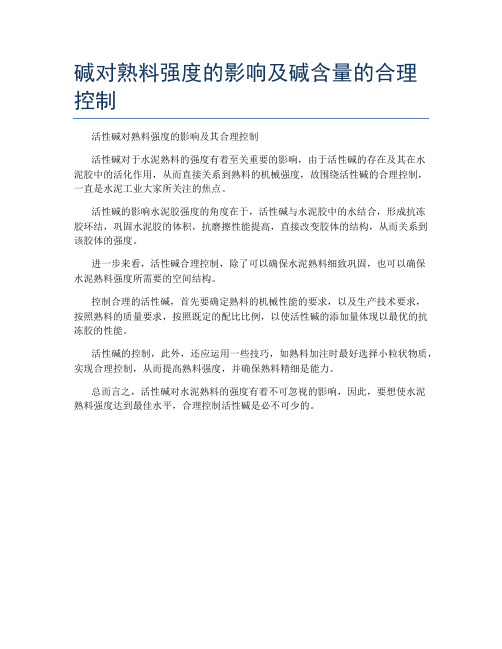
碱对熟料强度的影响及碱含量的合理控制
活性碱对熟料强度的影响及其合理控制
活性碱对于水泥熟料的强度有着至关重要的影响,由于活性碱的存在及其在水
泥胶中的活化作用,从而直接关系到熟料的机械强度,故围绕活性碱的合理控制,一直是水泥工业大家所关注的焦点。
活性碱的影响水泥胶强度的角度在于,活性碱与水泥胶中的水结合,形成抗冻
胶环结,巩固水泥胶的体积,抗磨擦性能提高,直接改变胶体的结构,从而关系到该胶体的强度。
进一步来看,活性碱合理控制,除了可以确保水泥熟料细致巩固,也可以确保
水泥熟料强度所需要的空间结构。
控制合理的活性碱,首先要确定熟料的机械性能的要求,以及生产技术要求,
按照熟料的质量要求,按照既定的配比比例,以使活性碱的添加量体现以最优的抗冻胶的性能。
活性碱的控制,此外,还应运用一些技巧,如熟料加注时最好选择小粒状物质,实现合理控制,从而提高熟料强度,并确保熟料精细是能力。
总而言之,活性碱对水泥熟料的强度有着不可忽视的影响,因此,要想使水泥
熟料强度达到最佳水平,合理控制活性碱是必不可少的。
预分解窑生产中碱对熟料质量的影响
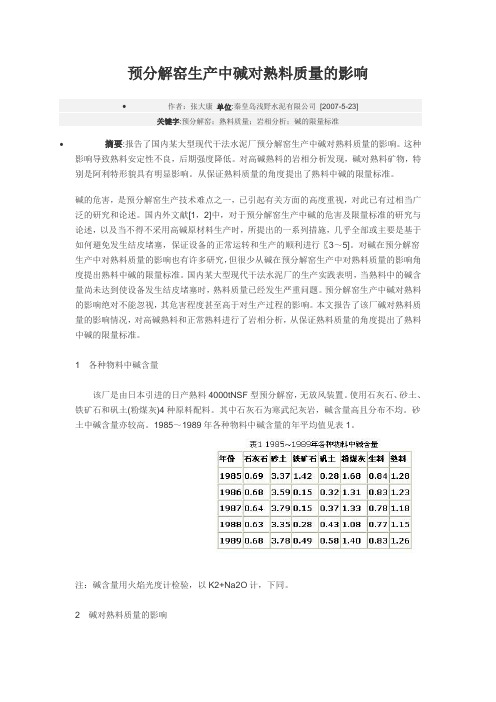
预分解窑生产中碱对熟料质量的影响∙作者:张大康单位:秦皇岛浅野水泥有限公司[2007-5-23]关键字:预分解窑;熟料质量;岩相分析;碱的限量标准∙摘要:报告了国内某大型现代干法水泥厂预分解窑生产中碱对熟料质量的影响。
这种影响导致熟料安定性不良,后期强度降低。
对高碱熟料的岩相分析发现,碱对熟料矿物,特别是阿利特形貌具有明显影响。
从保证熟料质量的角度提出了熟料中碱的限量标准。
碱的危害,是预分解窑生产技术难点之一,已引起有关方面的高度重视,对此已有过相当广泛的研究和论述。
国内外文献[1,2]中,对于预分解窑生产中碱的危害及限量标准的研究与论述,以及当不得不采用高碱原材料生产时,所提出的一系列措施,几乎全部或主要是基于如何避免发生结皮堵塞,保证设备的正常运转和生产的顺利进行〖3~5]。
对碱在预分解窑生产中对熟料质量的影响也有许多研究,但很少从碱在预分解窑生产中对熟料质量的影响角度提出熟料中碱的限量标准。
国内某大型现代干法水泥厂的生产实践表明,当熟料中的碱含量尚未达到使设备发生结皮堵塞时,熟料质量已经发生严重问题。
预分解窑生产中碱对熟料的影响绝对不能忽视,其危害程度甚至高于对生产过程的影响。
本文报告了该厂碱对熟料质量的影响情况,对高碱熟料和正常熟料进行了岩相分析,从保证熟料质量的角度提出了熟料中碱的限量标准。
1各种物料中碱含量该厂是由日本引进的日产熟料4000tNSF型预分解窑,无放风装置。
使用石灰石、砂土、铁矿石和矾土(粉煤灰)4种原料配料。
其中石灰石为寒武纪灰岩,碱含量高且分布不均。
砂土中碱含量亦较高。
1985~1989年各种物料中碱含量的年平均值见表1。
注:碱含量用火焰光度计检验,以K2+Na2O计,下同。
2碱对熟料质量的影响2.1碱对熟料安定性的影响该厂自投产以来,分别在1986年9月24日~10月3日、1988年7月21~24日及1989年4月21~25日熟料中碱含量偏高时,熟料安定性(煮沸安定性饼法,无特殊说明下同)试饼发生干缩裂纹、弯曲、崩溃。
碱对熟料煅烧和水泥性能的影响

( 摘 自中 国 建 材 数 字 报 网)
膜 法 富 氧 燃 烧 技 术 应 该 尽 快 普 及 应 用
据 了 解 , 富 氧 燃 烧 技 术 起 源 于 美 国 , 兴 起 在 德 国 , 发 展 在 日本 。 2 0世 纪 9 0年 代 , 日本 引 进 该 技 术 , 政 府 介 入 推 广 , 包 括 工 业 炉 窑 、 工 业 锅
制 氧 浓 度 只有 3 0 % , 明 火 点 不 着 , 安 全 可 靠 , 所
以膜 法 制 氧 技 术 常 用 于 燃 烧 领 域 。
现 代 制 氧 方 式 分 3种 : 深 冷 法 制 氧 , 氧 浓 度
明 在 签 约 仪 式 上 说 , 作 为 百 年 企 业 的 华 新 水 泥 近
为 9 9 % ;变压 吸 附 法 制氧 ,氧 浓度 为 9 3 % ; 膜 法 制 氧 ,氧 浓 度 小 于 4 0 %。氧 浓度 大 干 9 3 % 的 气 体 称 为 全 氧 ,氧 浓 度 大 干 2 1 %、 小 于 4 0 % 的 气 体 称
窑 应采 取 旁路 放风 排 碱 。
( 2 ) 在 水 泥 中 掺 入 一 定 量 的 在 特 定 温 度 下 煅 烧 制 得 的氧 化镁 ( 菱苦土 ) , 氧 化 镁 水 化 时 产 生 体 积膨 胀 。煅 烧 温度 通 常 控制 在 9 0 0 ~ 9 5 0 ℃。
( 3 ) 在 水 泥 石 中形 成 高硫 型 水 化硫 铝 酸 钙 ( 钙 矾石 ) , 产 生 体 积 膨 胀 。 由 于 环 境 温 度 对 氧 化 钙 和
有 得 到 广 泛 的 应 用 。 目前 广 泛 使 用 的 是 以 钙 矾 石
为膨 胀 组分 的各 种膨 胀 水 泥 。
烧成过程中碱对熟料强度的影响及对策

40纳K2O时,K2O就会与C3S反应生成KC23S12,每增加0.1%的K2O就要消耗2.91%C3S,析出0.77%的CaO。
即使提高烧成温度,这部分CaO也不能再和KC23S12反应生成C3S[1]。
图1 熟料中四相矿物对强度的贡献**来源于葛洲坝检测中心提供数据根据以上的反应机理,和我们认知的总碱含量(表示为Na2O百分含量)对熟料强度的影响见图2。
图2 总碱含量对熟料强度的影响**来源于葛洲坝检测中心提供数据从图2可以看出,总碱含量(Na2O当量)的增中图分类号:TQ172.625.3 文献标识码:B 文章编号:1008-0473(2019)05-0040-04 DOI编码:10.16008/ki.1008-0473.2019.05.006烧成过程中碱对熟料强度的影响及对策朱精瑞 刘继斌 颜新传中国葛洲坝集团水泥有限公司,湖北 武汉 430000摘 要 根据熟料中碱、钾等对熟料28 d强度的影响机理,对四家公司各种原材特性与强度之间的相关性进行分析,并采取相关措施:采用平衡“硫碱比”、引入钢渣中的晶种,或者调整配料、改善煅烧等方法使熟料28 d强度得到小幅提升。
关键词 水泥窑 熟料 碱 钾 影响 强度 性能0 引言碱对熟料烧成过程的危害,曾是预分解窑生产技术的难点之一,国内外已有相当广泛的研究和论述。
在国内外文献中,对于预分解窑生产中碱的危害及限量标准的研究与论述,以及在不得不采用高碱原材料生产时所提出的一系列措施,主要偏重于如何避免发生结皮堵塞,保证设备的正常运转和生产的顺利进行。
对碱、结晶硅在预分解窑生产中对熟料质量的影响也有许多研究,但很少从碱在预分解窑生产中对熟料质量强度和煅烧机理影响的角度分析。
多家国内外知名水泥生产企业统计数据和生产实践表明,当熟料中的碱含量尚未达到使设备发生结皮堵塞时,熟料质量已经发生严重问题。
预分解窑生产中碱对熟料的影响绝对不能忽视,其关系到熟料的强度。
关于硫对硅酸盐水泥熟料烧成过程的影响规律研究

关于硫对硅酸盐水泥熟料烧成过程的影响规律研究摘要:水泥工业随着优质资源的不断减少,现阶段已经逐渐的朝着利用低质燃料的方向进行发展,但是因为如今水泥的生产工艺水平比较低,所以实际可以适应水泥生产的煤种范围还是比较狭窄,在我国多数新型干法水泥厂中,一般都使用低硫含量烟煤。
如果在水泥生产中可以应用高硫煤,这样和其他行业之间的竞争就可以得到缓解,本文论述现在水泥生产中高硫煤的研究现状,并探在硅酸盐水泥熟料烧制中硫的影响。
关键词:硅酸盐;高硫煤;熟料烧制引言:在人类社会的发展过程中,资源和人口以及环境是一直都是需要面对的难题,现今广大的科技人员和各国政府,都十分关注实际社会的可持续发展问题,同时,材料生产和环境的协调性之间的研究,直接影响着社会的可持续发展。
一、在水泥生产中高硫煤应用研究的现状最早使用煤粉当做燃料的设备就是水泥窑,这个时候也是研究煤的起步阶段,最近这些年来,为了更好的去利用廉价的燃料,并将水泥的成本降低,使环境得到保护,我们国家的水泥研究者和生产者已经相继开展了很多研究工作。
在我们国家,很早就已经有了水泥立窑生产中利用高硫煤的相关报道,但是在实际立窑的时候,利用高硫煤作为主要燃料,十分容易出现结大块或挂边结窑的情况,而且在很多熟料这中的很高,强度不断下降,最终水泥十分容易出现快凝等问题。
所以很多立窑厂烧制水泥的时候,并不敢自己单独去利用高硫煤,一般为了降低成本都会就地取材,或者使用一些比较劣质的高硫煤,但是针对这样的方法来说,预期效果只能在预均化条件比较好的情况下达到,如果预均化条件并不是十分好的时候,使用优劣搭配这样的方法会导致配热出现不稳定的情况,尤其配料的难度比较大,实际进行立窑煅烧的时候操作起来也十分困难,最终导致熟料质量存在较大波动的情况。
在水泥熟料实际烧制的时候,高硫煤有着很好的降温和加速阿利特形成的作用,同时在控制不当的时候,也会出现结皮堵塞等情况。
最近这些年来,水泥的生产方法在不断的进行着演变。
l硫碱比-关于“硫碱比”问题的讨论

2关干"硫碱比"的适用范围硫碱比即新型干法窑入窑原、燃料中硫和碱的摩尔比:S/R-molS03/(molNazO十molKzO),本文采用文献「'l推荐的S/R=S03/(0.85K20+1·29NazO)计算式。
世界各大水泥公司提出的具体计算式与之大同小异,但取值各有不同,多在0.5-1.0之间,其理论依据为:控制合适的"硫碱比",使锻烧过程挥发在窑气中的硫、碱组份能尽量多的结合成硫酸盐,由于硫酸盐的沸点较高,二次挥发率低,随熟料排出窑外,从而避免在窑尾富集形成结皮。
文献[']指出:"具有决定意义的不是原、燃烧中硫碱的比率,而是存在于气氛中硫碱的比率。
对于烧煤,特别是烧高灰份煤的水泥窑,不但要考虑碱的挥发率,而且还耍看到挥发性碱在高温窑气中研发生的反应。
因此,国外水泥工作者根据其原料、配料率值以及烧油等条件下总结出来的硫碱比需要进行分析。
"我厂PC窑在S/R<0.4的情况下,因为SO3而发生堵塞就是一个例子。
我厂地处北方,原、燃料中的碱含量较高,硫含量较低,设计计算生料中的硫碱比仅为0.152,详见表1。
对于这种原、燃料,预分解窑能否正常运转。
我们在进行薄行性研究时,对条件类似的牡丹江、鹤岗、绥化三厂进行了调研,三厂生料的挥发性组份含量见表2。
表1 哈尔滨水泥厂PC窑物料中挥发性组分含量(%)表2 北方三厂生料中的挥发性组分含量(%)调研结果表明,三厂在生料中碱含量偏高,硫含量较低,在煤粉硫含量很低的条件下,都能较正常地运转。
因此我厂改造选用了预分懈窑,同时预留了必要时上放风系统的余地。
该窑1992年10月点火调试,到1993年4一6月出现了频繁的预热器堵寨现象。
查找原因发现在三风道喷嘴旋流风的螺旋体角度小、燃烧效率较低的情况下,生料中SO3含量偏高。
生料中SO3<0.16%时,运行基本正常;预热器经常塌料;SO2>0.25%时,就有堵塞的危险SO3>0.4时,很快就会堵塞。
含高氯硫碱对水泥生产的影响[2]
![含高氯硫碱对水泥生产的影响[2]](https://img.taocdn.com/s3/m/b905b10d90c69ec3d5bb75c5.png)
含高氯、硫、碱原料对水泥生产的影响L、M、Frang H、M、Kamel(埃及)—《水泥、石灰》1995.№6【摘要】本文以一条设计能力为4500t/d、分解炉燃料比为0.6的带预分解炉和三次风管的干法水泥窑为例,着重分析了含高氯、硫、碱的原料对干法水泥工艺生产操作及熟料质重的影响。
所用原料氯、硫、碱的平均含量分别为SO21.5%, K2 O 0.2%,Na2O 0.5%,Cl_ 0.4%,所用燃油含硫3%。
该窑旁路放风设计值为0.5或1.0,但为了避免硫和氯在预热器中沉积,窑操作时采用100%的旁路放风,这样既克服了硫和氯在预热器中的沉积问题,又有效地降低二次组分中70%的Cl,56%的K2O,40%的Na2O和27%的SO2 ;并使分解炉燃料比例达0.69,预分解率达0.9。
但将导致熟料中SO2含量过高(约24g/kg.熟料),窑中SO2挥发性特别低(0.24g/kg.熟料),可能是窑气中SO2分压较太,气体温度相对较低(980℃~1000℃)及窑尾过剩O2存在的缘故。
这一影响主要由生产过程中SO2输入量过高和单位窖气体量过小而致。
为减少熟料中的SO2含量,本文通过分折、研究,推荐使用无硫燃料。
同时在生料中掺加碳粉以增强对硫的分解能力。
l 前言生产水泥的主要原料中含有数量不等的二次组分如,氯、碱(钾和钠)和硫,且能或多或少地形成挥发性化合物,这些化合物在预分解干法生产过程中,随着温度的升高将有不同程度的蒸发(或分解),其产物将随窑气体进入预热器—分解炉系统凝结在悬浮的生料颗粒上或与之发生化学反应。
二次组分在窑和预热器—分解炉之间这种不断挥发和凝结将形成循环现象,在700℃~l00O℃之间循环盐大多处于熔融状态。
这种挥发性组分的强烈循环会给生产操作、热料质量和排放带来严重问题。
为缓解循环,窑内部分l0O0~ 12O0℃的高温气体不得不通过旁路排放。
影响熟料质量的主要成分是氯、碱、硫。
SO3含量既影响水泥强度又影响水泥的凝结性能。
水泥熟料中含碱量过高的影响与控制

International Conference,2006.37.
偏高岭土基土聚物水泥的制备及性能研究[J].
[8]
砖瓦,2017(5):36-39.
[6] 王鸿灵,李海红,冯治中等 . 偏高岭石基土聚水
泥的研究[J]. 硅酸盐通报,2005(2):113-116.
[7] Nair, Wright P N H, Ledger R O, et al. Investiga
Abstract: Because of the differences in varieties of limestone clinker of high alkali storage, post strength, weight
and other indicators of clinker quality has great influence. In this paper, through the use of high sulfur coal sulfur al⁃
尘器收集下来的粉尘一起重新入窑。这些挥发性微
量组分如此反复循环,由较低浓度富集至较高浓度,与
物料的粉尘一起构成熔融温度低的粘聚性物质,从而
造成结皮堵塞,并在熟料中富集较高含量的碱,对水泥
熟料的后期强度有较大的影响[2]. 高碱水泥游离钙增
加,煤耗高,后期强度低以及需水量高,当碱含量较高
时,K2O、Na2O 会与主要熟料矿物发生反应生成含碱矿
kali ratio balance in clinker quality improvement, the experimental results show that through the use of high sulfur
coal clinker water, strength and cement adaptability have been improved.
矿渣和熟料的比表面积及粉磨方式对水泥浆体流变性的影响

90
Marsh 时间/min
80 0
20
40
60
80 100
时间/min
图 1 熟料比表面积对水泥浆体流动度的影响
180 5 min
160 60 min
140 120 100
80
60
40
20
0 200 220 240 260 280 300 320 340 熟料比表面积(/ m·2 kg-1)
图 2 熟料比表面积对水泥浆体 Marsh 时间的影响
0 前言
水泥工作性能直接关系到水泥的销售和企业的 经济效益,并影响水泥企业乃至整个水泥与混凝土 行业的发展。水泥浆体的流变性是其工作性的一个 重要方面[1]。本文重点就矿渣和熟料的比表面积以 及水泥粉磨方式对浆体流变性的影响进行了研究; 同时又考察了水泥强度、凝结时间、标准稠度用水量 等指标。
1 试样的制备及实验方法
(1)
将表 4 中的粉磨时间代入(1)式,计算得到混合粉磨
时间为 23 min。据此将三种物料按表 4 质量配比进
行配料混合,粉磨 23 min 得到混合粉磨矿渣水泥样。
1.2 实验方法
(1)Marsh 筒法。按照文献[2,3]的规定进行,净
浆水灰比为 0.4,水泥用量为 4000g。用净浆搅拌机 搅拌 20min 后,再人工搅拌 20min,然后将净浆加入 Marsh 筒内,筒出口用玻璃板控制浆体的流出,抽玻
公司生产的 C80 型水化放热速率测试仪对不同水泥
试样进行 20h 水化放热速率测定,称取 1.50g 试样,水 灰比取 0.5,测试温度为 300℃。
2 实验结果及分析
2.1 熟料、矿渣比表面积对水泥浆体流变性的影响
2.1.1 熟料比表面积对矿渣水泥浆体流变性的影响
硫碱成分对水泥生产及质量有何影响

1、碱成分对水泥质量有什么危害?众所周知,碱不论以何种形式存在,都会对水泥生产与质量带来如下不利。
①使水泥快凝、早强,碱含量偏高时,可提高早期强度,但降低28天强度,易出现急凝、安定性不合格等现象。
②K2O、Na2O含量高的水泥易与碱活性骨料发生碱-骨料反应而造成混凝土破坏性膨胀,即俗称的“混凝土癌症”。
③过量的碱(K、Na)在生产中易造成窑内结圈、预热器及窑尾结皮堵塞,特别是影响窑后烟室的结皮。
2、硫成分在生料及煤中超量会对生产及质量有何不利?虽然以生料的灼烧基,或以熟料为基准,SO3仅占0.1%~2%,碱总量小于1%,但它们对窑的正常运转以及对水泥、混凝土质量的影响是不可忽视的。
①影响煅烧工艺的正常运行:过量的硫易引起窑内结圈。
为满足低碱规定,特别是生产低碱水泥,煅烧时会因SO3过量而阻止熟料中C3S的形成。
②不合理的硫碱比会影响熟料质量及易烧性。
③熟料中的SO3越高,在水泥磨中的易磨性越差,并限制了石膏的加入量,继而又影响水泥凝结时间。
④影响水泥及混凝土强度:SO3较高时,有利于增加28天强度;最佳的SO3量可使一天的砂浆强度最大化,对后期强度或在升高温度下的最大强度也有利。
对于细度越粗、C3A和碱含量越高的水泥,需要更多的SO3,有利于强度;含有减水剂的混凝土也需要更高的SO3。
⑤形成的硫化物会对设备装置腐蚀,特别是导致对烟气管道严重腐蚀。
3、硫的循环及硫碱比对生产的影响机理是什么?①来自燃料中硫的氧化及硫酸盐分解而成的硫化物主要形式是SO2,它们在窑内遇高温挥发,在预热器中降温后又凝集的过程就是硫在窑内的循环。
理论上,SO2低温下可氧化成SO3,但实际上99%的气态硫化物将是SO2,它们几乎都与预热器中的K2O、Na2O和CaO结合,并在烧成区再度挥发,又到窑尾和四、五级预热器形成硫循环结皮,不易挥发的碱性硫酸盐才存在于熟料中,这种循环最终将引发预热器结皮或堵塞出现。
②碱在熟料中的赋存状态取决于硫碱的摩尔比:SG=SO3/(1.292Na2O+0.85K2O)当SG<1时,除形成K2SO4和Na2SO4外,K2O还和C2S形成不规则圆形KC23S12颗粒及残留较多的f-CaO;Na2O和C3A形成暗色长条状NC8A3。
预分解窑生产中碱对熟料质量的影响2
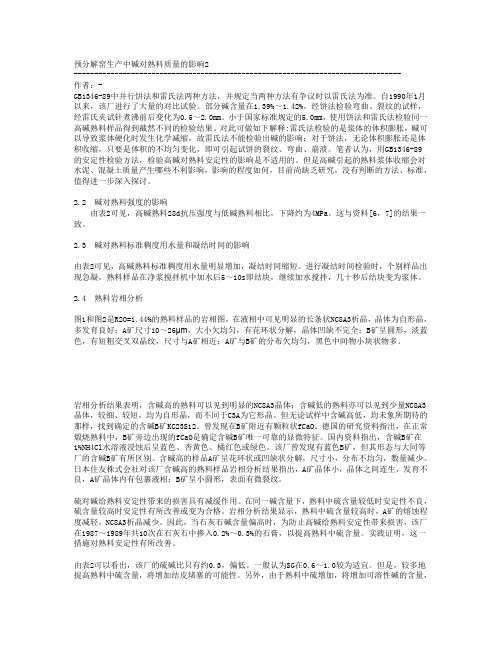
预分解窑生产中碱对熟料质量的影响2--------------------------------------------------------------------------------作者:-GB1346-89中并行饼法和雷氏法两种方法,并规定当两种方法有争议时以雷氏法为准。
自1990年1月以来,该厂进行了大量的对比试验。
部分碱含量在1.39%~1.42%,经饼法检验弯曲、裂纹的试样,经雷氏夹试针煮沸前后变化为0.5~2.0mm。
小于国家标准规定的5.0mm,使用饼法和雷氏法检验同一高碱熟料样品得到截然不同的检验结果。
对此可做如下解释:雷氏法检验的是浆体的体积膨胀,碱可以导致浆体硬化时发生化学减缩,故雷氏法不能检验出碱的影响;对于饼法,无论体积膨胀还是体积收缩,只要是体积的不均匀变化,即可引起试饼的裂纹、弯曲、崩溃。
笔者认为,用GB1346-89的安定性检验方法,检验高碱对熟料安定性的影响是不适用的。
但是高碱引起的熟料浆体收缩会对水泥、混凝土质量产生哪些不利影响,影响的程度如何,目前尚缺乏研究,没有判断的方法、标准,值得进一步深入探讨。
2.2 碱对熟料强度的影响由表2可见,高碱熟料28d抗压强度与低碱熟料相比,下降约为4MPa。
这与资料[6,7]的结果一致。
2.3 碱对熟料标准稠度用水量和凝结时间的影响由表2可见,高碱熟料标准稠度用水量明显增加,凝结时间缩短。
进行凝结时间检验时,个别样品出现急凝,熟料样品在净浆搅拌机中加水后5~10s即结块,继续加水搅拌,几十秒后结块变为浆体。
2.4 熟料岩相分析图1和图2是R2O=1.44%的熟料样品的岩相图,在液相中可见明显的长条状NC8A3析晶,晶体为自形晶,多发育良好;A矿尺寸10~26μm,大小欠均匀,有花环状分解,晶体凹缺不完全;B矿呈圆形,淡蓝色,有短粗交叉双晶纹,尺寸与A矿相近;A矿与B矿的分布欠均匀,黑色中间物小块状物多。
岩相分析结果表明,含碱高的熟料可以见到明显的NC8A3晶体;含碱低的熟料亦可以见到少量NC8A3晶体,较细、较短,均为自形晶,而不同于C3A为它形晶。
挥发性组分碱、氯、硫对熟料烧成的影响

挥发性组分碱,氯,硫对熟料煅烧的影响碱,氯,硫主要来源于原料和燃煤之中,它们在熟料的煅烧过程中表现为有利和不利的两个方面:一方面是微量的碱氯硫的存在可以降低最低共熔点温度,增加液相量,降低液相粘度,起助熔作用,促进C3S的形成。
另一方面是含量太高产生不利的影响,危害熟料质量。
1.挥发性组分的挥发凝聚循环(1).挥发凝聚循环。
碱氯硫化合物在熟料煅烧过程中,先后分解,气化和挥发,并随窑内气流由低温区窑尾系统逸散。
在温度降低到一定程度时挥发性组分中的一部分凝聚,聚集。
粘附于生料颗粒表面并随生料重又返回高温区,然后再度挥发凝聚,如此循环过程称作挥发凝聚循环。
在挥发凝聚循环中,随生料和燃料带入的碱氯硫所造成的凝聚循环称内循环。
随窑内气流及所含粉尘离开窑系统的挥发性组分,在利用窑尾废气余热烘干生料和煤粉的系统中,部分又凝聚于生料或煤粉中,收尘装置收集的粉尘也含有一部分挥发性组分,这些挥发性组分或混入生料中,或单独喂入窑内,这些就构成了挥发性组分的外循环。
(2).挥发凝聚循环的危害及防范措施。
危害主要是窑尾烟室,缩口,下料溜子及五级筒内壁结皮,堵塞,熟料结大块和窑内结圈。
防范措施主要是限制原燃材料中的碱氯硫含量.生料中K2O+Na2O小于1.0%,CL控制在0.015~0.020%.生料中SO3控制在0.4%~0.7%。
2.较高碱含量对熟料煅烧和质量的影响 (1)破坏熟料矿物C3S,C2S. C3A 的形成 (2)影响液相粘度。
(3)水泥结块,快凝。
(4)水泥制品性能变坏 。
碱(K2O,Na2O)使熟料液相粘度提高,因此常使煅烧温度提高,但碱的存在又使C3S和C3A等矿物水化加速,造成水泥凝结快,早强较高而28d强度却有所降低。
如果采用含硫煤或在高碱熟料煅烧过程中加入一定SO3,使之达到适宜的硫酸盐化程度,则可减轻碱的不良作用,但即使如此,熟料强度仍然是下降的。
碱和MgO对熟料性能的影响
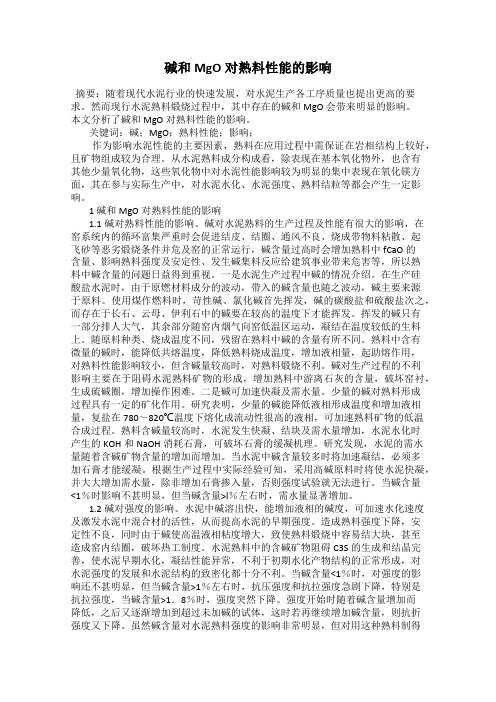
碱和MgO对熟料性能的影响摘要:随着现代水泥行业的快速发展,对水泥生产各工序质量也提出更高的要求。
然而现行水泥熟料煅烧过程中,其中存在的碱和MgO会带来明显的影响。
本文分析了碱和MgO对熟料性能的影响。
关键词:碱;MgO;熟料性能;影响;作为影响水泥性能的主要因素,熟料在应用过程中需保证在岩相结构上较好,且矿物组成较为合理。
从水泥熟料成分构成看,除表现在基本氧化物外,也含有其他少量氧化物,这些氧化物中对水泥性能影响较为明显的集中表现在氧化镁方面,其在参与实际生产中,对水泥水化、水泥强度、熟料结粒等都会产生一定影响。
1 碱和MgO对熟料性能的影响1.1碱对熟料性能的影响。
碱对水泥熟料的生产过程及性能有很大的影响,在窑系统内的循环富集严重时会促进结皮、结圈、通风不良、烧成带物料粘散、起飞砂等恶劣煅烧条件并危及窑的正常运行,碱含量过高时会增加熟料中fCaO的含量、影响熟料强度及安定性、发生碱集料反应给建筑事业带来危害等,所以熟料中碱含量的问题日益得到重视。
一是水泥生产过程中碱的情况介绍。
在生产硅酸盐水泥时,由于原燃材料成分的波动,带入的碱含量也随之波动,碱主要来源于原料。
使用煤作燃料时,苛性碱、氯化碱首先挥发,碱的碳酸盐和硫酸盐次之,而存在于长石、云母、伊利石中的碱要在较高的温度下才能挥发。
挥发的碱只有一部分排人大气,其余部分随窑内烟气向窑低温区运动,凝结在温度较低的生料上。
随原料种类、烧成温度不同,残留在熟料中碱的含量有所不同。
熟料中含有微量的碱时,能降低共熔温度,降低熟料烧成温度,增加液相量,起助熔作用,对熟料性能影响较小,但含碱量较高时,对熟料煅烧不利。
碱对生产过程的不利影响主要在于阻碍水泥熟料矿物的形成,增加熟料中游离石灰的含量,破坏窑衬,生成硫碱圈,增加操作困难。
二是碱可加速快凝及需水量。
少量的碱对熟料形成过程具有一定的矿化作用。
研究表明,少量的碱能降低液相形成温度和增加液相量,复盐在780~820℃温度下熔化成流动性很高的液相,可加速熟料矿物的低温合成过程。
熟料硫碱比对水泥浆流变性的影响

熟料硫碱比对水泥浆流变性的影响流变性能是水泥的重要性能,对混凝土的施工具有重大意义。
以往水泥企业往往只注重水泥的凝结时间和强度,但是对其流变性能则重视不够[1]。
随着建筑施工技术的不断发展,建筑业对水泥的流变性能提出了越来越高的要求。
预分解窑生产水泥,当原料中的碱含量过高时,经常出现水泥的需水量高和配制的混凝土坍落度经时损失过大的问题。
这种现象不但与熟料的碱含量有关,而且还与其硫碱比有关。
为此,我们就熟料的硫碱比与水泥浆体流变性能之间的关系问题进行了研究。
实验中,我们采用冀东水泥有限责任公司(以下简称冀东)的生料调配成不同硫碱比的生料进行煅烧,通过旋转粘度计、净浆流动度、净浆针入度等试验方法测定水泥浆的流变性能。
同时还收集到冀东的生产数据,进一步验证实验室的研究结果。
最后利用现代测试方法进行相关的机理分析探讨。
1 实验1.1 实验原料与试样配制1. 实验原料生料取自冀东,化学组成与率值如表1所示。
表1冀东生料的化学组成与率值化学组成(%)率值CaO SiO2Al2O3Fe2O3MgO K2O Na2O R2O Loss HM SM IM 43.8814.02 3.01 2.20 1.170.780.070.5834.30 2.28 2.70 1.372. 试样的配制用冀东生料、NaOH、KOH、二水石膏自行配制成不同硫碱比的生料,并用石灰石调整生料中氧化钙含量一致。
所配制生料的硫、碱组分如表2所示。
表2 自制生料中的硫、碱组分(%)试样Na2O K2O SO3R2O1 0.20 1.50 0.31 1.192 0.20 1.50 0.92 1.193 0.20 1.50 1.23 1.194 0.20 1.50 1.58 1.191.2 实验方法1. 熟料的煅烧将不同硫碱比生料,混合均匀,加8%的水,压制成Φ30mm×10mm的圆片,烘干后放在匣钵内,于预热到950℃的电炉中煅烧30min ,然后放入1450℃的电炉中再煅烧60min ,取出并立即用电风机吹冷。
碱对熟料煅烧过程和水泥水化过程的影响
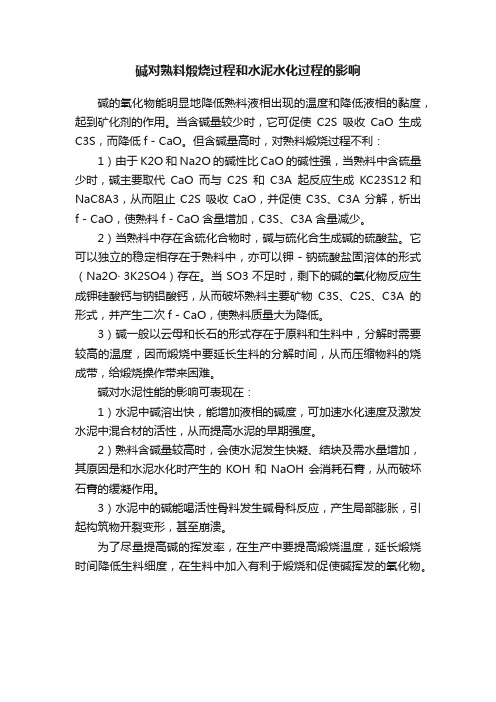
碱对熟料煅烧过程和水泥水化过程的影响
碱的氧化物能明显地降低熟料液相出现的温度和降低液相的黏度,起到矿化剂的作用。
当含碱量较少时,它可促使C2S吸收CaO生成C3S,而降低f - CaO。
但含碱量高时,对熟料煅烧过程不利:1)由于K2O和Na2O的碱性比CaO的碱性强,当熟料中含硫量少时,碱主要取代CaO而与C2S和C3A起反应生成KC23S12 和NaC8A3,从而阻止C2S吸收CaO,并促使C3S、C3A分解,析出f - CaO,使熟料f - CaO含量增加,C3S、C3A含量减少。
2)当熟料中存在含硫化合物时,碱与硫化合生成碱的硫酸盐。
它可以独立的稳定相存在于熟料中,亦可以钾 - 钠硫酸盐固溶体的形式(Na2O· 3K2SO4)存在。
当SO3不足时,剩下的碱的氧化物反应生成钾硅酸钙与钠铝酸钙,从而破坏熟料主要矿物C3S、C2S、C3A的形式,并产生二次f - CaO,使熟料质量大为降低。
3)碱一般以云母和长石的形式存在于原料和生料中,分解时需要较高的温度,因而煅烧中要延长生料的分解时间,从而压缩物料的烧成带,给煅烧操作带来困难。
碱对水泥性能的影响可表现在:
1)水泥中碱溶出快,能增加液相的碱度,可加速水化速度及激发水泥中混合材的活性,从而提高水泥的早期强度。
2)熟料含碱量较高时,会使水泥发生快凝、结块及需水量增加,其原因是和水泥水化时产生的KOH和NaOH会消耗石膏,从而破坏石膏的缓凝作用。
3)水泥中的碱能喝活性骨料发生碱骨科反应,产生局部膨胀,引起构筑物开裂变形,甚至崩溃。
为了尽量提高碱的挥发率,在生产中要提高煅烧温度,延长煅烧时间降低生料细度,在生料中加入有利于煅烧和促使碱挥发的氧化物。
硫对水泥熟料煅烧的影响(下)
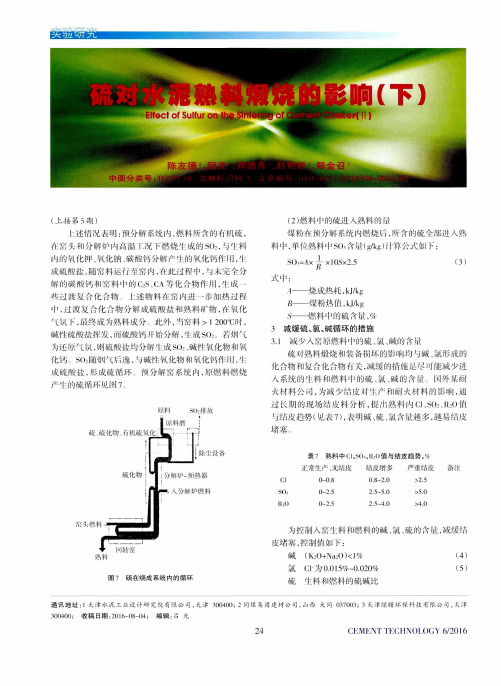
采取 决措 施 ( 8 )
堵怅 J . 必须 合 怵 t 分折结皮
} I } 仃 欠, 多的 ’ j 硫、 瞅 『 氽、
I I T J ' ( 常l L { J 现 系统 心 水 进 行 分忻 ' Z : 】 l
_ j 寸 存时 的
埘 次 8
仃火
的 热物 料
| _ 0 I 蛇 ( K ! ( ) + a 0) <1 %
z
. 减 缓
( 4)
熟 图 7 硫在 烧 成 系 统 内 的循 环
熟 - ( . : 1 为0 . ( ) l 5 %~ 0 . 0 2 ( ) % 料f ¨ 燃 料 的硫 碱 比
( 5 Байду номын сангаас
硫
通讯 地址 : l天津 水 泥 工 业 设 计 研 究 院 有 限公 司 ( ) 4 ( ) ( ) ; 收 稿 日期 : 2 0 1 6 - 0 8 — 0 4; 编辑 : 吕 光
【 ) I X音 ×l O S x 2 . 5
,J
( 3)
』 f i l :
1 — — 烧 成热 耗 , k J / k g
— —
【 l l , 过渡 介 化合物 分晰成硫酸盐和熟料矿物 , 存 化
— —
煤粉热 f I f f = , k J / k g
燃 料・ I 的 硫 , %
Z
4
勿
f
I
l
L
( 上接 第 5 期)
( 2 ) 燃料 t f I 佝硫进 入 I 粒 I . 的 艟 粉( i i @ i 分解 系统 I J 、 】 燃烧 后 . 昕 的 硫 全 进 入热 料r 『 l f ’ 熟 料r 1 - ) 含 g / k g ) 汁钟 : 公 『 』 【 1 下:
关于硫碱比问题

关于“硫碱比”问题
从悬浮预热及预分解窑诞生以来,由于窑气中挥发性组份能绝大部分冷凝在悬浮物料上形成闭路循环,对生产过程和熟料质量有较大的危害,因此引起了世界范围的关注,其中,对碱和硫的允许含量及其之间的比例也作了大量的研究,并明确地提出了"硫碱比"的概念。
关干"硫碱比"的适用范围
硫碱比即新型干法窑入窑原、燃料中硫和碱的摩尔比:S/R-molS03/(molNazO十molKz O),本文采用文献「'l推荐的S/R=S03/(0.85K20+1·29NazO)计算式。
世界各大水泥公司提出的具体计算式与之大同小异,但取值各有不同,多在0.5-1.0之间,其理论依据为:控制合适的"硫碱比",使锻烧过程挥发在窑气中的硫、碱组份能尽量多的结合成硫酸盐,由于硫酸盐的沸点较高,二次挥发率低,随熟料排出窑外,从而避免在窑尾富集形成结皮。
文献[']指出:"具有决定意义的不是原、燃烧中硫碱的比率,而是存在于气氛中硫碱的比率。
对于烧煤,特别是烧高灰份煤的水泥窑,不但要考虑碱的挥发率,而且还耍看到挥发性碱在高温窑气中研发生的反应。
因此,国外水泥工作者根据其原料、配料率值以及烧油等条件下总结出来的硫碱比需要进行分析。
"。
矿渣和熟料的比表面积及粉磨方式对水泥浆体流变性的影响

Ab ta t h h oo ia r p r f e n t i e e t p cf r a n rn ig meh d fci k ro lg i tse y c me t s r c :T e r e l ge l o e t o me t h d f r n e i c a e sa d g i d n t o s o l e rsa s e td b e n p y c wi f s i n p se f i i n rh c n x e i n s I i u d t a p cf r a o l k ro l g a d t e r e lg c l r p r r n n g t e a t l d t a d Ma s o e e p rme t. t sf n h ts e i c a e f i e rsa n h h oo i a p o e t a e i e a i u y o i cn y v c rea in a dt e i f e c f l k r Ss e i cs ra ea e c r ae ; h t h o o rl t , n h l n eo i e ’ p cf u f c r a i mu h g e tr t a ec mmo r d n t o s et r An hev — o n u cn i s t n g i i g me h d i b t n e d t e
表 2 熟料 的矿 物 组成 与 率值
0 前 言
水泥工 作性 能直 接关 系 到水 泥的销 售 和企业 的
经济 效 益 , 并影 响 水 泥企 业 乃 至整 个 水 泥 与混 凝 土