轻量化材料的选材
汽车车身结构的轻量化材料研究

汽车车身结构的轻量化材料研究随着环保理念的推广和汽车制造技术的不断发展,轻量化成为了汽车行业的重要发展方向。
汽车车身结构作为汽车重要的组成部分,其轻量化研究具有重要的意义。
本文将从轻量化材料的研究和车身结构的设计两个方面来探讨汽车车身结构的轻量化材料研究。
一、轻量化材料的研究1. 铝合金铝合金是一种重要的轻量化材料,在汽车制造中有广泛的应用。
由于铝合金的密度相对较小,因此可以在不影响安全性能的前提下减轻车身重量。
另外,铝合金具有良好的强度和刚性,可以提高汽车的整体刚度,提升操控性能。
目前,许多汽车制造商都在应用铝合金材料来制造车身。
2. 高强度钢钢材是传统汽车制造中常用的材料,但传统的钢材密度较大,不利于轻量化。
为了满足轻量化的需求,研究人员开发了高强度钢材。
高强度钢材在保证强度和刚性的同时,相对密度较小,能够有效地减轻汽车车身的重量。
高强度钢材具有良好的成形性,可以满足车身多样化的设计需求。
3. 碳纤维复合材料碳纤维复合材料是目前汽车轻量化材料研究中的热点。
碳纤维具有重量轻、强度高、刚性好等特点,可以满足汽车制造中对材料强度和刚性的要求。
利用碳纤维复合材料可以实现汽车车身的重量减轻,并且具有良好的耐久性和抗腐蚀性能。
然而,碳纤维复合材料的成本较高,目前仍处于研究和应用初期。
二、车身结构的设计1. 结构优化为了实现汽车车身的轻量化,需要进行结构优化设计。
通过对车身结构进行仿真分析和优化设计,可以最大程度地减少材料的使用量,提高车身的结构强度和刚性。
结构优化设计的关键是在不影响安全性能的前提下,尽可能减轻车身的重量,提高车辆的燃油经济性。
2. 多材料组合将不同的材料进行合理的组合,可以实现汽车车身的轻量化。
通过在合适的位置选择合适的材料,可以兼顾安全性和轻量化的需求。
例如,在车身的关键结构部位使用高强度钢材料,而在非关键结构部位使用轻量化材料,可以最大限度地实现车身的轻量化。
3. 全车轻量化设计汽车的轻量化不仅仅局限于车身部分,还需要在整车层面进行综合考虑。
装配式建筑施工中的轻量化设计与材料选择

装配式建筑施工中的轻量化设计与材料选择轻量化是当今建筑行业追求的一个重要方向,装配式建筑施工中的轻量化设计与材料选择对建筑的质量、成本和环境影响具有重要意义。
在这篇文章中,我们将探讨轻量化设计与材料选择在装配式建筑施工中的应用及其优势。
一. 装配式建筑施工中的轻量化设计装配式建筑施工是一种先进的现代施工方式,通过在制造厂进行组装,然后运输到现场扩展使用。
轻量化设计是为了满足装配式建筑施工这一特殊流程所需,旨在提高建筑构件的生产效率和安装速度。
1. 材料选用为了实现轻量化设计,在装配式建筑施工中选择合适的材料非常重要。
首先,应考虑采用轻型材料替代传统砖石和混凝土等重型材料。
例如,可使用薄壁钢结构、轻质混凝土或复合板材等。
其次,还可以使用聚合物材料替代传统绝缘材料,以减少构件自身的重量。
2. 结构设计轻量化设计还需要考虑建筑结构的优化。
例如,可以采用薄壁钢结构来替代传统的混凝土框架,从而减轻建筑自身重量并提高承载能力。
此外,还可以利用空心结构和网壳结构等创新设计,有效减少自重。
3. 节能设计轻量化设计也与节能要求密切相关。
装配式建筑通常具有较好的隔热性能和气密性,因此在施工过程中采用合适的材料和技术来实现节能效果非常重要。
例如,在墙体、屋顶和地板等部位使用保温材料,并加强边缘密封以防止冷热桥效应。
二. 装配式建筑施工中轻量化设计与材料选择的优势1. 提高生产效率装配式建筑施工中的轻量化设计使得构件更加轻便,并且早期进行预制,这大大提高了生产效率。
通过在制造厂进行组装,可以减少现场施工时间,并确保质量控制。
2. 减少施工成本轻量化设计降低了施工成本。
首先,使用轻型材料减少了材料成本。
其次,装配式建筑施工减少了现场施工时间,节约了劳动力成本和机械设备租赁成本。
此外,由于轻量化设计降低了施工过程中对重型机械的需求,还能够节省运输成本。
3. 节约资源装配式建筑施工中的轻量化设计有助于节约资源。
首先,通过使用更轻便的材料减少了对原材料的需求。
汽车轻量化设计与材料选择

汽车轻量化设计与材料选择随着环境保护和能源危机的日益严重,汽车轻量化已经成为了全球汽车工业发展的趋势。
轻量化设计可以减少汽车的整体质量,降低燃料消耗和排放,提高车辆的性能和安全性。
本文将探讨汽车轻量化的设计原则和常用的材料选择方法,旨在为汽车工程师和制造商提供一些有用的参考。
一、汽车轻量化设计原则1. 结构优化:通过优化汽车的结构设计,可以实现对重要部位和关键连接的强化,减少车身重量并提高整体刚性。
结构优化的方法包括有限元分析、疲劳试验、原型制造和模拟仿真等。
2. 部件集成:将不同功能的部件进行集成,可以减少重复的结构和材料,提高汽车的空间利用率和运动效率。
部件集成可以通过设计共享平台、模块化设计和系统集成等方法来实现。
3. 材料优化:选择合适的材料可以在保证安全性和性能的前提下减轻汽车的重量。
常见的轻量化材料包括高强度钢、铝合金、镁合金、碳纤维复合材料等。
不同材料的优缺点需要结合实际需求进行综合评估。
4. 智能设计:引入智能化技术可以提高车辆的轻量化设计效果,如使用先进的CAD/CAM软件进行设计和优化、运用虚拟现实技术进行仿真和验证等。
二、汽车轻量化材料选择1. 高强度钢:高强度钢具有较高的强度和刚度,可以减少车身和车架的重量。
它能够有效吸收能量,在碰撞事故中提供良好的安全保护。
高强度钢的选择需要综合考虑强度、塑性、焊接性等因素。
2. 铝合金:铝合金具有较低的密度和良好的加工性能,适用于制造车身和发动机等部件。
铝合金的使用可以有效降低汽车的燃料消耗和排放。
3. 镁合金:镁合金是一种轻质高强度材料,具有良好的耐腐蚀性和可回收性。
它可以用于制造车身结构、发动机零部件和底盘等,有助于降低车辆的整体重量。
4. 碳纤维复合材料:碳纤维复合材料具有高强度、高模量和低密度的特点,广泛应用于汽车领域。
它可以用于制造车身、车架和零部件等,具有良好的刚性和抗冲击性能。
5. 塑料材料:塑料材料具有较低的密度和良好的成型性能,可以替代传统的金属材料。
轻量化汽车材料的研究与应用分析

轻量化汽车材料的研究与应用分析近年来,随着对环境污染和燃油消耗的关注,轻量化成为了汽车行业的研发重点。
通过使用轻量化材料,可以减轻汽车质量,降低油耗、减少尾气排放,提高车辆性能和使用寿命,为汽车行业的可持续发展贡献力量。
轻量化汽车材料主要包括高强度钢、铝合金、镁合金、碳纤维复合材料等。
这些材料相比传统材料具有重量轻、强度高、密度低等优点,被广泛应用于车身、底盘、发动机等方面。
下面就各种材料的研究和应用进行一一分析。
1. 高强度钢高强度钢是目前应用最广泛的轻量化材料之一,具有强度高、延展性好、重量轻等优点。
目前,高强度钢的种类众多,可以根据所需的强度和塑性来选择不同的材料。
高强度钢主要应用于车身结构中,通过使用高强度钢可以减轻车身重量,提升车身的刚性和安全性能。
2. 铝合金铝合金是另一种常用的轻量化材料,相比于钢材,铝合金的密度更低,重量更轻,强度也比较高。
铝合金具有良好的耐腐蚀性和导热性能,在汽车行业中被广泛应用于汽车车身的覆盖件、底盘、发动机以及轮毂等部件。
3. 镁合金镁合金是一种新型轻量化材料,在汽车行业中使用还比较少。
镁合金具有密度低、强度高、耐腐蚀性好等优点,可以大幅减轻车身重量。
同时,镁合金的熔点较低,容易加工,而且可进行循环利用。
目前,镁合金主要应用于汽车车身结构中。
4. 碳纤维复合材料碳纤维复合材料是一种高性能材料,具有强度高、耐腐蚀性好、重量轻等优点。
在汽车行业中,碳纤维复合材料主要应用于高端豪华车型及赛车型号的车身,通过使用这种材料可以提高车辆的性能和设计美感。
总的来说,轻量化材料在汽车行业中具有广泛应用前景,可以减轻车身重量,降低燃油消耗,提高车辆性能和安全性能。
同时,轻量化材料的研究和应用还存在许多挑战,如材料成本高、加工难度大等问题,需要进一步探索和解决。
相信随着技术的进步和研发经验的累积,轻量化材料必将成为汽车行业的一个重要发展方向。
轻量化玻璃钢和碳纤维

轻量化玻璃钢和碳纤维引言:随着科技的不断进步,轻量化材料在各个领域得到了广泛的应用。
轻量化材料的使用可以降低结构的重量,提高材料的强度和刚度,同时具有耐腐蚀和耐磨损等优点。
在轻量化材料中,玻璃钢和碳纤维是两种常见的材料。
本文将分别介绍玻璃钢和碳纤维的特点及其在各个领域的应用。
一、轻量化玻璃钢1. 特点:轻量化玻璃钢,又称玻璃纤维增强塑料,是由玻璃纤维和树脂组成的复合材料。
玻璃纤维具有高强度、低密度、耐腐蚀等优点,树脂具有耐化学腐蚀、耐高温等特性。
轻量化玻璃钢具有重量轻、强度高、热膨胀系数低、耐腐蚀、绝缘性能好等特点。
2. 应用领域:轻量化玻璃钢广泛应用于船舶、汽车、建筑、化工等领域。
在船舶领域,轻量化玻璃钢可以制造船身、甲板、船舱等部件,提高船舶的载重量和航行速度。
在汽车领域,轻量化玻璃钢可以制造车身、车顶、车门等部件,减轻车辆的整体重量,提高燃油经济性。
在建筑领域,轻量化玻璃钢可以制造外墙板、屋顶、管道等部件,增加建筑物的抗风能力和耐久性。
在化工领域,轻量化玻璃钢可以制造储罐、管道、风机叶片等部件,具有耐腐蚀、耐高温的特性,适用于各种腐蚀性介质的输送和处理。
二、碳纤维1. 特点:碳纤维是由碳元素组成的纤维材料,具有重量轻、强度高、刚度大、耐高温等特点。
碳纤维的比强度和比刚度远高于传统的金属材料,具有很好的抗拉强度和抗压强度,同时具有优异的耐腐蚀性和耐磨损性。
2. 应用领域:碳纤维广泛应用于航空航天、汽车、体育器材等领域。
在航空航天领域,碳纤维可以制造飞机机身、翼面、悬挂件等部件,减轻飞机的整体重量,提高飞行速度和燃油经济性。
在汽车领域,碳纤维可以制造车身、车顶、转向架等部件,提高车辆的性能和安全性。
在体育器材领域,碳纤维可以制造高尔夫球杆、自行车车架、网球拍等器材,减轻器材的重量,提高运动员的竞技水平。
结论:轻量化玻璃钢和碳纤维作为轻量化材料,在各个领域都有着广泛的应用。
它们具有重量轻、强度高、耐腐蚀和耐磨损等特点,可以提高结构的性能和耐久性。
轻量化材料的选材

轻量化材料的选材Via 常州精密钢管博客从对机械制造类产品的市场需求出发,定义了产品的功能目标与适用于产品寿命周期的边界条件。
在产品开发的规划阶段,引出了与要求、构造和材料相适应的目标函数。
借助“Ashby图”,可以从众多的材料选择项中预选出与性能要求相符合的材料。
在规划设计阶段,需要对相应材料效率的要求加以规范化,因为这些要求与用于轻量化的材料质量有关。
本节中,采用形状因子对改善使用性能的成形方法进行量化,性能指标的成本则通过价格指数加以关联。
借助自行车车架的例子,说明了按照基本要求和边界条件分步选择材料的方法。
借助用于内燃机的铸造合金适合度的评估示例,来说明用于重量组合的要求和边界条件,并进行相互比较。
为了对材料方案进行评估,还将得出的合金性能范围与在材料组中的加工消耗进行比较。
作为示例,还对可能用于一款面向市场的、大批量生产的高性能发动机的材料进行了比较和选择。
引言结构材料必须首先能够承受机械载荷,其次要满足其他的功能,如:导热或者热绝缘。
对材料的力学性能要求还有:刚度、动态强度和静态强度、减振、断裂韧度、抗磨损能力和抗蠕变能力。
材料可以如下分类:陶瓷、非晶形材料(玻璃)、金属、聚合物与复合材料(见2.1节)[1,2]。
轻量化所需要的材料要与结构相匹配,特别是要能够实现轻量化的目标。
图2-3-1展示了由不同材料制成的两个自行车车架:一个车架是1896年用竹管组装的[3],一个是100年后用碳纤维增强塑料加工而成的(CFK)[4]。
如今,大部分的自行车的梯形车架是用钢或者铝合金加工而成的。
为什么选择这些材料来制造车架?不同的材料之间有什么区别?如何选择合适的材料?本章节就是要回答这些问题。
图2-3-1自行车作为轻量化示例a)竹车架1896[3]b)碳纤维增强塑料车架2007[4]轻量化意味着将一个用于特定应用的构件体系的重量最小化。
一个运动构件越轻,构件用于运动改变所需要的能量就越少。
对于所有的产品来说,都要用市场可接受的成本来进行生产。
新能源汽车轻量化设计与材料选择

新能源汽车轻量化设计与材料选择随着环境保护和能源危机的日益突出,新能源汽车作为一种绿色、高效、可持续发展的交通工具受到了广泛关注。
而在新能源汽车的设计与制造过程中,轻量化是一个至关重要的问题。
本文将探讨新能源汽车轻量化设计的必要性,并介绍一些常用的轻量化材料选择。
一、背景新能源汽车市场发展迅速,但其发展过程中面临着一些挑战,如续航里程的限制、电池成本昂贵等。
而新能源汽车的轻量化设计可以有效解决这些挑战,提高续航里程、减少能源消耗、增加乘坐空间等。
二、轻量化设计的意义1. 提高续航里程:新能源汽车通常搭载大容量的电池,而电池的重量是限制续航里程的主要因素之一。
通过轻量化设计,可以减少车辆自重,降低电池的负担,从而提高续航里程。
2. 降低能源消耗:轻量化设计可以减少车辆的阻力,提高车辆的能源利用率。
例如,在车身结构设计中,采用轻质材料可以减少风阻,从而降低车辆在行驶中的能源消耗。
3. 增加乘坐空间:传统汽车中,大量的材料被用于增加车辆的结构强度,导致车厢空间有限。
而通过轻量化设计,可以减少车辆的自重,提高结构强度的同时增加乘坐空间。
三、轻量化材料的选择1. 轻质金属材料:铝合金是一种常用的轻质金属材料,具有密度小、强度高的特点,适合用于车身和车架的制造。
铝合金的使用可以有效减轻车辆重量,提高能源利用效率。
2. 高强度钢材:高强度钢材具有高强度和较低的密度,可以在保证安全性的前提下减少车身重量。
在新能源汽车的设计中,采用高强度钢材可以降低车辆的自重,提高续航里程。
3. 复合材料:碳纤维复合材料是一种轻质高强度材料,具有优异的力学性能和良好的耐腐蚀性。
在新能源汽车的设计中,使用碳纤维复合材料可以既减轻车身重量,又提高车辆的结构刚性。
四、轻量化设计的挑战和展望虽然新能源汽车的轻量化设计能够带来许多好处,但也面临一些挑战。
例如,轻量化设计可能增加材料和制造成本,影响车辆的安全性以及抗撞性能。
此外,新材料的使用也需要对其可持续性进行评估。
轻量化材料素材

材料轻量化,一般通过采用轻量化的金属和非金属材料实现,主要包括工程塑料以及各种复合材料。
轻量化材料中,目前钢铁材料仍保持主导地位,但钢铁材料的比例逐年下降,铝合金、镁合金、工程塑料、复合材料等材料比例逐渐增加。
目前在汽车行业的材料轻量化已经成为一种趋势,在不影响车身强度的情况下,使用更多的铝合金、镁合金、工程塑料等有助于降低车身自重,从而带来更好的燃油经济性。
汽车轻量化材料面面观前言在全球参与节能减排的大背景下,轻量化已然成为汽车发展的重要趋势之一,尤其在乘用车燃料消耗量第四阶段标准即2020年实现5.0L/100km油耗的当下。
最近几年,各种汽车轻量化技术不断革新、各种新材料不断涌现,那么,在这场轻量化材料的激战中,各种材料的表现如何?它们推广过程中存在哪些问题亟待解决?《中国汽车报》网先后对汽车用高强度钢、铝合金、镁合金、复合材料等主流轻量化材料进行了介绍。
高强度钢高强度钢在汽车上应用比例将提升目前高强度钢主要应用在汽车安全件、底盘及车身等方面,未来其应用肯定会越来越广。
汽车轻量化不是用镁铝合金代替钢材,而是综合利用即‘把最好的材料用在最合适的地方’。
汽车用钢不会被完全取代自从轻量化的概念提出以来,尤其是为实现轻量化和达到节能减排的目标,铝合金、镁合金、碳纤维、工程塑料等新材料逐... 全文>>铝合金高成本阻碍车用铝合金普及由于大气污染、油耗法规加严、新能源汽车发展及资源循环利用等多方面因素,铝材已经成为汽车轻量化发展的趋势之一,如何更好地利用铝材降低车重成为车企正在研究和追求的方向。
记者通过采访了解到,目前汽车用铝合金主要分成两类:铸造铝合金和变形铝合金。
目前铝合金已经在发动机、变速器、轮毂、防撞梁等方面大规模应用,但... 全文>>汽车用铝合金的发展历程据了解,最早把铝材运用到汽车上的是印度人。
1896年印度人率先用铝制做了汽车曲轴箱。
进入20世纪早期,铝在制造豪华汽车和赛车上有一定的应用,铝制车身的汽车开始出现,如亨利·福特的Model T型汽车和二三十年代欧洲赛车场上法拉利360赛车都是铝制车身。
汽车轻量化材料

汽车轻量化材料汽车轻量化材料是指用于减轻汽车整车重量的材料,在汽车制造中起着至关重要的作用。
随着能源短缺和环境污染的日益严重,汽车工业也越来越关注汽车轻量化技术的研究和应用。
下面我们来了解一些常见的轻量化材料。
1. 铝合金:铝合金是一种轻质、耐腐蚀的金属材料,广泛应用于汽车的制造中。
使用铝合金替代传统的钢铁材料可以显著减轻车辆的重量,提高燃油经济性。
此外,铝合金还具有优良的加工性能和可回收性,对于提高汽车的可持续性也起着重要作用。
2. 碳纤维复合材料:碳纤维复合材料是一种高强度、轻质的材料,由碳纤维和树脂基础材料组成。
它的密度只有钢的四分之一,但却具有比钢材更高的强度和刚度。
汽车使用碳纤维复合材料可以显著减少车身重量,提高车辆的性能和操控稳定性。
3. 高强度钢:高强度钢是一种具有较高强度和耐腐蚀性的钢材,可以用于替代传统的低碳钢。
相对于低碳钢,高强度钢的重量更轻,但具有更高的强度和刚度。
使用高强度钢可以减轻汽车重量,同时保证车身的安全性能。
4. 镁合金:镁合金是一种密度很低的金属材料,比铝还轻。
镁合金具有良好的强度和刚度,同时具有优异的耐腐蚀性能。
用镁合金制造汽车零部件可以显著减轻车辆的重量,提高燃油经济性。
5. 聚合物复合材料:聚合物复合材料是一种由纤维和树脂组成的材料,广泛应用于汽车的制造中。
聚合物复合材料具有良好的强度和刚性,而且重量轻,可以减轻汽车的重量,提高燃油经济性。
聚合物复合材料还具有优良的吸能性能,在碰撞事故中能够提供更好的保护。
总的来说,汽车轻量化材料对于提高汽车的燃油经济性、降低能源消耗、减少对环境的污染非常重要。
随着科技的不断发展和创新,轻量化材料将会得到更广泛和深入的应用,为汽车工业的可持续发展做出更大的贡献。
低成本的轻量化解决方案

低成本的轻量化解决方案一、概述轻量化技术在各个领域中得到了广泛应用,可以显著降低产品的重量、提高产品的性能和效率。
本文将针对低成本的轻量化解决方案进行详细的介绍和分析。
二、背景随着全球经济的发展和竞争的加剧,企业对产品成本的控制变得越来越重要。
轻量化技术可以在不降低产品质量和性能的前提下,降低产品的材料和制造成本,提高产品的竞争力。
三、轻量化材料1. 高强度钢:高强度钢具有较高的强度和刚性,可以减少材料的使用量,提高产品的强度和耐久性。
2. 铝合金:铝合金具有较低的密度和良好的可塑性,可以用于制造轻量化的结构件。
3. 碳纤维复合材料:碳纤维复合材料具有极高的强度和刚度,同时具有较低的密度,可以显著降低产品的重量。
四、轻量化设计1. 结构优化:通过对产品结构进行优化设计,减少材料的使用量,提高产品的强度和刚性。
2. 空心结构:采用空心结构可以减少产品的重量,同时保持足够的强度和刚性。
3. 多材料组合:将不同材料的优势进行组合,可以在保证产品性能的前提下降低产品的重量。
五、轻量化制造1. 成型技术:采用先进的成型技术,如压铸、注塑等,可以实现复杂形状的零件制造,减少材料的浪费。
2. 加工工艺优化:通过优化加工工艺,减少材料的切削量和加工时间,降低产品的制造成本。
六、轻量化应用案例以汽车行业为例,采用低成本的轻量化解决方案可以实现以下效果:1. 减少燃料消耗:通过降低汽车的重量,减少燃料的消耗量,降低运营成本。
2. 提高安全性能:轻量化材料具有较高的强度和刚性,可以提高汽车的安全性能。
3. 增加载重能力:轻量化材料可以减少车身的重量,增加汽车的载重能力,提高运输效率。
七、总结低成本的轻量化解决方案可以在降低产品成本的同时提高产品的性能和竞争力。
通过选择合适的轻量化材料、优化设计和制造工艺,可以实现产品的轻量化目标。
轻量化技术的应用不仅可以在汽车行业中发挥作用,还可以在航空航天、建筑、电子等领域中得到广泛应用。
汽车轻量化设计中的材料选择与研究

汽车轻量化设计中的材料选择与研究一、前言随着社会经济的快速发展,汽车行业也在不断的发展创新,其中汽车轻量化是近年来汽车技术和设计的热点之一。
轻量化设计通过减少汽车自身的重量以提高车辆行驶的性能和节省燃料,同时也减少了车辆对环境的污染,可谓一举多得。
在轻量化设计方面,材料选择是其关键的环节之一。
二、轻量化设计中的材料选择随着科技的不断进步和材料的不断发展,轻量化设计中的材料选择也有了更多的选择。
这些材料的性能不断地被优化,既能满足汽车轻量化的需求,又能同时满足汽车行驶的安全和舒适度。
具体的材料包括:1. 高强度钢高强度钢是目前应用最广泛的轻量化材料之一,它具有高强度、高质量、低成本等优点。
它在汽车架构设计中可极大地减轻汽车自身的重量,在碰撞事故中也可以具有较好的防护性能。
随着高强度钢的不断优化,更多种类的高强度钢被应用于汽车轻量化设计之中。
2. 铝合金铝合金具有较轻的重量,优良的强度和刚性,同时具有良好的成型性和可塑性。
由于其材料的物理特性和机械性能较为独特,使得铝合金应用在多种汽车零部件生产中具有广泛的价值和极大的发展潜力。
铝合金的优势在于它使用时可让车辆的质量减轻30%左右。
3. 炭纤维复合材料炭纤维复合材料具有高刚性、强度、低重量、高耐腐蚀性等特点。
然而,它的制造成本较高,且生产过程中的能耗较大。
不过,它的轻量化性能十分突出,与上述其他材料相比,炭纤维复合材料在其长期的应用过程中,对紫外线和酸钝性环境的抵御力也较高,为汽车制造领域的轻量化设计提供了更为丰富的选择和更高的发展潜力。
4. 镁合金镁合金是近几年来发展起来的一种轻量化材料,材料的密度比铝合金还轻,而且具备较好的强度和刚度,在机械性能达到要求的同时,还能减轻飞机/汽车自身质量,从而提高飞机/汽车动力性能。
正因为这个优势,镁合金被认为是新一代轻量化材料领域中的最具潜力的材料。
三、轻量化设计中材料选择的研究轻量化设计中材料选择的研究旨在确定哪些材料可以满足汽车轻量化设计的要求,对不同材料的性能进行理论分析,从而选出最优的材料。
汽车轻量化材料及工艺的研究与应用
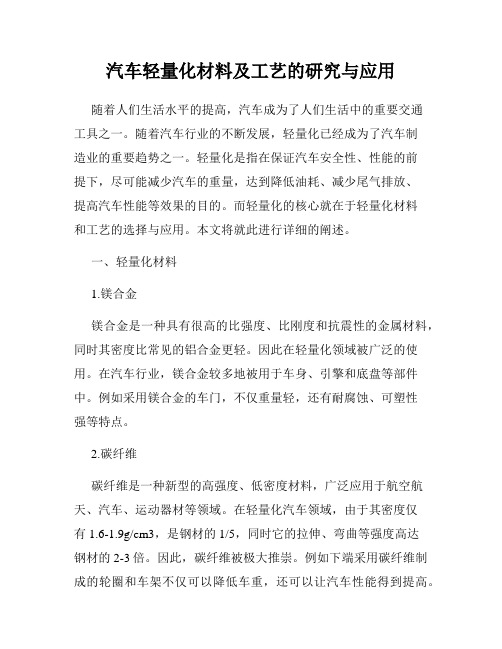
汽车轻量化材料及工艺的研究与应用随着人们生活水平的提高,汽车成为了人们生活中的重要交通工具之一。
随着汽车行业的不断发展,轻量化已经成为了汽车制造业的重要趋势之一。
轻量化是指在保证汽车安全性、性能的前提下,尽可能减少汽车的重量,达到降低油耗、减少尾气排放、提高汽车性能等效果的目的。
而轻量化的核心就在于轻量化材料和工艺的选择与应用。
本文将就此进行详细的阐述。
一、轻量化材料1.镁合金镁合金是一种具有很高的比强度、比刚度和抗震性的金属材料,同时其密度比常见的铝合金更轻。
因此在轻量化领域被广泛的使用。
在汽车行业,镁合金较多地被用于车身、引擎和底盘等部件中。
例如采用镁合金的车门,不仅重量轻,还有耐腐蚀、可塑性强等特点。
2.碳纤维碳纤维是一种新型的高强度、低密度材料,广泛应用于航空航天、汽车、运动器材等领域。
在轻量化汽车领域,由于其密度仅有1.6-1.9g/cm3,是钢材的1/5,同时它的拉伸、弯曲等强度高达钢材的2-3倍。
因此,碳纤维被极大推崇。
例如下端采用碳纤维制成的轮圈和车架不仅可以降低车重,还可以让汽车性能得到提高。
3.铝合金铝合金是一种轻量、结构强度高、耐腐蚀、抗震性好等特点的金属材料。
因此在汽车制造业中得到广泛的应用。
目前,众多汽车生产商,例如宝马、奥迪等都采用铝合金制造车身结构框架,如宝马采用了大量的铝合金制造车身结构框架,使车身重量比同类车型轻500-1,000公斤。
4.钛合金钛合金是一种相对来说比较昂贵的金属材料,但是它的优点也是显而易见的。
例如钛合金比钢材轻40%,比铝材更轻盈,同时其耐腐蚀性能也非常优秀。
在汽车轻量化领域,钛合金可以用于各种零部件的制造,例如发动机、变速器等。
二、轻量化工艺1.冷成形冷成形是一种在保证材料性质和机械性能的前提下,采用冷挤压机进行轻量化成形材料加工工艺的方法。
通过利用外重锤和内空心压头的相互作用,将材料压入模具中成型。
这种工艺可以避免对材料的脆化,保持了材料的强度和抗震性能。
汽车机械制造中的轻量化设计与材料选用

汽车机械制造中的轻量化设计与材料选用随着环境保护和能源效率的要求不断提高,汽车制造业正积极寻求轻量化解决方案,以减少燃料消耗和减排。
轻量化设计和合适的材料选用在汽车工业中变得愈发重要。
本文将深入探讨汽车机械制造中的轻量化设计原则与材料选用的相关问题。
一、轻量化设计原则1. 结构优化:通过结构优化,合理设计汽车零部件的几何形状和钢板的壁厚。
使用有限元分析等工具,优化组件的重量和强度之间的平衡,确保在不破坏结构安全性和性能的前提下,最大限度地减少重量。
2. 材料选择:选择高强度、高刚度和轻质材料,如高强度钢、铝合金、纤维增强塑料等。
这些材料具有较高的强度-重量比,能有效减轻汽车结构的重量。
3. 制造工艺改进:通过改进制造工艺,减少材料浪费和能源消耗。
采用先进的成型工艺,如双面模压、注塑成形等,可以降低零部件生产过程中的废料率。
二、材料选用1. 高强度钢:作为最常用的轻量化材料之一,高强度钢具有较高的强度和刚度,同时重量较轻。
钢的成本相对较低且容易加工,可以满足汽车零部件的制造要求。
2. 铝合金:具有良好的耐腐蚀性和导热性能,同时重量轻、强度高。
铝合金在车身和发动机零部件中的应用广泛,如车门、车顶、减震器等。
3. CFRP(碳纤维增强塑料):碳纤维增强塑料具有极高的强度和刚度,同时具备重量轻、抗腐蚀性能优秀的特点。
其在高性能车辆中的应用越来越普遍,如车身、底盘和内饰等。
4. 高性能塑料:如聚酰亚胺、聚醚醚酮等,这些材料具有较低的密度、良好的热稳定性和电性能,广泛应用于车身板件、电器连接器和电子组件等。
5. 镁合金:镁合金是一种重量轻、强度高的金属材料,具有良好的机械性能和抗冲击性能。
它在汽车零部件中的应用逐渐增多,如发动机缸盖、悬挂系统等。
6. 复合材料:利用复合材料的轻量化设计,将不同材料的优势结合起来,如玻璃纤维增强塑料、碳纤维/镜像碳纤维等。
它们具有高强度、耐疲劳性和良好的冲击吸收性能。
总结:汽车机械制造中的轻量化设计和材料选用对提高汽车的燃油效率、减少对环境的影响具有重要意义。
浅析我国汽车轻量化材料发展

浅析我国汽车轻量化材料发展近年来,随着环保意识的增强和汽车工业的不断发展,汽车轻量化成为了汽车制造业发展的热点话题。
通过采用轻量化材料,车辆重量可以降低,从而减少能源消耗和二氧化碳排放。
我国汽车轻量化材料的发展也在逐步加强。
目前,我国汽车轻量化材料主要包括金属材料和非金属材料两大类。
金属材料主要是铝合金、镁合金和钛合金,非金属材料主要是高强度钢、先进复合材料和高分子材料等。
其中,铝合金是当前应用最为广泛的轻量化金属材料之一。
尤其在汽车车身板及零部件的轻量化中,铝合金的应用非常广泛。
铝合金的优点是密度低、强度高、可加工性好、抗腐蚀性强等。
但是,铝合金也存在一些缺点,如生产成本高、成型难度大、焊接难度大等。
钛合金是一种重要的高强度、耐腐蚀性能极佳的金属材料。
虽然钛合金的密度较高,但其具有良好的机械性能和热稳定性,因此被广泛应用于高档汽车的车身结构、底盘零部件和发动机部件等。
在非金属材料方面,高强度钢以其优异的机械性能和成本效益而成为汽车轻量化时的首选材料之一。
先进复合材料由于具有轻质、高强度、高刚度、耐腐蚀性和较好的吸音隔音等特性,也成为汽车轻量化的一种主要材料。
而高分子材料则在汽车内饰件制造中已经广泛应用。
总体而言,随着我国汽车工业的快速发展,汽车轻量化材料也得到了快速发展。
未来,面对越来越严格的环保要求和节能减排政策,汽车企业需要不断进行技术改进和材料创新,不断推动汽车轻量化技术的发展。
同时,政府也应该提供相应的政策支持和资金支持,促进汽车轻量化材料的发展,为构建绿色低碳的汽车产业链做出更大的贡献。
低成本的轻量化解决方案

低成本的轻量化解决方案概述:轻量化是指通过减少产品的分量,以达到减少材料和能源消耗的目的。
在现代工业中,轻量化已成为一种重要的趋势,因为它可以提高产品的性能和效率,并降低生产成本。
本文将介绍一种低成本的轻量化解决方案,以满足不同行业的需求。
1. 轻量化材料选择:选择合适的轻量化材料是实现低成本轻量化解决方案的关键。
根据不同的应用需求,常用的轻量化材料包括铝合金、复合材料、塑料和纤维增强材料等。
这些材料具有分量轻、强度高、耐腐蚀性好等特点,适合于各种工业领域。
2. 结构优化设计:通过优化产品的结构设计,可以减少材料的使用量,从而实现轻量化的目标。
结构优化设计可以采用有限元分析等工具,通过摹拟和计算来确定最佳结构方案。
通过减少材料的使用量,可以降低生产成本,并提高产品的性能和效率。
3. 创造工艺改进:改进创造工艺是实现低成本轻量化解决方案的另一个重要步骤。
通过采用先进的创造工艺,可以提高生产效率并减少废品率。
例如,采用先进的成型技术,如压铸、注塑成型等,可以实现复杂形状的轻量化产品的高效生产。
4. 节能环保考虑:在实施低成本轻量化解决方案时,还应考虑节能环保因素。
选择轻量化材料和改进创造工艺不仅可以减少材料和能源消耗,还可以降低产品的碳排放和环境影响。
通过减少资源的使用和废弃物的产生,可以实现可持续发展的目标。
5. 成本效益评估:在实施低成本轻量化解决方案之前,需要进行成本效益评估。
这包括评估轻量化材料的成本、改进创造工艺的投资和预期的经济效益。
通过综合考虑成本和效益,可以确定最佳的轻量化解决方案,以实现成本降低和效率提高的目标。
案例研究:以汽车创造业为例,采用低成本的轻量化解决方案可以显著降低汽车的燃料消耗和排放,提高汽车的性能和安全性。
通过使用铝合金和复合材料等轻量化材料,可以减少汽车的分量,提高燃油效率。
同时,优化车身结构和改进创造工艺,可以降低生产成本并提高汽车的安全性能。
这些措施不仅可以满足消费者对节能环保的需求,还可以提高企业的竞争力。
汽车车身轻量化材料优化设计
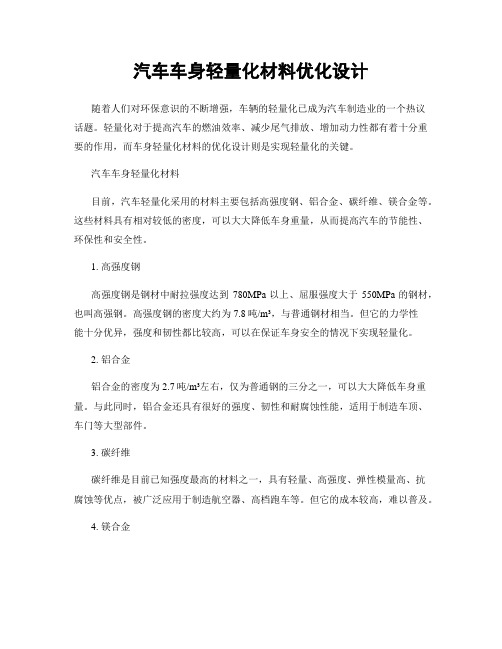
汽车车身轻量化材料优化设计随着人们对环保意识的不断增强,车辆的轻量化已成为汽车制造业的一个热议话题。
轻量化对于提高汽车的燃油效率、减少尾气排放、增加动力性都有着十分重要的作用,而车身轻量化材料的优化设计则是实现轻量化的关键。
汽车车身轻量化材料目前,汽车轻量化采用的材料主要包括高强度钢、铝合金、碳纤维、镁合金等。
这些材料具有相对较低的密度,可以大大降低车身重量,从而提高汽车的节能性、环保性和安全性。
1. 高强度钢高强度钢是钢材中耐拉强度达到780MPa以上、屈服强度大于550MPa的钢材,也叫高强钢。
高强度钢的密度大约为7.8吨/m³,与普通钢材相当。
但它的力学性能十分优异,强度和韧性都比较高,可以在保证车身安全的情况下实现轻量化。
2. 铝合金铝合金的密度为2.7吨/m³左右,仅为普通钢的三分之一,可以大大降低车身重量。
与此同时,铝合金还具有很好的强度、韧性和耐腐蚀性能,适用于制造车顶、车门等大型部件。
3. 碳纤维碳纤维是目前已知强度最高的材料之一,具有轻量、高强度、弹性模量高、抗腐蚀等优点,被广泛应用于制造航空器、高档跑车等。
但它的成本较高,难以普及。
4. 镁合金镁合金的密度为1.8吨/m³左右,较铝合金更轻。
但与此同时,它的耐腐蚀性差,容易遇水氧化。
因此,镁合金目前主要应用于制造汽车的一些重要零部件,如发动机缸体、减震器等。
汽车车身轻量化材料优化设计在汽车制造过程中,材料的选择只是轻量化的第一步,更为关键的是对材料的优化设计。
一方面,在汽车的车身结构设计中,要将各种材料选用合理组合,确保达到优化的轻量化效果。
另一方面,在车身的板材设计中,在保证安全性的前提下,可以通过减少板材厚度、采用复合材料等方式降低车重。
现在,越来越多的汽车制造企业开始注重轻量化的研发。
比如,福特公司利用汽车制造的先进技术和工艺,成功实现汽车的高强度钢和铝制组合车身,实现了轻量化和强度的均衡。
铸件材料轻量化
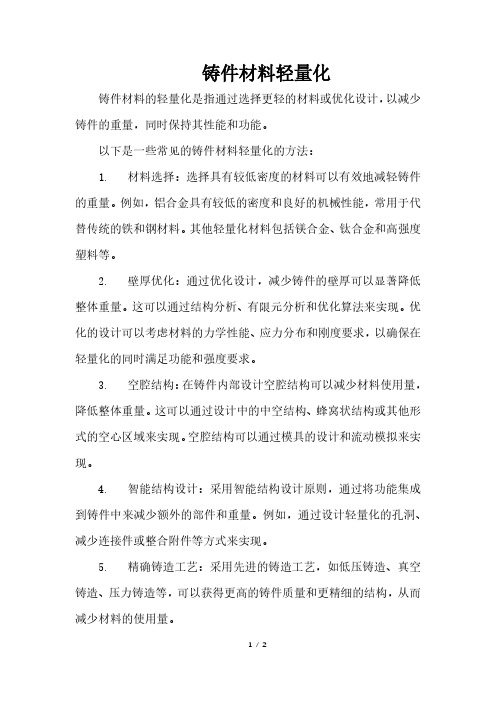
铸件材料轻量化
铸件材料的轻量化是指通过选择更轻的材料或优化设计,以减少铸件的重量,同时保持其性能和功能。
以下是一些常见的铸件材料轻量化的方法:
1. 材料选择:选择具有较低密度的材料可以有效地减轻铸件的重量。
例如,铝合金具有较低的密度和良好的机械性能,常用于代替传统的铁和钢材料。
其他轻量化材料包括镁合金、钛合金和高强度塑料等。
2. 壁厚优化:通过优化设计,减少铸件的壁厚可以显著降低整体重量。
这可以通过结构分析、有限元分析和优化算法来实现。
优化的设计可以考虑材料的力学性能、应力分布和刚度要求,以确保在轻量化的同时满足功能和强度要求。
3. 空腔结构:在铸件内部设计空腔结构可以减少材料使用量,降低整体重量。
这可以通过设计中的中空结构、蜂窝状结构或其他形式的空心区域来实现。
空腔结构可以通过模具的设计和流动模拟来实现。
4. 智能结构设计:采用智能结构设计原则,通过将功能集成到铸件中来减少额外的部件和重量。
例如,通过设计轻量化的孔洞、减少连接件或整合附件等方式来实现。
5. 精确铸造工艺:采用先进的铸造工艺,如低压铸造、真空铸造、压力铸造等,可以获得更高的铸件质量和更精细的结构,从而减少材料的使用量。
6. 环境友好材料:选择可回收材料或环境友好材料可以在轻量化的同时减少对环境的负面影响。
需要注意的是,在进行铸件材料轻量化时,需要综合考虑材料的力学性能、成本、可加工性、耐久性和可靠性等因素。
此外,轻量化设计还需要满足相关的法规和标准要求。
因此,在实施铸件材料轻量化之前,建议进行充分的工程分析和评估,并与专业工程师和设计团队合作。
汽车轻量化高端铝材料

汽车轻量化高端铝材料
汽车轻量化是当前汽车工业的一个重要发展趋势,目的是通过减少汽车的自重来提高燃油经济性和减少碳排放。
高端铝材料是实现汽车轻量化的重要选择之一。
高端铝材料具有以下特点:
1. 轻量化:相比传统的钢材,铝材料具有更轻的重量,使得汽车整体重量减少。
使用高端铝材料可以降低汽车的重量,提高燃油经济性和行驶性能。
2. 高强度:高端铝材料具有较高的强度和刚度,可以满足汽车结构的强度要求,保证车辆的安全性能。
3. 抗腐蚀性:铝材料具有良好的抗腐蚀性能,不容易生锈和腐蚀,能够提高汽车的使用寿命和经济效益。
4. 可回收性:铝材料可以被完全回收再利用,符合环保要求,降低资源消耗和环境污染。
5. 良好的加工性能:铝材料易于加工成型,适合大规模生产,符合汽车制造的工艺要求。
高端铝材料在汽车制造中的应用包括车身结构、车身外壳、传动系统、制动系统等。
例如,车身结构中可以采用铝合金板材或者铝合金型材来替代部分钢材,以降低整车重量。
车身外壳中使用铝材料可以使车辆更加轻盈和经济。
需要注意的是,高端铝材料的成本相对较高,对于汽车制造企业而言是一个考虑因素。
此外,铝材料在高温环境下的性能相对较差,对于发动机等部件的应用需要特别注意。
总之,高端铝材料作为一种轻量化的材料选择,具有重要的应用前景。
随着汽车轻量化需求的增加,高端铝材料在汽车工业中的应用会进一步扩大。
低成本的轻量化解决方案
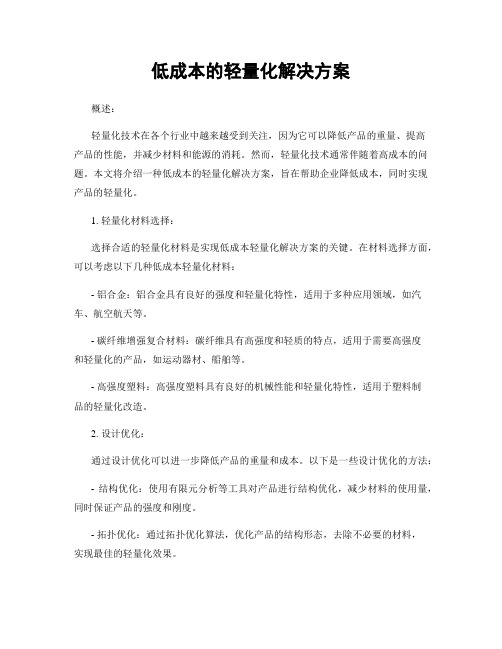
低成本的轻量化解决方案概述:轻量化技术在各个行业中越来越受到关注,因为它可以降低产品的重量、提高产品的性能,并减少材料和能源的消耗。
然而,轻量化技术通常伴随着高成本的问题。
本文将介绍一种低成本的轻量化解决方案,旨在帮助企业降低成本,同时实现产品的轻量化。
1. 轻量化材料选择:选择合适的轻量化材料是实现低成本轻量化解决方案的关键。
在材料选择方面,可以考虑以下几种低成本轻量化材料:- 铝合金:铝合金具有良好的强度和轻量化特性,适用于多种应用领域,如汽车、航空航天等。
- 碳纤维增强复合材料:碳纤维具有高强度和轻质的特点,适用于需要高强度和轻量化的产品,如运动器材、船舶等。
- 高强度塑料:高强度塑料具有良好的机械性能和轻量化特性,适用于塑料制品的轻量化改造。
2. 设计优化:通过设计优化可以进一步降低产品的重量和成本。
以下是一些设计优化的方法:- 结构优化:使用有限元分析等工具对产品进行结构优化,减少材料的使用量,同时保证产品的强度和刚度。
- 拓扑优化:通过拓扑优化算法,优化产品的结构形态,去除不必要的材料,实现最佳的轻量化效果。
- 模块化设计:采用模块化设计可以降低产品的重量和成本,同时提高生产效率。
3. 制造工艺改进:改进制造工艺可以进一步降低产品的成本。
以下是一些制造工艺改进的方法:- 热成型:采用热成型工艺可以降低产品的成本,提高生产效率。
热成型可以用于制造塑料制品、铝合金制品等。
- 3D打印:3D打印技术可以实现快速制造和个性化定制,同时可以减少材料的浪费,降低成本。
- 自动化生产线:引入自动化生产线可以提高生产效率,降低人工成本,同时减少产品的重量。
4. 质量控制:在实施低成本轻量化解决方案的过程中,质量控制是至关重要的。
以下是一些质量控制的方法:- 严格的材料检测:对采购的材料进行严格的检测,确保材料的质量符合要求。
- 制造过程控制:建立完善的制造过程控制体系,确保产品的质量稳定。
- 产品测试和验证:对产品进行全面的测试和验证,确保产品的性能和质量达到要求。
- 1、下载文档前请自行甄别文档内容的完整性,平台不提供额外的编辑、内容补充、找答案等附加服务。
- 2、"仅部分预览"的文档,不可在线预览部分如存在完整性等问题,可反馈申请退款(可完整预览的文档不适用该条件!)。
- 3、如文档侵犯您的权益,请联系客服反馈,我们会尽快为您处理(人工客服工作时间:9:00-18:30)。
轻量化材料的选材Via 常州精密钢管博客从对机械制造类产品的市场需求出发,定义了产品的功能目标与适用于产品寿命周期的边界条件。
在产品开发的规划阶段,引出了与要求、构造和材料相适应的目标函数。
借助“Ashby图”,可以从众多的材料选择项中预选出与性能要求相符合的材料。
在规划设计阶段,需要对相应材料效率的要求加以规范化,因为这些要求与用于轻量化的材料质量有关。
本节中,采用形状因子对改善使用性能的成形方法进行量化,性能指标的成本则通过价格指数加以关联。
借助自行车车架的例子,说明了按照基本要求和边界条件分步选择材料的方法。
借助用于内燃机的铸造合金适合度的评估示例,来说明用于重量组合的要求和边界条件,并进行相互比较。
为了对材料方案进行评估,还将得出的合金性能范围与在材料组中的加工消耗进行比较。
作为示例,还对可能用于一款面向市场的、大批量生产的高性能发动机的材料进行了比较和选择。
引言结构材料必须首先能够承受机械载荷,其次要满足其他的功能,如:导热或者热绝缘。
对材料的力学性能要求还有:刚度、动态强度和静态强度、减振、断裂韧度、抗磨损能力和抗蠕变能力。
材料可以如下分类:陶瓷、非晶形材料(玻璃)、金属、聚合物与复合材料(见2.1节)[1,2]。
轻量化所需要的材料要与结构相匹配,特别是要能够实现轻量化的目标。
图2-3-1展示了由不同材料制成的两个自行车车架:一个车架是1896年用竹管组装的[3],一个是100年后用碳纤维增强塑料加工而成的(CFK)[4]。
如今,大部分的自行车的梯形车架是用钢或者铝合金加工而成的。
为什么选择这些材料来制造车架?不同的材料之间有什么区别?如何选择合适的材料?本章节就是要回答这些问题。
图2-3-1自行车作为轻量化示例a)竹车架1896[3]b)碳纤维增强塑料车架2007[4]轻量化意味着将一个用于特定应用的构件体系的重量最小化。
一个运动构件越轻,构件用于运动改变所需要的能量就越少。
对于所有的产品来说,都要用市场可接受的成本来进行生产。
每种材料可接受的价格在很大程度上取决于其应用,如图2-3-2所示。
一般来说,用于建筑业的材料的价格必须低于用于汽车制造和医疗技术的材料的价格。
价格与市场容量成反比例关系:使用量越大,价格就越低。
在航天工业中省下1kg的重量,就可以节省大约5000欧元的费用。
不过,这种按照应用领域进行的一般性考察并不适用于某些特殊的案例:用于在(西班牙)比尔堡古根海姆博物馆的挡板是采用昂贵的钛合金制造的,或者宝马豪华轿车的发动机是采用镁合金制造的。
虽然这些特殊的案例产品所占有的市场容量非常小,但是仅仅采用技术功能来评估这些产品是不够的,因为建筑同时也是艺术品,而汽车则是身份和社会地位的象征。
图2-3-2材料的平均价值(价格/质量)与应用有关,反过来与市场容量成比例关系[17]2.3.2在产品开发要求的框架内选择材料问题:“对于一个特定的应用来说,何种材料是最佳的?”回答这一问题的前提是:对构件的使用条件进行了分析,并在需求框架(任务书)内整理出了任务要求[5]。
只有在需求框架与构件参数的功能框架完全明确后,才有可能对设计进行优化。
一般来说,通常需要根据评估作出妥协。
材料选择[6]始于市场对新产品的需求或者对已有产品在功能以及合理的加工方法方面的需求(表2-3-1)。
在初始阶段,首先要生成能够满足构件要求的规划。
材料供应商以及新材料开发研究人员可以提供范围广泛的材料,这些材料的力学、摩擦、物理、化学以及生态性能与产品所要求的使用性能相对应。
下一步是用构件的构造参数来确定构件的成形方法,从而限定材料的范围。
这样,一个设计的抉择就和一个材料的选择联系起来了,并可以用来评估对产品和材料要求的满足程度。
虚拟产品开发和使用仿真可以验证材料对所提出的要求的满足程度,不过可能要按照实现目标的能力对预期设计进行修正。
这一问题解决周期可以多次循环进行。
通过这种方法,可以定义材料规格与制造允差,确定加工工艺链。
最后,则可以确定用于产品加工的准确生产计划,生产出的产品可以满足现有的应用需求或者新的应用需求。
对于材料供应商和后续加工者的质量要求也是这样定义的,这些质量要求也包括了产品的功能和供货条件等要求。
在选择材料时,材料研发人员、工程师与销售人员一起工作、相互配合是最重要的,它可以带来满足市场的创新——新的产品、材料替代或者制造方法的改变。
2.3.3材料效率在考虑到不同要求的情况下,如何对现有的材料进行评估?首先,必须将构件功能与材料性能相关联,以便于对特征值进行比较。
要对不同的材料进行比较以及对材料进行预选,材料数据库以及供应商的数据表是必不可少的。
Ashby和他的团队[7,8]开发出了一个方法,用来对材料的性能进行图形比较。
图2-2-3显示了不同材料种类的屈服强度与密度关系的双对数图。
材料性能可近似为一个椭圆,垂直主轴作为强度离散区域。
相对来说,密度的变化很小。
可以将材料种类归纳到域,例如,钛合金的椭圆位于屈服强度100~1000MPa的区间,密度区间为4.4~4.6g/cm3,在图中具体的位置则取决于合金成分和热处理工艺。
图2-3-3借助材料效率线RDZ、RB、RP得出的不同材料的屈服极限与材料密度的关系[18]如何利用Ashby图呢?如果要寻找确定了最小强度的材料,则可以将这个最小强度作为界线绘到图表中,屈服强度位于界线之上的材料都可供选择使用。
例如,在水平线100MPa之上的材料有金属、高技术陶瓷与复合材料。
该界线对应于如下归纳的要求:“材料在100MPa载荷的作用下,既不会产生塑性变形,也不会发生断裂”。
在图2-3-3中,越是位于左边的材料,就越轻:当强度大于100MPa时,碳纤维增强塑料是最轻的材料。
泡沫聚合物、木与皮革更轻,但是强度达不到要求。
不过,只满足轴向的要求往往并不能保证材料能够承受相应的载荷。
随之而来的问题是:材料会在多大程度上满足一个特定的应用要求?第二个例子见图2 3 4。
该图显示了材料弹性模量与材料密度区域的双对数图,图中的材料有泡沫塑料、木、合成橡胶、聚合物、复合材料、合金、多孔陶瓷和工程陶瓷。
表中的辅助线对应于不同的单一材料在低频率下机械波的传播速度(v)。
声波速度v取决于材料的弹性模量(E)和密度(ρ):就是说:材料的弹性模量越大以及密度越小,波在该材料中传播的速度就越快。
在双对数图表中,速度v可以改写为:方程式(2.3.2)对应于一个直线方程:γ=ax+b,其中,γ为logE,x为logρ,斜率a=1(在每个轴上一个十进位数)。
在ρ=1下的纵坐标值对应于密度为1mg/m3的材料,其弹性模量为E=v2。
该方程描述了一个直线族,其对于各种声波传播速度v以及比弹性模量E/ρ平方根的斜度为1。
v越高,比弹性模量越大,则直线就越向上移动。
在根据方程式(2.3.2)得出的位于直线上方的所有材料都有相同的比弹性模量,例如:在纤维方向上的木材、一些复合材料、泡沫陶瓷和绝大多数的合金。
图2-3-4不同材料类别的弹性模量 密度对数示意图:木材、聚合物、合金、陶瓷与复合材料,带有不同声波扩散速度直线(=比弹性模量)2.3.4方法学如何将材料选择过程系统化呢?Ashby等人[8]建议采取下列步骤:●定义构件使用目标函数的最大值或最小值:能源、成本、质量、刚度等。
●针对这些目标函数(P)开发出一个方程[方程式(2.3.3)],方程与功能要求(F)、几何形状(G)和材料性能(W)相关:P=f(F,G,W):P=f[(功能要求F),(几何参数G),(材料性能W)](2.3.3)●识别目标函数的变量:要求、形状、性能。
●确定最低要求,如:价格界限、供货能力等(边界条件前沿)。
●在目标函数中使用变量。
●如果可能,将目标函数分为三个部分:P=f1(F)·f2(G)·f3(W)(2.3.4)以便于对每个部分进行优化。
f1是由市场需求和使用者来确定的;f2是设计人员的主要任务;这两个函数的求解都取决于材料选择f3。
这样可以将独立的解法叠加组合起来,用来在关联中找到“创新妥协”。
●要得出使用性能的表达式f3(W),需要定义与使用相关的材料效率的最大值:M=f(W)。
考虑到M=f(W,G),不仅是高效利用材料使用性能的要求,也是在材料选择与成形方法之间变化关系的要求。
●借助数据库、图表加以量化。
目标函数的定义是材料选择成功的关键。
一般来说,针对要求设定的使用参数和边界条件是多维的,绝大多数情况下是相互矛盾的,所以要设置优先次序:价格与/或重量与/或体积,哪个重要?有多重要?对设计材料的功能要求在于要满足特定的热—力学功能。
举例来说,当演员站在舞台上时,舞台的变形必须是不可见的;热交换器必须能实现良好的导热;轿车的车身在发生事故的时候要能保护乘客。
另外,舞台建筑看上去要有艺术感,热交换器要可回收,汽车要有运动感。
除了这些很难量化的目标参数之外,还要注意到严格的边界条件:最大成本、最小特征值、标准尺寸、生态指标以及贸易保护法规(例如:在一级方程式赛车中禁止采用金属基复合材料)等。
2.3.5刚度与质量对轻量化设计来说,最重要的性能组合是在低重量下的高刚度。
刚度(S)取决于构件几何形状(G)上的弹性模量(E)以及机械载荷类型。
材料的弹性模量是材料在拉载荷或者压载荷作用下抵抗弹性变形的能力(参见2 1节)。
胡克定律σ=Eε适用于材料在单轴拉应力或者压应力(σ)作用下的弹性应变(ε=Δl/l)。
刚度(S)与构件的弹性变形有关,取决于构件的几何形状与载荷方向:构件的横截面为A,长度为l,在外拉力(F)作用下产生了弹性变形(ΔL),因此有:刚度不仅与材料的弹性模量有关,也与构件的几何形状,即横截面与长度的比例有关。
这个问题可以归纳如下:要找到对于一根刚度确定的(要求)、尽可能轻的杆的材料(目标函数)。
这根杆在规定的力(F)作用下产生的变形不能超出规定值Δl。
这样可以得出目标函数:针对给定刚度(S)的最小质量(m),刚度定义了可允许的弹性变形。
图2 3 5显示了两种载荷类型:单轴拉伸以及圆柱杆的弯曲,圆柱杆的一端固定、初始长度(l)确定、直径(d)和横截面(A)可选择。
图2-3-5在力F作用下,横截面为A、长度l的圆柱杆的弹性变形Δla)单轴拉/压载荷b)一端固定情形下的弯曲1 拉应力载荷与压应力载荷图2-3-5a中的杆在单轴拉载荷或者压载荷作用下应当只发生弹性变形。
●目标函数P可定义为:P=m=V·ρ=A·l·ρ→最小值(2.3.6)式中,V为体积;ρ为密度;m为应当最小化的质量。
刚度SZ可以表示为力(F)和延长(Δl)的函数,见方程式(2.3.5)。
针对横截面的变化,对方程式(2.3.5)进行转换,可以得到方程式(2.3.7):●变量及其分类的识别:如果将方程式(2.3.7)中的A代入方程式(2.3.6),则可以将目标函数分解为三个部分作为因子:式中,f1为给出的刚度要求;f2为给出的构件几何形状,其长度为l,横截面变量为A;f3则是材料的使用参数,由弹性模量和密度给定。