切削加工和刀具技术的现状与发展
中国刀具行业现状及趋势分析

中国刀具行业现状及趋势分析一、刀具行业产业链分析刀具是机械制造中用于切削加工的工具,又称切削工具。
金属切削刀具材料主要包括硬质合金、高速钢、陶瓷和超硬材料(包括人造金刚石、立方氮化硼等)。
硬质合金刀具是全球市场目前的主流刀具。
与高速钢相比,硬质合金具有较高的硬度、耐磨性和红硬性;与陶瓷和超硬材料相比,硬质合金具有较高的韧性。
因此,硬质合金刀具是全球市场目前采用的主流刀具。
2019年,硬质合金刀具在全球刀具市场中占比63%,国内市场占比53%。
二、刀具行业驱动因素2020年年初受疫情影响导致PMI指数出现大幅度下降,但自2020年第二季度以来,我国PMI保持在50%以上水平,制造业景气度回暖,提高机床开工率。
从工业增加值数据来看,2020年下半年以来,工业增加值同比依然保持较好的增长。
随着产业结构的调整升级,我国机床数控化率稳步增长,机床数控化率从2013年的28.83%稳定上升至2020年的43.27%。
数控机床一方面造就更多高端刀具的消费,另一方面也会推动刀具整体价格的上升。
三、刀具行业发展现状2016-2020年全球刀具市场规模保持稳步增长的状态,2020年全球切削刀具消费金额达370亿美元,同比增长3.06%。
我国切削刀具市场消费情况与我国制造业发展水平和结构调整息息相关。
2016-2018年,随着“十三五”规划落地,制造业的转型升级推动了我国刀具行业快速发展,切削刀具年消费规模快速增至421亿元,达到历史最高水平。
而2019年受中美贸易摩擦加剧、汽车等下游行业下行的影响,我国刀具消费额下降至393亿元。
2020年以来,我国刀具市场增速恢复至10%以上,金额达到446亿元,同比上升13.49%。
四、刀具行业竞争情况目前,国际刀具行业竞争格局大致分为三个梯队。
第一梯队是欧美刀具企业,主导高端定制化刀具市场;第二梯队是日韩刀具企业,非定制化刀具认可度高;而第三梯队才是我国国内刀具企业,在非定制化市场逐步追赶日韩。
车削刀具的发展趋势
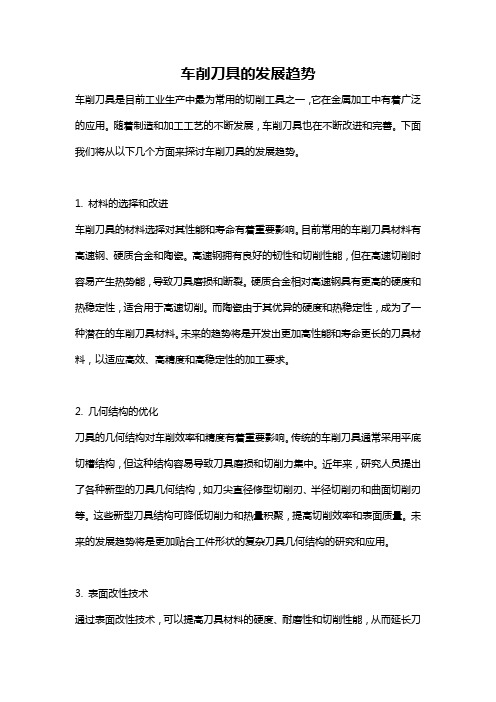
车削刀具的发展趋势车削刀具是目前工业生产中最为常用的切削工具之一,它在金属加工中有着广泛的应用。
随着制造和加工工艺的不断发展,车削刀具也在不断改进和完善。
下面我们将从以下几个方面来探讨车削刀具的发展趋势。
1. 材料的选择和改进车削刀具的材料选择对其性能和寿命有着重要影响。
目前常用的车削刀具材料有高速钢、硬质合金和陶瓷。
高速钢拥有良好的韧性和切削性能,但在高速切削时容易产生热势能,导致刀具磨损和断裂。
硬质合金相对高速钢具有更高的硬度和热稳定性,适合用于高速切削。
而陶瓷由于其优异的硬度和热稳定性,成为了一种潜在的车削刀具材料。
未来的趋势将是开发出更加高性能和寿命更长的刀具材料,以适应高效、高精度和高稳定性的加工要求。
2. 几何结构的优化刀具的几何结构对车削效率和精度有着重要影响。
传统的车削刀具通常采用平底切槽结构,但这种结构容易导致刀具磨损和切削力集中。
近年来,研究人员提出了各种新型的刀具几何结构,如刀尖直径修型切削刃、半径切削刃和曲面切削刃等。
这些新型刀具结构可降低切削力和热量积聚,提高切削效率和表面质量。
未来的发展趋势将是更加贴合工件形状的复杂刀具几何结构的研究和应用。
3. 表面改性技术通过表面改性技术,可以提高刀具材料的硬度、耐磨性和切削性能,从而延长刀具的使用寿命。
目前常用的表面改性技术包括涂层技术、离子注入技术和等离子体增强化学气相沉积技术等。
涂层技术主要是通过在刀具表面形成一层硬度高、耐磨性好的涂层,以增加刀具的耐磨性和切削性能。
离子注入技术则是通过注入氮、碳等元素到刀具表面,改善其硬度和耐磨性。
等离子体增强化学气相沉积技术则是一种利用等离子体沉积技术制备薄膜的方法,可获得较好的附着力和热稳定性。
未来的发展趋势将是进一步提高表面改性技术的效果和性能,以满足更高要求的切削工艺。
4. 自动化和智能化随着制造业的发展,对高效率、高精度和高稳定性的加工需求不断增加。
自动化和智能化技术的应用将成为未来车削刀具发展的重要方向。
2023年切削刀具行业市场分析现状

2023年切削刀具行业市场分析现状切削刀具是机械加工中不可或缺的重要工具之一,广泛应用于各种机械加工和制造业行业。
根据调查研究,切削刀具行业市场目前呈上升趋势,预计未来几年内市场规模将不断扩大。
先从切削刀具的品种入手:切削刀具种类繁多,根据功能可分为钻头、铣刀、齿轮刀具等。
根据不同材料可分为超硬合金刀具、高速钢刀具、硬质合金刀具等。
市场上的品牌也较为丰富,比如国内外知名品牌有:美孚、Tungaloy、Sumitomo Electric、三菱重工、塔司特等。
目前,切削刀具行业的市场规模逐渐扩大,特别是在我国经济不断发展和国家鼓励基础制造业转型升级的政策背景下,该行业市场空间更加广阔。
据统计,2019年全球切削刀具市场规模已达到114亿美元,在谷歌搜索趋势中,搜索量也逐年上升。
在中国近年的经济状况下,也大力发展各种制造业,市场容量增大,切削刀具行业的市场潜力逐渐释放。
那么面临这样一个比较良好的市场机遇,企业们应该如何排兵布阵呢?首先,要规划好企业自身的定位和发展战略。
切削刀具行业属于高端装备制造行业,对研发能力和技术水平的要求也很高。
企业应该注重提升技术和研发能力,确保产品质量和技术水平处于行业领先地位。
此外,在市场营销上也要下功夫,找准客户标的、提高品牌影响力是企业做好市场开拓的关键。
此外,切削刀具行业的市场竞争也日益激烈。
目前,切削刀具的生产企业数量较多,由于产能过剩严重,很多企业降低了价格竞争来争夺市场份额。
想要在激烈的市场竞争中脱颖而出,企业需要在产品品质、生产效率、品牌维护和销售渠道等方面都要下功夫。
综上所述,切削刀具行业市场作为一个高度技术性行业,挑战和机遇共存。
企业要在技术研发、品质管理、市场拓展等方面加强自身能力;进一步增强核心竞争力,以面对激烈的市场竞争和日趋规范的市场需求,赢得更多客户的信赖和支持。
2022年我国刀具行业发展现状及趋势分析
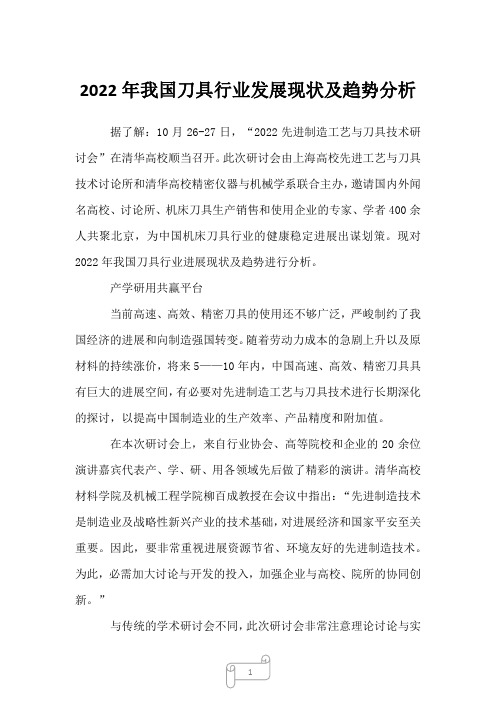
2022年我国刀具行业发展现状及趋势分析据了解:10月26-27日,“2022先进制造工艺与刀具技术研讨会”在清华高校顺当召开。
此次研讨会由上海高校先进工艺与刀具技术讨论所和清华高校精密仪器与机械学系联合主办,邀请国内外闻名高校、讨论所、机床刀具生产销售和使用企业的专家、学者400余人共聚北京,为中国机床刀具行业的健康稳定进展出谋划策。
现对2022年我国刀具行业进展现状及趋势进行分析。
产学研用共赢平台当前高速、高效、精密刀具的使用还不够广泛,严峻制约了我国经济的进展和向制造强国转变。
随着劳动力成本的急剧上升以及原材料的持续涨价,将来5——10年内,中国高速、高效、精密刀具具有巨大的进展空间,有必要对先进制造工艺与刀具技术进行长期深化的探讨,以提高中国制造业的生产效率、产品精度和附加值。
在本次研讨会上,来自行业协会、高等院校和企业的20余位演讲嘉宾代表产、学、研、用各领域先后做了精彩的演讲。
清华高校材料学院及机械工程学院柳百成教授在会议中指出:“先进制造技术是制造业及战略性新兴产业的技术基础,对进展经济和国家平安至关重要。
因此,要非常重视进展资源节省、环境友好的先进制造技术。
为此,必需加大讨论与开发的投入,加强企业与高校、院所的协同创新。
”与传统的学术研讨会不同,此次研讨会非常注意理论讨论与实施实效性相结合。
来自北京航天航空高校的陈五一教授介绍了镍基合金切削加工技术,天津高校的林彬教授介绍了轴向超声振动帮助磨削机理讨论,北京航天航空高校的张德远教授介绍了有用化振动切削工具技术,西北工大高校的张定华教授介绍了航空难加工材料切削加工及其表面完整性试验讨论,装甲兵工程学院的田欣利教授介绍了工程陶瓷高效低成本加工技术的讨论进展,中国矿业高校的邓福铭教授介绍了我国超硬刀具的进展历程、问题及展望,北京交通高校的张勤俭教授介绍了聚晶金刚石精密加工技术进展现状,华南理工高校的全燕鸣教授介绍了热管刀具与无钴硬质合金切削性能讨论。
刀具国内发展现状及未来趋势分析
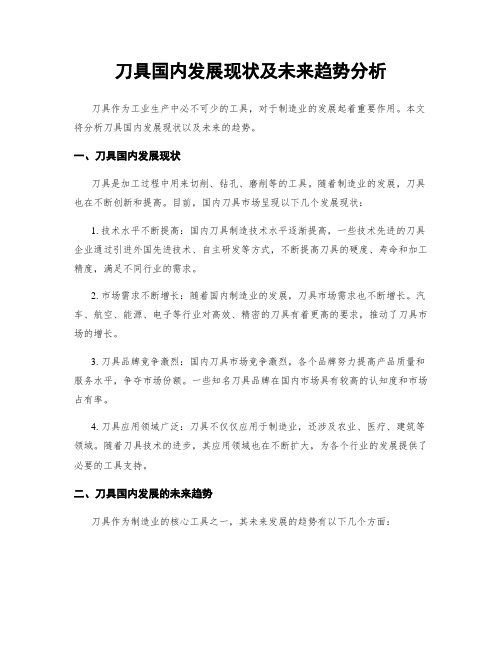
刀具国内发展现状及未来趋势分析刀具作为工业生产中必不可少的工具,对于制造业的发展起着重要作用。
本文将分析刀具国内发展现状以及未来的趋势。
一、刀具国内发展现状刀具是加工过程中用来切削、钻孔、磨削等的工具。
随着制造业的发展,刀具也在不断创新和提高。
目前,国内刀具市场呈现以下几个发展现状:1. 技术水平不断提高:国内刀具制造技术水平逐渐提高,一些技术先进的刀具企业通过引进外国先进技术、自主研发等方式,不断提高刀具的硬度、寿命和加工精度,满足不同行业的需求。
2. 市场需求不断增长:随着国内制造业的发展,刀具市场需求也不断增长。
汽车、航空、能源、电子等行业对高效、精密的刀具有着更高的要求,推动了刀具市场的增长。
3. 刀具品牌竞争激烈:国内刀具市场竞争激烈,各个品牌努力提高产品质量和服务水平,争夺市场份额。
一些知名刀具品牌在国内市场具有较高的认知度和市场占有率。
4. 刀具应用领域广泛:刀具不仅仅应用于制造业,还涉及农业、医疗、建筑等领域。
随着刀具技术的进步,其应用领域也在不断扩大,为各个行业的发展提供了必要的工具支持。
二、刀具国内发展的未来趋势刀具作为制造业的核心工具之一,其未来发展的趋势有以下几个方面:1. 高速、高效、高精度的要求:随着制造业对产品质量要求的提高,刀具市场将趋向于发展高速、高效、高精度的产品。
新材料的使用、刀具的设计和制造技术的进步,将进一步推动刀具的发展和应用。
2. 自动化生产的需求:随着制造业的智能化和自动化发展,刀具也需要适应自动化生产的需求。
自动化生产线对刀具的稳定性、耐用性和互换性要求更高,刀具制造商需要加强与自动化设备制造商的合作,研发适应自动化生产流程的刀具产品。
3. 个性化定制的市场需求:随着大规模定制的发展,刀具市场将趋向于个性化定制。
不同行业、不同企业对刀具的需求有所不同,刀具制造商需要根据客户需求,提供定制化的产品和解决方案。
4. 网络销售模式的普及:随着互联网的普及,电商对于传统行业的影响日益加深。
超高速切削的发展现状

超高速切削的发展现状超高速切削是一种先进的切削加工技术,采用高速转速和小切削深度进行切削,能够有效提高切削效率和加工精度。
本文将对超高速切削的发展现状进行详细介绍。
超高速切削技术的发展可以追溯到20世纪60年代,当时由于切削过程容易产生几何形状的误差和表面质量问题,因此一直未能得到广泛应用。
随着计算机数控技术和精密制造技术的快速发展,超高速切削技术在上世纪80年代出现了突破性的进展。
发展初期,超高速切削主要用于加工金属材料,如铝合金、镁合金等,通过提高切削速度和减小切削深度,大大提高了切削效率和表面质量。
随着材料科学和刀具制造技术的进步,超高速切削技术逐渐应用到切削硬度较高的材料,如钢、铁等。
近年来,随着新材料和复杂工件的出现,超高速切削技术迎来了新的发展机遇。
首先是新材料的应用,如高性能陶瓷、纳米材料等,这些材料具有高硬度和高韧性,传统切削技术难以满足对其加工精度和表面质量的要求,而超高速切削技术能够有效解决这一问题。
其次是复杂工件的加工,如汽车发动机缸体、飞机发动机叶片等,这些工件形状复杂,表面精度要求高,传统加工方法效率低、成本高,而超高速切削技术具有快速、高效的优势。
随着超高速切削技术的不断发展,相关设备和工具也在不断更新迭代。
首先是刀具材料的优化,采用纳米材料、复合材料等先进材料制造刀具,能够提高切削效率和切削质量。
其次是机床的改进,采用高刚性、高速度的数控机床,能够满足高速切削的要求。
同时,先进的控制系统和传感器技术的应用,能够实时监测切削过程中的温度、压力等参数,保证整个加工过程的稳定性和安全性。
超高速切削技术的发展带来了巨大的经济效益和社会效益。
首先是加工效率的提高,相比传统切削技术,超高速切削能够大幅度提高切削速度和加工效率,节约了生产时间和成本。
其次是加工精度和表面质量的提升,超高速切削能够实现微米级的精度和纳米级的表面粗糙度,满足了高精度工件的需求。
此外,超高速切削技术还可以减少切削力和切削温度,降低刀具磨损和能量消耗,从而延长刀具寿命,减少了对自然资源的消耗,对环境保护具有积极意义。
切削刀具的发展现状与趋势及对策
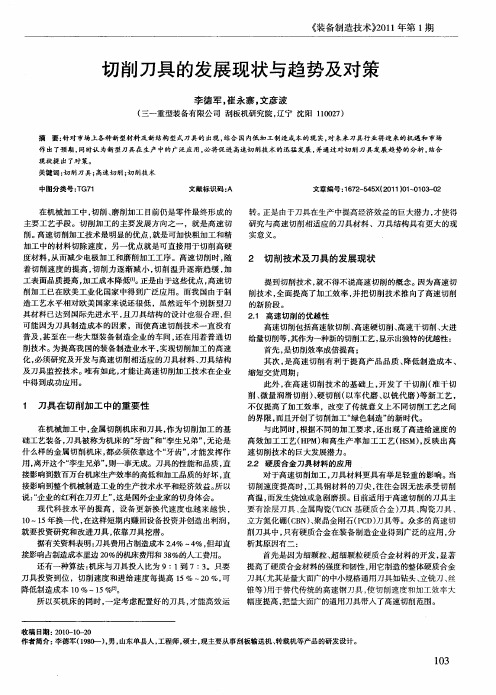
现代科 技水平 的提高 ,设 备更新换 代速度也越 来越 快 , 1 0~1 5年换 一代 , 在这样短期 内赚 回设备投资并创造 出利润 ,
就要投资研究和改进刀具 , 依靠刀具挖潜。 据有关资料表 明: 刀具费用占制造成本 2 % ~ % , . 4 4 但却直 接 影 响 占制造 成本 里 边 2 % 的机床 费 用 和 3 % ̄A3 费用 。 0 8 2 还有一种算法 : 机床与刀具投入 比为 9: 到 7: 。只要 1 3
削技术 。 为提高我 国的装备制造业水平 , 实现切削加工 的高速 化, 必须研究及开发与高速切削相适应 的刀具材料 、 刀具结 构
及 刀具监控技术 。 唯有如此 , 才能让高速切削加工技术 在企业
中得 到 成 功 应 用 。
1 刀具在 切 削加 工 中的重 要性
在机械加工 中, 金属切削机床和刀具 , 为切削加工 的基 作
刀具投资到位 ,切 削速度 和进 给速 度每提高 1 2 5% O%, 可
降低制造成本 1 ~1 0% 5%田 。
础工艺装备 , 刀具被称为机床 的“ 牙齿 ” 孪生兄 弟” 无论是 和“ , 什么样的金属切削机床 , 都必须依 靠这个“ 牙齿 ” 才能发挥作 ,
用, 离开这个“ 孪生兄弟 ”则一事无成 。刀具的性能和品质 , , 直
高效加工 工艺 ( P 和高生产率 加工工 艺 ( s , H M) H M) 反映 出高 速切削技术 的巨大发展潜力 。
高速切削包括高速软切削、 高速硬 切削 、 高速干切削、 大进 给量切削等 , 其作为一种新的切削工艺 , 显示出独特的优越性: 首先 , 是切削效率成倍提高 ; 其次 , 高速切削有利 于提高产 品 品质 、 是 降低 制造成本 、 缩短交货周期 ; 此外 , 高速 切削技术 的基础上 , 发了干切 削( 在 开 准干切 削、 微量 润滑切削 )硬切削 ( 、 以车代磨 、 以铣代磨 ) 等新工艺 , 不仅提高 了加工效率 ,改变 了传统意 义上 不同切削工艺之间 的界限 , 而且开创 了切削加工“ 绿色制造” 的新 时代 。 与此同时 , 根据不 同的加 工要求 , 出现了高进给速度的 还
中国刀具与切削加工技术的发展现状与趋势
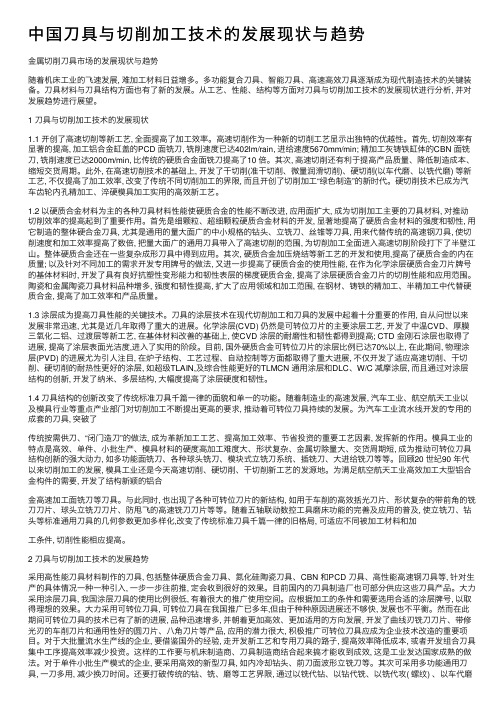
中国⼑具与切削加⼯技术的发展现状与趋势⾦属切削⼑具市场的发展现状与趋势随着机床⼯业的飞速发展, 难加⼯材料⽇益增多。
多功能复合⼑具、智能⼑具、⾼速⾼效⼑具逐渐成为现代制造技术的关键装备。
⼑具材料与⼑具结构⽅⾯也有了新的发展。
从⼯艺、性能、结构等⽅⾯对⼑具与切削加⼯技术的发展现状进⾏分析, 并对发展趋势进⾏展望。
1 ⼑具与切削加⼯技术的发展现状1.1 开创了⾼速切削等新⼯艺, 全⾯提⾼了加⼯效率。
⾼速切削作为⼀种新的切削⼯艺显⽰出独特的优越性。
⾸先, 切削效率有显著的提⾼, 加⼯铝合⾦缸盖的PCD ⾯铣⼑, 铣削速度已达402lm/rain, 进给速度5670mm/min; 精加⼯灰铸铁缸体的CBN ⾯铣⼑, 铣削速度已达2000m/min, ⽐传统的硬质合⾦⾯铣⼑提⾼了10 倍。
其次, ⾼速切削还有利于提⾼产品质量、降低制造成本、缩短交货周期。
此外, 在⾼速切削技术的基础上, 开发了⼲切削(准⼲切削、微量润滑切削)、硬切削(以车代磨、以铣代磨) 等新⼯艺, 不仅提⾼了加⼯效率, 改变了传统不同切削加⼯的界限, ⽽且开创了切削加⼯“绿⾊制造”的新时代。
硬切削技术已成为汽车齿轮内孔精加⼯、淬硬模具加⼯实⽤的⾼效新⼯艺。
1.2 以硬质合⾦材料为主的各种⼑具材料性能使硬质合⾦的性能不断改进, 应⽤⾯扩⼤, 成为切削加⼯主要的⼑具材料, 对推动切削效率的提⾼起到了重要作⽤。
⾸先是细颗粒、超细颗粒硬质合⾦材料的开发, 显著地提⾼了硬质合⾦材料的强度和韧性, ⽤它制造的整体硬合⾦⼑具, 尤其是通⽤的量⼤⾯⼴的中⼩规格的钻头、⽴铣⼑、丝锥等⼑具, ⽤来代替传统的⾼速钢⼑具, 使切削速度和加⼯效率提⾼了数倍, 把量⼤⾯⼴的通⽤⼑具带⼊了⾼速切削的范围, 为切削加⼯全⾯进⼊⾼速切削阶段打下了半壁江⼭。
整体硬质合⾦还在⼀些复杂成形⼑具中得到应⽤。
其次, 硬质合⾦加压烧结等新⼯艺的开发和使⽤,提⾼了硬质合⾦的内在质量; 以及针对不同加⼯的需求开发专⽤牌号的做法, ⼜进⼀步提⾼了硬质合⾦的使⽤性能, 在作为化学涂层硬质合⾦⼑⽚牌号的基体材料时, 开发了具有良好抗塑性变形能⼒和韧性表层的梯度硬质合⾦, 提⾼了涂层硬质合⾦⼑⽚的切削性能和应⽤范围。
我国超硬刀具高速切削技术发展现状、问题及前景
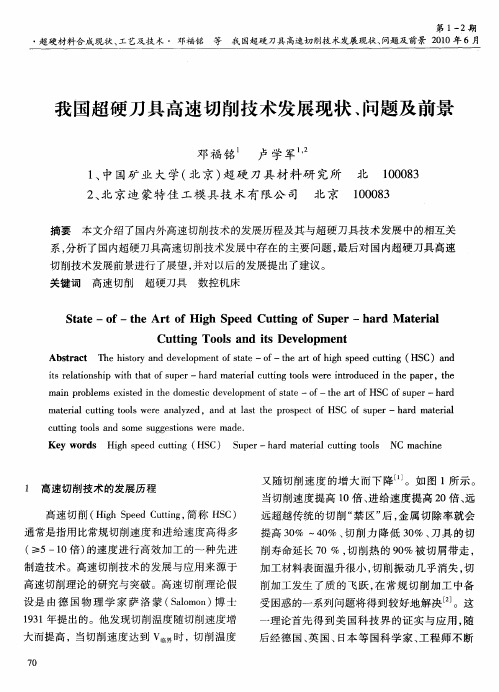
・
超 硬材料合 成现状 、 艺及技 术 ・ 邓福铭 工
等
我 国超硬 刀具 高速切 削技术发展现状 、 问题及前景 2 1 6月 0 0年
我国超硬刀具高速切 削技术发 展现状 、 问题及前景
邓 福铭 卢 学军 ’
1 中国矿 业 大学 ( 、 北京 ) 硬 刀 具材 料研 究 所 北 10 8 超 003 2 北 京迪 蒙特 佳 工模 具技 术 有 限公 司 北京 10 8 、 003
又 随切 削 速 度 的增 大 而 下 降 j 。如 图 1所 示 。
当切削速度提高 1 、 O倍 进给速度提高 2 O倍 、 远
高速切 削 ( ihSedC tn , Hg pe ut g 简称 H C) i S
通 常是 指 用 比常规 切 削 速 度 和 进 给 速 度 高 得 多
摘要 本文介绍 了国内外高速切削技术 的发展历程及其与超硬刀具 技术发展 中的相互关
系, 分析了国内超硬刀具高速切削技术发展 中存在 的主要问题 , 最后对 国内超硬刀具高速
切削技术发展前景进行 了展望 , 并对 以后的发展提出了建议 。 关键词 高速切削 超硬刀具 数控机床
St t 一 0 ae f— t e Ar fH ih e d Cuti f S pe —ha d M a e i l h to g Sp e tng o u r r t ra
提高切削效率 、 降低 生产成本 。因此 , 改进刀具
材料对于降低切削成本 比其它任何单一 过程 的
礴
疆 签
改变更具 潜力 , 如何 合理 地选 择 与应用 现代 刀
具材料是降低加工成本 、 获得经济效益 的关键 。
无独有偶 的是 , 上世 纪七十年代 中期 , 在美
切削加工的趋势
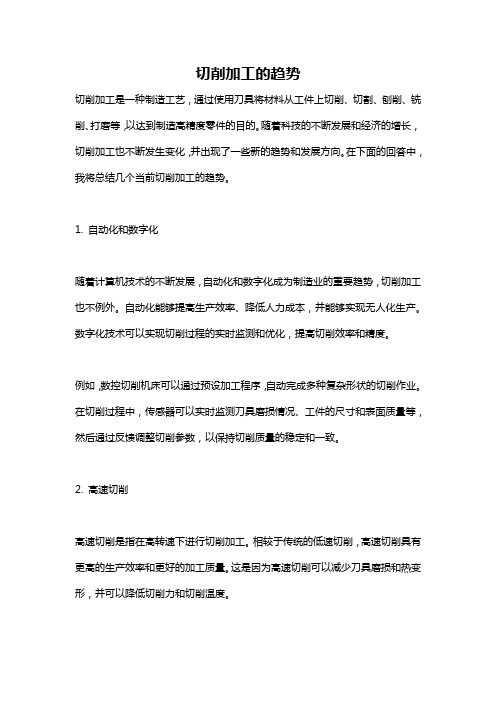
切削加工的趋势切削加工是一种制造工艺,通过使用刀具将材料从工件上切削、切割、刨削、铣削、打磨等,以达到制造高精度零件的目的。
随着科技的不断发展和经济的增长,切削加工也不断发生变化,并出现了一些新的趋势和发展方向。
在下面的回答中,我将总结几个当前切削加工的趋势。
1. 自动化和数字化随着计算机技术的不断发展,自动化和数字化成为制造业的重要趋势,切削加工也不例外。
自动化能够提高生产效率、降低人力成本,并能够实现无人化生产。
数字化技术可以实现切削过程的实时监测和优化,提高切削效率和精度。
例如,数控切削机床可以通过预设加工程序,自动完成多种复杂形状的切削作业。
在切削过程中,传感器可以实时监测刀具磨损情况、工件的尺寸和表面质量等,然后通过反馈调整切削参数,以保持切削质量的稳定和一致。
2. 高速切削高速切削是指在高转速下进行切削加工。
相较于传统的低速切削,高速切削具有更高的生产效率和更好的加工质量。
这是因为高速切削可以减少刀具磨损和热变形,并可以降低切削力和切削温度。
为了实现高速切削,需要使用高刚性和高精度的切削工具和切削机床,并需采取适当的冷却和润滑措施。
同时,需经过充分的工艺研究和刀具优化,以确保切削过程的稳定性和安全性。
3. 精密与微加工随着电子、通信和医疗器械等领域的快速发展,对零件精度和尺寸的要求也越来越高。
因此,精密和微加工成为切削加工的一个重要趋势。
精密切削加工可以实现更高的几何形状和表面质量要求,例如使用高精度的数控切削机床和刀具,尽可能减少切削力和振动。
同时,精密切削加工还需要采用高级的切削液和冷却系统,以控制和降低切削温度,并确保零件的尺寸和表面质量。
微加工是指加工微小尺寸的零件,通常具有亚毫米或微米级的尺寸和特征。
微加工的关键是精密和稳定的切削工艺,以及特殊的切削工具和切削机床。
例如,微铣削、微打磨和微铣削技术已经得到广泛应用,适用于制造光学器件、微机械系统和生物传感器等。
4. 绿色和可持续发展在面对全球环境问题和能源危机的背景下,绿色和可持续发展已经成为全球关注的焦点。
国外金属切削加工发展概况

国外金属切削加工发展概况近年来,随着全球制造业的不断发展,金属切削加工作为制造业的重要环节之一,也得到了越来越多的关注和发展。
国外金属切削加工技术在自动化、高精度、高效率等方面取得了显著的进展,在不同领域都得到了广泛应用。
一、自动化水平的提升国外金属切削加工领域的重要进展之一就是自动化水平的提升。
自动化技术的应用使得金属切削加工过程更加智能化和高效化。
例如,引入了数控技术,通过编程控制机床进行操作,大大提高了生产效率和加工精度。
同时,还出现了一些先进的自动化设备,如自动送料机、自动换刀装置等,使得整个加工过程更加连续、稳定。
二、高速切削技术的应用高速切削技术是国外金属切削加工的另一个重要发展方向。
通过提高切削速度和进给速度,可以显著缩短加工时间,提高生产效率。
同时,高速切削技术还能够减少切削力和切削温度,降低刀具磨损和加工表面质量,从而提高加工精度。
这种技术的应用已经在航空航天、汽车制造等领域得到了广泛推广。
三、多轴加工技术的发展随着复杂零件的需求不断增加,多轴加工技术成为了国外金属切削加工的热点领域。
多轴加工技术可以同时进行多个切削轴向的加工,大大提高了加工效率和精度。
例如,五轴加工中心可以在一个机床上完成五个方向的切削,适用于复杂曲面的加工。
这种技术的发展对于提高加工质量和缩短生产周期具有重要意义。
四、先进刀具材料的应用刀具材料的发展也为国外金属切削加工带来了新的突破。
先进的刀具材料,如硬质合金、陶瓷刀具等,具有高硬度、高耐磨性和高热稳定性,可以承受高速切削和高温切削的要求。
这些刀具材料的应用,不仅提高了切削效率和切削质量,还延长了刀具的使用寿命,降低了加工成本。
五、绿色化加工的推进国外金属切削加工在环保方面也取得了一些进展。
为了减少对环境的影响,国外加工企业逐渐采用环保型切削液,降低了切削液的使用量和废水的排放。
同时,还推广了无润滑切削技术,减少了切削过程中对切削液的依赖。
这些举措不仅有助于改善工作环境,还有利于可持续发展。
高速高效切削加工技术的现状及发展趋势

高速高效切削加工技术的现状及发展趋势一、前言目前,我国已成为世界飞机零部件的重要转包生产国,波音、麦道、空客等世界著名飞机制造公司都在我国转包生产从尾翼、机身、舱门到发动机等各种零部件,这些飞机零部件的加工生产必须采用先进的加工装备和加工工艺。
为此,国内各飞机制造公司均进行了大规模的技术改造,引进了大量国外先进的加工装备,使我国的飞机制造业设备的数控化率越来越高。
与此同时,大量高速、高效、柔性、复合、环保的国外切削加工新技术不断涌现,使切削加工技术发生了根本的变化。
刀具在航空航天加工领域的应用技术进入了以发展高速切削、开发新的切削工艺和加工方法、提供成套技术为特征的新阶段。
与此形成鲜明对比的是,我国的装备制造业和以制造业为主要服务对象的传统的工具工业却无法满足航空航天工业对现代制造装备和先进加工工艺的要求。
下面结合我国航空航天工业加工技术的现状及发展趋势,着重介绍我国高效、高速切削刀具的生产应用情况,对我国工具工业的发展现状和存在的问题提出自己的看法。
二、航空航天工业加工技术的现状及发展趋势1.航空结构件材料的发展趋势及其特点①以整体件为代表的铝合金结构件为了提高零件的可靠性、降低成本和减轻重量,传统的铆接结构逐步被整体薄壁的机加工结构件所代替。
这类零件由于大部分是用整体实心铝合金材料制成的薄壁、细筋结构件,70%~95%的材料要在加工中去除掉,而高速切削产生的热量少、切削力小、零件变形小,因此提高生产效率的唯一途径是采用四轴或五轴联动机床进行高速铣削加工。
②以钛基和镍基合金零件为代表的难切削材料零件由于钛(镍)合金具有比强度高、热强度好、化学活性大等特点,目前飞机发动机重要部件采用钛基和镍基合金材料的逐渐增多。
采用高速切削后,其切削速度可提高到100m/min以上,为常规切削速度的10倍。
这类材料的加工特点是:切削力大、切削温度高、加工硬化和粘刀现象严重、刀具易磨损。
③以碳纤维复合材料零件为代表的复合材料结构件复合材料现已成为新一代飞机机体结构主要材料之一,如飞机上的大型整体成形的翼面壁板、带纵墙的整体下翼面等。
超精密切削加工技术的现状与发展毕业论文

哈尔滨工业大学金属工艺学课程论文题目:超精密切削加工技术的现状与发展院系:能源学院专业:能源与动力工程专业班级:学号:姓名:超精密切削加工技术的现状与发展摘要:随着航空、航天、仪表和微电子技术的的发展,对零件的尺寸精度和形位精度及表面粗糙度的要求越来越严格,本世纪六十年代产生了超精密加工技术。
超精密切削加工是在传统切削加工的基础上,汇集了大量的新技术所形成的近年来发展较快的一项重要技术,是超精加工技术的一个重要分支。
到目前为止,超精密切削加工的尺寸精度已达到1微米以内,表面粗糙度为Ra0.001~0.002。
加工平面度低于波长的1/2以下。
具有超高精度、高刚度的机床,超精密级的切削刀具,超稳定的切削加工条件是实现超精密切削加工的先决条件。
在这里,就结合课上所学知识,对超精密切削加工技术进行详细介绍。
关键词:超精密切削加工技术;液体静压导轨;金刚石刀具;1 超精密切削加工概况超精密切削以SPDT技术开始,该技术以空气轴承主轴、气动滑板、高刚性、高精度工具、反馈控制和环境温度控制为支撑,可获得纳米级表面粗糙度。
所用刀具为大块金刚石单晶,刀具刃口半径极小,可以加工出光洁度极高的镜面。
金刚石刀具的优点在于其与有色金属亲和力小,硬度、耐磨性以及导热性都非常优越,且能刃磨得非常锋利,其刃口圆弧半径可小于0.01微米,实际应用的一般为0.05微米,可加工出优于0.01微米的表面粗糙度。
此外,超精密切削加工还采用了高精度的基础元部件(如空气轴承、气浮导轨等)、高精度的定位检测元件(如光栅、激光检测系统等)以及高分辨率的微量进给机构。
机床本身采取恒温、防振以及隔振等措施,还要有防止污染工件的装置。
机床必须安装在洁净室内。
进行超精密切削加工的零件材料必须质地均匀,没有缺陷。
在这种情况下加工无氧铜,表面粗糙度可达0.05微米。
加工直径800mm的非球面透镜,形状精度可达0.2微米。
最先用于铜的平面和非球面光学元件的加工,随后,加工材料拓展至有机玻璃、塑料制品(如照相机的塑料镜片、隐形眼镜镜片等)、陶瓷及复合材料等。
切削加工和刀具技术的现状与发展
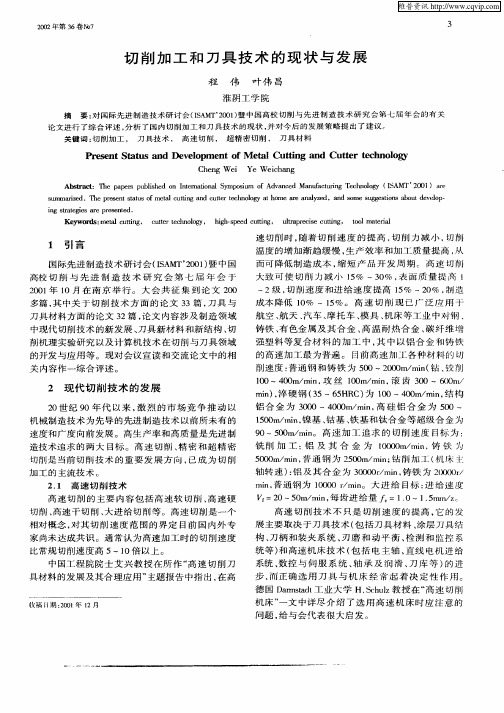
20 02年 第 3 6卷 N 7 o 3
切 削 加 工 和 刀 具 技 术 的 现 状 与 发 展
程 伟 叶 伟 昌
淮 阴工 学 院
摘 要 : 国 际 先 进 制 造 技 术 研 讨 会 (S MT 20 ) 中 国 高 校 切 削 与 先 进 制 造 技 术 研 究 会 第 七 届 年 会 的 有 关 对 IA ’0 1 暨
10m/ i. 基 、 基 、 基 和 钛 合 金 等 超 级 合 金 为 50 rn 镍 a 钴 铁 9 0~50 / n 高 速 加 工 追 求 的 切 削 速 度 目标 为 : 0 m mi。 铣 削 加 工 : 及 其 合 金 为 10 m/ n 铸 铁 为 铝 0 ̄ mi,
5 0 r/ n 普 通 钢 为 2 0 m m n 钻 削 加 工 ( 床 } 0 0n mi , 5 0 / i; 机 轴 转 速 ) 铝 及 其 合 金 为 3 0 0 / n 铸 铁 为 2 0 %- : 0 0 r mi, 00 / m n 普 通 钢 为 10 0 rm n 大 进 给 目标 : 给 速 度 i, 0 0 / i。 进 V 2 0~5 m r n 每 齿 进 给 量 =1 0~1 5m / 。 0 / i, a . .r n z
10~4 0 r n 攻 丝 10 / n 滚 齿 3 0~6)n/ 0 0 m/ i . a 0 m mi. 0 ( r 0
中现 代 切 削 技 术 的新 发 展 、 具 新 材 料 和新 结 构 、 刀 切
削 机 理 实 验 研 究 以及 计 算 机 技 术 在 切 削 与 刀 具 领 域 的开 发 与 应 用 等 。 现 对 会 议 宣 读 和 交 流 论 文 中 的相 关 内容 作 一 综 合 评 述 。
2022年行业报告我国刀具行业市场发展情况及趋势分析

我国刀具行业市场发展情况及趋势分析要实现国内刀具企业的又好又快进展,需打破现有的研发思路,从客户的角度动身,与客户一起成长,从实际需求中开发出自己的产品,而不是仅仅替代国外的刀具。
我们不仅需要有制造刀具的力量,还需要有将刀具应用到实际生产过程中的力量,这样才能真正有扎实的理论和实践基础,才能拥有自己的学问产权。
刀具制作过程中需要模具进行成型工艺,对我国的模具产业大有裨益。
我国五金刀具的高速进展,与强大的市场需求密不行分。
2022年我国国产刀具的生产总量达到了350亿元,出口刀具85亿元,同比增长21.4.按此增速计算,估计2022年刀具消费规模将达到485亿以上。
在消费的刺激下,我国的刀具生产规模正在不断扩大。
在刀具市场的推动下,我国的刀具模具的市场需求必定会得到提升,将会促进国内刀具模具产业更好进展。
刀具行业涵括了基体材质设计、涂层组织结构设计、刀具外观结构设计、专用数字化技术开发等学问领域,任一学科理论、技术的更新换代都会随之带动整个刀具行业技术系统性变化调整。
同样在生产线上,与以上技术关联的任一环节程序的微小缺失或浮动势必影响刀具产品性能指标的稳定性。
就刀具基体材料而言,成分在国内各家公司对应的牌号基本相同,硬度、密度、矫顽磁力等常规性能报告也基本全都,然而实际使用性能的反馈良莠不齐。
要打破这种“形似神不似”的尴尬,亟待对刀具研发进行系统性夯实积累,对各环节相关性探究连接,层层相符、环环相扣,从而指导实际生产,确保产品的稳定性,找到“神形兼备”的关键。
配套服务力量缺失国产刀具无法尽施其“神”高速、高效切削在航空零部件加工中,高速切削正在被大量应用,主要有以下几个缘由:(2)飞机零件的结构简单、精度高,零件的薄壁、细筋结构刚度差,要尽量削减加工中的径向切削力和热变形,只有采纳高速切削加工才能满意这些要求。
(3)难加工材料,如镍基高温合金、钛合金、高强度结构钢被现代航空产品大量采纳,这些材料强度大、硬度高,耐冲击、加工中简单硬化,切削温度高、刀具磨损严峻,属于难加工材料。
金属切削加工技术的发展与应用
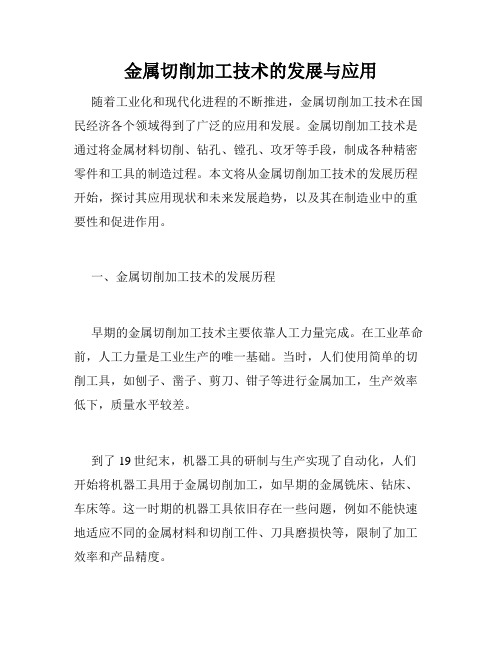
金属切削加工技术的发展与应用随着工业化和现代化进程的不断推进,金属切削加工技术在国民经济各个领域得到了广泛的应用和发展。
金属切削加工技术是通过将金属材料切削、钻孔、镗孔、攻牙等手段,制成各种精密零件和工具的制造过程。
本文将从金属切削加工技术的发展历程开始,探讨其应用现状和未来发展趋势,以及其在制造业中的重要性和促进作用。
一、金属切削加工技术的发展历程早期的金属切削加工技术主要依靠人工力量完成。
在工业革命前,人工力量是工业生产的唯一基础。
当时,人们使用简单的切削工具,如刨子、凿子、剪刀、钳子等进行金属加工,生产效率低下,质量水平较差。
到了19世纪末,机器工具的研制与生产实现了自动化,人们开始将机器工具用于金属切削加工,如早期的金属铣床、钻床、车床等。
这一时期的机器工具依旧存在一些问题,例如不能快速地适应不同的金属材料和切削工件、刀具磨损快等,限制了加工效率和产品精度。
进入20世纪,金属切削加工技术开始迎来全新的发展机遇。
随着自动化技术和计算机技术的快速发展,新一代数控机床、自动化生产线和智能化加工技术的出现,使得金属切削加工技术实现了从传统机械式到数字化、自动化、智能化的伟大飞跃,使得金属切削加工技术在制造业中的地位得到进一步巩固和提升。
二、金属切削加工技术的应用现状与未来发展趋势1、应用现状目前,金属切削加工技术被广泛应用于各个制造行业中,如飞行器、汽车、军工、机械、电子、船舶等。
它是现代工业的基础和关键技术,是制造业高质量、高效益、高附加值的重要手段。
现代金属切削加工技术具有加工精度高、生产效率高、成本低等优点,可以满足各种金属加工的需求,特别是在微细加工、高速加工、高精度加工和复杂曲面加工等方面表现出优越性。
2、未来发展趋势未来金属切削加工技术的发展,将主要集中在以下几个方面:(1) 精密加工:随着高精度和微米级等精密加工技术的不断发展,金属切削加工技术也将不断提高自己的精度和稳定性。
(2) 高速加工:高速切削加工技术将成为金属切削加工技术的重要发展方向。
2024年车刀市场发展现状
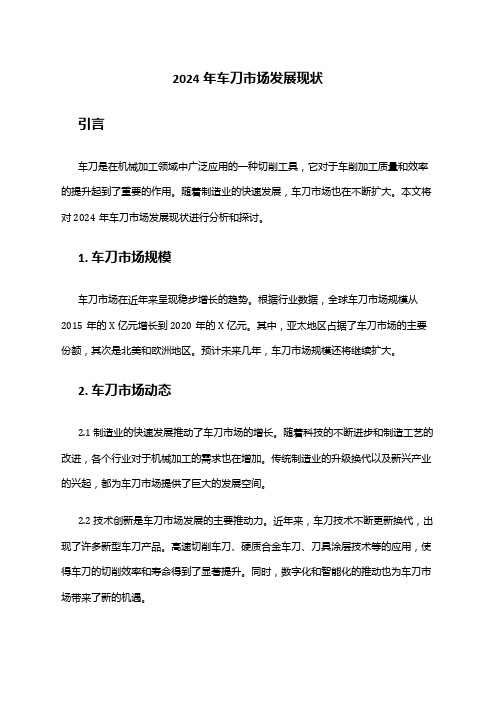
2024年车刀市场发展现状引言车刀是在机械加工领域中广泛应用的一种切削工具,它对于车削加工质量和效率的提升起到了重要的作用。
随着制造业的快速发展,车刀市场也在不断扩大。
本文将对2024年车刀市场发展现状进行分析和探讨。
1. 车刀市场规模车刀市场在近年来呈现稳步增长的趋势。
根据行业数据,全球车刀市场规模从2015年的X亿元增长到2020年的X亿元。
其中,亚太地区占据了车刀市场的主要份额,其次是北美和欧洲地区。
预计未来几年,车刀市场规模还将继续扩大。
2. 车刀市场动态2.1 制造业的快速发展推动了车刀市场的增长。
随着科技的不断进步和制造工艺的改进,各个行业对于机械加工的需求也在增加。
传统制造业的升级换代以及新兴产业的兴起,都为车刀市场提供了巨大的发展空间。
2.2 技术创新是车刀市场发展的主要推动力。
近年来,车刀技术不断更新换代,出现了许多新型车刀产品。
高速切削车刀、硬质合金车刀、刀具涂层技术等的应用,使得车刀的切削效率和寿命得到了显著提升。
同时,数字化和智能化的推动也为车刀市场带来了新的机遇。
2.3 车刀市场竞争激烈。
由于车刀市场前景广阔,吸引了众多企业进入竞争。
国内外知名车刀制造商纷纷加大研发投入,提高产品品质和技术水平。
同时,一些新兴的本土企业也在逐渐崛起,与国际巨头展开竞争。
3. 车刀市场面临的挑战3.1 市场竞争压力增大。
由于车刀市场的潜力广阔,吸引了众多企业进入。
市场竞争激烈,价格竞争十分激烈,企业需降低成本、提高产品质量以及注重品牌建设,才能在激烈的市场环境中生存和发展。
3.2 技术创新的压力不断增加。
随着科技的不断进步,客户对车刀产品的要求也在不断提高。
需要不断提高切削效率、延长刀具寿命、降低加工成本等。
企业需要加大研发投入,提升自身的技术水平和创新能力,才能在市场上保持竞争优势。
3.3 进一步开拓国际市场的挑战。
国内车刀市场规模庞大,但国内市场已经逐渐饱和,未来的增长空间有限。
要进一步扩大市场份额,企业需要加大对国际市场的开拓力度,面对不同国家和地区的市场需求和竞争。
2024年PCBN刀具市场分析现状
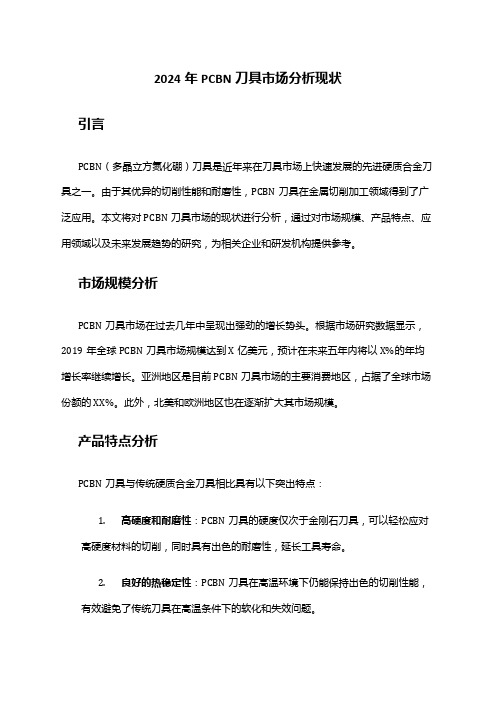
2024年PCBN刀具市场分析现状引言PCBN(多晶立方氮化硼)刀具是近年来在刀具市场上快速发展的先进硬质合金刀具之一。
由于其优异的切削性能和耐磨性,PCBN刀具在金属切削加工领域得到了广泛应用。
本文将对PCBN刀具市场的现状进行分析,通过对市场规模、产品特点、应用领域以及未来发展趋势的研究,为相关企业和研发机构提供参考。
市场规模分析PCBN刀具市场在过去几年中呈现出强劲的增长势头。
根据市场研究数据显示,2019年全球PCBN刀具市场规模达到X亿美元,预计在未来五年内将以X%的年均增长率继续增长。
亚洲地区是目前PCBN刀具市场的主要消费地区,占据了全球市场份额的XX%。
此外,北美和欧洲地区也在逐渐扩大其市场规模。
产品特点分析PCBN刀具与传统硬质合金刀具相比具有以下突出特点:1.高硬度和耐磨性:PCBN刀具的硬度仅次于金刚石刀具,可以轻松应对高硬度材料的切削,同时具有出色的耐磨性,延长工具寿命。
2.良好的热稳定性:PCBN刀具在高温环境下仍能保持出色的切削性能,有效避免了传统刀具在高温条件下的软化和失效问题。
3.优异的切削效率:PCBN刀具切削时摩擦系数低,热导率高,减少了切削区域的热积聚,提高了切削效率和加工精度。
4.广泛的应用领域:PCBN刀具适用于切削复杂的材料,如高硬度合金、淬火钢、工具钢、高速钢等,广泛应用于航空航天、汽车制造、模具加工等行业。
应用领域分析PCBN刀具在多个领域具有广泛的应用,包括但不限于以下几个方面:1.汽车制造业:PCBN刀具可以用于汽车发动机缸体、汽缸套、曲轴等零部件的加工,提高加工精度和效率。
2.模具加工:PCBN刀具可以用于模具加工过程中对高硬度材料的切削,如模具钢、硬质合金等,提高模具的使用寿命和加工质量。
3.航空航天业:PCBN刀具在航空航天制造领域的应用广泛,包括航空发动机零部件的切削加工、航空铝合金的铣削等。
4.硬质合金切削:PCBN刀具可以在切削硬质合金时提供高效、精确的加工,并且具有较长的寿命。
超精密机械制造技术研究
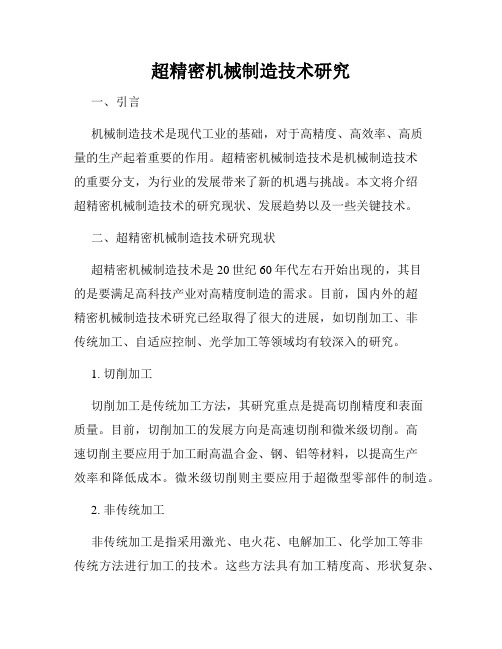
超精密机械制造技术研究一、引言机械制造技术是现代工业的基础,对于高精度、高效率、高质量的生产起着重要的作用。
超精密机械制造技术是机械制造技术的重要分支,为行业的发展带来了新的机遇与挑战。
本文将介绍超精密机械制造技术的研究现状、发展趋势以及一些关键技术。
二、超精密机械制造技术研究现状超精密机械制造技术是20世纪60年代左右开始出现的,其目的是要满足高科技产业对高精度制造的需求。
目前,国内外的超精密机械制造技术研究已经取得了很大的进展,如切削加工、非传统加工、自适应控制、光学加工等领域均有较深入的研究。
1. 切削加工切削加工是传统加工方法,其研究重点是提高切削精度和表面质量。
目前,切削加工的发展方向是高速切削和微米级切削。
高速切削主要应用于加工耐高温合金、钢、铝等材料,以提高生产效率和降低成本。
微米级切削则主要应用于超微型零部件的制造。
2. 非传统加工非传统加工是指采用激光、电火花、电解加工、化学加工等非传统方法进行加工的技术。
这些方法具有加工精度高、形状复杂、工件硬度高等优点,因此被广泛用于微机电系统(MEMS)、光学设备、半导体器件等领域。
3. 自适应控制自适应控制是指在机床加工过程中对加工条件进行自适应调节,以实现高精度、高效率的加工。
自适应控制的关键是实时采集加工过程中的信息,对加工参数进行调整以达到最优化的加工效果。
该技术适用于加工复杂曲面和超硬材料。
4. 光学加工光学加工是利用激光将能量聚焦在工件表面,以实现高精度的加工。
在光学加工中,激光的波长对加工精度有着非常重要的影响。
如在微细加工中,波长越小加工的精度越高。
目前,脉冲激光加工的加工精度已经可以达到亚微米级别。
三、超精密机械制造技术的发展趋势超精密机械制造技术的发展趋势是集成化、自动化、智能化、高速化和柔性化。
集成化技术是利用自动化技术将加工、检测、装备和控制等部分集成在一起,实现一条龙服务。
自动化技术是通过机器人等装备对加工过程进行监控和控制,以提高生产效率和加工精度。
- 1、下载文档前请自行甄别文档内容的完整性,平台不提供额外的编辑、内容补充、找答案等附加服务。
- 2、"仅部分预览"的文档,不可在线预览部分如存在完整性等问题,可反馈申请退款(可完整预览的文档不适用该条件!)。
- 3、如文档侵犯您的权益,请联系客服反馈,我们会尽快为您处理(人工客服工作时间:9:00-18:30)。
切削加工和刀具技术的现状与发展摘要:高速加工是以较快生产节拍进行加工,提高切削和进刀速度是高速加工技术的重要环节。
高速加工技术的发展涉及到零科毛坯、刀具、机床、自动控制与检测等多种技术的综合优化,需要变革传统的机加工工艺路线。
我国引进的轿车零部件数控自动生产线上已广泛应用高速加工技术,其主要目的是在确保产品质量的前提下,尽量缩短零件的机加工工艺路线,加快生产节拍(轿车发动机生产节拍已缩短为30秒),满足轿车高质量、高速率、低成本、大批量、杜会化生产的技术要求。
高速加工技术必将带动零件毛坯制造、刀具(工具)、数控机床、自动控制、在线检侧、材料等技术的发展与进步。
随着我国制造业加快融人全球化生产制造体系,预计高速加工技术将在信息化、柔性化机械加工领域得到进一步发展和推广应用。
1、引言对于机械零件而言,高速加工即是以较快的生产节拍进行加工。
一个生产节拍:零件送进--定位夹紧--刀具快进--刀具工进(在线检测)--刀具快退--工具松开、卸下--质量检测等七个基本生产环节。
而高速切削是指刀具切削刃相对与零件表面的切削运动(或移动)速度超过普通切削5~10倍,主要体现在刀具快进、工进及快退三个环节上,是高速加工系统技术中的一个子系统;对于整条生产自动线而言,高速加工技术表征是以较简捷的工艺流程、较短、较快的生产节拍的生产线进行生产加工。
这就要突破机械加工传统观念,在确保产品质量的前提下,改革原有加工工艺(方式):或采用一工位多工序、一刀多刃,或以车、铰、铣削替代磨削,或以拉削、搓、挤、滚压加工工艺(方式)替代滚、插、铣削加工…等工艺(方式),尽可能地缩短整条生产线的工艺流程;对于某一产品而言,高速加工技术也意味着企业要以较短的生产周期,完成研发产品的各类信息采集与处理、设计开发、加工制造、市场营销及反馈信息。
这与敏捷制造工程技术理念有相同之处。
2、现代切削技术的发展20世纪90年代以来,激烈的市场竞争推动以机械制造技术为先导的先进制造技术以前所未有的速度和广度向前发展。
高生产率和高质量是先进制造技术追求的两大目标。
高速切削、精密和超精密切削是当前切削技术的重要发展方向,已成为切削加工的主流技术。
高速切削技术高速切削的主要内容包括高速软切削、高速硬切削、高速干切削、大进给切削等。
高速切削是一个相对概念,对其切削速度范围的界定目前国内外专家尚未达成共识。
通常认为高速加工时的切削速度比常规切削速度高5~10倍以上。
中国工程院院士艾兴教授在所作“高速切削刀具材料的发展及其合理应用”主题报告中指出,在高速切削时,随着切削速度的提高,切削力减小,切削温度的增加渐趋缓慢,生产效率和加工质量提高,从而可降低制造成本,缩短产品开发周期。
高速切削大致可使切削力减小15%~30%,表面质量提高1~2级,切削速度和进给速度提高15%~20%,制造成本降低10%~15%。
高速切削现已广泛应用于航空、航天、汽车、摩托车、模具、机床等工业中对钢、铸铁、有色金属及其合金、高温耐热合金、碳纤维增强塑料等复合材料的加工中,其中以铝合金和铸铁的高速加工最为普遍。
目前高速加工各种材料的切削速度:普通钢和铸铁为500~2000m/min(钻、铰削100~400m/min,攻丝100m/min,滚齿300~600m/min),淬硬钢(35~65HRC)为100~400m/min,结构铝合金为3000~4000m/min,高硅铝合金为500~1500m/min,镍基、钴基、铁基和钛合金等超级合金为90~500m/min。
高速加工追求的切削速度目标为:铣削加工:铝及其合金为10000m/min,铸铁为5000m/min,普通钢为2500m/min;钻削加工(机床主轴转速):铝及其合金为30000r/min,铸铁为20000r/min,普通钢为10000r/min。
大进给目标:进给速度Vf=20~50m/min,每齿进给量fz=1.0~1.5mm/z。
高速切削技术不只是切削速度的提高,它的发展主要取决于刀具技术(包括刀具材料、涂层刀具结构、刀柄和装夹系统、刃磨和动平衡、检测和监控系统等)和高速机床技术(包括电主轴、直线电机进给系统、数控与伺服系统、轴承及润滑、刀库等)的进步,而正确选用刀具与机床经常起着决定性作用。
德国Darmstadt工业大学H.Schulz教授在“高速切削机床”一文中详尽介绍了选用高速机床时应注意的问题,给与会代表很大启发。
随着环境保护法律法规的严格实施,作为绿色制造工艺的干切削日益受到人们的高度重视。
据国外企业统计,在集中冷却加工系统中,切削液占加工总成本的14%~16%,刀具成本仅占2%~4%。
据测算,如果20%的切削加工采用干式加工,制造总成本可降低1.6%。
因此,干切削是未来切削加工的发展方向。
目前倡导的干切削并不是简单地去掉原有工艺中的切削液,也不是消极地通过降低切削参数来保证刀具使用寿命,而需要采用耐热性更好的新型刀具材料及涂层,设计合理的刀具结构与几何参数,选择最佳切削速度,形成新的工艺条件。
干切削是实现清洁高效加工的新工艺,是制造技术向高速切削发展总趋势的组成部分,也是随着人类社会进步和生产力发展而出现的新型切削方式,它的推广应用推动着刀具材料、涂层技术、机床结构、加工条件和刀具结构技术的不断发展。
目前,干切削技术在车削、镗削和铣削上的应用日益广泛,在钻削、拉削和滚齿方面也有重大突破。
上海大众汽车有限公司、上海交通大学、哈尔滨理工大学、哈尔滨工业大学等单位在“干切削及其应用”等有关论文中详细介绍了干切削的机理和实施该工艺的途径,以及采用激光辅助加工干切削、使用最少量润滑液(MQL)的准干切削(Near Dry Cutting)、用压缩空气冷风切削以及采用氮气进行干切削等加工方法。
精密和超精密切削发展尖端技术、国防工业和微电子工业都离不开通过精密和超精密加工制造的精密零件和产品。
通常将加工精度在0.1~1μm,加工表面粗糙度在Ra0.02~0.1μm的加工称为精密加工;而将加工精度高于0.1μm,加工表面粗糙度小于Ra0.01μm的加工称为超精密加工。
超精密加工可达到纳米(nm)级水平。
该领域主要包含三个分支:①精密和超精密切削加工;②精密和超精密磨削加工;③精密电子束和离子束等特种加工。
用金刚石刀具实施超精密切削已由过去只能加工铜、铝及其合金等有色金属,扩展到加工塑料、陶瓷和复合材料。
为了切除极薄切屑,要求金刚石刀具切削刃的刃口半径p极小,经精密研磨的单晶天然金刚石刀具的刃口半径p<0.05~0.1μm,研磨质量高的甚至可达几个nm,可实现纳米级切削。
超精密切削技术是一项系统工程,其实施不仅需要超精密机床设备和刀具,还要求超稳定的工作环境、超精密测量、用计算机技术进行实时检测和误差补偿、以及掌握熟练的操作技能等。
河北工业大学提出了“基于流体力学的超精密切削机理分析模型”,考虑了刀具几何形状(包括刀刃的刃口半径)及后刀面处工件弹性恢复的影响,研究了切削力的传递机理。
北京天地东方超硬材料公司在“超精密金刚石刀具研磨技术的研究”论文中探讨了金刚石的晶体定向和晶面选择,并对影响研磨效率和研磨质量的几个主要工艺因素进行了试验研究。
香港理工大学介绍了利用超精密测量技术及在加工中进行误差补偿而获得的具有亚微米级形状精度及纳米级表面粗糙度的非球面光学产品。
该校拥有亚洲地区最先进的超精密加工中心,可为香港及大陆地区的精密模具制造商、光学产品制造商及计算机制造商提供加工服务及技术支持。
黑色金属和钛合金材料的超精密切削难度较大,但近年来该技术也有较大进展。
3、刀具材料的发展刀具材料的开发与应用是本次会议的重点议题。
近十年来,随着高强度钢、高温合金、喷涂材料等难加工金属材料以及非金属材料与复合材料的应用日趋增多,现代刀具已不再局限于目前广泛使用的高速钢刀具和硬质合金刀具,陶瓷刀具、金刚石与立方氮化硼等超硬材料刀具、涂层刀具、复合材料刀具已成为今后的发展趋势,新型刀具材料的应用预示着切削效率将提高到一个新水平。
虽然目前可供使用的刀具材料品种较多,但由于高速钢(HSS)在强度、韧性、热硬性、工艺性等方面具有优良的综合性能,因此在切削某些难加工材料以及在复杂刀具(尤其是切齿刀具、拉刀和立铣刀等)制造中仍占有较大比重。
由于HSS中的主要元素钨、钴等资源紧缺,所以HSS的发展方向为:①发展各种少钨的通用型高速钢;②扩大使用各种无钴、少钴的高性能高速钢,如W6Mo5Cr4V2Al(501)、W12Mo3Cr4VCo3N(Co3N)等钢种;③推广使用粉末冶金高速钢(PM HSS)和涂层高速钢。
例如,用ERASTEEL公司生产的ASP2030 PM HSS钢加TiN涂层制造的插齿刀插削12Cr2Ni钢制齿轮时,刀具寿命比普通熔炼高速钢W6Mo5Cr4V2(M2)提高3~4倍。
高速钢是铁磁性材料,具有较高的剩磁感应和较大的矫顽磁力,而正常的切削温度不超过650℃,因此高速钢刀具可进行磁化切削。
浙江大学提交的“磁化切削研究”论文中,详细介绍了磁化原理与方法,分析比较了磁化切削与普通切削在切削力、切削功率、切削热、加工精度等方面的差别。
结果表明,磁化切削可显著改善高速钢的切削性能,延长刀具使用寿命,提高加工质量。
硬质合金刀具材料的发展主要体现在两个方面:①细晶粒(1~0.5μm)和超细晶粒(<0.5μm)硬质合金材料及整体硬质合金刀具的开发,使硬质合金的抗弯强度大大提高,可替代高速钢用于制造小规格钻头、立铣刀、丝锥等量大面广的通用刀具,其切削速度和刀具寿命远超过高速钢。
整体硬质合金刀具的使用可使原来采用高速钢刀具的大部分应用领域的切削效率显著提高。
过去细晶粒多应用于K类(WC+Co)硬质合金,近年来P类(WC+TiC+Co)和M类(WC+TiC+TaC或NbC+Co)硬质合金也向晶粒细化方向发展。
为提高硬质合金的韧性,通常采取增加Co含量的方法,由此引起的硬度降低现在可通过细化晶粒得到补偿,并可使硬质合金的抗弯强度提高到4.3GPa,已达到并超过了普通HSS钢的抗弯强度,从而改变了过去普遍认为P类硬质合金适于切削钢,而K类硬质合金只适于加工铸铁和铝等有色金属的刀具选材格局。
细晶粒硬质合金的另一优点是刀具刃口锋利,尤其适于高速切削粘而韧的材料。
②涂层技术的发展从过去只能涂覆单一的TiC、TiN涂层,已进入开发厚膜、复合和多元涂层的新阶段。
新开发的TiCN、TiAlN多元、超薄、超多层涂层与TiC、TiN、Al2O3等涂层的复合,加上新型抗塑性变形基体的应用,在改善涂层韧性、涂层与基体结合强度、涂层耐磨性方面已有重大进展,全面提高了硬质合金刀具材料的切削性能。
目前,在硬质合金可转位刀片表面涂覆金刚石的技术已获得突破,从而使硬质合金刀具不仅在加工黑色金属领域而且在加工有色金属领域的切削效率全面提高。