插件制程检验规范[1]
装配制程检验规范

乐清市莱恩科技有限公司文件编号WI/LE-PZ-03-2009版 / 次 A / 1制程检验规范页码 1 / 81、目的为了严格执行ISO9001-2008质量体系管理要求、确保制造产品符合本公司使用要求,保证生产顺利进行,特制订本规范。
2、范围公司自行生产的半成品及成品检验指导。
3、职责制程检验(IPQC检验员)负责执行检验、指导及判定,负责品质异常开立《品质异常处理单》、负责客户抱怨及制程不良的内容分析及不良查核、处理并记录。
品质部经理负责对处理结果进行核准。
4、工作内容4.1检验依据:检验图、制程检验规范4.2检验制程检验(IPQC)员首检,巡检,完工检应快速对产品进行外观、尺寸、结构、性能等的检验、试验,并做出合理合理判定。
4.3判定/标示A、 制程中产品所有检验、试验项目无任何缺陷,或存在缺陷但在允收范围内,应判定合格状态并签名确认,报部门经理核准通过后方可进行批量生产,完工产品判定合格进行标识后将物料移至QC待检区。
B、制程所有检验、试验项目存在任何一项质量缺陷,在允收范围外,应判定为不合格状态并签名确认,报部门经理核准通过后责令整改.完工品不合格进行标识后进行封样,并将物料移至不合格区或立即通知车间返工.4.5信息反馈制程所有检验、试验项目存在任何一项质量缺陷,在允收范围外,由制程检验(IPQC)员开立《品质异常处理单》报部门经理进行审批。
常规状况下,产品出现异常时品质部经理直接批准不合格处理,转发生产部、技术部,由巡检跟进处理进度及效果,特殊情况可由相关部门提出评审。
4.6质量评审制程中发现产品出现异常,但由于特殊原因有必要提出评审的参照《不合格品控制程序》.4.7检验记录制程中所有检验项目应得到真实,完好记录,并得到审批,记录保存周期为24个月。
制程通用检验标准
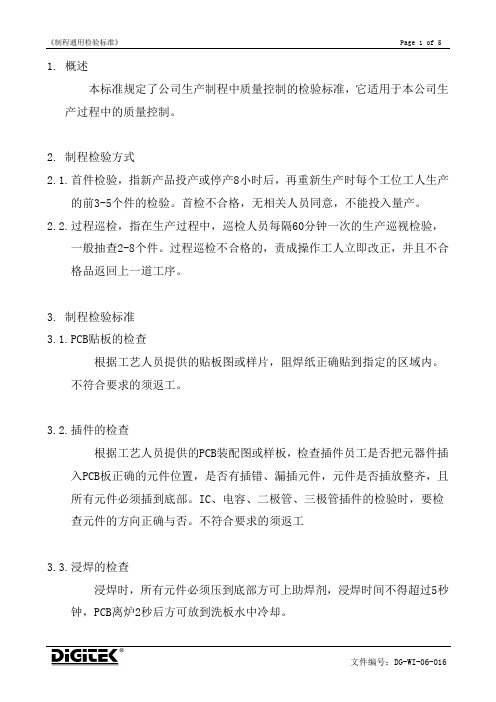
1.概述本标准规定了公司生产制程中质量控制的检验标准,它适用于本公司生产过程中的质量控制。
2.制程检验方式2.1.首件检验,指新产品投产或停产8小时后,再重新生产时每个工位工人生产的前3-5个件的检验。
首检不合格,无相关人员同意,不能投入量产。
2.2.过程巡检,指在生产过程中,巡检人员每隔60分钟一次的生产巡视检验,一般抽查2-8个件。
过程巡检不合格的,责成操作工人立即改正,并且不合格品返回上一道工序。
3.制程检验标准3.1.P CB贴板的检查根据工艺人员提供的贴板图或样片,阻焊纸正确贴到指定的区域内。
不符合要求的须返工。
3.2.插件的检查根据工艺人员提供的PCB装配图或样板,检查插件员工是否把元器件插入PCB板正确的元件位置,是否有插错、漏插元件,元件是否插放整齐,且所有元件必须插到底部。
IC、电容、二极管、三极管插件的检验时,要检查元件的方向正确与否。
不符合要求的须返工3.3.浸焊的检查浸焊时,所有元件必须压到底部方可上助焊剂,浸焊时间不得超过5秒钟,PCB离炉2秒后方可放到洗板水中冷却。
3.4.切脚的检查PCB板元件脚贴着PCB板切割整齐,不符合要求的须返工。
3.5.补焊的检查根据工艺人员提供的PCB装配图或样板,检查元件是否焊到PCB正确元件位置,是否有虚焊、连焊、漏焊、错焊。
洗板后第二次补焊,PCB上不能残留松香污迹,不符合要求的须返工。
3.6.洗板的检查超声波洗涤,根据清洗机的容量,洗板水的液面刚好能浸没PCB板,每次清洗时间为3-5分钟。
3.7.烘干的检查烘箱温度约为60℃(不超过70℃),烘干时间为15-30分钟。
3.8.装配的检查根据工艺人员提供的《作业指导书》,检查操作人员是否按《作业指导书》进行标准操作。
3.9.功能的检验(初调/复调)所有功能检查工位调试后流出的坏机,经相应修理工位修理后,须从功能检查的第一个工位开始重测,相应修理工位须做好坏机修理记录。
3.9.1.电阻(Ω)的检验接入规定的标准电阻,根据相应被测表型号的调试检验卡,输入规定的电阻值,被测表相应电阻值的读数,在误差范围内。
接插插件外观检验规范
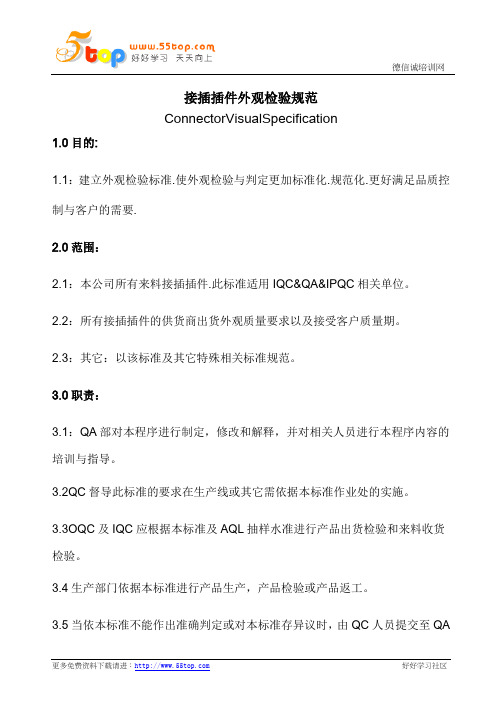
接插插件外观检验规范ConnectorVisualSpecification1.0目的:1.1:建立外观检验标准.使外观检验与判定更加标准化.规范化.更好满足品质控制与客户的需要.2.0范围:2.1:本公司所有来料接插插件.此标准适用IQC&QA&IPQC相关单位。
2.2:所有接插插件的供货商出货外观质量要求以及接受客户质量期。
2.3:其它:以该标准及其它特殊相关标准规范。
3.0职责:3.1:QA部对本程序进行制定,修改和解释,并对相关人员进行本程序内容的培训与指导。
3.2QC督导此标准的要求在生产线或其它需依据本标准作业处的实施。
3.3OQC及IQC应根据本标准及AQL抽样水准进行产品出货检验和来料收货检验。
3.4生产部门依据本标准进行产品生产,产品检验或产品返工。
3.5当依本标准不能作出准确判定或对本标准存异议时,由QC人员提交至QA工程师级以上决定。
4.0条件:4.1除特别规定外,目检时应用正常视力,在自然的光线下对产品或所抽取的样品进行检验。
4.2对于长度的测量应采用精度达0.02mm以上的测量工具,如游标卡尺,千分卡尺,显微镜等。
5.0外观检验项目及定义:5.1开口:因尺寸不良开口导致成型刮伤或无法与模腔兼容。
5.2氧化:因电镀不良或储存方式和环境不符合规范而接件金属表面附着氧化物。
5.3刮伤,碰伤。
刮花:是由操作失误或搬运引起外表面不良。
5.4高低Pin:pin的高度与规格pin高度之间产生差异。
5.5歪Pin与缺Pin:Pin偏离垂直位置,比规格所要缺少Pin。
5.6污秽:接插件表面不洁净,在运转过程中受外界环境作用产生。
5.7:镶印不良:是生产不当使产品表面所镶印的标志不清楚或不完整或深度不够。
5.8:杂色,杂质:因供货商在制程中调配不当而出不同之颜色或其它的颗粒。
5.9:缺料:塑料件未完全显出来,而导致塑料不完整。
6.0合格限度描述:6.1:开口:6.1.1接插铁壳铆压开口范围不可超过0.1mm,可以允收。
插件工序注意及检查细则
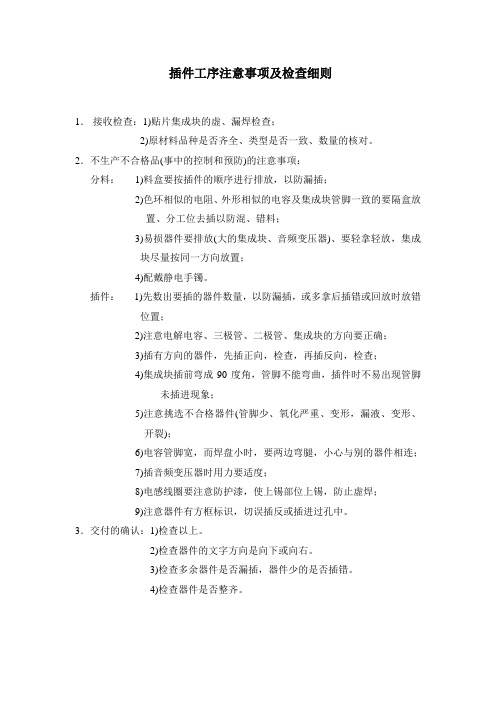
插件工序注意事项及检查细则1.接收检查:1)贴片集成块的虚、漏焊检查;2)原材料品种是否齐全、类型是否一致、数量的核对。
2.不生产不合格品(事中的控制和预防)的注意事项:分料:1)料盒要按插件的顺序进行排放,以防漏插;2)色环相似的电阻、外形相似的电容及集成块管脚一致的要隔盒放置、分工位去插以防混、错料;3)易损器件要排放(大的集成块、音频变压器)、要轻拿轻放,集成块尽量按同一方向放置;4)配戴静电手镯。
插件:1)先数出要插的器件数量,以防漏插,或多拿后插错或回放时放错位置;2)注意电解电容、三极管、二极管、集成块的方向要正确;3)插有方向的器件,先插正向,检查,再插反向,检查;4)集成块插前弯成90度角,管脚不能弯曲,插件时不易出现管脚未插进现象;5)注意挑选不合格器件(管脚少、氧化严重、变形,漏液、变形、开裂);6)电容管脚宽,而焊盘小时,要两边弯腿,小心与别的器件相连;7)插音频变压器时用力要适度;8)电感线圈要注意防护漆,使上锡部位上锡,防止虚焊;9)注意器件有方框标识,切误插反或插进过孔中。
3.交付的确认:1)检查以上。
2)检查器件的文字方向是向下或向右。
3)检查多余器件是否漏插,器件少的是否插错。
4)检查器件是否整齐。
1.接收检查:1)原材料种类、数量的核对;2)检查原材料的插针是否符合要求;3)检查插件工序转来的线路板是否缺件、错件、反向;4)器件的高低、文字方向是否一致,器件是否整齐;5)器件的管脚是否未插进去,是否插到过孔中,是否插到位;6)电感线圈的位置,注意不能浸在防护漆部位,要前向见锡。
2.不生产不合格品(事中的控制和预防)的注意事项:1)插插座时注意槽口的方向;2)每日将锡炉降为200℃进行除铜,温度控制在250℃±10℃左右;3)注意助焊剂的使用情况,松香水的浓淡;4)在浸助焊剂时线路板要用力压,且不得超过线路的上面;5)锡是否浸入到接插件或线路板上面;6)浸焊时前三块线路板要检查是否有大块连锡,或不上锡情况;7)在割腿时前三块要检查断腿情况(刀是否锋利);8)线路板卡要按序排放。
电子元器件插件工艺检验标准

元件插件工艺及检测标准一、目的:使LED电源PCB板组装(PCBA)工作人员掌握基本的电子元件操作工艺;规范电子元件在PCBA上的插件/焊锡等操作要求, 并为PCBA检验提供检查标准二、范围:适用于本公司PCBA(LED电源PCB的插件/焊锡)的工艺操作和检查。
三、参考文件:工艺要求参照:IPC-A-610B (Class Ⅱ)四、定义:PCBA: Printed CircuitBoard Assembly (印刷线路板组装)AX: (轴向)RD: Radial (径向)HT: Horizontal (卧式)VT: Vertical (立式)SMT: Surface Mount Technology (表面安装技术)SMD: Surface Mount Device(表面安装元件)SMC:Surface Mounting Components(表面安装零件)SIP: Simplein-line package 单列直插式封装SOJ:Small Outline J-leadpackage (具有J型引线的小外形封装) SOP: Small Outline package (小外形封装)SOT: Small Outline Transistor (小外形晶体管)IC:IntegratedCircuit (集成电路)PR: Preferred (最佳)AC: Acceptable (可接受的)RE:Reject (拒收)五、元件类别:电阻,电容, 电感, 二极管, 三极管, IC, ICSocket,晶体,整流器, 蜂鸣器, 插头,插针, PCB,磁珠等, 在此文件中, 根据本公司情况暂时定义电阻, 电容,电感, 二极管, 三极管,MOS管工艺标准六、元件插件工艺及检测标准1. 卧式(HT) 插元件卧式插元件主要是小功率,低容量, 低电压的电阻,电容,电感, Jumpe r(跳线),二极管, IC等,PCBA上的组装工艺要求和接收标准如下: 1.1元件在基板上的高度和斜度1.1.1轴向(AX)元件1.1.1.1功率小于1W的电阻, 电容(低电压,小容量的陶瓷材料),电感, 二极管,IC等元件PR:元件体平行于PCB板面且紧贴PCB板面, 如图示:AC:元件体与PCB表面之间最大倾斜距离(D)不大于3mm, 元件体与PCB表面最低距离(d)不大于0.7mm,如图示:RE: 元件体与PCB板面距离D>3mm, 或d>0.7mm1.1.1.2耗散功率大于或等于1W的元件PR: 元件体平行于PCB板面且与PCB板面之间的距离D≥1.5mm,如图示:AC:元件体与PCB板面之间的距离D≥1.5mm, 元件体与PCB板面的平行不作要求RE: 元件体与PCB板面之间的距离D≤1.5mm1.1.1.3ICPR: 元件体平行于PCB, IC引脚全部插入焊盘中, 引脚突出PCB面1.mm,倾斜度=0, 如图示:AC:IC引脚全部插入焊盘中, 引脚突出PCB面大于0.5mm, 如图:RE: IC引脚突出PCB面小于0.5mm, 或看不见元件引脚, 如图:1.1.2径向(RD)元件(电容, 晶振)PR: 元件体平贴于PCB板面,如图示:AC:元件脚最少有一边贴紧PCB板面,如图示:RE:元件体未接触PCB板面,如图示:1.2元件的方向性与基板对应符号的关系:1.2.1 轴向(AX)无极性元件(电阻,电感, 小陶瓷电容等)PR: 元件插在基板中心标记且元件标记清晰可见,元件标记方向一致(从左到右,从上到下), 如图:AC: 元件标记要求清晰,但方向可不一致, 如图:RE: 元件标记不清楚或插错孔位, 如图:1.2.2轴向(AX)有极性元件, 如二几管, 电解电容等PR: 元件的引脚插在对应的极性脚位, 元件标记清晰可看见,如图:AC:元件的引脚必须插在相应的极性脚位上,元件标记可看见, 如图:RE: 元件的引脚未按照极性方向插在相应的脚位上, 如图:1.3元件引脚成形与曲脚1.3.1引脚成形PR: 元件体或引脚保护层到弯曲处之间的距离L>0.8mm, 或元件脚直径弯曲处无损伤,如图:A元件脚直径或厚度( D半径( R )/T )≤0.8mm 1 X D0.8~1.2mm 1.5X D≥1.2mm 2 X DRE: ( 1) 元件体与引脚保护弯曲处之间L<0.8mm,且弯曲处有损伤, 如图:( 2) 或元件脚弯曲内径R小于元件直径, 如图:1.3.2屈脚PR: 元件屈脚平行于相连接的导体,如图:AC:屈脚与相间的裸露导体之间距离(H)大于两条非共通导体间的最小电气间距, 如图:RE: 屈脚与相间的裸露导体之间距离(H)大于两条非共通导体间的最小电气间距,如图:1.4元件损伤程度1.4.1元件引脚的损伤PR: 元件引脚无任何损伤, 弯脚处光滑完好, 元件表面标记清晰可见, 如图:AC: 元件引脚不规则弯曲或引脚露铜,但元件或部品引脚损伤程度小于该引脚直径的10%,如图:RE:( 1 )元件引脚受损大于元件引脚直径的10%,如图:(2)严重凹痕锯齿痕,导致元件脚缩小超过元件的10%,如图:1.4.2 IC元件的损伤PR: IC 元件无任何损伤, 如图:AC: 元件表面受损, 但未露密封的玻璃,如图:RE:元件表面受损并露出密封的玻璃, 如图:1.4.3轴向(AX)元件损伤PR: 元件表面无任何损伤,如图:AC:元件表面无明显损伤,元件金属成份无暴露,如图:RE:(1 )元件面有明显损伤且绝缘封装破裂露出金属成份或元件严重变形,如图:(2 )对于玻璃封装元件,不允许出现小块玻璃脱落或损伤.1.5元件体斜度PR:元件体与其在基板上两插孔位组成的连线或元件体在基板上的边框线完全平行,无斜度,如图:AC:元件体与其在基板上两插孔位组成的连线或元件体在基板上的边框线斜度≤1.0mm,如图:RE: 元件体与其在基板上两插孔位组成的连线或元件体在基上的边框线斜度>1.0mm,如图:2.立式(VT)插元件2.1.1轴向(AX)元件PR: 元件体与PCB板面之间的高度H在0.4mm-1.5mm之间, 且元件体垂直于PCB板面, 如图:AC: H在0.4-3mm之间, 倾斜Q<15°,如图:RE: 元件体与PCB板面倾斜, 且间距H<0.4mm或H>3mm或Q>15°.2.1.2径向(RD)元件2.1.2.1引脚无封装元件PR: 元件体引脚面平行于PCB板面, 元件引脚垂直于PCB板面,且元件体与PCB板面间距离为0.25-2.0mm, 如图:AC: 元件体与PCB板面斜倾度Q小于15°, 元件体与PCB板面之间的间隙H在0.20-2.0mm之间,三极管离板面高度最高大于4.0mm,如图:RE: 元件与PCB板面斜倾角Q>15°或元件体与PCB板面的间隙H>2.0mm或三极管>4.0mm.2.1.2.2:引脚有封装元件PR: 元件垂直PCB板面,能明显看到封装与元件面焊点间有距离,如图:AC:元件质量小于10g且引脚封装刚好触及焊孔且在焊孔中不受力,而焊点面的引脚焊锡良好(单面板), 且该元件在电路中的受电压<240VAC或DC,如图:RE: 引脚封装完全插入焊孔中,且焊点面焊锡不好,可看见引脚封装料, 如图:2.2元件的方向性与基板符号的对应关系2.2.1轴向(AX)元件PR: 元件引脚插入基板时,引脚极性与基板符号极性完全吻合一致,且正极一般在元件插入基板时的上部,负极在下部,如图:AC:元件引脚插入基板时,引脚极性与基板符号极性吻合一致,但元件在插入基板时,正极在上和负极在下不作要求,如图:RE: 元件引脚插入基板时,引脚极性与基板符号极性刚好相反,如图:2.2.2径向(RD)元件AC: 元件引脚极性与基板符号极性一致,如图:RE: 元件体引脚极性与基板符号极性相反,如图:2.3元件引脚的紧张度PR:元件引脚与元件体主轴之间夹角为0°(即引脚与元件主轴平行, 垂直于PCB板面), 如图:AC: 元件引脚与元件体主轴袒闪角Q<15°,如图:RE: 元件引脚与元件体主轴之间夹角Q>15°.2.4元件引脚的电气保护在PCBA板上有些元件要有特殊的电气保护,则通常使用胶套,管或热缩管来保护电路PR:元件引脚弯曲部分有保护套,垂直或水平部分如跨过导体需有保护套且保护套距离插孔之间距离A为1.0mm-2.0mm,如图:AC: 保护套可起到防止短路作用, 引脚上无保护套时, 引脚所跨过的导体之间的距离B≥0.5mm, 如图:RE: 保护套损坏或A>2.0mm时, 不能起到防止短路作用或引脚上无保护套时,或引脚所跨过的导体之间距离B<0.5mm,如图:2.5元件间的距离PR: 在PCBA板上,两个或以上踝露金属元件间的距离要D≥2.0mm,如图:AC: 在PCBA板上, 两个或以上踝露金属元件的距离最小D≥1.6mm, 如图:RE: 在PCBA板上, 两个或以上踝露金属元件间的距离D<1.6mm,如图:2.6元件的损伤PR:元件表面无任何损伤,且标记清晰可见,如图:AC: 元件表面有轻微的抓、擦、刮伤等,但未露出元件基本面或有效面,如图:RE: 元件面受损并露出元件基本面或有效面积,如图:3. 插式元件焊锡点工艺及检查标准3.1单面板焊锡点单面板焊锡点对于插式元件有两种情形:a.元件插入基板后需曲脚的焊锡点b.元件插入基板后无需曲脚(直脚)的焊锡点3.1.1标准焊锡点之外观特点A.焊锡与铜片, 焊接面, 元件引脚完全融洽在一起, 且可明显看见元件脚B. 锡点表面光滑,细腻, 发亮C. 焊锡将整个铜片焊接面完全覆盖,焊锡与基板面角度Q<90°, 标准焊锡点如图示:3.1.2可接受标准A. 多锡焊接时由于焊锡量使用太多,使零件脚及铜片焊接面均被焊锡覆盖着,使整个锡点象球型,元件脚不能看到.AC:焊锡点虽然肥大Q>90°,但焊锡与元件脚,铜片焊接面焊接良好,焊锡与元件脚,铜片焊接面完全融洽在一起,如图:RE:焊锡与元件引脚, 铜片焊接状况差,焊锡与元件脚/铜片焊接面不能完全融洽在一起,且中间有极小的间隙, 元件引脚不能看到, 且Q>90°,如图:B. 上锡不足(少锡)焊锡、元件引脚、铜片焊接面在上锡过程中,由于焊锡量太少,或焊锡温度及其它方面原因等造成的少锡.AC: 整个焊锡点,焊锡覆盖铜片焊接面≥75%, 元件脚四周完全上锡,且上锡良好,如图:RE: 整个焊锡点, 焊锡不能完全覆盖铜片焊接面<75%,元件四周亦不能完全上锡,锡与元件脚接面有极小的间隙, 如图:C. 锡尖AC: 焊锡点锡尖, 只要该锡尖的高度或长度h<1.0mm,而焊锡本身与元件脚、铜片焊接面焊接良好,如图:RE: 焊锡点锡尖高度或长度h≥1.0mm,且焊锡与元件脚、铜片焊接面焊接不好, 如图:D. 气孔AC: 焊锡与元件脚、铜片焊接面焊接良好, 锡点面仅有一个气孔且气孔要小于该元件脚的一半, 或孔深<0.2mm,且不是通孔, 只是焊锡点面上有气孔, 该气孔没有通到焊接面上, 如图:RE:焊锡点有两个或以上气孔,或气孔是通孔, 或气孔大于该元件脚半径,如图:D. 起铜皮AC: 焊锡与元件脚、铜片焊接面焊接良好,但铜皮有翻起h<0.1mm,且铜皮翻起小于整个Pad位的30%, 如图:RE:焊锡与元件脚、铜片焊接面焊接一般, 但铜皮翻起h>0.1mm,且翻起面占整个Pad位的的30%以上, 如图:E. 焊锡点高度对焊锡点元件脚在基板上的高度要求以保证焊接点有足够的机械强度AC: 元件脚在基板上高度0.5<h≤2.0mm, 焊锡与元件脚,铜片焊接面焊接良好,元件脚在焊点中可明显看见, 如图:RE: 元件脚在基板上的高度h<0.5mm或h>2.0mm,造成整个锡点为少锡, 不露元件脚, 多锡或大锡点等不良现象,如图:注:对用于固定零件之插脚如变压器或接线端子之插脚高度可接受2.5mm为限.3.1.3不可接受的缺陷焊锡点在基板焊锡点中有些不良锡点绝对不可接收, 现列举部分如下RE: ( 1)冷焊(假焊/虚焊)如图:(2 )焊桥(短路),锡桥,连焊,如图:( 3 )溅锡, 如图:( 4 )锡球, 锡渣,脚碎,如图:(5) 豆腐渣,焊锡点粗糙, 如图:( 6 ) 多层锡, 如图:( 7)开孔(针孔),如图:3.2双面板焊锡点双面板焊锡点同单面板焊锡点相比有许多的不同点:a.双面板之PAD位面积较小(即外露铜片焊接面积)b.双面板每一个焊点PAD位都是镀铜通孔鉴于此两点, 双面板焊锡点在插元件焊接过程及维修过程就会有更高要求, 其焊锡点工艺检查标准就更高, 下面将分别详细讨论双面板之焊锡点收货标准3.2.1标准焊锡点之外观特点A.焊锡与元件脚,通孔铜片焊接面完全融洽在一起, 且焊点面元件脚明显可见.B.元件面和焊点面的焊锡点表面光滑, 细腻, 发亮.C.焊锡将两面的Pad位及通孔内面100%覆盖, 且锡点与板面角度Q<90°, 如图:3.2.2可接收标准A.多锡焊接时由于焊锡量过多,使元件脚,通孔, 铜片焊接面完全覆盖,不是使焊接时的两面元件脚焊点肥大, 焊锡过高AC:焊锡点元件面引脚焊锡虽然过多,但焊锡与元件脚,通孔铜片焊接面两面均焊接良好, 且Q<90°,如图:RE:焊锡点元件面引脚肥大, 锡点面引脚锡点肥大,不能看见元件脚且焊锡与元件脚, 铜片焊接面焊接不良, 如图:B.上锡不良AC: 焊锡与元件脚,通孔铜片焊接面焊接良好, 且焊接锡在通孔铜片内的上锡量高度h>75%·T(T: 基板厚度),从焊点面看上锡程度大于覆盖元件脚四周(360°)铜片的270°, 或从元件面能清楚的看到通孔铜片中的焊锡, 如图:RE:从焊点面看, 不能清晰的看到元件引脚和通孔铜片焊接面中的焊锡或在通孔铜片焊接面完全无焊锡或元件引脚到Pad位无焊锡或h<75%·T或上锡角度Q<270°(针对SolderPad360°而言),如左图:C. 锡尖在焊接过程中由于焊锡温度过低或焊接时间过长等原因造成的锡尖AC: 焊锡点的锡尖高度或长度h<1.0mm,而焊锡本身与元件引脚及通孔铜片焊接面焊接良好,Q<90°,如图:RE:焊锡点锡尖高度或长度h≥1.0mm,且焊锡与元件引脚, 通孔铜片焊接面焊接不良, 如图:D.气孔AC:焊锡与元件脚,铜片焊接面焊接良好, 锡点面仅有一个气孔且气孔要小于该元件脚的1/2, 且不是通孔(只是焊锡点表面有气孔,未通到焊接面上), 如图:RE:焊锡点上有两个或以上气孔, 或气孔是通孔, 或气孔大于该元件脚直径的1/2,焊点面亦粗糙,如图:E.起铜皮AC: 焊锡点与元件脚, 通孔铜片焊接面焊接良好, 但铜皮翘起高度h<0.1mm,翘起面积S<30%·F (F为整个焊盘的面积)RE: 焊锡与元件脚, 通孔铜片焊接面焊接质量一般,但铜皮翘起h>0.1mm, 且翘起面积S>30%·F(F为整个焊盘的面积),如图:F.焊接点高度PR:元件脚在焊锡点中明显可见, 引脚露出高度h=0.1mm,且焊锡与元件脚,通孔铜片焊接面焊接良好,如图:AC: 元件脚露出基板的高度0.5mm<h≤2.0mm,元件脚在焊锡点中可明显看见, 且焊锡与元件脚,通孔铜片焊接面焊接良好. (但对于通孔铜片焊接面的双面PCB板, 基板厚度T>2.3mm, 则元件脚露出基板高度可接收0<h≤0.5mm),如图:RE:元件脚露出基板高度h<0.5mm或h>2.0mm (仅对于厚度T≤2.3mm的双面板), 造成整个锡点为少锡, 不露元件脚, 多锡或大锡点等不良现象,且焊接不良,如图:3.2.3 不可接收的缺陷焊锡点:在双面板(镀铜通孔铜片焊接面)焊锡点中,有些不良焊点绝对不可接收, 其不可接收程度完全同于单面板,详细请参考3.1.3。
直插件焊接检验规范书
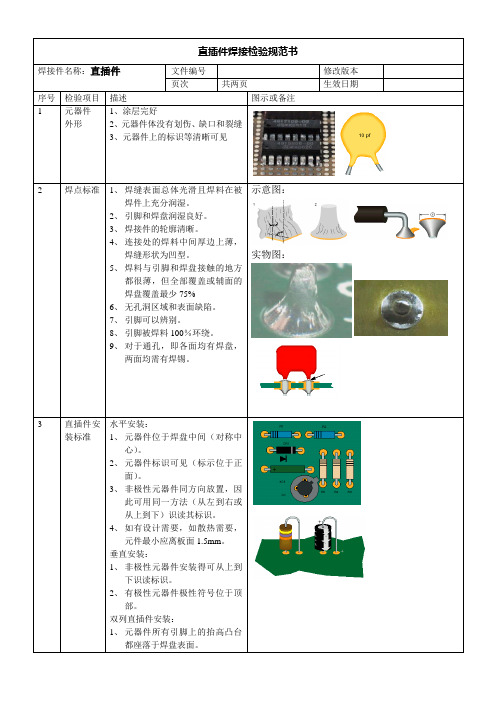
直插件焊接检验规范书焊接件名称:直插件文件编号修改版本页次共两页生效日期序号检验项目描述图示或备注1 元器件外形1、涂层完好2、元器件体没有划伤、缺口和裂缝3、元器件上的标识等清晰可见2 焊点标准1、焊缝表面总体光滑且焊料在被焊件上充分润湿。
2、引脚和焊盘润湿良好。
3、焊接件的轮廓清晰。
4、连接处的焊料中间厚边上薄,焊缝形状为凹型。
5、焊料与引脚和焊盘接触的地方都很薄,但全部覆盖或辅面的焊盘覆盖最少75%6、无孔洞区域和表面缺陷。
7、引脚可以辨别。
8、引脚被焊料100%环绕。
9、对于通孔,即各面均有焊盘,两面均需有焊锡。
示意图:实物图:3 直插件安装标准水平安装:1、元器件位于焊盘中间(对称中心)。
2、元器件标识可见(标示位于正面)。
3、非极性元器件同方向放置,因此可用同一方法(从左到右或从上到下)识读其标识。
4、如有设计需要,如散热需要,元件最小应离板面1.5mm。
垂直安装:1、非极性元器件安装得可从上到下识读标识。
2、有极性元器件极性符号位于顶部。
双列直插件安装:1、元器件所有引脚上的抬高凸台都座落于焊盘表面。
2、 引线伸出量满足要求。
4 引脚凸出引脚伸出量不能违反最小导体间距的要求,不能因引脚折弯而引起焊点损坏,或在随后的工序操作、环境操作中刺穿防静电袋,不能影响后续装配。
引脚凸出焊盘在最大和最小引脚之内;最大为 2.3mm ,最小为0.6mm ,一般标准为1--1.5mm 。
4元器件固定对于水平安装的元器件,若需要粘结,粘接长度至少为元器件长度的50%;粘接高度为元器件直径的25%。
粘接胶堆集不超过元器件直径的50%。
安装表面存在粘接胶,粘结胶大致位于元器件体中部。
对于垂直安装的元器件,若需要粘结,粘接高度至少超过引线的高度,圆周粘接范围至少达到50%。
安装表面存在粘接胶。
5检查方法 1、 用双手举板检查与放大镜检查。
2、 把板倾斜45°,并保持离眼睛30cm 距离,检查整体外观;放大镜抽检焊点。
插件工艺检验标准
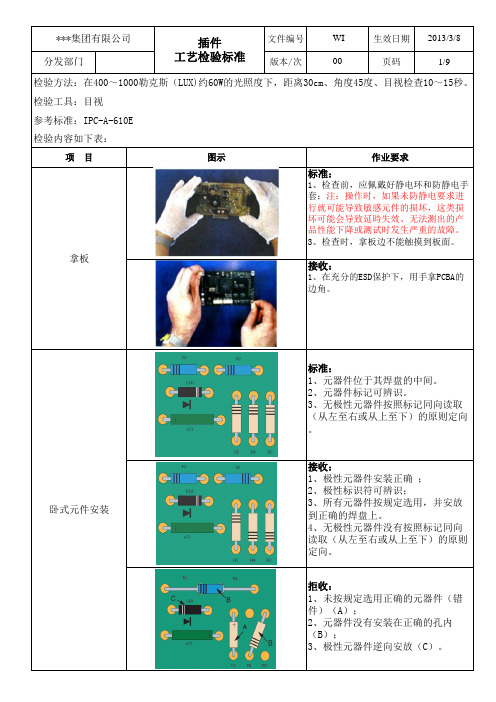
文件编号生效日期2013/3/8版本/次页码1/9标准:1、元器件位于其焊盘的中间。
2、元器件标记可辨识。
3、无极性元器件按照标记同向读取(从左至右或从上至下)的原则定向。
接收:1、极性元器件安装正确 ;2、极性标识符可辨识;3、所有元器件按规定选用,并安放到正确的焊盘上。
4、无极性元器件没有按照标记同向读取(从左至右或从上至下)的原则定向。
卧式元件安装拒收:1、未按规定选用正确的元器件(错件)(A);2、元器件没有安装在正确的孔内(B);3、极性元器件逆向安放(C)。
WI 检验方法:在400~1000勒克斯(LUX)约60W的光照度下,距离30cm、角度45度、目视检查10~15秒。
标准:1、检查前,应佩戴好静电环和防静电手套;注:操作时,如果未防静电要求进行就可能导致敏感元件的损坏,这类损坏可能会导致延時失效、无法测出的产品性能下降或测试时发生严重的故障。
3、检查时,拿板边不能触摸到板面。
项 目图示作业要求***集团有限公司插件工艺检验标准00分发部门检验工具:目视检验内容如下表:参考标准:IPC-A-610E 拿板接收:1、在充分的ESD保护下,用手拿PCBA的边角。
负极2、元器件引线的角度不会导致违反最小电气间隙。
凹白层圆标准:1、引线末端与板面平行,沿着与焊盘相连的导体的方向弯折。
接收:1、弯折的引线不违反与非公共导体间的最小电气间隙(C);2、伸出焊盘的长度(L)不大于类似的直插引线的长度。
拒收:1、引线朝向非公共导体弯折并违反最小电气间隙(C)。
标准:1、引线和孔壁呈现360°的润湿。
元件焊接连接器/插座的安装标准:1、连接器与板面平贴。
2、引线伸出满足要求。
3、板销(如果有)完全插入/扣住板子。
标准:1、焊料填充与绝缘层之间有1倍线径的间隙。
拒收:1、焊接连接内可看到绝缘层。
标准:1、焊料填充与绝缘层之间有1倍线径的间隙。
拒收:1、焊接连接内可看到绝缘层。
涂有绝缘引脚的器件焊接缺口方向反向拒收:1.插件孔堵塞拒收:1、PCB板线路断开(开路)板面焊点PCB板外观拒收:1、元件之间没有铜皮相连,但却有锡相连,电路短路或叫桥连。
制程检验规范

产品(半成品、成品).3.2全检:对制程中的产品或产品的某些检验项目进行100%检验。
3.3巡检:指对生产过程中影响产品品质的因素进行随机抽样检验、确认。
4.职责4.1品管部4。
1.1 负责制程中产品外观、检验流程、检验标准、检验规范、检验站的编制和设置.4.1。
2 IPQC:负责对产品、物料首件确认的主导工作,并对产品首件做出合格与否的判定;制程品质检控,品质异常之追踪与确认;主导不合格品或异常品管问题的提出、跟进、落实、效果确认.4。
1.3 FQC:负责制程中产品外观、产品指定项目的全检。
4.1.4 测试员:负责制程中产品接地、耐压、点亮的全检4。
2工程部4.2.1 参与新产品、试产、设计变更首件的确认,负责制程中产品电气、结构、功能、测试标准,品质异常、不合格品原因的分析及改善对策的提出。
4.2.2 负责制程中产品SOP的制定,工装夹具制作,工艺跟进改善,产能效率的提升,结构性能异常的跟进与落实。
4。
2。
3 负责制程中仪器、设备测试规范的制定;机器、设备、仪器、仪表、治夹具、工具运行状况的监控,设备的正常运转的巡视及日常保养工作监管。
4。
3 业务部:参与新客户第一次生产及客户要求变更后首次生产时首件的确认.4.4 生产部4。
4.1 负责首件的制作与送样确认,自验互检。
4.4.2 制程中5M1E 的落实及制造过程的监控,配合IPQC与PIE的工作;品质异常的受理与改善,改善对策的具体实施。
5.作业内容5.1生产、检验前作业准备5.1.1生产部门5。
1.1.1生产部门在开拉生产前进行自我核查,发现不合格品及异常,采取措施立即纠正,再行生产。
5.1.1。
2 生产部门开拉生产前需查核领用物料是否与制令工单相符,是否有相应的BOM、或样品,工作环境是否符合产品生产需求,各作业工站是否悬挂相应的SOP,人员对作业方法、产品品质是否清楚了解。
【首件确认报告】、【耐压/极性测试记录表】5。
1.1.3 机器、设备、作业工具是否处于正常状态,风批、电批扭力设置是否正确符合作业需求.5。
制程检验规范(1)

规范文件
文件编号: 版次: 页次:
制程检验作业规范
6.7.1 良品退料:经过外观及性能检验合格,标识准确无误的良品物料,将贴上“良品退料” 的合格标贴后,IPQC员在生产线开具的《退料单》上确认签字后,予以良品退料。 6.7.2 不良品退料: 经过外观及性能检验不合格,标识准确无误的不良品物料,将贴上“不良 品退料”的不合格标贴标识清楚,不同供应商的不良品退料要用不同的外卡通包装,且 须分析其不良原因与《不良品退料单》上原因相符, 并判定准确无误后,IPQC员在生 产线开具的《退料单》上签字(有特殊原因的须在不良原因中作特别注明)后,予以 不良品退料。 6.8 数据分析及总结 6.8.1 IPQC员每天及时负责收集、整理、查核生产线《生产全检记录表》、《生产线老化 记录表》等品质记录报表, 经生产线管理人员签字确认后、送交品质主管审核后, 进行数据分析,以便考察目标合格率完成状况,然后予以存档。 6.8.2 及时将生产过程中所发生的各种品质状况记录于工作笔记中,并将信息传达于该产 品检验之相关人员知悉。 6.8.3 关闭、清点、整理检验所使用的仪器、设备,治、工、夹具,摆放在适当区域,做 好6S的维护工作。 7 记录表单 7.1 《首检记录表》 7.2 《巡检记录表》 7.3 《生产线老化记录表》 7.4 《品质异常处理单》
规范文件
文件编号: 版次2 巡回检查中的控制点依相关工序确定,所有控制点的检查项目及其检查结果必须记录 于相关制程巡检记录表内,呈品质组长签核。生产过程中因人员、场所变更时,需确 保操作人员能了解作业要求,同时对现场一些孤立的作业场所、孤立的作业人员, IPQC需作重点监控 6.4.3 生产过程中由于零件缺损或其他原因造成材料短缺而需补尾数时,须在生产拉不生产 其他产品的情况下进行补尾数作业,且其材料上线前须经由多能工实施全检,并通知 IPQC确认合格后方可投入生产,IPQC需对尾数的生产进行全程跟进,并在验证尾数合 格后签名确认。 6.4.4 巡回检查中如发现不合格品时需依《不合格品控制程序》处理,如发生品质异常时则 需开立《异常跟踪表》,要求相关部门解决。 6.4.5 对于检验中发现不合格且经品管判定需重工处理时,由生产单位进行返工,IPQC全程 跟进返工状况并对返工品进行复检。 6.4.5 巡回检查中IPQC需对生产单位作业指导书及相关测试标准之悬挂状况进行管控,并需 对操作人员之作业动作进行监督,对于违规作业者须及时提出纠正并视具体情况作其 他相应处理。 6.5 生产老化测试 6.5.1 在正常情况下,所有产品需进行老化测试(包括产出半品时和制成成品后)。 6.5.2 老化时间: 大功率产品老化时间最少为24小时,其中成品老化部分不小于8小时 小功率产品老化时间最少为18小时,其中成品老化部分不小于6小时 对于充电式产品可不全做老化测试,但应抽取10~20pcs作相应的完全充电和放电测试 开关冲击测试:可以不全做,但须抽10--20pcs做冲击测试(通45s关15s),不低 于1000次 若有客户特殊要求者,按客户要求进行相关老化。 6.6 异常处理 6.6.1 当在巡检过程中,若出现重大品质异常,不良率超过20%,导致大批量不良品或无法生 产时,IPQC员必须及时知会生产线现场管理人员和PE/QE工程师予以现场处理,并根据 实际情况,提出停拉申请, 并知会相关部门责任人员解决;待问题改善后,通知生产线 复产,并跟踪改善效果。 6.6.2 其它异常参照《不合格处理程序》执行。 6.7 退料检查
制程检验规范及标准
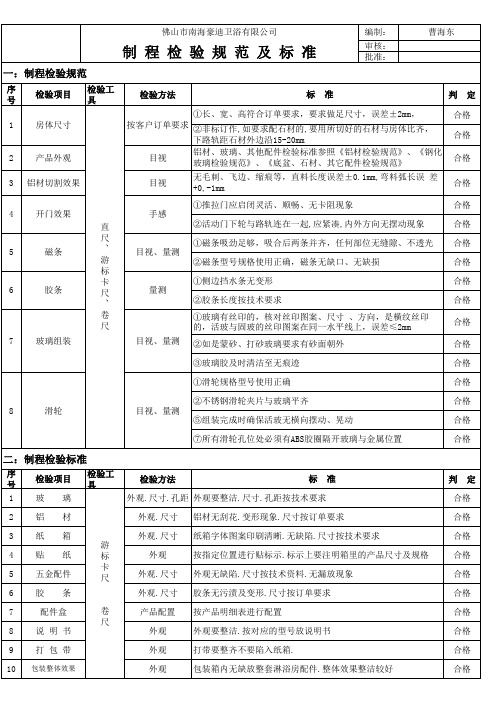
合格 合格 合格 合格 合格 合格 合格 合格 合格 合格 合格 合格 合格 合格 合格 合格 合格
2 3
产品外观 铝材切割效果
目视 目视
5
磁条
6
胶条
7
玻璃组装
二:制程检验标准
序号 1 2 3 4 5 6 7 8 9 10 检验项目 玻 铝 纸 贴 璃 材 箱 纸 游 标 卡 尺 检验工具 检验方法 标 准 判 定
合格 合格 合格 合格 合格 合格 合格 合格 合格 合格
五金配件 胶 条
配件盒 说 明 书 打 包 带
包装整体效果
外观.尺寸.孔距 外观要整洁.尺寸.孔距按技术要求 外观.尺寸 外观.尺寸 外观 外观.尺寸 外观.尺寸 卷 尺 产品配置 外观 外观 外观 铝材无刮花.变形现象.尺寸按订单要求 纸箱字体图案印刷清晰.无缺陷.尺寸按技术要求 按指定位置进行贴标示.标示上要注明箱里的产品尺寸及规格 外观无缺陷.尺寸按技术资料.无漏放现象 胶条无污渍及变形.尺寸按订单要求 按产品明细表进行配置 外观要整洁.按对应的型号放说明书 打带要整齐不要陷入纸箱. 包装箱内无缺放整套淋浴房配件.整体效果整洁较好
佛山市南海豪迪卫浴有限公司
编制: 审核: 批准:
:制程检验规范
序号 1 检验项目 房体尺寸 检验工具 检验方法 按客户订单要求 标 准
判
定
①长、宽、高符合订单要求,要求做足尺寸,误差±2mm, ②非标订作,如要求配石材的,要用所切好的石材与房体比齐, 下路轨距石材外边沿15-20mm 铝材、玻璃、其他配件检验标准参照《铝材检验规范》、《钢化 玻璃检验规范》、《底盆、石材、其它配件检验规范》 无毛刺、飞边、缩痕等,直料长度误差±0.1mm,弯料弧长误 差 +0,-1mm ①推拉门应启闭灵活、顺畅、无卡阻现象 4 开门效果 直 尺 、 游 标 卡 尺 、 卷 尺 手感 ②活动门下轮与路轨连在一起,应紧凑,内外方向无摆动现象 ①磁条吸劲足够,吸合后两条并齐,任何部位无缝隙、不透光 目视、量测 ②磁条型号规格使用正确,磁条无缺口、无缺损 ①侧边挡水条无变形 量测 ②胶条长度按技术要求 ①玻璃有丝印的,核对丝印图案、尺寸 、方向,是横纹丝印 的,活玻与固玻的丝印图案在同一水平线上,误差≤2mm 目视、量测 ②如是蒙砂、打砂玻璃要求有砂面朝外 ③玻璃胶及时清洁至无痕迹 ①滑轮规格型号使用正确 ②不锈钢滑轮夹片与玻璃平齐 8 滑轮 目视、量测 ⑤组装完成时确保活玻无横向摆动、晃动 ⑦所有滑轮孔位处必须有ABS胶圈隔开玻璃与金属位置
PCB插件、焊接检验标准

PCB插件、焊接检验标准一、目的规范本公司生产的半成品检验,确保产品质量要求,防止不良品流出。
二、范围适用于本公司内所有半成品板的外观检验和特性检验。
三、检验要求3.1 安装元器件准位要求3.1.1 元器件引线成形元器件引线成形要求同类元件保持高度一致,成形元器件两端余量一致。
元器件引脚同焊盘引脚对应整齐,无明显倾斜。
元器件引线不允许出现超过引线截面积10%的缺口或变形。
外露基体金属不超过引线可焊表面面积的5%。
(GBT19247.1-2003;6.4)引线从元器件本体或弯曲半径前的容焊点的伸出长度,至少应为引线直径或厚度,不能小于0.8mm。
(GBT19247.3-2003;4.2.3)如图1:最大引线直径/mm 最小弯曲半径R<0.8 直径/厚度0.8~1.2 1.5倍直径/厚度>1.2 2倍直径/厚度图1 引线弯曲引线成形要求应使元器件衬底表面与印制板表面的不平行度(即元器件斜面)最大间距≤2.0mm。
(GBT19247.2-2003/IEC61191-2:1998;4.2.1)如图23.1.2 元器件引线的弯曲元器件弯曲要求不允许延伸到密封部分内。
引线弯曲半径(R)必须大于引线标称厚度。
上、下弯曲的引线部分和安装的连接盘之间的夹角最小45°,最大为90°。
(GBT19247.2-2003/IEC61191-2:1998;4.2.2)如图2:图2双引线元器件独立垂直安装时,较大的侧面应垂直于印制板表面,最多倾斜15°。
(GBT19247.3-2003;A.4.2)3.1.3 晶体管、二极管等极性元器件的安装元器件要求按极性正确安装保持元器件极性标识同电路板上极性标识一致。
元器件比较密集的地方要求各引脚分别套上不同彩色的塑料套管,防止碰极短路。
对于一些大功率晶体管,要求固定散热片。
3.1.4 集成电路的安装集成电路方向正确安装,插到低,保持两边余量一致。
不允许插错、插反。
PCB插件焊接检验标准

PCB插件焊接检验标准1.目的规范本公司生产的半成品检验,确保产品质量要求,防止不良品流出。
2.范围适用于本公司内所有半成品板的外观检验和特性检验。
3.检验要求3.1安装直插元器件准位要求3.1.1元器件引线成形a).元器件引线成形要求同类元件保持高度一致,成形元器件两端余量一致。
元器件引脚同焊盘引脚对应整齐,无明显倾斜。
b).元器件引线不允许出现超过引线截面积10%的缺口或变形。
外露基体金属不超过引线可焊表面面积的5%。
(GBT19247.1-2003;6.4)c).引线从元器件本体或弯曲半径前的容焊点的伸出长度,至少应为引线直径或厚度,不能小于0.8mm。
(GBT19247.3-2003;4.2.3)如图1:最大引线直径/mm 最小弯曲半径R<0.8 直径/厚度0.8~1.2 1.5倍直径/厚度>1.2 2倍直径/厚度图1 引线弯曲d).引线成形要求应使元器件衬底表面与印制板表面的不平行度(即元器件斜面)最大间距≤2.0mm。
(GBT19247.2-2003/IEC61191-2:1998;4.2.1)如图23.1.2元器件引线的弯曲a).元器件弯曲要求不允许延伸到密封部分内。
引线弯曲半径(R)必须大于引线标称厚度。
上、下弯曲的引线部分和安装的连接盘之间的夹角最小45°,最大为90°。
(GBT19247.2-2003/IEC61191-2:1998;4.2.2)如图2:图2b).双引线元器件独立垂直安装时,较大的侧面应垂直于印制板表面,最多倾斜15。
(GBT19247.3-2003;A.4.2)3.1.3晶体管、二极管等极性元器件的安装a).元器件要求按极性正确安装保持元器件极性标识同电路板上极性标识一致。
b).元器件比较密集的地方要求各引脚分别套上不同彩色的塑料套管,防止碰极短路。
对于一些大功率晶体管,要求固定散热片。
3.1.4集成电路的安装集成电路方向正确安装,插到低,保持两边余量一致。
插件料检验规范新6

√
√
√
√
目测/卡 尺
√ √
√
√
√
√
√
√
√
√
目测/卡
√
尺/万能
测试盒
√
√
√
√
√
√
√
√
目测/卡 尺
√
√
√
√
***** 本文件及其内容为公司之财产, 未经授权不得复制 *****
Page 4 of 7
深圳佳力拓科技有限公司
接口类检验规范
文件编号:GFJLT-ZL-06A 版次:A 生效日期:2014-06-25
1,表面脏污、划痕、氧化、生锈等
2,金针错位、下陷、变形、氧化等
外观 3,插口内有毛屑、杂物等
4,引脚氧化、变形、缺脚等
6 网口
5,混料(带灯与不带灯)
试装 每批来料进行对应的 PCB 试插 10pcs
可靠性 每批来料抽检 3pcs 做可靠性试验(参考物料规格书)
包装
标示明确,包装方式符合要求 外箱破损,损坏物料
7. 检验项目及方法
***** 本文件及其内容为公司之财产, 未经授权不得复制 *****
Page 3 of 7
深圳佳力拓科技有限公司
接口类检验规范
文件编号:GFJLT-ZL-06A 版次:A 生效日期:2014-06-25
序 号
物料 名称
检验项目
检 验 内容
1,外观脏污、划伤、缩水、缺胶、生锈、破裂、变形等
4. 缺点定义 4.1 严重缺点(CRITICAL DEFECT,简写 CRI):不良缺陷,使产品在生産﹑运输或使用过程中可能出现危及人身财产安全之缺点,称为
严重缺点. 4.2 主要缺点(MAJOR DEFECT,简写 MAJ):不良缺陷,使产品失去全部或部分主要功能,或者相对严重影响的结构装配的不良,从而
电子厂插件工序要求

电子厂插件 WI工艺作业指导书
1,每个工位的工时要一致,零件数量大致相同。
一个工位不能超过15PCS元件。
2,同一个工位的零件方向要一致
3,同一工位零件尽量不单一,要用多种零件组成(如电阻,电容,IC,二极管,插座等)
4,从第一工位到最后一工位,零件排序为:先体积小,后体积大。
先易插,后难插。
插座插头有卡口的先插,直针和无卡口的后插。
前面工位零件不能影响后面的工位零件插放。
5,瓷片电容颜色相同,电解电容大小相同的不能插在同一工位。
6,电阻颜色相同,阻值数值相同(如31.4K和3.14K)和阻值相近的(如10.2K与10.5K)不能插在同一工位7,IC、二极管大小相同,外观相差不大的,不同P/N的分放在多个工位。
- 1、下载文档前请自行甄别文档内容的完整性,平台不提供额外的编辑、内容补充、找答案等附加服务。
- 2、"仅部分预览"的文档,不可在线预览部分如存在完整性等问题,可反馈申请退款(可完整预览的文档不适用该条件!)。
- 3、如文档侵犯您的权益,请联系客服反馈,我们会尽快为您处理(人工客服工作时间:9:00-18:30)。
17
零件傾斜
1.DIP零件傾斜≧±30°
2.SMD零件傾斜≧1/3T(T為焊墊寬度)
18
包焊(焊錫過多)
1.DIP零件腳太短或焊錫太多以致無法判定零件腳和焊錫間是否沾錫良好.
2.SMD焊錫太多不良,不良情形:無法看見零件腳輪廓.
19
錫裂
切腳機不鋒利或搖動零件造成錫點與零件腳間有裂痕.
各機種與實裝為準
20
剪腳長度
1.2mm≦剪腳長度,≦1.8mm.
各機種與實裝為準
21
倒腳
不可有倒腳
22
PCBA不潔
1.PCBA過熱變黃
2.PCBA殘留物點總面積的3%
23
PCBA起泡
起泡大小≧0.5mm.且數目在三個以上.
24
腳未入
零件腳未露出,用手可拉起零件腳.
25
LED顏色
LED顏色不符或不在限度范圍內
5
空焊
1.零件焊錫與零件腳間≧50%未吃錫.
2.SMD無吃錫或吃錫不足.
6
孔爆
焊錫點成爆裂狀或內含空氣.
7
錫(渣)珠
不可有錫珠、錫渣.
8
沾錫
在PCB絕緣漆上的錫點:錫點≦0.3mm.距離線路和零件≦0.5mm
9
吃錫不良
鍍錫通孔吃錫≦75%或未成錐狀.
10
針孔
在錫點上細小如針尖般的孔≧3個
11
翹皮
線路和焊墊均不可翹皮.
26
錫尖
錫尖高度距離焊錫面≦1mm.且與監近錫點和線路的距離≧0.5mm.
27
SMD
破件、倒立、歪斜等.
28
未修改
未依EN、ECN修改零件或制程.
5.2.6功能部分如下表
NO.
不良項目
說明
CR
MA
MI
備注
1
功能測試
1.死機
2.無動作,或誤動作.
3.Switch無功能卡鍵或斷裂
4.彈力弱,兩按鍵明顯差異.
AQL: CR=0
MA=0.4 (A12 B02 B10采用MA=0.25)
MI=1.0
5.制程檢驗
5.1制程檢驗程序依照《制程檢驗作業程序》辦理
5.2制程條件查核
5.2.1制程中各工位是否挂正確之作業規范.
5.2.2各站是否確實配戴靜電環,(參照作業規范規定)靜電環需每天測試並記錄.
5.2.3錫爐溫度及鏈條速度是否是規定范圍內,並記錄于巡檢表上.
12
殘腳
不得有殘腳在PCBA上.
13
零件標示
須能讀出規格、品名或料號
14
插反
(有極性之零件)
所有有極性之零件,未依規定的極性裝置,如IC、電解電容、二極體等.
15
補線
1.補線於零件面長度不可>1cm.焊錫面長度不可>0.5cm.
補線需不影響組裝后之外觀
16
零件浮高
1.如IC、IR、Switch等機購相關零件不可≧0.2mm.
5.2.4烙鐵溫度是否在規定范圍內.每天需測試並記錄.
5.2.5外觀部分如下表:
NO.
不良項目
說明
CR
MA
MI
備注
1
BOM不符
與BOM核對,漏件,錯件
2
短路
1.錫點或線路間,焊錫太多所造成的短路或零件腳碰撞短路.
2.各屬外殼與零件之間的距離≧0.5mm.
3
開路
線路斷或導電炭墨開路.
4
冷焊
錫點的外表粗糙、灰白或成結晶狀有晦暗的聚集物或焊錫帶不平滑.
1.目的
規定插件制程檢驗的品質標準,期使所有的產品均能符合客戶的要求.
2.范圍
本公司所有機種,各類型的Mouse.1.1裸視檢驗.
3.1.2距離30cm.
3.1.3照明:300LUX~800LUX.
4.抽樣計劃
4.1采用MIL-STD-105D II級水準.
5.卷頁無功能.
6.尾燈不亮,顏色錯.
5.2.7機構部分如下表
NO.
不良項目
說明
CR
MA
MI
備注
1
組裝
1.無法順利組裝
2.能順利組裝但會干涉磨擦等現象.
每批抽5pcs
6.參考文件
6.1不合格品處理作業程序.(Q-QP-010)
6.2矯正及預防措施作業程序(Q-QP-011)
6.3制程檢驗作業程序(Q-QP-008)
7.特記事項:
7.1零件材料外觀依據各零件材料進料檢驗規范.
7.2除非另有說明,否則所有PCBA之品質判定,以本標準判定之,本標準所定規格乃最大容許之缺點.
7.3此標準亦作為首件查核之標準.