浅析影响电解铜箔抗剥离强度的因素及对策
电解铜箔生产常见问题及处理

电解铜箔生产常见问题及处理
一、生产常见问题
1、电解池漏电
运行时出现电解池漏电现象,可能是电解池封口有问题,搭接条带有氧化物或封口螺栓松动引起的,该情况须及时检修,将封口板拆洗干净,检查搭接条是否有氧化物,如有清洗后,再重新安装封口板并加紧螺栓。
2、阴极结焦
经常出现阴极结焦,可能是由于电解池的工作温度过高,涂锌箔厚度不足,抗熔化点不够高的铜溶液导致,该情况清洗阴极,更换阴极,检查铜溶液,补充锌箔。
3、电解池燃烧
电解池经常出现燃烧,可能是由于电解池热控不当、离心机失压而导致的,该情况应及时关闭离心机,检查温控装置是否正常运转,降低电解池温度,加强温控的操作。
4、电流过大
经常出现电流过大的情况,可能是由于电解池的内电阻过小引起的,该情况及时更换电解池,更换新的电解池,并检查电解池内部的内电阻是否正常。
5、铜溶液长时间无法得到
铜溶液长时间无法得到,可能是由于电解池容积过小,铜溶液浓度过大,沉淀物淤积过多引起的,该情况应减少电解池的容积,同时减小铜溶液的浓度,清除沉淀物淤积。
二、处理措施
1、电解池漏电。
电解铜箔常见问题及解决办法

电解铜箔常见问题及解决办法摘要:现代电子工业材料中常使用到电子铜箔,电子工业的不断发展,要求其有更高的技术支持,生产电子铜箔的厂家有许多,且各厂家的生产工艺相差不大,而产出的铜箔质量可能存在一定差异。
我国电子工业的发展,不少厂家逐步生产电子铜箔,但我国这种材料的质量相比国外有非常大的差距,通常体现在放置铜箔之后出现变色情况,成品合格率也难以保障,使得电耗高成本增加,经济效益低下。
电解铜箔需要有非常高的生产实践性,本文主要分析了近年来电解铜箔生产过程中常见的问题与处理手段供参考。
关键词:电解铜箔,问题,毛刺,方法电解铜箔发展有三个阶段,第一个阶段是起步阶段,这个阶段重点在于印刷,通过铜箔来生产电路板,厚度在70-100cm之间。
第二个阶段是快速发展阶段,这个阶段的铜箔厚度在18-35cm之间,被日本铜箔业所垄断。
第三个阶段是发展成熟阶段,这个阶段生产的铜箔厚度在3-5cm之间,且在电池上应用,全球各个国家对其研究程度不等。
随着铜箔生产企业在产品质量和工艺流程上改善较大,而对比国外先进生产企业来说仍有非常大的差距。
我国进口铜箔通常是高档铜箔,出口铜箔90%以上为低档铜箔。
技术含量及附加值高的HD内层用柔性电路板及铜箔,基本上都是从国外进口。
因材料价格精度因素,我国生产企业购买的生箔机在持续工作中材料表面情况不良致使铜箔品质降低,那么对这部分企业来说,需要不断提升产品的性能,采取科学可行的方法来改进电解铜箔的表面处理工艺。
生产厂家质量有差异,但关键生产工艺及设备的原理大同小异,通常是生箔机大小不一致,后处理在点解时添加的电解添加剂不一样,工艺不一样。
在生箔机中经过电沉积,对阴极辊的转速控制下获取厚度不等的铜箔,在生产过程中容易产生一系列问题,下面将介绍常见的几个问题。
1 电解铜箔常见问题及解决办法1.1毛刺生箔机会产生毛刺,收集辊中能够发现铜箔有突出,有些毛刺还可能刺穿铜箔造成破坏,小毛刺的情况可佩带手套来感觉生箔机收卷,会有刺手感。
电解铜箔常见问题及解决对策分析
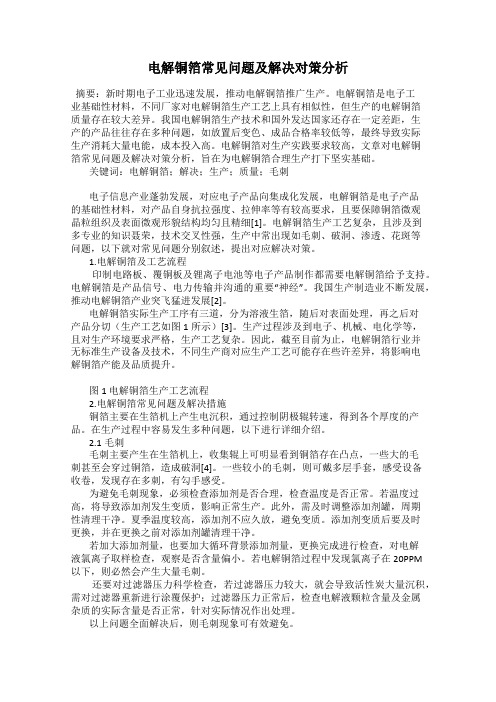
电解铜箔常见问题及解决对策分析摘要:新时期电子工业迅速发展,推动电解铜箔推广生产。
电解铜箔是电子工业基础性材料,不同厂家对电解铜箔生产工艺上具有相似性,但生产的电解铜箔质量存在较大差异。
我国电解铜箔生产技术和国外发达国家还存在一定差距,生产的产品往往存在多种问题,如放置后变色、成品合格率较低等,最终导致实际生产消耗大量电能,成本投入高。
电解铜箔对生产实践要求较高,文章对电解铜箔常见问题及解决对策分析,旨在为电解铜箔合理生产打下坚实基础。
关键词:电解铜箔;解决;生产;质量;毛刺电子信息产业蓬勃发展,对应电子产品向集成化发展,电解铜箔是电子产品的基础性材料,对产品自身抗拉强度、拉伸率等有较高要求,且要保障铜箔微观晶粒组织及表面微观形貌结构均匀且精细[1]。
电解铜箔生产工艺复杂,且涉及到多专业的知识聂荣,技术交叉性强,生产中常出现如毛刺、破洞、渗透、花斑等问题,以下就对常见问题分别叙述,提出对应解决对策。
1.电解铜箔及工艺流程印制电路板、覆铜板及锂离子电池等电子产品制作都需要电解铜箔给予支持。
电解铜箔是产品信号、电力传输并沟通的重要“神经”。
我国生产制造业不断发展,推动电解铜箔产业突飞猛进发展[2]。
电解铜箔实际生产工序有三道,分为溶液生箔,随后对表面处理,再之后对产品分切(生产工艺如图1所示)[3]。
生产过程涉及到电子、机械、电化学等,且对生产环境要求严格,生产工艺复杂。
因此,截至目前为止,电解铜箔行业并无标准生产设备及技术,不同生产商对应生产工艺可能存在些许差异,将影响电解铜箔产能及品质提升。
图1 电解铜箔生产工艺流程2.电解铜箔常见问题及解决措施铜箔主要在生箔机上产生电沉积,通过控制阴极辊转速,得到各个厚度的产品。
在生产过程中容易发生多种问题,以下进行详细介绍。
2.1毛刺毛刺主要产生在生箔机上,收集辊上可明显看到铜箔存在凸点,一些大的毛刺甚至会穿过铜箔,造成破洞[4]。
一些较小的毛刺,则可戴多层手套,感受设备收卷,发现存在多刺,有勾手感受。
电解铜箔生产常见问题及处理
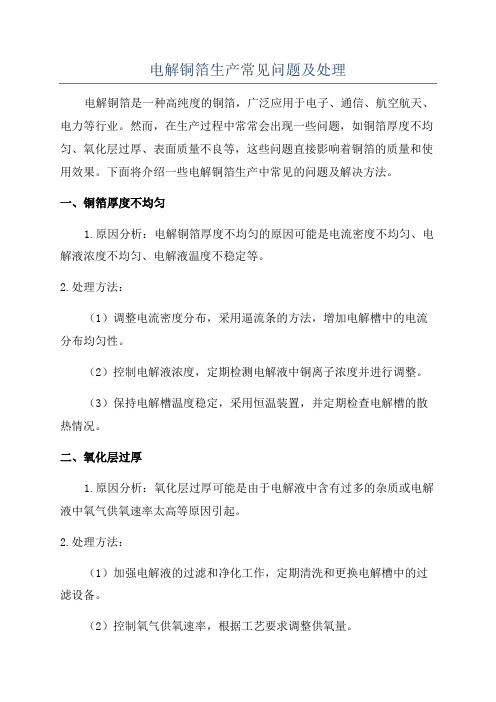
电解铜箔生产常见问题及处理电解铜箔是一种高纯度的铜箔,广泛应用于电子、通信、航空航天、电力等行业。
然而,在生产过程中常常会出现一些问题,如铜箔厚度不均匀、氧化层过厚、表面质量不良等,这些问题直接影响着铜箔的质量和使用效果。
下面将介绍一些电解铜箔生产中常见的问题及解决方法。
一、铜箔厚度不均匀1.原因分析:电解铜箔厚度不均匀的原因可能是电流密度不均匀、电解液浓度不均匀、电解液温度不稳定等。
2.处理方法:(1)调整电流密度分布,采用逼流条的方法,增加电解槽中的电流分布均匀性。
(2)控制电解液浓度,定期检测电解液中铜离子浓度并进行调整。
(3)保持电解槽温度稳定,采用恒温装置,并定期检查电解槽的散热情况。
二、氧化层过厚1.原因分析:氧化层过厚可能是由于电解液中含有过多的杂质或电解液中氧气供氧速率太高等原因引起。
2.处理方法:(1)加强电解液的过滤和净化工作,定期清洗和更换电解槽中的过滤设备。
(2)控制氧气供氧速率,根据工艺要求调整供氧量。
(3)采取适当的操作方法和电解条件,减少氧气在电解过程中的消耗。
三、表面质量不良1.原因分析:电解铜箔表面质量不良的原因可能是电解液中杂质太多、电解工艺条件不合理等。
2.处理方法:(1)加强电解液的净化工作,定期清洗和更换电解槽中的过滤设备。
(2)优化工艺条件,合理控制电解温度、电流密度、电解时间等参数。
(3)定期对电解设备进行维护和检查,确保设备的正常运转。
四、其他问题1.电解液成分不稳定:可能是由于电解槽内的溶液浓度不稳定、电解液配制不当等原因引起的。
处理方法:定期检测电解液的成分,并根据需要进行调整和补充。
2.铜箔强度不达标:可能是由于电解液的复配配比不合理、电解温度过高等原因引起的。
处理方法:调整电解液的复配配比,优化工艺条件,控制电解温度在合理范围内。
3.气泡和缺陷:可能是由于电解槽内的电解液中含有杂质、电解温度设定不合理等原因引起的。
处理方法:加强电解液的过滤和净化工作,控制电解温度在合理范围内。
渗镀,浸焊起泡,剥离强度不足原因分析及对策

渗镀,浸焊起泡,剥离强度不足原因分析及对策PCB刚性线路板及FPC软性线路板生产过程中均会时常碰到以下问题:一,线路工段出现干膜或湿膜处理后在蚀刻线路时出现侧蚀,凹蚀现象,导致线宽不足或线路不平整.究其原因不外乎与干湿膜材料选择不当,曝光参数不当,曝光机性能不良.显影,蚀刻段喷头调节,相关参数调节不合理,药液浓度范围不当,传动速度不当等系列可能导致出现问题的原因.然而我们经常会发现经过检查以上参数及相关设备性能并没有异常,然而在做板时依然会出现线路过蚀,凹蚀等问题.究竟是什么原因呢?二,在做PCB图形电镀,PCB,FPC终端表面处理如沉金,电金,电锡,化锡等工艺处理时.我们常会发现做出来的板在干湿膜边缘或阻焊层边缘出现渗镀的现象,或大部分板出现,或部分板的部分地方出现,无论是哪一种情况都会带来不必要的报废或不良为后工段加工带来不必要的麻烦,乃至最终报废,令人心痛!究其原因分析大家通常会想到是干湿膜参数,材料性能出现问题;阻焊如硬板用的油墨,软板用的覆盖膜有问题,或在印刷,压合,固化等工段出现了问题.的确,这些地方每一处都可能引起此问题发生.那么我们同样也困惑的是经检查以上工段并没有问题或有问题也解决了,但依然会出现渗镀的现象.究竟还有什么原因没查出来呢?三,线路板在出货前会做上锡试验,客户当然在使用时会上锡焊接元件.有可能两个阶段均会出现,或在某一阶段会出现浸锡或焊锡时阻焊起泡,剥离基板.乃至做胶带测试油墨剥离强度时,拉力机测试软板覆盖膜剥离强度时即会出现油墨可被明显剥离或覆盖膜剥离强度不足或不均的问题.这类问题客户尤其是做精密SMT贴装的客户是绝对不能接受的.阻焊层一旦在焊接时出现起泡剥离现象将导致无法精确贴装原件.导致客户损失大量元件及误工.线路板厂同时将面临扣款,补料,乃至丢失客户等巨大损失.那么我们平时在碰到此类问题时会在那几方面着手呢?我们通常会去分析是不是阻焊(油墨,覆盖膜)材料的问题;是不是丝印,层压,固化阶段有问题;是不是电镀药水有问题?等等...于是我们通常会责令工程师务必从这些工段一一查找原因,并改善.我们也会想到是不是天气的原因?最近比较潮湿,板材吸潮了?(基材及阻焊均易吸潮)经过一番苦战,多少能收获些效果,问题暂时得到表面上的解决.然不经意间此类问题又发生了,又是什么原因?那些可能发生问题的工段明明已经查过改善过了呀.还有什么是没注意到的?针对以上属于PCB,FPC行业广泛的困惑,难题.我们进行了大量的试验和研究,终于发现产生线路不良,渗镀,分层,起泡,剥离强度不足等问题的一个重要原因竟然在于前处理部分.包括干湿膜前处理,阻焊前处理,电镀前处理等多工段的前处理部分.说到这里,或许很多行业人士不禁要笑.前处理是最简单不过的了,酸洗,除油,微蚀.其中哪一样前处理药水,性能,参数,乃至配方,行业内很多技术人员都清楚.线路板生产过程中涉及大量复杂的表面处理药水,如沉电铜,沉电金,沉电锡,OSP,蚀刻,等.这些较为复杂的工艺在多数情况下,工艺工程师都会选择去深入钻研,分析;力求掌握这些工艺技术,并以此作为提升自身技术能力的突破点.同时多数工厂也以此来作为工程师的薪资标准,绩效考核标准.而前处理这块基本上很少有工程师人员去细心研究.要么直接从供应商处购买成品除油,微蚀剂,酸洗自已用稀硫酸作为酸洗液.乃至有不少厂微蚀也自已配,要么配过钠,过铵体系(配方已众所周知),要么购买双氧水稳定剂自已配双氧水-硫酸体系的.而除油则通过购买供应商成品除油剂或购买除油粉稀释使用.据我们的调查研究发现,众多厂家没有从根本上去认识前处理工艺中各药液的细微作用,或者说是关键作用,只注重表面外观效果.如除油段,大家可能一直认为能把板面的油污,手指印除去即可,肉眼看不到即为除油OK,殊不知除油工艺对线路板而言不仅是将已于铜面深度结合的油污剥落,同时更重要的药液要能把剥离下来的油分子分解掉.这样方能对板面不形成二次污染.市场上现在出售的除油剂,除油粉,通常只含有除油,除锈成分,而其它组分如抗蚀剂,表面活性剂,乳化剂,等重要组分为降低成本根本没加;甚至很多供应商的配方从别处购买而来,根本不了解各成分的作用,更谈不上研究,或结合线路板的实际工艺需求调配加入有效的组份.这样实际上很多线路板厂所使用的除油剂并非适用于线路板行业专用的的除油剂,而是通用于五金,矿产加工业的传统除油剂.如此产品怎么达到良好的除油效果,板面用肉眼看着除油效果不错.实际上呢?我们通过高倍显微镜或油膜测试能发现大量细微的油分子附着在板面上.这样的处理效果如何能保证后续生产抗蚀层,阻焊层,终端表面处理时良好的结合力,剥离强度,可焊性等必须性能的效果及稳定性呢.尤为严重的是我们对微蚀这一块的认识.线路板行业的微蚀工艺实际上要具备1.除去铜面锈层,氧化层,及其它异物;2.均匀粗化铜表面,形成微观凸凹,宏观平坦的粗化层.达到速率稳定的粗化效果.3.活化铜表面,并具有短时期抗气相及液相腐蚀的作用,保证后续表面加工的可操作性.4,较低的过氧化物及硫酸含量,防止药液暴沸及形成高分子有机物残留板面.而实际生产中,我们自配的或购买的微蚀液大多把微蚀当成了蚀刻液.认为只有板面的锈渍异物除去,能露出新鲜的铜面就是达到了微蚀效果.而实际上呢?我们自配的微蚀液中过氧化物如过氧化氢,过硫酸钠,过硫酸铵等,强酸如硫酸.为达到效果含量均较高,如过氧化物含量达到120乃至150克/升,硫酸含量超过5%,如此高的浓度实际上是把微蚀变成了蚀刻,大量的铜被咬蚀,且由于没有调节剂的加入,咬蚀深度粗浅不一,轻则导致板面处理效果不一致,重则二次返工即导致铜层严重被咬蚀,无法进行后工段加工,造成报废.很多配双氧水体系的还会犯以为加了双氧水稳定剂就能达到均匀微蚀作用的常见错误理解.双氧水稳定剂只是为了抑制双氧水过快分解而加入,并不能起到均匀性方面的作用.而实际上用于线路板行业的专业微蚀剂它除了应该配以低泡表面活性剂,专用湿润剂,有机络合剂,微定剂,抗蚀剂等多种添加剂.从而使过氧化物,硫酸等咬蚀速率过快,副反应产物较高的主组分含量尽可能降低,并使药液更稳定,除了除锈基本功能外更能均匀稳定的粗化铜面,形成表面宏观平坦光滑(利于终端表面处理外观),无色差,异样区或点;同时微观达到均匀一致的凸凹粗化层(利于后续抗蚀干湿膜,阻焊层的加工),实际上单靠氧化剂和强酸并不能增加理想的铜表面粗化面积,必须加入活性剂,湿润剂等方能达到良好深度粗化效果,增加铜表面粗化面积,从面提升后加工的结合力及剥离强度.经过完善和改进的线路板专用微蚀液整体应达到:药液无暴沸,无高分子副产物形成污染,良好除锈能力,良好的均匀平坦外观,深度粗化铜面,蚀铜量小.达到板面外观平滑,阻焊或镀层加工时结合强等作用.随着线路板向超薄铜型转化,我们越来越需要一种蚀铜量更小的微蚀液(同时保证除锈及粗化效果)随着线路板的线路精度要求越来越高,我们越来越需要一种前处理效果更好的除油,微蚀液.以确保抗蚀层(干湿膜)的抗渗透力.随着线路板终端表面处理的外观要求越来越高,我们需要引进优质的前处理工艺.随着表面焊接向无铅型转化,线路板需承受的焊接温度越来越高,对表面阻焊层的抗热冲击能力要求越来越高,对终端表面处理及阻焊层(油墨,覆盖膜)的剥离强度,与基底铜的结合力要求也越来越高,我们需要一种具有更佳效果的前处理工艺来做保障.随着线路板行业竞争的日益激烈,我们需要通过改良我们的工艺以使产品良率提高,以获得利润增长点.优质的前处理药水无疑能低成本帮我们的大忙.线路板产业前沿如日本,美国,韩国,台湾早已重视并启用新一代前处理工艺.使所生产的产品更具竞争力,性能更稳定.以小带大,从前处理着手确保整体工艺的稳定性.以上谨以我们的研究成果分享于广大线路行业经营者及技术工作者,不足及错误之处敬请批评指正.若您有更多问题需要探讨或对我们的前处理药水及我们所研发的更多专业线路板行业的药水,化学品需要咨询请按以下方式与我们联系,我们将及时与您联系提供相关咨询支持及产品服务.。
电解铜箔生产常见问题及处理

电解铜箔生产常见问题及处理随着电子信息产业的发展,电子产品轻量化、集成化要求越来越高,电解铜箔作为电子行业的基础性材料,不仅对产品的抗拉强度、延伸率、抗剥离强度、防氧化性等物化性能指标提出了更高要求,而且要求铜箔微观晶粒组织和表面微观形貌结构更均匀精细。
电解铜箔生产工艺复杂,涉及专业广泛,生产过程既有机械电子设备又有电化学过程,分系统之间相互关联相互影响,相关技术大多是交叉、边缘学科,对处理实际生产中遇到的复杂问题缺乏成熟的理论支持。
本文通过对实际生产中常见问题的总结,提出了一些有参考价值的处理方法,希望能引起同行的注意和指正,引发更成熟的研究方法和处理方法。
1、溶液净化未处理箔(毛箔)的制造过程是铜箔生产中最关键的环节,绝大多数的物化性能指标与毛箔有着直接或间接的关系。
毛箔的电沉积过程离不开溶液,所以其溶液尤为重要,纯净无杂质、成分均匀稳定的毛箔溶液是生产高品质铜箔的必需条件。
实际生产中不可避免会有一些杂质通过原料铜、废箔、水、酸的加入和设备自身的磨损腐蚀进入到溶液中,因此生产中的溶液含有不溶性的微粒、可溶的离子分子基团和有机物等各种杂质,这些杂质大多数对铜箔品质有负面影响,应尽可能减少杂质进入溶液系统或采用有效方法把杂质控制在合理范围内。
不溶性微粒主要来源于原料铜的加入和废箔回用,活性炭和其它有机物吸附剂在使用中也会少量分解形成不溶性微粒。
在基箔电沉积过程中微粒夹杂于组织内或吸附于铜箔表面,造成箔面粗糙、针孔、渗透点等质量缺陷。
一般采用多级过滤的办法将微粒由大到小逐级过滤去除,过滤精度最高可以达到0. 5μm以内。
随着过滤层级的增加和过滤精度的提高溶液净化效果相应提高,铜箔组织的致密性和表面微观结构的细致性都明显优化,表现为延伸率、抗拉强度等指标的提高。
高度净化的基箔溶液是生产高品质铜箔前提条件之一。
增加过滤次数也是溶液净化的有效方法,通常循环过滤液量应为生产供液量的1.5倍以上。
提高溶液的净化,设备投入和运行费用会大幅增加,在净化工艺设计时要兼顾工艺性和经济性。
电解铜箔变形的影响因素分析
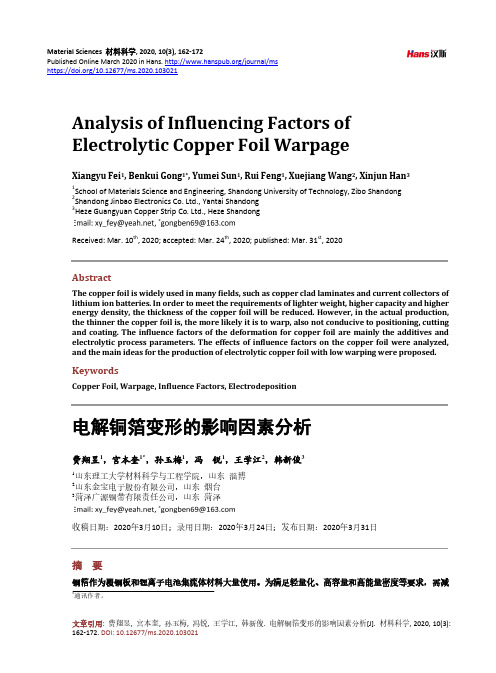
Material Sciences 材料科学, 2020, 10(3), 162-172Published Online March 2020 in Hans. /journal/mshttps:///10.12677/ms.2020.103021Analysis of Influencing Factors ofElectrolytic Copper Foil WarpageXiangyu Fei1, Benkui Gong1*, Yumei Sun1, Rui Feng1, Xuejiang Wang2, Xinjun Han31School of Materials Science and Engineering, Shandong University of Technology, Zibo Shandong2Shandong Jinbao Electronics Co. Ltd., Yantai Shandong3Heze Guangyuan Copper Strip Co. Ltd., Heze ShandongReceived: Mar. 10th, 2020; accepted: Mar. 24th, 2020; published: Mar. 31st, 2020AbstractThe copper foil is widely used in many fields, such as copper clad laminates and current collectors of lithium ion batteries. In order to meet the requirements of lighter weight, higher capacity and higher energy density, the thickness of the copper foil will be reduced. However, in the actual production, the thinner the copper foil is, the more likely it is to warp, also not conducive to positioning, cutting and coating. The influence factors of the deformation for copper foil are mainly the additives and electrolytic process parameters. The effects of influence factors on the copper foil were analyzed, and the main ideas for the production of electrolytic copper foil with low warping were proposed.KeywordsCopper Foil, Warpage, Influence Factors, Electrodeposition电解铜箔变形的影响因素分析费翔昱1,宫本奎1*,孙玉梅1,冯锐1,王学江2,韩新俊31山东理工大学材料科学与工程学院,山东淄博2山东金宝电子股份有限公司,山东烟台3菏泽广源铜带有限责任公司,山东菏泽收稿日期:2020年3月10日;录用日期:2020年3月24日;发布日期:2020年3月31日摘要铜箔作为覆铜板和锂离子电池集流体材料大量使用。
浅谈电解铜箔常见问题

浅谈电解铜箔常见问题摘要:电解铜箔作为现代电子工业的基础材料,随着电子工业的发展,要求越来越高。
然而,各厂家生产的电解铜箔的质量不一样,哪怕是各厂家生产的差不多工会的电解铜箔。
随着我国电子工业的发展,国内许多厂家已开始从事电解铜箔的生产,但国内铜箔的质量远远落后于国外产品,这主要体现在铜箔成品率也无法提高,导致能耗高、成本高、经济效益差。
电解铜箔是一项需要很强的实践性生产的工作。
本文主要介绍了近几年来电解铜箔的生产情况常见质量问题及解决办法,对同行在电解铜箔生产中有一定的参考价值。
关键字:电解铜箔;生产;毛刺;花斑;在电子工业中,电解铜箔是最重要的材料之一,是电子工业发展的基础材料。
所谓电解铜箔,是指利用镀锡工艺来获得沉积层.该技术具有操作简单、效率高、纯度高等优点,已广泛应用于电子工业如印刷电路板(PCB)和覆铜箔层压板(CCL)的各个领域。
在电解铜箔的生产中,需要进一步提高电解铜箔的生产效率和质量,并在生产过程中使用添加剂。
电解铜箔工艺可以使用多种添加剂,在制备过程中起着有效的效果。
例如,氯离子可以抑制金属的异常生长,胺化合物对高电流密度区的化学效应增强,添加剂可以进一步提高电解铜箔产品的性能,因此,研究电解铜箔添加剂对电子工业的意义十分重要。
1.电解铜箔定义电解铜箔作为电子工业的基本原料,主要用于印刷电路板(PCB)和覆铜箔层压板(CCL),用于电子信号传输和电力传输,被称为神经网络(Neural Network)。
电解铜箔是以不溶性金属(如铅、钛电镀)为阳极,钛辊为阴极的工艺。
通过使硫酸铜溶液流经阳极和阴极电池,并通过直流电解,在钛辊表面沉积铜离子,从而获得电解液中的铜离子。
然后将铜箔连续脱离钛辊表面,进行洗涤、干燥,并得到成品铜箔。
电解铜箔生产厂家的质量不同,但主要生产工艺和设备原理基本相同,主要是铝箔机的尺寸,后处理只在电解过程中添加不同的电解添加剂,后处理工艺不同,其主要生产工艺包括以下几个方面。
铜箔抗拉强度降低的原因

铜箔抗拉强度降低的原因
铜箔是一种广泛应用于电子、通信和航空航天等领域的重要材料。
然而,随着生产和使用的不断发展,铜箔的抗拉强度会发生降低,这一
现象引起了广泛的关注和研究。
本文将对铜箔抗拉强度降低的原因进
行探讨。
一、材料本身的质量不均匀
铜箔的抗拉强度降低可能与其本身的材料质量不均匀有关。
具体来说,铜箔制备过程中可能会出现铜原料的成分不一致、金属晶粒的大小不均、铜箔表面的缺陷等问题,这些都会影响到铜箔的力学性能。
长期
以来,铜箔制造商一直在研究和改进生产工艺,旨在提高铜箔的均匀
性和稳定性,以确保其具有优良的力学性能。
二、工艺过程中的因素
铜箔制备过程中的一些因素也会影响到其抗拉强度的稳定性。
例如,
铜箔的冲压、拉伸和退火等过程中可能会因为参数设置不当、机器的
磨损、工艺的不规范等原因导致抗拉强度的降低。
此外,制备过程中
的温度、湿度、环境等因素也可能会对铜箔的力学性能产生影响,需
要加以注意和控制。
三、外部因素
除了材料本身和工艺因素外,外部因素也会对铜箔的抗拉强度产生影响。
例如,铜箔在使用过程中可能会受到机械冲击、化学腐蚀、高温等环境的影响,从而导致抗拉强度的下降。
因此,在选用铜箔作为材料时需要仔细考虑外部环境的因素,以确保其具有足够的耐久性和稳定性。
综上所述,铜箔抗拉强度的降低可能是由多种因素导致的,在实际生产和使用中需要注意控制和改进相应的因素,以确保铜箔具有优异的力学性能。
铜箔抗剥离强度公式

铜箔抗剥离强度公式一、引言铜箔作为一种重要的金属材料,在电子、电力、建筑等多个领域得到了广泛应用。
在铜箔的应用过程中,抗剥离强度是一个关键的性能指标,直接关系到材料的使用寿命和安全性。
因此,准确测量和评估铜箔的抗剥离强度至关重要。
本文将重点探讨铜箔抗剥离强度的计算公式及其应用。
二、铜箔抗剥离强度公式的概述铜箔抗剥离强度公式是一种用于描述铜箔在受到外力作用时抵抗剥离的能力的数学模型。
该公式基于力学原理,通过测量铜箔在不同条件下的剥离力或剥离应力,结合相关参数,计算出铜箔的抗剥离强度。
三、铜箔抗剥离强度公式的解析铜箔抗剥离强度公式通常由以下几个部分组成:1.加载速率:指施加在铜箔上的外力随时间的变化率。
加载速率对铜箔的抗剥离强度有一定影响,通常情况下,加载速率越快,铜箔的抗剥离强度越低。
2.温度:温度对抗剥离强度的影响较为显著。
随着温度的升高,铜箔的抗剥离强度通常会降低。
这主要是因为温度升高会导致材料软化,降低其力学性能。
3.铜箔厚度:铜箔的厚度对抗剥离强度具有重要影响。
一般来说,随着厚度的增加,铜箔的抗剥离强度会有所提高。
这主要是因为厚度的增加提供了更大的剪切力和摩擦力,有助于抵抗剥离力。
4.表面处理:铜箔的表面处理方式对其抗剥离强度也有一定影响。
例如,通过涂层、镀层或采用不同的表面粗糙度处理,可以改变铜箔的抗剥离强度。
5.应变速率:指铜箔在受力过程中应变的速率。
应变速率越高,铜箔的抗剥离强度通常会降低。
这是因为应变率的增加会导致材料内部结构的改变,从而降低其力学性能。
基于上述影响因素,铜箔抗剥离强度的计算公式可表示为:R = f(P, T, d, τ, ε)其中,R表示铜箔的抗剥离强度,P表示施加在铜箔上的外力,T表示温度,d表示铜箔厚度,τ表示表面处理方式,ε表示应变速率。
四、铜箔抗剥离强度公式的应用铜箔抗剥离强度公式的应用主要涉及以下几个方面:1.试验设计:通过使用该公式,可以合理设计试验方案,根据具体的应用需求和条件,选择适当的参数进行测试。
水分影响锂电池铜箔强度的机理
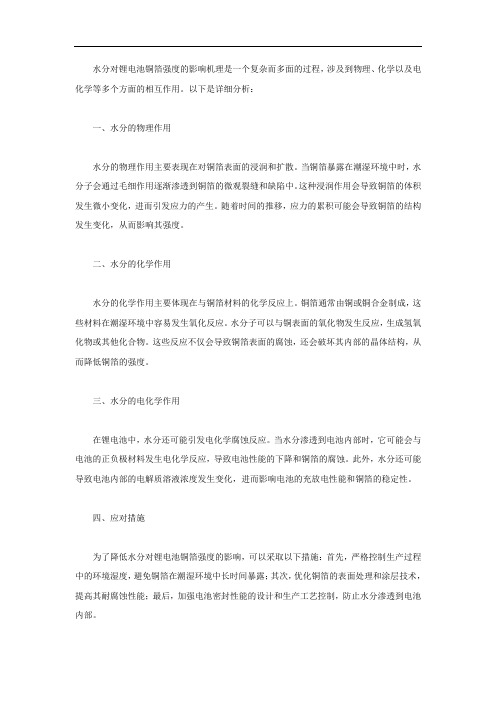
水分对锂电池铜箔强度的影响机理是一个复杂而多面的过程,涉及到物理、化学以及电化学等多个方面的相互作用。
以下是详细分析:一、水分的物理作用水分的物理作用主要表现在对铜箔表面的浸润和扩散。
当铜箔暴露在潮湿环境中时,水分子会通过毛细作用逐渐渗透到铜箔的微观裂缝和缺陷中。
这种浸润作用会导致铜箔的体积发生微小变化,进而引发应力的产生。
随着时间的推移,应力的累积可能会导致铜箔的结构发生变化,从而影响其强度。
二、水分的化学作用水分的化学作用主要体现在与铜箔材料的化学反应上。
铜箔通常由铜或铜合金制成,这些材料在潮湿环境中容易发生氧化反应。
水分子可以与铜表面的氧化物发生反应,生成氢氧化物或其他化合物。
这些反应不仅会导致铜箔表面的腐蚀,还会破坏其内部的晶体结构,从而降低铜箔的强度。
三、水分的电化学作用在锂电池中,水分还可能引发电化学腐蚀反应。
当水分渗透到电池内部时,它可能会与电池的正负极材料发生电化学反应,导致电池性能的下降和铜箔的腐蚀。
此外,水分还可能导致电池内部的电解质溶液浓度发生变化,进而影响电池的充放电性能和铜箔的稳定性。
四、应对措施为了降低水分对锂电池铜箔强度的影响,可以采取以下措施:首先,严格控制生产过程中的环境湿度,避免铜箔在潮湿环境中长时间暴露;其次,优化铜箔的表面处理和涂层技术,提高其耐腐蚀性能;最后,加强电池密封性能的设计和生产工艺控制,防止水分渗透到电池内部。
五、总结综上所述,水分对锂电池铜箔强度的影响是多方面的,既包括物理浸润和应力累积,也包括化学腐蚀和电化学反应。
为了确保锂电池的性能和安全性,需要深入研究水分对铜箔强度的影响机理,并采取相应的措施降低其影响。
这不仅可以提高锂电池的使用寿命和安全性能,也有助于推动电池技术的持续创新和发展。
对剥离强度产生影响的因素
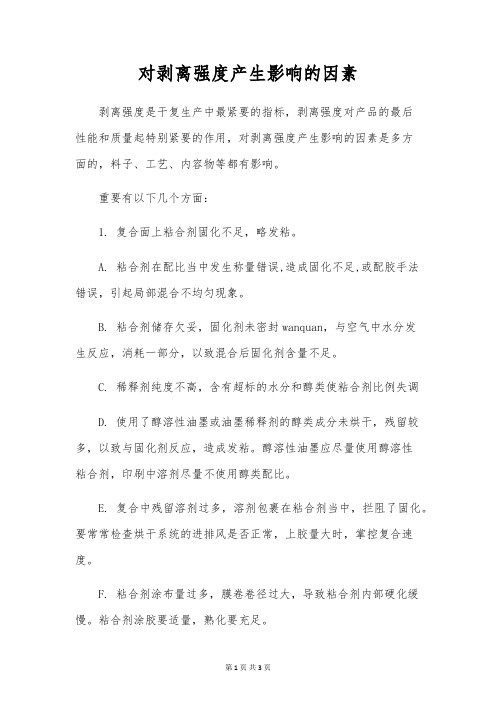
对剥离强度产生影响的因素剥离强度是干复生产中最紧要的指标,剥离强度对产品的最后性能和质量起特别紧要的作用,对剥离强度产生影响的因素是多方面的,料子、工艺、内容物等都有影响。
重要有以下几个方面:1. 复合面上粘合剂固化不足,略发粘。
A. 粘合剂在配比当中发生称量错误,造成固化不足,或配胶手法错误,引起局部混合不均匀现象。
B. 粘合剂储存欠妥,固化剂未密封wanquan,与空气中水分发生反应,消耗一部分,以致混合后固化剂含量不足。
C. 稀释剂纯度不高,含有超标的水分和醇类使粘合剂比例失调D. 使用了醇溶性油墨或油墨稀释剂的醇类成分未烘干,残留较多,以致与固化剂反应,造成发粘。
醇溶性油墨应尽量使用醇溶性粘合剂,印刷中溶剂尽量不使用醇类配比。
E. 复合中残留溶剂过多,溶剂包裹在粘合剂当中,拦阻了固化。
要常常检查烘干系统的进排风是否正常,上胶量大时,掌控复合速度。
F. 粘合剂涂布量过多,膜卷卷径过大,导致粘合剂内部硬化缓慢。
粘合剂涂胶要适量,熟化要充足。
G. 熟化温度过低,固化缓慢,交联不充足。
要选用适当的熟化温度,熟化时间要充足,必须时选用快速固化粘合剂。
H. 复合膜基材中添加剂的影响。
如,PVCD中的添加剂能延迟和阻拦粘合剂交联固化,PVA中的柔嫩剂能与固化剂的—NCO基团反应,软质PVC的增塑剂能渗入到粘合剂中,因此会降低粘接力和热稳定性,对此要适当加添固化剂使用量。
2. 固化但无剥离强度。
A. 粘合剂选择错误。
依据不同的基材、产品结构、后加工要求、内容物等选择粘合剂。
另外,不同的粘合剂性能差异很大,应使用专用粘合剂,如铝箔粘合剂、镀铝膜粘合剂、抗介质粘合剂等。
B. 粘合剂涂布量太少。
粘合剂布量太少会导致表面浸润铺不足。
基材的平滑度不一,产品用途不同都需用不同的涂布量。
上胶网纹辊要定期清洗,防止堵塞。
C. 粘合剂与油墨层的相容性不好,特别是多套色、油墨层厚的地方。
不可用聚酰胺油墨里印,注意油墨添加剂的作用,对油墨面大,油墨厚的印刷膜,要提高上胶量,选用低粘度、高固含量粘合剂,使胶液能渗透到基材表面,充足干燥D. 基材表面张力不好,基材的电晕处置不足或不均匀,复合基材表面张力达不到38mN/m,复合强度不佳,若达40~42mN/m,则效果更好。
电解铜箔表面结构及性能影响因素

实用文档西安工业大学题目:电解铜箔表面结构及性能影响因素姓名:刘畅专业:机械设计制造及其自动化班级:080217班学号:080217指导教师:贾建利电解铜箔表面结构及性能影响因素摘要:对铜箔进行化学处理,考察阴极钛辊表面粗糙度及阴极钛辊的腐蚀对铜箔的性能及表面图像影响。
研究结果表明:增加处理液中 Cu2+浓度及提高电流密度,有利于表面粗糙度增加,抗剥离强度增大,蚀刻因子 Ef降低。
若同时降低浸泡复合液中 Cu2+和 Zn2+浓度,增加 Sb2+浓度,则表面粗糙度及抗剥离强度降低,蚀刻因子增加;复合液中 Sb2+浓度增加也能使表面粗糙度增加,蚀刻因子增加,但是,抗剥离强度基本没有变化。
添加 CuSO4后,阴极钛辊腐蚀速度下降,当 CuSO4质量浓度达到 20 g/L后,钛的耐腐蚀速度在 0.050 mm/a 以下;当钛辊表面粗糙度 Rz降低时,电解铜箔表面相对平整,晶粒大小较均匀,排列较规则。
关键词:电解铜箔;化学处理;表面粗糙度;腐蚀Abstract: Effects of surface roughness and erosion of titanium cathode drum on performance of electrolytic copper foils and surface images were studied by chemical treatments. The results show that surface roughness and contradict debonding intensity increases and etch factorial (Ef) decreases with the increase of copper concentration and electric current density. When the concentration of copper and zinc of leached compound solution decreases, surface roughness and contradict debonding intensity decreases but etch factorial (Ef) increases. When the concentration of Sb2+ of leached compound solution increases, surface roughness and contradict debonding intensity increases but etch factorial (Ef) has litter change. The erosion rate of titanium cathode drum decreases when CuSO4 is added. When the mass concentration of CuSO4 is added up to 20 g/L, the erosion rate is less than 0.050 mm/a. Moreover, the surface of electrolytic copper foils is even and the size is well-proportioned and ranks regularly when surface roughness of titanium cathode drum (Rz) decreases. Key words:electrolytic copper foils; chemical treatment; surface roughness; corrosion0引言高性能电解铜箔是一种缺陷少、晶粒细、表面粗昆山—苏州地区为中心的两大电子工业生产基地。
电解铜箔生产常见问题及处理
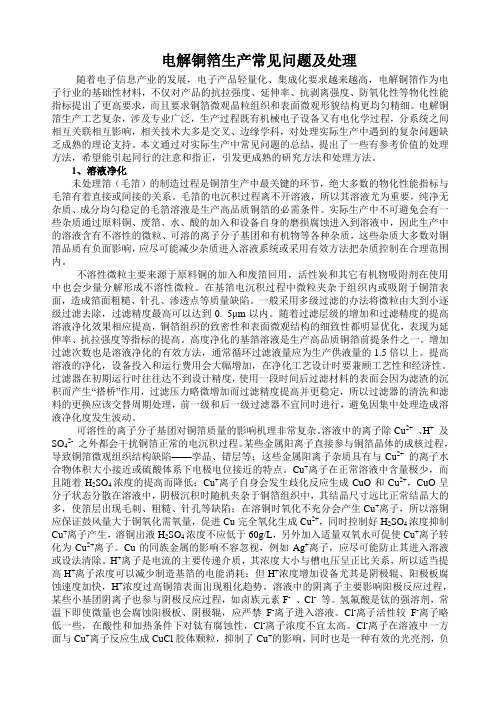
电解铜箔生产常见问题及处理随着电子信息产业的发展,电子产品轻量化、集成化要求越来越高,电解铜箔作为电子行业的基础性材料,不仅对产品的抗拉强度、延伸率、抗剥离强度、防氧化性等物化性能指标提出了更高要求,而且要求铜箔微观晶粒组织和表面微观形貌结构更均匀精细。
电解铜箔生产工艺复杂,涉及专业广泛,生产过程既有机械电子设备又有电化学过程,分系统之间相互关联相互影响,相关技术大多是交叉、边缘学科,对处理实际生产中遇到的复杂问题缺乏成熟的理论支持。
本文通过对实际生产中常见问题的总结,提出了一些有参考价值的处理方法,希望能引起同行的注意和指正,引发更成熟的研究方法和处理方法。
1、溶液净化未处理箔(毛箔)的制造过程是铜箔生产中最关键的环节,绝大多数的物化性能指标与毛箔有着直接或间接的关系。
毛箔的电沉积过程离不开溶液,所以其溶液尤为重要,纯净无杂质、成分均匀稳定的毛箔溶液是生产高品质铜箔的必需条件。
实际生产中不可避免会有一些杂质通过原料铜、废箔、水、酸的加入和设备自身的磨损腐蚀进入到溶液中,因此生产中的溶液含有不溶性的微粒、可溶的离子分子基团和有机物等各种杂质,这些杂质大多数对铜箔品质有负面影响,应尽可能减少杂质进入溶液系统或采用有效方法把杂质控制在合理范围内。
不溶性微粒主要来源于原料铜的加入和废箔回用,活性炭和其它有机物吸附剂在使用中也会少量分解形成不溶性微粒。
在基箔电沉积过程中微粒夹杂于组织内或吸附于铜箔表面,造成箔面粗糙、针孔、渗透点等质量缺陷。
一般采用多级过滤的办法将微粒由大到小逐级过滤去除,过滤精度最高可以达到0. 5μm以内。
随着过滤层级的增加和过滤精度的提高溶液净化效果相应提高,铜箔组织的致密性和表面微观结构的细致性都明显优化,表现为延伸率、抗拉强度等指标的提高。
高度净化的基箔溶液是生产高品质铜箔前提条件之一。
增加过滤次数也是溶液净化的有效方法,通常循环过滤液量应为生产供液量的1.5倍以上。
提高溶液的净化,设备投入和运行费用会大幅增加,在净化工艺设计时要兼顾工艺性和经济性。
添加剂对电解铜箔组织性能的影响及优化

详细讲解添加剂对电解铜箔组织性能的影响及优化,不同添加剂对电解铜箔组织性能的影响,以及新型添加剂对组织性能的优化摘要:近年来,高性能电解铜箔被广泛应用于电子行业和锂电池行业等。
在铜箔的制备和生产过程中,添加剂对铜箔组织性能产生较大影响。
因普通添加剂暴露的问题多,已较难满足新产品的需求,为进一步提升产品,需开发性能更优越的添加剂。
文章先总结了普通添加剂对电解铜箔组织性能的影响,有无机类的氯离子,有机类的聚醚类化合物、含硫类化合物和明胶等。
在此基础上,对新型添加剂对电解铜箔组织性能的优化进行探讨:第一、6.0mg/L 硫酸铈盐可均匀细化晶粒,改善铜箔力学性能。
第二、聚二硫二丙烷磺酸钠-羟乙基纤维素-钨酸钠复合添加剂能使铜晶面向(220)择优取向,促进镀层均匀致密化。
第三、二巯基苯并咪唑后使铜箔晶粒尺寸变大且晶界数目变小,降低铜箔强度和表面粗糙度。
关键词:电解铜箔;添加剂;织构;力学性能;组织性能引言电解铜箔[1]是电子工业中的重要原料,主要应用于电路板及锂离子电池中。
电解铜箔采用直流电沉积技术,不溶性金属为阳极,钛锟为阴极,将两者浸入到硫酸铜电解液中进行电解,铜离子沉积在钛锟表面形成铜箔,再剥离、水洗、干燥,收卷后形成生箔,再经过表面处理工序得到铜箔。
1.电解铜箔组织性能及其影响电解铜箔的组织性能主要指铜箔的晶粒和晶面的生长、表面粗糙度及其织构[2]这三方面。
晶粒和晶面生长的宏观表现为对铜箔光面和毛面外观形貌和粗糙度的影响,因为铜晶粒晶面生长过程是在电解过程中析出铜原子,由液相铜离子转变为固相铜晶体,然后由一个固相转变为另一个固相的过程。
表面粗糙度是受晶粒的影响,晶粒有大小之分,统计后发现,大晶粒沉积形成的铜箔表面往往凹凸不平、甚至出现顶部聚集和铜刺等现象,颗粒大小不均匀现象,此时形成的铜箔其表面粗糙度较大。
当铜箔由小铜晶粒沉积形成时则情况相反。
铜箔的织构指的是晶面的择优取向[2]和晶面生长。
织构形成的实质是铜原子遵循各种不同的机制沉积排列成相对应的各种晶面,各个晶面的生长速度不同,部分晶面会择优生长,而择优生长的晶面就会形成织构,这些晶粒择优取向是无规律的。
电解铜箔论文:添加剂对电解铜箔组织性能的影响及优化

电解铜箔论文:添加剂对电解铜箔组织性能的影响及优化【中文摘要】近年来铜的电沉积已经受到了广泛研究,因为铜箔在印刷电路板和覆铜板行业中得到很好的应用。
而添加剂在铜电沉积过程对铜箔性能的影响中起着很重要的作用,即使是很微量的添加剂也能显著改变沉积层的性能。
本文利用SEM、微机控制万能试验机、高温拉伸机、电子背散射衍射分析技术、应力仪研究了聚二硫二丙烷磺酸钠(SP)、羟乙基纤维素(HEC)、聚乙二醇(PEG)、明胶、稀土铈盐等添加剂单独及共同作用时对铜电沉积的影响。
实验表明:SP整平效果较好,能提高铜箔抗拉强度和延伸率,尤其是高温延伸率。
加入0.2 mgL左右的SP,铜箔综合性能最好。
HEC能促使晶粒面向生长,抑制针孔,但会引起铜箔翘曲。
PEG能加大阴极极化,细化晶粒,使晶粒面向生长。
能抑制杂质金属的电沉积,防止异常晶粒长大。
同时能光滑尖锥状晶粒的峰尖,避免粗糙过度,但PEG过量会降低铜箔高温抗拉强度和延伸率。
P-6000效果要好于P-8000。
明胶具有细化晶粒和整平的效果,能够保证铜箔具有一定的粗糙度和提高铜箔常温抗拉强度和延伸率,但会降低铜箔高温抗拉强度和延伸率。
骨胶的效果要好于胶原蛋白。
适量的硫酸铈盐可以细化晶粒,使晶粒均匀致密,并能改善铜箔的力学性能,当铈离子浓度为6 mg/L,晶粒细化效果最好,力学性能最高。
通过正交试验,研究了不同添加剂配方对铜箔亮面晶粒微观结构、力学性能,以及内应力的影响,利用直观图示和数据分析得出了最优的3种添加剂配方,经过试验验证确定了添加剂最佳配比为:明胶、PEG、SP、HEC浓度分别为1.4mg/L、1.5 mg/L、0.35 mg/L、0.6mg/L。
制备出的铜箔内应力减少,铜箔缺陷也有所减少,亮面晶粒微观结构:孪晶(界)24.3%,(111)织构22.8%,晶粒平均尺寸250.4nm,毛面晶粒分布较均匀,铜箔力学性能也能提高,其中常温和高温抗拉强度分别是:376.5 MPa、197.1MPa,常温和高温延伸率分别是:5.6%、2.8%。
粗化工艺对电解铜箔抗剥离强度和劣化率的影响

粗化工艺对电解铜箔抗剥离强度和劣化率的影响
彭雪嵩;由宏伟;李兰晨;宋姝嬛;乐士儒;张锦秋;杨培霞;安茂忠
【期刊名称】《电镀与精饰》
【年(卷),期】2024(46)3
【摘要】铜箔粗化工艺与固化工艺是铜箔表面后处理中最关键的两个环节,粗化与固化工艺的好坏直接决定铜箔的性能。
根据铜箔粗化与固化工艺过程,本文研究了Cu2+浓度、电流密度、镀液温度等因素对铜箔表面形貌和抗剥离性能以及劣化率的影响,在优化后的工艺条件下制备出了抗剥离强度为1.29N/mm,劣化率为3.01%且无侧蚀的粗化电解铜箔。
【总页数】7页(P95-101)
【作者】彭雪嵩;由宏伟;李兰晨;宋姝嬛;乐士儒;张锦秋;杨培霞;安茂忠
【作者单位】哈尔滨工业大学化工与化学学院
【正文语种】中文
【中图分类】TQ153.1
【相关文献】
1.浅析影响电解铜箔抗剥离强度的因素及对策
2.粗化和固化电流密度对压延铜箔剥离强度的影响
3.钨酸钠复合添加剂深镀粗化电解铜箔表面处理工艺研究
4.钼酸钠-HEC-SPS复合添加剂对电解铜箔粗化效果的影响
5.钼酸钠-钨酸钠复合添加剂对铜箔电解粗化的影响
因版权原因,仅展示原文概要,查看原文内容请购买。
- 1、下载文档前请自行甄别文档内容的完整性,平台不提供额外的编辑、内容补充、找答案等附加服务。
- 2、"仅部分预览"的文档,不可在线预览部分如存在完整性等问题,可反馈申请退款(可完整预览的文档不适用该条件!)。
- 3、如文档侵犯您的权益,请联系客服反馈,我们会尽快为您处理(人工客服工作时间:9:00-18:30)。
越高 。粗化层 的结 构取 决 于溶 液 中 的 Cu 含 量 和 电流密度,Cun浓度越高 ,所需 电流密度越大,毛面 粗糙度 Rz越大 ,抗剥离强度越高。适当降低溶液中
抛 光 材 料
ER(I/IV)
cun浓度 和电流 密度 (大 于极 限 电流 ),既可 获 得较
2.2 表 处粗化பைடு நூலகம்层影响
 ̄PVA轮与阴极辊表面接触力的大小 ;
表 处粗化层 是为 了保 证铜 箔与基材 之 间具 有较
④冷却 液 的选 择 。
高 的结 合力 。粗 化 层 处 理 包 括 粗 化 和 固化 两 个 过
(2)在线抛光。在线抛光是将抛光装置安装在 程;粗化处理时 ,电解液应控制较低的含铜量及较高
之 钛晶粒 越粗 大 ,生 箔结 晶也 就 越 粗 大 ;见 图 1:钛 晶粒不 同时 的生箔 晶粒对 比。在铜 箔生产 中影 响 阴 极辊 表面状 况 主要 由阴极辊 研磨 、在线抛 光所决 定 。
2 影 响抗剥离强度因素
在 铜箔 生 产过 程 中 ,影 响铜箔 的抗剥 离 强 度 因 素较多 ,但主要 以生 箔 、表处 粗化层 、硅烷 最为 密切 。 2.1 生箔影 响
阴极辊是生产铜箔 的重要设备,目前阴极辊表 面 的材质大 多 数 为钛 。 阴极辊 表 面 钛 晶粒 的状 况 , 在一定程度上直接决定着生箔晶粒大小 、均匀性 。 阴极 辊表 面 的钛 晶粒越 细密 ,生箔 晶粒也越 细密 ;反
图 1 钛晶粒 不同时的生箔 晶粒对比
(1)阴极辊研磨。阴极 辊研磨工艺很多 ,但 目 前所使用 的研磨 材料主要为 :各种规格砂纸 (布)、 尼龙 轮 、尼龙刷 轮 、PVA轮 、研 磨绒 片 、绒 纱 轮 、绒 片 刷等。各铜箔厂根 据研磨工艺选用不 同的研磨材 料 。
a电解铜箔作为电子工业的重要基础材料随着电子产品向微型化尖端化高速发展对电子材料性能的要求也越来越高对铜箔质量也提出了更高的要求
2oo9 No4
铜 业 工 程
55
文章 编号 :1009—3842(2009)04—0055—03
浅析影响 电解铜箔抗剥离强度的 因素及对策
黄芳恩 (江铜 一耶兹铜箔有限公司,江西 南昌 330034)
密 的铜 。
①抛光材料 的选择 ,不 同的抛光材料对铜箔 的
粗化 层 的好 坏 直 接 影 响铜 箔 抗 剥 离 强 度 的 能
组 织结构及 毛面 的粗糙 度影 响很大 。表 l可看 出不 力 。在一定范 围 内,铜 箔粗化 层越 大 ,抗剥 离强度就
同抛光材料的影响。 目前在铜箔行业 ,经常使用的 抛光材料为碳化硅和氧化铝 ,碳化硅使用效果更好 。
生箔机上,阴极辊每生产一段时间或阴极辊表面出 的含酸量 ,通过电解作用 ,在铜箔表面发生铜沉积;
现细微 缺陷就 对 阴极辊辊 面进行 抛光 。在线 抛光能 形 成粗 大的粒状 和树 枝 状结 晶 ,获 得较 高 展 开度 的
保 证 阴极 辊表 面 的光 洁度 ,阴极辊 表 面光洁度 越高 , 粗糙面,达到高 比表面积。粗化是使铜箔表面镀上
高,研磨 阴极辊表 面越 细腻。PVA轮 按粒度 分为 (骨胶和皮胶)、HEC。
120 、220 、320 、600 等不同型号 ;
当然除添 加剂 因素 外 ,还 与 电流 密度 、溶 液 中杂
②研磨时 PVA轮旋转 、径给速度与阴极辊的旋 质含量 以及溶液中氯离子含量等有关。
转 速度 ;
金 刚 石 抛 光 膏
A12O3
— — 360—-——120
—
—
130一 。.70
低 的 Rz,又可稳定 抗剥 离强度 。一 般情 况下 获 得最 佳 抗 剥 离 强 度 和 蚀 刻 因 子 的 Cu¨ 浓 度 为
②抛光刷粒度的选择 ,抛光刷的粒度越高 ,抛光 2O一3Og/L、电 流 密度 为 25A/dm ~35A/dm 。表 2
生箔 结 晶状 况 的好 坏直 接影 响铜箔 的抗剥 离强 度 ;生箔晶粒致密、大小均匀 ,其抗剥离强度就越高 ; 生箔晶粒一般每平方英尺面积上有 4.5 X 10 个 ,毛 面粗糙度 Rz为 5 m左 右 (和铜 箔 的厚 度成 正 向关 系 ),生箔 毛 面 的抗 剥 离 强 度必 须 大 于 0.4kg/em , 一 般为 0.5—0.8kg/em 。经生 产 实 际证 明 ,影 响生 箔 结 晶状 况 的因素 主要 有 两个 方 面 ,一 是 阴极 辊 表 面状 况 ,二 是 电解 液 中的添加 剂 。 2.1.1 阴极 辊
摘 要 :该文对电解铜 箔生产过程 中影响抗剥 离强度 的原 因进行 了分析 ,重点 分析 了生 箔、表 处粗 化层、硅 烷
对 抗 剥 离强度 的影 响 。
关键 词 :生箔 ;表处粗化层 ;硅烷
中 图分 类号 :TM205
文献标 识 码 :A
1 前言
电解 铜 箔 作为 电子 工业 的重要 基 础材 料 ,随着 电子产品向微型化、尖端化高速发展 ,对电子材料性 能的要求也越来越高,对铜箔质量也提出了更高 的 要求。抗剥离强度作为 电解铜箔的基本性能 ,必须 满足电子行业中不同客户的要求 。但在铜箔生产过 程 中 ,经常 出现抗 剥 离 强度 低 、不稳 定 等 情 况 ,影 响 产品质量 ;导致产品降级 ,甚至报废 。
阴极 电位越 向负的方 向转 变 ,使 阴极极 化值增 大 ,提 均匀 球状结 晶 的氧化亚铜 ,增加 粗糙度 ,粗化镀 铜量
高铜 的析出过 电位 ,利于铜 离子结 晶细 腻。
为 3~5g/m 。固化 是 在 粗化 形 成 的结 晶面 镀 上 致
在线 抛光应 注意 以下几 个关键 问题 。
收稿 日期 :2009—09—22
铜 业 工 程
20o9 No4
我公司采 用 PVA轮研磨工艺 ;为保证 研磨质 不同的产品晶粒结构。合理地调整添加剂配方 ,且
量 ,研磨 时应考 虑几个 关键 问题 。
添加剂加入方式持续均匀 ,才能保证生箔晶粒细致、
O)PVA轮的选择 ,正常情况下 PVA轮的粒度越 均匀 。添 加 剂 种 类 也 有 很 多 ,常 见 的 主要 为 明胶