挤出复合剥离强度的影响因素
复合薄膜剥离强度影响因素探讨

作 用 。 化 学 作 用 发 生 在 黏 合 剂 与 薄 膜 表 面 的 活 性 基 团 之 间 ;物 理 作 用 主 要 是 ” 锚 效 应 ”和 分 子 间 的 作 用 力 。 投
黏合效果既由黏合剂决定 , 由复合材料的表面状态决 又 定 。由于黏合过程较复杂 . 在现有条件下无法进行测试和检
维普资讯
【 包 专ห้องสมุดไป่ตู้】 曼堕 _ 软 装 刊 蕉
P it g T c n lg r i e h oo y nn
复合 薄膜剥离强度
大连 大 富塑料彩 印有 限公 司 邢顺 川
剥离强度 是检测复合薄膜 物理性 能的一项 重要指标 。
一
5
4
5
4
5
5
5
5
4
m 5
∞ 电晕 电流 ∞ ∞ ∞ ∞ 布量 ∞ P 膜种类 黏合 剂选择 涂 ∞ E ∞ ∞
次要 因素
5
7
主要 因素
D E F F D E E F D
0
畸= 2
5
, 5
印刷 技术 一 0 6 1 — 3 — 2 0 / 3
维普资讯
一
剥离强度

挤出复合薄膜剥离强度的影响因素挤出复合工艺具有投资少,成本低,生产效率高,操作简便等多方面的优点,因此,它在塑料薄膜的复合加工中占有相当重要的地位。
但是,在实际生产中也难免会出现这样或那样的问题,在此,就以最为常见的剥离强度差为例与大家共同分析探讨。
基材对剥离强度的影响1.基材表面处理效果对剥离强度的影响被涂布基材应当预先进行电晕处理,使表面张力达到4.0×10-2N/m以上,以改进基材同熔融挤出树脂的黏结性,从而提高挤出复合强度。
因此,生产前要检测基材的表面张力是否达到要求,一旦发现表面张力太低,应立即更换基材或对基材重新进行表面处理。
此外,经表面处理过的薄膜,其表面张力应当是均匀一致的,否则也会对剥离强度产生一定的影响,造成剥离强度不均匀、不一致。
2.基材表面清洁度对剥离强度的影响被涂布基材表面应当无灰尘、无油污。
如果基材表面的清洁度差,黏附了灰尘、油脂等污物,就会直接影响到熔融树脂与塑料薄膜表面的黏合力,从而使挤出复合膜的黏结强度下降。
3.其他因素的影响对于一些易吸湿的薄膜材料(如尼龙薄膜),如果已经发生吸湿现象,也会影响挤出复合膜的黏结牢度。
因此,对于易吸湿的薄膜材料一定要注意防潮,尼龙薄膜在使用前和使用后应当及时用铝箔包裹好。
油墨对剥离强度的影响1.油墨质量对剥离强度的影响在实际生产过程中,有时候会出现无油墨或油墨较少部位的剥离强度好,而有油墨或油墨较多部位的黏合牢度比较差的现象。
这就是由于所用的油墨印刷适性不好,油墨与基材之间黏结不良,从而造成挤出复合膜的剥离强度差。
一旦发生这种情况,应当及时更换合适的油墨,并同油墨厂商联系,共同协商和研究解决办法。
2.油墨干燥性对剥离强度的影响如果油墨干燥不良,特别是当油墨中大量地使用了甲苯、丁醇等沸点比较高的溶剂,而且干燥箱温度设置不当时,就会有少量或较大量的溶剂残留在油墨层中,复合后可能会造成复合膜的分层,使剥离强度变差。
因此,在印刷过程中一定要对油墨的干燥性能进行严格的控制,保证油墨能够充分干燥。
挤出复合剥离强度的影响因素

挤出复合剥离强度的影响因素随着我国挤出复合设备技术性能的不断提高,涂复级树脂如LDPE、PP等及复合粘接级树脂EVA、EMA、EAA等的不断开发,挤出复合工艺以本钱低、无残留溶剂等长处,逐渐被广大软包装企业所同意。
而高涂复速度和高剥离强度是困扰众多软包装企业的两难问题。
笔者按照生产实践,就挤出复合工艺对剥离强度的影响因素与包装同行一路探讨。
一、树脂塑化混炼程度挤出复合是将热塑性树脂如LDPE、PP、EVA、EMA、EAA等加入料筒,在螺杆的作用下,经紧缩区高温熔融成粘流态,在均化区高温、高压、高剪切条件下,进一步塑化混炼均匀,随着螺杆的推动而被定压、定量、定温地经T模头持续均匀挤出。
树脂的塑化混炼程度是影响挤出复合剥离强度的主要因素之一。
树脂塑化混炼越充分,复合后剥离强度越高。
通常采用以下方式增加树脂塑化混炼程度:1.选用熔融指数(MI)较大的树脂熔融指数(MI)越大,流动性越好,塑化混炼效果越好。
但MI太大,则挤出薄膜发生边厚现象。
故宜选用MI为8g/10min左右的树脂。
2.适当提高加热温度紧缩区、均化区加热温度越高,树脂塑化混炼越充分;但温度太高树脂易分解。
加热温度的设定要按照树脂种类及其熔融指数(MI)来设定。
如牌号为1C7A的LDPE树脂,其加热温度在300~325℃范围内设定。
3.适当提高熔体压强熔体所受压强越大,塑化混炼就越充分;增加熔体压强,常采用增加滤网层数或目数的方式。
如牌号为1C7A的LDPE树脂采用目数别离为85、110、85的三层滤网,使溶体压强在1.2~1.4MPa范围内。
4.适当提高螺杆转速螺杆转速越大,单位熔体所受螺杆剪切次数越多,塑化混炼就越充分。
但螺杆转速增大,挤出薄膜厚度增加。
故应注意螺杆转速、涂复速度与挤出薄膜厚度三者的匹配。
二、树脂的氧化程度粘流态树脂经模唇挤出到接触基材的进程中,被空气中的氧气氧化而产生极性,提高挤出复合剥离强度。
气隙即模唇到两薄膜(即挤出薄膜与基材)复合线的距离。
造成剥离强度偏低的几大原因
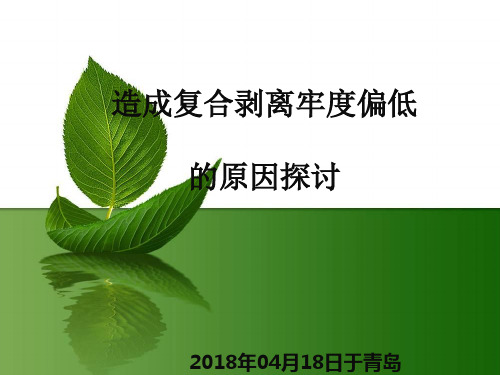
2021/5/27
15
3、油墨残留溶剂消耗固化剂: 此类现象在使用聚氨酯油墨的产品上比较多见,由于聚氨酯油
墨中的羟基与双组分胶黏剂中的-NCO发生反应,消耗掉部分固化剂, 导致胶水不能完全固化,影响产品剥离强度。因的溶剂,在印刷工序中,尽量减少 溶剂的残留。
2021/5/27
30
残留溶剂太多引起析皱脱层;
2021/5/27
31
五、其它因素影响:
1、生产车间周边环境脏、灰尘多;湿度大影响: 环境因素影响如灰尘及杂质、水气,胶液中含有其它物质,胶液混 浊反白都会影响复合牢。
R-NCO+H2O----R-NH2+CO2
这一步反应虽然不是很快,但比起固化剂中的异氰酸酯和主剂反应 要快得多约20倍。若加上空气中的灰尘或杂质形成有核的气泡
2021/5/27
16
常用的塑料油墨、胶粘剂(检测适用)标准:
1、细度:GB/T13217.3—2008; 2、粘度: GB/T13217.4—2008; 3、初干性: GB/T13217.5—2008; 4、着色力: GB/T13217.6—2008; 5、附着牢度: GB/T13217.7—2008; 6、QB/T2024—2012凹版塑料薄膜复合油墨; 7、QB/T1046—2012表印油墨;
2021/5/27
19
B-1芳香族---固化剂异氰酸酯基(NCO)直接与芳香环相连接,经 水解后会变成芳香胺,生成的聚氨酯有较大的毒性,是一种致癌物, 不可用于水煮、蒸煮袋。
B-2脂肪族---NCO不直接与芳香环相接,水解后只生成脂肪胺,一 般可用于水煮蒸煮袋用胶。
2021/5/27
20
三、胶粘剂原因:
2021/5/27
浅谈软塑包装复合剥离强度及控制方法
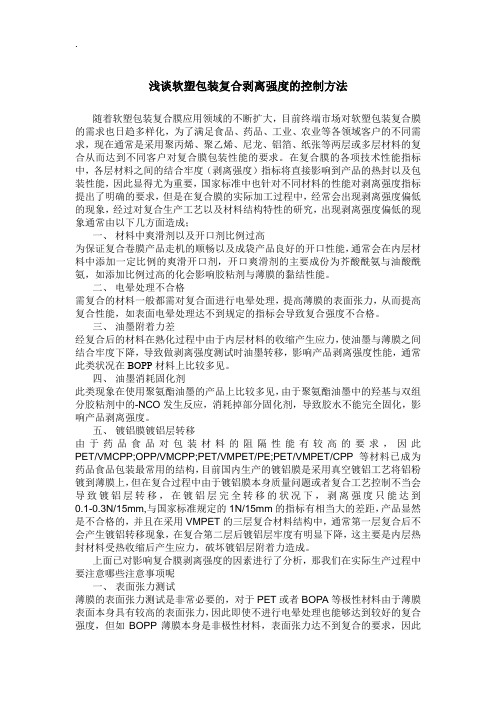
浅谈软塑包装复合剥离强度的控制方法随着软塑包装复合膜应用领域的不断扩大,目前终端市场对软塑包装复合膜的需求也日趋多样化,为了满足食品、药品、工业、农业等各领域客户的不同需求,现在通常是采用聚丙烯、聚乙烯、尼龙、铝箔、纸张等两层或多层材料的复合从而达到不同客户对复合膜包装性能的要求。
在复合膜的各项技术性能指标中,各层材料之间的结合牢度(剥离强度)指标将直接影响到产品的热封以及包装性能,因此显得尤为重要,国家标准中也针对不同材料的性能对剥离强度指标提出了明确的要求,但是在复合膜的实际加工过程中,经常会出现剥离强度偏低的现象,经过对复合生产工艺以及材料结构特性的研究,出现剥离强度偏低的现象通常由以下几方面造成;一、材料中爽滑剂以及开口剂比例过高为保证复合卷膜产品走机的顺畅以及成袋产品良好的开口性能,通常会在内层材料中添加一定比例的爽滑开口剂,开口爽滑剂的主要成份为芥酸酰氨与油酸酰氨,如添加比例过高的化会影响胶粘剂与薄膜的黏结性能。
二、电晕处理不合格需复合的材料一般都需对复合面进行电晕处理,提高薄膜的表面张力,从而提高复合性能,如表面电晕处理达不到规定的指标会导致复合强度不合格。
三、油墨附着力差经复合后的材料在熟化过程中由于内层材料的收缩产生应力,使油墨与薄膜之间结合牢度下降,导致做剥离强度测试时油墨转移,影响产品剥离强度性能,通常此类状况在BOPP材料上比较多见。
四、油墨消耗固化剂此类现象在使用聚氨酯油墨的产品上比较多见,由于聚氨酯油墨中的羟基与双组分胶粘剂中的-NCO发生反应,消耗掉部分固化剂,导致胶水不能完全固化,影响产品剥离强度。
五、镀铝膜镀铝层转移由于药品食品对包装材料的阻隔性能有较高的要求,因此PET/VMCPP;OPP/VMCPP;PET/VMPET/PE;PET/VMPET/CPP等材料已成为药品食品包装最常用的结构,目前国内生产的镀铝膜是采用真空镀铝工艺将铝粉镀到薄膜上,但在复合过程中由于镀铝膜本身质量问题或者复合工艺控制不当会导致镀铝层转移,在镀铝层完全转移的状况下,剥离强度只能达到0.1-0.3N/15mm,与国家标准规定的1N/15mm的指标有相当大的差距,产品显然是不合格的,并且在采用VMPET的三层复合材料结构中,通常第一层复合后不会产生镀铝转移现象,在复合第二层后镀铝层牢度有明显下降,这主要是内层热封材料受热收缩后产生应力,破坏镀铝层附着力造成。
影响粘结力和剥离强度的因素

影响塑料薄膜粘结力和剥离强度的因素塑料薄膜表面电晕处理不好,表面张力低,就会导致墨层附着牢度低,复合膜粘结强度低,在薄膜投入前应认真检测其表面张力值务必提高到3.8×10-2N/m以上,最好能达到4.0-4.2×10-2N/m,因为3.8×10-2N/m只是最低要求,表面张力值低于3.8×10-2N/m的薄膜根本就不能使油墨和胶粘剂完全铺展,复合后的成品当然达不到剥离强度的要求。
检测薄膜表面张力的方法通常有两种:1)达因笔测试,达因笔的笔液通常呈红色,规格有3.8×10-2N/m、4.0×10-2N/m、4.2×10-2N/m、4.4×10-2N/m以及4.8×10-2N/m这五种,如果用达因笔在薄膜上的笔液不收缩,均匀,无断层,则说明薄膜的表面张力已经达到使用要求,相反,笔液收缩,消失,不均匀,不连续,则说明处理不够;2)用BOPP单面胶布测试,将BOPP单面胶布贴在待测薄膜表面再撕开,电晕处理好的通常剥离声音小,粘贴牢固,相反则粘贴不牢,容易剥离,这种测试方法要依靠经验,不适合测试PET、PA等薄膜。
电晕处理不符合要求的基材决不能进行复合,因为复合后肯定达不到包装产品对剥离强度的要求。
常用基材的表面张力值为:BOPP3.8×10-2N/m、PET5.0×10-2N/m、PA5.2×10-2N/m。
溶剂残留量太高影响剥离强度,影响粘结力残留溶剂太多,复合后会形成许多微小气泡,使相邻的复合基材脱离、分层、气泡越多,剥离强度越低,要提高剥离强度,就必须减少气泡的产生。
气泡的产生与许多因素有关,诸如上胶不均匀,烘干道温度过低,热压辊温度偏低及室内温湿度不合适等,通常,室内温度宜控制在23-25℃,相对湿度应控制在50%-60%为宜,另外,避免使用高沸点溶剂,也可减少气泡的产生。
总之为提高剥离强度,提高粘接力应尽可能降低残留溶剂。
层间剥离强度差的原因及解决方法,请收好!

层间剥离强度差的原因及解决方法,请收好!
珠光膜复合产品剥离强度不高的原因主要包括层间剥离强度问题和热封剥离强度问题。
接下来,本文将重点讲解导致层间剥离强度差的原因及解决方法。
层间剥离强度差的原因:
①珠光膜材料或印刷BOPP材料表面张力低,不符合印刷或复合要求。
②干燥温度控制不当或使用的溶剂大量残留影响剥离强度。
③印刷油墨与印刷基材不亲和,相容性不好。
④选择的黏合剂不合。
⑤复合烘箱温度控制不当,对溶剂挥发造成严重影响。
⑥复合辊温度太低。
⑦熟化时间或温度控制上出现问题。
双组份聚氨酯黏合剂熟化时间一般控制在24~48小时,熟化温度控制在50%左右。
解决办法是:
①提高材料的表面张力。
BOPP38达因,PET50达因。
②调整印刷温度或降低印刷速度,对溶剂进行调节。
③严禁混用不相同的树脂体系油墨。
④更换黏合剂,建议选择专用的黏合剂。
该黏合剂主要特点是胶体柔软,抗冷冻性特别好,产品不发硬,高流动性,使用成本更低,固化速度快,8小时就可分切加工,复合适性及产品平整性佳。
⑤提高胶水的浓度,检测刮刀的角度,检测涂胶辊的网孔深度与线数。
⑥温度采用由低到高的控制方法,另外要考虑排风系统的风速问题,或降低复合机速。
⑦提高复合辊温度。
其实复合辊温度的高低,应该与机速、材料的厚薄有很大的关系,还与胶水的性质有关系。
⑧控制好熟化时间和温度。
复合薄膜竟出现剥离强度低的现象,搞不清楚这几点就晚了!
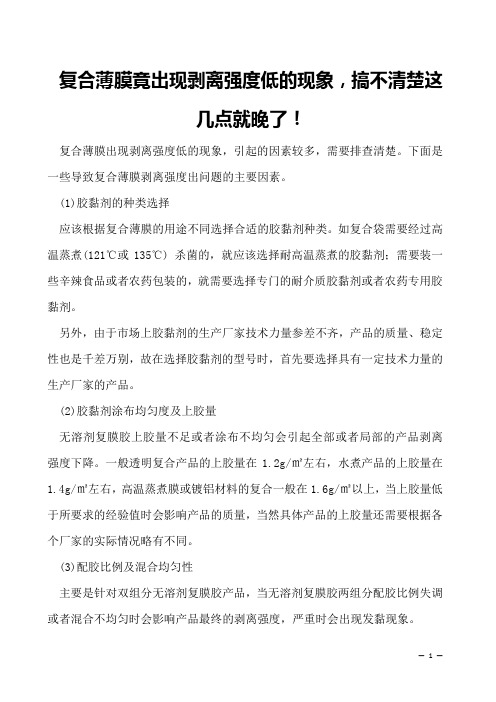
复合薄膜竟出现剥离强度低的现象,搞不清楚这几点就晚了!复合薄膜出现剥离强度低的现象,引起的因素较多,需要排查清楚。
下面是一些导致复合薄膜剥离强度出问题的主要因素。
(1)胶黏剂的种类选择应该根据复合薄膜的用途不同选择合适的胶黏剂种类。
如复合袋需要经过高温蒸煮(121℃或135℃) 杀菌的,就应该选择耐高温蒸煮的胶黏剂;需要装一些辛辣食品或者农药包装的,就需要选择专门的耐介质胶黏剂或者农药专用胶黏剂。
另外,由于市场上胶黏剂的生产厂家技术力量参差不齐,产品的质量、稳定性也是千差万别,故在选择胶黏剂的型号时,首先要选择具有一定技术力量的生产厂家的产品。
(2)胶黏剂涂布均匀度及上胶量无溶剂复膜胶上胶量不足或者涂布不均匀会引起全部或者局部的产品剥离强度下降。
一般透明复合产品的上胶量在1.2g/㎡左右,水煮产品的上胶量在1.4g/㎡左右,高温蒸煮膜或镀铝材料的复合一般在1.6g/㎡以上,当上胶量低于所要求的经验值时会影响产品的质量,当然具体产品的上胶量还需要根据各个厂家的实际情况略有不同。
(3)配胶比例及混合均匀性主要是针对双组分无溶剂复膜胶产品,当无溶剂复膜胶两组分配胶比例失调或者混合不均匀时会影响产品最终的剥离强度,严重时会出现发黏现象。
(4)复合基材的表面张力当复合基材的表面张力低于要求值时,会严重影响产品复合后的剥离强度,一般薄膜电晕处理后应尽快使用,随着时间的延长,处理过的薄膜表面张力会逐渐降低。
建议每次开机前用达因笔检查待复合材料的表面张力是否合格。
(5)熟化程度无溶剂胶无溶剂胶黏剂的分子量较低,基本没有初黏力;复合后需要在40~ 50°C的熟化室中进行进一步的交联固化。
当熟化室温度过低、熟化时间较短或者低温存放时间过长都会影响产品的最终剥离强度,有些重新放置熟化也没有明显的效果,这主要是部分异氰酸酯组分已经与水汽发生了反应的缘故。
(6)基材添加剂等其他因素的影响塑料薄膜中添加剂 (如滑爽剂)迁移到复合材料的表面与胶黏剂的异氰酸酯组分反应,降低产品最终的剥离强度;可以适当降低熟化温度来减少塑料薄膜中添加剂的迁移。
pvb 剥离强度

pvb 剥离强度在我们日常生活中,剥离强度这一概念显得尤为重要。
它通常用来衡量材料之间的粘结或连接强度,特别是在工业生产和日常用品中。
本文将详细介绍剥离强度的定义、影响因素、提高方法以及在实际应用中的案例。
一、剥离强度的定义和重要性剥离强度,又称剥离力,是指在特定条件下,材料之间粘结或连接所能承受的最大力量。
它是一个重要的性能指标,关系到产品质量和使用寿命。
剥离强度越高,表明材料之间的粘结或连接越牢固,产品在使用过程中不易出现脱落、损坏等现象。
二、影响剥离强度的因素1.材料性质:不同材料之间的剥离强度有较大差异,如塑料与金属之间的剥离强度通常较低,而同种材料之间的剥离强度较高。
2.粘结剂:粘结剂的种类和质量对剥离强度有很大影响。
选用高性能的粘结剂可以提高剥离强度。
3.表面处理:对粘结表面进行处理,如活化、粗糙化等,可以提高剥离强度。
4.粘结面积:剥离强度与粘结面积成正比,粘结面积越大,剥离强度越高。
5.环境条件:温度、湿度等环境条件会影响剥离强度。
在特定环境下,剥离强度可能出现波动。
三、提高剥离强度的方法1.选用高性能的粘结剂:提高剥离强度最直接的方法就是使用优质的粘结剂,以增强材料之间的粘结力。
2.对表面进行处理:对粘结表面进行适当的表面处理,如粗糙化、活化等,以提高剥离强度。
3.增加粘结面积:在条件允许的情况下,适当增加粘结面积,可以提高剥离强度。
4.优化生产工艺:改进生产工艺,如调整温度、压力等参数,以提高剥离强度。
四、剥离强度在实际应用中的案例1.包装行业:在包装材料中,剥离强度是一个关键性能指标。
高剥离强度的包装可以确保产品在运输、存储过程中不易损坏。
2.电子产品:在电子产品中,剥离强度关系到零部件的稳定性和使用寿命。
例如,手机屏幕与边框之间的剥离强度要求较高,以防止屏幕脱落。
3.汽车制造:汽车制造中的车身涂装、内饰等领域,都需要考虑剥离强度。
高剥离强度的涂装可以提高车身的耐久性,内饰材料的高剥离强度可以确保零部件的稳定性。
造成剥离强度偏低的几大原因

陈孟杰
2018年04月18日于青岛
造成复合剥离牢度偏低的因素很多,除复合工序因素外,如:
印刷薄膜表面润湿张力处理度不足,复合的油墨与薄膜附着牢度不好, 薄膜中增塑剂、抗氧化剂等添加剂的类型、品质、粒径大小、含量
多少都对复合牢度产生影响,这些添加物会影响到薄膜的表面极性
4、热封层厚度:
热封层厚度一般不低于40um,厚度过低,则易产生剥离牢度偏 低。但是厚度大的热封层薄膜(60um以上),生产时都会加入大量
添加剂。因此,在购买CPP或PE时要购尽量少加或不加添加剂的
薄膜。(水煮、蒸煮袋热封层不低于60um)
常用塑料薄膜外观质量应符合:
项
1、 2、 3、
目 名 称
塑料凹版里印油墨常规检测:
检测项目 着色力 检 验 方 法 分别取试样和标准样油墨各1g,白墨10g用同数 量冲淡剂分别冲淡,并在标准刮样纸上刮样对比 至试样与标准一致,S=D/C×100%。其中S=着色 力百分比、C=冲淡标准样所用白墨量 D=冲淡标准墨所用白墨量。 试样和标准样在试验纸上并排用小刮刀刮样目测对比 标 准 95~100% 工 具 广口烧杯 天平 玻璃棒 标准白墨 带黑条试验纸 小刮墨刀
以上蒸煮油墨除选择耐热度外,还应根据厂家要求加入一定量的油 墨专用固化剂以加强油墨对薄膜的附着力,提高复合牢度。
2、油墨附着力差: 经复合后的材料在熟化过程中由于内层材料的收缩产生应力, 使油墨与薄膜之间结合牢度下降,导致做剥离强度测试时油墨转移, 影响产品剥离强度性能,此类状况在BOPP 材料上比较多见。另外, 在油墨品种中一些染料油墨、金银油墨、珠光油墨对复合强度影响 较大,我们在选择油墨上要从油墨类型、细度、耐热度或油墨与材料、 胶粘剂的相互匹配上加以注意。
无溶剂复合剥离强度低下的问题

无溶剂复合剥离强度低下的问题(1)薄膜基材的表面张力偏低薄膜基材的表面张力偏低,是引起无溶剂复合产品剥离强度低下的最常见的因素之一,因此当发现复合产品的剥离强度低时,首先应当检查基材的表面张力,若基材的表面张力达不到复合的最低要求时,应对它进行电晕处理,若经电晕处理之后,仍达不到要求,则应当更换基材之后,再进行复合。
(2)无溶剂复合的胶黏剂两组分的配比不当无溶剂复合的胶黏剂两组分的配比不当,也是引起复合产品剥离强度低下的一个常见的原因。
胶黏剂两组分配比不当,熟化时胶黏剂的化学反应不良,必然会导致复合产品的剥离强度低下,因此在确定基材的表面张力没有问题的情况下,一旦发现剥离强度欠佳,应当首先考虑胶黏剂的组分间的配比问题,仔细检查胶黏剂的主剂与交联剂的比例是否在胶黏剂供应商提供的参考值的范围之内,如偏离参考值,应予以及时调节。
双组分胶黏剂配比的准确与否,直接关系到复合后的产品质量,这是不言而喻的。
为保证配比准确性,一般都采用自动供胶、混胶系统。
自动供胶、混胶系统中的混胶泵(不管是柱塞泵或是齿轮泵),一般都带有胶液比例失调自动报警系统,新胶泵使用时都不会有问题,但随着使用年限的延长,或相关保证措施跟不上,混胶泵可能会出现问题(胶黏剂比例失衡而出现混胶泵不报警的情况)。
这种情况下,若没有必要、及时的监测手段,就会出现大批量的质量事故;普通物性检测反馈较慢,一般24h后才会知道结果,若真有问题,那么这么长时间的损失也很大。
为弥补这种缺憾,最原始的办法是定时人工称量配比,简单有效,但这种方法适合在开机前实施,而在设备运行中实施则不方便进行。
吴孝俊等提出了一•种对胶黏剂组分实际比例的监控方法,对实际生产具有较大的参考价值,那就是利用折射仪测试胶液折射率,来观察胶黏剂的组分比例是否失常。
因为只要胶黏剂的两组分是比例确定,一定温度下,混合后的胶液折射率是一定的,虽然在无溶剂复合的过程中,因为温度、测试时间的影响,折射率会有一些变化,但都是有规律可循的,如果胶黏剂比例发生明显变化,那么测出的胶液折射率也会相应变化。
挤出复合薄膜剥离强度影响因素(一)
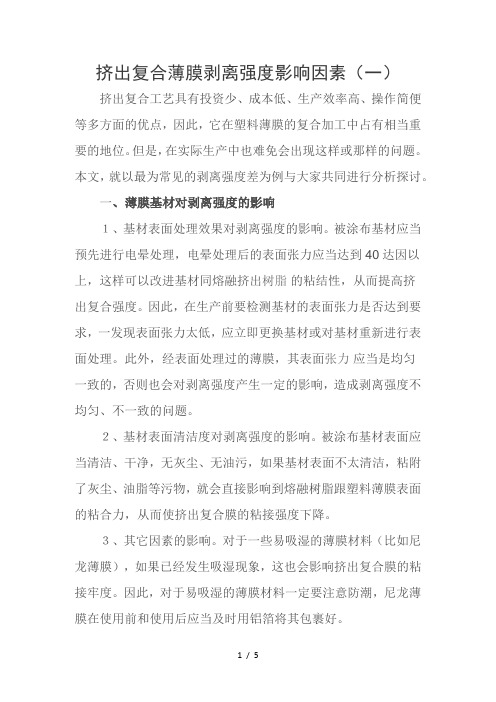
挤出复合薄膜剥离强度影响因素(一)挤出复合工艺具有投资少、成本低、生产效率高、操作简便等多方面的优点,因此,它在塑料薄膜的复合加工中占有相当重要的地位。
但是,在实际生产中也难免会出现这样或那样的问题。
本文,就以最为常见的剥离强度差为例与大家共同进行分析探讨。
一、薄膜基材对剥离强度的影响1、基材表面处理效果对剥离强度的影响。
被涂布基材应当预先进行电晕处理,电晕处理后的表面张力应当达到40达因以上,这样可以改进基材同熔融挤出树脂的粘结性,从而提高挤出复合强度。
因此,在生产前要检测基材的表面张力是否达到要求,一发现表面张力太低,应立即更换基材或对基材重新进行表面处理。
此外,经表面处理过的薄膜,其表面张力应当是均匀一致的,否则也会对剥离强度产生一定的影响,造成剥离强度不均匀、不一致的问题。
2、基材表面清洁度对剥离强度的影响。
被涂布基材表面应当清洁、干净,无灰尘、无油污,如果基材表面不太清洁,粘附了灰尘、油脂等污物,就会直接影响到熔融树脂跟塑料薄膜表面的粘合力,从而使挤出复合膜的粘接强度下降。
3、其它因素的影响。
对于一些易吸湿的薄膜材料(比如尼龙薄膜),如果已经发生吸湿现象,这也会影响挤出复合膜的粘接牢度。
因此,对于易吸湿的薄膜材料一定要注意防潮,尼龙薄膜在使用前和使用后应当及时用铝箔将其包裹好。
二、油墨对剥离强度的影响在实际生产过程中,有时候会出现无油墨或油墨较少部位的剥离强度好、而有油墨或油墨较多部位的粘合牢度反而比较差的现象,这就是由于所用的印刷油墨的适性不好,油墨与基材之间的粘接不良,从而造成挤出复合膜的剥离强度差。
一旦发生这种情况,应当及时更换合适的油墨,并同油墨厂商了解,共同协商和研究解决办法。
2、油墨干燥性对剥离强度的影响。
如果油墨干燥不良,特别是当油墨中大量地使用了甲苯、丁醇等沸点比较高的溶剂,而且干燥箱温度设置不当的话,就会有少量或较大量的溶剂残留在油墨层中,复合后可能会造成复合膜的分层,使剥离强度变差。
影响剥离强度的因素有哪些
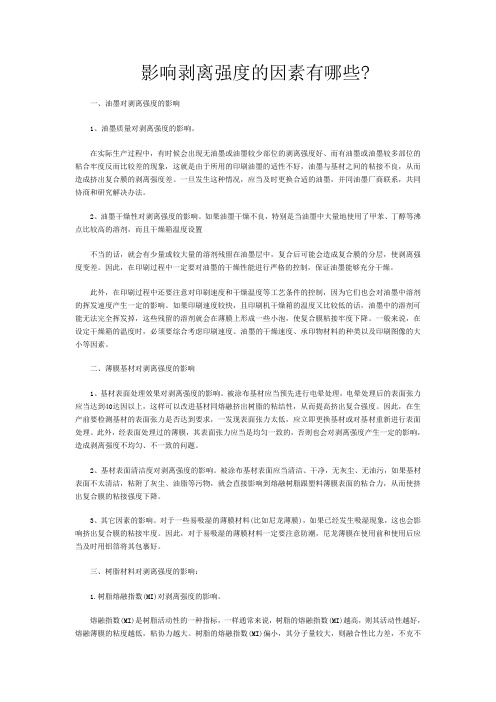
影响剥离强度的因素有哪些?一、油墨对剥离强度的影响1、油墨质量对剥离强度的影响。
在实际生产过程中,有时候会出现无油墨或油墨较少部位的剥离强度好、而有油墨或油墨较多部位的粘合牢度反而比较差的现象,这就是由于所用的印刷油墨的适性不好,油墨与基材之间的粘接不良,从而造成挤出复合膜的剥离强度差。
一旦发生这种情况,应当及时更换合适的油墨,并同油墨厂商联系,共同协商和研究解决办法。
2、油墨干燥性对剥离强度的影响。
如果油墨干燥不良,特别是当油墨中大量地使用了甲苯、丁醇等沸点比较高的溶剂,而且干燥箱温度设置不当的话,就会有少量或较大量的溶剂残留在油墨层中,复合后可能会造成复合膜的分层,使剥离强度变差。
因此,在印刷过程中一定要对油墨的干燥性能进行严格的控制,保证油墨能够充分干燥。
此外,在印刷过程中还要注意对印刷速度和干燥温度等工艺条件的控制,因为它们也会对油墨中溶剂的挥发速度产生一定的影响。
如果印刷速度较快,且印刷机干燥箱的温度又比较低的话,油墨中的溶剂可能无法完全挥发掉,这些残留的溶剂就会在薄膜上形成一些小泡,使复合膜粘接牢度下降。
一般来说,在设定干燥箱的温度时,必须要综合考虑印刷速度、油墨的干燥速度、承印物材料的种类以及印刷图像的大小等因素。
二、薄膜基材对剥离强度的影响1、基材表面处理效果对剥离强度的影响。
被涂布基材应当预先进行电晕处理,电晕处理后的表面张力应当达到40达因以上,这样可以改进基材同熔融挤出树脂的粘结性,从而提高挤出复合强度。
因此,在生产前要检测基材的表面张力是否达到要求,一发现表面张力太低,应立即更换基材或对基材重新进行表面处理。
此外,经表面处理过的薄膜,其表面张力应当是均匀一致的,否则也会对剥离强度产生一定的影响,造成剥离强度不均匀、不一致的问题。
2、基材表面清洁度对剥离强度的影响。
被涂布基材表面应当清洁、干净,无灰尘、无油污,如果基材表面不太清洁,粘附了灰尘、油脂等污物,就会直接影响到熔融树脂跟塑料薄膜表面的粘合力,从而使挤出复合膜的粘接强度下降。
挤出复合薄膜剥离强度影响因素浅析(二)

挤出复合薄膜剥离强度影响因素浅析(二)4、复合压力对剥离强度的影响。
复合压力小,熔融树脂与基材之间贴合不紧密,会使剥离牢度下降。
但复合压力也不可太大,否则基材容易被压变形。
5、冷却钢辊表面温度对剥离强度的影响。
冷却辊采用的是表面镀铬的钢辊筒,其作用是将熔融树脂薄膜的热量带走,让粘合后的复合膜立即冷却、固化,以形成较强的内聚力,使熔融薄膜跟被涂布基材粘牢、定型,不产生相对位移,从而保证良好的剥离强度。
因此,冷却钢辊表面的温度对挤出复合薄膜的剥离强度有着一定的影响。
如果冷却钢辊的表面温度太高,则冷却定型效果不好,可能使挤出复合膜起皱,会使复合牢度下降;但如果冷却钢辊的表面温度太低,冷却速度太快的话,也会引起复合强度的降低。
一般来说,冷却辊的表面温度控制在30'C左右最佳。
而且,冷却辊表面必须光滑,表面温度分布应当均匀一致,这样才能保证挤出复合膜的冷却效果一致,从而保证其粘接牢度和剥离强度的一致性。
6、硅橡胶压力辊表面状态对剥离强度的影响。
硅橡胶压力辊的作用是将基材和熔融树脂膜以一定的压力压向冷却辊,使基材和熔融膜压紧、粘合,并冷却、固化成型。
硅橡胶压力辊是在钢辊的外表面包覆了20—25mm厚的硅橡胶而制成的,硅橡胶的硬度一般为80--85肖氏硬度为最佳,而且,硅橡胶压力辊表面的硬度应当均匀一致,这样才能保证整体压力基本保持均匀一致,从而保证挤出复合产品剥离牢度的均匀、恒定。
7、复合线速度对剥离强度的影响。
在挤出量一定的情况下,即挤出主电机转速不变的情况下,复合线速度越快,则复合层越薄,热熔膜温度将会下降,涂布基材上的热量减少,熔融树脂的钻合力降低,从而也就造成剥离强度的下降。
相反,复合线速度降低,复合层厚度增加,复合强度也会有所提高,但却会影响生产速度。
因此,在生产过程中一定要根据实际情况控制好适当的生产速度,既要保证生产进度,又要保证挤出剥离强度和复合质量。
8、挤出涂复层厚度对剥离强度的影响。
浅谈软塑包装复合剥离强度的控制方法精选版

浅谈软塑包装复合剥离强度的控制方法Document serial number【KKGB-LBS98YT-BS8CB-BSUT-BST108】浅谈软塑包装复合剥离强度的控制方法随着软塑包装复合膜应用领域的不断扩大,目前终端市场对软塑包装复合膜的需求也日趋多样化,为了满足食品、药品、工业、农业等各领域客户的不同需求,现在通常是采用聚丙烯、聚乙烯、尼龙、铝箔、纸张等两层或多层材料的复合从而达到不同客户对复合膜包装性能的要求。
在复合膜的各项技术性能指标中,各层材料之间的结合牢度(剥离强度)指标将直接影响到产品的热封以及包装性能,因此显得尤为重要,国家标准中也针对不同材料的性能对剥离强度指标提出了明确的要求,但是在复合膜的实际加工过程中,经常会出现剥离强度偏低的现象,经过对复合生产工艺以及材料结构特性的研究,出现剥离强度偏低的现象通常由以下几方面造成;一、材料中爽滑剂以及开口剂比例过高为保证复合卷膜产品走机的顺畅以及成袋产品良好的开口性能,通常会在内层材料中添加一定比例的爽滑开口剂,开口爽滑剂的主要成份为芥酸酰氨与油酸酰氨,如添加比例过高的化会影响胶粘剂与薄膜的黏结性能。
二、电晕处理不合格需复合的材料一般都需对复合面进行电晕处理,提高薄膜的表面张力,从而提高复合性能,如表面电晕处理达不到规定的指标会导致复合强度不合格。
三、油墨附着力差经复合后的材料在熟化过程中由于内层材料的收缩产生应力,使油墨与薄膜之间结合牢度下降,导致做剥离强度测试时油墨转移,影响产品剥离强度性能,通常此类状况在BOPP材料上比较多见。
四、油墨消耗固化剂此类现象在使用聚氨酯油墨的产品上比较多见,由于聚氨酯油墨中的羟基与双组分胶粘剂中的-NCO发生反应,消耗掉部分固化剂,导致胶水不能完全固化,影响产品剥离强度。
五、镀铝膜镀铝层转移由于药品食品对包装材料的阻隔性能有较高的要求,因此PET/VMCPP;OPP/VMCPP;PET/VMPET/PE;PET/VMPET/CPP等材料已成为药品食品包装最常用的结构,目前国内生产的镀铝膜是采用真空镀铝工艺将铝粉镀到薄膜上,但在复合过程中由于镀铝膜本身质量问题或者复合工艺控制不当会导致镀铝层转移,在镀铝层完全转移的状况下,剥离强度只能达到与国家标准规定的1N/15mm的指标有相当大的差距,产品显然是不合格的,并且在采用VMPET的三层复合材料结构中,通常第一层复合后不会产生镀铝转移现象,在复合第二层后镀铝层牢度有明显下降,这主要是内层热封材料受热收缩后产生应力,破坏镀铝层附着力造成。
对剥离强度产生影响的因素
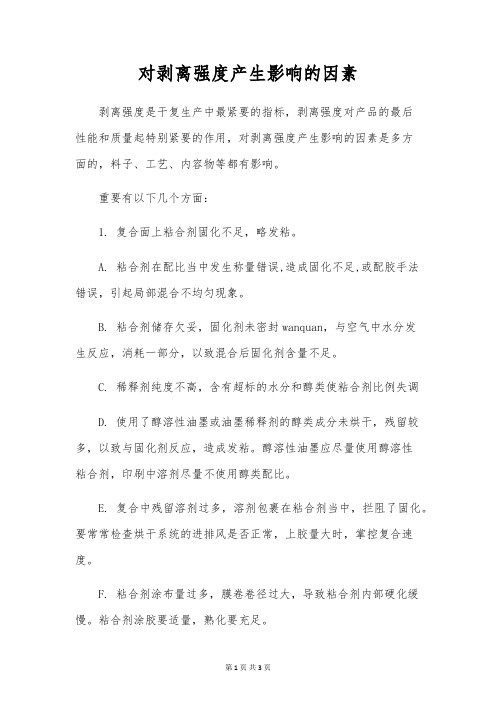
对剥离强度产生影响的因素剥离强度是干复生产中最紧要的指标,剥离强度对产品的最后性能和质量起特别紧要的作用,对剥离强度产生影响的因素是多方面的,料子、工艺、内容物等都有影响。
重要有以下几个方面:1. 复合面上粘合剂固化不足,略发粘。
A. 粘合剂在配比当中发生称量错误,造成固化不足,或配胶手法错误,引起局部混合不均匀现象。
B. 粘合剂储存欠妥,固化剂未密封wanquan,与空气中水分发生反应,消耗一部分,以致混合后固化剂含量不足。
C. 稀释剂纯度不高,含有超标的水分和醇类使粘合剂比例失调D. 使用了醇溶性油墨或油墨稀释剂的醇类成分未烘干,残留较多,以致与固化剂反应,造成发粘。
醇溶性油墨应尽量使用醇溶性粘合剂,印刷中溶剂尽量不使用醇类配比。
E. 复合中残留溶剂过多,溶剂包裹在粘合剂当中,拦阻了固化。
要常常检查烘干系统的进排风是否正常,上胶量大时,掌控复合速度。
F. 粘合剂涂布量过多,膜卷卷径过大,导致粘合剂内部硬化缓慢。
粘合剂涂胶要适量,熟化要充足。
G. 熟化温度过低,固化缓慢,交联不充足。
要选用适当的熟化温度,熟化时间要充足,必须时选用快速固化粘合剂。
H. 复合膜基材中添加剂的影响。
如,PVCD中的添加剂能延迟和阻拦粘合剂交联固化,PVA中的柔嫩剂能与固化剂的—NCO基团反应,软质PVC的增塑剂能渗入到粘合剂中,因此会降低粘接力和热稳定性,对此要适当加添固化剂使用量。
2. 固化但无剥离强度。
A. 粘合剂选择错误。
依据不同的基材、产品结构、后加工要求、内容物等选择粘合剂。
另外,不同的粘合剂性能差异很大,应使用专用粘合剂,如铝箔粘合剂、镀铝膜粘合剂、抗介质粘合剂等。
B. 粘合剂涂布量太少。
粘合剂布量太少会导致表面浸润铺不足。
基材的平滑度不一,产品用途不同都需用不同的涂布量。
上胶网纹辊要定期清洗,防止堵塞。
C. 粘合剂与油墨层的相容性不好,特别是多套色、油墨层厚的地方。
不可用聚酰胺油墨里印,注意油墨添加剂的作用,对油墨面大,油墨厚的印刷膜,要提高上胶量,选用低粘度、高固含量粘合剂,使胶液能渗透到基材表面,充足干燥D. 基材表面张力不好,基材的电晕处置不足或不均匀,复合基材表面张力达不到38mN/m,复合强度不佳,若达40~42mN/m,则效果更好。
复合材料剥离强度不够的几个原因

复合薄膜剥离强度不够的几个原因:剥离强度是干复生产中最重要的指标,剥离强度对产品的最终性能和质量起非常重要的作用,对剥离强度产生影响的因素是多方面的,材料、工艺、内容物等都有影响。
主要有以下几个方面:1. 复合面上粘合剂固化不足,略发粘。
A. 粘合剂在配比当中发生称量错误,造成固化不足,或配胶手法错误,引起局部混合不均匀现象。
B. 粘合剂储存不当,固化剂未密封完全,与空气中水分发生反应,消耗一部分,以致混合后固化剂含量不足。
C. 稀释剂纯度不高,含有超标的水分和醇类使粘合剂比例失调D. 使用了醇溶性油墨或油墨稀释剂的醇类成分未烘干,残留较多,以致与固化剂反应,造成发粘。
醇溶性油墨应尽量使用醇溶性粘合剂,印刷中溶剂尽量不使用醇类配比。
E. 复合中残留溶剂过多,溶剂包裹在粘合剂当中,阻碍了固化。
要经常检查烘干系统的进排风是否正常,上胶量大时,控制复合速度。
F. 粘合剂涂布量过多,膜卷卷径过大,导致粘合剂内部硬化缓慢。
粘合剂涂胶要适量,熟化要充分。
G. 熟化温度过低,固化缓慢,交联不充分。
要选用适当的熟化温度,熟化时间要充分,必要时选用快速固化粘合剂。
H. 复合膜基材中添加剂的影响。
如,PVCD中的添加剂能延迟和阻止粘合剂交联固化,PVA中的柔软剂能与固化剂的—NCO基团反应,软质PVC的增塑剂能渗入到粘合剂中,因此会降低粘接力和热稳定性,对此要适当增加固化剂使用量。
2. 完全固化但无剥离强度。
A. 粘合剂选择错误。
根据不同的基材、产品结构、后加工要求、内容物等选择粘合剂。
另外,不同的粘合剂性能差异很大,应使用专用粘合剂,如铝箔粘合剂、镀铝膜粘合剂、抗介质粘合剂等。
B. 粘合剂涂布量太少。
粘合剂布量太少会导致表面浸润铺不够。
基材的平滑度不一,产品用途不同都需用不同的涂布量。
上胶网纹辊要定期清洗,防止堵塞。
C. 粘合剂与油墨层的相容性不好,特别是多套色、油墨层厚的地方。
不可用聚酰胺油墨里印,注意油墨添加剂的作用,对油墨面大,油墨厚的印刷膜,要提高上胶量,选用低粘度、高固含量粘合剂,使胶液能渗透到基材表面,充分干燥D. 基材表面张力不好,基材的电晕处理不足或不均匀,复合基材表面张力达不到38mN/m,复合强度不佳,若达40~42mN/m,则效果更好。
造成剥离强度偏低的几大原因PPT参考幻灯片
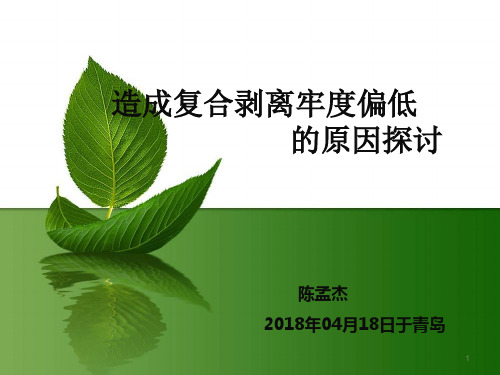
拉伸强度 断裂伸長率 撕裂强度(g/25.4mm厚) 热收缩率 润湿张力 雾度 热焊温度
纵向 横向 纵向 横向 纵向 横向 纵向 横向 处理面 非处面
MPa % mN % mN/m %
℃
摩擦系数
动
静
氧气透过系数 23℃ 0%
【cm.cm/(cm2.s.pa)】、cm2/m2.d.pa
水蒸气透过率 38℃
9
4、热封层厚度:
热封层厚度一般不低于40um,厚度过低,则易产生剥离牢度偏 低。但是厚度大的热封层薄膜(60um以上),生产时都会加入大量 添加剂。因此,在购买CPP或PE时要购尽量少加或不加添加剂的 薄膜。(水煮、蒸煮袋热封层不低于60um)
10
11
常用塑料薄膜外观质量应符合:
项目名称
验 收要 求
4
2、塑料薄膜中添加剂析出及材料中爽滑剂以及开口剂比例过高:
一般为保证薄膜产品生产中的顺畅以及成品袋良好的开口性能, 内层材料中会添加一定比例的爽滑剂、开口剂,这些添加剂都是低 分子物质,塑料薄膜中的添加剂也会影响到粘接牢度,如添加比例 过高会影响胶粘剂与薄膜的粘结性能。刚复合好的薄膜短时内迁移 出来的添加剂量并不多,还不至于引起粘结牢度下降。但时间长了, 迁移出的添加剂就把胶膜与该基膜隔离开来,破坏了原有的粘结状 态,使复合牢度降低。
≤7.0
≥120 ≥200 ≤180 ≤65 4~6
≤5 ≤4 ≥38
≤1.5
CPP
未拉聚丙 烯
0.88/0.9 1
≥35 ≥25 ≥400 ≥500 ≥80 ≥80 ≤5
HDPE
吹塑聚乙烯
0.915/0.9 25 ≥25
≥180 ≥230
15~300
复合集流体 铜 剥离强度
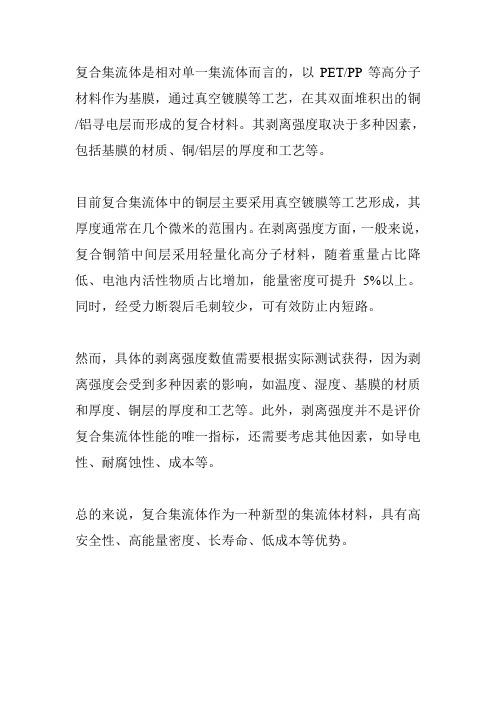
复合集流体是相对单一集流体而言的,以PET/PP等高分子材料作为基膜,通过真空镀膜等工艺,在其双面堆积出的铜/铝寻电层而形成的复合材料。
其剥离强度取决于多种因素,包括基膜的材质、铜/铝层的厚度和工艺等。
目前复合集流体中的铜层主要采用真空镀膜等工艺形成,其厚度通常在几个微米的范围内。
在剥离强度方面,一般来说,复合铜箔中间层采用轻量化高分子材料,随着重量占比降低、电池内活性物质占比增加,能量密度可提升5%以上。
同时,经受力断裂后毛刺较少,可有效防止内短路。
然而,具体的剥离强度数值需要根据实际测试获得,因为剥离强度会受到多种因素的影响,如温度、湿度、基膜的材质和厚度、铜层的厚度和工艺等。
此外,剥离强度并不是评价复合集流体性能的唯一指标,还需要考虑其他因素,如导电性、耐腐蚀性、成本等。
总的来说,复合集流体作为一种新型的集流体材料,具有高安全性、高能量密度、长寿命、低成本等优势。
挤出复合膜的常见故障举例及其解决办法

挤出复合膜的常见故障举例及其解决方法复合膜显现鲨鱼皮、鱼眼斑等现象故障原因:1.挤出机温度设置不当,特别是模头和树脂的温度太低,造成树脂塑化不良,使熔融树脂显现鲨鱼皮现象或者仿佛鱼眼状的斑痕。
2.树脂中含有水分,影响树脂的塑化情形。
3.树脂中混进熔融指数或密度不同的其他树脂,使树脂塑化不好或塑化不*。
4.更换树脂时没有将料筒*清洗干净,料筒中残存的其他树脂或杂质对树脂塑化情形产生不良影响。
解决方法:1.将挤出机的挤出温度和树脂的温度调整到适当值,保证树脂塑化良好。
2.对树脂进行搅拌和烘干,去除其中所含的水分,使树脂能够充分塑化。
3,更换熔融指数和密度适当的树脂。
4.*清洗料筒,去除杂质等的影响。
复合膜有异味故障原因:1.挤出机温度或树脂温度过高,造成树脂分解,产生臭味。
2.气隙太大,树脂氧化过度,表面产生有异味的各种含氧基团,使复合膜产生气味。
3.树脂本身就有异味,用其进行挤出复合后的复合膜也会有异味。
4.底涂剂中使用高沸点、不易挥发的溶剂,导致溶剂残留,造成复合后薄膜产生异味。
解决方法:1.适当降低挤出温度,防止树脂发生分解。
2.调整气隙的大小到合适的值。
3.采纳低臭度的树脂进行挤出复合。
4.提高烘道的干燥温度,加大吹风量,保证溶剂充分干燥。
复合膜图案拉伸变形故障原因:1.张力设置和掌控不当,各部之间的张力值不适应。
2.烘道温度设置太高。
3.复合压力过大,使复合膜产生拉伸。
4.冷却钢辊表面温度太高,复合膜冷却效果差,简单枯辊产生拉伸现象。
解决方法:1.检查并确定拉伸现象发生在设备哪一段,依据实在情况将该段的张力值调整到合适,与其他段的张力大小相匹配。
2.适当降低烘道的温度。
3.适当降低复合压力。
4.降低并掌控好冷却钢辊的表面温度,使其分布均匀,有良好冷却效果。
复合膜粘在冷却钢辊表面故障原因:1.冷却钢辊表面温度太高,对熔融树脂冷却效果不佳,影响复合膜的冷却、固化及成型,导致熔融树脂粘在冷却钢辊表面。
- 1、下载文档前请自行甄别文档内容的完整性,平台不提供额外的编辑、内容补充、找答案等附加服务。
- 2、"仅部分预览"的文档,不可在线预览部分如存在完整性等问题,可反馈申请退款(可完整预览的文档不适用该条件!)。
- 3、如文档侵犯您的权益,请联系客服反馈,我们会尽快为您处理(人工客服工作时间:9:00-18:30)。
挤出复合剥离强度的影响因素随着我国挤出复合设备技术性能的不断提高,涂复级树脂如LDPE、PP等及复合粘接级树脂EVA、EMA、EAA等的不断开发,挤出复合工艺以成本低、无残留溶剂等优点,逐渐被广大软包装企业所接受。
而高涂复速度和高剥离强度是困扰众多软包装企业的两难问题。
笔者根据生产实践,就挤出复合工艺对剥离强度的影响因素与包装同行共同探讨。
一、树脂塑化混炼程度挤出复合是将热塑性树脂如LDPE、PP、EVA、EMA、EAA等加入料筒,在螺杆的作用下,经压缩区高温熔融成粘流态,在均化区高温、高压、高剪切条件下,进一步塑化混炼均匀,随着螺杆的推动而被定压、定量、定温地经T模头持续均匀挤出。
树脂的塑化混炼程度是影响挤出复合剥离强度的主要因素之一。
树脂塑化混炼越充分,复合后剥离强度越高。
通常采用以下方法增加树脂塑化混炼程度:1.选用熔融指数(MI)较大的树脂熔融指数(MI)越大,流动性越好,塑化混炼效果越好。
但MI太大,则挤出薄膜发生边厚现象。
故宜选用MI为8g/10min左右的树脂。
2.适当提高加热温度压缩区、均化区加热温度越高,树脂塑化混炼越充分;但温度过高树脂易分解。
加热温度的设定要根据树脂种类及其熔融指数(MI)来设定。
如牌号为1C7A的LDPE树脂,其加热温度在300~325℃范围内设定。
3.适当提高熔体压强熔体所受压强越大,塑化混炼就越充分;增加熔体压强,常采用增加滤网层数或目数的方法。
如牌号为1C7A的LDPE树脂采用目数分别为85、110、85的三层滤网,使溶体压强在1.2~1.4MPa范围内。
4.适当提高螺杆转速螺杆转速越大,单位熔体所受螺杆剪切次数越多,塑化混炼就越充分。
但螺杆转速增大,挤出薄膜厚度增加。
故应注意螺杆转速、涂复速度与挤出薄膜厚度三者的匹配。
二、树脂的氧化程度粘流态树脂经模唇挤出到接触基材的过程中,被空气中的氧气氧化而产生极性,提高挤出复合剥离强度。
气隙即模唇到两薄膜(即挤出薄膜与基材)复合线的距离。
气隙大、氧化程度高。
但气隙过大,热损失就大,从而降低剥离强度。
气隙一般在9~12cm范围内调整。
三、树脂温度与基材接触时的树脂温度高,则剥离强度高。
通常采用提高模头温度的方法,来提高树脂温度。
但模头温度过高,则挤出薄膜发生边厚,且易使模唇发生氧化、树脂发生碳化现象。
如挤出牌号为1C7A的LDPE树脂时,模头各区温度在323~328℃范围内设定。
要注意做好日常的模唇维护保养工作。
停车时要使树脂挤出模唇外少许,防止氧气进入;开车时要用软铜片反复清理模唇,防止碳化的树脂附在其上,影响复合质量。
四、挤出薄膜在高温状态与基材接触的时间树脂经模唇挤出后,其在高温状态与基材接触的时间越长,剥离强度越高。
故应调整模头适当偏向胶辊侧少许,使挤出薄膜与基材接触的时间增加。
但要注意被复合基材的耐高温性,以免影响复合质量。
五、压辊压力与冷却辊状态1.挤出薄膜与基材接触后经冷却辊与胶辊挤压后粘接在一起。
压辊压力大,冷却辊与胶辊对复合膜的挤压力大,剥离强度就大。
但要考虑设备的承受能力,一般压辊压力在4kg/cm2左右调节。
2.冷却辊表面温度应适当提高,可增加剥离强度。
但温度过高不利于操作,一般在20~25℃范围内,在不影响产品外观的情况下,选用网线式冷却辊,可增加对薄膜的挤压面积,从而提高挤出复合的剥离强度。
六、涂复速度涂复速度降低,则可提高挤出复合剥离强度。
但涂复速度降低,意味着班产量降低、产品成本增加。
七、被复合基材的表面张力及温度被复合基材的表面张力越大,挤出复合剥离强度越高;其表面张力应大于38dyn/cm2。
被复合基材与挤出薄膜复合时的温度差越小,挤出复合剥离强度越高。
因而在保证被复合基材干燥清洁的基础上,通过干燥箱对基材进行预热,降低与挤出薄膜复合时的温度差。
八、涂布异氰酸酯类AC剂或双组份聚氨酯粘合剂在挤出复合工艺,基材涂布异氰酸酯类AC剂后,经干燥箱干燥后与挤出薄膜复合,可提高挤出复合剥离强度。
也可采用涂布双组份聚氨酯粘合剂,以较少的干量如1~2g来获得理想的剥离强度。
提高挤出复合的剥离强度,还可通过对螺杆的专业化设计来进行。
拥有挤出复合设备的软包装企业,要通过对以上各工艺因素的优化组合,在保证产品剥离强度的基础上,提高生产效率,降低制造成本,不断提升企业市场竞争力。
挤出复合工艺具有投资少、成本低、生产效率高、操作简便等多方面的优点,因此,它在塑料薄膜的复合加工中占有相当重要的地位。
但是,在实际生产中也难免会出现这样或那样的问题。
本文,就以最为常见的剥离强度差为例与大家共同进行分析探讨。
一、薄膜基材对剥离强度的影响1、基材表面处理效果对剥离强度的影响。
被涂布基材应当预先进行电晕处理,电晕处理后的表面张力应当达到40达因以上,这样可以改进基材同熔融挤出树脂的粘结性,从而提高挤出复合强度。
因此,在生产前要检测基材的表面张力是否达到要求,一发现表面张力太低,应立即更换基材或对基材重新进行表面处理。
此外,经表面处理过的薄膜,其表面张力应当是均匀一致的,否则也会对剥离强度产生一定的影响,造成剥离强度不均匀、不一致的问题。
2、基材表面清洁度对剥离强度的影响。
被涂布基材表面应当清洁、干净,无灰尘、无油污,如果基材表面不太清洁,粘附了灰尘、油脂等污物,就会直接影响到熔融树脂跟塑料薄膜表面的粘合力,从而使挤出复合膜的粘接强度下降。
3、其它因素的影响。
对于一些易吸湿的薄膜材料(比如尼龙薄膜),如果已经发生吸湿现象,这也会影响挤出复合膜的粘接牢度。
因此,对于易吸湿的薄膜材料一定要注意防潮,尼龙薄膜在使用前和使用后应当及时用铝箔将其包裹好。
二、油墨对剥离强度的影响1、油墨质量对剥离强度的影响。
在实际生产过程中,有时候会出现无油墨或油墨较少部位的剥离强度好、而有油墨或油墨较多部位的粘合牢度反而比较差的现象,这就是由于所用的印刷油墨的适性不好,油墨与基材之间的粘接不良,从而造成挤出复合膜的剥离强度差。
一旦发生这种情况,应当及时更换合适的油墨,并同油墨厂商联系,共同协商和研究解决办法。
2、油墨干燥性对剥离强度的影响。
如果油墨干燥不良,特别是当油墨中大量地使用了甲苯、丁醇等沸点比较高的溶剂,而且干燥箱温度设置不当的话,就会有少量或较大量的溶剂残留在油墨层中,复合后可能会造成复合膜的分层,使剥离强度变差。
因此,在印刷过程中一定要对油墨的干燥性能进行严格的控制,保证油墨能够充分干燥。
此外,在印刷过程中还要注意对印刷速度和干燥温度等工艺条件的控制,因为它们也会对油墨中溶剂的挥发速度产生一定的影响。
如果印刷速度较快,且印刷机干燥箱的温度又比较低的话,油墨中的溶剂可能无法完全挥发掉,这些残留的溶剂就会在薄膜上形成一些小泡,使复合膜粘接牢度下降。
一般来说,在设定干燥箱的温度时,必须要综合考虑印刷速度、油墨的干燥速度、承印物材料的种类以及印刷图像的大小等因素。
三、挤出复合用树脂对剥离强度的影响1、树脂类型对剥离强度的影响。
挤出涂布复合用树脂可以是聚乙烯、聚丙烯、EVA、Surlyn、 Nucler、Bynel、EVAL、EAA、EMAM等。
挤出涂布复合的目的不同,选用的树脂也不同。
例如,用于普通层复合塑料制袋用的,可以采用热封性较好的各种热封用树脂;用于夹心挤复用的树脂,要求同面层和内封层塑料层均有良好的相容性的,可根据面层及内封层材料的不同选用各种相容剂树脂,如 Surlyn、Nucler、Bynelr等。
如果树脂选用不当,会影响到它同被涂布基材的相容性,从而影响到挤出复合强度。
2、树脂熔融指数(MI)对剥离强度的影响。
熔融指数(MI)是指树脂熔融料在一定温度和一定压力下,在lOmin内通过标准毛细管的重量值,以克/1Omin表示。
熔融指数(MI)是树脂流动性的一种指标,一般来说,树脂的熔融指数(MI)越高,则其流动性越好,熔融薄膜的粘度越低,粘合力越大。
在挤出复合工艺中,不宜选用熔融指数(MI)太小的树脂。
如果树脂的熔融指数(MI)偏小,其分子量较大,则融合性比较差,不能与被涂布基材很好地粘合,致使剥离牢度有所下降。
比如在使用LDPE树脂进行挤出复合时,一般选用熔融指数(MI)在4--7g/1Omin 的LDPE树脂。
3、树脂密度对剥离强度的影响。
树脂的密度越小,支链含量越高,表面越容易被活化,粘合力就越大,对剥离强度的提高也就越有利。
4、树脂中助剂及水分含量对剥离强度的影响。
树脂中的助剂,特别是润滑剂对挤出复合膜的剥离强度有着很大的影响,比如在使用LDPE树脂进行挤出复合时,应当选用不含或少含润滑剂的挤出涂覆级树脂粒子,例如北京燕山石化公司的1C7A树脂。
此外,如果树脂中所含的水分比较多的话,在挤出复合过程中可能会发生塑化不良现象,从而影响复合膜的剥离强度。
四、挤出复合工艺对剥离强度的影响1、挤出机温度对剥离强度的影响。
挤出机机筒温度和T模温度的控制极为重要,是挤出复合工艺的关键和核心。
温度太低,树脂塑化不良,从模口流延下来不能很好地与基材复合,致使剥离牢度下降;温度高,流出的熔薄膜氧化越充分,表面产生极性分子,对基材的亲和力越大,剥离强度也就越高。
但是温度也不宜过高,否则树脂容易分解,还可能会烫伤基材,而且还会产生烟雾,污染工作环境。
一般来说,挤出机机筒的温度通常控制在150℃一340℃之间,T模的温度通常控制在310℃--340'C左右,这还要根据挤出复合设备和所用树脂的具体情况来设定。
2、树脂温度对剥离强度的影响。
树脂温度高,有利于熔融塑料膜在被涂布基材上的润湿和渗透,因而有利于复合强度的提高,但过高会引起分解,一般不超过350℃。
如果树脂与基材压着时的温度过低,树脂表面氧化不充分,应当适当提高树脂温度。
3、气隙对剥离强度的影响。
气隙是指从挤出模口到复合冷却钢辊、压力辊接触线之间的距离。
由于气隙的存在,热熔膜表面会同空气中的氧气发生氧化作用,氧化后的热熔膜被涂布塑料薄膜复合时的剥离牢度会大大提高。
气隙的大小对挤出剥离强度也有很大的影响,气隙太小,树脂表面氧化不充分,致使挤出复合强度变差;气隙大,热熔膜同空气接触的时间长,热熔膜表面被空气中氧气氧化的程度越厉害。
增加极性基因,树脂同基材表面的黏结力也就越大,从而有利于复合强度的提高。
但如果气隙太大,则热熔膜的热损失过大,温度会降低得过多,在复合时的温度过低,反而会引起剥离强度的下降,而且热封性也变差。
因此,挤出复合时应当根据实际情况来调节气隙的大小,一般来说,气隙控制在 50mm—l00mm之间为宜。
4、复合压力对剥离强度的影响。
复合压力小,熔融树脂与基材之间贴合不紧密,会使剥离牢度下降。
但复合压力也不可太大,否则基材容易被压变形。
5、冷却钢辊表面温度对剥离强度的影响。
冷却辊采用的是表面镀铬的钢辊筒,其作用是将熔融树脂薄膜的热量带走,让粘合后的复合膜立即冷却、固化,以形成较强的内聚力,使熔融薄膜跟被涂布基材粘牢、定型,不产生相对位移,从而保证良好的剥离强度。