高炉沟下返矿率变化情况
提高高炉炉料中球团矿配比,促进节能减排

提高高炉炉料中球团矿配比、促进节能减排(资料来源:冶金管理,王维兴)一、优化炼铁炉料结构的原则高炉炼铁炉料是由烧结矿、球团矿和块矿组成,各高炉要根据不同的生产条件,决定各种炉料的配比,实现优化炼铁生产和低成本。
世界各国、各钢铁企业没有一个标准的炼铁炉料结构,都要根据各企业的具体情况制定适宜的炉料结构,同时还要根据外界情况的变化,进行及时调整。
2017 年中钢协会员单位高炉的炉料中平均有13%左右的球团矿,78%烧结矿,9%块矿。
在高炉生产时,各企业要根据其具体生产条件下,实现科学高炉炼铁操作(满足炼铁学基本原理),完成环境友好、低成本生产的目的。
实现低成本炼铁的方法包括:优化配矿、优化高炉操作、设备维护完好、生产效率高。
而实现高产低耗就要高炉入炉矿含铁品位高,有优质的炉料,包括高质量烧结矿要实现高碱度(1.8-2.2倍)。
但炼铁炉渣碱度要求在1.0-1.1 倍,炉料就需要配低碱度的球团矿(或块矿)。
高炉生产实现低燃料比,要求原燃料质量要好(入炉铁品位要高、冶金性能好、低MgO 和Al2O3、低渣量、焦炭质量好、含有害杂质少等),成分稳定,粒度均匀等。
要实现资源的合理利用,就要合理回收利用企业内含铁尘泥等等资源。
建议将含有害杂质高的烧结机头灰、高炉布袋灰,加石灰混合,造球,干燥,给转炉生产用,切断炼铁系统有害杂质的循环富集。
此外,球团工艺相比烧结工艺具有一定的优越性:1)产品冶金性能一般来说,烧结矿综合冶金性能优于球团矿,因此,高炉炼铁炉料中以高碱度烧结矿(在1.8-2.2 倍)为主。
但是,炼铁炉渣碱度要求在1.0 左右,必须搭配一部分酸性球团矿,这样结构炉料的冶金性能才最优,使高炉生产正常进行。
球团矿的缺点是膨胀率高,易粉化。
目前,北美和欧洲一些高炉使用100%自熔性球团矿,冶金性能完全能满足高炉炼铁的要求,也取得了较好的高炉生产指标。
2)生产运行费用球团工序能耗是烧结的2/3,环保治理费用低,球团矿铁品位比烧结矿高5-9 个百分点(原料品位、碱度相同条件下),炼铁生产效益高10 元/t。
烧结矿返矿增多的原因
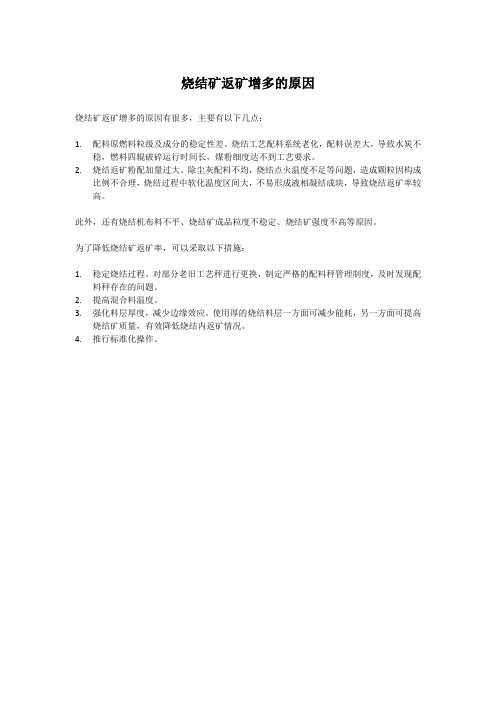
烧结矿返矿增多的原因
烧结矿返矿增多的原因有很多,主要有以下几点:
1.配料原燃料粒级及成分的稳定性差。
烧结工艺配料系统老化,配料误差大,导致水炭不
稳,燃料四辊破碎运行时间长,煤粉细度达不到工艺要求。
2.烧结返矿粉配加量过大。
除尘灰配料不均,烧结点火温度不足等问题,造成颗粒因构成
比例不合理,烧结过程中软化温度区间大,不易形成液相凝结成块,导致烧结返矿率较高。
此外,还有烧结机布料不平、烧结矿成品粒度不稳定、烧结矿强度不高等原因。
为了降低烧结矿返矿率,可以采取以下措施:
1.稳定烧结过程。
对部分老旧工艺秤进行更换,制定严格的配料秤管理制度,及时发现配
料秤存在的问题。
2.提高混合料温度。
3.强化料层厚度,减少边缘效应。
使用厚的烧结料层一方面可减少能耗,另一方面可提高
烧结矿质量,有效降低烧结内返矿情况。
4.推行标准化操作。
返矿率和返矿平衡

返矿率和返矿平衡(return fines and It’s balance)铁矿石烧结后因强度较差和未完全烧结的烧结矿经破碎筛分处理而返回烧结工序的筛下物称返矿。
返矿量与烧结混合料总量之比为返矿率。
在西欧国家根据控制技术方面的需要,返矿率均以返矿量占矿石量的百分比来计算。
烧结产出的返矿量(R A)与烧结混合料中配入的返矿量(R E)相等时,叫返矿平衡(B),即B=R A/R E=1。
它是烧结过程得以进行的必要条件。
返矿的种类烧结矿返矿分为热返矿、冷返矿和高炉料槽下返矿3种。
(1)热返矿。
烧结台车运行到烧结机尾时,烧结机两侧和表层的未烧好的烧结矿;黏结成块的热烧结饼经机尾单辊破碎机剪切和热振动筛筛分后的筛下物。
(2)冷返矿。
热烧结矿经冷却和整粒后的筛下物。
(3)高炉料槽下返矿。
高炉料槽中的烧结矿在入炉前进行筛分时的筛下物。
返矿粒度一般都在5mm以下;热返矿送到烧结混合料皮带上返回烧结;冷返矿和高炉料槽下返矿则返回烧结配料室。
返矿率与返矿质量烧结返矿率取决于原料的性质、原料的准备技术和设备状况以及烧结的操作技术。
赤铁矿、褐铁矿和含结晶水脉石高的矿粉,以及不易脱水的高湿度的细精矿等返矿率一般较高,可达40%~50%。
混合料的混合和制粒不好、烧结机的布料不均、烧结点火热量不足、烧结终点控制不好或未能烧透以及烧结矿卸出后的多次破碎及筛分等都会增加返矿率。
此外,当烧结制度(如料层高度、点火温度、燃料用量、抽风负压等)与原料性质不相适应,或烧结作业失常未能及时调整时,返矿率也会升高。
返矿中如含有大量未经烧结的烧结混合料,则返矿细粉多、含碳高、质量差,对烧结过程有不利的影响。
质量良好的返矿多数是已烧结成矿但机械强度较差的粒状物料,其粒度一般应在5mm以下。
返矿对烧结过程的影响质量良好的返矿可改善混合料的粒度组成,提高料层的透气性,特别是在细精矿烧结时,返矿有利于细精矿制粒,从而提高细精矿的烧结生产率。
质量好的返矿在烧结过程中易形成液相可增加烧结过程的液相量,从而提高了烧结矿的机械强度。
高炉返矿率

高炉返矿率
高炉返矿率是指高炉冶炼时所使用的返矿的占比。
返矿是指来自废钢料、废钢铁、废钢锭、废钢块等回收的原材料。
高炉返矿率的提高可以降低生铁成本,减少铁矿石消耗,对环境也有较好的影响。
返矿对高炉冶炼有以下几个作用:一是可以增加高炉的产量和生产率,二是可以提高炉渣的脱硫能力,三是可以降低高炉的燃料消耗,四是可以改善高炉的冶炼条件,五是可以减轻环境污染。
为了提高高炉返矿率,可以采取以下措施:一是加强回收废钢的力度,二是选择合适的返矿种类,三是加强返矿的预处理,四是优化高炉操作,五是提高高炉炉壳的耐热性。
总之,高炉返矿率对于钢铁企业的经济效益和环境保护都具有重要的意义,需要钢铁企业加强管理,不断探索新的技术和方法,提高返矿利用率。
- 1 -。
降低返矿量提高烧结主矿配量

谢 谢 观 赏!
汇报人:周金虎 2012年1月16日
2012年度目前现状: 二、技改的必要性: 三、实施方案:
一、目前现状:
我厂1280m3高炉投产后,烧结矿使用筛底为河南 太行5.5mm梳齿筛。烧结筛粉效果好,使得返矿大于 8mm占到18—23%,每天返矿量单高炉达到1600多吨, 返矿率15—17%,这样使得汽车每天从高炉返矿仓到 仓储料仓倒运达3000多吨,从仓储中心运入烧结焙烧, 再次入高炉同于返矿中大于5mm的占到48%—52%,使 得烧结难以矿化,烧结成品率下降。每天这样周而复 始,使得过程中增加了过程汽车费用,由于返矿粒度 大在焙烧过程中难以矿化,破坏了烧结的正常生产, 成品率下降。
二、技改的必要性:
通过几次外出考察学习,部分高炉使用烧结筛底为4mm, 尤其是唐山九江高炉使用3.5mm筛底,控制入炉烧结矿5mm 小于5%,5—10mm小于30%,就能满足高炉正常生产需要。 高炉表现正常顺行,而且烧结矿粒度大时与煤气流程接触 面积小,还原速度慢,影响冶炼强度。我厂与同行相比差 距较大,原因是操作理念和指导思路不正确,认为粒度越 大透气性越好,实际生产中透气性好坏主要决定在软熔带, 是依靠合理的上下部匹配,形成中心开放,边缘稳定,倒 “V”型软熔带,减小软熔带体积利于煤气流通过。从而 提高透气性,确保炉况顺行而粒度过大,在煤气流通过软 熔带后上升过程中,由于在块状带粒度大,易造成管道等 不利于炉况顺行的现象发生。
三、实施方案:
• 我厂200m2烧结机强度大于76,是比较理想的,主要原因是高 炉使用烧结筛底结构不合理,筛分效率低,原先使用筛底为梳子 筛,由于梳齿弹性小,小粒度卡筛严重,后学习太钢改用济南中 燃筛底,同时棒条筛改为4mm的,这样返矿量大幅度减少,由原来 日产1600多吨降到950T—100T,返矿率由原15—17%降到现在 9.5—10.5%,减小了汽车运输费用,更重要的是烧结配料中高了 主矿配量,由原52%提高到60%,使得烧结品位提高了10.8%,在更 换筛底后返矿粒度抽查大于8mm的为零,大于5mm为14—21%,高炉 入炉烧结小于5mm为1—2%,5—10mm为18—26%,完全满足高炉正 常生产的工艺要求,炉况表现正常稳定,冶炼强度得到了进一步 的提升,完成了公司下达的7000T/日任务,在实施过程中,以小 步慢走,四块烧结筛底以10天为一周期更换,每更换一块筛底, 跟踪抽查返矿和入炉烧结粒级,更换后密切关注炉况的变化和反 应,利于一个半月的时间俩高炉全部换为4mm的济南中燃棒条筛, 炉况表现正常顺行,更换筛底明细附后:
降低烧结矿返矿率
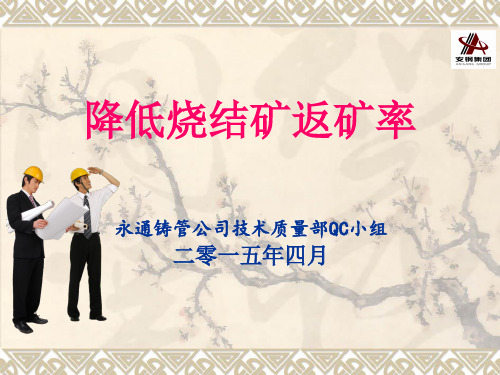
要因确认9
焦粉粒度粗、 生石灰质量差 二次混合机 工艺参数不 合理 原燃料配比 不当 烧结布料 技术差 烧结布料装 置不合理 烧结主抽风 机能力不够 混合料预热 效果差 煤气和空气 配比不稳 点火助燃空 气温度不够 烧结点火真 空度不适宜
原
因
煤气和空气配比不稳
验证标准
烧结车间工艺技术规程,SQWp—02—01
2
3 4 5
副组长
顾 问
徐德强
胡明意 郑 华
男
男 女 男
38
40 35 34
本科
本科 本科 本科
技术质量副部长、炼铁工程师
烧结高级工程师、安阳市青年岗位能手 机械、质量工程师 自控、仪表工程师
联络员 组 员
左武新
6
7 8
组
组 组
员
员 员
付林林
柴 强
女
男 男
33
34 33
本科
本科 本科
程序员、化验工程师
要因分析
确
认
负 责 人 验证时间
要因确认4
焦粉粒度粗、 生石灰质量差 二次混合机、 工艺参数不 合理 原燃料配比 不当 烧结布料 技术差 烧结布料装 置不合理 抽风系统漏 风率过高 烧结主抽风 机能力不够 混合料预热 效果差 煤气和空气 配比不稳 点火助燃空 气温度不够 烧结点火真 空度不适宜
原
因
烧结布料技术差
验证标准
烧结机岗位作业制度, SQWs-02-13 我公司烧结机投产九年,绝大部分布料操作工人都具 备多年实际工作经验,布料技术得到较大提高,经过 烧结工操作技能鉴定,工人布料操作合格率达到100%。
非要因 左武新 2014.2.21~3.12
降低高炉综合返矿率生产实践

降低高炉综合返矿率生产实践摘要:乌海市包钢万腾钢铁有限责任公司拥有两座1200m³高炉,从2021年6月开始,炼铁厂对降低高炉综合返矿率进行了专项攻关,最终取得了满意的效果。
本文就本次降低高炉综合返矿率过程进行了深入的剖析和总结,对同类企业生产实践有一定程度的借鉴意义。
关键字:高炉;返矿率;1、前言包钢万腾钢铁有限责任公司拥有两座1200m³高炉,配备1台360㎡烧结机,无球团厂,球团资源全部来自当地一家球团厂,球团质量较为稳定。
2021年开始高炉综合返矿率(本文中高炉综合返矿率指高炉槽下烧结矿、球团矿、块矿筛下物的总量占入炉毛矿的百分比)出现升高趋势,2021年1-6月高炉综合返矿率完成12.25%,对标其他同炉容级别企业的高炉综合返矿率基本维持在11%左右,这势必对降低铁水成本起到阻碍作用。
于是从2021年6月开始,炼铁厂开始对降低高炉综合返矿率展开了为期一年的专项攻关,目标高炉综合返矿率达到10.5%以下。
2、降低高炉综合返矿率实践2.1探究影响高炉综合返矿率的因素系统性的对可能影响到高炉返矿率的因素进行梳理,最终得出影响高炉返矿率的因素主要有两方面:①入炉料(烧结矿、球团矿、块矿)本身的含粉率②高炉槽下的筛分。
对于入炉料含粉来说,烧结矿为公司自产,所以烧结矿含粉的高低主要由烧结矿质量(主要是转鼓指标)和物料转运过程的二次粉化决定;对于球团、块矿来说因为均为外购,所以可以通过采购合同控制其含粉率高低,当球团、块矿入厂后同样也会受转运过程导致二次粉化的影响。
对于高炉槽下筛分来说主要是两方面因素影响高炉综合返矿率,即①筛板规格与筛板磨损情况②筛子的料流控制。
2.2降低高炉综合返矿率措施2.2.1降低入炉料的含粉率包钢万腾高炉正常生产过程中,炉料结构为:烧结矿比75%+球团矿19%+块矿6%,所以烧结矿的含粉率在很大程度上决定了入炉料含粉率的高低。
2021年包钢万腾高炉槽下烧结矿含粉率(烧结矿含粉率指高炉槽下烧结矿返矿/高炉槽下烧结矿毛矿)在12.5%左右,烧结矿转鼓在76%,烧结矿中Al2O3基本控制在2.8%,为了保高炉镁铝比,烧结矿中MgO控制在3%以内,烧结矿中TiO2达到0.5%,碱金属达到0.16%。
降低3号烧结机高炉槽下返矿率生产实践

2016年 第 3期
梅 山科 技
·7 ·
降低 3号烧结机高炉槽下返矿率生产实践
钟 家华 李和 平 (梅 山钢铁公 司炼铁 厂 南京 210039)
摘 要 :深入 分析 3号烧 结机返 矿 率 高的原 因 ,通 过 改进 加 水 方 式、布 料 工 艺设 备 优化 生 产工艺参数的控制 ,提 高了烧结矿的强度 ,降低 了返矿率。
5)许 多 重要工 艺 参 数 的 波 动影 响 因素 ,如 混 合料 水 分 、FeO、燃 料 消 耗 等 ,所 以返 矿 是 最 容 易 忽视 而 又最不 能 忽视 的一个 因素 。
6)根 据柳 钢研究 ,返 矿率 降 低 1% ,烧 结 比上 升 0.7% ,焦 比下 降 0.7 kg/t,以炼 铁 900万 吨产 能算 ,每 年可 降低成 本 945万元 。
关 键词 :烧 结 ;返 矿 率 ;生产 实践
Product ion Pract ice of Reducing Blast Furnace Return Fines Rat io at No.3 Sintering M achine
Zhong Jiahua Li Heping
日本高炉炼铁的新发展

传动齿轮箱上方有两个料仓轮换装卸炉料。每个料仓的上下口各有
一个密封阀、上密封阀3和下密封阀10。每个下密封阀上面设有节流 阀9(也称料流调节阀或料流调节闸门),以保护密封阀不与炉料接触,
同时可通过调节节流阀的开口度来控制料流量。为了交替往两个料
仓内装料,受料漏斗是可移动的。两个料仓均放置在电子秤8上,且 设有料仓空、满检测显示讯号,以便及时发现卡堵料现象。
2 煤和铁矿石资源环境利用价值变化及预加工技术
2.1 铁矿石资源环境变化
降低烧结矿中Al2O3含量,满足高炉生产的需求,铁矿石的 Al2O3 含量由1.52%上升到2.47%,粒度-0.15mm由4.58%升至28.8%。
7 COURSE 50技术
7.1 COURSE 50的基本内容:
COURSE 50是由JIFS会同日本六大钢铁公司提出的,是 指“美丽星球50”倡议,用技术创新从根本上减少CO2排放。
低碳炼铁工艺分两部分:
H 2 还原实用技术开发 1 廉价H 2 生产技术开发
高炉煤气中CO2 分离和收集技术 2 用技术 余热余能在CO2 分离及收集6.1减少CO2排放 日本提出了2020年与1990年相比减少温室气体排放25% 目标,已投入大量人力和物力实现目标。 6.2 炼铁工艺革新 2008年12月启动,是技术创新项目(为降低CO2排放), 其核心是复合铁矿石(铁氧化物与C和金属铁软化)的还原性和 生产工艺,目标是提高高炉炉身功效和热储备区的温度,由 1000℃降低到800℃,将炼铁能耗降低10%,该革新技术还有 相关炼铁过程数字模拟系统开发、高温和荷重软化实验数据。 根据这些数据使铁矿石还原更佳,使高炉内透气性得到明显 改善。
炼铁高炉总结报告

炼铁高炉总结报告1. 引言本报告旨在对炼铁高炉的运营情况进行总结分析,提供有效的决策依据。
本文将从以下几个方面进行分析:高炉运行情况、原料消耗、环境影响、安全生产等。
2. 高炉运行情况2.1 炉况指标我们对炼铁高炉的运行情况进行了全面的监测和记录,主要关注以下炉况指标:煤气利用率、产铁率、煤炭消耗量等。
经过统计和分析,我们得出以下结论:•煤气利用率在过去一年中呈下降趋势,这可能表明高炉存在一定的燃烧问题,需要进一步进行调整和优化。
•产铁率在稳定在80%左右,表明高炉的炉况整体较为稳定。
•煤炭消耗量与产量呈正相关,但在过去几个月中出现了一定的波动,这可能与原料配比和燃烧状态的变化有关,需要进一步研究。
2.2 炉渣和炉渣成分炉渣是高炉运行中的一种副产品,对炉渣成分进行分析可以帮助我们了解高炉的运行情况和原料的利用程度。
经过对炉渣成分的分析,我们得出以下结论:•炉渣中SiO2和Al2O3的含量较高,可能表明原料中铁矿石的质量有所下降。
•炉渣中CaO和MgO的含量较低,可能导致高炉炉渣的流动性较差,影响高炉的正常运行。
3. 原料消耗3.1 铁矿石铁矿石是炼铁高炉的主要原料,对铁矿石的消耗情况进行分析可以帮助我们了解原料利用的效果和成本情况。
经过统计和分析,我们得出以下结论:•铁矿石消耗量与产量呈正相关,但在过去几个月中出现了一定的波动,这可能与原料配比和炉况的变化有关。
•铁矿石的质量对高炉的运行和铁水质量有重要影响,需要进一步加强原料的质量控制。
3.2 煤炭煤炭是高炉的主要能源,对煤炭的消耗情况进行分析可以帮助我们了解能源的利用效率和成本情况。
经过统计和分析,我们得出以下结论:•煤炭消耗量与产量呈正相关,但在过去几个月中出现了一定的波动,这可能与原料配比和炉况的变化有关。
•煤炭的质量对高炉的燃烧效果和炉温控制有重要影响,需要进一步加强煤炭的质量控制。
4. 环境影响高炉的运行会对环境产生一定的影响,对环境影响进行监测和评估可以帮助我们制定合理的环保措施。
高碱度烧结矿生产分析

2011年包钢炼铁厂烧结矿碱度调整分析1.烧结矿碱度调整的原因高炉炼铁生产是“碱平衡下的铁平衡”,碱平衡是高炉冶炼的必要前提。
根据含铁炉料资源的变化,必须对烧结矿的碱度进行调整。
由于烧结、球团生产车间检修、外购进口块矿量的变化,特别是二烧车间的停产,炼铁厂在2011年多次进行了烧结矿碱度调整。
2.2011年包钢炼铁厂烧结矿碱度调整情况1)2011年1月19日:一、二烧车间烧结矿碱度由2.00调整至2.05 2)2011年2月18日:四烧车间烧结矿碱度由1.95调整至2.003)2011年5月25日:三烧车间烧结矿碱度由1.63调整至1.724)2011年6月27日:三烧车间烧结矿碱度由1.72调整至1.635)2011年7月4日:四烧车间烧结矿碱度由2.00调整至1.956)2011年7月20日:一、二烧车间烧结矿碱度由2.05调整至2.00 7)2011年7月26日:三烧车间烧结矿碱度由1.63调整至1.688)2011年8月25日:三烧车间烧结矿碱度由1.68调整至1.779)2011年9月5日:一烧车间烧结矿碱度由2.00调整至2.05 10)2011年9月5日:三烧车间烧结矿碱度由1.77调整至1.85 11)2011年9月5日:四烧车间烧结矿碱度由1.95调整至2.00 12)2011年9月19日:三烧车间烧结矿碱度由1.85调整至1.9013)2011年9月19日:一烧车间烧结矿碱度由2.05调整至2.10114)2011年9月22日:三烧车间烧结矿碱度由1.90调整至2.10 15)2011年10月17日:四烧车间烧结矿碱度由2.00调整至2.10 3.烧结矿碱度调整后烧结矿质量变化3.1高炉返矿率变化表1 2011年各高炉返矿率(%)#####高炉全厂56月份1高炉-3高炉4 高炉15.85 19.05 月1-8 16.04 12.92 15.4015.98 11.51 16.28 9月15.77 19.5415.29 15.32 11.57 13.42 10月19.8014.96 12.47 21.52 13.76 11月1--13日12.89由表1中数据可以看出:随着烧结矿碱度的升高,特别是进入10月份后各高炉返矿率明显下降,说明烧结矿质量呈变好趋势。
张钢转炉配吃高炉烧结矿返矿实践

张钢转炉配吃高炉烧结矿返矿实践摘要:张钢炼钢厂根据铁钢平衡及冶炼条件变化,本着降低生产成本的要求,对转炉配吃高炉烧结矿返矿进行可行性分析研究,通过有针对性的调整转炉炉料结构,减少废钢用量,优化工艺操作,在生产中取得了良好的实用效果。
关键词:转炉高炉烧结矿废钢1. 前言张钢炼钢厂现有两座120吨顶底复吹转炉,其中1#转炉2009年5月投产,2#转炉2011年3月投产。
目前主要冶炼HRB335系列钢种和Q235钢种直接去连铸,有时冶炼45#钢以及20#钢进精炼炉精炼之后去连铸。
2#转炉投产后,张钢炼铁厂现在仅有的一座1350m3高炉所生产的铁水不够两座转炉同时使用,炼钢厂转炉所用铁水由1350m3高炉铁水和外购铁水两部分组成。
两条线生产时,炼铁厂高炉铁水一罐到底兑入转炉,铁水温度一般在1400℃以上,铁水含硅量一般在0.4-0.7%范围。
外购铁水由汽车小罐运至混铁炉区域后折入铁包兑入转炉,一般三罐或四罐折够一包铁水。
外购铁水从不同厂家购进,温度一般在1200-1280℃范围,成分波动较大。
转炉两条线生产时,即使有外购铁水,铁水供应还是比较紧张,有时是来一包干一包。
经常是转炉开吹后还不知道下一包铁水是炼铁厂过来的还是外购的,废钢不好准备,准备少了,如果是炼铁厂铁水,温度不好控制,准备多了,外购铁水又拉不起温度来,过氧化拉温对炉况不利。
另外,外购铁水经常硅低硫高,转炉冶炼过程中化渣困难,对转炉脱磷脱硫不利。
高炉炼铁生产为了保证料柱的透气性,要求入炉矿石的最小粒度要大于5mm,因此要对入炉料进行筛料处理。
高炉烧结矿返矿是烧结矿经过筛选后的筛下料,张钢的一般处理方法是返回烧结工序混入精矿粉内重新进行烧结。
根据相关文献,烧结环节返矿加入量不宜超过30%,否则由于料层透气性过好导致垂直烧结速度过快高温保温时间不够产生不了足够的液相,急冷后烧结矿很脆转鼓指数下降。
张钢烧结环节烧结矿返矿配比在40—50%范围,烧结矿质量受到很大影响,粉化严重。
重钢降低高炉槽下返矿率的生产实践

为保证高炉生产顺利 ,烧结矿人炉前粒度小于 5 m的部分 , m 须筛分出来形成返矿 , 重新进行烧结。 适量的返矿 可以改善烧结过程 中料层 的透气性 ,促 进低熔点液相物的生成。但返矿量过大会导致烧结 厂返矿积压 ,给生产带来严重 的负担 , 并且烧结矿 中配入返矿量过多,会导致烧结成品率降低 ,固体 燃料消耗增加 ,提高生产运营的成本。
《 重钢降低高炉槽 下返矿率的生产实践 》
同时 目前商炉槽下筛板使用 的是 6 m 的筛 . m 5 孑, L 使部分+ m 5 m的烧结矿筛人返矿中, 增加了烧结 返 矿量 。在 调研 过 程 中还 发现 在烧 结 矿 的运 输 以及
从而使烧结矿的强度提高 了近 1 %,见表 5 。
表5 2 0 2 0 年5 0 6~ 0 7 月烧结矿转鼓 强度 状况
储存过程 中,由于操作和工艺环节不 当也直接导致 了较高的返矿率。 针对发现 的问题 ,重钢积极开展了工作 ,20 07 年 重钢返 矿率 从 1.1 降到 1.5 取 得 了 良好 69%下 35%, 的效果 ,使重钢返矿率基本与国内平均水平持平。 3 降低 槽 下返 矿率 的技 术措 施及 效果
重钢现有15 2 结机2 0 m' ]  ̄ ? 台,20 4m 烧结机 1 台, 年生产能力40 。但槽下返矿率与国内大于10 8 万t 0m 烧结机的平均返矿率相 比存在一定的差距 ,见表1 , 特别是2 6 月返矿率高达2 . O 年5 3 %, 7 严重影响了正 常的生产。为此 ,我们对影响烧结返矿率的因素进
表3 0 5~ 0 7 月烧结矿质量状况 2 0 2 0 年5
并加强了对料仓的管理 ,防止空仓操作 ,控制 料仓料位大于 2 ,减小落差。并改造 了三烧整粒系 / 3 统 ,对转运落差较高 的梭槽 ,在梭槽内增加了缓 冲 阶梯 ,减少因转运落差高而造成的烧结矿摔打粉碎。
高炉炉况分析

舞钢高炉周分析(3.28~4.3)一、高炉成本指标变化日产全焦比煤比焦丁比燃料比一级品上周3072.9 415.5 90.44 25.4 531.34 99.1本周3299.7 400.3 80.47 25.5 506.27 100变化226.8 -15.2 -9.97 -0.1 -25.07 0.9二、本周重要生产记事1、3月28日19:1520#堵砖风口吹开,之前捅6次未捅开,至此22个风口全部送风,焦比400;2、28日14:00之后炉温下行,顶温低至70℃,44批开始附加美锦焦0.2t/批,走10批,20:30开口后炉温上行至0.7;3、29日白班10:00压差关系大幅走松,最低压差120kpa,最低减风至2250控制气流,12:00之后关系正常,逐步加风,14批开始附加美锦焦炭0.3t/批,走7批;中班22:00之后关系走紧,被迫减风至2250;4、30日夜班开始关系不稳,整体紧,冶强偏低,3:53-4:00、10:58-11:14、16:52-17:33停煤3次,9:05倒西场开始双场出铁,西场连出一次;白班风量萎缩,关系紧,探尺工作不好,平均风量2338,21-30批附加美锦焦0.3t;16:50东场开口后大喷不出铁,堵口再开后依然较喷,顶压撤至150,中班7-11批每批附加美锦焦1t,19:00之后炉况逐步好转,风量恢复到2450;5、31日夜班前期炉温低,1-21批附加焦丁0.2t/批,后期返热至0.57,中班开始压差关系走紧,负荷做重,中班燃料比487,致4月1日夜班开始冶强高,夜班料批53,燃料比未及时跟上(501),炉温下行严重;6、1日白班开始压差关系急剧走松,至11:00压差维持在120-130之间,最低控风至2300,3-20批附加美锦焦0.2t/批,7-11批额外附加美锦焦1t/批,13:00炉温上行正常,中班燃料比按510控制;2日7:49、8:23两次崩料至2.5m左右,白班开始关系又大幅走松,1-12批附加美锦焦0.3t/批,后炉温上行后13:51-14:08停煤;7、3日夜班24-31批因关系紧料慢附加美锦焦0.3t/批,3:45-4:16停煤,47批减100kg美锦焦批,焦比398,白班50批减美锦焦批150kg,焦比391,17:00-17:11停煤一次,全天炉况较顺行,炉温物理热充足(1510℃左右);8、另3月26日休风送风之后风口开始出现大面积结焦现象,4#、7#、12#、15#、22#风口结焦较为严重,尤其在炉温向凉时结焦加剧。
降低烧结矿返矿率的措施

Co nt r e s r sf r Re cng t t n Fi t fSi e u e m a u e o du i he Re ur ne Ra e o nt r
T N h— o g L O X u—h a N N h-in WA G Z— o g X O G L n xag A G Z ih n U i— u n O G Z ij — c a N ih n I N a - i — n
1 前
言
国 内 lO 以上 烧 结 机 的 平 均 水 平 ( 表 1 。 Om 见 )
柳钢 烧结 返 矿分 为 内返 矿 和外 返 矿 两部 分 。
由表 1 见 ,20 可 07年后 柳 钢 返 矿率 突增 ,且 居
高不 下 。
内返 矿 为烧 结 厂 内经一 次 和二 次 成 品筛 筛 出的 <
返 矿 率 一 直 是 炼 铁 和烧 结 工序 共 同追 求 的 目标 之 一 。本 文 就 如 何 降低 柳 钢 烧 结 矿 返 矿 率 进 行 初 步地探 讨 。 柳 钢 现 有 8 m 烧 结 机 2台 , lm22 5m 、 0 1O ,6 3 0m 烧结 机各 1台 ,年 生产 能力达 到 10 0万 6 8
部 分组成 比例 为 3 4 %~ %,而 经过缓 冲仓及 途 中 皮 带运 输 到 高炉 槽 上后 ,其 比例 上 升 至 1%左 . 2
右 ,运 输途 中破 碎产 生 的烧 结矿 粉末 接近 1 %。 0 可 见 ,烧结 矿 转 鼓 强度 偏 低是 造 成 柳 钢烧 结 矿
m e ta d pr d c in p a tc . n n o u to r c i e
Ke o d y W r s: S n e i g; Re u n Fi e Ra e; Tu i t rn tr n t mblrS r ngh; P o e s Te h o o y; Ma a e n e te t rcs; c n lg n g me t
炼铁厂烧结工序能耗降低的途径

图3 涟钢四烧 21 年 1 00 月至 8 月份工序能耗结构
要 由 4部 分构 成 : 固体燃 耗 、 煤气 和 压风 , 电、
22 涟钢与其他钢铁企业烧结工序能耗对比 .
・
21 ・
烧 结工序 能耗对 比见 表 1。
表 1数据 显 示 , 涟钢 烧 结工 序 能耗 水 平 略 优于行业 平 均 水 平 , 指标 情 况在 行 业 中处 于 中下游 的位 置 , 行业 先 进 水平 相 比相距 与 甚远 , 但也 要看 到 涟 钢烧 结 工序 能耗 的 降低
燃耗 升高 , 结工序 能耗升高 。( ) 份 以 烧 C 7月 来 , l 高炉 停炉 影 响 , 烧 1 0 烧 结 机 受 # 三 8m
2 涟 钢烧结工序能耗 现状
2 1 涟 钢烧 结工 序能 耗结 构 .
涟 钢烧结 工 序能 耗见 图 1 图 2 图 3 、 、 。
黧压 风
{ 固体 燃 耗 豳 i 鞠煤 气 消 耗
a水
0 电
穗 压 风
8 % 5
图1 21 0 0年 1 8月份 二 烧 烧 结 工 序 能 耗 结构 至
表 1 21 00年 1 8月 涟钢 与 国 内 7 主 要 钢 铁 企 业烧 结 工 序 能 耗 对 比 至 5家
_
T序 能 -
;ge k c/t
固体 燃耗 ;get kc/
月 份
行 业水平
最好水平
涟钢
与行业比较
行 业水平
最好水平
涟钢
与行 业比较
注: 为使 数 据 具 有 可 比性 , 计 数 据 均 为算 术 平 均值 。 合
槽下返矿配比对烧结矿质量的影响

2021225槽下返矿配比对烧结矿质量的影响李雪松1贾秀凤$(1.唐山瑞丰钢铁有限公司唐山063303;2.宁波钢铁有限公司宁波315800)摘要:通过烧结杯实验,研究槽下返矿含量的提高对烧结矿质量的影响规律并揭示了其作用机理。
结果表明:随着返矿含量的增加,成品率逐渐上升,垂直烧结速度逐渐下降,转鼓指数和低温还原粉化指数RDI+3.15,呈现先升高后下降的趋势。
综合考虑,槽下返矿含量为6%为最佳配比,此条件下,成品率为78.97%,垂直烧结速度为21.98mm/miii,转鼓指数为65.07%,低温还原粉化指数RDI+3.15为68.34%;利用扫描电子显微镜(SEM)对烧结矿矿相进行分析,从微观角度阐明不同槽下返矿配比对烧结矿冶金性能的影响机理。
关键词:槽下返矿;粉烧;烧结;转股指数;低温还原粉化0前言烧结矿返矿[1一引分为热返矿、冷返矿和高炉槽下返矿3种,其中热返矿为烧结台车运行到烧结机尾时烧结机两侧及表层未烧好的烧结矿经机尾剪切和筛分后的筛下物;冷返矿为热烧结矿经冷却和整粒后的筛下物;高炉料槽下返矿,又称粉烧,为在高炉槽下收集的烧结矿在输送过程中产生的细颗粒。
烧结矿返矿粒度一般在5mm以下〔4-7],热返矿送到烧结混合料皮带上返回烧结;冷返矿和高炉料槽下返矿则返回烧结配料室,且返回烧结的返矿化学成分基本上与烧结矿相同。
目前部分烧结厂把烧结返矿按一定比例与精矿粉、溶剂、返矿、除尘灰配比后再进行烧结,其目的主要是废料再利用,节约资源。
本文主要研究高炉槽下返矿含量对烧结矿的影响。
烧结返矿率取决于混合制粒、烧结机布料、烧结点火热量、烧结终点控制等种种因素4⑵。
烧结配矿方案中,槽下返矿配比通常低于10%,而现场混合矿配矿方案中返矿配比较高,反映出烧结矿强度较差以及粉化性能较差。
因此,考察烧结返矿配比对烧结的影响,研究其配比对烧结矿烧结工艺指标和冶金性能的影响规律,并对其恶化粉化性能进行机理分析,通过对配矿中返矿配比的调节,以确定最佳粉烧配比,使烧结矿的冶金性能最佳,为现场生产提供指导。
八钢高炉炉况失常原因及处理
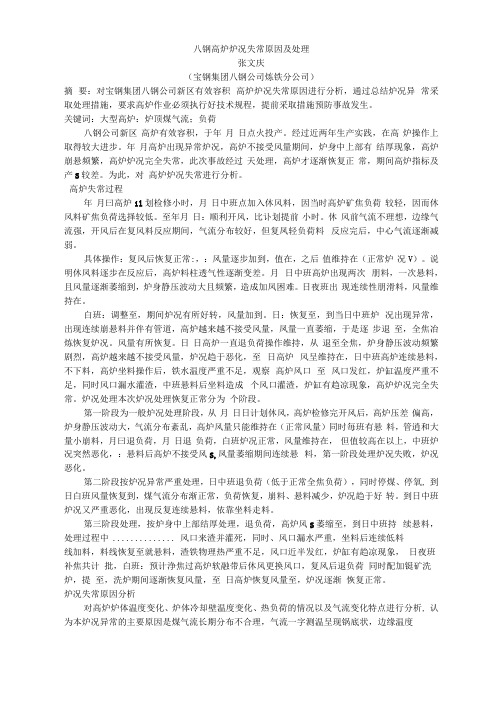
八钢高炉炉况失常原因及处理张文庆(宝钢集团八钢公司炼铁分公司)摘要:对宝钢集团八钢公司新区有效容积高炉炉况失常原因进行分析,通过总结炉况异常采取处理措施,要求高炉作业必须执行好技术规程,提前采取措施预防事故发生。
关键词:大型高炉:炉顶煤气流;负荷八钢公司新区高炉有效容积,于年月日点火投产。
经过近两年生产实践,在高炉操作上取得较大进步。
年月高炉出现异常炉况,高炉不接受风量期间,炉身中上部有结厚现象,高炉崩悬频繁,高炉炉况完全失常,此次事故经过天处理,高炉才逐渐恢复正常,期间高炉指标及产S较差。
为此,对高炉炉况失常进行分析。
高炉失常过程年月曰高炉il划检修小时,月日中班点加入休风料,因当时高炉矿焦负荷较轻,因而休风料矿焦负荷选择较低。
至年月日:顺利开风,比讣划提前小时。
休风前气流不理想,边缘气流强,开风后在复风料反应期间,气流分布较好,但复凤轻负荷料反应完后,中心气流逐渐减弱。
具体操作:复风后恢复正常:,:风量逐步加到,值在,之后值维持在(正常炉况V)。
说明休凤料逐步在反应后,高炉料柱透气性逐渐变差。
月日中班高炉出现两次朋料,一次悬料,且风量逐渐萎缩到,炉身静压波动大且频繁,造成加凤困难。
日夜班出现连续性朋滑料,风量维持在。
白班:调整至,期间炉况有所好转,风量加到。
日:恢复至,到当日中班炉况出现异常,出现连续崩悬料并伴有管道,高炉越来越不接受风量,凤量一直萎缩,于是逐步退至,全焦冶炼恢复炉况。
风量有所恢复。
日日高炉一直退负荷操作维持,从退至全焦,炉身静压波动频繁剧烈,高炉越来越不接受风量,炉况趋于恶化,至日高炉风呈维持在,日中班高炉连续悬料,不下料,高炉坐料操作后,铁水温度严重不足,观察高炉风口至风口发红,炉缸温度严重不足,同时风口漏水灌渣,中班悬料后坐料造成个风口灌渣,炉缸有趋凉现象,高炉炉况完全失常。
炉况处理本次炉况处理恢复正常分为个阶段。
第一阶段为一般炉况处理阶段,从月日日计划休风,高炉检修完开风后,高炉压差偏高,炉身静压波动大,气流分布紊乱,高炉风量只能维持在(正常风量)同时毎班有悬料,管逍和大量小崩料,月曰退负荷,月日退负荷,白班炉况正常,风量维持在,但值较高在以上,中班炉况突然恶化,:悬料后高炉不接受风S,凤量萎缩期间连续悬料,第一阶段处理炉况失败,炉况恶化。
炼铁厂降本增效总结_1

炼铁厂降本增效总结导读:本文炼铁厂降本增效总结,仅供参考,如果觉得很不错,欢迎点评和分享。
除尘系统改造、优化2011年10月份利用2#炉停炉期间,使用2#炉3个箱体,解决了高炉布袋箱体不足的问题,使1#炉布袋的寿命延长了2——3倍,降低成本20万元以上。
同月改造1#炉布袋卸灰球阀密封,节约成本10万元。
(3)改造高炉供料系统,减少高炉返矿率受场地限制,高炉上料系统皮带多,中转此次多,烧结矿经多次中转后返矿率升高,小粒级增多,制约高炉生产,同时成本升高。
为此,2012年1月2日,对3#高炉供料系统进行改造,并于1月16日投入使用。
该改造项目实施后,使烧结矿不经过中转仓,直接经过皮带进入槽上料仓,降低了烧结矿的返矿率,改善了入炉烧结矿粒级。
(4)2011年下半年,通过对3#炉槽下压系统改造、冷却水过滤器改造、净环更换网格式滤料,以及1#炉卷扬料车做溜车保护装置等一系列技术创新活动,非计划检修率为零的最佳指标。
其中2011年6——11月份设备慢风率为零。
3、辅助支撑方面(1)3#高炉单炉生产期间,利用磨煤能力较大,在非用电高峰时间将煤粉提前磨好,减少用电高峰磨煤时间,节约电费6.5万元/月左右(2)对除尘风机及冲渣水泵进行控制,在不出铁时将风机转速调至最低,降低负荷,同时停用冲渣泵,有效的降低了电耗。
(3)配吃FMG粉期间,协调倒运焦炭车辆,使倒运时间由原来的15分钟/车,降到现在的9分钟/车,既保证了仓位,又减少了皮带运转时间,降低了电耗;同时焦炭直接入仓,减少焦炭倒运次数,避免了车辆的碾轧减少入炉粉末。
(4)为减少入炉料的摔打,保证槽上料位在两米以下;槽下每个班做两次检测,发现烧结矿含粉在3%以上的,及时控制振筛振幅和下料速度;以上两项分厂派专人负责抽查,实施后效果良好,入炉含粉量得到有效的控制。
4、自主管理和提案制度2011年荣获公司“自主管理”和“提案制度”绩优先进单位称号2012年,炼铁厂圆满组织完成了第六、七、八届三届自主管理活动,针对成本、生产、能源、维护、环保、其它等六方面开展活动,有效解决了生产过程中存在的实际问题。