2200Nm3天然气制氢方案
最新1500Nm3-h天然气转化制氢装置项目建议书

xxxx集团有限公司1500Nm3/h天然气转化制氢装置项目建议书编号:xxxx-xxxx-1112一、总论1.1 装置名称及建设地点装置名称:1500Nm3/h 天然气制氢装置建设地点:xxxx1.2 装置能力和年操作时间装置能力::1500Nm3/h;H2纯度: ≧99.99(V/V)压力≧2.0 MPa(待定)年操作时间:≧8000h操作范围:40%-110%1.3 原料天然气(参考条件,请根据实际组分修改完善):1.4 产品氢气产品1.5 公用工程规格1.5.1 脱盐水●温度:常温●压力:0.05MPa(G)●水质:电导率≤5μS/cm溶解O2 ≤2 mg/kg氯化物≤0.1 mg/kg硅酸盐(以SiO2计) ≤0.2 mg/kgFe ≤0.1 mg/kg1.5.2 循环冷却水●供水温度:≤28℃●回水温度:≤40℃●供水压力:≥0.40MPa●回水压力:≥0.25MPa●氯离子≤25 mg/kg1.5.3 电●交流电:相数/电压等级/频率 3 PH/380V/50Hz●交流电:相数/电压等级/频率 1 PH/220V/50Hz● UPS交流电:相数/电压等级/频率 1 PH/220V/50Hz1.5.4 仪表空气●压力: 0.7MPa●温度:常温●露点: -55 ℃●含尘量: <1mg/m3,含尘颗粒直径小于3μm。
●含油量:油份含量控制在1ppm以下1.5.5 氮气●压力: 0.6MPa●温度: 40℃●需求量:在装置建成初次置换使用,总量约为5000 Nm3正常生产时不用1.6 公用工程及原材料消耗注:电耗与原料天然气压力有关。
1.7 占地面积主装置占地:约50×40=2000 m2 (不包括公用工程及生活设施等)二、工艺方案2.1 工艺流程简述基本的工艺流程框图如下:器,进一步预热后进入转化管,在催化剂床层中,甲烷与水蒸汽反应生成H2、CO和CO2,甲烷转化所需热量由转化器烧嘴燃烧燃料混合气提供。
天燃气制氢操作规程

天然气制氢第一章天然气制氢岗位基本任务以天燃气为原料的烃类和蒸汽转化,经脱硫、催化转化、中温变化,制得丰富含氢气的转化气,再送入变压吸附装置精制,最后制得纯度≥99.9%的氢气送至盐酸。
1.1工艺流程说明由界区来的天然气压力为1.8~2.4MPa,经过稳压阀调节到1.8Mpa,进入原料分离器F0101后,经流量调节器调量后入蒸汽转化炉B0101对流段的原料气预热盘管预热至400℃左右,进入脱硫槽D0102,使原料气中的硫脱至0.2PPm以下,脱硫后的原料气与工艺蒸汽按水碳比约为3.5进行自动比值调节后进入混合气预热盘管,进一步预热到~590℃左右,经上集气总管及上猪尾管,均匀地进入转化管中,在催化剂层中,甲烷与水蒸汽反应生产CO和H2。
甲烷转化所需热量由底部烧咀燃烧燃料混合气提供。
转化气出转化炉的温度约650--850℃,残余甲烷含量约3.0%(干基),进入废热锅炉C0101的管程,C0101产生2.4MPa(A)的饱和蒸汽。
出废热锅炉的转化气温度降至450℃左右,再进入转化冷却器C0102,进一步降至360℃左右,进入中温变换炉。
转化气中含13.3%左右的CO,在催化剂的作用下与水蒸气反应生成CO2和H2,出中变炉的转化气再进入废热锅炉C0101的管程换热后,再经锅炉给水预热器C0103和水冷器C0104被冷至≤40℃,进入变换气分离器F0102分离出工艺冷凝液,工艺气体压力约为1.4MPa(G)。
燃料天然气和变压吸附装置来的尾气分别进入转化炉的分离烧嘴燃烧,向转化炉提供热量≤1100℃。
为回收烟气热量,在转化炉对流段内设有五组换热盘管:(由高温段至低温段)蒸汽-A原料混合气预热器, B 原料气预热器,C烟气废锅,D燃料气预热器,E尾气预热器压力约为1.4的转化工艺气进入变化气缓冲罐,再进入PSA装置。
采用5-1-3P,即(5个吸附塔,1个塔吸附同时3次均降)。
常温中压下吸附,常温常压下解吸的工作方式。
天然气制氢工艺技术规程

天然气制氢装置工艺技术规程1.1装置概况规模及任务本制氢装置由脱硫造气工序、变换工序、PSA制氢工序组成1.2工艺路线及产品规格该制氢装置已天然气为原料,采用干法脱硫、3.8MPa压力下的蒸汽转化,一氧化碳中温变换,PSA工艺制得产品氢气。
1.3消耗定额(1000Nm3氢气作为单位产品)2.1工艺过程原料及工艺流程2.1.1工艺原理1.天然气脱硫本装置采用干法脱硫来解决该原料气中的硫份。
为了脱除有机硫,采用铁锰系转化吸取型脱硫催化剂,并在原料气中加入约1-5%的氢,在约400℃高温下发生下述反映:RSH+H2=H2S+RHH2S+MnO=MnS+H2O经铁锰系脱硫剂初步转化吸取后,剩余的硫化氢,再在采用的氧化锌催化剂作用下发生下述脱硫反映而被吸取:H2S+ZnO=ZnO+H2OC2H5SH+ZnS+C2H5+H2O氧化锌吸硫速度极快,因而脱硫沿气体流动方向逐层进行,最终硫被脱除至0.1ppm以下,以满足蒸汽转化催化剂对硫的规定。
2.蒸汽转化和变换原理原料天然气和蒸汽在转化炉管中的高温催化剂上发生烃—蒸汽转化反映,重要反映如下:CH4+H2O= CO+3H2-Q (1)一氧化碳产氢CO+H2O=CO2+H2+Q (2)前一反映需大量吸热,高温有助于反映进行;后一反映是微放热反映,高温不利于反映进行。
因此在转化炉中反映是不完全的。
在发生上述反映的同时还伴有一系列复杂的付反映。
涉及烃类的热裂解,催化裂解,水合,蒸汽裂解,脱氢,加氢,积碳,氧化等。
在转化反映中,要使转换率高,残余甲烷少,氢纯度高,反映温度要高,但要考虑设备承受能力和能耗,所以炉温不宜太高。
为缓和积碳,增长收率,要控制较大的水碳比。
3.变化反映的反映方程式如下:CO+H2O=CO2+H2+Q这是一个可逆的放热反映,减少温度和增长过量的水蒸气,均有助于变换反映向右侧进行,变换反映假如不借助于催化剂,其速度是非常慢的,催化剂能大大加速其反映速度。
天然气制氢装置工艺过程原料及工艺流程
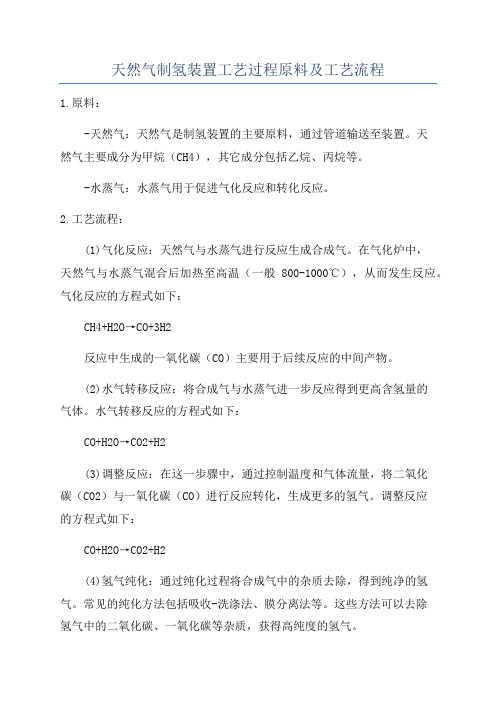
天然气制氢装置工艺过程原料及工艺流程
1.原料:
-天然气:天然气是制氢装置的主要原料,通过管道输送至装置。
天
然气主要成分为甲烷(CH4),其它成分包括乙烷、丙烷等。
-水蒸气:水蒸气用于促进气化反应和转化反应。
2.工艺流程:
(1)气化反应:天然气与水蒸气进行反应生成合成气。
在气化炉中,
天然气与水蒸气混合后加热至高温(一般800-1000℃),从而发生反应。
气化反应的方程式如下:
CH4+H2O→CO+3H2
反应中生成的一氧化碳(CO)主要用于后续反应的中间产物。
(2)水气转移反应:将合成气与水蒸气进一步反应得到更高含氢量的
气体。
水气转移反应的方程式如下:
CO+H2O→CO2+H2
(3)调整反应:在这一步骤中,通过控制温度和气体流量,将二氧化
碳(CO2)与一氧化碳(CO)进行反应转化,生成更多的氢气。
调整反应
的方程式如下:
CO+H2O→CO2+H2
(4)氢气纯化:通过纯化过程将合成气中的杂质去除,得到纯净的氢气。
常见的纯化方法包括吸收-洗涤法、膜分离法等。
这些方法可以去除
氢气中的二氧化碳、一氧化碳等杂质,获得高纯度的氢气。
(5)氢气储存:将纯净的氢气储存起来,以便后续使用。
常用的储氢方式包括压缩氢气储存和液态氢气储存。
以上是天然气制氢装置的工艺过程、原料及工艺流程的详细介绍。
该装置通过将天然气与水蒸气进行一系列反应和处理,最终得到纯净高纯度的氢气。
天然气制氢装置在能源转型和环保领域具有重要的应用价值。
天然气制氢装置工艺技术规范
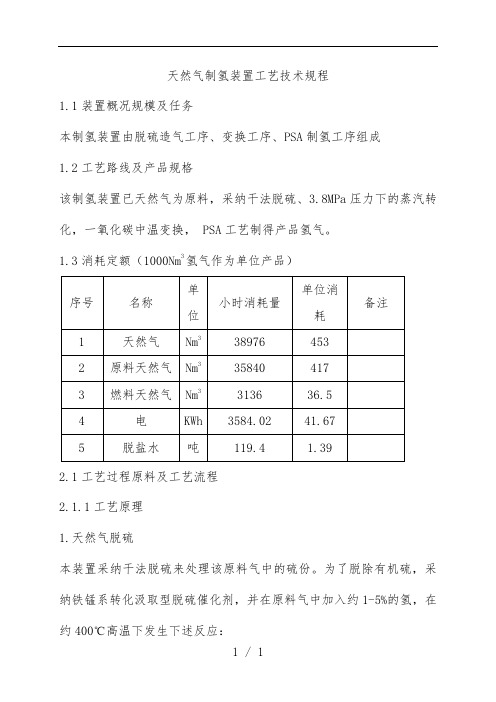
天然气制氢装置工艺技术规程1.1装置概况规模及任务本制氢装置由脱硫造气工序、变换工序、PSA制氢工序组成1.2工艺路线及产品规格该制氢装置已天然气为原料,采纳干法脱硫、3.8MPa压力下的蒸汽转化,一氧化碳中温变换, PSA工艺制得产品氢气。
1.3消耗定额(1000Nm3氢气作为单位产品)2.1工艺过程原料及工艺流程2.1.1工艺原理1.天然气脱硫本装置采纳干法脱硫来处理该原料气中的硫份。
为了脱除有机硫,采纳铁锰系转化汲取型脱硫催化剂,并在原料气中加入约1-5%的氢,在约400℃高温下发生下述反应:RSH+H2=H2S+RHH2S+MnO=MnS+H2O经铁锰系脱硫剂初步转化汲取后,剩余的硫化氢,再在采纳的氧化锌催化剂作用下发生下述脱硫反应而被汲取:H2S+ZnO=ZnO+H2OC2H5SH+ZnS+C2H5+H2O氧化锌吸硫速度极快,因而脱硫沿气体流淌方向逐层进行,最终硫被脱除至0.1ppm以下,以满足蒸汽转化催化剂对硫的要求。
2.蒸汽转化和变换原理原料天然气和蒸汽在转化炉管中的高温催化剂上发生烃—蒸汽转化反应,要紧反应如下:CH4+H2O= CO+3H2-Q (1)一氧化碳产氢 CO+H2O=CO2+H2+Q (2)前一反应需大量吸热,高温有利于反应进行;后一反应是微放热反应,高温不利于反应进行。
因此在转化炉中反应是不完全的。
在发生上述反应的同时还伴有一系列复杂的付反应。
包括烃类的热裂解,催化裂解,水合,蒸汽裂解,脱氢,加氢,积碳,氧化等。
在转化反应中,要使转换率高,残余甲烷少,氢纯度高,反应温度要高,但要考虑设备承受能力和能耗,因此炉温不宜太高。
为缓和积碳,增加收率,要操纵较大的水碳比。
3.变化反应的反应方程式如下:CO+H2O=CO2+H2+Q这是一个可逆的放热反应,降低温度和增加过量的水蒸气,均有利于变换反应向右侧进行,变换反应假如不借助于催化剂,其速度是特不慢的,催化剂能大大加速其反应速度。
制氢装置生产工艺规程

3000Nm3∕h制氢装置生产工艺规程一、项目概述设计规模为:3000Nm3∕h o二、产品性能氢气广泛应用于国民经济各领域,氢气分子式为H2,分子量为2.0158,系无色无味的可燃性气体。
气体密度为0.0899Kg∕m3,熔点-259.14℃,沸点-252.8C(76OmmHg柱),自然点为400℃,爆炸极限 4.1-74.2%,极微溶于水、甲醇、乙醛及各种液体。
常温稳定,高温有催化剂时很活泼,极易燃、易爆,并能与非金属和金属化合。
氢气:符合国标GB/T3634——1995优等品标准要求,其技术指标要求如下:1、天然气技术指标如下:90℃以下稳定,对碳刚、不锈钢无腐蚀;电导率W30us∕cm四、反应方程式1脱硫烯烬:RC=CR ∠>+H 2 RC-CR ,+Q硫醇:RSH+>H 2R I H+R 2H+H 2SR1H+R2H+2H2S睡吩:C4H4S+4⅛rC4H10+H2S氧硫化碳:CoS→h CO+H 2S 二硫化碳:CS2+4H 2CH 4+2H 2S2转化 CH 4+H 2O-÷g) CO+3H 2 CO+H2O-^g) CO2+H23中变二硫酸:RISSRTTH2 ∆H 298=206.29KJ ∆H298=41.19KJ∆H 298=41.19KJ4脱碳R2CH3N+CO2+H2O=R2CH3NHHCO3五:工艺流程方框图100co+H 2O -÷^)CO2+H2 原淞缓冲罐天然气压缩机加氢反应器R1OO1脱硫反应器 R1002A/BC02再生塔TIoo2 F ------ 污CO2冷却器|E1006纯僧大干999%的产品软C02分液罐除盐水预热器E1005变压吸附放空六、工艺配比水碳比:3.5-4.5七、工艺操作规程1、开车准备1)检查水、电、气、脱盐水、仪表空气、天然气、氮气等供应情况; 2)检查压力表、程控阀、循环水是否正常;配制好脱碳溶剂;3)开启色谱机,做好生产控制分析的准备;4)检查动力设备的完好情况,检查所有仪表电源、气源、信号是否正常;5)对系统进行气密性试验;6)建立汽包、除氧器液位,氯离子含量是否正常;7)排净各管道、设备冷凝水、设备内冷凝水,检查各类阀门是否处在待开车状态。
天然气制氢技术方案及设备配置模板

天然气制氢气装置技术方案项目名称:****Nm3/h天然气制氢装置技术方案及设备配置第一部分技术方案1、产品方案装置氢气生产能力:***Nm3/h2、天然气裂解制氢工艺方案2.1 烃类蒸汽转化制氢工艺简介以轻烃为原料制取工业氢,国内外均认为蒸汽转化法为最佳方案。
大型合成氨厂以及炼油厂和石油化工厂的制氢装置,其造气工艺大多为水蒸汽转化法。
经过多年的生产实践,目前已积累了许多成功的工程设计和操作经验。
因此本方案采用水蒸汽转化法造气工艺。
国内外蒸汽转化制氢的净化工艺主要有两种。
即化学净化法和变压吸附净化法(PSA净化法)。
国内早期建设的制氢装置均采用化学净化法。
由于近年PSA技术的进步(多床多次均压,吸附剂性能的改进等),使氢的回收率最高达95%,加之PSA 技术的国产化,极大降低了PSA装置的投资以及其操作成本,使该技术在新建制氢装置中占主导地位。
采用天然气为原料生产氢气。
选择PSA净化气体,其制氢成本比采用化学净化法的制氢成本低,同时采用PSA技术具有流程简短、自动化程度高、产品氢纯度高等特点,因此,我们推荐用户采用PSA净化技术。
综上所述,制氢装置采用水蒸汽转化法加PSA净化工艺。
2.2原料组成压力:≤0.2Mpa温度:40℃。
原料气组成(V%):3、工艺流程3.1工艺概述本制氢装置是以天然气为原料,采用蒸汽转化造气工艺制取粗氢气。
转化压力~2.0MPa(G),粗氢经变换和PSA 分离杂质后得产品氢气。
3.2基本原理 3.2.1 原料脱硫脱硫分两步进行:原料气中有机硫化物的加氢转化反应,硫化氢的脱除。
在一定温度、压力下,原料气通过钴钼加氢催化剂,将有机硫转化成无机硫;原料经过有机硫转化后,再通过氧化锌脱硫剂,将原料气中的H 2S 脱至0.2ppm 以下,以满足蒸汽转化催化剂对硫的要求,其主要反应(以硫醇和噻酚为例)为:3.2.2 烃类的蒸汽转化烃类的蒸汽转化是以水蒸汽为氧化剂,在镍催化剂的作用下将烃类物质转化,得到制取氢气的原料气。
天然气制氢方案

天然气制氢方案1. 简介天然气作为一种清洁、高效、广泛应用的能源,其可持续利用的方式一直备受关注。
本文讨论了一种利用天然气制氢的方案,通过分析其原理、技术路线和应用前景,探讨了其在能源转型中的关键作用。
2. 原理天然气制氢是通过将天然气与水蒸气经过催化剂反应,产生含有氢气的气体。
该反应过程称为蒸汽重整反应。
天然气中的甲烷和水蒸气在高温条件下通过反应生成氢气和一氧化碳。
蒸汽重整反应的化学方程式如下所示:CH4 + H2O -> CO + 3H2可见,甲烷和水蒸气通过反应生成一氧化碳和氢气。
制氢反应需要适宜的温度和催化剂以保证反应的高效进行。
3. 技术路线天然气制氢主要有两种技术路线:蒸汽重整和部分氧化。
3.1 蒸汽重整蒸汽重整是目前最成熟的天然气制氢技术路线。
该路线通过直接将天然气和水蒸气经过催化剂反应,生成含有氢气的气体。
蒸汽重整技术路线具有操作稳定、氢气纯度高等优点,被广泛应用于工业生产和燃料电池等领域。
3.2 部分氧化部分氧化是另一种常见的天然气制氢技术路线,通过在天然气中加入氧气并经过催化剂反应,产生氢气和一氧化碳。
这种技术路线操作相对简单,但氢气纯度较低,需要进一步的纯化处理。
4. 应用前景天然气制氢方案在能源转型中具有重要作用。
4.1 温室气体减排天然气制氢是一种低碳能源生产方式,相较于传统煤炭和石油氢气生产方式,其减排潜力更大。
通过采用天然气制氢方案,可以有效减少CO2、SOX等温室气体的排放,为应对气候变化做出贡献。
4.2 新能源利用制氢技术对于新能源的利用具有重要意义。
利用可再生能源(如风能、太阳能等)产生电力,再通过电解水制氢,可实现清洁能源的转化储存。
天然气制氢方案在新能源开发和利用方面具有巨大潜力。
4.3 燃料电池应用天然气制氢方案与燃料电池技术相结合,可以实现高效的清洁能源利用。
燃料电池将氢气与氧气进行反应,产生电能和水,在交通、家庭和工业领域等多个领域具有广阔的应用前景。
中小型天然气转化制氢与甲醇制氢技术的选择
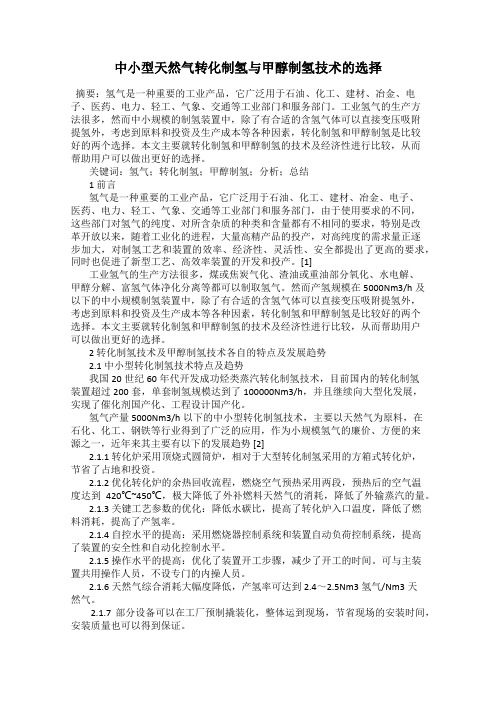
中小型天然气转化制氢与甲醇制氢技术的选择摘要:氢气是一种重要的工业产品,它广泛用于石油、化工、建材、冶金、电子、医药、电力、轻工、气象、交通等工业部门和服务部门。
工业氢气的生产方法很多,然而中小规模的制氢装置中,除了有合适的含氢气体可以直接变压吸附提氢外,考虑到原料和投资及生产成本等各种因素,转化制氢和甲醇制氢是比较好的两个选择。
本文主要就转化制氢和甲醇制氢的技术及经济性进行比较,从而帮助用户可以做出更好的选择。
关键词:氢气;转化制氢;甲醇制氢;分析;总结1 前言氢气是一种重要的工业产品,它广泛用于石油、化工、建材、冶金、电子、医药、电力、轻工、气象、交通等工业部门和服务部门,由于使用要求的不同,这些部门对氢气的纯度、对所含杂质的种类和含量都有不相同的要求,特别是改革开放以来,随着工业化的进程,大量高精产品的投产,对高纯度的需求量正逐步加大,对制氢工艺和装置的效率、经济性、灵活性、安全都提出了更高的要求,同时也促进了新型工艺、高效率装置的开发和投产。
[1]工业氢气的生产方法很多,煤或焦炭气化、渣油或重油部分氧化、水电解、甲醇分解、富氢气体净化分离等都可以制取氢气。
然而产氢规模在5000Nm3/h及以下的中小规模制氢装置中,除了有合适的含氢气体可以直接变压吸附提氢外,考虑到原料和投资及生产成本等各种因素,转化制氢和甲醇制氢是比较好的两个选择。
本文主要就转化制氢和甲醇制氢的技术及经济性进行比较,从而帮助用户可以做出更好的选择。
2 转化制氢技术及甲醇制氢技术各自的特点及发展趋势2.1 中小型转化制氢技术特点及趋势我国20世纪60年代开发成功烃类蒸汽转化制氢技术,目前国内的转化制氢装置超过200套,单套制氢规模达到了100000Nm3/h,并且继续向大型化发展,实现了催化剂国产化、工程设计国产化。
氢气产量5000Nm3/h以下的中小型转化制氢技术,主要以天然气为原料,在石化、化工、钢铁等行业得到了广泛的应用,作为小规模氢气的廉价、方便的来源之一,近年来其主要有以下的发展趋势 [2]2.1.1 转化炉采用顶烧式圆筒炉,相对于大型转化制氢采用的方箱式转化炉,节省了占地和投资。
煤制氢与天然气制氢对比
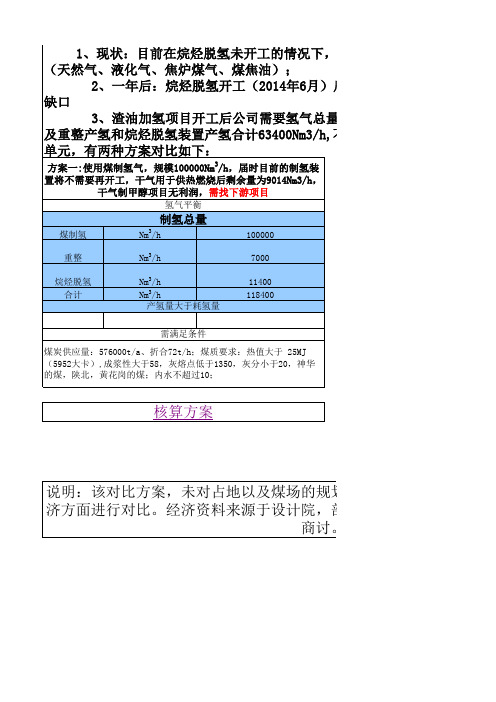
项
目
粒度,mm 块煤限下率,% 含矸率,% 灰分Ad,% 煤灰熔融软化温度ST(℃) 全硫Std,% 热稳定性TS-6,% 抗碎强度SS,% 胶质层最大厚度(1)Y,mm 发热量Qnet.ar,MJ/kg
方案一:使用煤制氢气,规模100000Nm3/h,届时目前的制氢装 置将不需要再开工,干气用于供热燃烧后剩余量为9014Nm3/h, 干气制甲醇项目无利润,需找下游项目
氢气平衡
制氢总量
煤制氢 重整 烷烃脱氢 合计 Nm /h Nm3/h Nm3/h 3 Nm /h 产氢量大于耗氢量 需满足条件 煤炭供应量:576000t/a、折合72t/h;煤质要求:热值大于 25MJ (5952大卡),成浆性大于58,灰熔点低于1350,灰分小于20,神华 的煤,陕北,黄花岗的煤;内水不超过10;
场的规划进行比较,仅从原料,产品以及技术经 计院,部分内容来源于网络,有不周之处待共同 商讨。
3
100000 7000 11400 118400
Байду номын сангаас
核算方案
说明:该对比方案,未对占地以及煤场的规划进行比较,仅从原料,产 济方面进行对比。经济资料来源于设计院,部分内容来源于网络,有不 商讨。
情况下,一期上4台煤制气炉解决代替干气以外的燃料 ; 年6月)后,燃料气增加,需上两台煤制气炉解决燃料
氢气总量为:107500Nm3/h,结合目前公司的制氢规模 Nm3/h,不能满足渣油加氢项目开工需求,需新上制氢
天燃气制氢操作规程
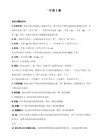
天然气制氢第一章天然气制氢岗位基本任务以天燃气为原料的烃类和蒸汽转化,经脱硫、催化转化、中温变化,制得丰富含氢气的转化气,再送入变压吸附装置精制,最后制得纯度≥99.9%的氢气送至盐酸。
1.1工艺流程说明由界区来的天然气压力为1.8~2.4MPa,经过稳压阀调节到1.8Mpa,进入原料分离器F0101后,经流量调节器调量后入蒸汽转化炉B0101对流段的原料气预热盘管预热至400℃左右,进入脱硫槽D0102,使原料气中的硫脱至0.2PPm以下,脱硫后的原料气与工艺蒸汽按水碳比约为3.5进行自动比值调节后进入混合气预热盘管,进一步预热到~590℃左右,经上集气总管及上猪尾管,均匀地进入转化管中,在催化剂层中,甲烷与水蒸汽反应生产CO和H2。
甲烷转化所需热量由底部烧咀燃烧燃料混合气提供。
转化气出转化炉的温度约650--850℃,残余甲烷含量约3.0%(干基),进入废热锅炉C0101的管程,C0101产生2.4MPa(A)的饱和蒸汽。
出废热锅炉的转化气温度降至450℃左右,再进入转化冷却器C0102,进一步降至360℃左右,进入中温变换炉。
转化气中含13.3%左右的CO,在催化剂的作用下与水蒸气反应生成CO2和H2,出中变炉的转化气再进入废热锅炉C0101的管程换热后,再经锅炉给水预热器C0103和水冷器C0104被冷至≤40℃,进入变换气分离器F0102分离出工艺冷凝液,工艺气体压力约为1.4MPa(G)。
燃料天然气和变压吸附装置来的尾气分别进入转化炉的分离烧嘴燃烧,向转化炉提供热量≤1100℃。
为回收烟气热量,在转化炉对流段内设有五组换热盘管:(由高温段至低温段)蒸汽-A原料混合气预热器, B 原料气预热器,C烟气废锅,D燃料气预热器,E尾气预热器压力约为1.4的转化工艺气进入变化气缓冲罐,再进入PSA装置。
采用5-1-3P,即(5个吸附塔,1个塔吸附同时3次均降)。
常温中压下吸附,常温常压下解吸的工作方式。
先进的蒸汽转化制氢工艺

先进的蒸汽转化制氢工艺1 前言现在,许多国家对氢气的需求量日益增长。
尤其是炼油厂为了生产更环保的汽柴油产品,必须提高氢气规模以降低硫等杂质的含量。
在炼油厂,制氢装置已经被视为公用工程,要求操作可靠、灵活,装置投资要低。
操作费用是制氢装置一个非常重要的参数。
从图1可以看出,氢气的用途十分广泛。
对于最小规模(在100Nm3/h以下),氢气可以采用电解法制取或者在市场上买瓶装的氢气。
氨/甲醇分解转化制氢适用用规模小、需求时而连续、时而间断的场合,一般用于食品、电子和医药等行业。
对于较大规模(500Nm3/h以上),制氢主要采用以烃为原料,水蒸汽转化或者高温氧化转化工艺。
工艺路线包括原料烃蒸汽转化、变换反应和产品氢净化等几个步骤。
炼油行业是用氢大户,约占50%,规模大多在5000Nm3/h以上,而且对氢气的需求仍在继续增长。
其次是钢铁行业和基础化工产品行业,例如:氨和甲醇。
根据所需用氢量,炼油厂有小的制氢装置,也有处理量大到120000Nm3/h的装置,主要为炼油厂的加氢裂化、加氢脱硫和脱芳构化装置提供了氢源。
蒸汽转化工艺路线的选择取决于装置规模、原料和产品氢气规格。
2 蒸汽转化工艺Topsφe公司50多年来一直致力于蒸汽转化工艺和催化剂的研究开发,并取得了明显的成就,开发出一系列制氢流程。
用户可根据不同工况,选择最佳工艺方案。
在制氢工艺中,蒸汽转化已经占据了主导地位。
表1列出Topsφe公司的蒸汽转化工艺。
绝热预转化工艺可将原料中重烃转化为甲对流式转化炉或者自热式转化(取决工艺方案),能在苛刻条件的操作。
Topsφe管式转化炉设计是基于侧烧模式,这种炉型通过对炉管温度精确控制,确保高合金管材的最优使用,延长炉管的使用寿命。
侧烧式蒸汽转化炉实现其它炉型不能达到的操作条件。
在有氧气来源的场所,自热式转化工艺是有效的选择。
原料和氧气以及水蒸汽在装有专用转化催化剂的反应器中反应,进入自热式反应器的原料可以是烃,也可以是经过预转化的气体;氧气燃烧二段转化工艺,又称二段转化,原料首先在常规转化炉中反应,然后出口的气体进入氧气燃烧转化炉。
天然气制氢工艺流程
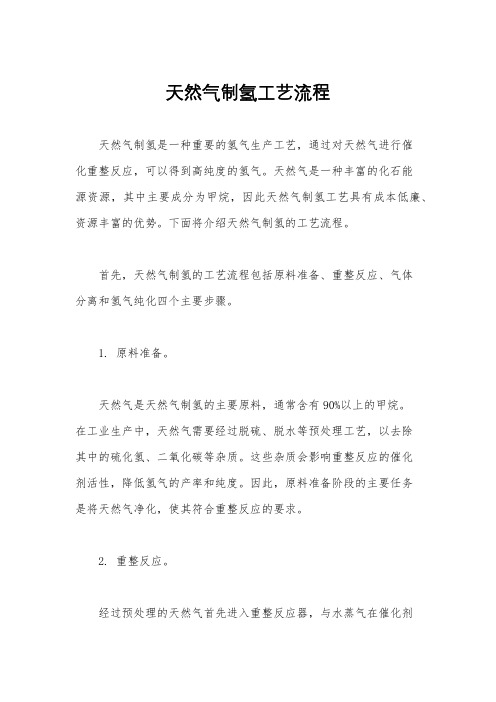
天然气制氢工艺流程天然气制氢是一种重要的氢气生产工艺,通过对天然气进行催化重整反应,可以得到高纯度的氢气。
天然气是一种丰富的化石能源资源,其中主要成分为甲烷,因此天然气制氢工艺具有成本低廉、资源丰富的优势。
下面将介绍天然气制氢的工艺流程。
首先,天然气制氢的工艺流程包括原料准备、重整反应、气体分离和氢气纯化四个主要步骤。
1. 原料准备。
天然气是天然气制氢的主要原料,通常含有90%以上的甲烷。
在工业生产中,天然气需要经过脱硫、脱水等预处理工艺,以去除其中的硫化氢、二氧化碳等杂质。
这些杂质会影响重整反应的催化剂活性,降低氢气的产率和纯度。
因此,原料准备阶段的主要任务是将天然气净化,使其符合重整反应的要求。
2. 重整反应。
经过预处理的天然气首先进入重整反应器,与水蒸气在催化剂的作用下进行重整反应。
重整反应的化学方程式如下所示:CH4 + H2O → CO + 3H2。
CO + H2O → CO2 + H2。
在这个反应过程中,甲烷和水蒸气在高温、高压下发生催化重整反应,生成一氧化碳和氢气。
这是天然气制氢的关键步骤,也是氢气的主要生产途径之一。
3. 气体分离。
经过重整反应的气体混合物中含有大量的CO、CO2和H2,需要进行气体分离以获取高纯度的氢气。
气体分离通常采用吸附分离或膜分离技术,将CO、CO2等副产物从氢气中分离出去,得到高纯度的氢气。
4. 氢气纯化。
得到的高纯度氢气需要经过进一步的纯化处理,以满足工业和化工领域对氢气纯度的要求。
常见的氢气纯化方法包括压力摩尔吸附、膜分离、液体吸附等技术,可以去除氢气中的微量杂质,提高氢气的纯度。
总的来说,天然气制氢工艺流程包括原料准备、重整反应、气体分离和氢气纯化四个主要步骤。
通过这些步骤,可以将天然气中的甲烷转化为高纯度的氢气,满足工业和化工领域对氢气的需求。
天然气制氢工艺具有成本低廉、资源丰富的优势,是一种重要的氢气生产途径。
随着氢能源的发展和应用,天然气制氢工艺将在未来发挥越来越重要的作用。
天然气制3000Nm3H氢工程的物料衡算和热量平衡一段转化炉的主要
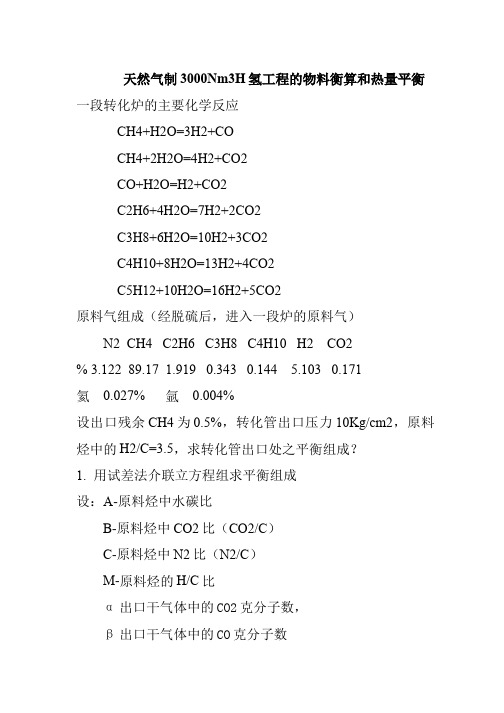
天然气制3000Nm3H氢工程的物料衡算和热量平衡一段转化炉的主要化学反应CH4+H2O=3H2+COCH4+2H2O=4H2+CO2CO+H2O=H2+CO2C2H6+4H2O=7H2+2CO2C3H8+6H2O=10H2+3CO2C4H10+8H2O=13H2+4CO2C5H12+10H2O=16H2+5CO2原料气组成(经脱硫后,进入一段炉的原料气)N2 CH4 C2H6 C3H8 C4H10 H2 CO2% 3.122 89.17 1.919 0.343 0.144 5.103 0.171氦 0.027% 氩 0.004%设出口残余CH4为0.5%,转化管出口压力10Kg/cm2,原料烃中的H2/C=3.5,求转化管出口处之平衡组成?1.用试差法介联立方程组求平衡组成设:A-原料烃中水碳比B-原料烃中CO2比(CO2/C)C-原料烃中N2比(N2/C)M-原料烃的H/C比α出口干气体中的CO2克分子数,β出口干气体中的CO克分子数γ出口干气体中的H2克分子数δ被转化了H2O的克分子数x出口干气体中CH4的百分含量V出口干气体总克分子数以100克分子原料烃为计算基准:按C平衡:M=∑H%/∑C%=4V CH4+4VC2H6+4*V C3H8…/V CH4+2V C2H6+V CO2+……=4*0.8917+4*0.01919+4*0.00343+4*0.00144+0.05103/0.8917+2*0.01919+3*0.00343+4*0.00144+O.OO171=3.5668+0.007676+0.01372+0.00576+0.05103/0.8917+0.03838+0.01029+0.00576+0.00171=3.645/0.94784=3.845M=3.845原料烃中之H2O/气为:A=3.5(0.8917+0.03838+0.01029+0.00576+0.00171)=3.5*0.94784=3.317A=3.3174将上述条件代入式得:按碳平衡式 ∑nCnHm+B=α++XV0.94784(为总碳量)=α+β+0.005V (1)0.005-为出转化炉的剩余CH4量按氧平衡 B+1/2A=α+1/2β+1/2(A-δ)0.00162+1/2*3.3174=α+1/2β+1/2(3.3174-δ)0.00171=α+0.5β-0.5δ (2)按氢平衡A+1/2(∑nCnHm+B)=γ+2XV+(A-δ)3.3174+1/2*(0.8917*4+0.01919*4+0.00343*4+0.00144*4.)=γ+2*0.005*V+(3.31744-δ)3.3174+1/2*(3.567+0.07676+0.0137+0.00576+0.05103)=γ+0.01V+3.31744-δ3.3174+3.645/2=γ+0.01V-δ+3.31741.8225-γ-0.01V=δδ=γ+0.01V-1.8225 (3)V=α+β+γ+0.005V+0.03122 (4)先假设出口温度为850℃,查变換反应平衡常数KP2=0.8552 KP2=CO2*H2/CO*H2O=α*γ/β(A-δ)α*γ/β(3.31744-δ)=0.8552 (5)由(1)减(4)得:0.94784-V=α-α+β-β+0.005V-γ-0.005V-0.0329γ= V-0.981 (6)代(6)入(3)得:δ=V-0.981+0.01V-1.8225δ=1.01V-2.804 (7)由(1)减(2)得:0.94784-0.00171=α-α+β-0.5β+0.5δ+0.005V0.9461=0.5β+0.5δ+0.005V (8)代(7)入(8)得0.9461=0.5β+0.5(1.01V-2.804)+0.005V0.9461=0.5β+0.505V-1.402+0.005V0.5β=0.51V-2.348β=4.696-1.02V (9)代(6)(9)入(4)得V=α+V-0.981+4.696-1.02V+0.005V+0.03122α=1.015V-3.74622 (10)代(6)(7)(9)(10)入(5)得〈1.015V-3.7489〉(V-0.981)/(4.696-1.02V)(3.31744-〈1.01V-2.804〉)=0.85521.015V2-3.7489V-0.996V+3.678/(4.696-1.02V)(〈3.3174〉-〈1.01V-2.804)=0.85521.015V2-4.745V+3.678/ 1.03V2-10.986V+28.744=00.85521.015V2-4.745V+3.678=0.7.63V2-8.14V+21.300.252V2+3.395V-17.622=0V2+13.47V-69.93=0V2+13.47V+(13.47/2)2=69.93+(13.47/2)2(V+13.47/2)2=69.93+(6.735)2V+6.737=√ 69.93+45.36V=10.735-6.735=4.0003α=1.015*4.0003-3.7489=0.3114β=4.696-1.02*4.0003=0.615γ=V-0.981=4.0003-0.981=3.0193δ=1.01V-4.0003=4.0403-4.0003=0.04出口水:H2O=3.3174-δ=3.3174-(1.01V-2.804)=2.081 CH4=0.005N2=0.03122出口湿基总和为:6.45795出口湿转化气组成为:CO2 CO H2 CH4 N2 H2O ∑0.0482 0.0952 0.4675 0.0619 0.0048 0.3222 0.9998出口干基总和0.3114+0.615+3.0193+0.005+0.03122=3.98129 CO2 CO H2 CH4 N2 ∑7.82 15.445 75.8252 0.1256 0.784 99.9998计算甲烷蒸汽转化平衡常数K1值:K1=Vco*V3H2/V CH4*V H2O*P2=0.0952*(0.4675)3 /0.0619*0.3222*(15)2=0.009727/0.019944*225=109.736查出平衡温度为780℃<850℃,计算符合要求。
天然气制氢装置区开工方案
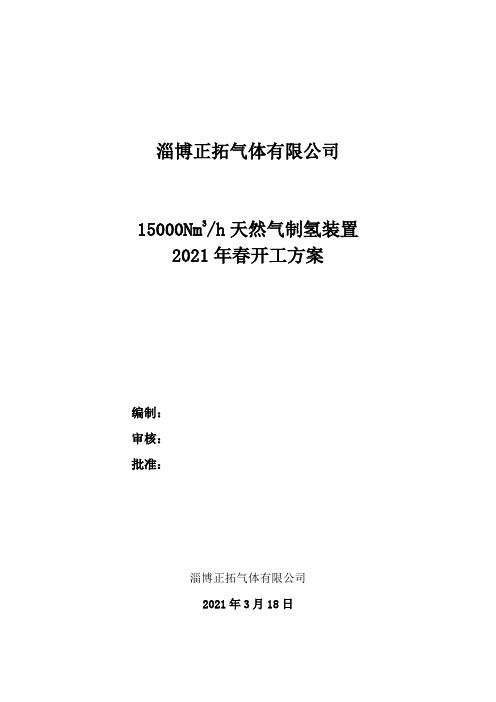
淄博正拓气体有限公司15000Nm3/h天然气制氢装置2021年春开工方案编制:审核:批准:淄博正拓气体有限公司2021年3月18日15000Nm3/h天然气制氢装置2021年春开工方案公司自2020年8月停产至今,因设备设施停运时间较长,复工复产的安全风险相应增加,生产设备、线路管道停产停工后重新启动,容易出现故障,部分从业人员还沉浸在停工的气氛之中,存在思想松懈、注意力不集中等问题,这些都极易引发生产安全事故。
根据上级有关要求,为使我公司复工复产有序开展,确保复工复产期间我公司安全生产,结合公司实际情况,特制定本方案。
本开车方案只适用于15000Nm3/h天然气制氢装置区,不包括LNG 储存设施。
一、成立复工复产领导小组。
1、为保证复工复产期间有计划、有组织、有秩序的安全进行,特成立了以公司主要负责人为组长的领导小组,负责复工复产期间的各项工作。
组长:谭敬副组长:江来组员:段伟明、孙振生、宋帅、杨娟娟、孙启治2、装置开车实行三班两倒制度,相关人员安排如下:一班:孙振生(班长)、宋飞(内操)、安丰硕(外操)二班:宋帅(班长)、阎荣(内操)、李存智(外操)三班:杨娟娟(班长)、孙朋(内操)、崔光晓(外操)工艺操作人员满足复工复产需求。
3、复工期间相关人员的职责:(1)复工复产组长(总经理):谭敬总经理是公司法人代表、是复工复产安全生产的第一责任人,对公司的安全生产主体负全面责任,具体履行以下职责:1、加强复工复产期间安全生产管理,建立建全并落实全员安全生产责任制。
2、组织制定、审批并督促复工复产期间公司的安全生产规章制度和操作规程的落实。
3、保证复工复产期间安全生产投入的有效实施。
4、组织制定并实施复工复产期间本单位安全生产教育和培训工作。
5、组织制定并实施复工复产期间事故应急救援预案。
6、及时、如实报告事故,组织事故抢救。
7、法律、法规、规章规定的其他职责。
(2)复工复产副组长(副总经理):江来副总经理(分管生产)具体履行以下安全职责:1、在总经理的领导下,对公司复工复产期间的生产工作负责。
2万标方制氢工艺管道施工方案

1 工程概况1.1 工程简介我公司承建的润邦化工有限公司2×104Nm3/h制氢装置,位于东明县菜园集乡,距东明石化集团9km,装置占地面积5916平方米,其中南北长116m、东西宽51m。
主要包括炉区、压缩机区、反应区、换热分离区、管带区等的工艺管道安装任务。
2×104Nm3/h制氢装置的主要工艺流程为来自120×104t/a重油催化裂化制烯烃联合装置来的0.6Mpa干气经原料气压缩机升压至3.1Mpa后进入原料预热炉预热至250℃进入脱硫部分,进入脱硫部分的原料气首先进入变温反应器,在其中有机硫加氢转化为硫化氢,烯烃双键断裂,加氢饱和,再进入绝热加氢反应器,将反应不完全的烯烃进一步加氢饱和,然后进入氧化锌脱硫反应器中分两段脱除氯和硫化氢,精制后的原料气和中压蒸汽按1:3.5的混合比进入转化炉管,在炉管催化剂的作用下发生复杂的反应,从而产生氢气,一氧化碳、二氧化碳、和水的平衡混合物,出转化炉的840℃高温混合气经换热冷却至360℃进入中温变换反应器将反应混合气中的CO含量降至3%左右,同时继续生产氢气,中变气经冷却至40℃后进入PSA部分,在PSA系统里,中变气在吸附塔多种吸附剂的依次选择吸附下,一次性除去氢气以外的几乎所有介质,获得纯度大于99.9%的产品氢气,经压力调节系统稳压后送出界区。
管道输送工艺介质主要有:干气、转化气、中变气、氢气、低压蒸汽、中压蒸汽、燃料气、循环水、除盐水、酸性水、导热油、磷酸钠溶液、氮气、仪表风、非净化风等。
1.2 工程特点1.2.1 工期短,施工质量要求高,管理难度大。
从施工准备、过程控制到最终检验,管理的工作量大,难度也大。
1.2.2 本装置的工艺介质主要是干气、转化气、氢气等,属于甲类可燃气体。
1.2.3 管道材质有:20#、20#+Zn、Q345、0Cr18Ni9、15CrMo、15CrMoG。
1.2.4 管道规格最小公称直径DN15mm,最大公称直径DN500mm。
炼油三部各装置低负荷运行生产和检查方案(5)(1)
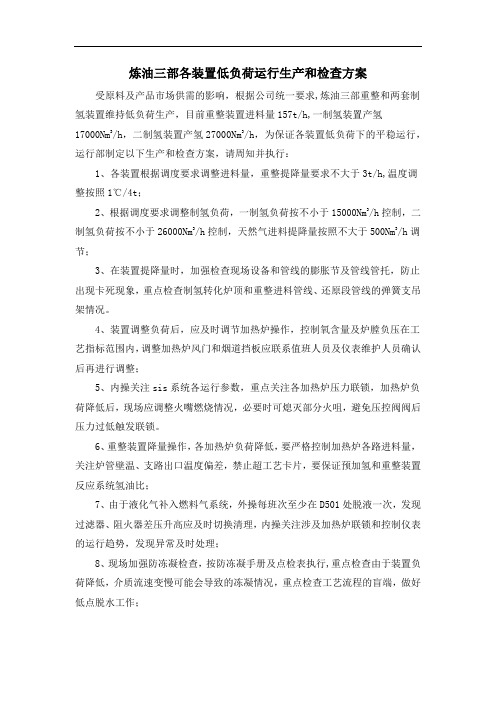
炼油三部各装置低负荷运行生产和检查方案受原料及产品市场供需的影响,根据公司统一要求,炼油三部重整和两套制氢装置维持低负荷生产,目前重整装置进料量157t/h,一制氢装置产氢17000Nm3/h,二制氢装置产氢27000Nm3/h,为保证各装置低负荷下的平稳运行,运行部制定以下生产和检查方案,请周知并执行:1、各装置根据调度要求调整进料量,重整提降量要求不大于3t/h,温度调整按照1℃/4t;2、根据调度要求调整制氢负荷,一制氢负荷按不小于15000Nm3/h控制,二制氢负荷按不小于26000Nm3/h控制,天然气进料提降量按照不大于500Nm3/h调节;3、在装置提降量时,加强检查现场设备和管线的膨胀节及管线管托,防止出现卡死现象,重点检查制氢转化炉顶和重整进料管线、还原段管线的弹簧支吊架情况。
4、装置调整负荷后,应及时调节加热炉操作,控制氧含量及炉膛负压在工艺指标范围内,调整加热炉风门和烟道挡板应联系值班人员及仪表维护人员确认后再进行调整;5、内操关注sis系统各运行参数,重点关注各加热炉压力联锁,加热炉负荷降低后,现场应调整火嘴燃烧情况,必要时可熄灭部分火咀,避免压控阀阀后压力过低触发联锁。
6、重整装置降量操作,各加热炉负荷降低,要严格控制加热炉各路进料量,关注炉管壁温、支路出口温度偏差,禁止超工艺卡片,要保证预加氢和重整装置反应系统氢油比;7、由于液化气补入燃料气系统,外操每班次至少在D501处脱液一次,发现过滤器、阻火器差压升高应及时切换清理,内操关注涉及加热炉联锁和控制仪表的运行趋势,发现异常及时处理;8、现场加强防冻凝检查,按防冻凝手册及点检表执行,重点检查由于装置负荷降低,介质流速变慢可能会导致的冻凝情况,重点检查工艺流程的盲端,做好低点脱水工作;9、外操加强现场巡检,做好夜间闭灯检查工作,关注各大机组、换热器等的运行情况,外操加强检查冷换设备冷热介质压力温度,防止憋压和温度波动造成泄漏,重点检查机泵的运转情况,避免由于负荷降低,泵出口开度变小,造成机泵出口压力升高,造成机械密封泄漏等问题,如果出口流量过低可稍开返回线;苯抽提P404、P405、P407为在运行的磁力泵,需重点关注;10、加强检查K201、K202干气密封系统伴热情况,增加排凝次数,加强重整和两套制氢往复式压缩机入口、级间分液罐液位、排液的检查,增加排凝次数,确保不带液。
- 1、下载文档前请自行甄别文档内容的完整性,平台不提供额外的编辑、内容补充、找答案等附加服务。
- 2、"仅部分预览"的文档,不可在线预览部分如存在完整性等问题,可反馈申请退款(可完整预览的文档不适用该条件!)。
- 3、如文档侵犯您的权益,请联系客服反馈,我们会尽快为您处理(人工客服工作时间:9:00-18:30)。
2200Nm3天然气制氢方案摘要:687-H-040113 2200Nm3/h天然气制氢技术方案1、前言以轻烃为原料制取工业氢,国内外均认为蒸汽转化法为最佳方案。
大型合成氨厂以及炼油厂和石油化工厂的制氢装置,其造气工艺大多为水蒸汽转化法。
经过多年的生产实践,目前已积累了许多成功的工程设计和操作经验。
因此本方案采用水蒸汽转化法造气工艺。
国内外蒸汽转化制氢的净化工艺主要有两种。
即化学净化法和变压吸附净化法(PSA净化法)。
国内早期建设的制氢装置均采用化学净化法。
由于近年PSA技术的进步(多床多次均压,吸附剂性能的改进等),使氢的回收率最高达95%,加之PSA技术的国产化,极大降低了PSA装置的投资以及其操作成本,使该技术在新建制氢装置中占主导地位。
由于装置采用价格较低而且产氢量高的天然气为原料。
选择PSA净化气体,其制氢成本比采用化学净化法的制氢成本低。
同时采用PSA技术具有流程简单、自动化程度高、产品氢纯度高(纯度可达99.999%)等特点,因此,我们推荐用户采用PSA净化技术。
综上所述,以天然气为原料的制氢装置采用水蒸汽转化法加PSA净化工艺。
2、原料天然气组成及产品方案2.1原料气组成本方案以天然气为原料。
其组成如下表:天然气组成名称甲烷乙烷丙烷丁烷戊烷己烷组成(V%)96.97 1.75 0.33 0.1 0.03 0.01 名称氧氮水硫化氢二氧化碳氩、氦、氢组成(V%)0.48 0.24 0.090 进装置温度:常温进装置压力:常压2.2 生产规模2200Nm3/h纯氢2.3产品方案产品压力:~0.3MPa产品H2气体组成组成H2 N2 O2 CH4 CL C2 CO2 S含量,% 98 <1.6 <0.4 <2 <10ppm <10ppm <10ppm <0.1ppm3、工艺流程3.1工艺概述本制氢装置是以天然气为原料,采用蒸汽转化造气工艺制取转化气,回收部分热量后,经变换得粗氢气,粗氢经PSA除去杂质得纯H2。
转化压力~1.9MPa(A)。
3.2基本原理3.2.1天然气脱硫(注:硫含量以管输天然气标准计)本装置选用行之有效的干法脱硫来处理原料气中的硫分,根据原料气中硫组分和含量,在一定温度、压力下,原料气通过氧化锰及氧化锌脱硫剂,将原料气中的有机硫、H2S脱至0.2PPM 以下,以满足蒸汽转化催化剂对硫的要求,其主要反应为:3.2.2烃类的蒸汽转化烃类的蒸汽转化是以水蒸汽为氧化剂,在镍催化剂的作用下将烃类物质转化,得到制取氢气的原料气。
这一过程为吸热过程,故需外供热量,转化所需的热量由转化炉辐射段提供。
在镍催化剂存在下其主要反应如下:3.2.3转化气中CO变换变换工序的作用是使CO在变换催化剂存在条件下,与水蒸汽反应而生成CO2和H2,既降低后工序分离CO负荷,更增加了氢气产量降低了原料消耗。
其反应式如下:以上反应是可逆的放热反应,降低温度或增加H2O蒸汽用量,均有利于变换反应进行。
3.2.4变压吸附提氢吸附是指:当两种相态不同的物质接触时,其中密度较低物质的分子在密度较高的物质表面被富集的现象和过程。
具有吸附作用的物质(一般为密度相对较大的多孔固体)被称为吸附剂,被吸附的物质(一般为密度相对较小的气体)称为吸附质。
吸附按其性质的不同可分为四大类,即:化学吸附、活性吸附、毛细管凝缩和物理吸附。
PSA氢提纯装置中的吸附主要为物理吸附。
物理吸附是指依靠吸附剂与吸附质分子间的分子力(包括范德华力和电磁力)进行的吸附。
其特点是:吸附过程中没有化学反应,吸附过程进行的极快,参与吸附的各相物质间的动态平衡在瞬间即可完成,并且这种吸附是完全可逆的。
变压吸附氢提纯工艺过程之所以得以实现是由于吸附剂在这种物理吸附中所具有的两个性质:一是对不同组分的吸附能力不同,二是吸附质在吸附剂上的吸附容量随吸附质的分压上升而增加,随吸附温度的上升而下降。
利用吸附剂的第一个性质,可实现对含氢气源中杂质组分的优先吸附而使氢气得以提纯;利用吸附剂的第二个性质,可实现吸附剂在低温、高压下吸附而在高温、低压下解吸再生,从而构成吸附剂的吸附与再生循环,达到连续分离提纯氢气的目的。
工业PSA-H2装置所选用的吸附剂都是具有较大比表面积的固体颗粒,主要有:活性氧化铝类、活性炭类、硅胶类和分子筛类。
吸附剂最重要的物理特征包括孔容积、孔径分布、表面积和表面性质等。
不同的吸附剂由于有不同的孔隙大小分布、不同的比表面积和不同的表面性质,因而对混合气体中的各组分具有不同的吸附能力和吸附容量。
正是吸附剂所具有的这种:吸附杂质组分的能力远强于吸附氢气能力的特性,使我们可以将混合气体中的氢气提纯。
吸附剂对各种气体的吸附性能主要是通过实验测定的吸附等温线来评价的。
优良的吸附性能和较大的吸附容量是实现吸附分离的基本条件。
同时,要在工业上实现有效的分离,还必须考虑吸附剂对各组分的分离系数应尽可能大。
所谓分离系数是指:在达到吸附平衡时,(弱吸附组分在吸附床死空间中残余量/弱吸附组分在吸附床中的总量)与(强吸附组分在吸附床死空间中残余量/强吸附组分在吸附床中的总量)之比。
分离系数越大,分离越容易。
一般而言,变压吸附氢提纯装置中的吸附剂分离系数不宜小于3。
另外,在工业变压吸附过程中还应考虑吸附与解吸间的矛盾。
一般而言,吸附越容易则解吸越困难。
如对于C5、C6等强吸附质,就应选择吸附能力相对较弱的吸附剂如硅胶等,以使吸附容量适当而解吸较容易;而对于N2、O2、CO等弱吸附质,就应选择吸附能力相对较强的吸附剂如分子筛、CO专用吸附剂等,以使吸附容量更大、分离系数更高。
此外,在吸附过程中,由于吸附床内压力是不断变化的,因而吸附剂还应有足够的强度和抗磨性。
在变压吸附氢提纯装置常用的几种吸附剂中,活性氧化铝类属于对水有强亲和力的固体,一般采用三水合铝或三水铝矿的热脱水或热活化法制备,主要用于气体的干燥。
硅胶类吸附剂属于一种合成的无定形二氧化硅,它是胶态二氧化硅球形粒子的刚性连续网络,一般是由硅酸钠溶液和无机酸混合来制备的,硅胶不仅对水有极强的亲和力,而且对烃类和CO2等组分也有较强的吸附能力。
活性炭类吸附剂的特点是:其表面所具有的氧化物基团和无机物杂质使表面性质表现为弱极性或无极性,加上活性炭所具有的特别大的内表面积,使得活性炭成为一种能大量吸附多种弱极性和非极性有机分子的广谱耐水型吸附剂。
沸石分子筛类吸附剂是一种含碱土元素的结晶态偏硅铝酸盐,属于强极性吸附剂,有着非常一致的孔径结构,和极强的吸附选择性。
对于组成复杂的气源,在实际应用中常常需要多种吸附剂,按吸附性能依次分层装填组成复合吸附床,才能达到分离所需产品组分的目的。
吸附平衡:吸附平衡是指在一定的温度和压力下,吸附剂与吸附质充分接触,最后吸附质在两相中的分布达到平衡的过程。
在实际的吸附过程中,吸附质分子会不断地碰撞吸附剂表面并被吸附剂表面的分子引力束缚在吸附相中;同时吸附相中的吸附质分子又会不断地从吸附剂分子或其它吸附质分子得到能量,从而克服分子引力离开吸附相;当一定时间内进入吸附相的分子数和离开吸附相的分子数相等时,吸附过程就达到了平衡。
在一定的温度和压力下,对于相同的吸附剂和吸附质,该动态平衡吸附量是一个定值。
在压力高时,由于单位时间内撞击到吸附剂表面的气体分子数多,因而压力越高动态平衡吸附容量也就越大;在温度高时,由于气体分子的动能大,能被吸附剂表面分子引力束缚的分子就少,因而温度越高平衡吸附容量也就越小。
我们用不同温度下的吸附等温线来描述这一关系,如下示意图:从上图的B→C和A→D可以看出:在压力一定时,随着温度的升高吸附容量逐渐减小。
吸附剂的这段特性正是变温吸附(TSA)工艺所利用的特性。
从上图的B→A可以看出:在温度一定时,随着压力的升高吸附容量逐渐增大;变压吸附过程正是利用上图中吸附剂在AB 段的特性来实现吸附与解吸的。
吸附剂在常温高压(即A点)下大量吸附原料气中除氢以外的杂质组分,然后降低杂质的分压(到B点)使各种杂质得以解吸。
在实际应用中一般依据气源的组成、压力及产品要求的不同来选择PSA、TSA或PSA+TSA工艺。
变温吸附法的循环周期长、投资较大,但再生比较彻底,通常用于微量杂质或难解吸杂质的净化;变压吸附的循环周期短,吸附剂利用率高,吸附剂用量相对较少,不需要外加换热设备,被广泛用于大气量多组分气体的分离与纯化。
3.3工艺流程简述3.3.1本装置由脱硫及蒸汽转化工序、变换工序及PSA工序等组成,见工艺流程框图。
天然气制氢工艺流程框图3.3.2脱硫及蒸汽转化由界区外来的天然气进入蒸汽转化炉对流段的原料气预热盘管顶热至一定温度,进入脱硫槽使原料气中的硫脱至0.2PPm以下。
脱硫后的原料气与工艺蒸汽按一定比例进入混合气预热盘管,进一步预热到550~600℃,进入转化管,在催化剂的作用下,天然气中的大部分甲烷等烃类物质与水蒸汽反应生成CO2、CO和H2为主要成份的转化气。
甲烷转化所需热量是由燃烧燃料混合气提供。
转化气出转化炉进入废热锅炉产生~2.3MPa的饱和蒸汽。
出废热锅炉的转化气进入变换工序。
燃料天然气入烧咀前与变压吸附装置来的尾气混合,经预热后进入烧咀燃烧,向转化炉提供热量。
3.3.3变换由转化工序废热锅炉来的转化气进入变换炉,转化气中的CO在变换催化剂的作用下,与水蒸气反应生成以H2和CO2为主的变换气。
出变换炉的气体经废热锅炉、锅炉给水预热器回收热量,再经变换气冷却器降至常温,分离水后送PSA工段。
3.4 PSA提纯H2 本方案变压吸附采用7-2-3/P(7个吸附塔,2个塔同时吸附,3次均压)的工作方式。
每个吸附塔在一次循环中均需经历吸附(A)、一均降(E1D)、二均降(E2D)、三均降(E3D)、顺放(PP)、逆放(D)、冲洗(P)、三均升(E3R)、二均升(E2R)、一均升(E1R)以及终充(FR)等十一个步骤。
七个吸附塔在执行程序的安排上相互错开,构成一个闭路循环,以保证原料连续输入和产品不断输出。
4、主要设备及三剂4.1 主要设备序号名称规格数量,台(组)单重, kg 总重, kg 备注一、天然气转化工序1、反应器类1.1 脱硫槽15CrMoR/15CrMoⅢ21.2 一段转化炉多种 1 附烟道气废热锅炉 1 低合金钢 1 混合气加热器不锈钢 1 原料气预热器低合金钢1 蒸汽过热器碳钢1 烟道气废热锅炉2 碳钢1 废锅水预热器碳钢 1 燃烧气预热器不锈钢 11.3 中变炉低合金钢12、换热器类2.1 废热锅炉碳钢+不锈钢12.2 变换气低压锅炉碳钢+不锈钢12.3 锅炉给水预热器碳钢+不锈钢12.4 中变水冷器不锈钢12.5 回路冷却器碳钢。