多功能分散剂对色母粒性能的影响
盘点分散剂 在涂料中的八大作用

盘点分散剂在涂料中的八大作用以盘点分散剂在涂料中的八大作用为题,本文将对分散剂在涂料中的作用进行详细介绍。
第一,分散作用。
分散剂在涂料中起到了分散固体颜料的作用,使得颜料能够均匀分散在涂料中,防止颜料团聚和沉淀,从而保持涂料的稳定性和均匀性。
第二,增稠作用。
分散剂能够在涂料中形成聚集体,增加涂料的粘度,从而提高涂膜的厚度和光泽度,使得涂料具有更好的覆盖性和遮盖性。
第三,抗沉淀作用。
分散剂通过吸附在颜料表面或形成胶束结构,阻碍颜料颗粒的团聚和沉积,从而有效地防止涂料在储存和使用过程中发生沉淀现象。
第四,乳化作用。
分散剂在涂料中可以形成乳化液,将水性涂料中的颜料和树脂分散在水相中,使得涂料具有良好的乳化稳定性和均匀性。
第五,增溶作用。
分散剂可以与涂料中的树脂相互作用,增加树脂的溶解度,提高涂料的附着力和耐候性,使得涂料具有更好的性能和持久性。
第六,调节pH值作用。
分散剂可以调节涂料的pH值,使得涂料处于最佳的pH范围内,提高涂料的稳定性和使用性能。
第七,防止氧化作用。
分散剂可以与涂料中的氧气发生反应,形成一层保护膜,防止涂料氧化和老化,延长涂料的使用寿命。
第八,抗菌作用。
分散剂中的活性成分可以抑制涂料中的细菌和霉菌的生长繁殖,防止涂料发霉变质,保持涂料的质量和卫生。
分散剂在涂料中具有分散、增稠、抗沉淀、乳化、增溶、调节pH 值、防止氧化和抗菌等八大作用。
它们使得涂料具有更好的稳定性、均匀性、附着力、耐候性、使用性能和卫生性,从而满足人们对涂料的各种需求。
分散剂的应用不仅提高了涂料的质量和性能,也推动了涂料行业的发展和进步。
分散剂防止返粗,增加贮存稳定

分散剂防止返粗,增加贮存稳定一、颜料分散过程颜料的分散过程由润湿、分散、稳定3个步骤组成。
润湿:润湿过程中颜料表面的的空气和水气被树脂溶液所替换,颜料/空气被转换成颜料/树脂溶液。
分散剂尤其是低分子型的润湿分散剂能加快润湿的过程。
分散:分散过程中,主要依靠冲击和剪切力,颜料的团聚态被打碎成较小的微粒,成为分散状态(均匀布)。
稳定:稳定的过程,分散剂用于保持颜料分散状态的稳定,阻止失控的凝,并依据颜料表面所吸附的黏结剂种类和分子结构,促使悬浮液获得稳定状态。
分散剂尤其是高分子分散剂对颜料粒子的稳定起了很大的作用。
二、使用分散剂好处分散剂在涂料生产中发挥了非常重要的作用。
分散体系的稳定能避免诸多的涂料问题及漆膜弊病,如果配方合理,适量地添加分散剂能够有效降低成本,改善涂料性能。
1、提升光泽,增加流平效果有试验表明,完全相同的配方,采用不同的分散剂,得出的漆膜光泽会有明显的差别。
2、防止浮色发花防止浮色发花,是大家所熟知的分散剂的作用之一。
要防止浮色发花,应该选用合适的分散剂,无论是罐内浮色发花还是漆膜的浮色发花,都可以得到改善或消除。
3、提高着色力颜料分散和稳定得更好,其着色力会明显加强。
4、降低粘度,增加颜料载入量采用合适的分散剂,所得的色浆黏度会明显降低。
这样可以增加颜料的载入量,提高生产效率。
5、防止返粗,增加贮存稳定性如果选用不合适的分散剂,色浆发生返粗或因絮凝而产生颜色的变化,都不是大家所希望的。
除树脂体系外,分散剂是影响涂料贮存稳定性的重要因素。
分散不佳的色浆会发生返粗、沉降及着色力下降。
6、增加展色性和颜色饱和度分散剂的这个作用最易为大家所忽略。
有实例表明,采用不同的分散剂分散相同的颜料,其色相及饱和度会有明显差别。
通常来说,分散得越好,饱和度会越高(如果是碳黑,则是分散得越好,L值越低,黑度越高)。
7、增加透明度或遮盖力对于铝粉漆来说,会希望色浆的透明性越高越好。
而针对素色漆,又希望色浆的遮盖力越高越好。
分散剂对有色体系中颜料分散稳定性的影响_谢慕华

淮南工业学院学报
JOU R NA L OF HU AI NA N IN ST IT U T E OF T ECHNO L OG Y
Vol . 22 №. 2 2002
分散剂对有色体系中颜料分散稳定性的影响
谢慕华, 周丽华, 马家举, 江 棂
( 安徽理工大学化学工程系, 安徽 淮南 232001)
现代环境工程技术有限公司。
2. 2 涂料的配制 2. 2. 1 颜料膏的制备 取一定量的环氧豆油丙烯 酸酯, 再加入立索尔大红, 少量稀释剂 T PGDA, 分 散剂, 添加方式按实验需要, 用量按颜料总量计, 搅 拌均匀后, 在三辊研磨机上进行研磨分散, 用刮板 细度计测定细度, 达到要求后出料。 2. 2. 2 涂料的配制 根据实验需要, 称取一定量 的 环 氧 豆 油 丙 烯 酸 酯, 加 入 研 磨 好 的 颜 料 膏, T MP T A , HDDA, T PGDA, 搅拌均匀后, 即得实验 所用有色涂料。 2. 3 涂料的配方
表2分散剂的添加方式与分散体系稳定性的关系添加方式第一种第二种贮存前后细度变化m2028相对沉降率k可知分散剂的添加方式对分散体系稳定性有一定影响第一种添加方式与第二种添加方式相比由于分散剂在研磨分散前加入在研磨分散过程中分散剂能有效地吸附在颜料表面形成的高分子吸附层厚且牢固空间位阻大所以颜料粒子不易聚集返粗分散体系稳定性较好
4 结语
( 1) 在环氧豆油丙烯酸酯和立索尔大红构成 的分散体系中加入分散剂后, 体系的分散稳定性加 强。并且体系稳定性的大小与分散剂的种类、用量、 添加方式和复合皆有关;
( 2) 活性 ABA 型高分子类分散剂比一般的高 分子类分散剂效果好, 复合分散剂比单一分散剂效 果好, 如果分散剂在研磨分散前加入, 用量为最佳, 增稳效果最明显。
分散剂流动性、高光泽、着色力高

分散剂流动性、高光泽、着色力高
分散剂广泛应用于内外墙涂料分为很多中,例如乳胶漆、彩瓦漆、真石漆等,他们体系分为很多种,丙烯酸、聚氨酯、丙烯酸聚氨酯、丁苯、硅丙等,但是内外墙涂料团聚的话,会极大影响涂料的质量,因此需要一款适用于内外墙涂料的分散剂来打破团聚、流动性不够等问题,同时对有机、无机颜料,具有出色的流动性、高光泽、着色力高、可做高固含色浆,具有长期的颜料分散储存稳定性,并且与各种水性体系有良好的相容性,并且此款产品不含APEO,不含有VOC。
涂料分散剂基本原理:
①空间位阻效应
高分子化合物具有较大的分子量,高分子链在介质中充分伸展形成几纳米到几十纳米厚的吸附层,从而产生空间位阻效应。
②静电排斥理论
分散剂通过离子键、共价键、氢键及范德华力等相互作用在农药颗粒界面吸附时,亲水基使颗粒带上负电荷,在分散粒子周围形成扩散双电层,产生电动电势即Zeta电势。
当两个带有相同电荷的分散相离子相互靠近时,扩散双电层重叠而产生的静电排斥迫使带电的分散相离子相互分开,阻止了其合并,使悬浮体系保持其分散稳定性。
③溶剂化链作用
通过其疏水基对农药颗粒产生齿形吸附,亲水基朝水定向排列与水分子可以形成氢键,从而形成亲水性立体保护膜,该保护膜也进一步保证了离子的分散稳定性。
因此,涂料分散剂在整个涂料体系中,是至关重要的重要!。
色母粒配方设计必须遵守的五大载体选择原则
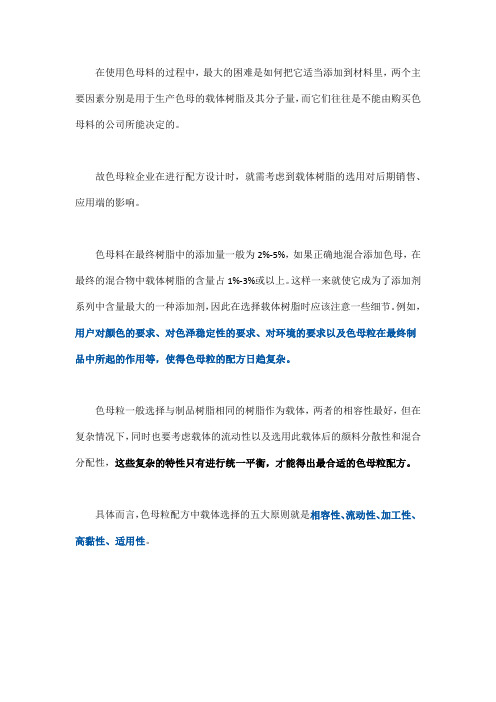
在使用色母料的过程中,最大的困难是如何把它适当添加到材料里,两个主要因素分别是用于生产色母的载体树脂及其分子量,而它们往往是不能由购买色母料的公司所能决定的。
故色母粒企业在进行配方设计时,就需考虑到载体树脂的选用对后期销售、应用端的影响。
色母料在最终树脂中的添加量一般为2%-5%,如果正确地混合添加色母,在最终的混合物中载体树脂的含量占1%-3%或以上。
这样一来就使它成为了添加剂系列中含量最大的一种添加剂,因此在选择载体树脂时应该注意一些细节。
例如,用户对颜色的要求、对色泽稳定性的要求、对环境的要求以及色母粒在最终制品中所起的作用等,使得色母粒的配方日趋复杂。
色母粒一般选择与制品树脂相同的树脂作为载体,两者的相容性最好,但在复杂情况下,同时也要考虑载体的流动性以及选用此载体后的颜料分散性和混合分配性,这些复杂的特性只有进行统一平衡,才能得出最合适的色母粒配方。
具体而言,色母粒配方中载体选择的五大原则就是相容性、流动性、加工性、高黏性、适用性。
相容性所谓相容性是指两种物质彼此相互容纳的能力,按照相似相容原则,色母粒载体树脂与被着色树脂结构相同或相似。
其相容性好。
常规情况下色母粒载体树脂与制品的基体树脂应选择相同类型的聚合物,目的是保证载体树脂与基体树脂具有良好的化学相容性。
例如ABS色母载体可选用AS树脂,PBT可用作PET色母粒的载体。
但如果相同类型树脂之间亦不相容,就会影响着色产品质量,如聚乙烯和聚丙烯虽同属烯烃类,选用聚乙烯为载体的色母用在注塑、吹膜等产品没有问题,但将聚乙烯载体色母用于聚丙烯纺丝会影响可纺性、用于高亮度注塑产品,会在产品上有流痕,也说明了聚乙烯与聚丙烯虽同为烯烃树脂、但两树脂的相容性不是很好。
哪怕是使用聚乙烯蜡为载体的万能色母粒,在面对工程塑料时也不免有所缺陷,表面容易出现“起皮”的现象。
故万能母粒现有的市场规模远远达不到预期的目标。
流动性所谓流动性就是色母载体树脂自身的流动性要好,载体熔体流动速率要高于被着色树脂,如使用与需要着色的塑料相同的聚合物作载体,其分子量应低于着色的塑料(即载体的熔体流动速率大于需着色的塑料的熔体流动速率)。
分散剂的作用分类和选择依据

分散剂的作用分类和选择依据分散剂是一种在液体中将固体颗粒均匀分散的化学物质。
它能够改善固体颗粒与液体之间的相互作用力,使得颗粒之间不容易聚集,从而达到保持颗粒分散状态的目的。
在许多领域,包括化妆品、农药、油墨、食品等的制造过程中,分散剂发挥着重要的作用。
1.稳定分散系统:分散剂可以降低固体颗粒聚集的倾向,使得颗粒能够均匀分散在液体中,避免颗粒沉淀或结块。
2.提高颜料的颜色强度和饱和度:分散剂可以加强颜料与液体的相互作用力,使得颜料的颜色更加鲜艳、饱和。
3.增加涂料和油墨的粘度:分散剂可以改变涂料和油墨的流动性,使其更易于涂覆在物体表面,提高涂层的均匀性和光泽度。
4.提高颗粒的稳定性:分散剂能够防止颗粒在储存和运输过程中的析出和沉淀,保持颗粒的稳定性。
根据分散剂的化学性质和用途,可以将分散剂分为以下几类:1.表面活性剂:表面活性剂是一类分子,在其中一个部分吸附在固体颗粒表面,而另一个部分在液体中溶解,形成胶体颗粒,防止颗粒聚集。
例如,十二烷基硫酸钠(SDS)等。
2.聚合物分散剂:聚合物分散剂是一类高分子化合物,其分子链可以与颗粒表面形成物理或化学结合,阻止颗粒之间的聚集。
例如,聚乙烯醇(PVA)等。
3.离子型分散剂:离子型分散剂通过电荷排斥作用防止颗粒聚集。
根据离子性质,离子型分散剂可分为阳离子型和阴离子型。
例如,亚甲基蓝等。
4.高分子抗缩剂:高分子抗缩剂可以使液体中的固体颗粒均匀分散,防止颗粒在固化过程中发生缩水和聚集。
例如,聚丙烯酰胺(PAM)等。
选择分散剂的依据主要包括以下几个方面:1.要分散的颗粒性质:包括颗粒的大小、形状、表面性质以及颗粒之间的相互作用力等。
不同的颗粒可能对分散剂有不同的选择要求。
2.分散液体的性质:包括液体的粘度、pH值、离子强度等。
分散剂的选择应根据液体的性质进行调整,以确保最佳的分散效果。
3.分散剂的毒性和环境安全性:分散剂应具有较低的毒性,并且在环境中容易降解,以避免对人体和环境造成危害。
色母粒的5个关键点

色母粒是由一种或多种组分的大量颜料或染料与载体树脂等,经严格加工分散工艺制成的高效能和高浓度颜色的树脂着色用混合物。
国内色母粒需求量很大,发展潜力巨大。
因此色母粒生产工艺技术研发很有必要。
下面我们全面了解下色母粒,包含常见分类、基本成分、色母粒生产工艺及设备,最后一起眺望一下色母粒的应用和未来的发展。
一、色母粒分类01 根据用途不同色母粒分为注射色母、吹塑色母、纺丝色母等,各品种又可分为不同等级。
高级注射色母用于化妆品包装盒、玩具、电器外壳及其他高级制品;普通注射色母用于一般日用塑料制品、工业容器等。
高级吹塑色母用于超薄制品吹塑着色。
普通吹塑色母用于一般包装袋、编织袋吹塑着色。
纺丝色母用于纺织纤维纺丝着色,色母颜料颗粒细,浓度高,着色力强,耐热、耐光性好。
低级色母用于制造对颜色品质要求不高的低级产品。
02 根据载体不同分为PE、PP、PVC、PS、ABS、EVA、PC、PET、PEK、酚醛树脂、环氧树脂、丙烯酸树脂、不饱和聚酯树脂、聚氨酯、聚酰胺、氟树脂色母等。
03 根据功能的不同分为抗静电、阻燃、抗老化、抗菌、增白增亮、增透、耐候、消光、珠光、仿大理石纹(流纹)、木纹色母粒等。
04 根据用户的使用情况分为通用色母和专用色母。
低熔点PE色母往往作为通用色母,适用于载体树脂之外的其他树脂着色。
国际上绝大多数正规色母粒企业一般不生产通用色母,通用色母通用范围很狭小,技术指标、经济效益较差。
通用色母在不同塑料中呈现不同颜色,着色效果的预见性差。
通用色母影响产品强度,产品易变形、扭曲,对工程塑料更为明显。
通用色母为了通用,选用较高耐热等级颜料,成本较高,造成浪费。
专用色母在制品加工过程中,具有浓度高、分散性好、清洁等显著优点。
专用色母耐热等级一般与用于制品的塑料是相适应的,正常温度下放心使用,仅在温度超出正常范围和停机时间过长情况下会引起不同程度变色。
05 按颜色的不同分为黑、白、黄、绿、红、橙、棕、蓝、银、金、紫、灰、粉红色母粒等。
色母粒性能质量介绍

色母粒相信大家应该都是知道的,那我再给大家详细介绍一下吧,色母粒是20世纪60年代开发的一种塑料、纤维的着色新产品,它是把颜料超常量均匀的载附于树脂中而制得的聚合物的复合物。
色母粒主要组成为着色剂、载体、分散剂三部分。
【图例-1】色母粒性能质量丙纶是一种纯粹的碳氢化合物,分子链中含有叔碳原子,受热,受光后在叔碳原子处分子易裂解,使丙纶品质变坏,所以要求制成的色母粒在高温纺丝中易于扩散,不损坏纤维品质,不使纤维褪色,有优良的耐光、耐磨、抗溶剂性,经受得起严格的纺丝牵伸。
(1)耐热性色母粒所选用的颜料,最基本的要求经得起聚丙烯纤维生产过程中的温度,保持其性能的稳定。
耐温温度一般要求为270~280℃以上。
(2)分散性色母粒用颜料应分散性优良,而且在色母粒中要分散均匀,且使用的分散剂不会降低丙纶纤维的品质。
否则不能生产出品质好的原液着色纤维,运行也不稳定,在牵伸纤维时易断裂或产生异常纤维。
【图例-2】(3)光亮度丙纶原液着色有多种用途,其中用于床罩基布及针织物,要求明亮的色调。
因有机颜料比较明亮鲜艳,且容易上色,故凡使用于上述用途的需使用有机颜料。
(4)耐光性在光的作用下有些颜料有光敏作用,使着色纤维褪色和脆损,而颜料的耐光性基本上与其化学结构有关,所以在制作色母粒时要充分注意颜料的耐光性,耐光性的颜料需要使用时,可以考虑添加紫外线吸收剂。
(5)稳定性色母粒中使用的颜料,对着色丙纶纤维要有优良的稳定性。
意即着色纤维聚合物经长时间接触热、光或经受高温时颜料不会与纤维反应,形成新的化学基团使聚合物性能绛低。
所以色母粒中应选用尽可能纯的颜料,不含铁、铜、铅等盐的杂质,保证着色丙纶纤维的物理性能优良。
(6)耐水性、耐干洗性、耐油性、着色丙纶纤维制品在使用过和中难免要经过水洗或溶剂干洗,要接触到油剂,特别是用于地毯时,所以其使用的着色剂要有良好的耐水洗性、耐干洗性、耐油性。
【图例-3】寿光市富鑫塑料助剂有限公司是一家生产销售消泡母料、色母料、填充母料的专业公司,价格合理,性价比非常高。
无纺布色母粒介绍
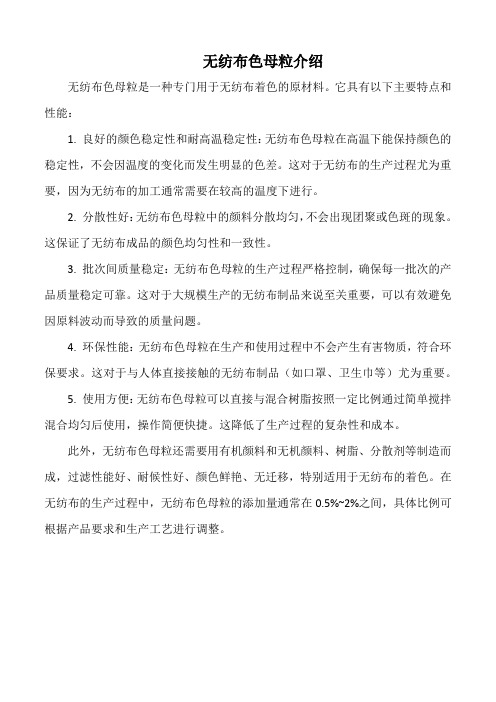
无纺布色母粒介绍
无纺布色母粒是一种专门用于无纺布着色的原材料。
它具有以下主要特点和性能:
1. 良好的颜色稳定性和耐高温稳定性:无纺布色母粒在高温下能保持颜色的稳定性,不会因温度的变化而发生明显的色差。
这对于无纺布的生产过程尤为重要,因为无纺布的加工通常需要在较高的温度下进行。
2. 分散性好:无纺布色母粒中的颜料分散均匀,不会出现团聚或色斑的现象。
这保证了无纺布成品的颜色均匀性和一致性。
3. 批次间质量稳定:无纺布色母粒的生产过程严格控制,确保每一批次的产品质量稳定可靠。
这对于大规模生产的无纺布制品来说至关重要,可以有效避免因原料波动而导致的质量问题。
4. 环保性能:无纺布色母粒在生产和使用过程中不会产生有害物质,符合环保要求。
这对于与人体直接接触的无纺布制品(如口罩、卫生巾等)尤为重要。
5. 使用方便:无纺布色母粒可以直接与混合树脂按照一定比例通过简单搅拌混合均匀后使用,操作简便快捷。
这降低了生产过程的复杂性和成本。
此外,无纺布色母粒还需要用有机颜料和无机颜料、树脂、分散剂等制造而成,过滤性能好、耐候性好、颜色鲜艳、无迁移,特别适用于无纺布的着色。
在无纺布的生产过程中,无纺布色母粒的添加量通常在0.5%~2%之间,具体比例可根据产品要求和生产工艺进行调整。
印染用分散剂种类及作用
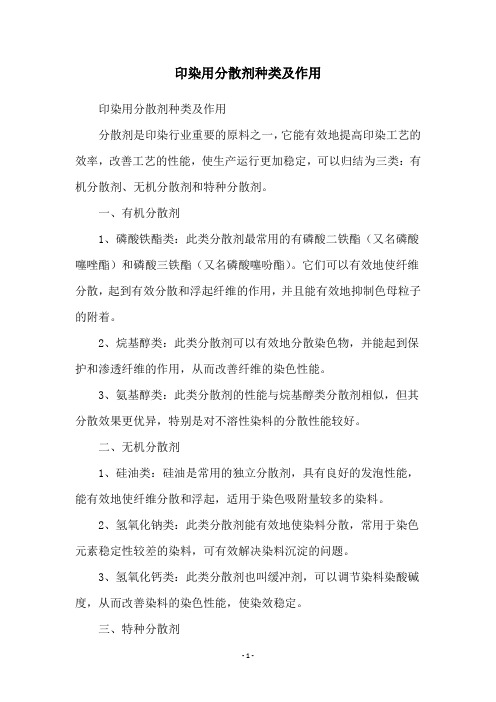
印染用分散剂种类及作用
印染用分散剂种类及作用
分散剂是印染行业重要的原料之一,它能有效地提高印染工艺的效率,改善工艺的性能,使生产运行更加稳定,可以归结为三类:有机分散剂、无机分散剂和特种分散剂。
一、有机分散剂
1、磷酸铁酯类:此类分散剂最常用的有磷酸二铁酯(又名磷酸噻唑酯)和磷酸三铁酯(又名磷酸噻吩酯)。
它们可以有效地使纤维分散,起到有效分散和浮起纤维的作用,并且能有效地抑制色母粒子的附着。
2、烷基醇类:此类分散剂可以有效地分散染色物,并能起到保护和渗透纤维的作用,从而改善纤维的染色性能。
3、氨基醇类:此类分散剂的性能与烷基醇类分散剂相似,但其分散效果更优异,特别是对不溶性染料的分散性能较好。
二、无机分散剂
1、硅油类:硅油是常用的独立分散剂,具有良好的发泡性能,能有效地使纤维分散和浮起,适用于染色吸附量较多的染料。
2、氢氧化钠类:此类分散剂能有效地使染料分散,常用于染色元素稳定性较差的染料,可有效解决染料沉淀的问题。
3、氢氧化钙类:此类分散剂也叫缓冲剂,可以调节染料染酸碱度,从而改善染料的染色性能,使染效稳定。
三、特种分散剂
1、磷酸丙烷酯:此类分散剂具有优异的发泡性能,可以有效地使纤维浮起,特别适用于浅色纤维的深色染色。
2、磷脂类:此类分散剂具有优异的润湿性能,可降低表面张力,使染色物与纤维更容易接触,能大大提高染色效果。
3、聚氧化乙烯类:此类分散剂具有抗染料凝固有效果,有助于减少染色成型过程中的回潮,提高印染工艺的稳定性。
色母粒应用一些常见问题总结和解决办法

色母粒在使用的过程中,有多种不同的加工工艺:注塑、吹膜、挤塑、吹塑、拉丝、流延等工艺,不同工艺加工过程中会出现各种各样的问题,根据御冠新材料总结,这里给出几个常见问题的原因和解决方法。
1、制品中有色点、色纹这种情况一般是色母粒分散性不好,使用分散性更好的色母粒;另一个原因就是机器混合分散效果不佳,调整参数,增加注塑、挤出、吹膜等机器混合分散效果。
2、添加色母粒后,制品变脆了这种原因是因为色母粒与塑料原料之间相容性差,发生了化学反应,这种问题首先检查色母粒添加比例是否过高,色母粒中填充添加量过大,色母粒载体与原树脂载体相容性测试。
更换与树脂材料一样的色母粒载体,降低或者不加填充物,降低色母粒中分散剂蜡的含量。
3、同样的添加量,不同注塑机、吹膜机生产的产品,颜色有差异首先产品颜色差异是有的,但是这种颜色差异不大,通过调整工艺可以控制。
产生这种现象的原因与分散效果有关,不同的机器,加工精度、分散效果是有差别的,而分散效果不一样,直接就导致颜料在制品中的分布不一样,这样制品的颜色效果就有差异。
通过对比产品之间颜色差异,适当增加、降低各机器之间的分散效果,达到一个同步水平,就可以解决这个问题。
4、同种色母粒,同样的添加量,不同的树脂材料,颜色不一样这种现象很普遍,对于老师傅来说,已经熟悉了,但是对于新手,就有些难以理解。
这和树脂材料有关,例如PP、ABS、PA材料,聚丙烯树脂、三元共聚物、聚酰胺树脂,这三种材料的分子分布、分子链长度、空间结构、熔体流动能力都是不一样的,添加同样的色母粒,色母粒在树脂中的分散性,分布性差别就很大,直接就导致颜色差异很大。
5、同种树脂材料,不同牌号,添加同样的色母粒比例,颜色有差异产生这个现象的原因与熔融指数有关,就是树脂的流动能力,同一种树脂,不同牌号,熔融流动性能不一样,这也直接导致颜料在树脂中的分散效果不一样,制品整体颜色效果显示有区别。
6、添加色母粒制备的产品,发生褪色现象产生这种的原因是颜料选择问题。
分散剂对PA6纤维蓝色母粒着色性能的影响

Li Jianping1,Qiao Hui1,Ding Yun1,Wu Yanjie1,Li Shanshan1,Sheng Pinghou2,Jin Jian2
(1. Beijing University of Chemical Technology,Beijing 100029,China ; 2. China Textile Academy,Beijing 100025,China)
(1. 北京化工大学,北京 100029 ; 2. 中国纺织科学研究院,北京 100025)
摘要:以纺丝级聚酰胺 (PA)6 为载体树脂,酞菁蓝 9680,K7090,BGSP–3SD 为颜料,A–C540A,AClyn295A, A–C6A 为分散剂制备纤维用蓝色母粒,并将制得的蓝色母粒用于 PA6 着色。用 Datacolor 测色仪测定材料的着色性 能,用光学显微镜观察颜料的分散性,研究了三种颜料及三种分散剂对 PA6 纤维母粒色彩性能及分散性的影响。结 果表明,三种颜料的着色力度相差不大,其中酞菁蓝 9680 分散相对较好;分散剂 A–C540A 相对更适用于 PA6 纤维 原液着色,当其添加量为 7% 时,着色力达到 119.73%,着色性能提高显著。
色母粒的着色性能差异,并考察了三种不同的分散 剂对颜料的着色力度及分散性的影响。 1 实验部分 1.1 原材料
影响涂料颜填料着色力的因素及分散剂的作用

影响涂料颜填料着色力的因素及分散剂的作用
颜料的着色力是某种原料和另一种颜料混合后形成颜色强弱的能力。
涂料中颜料的着色力是以其本身的色彩来影响整个混合物颜色的能力。
着色力越好、颜料用量越少,成本越低。
影响颜料着色力的因素
着色力与颜料本身性质有关,也与其粒径大小有关。
一般有机颜料比无机颜料着色力好。
颜料粒径越小,着
色力越好,颜料的分散性好,同样的着色力也越好。
着色力与遮盖力无关,透明颜料的遮盖力差,而着色力可能很好。
不管是粒径大小、无机或有机颜料,由于受布朗作用力的影响,都会导致颜料颗粒团聚,这样子反而影响颜料颗粒的着色力,而且还会影响遮盖力、流平性能其它性能,因此需要在涂料体系中加入合适的颜料分散剂来对消除颜料颗粒间的作用力,保证颜料能均匀分散在涂料体系中,同时配备相信的润湿流平剂,保证颜填料涂覆过程中的流平性能,充分发挥颜填料在涂料体系中的作用。
色母粒用量标准(一)

色母粒用量标准(一)色母粒用量标准在塑料制品的生产中,色母粒被广泛应用于各类颜色的生产中,那么在使用色母粒时,我们需要注意什么呢?色母粒的用途色母粒是一种专门用于调色的粒状物料,用于塑料、橡胶等材料的染色。
在塑料制品生产中,通常会通过加入色母粒达到调整色彩、强度等目的。
色母粒的用量色母粒的用量是需要掌握的重要指标。
在用色母粒进行塑料制品染色时,如果添加不合适的数量,容易造成色差、瑕疵、变形等问题,在使用过程中也可能会导致效果不佳、浪费资源等问题。
因此,在生产过程中,需要根据材料的不同、染色要求的不同、实际效果的不同等多种因素,来确定色母粒的用量。
色母粒用量标准以下是基于染色效果、成本等多方面因素,所推荐的若干色母粒用量标准供参考:•普通颜色:15-25%•高品质颜色:20-30%•特殊颜色:25-35%需要注意的是,具体的色母粒用量还会受到多种因素(如材料特性、塑料制品的目的等)的影响,因此还需要根据生产实际情况,制定出更准确的用量标准。
小结色母粒的用量是影响生产效果的重要因素。
在使用色母粒时,需要遵循科学、合理、标准化的原则,根据实际情况进行适当的调整,以达到最佳的染色效果。
色母粒用量调整生产过程中,如果出现色差、瑕疵等问题,就需要对色母粒用量进行调整。
具体方法如下:1.首先需要确定问题的具体表现,比如色差是偏红还是偏绿,瑕疵是云纹还是气泡等。
2.然后根据问题类型,调整色母粒的用量。
对于色差问题,可以适当增加或减少色母粒用量,对于瑕疵问题,可以适当加入其他助剂等。
3.在进行调整时,需要及时进行检测,以验证调整效果。
如果问题得到解决,就可以按照调整后的用量进行生产。
常见问题及解决方法在使用色母粒时,还可能会出现以下常见问题:1.色差问题。
针对此类问题,可以根据颜色偏差的具体情况增加或减少色母粒用量,或者尝试调整其它辅助剂的使用量。
2.称量准确性问题。
在使用色母粒前,需要对色母粒的称量准确性进行检测,并校准读数误差。
如何提高着色母粒的性能-中国塑料技术网
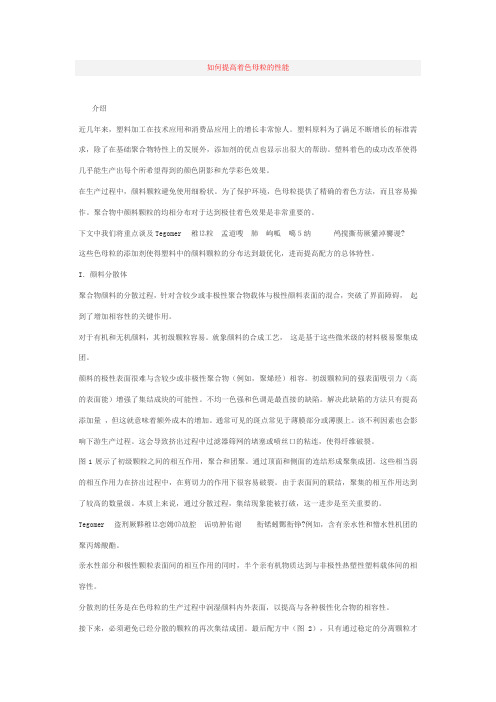
介绍近几年来,塑料加工在技术应用和消费品应用上的增长非常惊人。
塑料原料为了满足不断增长的标准需求,除了在基础聚合物特性上的发展外,添加剂的优点也显示出很大的帮助。
塑料着色的成功改革使得几乎能生产出每个所希望得到的颜色阴影和光学彩色效果。
在生产过程中,颜料颗粒避免使用细粉状。
为了保护环境,色母粒提供了精确的着色方法,而且容易操作。
聚合物中颜料颗粒的均相分布对于达到极佳着色效果是非常重要的。
下文中我们将重点谈及Tegomer稚⒓粒孟道嗖肺岣呱噶5纳鸬搅撕芴厥獾淖饔谩?这些色母粒的添加剂使得塑料中的颜料颗粒的分布达到最优化,进而提高配方的总体特性。
I.颜料分散体聚合物颜料的分散过程,针对含较少或非极性聚合物载体与极性颜料表面的混合,突破了界面障碍,起到了增加相容性的关键作用。
对于有机和无机颜料,其初级颗粒容易。
就象颜料的合成工艺,这是基于这些微米级的材料极易聚集成团。
颜料的极性表面很难与含较少或非极性聚合物(例如,聚烯烃)相容。
初级颗粒间的强表面吸引力(高的表面能)增强了集结成块的可能性。
不均一色强和色调是最直接的缺陷。
解决此缺陷的方法只有提高添加量,但这就意味着额外成本的增加。
通常可见的斑点常见于薄膜部分或薄膜上。
该不利因素也会影响下游生产过程。
这会导致挤出过程中过滤器筛网的堵塞或喷丝口的粘连,使得纤维破裂。
图1展示了初级颗粒之间的相互作用,聚合和团聚。
通过顶面和侧面的连结形成聚集成团。
这些相当弱的相互作用力在挤出过程中,在剪切力的作用下很容易破裂。
由于表面间的联结,聚集的相互作用达到了较高的数量级。
本质上来说,通过分散过程,集结现象能被打破,这一进步是至关重要的。
Tegomer盗刑厥夥稚⒓恋姆⒄故腔诟叻肿佑谢衔锘蚓酆衔铮?例如,含有亲水性和憎水性机团的聚丙烯酸酯。
亲水性部分和极性颗粒表面间的相互作用的同时,半个亲有机物质达到与非极性热塑性塑料载体间的相容性。
分散剂的任务是在色母粒的生产过程中润湿颜料内外表面,以提高与各种极性化合物的相容性。
吹膜色母粒选择注意事项
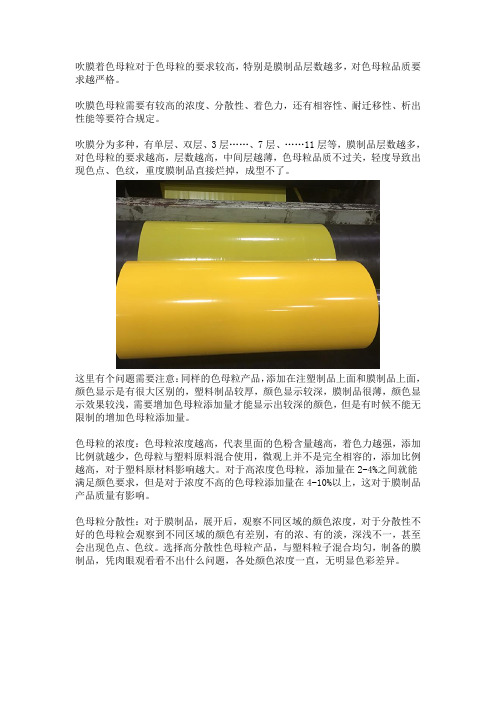
吹膜着色母粒对于色母粒的要求较高,特别是膜制品层数越多,对色母粒品质要求越严格。
吹膜色母粒需要有较高的浓度、分散性、着色力,还有相容性、耐迁移性、析出性能等要符合规定。
吹膜分为多种,有单层、双层、3层……、7层、……11层等,膜制品层数越多,对色母粒的要求越高,层数越高,中间层越薄,色母粒品质不过关,轻度导致出现色点、色纹,重度膜制品直接烂掉,成型不了。
这里有个问题需要注意:同样的色母粒产品,添加在注塑制品上面和膜制品上面,颜色显示是有很大区别的,塑料制品较厚,颜色显示较深,膜制品很薄,颜色显示效果较浅,需要增加色母粒添加量才能显示出较深的颜色,但是有时候不能无限制的增加色母粒添加量。
色母粒的浓度:色母粒浓度越高,代表里面的色粉含量越高,着色力越强,添加比例就越少,色母粒与塑料原料混合使用,微观上并不是完全相容的,添加比例越高,对于塑料原材料影响越大。
对于高浓度色母粒,添加量在2-4%之间就能满足颜色要求,但是对于浓度不高的色母粒添加量在4-10%以上,这对于膜制品产品质量有影响。
色母粒分散性:对于膜制品,展开后,观察不同区域的颜色浓度,对于分散性不好的色母粒会观察到不同区域的颜色有差别,有的浓、有的淡,深浅不一,甚至会出现色点、色纹。
选择高分散性色母粒产品,与塑料粒子混合均匀,制备的膜制品,凭肉眼观看看不出什么问题,各处颜色浓度一直,无明显色彩差异。
色母粒着色力:同样的色母粒浓度,对于着色力强的颜料,着色完成后,膜制品颜色更深,这样就可以少添加一些色母粒,节省添加量。
根据御冠新材料资料,析出性:色母粒中添加了分散剂,这种分散剂作用是用于分散色粉,通常使用低分子蜡作为分散剂,这种蜡在产品中会逐渐析出至表面,使得膜制品表面具有一种润滑的效果,当膜制品需要印刷、封口的时候,这种析出的蜡就会产生影响。
因此当有印刷、封口等膜制品加工工艺的时候,要选择低析出的色母粒。
分散剂用量对聚合的影响

分散剂用量对聚合的影响分散剂是一种在聚合过程中用于分散或稳定颗粒的物质。
它可以通过增加颗粒间的排斥力或降低颗粒的表面能来防止颗粒聚集。
在聚合反应中,分散剂的使用量会对聚合过程和聚合产物的性质产生影响。
分散剂的使用量会影响颗粒的分散程度。
在聚合过程中,当颗粒开始形成时,它们往往会相互吸引,导致颗粒聚集。
适量的分散剂可以增加颗粒间的排斥力,减少颗粒的相互吸引力,从而促进颗粒的分散。
然而,如果分散剂使用过量,它可能会导致分散剂与颗粒之间的相互作用过强,从而使颗粒难以分散。
分散剂的使用量还会对聚合反应的速率和产物的分子量分布产生影响。
在聚合反应中,分散剂可以通过调节反应物之间的扩散速率来影响聚合速率。
适量的分散剂可以增加反应物的扩散速率,促进聚合反应的进行。
然而,如果分散剂使用过量,它可能会形成一层过厚的界面层,阻碍反应物的扩散,从而降低聚合反应的速率。
分散剂的使用量还会影响聚合产物的分子量分布。
在聚合反应中,分散剂的存在可以防止聚合产物的聚集,从而使聚合产物的分子量分布更加均匀。
适量的分散剂可以提高聚合产物的分子量均一性,而过量的分散剂可能会导致聚合产物的分子量分布变宽。
分散剂的使用量还会对聚合产物的形貌和性质产生影响。
在聚合过程中,分散剂可以在颗粒表面形成一层保护膜,防止颗粒的聚集和团聚。
这样可以形成具有均匀形貌和较小颗粒尺寸的聚合产物。
此外,分散剂的选择还会影响聚合产物的性质,例如颜色、透明度、抗氧化性等。
分散剂的使用量对聚合过程和聚合产物的性质有重要影响。
适量的分散剂可以促进颗粒的分散、调节聚合反应的速率、提高聚合产物的分子量均一性和改善聚合产物的形貌和性质。
然而,过量的分散剂可能会导致颗粒难以分散、聚合反应速率降低、聚合产物的分子量分布变宽等问题。
因此,在聚合过程中,需要合理选择和控制分散剂的使用量,以达到理想的聚合效果。
CH系列超分散剂在塑料中的应用

CH系列超分散剂在塑料中的应用陈腊琼(上海三正高分子材料有限公司上海 200237)摘要:在介绍CH系列超分散剂的发展概况、结构特征和作用机理的基础上,重点介绍了塑料用超分散剂的主要品种及其在塑料加工中的使用方法和使用效果。
关键词:超分散剂聚合物加工色母粒随着我国塑料制品工业的发展,塑料加工助剂的发展前景看好。
以色母粒为例,我国的总需求量已由1995年的4万吨增至2000年的 6万吨,相应的有机颜料需求量也大幅度增长。
目前,我国有机颜料品种有100多个,年产量约占世界有机颜料总产量的25%,可惜的是,在我国有机颜料100多个品种中,高档颜料只占生产总量的0.5%。
由于高档颜料的限制,国内塑料加工业使用的红、黄等色母粒多靠进口。
因此必须注重改变颜料产品结构,同时发展高效、多功能、复合型或具有特殊性能的专用型助剂,以便提高色母粒加工技术和产品质量,增加塑料产品在国际和国内市场的竞争力。
在强烈的市场需求推动下,国内有关专家对新型颜料助剂产生了浓厚的兴趣,90年代初国内文献中出现了对颜料用超分散剂的介绍性报导,同一时期国外产品开始进军中国市场,而国内专家也开始了该类产品的研制工作。
近年来,上海三正高分子材料有限公司在充分吸取国内外研究成果的基础上成功地开发了CH系列超分散剂,并在有机颜料、油漆等领域中获得了广泛应用,为这些行业产品品质的提升作出了贡献。
随着CH系列超分散剂研究与应用的发展,CH系列超分散剂正逐渐地影响到更广泛的领域,对塑料的成型加工及塑料产品品质的提升也带来了越来越直接的影响。
一、CH系列超分散剂的分子结构特征及作用机理CH系列超分散剂是一类特殊的聚合物型润湿分散剂,目前有四十多个品种,用于塑料加工的超分散剂主要有CH-1A,CH-2C,CH-6,CH-11四种。
CH系列超分散剂的分子结构可分为两个部分,一部分为锚固基团,其主要作用是将超分散剂紧密吸附于颜料(填料)表面,防止超分散剂脱附;另一部分为溶剂化链,其主要作用是在颜料(填料)表面形成一定厚度的保护层。
光刻胶颜料分散液作用

光刻胶颜料分散液作用
光刻胶颜料分散液是一种常见的光刻胶材料,它在制备过程中的作用非常重要。
其作用主要体现在以下几个方面:
1. 促进颜料分散:光刻胶颜料分散液中含有一定量的分散剂,可以有效地分散颜料,并使其均匀地分布在光刻胶中,从而提高光刻胶的成膜性和显影性。
2. 保护颜料:在光刻胶制备过程中,颜料容易受到氧化或者其它化学反应的影响,导致其活性降低或者失去作用。
光刻胶颜料分散液中的分散剂可以保护颜料,使其活性得到保持,从而提高光刻胶的质量和稳定性。
3. 调节粘度:光刻胶颜料分散液中的分散剂可以调节颜料的粘度,从而改变光刻胶的流动性能,使其更易于制备和加工。
4. 提高成像质量:光刻胶颜料分散液中的颜料可以有效地吸收光线,从而提高光刻胶的敏感度和成像质量,使其更加适合微纳加工领域的应用。
总之,光刻胶颜料分散液的作用非常重要,它可以为光刻胶的制备和应用提供必要的支持和保障,使其更加适合各种微纳加工领域的应用。
- 1 -。
- 1、下载文档前请自行甄别文档内容的完整性,平台不提供额外的编辑、内容补充、找答案等附加服务。
- 2、"仅部分预览"的文档,不可在线预览部分如存在完整性等问题,可反馈申请退款(可完整预览的文档不适用该条件!)。
- 3、如文档侵犯您的权益,请联系客服反馈,我们会尽快为您处理(人工客服工作时间:9:00-18:30)。
工 程 塑 料 应 用ENGINEERING PLASTICS APPLICATION第44卷,第7期2016年7月V ol.44,No.7Jul. 2016128doi:10.3969/j.issn.1001-3539.2016.07.025多功能分散剂对色母粒性能的影响*冼彩虹1,杨婉琼1,刘婉培1,杨雄1,黎泽顺2,刘鹏2,阳范文1(1.广州医科大学,广州 511436; 2.广东波斯科技股份有限公司,广州 510530)摘要:研究了分散剂YY–5023及其与聚乙烯(PE)蜡复配对色母粒中酞青蓝分散性的影响。
结果表明,随着分散剂用量的增加,色母粒的熔体流动速率(MFR)增大,平衡扭矩降低,达到最大扭矩所需时间延长;当YY–5023用量为2%和4%时,平衡扭矩分别为5.3 N ·m 和4.4 N ·m ,比未添加分散剂时的平衡扭矩分别下降28.4%和40.5%,达到最大扭矩的时间分别为53.5 s 和57.3 s ;复合分散剂(YY-5023与PE 蜡配比为1∶1)用量为2%和4%时,平衡扭矩分别为5.7 N ·m 和5.1 N ·m ,比未添加分散剂时的平衡扭矩分别下降23.0%和31.1%,达到最大扭矩的时间分别为48.5 s 和52.3 s 。
当复合分散剂用量为2%时,色母粒中酞青蓝的分散效果最好,L *值、a *值、b *值分别为34.19,-9.82,-31.82,低密度聚乙烯薄膜表面的色点和晶点数目小于3个。
关键词:多功能分散剂;酞青蓝;色母粒中图分类号:TB322,TQ625 文献标识码:A 文章编号:1001-3539(2016)07-0128-05Effects of Multifunctional Dispersant on Masterbatch PropertiesXian Caihong 1, Yang Wanqiong 1, Liu Wanpei 1, Yang Xiong 1, Li Zeshun 2, Liu Peng 2, Yang Fanwen 1(1. Guangzhou Medical University , Guangzhou 511436, China ;2. Guangdong Bosi Science and Technology Co.,Ltd., Guangzhou 510530, China)Abstract : The dispersion properties of phthalocyanine blue in color masterbatch were studied using YY -5023 and its complex with polyethylene wax as dispersants. The results show that with the increase of dispersant content ,the melt flow rate of color mas-terbatch increases ,the balance torque decreases ,the time reached maximum torque increases. The balance torque of the color mas-terbatch with the content of YY -5023 in an amount of 2% and 4% respectively are 5.3 N ·m and 4.4 N ·m ,which respectively de-crease 28.4% and 40.5% compared with the color masterbatch without dispersant ,the maximum torque time are 53.5 s and 57.3 s. The balance torque of the color masterbatch with complex dispersant (YY -5023 and polyethylene wax ratio of 1∶1) in an amount of 2% and 4% are 5.7 N ·m and 5.1 N ·m ,which respectively decrease 23.0% and 31.1% compared with the color masterbatch with-out dispersant ,the maximum torque time are 48.5 s and 52.3 s. With 2% complex dispersant content ,the dispersion of phthalocya-nine blue in the masterbatch is the best, L * value ,a * value and b * value of the film are 34.19, -9.82,-31.82 respectively ,the number of color point and gel point of the film is less than three.Keywords :multifunctional dispersant ;phthalocyanine blue ;color masterbatch酞青蓝又名铜酞青、海利勤蓝B 、颜料兰、花青蓝宫、蒙纳斯蓝B 等,属于酞青颜料系列,分子式为C 32H 16CuN 8,其结晶性高、稳定性好、着色力强,透明性良好,不溶于大多数溶剂,加热到500℃时不升华和不发生化学变化,具有鲜艳的蓝色,现已成为有机颜料中产量最大、用途最广的蓝色品种之一[1–3]。
酞青蓝不仅用作着色剂,而且还用于有机半导体、光电导、感光性树脂的增感剂等领域。
然而,酞青蓝用于塑料着色时,其着色力与分散状况关系密切[4–5]。
分散良好时,显示出优异的着色力和稳定的着色性能;分散不良时,着色力较低,注塑制品表面会出现色点,薄膜产品会出现大量色点或晶点,表面粗糙,影响使用性能[6–7]。
因此,如何解决色母粒中酞青蓝的分散性能是获得良好着色效果的关键。
现有的分散剂如硬脂酸锌、聚乙烯蜡、乙撑双硬脂酸酰胺等对酞青蓝的分散效果都不太理想。
YY–5023是广州源泰合成材料有限公司针对酞青蓝、酞青绿、炭黑等难分散颜料*广东省科技厅产学研项目(2013B090500034),广州医科大学2014-2016年度本科教学质量与教学改革——卓越人才培养资助项目(2014012)联系人:阳范文,教授,博士,主要从事医用高分子材料改性及功能化研究收稿日期:2016-05-03129冼彩虹,等:多功能分散剂对色母粒性能的影响专门研发的一种多功能分散剂,分子结构中含有反应活性基团如—OH、—COOH等和极性基团如—CONH—、—COO—等,具有润滑、偶联、分散和增容等多种功能分散剂[8–9]。
笔者将YY–5023多功能分散剂应用于色母粒中酞青蓝色粉的分散,系统研究其与聚乙烯蜡复配对色母粒的着色力、分散性能和流变性能的影响,为酞青蓝的分散和着色提供理论参考。
1 实验部分1.1 主要原材料低密度聚乙烯(PE–LD):2420H,茂名石化公司;酞青蓝:BGS,15∶3,市售;多功能分散剂:YY–5023,广州源泰合成材料有限公司;抗氧剂:1010,168,北京天罡助剂有限责任公司;聚乙烯(PE)蜡:BASF公司。
1.2 主要设备与仪器双螺杆挤出机:SHT–40型,南京橡塑机械厂有限公司;傅立叶变换红外光谱(FTIR)仪:TENSOR27型,德国Bruker公司;转矩流变仪:ROTI–55/20型,广州普同实验分析设备有限公司;光学显微镜:ZOOM–700型,上海天省仪器有限公司;电脑测色仪:Coloreye 7000A型,日本X-rite 公司;吹膜机:2030型,浙江华瑞机械有限公司。
1.3 试样制备将PE–LD、酞青蓝、抗氧剂和YY–5023等原料按照表1配方进行称量,混合3~5 min,然后采用双螺杆挤出机进行熔融造粒制得色母粒。
挤出机的温度设定为:下料口120℃,其它区160℃,模头150℃,螺杆转速400 r/min。
表1 色母粒配方设计材料编号1#2#3#4#5#6#7#8#9#PE–LD71.671.170.669.667.671.170.669.667.6酞青蓝181818181818181818 YY–502300.51240.250.512 PE蜡0.250.512抗氧剂10100.20.20.20.20.20.20.20.20.2抗氧剂1680.20.20.20.20.20.20.20.20.2在PE–LD中添加质量分数3%的上述色母粒,混合均匀后采用吹膜机在160℃温度下吹膜厚度为30 μum左右的薄膜样品。
1.4 性能测试熔体流动速率(MFR)按ISO 1133–2011测试,温度190℃,载荷2.16 kg。
流变性能测试:采用转矩流变仪在160℃、转速60 r/min条件下测试其扭矩–时间曲线,根据平衡扭矩、达到最大扭矩所需时间评价其流变性能。
色点和分散性能按照QB/T 1648–1992测试,采用光学显微镜放大45倍进行观察。
着色力按照GB/T 7921–2008测试,采用色差仪测试色板的L*(明度)、a*(色度)、b*(色度)进行表征。
2 结果与讨论2.1 分散剂用量对色母粒MFR的影响单独用YY–5023作为分散剂以及将YY–5023与PE蜡按照1∶1比例进行复配作为复合分散剂,不同分散剂用量下色母粒的MFR如图1和图2所示。
4648505254YY 5023⩔䛻喒%MFR喒[ge(1min)1]图1 不同YY–5023用量下色母粒的MFR4648505254⩔䛻喒%MFR喒[ge(1min)1]图2 不同复合分散剂用量下色母粒的MFR单独采用YY–5023作为分散剂时,随着YY–5023含量的增加,色母粒的MFR呈逐渐增大的趋势;未添加YY–5023时,色母粒的MFR为46 g/(10 min),当YY–5023用量为2%时,MFR达到49.5 g/(10 min);当YY–5023用量为4%时,MFR达到55 g/(10 min)。
将YY–5023与PE蜡工程塑料应用2016年,第44卷,第7期130按照1∶1比例进行复合作为复合分散剂时,MFR也是随复合分散剂用量的增加而增大,当复合分散剂用量为2%时,MFR达到49 g/(10 min);当复合分散剂用量为4%时,MFR达到53.7 g/(10 min)。