Appendix IDS 100 RIE Install
elan-sc-100-quick-install-说明书

Quick Install Guide EL-SC-100QUICK INSTALL GUIDEThe EL-SC-100 Controller may be used as a standalone system controlleror as an Extender to any gSC OR SC controller or running g!6.6 or greater. Please check the ELAN Training Guide for EL-SC-100 control capabilities. The ELAN Training Guide contains valuable hardware and software reference documentation and is considered an important supplement to this document. Make sure you have the latest version by visiting the ELAN Dealer website at and follow the Dealer Resources link.Included in the box:• EL-SC-100 Controller• 12vDC Power SupplyImportant Safety Instructions:1. Read, understand and follow ALL safety and installation instructionsincluded in this manual. Failure to follow the included documentation may damage the product and will void manufacturer’s warranty.2. Follow ALL installation guidelines included with the product. Installationof the product in high humidity environments, in close proximity to heat sources and /or non-recommended locations will impede, interfere and/or damage the intended operation of the product3. Only use attachments and accessories which have been specified for useby the manufacturer.4. The use of abrasive, liquid or solvent based cleaning fluids will damagethe product. Please refer and follow all Product Care instructions included with the product.5. Product Servicing may only be completed by authorized or certifiedservice centers and personnel. For a complete list of product servicing options, please follow instructions included in the product documentation and /or contact original manufacturer for details.2EL-SC-100FCC and IC Information:This Class B digital apparatus complies with Part 15 of the FCC rules and with Canadian ICES-003 and RSS-247.Operation is subject to the following two conditions:1. This device may not cause interference and2. This device must accept any interference, including interference that maycause undesired operation of the device.Cet appareil numérique de classe B est conforme aux normes canadiennes ICES-003 et RSS-247. Son fonctionnement est soumis aux deux conditions suivantes : (1) cet appareil ne doit pas causer d’interférence et (2) cet appareil doit accepter toute interférence, notamment les interférencesqui peuvent affecter son fonctionnement.Warning:Changes or modifications to this unit not expressly approved by the party responsible for compliance could void the user’s authority to operate the equipment.FCC and IC Radiation Exposure Statement:This equipment complies with FCC radiation exposure limits set forth foran uncontrolled environment and meets the exemption from the routine evaluation limits in section 2.5 of RSS 102.1. This Transmitter must not be co-located or operating in conjunction withany other antenna or transmitter.2. This equipment complies with FCC RF radiation exposure limits setforth for an uncontrolled environment. This equipment should beinstalled and operated with a minimum distance of 20 centimeters from user and bystanders.3QUICK INSTALL GUIDE4Warning:The device meets the exemption from the routine evaluation limits in section 2.5 of RSS 102, and users can obtain Canadian information on RF exposure and compliance from the Canadian Representative Product Solutions Group at Tel: (519) 763-4538.FEDERAL COMMUNICATIONS COMMISSION INTERFERENCE STATEMENT:This equipment has been tested and found to comply with the limits for a Class B digital device, pursuant to part 15 of the FCC Rules.These limits are designed to provide reasonable protection against harmful interference in a residential installation. This equipment generates, uses and can radiate radio frequency energy and, if not installed and used in accordance with the instructions, may cause harmful interference to radio communications.However, there is no guarantee that interference will not occur in a particular installation. If this equipment does cause harmful interference to radio or television reception, which can be determined by turning the equipment off and on, the user is encouraged to try to correct the interference by one or more of the following measures:• Reorient or relocate the receiving antenna.• Increase the separation between the equipment and receiver.• Connect the equipment into an outlet on a circuit differentfrom that to which the receiver is connected.• Consult the dealer or an experienced radio/ TV technician for help.EL-SC-100 La puissance de sortie émise par l’appareil de sans fil est inférieure à la limite‘exposition aux fréquences radio d’Industry Canada (IC). Utilisez l’appareil de sans fil de façon à minimiser les contacts humains lors du fonctionnement normal.Ce périphérique a également été évalué et démontré conforme aux limitesd’exposition aux RF d’IC dans des conditions d’exposition à des appareils mobiles (antennes sont supérieures à 20 cm à partir du corps d’une personne). FCC and IC RegistrationsFCC ID: EF400186IC: 1078A-00186Z-Wave Operating FrequencyAustralia/New Zealand: 921.42/921.40/919.80MHzUS/Canada: 908.42/908.40/916MHzEuropean: 868.42/868.40/869.85MHzZ-Wave Developer’s Kit: 7.13.1This product can be operated in any Z-Wave™ network with other Z-Wave certified devices from other manufacturers. All mains operated nodes within the network will act as repeaters regardless of vendor to increase reliability of the network.In an ELAN SC Series System Controller, the host application controls the device reset feature.If this controller is the primary controller for your network, resetting it will result in the nodes in your network being orphaned and it will be necessary after the reset to exclude and re-include all of the nodes in the network. If this controller is being used as a secondary controller in the network, use this procedure to reset this controller only in the event that the network primary controller is missing or otherwise inoperable.5QUICK INSTALL GUIDE6EL-SC-100 OverviewDimensions: 6.95 in. x 4.94 in. x 1.30 in.PowerButton Status Indicator ResetEL-SC-10073 in.MountingThe EL-SC-100 is designed to mount on a shelf, hang in a cabinet or rack, or mount in a structured wiring enclosure with optional mounting bracket.Wall Mounting: The EL-SC-100 chassis has been designed to allowconvenient wall mounting in any orientation. Arrows on the rear panel may be used to mark the location for the screws. Mark the screw locations, mount the screws leaving approx. 3/16” (5mm) of screw exposed and slide the chassis over the screws.NOTE: Mounting height < 2 meters. Weight < 1 kg.Shelf Mounting: The EL-SC-100 has rubber feet to protect finished surfaces. Set the controller in a location that will allow you to properly manage connected wiring so that there is no tension on the connections.8EL-SC-1009Serial ConnectionConnect an RS-232 serial controlled device using an RJ45 connector (not included) to the RS232 port on the rear of the controller.The EL-SC-100 serial connector is not compatible with RS-485 serial devices. If your project requires RS-485 connections you will need to use a gSC10 controller.Below is the wiring pin-out for the RJ45 connector.12 (CD)3 (DTR)4 (SG)5 (RD)6 TD)7 (CTS)8 (RTS)12345678QUICK INSTALL GUIDESense Input ConnectionELAN sensors can be used to trigger events from 3rd party devices.The status is binary, either ON or OFF. This can be used to trigger an event map or as a condition of an event map. CONNECT ONLY an ELAN sensor to this port.Available ELAN sensors:Audio Sensor ...........................................P/N: AUDSENSORVideo Sensor............................................P/N: VIDSENSORContact Closure Sensor ...........................P/N: CTSENSORCurrent / Magnetic Field Sensor ...............P/N: CRSENSORLight / LED Sensor ...................................P/N: LTSENSORVoltage Sensor .........................................P/N: VTSENSORIR Output ConnectionThree discrete IR outputs are supplied to control third party devices.Each output is compatible with Xantech single and dual emitters10EL-SC-10011HDMI ConnectionThe EL-SC-100 includes an HDMI connector for an on screen display (OSD) interface. Connect the OSD output to an available HDMI input on a display or AVR.USB ConnectionThe USB connection is primarily designed for connecting the optional USB Z-Wave antenna. See the integration note for configuring Z-Wave devices through the EL-SC-100.LAN / PoE ConnectionThe EL-SC-100 has a Gigabit PoE compatible Ethernet port. Connect an Ethernet cable to an available port on the network.Note: The EL-SC-100 can be connected via Wi-Fi, however a wired connection is preferred.The EL-SC-100 can be powered over Ethernet (PoE). The minimum PoE requirement is IEEE 802.3at. 42.5 - 57 VDC, 600 mA maximum.RESET ButtonLocated on the right side of the controller, is the recessed pinhole button that can be used in three ways:1. 2 second press and release resets the controller to DHCP2. 20 second press and release removes all configuration information. Software version will be maintained.3. While applying power, a 10 second press and release will perform a full factory reset. Software will revert to factory default version. DO NOT remove power during a factory reset as it will permanently damage the unit. Allow the unit to reboot and become discoverable (about 4 minutes). Note: the LED will remain red during the reset process.WARNING! THESE ACTIONS CANNOT BE UNDONE!QUICK INSTALL GUIDEPowerOnce all other connections have been completed, connect an Ethernet cable connected to a PoE switch or the 12 VDC, 1A power supply to the DC input. Power ButtonWhen the controller is off, a short press powers unit onWhen the controller is on, a short press (less than three seconds)restarts controller.When the controller is on, a long press (3 seconds or longer)powers down the controllerLED Status IndicatorThe LED communicates the status of the controller:Blue = Connected OK / PowerBlue flashing = Boot upAmber = No network foundRed = Boot failureRed flashing = Self-check failure12EL-SC-100Network ConnectionThe EL-SC-100 is factory set to use DHCP. Connect to a wired network and use the ELAN Configurator to connect to the controller. Once connected, use configurator to set a static IP address or connect via Wi-Fi. Software UpdatePrior to configuring the controller, upgrade the software to the latest available version found on the ELAN Dealer Resources portal. Download and open the executable file and follow the on screen instructions.13QUICK INSTALL GUIDE Notes14EL-SC-100Limited WarrantyNortek Security & Control ( ‘NSC’ ) warrants the EL-SC-100 to be free from defects in materials and workmanship for the period of two years (2 years) from the date of purchase. If within the applicable warranty period above purchaser discovers that such item was not as warranted above and promptly notifies ‘NSC’ in writing, ‘NSC’ shall repair or replace the item at the company’s option. This warranty shall not apply (a) to equipment not manufactured by ‘NSC’,(b) to equipment which shall have been installed by other than an ‘NSC’ authorized installer,(c) to installed equipment which is not installed to ‘NSC’s’ specifications, (d) to equipment which shall have been repaired or altered by others than ‘NSC’, (e) to equipment which shall have been subjected to negligence, accident, or damage by circumstances beyond ‘NSC’s’ control, including, but not limited to, lightning, flood, electrical surge, tornado, earthquake, or other catastrophic events beyond ‘NSC’s’ control, or to improper operation, maintenance or storage, or to other than normal use of service. With respect to equipment sold by, but not manufactured by ‘NSC’, the warranty obligations of ‘NSC’ shall in all respects conform to the warranty actually extended to ‘NSC’ by its supplier. The foregoing warranties do not cover reimbursement for labor, transportation, removal, installation or other expenses which may be incurred in connection with repair or replacement. Except as may be expressly provided and authorized in writing by ‘NSC’, ‘NSC’ shall not be subject to any other obligations or liabilities whatsoever with respect to equipment manufactured by ‘NSC’ or services rendered by ‘NSC’. THE FOREGOING WARRANTIES ARE EXCLUSIVE AND IN LIEU OF ALL OTHER EX PRESSED AND IMPLIED WARRANTIES EXCEPT WARRANTIES OF TITLE, INCLUDING BUT NOT LIMITED TO IMPLIED WARRANTIES OF MERCHANTABILITY AND FITNESS FOR A PARTICULAR PURPOSE.ATTENTION: TO OUR VALUED CUSTOMERSTo ensure that customers obtain quality pre-sale and after-sale support and service, Nortek Security & Control products are sold exclusively through authorized dealers. Nortek Security & Control products are not sold online.The warranties on Nortek Security & Control products are NOT VALID if the products have been purchased from an unauthorized dealer or an online E-tailer. To determine if your Nortek Security & Control reseller is authorized, please call Nortek Security & Control at (707) 283-5900.15Main: 800-472-5555 | International: 707-283-5900 Mon-Fri 6am - 4pm ESTTech Support is closed every Tuesday between 1:20pm and 2:30pm PST for team development. 5919 Sea Otter Place, Suite 100, Carlsbad, CA, 92010For more information on Elan Control Systems, visit:©2021 Nortek Security & Control LLC. All rights reserved.Elan is a registered trademark of Nortek Security & Control LLC.P/N: 10024269 Rev-D。
oracleruninstaller参数
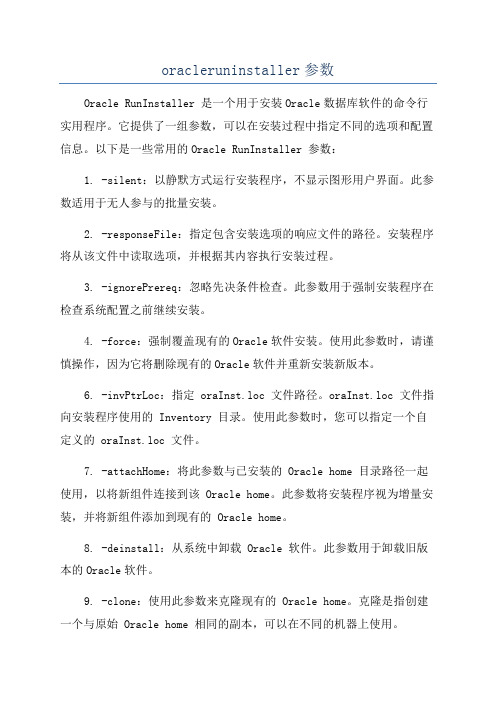
oracleruninstaller参数Oracle RunInstaller 是一个用于安装Oracle数据库软件的命令行实用程序。
它提供了一组参数,可以在安装过程中指定不同的选项和配置信息。
以下是一些常用的Oracle RunInstaller 参数:1. -silent:以静默方式运行安装程序,不显示图形用户界面。
此参数适用于无人参与的批量安装。
2. -responseFile:指定包含安装选项的响应文件的路径。
安装程序将从该文件中读取选项,并根据其内容执行安装过程。
3. -ignorePrereq:忽略先决条件检查。
此参数用于强制安装程序在检查系统配置之前继续安装。
4. -force:强制覆盖现有的Oracle软件安装。
使用此参数时,请谨慎操作,因为它将删除现有的Oracle软件并重新安装新版本。
6. -invPtrLoc:指定 oraInst.loc 文件路径。
oraInst.loc 文件指向安装程序使用的 Inventory 目录。
使用此参数时,您可以指定一个自定义的 oraInst.loc 文件。
7. -attachHome:将此参数与已安装的 Oracle home 目录路径一起使用,以将新组件连接到该 Oracle home。
此参数将安装程序视为增量安装,并将新组件添加到现有的 Oracle home。
8. -deinstall:从系统中卸载 Oracle 软件。
此参数用于卸载旧版本的Oracle软件。
9. -clone:使用此参数来克隆现有的 Oracle home。
克隆是指创建一个与原始 Oracle home 相同的副本,可以在不同的机器上使用。
10. -waitForLockTimeout:指定等待锁的超时时间(以秒为单位)。
默认情况下,安装程序将等待锁的时间为7200秒。
11. -instype:指定安装程序安装的 Oracle 软件类型。
例如,typical 表示典型安装,advanced 表示高级安装。
Perle SX设备驱动软件和硬件安装快速入门指南说明书
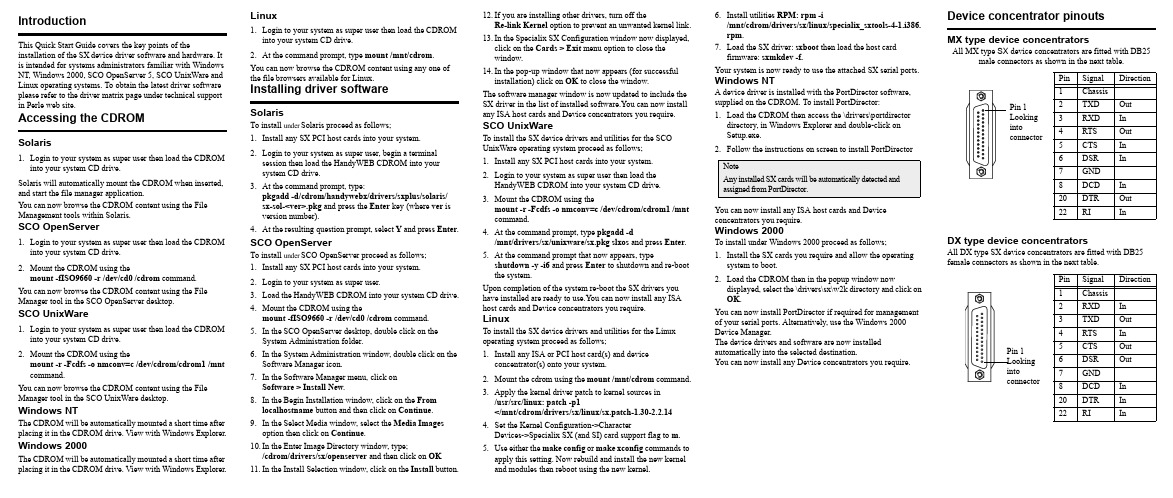
IntroductionThis Quick Start Guide covers the key points of the installation of the SX device driver software and hardware. It is intended for systems administrators familiar with Windows NT, Windows 2000, SCO OpenServer 5, SCO UnixWare and Linux operating systems. To obtain the latest driver software please refer to the driver matrix page under technical support in Perle web site.Accessing the CDROMSolaris1.Login to your system as super user then load the CDROMinto your system CD drive.Solaris will automatically mount the CDROM when inserted, and start the file manager application.You can now browse the CDROM content using the File Management tools within Solaris.SCO OpenServer1.Login to your system as super user then load the CDROMinto your system CD drive.2.Mount the CDROM using themount-fISO9660-r/dev/cd0/cdrom command.You can now browse the CDROM content using the File Manager tool in the SCO OpenServer desktop.SCO UnixWare1.Login to your system as super user then load the CDROMinto your system CD drive.2.Mount the CDROM using themount-r-Fcdfs-o nmconv=c/dev/cdrom/cdrom1/mnt command.You can now browse the CDROM content using the File Manager tool in the SCO UnixWare desktop.Windows NTThe CDROM will be automatically mounted a short time after placing it in the CDROM drive. View with Windows Explorer. Windows 2000The CDROM will be automatically mounted a short time after placing it in the CDROM drive. View with Windows Explorer.Linux1.Login to your system as super user then load the CDROMinto your system CD drive.2.At the command prompt, type mount /mnt/cdrom.You can now browse the CDROM content using any one ofthe file browsers available for Linux.Installing driver softwareSolarisTo install under Solaris proceed as follows;1.Install any SX PCI host cards into your system.2.Login to your system as super user, begin a terminalsession then load the HandyWEB CDROM into yoursystem CD drive.3.At the command prompt, type:pkgadd-d/cdrom/handywebx/drivers/sxplus/solaris/sx-sol-<ver>.pkg and press the Enter key (where ver isversion number).4.At the resulting question prompt, select Y and press Enter.SCO OpenServerTo install under SCO OpenServer proceed as follows;1.Install any SX PCI host cards into your system.2.Login to your system as super user.3.Load the HandyWEB CDROM into your system CD drive.4.Mount the CDROM using themount-fISO9660-r/dev/cd0/cdrom command.5.In the SCO OpenServer desktop, double click on theSystem Administration folder.6.In the System Administration window, double click on theSoftware Manager icon.7.In the Software Manager menu, click onSoftware>Install New.8.In the Begin Installation window, click on the Fromlocalhostname button and then click on Continue.9.In the Select Media window, select the Media Imagesoption then click on Continue.10.In the Enter Image Directory window, type;/cdrom/drivers/sx/openserver and then click on OK11.In the Install Selection window, click on the Install button.12.If you are installing other drivers, turn off theRe-link Kernel option to prevent an unwanted kernel link.13.In the Specialix SX Configuration window now displayed,click on the Cards>Exit menu option to close thewindow.14.In the pop-up window that now appears (for successfulinstallation) click on OK to close the window.The software manager window is now updated to include theSX driver in the list of installed software.You can now installany ISA host cards and Device concentrators you require.SCO UnixWareTo install the SX device drivers and utilities for the SCOUnixWare operating system proceed as follows;1.Install any SX PCI host cards into your system.2.Login to your system as super user then load theHandyWEB CDROM into your system CD drive.3.Mount the CDROM using themount-r-Fcdfs-o nmconv=c/dev/cdrom/cdrom1/mntcommand.4.At the command prompt, type pkgadd -d/mnt/drivers/sx/unixware/sx.pkg slxos and press Enter.5.At the command prompt that now appears, typeshutdown-y-i6 and press Enter to shutdown and re-bootthe system.Upon completion of the system re-boot the SX drivers youhave installed are ready to use.You can now install any ISAhost cards and Device concentrators you require.LinuxTo install the SX device drivers and utilities for the Linuxoperating system proceed as follows;1.Install any ISA or PCI host card(s) and deviceconcentrator(s) onto your system.2.Mount the cdrom using the mount /mnt/cdrom command.3.Apply the kernel driver patch to kernel sources in/usr/src/linux: patch -p1</mnt/cdrom/drivers/sx/linux/sx.patch-1.30-2.2.144.Set the Kernel Configuration->CharacterDevices->Specialix SX (and SI) card support flag to m.e either the make config or make xconfig commands toapply this setting. Now rebuild and install the new kerneland modules then reboot using the new kernel.6.Install utilities RPM: rpm -i/mnt/cdrom/drivers/sx/linux/specialix_sxtools-4-1.i386.rpm.7.Load the SX driver: sxboot then load the host cardfirmware: sxmkdev -f.Your system is now ready to use the attached SX serial ports.Windows NTA device driver is installed with the PortDirector software,supplied on the CDROM. To install PortDirector:1.Load the CDROM then access the \drivers\portdirectordirectory, in Windows Explorer and double-click onSetup.exe.2.Follow the instructions on screen to install PortDirectorYou can now install any ISA host cards and Deviceconcentrators you require.Windows 2000To install under Windows 2000 proceed as follows;1.Install the SX cards you require and allow the operatingsystem to boot.2.Load the CDROM then in the popup window nowdisplayed, select the \drivers\sx\w2k directory and click onOK.You can now install PortDirector if required for managementof your serial ports. Alternatively, use the Windows2000Device Manager.The device drivers and software are now installedautomatically into the selected destination.You can now install any Device concentrators you require.Device concentrator pinoutsMX type device concentratorsAll MX type SX device concentrators are fitted with DB25male connectors as shown in the next table.DX type device concentratorsAll DX type SX device concentrators are fitted with DB25female connectors as shown in the next table.NoteAny installed SX cards will be automatically detected andassigned from PortDirector.Pin Signal Direction1Chassis2TXD Out3RXD In4RTS Out5CTS In6DSR In7GND8DCD In20DTR Out22RI InPin Signal Direction1Chassis2RXD In3TXD Out4RTS In5CTS Out6DSR Out7GND8DCD In20DTR In22RIInPin 1LookingintoconnectorRJX type device concentratorsAll RJX type SX device concentrators are fitted with RJ45 female connectors as shown in the next table.Installing host cardsPCI host cards1.Turn off the power to your system and remove the cover.2.Insert each card into a vacant PCI slot.3.Replace and secure the cover of your computer and restartyour machine. The SX card(s) should be detectedautomatically.ISA host card1.Set the address on each ISA host card using the address oneach ISA host card using the rotary switches SW1, SW2 and jumper J2 to the first three digits of the address you want as shown by the next example.2.Turn off the power to your system and disconnect themains supply.3.Remove the system cover to expose the inside of theconnector panel for host cards.4.Insert the ISA card you want to install into a vacant hostcard slot and secure in place.5.Repeat step 2. until you have installed all the ISA cardsyou want.6.Replace and secure the system cover.7.Plug in the mains lead and turn on the power.6.Power up your computer system.SXSerial connectivity systemQuick start guide•Up to 32 ports per card•Up to 4 cards per server Pin Signal Direction1DCD In2DTR Out3DSR In4S/GND5TXD Out6RXD In7RTS Out8CTS InShieldWarningDangerous voltages exist inside computer systems.Before installing host cards in your system, turn offthe power supply and disconnect the mains lead.CautionFull anti-static precautions should be taken when handlinghost cards.Pin 1(looking intoAddress SW1SW2J2J3C00000C No jumper NojumperC80000C Jumper fittedD00000D No jumperContacting Perle Technical SupportPerle offers free technical support to Perle AuthorisedDistributors and Registered Perle Resellers.To access technical support please visit the Perle websiteat /support.Here you will find:• latest drivers and firmware updates for download• technical tips• frequently asked questions• documentation。
BRX MPU系统用户手册附录E:使用NetEdit实用程序的更新指南说明书

3C hapter C onfiguring ECoM su sing n Et E dit3Ethernet Communications Modules, 3rd Edition, Rev. E3–2Chapter 3: Configuring ECOMs Using NetEdit3NetEdit3 SoftwareNetEdit3 is a software utility which can be used to set network identifiers (Module ID or IP Address), perform diagnostic and troubleshooting tasks and upgrade the firmware in the ECOM module if necessary. The H0/H2/H4 -ECOM100 requires NetEdit 3.5 or later.Installing NetEdit3You can install NetEdit3 on Windows98/ME/2000/XPt or Windows NT4t. NetEdit3 is available online at . After loading the software the following window will appear.Click on Install NetEdit3. A series of windows will step you through the installation process.Fill in the necessary information as the installation wizard prompts through the install. In theSetup Type window, select Typical setup. This setup type is recommended for most users. The installation process places NetEdit3 in the C:\HAPT ools directory (default).Click on the Essential Tools button. The following window will be displayed.Ethernet Communications Modules, 3rd Edition, Rev. E3–3Launching NetEdit3There are three methods to launch NetEdit3. The three methods are:• using the Windows Start menu Programs>AutomationDirect Tools> NetEdit3as shown below• launching DirectSoft (if installed), from the programming window, selectPLC>Tools>NetEdit3• launching DirectSoft (if installed), then select Utilities>NetEdit3The NetEdit3 ScreenStarting NetEdit3 brings up the screen below. All NetEdit3 functions are accessedfrom this screen.Ethernet Communications Modules, 3rd Edition, Rev. E3–4Chapter 3: Configuring ECOMs Using NetEdit3Using NetEdit3This section steps through the features and uses of NetEdit3. We will describe the individual segments of the NetEdit3 screen and the function of each.NOTE: Your PC-based Control software may be capable of configuring the EBC module. If so, please refer to the appropriate documentation for that software product to determine the best method to configure the EBC.Depending on which software you are using, it may not be necessary to use NetEdit3.Ethernet Communication ProtocolIn the upper left corner of the NetEdit3 screen, you will find buttons labeled IPX and TCP/IP.The ECOM module understands these protocols. Both protocols are permanently resident in the firmware of the module.When you click on one of these buttons, you are selecting the protocol you want your PC to use to communicate with the ECOM module. You are not telling the module which protocol to use, because it is using both protocols all the time. IPX is a Novell standard in widespread use, and UDP/IP is a popular protocol supported by the TCP/IP suite of protocols in your PC.The figure to the right shows the Protocol selection buttons in the upper left corner of the NetEdit3 screen. The choice you make here tells your PC which protocol to send to the ECOM to link NetEdit3 to the module.Some PC-based control software products may support only one of these protocols. Read the documentation for your software to be sure the protocol you select issupported.Ethernet Communications Modules, 3rd Edition, Rev. E3–5Ethernet Communications Modules, 3rd Edition, Rev. E3–6Chapter 3: Configuring ECOMs Using NetEdit3Ethernet Communications Modules, 3rd Edition, Rev. E3–7Module Info> General InformationWhen the Module Info tab is selected, the General Info box lists the selected module’s Firmware Revision, Booter Revision, DIP Switch Setting, PWB Revision, PLD Revision and CPU Revision.This box is in the lower left section of the NetEdit3 screen.Module Info> Ethernet StatsWhen the Module Info tab is selected, the Ethernet Stats box displays statistics related to the selected module’s communication errors. Click on the Reset Stats button to reset all categories to 0 (zero).This box is in the lower middle section of the NetEdit3 screen.ECOM SettingsWhen the ECOM Settings tab is selected, the selected module’s Configuration, Utilities and Firmware tools can be accessed.This box is in the lower middle section of the NetEdit3 screenEthernet Communications Modules, 3rd Edition, Rev. E3–8Chapter 3: Configuring ECOMs Using NetEdit3Clicking the General button in the ECOM The General Settings box allows you to assign a Module ID each ECOM, but they do not have to be in sequence. The module’s DIP switches must be set to zero to allow NetEdit3 to set a Module ID. Do not use address zero for communications.Ethernet Communications Modules, 3rd Edition, Rev. E3–9ECOM Settings> Configuration> AdvancedClicking the Advanced button in the ECOM Settings>Configuration box brings up the ECOM Advanced Settings window below.RX/WX - Settings box in this window provides a place to make changes that affect PLC-to-PLC communications.ACK Time out - sets the time limit for receiving the acknowledge (ACK) response to an RX or WX instruction. The ECOM sends a message across the L AN. The acknowledge response comes back directly from the ECOM module receiving the transmission. This timeout is the maximum for transmission and acknowledgement from ECOM to ECOM across the LAN. It is not dependent on the PLC scan time.Resp. Timeout - sets the maximum time for the receiving PLC CPU to respond to the ECOM that initiated the communication. The instruction has travelled from the initiating PL C CPU to the initiating ECOM, across the Ethernet LAN to the receiving ECOM, then to thereceiving PLC CPU, and back again to the initiating ECOM. Multiple PLC scans may be required to execute an RX/WX instruction so the Resp. Timeout should allow for multiple scans. Also, communication errors may result in retries which require more time. Your response timeout setting must accommodate retries as well.The WX/RX Retries field shows the number of times the ECOM will retry transmissions to the network.The K- Sequence Retries field shows the number of times the backplane transmission between ECOM and CPU is to be retried.The OK button loads the communication settings in the ECOM module’s flash memory.Ethernet Communications Modules, 3rd Edition, Rev. E3–10Chapter 3: Configuring ECOMs Using NetEdit3ECOM Settings> Configuration> Peer to PeerThis function allows you to configure the client H0/H2/H4 -ECOM(100) module to use an IP protocol packet to perform the RX/WX instruction, as opposed to a broadcast packet to locate the slave ECOM or MODBUS TCP server.Chosing Peer to Peer: The following are reasons or conditions of when to configure the H0/H2/H4 -ECOM(100) for peer to peer communications with a TCP/IP server device:• T o eliminate network broadcast traffic when the ECOM(100) is a client executing RX/WX network instructions.• When an ECOM(100) is an “ECOM protocol client” and needs to access other server ECOMs through a router.• When an ECOM100 needs to serve as MODBUS TCP client Clicking the Peer to Peer Config button in the ECOM Settings>Configuration box brings up the Peer to Peer Configuration window shown below. Any previous peer to peer configurations will be listed in the table.The RX and WX ladder logic instructions used by the PLC allow you specify a Node (Device) Number as the slave identifer in the range of 1- 87. The Peer to Peer Configuration information is stored in the ECOM(100) module’s flash memory. This basically associates a Device Number (that is used by the RX/WX instructions) with a server’s IP address.Clicking on the Add button in the Peer to Peer Configuration window will display the Add Device Address window shown to the right. Enter the necessary server’s network information (i.e. Device Number, server’s IP address and protocol). You can manually enter the information or you can click on the Find Hx-ECOM button to display all local ECOMs currently on the network. MODBUS TCP device’s network information will have to be entered manually. Refer to page 6- 6 for information on Port and Unit ID Numbers. Clicking the OK button adds the Device Configuration to the main peer to peer configurationscreen. Be certain not to duplicate Device Numbers.Clicking on the Find Hx-ECOMbutton in the Add Device Addresswindow will display the SelectECOM window shown to the right.Highlight the server ECOM that youintend to communicate with peerto peer via the client ECOM(100)module. Then click the OK button.This will add the ECOM’s DeviceConfiguration information tothe previous Add Device Addresswindow.Once the module’s network information is in the Add Device Address window (previous page), click the OK button to add the information to the main Peer to Peer Configuration window. Repeat the steps to add other ECOMs to the configuration. Clicking the OK button on the main screen window writes the module(s) network information to the ECOM(100)’s flashmemory.Ethernet Communications Modules, 3rd Edition, Rev. E3–11Ethernet Communications Modules, 3rd Edition, Rev. E3–12Chapter 3: Configuring ECOMs Using NetEdit3ECOM Settings> Utils>T est CPU AccessClicking the Test CPU Access button in the ECOM Settings>Utilities box brings up the window shown below.The ECOM has two distinct “sides”, the network side, which contains the network configuration settings, and the backplane side, which the ECOM uses to communicate with the PLC CPU. It is possible that only one side could be operating correctly, while the other side is not. The T est CPU Access function will test the connection from your PC to the ECOM module through the network side, across the backplane to the PLC CPU and back to your PC.ECOM Settings> FirmwareThe functions in the Firmware box are used to update the selected module’s Firmware and Booter versions. The Restore Factory Settings buttons resets the selected module’s IP address, ID, Name and Description to factory defaults. Refer the sections on the next page to determine if updates are necessary.Clicking on the either of the Update buttons opens the appropriate ECOM folder within the Images folder, which is created during the install of NetEdit3. The Images folder is located in the same folder as NetEdit3.exe. Each module folder contains the module’s firmware and boot loader files. The next section discusses keeping thefirmware files up to date.Ethernet Communications Modules, 3rd Edition, Rev. E3–13FileMenu> Live UpdateThe L ive Update will retrieve the latest firmware and boot loader files from the Host Engineering web site and place them in the NetEdit3 Images folder that was created during the install of NetEdit3. The feature requires that you have a functional Internet connection (dial- up or broadband). If the Images folder does not exist on your PC, it will be created as part of the retrieval process.When you click the Go! button on the L ive Update window, NetEdit3 will compare the version information of the files on the Host Engineering web site against the files you have locally on your PC, and it will download any newer files. Once this process is complete, NetEdit3 will rescan the devices on your network and refresh the “F” and “B” columns next to the listed devices.F / B / C ColumnsThe F , B, and C columns are provided to signify potential issues with devices on the network.The “F” column will display an asterisk beside any device whose firmware is older than its firmware file in your Images folder.The “B” column will display an asterisk beside any device whose boot loader is older than its boot loader file in your Images folder.The “C” column will display an asterisk beside any device that has a configuration conflict with another device on the network. Duplicate module IDs (that are non- zero) and duplicate IPAddresses (that are not 255.255.255.255) will report as conflicts.。
Appendix

附录A.1 存储器构造 (1)A.2 特殊继电器 (3)A.3 指令清单 (12)附录A.1.1 位存储器设备位存储器设备是提供位读写的存储设备。
P , M, L, K, F 区域都是位存储器设备。
然而,位存储器设备也可以被用做字设备区域。
< 位存储器设备的符号 >< 位存储器设备的内存结构 >位地址赋值( 0 ~ F : 十六进制 ) 字地址赋值(十进制 ) 设备赋值( P, M, L, K, F )FEDCBA987654321000 001 002 003nnn = P002BA.1.2 位 / 字存储器设备( 定时器& 计数器)定时器和计数器存储区域包括三部分-输出位 、当前值字和设定值字。
当T 或 C 区域被当成位指令的运算对象时,指令对定时器和计数器的输出位有影响。
如果T 或C 区域被使用做字指令的运算对象,指令影响当前值。
用户不能改变设定值。
A.1.3 字存储器设备D 区域由字来使用。
因此,D 区域不能被用做位指令例如:LOAD, OUT 等的运算对象。
如要通过位来控制D 区域,请使用特殊指令如:BLD 、BAND 、BOR 等。
FEDCBA987654321D0000 D0001D0002 D0003Dnnnn = D0002A.2.1 K10S1 / K10S / K30S / K60S1) F 设备2) 其它特殊继电器A.2.2 K80S / K200S / K300S / K1000S1) F 继电器高速连接标志清单x : K1000S = 9, K300S / K200S = 4, n = 0 ~ 7 (槽号码)槽号& 标志清单高速连接信息标志清单的详细信息(m=0时)高速连接信息标志清单的详细信息(m= 1 到3)从属系统标志清单⏹●: 仅适用于K1000S, K300S, K200S 系列 : 仅适用于K10S,K10S1, K30S, K60S 系列 : 在K80S 不能使用。
Yeastar S100 VoIP PBX Installation Guide

Yeastar S100 VoIP PBX Installation GuideContentWelcome (3)Before You Start (4)Package Contents (4)Expansion Board (4)Yeastar S100 Overview (5)LED Indicators and Ports (6)Installation (8)Safety Disclaimers and Installation Warnings (8)Telephony Module Installation (8)DSP Module Installation (11)Desktop Installation (12)Rack Installation (12)Frame Ground Connection (13)Connecting the Equipment (14)Getting Started with the Configuration (15)WelcomeThank you for choosing Yeastar S100 IP PBX. S100 is a cost-effective business communication system with a base configuration of 100 users and 30 concurrent calls and can scale up to 200 users and 60 concurrent calls. The flexible S100 comes with support for analog ports, ISDN BRI, E1/T1/PRI, and GSM networks.This guide describes how to install the S100 and how to log in the web GUI to configure the system. Once you complete the installation, refer to the Yeastar S-Series Administrator Guide for instructions on how to perform configurations on the system.Related DocumentsThis Installation Guide only explains the installation of Yeastar S100 IPPBX. For more functionality and advanced settings, please refer to the relative documents as below:Before You StartBefore you begin to install the S100 IP Phone System, please check the package contents to verify that you have received the items below. If there is any problem, please contact your provider.Package ContentsExpansion BoardYeastar S100 supports expanding up to 2 Expansion boards and supports expanding one DSP module.Expansion Board – EX08EX08 board supports up to 4 modules (8 ports).Optional Module∙O2 Module∙S2 Module∙SO Module∙B2 Module∙GSM Module∙3G ModuleExpansion Board – EX30EX30 board supports 1 E1/T1 port.D30 ModuleD30 is a DSP module, used to expand the capacity of PBX. With per D30 module added, the extensions increase 100 and concurrent calls increase 30 in additional.Yeastar S100 OverviewFront Panel (1*EX08 + 1*EX30)Back PanelAntenna SocketsSD Slot Console Power SwitchPower LAN Power InletSystem WAN Protective EarthReset USB SlotLED Indicators and PortsLED IndicatorsPort DescriptionInstallationThis chapter shows you how to install Yeastar S100 IP phone system.Safety Disclaimers and Installation WarningsTo avoid unexpected accident, personal injury or device damage, please read the safety disclaimers and installation warnings.Power●Use only the power cord provided with the IP PBX.●Keep the power off during the installation.●Make sure that the supply voltage matches the specifications indicated on the back panel of thedevice.●To avoid the electric accident, do not open or remove the cover of IP PBX when it is working aswell as off the power.●Before cleaning the device, cut off the power supply.EnvironmentInstall the Yeastar S100 IP PBX in a location that is clean, free from vibration, electric shock, and temperature/humidity extremes. The operating temperature should be kept below 104°F (40°C).Telephony Module InstallationSTEP 1Loosen the screws on the enclosure and then remove the upper cover.STEP 2Push out the empty board from the inside of the device.STEP 3Push in the Expansion Board (EX08 or EX30).STEP 4Lock the screws to fix the Expansion Board.STEP 5Insert the Telephony Modules on the EX08 Board. Skip this step for EX30 Board.STEP 6Insert a SIM card on the GSM/3G module following the instructions. Skip this step if no GSM/3G module installed.STEP 7 Close the cover and fix the screws.STEP 8 Rotate the antenna into the Antenna Socket. Skip this step if no GSM/3G module installed.DSP Module InstallationSTEP 1 Open the device upper cover and insert the DSP module (D30) into the D-Slot from a tilt angle and then press it down.STEP 2 Lock the screws to fix the D30 module board.Desktop InstallationWARNING∙Please set 5~10cm gaps around the device for air circulation.∙Please avoid any heavy thing placed on the device.STEP 1 Place the IP PBX on a steady platform.STEP 2 Remove the adhesive backing paper from the rubber feet.STEP 3 Turn over the device and attach the supplied rubber feet to the recessed areas on the bottom at each corner of the device.Rack InstallationWARNING∙Be careful not to drop any components. Dropping components may damage them or cause an injury.∙Only use the 19-inch rack mounting kits (attached bracket and fittings) included with the PBX.STEP 1 Fix the brackets to the left and right sides of the PBX with 4 screws.STEP 2 Place the PBX in the 19-inch rack and fix both brackets to the rack with the rack’s proprietary mounting equipment.Ground ConnectionWARNING∙Proper grounding (connection to ground) is very important to reduce the risk to the user of electrocution or protect the PBX from the bad effects of external noise in the case of alightning strike.∙ A permanent connection between ground and the ground terminal of the PBX must be made.STEP 1 Tighten the provided screw stud into the Grounding port on PBX.STEP 2 Insert an 18AWG grounding wire (user supplied).STEP 3 Tighten the provided screw nut.STEP 4 Attach the grounding wire to the grounding terminal.Connecting the EquipmentSTEP 1 Connect one end of a network cable to the LAN port of Yeastar device, and the other end to any port of your company’s LAN switch/router.STEP 2 Plug the provided power cord into the power jack on S100 and the other end to a standard electrical wall socket. Wait for the system to boot up till the SYSTEM LED starts to blink.STEP 3 Connect the telephony line to the RJ11 port of the device.STEP 4 Connect one end of the E1 cable to the E1/T1 port. Connect the other end to the E1 provider’s equipment.NOTEConnect BRI/PSTN/analog phone/fax machine to the corresponding port based on the color of port indicator.Getting Started with the ConfigurationYeastar S100 IP Phone System provides web-based configuration interface for administrator. The administrator can manage the device by logging in the Web interface.∙Access path: https://192.168.5.150:8088∙User Name: admin∙Password: passwordSTEP 1 Connect your PC to the same network as Yeastar S100.STEP 2 Start the browser on PC. In the address bar, enter the IP address, click “Enter” key and then you can see the web GUI login page shows as below.STEP 3 For the detailed configurations of extensions, trunks and other system settings, please refer to the manual Yeastar S-Series Administrator Manual.NOTEAfter saving the changes, reme mber to click the “Apply” button at the top-right corner to make the changes take effect.[END]。
考研英语大纲5500词汇表(精选5篇)
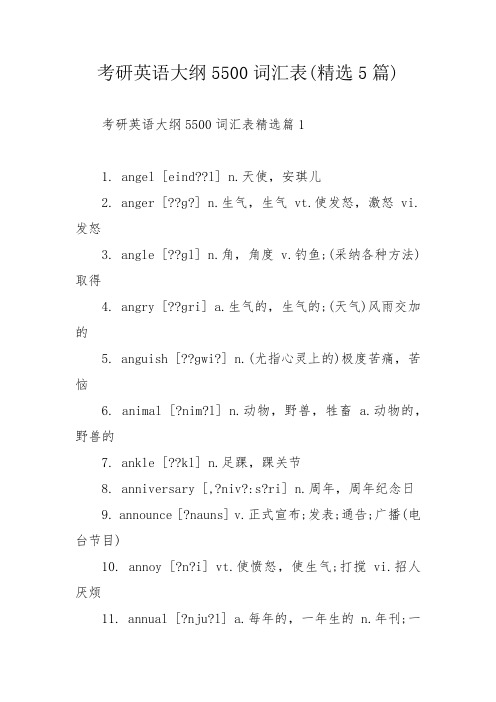
考研英语大纲5500词汇表(精选5篇)考研英语大纲5500词汇表精选篇11. angel [eind??l] n.天使,安琪儿2. anger [??ɡ?] n.生气,生气 vt.使发怒,激怒 vi.发怒3. angle [??ɡl] n.角,角度 v.钓鱼;(采纳各种方法)取得4. angry [??ɡri] a.生气的,生气的;(天气)风雨交加的5. anguish [??ɡwi?] n.(尤指心灵上的)极度苦痛,苦恼6. animal [?nim?l] n.动物,野兽,牲畜 a.动物的,野兽的7. ankle [??kl] n.足踝,踝关节8. anniversary [,?niv?:s?ri] n.周年,周年纪念日9. announce [?nauns] v.正式宣布;发表;通告;广播(电台节目)10. annoy [?n?i] vt.使愤怒,使生气;打搅 vi.招人厌烦11. annual [?nju?l] a.每年的,一年生的 n.年刊;一年生植物12. anonymous [?n?nim?s] a.匿名的,无名的,姓氏不明的13. another [?n?e?] a.另一个,又,再 pron.另一个,类似的一个14. answer [ɑ:ns?, ?n-] vt.回答,答复,答案 v.回答,答复,响应15. ant [?nt] n.蚁;蚂蚁16. antenna [?nten?] n.(无线电或电视的)天线17. anticipate [?ntisipeit] vt.预料;期望;预先考虑;抢先;提前使用18. antique [?nti:k] a.古式的,过时的n.有价值的古物,古董19. anxiety [??zai?ti] n.挂念,焦虑,着急,忧虑;渴望,热望20. anxious [?nk??s] a.焦虑的,担忧的;急于(得到的),渴望的21. any [eni] a.(用于否定句、疑问句等)什么,一些;任何的22. anybody [eni,b?di] pron.(否定句)任何人;(确定句)任凭哪个人23. anyhow [enihau] ad.不管怎么说,无论如何;不论用何种方法24. anyone [eniw?n] pron.(用于疑问句,否定式)任何人25. anything [eniθi?] pron.任何东西(事物);无论什么东西(事物)26. anyway [eniwei] ad.不管怎么说,无论如何;不论以何种方式27. anywhere [enihwε?] ad.无论哪里;(用于否定、疑问等)任何地方28. apart [?pɑ:t] ad.分别,离开,隔开 a.分别的,分隔的29. apartment [?pɑ:tm?nt] n.[英]房间,套间;[美]公寓30. apologise [?p?l?d?aiz] v.(to,for)赔礼,认错31. apology [?p?l?d?i] n.赔礼,认错,辩解,辩护32. appal [?p?:l] v.使惊骇,使恐怖33. apparatus [,?p?reit?s] n.器械,器具,仪器;机构,组织34. apparent [?p?r?nt] a.表面上的,貌似真实的;明显的,明明白白的35. appeal [?pi:l] vi.呼吁,请求;申诉 n.呼吁;申诉;吸引力36. appear [?pi?] vi.消失;出场;问世;仿佛;出版,发表37. appearance [?pi?r?ns] n.消失,露面;外表;(在会议等)作短暂露面38. appendix [?pendiks] n.附录,附属物;阑尾,盲肠39. appetite [?pitait] n.食欲,胃口;欲望,性欲;爱好,趣味40. applaud [?pl?:d] vt.鼓掌欢迎;赞同 vi.鼓掌欢迎,欢呼41. applause [?pl?:z] n.鼓掌;喝彩;夸奖,赞扬42. apple [?pl] n.苹果,苹果树43. appliance [?plai?ns] n.电器;器械,装置;应用,适用44. applicable [?plik?bl, ?plik?-] a.可应用(实施)的;适当的,合适的45. application [,?plikei??n] n.申请,恳求,申请书;应用,实施,有用性46. apply [?plai] vi.(以书面形式)申请;恳求 vt.应用;实施47. appoint [?p?int] vt.任命,委派;指定,商定(时间、地点等)48. appointment [?p?intm?nt] n.约会,商定;任命,委派;委任的职位49. appraisal [?preiz?l] n.对...作出的评价;评价,鉴定,评估50. appreciate [?pri:?ieit] vt.为...表示感谢,感谢;观赏,赏识,评价51. approach [?pr?ut?] v.靠近,接近n.接近;途径,入门;方式,方法52. appropriate [?pr?uprieit] a.适当的,恰当的,特有的 vt.拨给,挪用,盗用53. approval [?pru:v?l] n.批准,通过;赞成,同意54. approve [?pru:v] v.(of)赞成,赞许,同意;批准,审议,通过55. approximate a.近似的 vi.(to)接近56. April (名)四月57. apt [?pt] a.恰当的,适当的;易于…的,有…倾向的58. arbitrary [ɑ:bitr?ri] a.任意的,任性的,主观的;专断的,武断的59. arch [ɑ:t?] n.拱门,桥拱洞 v.拱起,(使)变成弓形60. architect [ɑ:kitekt] n.建筑师;设计师;缔造者;制造者61. architecture [ɑ:kitekt??] n.建筑,建筑学;建筑式样或风格,建筑物62. area [ε?ri?] n.面积;地区,地域;领域,范围63. argue [ɑɡju:] vi.辩论,争辩 vt.辩论,论证;劝说,劝告64. argument [ɑ:ɡjum?nt] n.争辩(吵),辩论;理由;论证65. arise [?raiz] v.消失,发生;(from)由…引起,由…产生66. arithmetic [?riθm?tik] n.算术,四则运算67. arm [ɑ:m] n.手臂,扶手,臂状物 v.武装;配备 n.武器68. army [ɑ:mi] n.军队,陆军,军;大群,大批69. around [?raund] ad.在...四周,处处 prep.在..四周(或四周)70. arouse [?r?uz] vt.唤醒,叫醒;唤起,激起71. arrange [?reind?] v.支配,筹划;整理,使有条理,排列,布置72. array [?rei] n.大量;排列;盛装 v.列阵;装扮;排列73. arrest [?rest] n.逮捕,扣留 vt.逮捕,扣留;阻挡;吸引74. arrival [?raiv?l] n.到达,到来;到达者,到达物75. arrive [?raiv] vi.到达;(时间、大事)到来,发生;达到76. arrogant [?r?ɡ?nt] a.高傲的,自大的77. arrow [?r?u] n.箭,矢,箭状物;箭头符号78. art [ɑ:t] n.艺术,美术;技术,技艺;文科,人文科学79. artery [ɑ:t?ri] n.动脉;干线,要道80. article [ɑ:tik?l] n.文章,论文;条款,条文;物件;冠词81. articulate [ɑ:tikjul?t] a.擅长表达的;有关节相连的 v.清晰地讲话82. artificial [,ɑ:tifi??l] a.人工的,人造的,人为的;虚伪的,做作的83. artist [ɑ:tist] n.艺术家,美术家;(某方面的)能手84. artistic [ɑ:tistik] a.艺术(家)的,美术(家)的;擅长艺术创作的85. as ad.同样地 conj.由于;像...一样 prep.作为86. ascend [?send] vi.慢慢上升,上升vt.攀登,登上87. ascertain [?send] vt.确定,查明,弄清88. ash [??] n.灰,灰末;(pl.)骨灰;(pl.)废墟89. ashamed [??eimd] a.惭愧的,耻辱的,害臊的90. ashore [:] ad.上岸;在岸上,向岸上91. aside [?said] ad.在旁边,到一边 n.旁白;离题的话92. ask [ɑ:sk, ?sk] vt.问,询问;恳求,要求;邀请,约请93. asleep [?sli:p] a.睡觉,睡着(用作表语)94. aspect [?spekt] n.样子, 外表, 面貌, (问题等的)方面95. aspire [?spai?] vi.(to,after)渴望,追求,有志于96. assassinate [?s?sineit] vt.暗杀,行刺;中伤97. assault [?s?:lt] v.猛烈地攻击,攻击 n.突然而猛烈的攻击98. assemble [?sembl] vt.集合,召集;装配;收集 vi.集合,聚集99. assembly [?sembli] n.集合;会议;装配;(美)洲议会的众议院100. assert [?s?:t] vt.断言,宣称;坚持;主见(权利、权威等)考研英语大纲5500词汇表精选篇21. bar [bɑ:] n.条,杆,闩;酒吧;栅,障碍(物) v.闩上,阻拦2. barbecue [bɑ:bikju:] n.烤肉;烤肉用的台架 vt.炙烤(肉等)3. barber [bɑ:b?] n.理发师 vt.为…理发修整 vi.当理发师4. bare [bε?] a.赤裸的,空的;稀有的,仅有的 v.露出,暴露5. barely [bε?li] ad.赤裸裸地,无遮挡地;仅仅,牵强,几乎没有6. bargain [bɑ:ɡin] n.廉价货;交易,契约,合同 v.议价,成交7. bark [bɑ:k] vi.(狗等)吠,叫n.吠声,叫声;树皮8. barn [bɑ:n] n.谷仓,仓库 vt.把…贮存入仓9. barrel [b?r?l] n.桶;枪管,炮管10. barren [b?r?n] a.贫瘠的;不育的;(植物)不结果的;无用的11. barrier [b?ri?] n.栅栏,屏障;障碍(物) vt.把…关入栅栏12. base [beis] n.基础,底部;依据地 v.(on)把…基于13. baseball [beisb?:l] n.棒球14. basement [beism?nt] n.建筑物的底部,地下室,地窖15. basic [beisik] a.基本的,基础的16. basin [beis?n] n.盆,脸盆;内海,盆地17. basis [beisis] n.基础,依据18. basket [bɑ:skit, b?s-] n.筐,篮,篓19. basketball [bɑ:skitb?:l, b?s-] n.篮球,篮球运动20. bat [b?t] n.球拍,球棒,短棒;蝙蝠21. batch [b?t?] n.一批,一组,一群22. bath [bɑ:θ/b?θ] n.沐浴,洗澡;浴室(池,盆) v.(给…)洗澡23. bathe [beie] v.游泳,洗澡,浸,弄湿24. bathroom [bɑ:θrum] n.浴室;盥洗室,卫生间25. battery [b?t?ri] n.电池(组);(器具等的)一组,一套;炮兵连26. battle [b?tl] n.战役,战斗;斗争 v.战斗,斗争,搏斗27. bay [bei] n.海湾,(港)湾28. be [强bi:, 弱bi] v.(就)是,等于;(存)在;到达,来到,发生29. beach [bi:t?] n.海滩,湖滩,河滩30. beam [bi:m] n.(横)梁,桁条;(光线的)束,柱 v.微笑31. bean [bi:n] n.豆;菜豆,蚕豆32. bear [bε?] n.熊 v.忍受,容忍;负担;结果实,生子女33. beard [bi?d] n.胡须34. bearing [bε?ri?] n.轴承;忍受;关系,影响;举止;方向35. beast [bi:st] n.兽,牲畜;凶残的人,举止粗鲁的人36. beat [bi:t] n.敲打;(心脏等)跳动 v.战胜;(心脏等)跳动37. beautiful [bju:tiful] a.美的,漂亮的;精彩的,完善的38. beauty [bju:ti] n.美,漂亮;美人,漂亮的事物39. because [bik?z] conj.由于,由于40. become [bik?m] vi.变成,开头变得vt.适合,同…相称41. bed [bed] n.床,床位;(苗)床,坛;河床,(湖、海的)底42. bee [bi:] n.蜂,蜜蜂;劳碌的人43. beef [bi:f] n.牛肉44. beer [bi?] n.啤酒45. before [bif?:] prep.(指时间)在…以前,在..前面,在..之前46. beforehand [bif?:h?nd] ad.预先,事先47. beg [beɡ] vt.恳求,恳求 vi.恳请,行乞48. begin [biɡin] v.(began,begun)开头,着手49. beginning [biɡini?] n.开头,开端;起源,早期阶段50. behalf [bihɑ:f] n.利益51. behave [biheiv] v.举止,举动,表现;运转,开动52. behavior [biheivj?] n.(behaviour)行为,举止;(机器等)运转状况53. behind [bihaind] prep.在...的背后,(遗留)在..后面;落后于54. being [bi:?] n.生物,生命,存在;55. belief [bili:f] n.信任,信任,信念;信仰,信条56. believe [bili:v] vt.信任,认为 vi.信任,信任,信奉57. bell [bel] n.钟,铃58. belly [beli] n.肚子,腹部;(像肚子一样)鼓起的部分,膛59. belong [bil??] v.(to)属于,附属,隶属;应归入(类别,范畴等)60. beloved [bil?vid, -l?vd] a./n.受爱戴的,尊敬的;爱人,被心爱的人61. below [bil?u] prep.在…下面,在…以下 ad.在下面,向下62. belt [belt] n.(皮)带,腰带;地带63. bench [bent?] n.长凳,条凳;(工作)台,座64. bend [bend] v.(使)弯曲;屈从,屈服 n.弯曲(处),曲折处65. beneath [bini:θ] prep.在…下边,在…之下 ad.在下方66. beneficial [,benifi??l] a.(to)有利的,有益的67. benefit [benifit] n.利益,好处,恩惠 v.有益于;(from,by)受益68. benign [binain] a.(病)良性的,(气候)良好的,慈爱的,和气的69. beside [bisaid] prep.在...旁边,在...四周;和...相比70. besides [bisaidz] ad.此外;并且 prep.于…之外;除…以外71. best [best] a.最好的(good和well最高级) ad.最好地;最72. bet [bet] v.赌,打赌 n.打赌,赌注73. betray [bitrei] v.背叛,出卖;暴露,流露,泄露74. better [bet?] a.较好的 ad.更好(地) v.改良 n.较佳者75. between [bitwi:n] prep.在…之间,在(两者)之间 ad.在中间76. beverage [bev?rid?] n.(水,酒等之外的)饮料77. beware [biwε?] v.当心,谨防78. bewilder [biwild?] v.使迷惑,难住79. beyond [bij?nd] prep.在(或向)...的那边,远于;超出;80. bias [bai?s] n./v.(使有)偏见,偏心,偏袒81. Bible n.圣经82. bibliography [,bibli?ɡr?fi] n.(有关某一专题的)书目;参考书目83. bicycle [baisikl] n.(bike)自行车 vi.骑自行车84. bid [bid] v.祝福;命令,叮嘱;报价,投标 n.出众,投标85. big [biɡ] a.大的;重要的;宽宏大量的;大受欢迎的86. bill [bil] n.账单;招贴,广告;(人员,职称等的)表;钞票87. billion [bilj?n] num./n.(美)十亿,(英)万亿88. bin [bin] n.(贮藏食物等用的)箱子89. bind [baind] v.捆,绑,包括,束缚90. biography [bai?ɡr?fi] n.传记;传记文学91. biology [bai?l?d?i] n.生物学92. bird [b?:d] n.鸟,雀;女人;嘘声93. birth [bɑ:θ] n.诞生,诞生;出身,血统;起源;消失94. birthday [b?:θdei] n.生日;(成方)纪念日95. biscuit [biskit] n.饼干,点心96. bit [bit] n.一点,一些;小块,少量;片刻; [计]位,比特97. bite [bait] v./n.咬,叮 n.一口98. bitter [bit?] a.(有)苦(味)的;苦痛的,厉害的99. bizarre [bizɑ:] adj.异乎寻常的,稀奇奇怪的 100. black [bl?k] a.黑(色)的;黑暗的 n.黑(色);黑暗;黑人考研英语大纲5500词汇表精选篇31. carry [k?ri] v.运输,搬运;传送,传播;领,带2. cart [kɑ:t] n.(二轮货运)马车,手推车3. cartoon [kɑ:tu:n] n.漫画,幽默画;动画片4. carve [kɑ:v] v.(雕)刻5. case [keis] n.箱,盒,容器;状况,事实;病例;案件6. cash [k??] n.现金,现款 v.兑现,付(或收)现款7. cashier [k??i?] n.收银员,出纳员8. cassette [k?set] n.盒子;盒式磁带9. cast [kɑ:s, k?st] v.投,扔,掷,抛;铸造;投票;n.演员表10. castle [kɑ:sl, k?-] n.城堡;(国际象棋中的)车11. casual [k??ju?l] a.偶然的,碰巧的;临时的,非正式的12. casualty [k??ju?lti] n.伤亡人员;受害人;损失的东西;急诊室13. cat [k?t] n.猫;猫科动物;14. catalog [k?t?l?ɡ] n.(catalogue)名目(册) v.编目(录)15. catastrophe [k?t?str?fi] n.大灾难;(悲剧)结局16. catch [k?t?] v.捕获,捕获;赶上;感染;理解,听到17. category [k?tiɡ?ri] n.种类,部属,类目;范畴,类型18. cater [keit?] vi.(for/to)满意,迎合;(for)供应饮食及服务19. cathedral [k?θi:dr?l] n.大教堂20. Catholic a.天主教的 n.天主教徒21. cattle [k?tl] n.牛;牲口,家畜22. cause [k?:z] n.缘由;事业,大事,奋斗目标 v.使产生,引起23. caution [k?:??n] n.谨慎;留意(事项),警告vt.劝…当心24. cautious [k?:??s] a.(of)当心的,谨慎的25. cave [keiv] n.洞,穴26. cease [si:s] v./n.停止,中止27. ceiling [si:li?] n.天花板;(规定价格、工资等的)最高限额28. celebrate [selibreit] vt.庆祝;颂扬,赞美vi.庆祝,过节29. celebrity [silebr?ti] n.名人,名流;闻名,名声,名望30. cell [sel] n.细胞;小房间;蜂房;电池31. cellar [sel?] n.地窑,地下室32. cement [siment] n.水泥;胶泥,胶接剂 v.胶合;巩固,加强33. cemetery [semit?ri] n.坟墓,墓地,坟场34. census [sens?s] n.人口普查(调查)35. cent [sent] n.分(币);百 per cent百分之36. centigrade [sentiɡreid] n./a.摄氏温度计(的);百分度(的)37. centimetre [senti,mi:t?] n.(centimeter)厘米38. central [sentr?l] a.中心的,中央的,中枢的;主要的39. centre [sent?] n.中心,中央,中间 vt.集中 vi.以..为中心40. century [sent?uri] n.世纪,(一)百年41. cereal [si?ri?l] n.加工而成的谷类食物;谷类植物,谷物42. ceremony [serim?uni] n.典礼,仪式;礼节,礼仪43. certain [s?:t?n] a.某,某一,某些;(of)肯定的,确信的,牢靠的44. certainly [s?:t?nli] ad.肯定,必定,无疑;当然,行45. certainty [s?:t?nti] n.必定,确定;必定的事46. certificate [s?tifikeit] n.证(明)书,执照47. certify [s?:tifai] vt.证明,证明;发证书(或执照)给48. chain [t?ein] n.链(条);(pl.)镣铐;一连串 v.用链条拴住49. chair [t?ε?] n.椅子;(会议的)主席 vt.当…的主席,主持50. chairman [t?ε?m?n] n.主席,议长,会长,董事长51. chalk [t??:k] n.粉笔,白垩52. challenge [t??lind?] n.挑战(书);艰难任务,难题 v.向…挑战53. chamber [t?eimb?] n.房间,室;会议室;议院;(动物体内)腔室54. champagne [,??mpein] n.香槟酒;微黄色55. champion [t??mpi?n] n.冠军,得胜者;拥护者,斗士56. chance [t?ɑ:ns, t??ns] n.机会;可能性;偶然性,运气v.碰巧,偶然发生57. chancellor n.(英)大臣;法官;(德、奥)总理;高校校长58. change [t?eind?] n.转变,变化;零钱 v.更换,调换,交换;转变59. channel [t??n?l] n.海峡,水道;信道,波道;路线,途径60. chaos [kei?s] n.混乱,紊乱61. chap [t??p] n./v.(皮肤)变粗糙;发痛;n.小伙子62. chapter [t??pt?] n. 章;回,篇63. character [k?r?kt?] n.性格,品质,特性;人物,角色;字符,(汉)字64. characteristic [,k?r?kt?ristik] a.(of)特有的,独特的 n.特征,特性65. characterize [k?r?kt?raiz] v.(characterise)表示…的特性;描述…特性66. charge [t?ɑ:d?] v.索(价);控告;充电 n.(pl.)费用,代价;电荷67. charity [t??r?ti] n.慈善(团体),慈爱,施舍68. charm [t?ɑ:m] n.吸引力,魅力 v.迷人,(使)沉醉;施魔法于69. chart [t?ɑ:t] n.图表;航海图;航行图 vt.绘图表,制图表70. charter [t?ɑt?] v.租船,租车,租用飞机;n.宪章,特许状71. chase [t?eis] v./n.追赶,追求72. chat [t??t] v./n.闲谈,谈天73. cheap [t?i:p] a.廉价的;低劣的,不值钱的74. cheat [t?i:t] v.哄骗;作弊 n.骗子;欺诈,哄骗行为75. cheek [t?i:k] n.脸蛋,脸76. cheer [t?i?] v.(使)兴奋,(使)兴奋 v./n.喝彩,欢呼77. cheese [t?i:z] n.干酪,乳酪78. chef [?ef] n.(餐馆等的)厨师长,厨师79. chemical [kemik?l] a.化学的 n.(pl.)化学制品,化学药品80. chemist [kemist] n.化学家;药剂师81. chemistry [kemistri] n.化学82. cheque [t?ek] n.(check)支票,空白支票;总收入83. cherish [t?eri?] vt.抱有,怀有(盼望等);爱惜,抚育;珍爱84. cherry [t?eri] n.樱桃(树)85. chess [t?es] n.棋,国际象棋86. chest [t?est] n.胸腔,胸膛;箱,柜87. chew [t?u:] v.咀嚼;思考88. chicken [t?ikin] n.鸡肉;鸡,小鸡,小鸟89. chief [t?i:f] a.主要的,首要的 n.首领,领袖90. child [t?aild] n.( [pl.] children)小孩,儿童,儿女91. childhood [t?aildhud] n.幼年,童年92. chill [t?il] n.寒冷,寒气,寒战 v.使寒冷93. chimney [t?imni] n.烟囱94. chin [t?in] n.下巴,颏95. china n.瓷器96. chip [t?ip] n.切屑,碎片;(土豆等的)薄片;集成电路块97. chocolate [t??k?lit] n.巧克力(糖),赭色98. choice [t??is] n.选择(机会),选择,选择项;入选者 a.精选的99. choke [t??uk] v.窒息,噎住;闷塞,堵塞,堵塞100. choose [t?u:z] v.选择,选择;甘愿考研英语大纲5500词汇表精选篇41. dependent [dipend?nt] a.依靠的,依靠的,从属的;随…而定的2. depict [dipikt] v.描绘;描写,描述3. deposit [dip?zit] v.存放;使沉淀;付(保证金) n.存款;沉积物4. depress [dipres] v.压抑,降低;使懊丧,压下5. deprive [dipraiv] vt.剥夺,夺去,使丢失6. depth [depθ] n.深,深度,浅显,深刻7. deputy [depjuti] n.代理人,代表 a.副的,代理的8. derive [diraiv] v.取得;导出;引申;来自;源自;出自9. descend [disend] v.下来,下降;遗传(指财产,气质,权利)10. descendant [disend?nt] n.子孙,后代11. descent [disent] n.下降,降下;斜坡;血统,家世12. describe [diskraib] v.描述,形容13. description [diskrip??n] n.描写,形容;种类14. desert [dez?t] n.沙漠,不毛之地 v.抛弃,遗弃;擅离,开小差15. deserve [diz?:v] v.应受,值得16. design [dizain] v.设计;构思;绘制;图案;企图 n.设计,图样17. designate [deziɡneit] v.指明,指出;任命,指派18. desirable [dizai?r?bl] a.值得做的;合意的,称心的;期望得到的19. desire [dizai?] v./n.愿望,欲望,要求20. desk [desk] n.书桌,办公桌,服务台21. desolate [des?l?t, des?leit] a.荒芜的;孤独的v.使荒芜22. despair [dispε?] n.无望;绝望;令人绝望的人(事物)v.无望23. despatch [disp?t?] n./v.(dispatch)派遣;发送 n.急件;新闻报道24. desperate [desp?r?t] a.不顾一切的,铤而走险的;无望的,危险的25. despise [dispaiz] v.轻视,蔑视26. despite [dispait] prep.不管,不顾27. dessert [diz?:t] n.正餐后的水果或甜食28. destination [,destinei??n] n.目的地,终点29. destiny [destini] n.命运;天数,天命30. destroy [distr?i] v.破坏,摧毁,毁灭31. destruction [distr?k??n] n.毁坏,毁灭(的缘由)32. destructive [distr?ktiv] a.破坏性33. detach [dit?t?] vt.分开, 分别, 分遣, 派遣(军队)34. detail [di:teil, diteil] n.细节,详情 v.详述35. detain [ditein] v.耽搁;扣押,拘留36. detect [ditekt] v.察觉,发觉,侦察,探测37. detective [ditektiv] n.侦探38. detector [ditekt?] n.发觉者,侦察器,探测器,检波器,检电器39. deteriorate [diti?ri?reit] v.(使)恶化,(使)变坏40. determine [dit?:min] v.决心,打算;确定,限定41. develop [divel?p] v.进展,开发,研制;显现,显影;发育,生长42. deviate [di:vieit, di:vi?t] v.(from)背离,偏离43. device [divais] n.装置,设备,仪表;方法,设计44. devil [dev?l] n.魔鬼45. devise [divaiz] vt.设计;创造;图谋;作出(方案);想出(方法)46. devote [div?ut] v.(to)奉献,致力47. dew [dju:, du:] n.露水48. diagnose [dai?ɡn?uz] vt.诊断(疾病);推断(问题)49. diagram [dai?ɡr?m] n.图表;图解50. dial [dai?l, dail] n.钟(表)面,刻度盘,拨号盘 v.拨号,打电话51. dialect [dai?lekt] n.方言52. dialog [dai?l?ɡ] n.(dialogue)对话,对白53. diameter [dai?mit?] n.直径54. diamond [dai?m?nd] n.金钢石,钻石;菱形55. diary [dai?ri] n.日记,日记簿56. dictate [dikteit, dikteit] v.口授;(使)听写;指令,指示,命令;57. dictation [diktei??n] n.听写,口述;命令58. dictionary [dik??n?ri] n.词典,字典59. die [dai] vi.死,死亡;(草木)枯萎,凋谢;渴望60. diet [dai?t] n.饮食,食物61. differ [dif?] v.(from)与…不同;(with)与…看法不同62. difference [dif?r?ns] n.差别,差异,分歧63. different [dif?r?nt] a.差异的,差异的,不同的64. differentiate [,dif?ren?ieit] v.区分,区分;(使)不同65. difficult [difik?lt] a.困难的,困难的66. difficulty [difik?lti] n.困难,逆境,难题67. diffuse [difju:s] v.集中;传播 a.(文章等)冗长的,漫无边际的68. dig [diɡ] v.挖,掘69. digest [did?est] vt.消化;领悟,融会贯穿 n.文摘,。
DVS-100 200安装指南说明书

DVS-100/200 Installation GuideDVS-100/200 can be installed on any system running the Ubuntu 14.04 64 bit Linux operating system, the guide below covers some common installation scenarios.The installation procedure for DVS-100 and DVS-200 is the same. Once installed the software will be running in free mode (DVS-100) you must install a valid licence to enable DVS-200 features.ContentsSystem resource recommendations (2)On-Premise Installations (2)Cloud hosting installations (2)Hosting Examples (2)Installation Walkthroughs (3)Digital Ocean (3)Installation on Amazon AWS Cloud (10)Generic Installation Instructions (All Providers) (16)Automated Script (16)Manual installation (Advanced Users) (16)Prerequisites (16)Packages (16)System resource recommendationsThe guide below makes some recommendations on system specifications, please use these as guidelines only. We assume one 1Mbps video stream with 96Kbps audio, the max viewer count is per instance (per server).On-Premise Installations8GB of RAM and a SSD (Solid state drive) is recommended for larger audiences, approximate network limitations are as below.For encoding / transcoding HD video we recommend a 4 core 7th generation i7 CPU and 8GB ram at minimum.Cloud hosting installationsHosting ExamplesDigital OceanDigital Ocean is ideal for scenarios with low viewer counts.All Digital Ocean instances share a 1Gbps connection to the internet, Digital Ocean recommend consistently not exceeding 300Mbps I/O.Massive GridMassive grid offer affordable dedicated servers with dedicated 1Gbps connectivity.Installation WalkthroughsDigital OceanVisit and sign up for a new accountOnce you have created your account click the ‘Create Droplet’ buttonYou will see the page below.First give your Droplet a hostname, here I have chosen DVSS.Next choose a size, the size required depends on how many users you need to serve. Use the guide at the begging of this document to help with selection.Next select the region closest to you for best performance.Finally you need to select an image, please choose Ubuntu 14.04 x64.Ignore the ‘Available Settings’ and ‘Add SSH Keys (optional)’ sections and c reate the droplet.Once the droplet has been created you will see the page below. We are now ready to install the stream server software.Click the blue ‘Console Access’ button, you will see the page belowHit return on the keyboard and you will be asked to login. The username and password for your server will have been e-mailed to you by Digital Ocean. Enter your username and hit the return key, then enter your password and again hit the return key to login (please note you will not see any characters appear on screen when typing your passwords).You will be asked to change your password the first time you login, please ensure you use a password that is at least 10 characters long it should be uppercase and lowercase and contain characters such as $%&@# for security.Once logged in type the commands below in order, hit return after each command.wget /install-dvss.shbash install-dvss.shYou will see the message below once the installation is complete.Now simply enter the IP address displayed into a web browser to access the login page.The default credentials are:User: adminPassword: 000000After logging in you will see the software is running in free (DVS-100) mode, to enable DVS-200 features you need a valid licence.Installation on Amazon AWS CloudVisit and sign up for a new accountOnce you have created your account sign in and you will see the page belowFirst change the region in the top right corner to the region where you would like to setup your cloud serverNow click the ‘EC2’ link under compute to the left of the pageClick t he ‘Launch Instance’ buttonSelect the Ubuntu 14.04 64 bit image as shown belowNow select your instance type, the size required depends on how many users you need to serve. Use the guide at the begging of this document to help with selection.One yo u have selected and instance size proceed and click the ‘Review and Launch’ button.Click the ‘Edit security groups’ linkAdd two new custom TCP rules for ports 80 and 1935 as shown below.Click the ‘Review and launch’ button againClick the ‘Launch’ buttonYou will see the prompt blow. Choose to create a new key pair and give the key pair a name.Click the ‘Download Key Pair’ button and save the file somewhere safe (you will need it later) before clicking the ‘Launch Instance’ button. You will see the page below, click the ‘View Instances’ button to proceed.Select ‘Connect’ from the actions menuYou will see the prompt below. Follow the instructions to connect to your instance via SSH.Once connected via SSH execute the following commands on the server.wget /install-dvss.sh -O - | bashOnce installation is complete enter the instances public IP or public DNS into a web browser to connect to the DVS-200 web interface.The default credentials are:User: adminPassword: 000000After logging in you will see the software is running in free (DVS-100) mode, to enable DVS-200 features you need a valid licence.Generic Installation Instructions (All Providers)Automated ScriptThe following command can be executed on any system running the Ubuntu 14.04 64 bit Linux operating system.Ensure the system has internet access and execute the commands below as the root user to install DVS-200.wget /install-dvss.sh -O - | bashAfter a successful installation the stream server’s web interface will be running on port 80. Manual installation (Advanced Users)Prerequisiteslibasound2 libyaml-0-2 libass4 libmp3lame0 libopencore-amrnb0 libopencore-amrwb0 libopus0 libpulse0 libsdl2-2.0-0 libsoxr0 libspeex1 libva-drm1 libva-x11-1 libva1 libvdpau1 libwavpack1libx264-142 libxcb-shape0 libxcb-shm0 libxv1 libxvidcore4 libluajit-5.1-2 libluajit-5.1-common libdouble-conversion1 liblz4-1 libpq5 libsnappy1 php5-fpm php5-cli binutils ghostscript gsfonts imagemagick-common libavahi-client3 libavahi-common-data libavahi-common3 libboost-context1.54.0 libboost-filesystem1.54.0 libboost-program-options1.54.0 libboost-regex1.54.0 libboost-system1.54.0 libboost-thread1.54.0 libc-client2007e libcups2 libcupsfilters1 libcupsimage2 libfftw3-double3 libgd3 libgflags2 libgoogle-glog0 libgs9 libgs9-common libijs-0.35 libjasper1 libjbig0 libjbig2dec0 libjemalloc1 libjpeg-turbo8 libjpeg8 liblcms2-2 liblqr-1-0 libltdl7 libmagickcore5 libmagickwand5 libmcrypt4 libmemcached10 libmysqlclient18 libonig2 libpaper-utils libpaper1 libsqlcipher0 libtbb2 libtiff5 libunwind8 libvpx1 libxpm4 libxslt1.1 mlock mysql-common poppler-dataPackages/updates/debian/hhvm_3.15.2~trusty_amd64.deb/updates/debian/ffmpeg_3.1.4+git1~trustyubuntu1_amd64.deb /updates/debian/nginx-dvss_1.8.0-4ubuntu34_amd64.deb/updates/debian/nginx-dvss-webui_1.12ubuntu25_all.deb。
卡尼达尔方向:罗琳·赫姆·罗琳·托朗斯的作品说明书
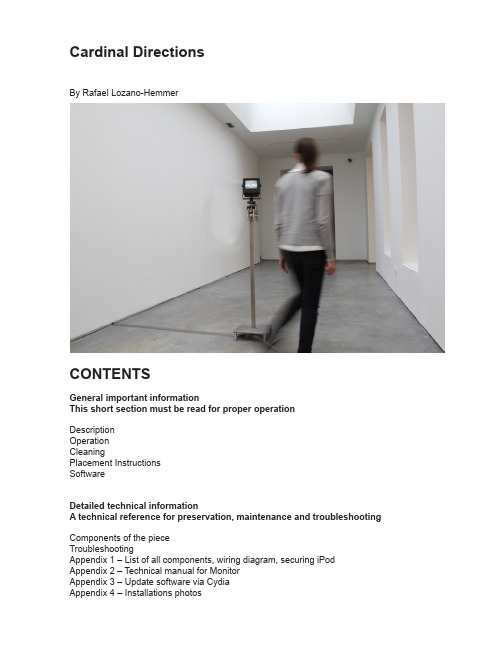
Cardinal DirectionsBy Rafael Lozano-HemmerCONTENTSGeneral important informationThis short section must be read for proper operationDescriptionOperationCleaningPlacement InstructionsSoftwareDetailed technical informationA technical reference for preservation, maintenance and troubleshootingComponents of the pieceTroubleshootingAppendix 1 – List of all components, wiring diagram, securing iPod Appendix 2 – Technical manual for MonitorAppendix 3 – Update software via CydiaAppendix 4 – Installations photosGeneral important informationCardinal Directions (2010)By Rafael Lozano-HemmerTechniqueMonitor, stepper motor, iPod touch, motion sensors, custom electronics, stainless steel stand. DimensionsThe piece has a footprint of 12 inch by 12 inch and is 45 inches high.Electrical detailsThe piece needs 100W peak consumption, 20W average, 110 to 240V.EditionEdition of 6 + 1 APDescriptionA surveillance monitor shows an extract of Vicente Huidrobo´s poem “Altazor” (1919-1931). Refering to the geography of his native Chile, Huidobro wrote “The four cardinal directions are three: North and South”. When a presence is detected by infrared sensors, the monitor starts to rotate. As the poem is “geolocated” it always aligns itself to the cardinal points, and the public must walk around the piece in order to read it, like a kind of periscope.Operation1. Take the piece out of the crate. The iPod is stored separately in the crate. Find it and connect it to the iPod cable under the motor unit. Also make sure none of the colored cables inside the motor unit are in the way of the rotating parts. Simply rotate the monitor by hand a few turns and take a close look at the piece’s mechanical parts.2. Connect the piece to electrical power via an extension cable. CardinalDirections comes with a 3-prong power plug (NEMA 5–15) (see image). You willneed to use an adapter to connect this plug to a non-American extension cable.You may connect the piece to 100-120V 60Hz (American) or to 210-240V 50Hz (European) current, as all the gear inside has auto switching power supplies.3. To turn the piece ON, plug the above mentioned power plug in to the walloutlet. The iPod will prompt you with a button that says “Tap to Unlock“. Aftertaping this button, next tap the Cardinal icon in the iPod’s dock.It is also possible to start the software by holding the home button until the screen with the “Tap to Unlock“ screen is gone and the home screen is shown. Then release the home button and again press and hold it until the software starts.4. To turn the piece OFF, unplug the power plug from the wall. After one minute the iPod software will exit. After another 5 minutes the iPod screen will go black and the iPod enters the hibernation mode.Cleaning and MaintenancePlease do not clean the iPod’s touch screen surface with Windex or soap. Use a lint-free cloth and screen liquid cleaner, such as Kensington Screen Guardian found in computer stores. For the metal base use normal soapy water or spray on cleaners to clean the metal.On a regular basis check that all the metal screws and nuts which hold the motor, metal plates and other elements in place are tight.Placement InstructionsMake sure the metal base is level. Adjust the length of all four feet by loosening the set-screws and sliding the inner cylinder in or out.The piece can be placed facing any direction.The software will later be used to set the north cardinal direction.The piece should not be closer than 2 meters from any wall as this will hinder people from walking around the piece.Because the piece uses infrared motion sensors, any human size heat source will trigger its rotation. If such behavior is noticed, check to see if a large sunny window, heater, fireplace etc. is in a 5 meter range of the piece. Try moving the piece further away from those elements. Use a cable channel or tape to secure the power cable running from the piece to the wall plug.NoteDo not update the iPod’s operating system. This could cause the piece to stop functioning.Software version 3.0 running on iPod touchThe piece includes custom-made software that runs on an iPod touch placed underneath the motor unit. There are some software options that may be useful if you would like to optimize the performance of the system. To change settings in the software, place two fingertips side by side on the iPod’s screen until you see the first settings panel appear as shown in the image below.Leave your two fingers on the screen for about 3 seconds.startup routine:the motor/ monitor rotate to thezero positioninteraction mode:the movements of theparticipants activate the pieceand it starts rotating for 10seconds.language settings:english, spanish1. language — Once the new settings panel appears, remove your fingers from the screen. At this point the monitor should quickly rotate to the zero position. Now tap the screen with one finger to change the language in which you would like the main poem will be displayed.To switch to the next settings panel, place two fingers on the screen again for at least 3 seconds.2. north — As you can see during the normal interaction mode, there is a line with letters S, SW, W, NW, N, NE, E, SE at the top of the screen. When highlighted these letters indicate the cardinal direction that should currently be faced by the monitor. This panel is where you can set the true north for your location. Tap the screen to rotate the monitor step by step (10º steps) until it faces the direction you know to be north.To switch to the next settings panel, place two fingers on the screen again for at least 3 seconds.3. default position — If no one interacts with the piece for 10 seconds it will first stop rotating. After an additional 10 seconds it will rotate to its default resting position and the screen will go dark. This feature allows the piece to face the direction of people entering the exhibition space.The text is aligned such that people will see the beginning of the poem in this position.north settings:align the piece to the true northdefault position:align the piece to its restingposition4. quit – There are two ways to stop the piece. The easiest and recommended one is to pull the main power plug. This will shut off the power to the monitor, motor and electronics. The iPod will go in to hibernation mode after about 6 min.You can also just press the iPod’s home button, while the piece is running. This will quit the software and take you to the iPod’s home screen.To turn the piece back ON plug the main power plug back in to the wall outlet. The iPod will prompt with a button that says “Tap to Unlock“. After taping this button, tap theCardinal icon in the iPod’s dock.Detailed technical informationComponents of the pieceMetal StandThe stand is made of stainless steel, 31cm x 31cm base, 145cm highMonitorThe piece uses a surveillance TV with a satin black plastic housing.iPod touchThe piece uses a jail broken, 2nd generation, 8.0 GB iPod touch, running the 3.1.3 firmware. The iPod communicates with the micro-controller over its serial port.Montion SensorsThe piece uses eight motion sensors which are pointed towards the eight cardinal directions (N, NE, E, SE, S, SW, W, NW)Motor + GearsThe piece uses a stepper motor with controller boards and two metal gears with a 48:10 ratio. All these components are combined in a setup we call spinmaster.Custom-made ElectronicsAn Arduino Nano micro-controller with an Atmel ATmega328 chip is running custom firmware.Troubleshootingif:- you tap the Cardinal icon and the software opens and closes right awaythen:Hold the iPod’s home + power button for about 5 seconds.A new panel will appear and ask you to “tap/slider to power off”.Do that.For a short time you will see a black screen with a white spinning icon.Once that is gone, restart the iPod by pressing the top power button.If the iPod gets stuck at the screen with the spinning icon, keep holding thepower and home button for about 15 seconds until the iPod goes dark.Restart the iPod by pressing the top power button.if:- the piece is not reacting to people’s presence- no words appear on the screen- the motor rotates continuously fast, does not stop, especially after the startup routine- the motor stutters back and forth, especially after the startup routinethen:After having plugged the piece to the main power, please wait a couple of minutes. The piece might catch itself and start to operate normally.If the problem persists, press the iPod’s home button to quit the software. Now press the Cardinal icon in the iPod’s dock to restart the piece.If the problem still persists, unplug the main power. Also press the iPod’s home button if the software is still running.Now re-plug the main power and start the software.if:- the piece reacts correctly to people’s presence but the text is not visible on the monitorthen:Go to page 7 of the monitor’s manual.If the monitor is power properly power indicator #2 should be illuminated.Press power switch #1 to see if that turns the power indicator #2 and monitor back on.Try adjusting the brightness #4 and/or contrast #3.Press buttons #6, #7 and/or #8 to select the right video input channel.then:This means the iPod has lost the setting that forces it to output it’s video signal to the monitor. To check this settings:Navigate to the iPod’s setting panel.Scroll down until you see the TV Out option. Tap it.You should see the panel below.Ensure that Enable TV Out and Force TV Out are ON.You should not need to change any of the other numbers. They are displayed here just for referencing reasons.We are currently using the TV Out Plugin v1.70 by c00ni, based on TVOut by ashikase.then:Hold the iPod’s home + power button until the iPod shuts off.A new panel will appear and ask you to “tap/slider to power off”.Keep holding the two buttons until the screen is black.Restart the iPod by pressing the top power button.Navigate to the TVOut settings panel. (see above)Turn TVOut off by sliding “Enable TV Out“ and “Force TV Out“ to their off positions.Start the Cardinal Directions software.Now you should see the piece perform correctly but the text will only be seen on the iPod’s screen.Now quit the software, navigate back to the TV Out settings and turn it back on.Close the settings panel and restart the Cardinal Directions software.Appendix IList of componentsiPod touch, Apple, A1288, 8GB memory, firmware 3.0, 3.1.2, 3.1.3 (june 1st 2010)custom stainless steel stand (12”x12”base, 2” feed of ground, 39.5” rectangular pole,162mmx92mm top plate)TV, 5.5 inch CRT, satin black car rear view monitorStepper controller, Trinamic, TMCM-110-42 with RS485,Stepper motor, Soyo, SY42STH38-1206B, 4V 1.2A 36oz-in Unipolar Stepper Motor (double shaft)Rotary Encoder, CUI Inc, AMT103-V, 500 lines pprRotary Encoder cable, CUI Inc, CUI-435-1FTTiming Pyllies, martinsprocket, 48 teeth, 10 teeth 10XL037Timing Beltcustom hollow shaftSlip ring, MOOG, AC-6023-6Power supply, 24 DC, 6.25amp, 120-240V auto switching, DT150PW240CPower cable DC extension, Tensility International Corp, CA-2216Arduino nano atmega 3288 x Motion sensors, zilog, ePIR Zdots SBCDc power converter, dimension engineering,DE-SW033 (3.3V), DE-SW050 (5V), DE-SWADJ (12V)RS485 transceiver, Texas Instruments, SN75176BP8-DIP chips socketPC Board, Vector Electronics, 8016, 2-SIDE PPH 6.0X9.0Low profile female header, Samtec Inc, SLW-150-01-S-SiPod Connector Male Style 1Polarizing connectors, Tyco Electronics, MTA-100 SeriesPhono (RCA) plug, CUI Inc, RCP-011Securing the iPod TouchThe iPod should be placed in the bottom compartment as shown in the images above. You will need to remove one of the two middle set screws. This will allow you to slide the iPod in place. Once the set screw and aluminium bushing are back in place the iPod is secure and cannot slide out.Metal Basebottom plateipod plateciruict boardmotor basebottom plate ipod plate main base main base1.25” rectangular pole feet39.5”40 mm 82 mm 16 mm 6 mm 16 mm 5”28 mm 18 mm 6 mm 18 mm 162 mm 58 m m 30 m m 30 m m 58 m m 92 m m bottom plate ipod plate ciruict board motor base cardinal directions, metal baseCircuit board and cablingAppendix IIAppendix III– Tap the Edit button at the top right of the screen.– Tap the Add button at the top left of the screen.– A pop up window will ask you to enter the following URL:/software/seismoscope??? (the ??? stand for version #)– Tap the “Add Source” button.– Tap the “Done” button at the top right of the screen.– Tap the ““ row in the section “Entered by User“– Tap the “Seismoscope“ row.– Compare your current version number with the one displayed in this screen. (ignore the number after the minus sign 2.0.0 - 1). Tap the install button if the two version number are different.– Tap the confirm button. The screen will switch to a black screen with white writing.– While on the black screen you might be prompted with a couple of error message. Tap Okay. It might take a while before the pop up message disappears.– Press the Home button to get back to the home screen.– Tap the Settings icon in the Dock.– Navigate to the Wi-Fi Network settings and tap the name of your current network. On the top tap “Forget this Network“.- Tap “Wi-Fi Networks“ on the top left. This will take you back to the list of available networks.- Tap the “seismoscope“ network. Make sure the Seismoscope table has power, since the table serves the network.– You might be prompted for a password which is: hemmer1234567– Tap on the arrow towards the right of the word “seismoscope“.– Tap the “Static” button.– Double check the IP Address (10.0.1.6), Subnet Mask (255.255.255.0) and Router (10.0.1.1).– Once connected, press the Home button.– Tap the Seismoscope icon in the Dock. Check the version number that is now displayed in the Seismoscope software.Appendix VIInstallations shots。
Sendyne SIM100MOD 隔离监控器安全指南说明书

Safety Manual for Sendyne SIM100MOD Isolation MonitorThis document describes how to use the Sendyne SIM100MOD isolation monitor in a safety related system. ContentsSafety Manual for Sendyne SIM100MOD Isolation Monitor 1Introduction (2)Sendyne SIM100MOD overview (2)Safety functions and diagnostics overview (3)Target applications (4)Assumptions (6)Custom development (6)Safety documentation (6)Audits and certification (6)Device operating states (6)Product lifecycle support (7)Appendix (8)Proper connection to the target system (8)Revision history (10)List of figuresFigure 1: SIM100MOD functional diagram (3)Figure 2: The boundary diagram of SIM100MOD as SEooC in EV implementations (4)Figure 3: The boundary diagram of SIM100MOD as SEooC in EV implementations (5)Figure 4: Operating states of the SIM100MOD (7)Figure 5: Proper connection to IT power system terminals (8)Figure 6: Proper connection at two distinct point to the chassis (8)Figure 7: Presence of Y-capacitors is a requirement for proper function of the SIM100MOD. (9)IntroductionThe system and equipment manufacturer or designer intending to use this product is responsible to ensure that their system incorporating Sendyne’s SIM100MOD meet all applicable safety, regulatory and system level performance requirements. All information presented in this document is for reference only. Users understand and agree that their use of SIM100MOD in safety-critical applications is entirely at their risk, and that user (as buyer) agrees to defend, indemnify, and hold harmless Sendyne from any and all damages, claims, suits, or expense resulting from such use.This safety manual provides information to assist system developers in creating safety-related systems incorporating the Sendyne SIM100MOD isolation monitoring device. This document contains:•Overview of the SIM100MOD architecture•Overview of the safety architecture for management of hardware failures•Assumptions of UseSendyne assumes that the user of this document has a general familiarity of the SIM100MOD. This document is intended to be used in conjunction with the relevant datasheet and application notes.Sendyne SIM100MOD overviewThe SIM100MOD is an electrically isolated device that when connected properly to an idle or active high voltage IT power system (floating ground) can estimate the resistive and capacitive paths between each power rail of the IT system and a third reference point. The SIM100MOD can communicate through CAN bus (250 or 500 kbits/s) and when interrogated by a host it can provide estimates on the values of each resistive and capacitive path.The SIM100MOD, based on information programmed by the host for the designed maximum voltage of the IT power system, will calculate a value for the minimum resistance path between the two IT power system rails and the third voltage reference point, expressed in Ohms/Volt (max designed voltage). In addition, it will estimate the total energy that can be potentially stored in the IT power system capacitances. If the CAN bus host fails to provide information on the maximum IT power system voltage, the SIM100MOD will calculate these values based on the maximum voltage observed during its operation.The SIM100MOD power input accepts any supply voltage between 4.8 V and 53 V. The input voltage is pre-regulated and then stepped down through a DC/DC converter feeding through galvanically isolated inputs the +5 V IC supply and the 12.5 V excitation voltage source supply.The SIM100MOD safety architecture includes a watchdog timer, CRC check on internal non-volatile program memory, diagnostics for proper connections of chassis and IT power system terminals, monitoring of the unregulated power supply voltage level for the main IC before local voltage regulator (LDO), environment temperature monitoring and excitation pulse voltage monitoring. In addition, theSIM100MOD safety architecture monitors the voltage divider values for chassis, positive and negative voltage connections and provides a visual heartbeat signal indicating proper IC operation.All estimates of isolation resistances and capacitances are submitted along with an uncertainty percentage value. This value defines the interval within which the actual value lies with a probability of 95%.Figure 1: SIM100MOD functional diagramSafety functions and diagnostics overviewThe SIM100MOD is intended for use in automotive and industrial safety-relevant applications. All components used are automotive rated.HardwareThe following list of monitoring functions are implemented in the SIM100MOD.•V U, SUPPLY monitor•V X, SUPPLY monitor•V X1 connection monitor•V X2 connection monitor•V X1 voltage divider ratio monitor•V X2 voltage divider ratio monitor•V CH1 and V CH2 connections monitor•V X_CH voltage divider ratio monitor•V X_CH Excitation Voltage Source voltage value monitor•V X_THR environment temperature monitorUpon diagnosing a hardware error, the SIM100MOD will set the appropriate flags and enter a SAFE state.SoftwareOn the RESET state the SIM100MOD performs CRC check on the non-volatile memory. During active operation a watchdog timer ensures proper program flow. In addition, every estimate on the isolation state of the monitored IT power system is accompanied by the uncertainty value of this estimate.Target applicationsThe Sendyne SIM100MOD has been designed to be used as an element for the isolation safety system in applications such as:•Automotive•Charging stations•Industrial high voltage ungrounded systemsFig. 2 and Fig. 3 show the boundary diagram for the SIM100MOD as a SEooC (Safety Element out of Context) in two different applications.Figure 2: The boundary diagram of SIM100MOD as SEooC in EV implementationsFigure 3: The boundary diagram of SIM100MOD as SEooC in EV implementationsAssumptionsThe following table lists the assumptions made for safe employment of the SIM100MOD is a safety critical system.ID Type Assumed RequirementAR01 Assumed Requirement The SEooC is defined as the SIM100MOD playing a role as an isolationmonitoring element as shown in Fig. 2 and Fig. 3AR02 Assumed Requirement Thermal environment is between -40 o C and +105 o C (Temperature range islimited by connector thermal specifications. For SIM100MODAZ1, operatingrange is -40 o C to +125 o C )AR03 Assumed Requirement The IT Power System voltage monitored by the SIM100MOD will varybetween 15 V and 962 VAR04 Assumed Requirement The IT Power System is connected to chassis through Y-Capacitors of at least100 nF on each side of the power supplyAR05 Assumed Requirement The SIM100MOD-xxx is supplied with proper power according to thespecifications of the SIM100MOD datasheetAR06 Assumed Requirement Safety Integrity Level is ASIL BAR07 Assumed Requirement No other isolation monitoring device is active in the monitored system Table 1: Assumed Requirements for SIM100MOD as a SEooCCustom developmentThe SIM100MOD has been developed as a safety element out of context and it is offered as a commercial off-the-shelf product. Safety requirements used were based on Sendyne’s understanding of the safety requirements of potential applications. Sendyne can customize the product in order to meet specific customer safety requirements through a development interface agreement (DIA). To request customization contact ****************Safety documentationVerification and validation of the SIM100MOD safety features was performed through testing and computer simulation. Results of SIM100MOD testing following guidelines of different standards as well as the model used for SIM100MOD safety function testing can be made available at Sendyne’s discretion under an NDA (non-disclosure agreement)Audits and certificationSendyne has no plans to perform an external audit of the SIM100MOD to ISO 26262 or other standards. Documentation, including this manual can be made available to support customer system audit and certification. Forward any request for an independent audit to your sales contact or ****************. Device operating statesFig. 3 shows an overview of the operating states of SIM100MOD. Refer to the product datasheet and other documentation for details.Figure 4: Operating states of the SIM100MODProduct lifecycle supportThe SIM100MOD contains a safe bootloader capable of field upgrades through the CAN bus interface.AppendixProper connection to the target systemConnection to the IT power systemFigure 5: Proper connection to IT power system terminalsConnection to chassisThe SIM100MOD should connect through J1 at two separate chassis points. The SIM100MOD relies on this type of connection to detect proper connection to the chassis. If both leads from J1 are connected to the same point there is a possibility of an undetected disconnection. Such an event will jeopardize theSIM100MOD safety function.Figure 6: Proper connection at two distinct point to the chassisPresence of Y-capacitorsThe SIM100MOD relies on the presence of the ubiquitous Y-capacitors to perform its safety function. Absence of Y-capacitors with a minimum value of 100 nF will flag a connection error and lead theSIM100MOD into the SAFE state.Figure 7: Presence of Y-capacitors is a requirement for proper function of the SIM100MOD. The capacitors should be connected directly to the power lines. Connecting them on the SIM100MOD boardinstead would impair the ability of the monitor to detect disconnection from the monitored IT power lines.Revision historyDate Revision Changes11/15/2018 0.1 Initial release1/17/2019 0.2 Added image for proper connection of Y capacitors2/11/2019 0.2a Added image for isolation monitoring in charging stations. Addedassumed requirement for no other active isolation monitoring device in theIT power systemTable 2: Document revision historyInformation contained in this publication regarding device applications and the like, is provided only for your convenience and may be superseded by updates. It is your responsibility to ensure that your application meets with your specifications.SENDYNE MAKES NO REPRESENTATIONS OR WARRANTIES OF ANY KIND WHETHER EXPRESSED OR IMPLIED, WRITTEN OR ORAL, STATUTORY OR OTHERWISE, RELATED TO THE INFORMATION, INCLUDING BUT NOT LIMITED TO ITS CONDITION, QUALITY, PERFORMANCE, MERCHANTABILITY OR FITNESS FOR PURPOSE. Sendyne disclaims all liability arising from this in-formation and its use. Use of Sendyne devices in life support and/or safety applications is entirely at the buyer’s risk, and the buyer agrees to defend, indemni-fy and hold harmless Sendyne from any and all dam-ages, claims, suits, or expenses resulting from such use. No licenses are conveyed, implicitly or otherwise, under any Sendyne intellectual property rights.。
DS2208数字扫描器产品参考指南说明书
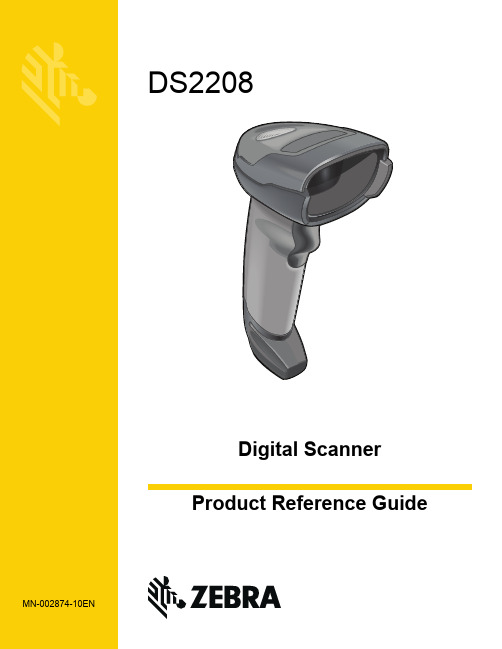
-05 Rev. A
6/2018
Rev. B Software Updates Added: - New Feedback email address. - Grid Matrix parameters - Febraban parameter - USB HID POS (formerly known as Microsoft UWP USB) - Product ID (PID) Type - Product ID (PID) Value - ECLevel
-06 Rev. A
10/2018 - Added Grid Matrix sample bar code. - Moved 123Scan chapter.
-07 Rev. A
11/2019
Added: - SITA and ARINC parameters. - IBM-485 Specification Version.
No part of this publication may be reproduced or used in any form, or by any electrical or mechanical means, without permission in writing from Zebra. This includes electronic or mechanical means, such as photocopying, recording, or information storage and retrieval systems. The material in this manual is subject to change without notice.
CBX100 LT 安装手册说明书

CBX100 LT Installation ManualThe CBX100 LT is a connection box which can be used as an accessory to facilitate system connections for installation and device replacement of several Datalogic family reading devices specifically designed to be used in subzero temperature applications.System cabling is made through spring clamp terminal blocks inside the CBX100 LT while the reading device is connected to the CBX100 LT through a 25-pin connector on the housing.A 9-pin connector placed inside the CBX100 LT facilitates connection between an external PC and the auxiliary serial interface of the reading device for configuration or data monitoring.GENERAL VIEWCBX100 LTFigure AFigure BSAFETY PRECAUTIONSATTENTION: READ THIS INFORMATION BEFORE INSTALLING THE PRODUCTPOWER SUPPLYThis product is intended to be installed by Qualified Personnel only.This device is intended to be supplied by a UL Listed NEC Class 2 power source. Each CBX100 LT supports only 1 single reading device + system accessories.OPENING THE CBX100 LTTo install the CBX100 LT or during normal maintenance, it is necessary to open it by unscrewing the two cover screws:MECHANICAL INSTALLATIONCBX100 LT can be mounted to various wooden or plastic surfaces using the two self-threading screws (3.9 x 45 mm) and washers provided in the package.Mounting to other surfaces such as concrete walls or metallic panels requires user-supplied parts (screws, screw anchors, nuts, etc). A mounting template is included in the package to facilitate hole drilling alignment.ELECTRICAL CONNECTIONS AND SETUPThe following figure shows a typical layout.Figure 2 – System LayoutThe dotted line in the figure refers to an optional (temporary) hardware configuration in which a portable PC can be quickly connected to the CBX100 LT (and consequently to the reading device auxiliary interface) through the internal 9-pin connector. This allows monitoring of the data transmitted by the reading device or configuration through the utility program (see the reading device Installation Manual for more details). The reading device auxiliary interface signals are also available on the internal spring clamp connectors.After making system cabling and switch settings, connect the reading device to the 25-pin connector on the CBX100 LT housing.Switch ON the CBX100 LT power switch (see Figure 3). The Power LED lights (blue) when the power connection has the correct polarity. The Power LED lights (red) in case of wrong polarity.After system functioning has been verified, close the CBX100 LT using the 2 cover screws.POWER SUPPLYPower is supplied to the CBX100 LT through the Vdc and GND pins provided on the spring clamp connector.The power switch (see Figure 3) switches the power supply ON or OFF for both the CBX100 LT and the connected reading device.POWER SUPPLYFigure 3 - Power Switch ON/OFF Positions and ConnectionsAlthough the CBX100 LT can be powered between 10 and 30 Vdc, the Subzero ∙ Using a device such as a screwdriver, push down on the lever directly next to the clamp (see Figure 4). ∙ Insert the wire into the clamp and release the lever. The wire will now be held in the spring clamp.5) Tighten the compression connector nuts so that the internal glands seal aroundthe cables.Figure 4 - System Cable ConnectionsFlexible stranded wire should be used and must meet the following specifications. All positions:24 - 16 AWG0.2 - 1.5 mm²The CBX100 LT spring clamp connector pinouts are indicated in the Pinout table.Refer to the reading device Installation Manual for signal details.PinoutsGroup Name FunctionVdc Power Supply Input Voltage +GND Power Supply Input Voltage - InputPowerEarth Protection Earth Ground +V Power Source – External TriggerI1A External Trigger A (polarity insensitive)I1B External Trigger B (polarity insensitive) ExternalTriggerInput-V Power Reference – External Trigger +V Power Source – Inputs I2A Input 2 A (polarity insensitive) I2B Input 2 B (polarity insensitive)GenericInput -V Power Reference – Inputs +V Power Source – Outputs -V Power Reference – Outputs O1+ Output 1 +O1- Output 1 - O2+ Output 2 + OutputsO2- Output 2 - TX Auxiliary Interface TXRX Auxiliary Interface RXAuxiliaryInterfaceSGND Auxiliary Interface Reference REF Network ReferenceID+ ID-NET™ Network +ID-NET™ ID- ID-NET™ Network -Network Shield Network Cable Shield RS232 RS485FD RS485HDTX TX+ RTX+ RTS TX- RTX-RX *RX+ CTS *RX- MainInterfaceSGND SGND SGNDThe input power signals Vdc , GND and Earth as well as the network signals REF , ID+, ID- and Shield are repeated to facilitate system cabling. In this way the power and network busses can enter and exit the CBX100 LT from different spring clamps but be physically connected together.POWER SOURCE JUMPER SETTINGSFor subzero applications input power is provided through the dedicated spring clamp connectors inside the CBX100 LT. Make sure that the Power source jumper is in the default position as shown in the figure below.power from clamps (default)Figure 5–Power Source Jumper SettingsSHIELD TO PROTECTION EARTH JUMPER SETTINGSThe network cable shield (Shield) can be connected to Earth Ground (Earth) either directly or through a filter circuit. If the jumper is left open, the network cable shield (Shield) is floating.Filtered Earth (default)floatingFigure 6– Shield to Protection Earth Jumper SettingsCHASSIS GROUNDING JUMPER SETTINGSThe reading device chassis grounding method can be selected by positioning a jumper (see Figure 7). In this way the reading device chassis can be connected to earth ground (only if pin Earth is connected to a good earth ground). The reading device chassis can alternatively be connected to the power supply ground signal (GND) or it can be left floating but, in this case, the jumper must be removed.to GNDfloatingFigure 7 – Chassis Grounding943215Indicator LEDs 1 Cover Screws (2)2 Subzero logo5 25-pin Decvice Connector 4 Compression Connectors (4) 3 Power switch (ON/OFF) 1 Auxiliary Port Connector 2 Mounting Holes (2) 3 RS485 TerminationResistance Switch 7 Spring Clamp Terminal Blocks 6 ID-NET™ TerminationResistance Switch 4 Indicator LEDs5 Chassis Grounding Selector10 Shield to Protection Earth Selector 9 Power Source Selector89-PIN READING DEVICE AUXILIARY SERIAL INTERFACEThe reading device auxiliary serial interface available on the internal CBX100 LT 9-pin connector can be used either for configuration or for data monitoring.Connections can be made to a PC or Laptop using a straight through cable or a USB-RS232 converter.The details of the connector pins are indicated in the following table:NETWORK BUS TERMINATIONID-NET™Figure 8 – ID-NET™ Termination Resistance SwitchThe ID-NET™ termination resistance switch enables or disables the insertion of the bus termination resistor for ID-NET™ network applications. RS485 HDFigure 9 – RS485 HD Termination Resistance SwitchMake sure the termination resistance switch is in the OFF position (default).INDICATOR LEDSblue/red yellow green yellow greenFigure 10 – Indicator LEDsThere are five Indicator LEDs which signal power and I/O activity and are visible from the CBX100 LT outside cover.The Power LED is blue when power is correctly applied to the CBX100 LT and the power switch is turned on.This LED is red if power polarity is incorrect. In this case the connected reading device and optional Backup Module are protected. If external I/O devices are powered through CBX100 LT (connected to +V/-V), they are not protected from polarity The remaining four LEDs signal activity on the relative I/O lines. Their meaning depends on the software configuration of the connected reading device.TECHNICAL FEATURESELECTRICAL FEATURESSupply Voltage10 to 30 Vdc * Consumption0.5 to 0.3 A Limited Current ConsumptionCBX + reading device consumption (see related manual) 2.5 A MaxUSER INTERFACELED IndicatorsPower On/Polarity Error (blue/red)Trigger (yellow) IN2 (green) OUT1 (yellow) OUT2 (green) PHYSICAL FEATURESMechanical Dimensions 138 x 128 x 62 mm (5.4 x 5 x 2.4 in.) Weightabout 380 g. (13.40 oz.)ENVIRONMENTAL FEATURESOperating Temperature-35° to 50 ︒C (-31° to 122 °F) ** Storage Temperature -35° to 70 ︒C (-31° to 158 °F)Humidity max. 90% non condensing Vibration Resistance 14 mm @ 2 to 10 Hz EN 60068-2-62 hours on each axis 1.5 mm @ 13 to 55 Hz 2 g @ 70 to 200 HzShock Resistance 30 g; 11 ms; EN 60068-2-27 3 shocks on each axisProtection Class EN 60529 IP65(when compression connectors and reading device are correctly connected)* for further details about minimum/maximum supply voltage refer to the manual of the connected reading device, since the minimum supply voltage required may be >10 (i.e. 24 Vdc ± 10% for Subzero readers). ** Installation must be made at a temperature not lower than -20 °C.BACKUP AND RESTORE (ALL-IN-ONE MODELS ONLY)Figure 11 General ViewThe CBX100 LT all-in-one models contain the BM100 Backup Module which provides the following functions:∙Backup and RestoreComplete Configuration and Environmental parameter storage for ID-NET™ network and reading devices. Includes write protection.∙Network Address SelectionHardware Address selection for the ID-NET™ Slave devices (overrides software configuration).∙Network Type SelectionSelection of the ID-NET™ Slave type networking (depends on the application).BACKUP AND RESTORE PROCEDUREThe backup and restore functions are valid for any application layout type (point-to-point or ID-NET™ network) using CBX100 LT all-in-one model connection boxes. They can be performed by:∙ the Genius™ Device Menu commands (always).∙ the BM100 button , (if Fam2/4K scanner X-PRESS™ Key Functionality parameteris enabled)If it ever becomes necessary to replace the reading device it can be quickly configured through the restore procedure.BM100 provides complete backup and restore functions (Configuration and Environmental parameters) and cannot be interrupted once started (LED quickly blinking).∙For network nodes, the backup module of the ID-NET™ Master saves the configuration of all the reading devices in the network, Master and all individual Slaves. The Slaves must be configured with the same network baudrate as the Master before performing the Restore procedure.∙For single reading device stations, Slaves, or for RS232 Master/Slave networks, the backup module saves the configuration only of the specific connected reading device.Backup Restore These functions are cyclical every 3 seconds:No ActionTo perform Backup :1. Make sure the Write Protection switch is unlocked.2. Press and hold the Backup & Restore button for approximately 3 seconds. Thegreen Backup LED (B) lights up. 3. Release the button to select Backup and within 1 second press and release itagain to activate the procedure. The green Backup LED (B) blinks quicklyindicating the backup procedure is active.At the end of the procedure both B and R LEDs turn on for about 2 seconds. When the LEDs turn off the procedure is complete. 4. Set the Write Protection switch to locked.To perform Restore :1. Press and hold the Backup & Restore button for approximately 6 seconds. Theyellow Restore LED (R) lights up. 2. Release the button to select Restore and within 1 second press and release itagain to activate the procedure. The yellow Restore LED (R) blinks quickly indicating the restore procedure is active.At the end of the procedure both B and R LEDs turn on for about 2 seconds. When the LEDs turn off the procedure is complete.To exit without performing Backup or Restore procedures do one of the following: ∙Release the button while both LEDs are off (No Action )∙After releasing the button the first time, do not re-press the button to activate the procedure but wait about 3 seconds (timeout during which the relative LED blinks slowly).NETWORK TYPE SELECTIONThe network type depends on the application layout.Net Type Switch0 = None (no network present) or ID-NET™ Master 1 - 7 = Not Available8 = ID-NET™ Slave Synchronized 9 = ID-NET™ Slave MultidataThe Net Type selector switch allows setting the ID-NET™ network:∙ ID-NET™ Masters communicating with the Host through the main serial interface, and all other non network applications must be set to None (0). ∙ If used for ID-NET™ Slaves, this switch must be set to Slave Synchronized (8) or Slave Multidata (9) depending on the ID-NET™ network Topology Role (same as Master).NETWORK ADDRESS SELECTIONFigure 12 – Address Selection SwitchesBM100 provides hardware network address selection for rapid installation of ID-NET™ networks. These switch settings are read at each power-up or reset, and override software configuration settings.The valid selection range for the ID-NET™ Slave addresses is from 01 to 31. Address selections outside of this range are not accepted by the ID-NET™ network. The x100 switch refers to the ID-NET™ baudrate.BAUDRATE SELECTIONWhen the BM100 is used for ID-NET™ network Slaves, the ID-NET™ baudrate is selected through the baudrate switch and must match the Master ID-NET™ baudrate. The settings are:ID-NET™ Baudrate Switch 0 = 19200 Baud 5 = 500 kBaud 1 = 38400 Baud 6 = 1 MBaud 2 = 57600 Baud 7 = Reserved 3 = 125 kBaud 8 = Reserved4 = 250 kBaud9 = ReservedSEARCH FOR BACKUP MEMORY AT DEVICE STARTUPThis reader configuration parameter is enabled by default, so that at startup, the reader sends a message to recognize the presence of, and communicate with, the Backup Module. If using the CBX100 LT all-in-one model, this parameter must be enabled.WRITE PROTECTION LOCKFigure 13 – Write ProtectionA write protection switch is provided to protect configuration data from being inadvertently overwritten. When this switch is in the lock position, the Backup function is not available (data cannot be written to the backup memory) and a diagnostic warning message can be sent. The Restore function is available.SERVICES AND SUPPORTDatalogic provides several services as well as technical support through its website. Log on to and click on the links indicated for further information including:∙PRODUCTSSearch through the links to arrive at your product page which describes specific Info, Features, Applications, Models, Accessories, and Downloads.∙SERVICE- Overview - Warranty Extensions and Maintenance Agreements - Repair Centers - Helpdesk- Material Return AuthorizationCE COMPLIANCEWarning: This is a Class A product. In a domestic environment this product may cause radio interference in which case the user may be required to take adequate measures.See the reading device Reference Manual for the Declaration of Conformity.821001541 (Rev. A)Backup/Restore Button 1 Display Connector (not used) 2 Backup/Restore Indicator LEDs 6 ID-NET™ Address Switches 5 ID-NET™ Baudrate Switch 4 Write Protection Lock 3 Network Type Switch 7 12345 6 7。
Kinetix 5100 辅助反馈连接器套件安装说明书
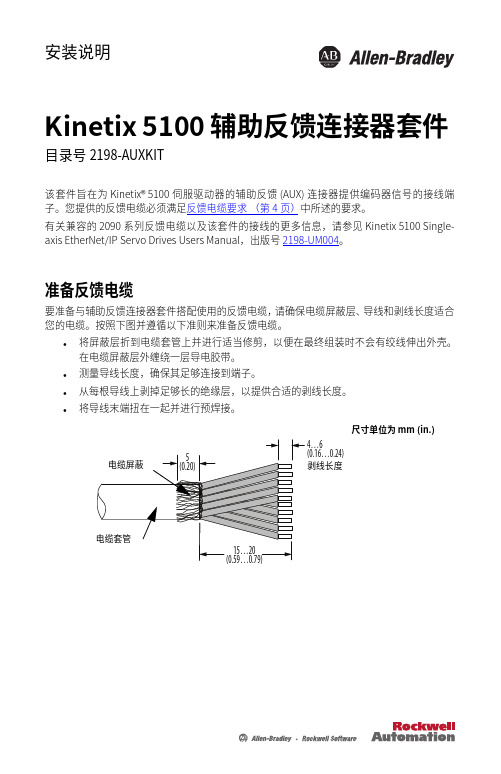
安装说明Kinetix 5100 辅助反馈连接器套件 目录号 2198-AUXKIT该套件旨在为 Kinetix®5100 伺服驱动器的辅助反馈 (AUX) 连接器提供编码器信号的接线端子。
您提供的反馈电缆必须满足反馈电缆要求(第4⻚)中所述的要求。
有关兼容的 2090 系列反馈电缆以及该套件的接线的更多信息,请参⻅ Kinetix 5100 Single-axis EtherNet/IP Servo Drives Users Manual,出版号 2198-UM004。
准备反馈电缆要准备与辅助反馈连接器套件搭配使用的反馈电缆,请确保电缆屏蔽层、导线和剥线长度适合您的电缆。
按照下图并遵循以下准则来准备反馈电缆。
•将屏蔽层折到电缆套管上并进⾏适当修剪,以便在最终组装时不会有绞线伸出外壳。
在电缆屏蔽层外缠绕一层导电胶带。
•测量导线长度,确保其足够连接到端子。
•从每根导线上剥掉足够长的绝缘层,以提供合适的剥线长度。
•将导线末端扭在一起并进⾏预焊接。
尺寸单位为 mm (in.)Kinetix 5100 辅助反馈连接器套件准备连接器对连接器触点进⾏预焊接,以简化最终组装及防⽌焊料滴落。
重要事项为避免损坏连接器,每个焊接均应在 3…5 秒内完成。
组装连接器套件按照以下步骤组装连接器套件。
1.将 10…20 mm (0.4…0.78 in.) 的绝缘管滑到每根电缆导线上。
2.将导线布线到适当的端子并焊接到位。
对于 10 针端子引脚,请参⻅第3⻚上的连接器数据。
将焊铁温度设置为 390 °C (734 °F)。
重要事项为防止损坏,请在 10 秒内完成每个焊接连接,并对端子施加最小的力。
3.将电缆和线装插座组件置于内壳的底部。
4.将顶部内壳搭扣对准底部内壳,然后推到一起。
5.为实现屏蔽编织层与夹具之间的高频搭接,可对缠绕导电胶带的 5 mm (0.20in.) 电缆屏蔽层使用屏蔽夹。
Kinetix 5100 AC Line Filter 安装指南说明书
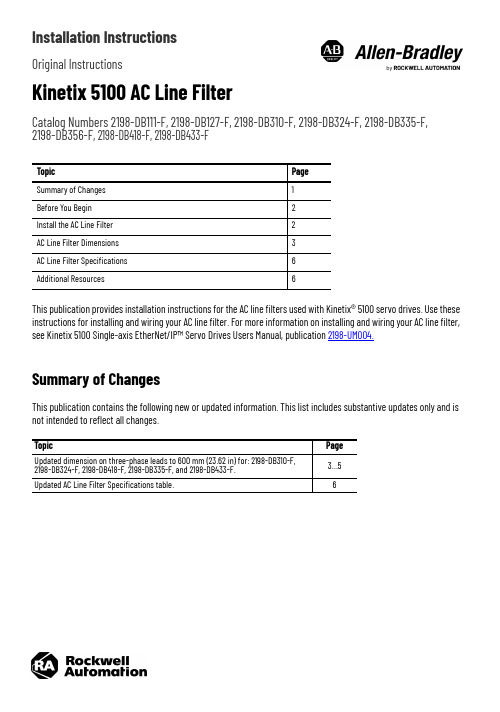
Installation InstructionsOriginal InstructionsKinetix 5100 AC Line FilterCatalog Numbers 2198-DB111-F, 2198-DB127-F, 2198-DB310-F, 2198-DB324-F, 2198-DB335-F, 2198-DB356-F, 2198-DB418-F, 2198-DB433-FThis publication provides installation instructions for the AC line filters used with Kinetix® 5100 servo drives. Use these instructions for installing and wiring your AC line filter. For more information on installing and wiring your AC line filter, see Kinetix 5100 Single-axis EtherNet/IP™ Servo Drives Users Manual, publication 2198-UM004.Summary of ChangesThis publication contains the following new or updated information. This list includes substantive updates only and is not intended to reflect all changes.Topic Page Summary of Changes 1Before You Begin 2Install the AC Line Filter 2AC Line Filter Dimensions 3AC Line Filter Specifications 6Additional Resources6Topic Page Updated dimension on three-phase leads to 600 mm (23.62 in) for: 2198-DB310-F, 2198-DB324-F, 2198-DB418-F, 2198-DB335-F, and 2198-DB433-F. 3…5Updated AC Line Filter Specifications table.62Rockwell Automation Publication 2198-IN017D-EN-P - June 2021Kinetix 5100 AC Line Filter Installation InstructionsBefore You BeginFor general guidelines when laying out your panel and mounting your AC line filter, refer to the System Design for Control of Electrical Noise Reference Manual, publication GMC-RM001.For guidelines specific to your application, refer to the Kinetix 5100 Single-axis EtherNet/IP Servo Drives Users Manual, publication 2198-UM004.Install the AC Line FilterMount the line filter to the cabinet panel with hardware as specified in this table.See the System Design for Control of Electrical Noise Reference Manual, publication GMC-RM001, for techniques on how to make proper high-frequency (HF) bonds to improve overall system performance.For wiring guidelines specific to your application, see the Kinetix 5100 Single-axis EtherNet/IP Servo Drives User Manual, publication 2198-UM004.ATTENTION: To avoid personal injury or damage to equipment due to hazardous voltages, follow these guidelines when installing your AC line filter. NEC and local regulations always take precedence.•Disconnect mains power before installation.•Verify that the rated voltage is compatible with the local supply voltage.•Connect the earth ground connection first when you make connections.Cat. No. Mounting BoltTorque Value N•m (lb•in)Mounting Bolt (1)(for piggybackmounting of the drive)(1)Piggyback mounting of the drive to the line filter is available only for 2198-DB418-F and hardware Rev 1.1 or later of 2198-DB111-F,2198-DB127-F, 2198-DB310-F, and 2198-DB324-F.Torque Value (1)N•m (lb•in)2198-DB111-F M5 (#10-24)1.6…2.0 (13.9…17.70)M5 (#10-24)1.6…2.0 (13.9…17.70)2198-DB127-F 2198-DB310-F 2198-DB324-F 2198-DB335-F ——2198-DB356-F ——2198-DB418-F M5 (#10-24) 1.6…2.0 (13.9…17.70)2198-DB433-F——Rockwell Automation Publication 2198-IN017D-EN-P - June 20213Kinetix 5100 AC Line Filter Installation InstructionsAC Line Filter DimensionsFor line filter dimensions specific to your application, see the Kinetix Servo Drives Specifications Technical Data, publication KNX-TD003.AC Line Filter Dimensions (Catalog number 2198-DB111-F)AC Line Filter Dimensions (Catalog number 2198-DB310-F)30.023.020.0(Minimum)30.023.020.0(Minimum)4Rockwell Automation Publication 2198-IN017D-EN-P - June 2021Kinetix 5100 AC Line Filter Installation Instructions AC Line Filter Dimensions (Catalog numbers 2198-DB127-F)AC Line Filter Dimensions (Catalog numbers 2198-DB324-F and 2198-DB418-F)29.128.029.128.0Rockwell Automation Publication 2198-IN017D-EN-P - June 20215Kinetix 5100 AC Line Filter Installation InstructionsAC Line Filter Dimensions (Catalog numbers 2198-DB335-F and 2198-DB433-F)AC Line Filter Dimensions (Catalog number 2198-DB356-F)33.028.0(Minimum)(0.22)28.0(1.10)33.0(1.30)Dimensions are in mm (in.).6Rockwell Automation Publication 2198-IN017D-EN-P - June 2021Kinetix 5100 AC Line Filter Installation InstructionsAC Line Filter SpecificationsFor more information about AC line filters, see AC Line Filters Installation Instructions, publication 2198-IN003.Additional ResourcesThese documents contain additional information concerning related products from Rockwell Automation.You can view or download publications at rok.auto/literature .Cat. No.Voltage Rating (1)(1)SCCR Rating of 5kA when used with UL branch circuit protection as listed in Kinetix 5100 EtherNet/IP Indexing Servo Drives,publication 2198-UM004.Current Rating A @ 50 °C (122 °F)Power Loss WLeakageCurrent mA, typicalWeight, approxkg (lb)Operating Temperature(Surrounding Air, max.)2198-DB111-F 120V s ingle-phase, 50/60 Hz200…230V single-phase, 50/60 HZ 11 4.952.9 1.05 (2.314)50 °C (122 °F)2198-DB127-F 2715.554.91.80 (3.968)2198-DB310-F 120V s ingle-phase, 50/60 Hz200…230V single-phase, 50/60 HZ 10 4.737.4 1.10 (2.425)2198-DB324-F 249.7901.95 (3.968)2198-DB310-F 200...240V AC, three-phase,50/60 Hz1014.0 3.9 1.10 (2.425)2198-DB324-F 2429.09.3 1.95 (3.968)2198-DB335-F 240V AC, three-phase,48...63 Hz34.830.0 5.8 2.90 (6.393)2198-DB356-F 5657.0 2.8 4.00 (8.818)2198-DB418-F 480V AC three-phase,48…63 Hz 18.416.0 4.21 1.20 (2.65)2198-DB433-F3335.0 3.58 1.90 (4.19)ResourceDescriptionKinetix Servo Drives Specifications Technical Data, publication KNX-TD003Provides product specifications for the Kinetix Integrated Motion over EtherNet/IP network, Integrated Motion over Sercos interface, EtherNet/IP networking, and component servo drive families.Kinetix Motion Accessories Specifications Technical Data, publication KNX-TD004Provides product specifications for Bulletin 2090 motor and interface cables, low-profile connector kits, drive power components, and other servo drive accessory items.AC Line Filters Installation Instructions, publication 2198-IN003Provides information on how to install and wire AC line filters used with the Kinetix 5500 and Kinetix 5700 servo drive systems and the Kinetix 5700 iTRAK® power supply.Kinetix 5100 Single-axis EtherNet/IP Servo Drives Users Manual, publication 2198-UM004Information on how to install, configure, start, and troubleshoot your Kinetix 5100 servo drive system.Servo Drive Installation Best Practices Application Technique, publication MOTION-AT004Provides best practice examples to help reduce the number of potential noise or electromagnetic interference (EMI) sources in your system and to make sure that the noise-sensitive components are not affected by the remaining noise.Industrial Automation Wiring and Grounding Guidelines, publication 1770-4.1 Provides general guidelines for installing a Rockwell Automation industrial system.Product Certifications website: rok.auto/certificationsProvides declarations of conformity, certificates, and other certification details.Kinetix 5100 AC Line Filter Installation Instructions Notes:Rockwell Automation Publication 2198-IN017D-EN-P - June 20217Publication 2198-IN017D-EN-P - June 2021 | Supersedes Publication 2198-IN017C-EN-P - August 2020Copyright © 2021 Rockwell Automation, Inc. All rights reserved.Rockwell Otomasyon Ticaret A.Ş. Kar Plazaİş Merkezi E Blok Kat:6 34752, İçerenköy, İstanbul, Tel: +90 (216) 5698400 EEE Yönetmeli ğine UygundurAllen-Bradley, expanding human possibility, FactoryTalk, iTRAK, Kinetix, and Rockwell Automation are trademarks of Rockwell Automation,Inc.EtherNet/IP is a trademark of ODVA, IncTrademarks not belonging to Rockwell Automation are property of their respective companies.Your comments help us serve your documentation needs better. If you have any suggestions on how to improve our content, complete the form at rok.auto/docfeedback.Waste Electrical and Electronic Equipment (WEEE)Rockwell Automation maintains current product environmental compliance information on its website at rok.auto/pec .At the end of life, this equipment should be collected separately from any unsorted municipal waste.Rockwell Automation SupportUse these resources to access support information.Technical Support Center Find help with how-to videos, FAQs, chat, user forums, andproduct notification updates.rok.auto/support KnowledgebaseAccess Knowledgebase articles.rok.auto/knowledgebase Local Technical Support Phone Numbers Locate the telephone number for your country.rok.auto/phonesupport Literature LibraryFind installation instructions, manuals, brochures, andtechnical data publications.rok.auto/literature Product Compatibility and Download Center (PCDC)Download firmware, associated files (such as AOP, EDS, and DTM), and access product release notes.rok.auto/pcdc。
Xpass 安装指南说明书
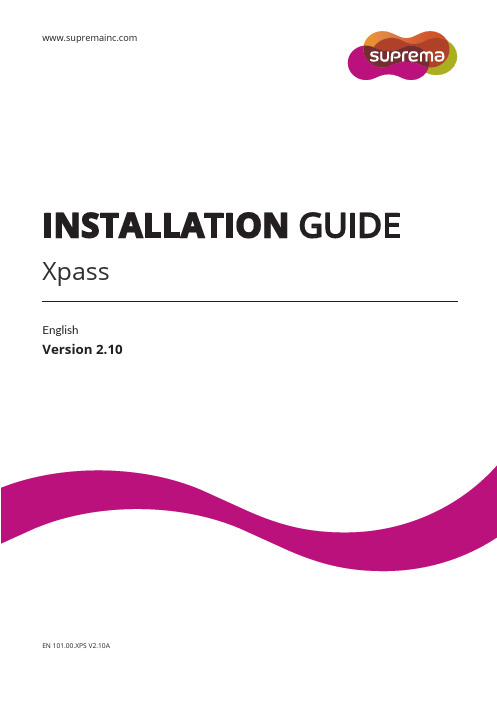
INSTALLATION GUIDEXpassEnglishVersion 2.10EN 101.00.XPS V2.10AContentsSafety Instructions (3)Getting Started (4)Components (4)Features (5)Part names and features (5)Cables and connectors (6)Installation (7)Mounting the Bracket and Product (7)Installing the bracket (7)Connecting to Power (8)Connecting to a Network (9)TCP/IP (9)Connecting to an Door button/Door sensor (10)Digital input connection (Door button, Door sensor) (10)Digital input connection (Alarm, Emergency switch) (10)Connecting to a R elay (11)Fail Safe Lock (11)Fail Secure Lock (11)Connecting to an Automatic door (12)Connecting as a standalone (12)Connecting to Secure I/O 2 (13)Connecting as a Wiegand device (13)External Power Output (14)Resetting Network Settings (14)Product Specifications (15)Dimensions (16)FCC Compliance Information (17)Appendix (18)Disclaimers (18)Copyright Notice (18)Safety InstructionsSafety InstructionsPlease read the following instructions carefully before using the product. This information is important for ensuring the safety of the user and for preventing damage to the user's property.WarningViolation of the instructions may cause serious injury or death.Installation InstructionsDo not install the product in direct sunlight or in a location that is damp or dusty.•This can cause a fire or electric shock.Install the product in a dry place.•Moisture can cause product damage or electric shock.Do not install the product near any heat source such as electric heaters.•This can cause a fire from overheat or electric shock.Install the product in a place where there is no electromagnetic interference.•This can cause product damage or electric shock.Have qualified service professionals install or repair the product.•Otherwise, it can cause a fire, electric shock, or injury.•If the product is damaged due to a user's unauthorized installation or dismantling of the product, a service fee will be charged for repair.Operating InstructionsBe careful not to spill any liquid such as water, drinks, or chemicals inside the product.•This can cause fire, electric shock, or product damage.CautionIgnoring these instructions may result in minor injuries or damage to the product.Installation InstructionsProtect the power cord from being walked on or pinched.•This can cause product damage or injury.Keep the product away from strong magnetic objects such as magnets, TVs, monitors (especially CRT monitors), or speakers. •This can cause a product failure.If installing the product outside where the product is completely exposed, it is recommended to install the product together with the enclosure.Use a separate power supply for Secure I/O 2, electric lock and Xpass respectively.•If connecting and using the power supply to these devices together, the devices may malfunction.Operating InstructionsDo not drop the product or subject it to shock or impact during use.•This can cause a product failure.Do not press the buttons on the product with excessive force or with a sharp tool.•This can cause a failure.Clean the product with a soft, dry cloth. Do not use alcohol, benzene, or water.•This can cause a product failure.Getting StartedComponentsThe components may differ depending on where the product is installed.NoteXpassMain bracketAdapterMounting screws for bracket(2 pcs) PVC anchors (2 pcs) Heat shrink tubesSoftware CDDiodeExtension bracketTCP/IPextension cableFeaturesPart names and featuresNameFeatureLED lamp• Green: Authentication success• Red: Authentication failure • Pink: Processing• Blue and sky-blue alternate flashing every 2 seconds: Normal operation • Red and pink alternate flashing every 2 seconds: The device is locked.• Blue and red alternate flashing every 2 seconds: The clock has been reset due to an empty internal battery. (The clock needs to be reconfigured.)• Blue and yellow alternate flashing every 2 seconds: An IP address has not been received when DHCP is set to USE.• Red flashes every 2 seconds on first use: Failure to reset. Contact the manufacturer. • Red flashes every 2 seconds in a normal operation: The device is secured. •Yellow flashes: Waiting for an input.RF card touch area Reads RF card for entering and exiting.Network reset button Resets the network configurations when the device does not work properly. For details, refer to the Resetting Network Setting .Cables and connectorsInstallationMounting the Bracket and ProductInstalling the bracket1With the mounting screws for the bracket, mount the bracket firmly onto the surface where Xpass is to be installed.If Xpass should be installed onto a concrete wall, make a hole with a drill, and then insert a PVC anchor into the hole before screwing the mounting screw.2Attach Xpass onto the mounted bracket.3Assemble Xpass with the bracket by screwing the mounting screws on the bottom of Xpass.NoteConnecting to Power•Use a power adapter that has a DC 12 V (± 10%) specification of with the minimum current of 1,500 mA and has IEC/EN 60950-1 certification. If the power adapter is shared by other devices, the power adapter should provide a current more than the sum of the power consumption from this device (1,500 mA) and other devices.• Use a separate power supply for Secure I/O 2, electric lock and Xpass respectively. If connecting and using the power supply to these devices together, the devices may malfunction.Note 14 - PWR +VDC Red16 - PWR GNDBlack (White stripe)UPS (Optional)DC powerXpass1614Connecting to a NetworkTCP/IPLAN connection (connecting to a hub)A normal CAT-5 cable can be used to connect to a hub.HubPCXpassLAN connection (connecting directly to a PC)Xpass can be connected directly to a PC by using a normal type CAT-5 cable because it supports an automatic MDI/MDIX function.PCXpassConnecting to an Door button/Door sensorDigital input connection (Door button, Door sensor)7 - TTL IN1 Brown9 - TTL GND Gray11 - TTL IN0 PurpleDoor sensor 97911Xpass Door buttonDigital input connection (Alarm, Emergency switch)7 - TTL IN1 Brown9 - TTL GND Gray11 - TTL IN0 PurpleInput 1 97911Xpass Input 0Connecting to a RelayFail Safe LockTo use fail safe lock, connect N/C terminal as shown below. Normally, there is a current flowing through the relay and the door is opened when the relay is activated by blocking current flows. The door is opened when there is a blackout or power failure caused by external conditions.• Install the diode at both ends of the wire for the door lock device as shown in the figure to protect the relay from being damaged by the reverse current induced when the door lock device operates.• Make sure that the direction of the installed diode is correct. • Install the diode close to the door lock device.•Use a separate power source for Xpass from the door lock device.Fail Secure LockTo use fail secure lock, connect N/O terminal as shown below. Normally, there is no current flowing through the relay and the door is opened when the relay is activated by a current flows. The door is locked when there is a blackout or power failure caused by external conditions.• Install the diode at both ends of the wire for the door lock device as shown in the figure to protect the relay from being damaged by the reverse current induced when the door lock device operates.• Make sure that the direction of the installed diode is correct. • Install the diode close to the door lock device.•Use a separate power source for Xpass from the door lock device.Note 8 - RLY NO Gray (White stripe) 10 - RL Y COMGreen (White stripe)Xpass8 10Deadbolt /Door strikeDC powerNote 10 - RL Y COM Green (White stripe) 12 - RLY NCOrange (Black stripe)XpassDeadbolt / Door strikeDC power10 12Connecting to an Automatic doorConnecting as a standaloneDoor buttonDoor sensorDoor lockInput 1RelayInput 09 7 12 10 911Xpass9 - TTL GND Gray 11 - TTL IN0 Purple 7 - TTL IN1 Brown10 - RL Y COM Green (White stripe) 12-RLY NCOrange (Black stripe)PC8 - RLY NO Gray (White stripe) 10 - RL Y COMGreen (White stripe)XpassSensorAutomatic door controllerDoor buttonDoor lock8 10Connecting to Secure I/O 2Refer to the following figure for connecting.• RS-485 should be AWG24, twisted pair, and maximum length is 1.2 km.• Connect a termination resistor (120Ω) to both ends of a RS-485 daisy chain connection. It should be installed at both endsof the daisy chain. If it is installed in the middle of the chain, the performance in communicating will deteriorate because it reduces the signal level. • Up to 32 devices can be connected via daisy chain (1 master device and 31 other devices).Connecting as a Wiegand deviceRFID reader2 - WG GND Black 4 - WG D1 White 6 - WG D0Green2 4 62 4 6ControllerXpassXpass Door lockInput 1Door buttonDoor sensorInput 05 3 11 - 485 GND White (Black stripe) 5 - 485 TRXP Blue (White stripe) 3 - 485 TRXNYellow (Black stripe)PCXpassSecure I/O 2External Power Output• The external output provides a maximum current of 620 mA. • Xpass connected to PoE supports the external power output.• Be careful not to disconnect the power supply to Xpass when the external power output is connected to a door lock. Disconnecting the power supply to Xpass may cause security problems.•The maximum switching current of the door lock should not exceed 620 mA. For more information on the maximum switching current of the door lock, contact the manufacturer.Resetting Network Settings1 Turn the power on.2 Press the network reset button on the rear of device until the device restart automatically.3 Connect the device with default values. • TCP/IP address: 192.168.0.1 • Server mode: Not checked• RS-485: PC connection, 115200 bps4 Change the TCP/IP address or RS-485 information.5Turn the power off later on and then check the network setting is properly.Note 10 - RLY COM Green (White stripe) 12 - RLY NC Orange (Black stripe) 18 - PWR OUT Sky-blue20 - PWR GNDBlack (White stripe)XpassDeadbolt / Door strike10 12 18 20Product SpecificationsMain IP Rating IP65RF Card 125KHz EM, 125KHz HID Prox, 13.56MHz Mifare/DESFire Multi-Controller Yes (RF)Capacity Max. User (1:1) 40,000 Max. User (1:N) 40,000 Max. Text L og 50,000Interface TCP/IP YesRS-485 1chWiegand 1ch In or Out (Selectable) TTL Input 2 InputsRelay 1 RelayRelay Voltage Max. 24VDC Current Typ. 0.5A, Max. 1.0AHardware CPU 533MHz DSP Memory 16MB RAM + 8MB Flash LED Multi-ColorSound 16-bit Hi-Fi Operating Temp. -20°C ~ 50°CTamper YesPower 12VDCPoE Optional Dimensions (W x H x D mm) 45 x 130 x 27 Certification CE, FCC, KC, RoHSDimensions(Unit: mm)Front viewExtension bracketMain bracketSide viewFCC Compliance InformationFCC Compliance InformationTHIS DEVICE COMPLIES WITH PART 15 OF THE FCC RULES.Operation is subject to the following two conditions:(1) This device may not cause harmful interference, and(2) This device must accept any interference received, including interference that may cause undesired operation.Note: This equipment has been tested and found to comply with the limits for a Class B digital device, pursuant to part 15 of the FCC Rules. These limits are designed to provide reasonable protection against harmful interference in a residential installation. This equipment generates, uses, and can radiate radio frequency energy and, if not installed and used in accordance with the instructions, may cause harmful interference to radio communications. However, there is no guarantee that interference will not occur in a particular installation. If this equipment does cause harmful interference to radio or television reception, which can be determined by turning the equipment off and on, the user is encouraged to try to correct the interference by one or more of the following measures:•Reorient or relocate the receiving antenna.•Increase the separation between the equipment and receiver.•Connect the equipment into an outlet on a circuit different from that to which the receiver is connected.•Consult the dealer or an experienced radio/TV technician for help.Modifications not expressly approved by the manufacturer could void the user's authority to operate the equipment under FCC rules.Appendix AppendixDisclaimersThis document provides the information pertaining to Suprema's products. The right of use is granted only to the products that are covered by the sales agreement and conditions guaranteed by Suprema. Any license of intellectual property that is not dealt within this document is not granted.Suprema does not provide any warranty or liability of fitness or merchantability for a particular purpose and of infringement of patents, copyrights, or other intellectual properties, regarding the sales or use of Suprema's products.Do not use Suprema's products in either circumstances where people could be hurt or die as a consequence of malfunctions of the products or circumstances related to medical treatments, the rescue of lives, or life supports. If a user suffers an accident in one of the circumstances mentioned above, employees, subsidiaries, branches, partners, and distributors of Suprema are exempt from liability even when it is claimed that there is a significant fault in the design or production process, and also they are not liable for any direct or indirect cost or expenditure including legal costs.Suprema can change the standard and specification of its products anytime without notice in order to improve the stability, functions, or design of the products. Designers should keep in mind that the functions or explanations denoted as "to be implemented" or "not defined" can be changed anytime. Suprema will implement or define such items in the shortest possible time, and will not accept any liability for problems incurred including compatibility issues.Contact Suprema, sales representatives of Suprema, or local distributors in order to get the latest specifications before ordering products. Copyright NoticeSuprema has the copyright of this document. The rights of other product names, brands, and trademarks belong to individuals or organizations who own them. 。
浪潮存储平台 Cinder-backup主机插件用户手册说明书

浪潮存储平台主机插件用户手册文档版本发布日期适用版本及以上尊敬的用户:衷心感谢您选用浪潮存储!浪潮存储秉承“云存智用运筹新数据”的新存储之道,致力于为您提供符合新数据时代需求的存储产品和解决方案。
本手册用于帮助您更详细地了解和便捷地使用本存储,涉及的截图仅为示例,最终界面请以实际设备显示的界面为准。
由于产品版本升级或其他原因,本手册内容会不定期进行更新,如有变动恕不另行通知。
除非另有约定,本手册仅作为使用指导,本手册中的所有陈述、信息和建议不构成任何明示或暗示的担保。
浪潮拥有本手册的版权,保留随时修改本手册的权利。
未经浪潮许可,任何单位和个人不得以任何形式复制本手册的内容。
如果您对本手册有任何疑问或建议,请向浪潮电子信息产业股份有限公司垂询。
技术服务电话:地址:中国济南市浪潮路号浪潮电子信息产业股份有限公司邮编:在您正式使用本存储之前,请先阅读以下声明。
只有您阅读并且同意以下声明后,方可正式开始使用本存储。
如果您对以下声明有任何疑问,请和您的供货商联系或直接与我们联系。
如您在开始使用本系统前未就以下声明向我们提出疑问,则默认您已经同意了以下声明。
请不要自行拆卸本存储的机箱及机箱内任何硬件设备。
在本存储出现任何硬件故障或您希望对硬件进行任何升级时,请您将机器的详细硬件配置反映给我们的客户服务中心。
请不要将本存储的设备与任何其他型号的相应设备混用。
本存储的内存、、散热片、风扇、硬盘托架、硬盘等都是特殊规格的。
在使用本存储时遇到任何软件问题,请您首先和相应软件的提供商联系。
由提供商和我们联系,以方便我们共同沟通和解决您遇到的问题。
对于数据库、网络管理软件或其他网络产品的安装、运行问题,我们尤其希望您能够这样处理。
上架安装本存储前,请先仔细阅读相关产品手册中的快速安装指南。
我们致力于产品功能和性能的持续提升,部分功能及操作与手册描述可能会有所差异,但不会影响使用。
如果您有任何疑难问题,请与我们的客户服务中心联系。
Appendix资料
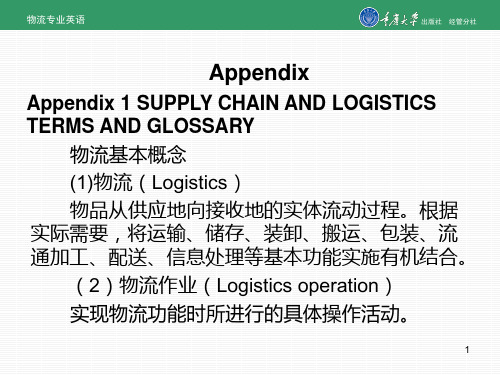
物流专业英语
出版社
经管分社
(9)ABC分类管理(ABC classification 将库存物品按品种和占用资金的多少分为特别 重要的库存(A类)、一般重要的库存(B类)和 不重要的库存(C类)三个等级,然后针对不同等 级分别进行管理与控制。 (10)电子订货系统(Electronic order system,EOS 不同组织间利用通讯网络和终端设备以在线联
2
物流专业英语
出版社
经管分社
(6)物流管理(Logistics management 为了以最低的物流成本达到用户所满意的服务 水平,对物流活动进行的计划、组织、协调与控制 (7)物流中心(Logistics center
3
物流专业英语
出版社
经管分社
(8)物流网络(Logistics network (9)物流信息(Logistics information 反映物流各种活动内容的知识、资料、图像、 (10)物流单证(Logistics documents 物流过程中使用的所有单据、票据、凭证的总
26
物流专业英语
出版社
经管分社
(26)业务外包(Outsourcing 企业为了获得不单纯利用不、内部资源更多的
27
物流专业英语
出版社
经管分社
(1)仓库(Warehouse (2)库房(Storehouse 有屋顶和围护结构,供储存各种物品的封闭式 (3)自动化仓库(Automatic warehouse) 由电子计算机进行管理和的控制,不需人工搬
19企业资源计划enterpriseresourceplanningerp在mrp的基础上通过反馈的物流和反馈的信息流资金流把客户需要和企业内部的生产经营活动以及供应商的资源整合在一起体现完全按用户需要进行经营管理的一种全新的管理方法
Agilent E4980A精密LCR测量仪用户指南第八版说明书

Agilent E4980A Precision LCR MeterUser’s GuideEighth EditionFIRMWARE REVISIONSThis manual applies directly to instruments that have the firmware revision A.02.11.For additional information about firmware revisions, see Appendix A.Manufacturing No. E4980-90080June 2010 1981NoticesThe information contained in this document is subject to change without notice.This document contains proprietary information that is protected by copyright. All rights are reserved. No part of this document may be photocopied, reproduced, or translated to another language without the prior written consent of Agilent Technologies.Microsoft®, MS-DOS®, Windows®, Visual C++®, Visual Basic®, VBA®, and Excel®are registered trademarksUNIX is a registered trademark in the U.S. and other countries, licensedexclusively through X/Open Company Limited.Portions ©Copyright 1996, Microsoft Corporation. All rights reserved.© Copyright 2006, 2008, 2010 Agilent TechnologiesManual Printing HistoryThe manual’s printing date and manufacturing number indicate its current edition. The printing date changes when a new edition is printed (minor corrections and updates that are incorporated at reprint do not cause the date to change). The manufacturing number changes when extensive technical changes are incorporated.March 2006 First Edition (manufacturing number: E4980-90000)July 2006 Second Edition (manufacturing number: E4980-90010)November 2006 Third Edition (manufacturing number: E4980-90020)May 2007 Fourth Edition (manufacturing number: E4980-90030)July 2007 Fifth Edition (manufacturing number: E4980-90050)October 2007 Sixth Edition (manufacturing number: E4980-90060)June 2008 Seventh Edition (manufacturing number: E4980-90070)June 2010 Eighth Edition (manufacturing number: E4980-90080)The latest manuals can be downloaded from the following site./find/e4980a/2Safety SummaryThe following general safety precautions must be observed during all phases of operation,service, and repair of this instrument. Failure to comply with these precautions or withspecific WARNINGS elsewhere in this manual may impair the protection provided by theequipment. Such noncompliance would also violate safety standards of design,manufacture, and intended use of the instrument. Agilent Technologies assumes no liabilityfor the customer’s failure to comply with these precautions.NOTE The E4980A complies with INSTALLATION CATEGORY II as well as POLLUTION DEGREE 2 in IEC61010-1. The E4980A is an INDOOR USE product.NOTE The LEDs in the E4980A are Class 1 in accordance with IEC60825-1,CLASS 1 LED PRODUCT•Ground the InstrumentTo avoid electric shock, the instrument chassis and cabinet must be grounded with thesupplied 3-pole power cable’s grounding prong.•DO NOT Operate in an Explosive AtmosphereDo not operate the instrument in the presence of inflammable gasses or fumes.Operation of any electrical instrument in such an environment clearly constitutes asafety hazard.•Keep Away from Live CircuitsOperators must not remove instrument covers. Component replacement and internaladjustments must be made by qualified maintenance personnel only. Do not replacecomponents with the power cable connected. Under certain conditions, dangerousvoltage levels may remain even after the power cable has been disconnected. To avoidinjuries, always disconnect the power and discharge circuits before touching them.•DO NOT Service or Adjust the Instrument AloneDo not attempt internal service or adjustment unless another person, capable ofrendering first aid and resuscitation, is present.•DO NOT Substitute Parts or Modify the InstrumentTo avoid the danger of introducing additional hazards, do not install substitute parts orperform unauthorized modifications to the instrument. Return the instrument to anAgilent Technologies Sales and Service Office for service and repair to ensure thatsafety features are maintained in operational condition.•Dangerous Procedure WarningsWarnings in this manual, such as the example below, precede potentially dangerousprocedures. Instructions contained in the warnings must be followed.WARNING Dangerous voltage levels, capable of causing death, are present in this instrument.Use extreme caution when handling, testing, and adjusting this instrument.34Safety SymbolsGeneral definitions of safety symbols used on the instrument or in manuals are listedbelow.Instruction Manual symbol: the product is marked with this symbol when it is necessary forthe user to refer to the instrument manual.Alternating current.Direct current.On (Supply).Off (Supply).In-position of push-button switch.Out-position of push-button switch.A chassis terminal; a connection to the instrument’s chassis, which includes all exposedmetal structure.Stand-by.WARNING This warning sign denotes a hazard. It calls attention to a procedure, practice, or condition that, if not correctly performed or adhered to, could result in injury or death to personnel.CAUTION This Caution sign denotes a hazard. It calls attention to a procedure, practice, or condition that, if not correctly performed or adhered to, could result in damage to or destruction of part or all of the instrument.NOTE This Note sign denotes important information. It calls attention to a procedure, practice, or condition that is essential for the user to understand.CertificationAgilent Technologies certifies that this product met its published specifications at the timeof shipment from the factory. Agilent Technologies further certifies that its calibrationmeasurements are traceable to the United States National Institute of Standards andTechnology, to the extent allowed by the Institution’s calibration facility or by thecalibration facilities of other International Standards Organization members.WarrantyThis Agilent Technologies instrument product is warranted against defects in material andworkmanship for a period corresponding to the individual warranty periods of itscomponent products. Instruments are warranted for a period of one year. During thewarranty period, Agilent Technologies will, at its option, either repair or replace productsthat prove to be defective.For warranty service or repair, this product must be returned to a service facility designatedby Agilent Technologies. The buyer shall prepay shipping charges to Agilent Technologies,and Agilent Technologies shall pay shipping charges to return the product to the Buyer.However, the Buyer shall pay all shipping charges, duties, and taxes for products returnedto Agilent Technologies from another country.Agilent Technologies warrants that its software and firmware designated by AgilentTechnologies for use with an instrument will execute its programming instruction whenproperly installed on that instrument. Agilent Technologies does not warrant that theoperation of the instrument, or software, or firmware, will be uninterrupted or error free.Limitation of WarrantyThe foregoing warranty shall not apply to defects resulting from improper or inadequatemaintenance by the Buyer, Buyer-supplied software or interfacing, unauthorizedmodification or misuse, operation outside the environmental specifications for the product,or improper site preparation or maintenance.IMPORTANT No other warranty is expressed or implied. Agilent Technologies specifically disclaims the implied warranties of merchantability and fitness for a particular purpose.Exclusive RemediesThe remedies provided herein are the Buyer’s sole and exclusive remedies. AgilentTechnologies shall not be liable for any direct, indirect, special, incidental, orconsequential damages, whether based on contract, tort, or any other legal theory.5AssistanceProduct maintenance agreements and other customer assistance agreements are availablefor Agilent Technologies products.For any assistance, contact your nearest Agilent Technologies Sales and Service Office.Addresses are provided at the back of this manual.Typeface ConventionsSample (bold)Boldface type is used for emphasis.Sample (Italic)Italic type is used for emphasis and manual title.[Sample] key Indicates a hardkey (key on the front panel orexternal keyboard) labeled “Sample.” “key” maybe omitted.Sample menu/button/box Indicates a menu/button/box on the screen labeled“Sample” that can be selected/executed byclicking “menu,” “button,” or “box,” may beomitted.Sample 1 - Sample 2 - Sample 3Indicates a sequential operation of Sample 1,Sample 2, and Sample 3 (menu, button, or box).“-” may be omitted.Documentation MapThe following manuals are available for the Agilent E4980A.•User’s Guide (Manufacturing Number E4980-900x0, attached to Option ABA,English)This manual describes most of the basic information on the E4980A. It provides adetailed operation procedure for each function (from the function overview to systemsettings), measurement examples, options, accessories, specifications, GPIBcommands, function lists by softkeys, and error messages.NOTE The number position shown by “x” in the manufacturing number above indicates theedition number.6Sample ProgramsThe customer shall have the personal, nontransferable rights to use, copy, or modify SAMPLE PROGRAMS in this manual for the Customer’s internal operations. The customer shall use the SAMPLE PROGRAMS solely and exclusively for their own purpose and shall not license, lease, market, or distribute the SAMPLE PROGRAMS or modifications of any part thereof.Agilent Technologies shall not be liable for the quality, performance, or behavior of the SAMPLE PROGRAMS. Agilent Technologies especially disclaims that the operation of the SAMPLE PROGRAMS shall be uninterrupted or error free. The SAMPLE PROGRAMS are provided AS IS.AGILENT TECHNOLOGIES DISCLAIMS IMPLIED WARRANTIES OF MERCHANTABILITY AND FITNESS FOR A PARTICULAR PURPOSE.Agilent Technologies shall not be liable for any infringement of any patent, trademark, copyright, or other proprietary rights by the SAMPLE PROGRAMS or their use. Agilent Technologies does not warrant that the SAMPLE PROGRAMS are free from infringements of such rights of third parties. However, Agilent Technologies will not knowingly infringe or deliver software that infringes the patent, trademark, copyright, or other proprietary right of a third party.78Contents 1.Unpacking and PreparationChecking the Shipment. . . . . . . . . . . . . . . . . . . . . . . . . . . . . . . . . . . . . . . . . . . . . . . . . . . . . . . . . . . . . . . . . 23 Preparations before Use . . . . . . . . . . . . . . . . . . . . . . . . . . . . . . . . . . . . . . . . . . . . . . . . . . . . . . . . . . . . . . . . 26 Verifying the Power Supply . . . . . . . . . . . . . . . . . . . . . . . . . . . . . . . . . . . . . . . . . . . . . . . . . . . . . . . . . . . 26 Setting up the Fuse . . . . . . . . . . . . . . . . . . . . . . . . . . . . . . . . . . . . . . . . . . . . . . . . . . . . . . . . . . . . . . . . . . 26 Verifying and Connecting the Power Cable . . . . . . . . . . . . . . . . . . . . . . . . . . . . . . . . . . . . . . . . . . . . . . . 27 How to Remove the Handle . . . . . . . . . . . . . . . . . . . . . . . . . . . . . . . . . . . . . . . . . . . . . . . . . . . . . . . . . . . . . 29 Caution when Using the Handle. . . . . . . . . . . . . . . . . . . . . . . . . . . . . . . . . . . . . . . . . . . . . . . . . . . . . . . . . . 30 Environmental Requirements. . . . . . . . . . . . . . . . . . . . . . . . . . . . . . . . . . . . . . . . . . . . . . . . . . . . . . . . . . . . 31 Operating Environments. . . . . . . . . . . . . . . . . . . . . . . . . . . . . . . . . . . . . . . . . . . . . . . . . . . . . . . . . . . . . . 31 Ventilation Requirements . . . . . . . . . . . . . . . . . . . . . . . . . . . . . . . . . . . . . . . . . . . . . . . . . . . . . . . . . . . . . 32 Protection Against Electrostatic Discharge (ESD) . . . . . . . . . . . . . . . . . . . . . . . . . . . . . . . . . . . . . . . . . . 33 Ensuring Adequate Free Space around the LCR meter for Immediate Disconnection of the Power Cable in Case of Emergency . . . . . . . . . . . . . . . . . . . . . . . . . . . . . . . . . . . . . . . . . . . . . . . . . . . . . . . . . . . . . . . . . . 33 Starting the E4980A . . . . . . . . . . . . . . . . . . . . . . . . . . . . . . . . . . . . . . . . . . . . . . . . . . . . . . . . . . . . . . . . . . . 34 Turning the Power ON and OFF. . . . . . . . . . . . . . . . . . . . . . . . . . . . . . . . . . . . . . . . . . . . . . . . . . . . . . . . 34 Disconnecting from the Supply Source. . . . . . . . . . . . . . . . . . . . . . . . . . . . . . . . . . . . . . . . . . . . . . . . . . . 35 2.OverviewProduct Introduction. . . . . . . . . . . . . . . . . . . . . . . . . . . . . . . . . . . . . . . . . . . . . . . . . . . . . . . . . . . . . . . . . . . 38 Front Panel: Names and Functions of Parts . . . . . . . . . . . . . . . . . . . . . . . . . . . . . . . . . . . . . . . . . . . . . . . . . 391. Power switch. . . . . . . . . . . . . . . . . . . . . . . . . . . . . . . . . . . . . . . . . . . . . . . . . . . . . . . . . . . . . . . . . . . . . 402. LCD . . . . . . . . . . . . . . . . . . . . . . . . . . . . . . . . . . . . . . . . . . . . . . . . . . . . . . . . . . . . . . . . . . . . . . . . . . . 403. Softkeys. . . . . . . . . . . . . . . . . . . . . . . . . . . . . . . . . . . . . . . . . . . . . . . . . . . . . . . . . . . . . . . . . . . . . . . . . 404. Menu keys. . . . . . . . . . . . . . . . . . . . . . . . . . . . . . . . . . . . . . . . . . . . . . . . . . . . . . . . . . . . . . . . . . . . . . . 405. Cursor keys . . . . . . . . . . . . . . . . . . . . . . . . . . . . . . . . . . . . . . . . . . . . . . . . . . . . . . . . . . . . . . . . . . . . . . 406. Entry keys . . . . . . . . . . . . . . . . . . . . . . . . . . . . . . . . . . . . . . . . . . . . . . . . . . . . . . . . . . . . . . . . . . . . . . . 407. LED indicator . . . . . . . . . . . . . . . . . . . . . . . . . . . . . . . . . . . . . . . . . . . . . . . . . . . . . . . . . . . . . . . . . . . . 418. Preset key . . . . . . . . . . . . . . . . . . . . . . . . . . . . . . . . . . . . . . . . . . . . . . . . . . . . . . . . . . . . . . . . . . . . . . . 419. Trigger key . . . . . . . . . . . . . . . . . . . . . . . . . . . . . . . . . . . . . . . . . . . . . . . . . . . . . . . . . . . . . . . . . . . . . . 4110. DC Bias key . . . . . . . . . . . . . . . . . . . . . . . . . . . . . . . . . . . . . . . . . . . . . . . . . . . . . . . . . . . . . . . . . . . . 4111. DC Source key. . . . . . . . . . . . . . . . . . . . . . . . . . . . . . . . . . . . . . . . . . . . . . . . . . . . . . . . . . . . . . . . . . . 4112. UNKNOWN terminals . . . . . . . . . . . . . . . . . . . . . . . . . . . . . . . . . . . . . . . . . . . . . . . . . . . . . . . . . . . . 4113. Front USB port . . . . . . . . . . . . . . . . . . . . . . . . . . . . . . . . . . . . . . . . . . . . . . . . . . . . . . . . . . . . . . . . . . 4214. Ground terminal . . . . . . . . . . . . . . . . . . . . . . . . . . . . . . . . . . . . . . . . . . . . . . . . . . . . . . . . . . . . . . . . . 4215. DC Source terminal. . . . . . . . . . . . . . . . . . . . . . . . . . . . . . . . . . . . . . . . . . . . . . . . . . . . . . . . . . . . . . . 42Rear Panel: Names and Functions of Parts. . . . . . . . . . . . . . . . . . . . . . . . . . . . . . . . . . . . . . . . . . . . . . . . . . 431. GPIB Interface Connector. . . . . . . . . . . . . . . . . . . . . . . . . . . . . . . . . . . . . . . . . . . . . . . . . . . . . . . . . . . 432. Interface Connector. . . . . . . . . . . . . . . . . . . . . . . . . . . . . . . . . . . . . . . . . . . . . . . . . . . . . . . . . . . . . . . . 433. USB (USBTMC) Interface Port . . . . . . . . . . . . . . . . . . . . . . . . . . . . . . . . . . . . . . . . . . . . . . . . . . . . . . 444. LAN Port. . . . . . . . . . . . . . . . . . . . . . . . . . . . . . . . . . . . . . . . . . . . . . . . . . . . . . . . . . . . . . . . . . . . . . . . 445. External Trigger Input Connector. . . . . . . . . . . . . . . . . . . . . . . . . . . . . . . . . . . . . . . . . . . . . . . . . . . . . 446. Serial Number Plate . . . . . . . . . . . . . . . . . . . . . . . . . . . . . . . . . . . . . . . . . . . . . . . . . . . . . . . . . . . . . . . 447. Power Cable Receptacle (to LINE). . . . . . . . . . . . . . . . . . . . . . . . . . . . . . . . . . . . . . . . . . . . . . . . . . . . 448. Fan. . . . . . . . . . . . . . . . . . . . . . . . . . . . . . . . . . . . . . . . . . . . . . . . . . . . . . . . . . . . . . . . . . . . . . . . . . . . . 45Screen Area: Names and Functions of Parts. . . . . . . . . . . . . . . . . . . . . . . . . . . . . . . . . . . . . . . . . . . . . . . . . 461. Display Page Area. . . . . . . . . . . . . . . . . . . . . . . . . . . . . . . . . . . . . . . . . . . . . . . . . . . . . . . . . . . . . . . . . 462. Comment Line Area . . . . . . . . . . . . . . . . . . . . . . . . . . . . . . . . . . . . . . . . . . . . . . . . . . . . . . . . . . . . . . . 463. Softkey Area . . . . . . . . . . . . . . . . . . . . . . . . . . . . . . . . . . . . . . . . . . . . . . . . . . . . . . . . . . . . . . . . . . . . . 479Contents4. Measurement Data/Conditions Area. . . . . . . . . . . . . . . . . . . . . . . . . . . . . . . . . . . . . . . . . . . . . . . . . . . 475. Input Line Area. . . . . . . . . . . . . . . . . . . . . . . . . . . . . . . . . . . . . . . . . . . . . . . . . . . . . . . . . . . . . . . . . . . 486. System Message Area. . . . . . . . . . . . . . . . . . . . . . . . . . . . . . . . . . . . . . . . . . . . . . . . . . . . . . . . . . . . . . 487. Status Display Area. . . . . . . . . . . . . . . . . . . . . . . . . . . . . . . . . . . . . . . . . . . . . . . . . . . . . . . . . . . . . . . . 48Basic Operation . . . . . . . . . . . . . . . . . . . . . . . . . . . . . . . . . . . . . . . . . . . . . . . . . . . . . . . . . . . . . . . . . . . . . . 49 How to Use Cursor Keys . . . . . . . . . . . . . . . . . . . . . . . . . . . . . . . . . . . . . . . . . . . . . . . . . . . . . . . . . . . . . 49 How to Use Skip Keys . . . . . . . . . . . . . . . . . . . . . . . . . . . . . . . . . . . . . . . . . . . . . . . . . . . . . . . . . . . . . . . 50 3.Display FormatMEAS DISPLAY Page. . . . . . . . . . . . . . . . . . . . . . . . . . . . . . . . . . . . . . . . . . . . . . . . . . . . . . . . . . . . . . . . . 52 Measurement Function. . . . . . . . . . . . . . . . . . . . . . . . . . . . . . . . . . . . . . . . . . . . . . . . . . . . . . . . . . . . . . . 54 Impedance range. . . . . . . . . . . . . . . . . . . . . . . . . . . . . . . . . . . . . . . . . . . . . . . . . . . . . . . . . . . . . . . . . . . . 57 Test Frequency . . . . . . . . . . . . . . . . . . . . . . . . . . . . . . . . . . . . . . . . . . . . . . . . . . . . . . . . . . . . . . . . . . . . . 64 Test Signal Level. . . . . . . . . . . . . . . . . . . . . . . . . . . . . . . . . . . . . . . . . . . . . . . . . . . . . . . . . . . . . . . . . . . . 66 DC Bias. . . . . . . . . . . . . . . . . . . . . . . . . . . . . . . . . . . . . . . . . . . . . . . . . . . . . . . . . . . . . . . . . . . . . . . . . . . 69 Measurement Time Mode. . . . . . . . . . . . . . . . . . . . . . . . . . . . . . . . . . . . . . . . . . . . . . . . . . . . . . . . . . . . . 73 Display Setting for Measurement Results . . . . . . . . . . . . . . . . . . . . . . . . . . . . . . . . . . . . . . . . . . . . . . . . 74 Displaying Errors instead of Measurement Results . . . . . . . . . . . . . . . . . . . . . . . . . . . . . . . . . . . . . . . . . 76 Monitor Information. . . . . . . . . . . . . . . . . . . . . . . . . . . . . . . . . . . . . . . . . . . . . . . . . . . . . . . . . . . . . . . . . 79 BIN NO. DISPLAY Page. . . . . . . . . . . . . . . . . . . . . . . . . . . . . . . . . . . . . . . . . . . . . . . . . . . . . . . . . . . . . . . 80 Comparator Function ON/OFF. . . . . . . . . . . . . . . . . . . . . . . . . . . . . . . . . . . . . . . . . . . . . . . . . . . . . . . . . 81 BIN COUNT DISPLAY Page . . . . . . . . . . . . . . . . . . . . . . . . . . . . . . . . . . . . . . . . . . . . . . . . . . . . . . . . . . . 82 Counter Function . . . . . . . . . . . . . . . . . . . . . . . . . . . . . . . . . . . . . . . . . . . . . . . . . . . . . . . . . . . . . . . . . . . 83 LIST SWEEP DISPLAY Page. . . . . . . . . . . . . . . . . . . . . . . . . . . . . . . . . . . . . . . . . . . . . . . . . . . . . . . . . . . 84 Sweep Mode. . . . . . . . . . . . . . . . . . . . . . . . . . . . . . . . . . . . . . . . . . . . . . . . . . . . . . . . . . . . . . . . . . . . . . . 85 DISPLAY BLANK Page . . . . . . . . . . . . . . . . . . . . . . . . . . . . . . . . . . . . . . . . . . . . . . . . . . . . . . . . . . . . . . . 87 4.Configuring Measurement Conditions (Display and Function Related Settings)Initializing the Instrument . . . . . . . . . . . . . . . . . . . . . . . . . . . . . . . . . . . . . . . . . . . . . . . . . . . . . . . . . . . . . . 90 MEAS SETUP page. . . . . . . . . . . . . . . . . . . . . . . . . . . . . . . . . . . . . . . . . . . . . . . . . . . . . . . . . . . . . . . . . . . 91 Comment line . . . . . . . . . . . . . . . . . . . . . . . . . . . . . . . . . . . . . . . . . . . . . . . . . . . . . . . . . . . . . . . . . . . . . . 93 Trigger mode. . . . . . . . . . . . . . . . . . . . . . . . . . . . . . . . . . . . . . . . . . . . . . . . . . . . . . . . . . . . . . . . . . . . . . . 94 Automatic level control . . . . . . . . . . . . . . . . . . . . . . . . . . . . . . . . . . . . . . . . . . . . . . . . . . . . . . . . . . . . . . 96 DC Bias Current Isolation. . . . . . . . . . . . . . . . . . . . . . . . . . . . . . . . . . . . . . . . . . . . . . . . . . . . . . . . . . . . 100 Averaging Factor. . . . . . . . . . . . . . . . . . . . . . . . . . . . . . . . . . . . . . . . . . . . . . . . . . . . . . . . . . . . . . . . . . . 101 Trigger Delay Time. . . . . . . . . . . . . . . . . . . . . . . . . . . . . . . . . . . . . . . . . . . . . . . . . . . . . . . . . . . . . . . . . 102 Step Delay Time . . . . . . . . . . . . . . . . . . . . . . . . . . . . . . . . . . . . . . . . . . . . . . . . . . . . . . . . . . . . . . . . . . . 104 DC Bias V oltage Monitor . . . . . . . . . . . . . . . . . . . . . . . . . . . . . . . . . . . . . . . . . . . . . . . . . . . . . . . . . . . . 106 DC Bias Current Monitor. . . . . . . . . . . . . . . . . . . . . . . . . . . . . . . . . . . . . . . . . . . . . . . . . . . . . . . . . . . . 107 DCR Range. . . . . . . . . . . . . . . . . . . . . . . . . . . . . . . . . . . . . . . . . . . . . . . . . . . . . . . . . . . . . . . . . . . . . . . 108 DCI Range . . . . . . . . . . . . . . . . . . . . . . . . . . . . . . . . . . . . . . . . . . . . . . . . . . . . . . . . . . . . . . . . . . . . . . . 109 DC Source. . . . . . . . . . . . . . . . . . . . . . . . . . . . . . . . . . . . . . . . . . . . . . . . . . . . . . . . . . . . . . . . . . . . . . . . 110 Automatic Bias Polarity Control . . . . . . . . . . . . . . . . . . . . . . . . . . . . . . . . . . . . . . . . . . . . . . . . . . . . . . 111 Deviation Measurement . . . . . . . . . . . . . . . . . . . . . . . . . . . . . . . . . . . . . . . . . . . . . . . . . . . . . . . . . . . . . 113 CORRECTION page . . . . . . . . . . . . . . . . . . . . . . . . . . . . . . . . . . . . . . . . . . . . . . . . . . . . . . . . . . . . . . . . . 115 To set the correct function to on or off . . . . . . . . . . . . . . . . . . . . . . . . . . . . . . . . . . . . . . . . . . . . . . . . . . 116 The correction functions of the E4980A are operated as follows:. . . . . . . . . . . . . . . . . . . . . . . . . . . . . 117 Open Correction . . . . . . . . . . . . . . . . . . . . . . . . . . . . . . . . . . . . . . . . . . . . . . . . . . . . . . . . . . . . . . . . . . . 118 10Short Correction . . . . . . . . . . . . . . . . . . . . . . . . . . . . . . . . . . . . . . . . . . . . . . . . . . . . . . . . . . . . . . . . . . . 121 Correction Based on User-Specified Frequency Points . . . . . . . . . . . . . . . . . . . . . . . . . . . . . . . . . . . . . 123 Relationships between Correction Based on All Frequency Points and Correction Based on SpecifiedFrequency Points. . . . . . . . . . . . . . . . . . . . . . . . . . . . . . . . . . . . . . . . . . . . . . . . . . . . . . . . . . . . . . . . . . . 127 Reading/Writing Correction Data. . . . . . . . . . . . . . . . . . . . . . . . . . . . . . . . . . . . . . . . . . . . . . . . . . . . . . 129 Measurement Functions for the Standard . . . . . . . . . . . . . . . . . . . . . . . . . . . . . . . . . . . . . . . . . . . . . . . . 130 Selecting Single/Multiple Correction Mode. . . . . . . . . . . . . . . . . . . . . . . . . . . . . . . . . . . . . . . . . . . . . . 131 Selecting the Cable Length. . . . . . . . . . . . . . . . . . . . . . . . . . . . . . . . . . . . . . . . . . . . . . . . . . . . . . . . . . . 132 LIMIT TABLE SETUP Page . . . . . . . . . . . . . . . . . . . . . . . . . . . . . . . . . . . . . . . . . . . . . . . . . . . . . . . . . . . 133 Parameter Swap Feature . . . . . . . . . . . . . . . . . . . . . . . . . . . . . . . . . . . . . . . . . . . . . . . . . . . . . . . . . . . . . 134 Comparator Limit Mode . . . . . . . . . . . . . . . . . . . . . . . . . . . . . . . . . . . . . . . . . . . . . . . . . . . . . . . . . . . . . 136 Tolerance Mode Nominal Value . . . . . . . . . . . . . . . . . . . . . . . . . . . . . . . . . . . . . . . . . . . . . . . . . . . . . . . 138 Turning On/Off the Comparator . . . . . . . . . . . . . . . . . . . . . . . . . . . . . . . . . . . . . . . . . . . . . . . . . . . . . . . 139 Turning On/Off the Auxiliary Bin. . . . . . . . . . . . . . . . . . . . . . . . . . . . . . . . . . . . . . . . . . . . . . . . . . . . . . 140 Beep Feature . . . . . . . . . . . . . . . . . . . . . . . . . . . . . . . . . . . . . . . . . . . . . . . . . . . . . . . . . . . . . . . . . . . . . . 142 Lower and Upper Limits . . . . . . . . . . . . . . . . . . . . . . . . . . . . . . . . . . . . . . . . . . . . . . . . . . . . . . . . . . . . 143 LIST SWEEP SETUP Page . . . . . . . . . . . . . . . . . . . . . . . . . . . . . . . . . . . . . . . . . . . . . . . . . . . . . . . . . . . . 146 Sweep Mode . . . . . . . . . . . . . . . . . . . . . . . . . . . . . . . . . . . . . . . . . . . . . . . . . . . . . . . . . . . . . . . . . . . . . . 147 List Sweep Parameters . . . . . . . . . . . . . . . . . . . . . . . . . . . . . . . . . . . . . . . . . . . . . . . . . . . . . . . . . . . . . . 148 Sweep Points and Limit Modes. . . . . . . . . . . . . . . . . . . . . . . . . . . . . . . . . . . . . . . . . . . . . . . . . . . . . . . . 149 Sweep Parameter Auto-completion. . . . . . . . . . . . . . . . . . . . . . . . . . . . . . . . . . . . . . . . . . . . . . . . . . . . . 152 5.System ConfigurationsSYSTEM INFO Page . . . . . . . . . . . . . . . . . . . . . . . . . . . . . . . . . . . . . . . . . . . . . . . . . . . . . . . . . . . . . . . . . 156 Bias Current Interface. . . . . . . . . . . . . . . . . . . . . . . . . . . . . . . . . . . . . . . . . . . . . . . . . . . . . . . . . . . . . . . 157 Handler Interface. . . . . . . . . . . . . . . . . . . . . . . . . . . . . . . . . . . . . . . . . . . . . . . . . . . . . . . . . . . . . . . . . . . 158 Scanner Interface. . . . . . . . . . . . . . . . . . . . . . . . . . . . . . . . . . . . . . . . . . . . . . . . . . . . . . . . . . . . . . . . . . . 159 Monitor Information . . . . . . . . . . . . . . . . . . . . . . . . . . . . . . . . . . . . . . . . . . . . . . . . . . . . . . . . . . . . . . . . 159 SYSTEM CONFIG Page . . . . . . . . . . . . . . . . . . . . . . . . . . . . . . . . . . . . . . . . . . . . . . . . . . . . . . . . . . . . . . 160 Turning On/Off the Beep Feature . . . . . . . . . . . . . . . . . . . . . . . . . . . . . . . . . . . . . . . . . . . . . . . . . . . . . . 161 Changing the Beep Tone . . . . . . . . . . . . . . . . . . . . . . . . . . . . . . . . . . . . . . . . . . . . . . . . . . . . . . . . . . . . 162 Changing the Beep Tone . . . . . . . . . . . . . . . . . . . . . . . . . . . . . . . . . . . . . . . . . . . . . . . . . . . . . . . . . . . . 163 Configuring the Time Zone. . . . . . . . . . . . . . . . . . . . . . . . . . . . . . . . . . . . . . . . . . . . . . . . . . . . . . . . . . . 164 Configuring the System Date . . . . . . . . . . . . . . . . . . . . . . . . . . . . . . . . . . . . . . . . . . . . . . . . . . . . . . . . . 165 Configuring the GPIB Address. . . . . . . . . . . . . . . . . . . . . . . . . . . . . . . . . . . . . . . . . . . . . . . . . . . . . . . . 167 Configuring the LAN IP address. . . . . . . . . . . . . . . . . . . . . . . . . . . . . . . . . . . . . . . . . . . . . . . . . . . . . . . 168 SELF TEST Page . . . . . . . . . . . . . . . . . . . . . . . . . . . . . . . . . . . . . . . . . . . . . . . . . . . . . . . . . . . . . . . . . . . . 171 Choosing a Test Item. . . . . . . . . . . . . . . . . . . . . . . . . . . . . . . . . . . . . . . . . . . . . . . . . . . . . . . . . . . . . . . . 172 SERVICE Page. . . . . . . . . . . . . . . . . . . . . . . . . . . . . . . . . . . . . . . . . . . . . . . . . . . . . . . . . . . . . . . . . . . . . . 173 Monitor Information . . . . . . . . . . . . . . . . . . . . . . . . . . . . . . . . . . . . . . . . . . . . . . . . . . . . . . . . . . . . . . . . 174 Saving the System Information into External Memory . . . . . . . . . . . . . . . . . . . . . . . . . . . . . . . . . . . . . 174 6.Save/RecallOverview of Save/Recall Functionality . . . . . . . . . . . . . . . . . . . . . . . . . . . . . . . . . . . . . . . . . . . . . . . . . . . 176 Save Methods and Their Uses. . . . . . . . . . . . . . . . . . . . . . . . . . . . . . . . . . . . . . . . . . . . . . . . . . . . . . . . . 176 Folder/File Structure on USB Memory. . . . . . . . . . . . . . . . . . . . . . . . . . . . . . . . . . . . . . . . . . . . . . . . . . 176 USB Memory Notes . . . . . . . . . . . . . . . . . . . . . . . . . . . . . . . . . . . . . . . . . . . . . . . . . . . . . . . . . . . . . . . . 177 Saving/Recalling Instrument Configuration States. . . . . . . . . . . . . . . . . . . . . . . . . . . . . . . . . . . . . . . . . . . 178。
PCAN-MicroMod通用I O模块带CAN接口用户手册说明书

Universal I/O Module with CAN Interface User ManualDocument version 2.2.0 (2021-01-29)Relevant ProductsProduct Name Part number ModelPCAN-MicroMod IPEH-002080 with firmware 2.xPCAN® is a registered trademark of PEAK-System Technik GmbH. CANopen®, CANopen FD®, and CiA® are registered EU trademarks of CAN in Automation e.V. Other product names in this document may be the trademarks or registered trade-marks of their respective companies. They are not explicitly marked by ™ or ®.© 2021 PEAK-System Technik GmbHDuplication (copying, printing, or other forms) and the electronic distribution of this document is only allowed with explicit permission of PEAK-System Technik GmbH. PEAK-System Technik GmbH reserves the right to change technical data without prior announcement. The general business conditions and the regulations of the license agreement apply. All rights are reserved.PEAK-System Technik GmbHOtto-Roehm-Strasse 6964293 DarmstadtGermanyPhone: +49 6151 8173-20Fax: +49 6151 8173-29********************Document version 2.2.0 (2021-01-29)Contents1Introduction 4 1.1Properties at a Glance 4 1.2Scope of Supply 5 1.3Prerequisites for Operation 62Hardware Settings 7 2.1Setting the Module Number 7 2.2Disconnecting the High-speed CAN Transceiver 83Connectors 104Installing the Configuration Program 135Operation 15 5.1Status LED 15 5.2Reserved CAN ID 0x7E7 15 5.3Overview of Existing Services 166New/Alternative Firmware 18 6.1CANopen® Support 18 6.2Creating Own Firmware 19 6.3Uploading Firmware to the MicroMod 197Technical Specifications 24Appendix A Frequency/Resolution Diagram 26Appendix B Dimension Drawing 271IntroductionThe PCAN-MicroMod is designed for quick and easy access to distri-buted I/O systems. Its kernel is the microcontroller MB90F497 by Fujitsu. With an integrated CAN bus controller and the analog and digital inputs and outputs it is an inexpensive solution for small, intelligent nodes.At delivery the MicroMod has a standard firmware. The configura-tion is done by a Windows program transferring the configuration data to the module via CAN.It is also possible to use an alternative firmware (e.g. for the opera-tion under CANopen®) or to create own programs for the integrated microcontroller.Note: The functionality described in this manual refers to thestandard firmware available with delivery. For the operationwith an alternative firmware, please study the correspondingdocumentation. See also chapter 6 New/Alternative Firmwareon page 18.1.1Properties at a GlancePCAN-MicroModStrips for piggyback connection8 digital inputs, CMOS levels8 digital outputs, CMOS levels8 analog inputs, reference voltage 5 V (resolution 10 bits,sampling rate 1 kHz)4 frequency/PWM outputs (depending on firmware)4 inputs for frequency measurementCAN connection with NXP 82C251 transceiverCAN bit rates from 10 kbit/s to 1 Mbit/sExtended operating temperature range of -40 to +85 °C (-40 to+185 °F)Standard firmwareUp to 32 MicroMods configurable on a single CAN busTransmission of CAN messages periodically or at level changeof a digital inputLogic operations for digital inputsAdaptation of analog quantities through characteristic curvesDirect transfer of analog quantities onto CAN IDsDirect support of rotary encoders up to 100 Hz (e.g. rotary switchfor manual operation)4 PWM outputs, 8-bit, 32 Hz - 100 Hz and 4 - 10 kHz- or -2 PWM outputs, 16-bit, 1 Hz - 10 kHz (from firmware 2.5)- or -2 frequency outputs, 1 Hz - 10 kHz1.2Scope of SupplyPCAN-MicroModConfiguration software for WindowsManual in PDF format1.3Prerequisites for OperationBoard with socket strips for holding the PCAN-MicroMod(Evaluation Board, motherboard by PEAK-System, or proprietary development)For transferring configurations:•Computer with Windows 10, 8.1 (32/64-bit)•PC-CAN interface from PEAK-System•CAN cabling between the PC-CAN interface and the PCAN-MicroMod (on a motherboard) with correct termination(each 120 Ohms on both ends of the CAN bus)2Hardware Settings2.1Setting the Module NumberOn its upper side, the PCAN-MicroMod has five positions for solder jumpers (indicated by the labels 0 to 4) for setups of different func-tions depending on the used firmware. Using the standard firmware the solder jumpers are determining the module number. This is described in the following. With the optional CANopen® firmware other functions are assigned to the individual positions (see user manual for the CANopen® firmware).The module number is used for the identification of a single Micro-Mod at the CAN bus when configurations are sent and received. The MicroMod does not use the module number for the reception or transmission of data during normal operation. At delivery status the MicroMod has the module number 0 (no solder jumper set).Figure 1: Soldering positions for module numberEach MicroMod connected to the CAN bus must have a unique mo-dule number for configuring, otherwise unpredictable results could occur when configuring those MicroMods. As well, it isn't possible to send a configuration to several MicroMods at the same time. The module number is put together as follows: Each solder jumper position represents a bit of a binary number (position closed bysolder jumper = bit set). Position 0 is the LSB and position 4 the MSB of this number. Because there are 5 bits, module numbers between 0 and 31 can be set.Solder jumper0 (LSB) 1 2 3 4 (MSB)positiondigit 00001 00010 00100 01000 10000Binaryequivalent1 2 4 8 16DecimalExample:Solder jumpers are on positions 0, 1, and 3. The corresponding bi-nary number is 01011b (reversed order of positions) being equiva-lent to decimal 11, the module number.To do it the other way around: If you like to assign the module num-ber 22 to a MicroMod, you would do following steps:1.22 = 1·16 + 0·8 + 1·4 + 1·2 + 0·1 = 10110b2.MSB (position 4) Ö 10110 Õ LSB (position 0)3.Solder jumpers to be set: 1, 2, 4 (0 and 3 stay open)2.2Disconnecting the High-speed CANTransceiverIf you want to use another mode of CAN transmission but High-speed CAN (ISO 11898-2), the CAN signals CAN-RxD and CAN-TxD from the microcontroller or the MicroMod respectively can directly be lead to the desired CAN transceiver. The High-speed CAN tran-sceiver on the MicroMod must be disconnected from the data trans-fer in this case. This is done by interrupting the RxD line between the microcontroller and the CAN transceiver. For this you must unsolder the 0-Ohm resistor on the MicroMod (below and right to the label “4”).Figure 2: Position of the 0-Ohm resistor(RxD line to the High-speed CAN transceiver)If you want to use the High-speed CAN transceiver on the MicroModlater on, set a solder jumper at the mentioned position.3ConnectorsThe PCAN-MicroMod has two double strips (J1, J2), each with 26 pins (first column in the following table). Thus, the MicroMod can be plugged onto boards with matching socket strips (100-mil/2.54-mm grid, see also dimension drawing in Appendix B on page 27). For better orientation at the plug-in process the MicroMod has a white marker on the upper left corner (pin J2:2).Figure 3: Positions of the connection stripsand the positioning marker (upper left)In the second column of the table the corresponding pin of the MB90F497 microcontroller is listed if a direct connection to the MicroMod pin exists.PinPin μC Name FunctionMicroModJ1:1 4 AIN 1 Input Analog, 10-bit, 0 - VrefJ1:2 3 AIN 0 Input Analog, 10-bit, 0 - VrefJ1:3 6 AIN 3 Input Analog, 10-bit, 0 - VrefJ1:4 5 AIN 2 Input Analog, 10-bit, 0 - VrefJ1:5 8 AIN 5 Input Analog, 10-bit, 0 - VrefJ1:6 7 AIN 4 Input Analog, 10-bit, 0 - VrefJ1:7 10 AIN 7 Input Analog, 10-bit, 0 - VrefJ1:8 9 AIN 6 Input Analog, 10-bit, 0 - VrefJ1:9 12 Vref Reference voltage Analog, 2.7 - 5 VPinPin μC Name FunctionMicroModAnalogJ1:10 11 Avcc SupplyJ1:11 24, 49 GND Ground DigitalAnalogJ1:12 13 AGND GroundTransmit,CMOSJ1:13 63 CAN-TxD CANJ1:14 64 CAN-RxD CAN Receive, CMOSJ1:15 CAN_H High-speed CAN signal CAN_HJ1:16 CAN_L High-speed CAN signal CAN_LJ1:17 62 TxD Serial Transmit, TTLTTLJ1:18 60 RxD SerialReceive,J1:19 51 SCL (SPI or I2C) Serial clock, function depending onfirmwareSerial Data Out/Serial Dataor(SPI)J1:20 50 SDOSDA (I2C)Low-activeJ1:21 19 Reset_In Reset,J1:22 52 SDI (SPI) Serial Data InJ1:23 18 M0 Run mode: 5 V (internal pull-up)Prog mode: 0 VJ1:24 21 M2 Run mode: 0 VProg mode: 5 V (internal pull-up) J1:25 56 Vcc Supply 5 VJ1:26 24, 49 GND Ground DigitalJ2:1 48 DO 7 Output Digital, CMOSJ2:2 47 DO 6 Output Digital, CMOSJ2:3 46 DO 5 Output Digital, CMOSJ2:4 45 DO 4 Output Digital, CMOSJ2:5 44 DO 3 Output Digital, CMOSJ2:6 43 DO 2 Output Digital, CMOSJ2:7 42 DO 1 Output Digital, CMOSJ2:8 41 DO 0 Output Digital, CMOSJ2:9 40 FO 3 Output Frequency/PWM, CMOSJ2:10 39 FO 2 Output Frequency/PWM, CMOSJ2:11 38 FO 1 Output Frequency/PWM, CMOSJ2:12 37 FO 0 Output Frequency/PWM, CMOSPinPin μC Name FunctionMicroModJ2:13 24, 49 GND Ground DigitalJ2:14 N/C NotusedJ2:15 36 FI 3 Input Frequency, CMOS J2:16 35 FI2 Input Frequency, CMOS J2:17 34 FI 1 Input Frequency, CMOS J2:18 33 FI 0 Input Frequency, CMOS J2:19 32 DI 7 Input Digital, CMOSJ2:20 31 DI 6 Input Digital, CMOSJ2:21 30 DI 5 Input Digital, CMOSJ2:22 29 DI 4 Input Digital, CMOSJ2:23 28 DI 3 Input Digital, CMOSJ2:24 27 DI 2 Input Digital, CMOSJ2:25 26 DI 1 Input Digital, CMOSJ2:26 25 DI 0 Input Digital, CMOS4Installing theConfiguration ProgramWith the enclosed configuration program PCAN-MicroMod Configu-ration for Windows you can create, edit, and then transfer configu-rations to one or more MicroMods via CAN.Figure 4: Configuration program PCAN-MicroMod Configuration for Windows For transmission the program needs access to a CAN network. For this purpose the computer must have a CAN interface of the PCAN series (e.g. PCAN-USB). However, you can create and edit a configu-ration with the program on a computer without PCAN environment and transfer it with another computer to the corresponding Micro-Mod in a CAN network later.For downloading and installing the software, do the following:1.Download the software package for PCAN-MicroModConfiguration from our website. Use the correspondingentry on the following download page:/quick/DL-Software-E2.Open the downloaded file micromodconfig.zip.3.Start the setup.exe file and confirm any prompts for runningand for “Changes to the computer”.4.Follow the instructions of the installation program.You can find further information about the use of the program PCAN-MicroMod Configuration in the help which you can invoke in the program.5Operation5.1Status LEDLED Status Description Blinking at 1 Hz Normal operationBlinking at 2 Hz Invalid or noconfiguration This may be the case after a firmware update because the new firmware is possibly expecting another data format. You can solve this problem by sending a new configuration.Blinking at 5 Hz Configuration mode Occurs during sending or receiving aconfiguration via CAN.Continuously on Internal MicroModerror This may be the case after uploading a faulty or incompatible firmware.Continuously off No voltage supply;MicroMod inprogramming mode Whether the MicroMod is in normal or in programming mode (for the firmware upload) is determined by the status of the MicroMod pins M0 and M2 (see table in chapter 3 on page 10).5.2Reserved CAN ID 0x7E7For configuring the MicroMod the CAN ID 0x7E7 is used. The pro-gram PCAN-MicroMod Configuration exchanges the according data with the MicroMod via the CAN bus.When designing your CAN network, make sure not to use the CAN ID 0x7E7 in any way.5.3Overview of Existing ServicesWith the standard firmware, the PCAN-MicroMod provides various functions, called services.Service RemarkMessage Settings / Internal Variables Internal variables are useful for communication between services (in principle corresponds to CAN messages)Digital input For the event-controlled transmission of CANmessages it can be determined which kind of signalchange is considered as trigger.Digital output Power-up and timeout values can be defined (e.g.for problems with CAN communication).Analog input The A/D value can be adjusted with scale and offset.Furthermore, a software low-pass can be activated. Analog Output This service is only available with the appropriateconnection of a D/A converter to the MicroMod (e.g.with the motherboard Analog 2).Frequency input Frequencies between 1 Hz and about 10 kHz can bemeasured.PWM and frequency output By the incoming CAN messages either the pulsewidth is influenced at a predefined frequency or thefrequency is influenced at a fixed pulse width (50%). Digital function All digital inputs may be logically connected. Theresult may either be passed on as a CAN message orto a digital output.Constant values / statistical data Constant values or statistical data generated by the MicroMod can be put into CAN messages.Curve Analog input data can be converted with the help ofa curve.Rotary encoder The service interprets the signals from a manualrotary encoder (standard quadrature with 2 bits)connected to digital inputs. Input frequency max.100 Hz.Analog hysteresis For converting analog to digital signals (e.g. in orderto avoid jitter).Find more details about the functionality and the application of the services in the help of the configuration program PCAN-MicroMod Configuration.6New/Alternative FirmwareWith its integrated microcontroller the PCAN-MicroMod is flexible at use, because the functionality may be adapted or changed through suitable controlling software, also called firmware. This chapter describes possible alternatives and the procedure for a firmware update.6.1CANopen® SupportAs an alternative to the standard firmware we provide a CANopen firmware for the PCAN-MicroMod free of charge. With this the MicroMod falls into the category of off-the-shelf CANopen generic I/O devices. The whole CANopen software package implements the CANopen standard CiA® 301 “Application Layer and Communica-tion Profile” version 4.02 and specifically the device profileCiA® 401 “Device Profile for Generic I/O Modules” version 2.1. Therefore the correspondingly set up MicroMod can be directly used as standardized CANopen generic I/O module.The CANopen firmware (incl. documentation) is part of the software package for the PCAN-MicroMod. You can download the package with the following download link:/fileadmin/media/files/pcanmicromod.zip6.2Creating Own FirmwareThe PCAN-MicroMod contains the microcontroller MB90F497 by Fujitsu (now: Cypress). With the C development environment Softune Workbench (available separately) you can create own firmware for the PCAN-MicroMod.Website of the microcontroller manufacturer: 6.3Uploading Firmware to the MicroModThe standard firmware can change regarding functionality and error correction so that an update can be necessary. On the other hand perhaps you would like to use an alternative firmware for the Micro-Mod. In both cases you must transmit the desired firmware to the MicroMod via a serial RS-232 port (upload).For a firmware upload you need:a motherboard for the MicroMod with the following features:•an RS-232 connector (with a driver connected ahead) MicroModpinName FunctionJ1:17 TxD Serial transmit (TTL levels)J1:18 RxD Serial receive (TTL levels)• a switch or jumper to set the MicroMod to programming modeMicroMod pin Name Programming mode Normal operationmodeJ1:23 M0 0 V 5 V (internal pull-up) J1:24 M2 5 V (internal pull-up) 0 V• a pushbutton to reset the MicroModMicroModpinName Status for resetJ1:21 Reset_In 0V•the possibility to set the digital inputs 0 and 1 to Low stateMicroMod pin Name Status forfirmware uploadJ2:25 DI 1 0 VJ2:26 DI 0 0 VTip: An easy way to do a firmware upload is using the PCAN-MicroMod Evaluation Board (optionally available). It has the necessary connectors and switches.a serial RS-232 port on a computer running Windowsa serial 1:1 cable with male D-Sub connectorsthe Windows software FLASH MCU Programmer for theF²MC-16LX microcontroller family.You can download a setup program of the current version from the Cypress website (). Search for “mcu programmer” there.the firmware file (*.mhx)Do the following to upload a new firmware:1.Make sure that the motherboard with the MicroMod isswitched off.2.Connect the motherboard and the serial port of your compu-ter with the serial cable.3.Set the corresponding switch or jumper so that the Micro-Mod will start in programming mode.4.Apply power.The LED on the MicroMod stays off.5.Make sure that a Low level is applied to digital inputs 0and 1.6.Reset the MicroMod.7.Under Windows, start the FUJITSU FLASH MCU Program-mer (FMC16LX).8.Select Set Environment in order to check that the indicatedserial port is corresponding to the actually used one.Confirm with OK.9.Do the following settings:Target Microcontroller: MB90F497/GCrystal Frequency: 4 MHze the Open button behind the Hex File field to select thefirmware file that shall be used for upload.11.Start the transfer sequence by clicking on Full Operation(D+E+B+P+R).The process takes approximately one minute. At its end a message is shown that confirms the proper sequence.12.Disconnect the power from the motherboard.13.Setup the normal operation mode (Run mode) for theMicroMod, before applying power again.The upload procedure is finished and you can use the MicroMod normally now.LED-Status After Updating the Standard FirmwareIf after an update the LED on the MicroMod is blinking fast (2 Hz) in normal operation mode, the current configuration is not compatible to the new firmware version. In this case, transfer the configuration to the MicroMod again, with adaptation if needed.If the LED stays off after the update, the firmware does not work. Repeat the upload procedure in this case or use another version of the standard firmware.7Technical SpecificationsPower supplySupply voltage +5 V DCCurrent consumption max. 160 mAConnectorsConnection strips 2 double strips, each with 26 pinsGrid 100 mil (2.54 mm)Control and communicationMB90F497G Microcontroller FujitsuStandard firmware Configuration via reserved CAN ID 0x7e7CANSpecification ISO 11898-2, High-speed CAN2.0A (standard format)2.0B (extended format) (from firmware 2.0) Bit rates 10 kbit/s - 1 Mbit/s (see also “Properties withstandard firmware” below)Transceiver NXP PCA82C251(disconnectable for use of an alternativetransceiver on the motherboard) Termination noneInputs/outputsDigital inputs 8, CMOSFrequency inputs 4, CMOSAnalog inputs 8, reference voltage 5 V, resolution 10 bits,sample rate 1 kHz, input impedance 3.2 kΩDigital outputs 8, CMOSFrequency/PWM outputs 4 (depending on firmware)Properties with standard firmwareFrequency inputs Measuring range 1 Hz – 10 kHz (maximumdepends on work load, min. 4 kHz) Frequency/PWM outputs 4 PWM (8-bit mode):32 - 100 Hz, 4 - 10 kHz,frequency-dependent resolution 1.3 - 1.0 %- or -2 PWM (16-bit mode, from firmware 2.5):1 Hz - 10 kHz,frequency-dependent resolution 0.205 - 0.005 %(see also diagram in Appendix A on page 26)- or -2 frequency: 1 Hz - 10 kHz,minimum step width 1 HzConfigurable CAN bit rates (kbit/s) 10; 20; 33.3; 47.6; 50; 83.3; 95.2; 100; 125; 250; 500; 800; 1000MeasuresSize 32 x 35 x 13 mm (W x L x H)See also dimension drawing in Appendix B onpage 27Weight 9gEnvironmentOperating temperature -40 - +85 °C (-40 - +185 °F)Temperature for storage andtransport-40 - +100 °C (-40 - +212 °F)Relative humidity 15 - 90 %, not condensingConformityRoHS 2 Directive 2011/65/EUDIN EN 50581 VDE 0042-12:2013-02Appendix A Frequency/Resolution DiagramFigure 5: Frequency-dependent resolution PWM 16-bit modeAppendix B Dimension DrawingFigure 6: Top view and side view PCAN-MicroMod。
- 1、下载文档前请自行甄别文档内容的完整性,平台不提供额外的编辑、内容补充、找答案等附加服务。
- 2、"仅部分预览"的文档,不可在线预览部分如存在完整性等问题,可反馈申请退款(可完整预览的文档不适用该条件!)。
- 3、如文档侵犯您的权益,请联系客服反馈,我们会尽快为您处理(人工客服工作时间:9:00-18:30)。
Plasmalab System100Modular Cluster System – RIEInstallation DataIssue 11: February 2011Plasmalab System100 Oxford Instruments Plasma Technology Installation DataInstallation Data (RIE)Issue 11: February 11Page 2 of 22Printed: 10-Feb-11, 9:03ContentsPage1. Introduction ............................................................................................................ 3 2. Installation information ........................................................................................... 4 2.1 Dimensions ........................................................................................................ 4 2.2 Weights .............................................................................................................. 4 2.3 Heat load ........................................................................................................... 4 3. Services connections ............................................................................................... 7 4. Gas handling .......................................................................................................... 9 5. Services ................................................................................................................ 12 5.1 Electrical Supply requirement ........................................................................... 12 5.2 Water Cooling requirement ............................................................................... 12 5.3 Lower Electrode Cooling requirement ............................................................... 12 5.4 Compressed Air requirement ............................................................................ 12 5.5 Nitrogen requirement ....................................................................................... 13 5.6 Process gas requirement .................................................................................. 13 5.7 Helium requirement ......................................................................................... 13 5.8 Extraction requirement ..................................................................................... 13 6. Pump set information ........................................................................................... 14 7. Heater/chiller information ..................................................................................... 16 8. PLC interlock chain ............................................................................................... 18 8.1 General description .......................................................................................... 18 8.2 Gas box interlocks ........................................................................................... 20 8.2.1 Incompatible gases .................................................................................... 20 8.2.2 System Link Configuration Table ................................................................ 21 8.2.3 System LED Monitoring Table (22)9. OIPT locations worldwide (22)Fig 1: RIE system layout (3-frame) ............................................................................... 5 Fig 2: RIE system layout (2-frame clusterable) ............................................................. 6 Fig 3: RIE services panel .............................................................................................. 7 Fig 4: Electrical connections ........................................................................................ 8 Fig 5: 4-Line gas pod .................................................................................................. 9 Fig 6: 8-Line gas pod ................................................................................................ 10 Fig 7: 12-line gas pod ............................................................................................... 11 Fig 8: Gas box interlock chain .. (20)Installation Data Oxford Instruments Plasma Technology Plasmalab System100Installation Data (RIE)Printed: 10-Feb-11, 9:03Page 3 of 22Issue 11: February 111.IntroductionThis installation specification document gives information about the Plasmalab System100 to enable customers to prepare the required environment for the system.Note that all dimensions shown in these data sheets are typical; precise dimensions depend on the actual equipment fit. All dimensions are given in millimetres unless otherwise stated. NOTE :All information, services, dimensions etc., refer only to thePlasmalab System100, i.e. plasma processing at up to 200 mm wafers in MESC compatible chambers.Consider access when planning the system installation. Ensure that good access isavailable to parts of the system that require maintenance. Ensure that all isolation points for the system services are easily accessible.Oxford Instruments Plasma Technology conducts a programme of continual product development, and reserves the right to change the design and/or specification of equipment without notice. The details contained in this document were correct at the time of printing but should be confirmed immediately prior to delivery. Details of the clean room interface will be advised at the time of delivery.Plasmalab System100 Oxford Instruments Plasma Technology Installation DataInstallation Data (RIE)Issue 11: February 11Page 4 of 22Printed: 10-Feb-11, 9:032.Installation information2.1DimensionsSystem dimensions are given in Fig 1 and Fig 2. Gas handling component dimensions are given in Fig 5, Fig 6 and Fig 7. Pump dimensions are given in Section 6. Heater/chiller dimensions are given in Section 7.2.2WeightsTypical weights of system components:2-frame system: 290 kg3-frame system: 360 kg6-line Gas pod: 35 kg12-line Gas pod: 65 kgPumps: See Section 6 (Pump set information).Heater/chillers: See Section 7 (Heater/chiller information).2.3Heat loadThe typical heat load for the clean room installation is:Operating: 2 kWPassive:1.5 kWNote that these specifications do not include externally sited components, e.g. pumps, heater/chillers, transformers, etc..Heat loads for typical chillers are given in the following table. The heat loads are quoted for a bath temperature of 20°C and 100% cooling.Installation Data Oxford Instruments Plasma Technology Plasmalab System100Fig 1: RIE system layout (3-frame)NOTE: For services panel details, see Fig 3.Installation Data (RIE)Printed: 10-Feb-11, 9:03Page 5 of 22 Issue 11: February 11Plasmalab System100 Oxford Instruments Plasma Technology Installation DataInstallation Data (RIE)Issue 11: February 11Page 6 of 22Printed: 10-Feb-11, 9:03Fig 2: RIE system layout (2-frame clusterable)NOTE: For services panel details, see Fig 3.Installation Data Oxford Instruments Plasma Technology Plasmalab System100Installation Data (RIE)Printed: 10-Feb-11, 9:03 Page 7 of 22Issue 11: February 113. Services connectionsFig 3: RIE services panelNOTE:The Automatic load lock services panel is similar to that shown above but only the CHAMBER BACKING connector is used.Plasmalab System100 Oxford Instruments Plasma Technology Installation DataInstallation Data (RIE)Issue 11: February 11Page 8 of 22Printed: 10-Feb-11, 9:03Fig 4: Electrical connectionsInstallation Data Oxford Instruments Plasma Technology Plasmalab System100Installation Data (RIE)Printed: 10-Feb-11, 9:03Page 9 of 22Issue 11: February 114. Gas handlingIMPORTANTOIPT gas pods typically weigh >40kg. If you intend fixing your gas pod to a wall, ensure the wall and gas pod fixings are sturdy enough to bear at least four times the weight of the gas pod. Periodically, e.g. annually, check the gas pod and its fixings are secure.Fig 5: 4-Line gas podPlasmalab System100 Oxford Instruments Plasma TechnologyInstallation DataInstallation Data (RIE)Issue 11: February 11Page 10 of 22Printed: 10-Feb-11, 9:03Fig 6: 8-Line gas podFig 7: 12-line gas pod5.ServicesThe required services are listed in the following sub-sections. For full details of servicesspecifications including connection diagrams, electrical connection schematic etc., read inconjunction with the Oxford Instruments Plasma Technology ‘Services Specifications forPlasmalab and Ionfab Systems’ document.5.1Electrical Supply requirementFunction Connection Parameter SpecificationSystem electrical supply (208V system) Cable (4 meterslong)Voltage 208Vac ±10%Current 32 AFrequency 50 / 60 HzPhases 3 phase, N + ESystem electrical supply (415V system) Cable (4 meterslong)Voltage 380Vac –10% to415Vac +6%Current 32 AFrequency 50 / 60 HzPhases 3 phase, N + E5.2Water Cooling requirementFunction Connection Parameter SpecificationProcess turbo 1/4” stainless steelSwagelok Flow 1 lpm (0.27 gpm (US)) Temperature 15 - 25°C (59 - 77°F)RF Generator (1200W only) 3/8” stainless steelSwagelokFlow 4 lpm (1.1 gpm (US))Temperature 10 - 25°C (50 - 77°F)AMU 3/8” stainless steelSwagelok Flow 2 lpm (0.53 gpm (US)) Temperature 10 - 25°C (50 - 77°F)Load lock turbo (if required) 1/4” stainless steelSwagelokFlow 1 lpm (0.27 gpm (US))Temperature 15 - 25°C (59 - 77°F)5.3Lower Electrode Cooling requirementFunction Connection Parameter SpecificationLiquid cooled lower electrode 3/8” stainless steelSwagelok to heater/ chiller unitFlow 2 lpm (0.53 gpm (US))Temperature As required by process5.4Compressed Air requirementFunction Connection Parameter SpecificationSystem CDA 4mm push-fitLegris Flow 5 lpm (0.2 cfm)(combined with gaspod)Pressure 4.0 – 6.0 Bar (60 – 90psi)Gas pod CDA 4mm push-fitLegris Flow 5 lpm (0.2 cfm)(combined withsystem)Pressure 4.0 – 6.0 Bar (60 – 90psi)5.5Nitrogen requirementFunction Connection Parameter Specification2Swagelok Flow 8 lpm (0.32 cfm) Pressure 3.0 Bar (45 psi)minimumRotary pump purge ¼” stainless steelSwagelok typically Flow Refer to sub-section6.1 Rotary pumppurging Pressure Refer to sub-section6.1 Rotary pumppurging5.6Process gas requirementFunction Connection Parameter SpecificationProcess gas in ¼” stainless steelwelded pipe at gaspod, ¼” stainlesssteel VCR atsystem. Pressure 2.0 – 3.0 Bar (30 – 45psi)5.7Helium requirementFunction Connection Parameter SpecificationHelium in ¼” stainless steelSwagelok Pressure 2.0 – 3.0 Bar (30 – 45psi)5.8Extraction requirementFunction Connection Parameter Specificationm3/hour (0.6 cfm)12-line gas pod – 3m3/hour (1.8 cfm)Rotary pump exhaust Refer to Section 6 Pump set information6.Pump set information6.1Process pump options6.1.1Rotary pump purgingThe requirements for rotary pump purging depend on the process used. Customersshould consult the pump manufacturer for their recommendations.For Alcatel 2033 and 2063 rotary pumps, the recommended minimum N2 purge rate is2 litres/minute at a pressure of 2bar to 5bar. For highly corrosive or pyrophoric gases,4 litres/minute is recommended.6.1.2Dry pump water coolingFor Alcatel ADP122P and ADS602P dry pumps, the recommended minimum cooling waterflow rate is 1 litre/minute.6.2Loadlock and wafer-handler pump options7.Heater/chiller informationIMPORTANT: Heater/chillers should be filled/topped up with one of the fluids listed Ithe following table, as appropriate. Refer the OIPT ‘Services Specificationsfor Plasmalab and Ionfab systems’ document, sub-section 2.1 for thewarranty impact of not using these products.8.PLC interlock chain8.1General descriptionThe interlocks form a continuous 24Vdc chain, which must be complete before theprocess gases and RF power supplies are enabled. An output to disable external devicesunless the lid/ hoist is closed is also provided; this is typically used to disable a lid-mounted endpoint detector laser.The interlock chain is monitored by the software, but acts independently. It is alsosupplemented by machine protection sensors, which operate only via the software.To enable RF power:∙The 600 mbar vacuum switch (‘Vacstat’) must be at low pressure∙The process chamber lid must be shut (or its hoist down)∙The primary process pump must be running∙The primary process pressure gauge (normally a capacitance manometer) must be on scale∙The load lock inter-chamber valve (where fitted) must be closed∙Customer-supplied external alarm devices must be in their safe state∙The inert gas purge to the primary process pump must be flowing.To enable process gases:∙RF power must be enabled∙The gas box lid must be shut∙Specific gases can be set in the gas box hardware to be mutually exclusive, so that they cannot be turned on together.Machine protections fitted where appropriate:∙ A nitrogen pressure switch, to detect adequate purge pressure to turbomolecular pump bearings.OR:∙ A nitrogen flow meter, to detect purge gas flow to pump bearings.∙Water flow switch(es).RF enable interlock chain details are given in Table 1; Refer to drawing 94-SE00A26865 (PC2003 interface schematic).Table 1: RF enable interlock chain detailsIf above satisfied, then 24V is at BLK20, 21 & 22 pin 1. This enables the K4 contactor to supply power to the RF Generator.8.2Gas box interlocksRefer to drawing: 94-SE81B26657 (PC2003 gas pod loom).To enable process gases, the RF interlock chain must be complete. The gas box interlockis shown in Fig 8.Fig 8: Gas box interlock chain8.2.1Incompatible gasesTable 2: Incompatible gasesThe gas box has a facility to prevent incompatible gases from being enabledsimultaneously, using soldered links.Installation Data Oxford Instruments Plasma Technology Plasmalab System100 8.2.2System Link Configuration TableTable 3: System link configurationInstallation Data (RIE)Printed: 10-Feb-11, 9:03Page 21 of 22 Issue 11: February 11Plasmalab System100 Oxford Instruments Plasma Technology Installation DataInstallation Data (RIE)Issue 11: February 11 Page 22 of 22Printed: 10-Feb-11, 9:038.2.3System LED Monitoring TableTable 4: System LED monitoringNote that when the interlock chain is complete, all LEDs are illuminated.9. OIPT locations worldwideUKOxford Instruments Plasma Technology North End, Yatton, Bristol, BS49 4APTel: +44(0)1934 837000 Fax: +44(0)1934 837001Email: plasma.technology@ Web: /plmchp5.htmUSAOxford Instruments Inc.300 Baker Avenue, Suite 150 Concord, MA 01742Phone: +1 978-369-9933 Toll Free: +1 800-447-4717 Fax: +1 978-369-8287 Email: a@GermanyOxford Instruments GmbH Otto-von-Guericke Ring 10, D-65205 Wiesbaden Tel: +49(0)6122 937161 Fax: +49(0)6122 937175 Email: plasma@oxford.deJapanOxford Instruments K.K. 2-11-6 TomiokaKoto-ku, Tokyo 135-0047 Tel: +81-3-5245-3261 Fax: +81-3-5245-4466 Email: oikkpt@oxinst.co.jpWeb: www.oxford-instruments.jpPeople‟s Republic of China (Beijing) Oxford Instruments China Room 714, Office Tower 3, Henderson Center,No. 18 Jianguomennei Ave, Dongcheng District, Beijing 100005Tel: +86 106518 8160/1/2 Fax: +86 106518 8155 Email: ptsales@Web: People‟s Republic of China (Shanghai)Oxford Instruments China Room 14-F, No.1 Plaza 800 Nanjing East Road Shanghai 200001 Tel: +86 216360 8530 Fax: +86 216360 8535 Email: ptsales@Web: SingaporeOxford Instruments Pte. Ltd 371 Beach Road, #02-07 Keypoint Singapore 199597 Tel: +65 6337 6848 Fax: +65 6337 6286Email: oipt.sales@.sgTaiwanOxford Instruments Overseas Marketing Ltd.1F, No 23 Jing-Shang 19thStreet, Hsinchu, Taiwan Tel: +65 6337 6848 Fax: +65 6337 6286Email: oipt.sales@.sg。