PDM-41M-3G中文资料
安徽伟仪科技有限公司产品选型手册说明书

安徽伟仪科技有限公司Anhui WEYII Science And Technology Co.,L TD.产品选型手册PRODUCT SELECTION GUIDE安徽伟仪科技有限公司Anhui WEYII Science And Technology Co.,L TD.地址(ADD):安徽省合肥市高新区创新大道2700号电话(TEL):400-997-0788 专注于气密检漏仪与气密检测设备专心 专注 专业专注于气密检漏仪与气密检测设备专心 专注 专业感谢以下品牌的长期支持与合作!安徽伟仪科技有限公司位于合肥市国家高新技术产业开发区,是一家专业从事气密检漏仪、气密检测设备、流体控制与气动技术领域的研发、生产与服务的高新技术企业。
Anhui Weiyi Technology Co., Ltd. is located in Hefei National High-tech Industrial Development Zone. Weiyi is a high-tech manufacturer specializing in R &D and service of air tightness detector, air tightness detection related equipment, fluid control and pneumatic technology.Since the establishment, We has always adhered to the management principle of talent oriented and core technology centered.Weiyi has gathered a large number of elites in the industry as technical backbones relying on the resources of China University of science and technology, Hefei University of Technolo-gy and other scientific research institutes. The advanced detection technology and design in China and abroad is combined with Weiyi's innovation also the requirement of customers. More professional solutions could provided based on this. We believe continuous improvement of product quality keeps its core competitiveness in the fierce market competition.We always strive for continuous innovation and excellence. We aim to win customers' trust with perfect products and high-quality services. We are concen-trating on being the first choice within international market.公司自成立以来,始终坚持以人才为本、核心技术为中心的经营原则,同时依托中科大、合工大及科研院所为资源,汇聚大量业内精英作为技术骨干,将国内外先进的检测技术、设计思路与伟仪的创新理念及用户的实际需求相结合,为客户提供更专业的解决方案,完善产品质量,使其在激烈的市场竞争中保持核心竞争力。
莫莎公司 OnCell G2111 G2151I 系列工业四频GSM GPRS模块产品简介说明书

OnCell G2111/G2151I SeriesIndustrial quad-band GSM/GPRS modemsFeatures and Benefits•Quad-band GSM/GPRS850/900/1800/1900MHz•DIN-rail mounting and wall mounting•2.5kV RMS isolation for1min.for all serial signals(G2151I only)•LED indicators for GSM/GPRS and data transmission status•Extended operating temperature from-25to70°C(G2111-T only)CertificationsIntroductionThe OnCell G2111/G2151I Series of industrial quad-band GSM/GPRS modems are designed to transmit data and short messages(SMS)over GSM/ GPRS mobile networks.The modems can be used to increase the efficiency of maintenance and communication,but do not require extensive training.In addition,the modems can be mounted on a DIN rail or wall.The OnCell G2111/G2151I Series modems accept a12to48VDC power input,making them suitable for use with a variety of field power sources.The serial ports feature15kV ESD line protection to protect the products from harmful electrical discharge,and separate RS-232and RS-422/485 interfaces are built into the OnCell G2151I,each with2.5kV RMS isolation protection for one minute.The two serial interfaces on the OnCell G2151I make it ideal for attaching all kinds of devices,such as stand-alone controllers,PC COM ports,and multi-dropped electric meters.In addition,the OnCell G2111-T has an extended operating temperature(-25to70°C)design that makes it suitable for heavy industrial use. SpecificationsCellular InterfaceCellular Standards GSM,GPRSBand Options Quad-band GSM/GPRS850MHz/900MHz/1800MHz/1900MHzGPRS Multi-Slot Class10GPRS Terminal Device Class Class BGPRS Coding Schemes CS1to CS4CSD Data Rates Up to14400bpsCellular Antenna Connectors1SMA femaleNo.of SIMs1SIM Control Voltage3VSerial InterfaceNo.of Ports1Serial Standards All models:RS-232(DB9female connector)OnCell G2151I:RS-232/422/485(5-pin terminal block connector)ESD Protection OnCell G2111:15kVIsolation OnCell G2151I:2kVData Bits8Stop Bits1Parity NoneFlow Control RTS/CTSBaudrate300bps to230.4kbpsSerial SignalsRS-232TxD,RxD,RTS,CTS,DTR,DSR,DCD,RI,GNDRS-422Tx+,Tx-,Rx+,Rx-,GNDRS-485-2w Data+,Data-,GNDRS-485-4w Tx+,Tx-,Rx+,Rx-,GNDPower ParametersInput Voltage12to48VDCPower Connector Terminal blockInput Current0.625A@12VDC,0.16A@48VDCPhysical CharacteristicsHousing ABS+PolycarbonateIP Rating IP30Dimensions27x123x79mm(1.06x4.84x3.11in)Weight155g(0.34lb)Environmental LimitsOperating Temperature OnCell G2111/G2151I:-20to55°C(-4to131°F)OnCell G2111I-T:-25to70°C(-22to158°F)Storage Temperature(package included)-40to75°C(-40to167°F)Ambient Relative Humidity5to95%(non-condensing)Standards and CertificationsSafety UL60950-1EMC EN55032/24EMI CISPR32,FCC Part15B Class AEMS IEC61000-4-2ESD:Contact:4kV;Air:8kVIEC61000-4-3RS:80MHz to1GHz:3V/mIEC61000-4-4EFT:Power:0.5kVIEC61000-4-5Surge:Power:1kVIEC61000-4-6CS:3VIEC61000-4-8PFMFRadio Frequency FCC Part22H,FCC Part24E,EN301489-1,EN301489-7,EN301511MTBFTime OnCell G2111:925,000hrsOnCell G2111-T:925,000hrsOnCell G2151I:864,000hrsStandards Telcordia SR332WarrantyWarranty Period5yearsDetails See /warrantyPackage ContentsDevice1x OnCell G2111/G2151I Series GSM/GPRS modem1Antenna1x GSM/GPRSAccessory1x terminal block for power jack connectorDocumentation1x quick installation guide1x warranty cardDimensionsOrdering InformationModel Name Cellular Standard Band Operating Temp.Serial Isolation Serial StandardsOnCell G2111GSM/GPRS 850/900/1800/1900MHz-20to55°C–RS-232OnCell G2111-T GSM/GPRS 850/900/1800/1900MHz-25to70°C–RS-232OnCell G2151I GSM/GPRS 850/900/1800/1900MHz-20to55°C✓RS-232/422/4851.An activated SIM card(not included)must be provided by a third party Cellular Service Provider.Accessories(sold separately)AntennasANT-CQB-AHSM-00-3m GSM/GPRS/EDGE,omni-directional magnetic base antenna,0dBi,3m cableANT-CQB-AHSM-03-3m GSM/GPRS/EDGE,omni-directional magnetic base antenna,3dBi,3m cableANT-CQB-AHSM-05-3m GSM/GPRS/EDGE,omni-directional magnetic base antenna,5dBi,3m cableANT-CQB-ASM-01GSM/GPRS/EDGE,omni-directional rubber duck antenna,1dBiANT-WCDMA-ANF-00GSM/GPRS/EDGE/UMTS/HSPA,omni-directional outdoor antenna,0dBiANT-WCDMA-ASM-1.5GSM/GPRS/EDGE/UMTS/HSPA,omni-directional rubber duck antenna,1.5dBiANT-WCDMA-AHSM-04-2.5m GSM/GPRS/EDGE/UMTS/HSPA,omni-directional magnetic base antenna,4dBiANT-LTE-ASM-02GPRS/EDGE/UMTS/HSPA/LTE,omni-directional rubber duck antenna,2dBiANT-LTE-ANF-04GSM/GPRS/EDGE/UMTS/HSPA/LTE,omni-directional outdoor antenna,4dBi,IP66AntennasANT-LTEUS-ASM-01GSM/GPRS/EDGE/UMTS/HSPA/LTE,omni-directional rubber duck antenna,1dBiWireless Antenna CableA-CRF-SMSF-R3-100Cellular magnetic-base SMA connector with1-meter RF cable©Moxa Inc.All rights reserved.Updated Nov12,2018.This document and any portion thereof may not be reproduced or used in any manner whatsoever without the express written permission of Moxa Inc.Product specifications subject to change without notice.Visit our website for the most up-to-date product information.。
LM41CIMT资料

LM41Hardware Monitor with Thermal Diode Inputs and SensorPath ™BusGeneral DescriptionThe LM41is a hardware monitor that measures 2tempera-ture zones,5voltages and has a single-wire interface com-patible with National Semiconductor’s SensorPath bus.Sen-sorPath data is pulse width encoded,thereby allowing the LM41to be easily connected to many general purpose micro-controllers.Several National Semiconductor Super I/O products include a fully integrated SensorPath master,that when connected to the LM41can realize a hardware monitor function that includes limit checking for measured values,autonomous fan speed control and many other functions.The LM41measures the temperature of its own die as well as one external device such as a processor thermal diode or a diode connected transistor.The LM41can resolve tem-peratures up to 255˚C and down to -256˚C.The operating temperature range of the LM41is 0˚C to +125˚ing Σ∆ADC it measures +1.2V,+2.5V,+3.3V,+5V and +12V analog input voltages with internal scaling resistors.The address programming pin allows two LM41’s to be placed on one SensorPath bus.Featuresn SensorPath Interface—2hardware programmable addresses n Voltage Monitoring —9-bit Σ∆ADC—Internal scaling resistors for all inputs—Monitors +1.2V,+2.5V,+3.3V,+5V and +12V n Temperature Sensing—Remote diode temperature sensor zone —Internal local temperature zone —0.5˚C resolution—Measures temperatures up to 140˚C n 14-lead TSSOP packageKey Specificationsn Voltage Measurement Accuracy ±2%(max)n Temperature Sensor Accuracy ±3˚C (max)n Temperature Range:—LM41junction0˚C to +85˚C —Remote Temp Accuracy 0˚C to +100˚C n Power Supply Voltage+3.0V to +3.6Vn Average Power Supply Current 0.5mA (typ)n Conversion Time (all Channels)22.1ms to 1456msApplicationsn Microprocessor based equipment(Motherboards,Video Cards,Base-stations,Routers,ATMs,Point of Sale,…)n Power SuppliesTypical Application20070301SensorPath ™is a trademark of National Semiconductor CorporationMay 2004LM41Hardware Monitor with Thermal Diode Inputs and SensorPath ™Bus©2004National Semiconductor Corporation Connection DiagramTSSOP-1420070302Top ViewNational Package Number MTC14COrder Number Package Marking NS Package Number Transport Media LM41CIMT LM41CIMT MTC14C 94units per railLM41CIMTXLM41CIMTMTC14C2500units in tape and reelPin DescriptionPin Number Pin NameDescription Typical Connection1,10,13,14NC No Connect May be tied to V+,GND or left floating.Do not tie active signals to pin 10.2GND GroundSystem ground3V+/+3.3V_SBYPositive power supply pin as well as a +3.3V voltage monitorConnected system 3.3V standby power and to a 0.1µF bypass capacitor in parallel with 100pF.A bulk capacitance of approximately 10µF needs to be in the near vicinity of the LM41.4SWD SensorPath Bus line;Open-drain outputSuper I/O,Pull-up resistor,1.6k5ADDDigital input -device number select input for the serial bus device numberPull-up to 3.3V or pull-down to GND resistor,10k;must never be left floating 6+1.2V +1.2V voltage monitoring input with scaling resistorsProcessor core voltage to be monitored 7+2.5V +2.5V voltage monitoring input with scaling resistorsPower supply voltage to be monitored 8D-Thermal diode analog voltage output and negative monitoring inputRemote Thermal Diode cathode(THERM_DC)-Can be connected to a CPU or thermal diode,an MMBT3904or a GPU thermal diode.A 100pF capacitor should be connected between respective D-and D+for noise filtering.9D+Thermal diode analog current output and positive monitoring input Remote Thermal Diode anode (THERM_DA)-Can be connected to a CPU or thermal diode,an MMBT3904or a GPU thermal diode.A 100pF capacitor should be connected between respective D-and D+for noise filtering.11+5V +5V voltage monitoring input with scaling resistorsPower supply voltage to be monitored 12+12V+12V voltage monitoring input with scaling resistorsPower supply voltage to be monitoredL M 41 2LM41 Block Diagram3Absolute Maximum Ratings(Notes 2,1)Supply Voltage (V +)−0.5V to 6.0V Voltage at Any Digital Input or Output Pin−0.5V to 6.0V Voltage on 12V Analog Input −0.5V to 16V Voltage on 5V Analog Input −0.5V to 6.67VVoltage on D+−0.5V to (V++0.05V)Voltage on Other Analog Inputs −0.5V to 6.0VCurrent on D-±1mA Input Current per Pin(Note 3)±5mA Package Input Current (Note 3)±30mAPackage Power Dissipation (Note 4)Output Sink Current 10mAESD Susceptibility (Note 5)Human Body Model 2500V Machine Model 250VStorage Temperature−65˚C to +150˚C Soldering process must comply with National’s reflow temperature profile specifications.Refer to /packaging/.(Note 6)Operating Ratings(Notes 1,2)Temperature Range for Electrical Characteristics LM41CIMT (T MIN ≤T A ≤T MAX )0˚C ≤T A ≤+85˚C Operating Temperature Range 0˚C ≤T A ≤+125˚C Remote Diode Temperature (T D )Range-5˚C ≤T D ≤+140˚C Supply Voltage Range (V+)+3.0V to +3.6VAnalog Input Voltage Rage:+1.2V and +2.5V −0.05V to (V++0.05V)+3.3V_SBY (V+)+3.0V to +3.6V +5V −0.05V to +6.67V +12V−0.05V to +16V DC Electrical CharacteristicsThe following specifications apply for V+=+3.0V DC to +3.6V DC ,and all analog source impedance R S =50Ωunless other-wise specified in the conditions.Boldface limits apply for LM41CIMT T A =T J =T MIN =0˚C to T MAX =85˚C;all other limits T A =+25˚C.T A is the ambient temperature of the LM41;T J is the junction temperature of the LM41;T D is the junction tem-perature of the remote thermal diode.POWER SUPPLY CHARACTERISTICS Symbol ParameterConditionsTypical (Note 7)Limits (Note 8)Units (Limit)V+Power Supply Voltage3.3 3.03.6V (min)V (max)I+ShutdownShutdown Power Supply CurrentSensorPath Bus Inactive (Note 9)260420µA (max)I+AverageAverage Power Supply Current SensorPath Bus Inactive;all sensors enabled;t CONV =182ms;(Note 9)900µA (max)I+PeakPeak Power Supply Current SensorPath Bus Inactive (Note 9)3.3mA (max)Power-On Reset Threshold Voltage1.6V (min)2.8V (max)TEMPERATURE-TO-DIGITAL CONVERTER CHARACTERISTICSParameterConditionsTypical (Note 7)Limits (Note 8)Units (Limits)Temperature Accuracy Using the Remote Thermal Diode,see (Note 12)for Thermal Diode Processor Type.T J =0˚C to +85˚C T D =+25˚C ±1±2.5˚C (max)T J =0˚C to +85˚C T D =0˚C to +100˚C ±3˚C (max)T J =0˚C to +85˚CT D =+100˚C to +125˚C±4˚C (max)Temperature Accuracy Using the Local Diode T J =0˚C to +85˚C (Note 10)±1±3˚C (max)Remote Diode and Local Temperature Resolution 10Bits 0.5˚C D−Source Voltage0.7VL M 41 4TEMPERATURE-TO-DIGITAL CONVERTER CHARACTERISTICSParameter Conditions Typical(Note7)Limits(Note8)Units(Limits)Diode Source Current (V D+−V D−)=+0.65V;High Current188280µA(max) Low Current11.75µADiode Source Current High Current to Low CurrentRatio16 ANALOG TO DIGITAL CONVERTER CHARACTERISTICSSymbol Parameter Conditions Typical(Note7)Limits(Note8)Units(Limit)TUE Total Unadjusted Error(Note11)±2%FS(max) Resolution9Bits DNL Differential Non-linearity1LSB Power Supply Sensitivity±1%/VInput Resistance,all analog inputs(total resistance of divider chain)210140kΩ(min)400kΩ(max)SWD and ADD DIGITAL INPUT CHARACTERISTICSSymbol Parameter Conditions Typical(Note7)Limits(Note8)Units(Limit)V IH SWD Logical High Input Voltage 2.1V(min)V++0.5V(max) V IL SWD Logical Low Input Voltage0.8V(max)-0.5V(min) V IH ADD Logical High Input Voltage90%x V+V(min) V IL ADD Logical Low Input Voltage10%x V+V(max) V HYST Input Hysteresis300mVI L SWD and ADD Input Current GND≤V IN≤V+±0.005±10µA(max)SWD Input Current with V+Open or Grounded GND≤V IN≤3.6V,and V+Open orGND±0.005µAC IN Digital Input Capacitance10pF SWD DIGITAL OUTPUT CHARACTERISTICSSymbol Parameter Conditions Typical(Note7)Limits(Note8)Units(Limit)V OL Open-drain Output Logic“Low”Voltage I OL=4mA0.4V(max) I OL=50µA0.2V(max)I OH Open-drain Output Off Current±0.005±10µA(max)C OUT Digital Output Capacitance10pF AC Electrical CharacteristicsThe following specification apply for V+=+3.0V DC to+3.6V DC,unless otherwise specified.Boldface limits apply forT A=T J=T MIN=0˚C to T MAX=85˚C;all other limits T A=T J=25˚C.The SensorPath Characteristics conform to the SensorPath specification revision0.98.Please refer to that speciation for further details.Symbol Parameter Conditions Typical(Note7)Limits(Note8)Units(Limits)HARDWARE MONITOR CHARACTERISTICSt CONV Total Monitoring Cycle Time(Note13)All Voltage andTemperature readings(Default)182163.8ms(min)200.2ms(max)LM415AC Electrical Characteristics(Continued)The following specification apply for V+=+3.0V DC to +3.6V DC ,unless otherwise specified.Boldface limits apply forT A =T J =T MIN =0˚C to T MAX =85˚C ;all other limits T A =T J =25˚C.The SensorPath Characteristics conform to the SensorPath specification revision 0.98.Please refer to that speciation for further details.SymbolParameterConditionsTypical (Note 7)Limits (Note 8)Units (Limits)SensorPath Bus CHARACTERISTICSt f SWD fall time (Note 16)R pull-up =1.25k Ω±30%,C L =400pF300ns (max)t r SWD rise time (Note 16)R pull-up =1.25k Ω±30%,C L =400pF1000ns (max)t INACTMinimum inactive time (bus at high level)guaranteed by the slave before an attention request11µs (min)t Mtr0Master drive for Data Bit 0write and for Data Bit 0-1read11.8µs (min)17.0µs (max)t Mtr1Master drive for Data Bit 1write 35.4µs (min)48.9µs (max)t SFEdet Time allowed for LM41activity detection 9.6µs (max)t SLout1LM41drive for Data Bit 1read by master 28.3µs (min)38.3µs (max)t MtrS Master drive for Start Bit 80µs (min)109µs (max)t SLoutA LM41drive for Attention Request 165µs (min)228µs (max)t RST Master or LM41drive for Reset354µs (min)t RST_MAXMaximum drive of SWD by an LM41,after the power supply is raised above 3V500ms (max)Note 1:Absolute Maximum Ratings indicate limits beyond which damage to the device may occur.Operating Ratings indicate conditions for which the device is functional,but do not guarantee performance limits.For guaranteed specifications and test conditions,see the Electrical Characteristics.The guaranteed specifications apply only for the test conditions listed.Some performance characteristics may degrade when the device is not operated under the listed test conditions.Note 2:All voltages are measured with respect to GND,unless otherwise noted.Note 3:When the input voltage (V IN )at any pin exceeds the power supplies (V IN <GND or V IN >V+),the current at that pin should be limited to 5mA.Parasitic components and/or ESD protection circuitry are shown below for the LM41’s pins.The nominal breakdown voltage of the zener is 6.5V.SNP stands for snap-back device.L M 41 6PIN #Pin Name Pin Circuit All Input Structure Circuits1NC A Circuit ACircuit CCircuit BCircuit D2GND B 3V+/3.3V SB B 4SWD A 5ADD A 6+1.2V C 7+2.5V C 8D-D 9D+E 10NC E 11+5V C Circuit E12+12V C 13NC none 14NCANote 4:Thermal resistance junction-to-ambient in still air when attached to a printed circuit board with 1oz.foil is 148˚C/W.Note 5:Human body model,100pF discharged through a 1.5k Ωresistor.Machine model,200pF discharged directly into each pin.Note 6:Reflow temperature profiles are different for lead-free and non lead-free packages.Note 7:“Typicals”are at T A =25˚C and represent most likely parametric norm.They are to be used as general reference values not for critical design calculations.Note 8:Limits are guaranteed to National’s AOQL (Average Outgoing Quality Level).Note 9:The supply current will not increase substantially with a SensorPath transaction.Note 10:Local temperature accuracy does not include the effects of self-heating.The rise in temperature due to self-heating is the product of the internal power dissipation of the LM41and the thermal resistance.See (Note 4)for the thermal resistance to be used in the self-heating calculation.Note 11:TUE ,total unadjusted error,includes ADC gain,offset,linearity and reference errors.TUE is defined as the "actual Vin"to achieve a given code transition minus the "theoretical Vin"for the same code.Therefore,a positive error indicates that the input voltage is greater than the theoretical input voltage for a given code.If the theoretical input voltage was applied to an LM41that has positive error,the LM41’s reading would be less than the theoretical.Note 12:The accuracy of the LM41CIMT is guaranteed when using the thermal diode of an Intel 90nm Pentium 4processor or any thermal diode with a non-ideality factor of 1.011and series resistance of 3.33Ω.When using a MMBT3904type transistor as a thermal diode the error band will be typically shifted by -4.5˚C.Note 13:This specification is provided only to indicate how often temperature and voltage data are updated.Note 14:The output fall time is measured from (V IH min )to (V IL max ).Note 15:The output rise time is measured from (V IL max )to (V IH min ).Note 16:The rise and fall times are not tested but guaranteed by design.LM417Timing Diagrams20070304FIGURE 1.Timing for Data Bits 0,1and Start Bit.See Section 1.2"SensorPath BIT SIGNALING"for further details.L M 41 8LM41 Timing Diagrams(Continued)20070305FIGURE2.Timing for Attention Request and Reset.See Section1.2"SensorPath BIT SIGNALING"for further details.9Typical Performance CharacteristicsRemote Diode Temperature Reading Sensitivity to DiodeFilter CapacitanceThermal Diode Capacitor or PCB Leakage Current Effecton Remote Diode Temperature Reading20070321200703221.0Functional DescriptionThe LM41hardware monitor measures up to 2temperature zones and 5power supply voltages.The LM41uses a ∆V be temperature sensing method.A differential voltage,repre-senting temperature,is digitized using a Sigma-Delta analog to digital converter.Internal scaling resistors allow direct measurement of the +1.6V,+2.5V,+5V,+3.3V and +12V power supply inputs.The digitized data can be retrieved over a simple single-wire interface called SensorPath.Sensor-Path has been defined by National Semiconductor and is optimized for hardware monitoring.National offers a royalty-free license in connection with its intellectual property rights in the SensorPath bus.The LM41has one address pin to allow up to two LM41s to be connected to one SensorPath bus.The physical interface of SensorPath’s SWD signal is identical to the familiar indus-try standard SMBus SMBDAT signal.The digital information is encoded in the pulse width of the signal being transmitted.Every bit can be synchronized by the master simplifying the implementation of the master when using a micro-controller.For micro-controller’s with greater functionality an asynchro-nous attention signal can be transmitted by the LM41to interrupt the micro-controller and notify it that temperature/voltage data has been updated in the readout registers.To optimize the LM41’s power consumption to the system requirements,the LM41has a shutdown mode and supports multiple conversion rates.1.1SensorPath BUS SWDSWD is the Single Wire Data line used for communication.SensorPath uses 3.3V single-ended signaling,with a pull-up resistor and open-drain low-side drive (see Figure 3).For timing purposes SensorPath is designed for capacitive loads (C L )of up to 400pF.Note that in many cases a 3.3V standby rail of the PC will be used as a power supply for both the sensor and the master.Logic high and low voltage levels for SWD are TTL compatible.The master may provide an inter-nal pull-up resistor.In this case the external resistor is not needed.The minimum value of the pull-up resistor must take into account the maximum allowable output load current of 4mA.1.2SensorPath BIT SIGNALINGSignals are transmitted over SensorPath using pulse-width encoding.There are five types of "bit signals":•Data Bit 0•Data Bit 1•Start Bit•Attention Request •ResetAll the "bit signals"involve driving the bus to a low level.The duration of the low level differentiates between the different "bit-signals".Each "bit signal"has a fixed pulse width.Sen-sorPath supports a Bus Reset Operation and Clock Training sequence that allows the slave device to synchronize its internal clock rate to the master.Since the LM41meets the ±15%timing requirements of SensorPath,the LM41does not require the Clock Training sequence and does not sup-port this feature.This section defines the "bit signal"behav-ior in all the modes.Please refer to the timing diagrams in the Electrical Characteristics section (Figure 1and Figure 2)while going through this section.Note that the timing dia-grams for the different types of "bit signals"are shown together to better highlight the timing relationships between them.However,the different types of "bit signals"appear on SWD at different points in time.These timing diagrams show the signals as driven by the master and the LM41slave as well as the signal as seen when probing SWD.Signal labels that begin with the label Mout_depict a drive by the master.20070307FIGURE 3.SensorPath SWD simplified schematic L M 41101.0Functional Description(Continued) Signal labels that begin with the label Slv_depict the drive by the LM41.All other signals show what would be seen when probing SWD for a particular function(e.g."Master Wr0"is the Master transmitting a Data Bit with the value of0).1.2.1Bus InactiveThe bus is inactive when the SWD signal is high for a period of at least t INACT.The bus is inactive between each"bit signal".1.2.2Data Bit0and1All Data Bit signal transfers are started by the master.A Data Bit0is indicated by a"short"pulse;a Data Bit1is indicated by a longer pulse.The direction of the bit is relative to the master,as follows:•Data Write-a Data Bit transferred from the master to the LM41.•Data Read-a Data Bit transferred from the LM41to the master.A master must monitor the bus as inactive before starting a Data Bit(Read or Write).A master initiates a data write by driving the bus active(low level)for the period that matches the data value(t Mtr0or t Mtr1 for a write of"0"or"1",respectively).The LM41will detect that the SWD becomes active within a period of t SFEdet,and will start measuring the duration that the SWD is active in order to detect the data value.A master initiates a data read by driving the bus for a period of t Mtr0.The LM41will detect that the SWD becomes active within a period of t SFEdet.For a data read of"0",the LM41 will not drive the SWD.For a data read of"1"the LM41will start within t SFEdet to drive the SWD low for a period of t SLout1.Both master and LM41must monitor the time at which the bus becomes inactive to identify a data read of"0" or"1".During each Data Bit,both the master and all the LM41s must monitor the bus(the master for Attention Request and Reset;the LM41s for Start Bit,Attention Request and Reset) by measuring the time SWD is active(low).If a Start Bit, Attention Requests or Reset"bit signal"is detected,the current"bit signal"is not treated as a Data Bit.Note that the bit rate of the protocol varies depending on the data transferred.Thus,the LM41has a value of"0"in reserved or unused register bits for bus bandwidth efficiency.1.2.3Start BitA master must monitor the bus as inactive before beginning a Start Bit.The master uses a Start Bit to indicate the beginning of a transfer.LM41s will monitor for Start Bits all the time,to allow synchronization of transactions with the master.If a Start Bit occurs in the middle of a transaction,the LM41being ad-dressed will abort the current transaction.In this case the transaction is not"completed"by the LM41(see Section1.3 "SensorPath Bus Transactions").During each Start Bit,both the master and all the LM41s must monitor the bus for Attention Request and Reset,bymeasuring the time SWD is active(low).If an AttentionRequest or Reset condition is detected,the current"bitsignal"is not treated as a Start Bit.The master may attemptto send the Start Bit at a later time.1.2.4Attention RequestThe LM41may initiate an Attention Request when the Sen-sorPath bus is inactive.Note that a Data Bit,or Start Bit,from the master may startsimultaneously with an Attention Request from the LM41.Inaddition,two LM41s may start an Attention Request simul-taneously.Due to its length,the Attention Request has pri-ority over any other"bit signal",except Reset.Conflict withData Bits and Start Bits are detected by all the devices,toallow the bits to be ignored and re-issued by their originator.The LM41will either check to see that the bus is inactivebefore starting an Attention Request,or start the AttentionRequest within the t SFEdet time interval after SWD becomesactive.The LM41will drive the signal low for t SLoutA time.After this,both the master and the LM41must monitor thebus for a Reset Condition.If a Reset condition is detected,the current"bit signal"is not treated as an Attention Request.After Reset,an Attention Request can not be sent before themaster has sent14Data Bits on the bus.See Section1.3.5for further details on Attention Request generation.1.2.5Bus ResetThe LM41issues a Reset at power up.The master must alsogenerate a Bus Reset at power-up for at least the minimumreset time,it must not rely on the LM41.SensorPath puts nolimitation on the maximum reset time of the master.Follow-ing a Bus Reset,the LM41may generate an Attention Re-quest only after the master has sent14Data Bits on the bus.See Section1.3.5for further details on Attention Requestgeneration.1.3SensorPath BUS TRANSACTIONSSensorPath is designed to work with a single master and upto seven slave devices.Each slave has a unique address.The LM41supports up to2device addresses that are se-lected by the state of the address pin ADD.The Register Setof the LM41is defined in Section2.0.1.3.1Bus Reset OperationA Bus Reset Operation is global on the bus and affects onlythe communication interface of all the devices connected toit.The Bus Reset operation does not affect either the con-tents of the device registers,or device operation,to theextent defined in LM41Register Set,see Section2.0.The Bus Reset operation is performed by generating a Resetsignal on the bus.The master must apply Reset after power-up,and before it starts operation.The Reset signal end willbe monitored by all the LM41s on the bus.After the Reset Signal the SensorPath specification requiresthat the master send a sequence of8Data Bits with a valueof"0",without a preceding Start Bit.This is required toenable slaves that"train"their clocks to the bit timing.TheLM41does not require nor does it support clock training.LM41111.0Functional Description(Continued)1.3.2Read TransactionDuring a read transaction,the master reads data from a register at a specified address within a slave.A read trans-action begins with a Start Bit and ends with an ACK bit,as shown in Figure 5.•Device Number This is the address of the LM41device accessed.Address "000"is a broadcast address and can be responded to by all the slave devices.The LM41ignores the broadcast address during a read transaction.•Internal Address The address of a register within the LM41that is read.•Read/Write (R/W)A "1"indicates a read transaction.•Data Bits During a read transaction the data bits are driven by the LM41.Data is transferred serially with the most significant bit first.This allows throughput optimiza-tion based on the information that needs to be read.The LM41supports 8-bit or 16-bit data fields,as de-scribed in Section 2.0"Register Set".•Even Parity (EP)This bit is based on all preceding bits (device number,internal address,Read/Write and data bits)and the parity bit itself.The parity -number of 1’s -of all the preceding bits and the parity bit must be even -i.e.,the result must be 0.During a read transaction,the EP bit is sent by the LM41to the master to allow the master to check the received data before using it.•Acknowledge (ACK)During a read transaction the ACK bit is sent by the master indicating that the EP bit was received and was found to be correct,when compared to the data preceding it,and that no conflict was detected on the bus (excluding Attention Request -see Section 1.3.5"Attention Request Transaction").A read transfer is considered "complete"only when the ACK bit is received.A transaction that was not positively acknowledged is not considered "complete"by the LM41and following are performed:—The BER bit in the LM41Device Status register is set —The LM41generates an Attention Request before,or together with the Start Bit of the next transactionA transaction that was not positively acknowledged is also not considered "complete"by the master (i.e.inter-nal operations related to the transaction are not per-formed).The transaction may be repeated by the master,after detecting the source of the Attention Request (the LM41that has a set BER bit in the Device Status regis-ter).Note that the SensorPath protocol neither forces,nor automates re-execution of the transaction by the master.The values of the ACK bit are:—1:Data was received correctly—0:An error was detected (no-acknowledge).1.3.3Write TransactionIn a write transaction,the master writes data to a register at a specified address in the LM41.A write transaction begins with a Start Bit and ends with an ACK Data Bit,as show in Figure 6.•Device Number This is the address of the slave device accessed.Address "000"is a broadcast address and is responded to by all the slave devices.The LM41re-sponds to broadcast messages to the Device Control Register.•Internal Address This is the register address in the LM41that will be written.•Read/Write (R/W)A "0"data bit directs a write transac-tion.20070308FIGURE 4.Bus Reset Transaction20070309FIGURE 5.Read Transaction,master reads data from LM41L M 41 121.0Functional Description(Continued)•Data Bits This is the data written to the LM41register, are driven by the master.Data is transferred serially with the most significant bit first.The number of data bits may vary from one address to another,based on the size of the register in the LM41.This allows throughput optimi-zation based on the information that needs to be written.The LM41supports8-bit or16-bit data fields,as de-scribed in Section2.0"Register Set".•Even Parity(EP)This data bit is based on all preceding bits(Device Number,Internal Address,Read/Write and Data bits)and the Even Parity bit itself.The parity(num-ber of1’s)of all the preceding bits and the parity bit must be even-i.e.the result must be0.During a write trans-action,the EP bit is sent by the master to the LM41to allow the LM41to check the received data before using it.•Acknowledge(ACK)During the write transaction the ACK bit is sent by the LM41indicating to the master that the EP was received and was found correct,and that no conflict was detected on the bus(excluding Attention Request-see Section1.3.5"Attention Request Transac-tion").A write transfer is considered"completed"only when the ACK bit is generated.A transaction that was not positively acknowledged is not considered complete by the LM41(i.e.internal operation related to the transaction are not performed)and the following are performed:—The BER bit in the LM41Device Status register is set;—The LM41generates an Attention Request before,or together with the Start Bit of the next transactionA transaction that was not positively acknowledged is also not considered"complete"by the master(i.e.inter-nal operations related to the transaction are not per-formed).The transaction may be repeated by the master, after detecting the source of the Attention Request(the LM41that has a set BER bit in the Device Status regis-ter).Note that the SensorPath protocol neither forces,nor automates re-execution of the transaction by the master. The values of the ACK bit are:—1:Data was received correctly;—0:An error was detected(no-acknowledge).1.3.4Read and Write Transaction ExceptionsThis section describes master and LM41handling of special bus conditions,encountered during either Read or Write transactions.If an LM41receives a Start Bit in the middle of a transaction, it aborts the current transaction(the LM41does not"com-plete"the current transaction)and begins a new transaction. Although not recommend for SensorPath normal operation, this situation is legitimate,therefore it is not flagged as an error by the LM41and Attention Request is not generated in response to it.The master generating the Start Bit,is re-sponsible for handling the not"complete"transaction at a "higher level".If LM41receives more than the expected number of data bits (defined by the size of the accessed register),it ignores the unnecessary bits.In this case,if both master and LM41 identify correct EP and ACK bits they"complete"the trans-action.However,in most cases,the additional data bits differ from the correct EP and ACK bits.In this case,both the master and the LM41do not"complete"the transaction.In addition,the LM41performs the following:•the BER bit in the LM41Device Status register is set •the LM41generates an Attention RequestIf the LM41receives less than the expected number of data bits(defined by the size of the accessed register),it waits indefinitely for the missing bits to be sent by the master.If then the master sends the missing bits,together with the correct EP/ACK bits,both master and LM41"complete"the transaction.However,if the master starts a new transaction generating a Start Bit,the LM41aborts the current transac-tion(the LM41does not"complete"the current transaction) and begins the new transaction.The master is not notified by the LM41of the incomplete transaction.1.3.5Attention Request TransactionAttention Request is generated by the LM41when it needs the attention of the master.The master and all LM41s must monitor the Attention Request to allow bit re-sending in case of simultaneous start with a Data Bit or Start Bit transfer. Refer to the"Attention Request"section,Section1.2.4in the "Bit Signaling"portion of the data sheet.The LM41will generate an Attention Request using the following rules:1.A Function event that sets the Status Flag has occurredand Attention Request is enabled and2.The"physical"condition for an Attention Request is met(i.e.,the bus is inactive),and3.At the first time2is met after1occurred,there has notbeen an Attention request on the bus since a read of the Device Status register,or since a Bus Reset.OR1.A bus error event occurred,and2.the"physical"condition for an Attention Request is met(i.e.,the bus is inactive),and3.At the first time2.is met after1occurred,there has notbeen a Bus Reset.20070310FIGURE6.Write Transaction,master write data to LM41LM4113。
艾默生 Rosemount 114P 保护管 数据表
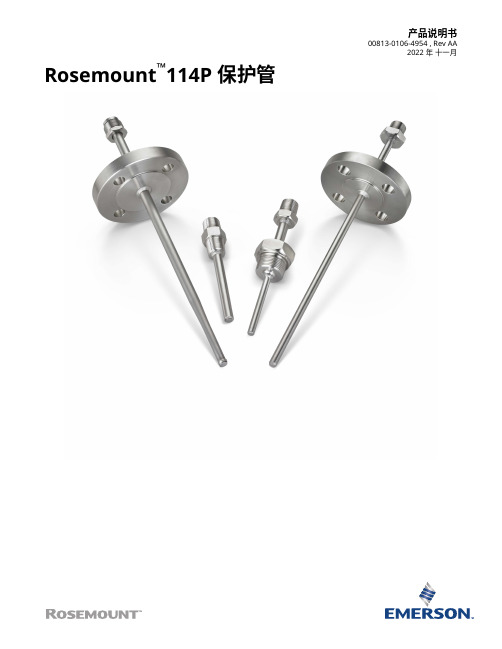
产品说明书00813-0106-4954 , Rev AA2022 年 十一月Rosemount™114P 保护管Rosemount 114P 保护管产品概述保护管由金属管制成,顶端用焊接端盖密封。
过程密封可使用法兰或沿管道焊接的机加工螺纹型接头。
保护管一般是统一管杆形状,不过某些行业有特殊的非统一管杆要求。
应用广泛的各种保护管选项和认证■特殊试验要求的选项,例如外部静压试验 (Q5) 和染色渗透试验 (Q73)■材料认证选项(Q8)保证材料可追溯性。
体验全球一致性以及由众多全球艾默生制造中心提供的本地支持■凭借全球制造,从各家工厂提供全球一致的产品以及满足任何规模的工程需求的能力。
■经验丰富的仪表顾问可帮助您为任何温度应用选择正确的产品,并提供最佳安装做法的建议。
■广泛的全球艾默生服务与支持人员网络能够在任何时间、任何地点提供现场服务。
研究艾默生 Complete Point Solution™的优势■通过“Assemble Sensor to Specific Transmitter(把传感器组装到特定变送器)”和“Assemble Sensor to Specific Protection Tube(把传感器组装到特定保护管)”选项,艾默生提供一体化解决方案,为您带来可直接安装的变送器、传感器和保护管组件。
■艾默生具有全系列单点和多点输入温度测量解决方案,使您能够凭借可靠的罗斯蒙特产品实现有效的测量和过程控制。
内容Rosemount 114P 保护管 (2)选择指南 (3)Rosemount 114P 螺纹型保护管 (4)Rosemount 114P 法兰型保护管 (15)详细订购信息 (24)Rosemount 114P 保护管2022 年 十一月选择指南确保传感器适合保护管若需要订购替换传感器和新的连接头,请咨询艾默生专家,确定 214C 的正确长度。
若订购替换传感器,不订购新的连接头(仅传感器),请按以下说明操作。
卓美仪表GP41无线变送器说明书

目录警告和注意 (2)第一章简介 (3)1-1、ZM-GP41系列智能远传变送器: (3)1-2、手册的使用: (3)1-3、注意事项及安全信息: (3)1-4、收货: (3)1-5、技术支持: (4)1-6、主要用途及适用范围: (4)1-7、防爆型仪表的特殊说明: (4)1-8、特点及工作原理: (5)1-8-1、特点: (5)1-8-2、结构及原理: (6)1-8-3、传感器: (7)1-8-4、变送器: (7)第二章:安装 (9)2-1、传感器的安装: (9)2-2、引压管的安装: (9)2-3、危险场所安装注意事项: (10)第三章:操作指导 (11)第四章:维护及报警 (15)4-1、报警: (15)4-2、维护: (16)附录A 技术参数 (17)警告和注意警告!●仪表防爆等级因不同型号而异。
在安装前请仔细核对仪表铭牌以确定仪表的防爆等级。
●所有的仪表连接件,隔离阀及安装附件都需与管道有相同或更高的压力等级。
●为了防止造成伤害,请勿在有压力的情况下松开螺丝。
●为防止触电,接电源时请遵循NEC或者地方规范。
否则会造成人身伤害甚至导致死亡。
所有交流电源连接件都必须有CE认证。
所有的接线工作都需在电源断开状态下进行●在进行任何维护工作前,请检定管道内无压力。
无论拆卸仪表任何部分,都必须关闭主电源。
注意!●标定必须由专业人员完成,本公司强烈建议用户将仪表送回制造厂家标定。
●为了获得高精度及良好的重复性,仪表需要有上下游的直管段。
第一章 简 介1-1、ZM-GP41系列智能远传变送器:ZM-GP41系列智能远传压力变送器是本公司在金属电容式压力变送器基础上结合现代数字芯片技术开发的新一代产品。
传感器信号转换原理上采用隔离数字电容电路替代传统模拟信号放大电路及A/D 转换电路,并利用数字化补偿技术对温度、静压进行补偿,提高了测量精度,降低了温度漂移。
具有长期稳定性,高可靠性,自诊断能力强等特点。
MCM-41的负载应用

MCM-41的负载应用摘要MCM-41一般用来做催化剂的负载骨架,使原本无吸附性的催化剂微粒附着到介孔分子筛的的孔道之中,使反应物通过吸附富集到MCM-41的孔道之中,增加反应物浓度,从而提高反应活性。
也有通过在MCM-41制备过程中掺杂金属离子,从而改变分子筛的耐温性能。
还有将MCM-41与特定复合物结合,制备特殊感光材料。
关键词MCM-41 负载吸附掺杂正文MCM-41的有序介孔材料,它是一种新型的纳米结构材料。
与其它沸石材料相比,MCM-41的骨架铝物种热稳定性相对较差,在焙烧过程中,骨架铝物种由骨架脱落成为非骨架铝物种。
它作为一种特殊的介孔分子筛,在化工领域、环境治理和保护领域、生物医药领域等众多领域,均有重要应用。
而MCM-41的负载产品则具有更多新的作用。
M41S[ 4 ] 具有有序孔道排列和狭窄的孔分布、大比表面积和高热稳定性,是一种良好的催化剂载体,但硅基介孔材料自身无催化活性,因此需要采取掺杂、改性等多种方法引入催化活性中心。
一、环境保护领域——TiO2-MCM-41降解有机污染物高级氧化对彻底广泛的降解有机污染物和细菌类物质是一个有效的措施。
而TiO2作为催化剂来高级氧化气体污染物和水污染物是近几年来所有已发表的化工文献中的最有效的措施。
但是TiO2本身对于催化反应来讲又有些局限性。
它不具备孔道,所以呈现出较低的吸附性能,尤其是对于非极性的化合物来讲尤其明显。
无孔道,降低了它的吸附能力,然而,吸附步骤是对于反应来说极其重要的一个前期步骤。
MCM-41的孔径在1.87-2.25nm之间,将TiO2负载到MCM-41上,较之裸露的TiO2极大提高了该催化剂的反应活性,因为负载之后的TiO2的比表面积得到了提高,从而使有机污染物在催化剂表面聚集,同时催化剂表面的电子空穴得以减少。
与此相关的实验已取得一些成果,虽然实际效果远非理想,但科研人员仍在坚持不懈地钻研。
二、材料开发领域——对氧气敏感的光致激发光材料此种材料对一种新型的铜复合材料【Cu(POP)(PTI)】BF4,此材料由铜化合物与无机多孔分子筛组成——在一种特定溶剂中溶解铜化合物,然后加入一定量MCM-41分子筛制成溶胶,在室温下搅拌、过滤,然后用溶剂洗涤三次,在空气中风干。
Mark VIe控制系统中文版第1册

GE EnergyMark VIe®控制系统指南 第一册 系统手册目录第1章综述1-1 介绍…………………………………………………………………………………….1-1 应用…………………………………………………………………………………….1-2 控制器………………………………………………………………………………….1-3 I/O网络(IONet)…………………………………………………………………….1-3 I/O模块…………………………………………………………………………………1-4 相关文献………………………………………………………………………………..1-5 如何获取帮助…………………………………………………………………………..1-5 缩写词和缩略语………………………………………………………………………..1-6第2章系统体系结构2-1 介绍……………………………………………………………………………………..2-1 系统部件………………………………………………………………………………..2-1 控制器……………………………………………………………………………..2-2控制器外罩………………………………………………………………………..2-4电源………………………………………………………………………………..2-4I/O包………………………………………………………………………………2-5终端块……………………………………………………………………………..2-6I/O类型……………………………………………………………………………2-7功率源……………………………………………………………………………..2-9 通信……………………………………………………………………………………..2-11 设备数据公路(UDH)……………………………………………………….....2-11工厂数据公路(PDH)…………………………………………………………..2-11IONet………………………………………………………………………………2-12人机接口(HMI)………………………………………………………………..2-12服务器……………………………………………………………………………..2-13计算机操作者接口(COI)………………………………………………………2-13与分布式控制系统(DCS)的连接……………………………………………….2-14EX2100励磁器……………………………………………………………………2-15发电机保护………………………………………………………………………..2-15LS2100静态启动器……………………………………………………………….2-15 控制和保护……………………………………………………………………………..2-16 平均故障间隔时间(MTBF)……………………………………………………2-16平均强制断电间隔时间(MTBFO)…………………………………………….2-17故障检测…………………………………………………………………………..2-18联机维修…………………………………………………………………………..2-19指定的控制器……………………………………………………………………..2-20UDH通信器……………………………………………………………………….2-21输出处理…………………………………………………………………………..2-22输入处理…………………………………………………………………………..2-24状态交换…………………………………………………………………………..2-29表决………………………………………………………………………………..2-29强制赋值…………………………………………………………………………..2-30对等I/O……………………………………………………………………………2-30命令操作…………………………………………………………………………..2-30响应速度…………………………………………………………………………..2-31涡轮保护…………………………………………………………………………..2-32 冗余选项………………………………………………………………………………..2-33 单工控制器………………………………………………………………………..2-34第3章网络3-1 介绍……………………………………………………………………………………...3-1 网络综述…………………………………………………………………………………3-1 网络层次……………………………………………………………………………3-2 数据公路…………………………………………………………………………………3-5 工厂数据公路(PDH)………………………………………………………….…3-5设备数据公路(UDH)……………………………………………………………3-7数据公路以太网交换机……………………………………………………………3-8为UDH和PDH选择IP地址…………………………………………………….3-9IONet………………………………………………………………………………3-10寻址……………………………………………………………………………….3-10以太网全局数据(EGD)……………………………………………………….3-12 光纤电缆……………………………………………………………………………….3-14 部件……………………………………………………………………………….3-14 单模光纤连线………………………………………………………………………….3-18 IONet部件………………………………………………………………………..3-19UDH/PDH部件…………………………………………………………………..3-20拓扑结构实例…………………………………………………………………….3-21以太网交换机故障检修………………………………………………………….3-21部件来源………………………………………………………………………….3-22 第4章法规、标准和环境4-1 介绍………………………………………………………………………………………4-1 安全标准…………………………………………………………………………………4-1 电气………………………………………………………………………………………4-1 印刷电路板部件……………………………………………………………………4-1电磁兼容性(EMC)………………………………………………………………4-2低压电指令…………………………………………………………………………4-2ATEX指令94/9/EC………………………………………………………………..4-2电源电压……………………………………………………………………………4-2 环境………………………………………………………………………………………4-4 温度…………………………………………………………………………………4-4运输和存储温度……………………………………………………………………4-6湿度…………………………………………………………………………………4-6海拔高度……………………………………………………………………………4-6污染物………………………………………………………………………………4-7振动…………………………………………………………………………………4-7 第5章安装和配置5-1 介绍………………………………………………………………………………………5-1 安装支持…………………………………………………………………………………5-1 前期规划……………………………………………………………………………5-1GE安装文献……………………………………………………………………….5-2技术咨询选项………………………………………………………………………5-2 设备接收和处理…………………………………………………………………………5-4 存储…………………………………………………………………………………5-5操作环境……………………………………………………………………………5-6 电源要求…………………………………………………………………………………5-7 安装支持图纸……………………………………………………………………………5-8 接地……………………………………………………………………………………..5-13设备接地…………………………………………………………………………..5-13电缆分级和排布………………………………………………………………………5-21 信号和电源等级的定义…………………………………………………………5-21电缆通道间距准则………………………………………………………………5-23布线准则…………………………………………………………………………5-26 电缆技术规格…………………………………………………………………………5-27 电缆的尺寸………………………………………………………………………5-27常规技术规格……………………………………………………………………5-28低压电屏蔽电缆…………………………………………………………………5-29 连接系统………………………………………………………………………………5-31 I/O布线………………………………………………………………………….5-31终端块特征………………………………………………………………………5-32电源系统…………………………………………………………………………5-33安装以太网………………………………………………………………………5-33 启动检查………………………………………………………………………………5-34 布线和电路检查…………………………………………………………………5-34 第6章工具和系统接口6-1 介绍………………………………………………………………………………………6-1 ToolboxST………………………………………………………………………………..6-1 人机接口(HMI)………………………………………………………………………6-2 基本说明……………………………………………………………………………6-2产品功能……………………………………………………………………………6-2 涡轮历史分析程序………………………………………………………………………6-4 系统配置……………………………………………………………………………6-4系统性能……………………………………………………………………………6-5数据流………………………………………………………………………………6-5涡轮历史分析程序工具……………………………………………………………6-6 uOSM…………………………………………………………………………………….6-8 OPC服务器……………………………………………………………………………..6-9 Modbus…………………………………………………………………………………6-10 以太网Modbus从机……………………………………………………………..6-11串行Modbus………………………………………………………………………6-12 以太网GSM……………………………………………………………………………6-16 时间同步化…………………………………………………………………………….6-17 冗余时间源……………………………………………………………………….6-17时间源的选择…………………………………………………………………….6-18 第7章维护和诊断7-1 介绍………………………………………………………………………………………7-1 维护………………………………………………………………………………………7-1 以太网交换机……………………………………………………………………………7-2 警告综述…………………………………………………………………………………7-3 进程警报…………………………………………………………………………………7-4 进程和保持警报数据流……………………………………………………………7-4 诊断警报…………………………………………………………………………………7-5 通过ToolboxST来浏览控制器诊断………………………………………………7-5针对表决器给出相异情况的诊断…………………………………………………7-6 总额计算器………………………………………………………………………………7-7 发光二极管快速参考……………………………………………………………………7-8 I/O包状态………………………………………………………………………….7-9IONet状态…………………………………………………………………………7-9第1章综述应用 ……………………………………………………..1-2控制器 ……………………………………………………..1-3I/O网络(IONet) ……………………………………..1-3I/O模块………………………………………………………1-4相关文献……………………………………………………..1-5如何获取帮助………………………………………………..1-5缩写词和缩略语……………………………………………..1-6介绍Mark VIe控制设备适用于多种控制和保护的应用场合,其中包括蒸汽和燃气涡轮以及电厂配套设施(BOP)等。
莫萨 MGate 4101-MB-PBS 系列 1 口 Modbus RTU ASCII-到-PRO
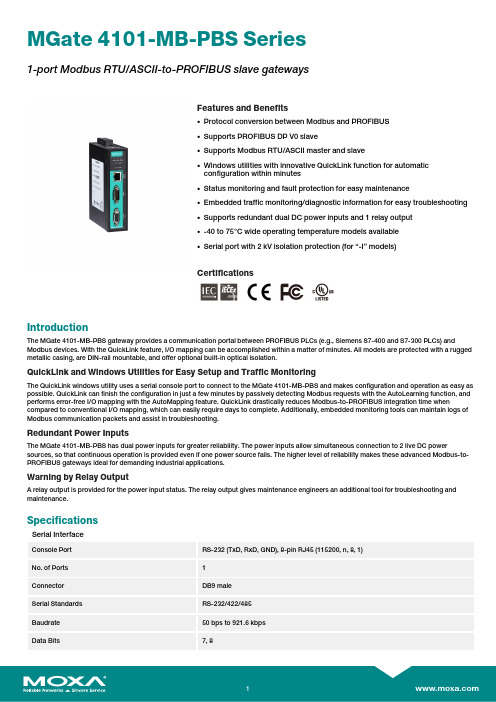
MGate4101-MB-PBS Series1-port Modbus RTU/ASCII-to-PROFIBUS slave gatewaysFeatures and Benefits•Protocol conversion between Modbus and PROFIBUS•Supports PROFIBUS DP V0slave•Supports Modbus RTU/ASCII master and slave•Windows utilities with innovative QuickLink function for automaticconfiguration within minutes•Status monitoring and fault protection for easy maintenance•Embedded traffic monitoring/diagnostic information for easy troubleshooting•Supports redundant dual DC power inputs and1relay output•-40to75°C wide operating temperature models available•Serial port with2kV isolation protection(for“-I”models)CertificationsIntroductionThe MGate4101-MB-PBS gateway provides a communication portal between PROFIBUS PLCs(e.g.,Siemens S7-400and S7-300PLCs)and Modbus devices.With the QuickLink feature,I/O mapping can be accomplished within a matter of minutes.All models are protected with a rugged metallic casing,are DIN-rail mountable,and offer optional built-in optical isolation.QuickLink and Windows Utilities for Easy Setup and Traffic MonitoringThe QuickLink windows utility uses a serial console port to connect to the MGate4101-MB-PBS and makes configuration and operation as easy as possible.QuickLink can finish the configuration in just a few minutes by passively detecting Modbus requests with the AutoLearning function,and performs error-free I/O mapping with the AutoMapping feature.QuickLink drastically reduces Modbus-to-PROFIBUS integration time when compared to conventional I/O mapping,which can easily require days to complete.Additionally,embedded monitoring tools can maintain logs of Modbus communication packets and assist in troubleshooting.Redundant Power InputsThe MGate4101-MB-PBS has dual power inputs for greater reliability.The power inputs allow simultaneous connection to2live DC power sources,so that continuous operation is provided even if one power source fails.The higher level of reliability makes these advanced Modbus-to-PROFIBUS gateways ideal for demanding industrial applications.Warning by Relay OutputA relay output is provided for the power input status.The relay output gives maintenance engineers an additional tool for troubleshooting and maintenance.SpecificationsSerial InterfaceConsole Port RS-232(TxD,RxD,GND),8-pin RJ45(115200,n,8,1)No.of Ports1Connector DB9maleSerial Standards RS-232/422/485Baudrate50bps to921.6kbpsData Bits7,8Parity None,Even,Odd,Space,MarkStop Bits1,2Flow Control DTR/DSR,RTS/CTSRS-485Data Direction Control ADDC®(automatic data direction control)Pull High/Low Resistor for RS-4851kilo-ohm,150kilo-ohmsTerminator for RS-485120ohmsIsolation2kV(I models)Serial SignalsRS-232TxD,RxD,RTS,CTS,DTR,DSR,DCD,GNDRS-422Tx+,Tx-,Rx+,Rx-,GNDRS-485-2w Data+,Data-,GNDRS-485-4w Tx+,Tx-,Rx+,Rx-,GNDSerial Software FeaturesConfiguration Options MGate ManagerIndustrial Protocols Modbus RTU/ASCII Master,Modbus RTU/ASCII Slave,PROFIBUS DP-V0Slave Modbus RTU/ASCIIMode Master,SlaveFunctions Supported1,2,3,4,5,6,15,16,23Max.No.of Commands100Input Data Size7744bytesOutput Data Size7744bytesPROFIBUS InterfaceIndustrial Protocols PROFIBUS DPNo.of Ports1Connector DB9femaleBaudrate9600bps to12MbpsIsolation2kV(built-in)Signals PROFIBUS D+,PROFIBUS D-,RTS,Signal Common,5VPROFIBUSRotary Switch PROFIBUS addresses0-99(addresses100-125supported through softwareconfiguration)Mode DP-V0SlaveMax.No.of Master Connections1Max.No.of PROFIBUS I/O Modules24per pageMax.No.of PROFIBUS Pages32Input Data Size7744bytesOutput Data Size7744bytesPower ParametersInput Voltage12to48VDCInput Current275mA@12VDCPower Connector Screw-fastened Euroblock terminalRelaysContact Current Rating Resistive load:1A@24VDCPhysical CharacteristicsHousing MetalDimensions36x105x140mm(1.42x4.14x5.51in)Weight500g(1.10lb)IP Rating IP30Note:It is recommended to attach the M3x3mm Nylok screws at the rear side Environmental LimitsOperating Temperature MGate4101I-MB-PBS:0to60°C(32to140°F)MGate4101I-MB-PBS-T:-40to75°C(-40to167°F)MGate4101-MB-PBS:0to60°C(32to140°F)MGate4101-MB-PBS-T:-40to75°C(-40to167°F)Storage Temperature(package included)-40to85°C(-40to185°F)Ambient Relative Humidity5to95%(non-condensing)Standards and CertificationsSafety EN60950-1,UL60950-1,EN62368-1,UL62368-1EMC EN55032/35EMI CISPR32,FCC Part15B Class AEMS IEC61000-4-2ESD:Contact:6kV;Air:8kVIEC61000-4-3RS:80MHz to1GHz:3V/mIEC61000-4-4EFT:Power:2kV;Signal:1kVIEC61000-4-5Surge:Power:2kV;Signal:2kVIEC61000-4-6CS:150kHz to80MHz:10V/m;Signal:10V/mIEC61000-4-8PFMFHazardous Locations ATEX,Class I Division2,IECExFreefall IEC60068-2-32Shock IEC60068-2-27Vibration IEC60068-2-6,IEC60068-2-64MTBFTime MGate4101-MB-PBS Series:1,537,948hrsMGate4101I-MB-PBS Series:1,315,666hrsStandards Telcordia SR332WarrantyWarranty Period5yearsDetails See /warrantyPackage ContentsDevice1x MGate4101-MB-PBS Series gatewayCable1x RJ45-to-DB9console cableInstallation Kit1x DIN-rail kitDocumentation1x quick installation guide1x warranty cardDimensionsOrdering InformationModel Name Serial Isolation Operating Temp. MGate4101-MB-PBS–0to60°C MGate4101I-MB-PBS2kV0to60°C MGate4101-MB-PBS-T–-40to75°C MGate4101I-MB-PBS-T2kV-40to75°C Accessories(sold separately)CablesCBL-F9M9-150DB9female to DB9male serial cable,1.5mCBL-F9M9-20DB9female to DB9male serial cable,20cmCBL-RJ45F9-150RJ45to DB9female serial cable,1.5mCBL-RJ45SF9-150RJ45to DB9female serial shielded cable,1.5mConnectorsMini DB9F-to-TB DB9female to terminal block connectorDIN-Rail Mounting KitsDK-25-01DIN-rail mounting kit,2screwsWall-Mounting KitsWK-36-02Wall-mounting kit,2plates,6screws,36x67x2mmPower CordsCBL-PJTB-10Non-locking barrel plug to bare-wire cable©Moxa Inc.All rights reserved.Updated Apr29,2020.This document and any portion thereof may not be reproduced or used in any manner whatsoever without the express written permission of Moxa Inc.Product specifications subject to change without notice.Visit our website for the most up-to-date product information.。
Omron G3VM-41AR DR MOS FET Relay数据手册说明书

G3VM-41AR/DR Higher power, 2.5-A switching with a 40-Vload voltage, DIP package.Low 50 mΩ ON Resistance.•Continuous load current of 2.5 A.•Switches minute analog signals.•Dielectric strength of 2,500 Vrms between I/O.■Application Examples■Terminal Arrangement/Internal Connections■List of Models*The AC peak and DC value are given for the load voltage.■Absolute Maximum Ratings (Ta = 25°C)RoHS compliant Note: The actual product is marked differently from theimage shown here.•Communication equipment•Test & Measurement equipment•Security equipment•Factory Automation equipment•Power circuitOMRON logoPin 1 markModel nameMold pin mark ∗LOT No.Note: The actual product is marked differently from the image shown here.∗The indentation in the corner diagonally opposite from the pin 1 mark is froma pin on the mold.Package type Contact form TerminalsLoad voltage(peak value) *ModelMinimum package quantityNumber per stick Number per tape and reel DIP41a(SPST-NO)PCB terminals40 VG3VM-41AR100---Surface-mounting terminalsG3VM-41DRG3VM-41DR (TR)---1,500 Item Symbol Rating Unit Measurement conditionsInputLED forward current I F30mANote: 1. The dielectric strength between the input andoutput was checked by applying voltagebetween all pins as a group on the LED side andall pins as a group on the light-receiving side.Repetitive peak LED forward current I FP 1 A100µs pulses, 100 ppsLED forward current reduction rate∆I F/°C−0.3mA/°C Ta≥ 25°CLED reverse voltage V R 5 VConnection temperature T J125 °COutputLoad voltage (AC peak/DC)V OFF40VContinuous load current (AC peak/DC)I O 2.5 AON current reduction rate∆I O/°C−25mA/°C Ta ≥ 25°CPulse ON current Iop7.5A t = 100 ms, Duty = 1/10Connection temperature T J125 °CDielectric strength between I/O (See note 1.)V I-O2500Vrms AC for 1 minOperating temperature Ta −40 to +85°C With no icing or condensationStorage temperature Tstg−55 to +125°C With no icing or condensationSoldering temperature---260 °C 10s12G3VM-41AR/DRMOS FET RelaysG3VM-41AR/DR■Recommended Operating ConditionsUse the G3VM under the following conditions so that the Relay will operate properly.■Engineering Data■Safety Precautions•Refer to "Common Precautions" for all G3VM models.ItemSymbol MinimumTypical MaximumUnit Load voltage (AC peak/DC)V DD --- --- 32V Operating LED forward current I F 51025mAContinuous load current (AC peak/DC)I O --- --- 2.5AOperating temperatureTa−20 --- 65 °CLED forward current vs.Ambient temperatureContinuous load current vs.Ambient temperatureLED forward current vs.LED forward voltageContinuous load current vs.On-state voltageOn-state resistance vs.Ambient temperatureTrigger LED forward current vs. Ambient temperatureTurn ON, Turn OFF time vs.LED forward currentTurn ON, Turn OFF time vs.Ambient temperatureCurrent leakage vs.Ambient temperatureI F - TaAmbient temperature Ta (°C)L E D f o r w a r d c u r r e n t I F (m A )03010204050-40100806040200-20I O - Ta-40100806040200-200321Ambient temperature Ta (°C)C o n t i n u o u s l oa d c u r r e n t I O (A )I - V 0.01LED forward voltage V F (V)L E D f o r w a r d c u r r e n tI F (m A )I - V On-state voltage V ON (V)C o n t i n u o u s l o a d c u rr e n t I O (A )R ON - Ta60204080100Ambient temperature Ta (°C)O n -s t a t e r e s i s t a n c e R O N (mΩ)I - Ta012Ambient temperature Ta (°C)T r i g g e r L E D f o r w a r d c u r r e n t I F T (m A )t ON , t OFF - I F0.010.1110100LED forward current I F (mA)T u r n O N , T u r n O F F t i m e t O N , t O F F (m s )t ON , tOFF - Ta0.011001010.1Ambient temperature Ta (°C)T u r n O N , T u r n O F F t i m e t O N , t O F F (m s)I - Ta0.011001010.1Ambient temperature Ta (°C)C u r r e n t l e a k a g e I L E A K (n A )■Dimensions(Unit: mm) Note: The actual product is marked differently from theimage shown here.PCB Dimensions (Bottom View)Actual Mounting Pad Dimensions(Recommended Value, Top View)Note: The actual product is marked differently from the image shown here.∗ The indentation in the corner diagonally opposite from the pin 1 mark is from a pin on the mold.+0.1−0.05PCB TerminalsWeight: 0.25 gSurface-mounting TerminalsWeight: 0.25 g• Application examples provided in this document are for reference only. In actual applications, confirm equipment functions and safety before using the product.• Consult your OMRON representative before using the product under conditions which are not described in the manual or applying the product to nuclear control systems, railroad systems, aviation systems, vehicles, combustion systems, medical equipment, amusement machines, safety equipment, and other systems or equipment that may have a serious influence on lives and property if used improperly. Make sure that the ratings and performance characteristics of the product provide a margin of safety for the system or equipment, and be sure to provide the system or equipment with double safety mechanisms.Cat. No. K137-E1-020412(0412)(O)Note: Do not use this document to operate the Unit. OMRON CorporationELECTRONIC AND MECHANICAL COMPONENTS COMPANY Contact: /ecb。
MMSZ4xxxT1G系列和SZMMSZ4xxxT1G系列零点电阻电源器件的商品说明书

MMSZ4686T1G MMSZ4686T1G.MMSZ4xxxT1G Series, SZMMSZ4xxxT1G Series Zener Voltage Regulators 500 mW, Low I ZT SOD−123 Surface MountThree complete series of Zener diodes are offered in the convenient, surface mount plastic SOD−123 package. These devices provide a convenient alternative to the leadless 34−package style.Features•500 mW Rating on FR−4 or FR−5 Board•Wide Zener Reverse V oltage Range − 1.8 V to 43 V•Low Reverse Current (I ZT) − 50 m A•Package Designed for Optimal Automated Board Assembly •Small Package Size for High Density Applications•ESD Rating of Class 3 (>16 kV) per Human Body Model•SZ Prefix for Automotive and Other Applications Requiring Unique Site and Control Change Requirements; AEC−Q101 Qualified and PPAP Capable•These Devices are Pb−Free and are RoHS Compliant*Mechanical Characteristics:CASE:V oid-free, transfer-molded, thermosetting plastic case FINISH:Corrosion resistant finish, easily solderableMAXIMUM CASE TEMPERATURE FOR SOLDERING PURPOSES: 260°C for 10 SecondsPOLARITY:Cathode indicated by polarity band FLAMMABILITY RATING:UL 94 V−0MAXIMUM RATINGSRating Symbol Max Units Total Power Dissipation on FR−5 Board,(Note 1) @ T L = 75°CDerated above 75°C P D5006.7mWmW/°CThermal Resistance, (Note 2) Junction−to−Ambient R q JA340°C/WThermal Resistance, (Note 2) Junction−to−Lead R q JL150°C/WJunction and Storage Temperature Range T J, T stg−55 to+150°CStresses exceeding those listed in the Maximum Ratings table may damage the device. If any of these limits are exceeded, device functionality should not be assumed, damage may occur and reliability may be affected.1.FR−5 = 3.5 X 1.5 inches, using the minimum recommended footprint.2.Thermal Resistance measurement obtained via infrared Scan Method.*For additional information on our Pb−Free strategy and soldering details, please download the ON Semiconductor Soldering and Mounting Techniques Reference Manual, SOLDERRM/D.Cathode AnodeSee specific marking information in the device marking column of the Electrical Characteristics table on page 3 of this data sheet.DEVICE MARKING INFORMATIONSOD−123CASE 425STYLE 1Device Package Shipping†ORDERING INFORMATIONMARKING DIAGRAM†For information on tape and reel specifications, including part orientation and tape sizes, please refer to our T ape and Reel Packaging Specifications Brochure, BRD8011/D.MMSZ4xxxT1G SOD−123(Pb−Free)3,000 /Tape & ReelMMSZ4xxxT3G SOD−123(Pb−Free)10,000 /Tape & Reel xx= Device Code (Refer to page 3)M= Date CodeG= Pb−Free Package(Note: Microdot may be in either location)1SZMMSZ4xxxT1G SOD−123(Pb−Free)3,000 /Tape & ReelSZMMSZ4xxxT3G SOD−123(Pb−Free)10,000 /Tape & ReelELECTRICAL CHARACTERISTICS (T A = 25°C unless otherwise noted, V F = 0.9 V Max. @ I F = 10 mA)Symbol ParameterV Z Reverse Zener Voltage @ I ZTI ZT Reverse CurrentI R Reverse Leakage Current @ V RVR Reverse VoltageI F Forward CurrentV F Forward Voltage @ I FProduct parametric performance is indicated in the Electrical Characteristics for the listed test conditions, unless otherwise noted. Product performance may not be indicated by the Electrical Characteristics if operated under different conditions.ELECTRICAL CHARACTERISTICS (T A = 25°C unless otherwise noted, V F = 0.9 V Max. @ I F = 10 mA)Device*DeviceMarkingZener Voltage (Note 3)Leakage CurrentV Z (Volts)@ I ZT I R @ V RMin Nom Max m A m A VoltsMMSZ4678T1G CC 1.71 1.8 1.89507.51 MMSZ4679T1G CD 1.90 2.0 2.105051 MMSZ4680T1G CE 2.09 2.2 2.315041 MMSZ4681T1G CF 2.28 2.4 2.525021 MMSZ4682T1G CH 2.565 2.7 2.8355011 MMSZ4683T1G CJ 2.85 3.0 3.15500.81 MMSZ4684T1G CK 3.13 3.3 3.47507.5 1.5 MMSZ4685T1G CM 3.42 3.6 3.78507.52 MMSZ4686T1G CN 3.70 3.9 4.105052 MMSZ4687T1G CP 4.09 4.3 4.525042 SZMMSZ4687T1G CG6 4.09 4.3 4.525042 MMSZ4688T1G CT 4.47 4.7 4.9450103 MMSZ4689T1G CU 4.85 5.1 5.3650103 MMSZ4690T1G/T3G CV 5.32 5.6 5.8850104 MMSZ4691T1G CA 5.89 6.2 6.5150105 MMSZ4692T1G CX 6.46 6.87.145010 5.1 MMSZ4693T1G CY7.137.57.885010 5.7 MMSZ4694T1G CZ7.798.28.61501 6.2 MMSZ4695T1G DC8.278.79.14501 6.6 MMSZ4696T1G DD8.659.19.56501 6.9 MMSZ4697T1G DE9.501010.505017.6 MMSZ4698T1G DF10.451111.55500.058.4 MMSZ4699T1G DH11.401212.60500.059.1 MMSZ4700T1G DJ12.351313.65500.059.8 MMSZ4701T1G DK13.301414.70500.0510.6 MMSZ4702T1G DM14.251515.75500.0511.4 MMSZ4703T1G†DN15.201616.80500.0512.1 MMSZ4704T1G DP16.151717.85500.0512.9 MMSZ4705T1G DT17.101818.90500.0513.6 MMSZ4706T1G DU18.051919.95500.0514.4 MMSZ4707T1G DV19.002021.00500.0115.2 MMSZ4708T1G DA20.902223.10500.0116.7 MMSZ4709T1G DX22.802425.20500.0118.2 MMSZ4710T1G DY23.752526.25500.0119.0 MMSZ4711T1G†EA25.652728.35500.0120.4 MMSZ4712T1G EC26.602829.40500.0121.2 MMSZ4713T1G ED28.503031.50500.0122.8 MMSZ4714T1G EE31.353334.65500.0125.0 MMSZ4715T1G EF34.203637.80500.0127.3 MMSZ4716T1G EH37.053940.95500.0129.6 MMSZ4717T1G EJ40.854345.15500.0132.6 3.Nominal Zener voltage is measured with the device junction in thermal equilibrium at T L = 30°C ±1°C.*Include SZ-prefix devices where applicable.†MMSZ4703 and MMSZ4711 Not Available in 10,000/Tape & ReelTYPICAL CHARACTERISTICSV Z , T E M P E R A T U R E C O E F F I C I E N T (m V /C )°θV Z , NOMINAL ZENER VOLTAGE (V)Figure 1. Temperature Coefficients (Temperature Range −55°C to +150°C)V Z , T E M P E R A T U R E C O E F F I C I E N T (m V /C )°θ100101V Z , NOMINAL ZENER VOLTAGE (V)Figure 2. Temperature Coefficients (Temperature Range −55°C to +150°C)1.21.00.80.60.40.20T, TEMPERATURE (5C)Figure 3. Steady State Power Derating P p k, P E A K S U R G E P O W E R (W A T T S )PW, PULSE WIDTH (ms)Figure 4. Maximum Nonrepetitive Surge PowerP D , P O W E R D I S S I P A T I O N (W A T T S )V Z , NOMINAL ZENER VOLTAGEFigure 5. Effect of Zener Voltage onZener ImpedanceZ Z T , D Y N A M I C I M P E D A N C E ()ΩTYPICAL CHARACTERISTICSC , C A P A C I T A N C E (p F )V Z , NOMINAL ZENER VOLTAGE (V)Figure 6. Typical Capacitance 1000100101V Z , ZENER VOLTAGE (V)1001010.10.01I Z , Z EN E R C U R R E N T (m A )V Z , ZENER VOLTAGE (V)1001010.10.01I R , L E A K A G E C U R R E N T (A )μV Z , NOMINAL ZENER VOLTAGE (V)Figure 7. Typical Leakage Current10001001010.10.010.0010.00010.00001I Z , Z E N E R C U R R E N T (m A )Figure 8. Zener Voltage versus Zener Current(V Z Up to 12 V)Figure 9. Zener Voltage versus Zener Current(12 V to 91 V)SOD−123CASE 425−04ISSUE GDATE 07 OCT 2009SCALE 5:1NOTES:1.DIMENSIONING AND TOLERANCING PER ANSIY14.5M, 1982.2.CONTROLLING DIMENSION: INCH.DIM MIN NOM MAXMILLIMETERSINCHESA0.94 1.17 1.350.037A10.000.050.100.000b0.510.610.710.020c1.600.150.055D 1.40 1.80E 2.54 2.69 2.840.100---3.680.140L0.253.860.0100.0460.0020.0240.0630.1060.1450.0530.0040.0280.0710.1120.152MIN NOM MAX3.56H E---------0.006------------GENERICMARKING DIAGRAM**For additional information on our Pb−Free strategy and solderingdetails, please download the ON Semiconductor Soldering andMounting Techniques Reference Manual, SOLDERRM/D.SOLDERING FOOTPRINT**This information is generic. Please refer to device datasheet for actual part marking. Pb−Free indicator, “G” ormicrodot “ G”, may or may not be present.XXX= Specific Device CodeM= Date CodeG= Pb−Free Package1STYLE 1:PIN 1. CATHODE2. ANODE0.910.036ǒmminchesǓSCALE 10:1------q001010°°°°(Note: Microdot may be in either location) MECHANICAL CASE OUTLINEPACKAGE DIMENSIONSON Semiconductor and are trademarks of Semiconductor Components Industries, LLC dba ON Semiconductor or its subsidiaries in the United States and/or other countries.ON Semiconductor reserves the right to make changes without further notice to any products herein. ON Semiconductor makes no warranty, representation or guarantee regarding the suitability of its products for any particular purpose, nor does ON Semiconductor assume any liability arising out of the application or use of any product or circuit, and specifically disclaims any and all liability, including without limitation special, consequential or incidental damages. ON Semiconductor does not convey any license under its patent rights nor theON Semiconductor and are trademarks of Semiconductor Components Industries, LLC dba ON Semiconductor or its subsidiaries in the United States and/or other countries.ON Semiconductor owns the rights to a number of patents, trademarks, copyrights, trade secrets, and other intellectual property. A listing of ON Semiconductor’s product/patent coverage may be accessed at ON Semiconductor makes no warranty, representation or guarantee regarding the suitability of its products for any particular purpose, nor does ON Semiconductor assume any liability arising out of the application or use of any product or circuit, and specifically disclaims any and all liability, including without limitation special, consequential or incidental damages.PUBLICATION ORDERING INFORMATIONTECHNICAL SUPPORTNorth American Technical Support:Voice Mail: 1 800−282−9855 Toll Free USA/Canada Phone: 011 421 33 790 2910LITERATURE FULFILLMENT :Email Requests to:*******************ON Semiconductor Website: Europe, Middle East and Africa Technical Support:Phone: 00421 33 790 2910For additional information, please contact your local Sales RepresentativeMMSZ4686T1G MMSZ4686T1G.。
Prosonic M FMU40、FMU41、FMU42、FMU44 产品说明书
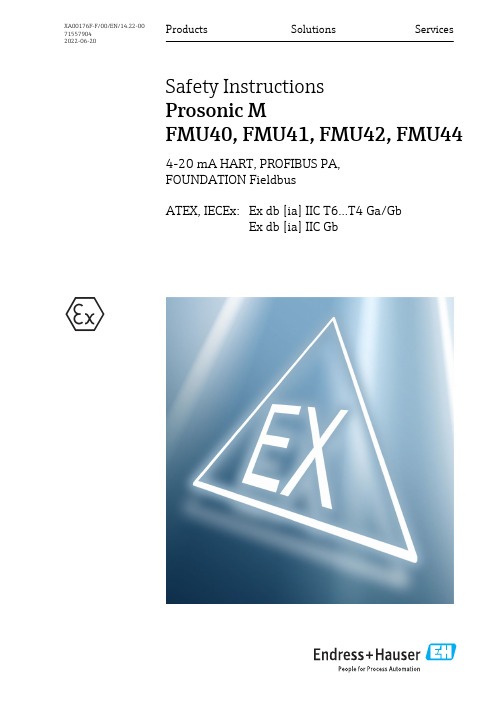
Products Solutions ServicesSafety Instructions Prosonic M FMU40, FMU41, FMU42, FMU444-20 mA HART, PROFIBUS PA,FOUNDATION FieldbusATEX, IECEx:Ex db [ia] IIC T6...T4 Ga/Gb Ex db [ia] IIC GbXA00176F-F/00/EN/14.22-00715579042022-06-20Prosonic M FMU40, FMU41, FMU42, FMU44XA00176F-F Prosonic M FMU40, FMU41, FMU42, FMU444-20 mA HART, PROFIBUS PA, FOUNDATION FieldbusTable of contentsAbout this document (4)Associated documentation (4)Supplementary documentation (4)Manufacturer's certificates (4)Manufacturer address (5)Other standards (5)Extended order code (5)Safety instructions: General (7)Safety instructions: Special conditions (8)Safety instructions: Installation (8)Safety instructions: Ex d joints (9)Temperature tables (9)Connection data (9)Endress+Hauser3XA00176F-F Prosonic M FMU40, FMU41, FMU42, FMU444Endress+HauserAbout thisdocumentThis document has been translated into several languages. Legally determined is solely the English source text.The document translated into EU languages is available:•In the download area of the Endress+Hauser website: -> Downloads -> Manuals and Datasheets ->Type: Ex Safety Instruction (XA) -> Text Search: …•In the Device Viewer: -> Product tools ->Access device specific information -> Check device features If not yet available, the document can be ordered.Associated documentationThis document is an integral part of the following Operating Instructions:HART:BA00237F/00PROFIBUS PA:BA00238F/00FOUNDATION Fieldbus:BA00239F/00Supplementary documentationExplosion-protection brochure: CP00021Z/11The Explosion-protection brochure is available:•In the download area of the Endress+Hauser website: -> Downloads -> Brochures and Catalogs -> Text Search: CP00021Z •On the CD for devices with CD-based documentation Manufacturer's certificatesEU Declaration of Conformity Declaration Number:EG02007The EU Declaration of Conformity is available:In the download area of the Endress+Hauser website: -> Downloads -> Declaration -> Type: EU Declaration -> Product Code: ...EU type-examination certificate Certificate number:KEMA 02ATEX1006 XProsonic M FMU40, FMU41, FMU42, FMU44XA00176F-F Endress+Hauser 5List of applied standards: See EU Declaration of Conformity.IEC Declaration of Conformity Certificate number:IECEx DEK 11.0014X Affixing the certificate number certifies conformity with the following standards (depending on the device version):•IEC 60079-0 : 2017•IEC 60079-1 : 2014•IEC 60529 : 2013Manufacturer addressEndress+Hauser SE+Co. KG Hauptstraße 179689 Maulburg, Germany Address of the manufacturing plant: See nameplate.Other standardsAmong other things, the following standards shall be observed in their current version for proper installation:•IEC/EN 60079-14: "Explosive atmospheres - Part 14: Electrical installations design, selection and erection"•EN 1127-1: "Explosive atmospheres - Explosion prevention and protection - Part 1: Basic concepts and methodology"Extended order codeThe extended order code is indicated on the nameplate, which is affixed to the device in such a way that it is clearly visible. Additional information about the nameplate is provided in the associated Operating Instructions.Structure of the extended order code FMU4x –*************+A*B*C*D*E*F*G*..(Device type)(Basic specifications)(Optional specifications)* =Placeholder At this position, an option (number or letter) selected from the specification is displayed instead of the placeholders.XA00176F-F Prosonic M FMU40, FMU41, FMU42, FMU446Endress+HauserBasic specifications The features that are absolutely essential for the device (mandatory features) are specified in the basic specifications. The number of positions depends on the number of features available.The selected option of a feature can consist of several positions.Optional specifications The optional specifications describe additional features for the device (optional features). The number of positions depends on the number of features available. The features have a 2-digit structure to aid identification (e.g. JA). The first digit (ID) stands for the feature group and consists of a number or a letter (e.g. J = Test, Certificate). The second digit constitutes the value that stands for the feature within the group (e.g. A = 3.1 material (wetted parts), inspection certificate).More detailed information about the device is provided in the following tables. These tables describe the individual positions and IDs in the extended order code which are relevant to hazardous locations.Extended order code: Prosonic M The following specifications reproduce an extract from the product structure and are used to assign:•This documentation to the device (using the extended order code on the nameplate).•The device options cited in the document.Device type FMU40, FMU41, FMU42, FMU44Basic specificationsProsonic M FMU40, FMU41, FMU42, FMU44XA00176F-F Endress+Hauser 7Optional specifications No options specific to hazardous locations are available.Safety instructions:General•The device is intended to be used in explosive atmospheres as defined in the scope of IEC 60079-0 or equivalent national standards. If no potentially explosive atmospheres are present or if additional protective measures have been taken: The device may be operated according to the manufacturer's specifications.•Staff must meet the following conditions for mounting, electrical installation, commissioning and maintenance of the device:•Be suitably qualified for their role and the tasks they perform •Be trained in explosion protection •Be familiar with national regulations •Install the device according to the manufacturer's instructions and national regulations.•Avoid electrostatic charging:•Of plastic surfaces (e.g. enclosure, sensor element, special varnishing, attached additional plates, ..)•Of isolated capacities (e.g. isolated metallic plates)•Refer to the temperature tables for the relationship between the permitted ambient temperature for the electronics enclosure,depending on the range of application and the temperature class.XA00176F-F Prosonic M FMU40, FMU41, FMU42, FMU448Endress+HauserSafety instructions:Special conditionsPermitted ambient temperature range at the electronics enclosure:–40 °C ≤ T a ≤ +60 °C •Observe the information in the temperature tables.•To avoid electrostatic charging: Do not rub surfaces with a dry cloth.•In the event of additional or alternative special varnishing on the enclosure or other metal parts or for adhesive plates:•Observe the danger of electrostatic charging and discharge.•Do not install in the vicinity of processes (≤ 0.5 m) generating strong electrostatic charges.Device type FMU42, FMU44Avoid electrostatic charging of the sensor (e.g. do not rub dry and install outside the filling flow).Safety instructions:Installation1A Zone 11Tank, hazardous area Zone 02Electronic insert 3Enclosure 4Connection compartment (Ex db)5Power supply 6Tank, hazardous area Zone 17Local potential equalizationProsonic M FMU40, FMU41, FMU42, FMU44XA00176F-F Endress+Hauser 9•In potentially explosive atmospheres:•Do not disconnect the electrical connection of the power supply circuit when energized.•Do not open the connection compartment cover when energized.•Only use certified cable entries suitable for the application. Observe national regulations and standards.•When operating the transmitter enclosure at an ambient temperature under –20 °C, use appropriate cables and cable entries permitted for this application.•Continuous service temperature of the connecting cable: ≥ T a +5 K.•When connecting through a conduit entry approved for this purpose,mount the associated sealing unit directly at the enclosure.•Seal unused entry glands with approved Ex db sealing plugs.•Option:•Remote display, e.g. FHX40 (Observe Safety Instructions)•Service interface: Commubox with associated ToF cable (Observe Safety Instructions)Potential equalization Integrate the device into the local potential equalization.Safety instructions: Ex d joints•If required or if in doubt: ask manufacturer for specifications.•Flameproof joints are not intended to be repaired.Temperature tablesZone 1 - Application Observe the permitted temperature range.Connection dataConnection compartment Ex dbXA00176F-F Prosonic M FMU40, FMU41, FMU42, FMU4410Endress+Hauser Option Remote display, e.g. FHX40:Power supply and signal circuit with protection type: intrinsic safety Ex ia IIC, Ex ia IIB.Connecting the Commubox service interface with the associated ToF cable*71557904*71557904。
MAX1978中文数据手册

用于Peltier模块的集成温度控制器概论MAX1978 / MAX1979是用于Peltier热电冷却器(TEC)模块的最小, 最安全, 最精确完整的单芯片温度控制器。
片上功率FET和热控制环路电路可最大限度地减少外部元件, 同时保持高效率。
可选择的500kHz / 1MHz开关频率和独特的纹波消除方案可优化元件尺寸和效率, 同时降低噪声。
内部MOSFET的开关速度经过优化, 可降低噪声和EMI。
超低漂移斩波放大器可保持±0.001°C的温度稳定性。
直接控制输出电流而不是电压, 以消除电流浪涌。
独立的加热和冷却电流和电压限制提供最高水平的TEC保护。
MAX1978采用单电源供电, 通过在两个同步降压调节器的输出之间偏置TEC, 提供双极性±3A输出。
真正的双极性操作控制温度, 在低负载电流下没有“死区”或其他非线性。
当设定点非常接近自然操作点时, 控制系统不会捕获, 其中仅需要少量的加热或冷却。
模拟控制信号精确设置TEC 电流。
MAX1979提供高达6A的单极性输出。
提供斩波稳定的仪表放大器和高精度积分放大器, 以创建比例积分(PI)或比例积分微分(PID)控制器。
仪表放大器可以连接外部NTC或PTC热敏电阻, 热电偶或半导体温度传感器。
提供模拟输出以监控TEC温度和电流。
此外, 单独的过热和欠温输出表明当TEC温度超出范围时。
片上电压基准为热敏电阻桥提供偏置。
MAX1978 / MAX1979采用薄型48引脚薄型QFN-EP 封装, 工作在-40°C至+ 85°C温度范围。
采用外露金属焊盘的耐热增强型QFN-EP封装可最大限度地降低工作结温。
评估套件可用于加速设计。
应用光纤激光模块典型工作电路出现在数据手册的最后。
WDM, DWDM激光二极管温度控制光纤网络设备EDFA光放大器电信光纤接口ATE特征♦尺寸最小, 最安全, 最精确完整的单芯片控制器♦片上功率MOSFET-无外部FET♦电路占用面积<0.93in2♦回路高度<3mm♦温度稳定性为0.001°C♦集成精密积分器和斩波稳定运算放大器♦精确, 独立的加热和冷却电流限制♦通过直接控制TEC电流消除浪涌♦可调节差分TEC电压限制♦低纹波和低噪声设计♦TEC电流监视器♦温度监控器♦过温和欠温警报♦双极性±3A输出电流(MAX1978)♦单极性+ 6A输出电流(MAX1979)订购信息* EP =裸焊盘。
敏迪产品硬件介绍

3300 MXe控制器配置选加配置MXe基本配置到MXe扩展配置扩展包,包括:1块选加的CPU处理器,用于E2T,1块128信道回波消除模块1块冗余硬盘,RAID模块以及一个冗余电源,提供冗余配置1 - 2个4电路DSP模块,用于G7.29语音压缩1- 4 Dual FIM模块,用于连接外围单元和NSU1- 3 双端口T1/E1 模块1- 3 T1/E1 Combo模块1- 3 4电路BRI模块1- 2个4端口CIM模块,可连接最大8个ASU II
模拟服务单元ASUII提供2个模拟接口板插槽,用于扩展模拟用户和模拟中继接口支持的接口板包括:16/24端口模拟分机板,12+4端口模拟用户模拟中继综合板
双端口T1/E1数字中继模块MMC支持多种数字中继信令,用于连接公网
单端口T1/E1数字中继模块MMC支持多种数字中继信令,用于连接公网还提供8信道语音压缩,还提供32信道回波消除资源
TDM Switch Matrix
E2T CardCall C源自ntrolRTC Card
DSP
3300控制器
Echo Canceller
CX(i)支持150分机16端口以太网交换机可选,支持 PoE可用于小型远程办公室
MXe 支持350/1500分机支持选加的核心组件冗余配置,支持双机热备冗余配置可被配置为用户控制器,中继网关和媒体网关
3300 ICP——3300 CX/CXi控制器
3300 CXi控制器配置标准配置1个266MHz CPU处理器,256M内存,1块硬盘2个内置DSP资源1个10/100 WAN端口(支持NAT和防火墙)和1个10/100/1G LAN端口模拟主板: 6 LS CLASS,4 ONS CLASS,2 PFT,1 MOH,1 广播L2 Switch:16个10/100 802.3af 端口3个空MMC槽位,1个不可视,2个可视
Vishay Semiconductors TFDU4101 无线短距离通信模块技术参数说明说明书

Infrared Transceiver Module (SIR, 115.2 kbit/s) for IrDA®ApplicationsDESCRIPTIONThe TFDU4101 transceiver is an infrared transceiver module compliant to the latest IrDA® physical layer standard for fast infrared data communication, supporting IrDA speeds up to 115.2 kbit/s (SIR), and carrier based remote control modes. Integrated within the transceiver module are a photo pin diode, an infrared emitter (IRED), and a low-power control IC to provide a total front-end solution in a single package. This device covers the full IrDA range of more than 1 m using the internal intensity control. With one external current control resistor the current can be adjusted for shorter ranges saving operating current operating in IrDA low power mode. This Vishay SIR transceiver is using the lead frame technology.The receiver output pulse duration is independent of the optical input pulse duration and recovers always a fixed pulse duration optimum for compatibility to standard Endecs and interfaces. TFDU4101 has a tristate output and is floating in shutdown mode with a weak pull-up.FEATURES•Operates from 2.4 V to 5.5 V within specification over full temperature range from- 30 °C to + 85 °C•Split power supply, transmitter and receivercan be operated from two power supplieswith relaxed requirements saving costs,US - patent no. 6,157,476•Low power consumption (< 0.12 mA supply current in receive mode, no signal)•Power shutdown mode (< 4 μA shutdown current in full temperature range, up to 85 °C, < 10 nA at 25 °C) •Surface mount package (L x W x H in mm): 9.7 × 4.7 × 4•High efficiency emitter•Low profile (universal) package capable of surface mount soldering to side and top view orientation•Directly Interfaces with various super I/O and controller devices as e. g. TOIM4232•Tri-state-receiver output, floating in shut down with a weak pull-up•Qualified for lead (Pb)-free and Sn/Pb processing (MSL4)•Material categorization: For definitions of compliance please see /doc?99912 APPLICATIONS•Printers, fax machines, photocopiers, screen projectors •Internet TV boxes, video conferencing systems•Medical data collection•Diagnostic systems•Notebook computers, desktop PCs, palmtop computers (Win CE, Palm PC), PDAs•Internet TV boxes, video conferencing systems •External infrared adapters (dongles)•Data loggers•GPS•Kiosks, POS, point and pay devices•Industrial applications PRODUCT SUMMARYPART NUMBER DATA RATE(kbit/s)DIMENSIONSH x L x W(mm x mm x mm)LINK DISTANCE(m)OPERATINGVOLTAGE(V)IDLE SUPPLYCURRENT(mA)TFDU4101115.2 4 x 9.7 x 4.70 to ≥ 1 2.4 to 5.50.07PARTS TABLEPART DESCRIPTION QTY/REEL TFDU4101-TR3Oriented in carrier tape for side view surface mounting1000 pcs TFDU4101-TT3Oriented in carrier tape for top view surface mounting1000 pcsFUNCTIONAL BLOCK DIAGRAMPIN DESCRIPTIONPINNUMBERSYMBOL DESCRIPTION I/O ACTIVE1V CC2IRED anodeIRED anode to be externally connected to V CC2. An external resistor isonly necessary for controlling the IRED current when a current reduction below 300 mA is intended to operate in IrDA low power mode.This pin is allowed to be supplied from an uncontrolled power supplyseparated from the controlled V CC1 - supply.2IRED cathode IRED cathode, internally connected to driver transistor3TXD This Schmitt-Trigger input is used to transmit serial data when SD is low.An on-chip protection circuit disables the LED driver if the TXD pin isasserted for longer than 50 μs (max. 300 μs).I High4RXD Received data output, push-pull CMOS driver output capable of drivingstandard CMOS or TTL loads. During transmission the RXD output isactive (echo-on). No external pull-up or pull-down resistor is required.Floating with a weak pull-up of 500 k (typ.) in shutdown mode.O Low5SD Shutdown I High 6V CC1Supply voltage7NC No internal connection I8GND GroundPINOUTTFDU4101 Weight 200 mgNote•Reference point pin, GND unless otherwise noted. Typical values are for DESIGN AID ONLY, not guaranteed nor subject to production testing.Note•Vishay transceivers operating inside the absolute maximum ratings are classified as eye safe according the above table.ABSOLUTE MAXIMUM RATINGSPARAMETER TEST CONDITIONS SYMBOL MIN.TYP.MAX.UNIT Supply voltage range, transceiver- 0.3 V < V CC2 < 6 V V CC1- 0.56V Supply voltage range, transmitter - 0.5 V < V CC1 < 6 V V CC2- 0.56V Voltage at RXD- 0.5 V < V CC1 < 6 V V RXD - 0.5V CC1 + 0.5V Voltage at all inputs and outputs V in > V CC1 is allowedV in- 0.56V Input currents For all pins, except IRED anode pin10mA Output sinking current 25mA Power dissipation See derating curveP D 250mW Junction temperature T J 125°C Ambient temperature range (operating)T amb - 30+ 85°C Storage temperature range T stg- 30+ 85°C Soldering temperature See “Recommended Solder Profile”260°C Average output current, pin 1I IRED (DC)80mA Repetitive pulse output current, pin 1 to pin 2< 90 μs, t on < 20 %I IRED (RP)400mAEYE SAFETY INFORMATIONSTANDARDCLASSIFICATIONIEC/EN 60825-1 (2007-03), DIN EN 60825-1 (2008-05) “SAFETY OF LASER PRODUCTS - Part 1: equipment classification and requirements”, simplified methodClass 1IEC 62471 (2006), CIE S009 (2002) “Photobiological Safety of Lamps and Lamp Systems”Exempt DIRECTIVE 2006/25/EC OF THE EUROPEAN PARLIAMENT AND OF THE COUNCIL of 5th April 2006 on the minimum health and safety requirements regarding the exposure of workers to risks arising from physical agents (artificial optical radiation) (19th individual directive within the meaning of article 16(1) of directive 89/391/EEC)ExemptNotes•T amb = 25 °C, V CC1 = V CC2 = 2.4 V to 5.5 V unless otherwise noted.•Typical values are for DESIGN AID ONLY, not guaranteed nor subject to production testing.(1)Standard illuminant A.(2)The typical threshold level is 0.5 x V CC1. It is recommended to use the specified min./max. values to avoid increased operating current.ELECTRICAL CHARACTERISTICSPARAMETER TEST CONDITIONS/PINSSYMBOL MIN.TYP.MAX.UNIT TRANSCEIVER Supply voltage V CC12.4 5.5V Dynamic supply currentSD = low, E e = 1 klx (1),T amb = - 25 °C to + 85 °C V CC1 = V CC2 = 2.4 V to 5.5 V I CC14090130μADynamic supply current SD = low, E e = 1 klx (1),T amb = 25 °CV CC1 = V CC2 = 2.4 V to 5.5 VI CC14075μA Average dynamic supply current, transmittingI IRED = 300 mA,25 % duty cycleI CC 0.65 2.5mA Shutdown supply currentSD = high, T = 25 °C, E e = 0 klx no signal, no resistive loadI SD 0.010.1μA SD = high, T = 70 °C no signal, no resistive load I SD 1μA SD = high, T = 85 °C no signal, no resistive loadI SD 1μA Operating temperature range T A - 30+ 85°C Output voltage low, RXD C load = 15 pFV OL - 0.50.15 x V CC1V Output voltage high, RXD I OH = - 500 μA, C Load = 15 pF V OH 0.8 x V CC1V CC1 + 0.5V I OH = - 250 μA, C Load = 15 pF V OH 0.9 x V CC1V CC1 + 0.5V RXD to V CC1 impedance R RXD 400500600k ΩInput voltage low (TXD, SD)V IL - 0.50.5V Input voltage high (TXD, SD) 1.5 V ≤ V logic ≤ 2.5 V (2)V IH 0.8 x V CC16V V logic > 2.5 V (2)V IH V CC1 - 0.56V Input leakage current (TXD, SD)V in = 0.9 x V CC1I ICH - 2+ 2μA Controlled pull down current 0 < V in < 0.15 V CC1 V in > 0.7 V CC1SD, TXD = “0” or “1”I IrTX - 10+ 1501μA μA Input capacitance (TXD, SD)C I5pFNotes (3)T amb = 25 °C, V CC1 = V CC2 = 2.4 V to 5.5 V unless otherwise noted.Typical values are for DESIGN AID ONLY, not guaranteed nor subject to production testing. (4)IrDA specification is 40 mW/m 2. Specification takes a window loss of 10 % into account.(5)IrDA sensitivity definition: minimum irradiance E ein angular range, power per unit area. The receiver must meet the BER specification while the source is operating at the minimum intensity in angular range into the minimum half-angular range at the maximum link length.(6)Maximum irradiance E ein angular range, power per unit area. The optical delivered to the detector by a source operating at the maximum intensity in angular range at minimum link length must not cause receiver overdrive distortion and possible ralated link errors. If placed at the active output interface reference plane of the transmitter, the receiver must meet its bit error ratio (BER) specification.(7)Using an external current limiting resistor is allowed and recommended to reduce IRED intensity and operating current when current reduction is intended to operate at the IrDA low power conditions. E.g. for V CC2 = 3.3 V a current limiting resistor of R S = 56 Ω will allow a power minimized operation at IrDA low power conditions.(8)Due to this wavelength restriction compared to the IrDA spec of 850 nm to 900 nm the transmitter is able to operate as source for the standard remote control applications with codes as e.g. Phillips RC5/RC6® or RECS 80.For more definitions see the document “Symbols and Terminology” on the Vishay website.OPTOELECTRONIC CHARACTERISTICS (1)PARAMETER TEST CONDITIONSSYMBOLMIN.TYP.MAX.UNITRECEIVERMinimum irradiance E e in angular range (3) SIR mode 9.6 kbit/s to 115.2 kbit/sλ = 850 nm to 900 nm; α = 0°, 15°E e, min.4(0.4)20(2)35 (2)(3.5)mW/m 2 (μW/cm 2)Maximum irradiance E e in angular range (4)λ = 850 nm to 900 nm E e, max.5(500)kW/m 2 (mW/cm 2)Rise time of output signal 10 % to 90 %, C L = 15 pF t r (RXD)20100ns Fall time of output signal 90 % to 10 %, C L = 15 pF t f (RXD)20100ns RXD pulse width Input pulse length > 1.2 μs t PW1.652.23μs Leading edge jitter Input irradiance = 100 mW/m 2,≤ 115.2 kbit/s 250ns Standby/shutdown delay, receiver startup time After shutdown active or power-on500μs Latency t L100150μsTRANSMITTER IRED operating current, switched current limiter No external resistor for current limitation (5)I D 250300350mA Forward voltage of built-in IREDI f = 300 mAV f 1.4 1.81.9V Output leakage IRED current I IRED - 11μA Output radiant intensity α = 0°, 15°TXD = high, SD = lowI e 4865mW/sr Output radiant intensity V CC1 = 5 V, α = 0°, 15°TXD = low or SD = high (receiver is inactiveas long as SD = high)I e 0.04mW/sr Output radiant intensity, angle of half intensityα± 24deg Peak - emission wavelength (6)λp 880900nm Spectral bandwidth ∆λ45nm Optical rise time, optical fall timet ropt , t fopt10300ns Optical output pulse duration Input pulse width 1.6 μs < t TXD < 20 μs t opt t TXD - 0.15t TXD + 0.15μs Optical output pulse duration Input pulse width t TXD ≥ 20 μst opt20300μs Optical overshoot25%RECOMMENDED CIRCUIT DIAGRAMOperated with a clean low impedance power supply the TFDU4101 needs no additional external components. However, depending on the entire system design and board layout, additional components may be required (see figure 1). That is especially the case when separate power supplies are used for bench tests. When using compact wiring and regulated supplies as e. g. in phone applications in most cases no external components are necessary.Fig. 1 - Recommended Test CircuitNote*) R1 is optional when reduced intensity is used.The capacitor C 1 is buffering the supply voltage and eliminates the inductance of the power supply line. This one should be a Tantalum or other fast capacitor to guarantee the fast rise time of the IRED current. The resistor R1 is the current limiting resistor, which may be used to reduce the operating current to levels below the specified controlled values for saving battery power.Vishay's transceivers integrate a sensitive receiver and a built-in power driver. The combination of both needs a careful circuit board layout. The use of thin, long, resistive and inductive wiring should be avoided. The shutdown input must be grounded for normal operation, also when theshutdown function is not used.The inputs (TXD, SD) and the output RXD should be directly connected (DC-coupled) to the I/O circuit. The capacitor C2 combined with the resistor R2 is the low pass filter for smoothing the supply voltage. R2, C1 and C2 are optional and dependent on the quality of the supply voltages V CC1and injected noise. An unstable power supply with dropping voltage during transmission may reduce the sensitivity (and transmission range) of the transceiver.The placement of these parts is critical. It is strongly recommended to position C 2 as close as possible to the transceiver power supply pins.When extended wiring is used (bench tests!) the inductance of the power supply can cause dynamically a voltage drop at V CC2. Often some power supplies are not able to follow the fast current rise time. In that case another 4.7 μF (type, see table under C1) at V CC2 will be helpful.Under extreme EMI conditions as placing an RF-transmitter antenna on top of the transceiver, we recommend to protect all inputs by a low-pass filter, as a minimum a 12 pF capacitor, especially at the RXD port. The transceiver itself withstands EMI at GSM frequencies above 500 V/m. When interference is observed, the wiring to the inputs picks it up. It is verified by DPI measurements that as long as the interfering RF - voltage is below the logic threshold levels of the inputs and equivalent levels at the outputs no interferences are expected.One should keep in mind that basic RF-design rules for circuit design should be taken into account. Especially longer signal lines should not be used without termination. See e.g. "The Art of Electronics" Paul Horowitz, Winfield Hill, 1989, Cambridge University Press, ISBN: 0521370957.Figure 2 shows an example of a typical application with a separate supply voltage V S and using the transceiver with the IRED anode connected to the unregulated battery V batt . This method reduces the peak load of the regulated power supply and saves therefore costs. Alternatively all supplies can also be tied to only one voltage source. R1 and C1 are not used in this case and are depending on the circuit design in most cases not necessary.In figure 2 an option is shown to operate the transmitter at two different power levels to switch for long range to lowpower mode for e.g. saving power for IrDA application but use the full range specification for remote control. The additional components are marked in the figure.For operating at RS232 ports TOIM4232 is recommendedas ENDEC.TABLE 1 - RECOMMENDED TESTS AND APPLICATION CIRCUIT COMPONENTSCOMPONENTRECOMMENDED VALUEVISHAY PART NUMBERC1 4.7 μF, 16 V 293D 475X9 016B C20.1 μF, ceramic VJ 1206 Y 104 J XXMT R1Depends on current to be adjusted, e. g. with V CC2 = 3.3 V 56 Ω is an option for minimum low power operationR247 Ω, 0.125 WCRCW-1206-47R0-F-RT1Fig. 2 - Typical Application CircuitGrey: Optional for High/Low SwitchingI/O AND SOFTWAREIn the description, already different I/Os are mentioned. Different combinations are tested and the function verified with the special drivers available from the I/O suppliers. In special cases refer to the I/O manual, the Vishay application notes, or contact directly Vishay Sales, Marketing or Application.CURRENT DERATING DIAGRAMFigure 3 shows the maximum operating temperature when the device is operated without external current limiting resistor.Fig. 3 - Current Derating DiagramTABLE 2 - TRUTH TABLEINPUTS OUTPUTS REMARKSD TXD OPTICAL INPUT IRRADIANCEmW/m2RXD TRANSMITTER OPERATIONHigh > 1 ms x xWeakly pulled(500 k ) to V CC10ShutdownLow High < 50 μs x Low active I e TransmittingHigh > 50 μs x High inactive0Protection is active Low< 4High inactive0Ignoring low signals below theIrDA defined threshold for noiseimmunity Low> min. irradiance E e< max. irradiance E eLow (active)0Response to an IrDA compliantoptical input signal Low> max. irradiance E e Undefined0Overload conditions can causeunexpected outputsRECOMMENDED SOLDER PROFILES Solder Profile for Sn/Pb SolderingFig. 4 - Recommended Solder Profile for Sn/Pb SolderingLead (Pb)-free, Recommended Solder ProfileThe TFDU4101 is a lead (Pb)-free transceiver and qualified for lead (Pb)-free processing. For lead (Pb)-free solder paste like Sn(3.0-4.0)Ag(0.5-0.9)C u, there are two standard reflow profiles: Ramp-Soak-Spike (RSS) and Ramp-To-Spike (RTS). The Ramp-Soak-Spike profile was developed primarily for reflow ovens heated by infrared radiation. With widespread use of forced convection reflow ovens the Ramp-To-Spike profile is used increasingly. Shown below in figure 5 and 6 are Vishay's recommended profiles for use with the TFDU4101 transceivers. For more details please refer to the application note “SMD Assembly Instructions”.A ramp-up rate less than 0.9 °C/s is not recommended. Ramp-up rates faster than 1.3 °C/s could damage an optical part because the thermal conductivity is less than compared to a standard IC.Wave SolderingFor TFDUxxxx and TFBSxxxx transceiver devices wave soldering is not recommended.Manual SolderingManual soldering is the standard method for lab use. However, for a production process it cannot be recommended because the risk of damage is highly dependent on the experience of the operator. Nevertheless, we added a chapter to the above mentioned application note, describing manual soldering and desoldering.StorageThe storage and drying processes for all Vishay transceivers (TFDUxxxx and TFBSxxx) are equivalent to MSL4.The data for the drying procedure is given on labels on the packing and also in the application note “Taping, Labeling, Storage and Packing”. Fig. 5 - Solder Profile, RSS Recommendation Fig. 6 - RTS RecommendationPACKAGE DIMENSIONS in millimetersFig. 7 - Package Drawing TFDU4101. Tolerance ± 0.2 mm if not otherwise mentionedFig. 8 - Recommended Footprint for Side View Applications and Solderpaste MaskFig. 9 - Recommended Footprint for Top View Applications and Solderpaste MaskREEL DIMENSIONSin millimetersTAPE WIDTH(mm)A MAX.(mm)N (mm)W 1 MIN.(mm)W 2 MAX.(mm)W 3 MIN.(mm)W 3 MAX.(mm)243306024.430.423.927.4TAPE DIMENSIONS in millimetersFig. 10 - Tape Drawing, TFDU4101 for Top View Mounting, Tolerance ± 0.1 mmHANDLING PRECAUTIONSagging of carrier tape may cause some units to rotate and will result to pick-and-place problem. Do not allow carrier tape to sag as shown in picture below.Fig. 11 - Tape Drawing, TFDU4101 for Side View Mounting, Tolerance ± 0.1 mmLegal Disclaimer Notice VishayDisclaimerALL PRODUCT, PRODUCT SPECIFICAT IONS AND DAT A ARE SUBJECT T O CHANGE WIT HOUT NOT ICE T O IMPROVE RELIABILITY, FUNCTION OR DESIGN OR OTHERWISE.Vishay Intertechnology, Inc., its affiliates, agents, and employees, and all persons acting on its or their behalf (collectively, “Vishay”), disclaim any and all liability for any errors, inaccuracies or incompleteness contained in any datasheet or in any other disclosure relating to any product.Vishay makes no warranty, representation or guarantee regarding the suitability of the products for any particular purpose or the continuing production of any product. To the maximum extent permitted by applicable law, Vishay disclaims (i) any and all liability arising out of the application or use of any product, (ii) any and all liability, including without limitation special, consequential or incidental damages, and (iii) any and all implied warranties, including warranties of fitness for particular purpose, non-infringement and merchantability.Statements regarding the suitability of products for certain types of applications are based on Vishay’s knowledge of typical requirements that are often placed on Vishay products in generic applications. Such statements are not binding statements about the suitability of products for a particular application. It is the customer’s responsibility to validate that a particular product with the properties described in the product specification is suitable for use in a particular application. Parameters provided in datasheets and / or specifications may vary in different applications and performance may vary over time. All operating parameters, including typical parameters, must be validated for each customer application by the customer’s technical experts. Product specifications do not expand or otherwise modify Vishay’s terms and conditions of purchase, including but not limited to the warranty expressed therein.Except as expressly indicated in writing, Vishay products are not designed for use in medical, life-saving, or life-sustaining applications or for any other application in which the failure of the Vishay product could result in personal injury or death. Customers using or selling Vishay products not expressly indicated for use in such applications do so at their own risk. Please contact authorized Vishay personnel to obtain written terms and conditions regarding products designed for such applications.No license, express or implied, by estoppel or otherwise, to any intellectual property rights is granted by this document or by any conduct of Vishay. Product names and markings noted herein may be trademarks of their respective owners.。
OmegaTM DP41系列数字面板表 控制器说明书
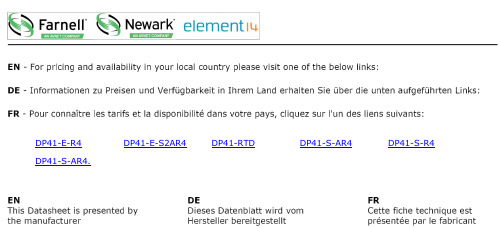
DP41-E-R4DP41-E-S2AR4DP41-RTD DP41-S-AR4DP41-S-R4 DP41-S-AR4.T he Omega TM DP41 Series of digital panel meter/controllers has set the world standard for accuracy and quality in industrial instrumentation. These meters can measure a broad spectrum of DC voltage and current ranges as well as inputs from 9 thermocouple types and from most RTDs, pressure transducers, load cells, strain gages, andpotentiometers. Models include the DP41-W, a legal-for-trade, NTEP-certified strain meter with enhanced features, and the DP41-U, which covers all the input types.Standard features include 6-digit display; 5 front-panel pushbutton keys; 4 open-collector outputs; and alarm/control, BCD, and analog outputs. Configurable analog output ranges are 0 to 20 mA, 4 to 20 mA, 0 to 5 Vdc, and 0 to 10 Vdc.On-board excitation allows these meters to power virtually any sensor or transmitter, and 4 setpoints give the user numerous control/alarm possibilities. Setpoint configurations include active above or below; latching or non-latching; and high deviation, low deviation, or band deviation.With the RS232/485 serialcommunications option, the user can set the display parameters and read the current, max, and min values remotely. The DP40-R board option provides dual 7 A mechanical relays, activated by the selected setpoint.1⁄8 DIN HIGH-PERFORMANCE METERS ALARM/CONTROL CAPABILITIESSTRAIN GAGE, PROCESS VOLTAGE AND CURRENT, TEMPERATUREDP41 SeriesAll Units Feature:U 5-Year Warranty U 6-Digit Display U Min/Max Storage U 4 Isolated Open-Collector OutputsU NEMA 4 (IP65) Front Panel U 12 Readings per Second U Alarm/Control Capabilities U S mart Filtering Detects the Difference Between a Spike or Process Change(Patent Applied for)U Peak and Valley Detection UDigital Tare U E asy Front-Panel ProgrammingU Optional BCD Output U Optional Analog Output U O ptional RS232/RS485 Communications U O ptional Mechanical Relays Thermocouple Input:U 0.01° Resolution U 0.2°C AccuracyU 9 Thermocouple Types U °C/°F/K Units U U ses Complete NIST Calibration Tables RTD Input:U 0.01° Resolution U 0.2°C Accuracy U 2-, 3-, or 4-WireU 385 and 392 Pt CurvesVoltage/Current Inputs:U ±0.005% Rdg Accuracy U 10 User-Selectable Voltage or 4 to 20/0 to 20 mA Input Ranges U F ully Scalable Display Up to 500,000 Counts U 1.5 to 11 Vdc or 24 Vdc Sensor ExcitationU Adjustable Decimal PointDP41-S strain meter shown actual size.HIGH-PERFORMANCE METERSThe DP41 thermocouple meter offers very high accuracy ensured by an advanced (patent applied for) thermocouple linearizing s ystem. Accuracy for most thermocouple types is 0.2°C (3.6ºF). The meter is front-panelprogrammable for any of 9 thermocouple types. The DP41 RTD input meter is programmable for any 6 to 6000 Ω DIN or NIST platinum RTD. It provides a precision ultra-low constant current excitation to minimize self-heating errors and maximize stability.DP41-T and DP41-RTD shown smaller than actual size.A complete selection ofthermocouple and RTD probes areavailable from Omega TMOffset Adjustment: 0 to 999,999 or 0 to -99,999, programmable Thermocouple Input Types: J, K, T, E, R, S, B, N, J DINRTD Input: Any 6 Ω to 6 k Ω NIST or DIN platinum and any linear RTD RTD Connection: 2-, 3- or 4-wireSensor Break Protection: Up-scale or down-scale, programmableSensor Excitation: 10 V at 30 mA; 24V at 25 mASPECIFICATIONSAccuracy: ±0.005% rdgSpan Temperature Coefficient: ±20 ppm Step Response: 1 s to 99.9%Warm-Up to Rated Accuracy: 50 minutes Operating Environment: 0 to 50°C (32 to 122°F); 95% RH, non-condensing Storage Temperature: -40 to 85°C (-40 to 185°F)Power: 115 or 230 Vac, 49 to 400 Hz; 10 to 32 VdcPower Consumption: 6 W nom., 10 W max Normal-Mode Rejection: 60 dB Common-Mode Rejection: 120 dB Common-Mode Voltage: 1500 Vp per HV test Resolution: 15-bitConversion: Dual-slope technique Reading Rate: 3/s or 13/s, 60 Hz; 3/s or 12/s, 50 HzDisplay: Red or green 6-digit, 14-segment, 13.7 mm (0.54") high; 4 alarm indicators Dimensions: 48 H x 96 W x 165 mm D (1.89 x 3.78 x 6.5")Panel Cutout: 45 H x 92 mm W (1.772 x 3.622"); 1⁄8 DIN Weight: 574 g (1.27 lb)Setpoint Outputs: 4 isolated open collector; rated 150 mA at 1V sink, 30V openBCD Output: Isolated, tri-state, TTL/CMOS compatible; external 5V supply required for isolated; internal 5V supply for non-isolatedDual Relays: Form “C”, 7 A @ 30 Vdc or 230 Vac4-Relay Option: Dual 7 A relays and dual 1 A relaysAnalog Output: 0 to 5V/1 to 5V/0 to 10V/0 to 20 mA/4 to 20 mA, user selectable; 354 Vp isolation; 15-bit resolution; 0.1% accuracy; 50 ms step responseRS232 Communications: 300/600/1200/2400/4800/9600/19.2K baud; RJ11 4-wire connection; programmable to transmit current display, alarm status, min/max, actual measured input value and status RS485 Communications: 300/600/1200/2400/4800/9600/19.2K baud; RJ12 6-wire connection; addressable from 0 to 199Voltage Input Ranges: 0 to 100 mV, 0 to 1V, 0 to 5V, 1 to 5V, 0 to 10V,0 to 100V, ±50 mV, ±500 mV, ±5V, ±50V Current Input Ranges: 0 to 20 mA, 4 to 20 mAInput Configuration: Single-endedPolarity: Unipolar/bipolar, programmable Span Adjustment: 0.00001 to 500,000, programmableused per unit. DC power option not available on models with DP40-R or DP40-R4.Ordering Example: DP41-TC-DC-S2A and DP40-9SC2, DP41 unit for thermocouple inputs, with 10 to 32 Vdc power,RS232 communications, analog output and 9-pin serial connector.termination. For proper termination to a computer, 9-pin and 25-pinconnectors are offered below.DP41Z-E split meter withremote display, panel mount or surface mount with bracket shownsmaller than actual size.DP41-TC with thermocouple probe, soldHIGH-PERFORMANCE METERSDP41-TBS bench stand, sold separately.DP41Z-E shownsmaller than actual size.1⁄8 DIN HIGH-PERFORMANCE PROCESS INDICATORSDP41 SERIESDP41-E-R4DP41-E-S2AR4DP41-RTD DP41-S-AR4DP41-S-R4 DP41-S-AR4.。
哈广1kW_全固态PDM_中波发射机改频案例及主要原理分析

45Internet Technology互联网+技术一、引言笔者有幸参与了1kW 中波发射机载波频率由603kHz 改频到1260kHz 以及1503kHz 改频到1557kHz 的工作,从中总结出一些经验方法,希望对今后类似的工作有一定的借鉴、指导作用。
因两次改频步骤方法一样,本文主要以603kHz 改频到1260kHz 为案例讲述。
发射机哈广1kWkW 全固态PDM 发射机的工作原理见图1所示。
图1中展示的发射机包含射频电路、音频电路、电源部分和控制电路等。
(一)射频系统哈广1kW 全固态PDM 中波发射机 改频案例及主要原理分析包括DDS 频率合成器、前置放大器、功率放大器、功率合成器、末级槽路、输出取样、输出监测等。
(二)调制系统包括调制器板(带音频处理器)、调制器驱动板。
调制系统用于将调制信号与载波信号相结合,以便发送信号传输。
(三)电源部分包括主整电源、低压稳压电源。
主整电源用于提供整体系统的电源供应,而低压稳压电源用于提供稳定的低电压供应。
摘要:本文介绍了哈广1kW 全固态PDM 中波发射机载波频率由603kHz 改频到1260kHz 的调整方法与步骤,其中进行了详细的原理分析,总结了一些有益的经验,与行业同仁分享。
关键词:1kW 中波射机;改频调试;射频系统;频率合成;谐振;阻抗、图2 射频系统关键部分工作原理图图1 PDM1kWkW 中波发射机原理方框图王绍强(1988.01-),男,彝族,云南永平,本科,工程师,研究方向:广播电视技术;林心平(1981.12-),男,汉族,云南大理,本科,助理工程师,研究方向:广播电视技术。
(四)控侧保护与状态显示系统包含LCD 显示屏、智能控制板键盘,包含输入、输出接口电路。
这个系统用于控制和保护整个系统,并通过LCD 显示屏和键盘与用户进行交互。
载波频率与控制电路、电源部分和音频电路没有相关性,可轻松适应中波频段,改动涉及功率合成母板、发射机输出网络、频率合成震荡板、输出监测板和天线调配网络,主要针对的还是射频电路。
W311 321 341硬件用户手册第七版,2009年7月说明书
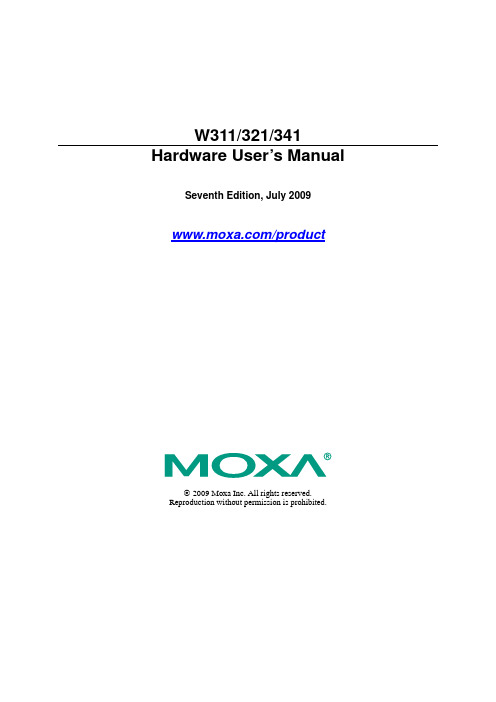
W311/321/341 Hardware User’s Manual Seventh Edition, July 2009/product© 2009 Moxa Inc. All rights reserved.Reproduction without permission is prohibited.W311/321/341Hardware User’s ManualThe hardware described in this manual is furnished under a license agreement and may be used only inaccordance with the terms of that agreement.Copyright NoticeCopyright © 2009 Moxa Inc.All rights reserved.Reproduction without permission is prohibited.TrademarksMOXA is a registered trademark of Moxa Inc.All other trademarks or registered marks in this manual belong to their respective manufacturers.DisclaimerInformation in this document is subject to change without notice and does not represent a commitment on the part of Moxa.Moxa provides this document “as is,” without warranty of any kind, either expressed or implied, including, but not limited to, its particular purpose. Moxa reserves the right to make improvements and/or changes to this manual, or to the products and/or the programs described in this manual, at any time.Information provided in this manual is intended to be accurate and reliable. However, Moxa assumes no responsibility for its use, or for any infringements on the rights of third parties that may result from its use.This product might include unintentional technical or typographical errors. Changes are periodically made to the information herein to correct such errors, and these changes are incorporated into new editions of the publication.Technical Support Contact Information/supportMoxa Americas:Toll-free: 1-888-669-2872 Tel: +1-714-528-6777 Fax: +1-714-528-6778 Moxa China (Shanghai office): Toll-free: 800-820-5036 Tel: +86-21-5258-9955 Fax: +86-10-6872-3958Moxa Europe:Tel: +49-89-3 70 03 99-0 Fax: +49-89-3 70 03 99-99 Moxa Asia-Pacific:Tel: +886-2-8919-1230 Fax: +886-2-8919-1231Table of ContentsChapter 1Introduction..................................................................................................1-1 Overview..................................................................................................................................1-2Package Checklist....................................................................................................................1-2Product Features......................................................................................................................1-3Product Hardware Specifications.............................................................................................1-3Hardware Block Diagram........................................................................................................1-6 W311............................................................................................................................1-6W321............................................................................................................................1-6W341............................................................................................................................1-7 Chapter 2Hardware Introduction.................................................................................2-1 Appearance..............................................................................................................................2-2 W311............................................................................................................................2-2W321............................................................................................................................2-2W341............................................................................................................................2-3 Dimensions..............................................................................................................................2-4 W311............................................................................................................................2-4W321............................................................................................................................2-5W341............................................................................................................................2-6 LED Indicators.........................................................................................................................2-7Reset Button.............................................................................................................................2-7Real Time Clock......................................................................................................................2-8 Chapter 3Hardware Connection Description.............................................................3-1 Installing the W311/321/341....................................................................................................3-2Wiring Requirements...............................................................................................................3-3 Connecting the Power...................................................................................................3-4Grounding the Unit.......................................................................................................3-4 Connecting Data Transmission Cables....................................................................................3-4 Connecting to the Network...........................................................................................3-4Connecting to the WLAN.............................................................................................3-5Connecting to a Serial Device......................................................................................3-5Serial Console Port.......................................................................................................3-5 SD Slot.....................................................................................................................................3-6USB (W341 only)....................................................................................................................3-8Relay Output (W341 only).......................................................................................................3-9 Appendix A Regulatory Approval Statement................................................................A-11Introduction The W311/321/341 series is a line of wireless RISC-based embedded computers that features802.11a/b/g WLAN, RS-232/422/485 serial ports, and an Ethernet port in a small, rugged chassis. In addition, all models feature an SD slot, and the W341 features two USB 2.0 hosts and one relayoutput channel.Your W311/321/341 series embedded computer is ideal for diverse, machine-to-machine embedded applications. It enables wireless operation for traditionally wired networks and serial devices. The W311/321/341 series not only provides transparent data transfers, but also numeric computing, protocol conversion, data processing and even data encryption. You will find it easierto build embedded systems for distributed peer-to-peer communication, turn wired devices into wireless devices, and introduce higher mobility and more intelligence to your system. In this chapter, you will learn about the capabilities of this embedded computer.This chapter covers the following topics:OverviewPackage ChecklistProduct FeaturesProduct Hardware SpecificationsHardware Block Diagram¾W311¾W321¾W341OverviewThe W311/321/341 Series wireless embedded computer is designed around the Moxa ART ARM932-bit RISC processor. Unlike the X86 CPU, which uses a CISC design, the Moxa ART ARM9uses RISC architecture and modern semiconductor technology to provide a powerful computingengine without generating significant heat. The processor also integrates UART and LANfunctions to provide exceptional communication performance, but without the bus bandwidthlimitations associated with general ARM-based communication products.On-board NOR Flash ROM and SDRAM provides ample storage capacity, and for select models,the SD slot gives applications extra room to expand. The built-in WLAN function supports the802.11a/b/g standard, providing transmission security with WEP, WPA and WPA2. The backupLAN port not only provides an alternative solution for networking but also supports Ethernetclients, allowing any network device to plug in and connect to the WLAN. The built-inRS-232/422/485 serial ports support a wide range of serial devices, making this platform suitablefor data acquisition and protocol conversion applications.The Linux-based operating system comes pre-installed and ready to run, providing an openplatform for software development. Software written for desktop PCs can easily be ported toW311/321/341 Series embedded computers by using a common complier, so little time is spentmodifying existing software code. In addition, the operating system, device drivers, anduser-developed software can all be stored in the built-in flash memory.Package ChecklistThe W311/321/341 Series includes the following models:W311-LXA small, RISC-based, ready-to-run, wireless embedded computer with WLAN, one serial port,Ethernet, SD slot, and Linux OSW321-LXA small, RISC-based, ready-to-run, wireless embedded computer with WLAN, two serial ports,Ethernet, SD slot, and Linux OSW341-LXA RISC-based, ready-to-run, wireless embedded computer with WLAN, four serial ports, Ethernet,SD slot, USB port, relay output, and Linux OSEach model is shipped with the following items:y 1 W311/321/341 embedded computery Wall mounting kit (W341 only)y Quick Installation Guidey Document & Software CDy Ethernet Cable: RJ45 to RJ45 cross-over cable, 100 cmy CBL-4PINDB9F-100: 4-pin header to DB9 female console port cable, 100 cmy WLAN Antennay Universal Power Adaptory Product Warranty StatementOptional Accessoriesy35 mm DIN-rail mounting kit (DK-35A)NOTE: Notify your sales representative if any of the above items are missing or damaged.1-2Product FeaturesW311/321/341 Series computers have the following features:y Moxa ART 32-bit ARM9 industrial communication processory32 MB on-board RAM (64 MB for W341)y16 MB built-in flash memoryy802.11a/b/g Wireless LANy WEP, WPA and WPA2 encryptiony Infrastructure mode and Ad-Hoc modey RS-232/422/485 serial ports with software selectable interfacey Baudrates between 50 and 921.6 Kbps; supports non-standard baudratesy10/100M Ethernet for backup networkingy SD card slot for storage expansiony Withstands 5G continuous vibration and 50G shocky LED indicators for status, serial transmission, and wireless signal strengthy Ready-to-run Linux platformy Installation on DIN-rail or wally Fanless design for increased ruggednessProduct Hardware SpecificationsSystemCPU Moxa ART ARM9 32-bit RISC CPU, 192 MHzDRAM W311: 32 MB W321: 32 MB W341: 64 MBFlash W311: 16 MB W321: 16 MB W341: 16 MBStorage Expansion W311: SD slot x 1 W321: SD slot × 1 W341: SD slot × 1USB W341: USB 2.0 host × 2Relay Output Form C, SPDT × 1Normal switching: 2A @ 30 VDCmax.Capacity:60WSwitching power: 220 VDC max.max.2ASwitchingvoltage:Switch current: 4 ms @ 20°COperation time: 100 Mohm max.Initial contact resistance:Console Port RS-232 × 1 (TxD, RxD, GND), 4-pin header output, “115200, n, 8, 1”Button Reset button × 1, supports “Reset to Factory Default”Others RTC, buzzer, Watchdog TimerOS Built-in Embedded Linux with MMU support, based on Linux Kemel2.61-3WLAN CommunicationStandard Compliance 802.11a/b/gRadio Frequency Type DSSS, CCK, OFDMMedia Access Protocol Carrier Sense Multiple Access with Collision Avoidance (CSMA/CA) Modulation 802.11a/g: OFDM (64-QAM, 16-QAM, QPSK, BPSK) 802.11b: DSSS(DBPSK, DQPSK, CCK)Transmission Power (Typical) 5.15 to 5.35 GHz: 15 dBm @6 Mbps; 12 dBm @54 Mbps5.725 to 5.825 GHz: 15 dBm @6 Mbps; 12 dBm @54 Mbps USA: 2.412 to 2.462 GHz (IEEE802.11g): 17 dBm @6 Mbps;15 dBm @54Mbps EU: 2.412 to 2.472 GHzUSA: 2.412 to 2.462 GHz (IEEE802.11b): 18 dBm@ 1 to 11 MbpsReceiver Sensitivity (Typical) 5.15 to 5.35 GHz: 6 Mbps @ -90 dBm; 54 Mbps @ -72 dBm 5.47 to 5.725 GHz: 6 Mbps @ -90 dBm; 54 Mbps @ -72 dBm 5.725 to 5.825 GHz: 6 Mbps @ -89 dBm; 54 Mbps @ -72 dBm USA: 2.412 to 2.462 GHz (IEEE802.11g): 6 Mbps @ -90 dBm;54 Mbps @ -73 dBm EU: 2.412 to 2.472 GHzUSA: 2.412 to 2.462 GHz (IEEE802.11b): 11 Mbps @ -87 dBm;1 Mbps @ -94 dBm EU: 2.412 to 2.472 GHzTransmission Rate 54 Mbps with auto fallback(54, 48, 36, 24, 18, 12, 11, 9, 6, 5.5, 2, 1 Mbps)802.11b supported rates: 1, 2, 5.5, 11 Mbps802.11a/g supported rates: 6, 9, 12, 18, 24, 36, 48, 54 Mbps Transmission Distance 100 meters at 11 Mbps (with no obstructions)Security WEP64-bit/128-bit,WPA, WPA2 data encryption Antenna Connector Reverse SMAAntenna External 2 dBi dipole antennaWLAN Mode Infrastructure, Ad-HocNetwork CommunicationLAN 10/100 Mbps RJ45 × 1, auto-sensingProtection 1.5 KV built-in magnetic isolation protectionSerial CommunicationSerial Port W311: RS-232/422/485 DB9 male × 1W321: RS-232/422/485 DB9 male × 2W341: RS-232/422/485 DB9 male × 4Protection 15 KV built-in ESD protection for all signalsData bits 5, 6, 7, 8Stop bits 1, 1.5, 2Parity None, Even, Odd, Space, MarkFlow Control RTS/CTS, XON/XOFF, RS-485 ADDC™Speed 50 bps to 921.6 Kbps; supports non-standard baudrates1-4LEDsSystem Ready, SD activityWLAN Enable,signalstrengthLAN 10 M/Link, 100 M/Link (RJ45 connector)Serial TxD,RxDPower RequirementsPower Input 12 to 24 VDC (W311 and W321); 12 to 48 VDC (W341)Power Consumption W311: 400 mA @ 12 VDCW321: 400 mA @ 12 VDCW341: 600 mA @ 12 VDC with no USB devices attached1.2A @ 12 VDC with USB devices on each port at max spec500 mA @ 5 VDCMechanicalDimension (W × D × H) (without wall mount ear or antenna) W311: 77 × 111 × 26 mmW321: 77 × 111 × 26 mmW341: 150 × 100 × 38 mmAntenna 110mmConstruction Material W311: aluminum, 1 mmW321: aluminum, 1 mmW341: aluminum, 1 mm / SECC, 1 mm for rear panel Mounting DIN-rail,wallEnvironmentalOperating Temperature -10 to 60°C (14 to 140°F), 5 to 95% RHStorage Temperature -20 to 80°C (-4 to 176°F), 5 to 95% RHAnti-Vibration 5 g rms @ IEC-68-2-34, random wave, 5-500 Hz, 1hr/axis Anti-Shock 50 g @ IEC-68-2-27, half sine wave, 11 msRegulatory ApprovalsEMC FCC, CE (Class A)Safety TUV,UL,cULOthers RoHS,CRoHS,WEEEWarranty 5 years1-5Hardware Block DiagramW311RS-232/422/485RS-232 W3211-6W3411-72Hardware Introduction The W311/321/341 series hardware is compact, well-designed, and built rugged for industrial applications. LED indicators help you monitor the performance and identify trouble spots. Multiple ports allow the connection of different devices for wireless operation. With the reliable and stable hardware platform that is provided, you may devote your attention to the developmentof your application. In this chapter, learn the basics about the embedded computer hardware and its different parts.This chapter covers the following topics:Appearance¾W311¾W321¾W341Dimensions¾W311¾W321¾W341LED IndicatorsReset ButtonReal Time ClockAppearanceW311(RS-232/422/485)W3212-2W341Top ViewFront View12 toSerial Port 1 to 4(RS-232/422/485)Bottom View2-3Dimensions W311(1.02 in)2-4(1.02 in)W3212-5W3412-6LED IndicatorsPlease note that the W311 does not include an SD slot, so it will not have an SD LED. LED Name LED Color LED FunctionGreen Power is on and functioning normallyReady OffPower is off or there is another power error Green SD card is detected SDOffNo SD card is detected ON: WLAN is readyGreen Blinking:Conflict with WLAN IP or no response fromDHCP serverWLANOff WLAN is not ready or function errorGreenNumber of glowing LEDs indicates signal strength 5: Excellent 4: Very good3: Good 2: Fair 1: BadSignal StrengthOff No signal or WLAN connection failed Orange 10 Mbps Ethernet link Green 100 Mbps Ethernet link LAN Off Disconnected or short circuit Green Serial ports P1-P4 transmitting data TxD P1-P4 Off Serial ports P1-P4 not transmitting data Yellow Serial ports P1-P4 receiving data RxD P1-P4Off Serial ports P1-P4 not receiving dataReset ButtonHold the reset button down for 5 seconds to load the factory default configuration. After loadingthe factory defaults, the system will reboot automatically. We recommend that you use thisfunction only if the software is not working properly. To reset the Linux system software, always use the software reboot command (“reboot”) to protect the integrity of data. The reset button is NOT designed as a hard reboot for the embedded computer.2-7Real Time ClockThe embedded computer’s real-time clock is powered by a lithium battery. We stronglyrecommend that you NOT replace the lithium battery on your own. If the battery needs to bechanged, please contact the Moxa RMA service team.2-83 Hardware Connection Description W311/321/341 Series wireless embedded computers are equipped for multiple types of connections. WLAN, Ethernet, and multiple serial interfaces are built into every model, including a serial console port for monitoring of bootup messages. Select models also include an SD slot for storage expansion, USB ports for additional device and storage options, and relay output connections. With the open-source Linux kernel, you are free to develop custom applications for remote, wireless operation of your device. In this chapter, learn how to connect the embedded computer to the network and to various devices.This chapter covers the following topics:Installing the W311/321/341Wiring Requirements¾Connecting the Power¾Grounding the UnitConnecting Data Transmission Cables¾Connecting to the Network¾Connecting to the WLAN¾Connecting to a Serial Device¾Serial Console PortSD SlotUSB (W341 only)Relay Output (W341 only)W311/321/341 Hardware User’s Manual Hardware Connection Description Installing the W311/321/341Wall or Cabinet MountingThe W311/321 embedded computers have built-in “ears” for attaching the Array embedded computers to a wall or the inside of a cabinet. We suggest using twoscrews per ear to attach the W311/321to a wall or cabinet. The heads of the screwsshould be less than 6.0 mm in diameter, and the shafts should be less than 3.5 mmin diameter, as shown by the figure at the right.For the W341, it comes with two metal attachment plates for attaching the embedded computer toa wall or the inside of a cabinet. First, use two screws per bracket to attach the brackets to the rearof the W341. Next, use two screws per bracket to attach the W341 to a wall or cabinet.DIN-Rail MountingDIN-rail attachments can be purchased separately to attach the product to a DIN-rail. Whensnapping the attachments to the DIN-rail, make sure that the stiff metal springs are at the top.Wiring RequirementsThis section describes how to connect serial devices to the embedded computer.You should heed the following common safety precautions before proceeding with the installationof any electronic device:y Use separate paths to route wiring for power and devices. If power wiring and device wiring paths must cross, make sure the wires are perpendicular at the intersection point.NOTE: Do not run signal or communication wiring and power wiring in the same wire conduit.To avoid interference, wires with different signal characteristics should be routed separately.y Use the type of signal transmitted through a wire to determine which wires should be kept separate. The rule of thumb is that wiring that shares similar electrical characteristics can bebundled together.y Keep input wiring and output wiring separate.y It is advisable to label the wiring to all devices in the system.3-3Connecting the PowerConnect the “live-wire” end of the 12-48 VDC power adapter to the embedded computer’sterminal block. When power is properly supplied, the “Ready” LED will glow a solid green after a25 to 30 second delay.Grounding the UnitGrounding and wire routing help limit the effects of noise due to electromagnetic interference(EMI). Before connecting any devices, run a ground wire from the ground screw to the groundingsurface.Connecting Data Transmission CablesThis section describes how to connect cables for the network, serial devices, and serial COMterminal.Connecting to the NetworkPlug your network cable into the embedded computer’s Ethernet port. The other end of the cableshould be plugged into your Ethernet network. When the cable is properly connected, the LEDs onthe embedded computer’s Ethernet port will glow to indicate a valid connection.The 10/100 Mbps Ethernet LAN port uses 8-pin RJ45 connectors. The following diagram showsthe pinouts for these ports.The LED indicator on the right glows a solid green color when the cable is properly connected to a 100 Mbps Ethernet network. The LED will flash on and off when Ethernet packets are being transmitted or received.The LED indicator on the left glows a solid orange color when the cable is properly connected to a 10 Mbps Ethernet network. The LED will flash on and off when Ethernet packets are being transmitted or received. Pin Signal1 ETx+2 ETx-3 ERx+4 ---5 ---6 ERx-7 ---8 --- 813-4Connecting to the WLANThe wireless embedded computer is WLAN ready and includes an 802.11 a/b/g WLAN module. Itsupports WEP, WPA and WPA2 data encryption. To verify WLAN operation, first configure yourWLAN settings on the embedded computer using the serial console or a wired network connection.Please refer to the operating system user’s manual for further detail.Connecting to a Serial DeviceYour serial device can plug into the embedded computer’s serial port using a serial cable. Serialports P1 to P4 have male DB9 connectors and can be configured for RS-232, RS-422, or RS-485communication through software. The pin assignments are shown in the following table:DB9 Male Port RS-232/422/485 PinoutsPin RS-232RS-422RS-485(4-wire)RS-485(2-wire)1 DCDTxDA(-)TxDA(-) ---2 RxDTxDB(+)TxDB(+) ---3 TxDRxDB(+)RxDB(+)DataB(+)4 DTRRxDA(-)RxDA(-)DataA(-)5 GND GND GND GND6 DSR --- --- ---7 RTS --- --- ---8 CTS --- --- --- Serial Console PortThe serial console port is a 4-pin pin-header RS-232 port. It is designed for serial consoleterminals, which are useful for viewing boot-up messages.Serial Console Port & Pinouts Serial Console Cable4321Pin Signal1 TxD2 RxD3 NC4 GND3-5SD SlotThe W311/321/341 provide an SD slot for storage expansion. Moxa provides an SD flash disk forplug & play expansion that allows users to plug in a Secure Digital (SD) memory card compliantwith the SD 1.0 standard for up to 1 GB of additional memory space, or a Secure Digital HighCapacity (SDHC) memory card compliant with the SD 2.0 standard for up to 16 GB of additionalmemory space. The following steps show you how to install SD card into the W311/321/341.W311/321The SD slot is located on the right side of the W311/321 enclosure. To install an SD card, youmust first remove the SD slot’s protective cover to access the slot, and then plug the SD carddirectly into the slot.The SD card will be mounted at /mnt/sd. Detailed installation instructions are shown below:Step 1: Use a screwdriver to remove the screws holding the SD slot’s outer cover.Step 2: After removing the cover, insert the SD memory card as shown.3-6W341The SD slot is located on the top panel of the W341. To install an SD card, you must first remove the SD slot’s protective cover to access the slot, and then plug the SD card directly into the slot. The SD card will be mounted at /mnt/sd. Detailed installation instructions are shown below: Step 1: Use a screwdriver to remove the screws holding the SD slot’s outer cover, and then remove the cover.3-7Step 2:Insert the SD memory card as shown.NOTE: To remove the SD card from the slot, press the SD card in slightly with your finger, and then remove your finger to cause the card to spring out partially. You may now grasp the top of the card with two fingers and pull it out.Before removing the SD card, remember to type /sync to ensure that your data has been written.USB (W341 only)The W341 includes two USB 2.0 hosts. These hosts can be used for an external flash disk or hard drive in order to store large amounts of data.USB 2.0 Ports3-8Relay Output (W341 only)The W341 includes a relay output channel. There is a 3-pin terminal block for the relay output connection, with pinouts as shown in the figure.RELAYON M O C CN3-9ARegulatory Approval StatementThis device complies with part 15 of the FCC Rules. Operation is subject to the following two conditions: (1) This device may not cause harmful m e istance of 20 cm hannel MSS operations.e party responsible for ould void the user authority to operate the equipment.ice, rovide reasonable protection n ,ures: interference, and (2) this device must accept any interference received, including interference that may cause undesired operation.plies with FCC radiation exposure limits set forth for an uncontrolledquipment should be installed and operated with a minimum d This equipment co environment. This away from the radiator or your body.With the 5.15-5.25 GHz band, U-NII devices will be restricted to indoor operations to reduce any potential for harmful interference to co-c Warning:Changes or modifications to this unit not expressly approved by th compliance c This product has been tested and complies with the specifications for a Class B digital dev pursuant to Part 15 of the FCC Rules. These limits are designed to p against harmful interference in a residential installation. This equipment generates, uses, and ca radiate radio frequency energy and, if not installed and used according to the instructions, may cause harmful interference to radio communications. However, there is no guarantee that interference will not occur in a particular installation. If this equipment does cause harmfulinterference to radio or television reception, which is found by turning the equipment off and on the user is encouraged to try to correct the interference by one or more of the following meas Reorient or relocate the receiving antenna Increase the separation between the equipment or devices Connect the equipment to an outlet other than the receiver's Consult a dealer or an experienced radio/TV technician for assistance。
CY28341资料
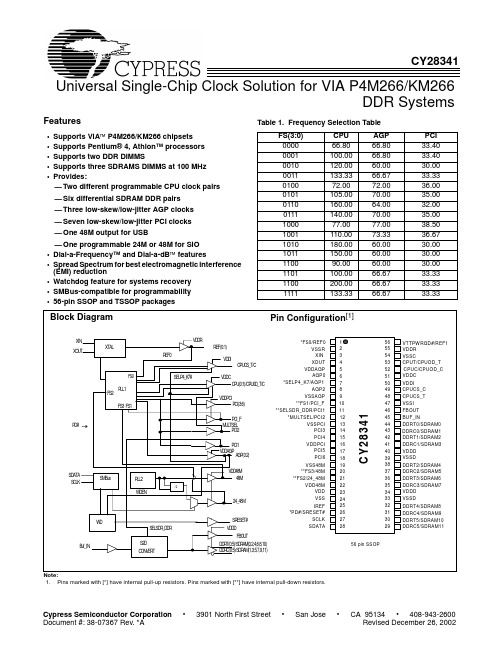
Cypress Semiconductor Corporation Document #: 38-07367 Rev. *A
•
3901 North First Street
•
San Jose
•
CA 95134 • 408-943-2600 Revised December 26, 2002
C Y 283 41
VDDAG P
I/O Power-on Bidirectional Input/Output. At power-up, SELP4_K7 is the input. PU When the power supply voltage crosses the input threshold voltage, SELP4_K7 state is latched and this pin becomes AGP1 clock output. SELP4_K7 = 1, P4 mode. SELP4_K7 = 0, K7 mode. I/O Power-on Bidirectional Input/Output. At power-up, MULTSEL is the input. PU When the power supply voltage crosses the input threshold voltage, MULTSEL state is latched and this pin becomes PCI2 clock output. MULTSEL = 0, Ioh is 4 x IREFMULTSEL = 1, Ioh is 6 x IREF. O 3.3V CPU Clock outputs. This pin is programmable through strapping pin7, SELP4_K7. If SELP4_K7 = 1, this pin is configured as the CPUT Clock Output. If SELP4_K7 = 0, this pin is configured as the CPUOD_T Open Drain Clock Output. See Table 1. 3.3V CPU Clock outputs. This pin is programmable through strapping pin7, SELP4_K7. If SELP4_K7 = 1, this pin is configured as the CPUC Clock Output. If SELP4_K7 = 0, this pin is configured as the CPUOD_C Open Drain Clock Output. See Table 1. 2.5V CPU Clock Outputs for Chipset. See Table 1. PCI Clock Outputs. Are synchronous to CPU clocks. See Table 1.