第三章《机械和超紧紧密加工第三章》
西工大机械设计第三章PPT

机械零件材料的疲劳特性除用s-N曲线表示外,还可用等寿命曲线来 描述。该曲线表达了不同应力比时疲劳极限的特性。
在工程应用中,常将等寿命曲线用直线来近似替代。
详细介绍
用A'G'C折线表示零件材料的极限应力线图是其中一种近似方法。 A‘G’直线的方程为
CG‘直线的方程为
s-1=sa'+jssm'
机械零件的疲劳强度
三、单向不稳定变应力时的疲劳强度计算
不稳定变应力
非规律性 规律性
用统计方法进行疲劳强度计算
机械零件的 疲劳强度计 算3
按损伤累积假说进行疲劳强度计算
规律性不稳定变应力
若应力每循环一次都对材料的破坏起相同的作用,则应力 s1 每循环一次 对材料的损伤率即为1/N1,而循环了n1次的s1对材料的损伤率即为n1/N1。如此 类推,循环了n2次的s2对材料的损伤率即为n2/N2,…… 当损伤率达到100%时,材料即发生疲劳破坏,故对应于极限状况有: n n1 n 2 3 1 详细分析 N 1 N 2 N3
详细介绍
s 1e
机械零件的疲劳强度
二、单向稳定变应力时的疲劳强度计算
机械零件的疲劳强度计算2
进行零件疲劳强度计算时,首先根据零件危险截面上的 smax 及 smin确定 平均应力sm与应力幅sa,然后,在极限应力线图的坐标中标示出相应工作应 力点M或N。 相应的疲劳极限应力应是极限应力曲线 上的某一个点所代表的应力 (s m ,s a ) 。 计算安全系数及疲劳强度条件为
s m ss sa
jσ为试件受循环弯曲应力时的材料
常数,其值由试验及下式决定钢,jσ≈0.1~0.2,对于合金钢,jσ≈0.2~0.3。
最新机械优化设计第3章精编版

2020年机械优化设计第3章精编版教案首页课程名称机械设计学任课教师李玉柱第三章机械产品的功能原理设计计划学时 3教学目的和要求:1.使学生了解机械产品的功能原理设计工作特点和工作内容;2.弄清楚功能原理的基本类型;3.基本掌握各种类型功能原理的求解思路;4.了解创造性思维活动的四大特性,初步具备一定的创造能力。
重点:功能原理的基本类型和各种类型功能原理的求解思路,尤其是工艺功能的求解思路。
难点:工艺功能的求解思路。
思考题:1.产品更新换代的三个途径是什么?举例说明。
2.各种类型功能原理的求解思路是什么?3.根据不同类型的功能原理的求解思路,分别举出2-3个例子。
4.创造性思维活动的特性有哪些?请试提出一些有创意的产品。
第三章机械产品的功能原理设计【教材自然节在课时中的分配】:第一、二节和第三、第四节的一部分作为1课时;第三、四节的一部分和第五节作为1课时;第六、七、八节作为1课时。
首先复习几个概念:1、设计的目的满足人类不断增长的物质、文化需求。
2、我们的责任能提出创新构思,并能尽快地将其转化为有竞争力的产品。
3、影响产品竞争力的三个关键设计环节:功能原理设计、实用化设计、商品化设计功能原理设计就是针对产品的主要功能提出一些原理性的构思。
功能原理新颖性实用化设计的核心是使产品具有优良的“性能”,从实用的角度使产品“好用”。
技术性能先进性商品化设计是产品进入市场前的精心打扮。
就是要使产品入眼、“迷人”。
从本章开始,我们的教学活动就围绕着“怎样才能设计出具有市场竞争力的产品”这一中心议题展开。
今天,我们讲第一个关键设计环节:机械产品的功能原理设计第一节基本概念1、功能指某一机器所具有的转化能量、运动或其它物理量的特征。
(见教材第30页)它与人们常用的“功用”、“用途”、“性能”、“能力”等概念既有联系又有区别。
以电动机为例:(P30)功能是产品的核心和本质。
“顾客购买的不是产品本身,而是产品的所具有的功能”,人们使用的也正是产品的功能。
机械设计-习题集答案
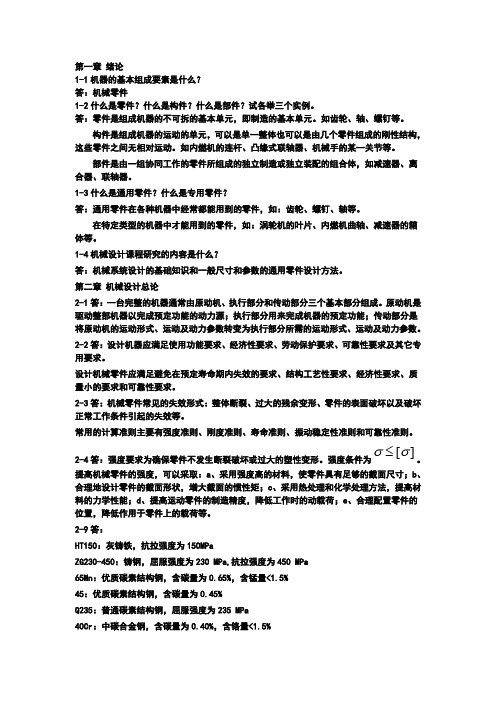
第一章绪论1-1机器的基本组成要素是什么?答:机械零件1-2什么是零件?什么是构件?什么是部件?试各举三个实例。
答:零件是组成机器的不可拆的基本单元,即制造的基本单元。
如齿轮、轴、螺钉等。
构件是组成机器的运动的单元,可以是单一整体也可以是由几个零件组成的刚性结构,这些零件之间无相对运动。
如内燃机的连杆、凸缘式联轴器、机械手的某一关节等。
部件是由一组协同工作的零件所组成的独立制造或独立装配的组合体,如减速器、离合器、联轴器。
1-3什么是通用零件?什么是专用零件?答:通用零件在各种机器中经常都能用到的零件,如:齿轮、螺钉、轴等。
在特定类型的机器中才能用到的零件,如:涡轮机的叶片、内燃机曲轴、减速器的箱体等。
1-4机械设计课程研究的内容是什么?答:机械系统设计的基础知识和一般尺寸和参数的通用零件设计方法。
第二章机械设计总论2-1答:一台完整的机器通常由原动机、执行部分和传动部分三个基本部分组成。
原动机是驱动整部机器以完成预定功能的动力源;执行部分用来完成机器的预定功能;传动部分是将原动机的运动形式、运动及动力参数转变为执行部分所需的运动形式、运动及动力参数。
2-2答:设计机器应满足使用功能要求、经济性要求、劳动保护要求、可靠性要求及其它专用要求。
设计机械零件应满足避免在预定寿命期内失效的要求、结构工艺性要求、经济性要求、质量小的要求和可靠性要求。
2-3答:机械零件常见的失效形式:整体断裂、过大的残余变形、零件的表面破坏以及破坏正常工作条件引起的失效等。
常用的计算准则主要有强度准则、刚度准则、寿命准则、振动稳定性准则和可靠性准则。
2-4答:强度要求为确保零件不发生断裂破坏或过大的塑性变形。
强度条件为[]σσ≤。
提高机械零件的强度,可以采取:a、采用强度高的材料,使零件具有足够的截面尺寸;b、合理地设计零件的截面形状,增大截面的惯性矩;c、采用热处理和化学处理方法,提高材料的力学性能;d、提高运动零件的制造精度,降低工作时的动载荷;e、合理配置零件的位置,降低作用于零件上的载荷等。
机械厂安全文明生产管理制度(三篇)

机械厂安全文明生产管理制度一、目的和依据为加强机械厂安全生产管理,保障员工身心健康,维护正常生产秩序,创建良好的工作环境,提高生产效益,根据《中华人民共和国安全生产法》及相关法律法规、标准以及公司内部管理制度,制定本制度。
二、适用范围本制度适用于机械厂所有工作人员、来访人员及其他相关方。
三、安全责任1. 机械厂负责人要以安全生产为首要任务,制定安全生产方针和目标,组织实施安全生产工作。
2. 各部门负责人要切实履行安全生产责任,落实本制度,并制定相应的安全生产工作计划,组织实施并定期检查、评估。
3. 所有员工要认真学习掌握安全操作规程和流程,严禁违章操作和违规行为,积极参与安全生产活动,提出改进建议并及时汇报安全隐患。
四、生产场所管理1. 生产车间必须保持整洁、通风良好,地面、通道等应保持平整无障碍。
2. 生产设备要定期检修和维护,确保正常运转。
3. 严禁在生产车间吸烟、乱丢乱放、打闹、吵闹等行为,严禁饮酒、饮食、使用手机等与工作无关的行为。
五、作业人员管理1. 所有作业人员必须参加安全教育和培训,持证上岗,掌握相应的安全操作规程。
2. 作业人员必须穿戴个人防护装备,保证个人安全。
3. 作业人员严禁在疲劳、酒后、药后作业,确保工作状态良好。
六、应急管理1. 各部门要建立健全应急管理机制,配备必要的应急设备和器材,组织定期演练。
2. 发生事故、灾害等情况时,要立即启动应急预案,组织人员撤离到安全地点,并报告上级领导和相关部门。
七、安全隐患排查和整改1. 安全隐患排查要定期进行,发现隐患要立即整改,并制定整改措施和时限。
2. 有关部门要对整改情况进行跟踪督促,确保整改措施得到落实。
八、安全检查和奖惩措施1. 安全检查要进行定期的自查和外部检查,对发现的问题要及时整改。
2. 对于遵守安全规程的人员,要进行表扬和奖励;对于违章操作和违规行为的人员,要进行批评教育和纪律处分。
九、安全宣传和教育1. 机械厂要定期组织安全宣传活动,提高员工的安全意识和应急能力。
机械原理第3版课件第三章

v
生无限值惯性力,并由此对凸轮产
生冲击
a
+∞
—— 刚性冲击
-∞
s = c0 c1 v = ds dt = c1 回程运动方程: a = dv dt = 0
边界条件
运动始点:=0, s=h 运动终点: = ,s=0
s = h (1 ) h v = ω a = 0 Nhomakorabeaf
从动件在运动起始、中点 和终止点存在柔性冲击 适用于中速轻载场合
f
O
f/2
4h2/f2
c)五次多项式运动规律 表达式为
v = ds / dt = C1 2C2 3C3 2 4C4 3 5C5 4 a = dv / dt = 2C2 2 6C3 2 12C4 2 2 20C5 2 3 s = C0 C1 C2 2 C3 3 C4 4 C5 5
推程边界条件
在始点处:=0, s1=0, v1=0, a1=0; 在终点处: = Φ s2=h, v2=0, a2=0; 解得待定系数为
C0=0,C1=0,C2=0,C3=10h/Φ 3,C4=-15/ Φ4,C5=6h/ Φ5
位移方程式为
S=10hφ 3/ Φ3-15hφ4/Φ4+6hφ5/Φ5
第二节
凸轮机构基本运动参数设计
一、凸轮工作转角的确定
二、从动件运动规律设计
一、凸轮工作转角的确定
s
*从动件在远停处对应 的转角s——远停角。
h
0
0
120º
s
180º
300º
360º
120º
精密和超精密加工技术(第三章)

精密加工技术- 精密加工技术-LYD
3.1 加工设备的精化
1.蜕化性加工(母性加工)原则: 1.蜕化性加工(母性加工)原则: 蜕化性加工
精度 1um 滚齿机分度误差 加工母机(机床) 加工母机(机床)
2um
工件
齿轮的分度误差= 齿轮的分度误差=机 床分度误差+ 床分度误差+刀具误 工件安装偏心+ 差+工件安装偏心+ 其它随机误差
•
创造性加工—— 创造性加工 工 工件 件
蜕化法
间 接 法
加工 的机床 精化 —— 的加工精 加工 精 件 • 创造性加工—— 创造性加工
工件
直接法
精化
的机床
工 精 件 精 加工
精 的机床 化 加工 ——
创造性加工原则
精密加工技术- 精密加工技术-LYD
3.1 加工设备的精化
获得高精度零件的两种加工途径: 获得高精度零件的两种加工途径:
2.影响最小切削深度的因素 2.影响最小切பைடு நூலகம்深度的因素
1. 刀具刃口半径ρ 2. 工艺系统的刚性
精密加工技术- 精密加工技术-LYD
3.2 微量切除原理
3.常用切削刀具的 3.常用切削刀具的 ρ
刀具材料 碳素工具钢 高速钢 硬质合金 陶瓷刀具 天然金刚石刀具 玻璃刀具 可以刃磨到的
ρ (um)
使用时的
花岗岩的吸振能力、稳定性和热胀系数均优于钢铁材料, 花岗岩的吸振能力、稳定性和热胀系数均优于钢铁材料,高/ 超精密机床的床身、导轨等基础部件多采用此石材制作。 超精密机床的床身、导轨等基础部件多采用此石材制作。
瑞士( 公司)制造的人造花岗岩,性能比天然花岗岩还好。 瑞士(Stude公司)制造的人造花岗岩,性能比天然花岗岩还好。
机械设备安全培训(三篇)
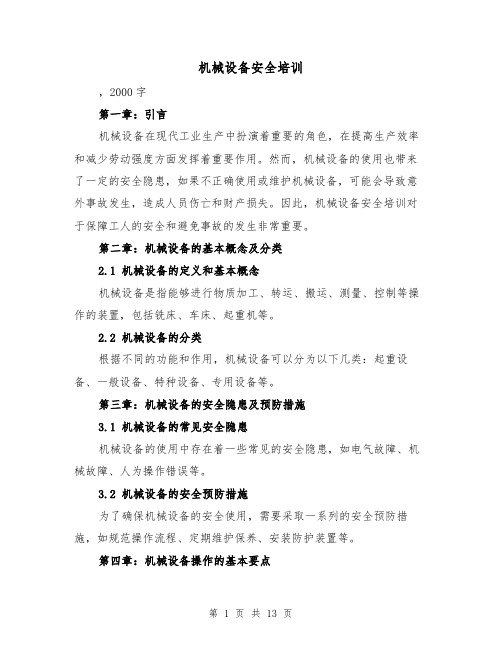
机械设备安全培训,2000字第一章:引言机械设备在现代工业生产中扮演着重要的角色,在提高生产效率和减少劳动强度方面发挥着重要作用。
然而,机械设备的使用也带来了一定的安全隐患,如果不正确使用或维护机械设备,可能会导致意外事故发生,造成人员伤亡和财产损失。
因此,机械设备安全培训对于保障工人的安全和避免事故的发生非常重要。
第二章:机械设备的基本概念及分类2.1 机械设备的定义和基本概念机械设备是指能够进行物质加工、转运、搬运、测量、控制等操作的装置,包括铣床、车床、起重机等。
2.2 机械设备的分类根据不同的功能和作用,机械设备可以分为以下几类:起重设备、一般设备、特种设备、专用设备等。
第三章:机械设备的安全隐患及预防措施3.1 机械设备的常见安全隐患机械设备的使用中存在着一些常见的安全隐患,如电气故障、机械故障、人为操作错误等。
3.2 机械设备的安全预防措施为了确保机械设备的安全使用,需要采取一系列的安全预防措施,如规范操作流程、定期维护保养、安装防护装置等。
第四章:机械设备操作的基本要点4.1 机械设备操作的基本原则机械设备操作需要遵循一些基本原则,如严格按照操作规程执行、确保操作人员的安全、定期检查设备的工作状态等。
4.2 机械设备操作的基本要点机械设备操作需要掌握一些基本要点,如启动和停止设备的方法、正常操作流程、设备故障的处理等。
第五章:机械设备的维护保养5.1 机械设备的定期检查定期检查机械设备的工作状态,防止设备发生故障或出现安全隐患。
5.2 机械设备的维护保养定期对机械设备进行维护保养,保证设备正常工作,并延长设备的使用寿命。
第六章:机械设备事故的处理流程6.1 机械设备事故发生后的处理步骤一旦发生机械设备事故,需要立即采取应急措施,并及时报告有关部门。
6.2 机械设备事故的调查和处理对机械设备事故进行调查和处理,找出事故原因,并采取相应的措施,防止类似事故再次发生。
第七章:机械设备安全培训的意义和方法7.1 机械设备安全培训的意义机械设备安全培训可以提高工人的安全意识,降低事故的发生概率,并提高工人的操作技能。
机械设计第三章(西北工业大学出版社)(第八版)汇编

机械电子工程学院
[例1] 发动机连杆大头螺钉工作最大拉力Pmax =58.3kN, 最小拉力Pmin =55.8kN ,螺纹小径为 d=11.5mm,试求 a 、m 和 r。
解:
max
Pmax 458300 561MPa 2 A 0.0115
Pmin 455800 min 537 .2MPa 2 A 0.0115
t
非对称循环 -1< r <1 max min m
a
2 max min
2
机械电子工程学院
o
t
2. 变应力的特性参数及类型
脉动循环变应力举例 齿轮的齿面接触应力 滚动轴承内圈、外圈和滚动 体上一点 FNi σH FNi σH
主动 被动 主动 被动
t
o
o
t
有载荷 无载荷
1
机械电子工程学院
t为轴的工作时间
1. 变应力的产生
转轴外表面一点
MR sin t A Iz
y A
RA
压
z
t yA
o
t
拉
机械电子工程学院
1. 变应力的产生
齿廓上一点
齿廓进入啮合到脱离啮合的过程中,表面上任意一 点的接触力是变应力。
t
机械电子工程学院
1. 变应力的产生
载荷做周期性 变化
3. 疲劳破坏的特征
循环应力多次反复作用下产生;
经过一定的载荷循环次数才会发生;
无宏观的、明显的塑性变形迹象;
循环应力远小于材料的静强度极限; 对材料的组成、零件的形状、尺寸、表面状态、 使用条件非常敏感。
机械电子工程学院
不同外部载荷作用下疲劳断面特征
机械制造装备设计北科大第三章

件
刚度,降低了噪声和振动;有较宽的调速 范围;有较大的驱动功率和转矩;便于组 织专业化生产。它广泛应用于精密机床、设 计ຫໍສະໝຸດ 高速加工中心和数控车床中。
高速内圆磨床电主轴图3
返回本节
下一页
返回主页
退出
3.1.3 主轴部件结构设计
第
三
1、主轴部件的支承数目
章
典
多数机床的主轴采用前、后两个支承。
型
为提高刚度和抗振性,有的机床采用三个
计
主轴前端悬伸量a的确定
主轴主要支承间跨距L的确定
返回本节
下一页
返回主页
退出
3.1.3 主轴部件结构设计
第
三
5、主轴
章
主轴的构造和形状主要取决于主轴上所安装的刀具、夹具、传动件、轴承 等零件的类型、数 量、位置和安装定位方法等。
主轴的材料和热处理是普通机床主轴可选用中碳钢(如45钢),调质处理
典 型
第三章 典型部件设计
第一节 主轴部件设计 第二节 支承件设计 第三节 导轨设计 第四节 机床刀架和自动换刀装置设计
退出
第 三 章 典 型 部 件 设 计
上一页
返
回
下一页
主
页
3.1 主轴部件设计
退出
一、主轴部件应满足的基本要求
第 三
章
二、主轴部件的传动方式
典
型
三、主轴部件结构设计
部 件
设
四、主轴滚动轴承
典
合理布置传动件在主轴上的轴向位置,可 以改善主轴的受力情况,减少主轴变形, 提高主轴的抗振性。主轴上传动件轴向布
型 部
置时,应尽量靠近前支承,有多个传动件
件
机械加工表面质量第三章
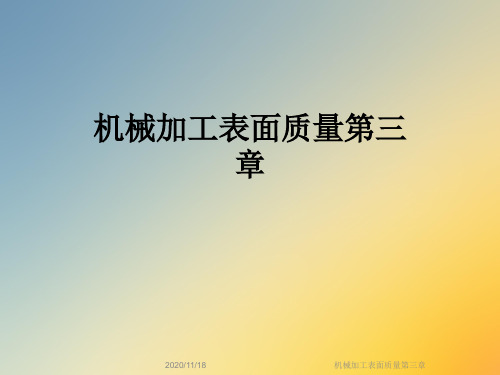
(4)光磨次数 通常磨削时,开始用较大切深提高生
产率,最后用小切深或无进给磨削(光磨),提高表面 粗糙度。
机械加工表面质量第三章
2、磨削时影响表面粗糙度的因素
其他影响 (1)砂轮硬度和工件材料 良好的“自励性”即磨
初期磨损
正常磨损
急剧磨损
实际接触面积只占名义接触 磨损缓慢,紧密接触的两个表面金属
面积的一小部分,实际接触 零件的正 分子间产生较大的亲和力,
部分的压强增大,破坏了润 常工作阶 超过了润滑油膜存在的临
滑油膜而形成局部的干摩擦, 段
界值,造成润滑条件恶化 ,
使其挤裂、破碎、切断等作
磨损加剧。
用增强,磨损增大。
机械加工表面质量第三章
一、概述
1.表面粗糙度与波度
(1)表面粗糙度:表面的微观几何形状误差; (2)波度:介于宏观几何形状误差与表面粗糙度之间的周期性几何形状误差。
L/H>1000称为宏观几何形状误差; L/H = 50~1000,称为波纹度; L/H<50,称为微观几何形状误差,亦称表面粗糙度。
粒磨钝后能及时脱落,露出新的磨粒,能磨出光滑的 表面,且能防止磨削烧伤。工件材料韧性越好,塑性 变形越大,则表面粗糙度越大。
(2)砂轮材料 可分为氧化物、碳化物和高硬磨料。
一般刚类零件用刚玉砂轮磨削,铸铁、硬质合金用碳 化物砂轮磨削,金刚石砂轮可获得极小的表面粗糙度, 但成本较高。
机械加工表面质量第三章
表面完整性
随着科学技术的发展,对产品的使用性能要求越来越高,一 些重要零件需在高温、高压、高速的条件下工作,表面层的任何 缺陷直接影响零件的工作性能,因此在研究表面质量的领域中提 出了“表面完整性”的概念,主要有:
《机械制造基础》第三章课后题及答案(题号可能不搭配)
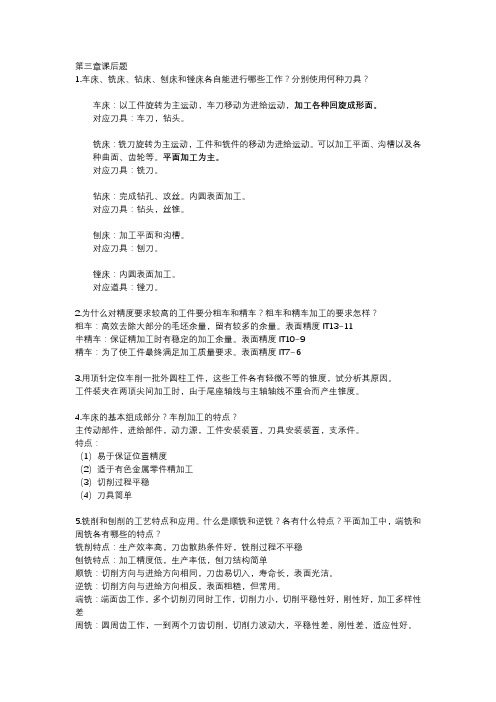
第三章课后题1.车床、铣床、钻床、刨床和镗床各自能进行哪些工作?分别使用何种刀具?车床:以工件旋转为主运动,车刀移动为进给运动,加工各种回旋成形面。
对应刀具:车刀,钻头。
铣床:铣刀旋转为主运动,工件和铣件的移动为进给运动。
可以加工平面、沟槽以及各种曲面、齿轮等。
平面加工为主。
对应刀具:铣刀。
钻床:完成钻孔、攻丝。
内圆表面加工。
对应刀具:钻头,丝锥。
刨床:加工平面和沟槽。
对应刀具:刨刀。
镗床:内圆表面加工。
对应道具:镗刀。
2.为什么对精度要求较高的工件要分粗车和精车?粗车和精车加工的要求怎样?粗车:高效去除大部分的毛坯余量,留有较多的余量。
表面精度IT13~11半精车:保证精加工时有稳定的加工余量。
表面精度IT10~9精车:为了使工件最终满足加工质量要求。
表面精度IT7~63.用顶针定位车削一批外圆柱工件,这些工件各有轻微不等的锥度,试分析其原因。
工件装夹在两顶尖间加工时,由于尾座轴线与主轴轴线不重合而产生锥度。
4.车床的基本组成部分?车削加工的特点?主传动部件,进给部件,动力源,工件安装装置,刀具安装装置,支承件。
特点:(1)易于保证位置精度(2)适于有色金属零件精加工(3)切削过程平稳(4)刀具简单5.铣削和刨削的工艺特点和应用。
什么是顺铣和逆铣?各有什么特点?平面加工中,端铣和周铣各有哪些的特点?铣削特点:生产效率高,刀齿散热条件好,铣削过程不平稳刨铣特点:加工精度低,生产率低,刨刀结构简单顺铣:切削方向与进给方向相同,刀齿易切入,寿命长,表面光洁。
逆铣:切削方向与进给方向相反,表面粗糙,但常用。
端铣:端面齿工作,多个切削刃同时工作,切削力小,切削平稳性好,刚性好,加工多样性差周铣:圆周齿工作,一到两个刀齿切削,切削力波动大,平稳性差,刚性差,适应性好。
6.为何内圆表面加工比外圆表面加工生产率低成本高?工件尺寸:所用刀具尺寸受到被加工孔本身的尺寸限制加工精度,表面粗糙度:孔内排屑、散热、冷却、润滑条件较差。
机械制造(第2版)第三章课后习题解答

3-27 试分析 JCS —018型加工中心自动换刀装置的优缺点。 答:(p125)刀具库可安装 16把刀具,自动换刀装置采用换刀机械手, 换刀动作是:
o
特点是动作简单、耗时较短;但有可能抓不紧,造成滑脱。
3-28 滚切直齿圆柱齿轮时需要哪些基本运动? 答:(p131-132 )主运动:滚刀的旋转运动 nc,进给运动:工件的旋转运动
3-3 机床有哪些基本组成部分?试分析其主要功用。 答:(p70-71)基本组成部分动力源、运动执行机构、传动机构、控制系统和伺服系 统、支承系统。 动力源为机床运动提供动力;运动执行机构产生主运动和进给运动;传动机构建立 从动力源到执行机构之间的联系;控制和伺服系统发出指令控制机床运动;支承系统为 上述部分提供安装的基础和支承结构。
外圆加工方法:车削、磨削、研磨、超精加工;孔的加工方法:钻孔、扩孔、铰孔、 镗孔、磨孔、研磨、珩磨、拉削等;孔的加工方法较多。
3-22 什么是逆铣?什么是顺铣?试分析逆铣和顺铣、对称铣和不对称铣的工艺特 征。
答:(p105-106)
3-23 试分析比较铣平面、刨平面、车平面的工艺特征和应用范围。
答:可以归纳如下:
6
答:(p143-145)总结归纳如下表:
加工原理 工艺特点 应用范围
立体光刻法
分层实体制造法
激光选区烧结法
强光照射光敏树脂,逐 点扫描固化,叠加成形
激光切割箔材,热压粘 接, 叠加成形
激光烧结粉末材料,熔 解粘接,叠加成形
误差可控 0.1%, 材料利 用率高
误差可控 0.25-0.5, 材 料利用率较低
2
3-12 试分析外圆表面车拉削方法的工作原理和工艺特点。 答:(p86)将车削和拉削组合在一起的加工方法。加工时,工件高速旋转,拉刀慢 速旋转拉削运动。 工艺特点:多齿拉刀,刀具寿命长,生产效率高,柔性较好,但拉刀制造难度大。 适于大批量生产加工结构复杂、精度要求较高的零件。
第三章 二战以后机械的发展

第三阶段:基于电子技术和计算机技术的自动化
随着 20 世纪后半叶以来控制理论、电子技术和传感 器技术的发展,特别是随着计算机在工业上的应用,自 动化的程度更高了。
现代机器的自动化和早期的自动化已不可同日而语。
Mechanical
—— 机械
Electronic
电子
——
Mechatronics
正确译文:机械电子学
120 km/h
2.5 倍
300 km/h
高速铁路车辆的发展 ◆ 1964年,日本建成东京到大阪的高速铁路——新干
线。速度快(230 km/h)、安全正点、能耗低(仅及汽
车的 1/5)、无污染、运量大、成本低,举世瞩目。 ◆ 80 年代,法国开通高速铁路,车速达 300 km/h, 试验列车的速度曾达到 574 km/h。
在建规模最大: 2020年前,再建设 16000公里
运营时速最高
232 km
243 km
277 km
350 km
德国
日本
法国
中国
部分国家高速铁路平均运营时速
正向世界延伸 美国通用电气公司与中国南车股份有限公司签订合作 框架协议,将共同投资,在美国本土合作制造高速列车。
伸向印度支那半岛的高铁(昆明-仰光)也在筹划之
5、汽车工业
▲ 汽车的发展已有 120 多年的历史。 二战以后,世 界汽车工业进入了飞速发展的时期。 ▲ 世界汽车产量的攀升 ▲ 目前全世界的 客货车拥有总量超
7761万 6653万
过 8 亿 辆。
2000万 1000万 1950
4000万
1963
1977
2005 2010
▲ 汽车工业是综合产业,是国民经济的一个支柱产业。
机制知识点第三章

第三章机械加工与装配工艺规程制定1.机械制造工艺过程:直接变原材料为零件的过程与产品装配的过程。
2.机械加工工艺过程:用机械加工的方法(包括钳工的手工操作),按规定的顺序把毛坯(包括轧制材料)变成零件的全过程。
3.工序:工序是工艺过程的基本单元。
是指一个工人(或者一组工人)在一个工作地点(一般是指一台机床)对一个工件(对多轴机床来说是对多个工件)所连续完成的那一部分工艺过程。
4.安装:一个工序有时在零件的几次装夹下完成,这时,在零件每装夹一次下所完成的那部分工作成为一次安装。
5.工位:在多轴机床上或者在带有转位夹具的机床上加工时,工件在机床上所占有的一个位置上所完成的那部分工作成为一个工位。
6.工步:工步是构成工序的基本单元。
是指在加工表面、切削刀具、和切削用量都不变的情况下所连续完成的那一部分工作。
7.走刀:有些工步由于余量太大,或由于其他原因,需要同一刀具在相同转速和进给量下(切削深度可能不同)对同一表面进行多次切削,这时,刀具在加工表面上对工件每一次切削所完成的那一部分工作成为一次走刀。
8.加工工艺规程:工程技术人员结合实际制定出一个最佳的加工工艺过程,而且用一个文件加以规定,将合理的工艺过程和操作方法,按照一定的格式写成文件,用来指导生产,这个文件就叫做加工工艺规程。
9.单件小批生产:工厂产品品种不固定,每一品种的产品数量很少,工厂大多数工作地点的加工对象经常地改变,如重型机械厂,修船造船厂。
10.中批生产:工厂产品类型基本固定,数量少品种多,需要周期性轮换生产,工厂的大多数工作地点的加工对象周期性地变换,如各种机械制造厂。
11.大批大量生产:工厂的产品品种已经固定,每种产品数量很多,工厂内大多数工作地点的加工对象固定不变,如汽车厂,拖拉机厂等。
12.装夹:在机床上进行加工时,必须先把工件安装在准确的加工位置上,并将其可靠地固定,以确保工件在加工过程中不发生位置的变化,才能保证加工出的表面达到对定的加工要求,工件从定位到夹紧的整个过程叫做装夹。
机械工程导论翻译第三章
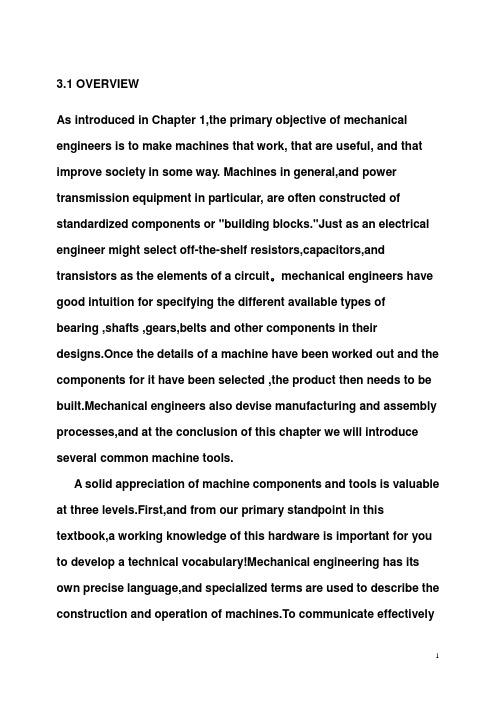
3.1 OVERVIEWAs introduced in Chapter 1,the primary objective of mechanical engineers is to make machines that work, that are useful, and that improve society in some way. Machines in general,and power transmission equipment in particular, are often constructed of standardized components or "building blocks."Just as an electrical engineer might select off-the-shelf resistors,capacitors,and transistors as the elements of a circuit。
mechanical engineers have good intuition for specifying the different available types ofbearing ,shafts ,gears,belts and other components in theirdesigns.Once the details of a machine have been worked out and the components for it have been selected ,the product then needs to be built.Mechanical engineers also devise manufacturing and assembly processes,and at the conclusion of this chapter we will introduce several common machine tools.A solid appreciation of machine components and tools is valuable at three levels.First,and from our primary standpoint in this textbook,a working knowledge of this hardware is important for you to develop a technical vocabulary!Mechanical engineering has its own precise language,and specialized terms are used to describe the construction and operation of machines.To communicate effectivelywith other engineers,you will need to learn,adopt,and share that language.Second,having such a background is necessary to select the poper component for an application and to specify the appropriate machine tool for a production process.Of course,it is not possible to list and describe every machine and component that embodies mechanical engineering principles,and that is not our intention in this chapter.However,by examining just a few machine components and tools,you will develop a growing appreciation for practical machinery issues.Finally,this chapter is a good place for you to begin the journey of understanding the inner workings of mechanical hardware.It's intellectually healthy for you to be curious about machines,wonder how they were made,dissect them,and think about they could have been made differently or better .3.1概述正如第1章介绍,机械工程师的首要目标是制造机器,制造能够工作的、有用的并以某种方式,改善社会的机器。
机械制造工艺学第三章

工序号 1 2
3
4 5
工序名称
工步
备料
1车大头端面
车
2车大外圆
3大端倒角
调头车
1车小头端面 2车小端外圆
3小端倒角
铣键槽
1粗铣键槽 2精铣键槽
(或同时对几个)工件所连续完成的那一部分工艺过程。 注意:在同一工序内完成的工作必须是连续的。只要工人、工作地点、工作对
象之一发生变化或工作不是连续的,那么,工作内容就应变成另一工序。
d1 d2
l L
工序2和3可合成一道工序
2、安装:
安装是工序中装夹工件所完成的那部分工艺过程。在一道工序中可以进
行多次安装。如上图…;在平面磨床上,磨车床的刀架座需装夹4次。
注意:从减少安装误差和装夹工件的时间来考虑,应尽量减少安装次数。
3、工位
在同一工序中,为了减少因多次安装带来的误差和时间损失往往采用 转位工作台或者转位夹具。
工位:是在工件的一次安装中,工件相对于机床刀具或机床固定部分所 占住一个每一个位置。
4、工步 在一道工序中可能需加工多个表面而只用一把刀具,也可能加工
2、如果必须保证某加工表面余量均匀就应该选择表面为粗基准
3、选择粗基准时务求定位准确夹紧可靠,选作粗 基准的平面要求平整光洁,有足够大的尺寸, 不允许有锻造飞边,铸造浇冒口,更不能用分 型面作粗基准。
4、粗基准应尽量避免重复使用,在同一尺寸方向 上只允许使用一次,以后加工都要选已经加工 过的表面作为精基准。
具体方法: 一般总是根据零件的结构特点、主要表面的技术要求(包括从工艺角 度提出来的)和工厂的具体条件,首先选择它的最终加工方法,然后再逐一选择前 道工序的加工方法,选择主要表面的加工方法以后,再选择次要表面的加工方法。
机械制造装备设计第三章习题答案(关慧贞)

机械制造装备设计第三章习题答案(关慧贞)第三章典型部件设计1.主轴部件应满足那些基本要求?答:主轴部件应满足的基本要求有旋转精度、刚度、抗振性、温升热变形和精度保持性等。
主轴的旋转精度是指装配后,在无载荷、低速转动条件下,在安装工件或刀具的主轴部位的径向和轴向跳动。
旋转精度取决于主轴、轴承、箱体孔等的制造、装配和调整精度。
主轴部件的刚度是指其在外加载荷作用下抵抗变形的能力,通常以主轴前端产生单位位移的弹性变形时,在位移方向上所施加的作用力来定义,主轴部件的刚度是综合刚度,它是主轴、轴承等刚度的综合反映。
主轴部件的抗振性是指抵抗受迫振动和自激振动的能力。
主轴部件的振动会直接影响工件的表面加工质量,刀具的使用寿命,产生噪声。
主轴部件的精度保持性是指长期地保持其原始制造精度的能力,必须提高其耐磨性。
2.主轴轴向定位方式有那几种?各有什麽特点?适用场合答:(1)前端配置两个方向的推力轴承都分布在前支撑处;特点:在前支撑处轴承较多,发热大,升温高;但主轴承受热后向后伸,不影响轴向精度;适用场合:用于轴向精度和刚度要求较高的高精度机床或数控机床。
(2)后端配置两个方向的推力轴承都布置在后支撑处;特点:发热小、温度低,主轴受热后向前伸长,影响轴向精度;适用范围:用于普通精度机床、立铣、多刀车床。
(3)两端配置两个方向的推力轴承分别布置在前后两个支撑处;特点:这类配置方案当主轴受热伸长后,影响轴承的轴向间隙,为避免松动,可用弹簧消除间隙和补偿热膨胀;适用范围:用于短主轴,如组合机床。
(4)中间配置两个方向的推力轴承配置在前支撑后侧;特点:此方案可减少主轴的悬伸量,使主轴热膨胀后向后伸长,但前支撑结构复杂,温升可能较高。
3.试述主轴静压轴承的工作原理答:主轴静压轴承一般都是使用液体静压轴承,液体静压轴承系统由一套专用供油系统、节流器和轴承三部分组成。
静压轴承由供油系统供给一定压力油,输进轴和轴承间隙中,利用油的静压压力支撑载荷、轴颈始终浮在压力油中。
机械设计第03章详解

公式推导
D E B
2.平均应力为常数:σm=C
当工作点是位于AOHG区域的M时,零件的疲劳强度条件为 推导见下页
当工作点是位于GCH区域的N时,零件的疲劳强度条件为
公式推导
3.最小应力为常数:σmin=C
P Q
若LM'与横坐标夹角为45° 对于LM'上任意一点
给定任意两个参数, 其它三个可算出
r = -1 对称循环应力 r = 0 脉动循环应力 r = 1 静应力
交变应力下,零件的主要损坏形式是疲劳断裂。
疲劳断裂过程: 1、零件表层产生微小裂纹 2、随着循环次数增加,微裂纹逐渐扩展 3、当剩余材料不足以承受载荷时,突然脆性断裂
微裂纹
扩展区
断裂区
s-N疲劳曲线(应力比r恒定,不同的σmax对应的循环次数N)
四、双向稳定变应力时的疲劳强度计算
机械零件的疲劳强度计算4
当零件上同时作用有同相位的稳定对称循环变应力σa 和τa时,由实验得出的极限应力关系式为:
切向应力幅
的极限值
法向应力幅 的极限值
2
2
a 1e
s a s 1e
1
零件受对称循环切应力 时的疲劳极限
零件受对称循环弯曲应 力时的疲劳极限
公式为圆的方程,由于应力都为正值,在第一象限。
抛光
未加工
零件的强化系数βq
对于扭转剪切,将前面公式中的σ 换成τ
φτ—试件受循环切应力时的材料常数 Kτ —剪切疲劳极限的综合影响系数
kτ﹣零件的有效应力集中系数 ετ﹣零件的尺寸及截面形状系数 βτ﹣零件的表面质量系数 βτ﹣零件的强化系数
- 1、下载文档前请自行甄别文档内容的完整性,平台不提供额外的编辑、内容补充、找答案等附加服务。
- 2、"仅部分预览"的文档,不可在线预览部分如存在完整性等问题,可反馈申请退款(可完整预览的文档不适用该条件!)。
- 3、如文档侵犯您的权益,请联系客服反馈,我们会尽快为您处理(人工客服工作时间:9:00-18:30)。
第4节 超精密磨削
二、超精密磨削机理
磨削加工过程
磨削加工是无数磨粒的连续磨削。加工的实质是工件被磨削的 表层,在无数磨粒瞬间的挤压,摩擦作用下产生变形,而后转为磨 屑,并形成光洁表面的过程。磨削过程可分为:三个阶段,砂轮表 面的磨粒与工件材料接触,发生弹性变形,磨粒继续切入工件(切 削深度增加),工件材料进入塑性阶段,材料晶粒发生滑移。塑性 变形不断增大,当力达到工件的强度极限时,被磨削层材料产生挤 裂,即进入切削阶段,最后被切离。当磨削切入量达到最大值后, 逐渐减少,最后到零,同时经历塑性区和弹性区。
2013-7-28
第3节 超硬磨料砂轮磨削
二、超硬磨料砂轮修整
整形 对砂轮进行微量切削,使砂 轮达到所要求的几何形状精 度,并使磨料尖端细微破碎, 形成锋利的磨削刃。
修锐
去除磨粒间的结合剂,使磨 粒间有一定的容屑空间,并 使磨刃突出于结合剂之外, 形成切削刃。
2013-7-28
第3节 超硬磨料砂轮磨削
2013-7-28
第2节 精密磨削
五、磨削用量
砂轮速度 工作速度 一般在15~30m/s
一般在6~12m/min
一般为50~100mm/min或0.06~0.5mm/r
工件纵向进给量 横向进给量(吃刀量) 横向进给次数 光磨(无火花磨削)
2013-7-28
一般取0.6~2.5μm/单行程 一般约2~3次(单行程)
第1节 精密和超精密磨削概述
金刚石刀具主要是对铝、铜及其合金等 材料进行超精密切削,而对于黑色金属、 硬脆材料的精密与超精密加工,则主要是 应用精密和超精密磨料加工。所谓精密和 超精密磨料加工,就是利用细粒度的磨粒 和微粉对黑色金属、硬脆材料等进行加工, 以得到高加工精度和低表面粗糙度值。
2013-7-28
2013-7-28
第3节 超硬磨料砂轮磨削
三、超硬磨料砂轮磨床
超精密磨削对磨床的要求: 1)要求磨床的精度较高,砂轮主轴回转精度其径向 跳动应<0.01mm,端面圆跳动<0.005mm。 2)比普通磨床刚度提高50%左右。 3)进给系统精度高、进给速度均匀准确,纵向进给 速度最小可达0.3m/min,横向进给最小可达0.001~ 0.002mm/单行程。 4)各运动件和主轴回转部分、进给运动导轨部分有 可靠的密封。 5)有比较完善的磨削液处理系统。 6)采取相应的防振、隔振措施。
2013-7-28
第1节 精密和超精密磨削概述
二、精密和超精密砂轮磨料磨具
磨料及其选择
普通磨料
碳化物系 碳化硼 碳化硅
超硬磨料
金刚石 天然 人造
刚玉系
2013-7-28
立方氮化硼
第1节 精密和超精密磨削概述
二、精密和超精密砂轮磨料磨具
磨料粒度及其选择
多选用180#~240#普通 磨料、170/200~325/400 超硬磨料的磨粒和各种 粒度的微粉。
2013-7-28
第4节 超精密磨削
二、超精密磨削机理
磨削加工过程
单颗粒磨削
1)磨粒是一颗具有弹性支承(结合 剂)的和大负前角切削刃的弹性体。 2)磨粒切削刃的切入深度是从零开 始逐渐增加,到达最大值再逐渐减 少,最后到零。 3)磨粒磨削时在工件的接触过程中, 开始是弹性区,继而塑性区、切削区、 塑性区,最后是弹性区。 4)超精密磨削时有微切削作用、塑性 流动和弹性破坏作用,同时还有滑擦 作用。
粗粒度砂轮精细修整后,光磨次数采用5~8次 细粒度砂轮精细修整后,光磨次数采用10~25次。
第3节 超硬磨料砂轮磨削
一、超硬磨料砂轮磨削特点
1)可用来加工各种高硬度、高脆性金属材料和非金属材料, 如硬质合金、陶瓷、玻璃、半导体、石材等。立方氮化硼砂 轮磨削时,热稳定性好,化学惰性强,不易与铁素元素产生 亲和作用和化学反应,加工黑色金属时,有较高的耐磨性。 2)磨削能力强,耐磨性好,耐用度高,易于控制加工尺寸 及实现加工自动化。 3)磨削力小,磨削温度低,加工表面质量好,无烧伤、裂 纹和组织变化。 4)磨削效率高。 5)综合成本低。
磨削液的种类 和组成
2013-7-28
第3节 超硬磨料砂轮磨削
五、超硬磨料砂轮的平衡
静平衡 力矩平衡,用于窄砂轮的平衡,是在一个平面上的平衡。 (1)机外静平衡架上平衡 (2)机上动态平衡 (3)机外动态平衡 动平衡
力偶平衡,用于宽砂轮和多砂轮轴的平衡,是在一个有一 定长度的体上进行力偶平衡。 一般在动平衡机上进行。
第1节 精密和超精密磨削概述
一、精密和超精密加工分类
精密和超精 密磨料加工
固结磨 料加工
游离磨 料加工
固结磨具
涂覆磨具
精密研磨
精密抛光
精密砂 轮磨削
油石研磨
精密珩磨
精密超 精加工
砂带磨削
砂带研磨
2013-7-28
第1节 精密和超精密磨削概述
一、精密和超精密加工分类
固结磨料加工
精密和超精密砂轮磨削
二、超硬磨料砂轮修整
电火花修整法
电火花放电加工,适 用于各种金属结合剂 砂轮。若在结合剂中 加入石墨粉,可用于 树脂、陶瓷结合剂砂 轮。既可整形,又可 修锐。
2013-7-28
第3节 超硬磨料砂轮磨削
二、超硬磨料砂轮修整
超声波振动修整法
用受激振动的 簧片或超声波 振动头驱动的 幅板作为修整 器,并在砂轮 和修整器间放 入游离磨料撞 击砂轮的结合 剂,使超硬磨 粒突出结合剂。
2013-7-28
第3节 超硬磨料砂轮磨削
二、超硬磨料砂轮修整
喷射法
碳化硅和刚玉
2013-7-28
第3节 超硬磨料砂轮磨削
二、超硬磨料砂轮修整
电加工法 电解修整法
利用电化学个腐 蚀作用蚀除金属结合 剂,多用于金属结合 剂砂轮的修锐,非金 属结合剂砂轮无效。
2013-7-28
第3节 超硬磨料砂轮磨削
二滚轮法
双滚轮法
第3节 超硬磨料砂轮磨削
二、超硬磨料砂轮修整
滚压挤轧法
用碳化硅、刚玉、硬质合金或钢铁等制成修整轮, 与超硬磨料砂轮在一定压力下进行自由对滚,使 结合剂破裂形成容屑空间,并使超硬磨粒表面崩 碎形成微刃。加入碳化硅、刚玉等游离磨料,依 靠游离磨料挤轧作用进行修锐。
2013-7-28
第1节 精密和超精密磨削概述
三、精密和超精密涂覆磨具
涂覆磨具分类
涂 覆 磨 具 基 底 材 料
工 作 条 件
形 状
耐 水
干 磨
复 合
塑 料 膜
化 纤 布
棉 布
纸
盘 状
带 状
环 状
卷 状
页 状
2013-7-28
第1节 精密和超精密磨削概述
三、精密和超精密涂覆磨具
2013-7-28
将磨料粘合在一起,形成一定的形状,并有 一定的强度。 树脂结合剂、陶瓷结合剂和金属结合剂
结合剂及其选择
组织和浓度及其选择
普通磨具中磨料的含量用组织表示,超硬磨具中磨料的含 量用浓度表示。成形磨削、沟槽磨削、宽接触面平面磨削 选用高质量浓度;半精磨、精磨选用细粒度、中质量浓度; 高精度、低表面粗糙度值的精密磨削和超精密磨削选用细 2013-7-28 粒度、低质量浓度。
第3节 超硬磨料砂轮磨削
四、超硬磨料砂轮磨削工艺
磨削液
磨削液的作用
降低磨削温度,减少磨削力,改善磨削 表面质量,提高磨削效率和砂轮寿命。 润滑、冷却、清洗性能,尚有渗透性、 防锈性、防腐性、防火性、切削性和极 压性等
油性液:成分是矿物油,如机油、轻质 柴油、煤油,加入脂肪油和添加剂。 水溶性液:成分是水,如乳化液、无机 盐水溶液和化学合成液等。 金刚石砂轮磨削时常用油性液和水溶性 液,立方氮化硼砂轮磨削时用油性液。
精密和超精密砂带磨削
精密砂带磨削:砂带粒度W63~W28,加工
精度1μm,Ra0.025; 超精密砂带磨削:砂带粒度W28~W3,加工精 度0.1μm,Ra0.025~0.008μm。
2013-7-28
第1节 精密和超精密磨削概述
一、精密和超精密加工分类
游离磨料加工
磨料或微粉不是固结在一起, 而是成游离状态。 传统方法:研磨和抛光 新方法:磁性研磨、弹性发射 加工、液体动力抛光、液中研 抛、磁流体抛光、挤压研抛、 喷射加工等。
2013-7-28
第2节 精密磨削
三、精密磨削时砂轮的修整
砂轮修整是精密磨削的关键,有单粒金刚石修整、 金刚石粉末烧结型修整器修整和金刚石超声波修 整等。 砂轮的修整用量有修整导程、修整深度、修整次 数和光修次数。修整导程(纵向进给量)为10~ 15mm/min,修整深度为2.5μm/单行程,精修次 数2~3次,光修次数1次单行程。
Precision and ultraprecision machining
精密和超精密加工技术
姜春晓 2005年9月
2013-7-28
第3章 精密磨削和超精密磨削 3.1 精密和超精密磨削概述 3.2 精密磨削 3.3 超硬磨料砂轮磨削 3.4 超精密磨削 3.5 精密和超精密砂带磨削
2013-7-28
2013-7-28
第1节 精密和超精密磨削概述
三、精密和超精密涂覆磨具
涂覆方法
重力落砂法
涂覆法
2013-7-28
静电植砂法
第2节 精密磨削
一、精密磨削机理
(1)微刃的微切削作用 (2)微刃的等高切削作用 (3)微刃的滑挤、摩擦、抛光作用
2013-7-28
第2节 精密磨削
二、精密磨削砂轮选择
精密磨削使所用砂轮的选择以易产生和保持微刃 及其等高性为原则。 磨削钢件及铸铁件时,采用刚玉磨料较好,单晶 刚玉最好,白刚玉、铬刚玉应用最普遍。 砂轮的粒度可选择粗粒度和细粒度两类。 结合剂选择树脂较好,加入石墨填料加强摩擦抛 光作用。