12V190机体主轴孔同轴度超差分析及改进
发动机曲轴孔同轴度超差精度调整方法

发动机曲轴孔同轴度超差精度调整方法作者:王元臣艾金龙胡士国李波赵秀荣来源:《中国新技术新产品》2020年第10期摘要:该文介绍了柴油发动机曲轴孔7个单孔的同轴度超差调整的方法。
曲轴孔同轴度是整个发动机缸体生产线加工质量控制的重点,也是难点,其直接影响了发动机曲轴高速运转的的状态,同轴度不好会产生“曲轴抱死、声音噪声异响及抱轴”的故障。
该加工设备安装初期加工的同轴度极不稳定,设备厂家几乎每月都要调整,都没有彻底解决,咨询同类设备的其他厂家也没有很好的解决方法,所以长期以来一直是通过技术偏离到0.035 mm使用。
该文就是对该问题的精度调整,达到工艺要求,满足装配需求。
关键词:同轴度精度调整;机床加工;同轴化超差中图分类号:TH162; ; ; 文献标志码:A1 项目背景及总体思路发动机曲轴孔作为发动机缸体上的一个关键部位,对发动机整体性能具有重大的影响。
它的作用主要是支撑曲轴,传递从曲轴柄传来的转矩并通过凸缘输出,吸收气缸活塞运动过程中的轴向力和侧向力[1]。
为了尽可能地减小曲轴运转时的摩擦力并保证曲轴在发动机运转过程中的平稳性,要求7个单曲轴孔要在一条同轴线上,同轴度要求在0.02 mm内,而实际同轴度已超过0.035 mm,不能满足工艺及使用要求,造成发动机总成因曲轴跳动大出现“曲轴抱死、声音噪声异响及抱轴卡死”等故障问题[2],导致整台发动机出现报废的严重后果。
为了保证发动机的质量稳定性,确保曲轴孔同轴度控制在工艺要求尺寸以内,需要彻底调整解决同轴度超差的问题。
2 主要科技创新创新发明发动机缸体曲轴孔同轴度调整的方法,解决长孔系(超过1 000 mm)加工中同轴度超差调整的技术难题。
打破长孔系同轴精度调整长期以来依靠外部力量例如国外技术支持的技术制约。
创新使用调整工具,创新调整方法,减少调整人员的调整时间及劳动强度。
编制长孔系同轴度调整作业指导书,固化检测及调整步骤,对其他精度调整起到技术指导作用。
浅析内燃机车柴油机机体主轴承孔同轴度的检测方法
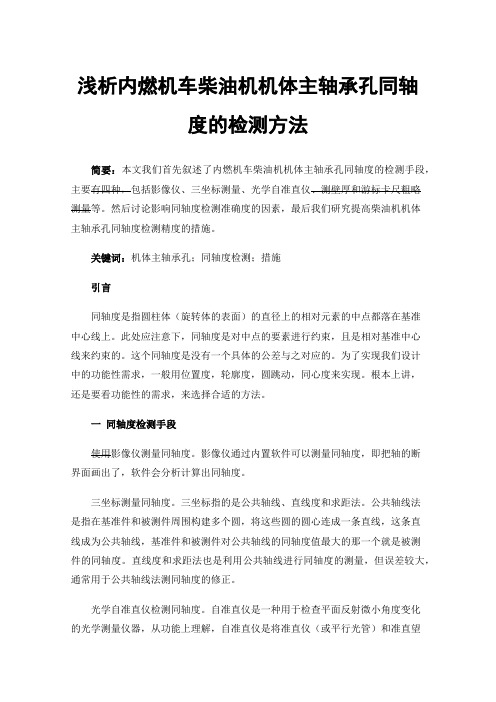
浅析内燃机车柴油机机体主轴承孔同轴度的检测方法简要:本文我们首先叙述了内燃机车柴油机机体主轴承孔同轴度的检测手段,主要有四种,包括影像仪、三坐标测量、光学自准直仪、测壁厚和游标卡尺粗略测量等。
然后讨论影响同轴度检测准确度的因素,最后我们研究提高柴油机机体主轴承孔同轴度检测精度的措施。
关键词:机体主轴承孔;同轴度检测;措施引言同轴度是指圆柱体(旋转体的表面)的直径上的相对元素的中点都落在基准中心线上。
此处应注意下,同轴度是对中点的要素进行约束,且是相对基准中心线来约束的。
这个同轴度是没有一个具体的公差与之对应的。
为了实现我们设计中的功能性需求,一般用位置度,轮廓度,圆跳动,同心度来实现。
根本上讲,还是要看功能性的需求,来选择合适的方法。
一同轴度检测手段使用影像仪测量同轴度。
影像仪通过内置软件可以测量同轴度,即把轴的断界面画出了,软件会分析计算出同轴度。
三坐标测量同轴度。
三坐标指的是公共轴线、直线度和求距法。
公共轴线法是指在基准件和被测件周围构建多个圆,将这些圆的圆心连成一条直线,这条直线成为公共轴线,基准件和被测件对公共轴线的同轴度值最大的那一个就是被测件的同轴度。
直线度和求距法也是利用公共轴线进行同轴度的测量,但误差较大,通常用于公共轴线法测同轴度的修正。
光学自准直仪检测同轴度。
自准直仪是一种用于检查平面反射微小角度变化的光学测量仪器,从功能上理解,自准直仪是将准直仪(或平行光管)和准直望远镜结合为一体的一台仪器。
自准直仪通常由光源、分划板、分光镜、物镜以及望远接收部分构成,光学自准直仪的望远接收部分由分划板和目镜组成,通过人眼观测结合机械测微装置完成测量,光电自准直仪的望远接收部分则由光电传感器完成接收和测量。
光源将位于物镜焦平面(物镜焦距=f)的分划板投射至无穷远(准直光出射),经过平面反光镜返回的准直光经物镜后再次成像于同样位于物镜焦平面(共焦系统)的光电传感器的探测面上,当反射镜发生了α角度的偏转后,返回的分划板在光电传感器上的像会产生的位移,通过精确测量出值,即可准确计算出平面反射镜的偏转角度,公式。
Z12V190BJ柴油机主轴承孔修复的探讨与实践

第2 卷第 2 8 期
20 0 8年 4月
江
西
冶
金
Vo . 1 28 , No. 2 Ap l i r 2 8 00
JANGXI I MET L AL URGY
文章编 号 :0 62 7 ( 0 8 0 -0 3 3 10 —7 7 2 0 ) 20 3 - 0
新余 钢 铁有 限责 任公 司铁 路运 输 主型 机车 为 内
燃 机车 。为 降低 机车 检修 成本 , 高机 车利用 率 , 提 新
钢 公 司充 分挖 掘 技术 人 员及 检 修 设 施 的潜 力 , 现 实 了 内燃机 车柴 油 机 大 修 不 出厂 。在 这 个 过 程 中 , 碰 到 了许 多技术 上 的难题 , 别是 柴 油机 大修后 , 特 品质
主轴承瓦修复工艺 。修复后 的柴油机 满足了使 用性能 。
关
键
词 : 内燃 机 车 ; 主轴承 孔 ; 变形 修 复 ; 主轴 承 瓦 ; 孔装 置工 艺 镗
文献 标识 码 : C
中 图分类 号 : U 6 . 1 2 2 1
D ic s i n a d a ia i n a o h e d t c o e s u so n Re lz to b utt e H a s o k H l
通过 对 多 台柴 油机 机 体 主轴 承 各 孔 尺 寸检 轴 承 孔 第 1 第 4 第 7 主 、 、
现过 主轴 承 瓦脱落 、 吸 器 冒蓝 烟 及异 常 敲击 声 等 呼
故障。
收 稿 日期 :0 71 - 2 0 —20 4
Re a rn fZ1 V1 0 J Dis l gn p ii g o 2 9 B ee En ie
提高柴油机机体主轴承孔同轴度检测准确度的措施

第47卷第3期Vol.47No.3铁道技术监督RAILWAY QUALITY CONTROL计量工作MEASUREMENT WORK提高柴油机机体主轴承孔同轴度检测准确度的措施李功岭(中国铁路呼和浩特铁路局集团有限公司大板机务段,内蒙古赤峰025150)摘要:简要阐述光学自准仪检测柴油机机体主轴承孔同轴度的原理,提出提高同轴度检测准确度的措施,包括提高数据采样准确度和数据处理准确度2个方面。
其中提高数据采样准确度包括测量仪器的检查校验、测量环境控制、测量操作控制3个方面,提髙数据处理准确度包括注意主轴承孔径在垂直方向的修正、重要计算参数检具桥跨距的作用、同轴度公差定义对计算结果的影响3个方面。
应用Excel电子表格软件编制柴油机机体主轴承孔同轴度检测数据计算处理记录表,实现测量数据计算处理的电子化,提高了柴油机机体主轴承孔同轴度检测数据计算处理的速度和可靠性。
关键词:柴油机;机体;主轴承孔;同轴度;测量;数据处理中图分类号:U262.11:TB922文献标识码:B文章编号:1006-9178(2019)03-0011-04Abstract:The article specifies the principle for an optical autocollimator to detect the coaxiality in a main bearing hole of a diesel engine block.It proposes the following measures to improve the coaxiality detection accuracy,including such two aspects as to improve the data sampling accuracy and data processing accuracy.Notably,the improvement of the data sampling accuracy also covers such three aspects as the inspection and verification of measuring instrument,the control of measuring environment and the control of measurement operation.The improvement of data processing accuracy also includes to pay atlention lo the correction of main bearing aperture in vertical direction,the role of key calculation parameters for gauge span and the influence of coaxiality tolerance definition on calculation results.Excel electronic form software is applied to prepare the record on main bearing hole coaxiality detection data calculation and processing for diesel engine blocks,which realizes the computerization of measured data calculation and processing,and improves the speed and reliability of main bearing hole coaxiality detect i o n data calculation and process for diesel engine blocks.Keywords:Diesel Engine;Block;Main Bearing Hole;Coaxiality;Measurement;Data Processing0引言作为柴油机机体主轴承孔形位公差的计量检测手段.柴油机机体主轴承孔同轴度检测是判定柴油机机体主轴承孔加丁.精度、变形程度和变形后修复结果的主要依据.在柴油机制造及检修中具冇重要作用目前,铁路各机务段在内燃机车柴油机检修时普遍采用具有较高准确度的光学II准仪检测柴油机机体主轴承孔同轴度经过多年检测实践发现,光学门准仪法在现场实际测量作业中存在2方面问 题:①测量数据准确度受测量环境和测量操作影响较大;②测量数据为角度偏差,并非直观的同轴度数值.需要将所测得的角度偏差经过计算处理收稿日期:2018-10-17作者简介:李功岭,I:程师方能得岀同轴度数值,涉及参数、数据较多.计算过程繁琐.容易导致计算结果出现错误.最终影响对柴油机机体主轴承孔同轴度变形的判定和主轴承孔修复质量的检验.进而导致检修后柴油机主轴瓦偏磨.严重的发生•轴瓦烧损、曲轴拉伤报废等恶性故障,造成较大的经济损失:因此.提高柴油机机体主轴承孔同轴度检测结果的准确度,对于铁路机务段部门的现场检修工作具有重要的现实意义,是亟待解决的问题1光学自准仪检测柴油机机体主轴承孔同轴度的原理在柴油机机体一端(输出端或自由端)主轴承孔外侧.固定光学自准仪及其专用支架.将带反光镜的检具桥置于被测主轴承孔内,光学自准仪可2019*1■3J1(总第389期)・简・计量工作提高柴油机机体主轴承孔同轴度检测准确度的措施测量自身发射的平行光束(主光轴)与检具桥反 射回光束的偏差角度。
轴孔类零件同轴度的检测与误差分析

轴孔类零件同轴度的检测与误差分析同轴度的检测直接影响着相关工业产品的质量和互换性。
针对轴孔类零件,主要探讨了其同轴度误差的检测方法,给出了检测的改进方法,并分析了引起测量误差的主要原因,为检测人员的检测操作提供指导。
标签:轴孔类零件;同轴度;检测;误差分析引言现代工业大批量和高效率的生产对产品质量以及互换性要求越来越高。
轴孔类零件作为工业产品中最为常见的一类,其形位公差检测的主要内容就是同轴度的检测,在已有检测方法的基础上加以改进,保证测量结果的真实和准确性,才能反应产品的真实状态从而保证产品的质量。
1 同轴度误差的检测轴孔类零件在实际生产中具有不同的结构形式,同轴度的要求在不同的使用场合也各有不同,所以相应的同轴度误差的检测方法也就不同。
1.1 轴类零件的同轴度误差检测对于轴类零件,测量时调整基准轴线和仪器的旋转轴线同轴,使仪器的旋转轴成为参考基准,这时测量所得被测轴线相对于参考基准的误差值就是该轴类零件的同轴度。
轴类零件同轴度的检测方法通常有:三坐标测量机测量法、圆度仪测量法、打表法(对径差法)测量。
下面主要介绍对径差法测量。
如图1所示装置,在测量以公共轴线为基准的同轴度误差时,平板面作为测量基准,由V形块模拟体现公共基准轴线。
首先放置被测零件要素的中截面在两个同等高度的V形块上,安装指示表,保证两个指示表和被测轮廓要素轴线铅垂面内的上下母线分别接触,一端调零后平行于基准线在平板上拉动测量架,使测量架从被测元素轮廓一端测到另一端,同时记录记录表读数Ma和Mb,那么这两个截面上的同轴度误差就是两记录表数值差值的绝对值f=|Ma-Mb|,再转动被测零件,按上述方法测量若干对截面上的同轴度误差值,选取其中最大的值作为最终该被测零件的同轴度误差。
1.2 孔类零件同轴度误差的检测随着科学技术的发展,三坐标测量机在几何量检测领域已经十分普及,与传统的测量方法相比,三坐标测量机测量同轴度的最大优点是利用建立工件坐标系,可以做到无须转动工件,无须专用芯轴或专用的支架,无须机械找准,只需用测头系统的探针对工件取点采样,利用测量软件快速输出测量结果。
12V190型柴油机修理方案

柴油机修理方案
一、检修内容:
1、机组进厂后、进行整机鉴定、解体前清洗、装框、煮洗、油洗、除漆、除碳、除垢(生铁件下烧咸池蒸气加温、铝合金件下金属清洗池蒸气加温)及二次清洗配件加工、零部件鉴定、配件采购、零部件修理、油洗连杆、曲轴,对新机体进行清沙处理,缸盖修理,泵滤修理,增压器修理,小件修理,散热器修理,水箱总成修理,对增压器总成、中冷器总成、机油冷却器总成、机油滤总成等进行大修理,对所有缸盖总成进行大修换件调整。
2、更换机组所有主轴瓦、连杆瓦、凸轮轴瓦及所有轴承件,更换所有缸套、活塞、活塞环,更换所有密封件,对曲轴、凸轮轴、连杆及连杆螺栓、活塞销进行探伤检查并对连杆进行弯曲度检查。
3、总装、单机试车;
4、配套、机组试车、整机喷漆、出厂;
二、其它事项:
1、送修方在提机时承修方必须提供该机的主要部件检修技术资料、检验报告和合格证。
2、大修过程中,以下大件报废另行收费:曲轴、凸轮轴、增压器总成、高压油泵总成、机油冷却器总成、中冷器总成、缸盖三只以上、连杆三根以上、水箱总成、机体等。
3、质保期:半年或1000小时二者以先到为准,在此期间,送修方在按规定的操作、维护、保养正确操作使用的情况下,机组发生
故障时,必须保持整机现状,并立即通知承修方,承修方在接到送修方通知后二十四小时内派出技术人员和现场服务人员到现场,双方共同检查分析,明确责任。
属承修方修理质量问题,则由承修方实行“三包”,如属送修方操作或保养原因造成的事故,所有费用由造成事故方全部负责。
Z12V190B柴油发动机涡轮增压系统改进分析
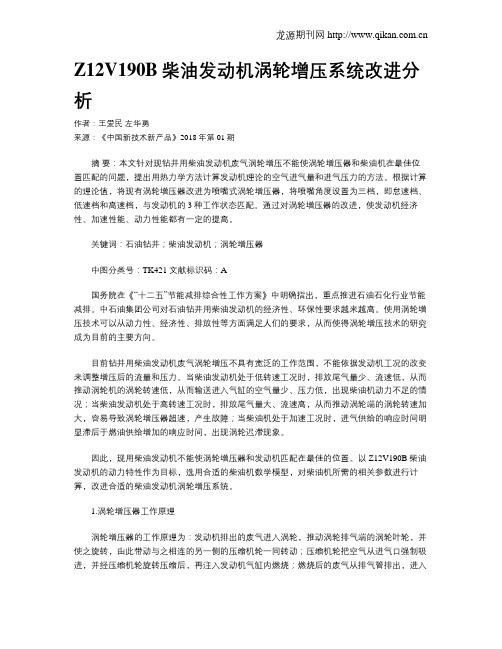
Z12V190B柴油发动机涡轮增压系统改进分析作者:王爱民左华勇来源:《中国新技术新产品》2018年第01期摘要:本文针对现钻井用柴油发动机废气涡轮增压不能使涡轮增压器和柴油机在最佳位置匹配的问题,提出用热力学方法计算发动机理论的空气进气量和进气压力的方法。
根据计算的理论值,将现有涡轮增压器改进为喷嘴式涡轮增压器,将喷嘴角度设置为三档,即怠速档、低速档和高速档,与发动机的3种工作状态匹配。
通过对涡轮增压器的改进,使发动机经济性、加速性能、动力性能都有一定的提高。
关键词:石油钻井;柴油发动机;涡轮增压器中图分类号:TK421 文献标识码:A国务院在《“十二五”节能减排综合性工作方案》中明确指出,重点推进石油石化行业节能减排。
中石油集团公司对石油钻井用柴油发动机的经济性、环保性要求越来越高。
使用涡轮增压技术可以从动力性、经济性、排放性等方面满足人们的要求,从而使得涡轮增压技术的研究成为目前的主要方向。
目前钻井用柴油发动机废气涡轮增压不具有宽泛的工作范围,不能依据发动机工况的改变来调整增压后的流量和压力。
当柴油发动机处于低转速工况时,排放尾气量少、流速低,从而推动涡轮机的涡轮转速低,从而输送进入气缸的空气量少、压力低,出现柴油机动力不足的情况;当柴油发动机处于高转速工况时,排放尾气量大、流速高,从而推动涡轮端的涡轮转速加大,容易导致涡轮增压器超速,产生故障;当柴油机处于加速工况时,进气供给的响应时间明显滞后于燃油供给增加的响应时间,出现涡轮迟滞现象。
因此,现用柴油发动机不能使涡轮增压器和发动机匹配在最佳的位置。
以Z12V190B柴油发动机的动力特性作为目标,选用合适的柴油机数学模型,对柴油机所需的相关参数进行计算,改进合适的柴油发动机涡轮增压系统。
1.涡轮增压器工作原理涡轮增压器的工作原理为:发动机排出的废气进入涡轮,推动涡轮排气端的涡轮叶轮,并使之旋转,由此带动与之相连的另一侧的压缩机轮一同转动;压缩机轮把空气从进气口强制吸进,并经压缩机轮旋转压缩后,再注入发动机气缸内燃烧;燃烧后的废气从排气管排出,进入涡轮,重复以上的动作。
浅析机械零件误差产生的原因及精度提高方法
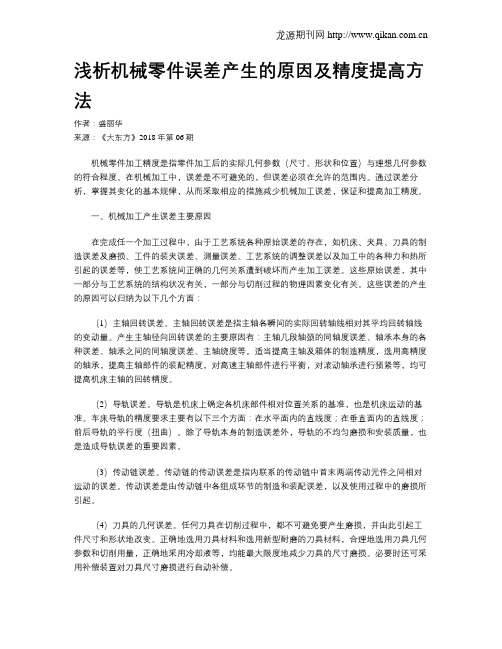
浅析机械零件误差产生的原因及精度提高方法作者:盛丽华来源:《大东方》2018年第06期机械零件加工精度是指零件加工后的实际几何参数(尺寸、形状和位置)与理想几何参数的符合程度。
在机械加工中,误差是不可避免的,但误差必须在允许的范围内。
通过误差分析,掌握其变化的基本规律,从而采取相应的措施减少机械加工误差,保证和提高加工精度。
一、机械加工产生误差主要原因在完成任一个加工过程中,由于工艺系统各种原始误差的存在,如机床、夹具、刀具的制造误差及磨损、工件的装夹误差、测量误差、工艺系统的调整误差以及加工中的各种力和热所引起的误差等,使工艺系统间正确的几何关系遭到破坏而产生加工误差。
这些原始误差,其中一部分与工艺系统的结构状况有关,一部分与切削过程的物理因素变化有关。
这些误差的产生的原因可以归纳为以下几个方面:(1)主轴回转误差。
主轴回转误差是指主轴各瞬间的实际回转轴线相对其平均回转轴线的变动量。
产生主轴径向回转误差的主要原因有:主轴几段轴颈的同轴度误差、轴承本身的各种误差、轴承之间的同轴度误差、主轴绕度等。
适当提高主轴及箱体的制造精度,选用高精度的轴承,提高主轴部件的装配精度,对高速主轴部件进行平衡,对滚动轴承进行预紧等,均可提高机床主轴的回转精度。
(2)导轨误差。
导轨是机床上确定各机床部件相对位置关系的基准,也是机床运动的基准。
车床导轨的精度要求主要有以下三个方面:在水平面内的直线度;在垂直面内的直线度;前后导轨的平行度(扭曲)。
除了导轨本身的制造误差外,导轨的不均匀磨损和安装质量,也是造成导轨误差的重要因素。
(3)传动链误差。
传动链的传动误差是指内联系的传动链中首末两端传动元件之间相对运动的误差。
传动误差是由传动链中各组成环节的制造和装配误差,以及使用过程中的磨损所引起。
(4)刀具的几何误差。
任何刀具在切削过程中,都不可避免要产生磨损,并由此引起工件尺寸和形状地改变。
正确地选用刀具材料和选用新型耐磨的刀具材料,合理地选用刀具几何参数和切削用量,正确地采用冷却液等,均能最大限度地减少刀具的尺寸磨损。
190 柴油机凸轮轴瓦座孔修复解读.doc

190 柴油机凸轮轴瓦座孔修复解读190 柴油机凸轮轴瓦座孔修复新钢运输部内燃机车全部配备了190 系列柴油机作为动力源。
其中柴油机凸轮轴轴瓦座孔是安装配气机构凸轮轴轴瓦座孔,座孔内轴瓦同其中高速旋转凸轮轴有相对磨擦,其中通过机油进行润滑,当磨擦付内润滑条件不会产生轴瓦粘结在凸轮轴上,从而产生轴瓦与座孔磨损。
在应用中相继有013、015、1048 等机车产生座孔磨损现象。
柴油机机体七万多元一台,因凸轮轴轴瓦座孔磨损而报损十分可惜,为此,我们对此进行修复攻关。
1 座孔磨损情况分析由图1 示意图及实际应用情况看,机体凸轮轴座孔磨损主要产生在第一位轴瓦座孔处,因为此处为主机油道末端,润滑条件最差,故易产生缺油造成轴瓦粘结在凸轮轴上,从而造成轴瓦同机体座孔相对磨损。
因此,修复工作主要在第一道轴瓦处。
修复工作主要是修补磨大座孔,使之恢复尺寸,保证同轴瓦配合尺寸及安装要求。
2 座孔修复方案确定2.1 190 柴油机凸轮轴座孔磨损有两种情况一是座孔磨损并不是很严重,磨损量在0.5mm 内。
故我们采用是用胶粘剂进行修复,用天山新材料公司1755 清洗剂进行清洗后,用粘结剂1680 进行锁固,从而保证轴瓦同座孔过盈量,该方法在013、015 机车修复中得到应用,效果较好。
二是座孔磨损较大,如1048 机车座孔磨损量达到在大多地方超过2mm,用胶粘剂不能效果,故只能进行其它方法,由于机体构造复杂,对孔进行堆焊加工会产生不可预测结构应力,产生变形等问题,故我们采用镗孔镶套方法来修复座孔磨损问题。
2.2 柴油机凸轮轴座孔须满足以下要求如图1 所示,柴油机机体上有7 个凸轮190 柴油机凸轮轴瓦座孔修复卢志刚裴盛晏晓彬(新余钢铁有限责任公司江西新余 338001)摘要: 本文重点是解决内燃机车柴油机凸轮轴轴瓦座孔非正常磨损。
通过对柴油机凸轮轴轴瓦座孔技术要求分析,自行设计了镗销及镶套修复方案,并制作了专用加工装置,从而较好地完成柴油机凸轮轴轴瓦座孔修复。
12V190柴油机轴瓦异常磨损原因分析

c.严 格操 作 规程 :起 动 前 预供 油 至要 求压 力 ; 停 车油 温 不 可太 高 ,应低 于 60℃ 以下 再停 车 ;避 免超速超负荷运行 ,保证运转时油温不高于 85℃。
= (0.000 9+,z/5 000 000)×d(n为 轴 的 转 速 ,r/min;d为轴 的直 径 ,为 160mm)。
a.装 配零 部件 清 洁度 不 达标 是新 机 试 车轴 瓦 异 常磨 损 的主要 原 因 。 因此 机 油滤 清 器壳 体 、机 油 泵 支架 、调压阀壳体内腔应确保无粘沙等颗粒 ,油管 等在超声波清洗机 中进行清洗 ,机体主油道 、曲轴 油道 的毛刺专门进行毛刺清理并增加清洗 。
表 1 曲轴主轴颈和机体瓦孑L尺寸随温度变化的试验数据 测量部位 材料 温度变化/℃ 测量尺寸变化量/mm
主 轴 颈 的 圆柱 度 不 好 ,其 在 运 转 时 ,间 隙 在 不 断变 化 ,引起 油膜厚 度 和 油膜压 力 的周 期 变化 , 当旋转 至 间 隙较 小 的点 时 , 由于 瓦孔 与 主轴 颈 的膨
胀 差 而易 引起 发 热 、咬死 等 问题 。而 这 些 问题会 随
着 负荷 和 转速 的增 大 ,而 越 发严 重 。
理论计算 (假设 冬季 与夏季 的温度 差为 20 cC) 如 下 :
曲 轴 材 料 为 35 CrMoA,线 膨 胀 系 数 ,: 12.5×10~,曲轴直 径 d =160 mm。
曲 轴 颈 径 的 变 化 △d =(△C × ×d ×1T)/
3.5 装 配各 部件 清 洁度 差 机 体 主 油 道 、 曲轴 油 道 、机 油 过 滤 器 滤 后 壳
发动机曲轴孔同轴度超差精度调整方法

- 85 -工 业 技 术1 项目背景及总体思路发动机曲轴孔作为发动机缸体上的一个关键部位,对发动机整体性能具有重大的影响。
它的作用主要是支撑曲轴,传递从曲轴柄传来的转矩并通过凸缘输出,吸收气缸活塞运动过程中的轴向力和侧向力[1]。
为了尽可能地减小曲轴运转时的摩擦力并保证曲轴在发动机运转过程中的平稳性,要求7个单曲轴孔要在一条同轴线上,同轴度要求在0.02 mm 内,而实际同轴度已超过0.035 mm,不能满足工艺及使用要求,造成发动机总成因曲轴跳动大出现“曲轴抱死、声音噪声异响及抱轴卡死”等故障问题[2],导致整台发动机出现报废的严重后果。
为了保证发动机的质量稳定性,确保曲轴孔同轴度控制在工艺要求尺寸以内,需要彻底调整解决同轴度超差的问题。
2 主要科技创新创新发明发动机缸体曲轴孔同轴度调整的方法,解决长孔系(超过1 000 mm)加工中同轴度超差调整的技术难题。
打破长孔系同轴精度调整长期以来依靠外部力量例如国外技术支持的技术制约。
创新使用调整工具,创新调整方法,减少调整人员的调整时间及劳动强度。
编制长孔系同轴度调整作业指导书,固化检测及调整步骤,对其他精度调整起到技术指导作用。
3 主要技术创新内容3.1 机床加工的工作原理机床加工的工作原理如下。
1)该加工设备是一台曲轴孔加工专用机床,使用曲轴孔加工专用镗刀杆,该镗刀杆长度为1 640 mm,安装了7组加工曲轴孔的刀架与刀片、2组加工止推面的刀架与刀片及加工油封孔的刀架与刀片,完成曲轴孔、止推面及油封孔的精加工,如图1所示。
2)镗刀杆与动力输出机构是通过联轴器与紧固螺栓的刚性连接,以此保证动力传输的稳定性与连续性,降低转速传动的衰减率,确保刀杆加工孔径粗糙度及孔径一致性符合工艺要求。
3)自动机械搬运机构把待加工缸体搬运到加工工位,完成缸体工装预定位,然后镗刀杆在动力输出机构的推动下以固定的姿态穿过第一个支撑套、3个单曲轴孔、第二个支撑套、4个单曲轴孔、进入刀杆第三个支撑套,完成加工前的工件工装定位与刀具定位。
某安装架同轴度超差的原因分析及解决措施
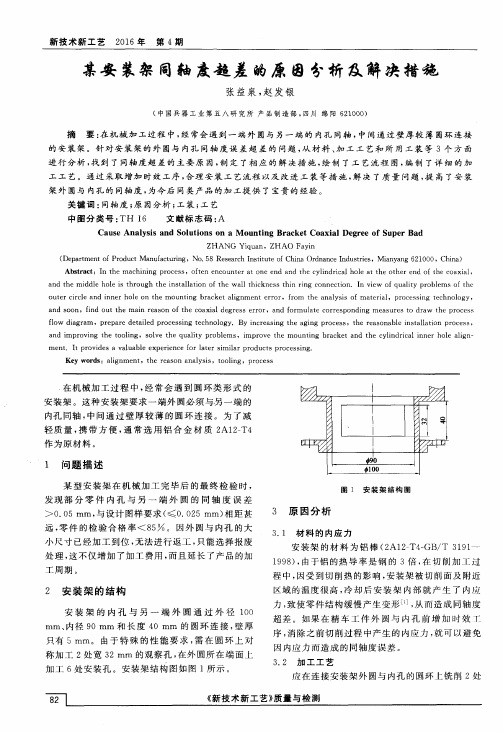
安 装 架 的 内 孔 与 另 一 端 外 圆 通 过 外 径 100 mm、内 径 90 mm 和 长 度 40 mm 的 圆 环 连 接 ,壁 厚 只有 5 mm。 由于 特 殊 的性 能 要 求 ,需 在 圆 环 上 对 称加 工 2处宽 32 mrn的观察 孔 ,在外 圆所 在 端 面上 加工 6处 安装 孔 。安装 架结 构 图如 图 1所 示 。
K ey words:alignm ent,the reason analysis,tooling,process
在机 械加 工过 程 中 ,经 常 会 遇 到 圆环 类 形 式 的 安装 架 。这种 安装架 要 求一端 外 圆必须 与另 一端 的 内孑L同轴 ,中间通 过 壁 厚 较 薄 的 圆环 连 接 。为 了减 轻 质 量 ,携 带 方 便 ,通 常 选 用 铝 合 金 材 质 2A12一T4 作 为原 材料 。
(Departm ent of Product M anufacturing,No.58 Research Institute of China O rdnance Industries, M ianyang 621000,China) Abstract:In the m achining process,often encounter at one end and the cylindrical hole at the other end of the coaxial,
图 1 安 装 架 结 构 图
3 原 因 分 析
3.1 材 料 的 内 应 力 安装架 的材 料 为铝 棒 (2A12-T4一GB/T 3191-一
1998),由于铝 的热 导 率 是 钢 的 3倍 ,在 切 削加 工 过 程 中 ,因受到 切削 热 的影 响 ,安装 架被 切削 面及 附 近 区域 的温度很 高 ,冷 却后 安装 架 内部 就 产 生 了 内应 力 ,致使 零件 结构 缓慢 产生 变形 ],从 而造 成 同轴 度 超 差 。如果 在 精 车 工 件 外 圆与 内 孔 前 增 加 时效 T 序 ,消 除之前 切 削过程 中产生 的 内应力 ,就 可 以避 免 因 内应 力 而造成 的同轴度 误差 。 3.2 加 工 工 艺
中间断开两孔加工同轴度超差原因分析及解决方案
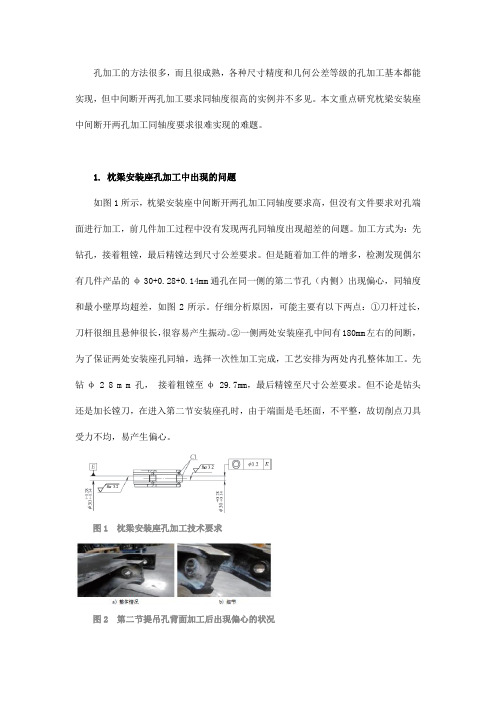
孔加工的方法很多,而且很成熟,各种尺寸精度和几何公差等级的孔加工基本都能实现,但中间断开两孔加工要求同轴度很高的实例并不多见。
本文重点研究枕梁安装座中间断开两孔加工同轴度要求很难实现的难题。
1. 枕梁安装座孔加工中出现的问题如图1所示,枕梁安装座中间断开两孔加工同轴度要求高,但没有文件要求对孔端面进行加工,前几件加工过程中没有发现两孔同轴度出现超差的问题。
加工方式为:先钻孔,接着粗镗,最后精镗达到尺寸公差要求。
但是随着加工件的增多,检测发现偶尔有几件产品的φ 30+0.28+0.14mm通孔在同一侧的第二节孔(内侧)出现偏心,同轴度和最小壁厚均超差,如图2所示。
仔细分析原因,可能主要有以下两点:①刀杆过长,刀杆很细且悬伸很长,很容易产生振动。
②一侧两处安装座孔中间有180mm左右的间断,为了保证两处安装座孔同轴,选择一次性加工完成,工艺安排为两处内孔整体加工。
先钻φ 2 8 m m 孔,接着粗镗至φ 29.7mm,最后精镗至尺寸公差要求。
但不论是钻头还是加长镗刀,在进入第二节安装座孔时,由于端面是毛坯面,不平整,故切削点刀具受力不均,易产生偏心。
图1 枕梁安装座孔加工技术要求图2 第二节提吊孔背面加工后出现偏心的状况2. 原因分析及解决方案针对枕梁安装座孔加工中出现的质量问题进行原因分析,若为第一种原因,即刀杆很细且悬伸很长,易产生振动,则在枕梁加工过程中,相当于加工了4次安装座孔,会出现同样的问题,但实际上并没有出现,说明刀杆刚性固然有一定的影响,但不是此质量问题的根本原因,因此还需要对第二种原因进行深入分析。
仔细研究了钻头和镗刀,并再次进行试验加工后,确认钻头和镗刀刀杆均没有问题,可以排除第一种原因。
得出的结论是同侧两安装座孔中间的间断距离过长,且第二节安装座孔端面是不平整的毛坯面,导致出现偏心。
于是对间断部位的第二节安装座孔端面进行检测,发现此端面很不平整,加工时与刀具主轴不垂直,如图3所示。
中间断开两孔加工同轴度超差原因分析及解决方案

Internal Combustion Engine &Parts0引言在现代化的加工生产过程中,在机械领域关于轴承的用处十分广泛,尤其是轴承的安装定位孔大多数都是呈现出成对的台阶性孔,由于安装定位孔的安装精度和同轴度越高,机械设备在运转过程中所产生的噪音也会越小,并且在一定程度上能够有效的降低轴承座的磨损程度,导致最终的使用寿命大大延长,尤其是在一些对精度要求比较高的图纸当中,同轴度的要求更是多达ϕ0.02,甚至比这个数值更高。
通常情况下,目前在加工过程中对于孔的加工方法有很多种,并且加工技术基本上处于成熟的阶段,能够满足各种精度尺寸和公差等级的基本要求,但是本文涉及的中间断开两孔加工同轴度要求很高的加工案例却并不多见。
本文主要以枕梁安装座的中间断开两孔的加工为例,首先简要分析了加工过程中出现的各种问题,接着详细的阐述了问题的产生原因以及相应的解决方案,最终简单的概述了批量生产该样品的加工效果。
1枕梁座中间断开两孔的加工方法在传统的加工过程中,对于枕梁座中间断开两孔的加工方法大致上可以分为以下两种类型:①将刀具调头进行再次加工:先钻枕梁座中一侧的孔,紧接着将刀具调头,以这个孔的端面作为定位基准,开始加工另外一个孔,这样可以确保两孔的中心在同一高度上;②利用特殊的刀具来反拉另外一侧的孔。
通过对大量加工零件进行抽样检测和分析可知,这两种方法在加工过程中都存在着一定的问题,其中第一种方法对于加工零件的夹具要求比较高,必须要确保两孔的轴心在同一高度上,使得中间断开两孔的同轴度不会出现超差,另外这对两孔内侧端面之间的距离和孔的定位标准有着明确的规定,因此在加工的过程中不仅需要控制好工装定位的基准面,还需要确定刀具的走向和垂直度。
因此面对不同尺寸的枕梁座加工零件,则需要制定出不同尺寸的工件夹具,最终导致中间断开两孔之间的配合间隙在标准尺寸公差的范围之内,另外工件还需要两次才能装夹完成,使得加工效率大大降低。
加工中心回转加工台阶孔同轴度超差原因与改进措施探析
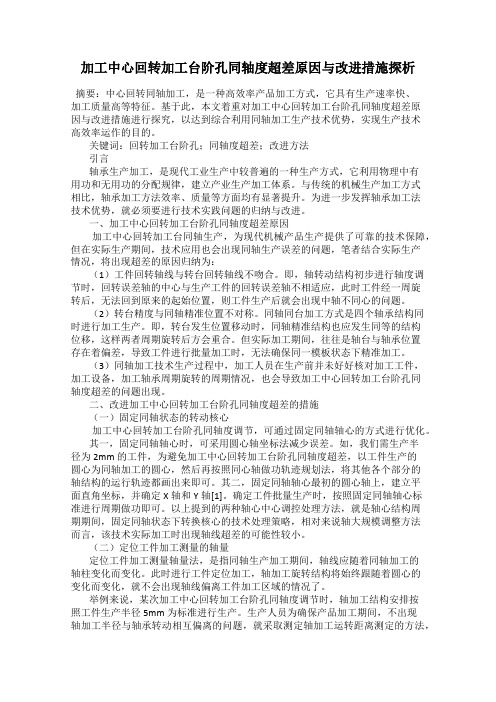
加工中心回转加工台阶孔同轴度超差原因与改进措施探析摘要:中心回转同轴加工,是一种高效率产品加工方式,它具有生产速率快、加工质量高等特征。
基于此,本文着重对加工中心回转加工台阶孔同轴度超差原因与改进措施进行探究,以达到综合利用同轴加工生产技术优势,实现生产技术高效率运作的目的。
关键词:回转加工台阶孔;同轴度超差;改进方法引言轴承生产加工,是现代工业生产中较普遍的一种生产方式,它利用物理中有用功和无用功的分配规律,建立产业生产加工体系。
与传统的机械生产加工方式相比,轴承加工方法效率、质量等方面均有显著提升。
为进一步发挥轴承加工法技术优势,就必须要进行技术实践问题的归纳与改进。
一、加工中心回转加工台阶孔同轴度超差原因加工中心回转加工台同轴生产,为现代机械产品生产提供了可靠的技术保障,但在实际生产期间,技术应用也会出现同轴生产误差的问题,笔者结合实际生产情况,将出现超差的原因归纳为:(1)工件回转轴线与转台回转轴线不吻合。
即,轴转动结构初步进行轴度调节时,回转误差轴的中心与生产工件的回转误差轴不相适应,此时工件经一周旋转后,无法回到原来的起始位置,则工件生产后就会出现中轴不同心的问题。
(2)转台精度与同轴精准位置不对称。
同轴同台加工方式是四个轴承结构同时进行加工生产。
即,转台发生位置移动时,同轴精准结构也应发生同等的结构位移,这样两者周期旋转后方会重合。
但实际加工期间,往往是轴台与轴承位置存在着偏差,导致工件进行批量加工时,无法确保同一模板状态下精准加工。
(3)同轴加工技术生产过程中,加工人员在生产前并未好好核对加工工件,加工设备,加工轴承周期旋转的周期情况,也会导致加工中心回转加工台阶孔同轴度超差的问题出现。
二、改进加工中心回转加工台阶孔同轴度超差的措施(一)固定同轴状态的转动核心加工中心回转加工台阶孔同轴度调节,可通过固定同轴轴心的方式进行优化。
其一,固定同轴轴心时,可采用圆心轴坐标法减少误差。
如,我们需生产半径为2mm的工件,为避免加工中心回转加工台阶孔同轴度超差,以工件生产的圆心为同轴加工的圆心,然后再按照同心轴做功轨迹规划法,将其他各个部分的轴结构的运行轨迹都画出来即可。
PZ12V190B柴油机的检测,修理,试验及调整
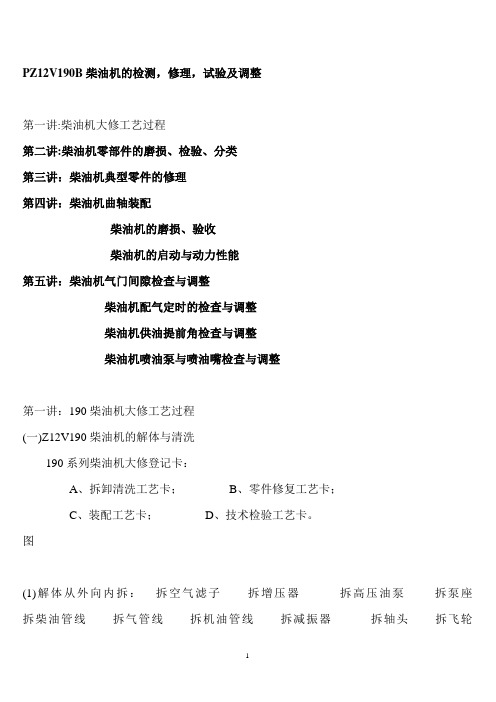
PZ12V190B柴油机的检测,修理,试验及调整第一讲:柴油机大修工艺过程第二讲:柴油机零部件的磨损、检验、分类第三讲:柴油机典型零件的修理第四讲:柴油机曲轴装配柴油机的磨损、验收柴油机的启动与动力性能第五讲:柴油机气门间隙检查与调整柴油机配气定时的检查与调整柴油机供油提前角检查与调整柴油机喷油泵与喷油嘴检查与调整第一讲:190柴油机大修工艺过程(一)Z12V190柴油机的解体与清洗190系列柴油机大修登记卡:A、拆卸清洗工艺卡;B、零件修复工艺卡;C、装配工艺卡;D、技术检验工艺卡。
图(1)解体从外向内拆:拆空气滤子拆增压器拆高压油泵拆泵座拆柴油管线拆气管线拆机油管线拆减振器拆轴头拆飞轮拆接臂横桥拆气缸盖拆活塞连杆拆齿轮壳拆齿轮系拆凸轮轴拆油衣拆曲轴拆缸套(2)主要件的鉴定和修理缸体维修——是否缸体下口接触带粘接连杆修理——连杆配重、配瓦、搪瓦、搪连杆铜套曲轴修理——修轴、磨轴、氮化齿轮修理——齿轮轴磨光、齿轮铜套搪孔缸盖修理——气门座孔下陷严重进行镶口凸轮轴修理——修理轴颈、修理进排凸轮传动部件修理——传动轴修理、风扇轴修理图(3)主要小件修理高压油泵修理——柱塞、柱塞弹簧有磨损,应更换。
最后装配好进行校对。
机油泵修理——轴泵、花键套、铜套有磨损,更换。
输油泵修理——检查磨损,更换机油滤子总成修理——检查滤芯,更换柴油滤子总成修理——检查滤芯,更换水泵总成修理——检查轴、轴承、水封更换增压器修理——检查各部轴、铜套磨损更换图高压油泵(4)选配件及总装活塞选配铜套选配活塞环选配活塞销选配曲轴与主轴瓦选配连杆选配凸轮子选配凸轮轴瓦选配齿轮轴与铜套选配缸盖选配(5)总装配后——试车——喷吐——封存图曲轴组装第二讲:柴油机主要零件图缸套尺寸的测量(2)气缸套:190系列柴油机采用湿式气缸套,高强度,耐磨,含硼含金铸铁制造,内壁具有较高的精度和较细的表面粗糙度,并经氮化处理。
要求精度很高RHC40——50。
轴孔类零件同轴度误差的检测探讨(精)

【摘要】文章围绕同轴度误差的检测问题,介绍了基准要素与被测要素的体现方法以及同轴度误差的几种检测方法,说明几种方法的选取原则,并对影响同轴度误差的主要因素进行分析。
叙词:同轴度测量误差检测方法●重型汽车集团有限公司邢杰轴孔类零件同轴度误差的检测探讨圆柱面是汽车及各类机械零件中应用最广泛的几何要素,轴与孔又是其在实际应用中的体现,含轴孔要素零件的同轴度误差对机械产品的质量影响很大,有时甚至成为影响整个产品组件的关键。
在形位误差测量中,测量比较复杂,采测数据的准确度受多方面因素的影响,最终数据处理更对检测结果产生直接影响。
针对这些,多年来理论和学术界经过反复研究探讨,统一了对形位误差概念的认识,提出按“最小条件”原则,采用最小包容区域的方法来简化评定圆柱面形位误差的问题。
本文就同轴度误差检测问题进行探讨。
1同轴度误差的检测在实际生产中,包含轴孔要素的零件很多,其结构形状各异,设计上提出的同轴度误差要求也不同。
在生产现场往往追求简捷、快速和小的检测成本,但这必须是建立在满足技术要求的基础上。
所以从被测零件的结构形式、设计要求、加工工艺方法、环境条件、检测成本等方面综合考虑,确定一个科学简便的检测方案是非常必要的。
1.1基准要素的体现测量同轴度误差必须建立基准,并用适当的方法体现基准。
(1模拟法通常采用具有足够精确形状的表面与基准实际要素接触来体现基准轴线。
模拟基准与基准实际要素接触时其间是否符合最小条件,一般根据是否形成稳定接触来判断。
当稳定接触时,能形成符合最小条件的相对位置关系。
否则,测量时应做适当调整,使基准实际要素与模拟基准之间尽可能达到符合最小条件的相对位置关系。
从理论上来讲是否稳定接触与符合最小条件是不一致的,因为它与基准实际要素的形状误差有关;但在实际生产中通常将这种关系忽略。
在精度允许的情况下,轴孔类零件的基准可用V 型架、心轴、中心孔来体现。
(2直接法是以基准实际要素直接代替基准。
该法适用于体现基准要素的零件形状误差较小、采用模拟法有难度的情况。
12V190天然气发动机的故障处理

!"
!"#$% &’%$( )$*#$))+#$*
停车解体检查发现:( ")联轴器及推力轴承无 故障;( %)各级密封有轻微摩擦现象,且转子中部 密封摩擦较重,密封间隙及密封与转子轴同心度符 合安装标准。 由幅频特性图分析可知,转子在通过第一临界 转速时峰值较平缓,在高速运转时振幅值增大趋势 很陡。解体检查结果表明,转子在低速运行时平衡 较好,高速运行时由于临时弯曲引起不平衡,并与 定子密封产生摩擦。 对转子进行动平衡检测发现,转子六级叶轮残 剧。 加上有的缸燃烧不好, 更加剧了气门磨损、 烧蚀。
气门间隙和摇臂下行距离的配合间隙以及调整气门密封接触带宽度、空燃比及气门间隙两方面提出了各自的 解决措施,确保了机组可靠运行。 关键词:天然气发动机;故障;处理 中图分类号: 6+/37/ 文献标识码: 8
临 盘 采 油 厂 的 四 台 "$4"2* 天 然 气 发 动 机 组 , 在使用初期先后出现一些问题,影响了正常运行。 针对这些问题进行了整改, 保证了机组的可靠运行。 一、摇臂组件断裂
收稿日期: $**’-*/-*$
质稳定,排污量大大减少。 参考文献:
水利电力出版社, 0"1 赵永民 # 汽轮机设备及运行 # 北京: "223#
0$1 严瑞
化学工业出版社, # 水处理剂应用手册 # 北京: $***#
!"#$% &’%$( )$*#$))+#$*
!"
可靠性与故障分析
文章编号:"*)".,)"" ( %,,&),-.,,-,.,%
中国设备工程
!""#$!
加工中心回转加工台阶孔同轴度超差原因分析及改进

加工中心回转加工台阶孔同轴度超差原因分析及改进随着四轴加工中心的广泛运用,一些有着较高同轴度要求的孔及台阶孔能通过第四轴(转台)回转加工一次完成。
通过分析找出同轴度超差的常见原因,并提出改进及前提调试时需要注意的地方。
标签:四轴;台阶孔;同轴度在现代工业中,轴承的运用非常广泛,轴承安装定位孔大多数为成对加工的台阶孔。
轴承安装孔的精度及同轴度越高,高速运转时噪音越小,震动越小,使用寿命越长。
在某些要求高的零件图纸中,同轴度要求为φ0.02甚至更高。
1 加工方法传统观念中,对于这类零件的加工方法可分为两种:(1)调头两次加工,即先加工一侧的台阶孔,再以台阶孔及端面作为定位基准,加工另一头台阶孔;(2)利用特殊刀具反拉另一侧的台阶孔。
但这两种加工工艺都有不足的地方,第一种加工工艺对工装夹具的要求较高,既要控制定位柱与台阶孔之间的间隙,又要控制工装定位面与走刀方向上的垂直度。
这样要么缩小第一次加工的台阶孔的公差带,要么需要制作不同尺寸的工装夹具,使其最大配合间隙不能大于同轴度要求的尺寸。
需要两次装夹才能完成,加工效率比较一般。
第二种加工方法会受到台阶孔及中间通孔的限制,假设D1为台阶孔通孔,D2为台阶孔,d为刀杆直径,L为刀尖到刀杆的径向最大距离,只有当L<D1、L-d<(D2-D1)/2时,才能用此工艺加工。
如果刀杆直径过大,在进刀与退刀时容易与D1发生干涉,刀杆直径太小时。
刀杆的强度会减弱,加工出来的台阶孔尺寸及表面粗糙度均难以控制。
随着四轴加工中心的广泛运用,通过第四轴(转台)回转加工成了新的加工工艺,此加工工艺基本没有局限性,一次装夹即可完成,加工效率高。
2 同轴度超差原因分析但在实际生产过程中,通过三坐标检测,我们依然发现其同轴度有超差现象,并且属于批量超差,通过对加工中心班长对某零件的调试到加工完整的观察及分析,找到了造成同轴度超差的原因。
2.1 工件回转轴线与转台回转轴线不重合导致超差在制作工装夹具时,可能由于加工误差,使其装夹定位后的回转轴线与转台的回转轴线超出图纸设计要求,调试人员没有按照转台的回转中心设定坐标系而是以工装定位轴线设定了坐标系,这样由于其回转中心不重合就会导致同轴度超差,如图1所示,回转加工后产生的同轴度误差值为2倍的L。
- 1、下载文档前请自行甄别文档内容的完整性,平台不提供额外的编辑、内容补充、找答案等附加服务。
- 2、"仅部分预览"的文档,不可在线预览部分如存在完整性等问题,可反馈申请退款(可完整预览的文档不适用该条件!)。
- 3、如文档侵犯您的权益,请联系客服反馈,我们会尽快为您处理(人工客服工作时间:9:00-18:30)。
2016年4月
第44卷第8期
机床与液压
MACHINETOOL&HYDRAULICS
Apr 2016
Vol 44No 8
DOI:10.3969/j issn 1001-3881 2016 08 058
收稿日期:2015-01-21
作者简介:王占宜(1980 ),男,在职硕士研究生,工程师,主要从事机械加工和设计工作㊂E-mail:78533383@
qq com㊂
通信作者:王兆君,E-mail:215491354@qq com㊂
12V190机体主轴孔同轴度超差分析及改进
王占宜1,2,王兆君1,华正治2,宋雪磊2
(1 山东理工大学机械工程学院,山东淄博255000;
2 胜利油田胜利动力机械集团有限公司,山东东营257032)
摘要:机体主轴孔的同轴度属于关键尺寸,如果超差可能导致发动机在运转中出现油压低㊁拉瓦等故障㊂针对12V190生产现场中出现的主轴孔同轴度在二次复装后测量数值变大以及试车中出现的油压低等问题,对12V190机体的同轴度测量控制现状进行了调研和测量试验,并最终通过数据分析,找到问题所在,对生产工艺进行改进,从而保证机体主轴孔的同轴度㊂
关键词:12V190机体主轴孔;同轴度;改进
中图分类号:TH741㊀㊀文献标志码:B㊀㊀文章编号:1001-3881(2016)08-174-3
㊀㊀机体主轴孔的同轴度属于关键尺寸,如果超差,可能导致发动机在运转中出现油压低㊁拉瓦等故障㊂因此机体主轴孔同轴度的要求均较高,12V190机体以主轴孔1㊁7为测量基准,其他各主轴孔相对于基准孔的同轴度要求为0 05mm㊂为保证该尺寸,机体主轴孔在三孔专用镗床上加工,加工完后,将主轴承盖拆掉,然后在总装装配好标准瓦后进行二次合装,并复测装瓦后的同轴度,以保证机体同轴度符合装配要求㊂目前,12V190机体在生产中出现主轴孔同轴度在二次复装测量时数值变大,以及试车中出现油压低等问题㊂针对这些问题,对12V190机体的同轴度测量控制现状进行了调研和测量试验,并最终通过数据分析找到问题所在,对生产工艺进行改进,从而保证机体主轴孔的同轴度㊂
1㊀机体主轴孔二次复装后主轴孔同轴度超差原因分析
1 1㊀机体主轴孔二次复装后同轴度测量及原因分析
对10台完工后机体的主轴孔内孔及其同轴度进行二次复装测量,根据10台机体的测量结果,通过对各支撑圆心位置在水平和垂直方向上求平均值,绘制出图1(这10台机体在加工后㊁未拆主轴瓦盖时,测量主轴孔同轴度均在0 05mm,在合格范围内)
㊂
图1㊀主轴承座孔水平方向和垂直方向同轴度
分析上述测量数据可以看出:测量数据的误差具有一定的规律性,并且在Y方向,其偏差较大,尤其在中间主轴孔位置最大㊂分析具体原因如下:
(1)机体三孔镗床各支撑间同轴度误差较大,
主要是靠近动力端的支撑孔中心偏离其他3道支撑孔轴线引起的㊂
机体三孔镗床各支撑分布及机体安装见图
2㊂
图2㊀三孔镗床结构示意图
机体定位在镗床上时,自由端靠近动力头,各支撑分布见图2,两端外部各有一个外支撑,在机体主
轴承座孔2和3之间㊁4和5之间各有一个内支撑㊂假设镗杆不经过支撑IV,按图构建的虚拟镗杆轴线,支撑IV位置距离主轴承座孔1的距离按6 8倍座孔间距计算,可以得到在支撑IV处水平方向上偏差19
μm,在垂直方向上偏差82μm,由此计算最大偏差为84μm㊂为验证此推测,将镗杆穿过前3道支撑,在镗杆头上固定磁力千分表,同步转动镗杆和第4道支撑内浮动套,支撑IV中心位于镗杆中心上部稍偏右(从支撑I看向支撑IV的方向),圆周最大跳动量200μm,即镗杆轴线与第4道支撑孔间有100μm的偏差㊂
由此可见,计算结果与测量结果基本符合㊂另外,经测量,镗杆与动力头之间的同轴度偏差为700μm(动力头位置靠下稍偏左),并且镗杆轴头连接外径动力头连接内孔配合间隙小,不能完全补偿镗杆与动力头之间的同轴度偏差,也会产生附加弯曲力,从而影响主轴孔同轴度㊂因此,规律性的同轴度偏移,是由三孔镗中间支架不同轴所造成的㊂(2)机体在二次复装后,同轴度较未拆之前增大,其主要原因为瓦盖经过重新拆装之后,同轴度测量偏差包含了瓦盖和机体主轴座孔的齿形定位产生的偏差㊂所以瓦盖与机体主轴座孔齿形的加工精度,以及两者齿形的贴合度对于机体复装后的同轴度有很大影响㊂目前,瓦盖和机体主轴座孔的齿形采用成型刨齿刀加工成型,齿形面的贴合度并不高,由于接触面积小,在合装时,容易造成螺栓压装方向上的尺寸变小㊂要减小二次合装的尺寸变化,应提高齿形精度㊂
(3)合装时的拧紧力矩前后应一致并精确控制,否则也会造成前后合装尺寸的变化㊂
(4)由于瓦片尺寸公差为15μm,同一片瓦厚度差为0居多,最大也不超过10μm,因此瓦片影响同轴度也就在5μm,所以二次复装后同轴度偏大,瓦并不是主要影响原因,但为了进一步缩小瓦片对同轴度的影响,按瓦的厚度,采用分级标准,根据瓦孔尺寸进行配瓦㊂
1 2㊀油压低机体的同轴度测量
对出现油压低的机体和2台拉瓦的机体同轴度进行了测量,测量结果如图3 5所示㊂其中图3是水平方向上各座孔中心位置图,图4是垂直方向上各座孔中心位置图,图5是根据机体同轴度测量数据绘制的各主轴孔中心位置分布图
㊂图3㊀
在水平方向上的各座孔中心位置图图4㊀
在垂直方向上的各座孔中心位置图图5㊀机体主轴承座孔圆心位置分布图
㊃571㊃
第8期王占宜等:12V190机体主轴孔同轴度超差分析及改进㊀㊀㊀
从测量数据可以看出:
(1)水平方向上同轴度要小于垂直方向上,并
且分布呈现出方向性,其中最大同轴度偏差围绕着
50μm附近直线波动,形成的原因就是前面分析验证的镗床支撑IV中心偏离其他3道支撑轴线㊂
(2)发动机油压低与主轴承孔水平方向上的同
轴性差有较明显关系㊂从图3 5可以看出,油压低的机体在水平方向上多数同轴度偏差大㊂由于瓦片接合处开有垃圾槽和减薄区,泄油压阻小,所以泄油间隙对泄流量的影响更显著㊂轴瓦与座孔间隙大泄油量大,但轴与孔在水平上的偏心也会造成泄油量加大㊂(3)拉瓦机组只有2台,测量数据较少,无法判断与机体主轴孔同轴度有明显的关联关系㊂
2㊀改进措施
(1)对三孔镗床的镗模架进行检修调整:①更
换4道镗模的铜套,并在龙门加工中心上进行一次镗孔,提高4道支撑孔的同轴度;②通过调整动力头与
镗杆连接方式,减小了镗杆与动力头之间的同轴度㊂
(2)为提高机体瓦盖和主轴座孔齿形的表面粗
糙度和贴合度,设计制作了机体齿形配研专机㊂机体齿形配研专机采用三相异步电动机经摆线针轮减速机减速后带动曲柄连杆机构,由曲柄连杆机构将圆周运动转化为往复直线运动,带动研磨导杆运动㊂与机体配合的7个瓦盖分别固定在研磨导杆半圆夹板间,瓦盖与机体主轴座孔通过齿形接触配合,配合面涂一层
80号氧化铬研磨砂,它做往复直线运动时,利用瓦盖自重形成的下压力对配合的齿形面进行研磨加工㊂配研后的瓦盖与机体主轴座孔进行打印标记,一一对应,以改善齿形的贴合度,进而减小复装后的尺寸变化㊂
通过机体齿形配研专机研磨后,能有效去除齿形凸点㊁毛刺,使齿形表面粗糙度达到Ra1 6μm,贴合度达到85%以上,减小了主轴孔二次复装后孔的变化,从而提高机体主轴孔的同轴度㊂机体齿形配研专机如图6所示
㊂
图6㊀机体齿形配研机原理图
㊀
(3)对轴瓦按厚度制定分级标准,装配时,根据
瓦孔和曲轴尺寸进行相应的配瓦,以进一步提高装瓦后的尺寸精度㊂
(4)瓦盖合装时,严格按工艺要求扭矩进行装配,并进行校验,以保证装配力矩精度㊂
(5)从拉瓦机组拆解分析看,拉瓦的原因主要
与清洁度有关系,加强装配前的清洁度控制,并在装配前重点对主油道进行清洗㊂
3㊀结束语
通过上述措施的采用,机体主轴孔二次复装后的同轴度得到了保证和提高,解决了复装同轴度尺寸变
化大的问题㊂
参考文献:
[1]王雪峰.柴油机主轴孔㊁凸轮轴孔同轴度探讨[J].内燃机,2001(2):10-12.
[2]陈彬,林健,魏建瑛.大尺寸同轴度检测技术研究[J].矿山机械,2006,34(6):106-107.[3]甘永立.形状和位置误差检测[M].北京:国防工业出版社,1995.
[4]许云平,温粤丽.机械制造检验手册[M].北京:中国卓越出版社,1991.[5]杨铁牛.互换性与技术测量[M].北京:电子工业出版
社,2010.㊃
671㊃机床与液压第44卷。