001铸造铝合金中的气体和氧化夹杂
铝合金精炼
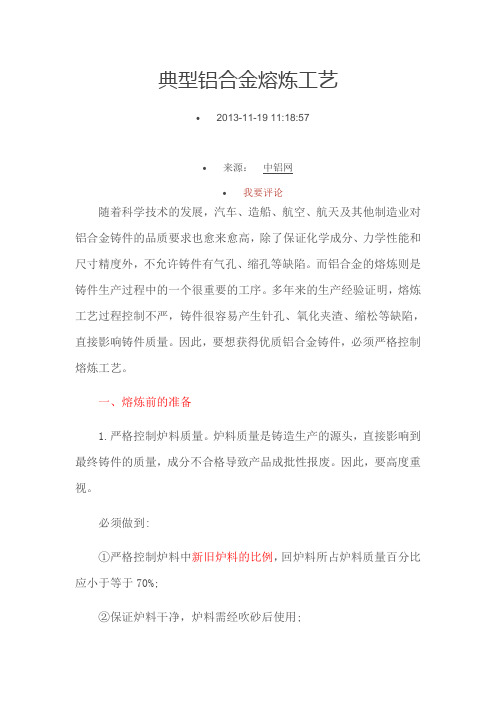
典型铝合金熔炼工艺∙2013-11-19 11:18:57∙来源:中铝网∙我要评论随着科学技术的发展,汽车、造船、航空、航天及其他制造业对铝合金铸件的品质要求也愈来愈高,除了保证化学成分、力学性能和尺寸精度外,不允许铸件有气孔、缩孔等缺陷。
而铝合金的熔炼则是铸件生产过程中的一个很重要的工序。
多年来的生产经验证明,熔炼工艺过程控制不严,铸件很容易产生针孔、氧化夹渣、缩松等缺陷,直接影响铸件质量。
因此,要想获得优质铝合金铸件,必须严格控制熔炼工艺。
一、熔炼前的准备1.严格控制炉料质量。
炉料质量是铸造生产的源头,直接影响到最终铸件的质量,成分不合格导致产品成批性报废。
因此,要高度重视。
必须做到:①严格控制炉料中新旧炉料的比例,回炉料所占炉料质量百分比应小于等于70%;②保证炉料干净,炉料需经吹砂后使用;③三等回炉料枷浇冒口匀使用前应经重熔精炼处理;④炉料应充分预热,去除水分、油污等杂质;⑤由于铭合金有铝硅类、铝铜类、铝镁类等合金,合金牌号较多,使用的元素也比较多,且互相影响,要求严格管理,不可混料;⑥配料、称量要准确,比如ZL104合金,考虑到除气、排渣及变质过程中的损耗,Mg元素应在实际配料时多加炉料质量的0.02%-0.03%,才能保证铸件的化学成分。
2.熔炼工具。
熔炼使用的址涓及熔炼工具须清理干净且涂上涂料,以保证使用时与铝合金有效隔离,减少合金液受到杂质污染,并且需要充分预热,址涓要烘烤至暗红色再加入炉料熔炼,以防水蒸气带入合金中使合金的气体增加、针孔度增加。
3.其他工作。
严格按已制订好的工艺规范作好覆盖剂、精炼剂及变质剂的准备工作。
二、熔炼操作熔炼步骤如下。
①装料。
在预热后的柑A中装入预制合金锭、优质回炉料,再加中fol合金,最后加合金元素。
②温度控制。
严格控制铝合金熔炼的温度,只有合适的温度才能获得高质量的合金液,避免过热。
若温度过高,会加大合金中各种元素的氧化烧损,引起合金中化学成分的变化。
铝合金消失模铸造的实践
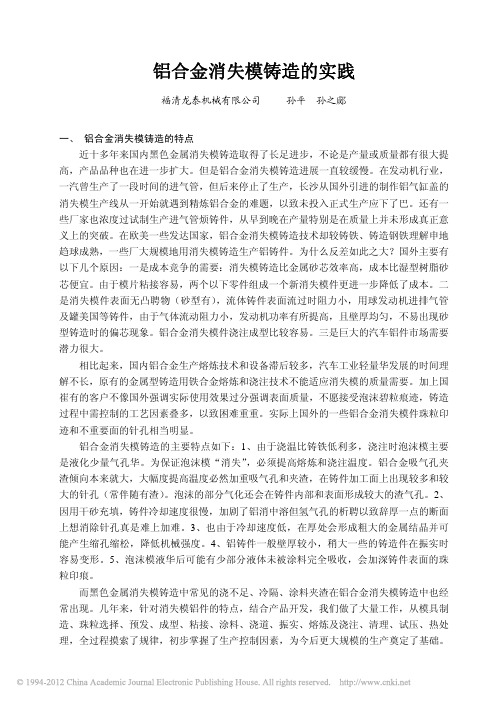
铝合金消失模铸造的实践福清龙泰机械有限公司 孙平 孙之郕一、 铝合金消失模铸造的特点近十多年来国内黑色金属消失模铸造取得了长足进步,不论是产量或质量都有很大提高,产品品种也在进一步扩大。
但是铝合金消失模铸造进展一直较缓慢。
在发动机行业,一汽曾生产了一段时间的进气管,但后来停止了生产,长沙从国外引进的制作铝气缸盖的消失模生产线从一开始就遇到精炼铝合金的难题,以致未投入正式生产应下了巴。
还有一些厂家也浓度过试制生产进气管烦铸件,从早到晚在产量特别是在质量上并未形成真正意义上的突破。
在欧美一些发达国家,铝合金消失模铸造技术却较铸铁、铸造钢铁理解申地趋球成熟,一些厂大规模地用消失模铸造生产铝铸件。
为什么反差如此之大?国外主要有以下几个原因:一是成本竞争的需要:消失模铸造比金属砂芯效率高,成本比湿型树脂砂芯便宜。
由于模片粘接容易,两个以下零件组成一个新消失模件更进一步降低了成本。
二是消失模件表面无凸聘物(砂型有),流体铸件表面流过时阻力小,用球发动机进排气管及罐美国等铸件,由于气体流动阻力小,发动机功率有所提高,且壁厚均匀,不易出现砂型铸造时的偏芯现象。
铝合金消失模件浇注成型比较容易。
三是巨大的汽车铝件市场需要潜力很大。
相比起来,国内铝合金生产熔炼技术和设备滞后较多,汽车工业轻量华发展的时间理解不长,原有的金属型铸造用铁合金熔炼和浇注技术不能适应消失模的质量需要。
加上国崔有的客户不像国外强调实际使用效果过分强调表面质量,不愿接受泡沫碧粒痕迹,铸造过程中需控制的工艺因素叠多,以致困难重重。
实际上国外的一些铝合金消失模件珠粒印迹和不重要面的针孔相当明显。
铝合金消失模铸造的主要特点如下:1、由于浇温比铸铁低利多,浇注时泡沫模主要是液化少量气孔华。
为保证泡沫模“消失”,必须提高熔炼和浇注温度。
铝合金吸气孔夹渣倾向本来就大,大幅度提高温度必然加重吸气孔和夹渣,在铸件加工面上出现较多和较大的针孔(常伴随有渣)。
泡沫的部分气化还会在铸件内部和表面形成较大的渣气孔。
铸造铝合金的熔炼

第一节 铝合金液的精炼原理
精炼的目的:
清除铝液中的气体和各类有害杂质,净化铝液,防 止在铸件中形成气孔和夹渣。
一、铝铸件中气孔的形态及对性能的影响
1、针孔 分布在整个铸件截面上,因铝液中的气体,夹杂含量高、
精炼效果差、铸件凝固速度低所引起。针孔可分三种类型。
(1) 点状针孔 此类针孔在低倍显微组织中呈圆点状, 轮廓清晰且互不相连,能清点出每平方厘米面积上的针孔数目并测 得针孔的直径。这类针孔容易和缩孔、缩松相区别。
在所有的炉气成分中,只有氢能大量地溶解于铝液中。 根据测定,存在于铝合金中的气体,氢占85%以上,因而 “含气量”可视为“含氢量”的同义词。
铝液中的氢和氧化夹杂主要来源于铝液与炉气中水 汽的反应。
1、铝和水汽的反应
低于250℃时,铝锭与大气中的水汽接触会产生下 列反应
Al+H2O→Al(OH)3+H2
气孔位于铸件表皮下面,因铝液和铸型中水分反 应产生气体所造成,一般和铝液质量无关.
3、单个大气孔
这种气孔产生的原因是由于铸件工艺设计不合理, 如铸型或型芯排气不畅,或者是由于操作不小心,如浇注 时堵死气眼,型腔中的气体被憋在铸件中所引起,也和铝 液纯净度无关。
二、铝铸件中氧化夹杂物形态及对性能的影响
图13-1为铝液与各种炉气成分反应 时标准状态自由能的变化。
从表13-1和图13-1可见,除按反应式(13-2)、(13-6)
生成Al4C3外,其余反应都将生成Al2O3,而AlN与H2O或O2按式(1310)、(13-11)反应, Al4C3与H2O或O2按式(13-8)、(13-9)反应又都 生成Al2O3,因此,表13-1所列众多反应的最终产物中大部分是Al2O3。 Al2O3的化学稳定性极高,熔点高达2015℃±15℃,在铝液中不再分 解,是铝铸件中主要的氧化夹杂物。
(完整版)铝合金压铸工艺

压铸产品基本工艺流程压铸工艺是将压铸机、压铸模和合金三大要素有机地组合而加以综合运用的过程。
而压铸时金属按填充型腔的过程,是将压力、速度、温度以及时间等工艺因素得到统一的过程。
模具结构设计、热处理工艺、模具制造及模具装配对铝合金压铸模寿命的影响。
压铸工艺流程图示1。
11压铸工艺原理压铸工艺原理是利用高压将金属液高速压入一精密金属模具型腔内,金属液在压力作用下冷却凝固而形成铸件。
冷、热室压铸是压铸工艺的两种基本方式,其原理如图1—1所示。
冷室压铸中金属液由手工或自动浇注装置浇入压室内,然后压射冲头前进,将金属液压入型腔。
在热室压铸工艺中,压室垂直于坩埚内,金属液通过压室上的进料口自动流入压室。
压射冲头向下运动,推动金属液通过鹅颈管进入型腔。
金属液凝固后,压铸模具打开,取出铸件,完成一个压铸循环。
1.12压铸工艺的特点优点(1)可以制造形状复杂、轮廓清晰、薄壁深腔的金属零件。
压铸件的尺寸精度较高,表面粗糙度达Ra0。
8—3.2um,互换性好。
(2)材料利用率高。
由于压铸件的精度较高,只需经过少量机械加工即可装配使用,有的压铸件可直接装配使用。
生产效率高。
由于高速充型,充型时间短,金属业凝固迅速,压铸作业循环速度快。
方便使用镶嵌件。
(3)缺点(1)由于高速填充,快速冷却,型腔中气体来不及排出,致使压铸件常有气孔及氧化夹杂物存在,从而降低了压铸件质量。
不能进行热处理。
(2)压铸机和压铸模费用昂贵,不适合小批量生产。
(3)压铸件尺寸受到限制。
压铸合金种类受到限制.主要用来压铸锌合金、铝合金、镁合金及铜合金。
1.13压铸工艺的应用范围压铸生产效率高,能压铸形状复杂、尺寸精确、轮廓清晰、表面质量及强度、硬度都较高的压铸件,故应用较广,发展较快.目前,铝合金压铸件产量较多,其次为锌合金压铸件。
第二章压铸合金2。
1 压铸合金压铸合金是压铸生产的要素之一,要生产优良的压铸件,除了要有合理的零件构造、设计完善的压铸模和工艺性能优越的压铸机外,还需要有性能良好的合金。
中南大学有色金属熔炼与铸锭重点整理

性能低。主要用于制造压铸仪表壳体类零件、模 具和模板等。 以 ZL102 合金为例,分析其组织形态在变质处
也大。 其他因素 使用不同的炉型,其熔池形状、面积
和加热方式不同,氧化烧损程度也不同;在其他 条件一定时,熔炼时间越长,氧化烧损也越大。 降低氧化烧损的方法: 选择合理炉型 采用合理的加料顺序和炉料处理工艺 采用覆盖剂 正确控制炉温 正确控制炉气性质 合理的操作方法 加入少量α>1 的表面活性元素。
3.1 常用铸造有色合金(包括铸造铝合金、铸造 镁合金、铸造铜合金、铸造锌合金及铸造轴承合 金,下同)的分类、合金牌号及其特点、掌握合 金材质选用及其熔铸工艺确定的原则;
3.1.1 简述 Al-Si、Al-Cu、Al-Mg 和 Al-Zn 系铸 造合金的主要特点及其用途。
答:铸造用的铝合金主要是由 Al-Si、Al-Cu、 Al-Mg 和 Al-Zn 四个二元基本合金系以及在此基 础上,再添加少量其他元素形成的多元合金系组 成的。
2)Al-Cu 合金系(≥4%Cu)该系合金添加的 Cu 起固溶强化的作用,所以合金具有较高的强度和 耐热性能;但密度大,耐蚀性能和铸造性能较差, 易产生热裂,常用于制造较高温度下(<300℃) 工作的高强度的零件,如内燃机气缸头、增压器 导风叶轮等。
3)Al-Mg(≥5%Mg)该系合金具有优异的耐蚀 性、强度高、密度小、切削及抛光性能也较好; 但其铸造性能差,合金液易氧化,熔炼和铸造工 艺较复杂。主要用于制造在大气和海水中工作的 耐腐蚀性高且承受一定冲击载荷、形状较简单的 零件,如船舶配件和机械壳体等。
提高Al—Si合金性能的主要处理措施探究

提高Al—Si合金性能的主要处理措施探究【摘要】铸造铝合金主要有Al-Si、Al-Cu、Al-Mg、Al-Zn四类,其中Al-Si 类合金(Si≥5%)在工业上应用的时间虽然比Al-Cu类合金晚,但它具有优良的铸造性能,如收缩率小、流动性好、气密性好和热裂倾向小等,经过变质处理之后,还具有很好的力学性能、物理性能和切削加工性能,因而成为铸造铝合金中品种最多,用量最大的合金。
【关键词】Al-Si合金;变质处理;铸造性能;加工性能;时效处理;双重变质0 引言铝的密度小、塑性好,具有优良的导电性和导热性,表面有致密的氧化膜保护,抗腐蚀性好,而且回收成本低,是一种可持续发展的有色金属。
在纯铝中,加入其它金属或非金属元素,能配制成各种可供压力加工或铸造用的铝合金。
1 Ai-Si合金的变质处理1.1 Al-Si合金共晶体的变质共晶成分的合金组织,通过加Na、Sr及Sb等变质处理,使共晶硅由原来的粗片状变为珊瑚状。
由于组织显著变化,合金的室温力学性能特别是伸长率得到很大的提高,切削加工性能也有明显改善。
近些年来,运用现代测试技术的观察结果,对Na变质机理提出了两种理论:Si晶粒的成长受抑制理论和Si晶核的生成受到抑制理论。
1.2 Al-Si合金初晶硅的变质Al-Si合金随着含硅量的增加,虽然铸造性能得到改善,但组织中出现针片状的共晶硅。
因此,Al-Si合金当含硅量高于6-8%时,必须进行变质处理。
当含硅量超过共晶成分(12.6%)后,组织中出现粗大的多角形板状初晶硅,在Si 相尖端和棱角处引起应力集中,合金容易沿晶粒的边界处,或者板状硅本身开裂处而形成裂纹,使合金变脆,力学性能特别是伸长率显著降低。
1.3 双重变质加磷能有效细化初晶硅,但不能细化共晶组织,如果能同时细化共晶组织,则还能提高力学性能,尤其是伸长率。
这种变质就称为“双重变质”,对于含硅量是在16%以下的合金,细化共晶组织,具有重要意义。
Al-Si合金的拉伸强度主要受合金中初晶硅的尺寸和形状的影响,而延伸率主要受合金中共晶组织的影响。
铝合金精炼新工艺

文章编号:100726077(2006)032029203铝合金精炼新工艺[俄罗斯]В.Л.Найдек等摘 要:本文介绍了使用预热和冷态下的气体-试剂对铝合金熔液进行精炼的工艺和精炼效果。
关键词:铝合金;精炼;工艺中图分类号:TG 27 文献标识码:B 为了精炼铝合金,使用在金属液(下称熔液)中分解时会析出氯气的试剂,例如,加入“除气剂”片剂中的六氯乙烷。
但是氯气具有很高的化学活性,会造成设备腐蚀,处理时会使大量金属损失,以及污染环境。
这一切均会导致逐步停止使用除气剂。
为了精炼,同时还需要使用各种熔剂,以便除去熔液中的各种气体和氧化夹杂物,改善显微组织以及为使金属获得特殊的性能而起某种作用。
为了处理铝合金而使用熔剂,会伴随着向大气中散发有害的氯和氟的化合物。
由此又产生了与安全技术和环境保护有关的难题。
ФТИМС(化合物研究所)研制出了1种新的用除气混合物来处理铝合金的工艺。
这种除气混合物可以有效地去除熔液中的氢气、氧化夹杂物及钠和镁的有害杂质。
其中的1项工艺是用РФ-1片剂和胶丸来处理熔液。
实践表明,试剂的用量为0.1%~0.15%时,可以使铝合金获得非常好的除去氢和氧化夹杂物的精炼效果。
根据对合金提出的要求,在РФ-1片剂的成分中要添加变质剂(T i ,B ,Z r 等)。
在精炼时,将片剂放入送气管中,在送气管中导入氩气或氮气,将片剂送入熔液中。
在金属温度为1000~1020K 时试剂会完全分解成各个组分。
这些组分以气化状态与精炼气体一起经过送气管的孔进入熔液。
在生产条件下,AK 7铝合金的精炼是在箱式电炉中进行的,处理时的温度为1030K 。
熔液按图1,b 所示的方式进行处理。
在蒸发室中向多喷嘴的T 型送气管中加入0.5kg 的试剂。
接通电磁开关,打开送气管中的氩气的通道,并将送气器浸入熔池。
质量为5t 、深度为0.6m 的熔池,其精炼时间在氩气耗量为0.8m 3Πh 的情况下需要20min 。
铝及铝合金圆铸锭缺陷

铝及铝合金圆铸锭缺陷目录前言………………………………………………………………………………………………………………21.铝及铝合金圆铸锭的表面缺陷 (3)Q001 拉痕、拉裂 (4)Q002 偏析浮出物(偏析瘤) (5)Q003 冷隔(成层) (6)Q004 弯曲 (7)Q005 竹节 (8)2.铝及铝合金圆铸锭的内部组织缺陷 (9)Q006 晶内偏析 (10)Q007 逆偏析 (11)Q008 非金属夹杂 (12)Q009氧化膜 (13)Q010 白斑 (14)Q011疏松 (15)Q012 气孔 (17)Q013 光亮晶粒 (18)Q014 羽毛状晶 (19)Q015 粗大晶粒 (20)Q016 过烧 (21)3.铝及铝合金圆铸锭的裂纹缺陷 (22)Q017 冷裂纹 (23)Q018 热裂纹 (24)前言1.在铝及铝合金的熔铸生产过程中,产生的各种缺陷,主要可分为三类,即圆铸锭的表面缺陷、圆铸锭的内部组织缺陷、圆铸锭的裂纹缺陷。
2.圆铸锭的表面缺陷,在生产现场产生能够立即发现,出现频度较高。
最主要的有拉痕拉裂、偏析浮出物(偏析瘤)、冷隔(成层)、弯曲、竹节等。
3.圆铸锭的内部组织缺陷,主要有晶内偏析、逆偏析、夹杂、氧化膜、白斑、疏松、气孔、光亮晶粒、羽毛状晶、粗大晶粒、粗晶硅、过烧等,这些缺陷往往使整根、整批产品报废,必须注意防止,特别是工业铝材的生产中应该特别注意。
4.圆铸锭的裂纹缺陷,按形成机理可分为冷裂纹、热裂纹两种,也有冷裂纹和热裂纹的混合裂纹。
裂纹缺陷属于致命缺陷,生产中必须严格控制;5.下面以列表的方式对各种缺陷的名称(英文对照按美国AA标准和数据技术语篇)、起因、定义、特征及对策进行较为全面的说明,供广大技术人员、生产人员、质检人员作为工作和学习参考。
1.铝及铝合金圆铸锭的表面缺陷铝合金圆铸锭的表面缺陷,大都在铸造过程中产生。
最主要的有拉痕、拉裂、偏析浮出物、冷隔(成层)、铸锭弯曲、竹节等。
铝合金阳极氧化缺陷明细表
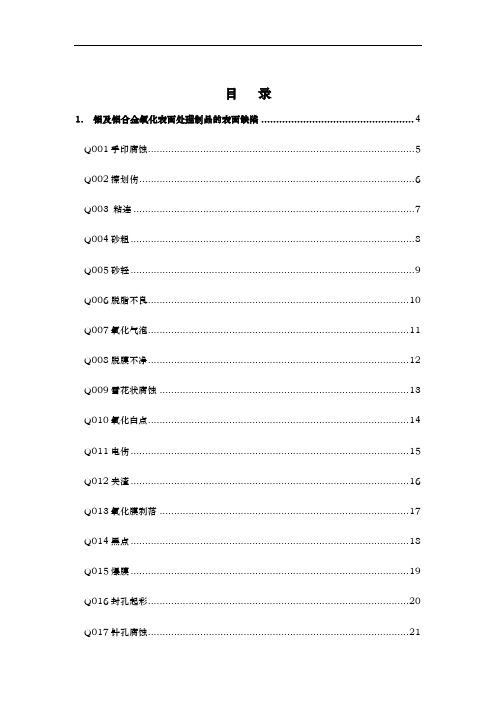
目录1.铝及铝合金氧化表面处理制品的表面缺陷 (4)Q001手印腐蚀 (5)Q002擦划伤 (6)Q003 粘连 (7)Q004砂粗 (8)Q005砂轻 (9)Q006脱脂不良 (10)Q007氧化气泡 (11)Q008脱膜不净 (12)Q009雪花状腐蚀 (13)Q010氧化白点 (14)Q011电伤 (15)Q012夹渣 (16)Q013氧化膜剥落 (17)Q014黑点 (18)Q015爆膜 (19)Q016封孔起彩 (20)Q017针孔腐蚀 (21)Q018色差 (22)Q019酸碱水腐蚀 (23)Q020封孔起灰 (24)Q021无漆膜 (25)Q022麻点 (26)Q023电泳气泡 (27)Q024氧化膜粉化 (28)Q025 复合膜发黄 (29)Q026凝胶粘附 (30)Q027漆留痕 (31)Q028水斑 (32)2.氧化表面处理制品的外观性能缺陷 (33)Q029封孔不合格 (34)Q030氧化膜厚度不达标 (35)Q031漆膜铅笔硬度不达标 (36)Q032漆膜耐腐蚀性不合格 (37)3.氧化表面处理制品的尺寸精度 (38)Q033扎线痕超标 (39)Q034返工壁厚薄 (40)前言1.在铝及铝合金的氧化生产过程中,产生的各种缺陷,主要可分为三类,即氧化表面处理制品的表面缺陷、氧化表面处理制品的形位尺寸缺陷、氧化表面处理制品的外观性能缺陷。
2.氧化表面处理制品的表面缺陷,在生产现场产生最多,废品率也最高。
最主要的有手印腐蚀、擦划伤、粘连、砂粗、砂轻、脱脂不良、氧化气泡、脱膜不净、雪花状腐蚀、氧化白点、电伤、夹渣、氧化膜剥落、麻点、爆膜、封孔起彩、针孔腐蚀、色差、酸碱水腐蚀、封孔起灰、无漆膜、麻点、电泳气泡、氧化膜粉化等。
3.氧化表面处理制品的尺寸缺陷,在生产中所占废品率不多,主要有返工壁厚薄、扎线痕超标等。
4.氧化表面处理制品的外观性能缺陷主要有封孔不合格、氧化膜厚度不达标、漆膜铅笔硬度不达标、漆膜耐腐蚀性不达标等5.下面以列表的方式对各种缺陷的名称(英文对照按美国AA标准和数据技术语篇)、起因、定义、特征及对策进行较为全面的说明,供广大技术人员、生产人员、质检人员作为工作和学习参考。
铝合金压铸件气泡产生的原因

铝合金压铸件气泡产生的原因
铝合金压铸件气泡产生的原因有以下几点:
1. 金属液在压射室充满度过低,易产生卷气,初压射速度过高。
2. 模具浇注系统不合理,排气不良。
3. 熔炼温度过高,含气量高,溶液未除气。
4. 模具温度过高,流模时间不够。
金属凝固时间不足,强度不够过早开模,受压气体膨胀起来。
5. 脱模剂、注射头油用量过多。
6. 喷涂后吹气时间过短,模具表面未吹干。
7. 挤压筒、挤压垫磨损超差或尺寸配合不当,两个垫片的直径差超过允许值。
8. 挤压筒和挤压垫太脏,沾有油污、水分、石墨等。
9. 润滑油中含有水。
10. 铸锭表面铲槽太多,过深;或铸锭表面有气孔、砂眼、组织疏松、油污、铸锭氢含量高等。
11. 更换合金时未清理干净。
12. 挤压简化温度和挤压铸锭温度过高。
13. 铸锭尺寸超过允许负偏差。
14. 铸锭过长,填充太快,铸锭温度不均,导致非鼓形填充。
因此,气缸内排气不完全,或操作不当,排气过程未执行。
15. 模孔设计不合理,或切残科不当,分流孔和导流孔中的残科被部分带出,挤压时空隙中的气体进入表面。
为消除气泡,需要严格操作,正确剪切残科和完全排气。
同时,也可以咨询专业人士获取帮助。
铝合金铸造件检验技术标准(企业标准) 20171223

Q/HX 江西华讯实业有限公司企业标准Q/HX001-2013 铝合金铸造件检验技术标准江西华讯实业有限公司企业标准Q/HX001-2013前言本《铝合金铸造件检验技术标准》依据国家标准及汽车零部件生产行业标准要求,结合我公司实际情况编制,旨在对我公司的质量管理提供企业内控标准,明确了铝合金铸造检验技术要求,它适用于我公司汽车发动机用铝合金铸造件进气歧管、进气接管等铸件的毛坯铸造、检验及毛坯外协件的采购和质量管理。
本《铝合金铸造件检验技术标准》由江西华讯实业有限公司提出,由技术部起草,管理者代表、技术副总及生产副总审核,总经理批准发布后开始实施。
所有外协铝合金铸造件厂家毛坯铸造、毛坯进厂检验、机械加工过程检验、及产品出厂检验的质量控制必须以本标准作为依据,确保本公司产品质量符合顾客要求,让顾客满意。
本《铝合金铸造件检验技术标准》起草人:审核人:批准人:江西华讯实业有限公司企业标准Q/HX001-2013铝合金铸造件检验技术标准1 内容及适用范围本标准根据GB/T 1173-1995及GB/T 9438-1999的相关内容,规定了铝合金铸件的分类和铸件的外观质量、内在质量以及铸件修补等内容的技术要求与检验规则等。
本标准适用于我公司采用金属型铸造所生产的进气歧管系列、进气接管系列等铸件。
根据产品的性能要求、工作条件、使用寿命以及在使用过程中如果损坏,所能造成的危害程度,将铝合金铸件分类如下:2 引用标准2.1 GB/T 1173-1995《铸造铝合金技术条件》2.2 GB/T 9438-1999《铝合金铸件技术条件》2.3 GB/T 1.1-2000《标准化工作导则标准的结构和编写规则》2.4 GB/T 6414-1999《铸件尺寸公差与机械加工余量》2.5 GB/T 6060.1-1997《表面粗糙度比较样块铸造表面》2.6 GB/T 228-2002《金属材料室温拉伸试验方法》2.7 JB/T 7946-1999《铸造铝合金金相》2.8 GB 1198《铝化学分析方法》3 技术要求3.1 化学成分3.1.1合金的化学成分根据GB/T 1173-1995的规定,应符合表3-1及表3-2的规定。
液态成形工艺与原理作业与思考题答案(部分)

第二讲1、哪些现象说明金属的熔化并不是原子间结合力的全部破坏?答:以下现象说明金属的熔化并不是原子间结合力的全部破坏:(1)物质熔化时体积变化、熵变(及焓变)一般均不大。
[注意:简答题此部分可略:如金属熔化时典型的体积变化△Vm/V(多为增大)为3~5%左右,表明液体原子间距接近于固体,在熔点附近其系统混乱度只是稍大于固体而远小于气体的混乱度。
](2)金属熔化潜热比其汽化潜热小得多(1/15~1/30),表明熔化时其内部原子结合键只有部分被破坏。
2、实际液态金属的结构是怎样的?3、名词解释:能量起伏、结构起伏、浓度起伏、粘度、运动粘度、雷诺数、层流、紊流、表面张力和表面能。
答:雷诺数:流体流动时的惯性力Fg和粘性力(内摩擦力)Fm之比称为雷诺数。
用符号Re 表示。
Re是一个无因次量。
层流:流体流动时,如果流体质点的轨迹(一般说随初始空间坐标x、y、z和时间t而变)是有规则的光滑曲线(最简单的情形是直线),这种流动叫层流。
紊流:在一定雷诺数下,流体表现在时间和空间上的随机脉动运动,流体中含有大量不同尺度的涡旋(eddy)。
4、分析粘度的影响因素及其对粘度的影响规律。
5、分析表面张力的影响因素及其对表面张力的影响规律。
第三讲1、流动性与充型能力的联系和区别。
答:区别:①二者概念不同。
铸造工艺学中的流动性指液态金属本身的流动能力,常用规定的铸型条件和浇注条件下的试样的长度或薄厚尺寸来衡量;而充型能力是指液态金属充满铸型型腔,并使铸件形状完整、轮廓清晰的能力。
②影响因素有区别。
流动性是液态金属本身的流动能力,与金属的成分、温度、杂质含量,及其物理性质有关;而充型能力除了取决于金属本身的流动能力外,还受外界条件,如铸型性质、浇注条件、铸件结构等因素的影响。
联系:都是影响成形产品质量的因素。
①流动性好的合金充型能力强;流动性差的合金充型能力亦差,但是,可以通过改善外界条件提高其充型能力。
②可认为合金的流动性是在确定条件(试样结构、铸型性质、浇注条件)下的充型能力。
铝合金铸造熔炼浇注工序颗粒物成分

铝合金铸造熔炼浇注工序颗粒物成分
铝合金铸造熔炼浇注工序中产生的颗粒物主要由以下几个部分组成:
1. 金属颗粒:这是最大的部分,主要是熔融的铝合金冷却后形成的固态颗粒。
这些颗粒可能包含铝合金的所有元素,包括铝、硅、镁、铜、铁、锰、锌、镉、铅等。
2. 氧化物和硫化物:在熔炼过程中,金属表面可能会氧化或硫化,形成氧化物和硫化物颗粒。
这些颗粒主要由氧和硫与金属反应形成。
3. 烟气颗粒:在熔炼过程中,可能会产生一些烟气,这些烟气在冷却后会形成烟气颗粒。
这些颗粒主要含有炭黑、重金属颗粒物和其他有害物质。
4. 非金属夹杂物:在熔炼和浇注过程中,可能会混入一些非金属物质,如砂粒、灰尘、油脂等,形成非金属夹杂物。
5. 其他杂质:在熔炼和浇注过程中,可能会混入一些其他物质,如化学添加剂、油脂、水分等,形成其他杂质。
这些颗粒物可能会影响铝合金的性能,如强度、硬度、耐腐蚀性等,因此需要在铸造过程中进行有效控制。
铝合金精炼
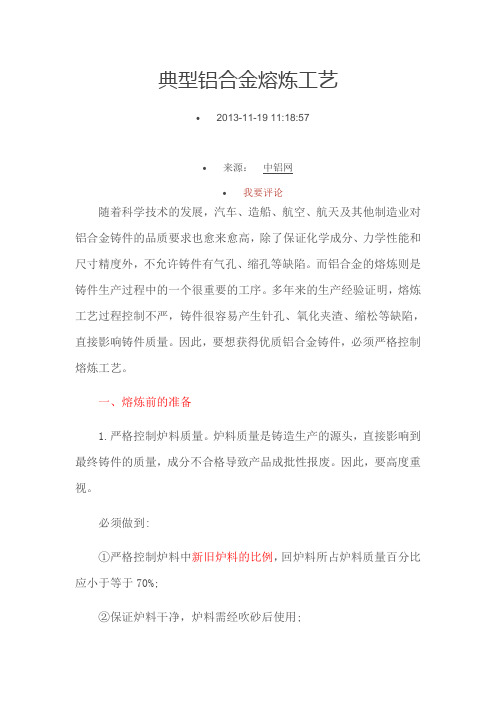
典型铝合金熔炼工艺∙2013-11-19 11:18:57∙来源:中铝网∙我要评论随着科学技术的发展,汽车、造船、航空、航天及其他制造业对铝合金铸件的品质要求也愈来愈高,除了保证化学成分、力学性能和尺寸精度外,不允许铸件有气孔、缩孔等缺陷。
而铝合金的熔炼则是铸件生产过程中的一个很重要的工序。
多年来的生产经验证明,熔炼工艺过程控制不严,铸件很容易产生针孔、氧化夹渣、缩松等缺陷,直接影响铸件质量。
因此,要想获得优质铝合金铸件,必须严格控制熔炼工艺。
一、熔炼前的准备1.严格控制炉料质量。
炉料质量是铸造生产的源头,直接影响到最终铸件的质量,成分不合格导致产品成批性报废。
因此,要高度重视。
必须做到:①严格控制炉料中新旧炉料的比例,回炉料所占炉料质量百分比应小于等于70%;②保证炉料干净,炉料需经吹砂后使用;③三等回炉料枷浇冒口匀使用前应经重熔精炼处理;④炉料应充分预热,去除水分、油污等杂质;⑤由于铭合金有铝硅类、铝铜类、铝镁类等合金,合金牌号较多,使用的元素也比较多,且互相影响,要求严格管理,不可混料;⑥配料、称量要准确,比如ZL104合金,考虑到除气、排渣及变质过程中的损耗,Mg元素应在实际配料时多加炉料质量的0.02%-0.03%,才能保证铸件的化学成分。
2.熔炼工具。
熔炼使用的址涓及熔炼工具须清理干净且涂上涂料,以保证使用时与铝合金有效隔离,减少合金液受到杂质污染,并且需要充分预热,址涓要烘烤至暗红色再加入炉料熔炼,以防水蒸气带入合金中使合金的气体增加、针孔度增加。
3.其他工作。
严格按已制订好的工艺规范作好覆盖剂、精炼剂及变质剂的准备工作。
二、熔炼操作熔炼步骤如下。
①装料。
在预热后的柑A中装入预制合金锭、优质回炉料,再加中fol合金,最后加合金元素。
②温度控制。
严格控制铝合金熔炼的温度,只有合适的温度才能获得高质量的合金液,避免过热。
若温度过高,会加大合金中各种元素的氧化烧损,引起合金中化学成分的变化。
001铸造铝合金中的气体和氧化夹杂

1997年第18卷第1期华 北 工 学 院 学 报V o l.18 N o.1 1997 (总第57期)JOURNAL OF NORTH CH INA INSTITUTE OF TECHNOLOG Y(Sum N o.57)铸造铝合金中的气体和氧化夹杂ΞΞΞ何 峰 程 军(华北工学院,太原030051)摘 要 本文就铝合金铸件中气孔和夹杂物的形成过程以及它们对铝合金铸件质量的影响进行了详细的分析.同时,就有关铝熔体中气体和夹杂物相互作用的各种理论和观点进行了综述.关键词 铸造;铝合金;氧化;夹杂;气体分类号 T G292铝及其合金在熔炼、浇铸过程中表现出易于氧化、吸收气体的特性,使得在铝液中极易形成气体和夹杂物,从而引起铸件的气孔、缩孔、缩松、裂纹、浇不足和渗漏等一系列缺陷,显著降低了材料的强度、塑性、疲劳抗力、耐蚀性能等,甚至造成铸件报废,直接影响了产品的质量,从而使铝合金的应用受到很大的限制.因此,研究铝及其合金中气体和夹杂物的行为,弄清气体和夹杂物影响铝铸件质量的机理,以及如何从熔铸工艺着手,采取积极有效的措施,最大限度地减少气体和夹杂物对铝铸件质量的影响,是铸造工作者应着力解决的一项重要课题.1 铝合金中的气体111 气体的来源和铸件中气孔的形成科学实验和生产实践证明,铝液中的氢主要来自铝液与水汽的反应3A l(液)+3H2O(汽)=A l2O3+3H2(1) 由热力学计算可知,在该体系中,即使p HO很小,与之相平衡的p H2也会很大,当T2=1000K时,在干空气条件下(p HO=2159×10-20M Pa),水汽就能与铝液发生反应[1,2].2也就是说,任何经过烘干的炉料、工具、熔剂和砂型对铝液来说都是潮湿的,其中残余的水份都足以引起该反应的发生,因此铝液中总有一定数量的氢.由于氢在固态和液态铝合金中的溶解度差别十分悬殊,随着温度下降氢不断析出.通常,铝液以扩散方式析出的氢量是有限的,而氢主要则是以气泡形式析出.形成气泡是一个新相形成的过程,它包括气核的形成和长大两个阶段.有计算表明,若靠自发形Ξ收稿日期:1996207217 第一作者 男 24岁 硕士生 导师:程军ΞΞ“九五”兵总重点预研项目65华 北 工 学 院 学 报1997年第1期核,氢在铝液中的浓度必须超过其在铝液中饱和溶解度的数十倍[3],需克服的附加压力>18kPa,因此气核的自发形成通常是很困难的[4,5].有研究表明[6],铝液中的夹杂物微粒表面不仅具有大量孔洞、空隙和裂纹,而且具有各种不规则的形状,气核在这些地方形成能显著降低形核所需要的能量.因此,冷凝铝液中的气泡往往是以非自发形核方式形核的.当铝液润湿气核材料时,气核的形成条件为p g≥p a+p m+2Ρ R c+p s(2) 当铝液不润湿气核材料时,气核的形成条件为p g≥p a+p m+2ΡsinΗ R c+p s (90°<Η<180°)(3)式中 p g为气泡内气体的压力;p a为铝液所处环境气氛的压力;p m为铝液对气泡的静压力;p s为铝液凝固时因体积收缩而产生的压力,其值为负;Ρ为铝液与气泡界面的表面张力;R c为气核形成的衬底上能成为气核的小孔半径;Η为湿润角.随着铝液中的氢不断向气核中扩散,当气泡长大到一定的临界尺寸,就会脱离形核表面而上浮.而新的气核又可以在同一地点再次形成.此过程中铝液氢浓度的变化,文献[7]作了详细的叙述.计算表明[3]:为使铝液中气泡能及时上浮而排除,其半径一般应大于(10-3~10-2)c m数量级,否则将保留在铸件中形成气孔.另外,有关铝合金铸件中形状各异的气孔,有研究表明这取决于铝液中晶体 枝晶生长对气泡长大过程所产生阻碍作用的大小[6].112 气体对铝铸件质量的影响气孔不仅减少铸件的有效截面积,使金属材料的强度下降,而且在局部形成应力集中,成为材料断裂的裂纹源,降低材料的韧性和疲劳抗力.尤其是当气孔呈细长的裂纹状,且大量集中分布在铸件表面层时,危害最大.对要求承受液压或气压的铸件,若含有气孔,则会明显降低其致密性.以固溶体形式存在的气体,虽然危害较小,但也会降低铸件的韧性.在一定条件下,从固溶体中析出的氢气压力使晶粒间形成须状裂纹.而在合金液凝固时析出的气体,不仅使合金液的流动性降低,而且由于气体的反压力,阻碍了金属液的补缩,形成浇不足、缩松等缺陷[8].2 铝合金中的氧化夹杂211 夹杂物的产生铝液中的非金属夹杂主要是氧化夹杂物,它一部分来源于炉料,而大部分则是在熔化和浇铸过程中形成的.根据夹杂物在熔铸过程中形成的时间,可分为一次氧化夹杂物和二次氧化夹杂物.通常将铝液在浇铸前的熔炼过程中所形成的氧化夹杂物称为一次氧化夹杂物.二次氧化夹杂物是在浇铸、充型过程中形成的.铝液在浇道中的飞溅和紊流,是二次氧化夹杂物形成的主要原因.Cam p bell认为,较大的铝液流动速度(>0.5m s),浇铸、充型过程中铝液的落差以及铝液充型前沿不能得以稳定的保持,都会使铝液中携带入氧化夹杂[9,10].另外,Cam p bell 还提出了新、旧表面膜的概念[11],认为新表面膜形成于浇铸过程中,很薄,只要铸造条件合适,它们在铸件中可以是无害的.旧表面膜则形成于炉内熔体表表1 氧化膜尺寸与下降速度的关系氧化膜尺寸Λm 20406080100下降速度c m m in114516121622143315面或重熔锭 铸件表面,较厚,面积通常也较大,且由于膜强、韧性较高,故能保持其尺寸.一般说来,旧膜聚集对铸件产生的损伤是永久性的.有研究表明,随着温度的升高,铝液的氧化速度以指数形式增长,如温度每升高(10~12)℃氧化率就加倍[12].由于A l 2O 3的密度比铝液的大,因此溶液底部的夹杂物比上部的要多.随着氧化物尺寸的增大,其下降速度也增大,由计算可得如下数据[3],见表1.212 夹杂物对铝铸件性能的影响由于大多数夹杂物与金属基体在弹性性能上有较大的差别,所以在金属变形过程中,夹杂物周围就会产生愈来愈大的应力集中,从而使之开裂或使夹杂物同基体的连结遭到破坏,形成显微空隙.随着变形的不断进行,空隙(微裂纹)不断地产生,并发展成为显微空洞,直至相邻的空洞相互连结,而导致材料的断裂.可以认为,夹杂物作为显微裂纹的发源地,对与断裂过程密切相关的诸如延伸率、断面收缩率、断裂韧性和疲劳抗力等一系列材料性能具有显著影响.文献[13]认为,氧化膜实际上就是一种裂纹.铝液中携带的氧化膜在紊流作用下,相互折叠和缠结,当铝液凝固后,在铸件中就形成弯弯曲曲的裂纹路径.可以想象,当这种裂纹路径贯穿铸件的两个表面时,必然导致铸件的渗漏.另外,在腐蚀介质中,由于金属基体与夹杂物的电极电位不同而构成腐蚀电池,引起电化学腐蚀,故夹杂物对材料的耐腐蚀性能也有很大影响.3 铝液中气体与氧化夹杂物的相互作用311 氧化夹杂物对铝液中氢的影响31111 A l 2O 3膜是水汽和氢的良好载体,加剧了铝液的吸氢研究表胆,就A l 2O 3膜而言,只是在其与铝液接触的一面才是致密的,而与空气接触的一面则由于铝液与水汽反应,在铝液表面形成疏松的氧化物组织,这样铝液表面就存在着大量(55~510)nm 的小孔,而在这些小孔中吸附有水汽和氢[1].同时,这种疏松的组织还使氧化膜的强度降低,使其更容易破裂.在熔炼及浇铸过程中铝液的飞溅、紊流,使覆盖在铝液表面的氧化膜破裂,并卷入铝液中,这就使由氧化膜所携带的水汽与铝液发生反应,从而使铝液增杂、增气.31112 氧化夹杂物能吸附铝液中的氢,因而增加了铝液中的含氢量在通常熔炼情况下,铝液中的氢有两种存在形式:(1)以间隙原子的形式溶于铝液75(总第57期)铸造铝合金中的气体和氧化夹杂(何 峰等)中;(2)以氢分子形成吸附于夹杂物的表面或缝隙中.前者约占90%以上,后者约占10%以下[1].因此铝液中氧化夹杂物愈多,所吸附的氢也就愈多,这会使其附近铝液中的氢原子浓度降低,为使体系重新达到平衡,就必须使铝液中溶入更多的氢原子.这样就增加了铝液中的含氢量.但是,夹杂物含量增加并不总是导致铝液含氢量的增加.从表2[3]中可以看出,只有当试样中(10~20)Λm大小的夹杂物含量增加时,铝液中的含氢量才增加.这说明,夹杂物愈细小,其表面活性愈大,对氢的吸附作用也愈强.文献[2]认为这是由于夹杂物的尺寸愈小,能吸附氢的活动中心(称为“窗”)也就愈多的缘故.表2 非金属夹杂物与含氢量间的关系合 金序号非金属夹杂物含量(%)夹杂物尺寸(Λm)及分布(%)102030含氢量c m3 100gA l2101010064133260118 02010173045250120 03010182563120144Z L10301010084141180188 02010215111281126 03010136634-115031113 夹杂物的存在,阻碍铝液的脱氢夹杂物能吸附水汽和氢,因而在夹杂物质点周围存在着吸附力场,力的作用半径可达10-5c m[1],在此吸附力场中,由于氢所受的吸附力方向与扩散脱氢的方向相反,因而降低了扩散脱氢的速度.当氧化夹杂物足够多时(>0101%),吸附力场将相互靠拢并连续地作用于整个铝熔体内部,这将会极大地制约氢原子的扩散,阻碍铝液的脱氢. 31114 夹杂物的存在,促使铝液冷凝时易于形成气孔当铝液中有多量A l2O3时,既增加了铝液的含氢量,又提供了气泡形核的现成界面,促使铸件中易于形成气孔;有人认为[4,14],由A l2O3所提供的气泡形核的现成界面,对铸件中气孔的形成起主导作用.据实验测定,当铝液中的A l2O3含量低于01001%时,铝液中已不再形成氢气泡.因此,由于A l2O3含量不同,尽管铝液含氢量相同,所形成的孔隙度等级也可能不相同.312 铝液中氢与氧化夹杂物的相互作用机制人们公认,铝液中氢与氧化夹杂物之间存在着相互作用,但相互作用的机制至今尚无一致的见解.综合起来主要有:机械作用理论、静电作用理论、吸附理论、非均质形核理论、气窝机制、寄生机制及复合物理论等.下面就这些理论和观点进行分析讨论.据文献[15]介绍,铝液中的氢在氧化夹杂物附近形成气泡,气体对氧化铝起着“气伞”的作用.氧化夹杂物的作用仅在于使气泡形核,其相互联系是机械的联系.有人认为[3],在带有不同介电常数的两接触相的分界面上将产生接触电势.具有小介电常数的带负电,而具有大介电常数的则带正电.氧化夹杂物与铝相比具有较小的介电常数,因此处于铝液内部而带负电.而在夹杂物2金属界面上存在着的势能将促使氢原85华 北 工 学 院 学 报1997年第1期子离化,离化的氢,由于其尺寸很小,很容易分布在整个铝熔体内部.当氢离子进入铝熔体后,带负电的夹杂物将靠近它.这种电离观点阐述了氧化夹杂与氢的同时存在,并已为直流电除氢的试验所证实.吸附学说是静电作用理论的延续,大致有以下两种观点[1]:大多数学者认为:铝液中存在对氢显活性的氧化夹杂物,因而能形成对氢的吸附作用.当气相2铝液2氧化夹杂物体系建立平衡时,这个过程就结束了.铝液中增加的含气量等于氧化物所吸附的氢量.另一种观点认为:氢被氧化物吸附,导致铝液中氧化物微粒近旁形成富氢微观区域,这仅仅是第一阶段,第二阶段则是在氧化物微粒上形成氢气泡,即形成含氢透镜.铝液凝固时氢透镜与支托它们的氧化物微粒一起转移到固体金属中,形成氢气孔.关于非均质形核理论,很多文献[2,4,6,14]认为,铝铸件中气孔的形成,主要是由于存在着氧化夹杂物,氢原子可以吸附在氧化夹杂物上,氧化夹杂物可以成为气泡形核的现成界面,能促使气泡的非均质形核和长大.该理论实质上是吸附理论的实际应用.近年来有人又提出气窝机制[16],认为在铝液表面形成的氧化膜,在其与炉气接触的一面疏松多孔,并为氢、水汽等介质所充满.当其被卷入铝液内部后,因氧化膜与铝液润湿性差,藏在小孔中的气体寄居于夹杂物和铝液中间(从而形成了气窝),这样就在气窝内部氧化膜2铝液之间形成了一个氢的浓度梯度(已为检验氢的分布所证实).平衡后,在氧化膜附近的铝液中存在着一个氢的浓度梯度.文献[2]还提出了一种寄生机制,认为在铝液中,由于夹杂和氢浓度及能量起伏的存在,在微片状的A l 2O 3周围将会出现非平衡状态的微观富氢区域,进而在夹杂和气之间所形成“综合聚积力场”(诸如接触电势场、静电力场、吸附力场、化学能和物理能等)的作用下,氢将不断地向夹杂的方向迁移,当聚积到一定量的分子体积后,借助夹杂的现成界面寄生形核.气核形成后,造成外层空间中氢的浓度梯度,由于扩散平衡的结果,促使寄生于夹杂物上的气核长大,形成气泡.此外,还有人认为[1,17]:A l 2O 3和氢在铝液中能形成复合物m Χ2A l 2O -3n H +,因而除了溶解于铝液中的氢以外,还有复合物中所包含的氢,这样铝液中的含氢量相应也就增加了.此观点目前还只是一种假设,尚有待于进一步研究.4 结论及展望(1)铝液中所溶解的气体主要是氢,而在铝液熔铸过程中形成的氧化夹杂物,则是铝液中夹杂物的主体.(2)铝熔体中的气体和夹杂物是造成铝铸件缺陷的重要原因:一则其本身就是造成铸件破坏的起源(裂纹源、渗漏源和腐蚀源),而且它们在铝液凝固、补缩过程中的行为还会影响所获得铸件内部和外部的质量.(3)铝液中气体和夹杂物是相互作用的,其作用机制主要是吸附作用.铝液中悬浮着的氧化夹杂物吸附着氢,并制约着氢的扩散脱除,同时还能为氢析出时气核的形成提供现成的界面.其结果是“杂多气多”,这是氢难以除净的根本原因.因此在铝液净化工艺上,应以除杂为主,辅以除气,遵循除气必须除杂,除杂是除气的基础的技术路线.95(总第57期)铸造铝合金中的气体和氧化夹杂(何 峰等)06华 北 工 学 院 学 报1997年第1期在关于铝合金中氧化夹杂和氢的研究目前尚有许多问题需作进一步的探讨:(1)对铝熔体中氧化夹杂和氢的来源以及它们的相互作用机制尚有待于进一步研究和认识;(2)有必要对氧化夹杂和氢在铝液冷凝、补缩过程中的行为及其对铸件质量的影响作进一步的研究;(3)有必要对铝液的净化机理作更为深入的研究,以开发出新型的净化方法;(4)迫切需要研究能快速、准确、经济地评定铝液质量的方法;(5)必须对能避免或尽量减少铝液在熔铸过程中被氢和氧化夹杂污染的,并能生产出优质铝合金铸件的新型铝合金熔铸工艺和技术作更为深入的研究.参考文献1 杨长贺,高钦.有色金属净化.大连:大连理工大学出版社,19892 康积行,傅高升.铝熔体中夹杂物和气体的行为.特种铸造及有色合金,1995,(5):5~83 王肇经,李东升.铸造铝合金的气体和非金属夹杂物.北京:兵器工业出版社,19894 边秀房.铝合金的渣2气孔.特种铸造及有色合金,1990,(2):15~215 朱培钺,刘贤功等译.铸造金属中的气体.北京:机械工业出版社,19846 Chen X G,Engler S.Fo rm ati on of gas po ro sity in alum in ium alloys.A FS.T ran s.,1994,102.673~6827 Zou J.M odeling of m icro structu re evo lu ti on and m icropo ro sity fo rm ati on in cast alum in ium alloys.A FS.T ran s.,1990,98.871~8778 张成林.金属净化技术.哈尔滨:哈尔滨船舶工程学院出版社,19899 Campbell J.P lann ing the21st cen tu ry casting p rocess.Foundrym an,1993,86.329~33410 Campbell John.Castings.Bu tterw o rth2H einem ann,199111 Campbell J,杨小永译.薄壁铸件.轻合金加工技术,1990,18(2).17~2812 L essiter M J.U nderstanding inclu si on s in alum in ium castings.M odern casting,1993,83.29~31 13 Green N R,Campbell J.Influence of ox ide fil m filling defects on the strength of A l27Si2M g alloy castings.A FS.T ran s.,1994,102.341~34714 L aslaz G.Gas po ro sity and m etal clean liness in alum in ium casting alloys.A FS.T ran s.,1991,99.83~9015 高泽生.国外铝合金精炼工艺技术的进展.轻金属,1978,(4):27~2916 傅高升.铝熔体熔剂净化机制与杂气关系:[福州大学硕士论文].福州:福州大学,199117 张成甫等.液态金属的净化与变质.上海:上海科技出版社,1989GA S AND O X I D I C I N CLU S I ON S I N CA ST ALUM I N I UM ALLO YSH e F eng Cheng J un(N o rth Ch ina In stitu te of T echno logy,T aiyuan030051)Abstract In th is p ap er,bo th the p rocess that the gas and inclu si on s in m o ltenalum in ium com e in to being and the influence effected by them on quality andp rop erties of alum in ium alloy castings are analysed in detail.M o reover,vari2ou s k inds of theo ries and view s on in teracti on betw een gas and inclu si on s inm o lten alum in ium are summ arized.Key words foundry;alum in ium alloys;ox idati on;inclu si on s;gas。
铝箔坯料铸轧工艺缺陷分析及处理方法

铝箔坯料铸轧工艺缺陷分析及处理方法范培卿【摘要】介绍了用电解铝液直接铸轧铝箔坯料的特点,分析了电解铝液直接铸轧铝箔坯料工艺过程以及常见的工艺缺陷和处理方法.【期刊名称】《轻合金加工技术》【年(卷),期】2014(042)003【总页数】4页(P24-27)【关键词】电解铝液;铝箔坯料;熔铸工艺;工艺缺陷【作者】范培卿【作者单位】烟台南山学院,南山轻合金有限公司,山东龙口265713【正文语种】中文【中图分类】TG2921 铸轧工艺1951年美国亨特、道格拉斯(Hunter,Douglas)两家公司首次将下注式双辊铸轧机用于铝板坯的生产,创立了铸轧工艺。
因下注式铸轧机供料嘴安装调整十分不便,1962年亨特公司提出了铸轧辊中心线与水平线成15°夹角的倾斜式铸轧机,继而法国的斯卡尔(Scal)公司研制出称之为3C法(Continuous Caster Between Cylinders)的双辊水平式铸轧机,进一步完善了铸轧工艺。
铸轧工艺是将金属铝液直接引入两个内部水冷却的旋转轧辊间隙,结晶凝固、变形后从轧辊的另一边引出带坯的方法。
它将铸造和轧制等一系列复杂的生产工艺融为一体。
利用电解铝液直接铸轧省去了铝锭的重熔和铸造工序,节约能源,提高了生产效率和成品率。
在生产实践中,一般重熔铝锭的烧损在2%左右,而电解铝液的烧损在0.5%左右(主要是氧化夹渣等)。
但受铸轧机冷却区域长度和冷却强度限制,铸轧工艺生产的材料范围较窄、热变形量小、深冲性不好、箔材轧制时易断带,这些问题限制了铸轧带坯的广泛应用。
2 直接用电解铝液生产铸轧坯料的工艺流程电解铝液铸轧坯料的工艺流程示于图1。
3 电解铝液直接铸轧的缺陷3.1 铝液温度过高,易吸气,含氢量大经测量,注入混合炉中的电解铝液含氢量在0.26 mL/(100 gAl)以上,超过了铝箔坯料含氢量在0.12 mL/(100 gAl)以下的规定。
3.2 铝液中含渣量大由于电解铝液没有经过用铝锭熔炼铸造过程中的净化工艺,虽然电解铝液在抽吸前经过除渣处理,但在铝液抽吸过程仍有一些电解质及氧化夹渣物进入铝液中,故含渣量大。
- 1、下载文档前请自行甄别文档内容的完整性,平台不提供额外的编辑、内容补充、找答案等附加服务。
- 2、"仅部分预览"的文档,不可在线预览部分如存在完整性等问题,可反馈申请退款(可完整预览的文档不适用该条件!)。
- 3、如文档侵犯您的权益,请联系客服反馈,我们会尽快为您处理(人工客服工作时间:9:00-18:30)。
1997年第18卷第1期华 北 工 学 院 学 报V o l.18 N o.1 1997 (总第57期)JOURNAL OF NORTH CH INA INSTITUTE OF TECHNOLOG Y(Sum N o.57)铸造铝合金中的气体和氧化夹杂ΞΞΞ何 峰 程 军(华北工学院,太原030051)摘 要 本文就铝合金铸件中气孔和夹杂物的形成过程以及它们对铝合金铸件质量的影响进行了详细的分析.同时,就有关铝熔体中气体和夹杂物相互作用的各种理论和观点进行了综述.关键词 铸造;铝合金;氧化;夹杂;气体分类号 T G292铝及其合金在熔炼、浇铸过程中表现出易于氧化、吸收气体的特性,使得在铝液中极易形成气体和夹杂物,从而引起铸件的气孔、缩孔、缩松、裂纹、浇不足和渗漏等一系列缺陷,显著降低了材料的强度、塑性、疲劳抗力、耐蚀性能等,甚至造成铸件报废,直接影响了产品的质量,从而使铝合金的应用受到很大的限制.因此,研究铝及其合金中气体和夹杂物的行为,弄清气体和夹杂物影响铝铸件质量的机理,以及如何从熔铸工艺着手,采取积极有效的措施,最大限度地减少气体和夹杂物对铝铸件质量的影响,是铸造工作者应着力解决的一项重要课题.1 铝合金中的气体111 气体的来源和铸件中气孔的形成科学实验和生产实践证明,铝液中的氢主要来自铝液与水汽的反应3A l(液)+3H2O(汽)=A l2O3+3H2(1) 由热力学计算可知,在该体系中,即使p HO很小,与之相平衡的p H2也会很大,当T2=1000K时,在干空气条件下(p HO=2159×10-20M Pa),水汽就能与铝液发生反应[1,2].2也就是说,任何经过烘干的炉料、工具、熔剂和砂型对铝液来说都是潮湿的,其中残余的水份都足以引起该反应的发生,因此铝液中总有一定数量的氢.由于氢在固态和液态铝合金中的溶解度差别十分悬殊,随着温度下降氢不断析出.通常,铝液以扩散方式析出的氢量是有限的,而氢主要则是以气泡形式析出.形成气泡是一个新相形成的过程,它包括气核的形成和长大两个阶段.有计算表明,若靠自发形Ξ收稿日期:1996207217 第一作者 男 24岁 硕士生 导师:程军ΞΞ“九五”兵总重点预研项目65华 北 工 学 院 学 报1997年第1期核,氢在铝液中的浓度必须超过其在铝液中饱和溶解度的数十倍[3],需克服的附加压力>18kPa,因此气核的自发形成通常是很困难的[4,5].有研究表明[6],铝液中的夹杂物微粒表面不仅具有大量孔洞、空隙和裂纹,而且具有各种不规则的形状,气核在这些地方形成能显著降低形核所需要的能量.因此,冷凝铝液中的气泡往往是以非自发形核方式形核的.当铝液润湿气核材料时,气核的形成条件为p g≥p a+p m+2Ρ R c+p s(2) 当铝液不润湿气核材料时,气核的形成条件为p g≥p a+p m+2ΡsinΗ R c+p s (90°<Η<180°)(3)式中 p g为气泡内气体的压力;p a为铝液所处环境气氛的压力;p m为铝液对气泡的静压力;p s为铝液凝固时因体积收缩而产生的压力,其值为负;Ρ为铝液与气泡界面的表面张力;R c为气核形成的衬底上能成为气核的小孔半径;Η为湿润角.随着铝液中的氢不断向气核中扩散,当气泡长大到一定的临界尺寸,就会脱离形核表面而上浮.而新的气核又可以在同一地点再次形成.此过程中铝液氢浓度的变化,文献[7]作了详细的叙述.计算表明[3]:为使铝液中气泡能及时上浮而排除,其半径一般应大于(10-3~10-2)c m数量级,否则将保留在铸件中形成气孔.另外,有关铝合金铸件中形状各异的气孔,有研究表明这取决于铝液中晶体 枝晶生长对气泡长大过程所产生阻碍作用的大小[6].112 气体对铝铸件质量的影响气孔不仅减少铸件的有效截面积,使金属材料的强度下降,而且在局部形成应力集中,成为材料断裂的裂纹源,降低材料的韧性和疲劳抗力.尤其是当气孔呈细长的裂纹状,且大量集中分布在铸件表面层时,危害最大.对要求承受液压或气压的铸件,若含有气孔,则会明显降低其致密性.以固溶体形式存在的气体,虽然危害较小,但也会降低铸件的韧性.在一定条件下,从固溶体中析出的氢气压力使晶粒间形成须状裂纹.而在合金液凝固时析出的气体,不仅使合金液的流动性降低,而且由于气体的反压力,阻碍了金属液的补缩,形成浇不足、缩松等缺陷[8].2 铝合金中的氧化夹杂211 夹杂物的产生铝液中的非金属夹杂主要是氧化夹杂物,它一部分来源于炉料,而大部分则是在熔化和浇铸过程中形成的.根据夹杂物在熔铸过程中形成的时间,可分为一次氧化夹杂物和二次氧化夹杂物.通常将铝液在浇铸前的熔炼过程中所形成的氧化夹杂物称为一次氧化夹杂物.二次氧化夹杂物是在浇铸、充型过程中形成的.铝液在浇道中的飞溅和紊流,是二次氧化夹杂物形成的主要原因.Cam p bell认为,较大的铝液流动速度(>0.5m s),浇铸、充型过程中铝液的落差以及铝液充型前沿不能得以稳定的保持,都会使铝液中携带入氧化夹杂[9,10].另外,Cam p bell 还提出了新、旧表面膜的概念[11],认为新表面膜形成于浇铸过程中,很薄,只要铸造条件合适,它们在铸件中可以是无害的.旧表面膜则形成于炉内熔体表表1 氧化膜尺寸与下降速度的关系氧化膜尺寸Λm 20406080100下降速度c m m in114516121622143315面或重熔锭 铸件表面,较厚,面积通常也较大,且由于膜强、韧性较高,故能保持其尺寸.一般说来,旧膜聚集对铸件产生的损伤是永久性的.有研究表明,随着温度的升高,铝液的氧化速度以指数形式增长,如温度每升高(10~12)℃氧化率就加倍[12].由于A l 2O 3的密度比铝液的大,因此溶液底部的夹杂物比上部的要多.随着氧化物尺寸的增大,其下降速度也增大,由计算可得如下数据[3],见表1.212 夹杂物对铝铸件性能的影响由于大多数夹杂物与金属基体在弹性性能上有较大的差别,所以在金属变形过程中,夹杂物周围就会产生愈来愈大的应力集中,从而使之开裂或使夹杂物同基体的连结遭到破坏,形成显微空隙.随着变形的不断进行,空隙(微裂纹)不断地产生,并发展成为显微空洞,直至相邻的空洞相互连结,而导致材料的断裂.可以认为,夹杂物作为显微裂纹的发源地,对与断裂过程密切相关的诸如延伸率、断面收缩率、断裂韧性和疲劳抗力等一系列材料性能具有显著影响.文献[13]认为,氧化膜实际上就是一种裂纹.铝液中携带的氧化膜在紊流作用下,相互折叠和缠结,当铝液凝固后,在铸件中就形成弯弯曲曲的裂纹路径.可以想象,当这种裂纹路径贯穿铸件的两个表面时,必然导致铸件的渗漏.另外,在腐蚀介质中,由于金属基体与夹杂物的电极电位不同而构成腐蚀电池,引起电化学腐蚀,故夹杂物对材料的耐腐蚀性能也有很大影响.3 铝液中气体与氧化夹杂物的相互作用311 氧化夹杂物对铝液中氢的影响31111 A l 2O 3膜是水汽和氢的良好载体,加剧了铝液的吸氢研究表胆,就A l 2O 3膜而言,只是在其与铝液接触的一面才是致密的,而与空气接触的一面则由于铝液与水汽反应,在铝液表面形成疏松的氧化物组织,这样铝液表面就存在着大量(55~510)nm 的小孔,而在这些小孔中吸附有水汽和氢[1].同时,这种疏松的组织还使氧化膜的强度降低,使其更容易破裂.在熔炼及浇铸过程中铝液的飞溅、紊流,使覆盖在铝液表面的氧化膜破裂,并卷入铝液中,这就使由氧化膜所携带的水汽与铝液发生反应,从而使铝液增杂、增气.31112 氧化夹杂物能吸附铝液中的氢,因而增加了铝液中的含氢量在通常熔炼情况下,铝液中的氢有两种存在形式:(1)以间隙原子的形式溶于铝液75(总第57期)铸造铝合金中的气体和氧化夹杂(何 峰等)中;(2)以氢分子形成吸附于夹杂物的表面或缝隙中.前者约占90%以上,后者约占10%以下[1].因此铝液中氧化夹杂物愈多,所吸附的氢也就愈多,这会使其附近铝液中的氢原子浓度降低,为使体系重新达到平衡,就必须使铝液中溶入更多的氢原子.这样就增加了铝液中的含氢量.但是,夹杂物含量增加并不总是导致铝液含氢量的增加.从表2[3]中可以看出,只有当试样中(10~20)Λm大小的夹杂物含量增加时,铝液中的含氢量才增加.这说明,夹杂物愈细小,其表面活性愈大,对氢的吸附作用也愈强.文献[2]认为这是由于夹杂物的尺寸愈小,能吸附氢的活动中心(称为“窗”)也就愈多的缘故.表2 非金属夹杂物与含氢量间的关系合 金序号非金属夹杂物含量(%)夹杂物尺寸(Λm)及分布(%)102030含氢量c m3 100gA l2101010064133260118 02010173045250120 03010182563120144Z L10301010084141180188 02010215111281126 03010136634-115031113 夹杂物的存在,阻碍铝液的脱氢夹杂物能吸附水汽和氢,因而在夹杂物质点周围存在着吸附力场,力的作用半径可达10-5c m[1],在此吸附力场中,由于氢所受的吸附力方向与扩散脱氢的方向相反,因而降低了扩散脱氢的速度.当氧化夹杂物足够多时(>0101%),吸附力场将相互靠拢并连续地作用于整个铝熔体内部,这将会极大地制约氢原子的扩散,阻碍铝液的脱氢. 31114 夹杂物的存在,促使铝液冷凝时易于形成气孔当铝液中有多量A l2O3时,既增加了铝液的含氢量,又提供了气泡形核的现成界面,促使铸件中易于形成气孔;有人认为[4,14],由A l2O3所提供的气泡形核的现成界面,对铸件中气孔的形成起主导作用.据实验测定,当铝液中的A l2O3含量低于01001%时,铝液中已不再形成氢气泡.因此,由于A l2O3含量不同,尽管铝液含氢量相同,所形成的孔隙度等级也可能不相同.312 铝液中氢与氧化夹杂物的相互作用机制人们公认,铝液中氢与氧化夹杂物之间存在着相互作用,但相互作用的机制至今尚无一致的见解.综合起来主要有:机械作用理论、静电作用理论、吸附理论、非均质形核理论、气窝机制、寄生机制及复合物理论等.下面就这些理论和观点进行分析讨论.据文献[15]介绍,铝液中的氢在氧化夹杂物附近形成气泡,气体对氧化铝起着“气伞”的作用.氧化夹杂物的作用仅在于使气泡形核,其相互联系是机械的联系.有人认为[3],在带有不同介电常数的两接触相的分界面上将产生接触电势.具有小介电常数的带负电,而具有大介电常数的则带正电.氧化夹杂物与铝相比具有较小的介电常数,因此处于铝液内部而带负电.而在夹杂物2金属界面上存在着的势能将促使氢原85华 北 工 学 院 学 报1997年第1期子离化,离化的氢,由于其尺寸很小,很容易分布在整个铝熔体内部.当氢离子进入铝熔体后,带负电的夹杂物将靠近它.这种电离观点阐述了氧化夹杂与氢的同时存在,并已为直流电除氢的试验所证实.吸附学说是静电作用理论的延续,大致有以下两种观点[1]:大多数学者认为:铝液中存在对氢显活性的氧化夹杂物,因而能形成对氢的吸附作用.当气相2铝液2氧化夹杂物体系建立平衡时,这个过程就结束了.铝液中增加的含气量等于氧化物所吸附的氢量.另一种观点认为:氢被氧化物吸附,导致铝液中氧化物微粒近旁形成富氢微观区域,这仅仅是第一阶段,第二阶段则是在氧化物微粒上形成氢气泡,即形成含氢透镜.铝液凝固时氢透镜与支托它们的氧化物微粒一起转移到固体金属中,形成氢气孔.关于非均质形核理论,很多文献[2,4,6,14]认为,铝铸件中气孔的形成,主要是由于存在着氧化夹杂物,氢原子可以吸附在氧化夹杂物上,氧化夹杂物可以成为气泡形核的现成界面,能促使气泡的非均质形核和长大.该理论实质上是吸附理论的实际应用.近年来有人又提出气窝机制[16],认为在铝液表面形成的氧化膜,在其与炉气接触的一面疏松多孔,并为氢、水汽等介质所充满.当其被卷入铝液内部后,因氧化膜与铝液润湿性差,藏在小孔中的气体寄居于夹杂物和铝液中间(从而形成了气窝),这样就在气窝内部氧化膜2铝液之间形成了一个氢的浓度梯度(已为检验氢的分布所证实).平衡后,在氧化膜附近的铝液中存在着一个氢的浓度梯度.文献[2]还提出了一种寄生机制,认为在铝液中,由于夹杂和氢浓度及能量起伏的存在,在微片状的A l 2O 3周围将会出现非平衡状态的微观富氢区域,进而在夹杂和气之间所形成“综合聚积力场”(诸如接触电势场、静电力场、吸附力场、化学能和物理能等)的作用下,氢将不断地向夹杂的方向迁移,当聚积到一定量的分子体积后,借助夹杂的现成界面寄生形核.气核形成后,造成外层空间中氢的浓度梯度,由于扩散平衡的结果,促使寄生于夹杂物上的气核长大,形成气泡.此外,还有人认为[1,17]:A l 2O 3和氢在铝液中能形成复合物m Χ2A l 2O -3n H +,因而除了溶解于铝液中的氢以外,还有复合物中所包含的氢,这样铝液中的含氢量相应也就增加了.此观点目前还只是一种假设,尚有待于进一步研究.4 结论及展望(1)铝液中所溶解的气体主要是氢,而在铝液熔铸过程中形成的氧化夹杂物,则是铝液中夹杂物的主体.(2)铝熔体中的气体和夹杂物是造成铝铸件缺陷的重要原因:一则其本身就是造成铸件破坏的起源(裂纹源、渗漏源和腐蚀源),而且它们在铝液凝固、补缩过程中的行为还会影响所获得铸件内部和外部的质量.(3)铝液中气体和夹杂物是相互作用的,其作用机制主要是吸附作用.铝液中悬浮着的氧化夹杂物吸附着氢,并制约着氢的扩散脱除,同时还能为氢析出时气核的形成提供现成的界面.其结果是“杂多气多”,这是氢难以除净的根本原因.因此在铝液净化工艺上,应以除杂为主,辅以除气,遵循除气必须除杂,除杂是除气的基础的技术路线.95(总第57期)铸造铝合金中的气体和氧化夹杂(何 峰等)06华 北 工 学 院 学 报1997年第1期在关于铝合金中氧化夹杂和氢的研究目前尚有许多问题需作进一步的探讨:(1)对铝熔体中氧化夹杂和氢的来源以及它们的相互作用机制尚有待于进一步研究和认识;(2)有必要对氧化夹杂和氢在铝液冷凝、补缩过程中的行为及其对铸件质量的影响作进一步的研究;(3)有必要对铝液的净化机理作更为深入的研究,以开发出新型的净化方法;(4)迫切需要研究能快速、准确、经济地评定铝液质量的方法;(5)必须对能避免或尽量减少铝液在熔铸过程中被氢和氧化夹杂污染的,并能生产出优质铝合金铸件的新型铝合金熔铸工艺和技术作更为深入的研究.参考文献1 杨长贺,高钦.有色金属净化.大连:大连理工大学出版社,19892 康积行,傅高升.铝熔体中夹杂物和气体的行为.特种铸造及有色合金,1995,(5):5~83 王肇经,李东升.铸造铝合金的气体和非金属夹杂物.北京:兵器工业出版社,19894 边秀房.铝合金的渣2气孔.特种铸造及有色合金,1990,(2):15~215 朱培钺,刘贤功等译.铸造金属中的气体.北京:机械工业出版社,19846 Chen X G,Engler S.Fo rm ati on of gas po ro sity in alum in ium alloys.A FS.T ran s.,1994,102.673~6827 Zou J.M odeling of m icro structu re evo lu ti on and m icropo ro sity fo rm ati on in cast alum in ium alloys.A FS.T ran s.,1990,98.871~8778 张成林.金属净化技术.哈尔滨:哈尔滨船舶工程学院出版社,19899 Campbell J.P lann ing the21st cen tu ry casting p rocess.Foundrym an,1993,86.329~33410 Campbell John.Castings.Bu tterw o rth2H einem ann,199111 Campbell J,杨小永译.薄壁铸件.轻合金加工技术,1990,18(2).17~2812 L essiter M J.U nderstanding inclu si on s in alum in ium castings.M odern casting,1993,83.29~31 13 Green N R,Campbell J.Influence of ox ide fil m filling defects on the strength of A l27Si2M g alloy castings.A FS.T ran s.,1994,102.341~34714 L aslaz G.Gas po ro sity and m etal clean liness in alum in ium casting alloys.A FS.T ran s.,1991,99.83~9015 高泽生.国外铝合金精炼工艺技术的进展.轻金属,1978,(4):27~2916 傅高升.铝熔体熔剂净化机制与杂气关系:[福州大学硕士论文].福州:福州大学,199117 张成甫等.液态金属的净化与变质.上海:上海科技出版社,1989GA S AND O X I D I C I N CLU S I ON S I N CA ST ALUM I N I UM ALLO YSH e F eng Cheng J un(N o rth Ch ina In stitu te of T echno logy,T aiyuan030051)Abstract In th is p ap er,bo th the p rocess that the gas and inclu si on s in m o ltenalum in ium com e in to being and the influence effected by them on quality andp rop erties of alum in ium alloy castings are analysed in detail.M o reover,vari2ou s k inds of theo ries and view s on in teracti on betw een gas and inclu si on s inm o lten alum in ium are summ arized.Key words foundry;alum in ium alloys;ox idati on;inclu si on s;gas。