培训教材-表面粗糙度计量
第四章表面粗糙度标准

影响配合性质的稳定性
三、表面粗糙度对零件性能的影响
影响零件的抗腐蚀性
表面越粗糙,凹痕越深于容易聚集腐蚀性物质,使 材料标称锈蚀。 表面粗糙,形成局部接触,使中间存在缝隙。
影响零件的密封性
对零件的外观、测量精度、表面光学性能、导 电导热性能和胶合强度等也有着不同程度的影 响。
第二节 表面粗糙度标准
二、表面粗糙度零件图上的标注
铣
6.3 0.8 3.2 3.2 (5) 3.2
a)
b) 表面粗糙度其它项目的标注
c)
d)
5、标注示例
注在可见 轮廓线上 注在尺寸界线的 延长线上上
注在轮廓 线的延长 线上
注在尺寸界线上
★ 在不同方向的表面上标注时,代号中的数 字及符号的方向必须下图的规定标注。
3.2
2.5
4.0 5.0 8.0 9.0 16.0 20
40
63
补 充 值
0.020 0.032 0.040 0.063 0.080
80
评定参数值的选用
一般尺寸公差、表面形状公差小时,表面粗糙度参 数值也小,但也不存在确定的函数关系。如机床的 手轮或手柄。 一般情况下,它们之间有一定的对应关系,设形状 公差为T,尺寸公差为IT,它们之间的关系可参照 以下对应关系: 若T≈0.6 IT,则Ra≤0.05 IT; Rz≤ 0.2 IT T≈0.4 IT,则Ra≤0.025 IT; Rz≤ 0.1 IT T≈0.25 IT,则Ra≤0.012 IT; Rz≤ 0.05 IT T<0.25 IT,则Ra≤0.15 T; Rz≤ 0.6 T
表面粗糙度培训课件
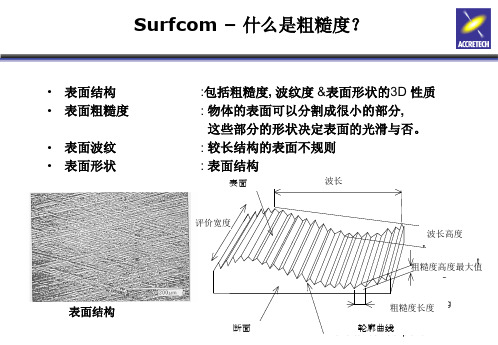
f(x)的绝对值
Ra
轮廓线 f(x)
取样长度 l
波峰波谷高度
• 粗糙度曲线的最大峰高 : Rp
• 粗糙度曲线的最大谷深 : Rv
• 最大高度粗糙度
: Rz (Rp+Rv)
Rp Rz
Rv
取样长度 lr
• 平均最大高度粗糙度 • 最大高度粗糙度 • 粗糙度高度的总高度 • 剖面曲线的最大剖面高度
: Ry, RzDIN : Rzmax, RmaxDIN : Rt : Pt
・ 每个取样长度的 Rz JIS 的平均值
Rz1JIS
R
Rz2JIS
1 5
5 1
1 5
5 | Rz31JIS
Zp
5
| | Zv R1 z4JIS
|
Rz5JIS
Zp2nd
Zp1st
Zp2nd
Zp1st
Zp5th
Zp3rd
Zp4tZh p5th
ISO12085:’96
GPS- 表面结构: 评价轮廓的图形参数
JIS B0631:’00
ISO135651 :’96
GPS- 表面结构: 评价轮廓具有符合加工特征的表面,第 一部分: 滤波 、一般测量条件
JIS B06711 :’02
ISO135652 :’96
GPS- 表面结构:评价轮廓具有符合加工特征的表面,第 二部分: 用线性负荷曲线描述的高度
RSm PSm 形状元素的平均长度 WSm
评价长度中轮廓曲线要素的长度 Xs 的平均 1m
RSm, PSm, WSm = ── ∑ Xsi m I=1
Xs1 Xs2
Xs3
表面粗糙度的培训PPT演示课件

図1:
有关表面粗糙度的指示记号、对面的指示 记号、表面粗度值、截止値及基准长度、 加工方法、加工方向的记号、表面弯曲等 如图1所示位置配置表示。
図1 各指示記号的記入位置 a : Ra値 b : 加工方法 c : 截止値・评价长度 c': 基准长度・评价长度 d : 加工所产生的料纹方向代号 f : Ra以外的参数(tp的时候、参数/切断标准)
廓线上的点与基准线之间距离绝对值的算术 平均值。 2).微观不平度十点高度Rz
指在取样长度内5个最大轮廓峰高的平均 值和5个最大轮廓谷深的平均值之和。 3).轮廓最大高度Ry
在取样长度内,轮廓最高峰顶线和最低谷 底线之间的距离。
•3
5、图纸上粗糙度专业术语介绍(1):
面的指示記号,表面可以用任何方法获取
2、粗糙度定义:
零件表面经过加工后,看起来很光滑,经放大 观察却是凹凸不平,表面精糙度是指加工后的 零件表面上具有的较小间距和微小峰谷所组成 的微观几何形状特征,一般是由所采取的加工 方法和(或)其他因素形成的。零件表面的功用 不同,需的表面粗糙度参数值也不一样。零件 图上要标注表面粗糙度代号,用以说明该表面 完工须达到的表面特性。表面粗糙度高度参数 有3种方式,具体请见下面的详细介绍吧。
0.4~1.6
二次精加工
∇∇∇∇:
0.012~0.20
精密精加工
•8
10、Ra、Ry、 Rz值的对应关系: (単位μm)
最大高度Ry的区分値 十点平均粗度Rzの区分値
0.1S 0.2S 0.3S 0.8S 1.6S 3.2S 6.3S 12.5S 25S 50S参数测量 值,例如 柯尼卡美 能达客户 图纸等
•1
3、粗糙度常见的3个参数值的介绍
第五章_表面粗糙度_新国标
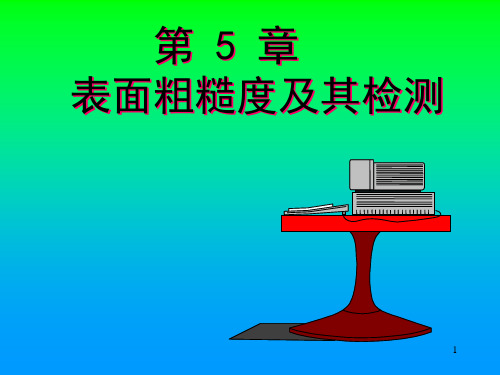
表示视图上构成封闭 轮廓的各表面具有相同 的表面粗糙度要求
30
二, 表面粗糙度标注代号
加工方法
加工纹理方向符号
c a d b
幅度参数代号及数值 附加参数符号及数值
加工余量
e
31
表面粗糙度要求在图形中注法
表面粗糙度轮廓单一要求标注示例
(1) 位置a处—注写表面粗糙度的单一要求,该要求不能省略。
① 上限或下限的标注:表示双向极限时应标注上限符号“U”和下限符号“ L”。 如果同一参数具有双向极限要求,在不引起歧义时,可省略“U”和 “ L” 的标注。若为单向下限值,则必需加注“ L” 。
极限判断规则及标注
(2) 最大规则
表面粗糙度参数的所有实测值均不得超过规定值。
在Ra(或Rz)后面标注“max”或“min”的标记
4、传输带和lr、ln的标注
① 传输带的标注
短滤波器—长滤波器 / Ra
(a) 标长—短滤波器
(b)标短滤波器“—”
(c)标“—”长滤波器
传输带和lr、ln的标注
② lr、ln的标注 默认评定长度不标,需要指定评定长度 ,要在幅度参数代号的后面注写取样长 度的个数。
34
(2) 位置b处—注写第二个(附加参数)表面粗糙度轮廓要求。 (3) 位置c处—注写加工方法。
(4) 位置d处—注写 所要求的表面纹理和纹理方向。
(5) 位置e处—注写 所要求的加工余量(mm)。
35
加工纹理符号及说明
36
三、极限判断规则及标注
(1) 16%规则 允许在表面粗糙度参数的所有实测值中超 过规定值的个数少于总数的16%。 默认规则,图样不标
18
5.2
表面粗糙度的评定
ppt课件-第五章-表面粗糙度精选全文完整版
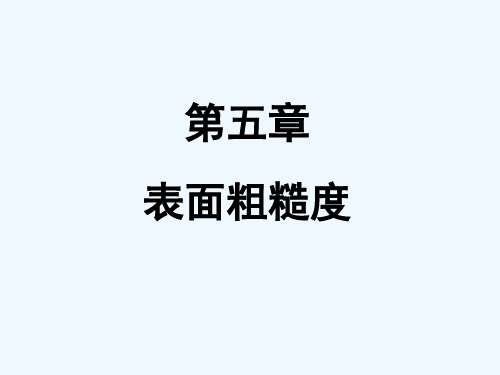
三 在图样和其他技术产品文件中的注法
按照国家标准的规定,表面结构的注写和读取方向与尺 寸的注写和读取方向一致,可以标注在轮廓线上,其符号 应从材料外指向并接触表面。必要时,表面粗糙度符号也 可以用带箭头或黑点的指引线因出标注,如教材图5-17、 5-18所示。
在不致引起误解时,表面结构要求可以标注在给定 的尺寸线上,见图5-19;也可以标注在形位公差框格 的上方,见图5-20。
0.020
0.20
2.0
0.002
0.025
0.25
2.5
0.003
0.032
0.32
3.2
0.004
0.040
0.40
4.0
0.005
0.050
0.50
5.0
0.006
0.063
0.63
6.3
0.008
0.080
0.80
8.0
0.010
0.100
1.00
10.0
注:与表5-1注相同。
第三节 表面粗糙度标注
均偏差Ra]
(2) 在取样长度内,轮廓的纵坐标值y(x)绝对值
的
(3) 算术R平a 均1l 值0l y。(x)dx
Ra
1 n
n i1
yi
(2)微观不平度十点高度Rz[新国标:无]
在取样长度内五个最大的轮廓峰高的平均值与五
个最大轮廓谷深的平均值之和 。
式中
Rz 15(i51ypii51yvi)
800
0.100
1.00
10.0
100
1000
注:与表5-1注相同
表5-3 轮廓微观不平度的平均间距Sm和轮廓的单峰平均间距S的数值 mm
粗糙度培训课件

原子力显微镜(AFM)
总结词
通过检测探针与样品表面间的微弱作用力来表征表面形貌。
详细描述
原子力显微镜(AFM)是一种高分辨率的表面形貌测量设备,其工作原理是通过 检测探针与样品表面间的微弱作用力来表征表面形貌。AFM可以在纳米尺度上对 样品表面进行无损、无污染的测量,广泛应用于材料科学、生物学等领域。
触针式仪器的针头磨损问题
触针式仪器针头磨损是常见的仪器问题,它会影响测量结果 的准确性和可靠性。
由于长时间使用或频繁接触粗糙表面,触针式仪器的针头容 易磨损。磨损的针头会导致测量结果失真,因此需要定期检 查和更换针头。为减少针头磨损,可以调整触针的施加压力 、选择更耐磨的针头材料或优化触针的结构设计。
人工智能与机器学习在粗糙度检测中的应用
01
02
03
深度学习算法
利用深度学习算法对粗糙 度图像进行自动识别和分 类,提高检测精度和效率 。
数据驱动模型
基于大量数据建立粗糙度 检测模型,通过机器学习 算法实现自适应调整和优 化。
智能传感器技术
将人工智能技术与传感器 技术相结合,实现实时、 在线、自动的粗糙度检测 。
用环境,保持清洁并稳定环境条件。
数据处理与分析中的误差来源
数据处理与分析过程中可能引入多种误差,如信号噪声、数据处理算法的误差等。
在获取表面粗糙度数据后,需要进行数据处理与分析以提取表面特征。在此过程中,数据采集的噪声、算法的不完善或人为 操作失误都可能导致误差的产生。为减小误差,可以采用数字滤波技术去除噪声、优化数据处理算法并提高操作人员的技能 水平。此外,对同一表面进行多次测量并取平均值也是一种减小误差的方法。
光干涉式仪器对环境的要求问题
光干涉式仪器对环境的要求较高,温度、湿 度和尘埃等因素都可能影响其测量精度。
表面粗糙度的测量(精品 值得参考)
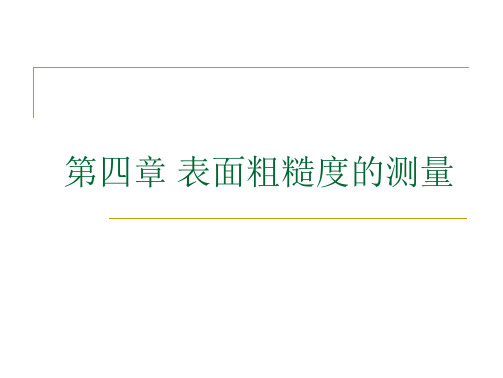
3、测量方法 测量前,选择相应的物镜并已知定度值C。然后调节 显微镜使视场呈现清晰的狭缝及表面像,且至狭缝像的一 个边缘最清晰为止。 (1)测量Rz值: 其测量方法应符合定义。Rz值可按下式计算:
(2)测量Ry值:
(3)测量单峰平均间距S值
(4)测量平均间距Sm
(5)用光切法测量Ra值 因测量与计算都很麻烦,故很少应用
第四章 表面粗糙度的测量
§4.1 概述
一、表面形貌误差的概念与形成
1. 表面形貌误差分类: 实际加工表面通常包括如下三种表面形貌 误差:
表面粗糙度:波距小于1mm,大体呈周期性变化, 属于微观几何形状误差; 表面波度:波距在1-10mm,呈周期性变化,属 于中间几何形状误差; 形状误差: 波距大于10mm,无明显周期性变化, 属于宏观几何形状误差。 纹理方向、伤痕
由于物镜分辨率及景深的限制,光切法测量范围 一般为: Rz=(80~0.8) m(旧国际▽3~▽9)。
双管显微镜
1-底座;2-立柱;3-横梁;4-手轮;5-固定螺丝;6-微调手轮;7-壳体 8-锁紧手柄;9-工作台;10-物镜组;11-测微目镜;12-燕尾导轨;13-千分尺
双管显微镜视场图
二、光切法测量表面粗糙度
1、光切法原理 用一狭窄的扁平光以一定倾斜角照射到被 测面,发生反射,将表面微观不平度用显微镜 放大成像进行观测。
2、测量仪器原理及定度 (1)原理
(a)测量装置结构简图;(b)目镜视场的影像;(c)测量原理简图 1—光源; 2—聚光镜;3—狭缝; 4、5—物镜; 6—分划板;7—目镜; 8—被测表面
(1)最小二乘中线: 使轮廓上各点的轮廓偏转距y(在测量方向 上轮廓上的点至基准线的距离)的平方和为最 小的基准线。
粗糙度培训课件

解决方案
采用先进的机械加工技术和表面处理方法 ,对产品表面进行优化处理。
06
粗糙度检测标准与规范解读
国家标准及行业标准介绍
国家标准定义
01
国家标准是由国家机构通过一定的程序制定的,用于规范行业
行为的准则。
行业标准定义
02
行业标准是由行业协会或组织制定的,用于指导行业内企业行
为的准则。
粗糙度检测的国家标准与行业标准
表面粗糙度测量仪
表面粗糙度测量仪是一种用于测量物体表面粗糙度的设备,通常由传感器、放大器 和记录器组成。
传感器用于接触物体表面并测量其粗糙度,放大器用于放大信号并记录测量结果。
表面粗糙度测量仪具有高精度、高稳定性和高可靠性,适用于各种材料和表面的粗 糙度测量。
轮廓仪
轮廓仪是一种用于测量物体表 面轮廓的设备,通常由传感器 、放大器和记录器组成。
零件,要求具有较高的表面粗糙度 。
效果评估
经过优化处理后,产品表面粗糙度得到显 著提高,满足使用要求。同时,生产效率 也得到了提高,降低了生产成本。
问题分析
原加工方法导致产品表面粗糙度不达标, 影响使用性能。
实施过程
选择合适的刀具、砂轮和抛光轮,调整切 削参数和磨削参数,进行多次试验和调整 。
用于记录测量结果。
光学轮廓仪具有非接触、高精度 和高分辨率等优点,适用于各种
材料和表面的轮廓测量。
04
粗糙度测量数据处理与分析
数据处理方法
平均法
拟合法
对一组数据取平均值,以消除随机误 差的影响。
将数据拟合为某种函数,以更好地描 述数据分布规律。
滤波法
通过设置滤波器,对数据进行平滑处 理,以减少随机误差。
计量人员培训教材
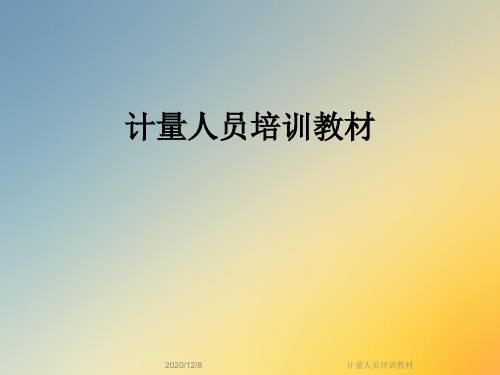
用干涉显微镜测量球形 表面粗糙度时,干涉图像中 的条纹间距不相等,这是由 于光程差造成
计量人员培训教材
第一节测量方法
使用干涉显微镜测量 表面粗糙度,调整 干涉条纹及在高精 度测量时,干涉光 的颜色有白光、红 色光、橙色光、绿 色光,应尽量选用 绿色光
度之间的间距的平均值。 注:对参数PSm、RSm、WSm需要 辨别高度和间距,若未另外规定,省 略标注的高度分辨力分别为Pz、Rz、 Wz的10%,省略标注的间距分辨力为 取样长度的1%,上述两个条件都应 满足.
a图单目镜双光束干涉显 微镜,中分光镜在目镜和 被测表面之间,目镜与被 测表面之间的距离大,所 以其数值孔径和放大倍数 都不能大,分辨率较低, 难于测量粗糙度值小的表 面。
计量人员培训教材
第一节测量方法
三、干涉法测量
图6-17光干涉法测量原理 L—光源:T—被测表面:R—参考镜:BS—分光镜 O—物镜:V—观测方向
计量人员培训教材
第一节测量方法
显然当被测表面是理想的平面时,任 一干涉条纹都呈一条直线,而且相互平行。如 果表面有凹凸不平,如图所示的被测表面有一 凹槽,那么干涉条纹也呈现相应的弯曲。此时 凹槽深度可由干涉条纹凹入深度a和相邻二暗 条纹的间距b的比值来确定,即
计量人员培训教材
第一节测量方法
在干涉显微镜中所得到 的干涉条纹图像,其垂直放 大倍率是可随意调整改变。
计量人员培训教材
第二节、粗糙度参数的评定
3、测量长度:
测量长度是7倍的取样长度 去除测量速度变化对粗糙度测量的影响
计量人员培训教材
第二节、粗糙度参数的评定
2、滤波 ISO 2CR- 第1、2个取样长度舍弃 2CR PC- 第1个和最后一个取样长度舍弃 Gaussian- 第1个半个和最后一个半个取样长度舍 弃
表面粗糙度(1)
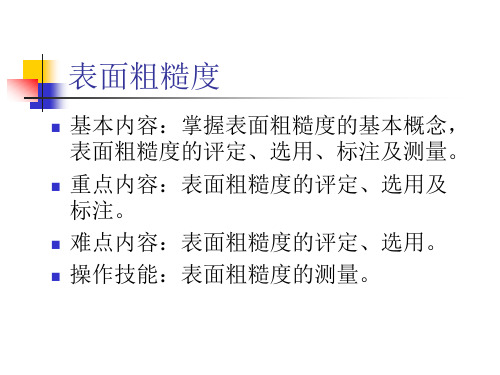
表面粗糙度(评定参数)的选择
评定参数的选择:如无特殊要求,一般仅选用 高度参数。推荐优先选用Ra值,因为Ra能充分 反映零件表面轮廓的特征。以下情况下例外:
当表面过于粗糙(Ra>6.3μm)或过于光滑 ( Ra< 0.025 μm )时,可选用Rz,因为此范 围便于选择用于测量Rz的仪器测量。
(2)表面波纹度:零件表面中峰谷的波长和波高之比等于 50~1000的不平程度称为波纹度。会引起零件运转时 的振动、噪声,特别是对旋转零件(如轴承)的影响 是相当大的目前表面波纹度还没有制定国家标准。国 际标准化组织第57技术委员会正在制定表面波纹度有 关国际标准。
(3)形状误差 :零件表面中峰谷的波长和波高之比大于 1000的不平程度属于形状误差。
表面粗糙度的评定参数(一)
国家标准GB3505-83和GB/T1031-95中规定了6个评定 参数,其中有关高度特性的参数3个,间距特性的参数 有2个,形状特性参数有1个,其中高度参数是主要的。
(1)轮廓算术平均偏差Ra
在取样长度内,被测实际轮廓上各点至轮廓中线距离绝 对值的平均值,即
1l
Ra l 0 y(x)dx
参数值的选用方法
可用类比法来确定。一般尺寸公差、表面形状 公差小时,表面粗糙度参数值也小,但也不存 在确定的函数关系。如机床的手轮或手柄。
一般情况下,它们之间有一定的对应关系,设 形状公差为T,尺寸公差为IT,它们之间的关 系可参照以下对应关系:
若T≈0.6 IT,则Ra≤0.05 IT; Rz≤ 0.2 IT T≈0.4 IT,则Ra≤0.025 IT; Rz≤ 0.1 IT T≈0.25 IT,则Ra≤0.012 IT; Rz≤ 0.05 IT T<0.25 IT,则Ra≤0.15 T; Rz≤ 0.6 T
粗糙度计量基础

Hardened peaks will eventually break off and the surface will breakdown
间距参数HSC (高点计数)
参数
A=选择的带宽 B= 中线
间距参数Rpc (峰数)
参数
Painted Surface
Base Sheet Steel
基底表面的峰将导致橙色油漆脱落
参数
中线 未滤波的图形
Rk 参数
参数
谷去除并保存在内存中
中线 谷拟制后的未滤波图形
Rk 参数
参数
最终的滤波之后的粗糙度曲线
Rk参数
参数
40 %
Rdc
0
tp(%)
100 %
Rk 参数
参数
40 % C E A B F D Rdc
0
tp(%)
100 %
Rk 参数
参数
40 % C Rk D1 E A B F D Rdc
2CR 粗糙度滤波效果
Filters
0.8 mm取样长度滤波
粗糙度幅值 = 20µ m 粗糙度波长
= 0.25 mm
波纹度幅值 = 2µ m
波纹度波长 = 8.0 mm
2CR 粗糙度滤波效果
Filters
0.25 mm取样长度滤波
粗糙度幅值 = 15µ m 粗糙度波长 = 0.25 mm 波纹度幅值 = 0µ m
2CR 粗糙度滤波效果
Filters
0.08 mm取样长度滤波
粗糙度幅值= 4µ m 粗糙度波长 = 0.25 mm
波纹度幅值 = 0µ m
2CR 粗糙度滤波效果
滤波
测量长度
启动长度
表面粗糙度培训

对于电镀的机体表面, 建议采用车削或端铣,而不 用磨削,并控制纹路间距和 沟槽截面形状,以使镀层牢 固。
二、表面粗糙度的评定
零件表面的粗糙度是否满足设计要求, 需要进行测量和评定。
为了使测量和评定结果统一,根据国家 标准的要求,应规定取样长度、评定长度、 基准线和评定参数,且测量方向应垂直于表 面的加工纹理方向。
小值为1.6μm
2.表面粗糙度高度参数值的注写及涵义
1.6 用任何方法获得的表面粗糙
度Ra的上限值为1.6μm
6.3
3.2
用去除材料的方法获得的表
面粗糙度Ra上限值为3.2μm,下
限值为1.6μm
2.表面粗糙度高度参数值的注写及涵义
①给定上限值:同一评定长度范围内,幅度 参数所有实测值中,大于上限值的个数少于总数 的16%,则认为合格。
表面粗糙度
一、表面粗糙度的基本概念 二、表面粗糙度的评定 三、粗糙度参数及数值的选择 四、表面粗糙度在图样上的标注
一、表面粗糙度的基本概念
表面粗糙度对零件的功能要求、使用 寿命、美观程度都有重大影响。
为了正确地测量和评定表面粗糙度以 及在零件图上正确地标注其要求,以保证 零件的互换性,我国发布了
GB/T3505-2000《产品几何技术规范 表面结构 轮廓法 表面结构的术语、定 义及参数》
三、粗糙度参数及数值的选择
2.参数值的选择: 在生产实际中,对零件表面微观特征 的控制,并不在于寻求最光滑的表面,而 是为了获得符合使用要求的适当的表面粗 糙度,而且要采取最经济的加工方法保证 实现这个目的。
计量人员培训教材(粗糙度)

加工痕迹深度时,则被检制件的表面粗糙度一般不超过样块的标称
值。
第一节测量方法
一、比较测量 表面粗糙度比较样板、比较的注意事项
第一节测量方法
一、比较测量
表面粗糙度比较样板、比较的注意事项
比较样板的加工方法与被测的加工方法相同 比较样板的参数值与被测的参数值接近 校准表面粗糙度比较样块时,需要计算出。 1、Ra的平均值 2、平均值对标称值的偏移量 3、平均值的标准偏差
准,凭触觉(如指甲)、视觉(可借助于放大镜、比较显微镜)与被检
制件表面进行比较,从而判断制件表面粗糙度是否合乎要求。
在进行比较时,所用的样块和被检制件的加工方法应该相同,
同时样块的材料、形状、表面色泽等也应尽可能与被检制件一致。
判断的准则是根据制件加工痕迹的深浅来决定表面粗糙度是否符合
图纸(或工艺)要求。当被检制件的加工痕迹深浅不超过样块工作面
第一节测量方法
三、干涉法测量
使用干涉显微镜测量表面粗糙度,调整干涉条纹 及在高精度测量时,干涉光的颜色有白光、红色光、 橙色光、绿色光,应尽量选用绿色光
第一节测量方法
由光波干涉原理可知:在等厚干涉的 条件下用一平晶与被测工件表面成一定的楔角 ,那么就可以得到明暗相间的干涉条纹,而相 邻暗条纹对应的空气层的厚度变化h为:
ha2b
第一节测量方法
在干涉显微镜中所得到 的干涉条纹图像,其垂直放 大倍率是可随意调整改变。
这个放大被率不是仪器 物镜的倍率、改变不了仪器 的分辨率。
用干涉显微镜测量球形 表面粗糙度时,干涉图像中 的条纹间距不相等,这是由 于光程差造成
第一节测量方法
使用干涉显微镜测量 表面粗糙度,调整 干涉条纹及在高精 度测量时,干涉光 的颜色有白光、红 色光、橙色光、绿 色光,应尽量选用 绿色光
表面粗糙度、尺寸公差在机械图纸上的标注培训

当所有表面粗糙度要求相 同时,可统一注在图样的右上角。
图例
说明
同一表面上有不同的表面粗 糙度要求时须用细实线画出其分界 线。
零件上连续表面及重复要素 (孔、槽、齿…等)的表面,只标 注一次。
图例
说明
对其中使用最多的一种代(符) 号可以统一标注在图样的右上角, 并加注“其余”两字,且应是其他 代(符)号的1.4倍。
μm
第一系 第二
列
系列
12.5 16 20
25 32 40
50 63 80
100
第一节 表面粗糙度
Ra取样长度l 的数值
Ra(μm)
l(μm)
Ra(μm)
l(μm)
≥0.008~0.020
0.08
>2.0~10.0
2.5
> 0.020~0.100
0.25
>10.0~80.0
8.0
>0.100~2.0
当地方狭小或不便标注时,代 号可引出标注。
对不连续的同一表面,可用细 线相连,其表面粗糙度代(符)号 可只标注一次。
图例
说明
螺纹的注法。 齿轮轮齿的注法。
花键的注法。
第一节 表面粗糙度
二、符号及其标注
标注示例(左图有错误)
回本节 回首页
第一节 表面粗糙度
3、表面粗糙度的选用
表面粗糙度是保证零件表面质量的技术要求,它 的等级是根据零件表面功能和加工的经济性合理地确 定的,选用时采用类比法。
0.40
>80-250
0.80
轴 >3-50
>50-500
IT6
>250-500 1.60 IT8
<3
粗糙度测量培训教案

粗糙度测量培训教案第一章:粗糙度测量概述1.1 粗糙度的定义和重要性1.2 粗糙度对产品性能的影响1.3 粗糙度的测量方法1.4 粗糙度测量的发展趋势第二章:粗糙度测量原理2.1 触针式粗糙度测量原理2.2 光束扫描式粗糙度测量原理2.3 激光散射式粗糙度测量原理2.4 超声波式粗糙度测量原理第三章:粗糙度测量仪器及操作3.1 粗糙度测量仪器概述3.2 粗糙度测量仪器的选择3.3 粗糙度测量仪器的操作步骤3.4 粗糙度测量仪器的维护与保养第四章:粗糙度测量参数及其选择4.1 粗糙度测量参数概述4.2 主要粗糙度测量参数4.3 粗糙度测量参数的选择与设定4.4 粗糙度测量参数的调整与优化第五章:粗糙度测量数据的处理与分析5.1 粗糙度测量数据的收集与记录5.2 粗糙度测量数据的处理方法5.3 粗糙度测量数据的分析与评价第六章:粗糙度测量实操训练6.1 实操训练目的与意义6.2 实操训练设备与工具6.3 实操训练步骤与要求6.4 实操训练注意事项第七章:不同材料粗糙度测量7.1 金属材料粗糙度测量7.2 非金属材料粗糙度测量7.3 复合材料粗糙度测量7.4 特殊材料粗糙度测量第八章:粗糙度测量在工业应用中的案例分析8.1 机械制造行业中的应用8.2 汽车制造行业中的应用8.3 电子制造行业中的应用8.4 其他行业中的应用第九章:粗糙度测量技术的创新与发展9.1 新型粗糙度测量技术介绍9.2 粗糙度测量技术的发展趋势9.3 粗糙度测量技术在未来的应用前景9.4 我国粗糙度测量技术的发展现状与展望第十章:粗糙度测量培训总结与考核10.1 培训课程总结10.2 粗糙度测量技能考核10.3 粗糙度测量知识问答10.4 优秀学员表彰与奖励重点和难点解析一、粗糙度测量概述难点解析:粗糙度的微观结构及其对产品性能的具体影响机制二、粗糙度测量原理难点解析:各种测量原理的物理基础和数学模型三、粗糙度测量仪器及操作难点解析:不同仪器的特点和适用范围,以及操作中的细节问题四、粗糙度测量参数及其选择难点解析:如何根据不同材料和表面特性选择合适的测量参数五、粗糙度测量数据的处理与分析难点解析:数据处理中的统计学和信号处理方法,以及分析评价的标准和技巧六、粗糙度测量实操训练难点解析:实操中可能遇到的问题及解决方案七、不同材料粗糙度测量难点解析:不同材料表面特性的差异及其对粗糙度测量的影响八、粗糙度测量在工业应用中的案例分析难点解析:如何根据粗糙度测量结果进行工艺优化和质量控制九、粗糙度测量技术的创新与发展难点解析:新技术的原理和应用前景,以及如何适应和应用这些新技术十、粗糙度测量培训总结与考核难点解析:如何评价和提高粗糙度测量技能及知识水平全文总结和概括:本教案全面覆盖了粗糙度测量的基本概念、原理、仪器操作、参数选择、数据处理、实操训练、应用案例、技术发展以及培训总结与考核等内容。
表面粗糙度讲义

1、微观不平度十点高度Rz
(1)定义 在取样长度内,5个最大的轮廓峰高ypi平均值与5个最大轮廓 谷深yvi平均值之和。即: 5 5 5 5 hi h j y pi yvi 或 i 1 j 1 i 1 i 1 Rz Rz 5 5
1、微观不平度十点高度Rz
特点
优点:简单、直观
GB6062-85 轮廓法触针式表面粗糙度测量仪—轮廓记录仪及中级制轮廓计;
GB10610—89Байду номын сангаас触针式仪器测量表面粗糙度的规则和方法; GB/T12472—2003 木制件表面粗糙度参数及其数值
§3.2 表面粗糙度GB介绍
一、主要术语及定义 1.取样长度l
定义: 评定表面粗糙度所规定的一段基准线长度,它在轮廓总的走向 上量取。 作用: 为了限制和减弱表面波纹度对表面粗糙测量结果的影响 取法: 一般在一个取样长度内应包含5个以上的波峰和波谷。
表示所有表面具有相同的表面粗糙度要求
(2)、Ra的标注 当选用Ra时,可省略代号Ra,只注出Ra值。
2、表面粗糙度代号及标注(2)
表面粗糙度Ra的标注示例:
3.2
3.2max 用任何方法获得的表面粗糙度, 用任何方法获得的表面粗糙度, Ra的上限值为3.2μm。 Ra的最大值为3.2μm。
3.2
用去除材料方法获得的表面粗 糙度, Ra的上限值为3.2μm。
2、表面粗糙度、表面波纹度、形状误差的划分
(1)波距小于1mm,属于微观几何形状误差——表面粗糙度。 (2)波距10mm以上的且不呈明显周期性变化的——宏观的几何形 状误差。 (3)波距介于1~10mm的并呈周期性变化的——表面波纹度
3、表面粗糙度对零件性能的影响
机械基础(表面粗糙度)讲解
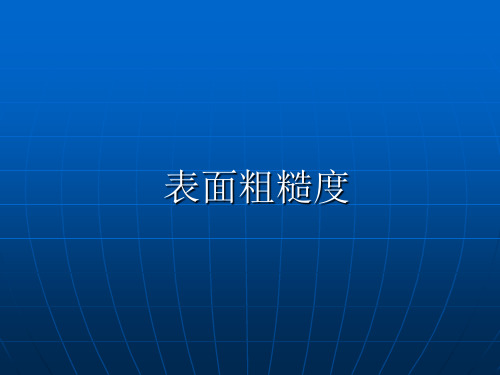
>0.2~0.4 >0.05~0.2
超精磨、精抛光、镜面 磨削
精密机床主轴颈表面,滚动轴承的滚珠,高 压油泵中柱塞和柱塞配合的表面
图4.1 加工误差示意图
2.表面粗糙度对互换性的影响 表面粗糙度直接影响产品的质量,对零件表面许多功 能都有影响。其主要影响:
1、配合性质的稳定性 2. 零件表面的耐磨性 3. 零件表面的耐腐蚀性 4. 疲劳强度 5、密封性 6、机器或仪器的工作精度 7、产品 外观 8、设备的震动、噪音及动力消耗。
表示不允许去除材料,双向极限值,两极限值均使用默认传 输带,R轮廓,上限值:算术平均偏差3.2m,评定长度为5个 取样长度(默认),“最大规则”,下限值:算术平均偏差 0.8m , 评 定 长 度 为 5 个 取 样 长 度 ( 默 认 ) , “ 16% 规 则 ” (默认)
表示去除材料,单向上限值,传输带0.8~25 mm,W轮廓, 波纹度最大高度10m,评定长度包含3个取样长度,“16%规 则”(默认)
加工法
应用举例
>80~160 >40~80
粗车、粗刨、粗铣、钻, 毛锉、锯断
半成品粗加工过的表面,非配合的加工表面, 如轴端面、倒角、钻孔、齿轮皮带轮侧面、 键槽底面、垫圈接触面等
>20~40 >10~20 >6.3~10
车、刨、铣、镗、钻、 轴上不安装轴承、齿轮处的非配合表面,紧
粗铰
固件的自由装配表面,轴和孔的退刀槽等
必要时,表面结构符号也可用带箭头或黑点的指引线引出标注。
图4.9 符号从材料外指向并接触表面
(3)用指引线引出标注表面结构要求,如图4.10所示。
图4.10 引出标注表面结构
(4)表面结构要求标注在尺寸线上。
(5)表面结构要求标注在形位公差框格的上方。
- 1、下载文档前请自行甄别文档内容的完整性,平台不提供额外的编辑、内容补充、找答案等附加服务。
- 2、"仅部分预览"的文档,不可在线预览部分如存在完整性等问题,可反馈申请退款(可完整预览的文档不适用该条件!)。
- 3、如文档侵犯您的权益,请联系客服反馈,我们会尽快为您处理(人工客服工作时间:9:00-18:30)。
第一章表面粗糙度的基本概念表面粗糙度所描述的是一种形状其复杂的三维空间曲面,它对机械和仪器的性能有重要的作用,特别是对高速、高压和重载荷条件下工作的机器和高精度运动的部件作用更大。
对机械零件必须进行粗糙度测量。
第一节零件表面的几何形状误差人们通常把表面几何形状的偏差分解成为粗糙度(微观的)、波纹度(中间的)和形状误差(宏观的),分别进行评定与控制。
图1-1-1为某一截面轮廓上几类几何状偏差及其又叠加在一起的示例。
如图1-1-1所示,若单纯从几何形状去分析,其曲折不平的高度有时没有很大差别,主要区别在于不平度的间距不一样。
各种大小不同的制作以及加工方法的差异,使三类几何形状偏差的间距值的变化范围很宽,例如有的大型零件的表面波纹度和粗糙度的间距可能比小零件本身的长度还要大,因此难以提出确切的、统一的分界值。
所以要把综合为一体的表面几图1-1-1 各类几何形状何形状偏差分成三类,是由于它们各自形成的原因以及对零件使用偏差的示意图功能的影响都各有特点,因此从这个意义上把三者区别开来才具有实际作用,但这不能定量地用一个(间距)数值简单地将其分类。
一、微观形状误差(表面粗糙度)表面粗糙度是由加工方法固有的内在作用所产生,是制件加工过程中由实际加工介质切削刀、磨料、喷等在完工表面上留下的微观不平度。
例如,切削过程中的残留面积、切屑分裂时材料的性变形、刀具对制作表面的磨擦造成的灼伤和刀瘤等因素,在加工后表面上形成各种形式不平的微细加工痕迹。
采用不同的工艺方法和条件便构成特定的表面微观几何结构。
表面粗糙度以往曾称作表面光洁度,但这个名称有时容易和表面光泽反射能力等其他表面特性相混淆,因而目前国内外已普遍采用表面粗糙度这一名称。
)。
二、中间形状误差(表面波纹度)一般称为表面度,简称波度。
它具有较明显的周期性的波距(见图4-1-1c中的B)和波高,只是在高速切削(主要是磨削)条件下才有时呈现,是由加工系统(机床一工件一刀具)中的振动所造成的,常见于滚动轴承的套圈等零件。
三、宏观形状误差简称形状误差。
它产生的原因是加工机床和工夹具本身有形状和位置误差,还有加工中的力变形和热变形以及较大的振动等。
零件上的直线不直,平面不平,圆截面不圆,都属此类误差。
相互位置误差与宏观形状误差无论产生的原因还是对零件及机器的影响,都有许多相近之处,故合称为。
形位误差。
其精确度的国家标准,也是同一标准,即“形状和位置公差”。
形位误差影响零件的配合性质和密封性,加剧磨损,降低连接强度和接触刚度,直接影响整机的工作精确度和寿命。
三种类型的表面几何形状偏差的一般数值范围,列于表1-1-1供参考,由表可见它们是相互交错重叠的,不可能用单一的数值将其区分开。
表1-1-1 三类几何形状偏差的不平度间距和高度的一般范围第二节表面粗糙度的评定基准和参数我国的表面粗糙度国家标准规定的最基本的粗糙度参数有三个,附加参数有三个,都是在1983年颁布,并于1985年开始实施的。
其中与测量最密切相关的是GBl031-83《表面粗糙度参数及其数值》,它取代了旧的国家标准,内容与国际标准ISO 468-82基本上相同。
另外两个国家标准主要是规定许多术语定义和介绍代号,以及图纸标注方法。
1995年制订了国家标准GB/J 1031-95代替了GBl031-83。
下面仅就与测量有关的主要内容进行介绍。
一、评定基准表面粗糙度误差的随机性很强,一般是用规定的评定参数来评定和控制。
规定的评定参数要先确定评定基准。
图1-2-1 轮廓的二乘中线(一)中线制(M 制)中线制是以中线为基准线评定轮廓的计算制。
中线有两种给出方式: 1.轮廓的最小二乘中线(简称中线)具有几何轮廓形状并划分轮廓的基准线,在取样长度内使轮廓上各点的轮廓偏距的平方和为最小。
参见图1-2-2。
中线的形状应该与被测表面的几何轮廓形状一致,如直线、圆弧线、渐开线等。
按照最小二乘法原理所求得的中线的方向和位置都是唯一的,只是在轮廓曲线记录图上计算求解中线的工作量较大。
2.轮廓的算术平均中线具有几何轮廓形状并在取样长度内与轮廓走向一致的基准线,在取样长度内由该线划分轮廓使上下两边的面积相等。
参见图1-2-2。
∑∑===ni ni i i F F 11'用算术平均法给出的这条上下 图1-2-2轮廓的算术平均中线两边面积相等的中心线不是唯一的。
对明显的周期轮廓,中线走向比较确定,易于取得和最小二乘中线相近的结果。
当轮廓曲线形状不规则和轮廓走向不清晰时,能绘出一簇不同的两边面积相等的中心线,其中只有一条与最小二乘中线相重合。
规定算术平均中线是为了便于用图解法近似地确定最小二乘中线的位置。
在实用中,若处理得当,对评定参数结果的影响很小。
(二)包络线制(E 制)用一个已定半径c r 的球在被测表面上滚动,把这个滚球球心的运动轨迹向被测轮廓移动一个半径c r ,便构成这条截面轮廓曲线的包络线,参见图1-2-3。
以包络线为基准线,测量出包络线到实际轮廓上各点的距离,计算得到各种参数,用这种方式来说事实上表面粗糙度称作包络线制。
由于至今仍没有按包络线制实现直接测量的仪器,故包络线制长期未得到公认和应用。
据分析,对于常用机加工方式所产生的表面,在限定条件下(主要是取样长度和滚球圆心半 径),用中线制或包络线制所测得的最大峰高只有很小的差 图1-2-3 包络线 异。
目前,绝大多数国家(包括我国)都是采用中线制评定表面粗糙度。
(三)确定中线的方法按中线制计测表面粗糙度参数时,中线的确定可以归纳为两类情况:一类是在记录的轮廓图形上绘制中线;另一类是由测量中仪器的模拟电路或软件确定中线,并直接给出表面糊糙度参数。
1.在轮廓图上绘制中线如果所记录的轮廓图是未经电气滤波的原始轮廓图形,则必须按规定在取样长度的范围内绘制中线;如果轮廓图是经过高通滤波器所获得的,是已经滤了波的粗糙度轮廓图形,则可在评定长度内确定中线。
绘制的方法有两种:(1)目测方向法:对于测定a R ,z R 和y R 参数,由于计算数值时并不需要预先确定中线相对于轮廓曲线的纵坐标位置,因而在选定的图形长度范围内只要目测中线的方向,使其平行于这一段轮廓的走向,以此作为横坐标轴,即可求得各参数值。
(2)均分法:对于某些需要确定中线的位置才能进一步计算数值的参数,则需采取把连续轮廓离散化的形式进行计算。
如图1-2-4所示,在选定的记录图形长度p l 内,按下式确定点1a 和2a 的坐标:()h a xV N x ∆=411 ∑==2/112N i pia hN h()h a xV N x ∆=432∑==NN i pia hN h 2/22式中:N —轮廓图中离散采样间隔的点数; x ∆—离散采样间隔,l xN =∆; h V —轮廓图的水平放大率;pi h —轮廓图中各离散采样点i x 的纵坐标值。
连接点1a 和2a 并延长获得的一条直线即为中线。
2.在测量仪器中确定中线对于 用电子模拟滤波器的表面粗糙度测量 仪,中线是由仪器中的RC 滤波电路直接给出。
在带微机的测量仪器中,被测轮廓已由连续的轮廓信号转换为离散的数字信息。
从而可按最小二乘原理,编制相应的程序来确定中线,参图1-2-4,即:()x x a m -+=tga 图 1-2-4 均分法绘制中线 式中,x ——取样长度l 的中心。
系数a 及角a 由下面两公式确定:∑==Ni pihNa 11()()()∑∑==+--∆⎥⎦⎤⎢⎣⎡+-∆=Ni pi Ni pi Na h N N X N N a ih x a 122211212122tg 式中:pi h —离散采样点上的轮廓纵坐标值;i —纵坐标个数;N —在选定的长度范围内的采样点数;x ∆—采样间隔。
二、取样长度和评定长度(一)取样长度在评定表面粗糙度时,如果选择的取样长度不同(见图1-2-5中的1l ,2l 和3l ),就会 得到不同的高度数值(1H ,2H 和3H )。
因此 图1-2-5 几何滤波作用的示例以中线制评定表面粗糙度各种参数的定义,都明确是在取样长度内计算的结果。
而且标准中规定:当提出表面粗糙度要求时,必须同时给出粗糙度参数值和测定时的取样长度值两项基本要求。
这种用几何学的方法达到滤除波纹度的手段,称作几何滤波,其作用见图1-2-5。
在触针式表面轮廓仪中则采用电气滤波的方式来实现,电滤波器的截止频率是由截止波长(亦称切除长度)导出,它与取样长度采用相同的数值。
由于实际加丁表面的不平度轮廓形状千变万化,其波距和粗距都有较宽的范围,用某个单一的取样长度值作为所有加工表面的粗糙度和波纹度的界限是不可能的。
一般应参照制件表面的加工方式和粗糙度参数值的大小,选择符合标准系列的适宜的取样长度值。
为了控制粗糙度测量结果中波纹度附加进去的成分不超过一定限度,取样长度不能太长,由此确定了它的上限。
试验表明,对大多数试样来说,取样长度为波距的1/3时,所造成的波纹度被计人粗糙度的数值一般不大于波高值的10%。
所以在一般情况下可选定取样长度的上限(最大值)不大于1/3的波距。
另一方面,又要保证在取样长度内求得的表面粗糙度数值,能充分反映表面粗糙度的特征,取样长度也不能太短。
分析表明:对于较规则的表面轮廓,取样长度若包含五个以上的粗糙度间距,所求得的粗糙度数值将稳定在±2%以内;再由滤波器的传输特性来看,当截止波长至少大于五倍粗距时,引起的信号衰减才会小于2%;对于Z R 参数来说,取样长度内至少应含有五个峰和谷。
因此,要选定取样长度的下限(最小值)应不小于五倍粗距。
国家标准GB /T 103l 一95中给出了国际上通用的取样长度系列值(即mm 08.0,,mm 0.8,mm 5.2,mm 8.0,mm 25.0和mm 25)。
取样长度的数值应从这个系列中选取。
在国家标准中还给出对应于a R 和y z R R ,参数值范围所推荐的取样长度选用值,如表1-2-1和表1-2-2所示。
如按表中选用推荐的取样长度值,则在图样上或技术文件中可以省略取样长度的标注。
1-2-1 a R 的取样长度l 和评定长度n l 的选用值表1-2-2 y z R R ,的取样长度l 评定长度n l 选用值(二)评定长度在某表面的一个取样长度区段内测得的表面粗糙度参数值,可能和相邻的另一段取样长度内所测结果相近;而另一表面上相邻两段取样长度内的测量结果也许相差较大,这说明各种加工表面的粗糙度均匀性不一样。
显然,如果表面粗糙度均匀性比较好,在 一个取样长度内测量,便能获得可信赖的结果;假若表面的均匀性较差,则必须在较长的包含几个取样长度段的范围内测量,然后取其平均值,才能代表这一表面的粗糙度特性。
因此要选定一个合适的最小表面段长度——评定长度,使能获得可信的测量结果,这可通过概率统计的方法进行分析。