表面粗糙度用
表面粗糙度等级对照表
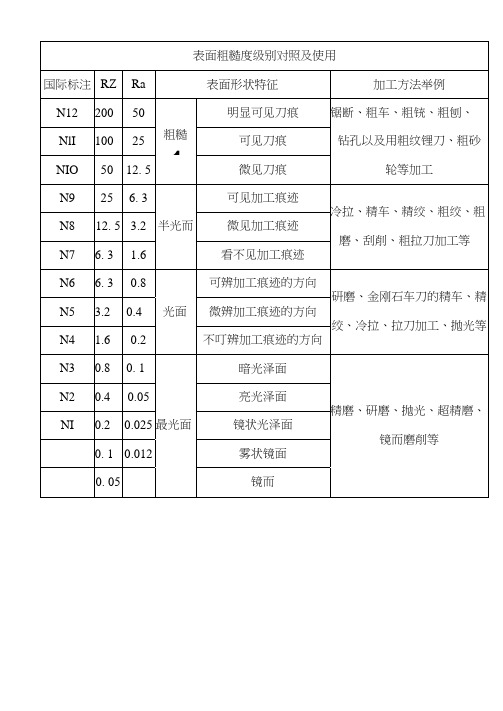
表面特征表而粗糙度(Ra)数值加工方法举例明显可见刀痕RaIOOX Ra50、Ra25、粗车、粗刨、粗铳、钻孔微见刀痕Ral2. 5x Ra6・ 3、Ra3∙2∖精车、精刨、精铳、粗铁、粗磨看不见加工痕迹,微辩加工方向Ral. 6. RaO. 8X RaO. 4、精车、精磨、精绞、研惟Jr暗光泽而RaO. 2 X RaO. 1X RaO.研熔、瑜磨、超精磨.05、镜面0.006微米雾状镜面0.012镜状光泽面0.025亮光泽面0.05暗光泽面0.1不可见加工痕迹的方向0.2可见加工痕迹方向0.8微见加工痕迹方向0.4看不清加工痕迹方向 1.6微见加工痕迹方向 3.2可见加工痕迹方向 6.3微见刀痕12.51级Ra 值不大f∖μm=100表面状况二明显可见的刀痕加工方法:=粗车、铿、刨、钻使用举例二粗加工的表面,如粗车、粗刨、切断等表面,用粗锐刀和粗砂轮等加工的表面,般很少采用2级Ra 值不大T^∖μm=2 5、50表面状况二明显可见的刀痕加工方法=粗车、锂、刨、钻使用举例二粗加工后的表面,焊接前的焊缝、粗钻孔壁等3级Ra值不大于∖μm=12.5表面状况二可见刀痕加工方法=:粗车、刨、诜、钻使用举例二一般非结合表面,如轴的端面、倒角、齿轮及皮带轮的侧面、键槽的非工作表面,减重孔眼表面表面状况二可见加工痕迹加工方法=车、铿、刨、钻、铳、锂、磨、粗狡、铳齿使用举例二不重要零件的配合表面,如支柱、支架、外壳、衬套、轴、盖等的端面。
紧固件的口由表面,紧固件通孔的表而,内、外花键的非定心表面,不作为计量基准的齿轮顶圈圆表面等5级Ra 值不大]∖μm=3.2表面状况=微见加工痕迹加工方法:=车、锂、刨、铳、刮1〜2点∕cmT∖拉、磨、锂、滚压、铳齿使用举例二和其他零件连接不形成配合的表面,如箱体、外壳、端盖等零件的端面。
要求有定心及配合特性的固定支承面如定心的轴间,键和键槽的工作表面。
不重要的紧固螺纹的表面。
表面粗糙度选用标准

表面粗糙度选用-----------------------------------------------------------序号=1Ra值不大于\μm=100表面状况=明显可见的刀痕加工方法=粗车、镗、刨、钻应用举例=粗加工的表面,如粗车、粗刨、切断等表面,用粗镗刀和粗砂轮等加工的表面,一般很少采用-----------------------------------------------------------序号=2Ra值不大于\μm=25、50表面状况=明显可见的刀痕加工方法=粗车、镗、刨、钻应用举例=粗加工后的表面,焊接前的焊缝、粗钻孔壁等-----------------------------------------------------------序号=3Ra值不大于\μm=12.5表面状况=可见刀痕加工方法=粗车、刨、铣、钻应用举例=一般非结合表面,如轴的端面、倒角、齿轮及皮带轮的侧面、键槽的非工作表面,减重孔眼表面-----------------------------------------------------------序号=4Ra值不大于\μm=6.3表面状况=可见加工痕迹加工方法=车、镗、刨、钻、铣、锉、磨、粗铰、铣齿应用举例=不重要零件的配合表面,如支柱、支架、外壳、衬套、轴、盖等的端面。
紧固件的自由表面,紧固件通孔的表面,内、外花键的非定心表面,不作为计量基准的齿轮顶圈圆表面等-----------------------------------------------------------序号=5Ra值不大于\μm=3.2表面状况=微见加工痕迹加工方法=车、镗、刨、铣、刮1~2点/cm^2、拉、磨、锉、滚压、铣齿应用举例=和其他零件连接不形成配合的表面,如箱体、外壳、端盖等零件的端面。
要求有定心及配合特性的固定支承面如定心的轴间,键和键槽的工作表面。
粗糙度应用范围
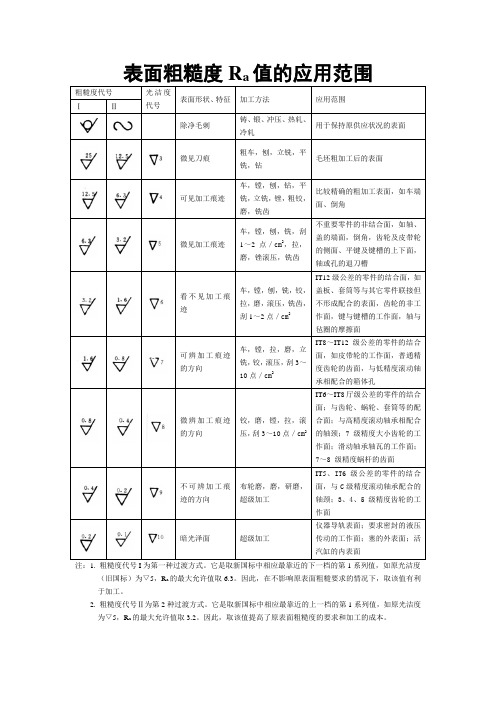
粗糙度代号
光洁度代号
表面形状、特征
加工方法
应用范围
Ⅰ
Ⅱ
除净毛刺
铸、锻、冲压、热轧、冷轧
用于保持原供应状况的表面
微见刀痕
粗车,刨,立铣,平铣,钻
毛坯粗加工后的表面
可见加工痕迹
车,镗,刨,钻,平铣,立铣,锉,粗铰,磨,铣齿
比较精确的粗加工表面,如车端面、倒角
微见加工痕迹
车,镗,刨,铣,刮1~2点/cm2,拉,磨,锉滚压,铣齿
车,镗,பைடு நூலகம்,磨,立铣,铰,滚压,刮3~10点/cm2
IT8~IT12级公差的零件的结合面,如皮带轮的工作面,普通精度齿轮的齿面,与低精度滚动轴承相配合的箱体孔
微辨加工痕迹的方向
铰,磨,镗,拉,滚压,刮3~10点/cm2
IT6~IT8厅级公差的零件的结合面;与齿轮、蜗轮、套筒等的配合面;与高精度滚动轴承相配合的轴颈;7级精度大小齿轮的工作面;滑动轴承轴瓦的工作面;7~8级精度蜗杆的齿面
2.粗糙度代号Ⅱ为第2种过渡方式。它是取新国标中相应最靠近的上一档的第1系列值,如原光洁度为▽5,Ra的最大允许值取3.2。因此,取该值提高了原表面粗糙度的要求和加工的成本。
不重要零件的非结合面,如轴、盖的端面,倒角,齿轮及皮带轮的侧面、平键及键槽的上下面,轴或孔的退刀槽
看不见加工痕迹
车,镗,刨,铣,铰,拉,磨,滚压,铣齿,刮1~2点/cm2
IT12级公差的零件的结合面,如盖板、套筒等与其它零件联接但不形成配合的表面,齿轮的非工作面,键与键槽的工作面,轴与毡圈的摩擦面
可辨加工痕迹的方向
不可辨加工痕迹的方向
布轮磨,磨,研磨,超级加工
IT5、IT6级公差的零件的结合面,与C级精度滚动轴承配合的轴颈;3、4、5级精度齿轮的工作面
2d表面表面粗糙度和3d形貌体征参数定义

2d表面表面粗糙度和3d形貌体征参数定义表面粗糙度是指物体表面不规则程度的度量,通常用来描述表面的凹凸程度和不平滑程度。
表面粗糙度可以用各种参数来定量描述,其中最常用的是2D表面粗糙度和3D形貌体征参数。
2D表面粗糙度是通过在二维平面上测量表面高度和间距来描述的。
常见的2D表面粗糙度参数包括均方根粗糙度(Ra)、平均峰谷高度(Rz)、最大峰谷高度(Rt)等。
其中,均方根粗糙度是指在某一测量区域内高度差的平方和的平均值的平方根,是最常用的2D表面粗糙度参数之一。
平均峰谷高度是指在某一测量区域内,峰值和谷值之间的平均高度差。
最大峰谷高度是指测量区域内最高点到最低点之间的距离。
然而,2D表面粗糙度只能提供表面的一部分信息,不能完全描述表面的形貌。
为了更准确地表征表面的凹凸特性,需要使用3D形貌体征参数。
3D形貌体征参数是通过在三维空间中测量表面高度来确定的,可以提供更多的表面形貌信息。
常见的3D形貌体征参数包括表面平均高度(Sa)、表面峰谷高度(Sz)、表面最大凹陷(Smr)、表面最大高度(Spr)等。
表面平均高度是测得表面上所有高度值与参考平面之间的平均高度差。
表面峰谷高度是测得表面上所有高度值与参考平面之间的最大高度差。
表面最大凹陷是测得在某一测量区域内,表面上所有凹陷的最大深度。
表面最大高度是测得在某一测量区域内,表面上所有突起的最大高度。
这些2D表面粗糙度和3D形貌体征参数在工程和科学研究中被广泛应用。
它们可以帮助我们定量描述物体表面的粗糙程度和不平滑程度,为材料表面的设计、制备和加工提供重要的依据。
不同的2D表面粗糙度和3D形貌体征参数适用于不同的实际应用需求,选择合适的参数可以更好地满足特定需求。
总之,2D表面粗糙度和3D形貌体征参数是对物体表面粗糙程度进行定量描述的重要指标。
它们通过测量表面高度和间距来确定,可以提供丰富的表面形貌信息,广泛应用于各个领域。
这些参数的正确使用可以帮助我们更好地了解和控制表面的性质,优化材料的表面处理和加工过程。
表面粗糙度仪使用方法

表面粗糙度仪使用方法
表面粗糙度仪是一种用于测量物体表面粗糙度的仪器。
它可以帮助我
们了解物体表面的平滑程度,以及表面上存在的微小凸起和凹陷。
下
面是使用表面粗糙度仪的详细方法:
1. 准备工作:首先需要将表面粗糙度仪放置在平稳的水平台上,并将
其连接到电源。
然后,打开电源开关并等待数秒钟,直到设备完全启动。
2. 校准:在进行任何测量之前,需要对设备进行校准。
这可以通过将
标准样品(通常由制造商提供)放置在设备上并按下校准按钮来完成。
3. 准备待测样品:将待测样品清洁干净,并确保其表面没有任何污垢
或杂质。
如果需要,可以使用清洁剂或酒精来清洁样品表面。
4. 测量:将待测样品放置在设备上,并按下开始按钮开始测量过程。
该过程可能需要一些时间才能完成,具体时间取决于待测样品的大小
和形状。
5. 结果分析:一旦测量过程完成,设备会自动显示结果。
这些结果通
常包括表面粗糙度、峰谷高度差等指标。
可以使用这些指标来评估样
品表面的平滑程度和质量。
6. 记录数据:最后,需要将测量结果记录下来。
这可以通过手动记录或使用计算机软件完成,具体取决于设备和用户的要求。
总之,使用表面粗糙度仪需要进行校准、准备待测样品、进行测量、分析结果和记录数据等步骤。
只有在正确执行这些步骤的情况下,才能获得准确和可靠的测量结果。
关于表面粗糙度对机械零件使用性能的影响分析

关于表面粗糙度对机械零件使用性能的影响分析表面粗糙度是指表面上微小凸起和凹陷的高低不平度,通常以微米(μm)为单位。
在机械工程中,表面粗糙度不仅仅是一种质量指标,更是影响零件使用性能的重要因素之一。
高质量的表面粗糙度可以提高零件的使用寿命和性能,而低质量的表面粗糙度则可能导致机械零件的损坏和失效。
对表面粗糙度对机械零件使用性能的影响进行分析,对于提高机械零件的质量和性能具有重要的意义。
表面粗糙度对机械零件使用性能的影响主要体现在以下几个方面:1. 润滑性能表面粗糙度对机械零件的润滑性能具有重要影响。
如果零件表面粗糙度较大,那么在零件与零件之间的接触区域会产生较大的摩擦力,从而降低了零件的润滑性能。
反之,如果零件表面粗糙度较小,接触区域的摩擦力也会相应减小,从而提高了零件的润滑性能。
合适的表面粗糙度有助于提高机械零件的润滑性能,延长零件的使用寿命。
2. 疲劳强度表面粗糙度对机械零件的疲劳强度也有着重要的影响。
当机械零件表面粗糙度较大时,零件在循环负荷作用下容易产生微观裂纹,从而降低了零件的疲劳强度。
而当机械零件表面粗糙度较小时,微观裂纹的产生几率也相应降低,从而提高了零件的疲劳强度。
适当控制表面粗糙度是提高机械零件疲劳强度的有效手段。
表面粗糙度对机械零件使用性能的影响是多方面的,适当控制表面粗糙度有助于提高机械零件的使用性能。
在零件的设计和加工过程中,应该合理控制表面粗糙度,以确保机械零件的质量和性能。
在实际生产中,通过采用合适的加工工艺和技术手段可以有效地控制表面粗糙度,提高机械零件的使用性能。
在机械零件的精密加工过程中,可以采用合适的切削参数,如切削速度、进给速度、切削深度等,以确保零件表面的粗糙度处于合适的范围。
还可以采用研磨、抛光等表面处理工艺,进一步提高机械零件的表面质量和精度。
还可以通过提高材料的硬度和强度,增加表面的涂层保护,以提高机械零件的耐磨性和抗腐蚀性。
也可以通过改进设计结构,减少零件的接触区域,进一步降低摩擦和磨损,提高机械零件的使用寿命。
关于新旧粗糙度标准的使用说明

关于新旧表面粗糙度的使用说明机械制造中,光洁度、粗糙度是用来表示另件表面的平整(光滑)程度的。
光洁度的数值越大,表示另件表面越平整、光滑,这是旧标准使用的表示方法,现在已经不使用。
粗糙度的数值越小,表示零件表面越平整、光滑,这是目前国家标准和国际标准的表示方法。
二、关于上述表格使用的说明1.▽1-▽14是旧国家标准GB1031-68表面光洁度级别14个等级。
随着数值的增大,其表面光洁度越高。
2.我公司产品图样中对零件表面粗糙度高度参数一般应选用轮廓算数平均值偏差Ra值3.新产品设计时,图样中零件表面粗糙度高度参数一般应该选用轮廓算数平均值偏差Ra的上限值,对有特殊要求的表面,可以选择Ra的最大值或同时选用最大值和最小值。
4.表面粗糙度高度参数Ra的数值选用按照GB/T1031-1995的标准系列选用,对某些特殊表面,标准系列不能满足要求的,可采用GB/T1031-1995的补充系列5. 标准“GB1031-68表面光洁度级别”已经作废,其最新版本升级为“GB/1031-1995 表面粗糙度参数及其数值”。
6.老产品图中表面粗糙度高度参数Ra的标注是按照GB131-83的规定,即表示Ra的最大允许值,在贯彻新标准的过程中,一般不需要改图,只是将原标准中最大允许值理解为上限值即可。
对极少数性能要求高的表面,如果一定要保持最大允许值,应通过改图,在原数值后面加max7.我厂制定的《设计师设计标准化工作手册》制定的企业标准“DL00003-2000 表面粗糙度使用的有关规定”中引用标准GB/T131-93也已经作废,其最新升级版本为“GB/T131-2006/ISO1302: 2002 产品几何技术规范技术产品文件中表面结构的表示法”其衍化对比如下表所示:(表面光洁度---表面粗糙度—表面结构)表二表面结构要求的图形标注的演变经过咨询公司标准化室缑智勇主任,明确“GB/T131-2006/ISO1302: 2002 产品几何技术规范技术产品文件中表面结构的表示法”这个标准变化比较大,兄弟工厂贯彻的不多,咱们工厂暂时不贯彻。
关于新旧粗糙度标准的使用说明
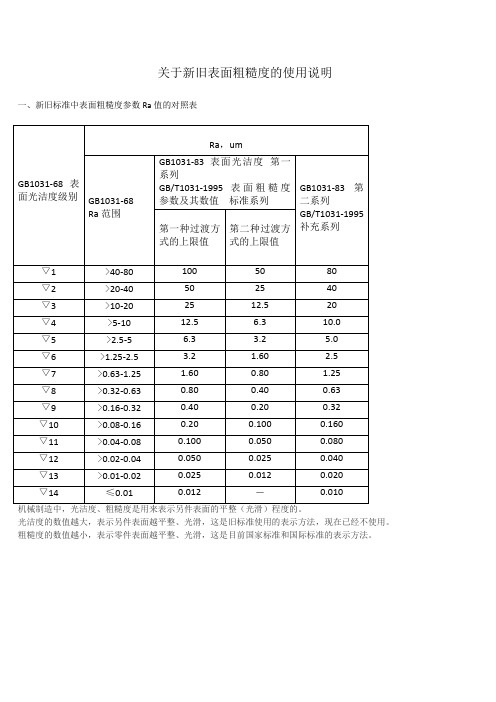
关于新旧表面粗糙度的使用说明一、新旧标准中表面粗糙度参数Ra值的对照表机械制造中,光洁度、粗糙度是用来表示另件表面的平整(光滑)程度的。
光洁度的数值越大,表示另件表面越平整、光滑,这是旧标准使用的表示方法,现在已经不使用。
粗糙度的数值越小,表示零件表面越平整、光滑,这是目前国家标准和国际标准的表示方法。
二、关于上述表格使用的说明1.▽1-▽14是旧国家标准GB1031-68表面光洁度级别14个等级。
随着数值的增大,其表面光洁度越高。
2.我公司产品图样中对零件表面粗糙度高度参数一般应选用轮廓算数平均值偏差Ra值3.新产品设计时,图样中零件表面粗糙度高度参数一般应该选用轮廓算数平均值偏差Ra的上限值,对有特殊要求的表面,可以选择Ra的最大值或同时选用最大值和最小值。
4.表面粗糙度高度参数Ra的数值选用按照GB/T1031-1995的标准系列选用,对某些特殊表面,标准系列不能满足要求的,可采用GB/T1031-1995的补充系列5. 标准“GB1031-68表面光洁度级别”已经作废,其最新版本升级为“GB/1031-1995 表面粗糙度参数及其数值”。
6.老产品图中表面粗糙度高度参数Ra的标注是按照GB131-83的规定,即表示Ra的最大允许值,在贯彻新标准的过程中,一般不需要改图,只是将原标准中最大允许值理解为上限值即可。
对极少数性能要求高的表面,如果一定要保持最大允许值,应通过改图,在原数值后面加max7.我厂制定的《设计师设计标准化工作手册》制定的企业标准“DL00003-2000 表面粗糙度使用的有关规定”中引用标准GB/T131-93也已经作废,其最新升级版本为“GB/T131-2006/ISO1302: 2002 产品几何技术规范技术产品文件中表面结构的表示法”其衍化对比如下表所示:(表面光洁度---表面粗糙度—表面结构)表二表面结构要求的图形标注的演变经过咨询公司标准化室缑智勇主任,明确“GB/T131-2006/ISO1302: 2002 产品几何技术规范技术产品文件中表面结构的表示法”这个标准变化比较大,兄弟工厂贯彻的不多,咱们工厂暂时不贯彻。
表面粗糙度的选用原则
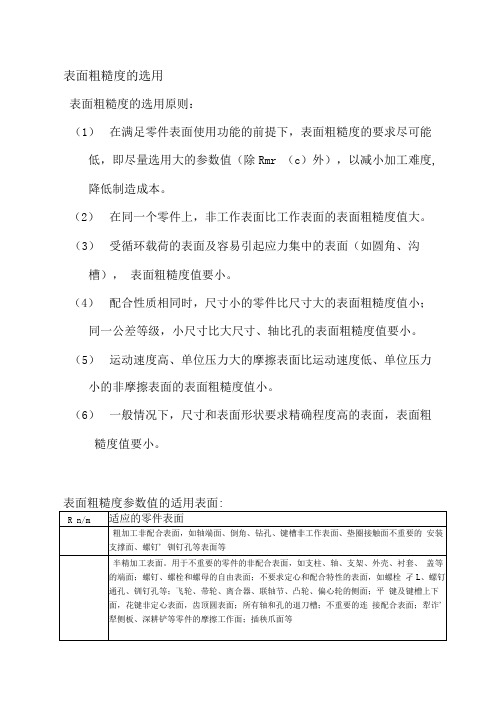
表面粗糙度的选用
表面粗糙度的选用原则:
(1)在满足零件表面使用功能的前提下,表面粗糙度的要求尽可能低,即尽量选用大的参数值(除Rmr (c)外),以减小加工难度, 降低制造成本。
(2)在同一个零件上,非工作表面比工作表面的表面粗糙度值大。
(3)受循环载荷的表面及容易引起应力集中的表面(如圆角、沟槽),表面粗糙度值要小。
(4)配合性质相同时,尺寸小的零件比尺寸大的表面粗糙度值小;
同一公差等级,小尺寸比大尺寸、轴比孔的表面粗糙度值要小。
(5)运动速度高、单位压力大的摩擦表面比运动速度低、单位压力小的非摩擦表面的表面粗糙度值小。
(6)一般情况下,尺寸和表面形状要求精确程度高的表面,表面粗糙度值要小。
表面粗糙度参数值的适用表面:
轴和孔的表面粗糙度参数推荐值
各种常用加工方法可能达到的表面粗糙度
注:对于飯金类的冲裁
在普通冲裁中,材料都是从模具刃口处产生裂纹而剪切分离,
制件尺寸精度低(VIT11),断面粗糙(Ra二〜uni),不平直,断面有一定斜度,往往不能满足零件较高的技术要求,有时还需再进行多道后续的机械加工。
精密冲裁是使材料呈纯剪切的形式进行冲裁,是通过改进模具来提高精度和改善断面质量的,制件尺寸精度可达到IT6〜IT9,断面粗糙度Ra 二〜urn,断面垂直度可达89° 30z或更佳。
表面粗糙度及表面粗糙度的标注方法
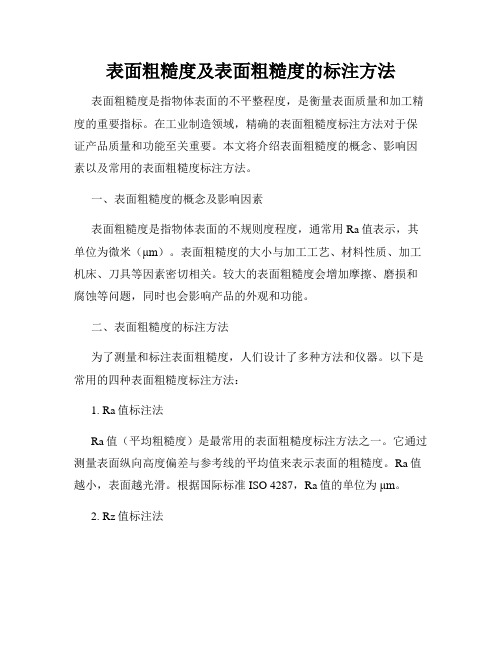
表面粗糙度及表面粗糙度的标注方法表面粗糙度是指物体表面的不平整程度,是衡量表面质量和加工精度的重要指标。
在工业制造领域,精确的表面粗糙度标注方法对于保证产品质量和功能至关重要。
本文将介绍表面粗糙度的概念、影响因素以及常用的表面粗糙度标注方法。
一、表面粗糙度的概念及影响因素表面粗糙度是指物体表面的不规则度程度,通常用Ra值表示,其单位为微米(μm)。
表面粗糙度的大小与加工工艺、材料性质、加工机床、刀具等因素密切相关。
较大的表面粗糙度会增加摩擦、磨损和腐蚀等问题,同时也会影响产品的外观和功能。
二、表面粗糙度的标注方法为了测量和标注表面粗糙度,人们设计了多种方法和仪器。
以下是常用的四种表面粗糙度标注方法:1. Ra值标注法Ra值(平均粗糙度)是最常用的表面粗糙度标注方法之一。
它通过测量表面纵向高度偏差与参考线的平均值来表示表面的粗糙度。
Ra值越小,表面越光滑。
根据国际标准ISO 4287,Ra值的单位为μm。
2. Rz值标注法Rz值(最大峰谷值)是指表面上最高峰和最低谷之间的垂直距离。
Rz值可以反映表面的不规则程度,是评价表面粗糙度变化的重要指标之一。
同样,根据国际标准ISO 4287,Rz值的单位也为μm。
3. Rq值标注法Rq值(均方根粗糙度)是通过计算表面各点高度偏差的平方和的平均值来表示表面的粗糙度。
Rq值能够反映表面粗糙度的整体分布情况,对于一些特殊需求的产品尤为重要。
单位同样为μm。
4. Rt值标注法Rt值(最大峰谷差)是指表面上最高峰和最低谷之间的总距离。
Rt 值可以直观地反映出表面是否有较大的凹凸不平,常用于对表面质量要求较高的产品。
单位同样为μm。
三、表面粗糙度的测量仪器为了准确测量表面粗糙度并进行标注,现代工业通常使用表面粗糙度测量仪器。
常见的测量仪器有:1. 表面粗糙度仪表面粗糙度仪是一种能够测量表面粗糙度的便携仪器,它通过传感器接触并扫描测量物体表面,然后将数据转化为相应的粗糙度数值,并进行显示和记录。
表面粗糙度参数及其数值的国家标准
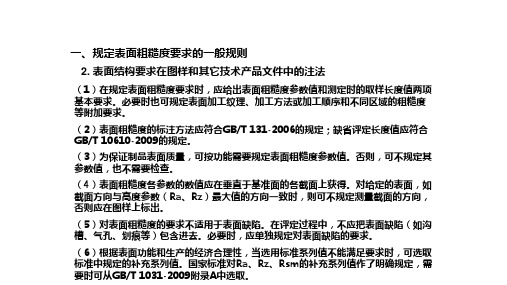
(4)表面粗糙度各参数的数值应在垂直于基准面的各截面上获得。对给定的表面,如 截面方向与高度参数(Ra、Rz)最大值的方向一致时,则可不规定测量截面的方向, 否则应在图样上标出。
(5面缺陷(如沟 槽、气孔、划痕等)包含进去。必要时,应单独规定对表面缺陷的要求。
一、规定表面粗糙度要求的一般规则
2. 表面结构要求在图样和其它技术产品文件中的注法
(1)在规定表面粗糙度要求时,应给出表面粗糙度参数值和测定时的取样长度值两项 基本要求。必要时也可规定表面加工纹理、加工方法或加工顺序和不同区域的粗糙度 等附加要求。
(2)表面粗糙度的标注方法应符合GB/T 131-2006的规定;缺省评定长度值应符合 GB/T 10610-2009的规定。
二、评定表面结构的参数及其数值系列
三、分类及表面粗糙度参数
三、分类及表面粗糙度参数
(6)根据表面功能和生产的经济合理性,当选用标准系列值不能满足要求时,可选取 标准中规定的补充系列值。国家标准对Ra、Rz、Rsm的补充系列值作了明确规定,需 要时可从GB/T 1031-2009附录A中选取。
二、评定表面结构的参数及其数值系列
国家标准规定,表面粗糙度参数从下列两项中选取: ——轮廓的算术平均偏差Ra; ——轮廓的最大高度Rz。 在幅度参数(峰和谷)常用的参数值范围内(Ra为0.025μm~6.3μm,Rz为 0.1μm~25μm)推荐优先选用Ra。
表面粗糙度的选用

第3章表面粗糙度3.1 表面粗糙度标注识读概念轮廓算术平均偏差Ra表面粗糙度轮廓最大高度Rz。
评定参数轮廓单元的平均宽度RS m轮廓支承长度率R mr(C)任务6 识读齿轮表面粗糙度标注表面粗糙度是一种微观几何形状误差,是零件的几何参数的精度指标之一。
以如图3-1所示的零件图为例,识读表面粗糙度的标注。
图3-1 表面粗糙度标注实例3.1.1 表面粗糙度概念任何零件的表面都不是绝对的光滑的,零件表面总会存在着由较小间距的峰谷组成的微观高低不平的痕迹,表面粗糙度是一种微观几何形状误差,也称为微观不平度。
表面误差通常按(波距)的大小划分为三类误差:表面粗糙度、表面波度和表面上宏观形状误差。
波距小于1mm的属于表面粗糙度(微观几何形状误差),波距在l~10 mm的属于表面波度(中间几何形状误差),波距大于10 mm的属于形状误差(宏观几何形状误差),如图3-2所示。
图3-2 零件表面的几何形状误差3.1.2 表面粗糙度对零件的影响表面粗糙度的大小对零件的实用性能和使用寿命有很大的影响:1.对摩擦和磨损的影响表面越粗糙,摩擦系数就越大,两相对运动的表面磨损也越快,表面过于光滑,由于润滑油被挤出和分子见的吸附作用等原因,也会使摩擦阻力增大和加剧磨损。
2.对配合性能的影响对于间隙配合,相对运动的表面因其粗糙不平而迅速磨损,致使间隙增大;对于过盈配合,表面轮廓峰顶在装配时容易被挤平,使实际有效过盈量减小,致使联接强度降低。
3.对抗腐蚀性的影响粗糙的表面,易使腐蚀性物质存积在表面的微观凹谷处,并渗入到金属内部,致使腐蚀加剧。
4.对疲劳强度的影响零件表面越粗糙,凹痕就越深,当零件承受交变荷载时,对应力集中很敏感。
使疲劳强度降低,导致零件表面产生裂纹而损坏。
5.对接触刚度的影响接触刚度影响零件的工作精度和抗振性。
这是由于表面粗糙度使表面间只有一部分面积接触。
一般情况下,实际接触面积只有公称接触面积的百分之几。
因此,表面越粗糙受力后局部变形越大,接触刚度也越低。
表面粗糙度的单位

表面粗糙度的单位
表面粗糙度单位是一种刻度系统,用来衡量表面粗糙度程度,不同表
面有不同的表面粗糙度单位,比如:
1. 毫米(mm):一种常用的表面粗糙度单位。
用于描述表面体积的粗
糙度,常用的范围为0.01mm~0.2mm。
2.微米(μm):也叫米微米,一种单位,用于衡量表面体积的粗糙度,常用的范围为0.1μm~3μm。
3. 英尺(ft):一种表面粗糙度单位,常用的范围为0.01ft~0.15ft。
4.毫微米(µm):一种表面粗糙度单位,常用的范围为0.1μm~0.2μm。
5. 吉微米(µin):一种表面粗糙度单位,常用的范围为
0.001in~0.004in。
6. 米微米(um):一种表面粗糙度单位,常用的范围为
0.001μm~0.03μm。
7. 几何米(mm):一种表面粗糙度单位,常用的范围为0.1mm~2mm。
8.田:也称为德语田,一种表面粗糙度单位,常用的范围为0.1~3。
9. 纳米(nm):一种表面粗糙度单位,常用的范围为0.001nm~0.03nm。
10.尼斯特里克(µm):一种常用的表面粗糙度单位,常用的范围为
1µm~10µm。
以上仅为表面粗糙度单位的部分概述,具体要看应用材料所用的类型。
表面粗糙度的评定参数及其数值的选用

0.8
1.6
滑动轴承表面
公差 等级
表面
Ra
轴
0.4~0.8
IT6至IT9
孔
0.8~1.6
IT10至 IT12
流体 润滑
轴
0.8~3.2
孔
1.6~3.2
轴
0.1~0.4
孔
0.2~0.8
5.4表面粗糙度符号、 代号及其标注
一、表面粗糙度符号、代号
1、表面粗糙度基本符号 任意加工方法获得表面 用去除材料方法获得表面 用不去除材料的方法获得的表面
f
Rz3.2 max Rz1.6 min
用去除材料的方法获得的表面粗糙度,Rz
的最大值为3.2μm,最小值为1.6μm
⑵、其他各项规定的标注
①、取样长度的标注(l 按国标选取,见表 5-1)。
1.
6.
6 2.5
3
取样长度的标注
其他各项规定的标注.1
②、附加参数Sm、S、tp的标注
a
Sm0.05
a)
5.3 表面精度设计
表面粗糙度的评定参数 及其数值的选用
一、评定参数的选择
1、高度评定参数的选用 ⑴、无特殊要求,一般选用高度参数。 当Ra为0.025~6.3μm、Rz为0.1~25μm,优
先选用Ra。 ⑵ห้องสมุดไป่ตู้特殊:Ra> 6. 3μm 或Ra <0.025 μm
选Rz;软材料选Rz;小平面选Ry。
0.05 0.8 12.5
0.1 1.6
表面粗糙度的参数值.1
表5-3 微观不平度十点高度Rz和轮廓不平度最 大高度Ry的数值μm
0.025 0.4 6.3 100 1600 0.05 0.8 12.5 200 Rz、 Ry 0.1 1.6 25 400 0.2 3.2 50 800
表面粗糙度比较样块使用说明

表面粗糙度比较样块使用说明
1.检查外观
表面粗糙度比较样块表面应无锈蚀、划伤、缺损及明显磨耗。
被测表面也应无铁屑、毛刺和油污。
2.比较测量方法
(1)样块工作面及被测工作面的表面粗糙度用表面轮廊算术平均偏差Ra参数来评定。
(2)样块与被测件同置一处。
比较样块在比较检验时,被测零部件与比较样块应处于同样的检测条件下,如照明亮度一致,将比较样块与被测部件置于一处;否则,将会有偏差。
(3)表面粗糙度判断的准则。
根据制件加工痕迹的深浅,决定表面粗糙度是否符合图纸(或工艺要求)。
当被检制件的加工痕迹深浅不超过样块工作面加工痕迹深度时,被检制件的表面粗糙度一般不超过样块的标称值。
(4)评定粗糙度方法。
以粗糙度样块工作面的表面粗糙度为标准,凭触觉(如指甲)、视觉(可借组放大镜、比较显微镜)与被检工件表面进行比较,被检工件表面加工痕迹的粗糙度与对应痕迹比较相近的一块比较样块的粗糙度一致,即该样块的粗糙度值就是被检工件的粗糙度值。
当采用放大镜观察时(适用Ra为0.8~1.6μm),可采用5~10倍数的放大镜。
日本有的企业在生产线上安置了5~10倍的放大镜,既可检查表面粗糙度,也可观察裂纹等缺陷。
(5)目视一般适合检查制件表面粗糙度Ra为3.2~12.5μm的制件。
对表面粗糙度Ra为0.1~0.4μm的制件,采用便携式粗糙度仪器定量测量较为准确。
表面粗糙度选用表
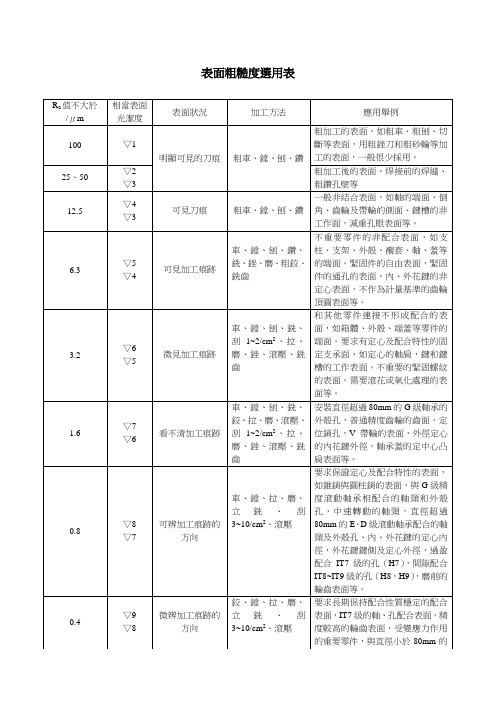
Ra值不大於/μm
相當表面光潔度
表面狀況
加工方法
應用舉例
100
▽1
明顯可見的刀痕
粗車、鏜、刨、鑽
粗加工的表面,如粗車、粗刨、切斷等表面,用粗銼刀和粗砂輪等加工的表面,一般很少採用。
25、50
▽2
▽3
粗加工後的表面,焊接前的焊縫、粗鑽孔壁等
12.5
▽4
▽3
可見刀痕
粗車、鏜、刨、鑽
一般非結合表面,如軸的端面、倒角、齒輪及帶輪的側面、鍵槽的非工作面,減重孔眼表面等。
0.4
▽9
▽8
微辨加工痕跡的方向
鉸、鏜、拉、磨、立銑、刮3~10/cm2、滾壓
要求長期保持配合性質穩定的配合表面,IT7級的軸、孔配合表面,精度較高的輪齒表面,受變應力作用的重要零件,與直徑小於80mm的E、D級軸承配合的軸頸表面,與橡膠密封件接觸的軸表面,尺寸大於1200mm的IT13~IT16級孔和軸用量規的測量表面。
0.2
▽10
▽9
不可辨加工痕跡的方向
工作時受變應力作用的重要零件的表面。保證零件的疲勞強度、防腐性和耐久性,並在工作時不破壞配合性質的表面,如軸頸表面、要求氣密度的表面和支承表面、圓錐與定心表面等。IT5、IT6級配合表面、高精度齒輪的齒面。與C級滾動軸承配合的軸頸表面,尺寸大於315mm的IT7~IT9級孔和軸用量規及尺寸大於120~315mm的IT10~IT12級孔和軸用量規的測量表面等。
0.025
▽13
▽12
鏡狀光澤面
高壓柱塞泵中柱塞和柱塞套的配合表面,中等精度儀器零件配合表面,尺寸大於120mm的IT6級孔用量規、小於120mm的IT7~IT9級軸用良規測量表面。
表面粗糙度用法
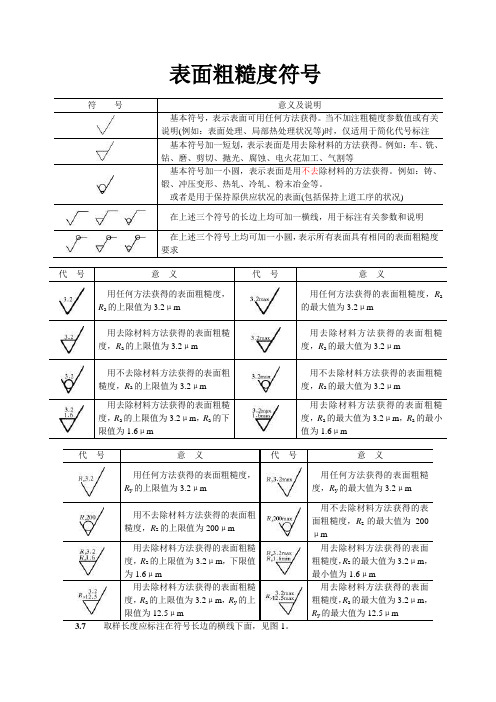
表面粗糙度符号符号意义及说明基本符号,表示表面可用任何方法获得。
当不加注粗糙度参数值或有关说明(例如:表面处理、局部热处理状况等)时,仅适用于简化代号标注基本符号加一短划,表示表面是用去除材料的方法获得。
例如:车、铣、钻、磨、剪切、抛光、腐蚀、电火花加工、气割等基本符号加一小圆,表示表面是用不去除材料的方法获得。
例如:铸、锻、冲压变形、热轧、冷轧、粉末冶金等。
或者是用于保持原供应状况的表面(包括保持上道工序的状况)在上述三个符号的长边上均可加一横线,用于标注有关参数和说明在上述三个符号上均可加一小圆,表示所有表面具有相同的表面粗糙度要求代号意义代号意义用任何方法获得的表面粗糙度,R a的上限值为3.2μm用任何方法获得的表面粗糙度,R a 的最大值为3.2μm用去除材料方法获得的表面粗糙度,R a的上限值为3.2μm用去除材料方法获得的表面粗糙度,R a的最大值为3.2μm用不去除材料方法获得的表面粗糙度,R a的上限值为3.2μm用不去除材料方法获得的表面粗糙度,R a的最大值为3.2μm用去除材料方法获得的表面粗糙度,R a的上限值为3.2μm,R a的下限值为1.6μm用去除材料方法获得的表面粗糙度,R a的最大值为3.2μm,R a的最小值为1.6μm代号意义代号意义用任何方法获得的表面粗糙度,R y的上限值为3.2μm用任何方法获得的表面粗糙度,R y的最大值为3.2μm用不去除材料方法获得的表面粗糙度,R z的上限值为200μm用不去除材料方法获得的表面粗糙度,R z的最大值为200μm用去除材料方法获得的表面粗糙度,R z的上限值为3.2μm,下限值为1.6μm用去除材料方法获得的表面粗糙度,R z的最大值为3.2μm,最小值为1.6μm用去除材料方法获得的表面粗糙度,R a的上限值为3.2μm,R y的上限值为12.5μm用去除材料方法获得的表面粗糙度,R a的最大值为3.2μm,R y的最大值为12.5μm3.7取样长度应标注在符号长边的横线下面,见图1。
粗糙度等级及各级适用类型
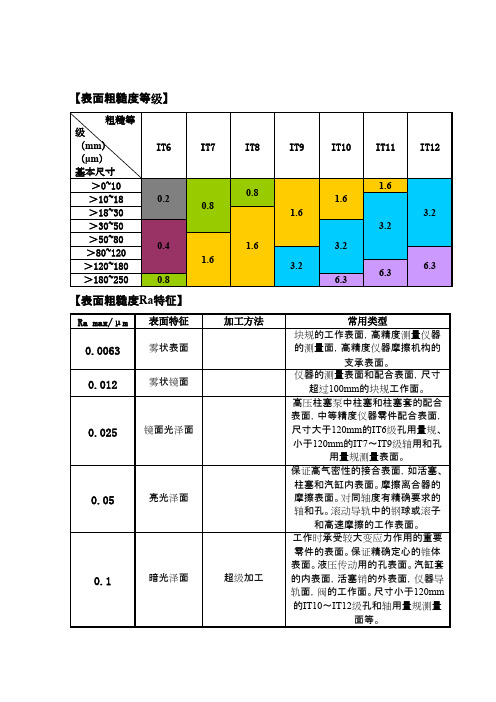
封件接触的表面,尺寸大于120mm
的IT13~IT16级孔和轴用量规的测
量表面。
要求保证定心及配合特性的表面,
如锥销与圆柱销的表面,与G级精度
滚动轴承相配合的轴颈和外壳孔,
车、磨、立铣、刮 中速转动的轴颈,直径超过80mm的
0.8
可辨加工痕 3~10点/cm2、镗 E、D级滚动轴承配合的轴颈及外壳 迹方向
、拉、滚压
孔,内、外花键的定心内径,外花键
键侧及定心外径,过盈配合IT7级的
孔,间隙配合IT8~IT9级的孔,磨靡
削的齿轮表面等。
安装直径超过80mm的G级轴承的外
车、镗、拉、磨、 壳孔,普通精度齿轮的齿面,定位销
1.6
看不清加工 铣、铰、刮1~2点 孔,V带轮的表面,外径定心的内花 痕迹
/cm2、磨、滚压 键外径,轴承盖的定中心凸肩表面
0.012
雾状镜面
0.025 镜面光泽面
0.05
亮光泽面
0.1
暗光泽面
超级加工
IT9
IT10 IT11 IT12
1Байду номын сангаас6
1.6
1.6
3.2
3.2
3.2
3.2
6.3
6.3
6.3
常用类型 块规的工作表面,高精度测量仪器 的测量面,高精度仪器摩擦机构的
支承表面。 仪器的测量表面和配合表面,尺寸
超过100mm的块规工作面。 高压柱塞泵中柱塞和柱塞套的配合 表面,中等精度仪器零件配合表面, 尺寸大于120mm的IT6级孔用量规、 小于120mm的IT7~IT9级轴用和孔
等。
与其他零件连接不形成配合的表面
车、镗、刨、铣、 ,如箱体、外壳、端盖等零件的端面
- 1、下载文档前请自行甄别文档内容的完整性,平台不提供额外的编辑、内容补充、找答案等附加服务。
- 2、"仅部分预览"的文档,不可在线预览部分如存在完整性等问题,可反馈申请退款(可完整预览的文档不适用该条件!)。
- 3、如文档侵犯您的权益,请联系客服反馈,我们会尽快为您处理(人工客服工作时间:9:00-18:30)。
d——加工纹理方向符号
表面粗糙度的代号及其标注位置 e——加工余量(mm) f——粗糙度间距参数值(mm)或轮廓支 承长度率(%)
4.2 表面粗糙度的评定
4.2.1 与评定参数有关的术语及定义
1.取样长度l(sampling length)——指用于判别具有表面 粗糙度特征的一段基准线长度,它在轮廓总的走向上量取。
规定和选取取样长度的目的是为了限制和削弱表面波纹 度对表面粗糙度测量结果的影响。 2.评定长度ln(evaluation length)——指评定轮廓所必 须的一段长度,它包括一个或几个取样长度。 ln=5l
4.3 表面粗糙度的选用
4.3.1 评定参数的选用
1.高度评定参数的选用
高度参数Ra、Rz中任选一个,但在常用值范围内(Ra为 0.025~6.3μm),国标推荐优先选用Ra。 对应力集中而导致疲劳破坏较敏感的表面,可在选取Ra同 时选取Rz参数,达到控制轮廓的最大高度不超过规定的允许值。
2.附加评定参数的选用
4.2.2 评定参数 为了完善地评定零件表面实际轮廓的粗糙程度,需要从 不同方向规定适当的参数。 高度特征参数、间距特征参数、形状特征参数 1.高度特征参数——沿着垂直于评定基准线的方向计量。 (1)轮廓算术平均偏差Ra——在取样长度内,轮廓偏距 绝对值的算术平均值。 l |y(x)| dx Ra= 1 ∫ 0 l
取样长度2.5mm
加工方法(铣削)
总加工余量(5mm)
附加标注示例
表面加工纹理方向
部分加工纹理方向符号
说
明
(1)当允许在表面粗糙度参数的所有实测值中超过规定值的个 数少于总数的16%时,应在图样上标注表面粗糙度参数的上限值或 下限值;
代号 意义
用任何方法获得的表面粗糙度, Ra的上限值为3.2μm 用去除材料的方法获得的表面粗 糙度,Ra的上限值为3.2μm 用不去除材料方法获得的表面粗 糙度,Ra的上限值为3.2μm 用去除材料方法获得的表面粗糙 度,Ra的上限值为3.2μm,Ra的下限 值为1.6μm
i= 1
3.形状特征参数——用轮廓支承长度率tp表示。 轮廓支承长度率tp——在取样长度内,一平行于中线与轮 廓相截所得到的各段截线长度bi之和与取样长度之比。 n 1 tp= ∑ b i l i= 1
与高度特性有关的参数(Ra,Rz)是标准规定必须标注 的参数,故称为基本评定参数。间距特性参数(Sm,S)与 形状特征参数(tp)称为附加参数,只有零件表面有特殊使 用要求时才选用。
4.4 表面粗糙度的标注
GB/T 131—93规定了零件表面粗糙度符号、代号及其 在图样上的注法。图样上所标注的表面粗糙度符号、代号 应是该表面完工后的要求。
4.4.1 表面粗糙度的符号 Nhomakorabea2H
H=1.4倍的字高
若仅表示需要加工(采用去除材料的方法或不去除材料的方法),但 对表面粗糙度的其他规定没有要求时,允许只注表面粗糙度符号。
12.5
未注表面粗糙度应在图纸的右上 角注出
2 3.
12.5
其余
2 锪平
6.3
地位狭小或不便标注时,符号、 代号可以引出标注
3. 2
0.8
6.3
1.6
抛光
同一表面粗糙度要求不同的注法
3.2
3.2
连续表面粗糙度注法
齿轮工作表面的粗糙度注法
改正如图所示表面粗糙度代号标注中的错误
4.5 表面粗糙度的测量
(3)对抗腐蚀性的影响 粗糙的表面,易使腐蚀性物质存积在表面的微观凹谷 处,并渗入到金属内部,致使腐蚀加剧。
(4)对疲劳强度的影响 零件表面越粗糙,凹痕就越深,当零件承受交变载荷 时,对应力集中就越敏感,使疲劳强度降低,导致零件表 面产生裂纹而损坏。
(5)对接触刚度的影响 接触刚度影响零件的工作精度和抗振性。这是由于表 面粗糙度使表面间只有一部分面积接触。一般情况下,实 际接触面积只有公称接触面积的百分之几。因此,表面越 粗糙受力后局部变形越大,接触刚度也越低。 (6)对结合面密封性的影响 粗糙的表面结合时,两表面只在局部点上接触,中间 有缝隙,影响密封性。因此,降低表面粗糙度,可提高其 密封性。
4.1 概 述
1.表面粗糙度(roughness)——指零件加工表面所具有 的较小间距和和微小峰谷不平度。 表面粗糙度形成的原因: 在加工过程中由于切削分离时金属断裂、切削层残留 面积、刀瘤脱落、鳞刺、受力所产生的金属塑性变形以及 工艺系统高频振动等原因。 表面粗糙度是一种微观几何形状误差,也称为微观不 平度。 表面不平度按表面轮廓误差曲线相邻两波峰或波谷之 间的距离(波距)λ 的大小划分为三类:
3.基准线——用于评定表面粗糙度参数给定的线。
(1)轮廓的最小二乘中线(简称中线 mean line)—— 具有几何轮廓形状并划分轮廓的基准线,在取样长度内使轮 廓上各点的轮廓偏距y的平方和为最小。
∫0 y dx=min
l
2
(2)轮廓的算术平均中线——在取样长度内,将实际轮 廓划分为上、下两部分,并使上、下两部分的面积相等的基 准线。 F1+F2+…Fn=S1+S2+…+Sm
3.2 1.6
3.2max
3.2max
Rz3.2max Rz1.6min
(2)当要求在表面粗糙度参数的所有实测值中不得超过规定值 时,应在图样上标注表面粗糙度参数的最大值或最小值;
表面粗糙度在图样中的标注方法
零件的每一个表面都应该有粗糙度要求,并且应在图样 上用代(符)号标注出来。 零件图上所标注的表面粗糙度代(符)号是指该表面完工 后的要求。 3.2
附加评定参数一般情况下不作为独立的参数选用。
只有零件的表面有特殊使用要求时,仅用高度特征参数 不能满足零件表面的功能 要求,才在选用了高度参数的基础 上,附加选用间距特征参数和形状特征参数。 一般情况下,对密封性、光亮度有特殊要求的表面,应 选用附加参数Sm或S。 为了使汽车外壳薄钢板具有较好的喷涂结合性和光洁美 观的外形,规定其高度特征参数Ra(0.9~1.3μm),还应控 制间距特征参数S(0.13~0.23mm) 对耐磨性有特殊要求的表面,应选用附加参数tp。
2.针描法——用电动轮廓仪测量
触针式电动轮廓仪是利用触针直接在被测表面上轻轻划过,从 而测出Ra值,测量值的范围一般为8~0.02μm。
性能比较完善的电动轮廓仪可以测量Ra 、Rz、Ry、Sm、S、tp各 参数。
3.光切法——用光切显微镜测量
光切显微镜又称双管显微镜。它可以测量Rz、Ry,以及规则表 面(车、铣、刨等)的Sm和S。测量的范围一般为0.5~60µm。
2.间距特征参数——沿着评定基准线的方向测量的, 反映表面加工痕迹细密程度。 (1)轮廓微观不平度的平均间距Sm——在取样长度内, 轮廓微观不平度的间距的平均值。 n Sm= 1 n ∑ Smi
i= 1
(2)轮廓的单峰平均间距S——在取样长度内,轮廓的 n 单峰间距的平均值。 1 S= n ∑ Si
在上述三个符号的长边上均可加一横线,用于标注有关参数和说 明
上述三个符号上均可加一小圆,表示所有表面具有相同的表面粗 糙度要求
4.4.2 表面粗糙度参数及其数值的标注 在表面粗糙度符号的基础上,注出表面粗糙度数值及其 有关的规定项目后就形成了表面粗糙度的代号。表面粗糙度 数值及其有关的规定在符号中注写的位置如下图所示。
H
表面粗糙度基本符号
图样上表示零件表面粗糙度的符号
符号 意义及说明
基本符号,表示表面可用任何方法获得。当不加注粗糙度参数值 或有关说明(例如:表面处理、局部热处理状况等)时,仅适用 于简化代号标注 基本符号加一短划,表示表面是用去除材料的方法获得。例如: 车、铣、钻、磨、剪切、抛光、腐蚀、电火花加工、气割等 基本符号加一小圆,表示表面是用不去除材料的方法获得。例 如:铸、锻、冲压变形、热轧、粉末冶金等。 或者用于保持原供应状况的表面(包括保持上道工序的状况)
C×45
3.2
表面粗糙度符号、 代号一般注在可见轮 廓线、尺寸界线、引 出线或它们的延长线 上。符号的尖端必须 从材料外指向表面
0.4
1.6
6 1.
12.5
1
5 2.
3.2
12
.5
30°
3.2
表面粗糙 度代号中数值 方向应与尺寸 数值方向一致
3.2
3.
2
12.5
3.2
30° 12
.5
3.2
12
.5
代号
意义
用任何方法获得的表面粗糙度,Ra 的最大值为3.2μm 用去除材料方法获得的表面粗糙 度,Ra的最大值为3.2μm 用不去除材料方法获得的表面粗糙 度,Ra的最大值为3.2μm 用去除材料方法获得的表面粗糙 度,Rz的最大值为3.2μm,Rz的最小值 为1.6μm
3.2
3.2max
3.2
3.2
S1—波峰 S2—波谷 如果被测表面粗糙不平,光带就弯曲。设表面微观不平度的高度为h, 则光带弯曲高度为S1S2=h /cos45o;而从目镜中看到的光带弯曲高度 S1”S2”=Kh/ cos45o(式中K为观测管的放大倍数)
表面粗糙度
4.1 4.2 4.3 4.4 4.5 概述 表面粗糙度的评定 表面粗糙度的选用 表面粗糙度的标注 表面粗糙度的测量
(1)表面粗糙度的含义及其对机械零件使用性能的影响。 (2)表面粗糙度的的评定标准和参数。
(3)零件表面粗糙度的选择。
(4)表面粗糙度的测量。 通过本章的学习,要求了解表面粗糙度对零件功能的 影响,掌握表面粗糙度的评定标准和参数,以及在图纸上 的标注方式。学会按零件表面的功能要求选择表面粗糙度 值,并会进行表面粗糙度的测量。