FMEA-Eng-3-8-00
FMEA简述

缺陷产品;不需要分拣;需要向供应商提供反馈
触感令人略微感觉不舒服。
1
非常低 没有可觉察到的影响
没有可觉察到的影响或没有影响
没有可觉察到的影响。
注:绿色为公司重点采用的相关评判标准,灰色为不常用标准。
十、第五版FMEA内容——失效原因
· 由小组结合特定的知识和经验来确定 · 失效原因能够直接确定或者通过理解失效的原理来确定
八、第四版FMEA
过程步骤/功能
要求
潜在失效模式
潜在失效影 响
SEV 严重度
分类
潜在失效原因
OCC发生 度
现行过程控制 预防
Plasma清洗
芯片背面 无污染
D/B 焊胶层 芯片背面污染 脱落,电参
失效
8
Plasma能量&时间参 数不恰当 Plasma工艺气压值偏 小或偏大
气体流量偏小
1.限制参数编辑权限,仅工程部负责人有
· 描述失效模式对客户的影响:
- 内部客户(下一个操作/后续操作/操作目标) - 外部客户(下一级/OEM/经销商)政府法律法规
- 产品或产品最终用户/操作者 - 立法机构
要求 四个螺钉
失效模式
影响
最终顾客:座垫松动,有噪音。
少于四个螺钉 制造和装配:由于受影响的部分,因而停止发
运,并进行额外挑选和返工。
1.要求作业员每班检查气罐接口是否漏气 2.气体流量超出范围时,设备自动报警
DET RP 探测度 N
4 64
4 64 2 32
推荐措施 NONE NONE NONE
Action Results/实施结果
职责和目标完 成日期
采取的措施 和有效日期
SE V 严重 度
2024年度FMEA培训教材ppt完整版

等级并制定应对措施,可提高系统或产品的可靠性和安全性。
2024/3/23
02 03
改进策略的制定
根据FMEA分析结果,针对高风险和中风险故障模式制定改进策略,包 括设计优化、工艺改进、材料替换等,以降低故障发生的可能性和影响 程度。
改进效果的跟踪
实施改进策略后,需对改进效果进行跟踪和评估,确保改进措施的有效 性。同时,将改进经验反馈到FMEA分析中,不断完善和优化分析过程 。
掌握了FMEA实施的基本技能
通过课程中的案例分析和实践操作,学员们表示已经掌握 了FMEA实施的基本技能,能够独立完成简单的FMEA分析 工作。
增强了团队协作和沟通能力
在课程中,学员们分组进行讨论和案例分析,不仅增强了 团队协作能力,还提高了沟通能力。
34
未来发展趋势预测
2024/3/23
01 02 03
23
05 FMEA在产品设 计阶段应用实践
2024/3/23
24
产品设计阶段FMEA实施流程
流程概述
01 明确FMEA在产品设计阶段的
目标和重要性,以及实施的基 本步骤。
团队组建与培训
02 组建专业的FMEA团队,并进
行必要的培训和技能提升。
功能分析与结构分解
03 对产品的功能进行详细分析,
并进行结构分解,以明确潜在 故障模式。
12
评估方法选择及实施流程
• 方法选择:根据失效模式的性质和影响程度选择合适的评 估方法,如风险矩阵、风险指数等。
2024/3/23
13
评估方法选择及实施流程
实施流程
1. 明确评估目标和范围
2. 收集相关数据和信息
2024/3/23
14
FMEA评分标准-含第四版

5 中等偶然 ≤0.2% Cpk≥1.0
2个 每1000辆车/项目
4 中等偶然 ≤0.1% Cpk≥1.10
1个 每1000辆车/项目
3 低,很少 ≤0.05% Cpk≥1.20
0.5个 每1000辆车/项目
2 低,很少 ≤0.01% Cpk≥1.30
0.1个 每1000辆车/项目
1 极低,不太可能≤0.001%Cpk≥1.67
配合和外观/尖响和卡嗒项目不舒服。有辨 识力顾客(25%以下)能发觉缺陷。
或部分(小于100%)产品可能需要 返工,无报废,在生产线上其它工 位返工。
1 无 无可辨别的后果。
1
无
无可辨别的影响
或对操作或操作者而言有轻微的不 方便或无影响。
推荐的DFMEA频度评价准则
发生度 O
可能的失效
10 很高,持续>5% Cpk<0.55
0.5件/每千件;每2,000件中有一件 0.1件/每千件;每10,000件中有一件 0.01件/每千件;每100,000件中有一件 ≤0.001件/每千件;每1,000,000件中有一件
通过预防控制消除失效
等级 PPK
10 <0.55
9
0.55
8
0.78
7
0.86
6
1.00
5
1.20
4
1.30
3
1.67
2
≥1.67
1
.推荐的DFMEA探测度评价准则
可探测度 D 准则:设计控制可能探测出来的可能性
探测度 定级
10 几乎不可能
设计控制将不能和/或不可能找出潜在的起因/ 机理及后续的失效小
设计控制只有很极少的机会能找出潜在的起因/ 机理及后续的失效模式
FMEA的严重度分级
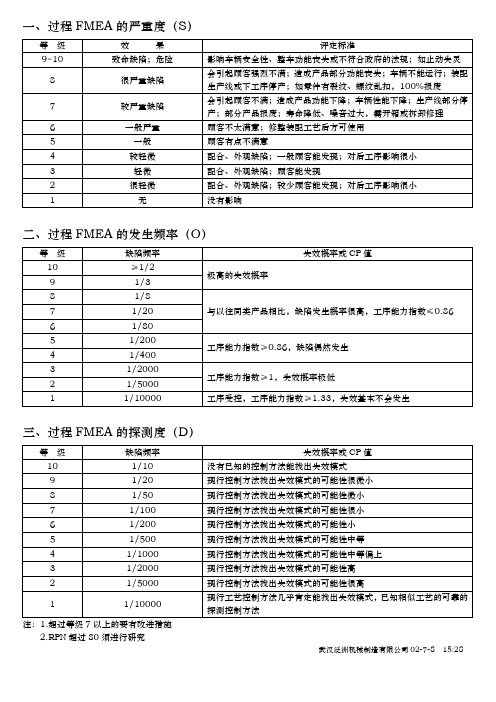
1/1000
现行控制方法找出失效模式的可能性中等偏上
3
1/2000
现行控制方法找出失效模式的可能性高
2
1/5000
现行控制方法找出失效模式的可能性很高
1
1/10000
现行工艺控制方法几乎肯定能找出失效模式,已知相似工艺的可靠的探测控制方法
注:1.超过等级7以上的要有改进措施
2.RPN超过80须进行研究
武汉泛洲机械制造有限公司02-7-8 15:28
9
1/3
8
1/8
与以往同类产品相比,缺陷发生概率很高,工序能力指数≤0.86
7
1/20
6
1/80
5
1/200
工序能力指数≥0.86,缺陷偶然发生
4
1/400
3
1/2000
工序能力指数≥1,失效概率极低
2
1/5000
1
1/10000
工序受控,工序能力指数≥1.33,失效基本不会发生
三、过程FMEA的探测度(D)
等 级
缺陷频率
失效概率或CP值
10
1/10
没有已知的控制方法能找出失效模式
9
1/20
现行控制方法找出失效模式的可能性很微小
8
1/50
现行控制方法找出失效模式的可能性微小
7
1/100
现行控制方法找出失效模式的可能性很小
6
1/200
现行控制方法找出失效模式的可能性小
5
1/500
现行控制方法找出失效模式的可能性中等
6
一般严重
顾客不太满意;修整装配工艺后方可使用
5
一般
顾客有点不满意
4
2019年新版FMEA手册(中文版)
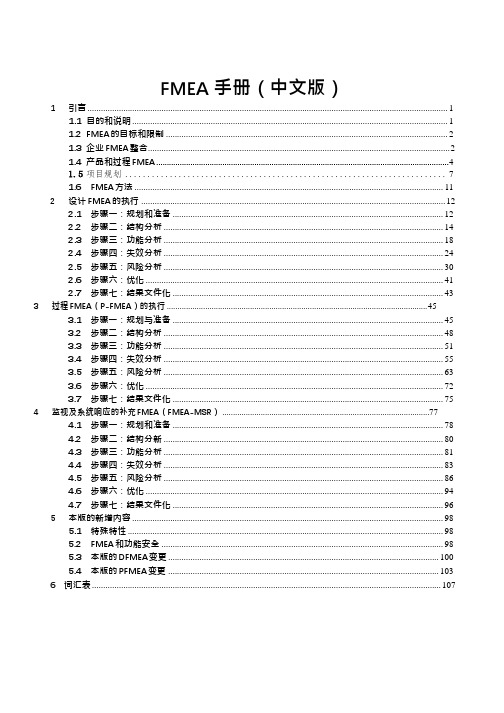
FMEA 手册(中文版)1引言 (1)1.1目的和说明 (1)1.2FMEA 的目标和限制 (2)1.3企业FMEA 整合 (2)1.4产品和过程FMEA (4)1.5项目规划 (7)1.6FMEA 方法 (11)2设计FMEA 的执行 (12)2.1步骤一:规划和准备 (12)2.2步骤二:结构分析 (14)2.3步骤三:功能分析 (18)2.4步骤四:失效分析 (24)2.5步骤五:风险分析 (30)2.6步骤六:优化 (41)2.7步骤七:结果文件化 (43)3过程FMEA(P-FMEA)的执行 (45)3.1步骤一:规划与准备 (45)3.2步骤二:结构分析 (48)3.3步骤三:功能分析 (51)3.4步骤四:失效分析 (55)3.5步骤五:风险分析 (63)3.6步骤六:优化 (72)3.7步骤七:结果文件化 (75)4监视及系统响应的补充F MEA(FMEA-MSR) (77)4.1步骤一:规划和准备 (78)4.2步骤二;结构分新 (80)4.3步骤三:功能分析 (81)4.4步骤四:失效分析 (83)4.5步骤五:风险分析 (86)4.6步骤六:优化 (94)4.7步骤七:结果文件化 (96)5本版的新增内容 (98)5.1特殊特性 (98)5.2FMEA 和功能安全 (98)5.3本版的DFMEA 变更 (100)5.4本版的PFMEA 变更 (103)6 词汇表 (107)1引言本联合出版物是美国汽车工业行动集团(AIAG)与德国汽车工业联合会(VDA)的整车厂(OEM)和一级供应商成员合作逾三年的成果。
本手册已进行改写,并在几个关键领域对 FMEA 方法进行了修订。
其目的是为这些组织所代表的汽车行业提供 FMEA 通用基础知识。
尽管我们尽了最大努力以达成共识,但可能仍有必要参考特定公司的出版物或顾客特定要求(CSR)。
一种新方法:本手册增加一个新的 FMEA 类别,即监视及系统响应 FMEA (FMEA-MSR)。
(完整版)FMEA简介

FMEA简介[ 2004年3月5日,阅读人数1024人 ]失效模式和效果分析(Failure Mode and Effect Analysis, FMEA)是一种用来确定潜在失效模式及其原因的分析方法。
具体来说,通过实行FMEA,可在产品设计或生产工艺真正实现之前发现产品的弱点,可在原形样机阶段或在大批量生产之前确定产品缺陷。
FMEA最早是由美国国家宇航局(NASA)形成的一套分析模式,FMEA是一种实用的解决问题的方法,可适用于许多工程领域,目前世界许多汽车生产商和电子制造服务商(EMS)都已经采用这种模式进行设计和生产过程的管理和监控。
FMEA简介FMEA有三种类型,分别是系统FMEA、设计FMEA和工艺FMEA,本文中主要讨论工艺FMEA。
实施FMEA管理的具体步骤见图1。
确定产品需要涉及的技术、能够出现的问题,包括下述各个方面:需要设计的新系统、产品和工艺;对现有设计和工艺的改进;在新的应用中或新的环境下,对以前的设计和工艺的保留使用;形成FMEA团队。
理想的FMEA团队应包括设计、生产、组装、质量控制、可靠性、服务、采购、测试以及供货方等所有有关方面的代表。
记录FMEA的序号、日期和更改内容,保持FMEA始终是一个根据实际情况变化的实时现场记录,需要强调的是,FMEA文件必须包括创建和更新的日期。
创建工艺流程图。
工艺流程图应按照事件的顺序和技术流程的要求而制定,实施FMEA需要工艺流程图,一般情况下工艺流程图不要轻易变动。
列出所有可能的失效模式、效果和原因、以及对于每一项操作的工艺控制手段:1.对于工艺流程中的每一项工艺,应确定可能发生的失效模式,如就表面贴装工艺(SMT)而言,涉及的问题可能包括,基于工程经验的焊球控制、焊膏控制、使用的阻焊剂(soldermask)类型、元器件的焊盘图形设计等。
2.对于每一种失效模式,应列出一种或多种可能的失效影响,例如,焊球可能要影响到产品长期的可靠性,因此在可能的影响方面应该注明。
fmea评级标准及示例
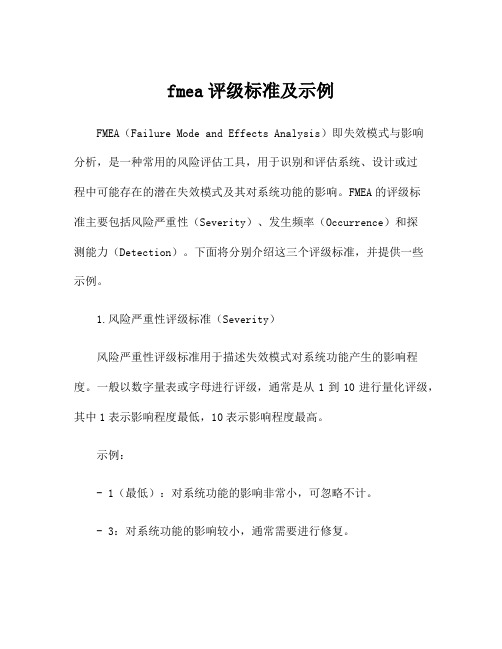
fmea评级标准及示例FMEA(Failure Mode and Effects Analysis)即失效模式与影响分析,是一种常用的风险评估工具,用于识别和评估系统、设计或过程中可能存在的潜在失效模式及其对系统功能的影响。
FMEA的评级标准主要包括风险严重性(Severity)、发生频率(Occurrence)和探测能力(Detection)。
下面将分别介绍这三个评级标准,并提供一些示例。
1.风险严重性评级标准(Severity)风险严重性评级标准用于描述失效模式对系统功能产生的影响程度。
一般以数字量表或字母进行评级,通常是从1到10进行量化评级,其中1表示影响程度最低,10表示影响程度最高。
示例:- 1(最低):对系统功能的影响非常小,可忽略不计。
- 3:对系统功能的影响较小,通常需要进行修复。
- 5:对系统功能的影响中等,可能导致系统的一部分功能无法正常工作。
- 8:对系统功能的影响较大,可能导致系统整体性能下降。
- 10(最高):对系统功能的影响非常严重,可能导致系统完全失效。
2.发生频率评级标准(Occurrence)发生频率评级标准用于描述失效模式的发生频率,即出现该失效模式的概率。
评级一般也采用1到10的量化评级,其中1表示非常低的发生频率,10表示非常高的发生频率。
示例:- 1(最低):失效模式的发生频率极低,非常罕见。
- 3:失效模式的发生频率较低,可能偶尔会发生。
- 5:失效模式的发生频率中等,有一定的风险。
- 8:失效模式的发生频率较高,可能会频繁发生。
- 10(最高):失效模式的发生频率非常高,几乎肯定会发生。
3.探测能力评级标准(Detection)探测能力评级标准用于描述系统中是否存在针对失效模式的有效探测手段以及探测的可靠程度。
评级同样采用1到10的量化评级,其中1表示探测能力非常强,10表示完全没有探测能力。
示例:- 1(最低):对失效模式有非常强的探测能力,几乎不会出现漏检。
FMEA介绍(绝对经典版)
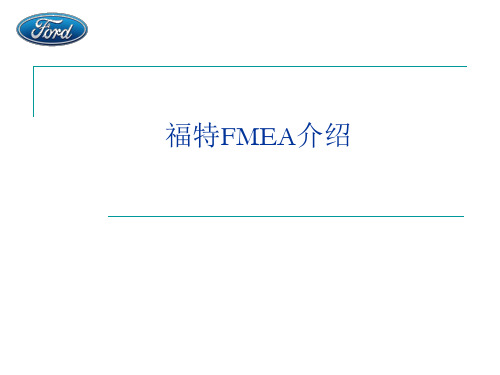
PFMEA:
流程图分析; 特性矩阵;
PFMEA的S/O/D 判定原则。
Change Point Approach 变化点的处理
FMEAs are living documents, and are updated when ... FMEA是动态文件,在以下情况下进行更新…
New design or process is planned 有新的设计或过程的变化 Modification to a component, process or system is planned, including those due to Global 8D 有部件,过程或系统的更改,包括由于G8D带来的更改 Component is to be used in new environment, location, or application 部件将要用于新的环境,位置或用途。
*Headdlamp Housing to Attachment
Attachment
Hood *Hood adjuster depth to Housing
GOP Align.
Tabs *Align tabs to Screws
Adjustment Screws (2) *Snap fit to Hdlm *Snap fit to Hdlm
*Elect Sys. to connector. Electrical System.
Environmental -Road salt *Elect Sys. location to Housing
Environmental -Road Material
* Denotes Relationship between hardware that goes on Interface Matrix
FMEA(失效模式与影响分析)

失效模式与影响分析即“潜在失效模式及后果分析”。
FMEA是在产品设计阶段和过程设计阶段,对构成产品的子系统、零件,对构成过程的各个工序逐一进行分析,找出所有潜在的失效模式,并分析其可能的后果,从而预先采取必要的措施,以提高产品的质量和可靠性的一种系统化的活动。
FMEA又根据产品故障可能产生的环节:设计、制造过程、使用、承包商(供应商)以及服务可细分为:1. DFMEA:设计FMEA2. PFMEA:过程FMEA3. EFMEA:设备FMEA4. SFMEA:体系FMEA一、概念潜在的失效模式及后果分析(Failure Mode and Effects Analysis,简记为FMEA),是“事前的预防措施”,并“由下至上。
关键词:潜在的—失效还没有发生,它可能会发生,但不一定会发生。
“核心”集中于:预防—处理预计的失效,其原因及后果/影响。
主要工作:风险评估—潜在失效模式的后果影响。
FMEA 开始于产品设计和制造过程开发活动之前,并指导贯穿实施于整个产品周期。
进行分析系统中每一产品所有可能产生的故障模式及其对系统造成的所有可能影响,并按每一个故障模式的严重程度,检测难易程度以及发生频度予以分类的一种归纳分析方法。
二、目的·能够容易、低成本地对产品或过程进行修改,从而减轻事后危机的修改。
·找到能够避免或减少这些潜在失效发生的措施;三、RPN的评价准则1.1 设计FMEA严重性(Severity :S)1)评分原则a)衡量是小的影响程度b)失效影响:产品或制程的某一失效对产品外观,结构,功能,性能稳定性,可靠性影响c)或对下一制程,使用者或设备的影响d)或对最终客户、政府法规、安全、环保的违及e)划分标准——主观判定2)设计:FMEA风险评估标准说明严重性(Severity :S):严重性是对下一个制程、系统或客户所发生的潜在失效模式效果的严重性进行评估,严重性仅适用于效果,严重性等级指数的减低只能透过设计变更才能够生效,严重性应该在1~10的等级上评估。
fmea 评分标准
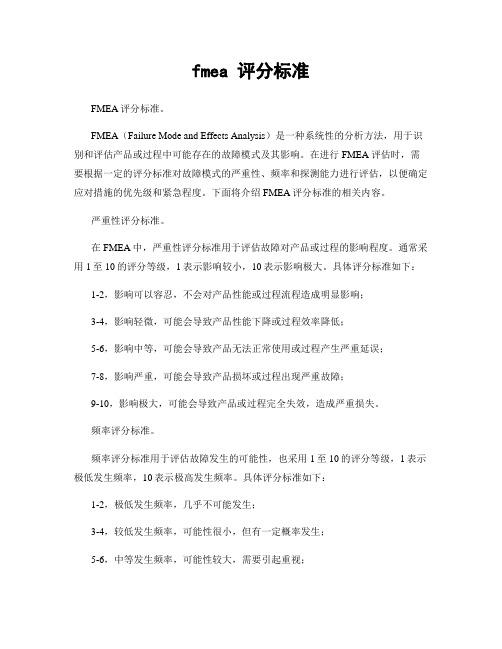
fmea 评分标准FMEA评分标准。
FMEA(Failure Mode and Effects Analysis)是一种系统性的分析方法,用于识别和评估产品或过程中可能存在的故障模式及其影响。
在进行FMEA评估时,需要根据一定的评分标准对故障模式的严重性、频率和探测能力进行评估,以便确定应对措施的优先级和紧急程度。
下面将介绍FMEA评分标准的相关内容。
严重性评分标准。
在FMEA中,严重性评分标准用于评估故障对产品或过程的影响程度。
通常采用1至10的评分等级,1表示影响较小,10表示影响极大。
具体评分标准如下:1-2,影响可以容忍,不会对产品性能或过程流程造成明显影响;3-4,影响轻微,可能会导致产品性能下降或过程效率降低;5-6,影响中等,可能会导致产品无法正常使用或过程产生严重延误;7-8,影响严重,可能会导致产品损坏或过程出现严重故障;9-10,影响极大,可能会导致产品或过程完全失效,造成严重损失。
频率评分标准。
频率评分标准用于评估故障发生的可能性,也采用1至10的评分等级,1表示极低发生频率,10表示极高发生频率。
具体评分标准如下:1-2,极低发生频率,几乎不可能发生;3-4,较低发生频率,可能性很小,但有一定概率发生;5-6,中等发生频率,可能性较大,需要引起重视;7-8,较高发生频率,经常会发生,需要立即采取措施;9-10,极高发生频率,几乎肯定会发生,需要立即采取紧急措施。
探测能力评分标准。
探测能力评分标准用于评估故障是否容易被检测到,也采用1至10的评分等级,1表示容易被检测到,10表示难以被检测到。
具体评分标准如下:1-2,容易被检测到,几乎可以立即发现;3-4,较容易被检测到,需要一定的检测手段才能发现;5-6,中等被检测到,需要较为复杂的检测手段才能发现;7-8,较难被检测到,需要专业的检测设备才能发现;9-10,难以被检测到,几乎不可能在事前发现,需要采取其他预防措施。
综合评分和优先级。
fmea评分标准
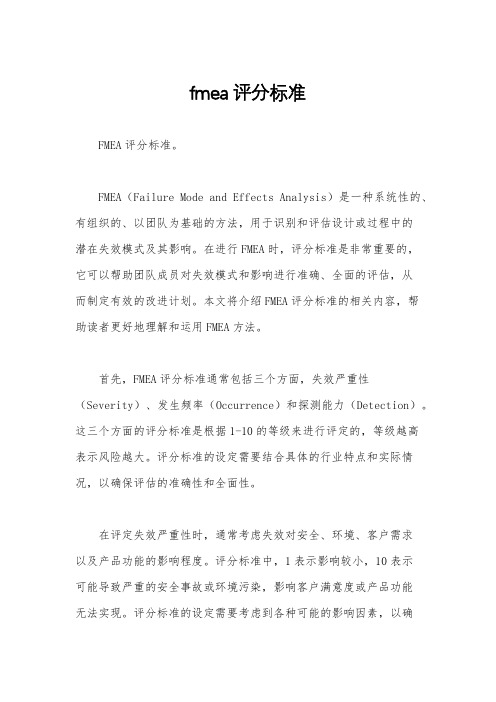
fmea评分标准FMEA评分标准。
FMEA(Failure Mode and Effects Analysis)是一种系统性的、有组织的、以团队为基础的方法,用于识别和评估设计或过程中的潜在失效模式及其影响。
在进行FMEA时,评分标准是非常重要的,它可以帮助团队成员对失效模式和影响进行准确、全面的评估,从而制定有效的改进计划。
本文将介绍FMEA评分标准的相关内容,帮助读者更好地理解和运用FMEA方法。
首先,FMEA评分标准通常包括三个方面,失效严重性(Severity)、发生频率(Occurrence)和探测能力(Detection)。
这三个方面的评分标准是根据1-10的等级来进行评定的,等级越高表示风险越大。
评分标准的设定需要结合具体的行业特点和实际情况,以确保评估的准确性和全面性。
在评定失效严重性时,通常考虑失效对安全、环境、客户需求以及产品功能的影响程度。
评分标准中,1表示影响较小,10表示可能导致严重的安全事故或环境污染,影响客户满意度或产品功能无法实现。
评分标准的设定需要考虑到各种可能的影响因素,以确保评估的全面性和准确性。
其次,发生频率评分标准通常考虑失效发生的可能性和频率。
评分标准中,1表示极低的发生概率,10表示极高的发生概率。
在评定发生频率时,需要考虑到失效的原因、历史数据、设备状态等因素,以确保评估的客观性和准确性。
最后,探测能力评分标准通常考虑探测失效的能力和有效性。
评分标准中,1表示能够及时有效地探测失效,10表示无法及时有效地探测失效。
在评定探测能力时,需要考虑到检测方法、设备状态、操作人员技能等因素,以确保评估的全面性和准确性。
综上所述,FMEA评分标准对于准确评估失效模式和影响非常重要。
评分标准的设定需要结合实际情况,确保评估的全面性和准确性。
团队成员在进行FMEA时,需要按照评分标准进行评定,以便制定有效的改进计划,降低潜在的风险。
希望本文能够帮助读者更好地理解和运用FMEA方法,提高产品质量和生产效率。
2024版年度FMEA培训教材版本

施效果。
21
改进措施实施计划编制要点
明确实施目标与时间节点
设定清晰的实施目标和时间节点,确保改进措施按计划推进。
细化实施步骤与责任分工
详细规划实施步骤,明确责任分工,确保各项任务得到有效落实。
2024/2/2
风险评估与预案制定
对实施过程中可能遇到的风险进行评估,并制定相应的预案,确保 改进措施平稳推进。
2024/2/2
18
实例演示:某产品FMEA分析
产品概述
FMEA分析过程
改进措施及效果
以某电子产品为例,该产品具有多种功 能,包括通信、数据处理和显示等。在 产品设计阶段,需要进行FMEA分析以 识别潜在的故障模式并采取相应的改进 措施。
首先,组建一个由设计、制造、质量等 人员组成的FMEA团队。然后,收集产 品的设计文档、历史故障数据等相关信 息。接下来,团队成员一起讨论并识别 潜在的故障模式,对每个故障模式进行 评估并计算RPN值。最后,根据RPN 值的大小进行优先级排序,并制定相应 的改进措施。
随着智能制造、工业互联网等新兴技术的不断发展,FMEA的应用领域将进一步拓展,需要 关注这些领域的新需求和新挑战。
FMEA方法和工具创新
随着大数据、人工智能等技术的不断进步,FMEA的方法和工具也将不断创新和完善,需要 关注这些新技术在FMEA中的应用前景。
2024/2/2
FMEA培训和人才培养
针对FMEA专业人才的需求,需要加强FMEA培训和人才培养工作,提高从业人员的专业素养 和综合能力。
25
学员心得体会分享交流环节
2024/2/2
学员心得分享
邀请几位优秀学员代表分享他们在 学习过程中的心得体会,以及在实 际工作中应用FMEA的经验和成果。
第五版FMEA管理程序

1.目的通过潜在失效模式及后果分析(以下简称FMEA)活动的开展,确定与产品设计和过程相关的潜在失效模式,分析失效后果及其起因,确定消除和减少潜在失效发生机会的措施,并将全过程文件化,使新开发产品的质量及交期满足顾客要求。
2.适用范围适用于对产品设计和制造过程开展的FMEA活动,包括设计、过程FMEA。
3.职责3.1总经理或管理者代表指定有关人员作为FMEA小组组长,并任命其领导FMEA活动。
3.2工程部、制造课、业务部(可行时包括顾客代表)、品保部等部门负责人作为小组成员参加FMEA活动3.3 FMEA小组长: FMEA活动的策划和组织;组织并协调各组员参与FMEA活动;组织相关责任单位完成优化措施;确认FMEA执行效果。
3.4 FMEA组员及相关部门职责:参与FMEA活动的7个步骤,包括:规划和准备、结构分析、功能分析、失效分析、风险分析、优化措施、结果文件化。
4.术语和定义无5.程序内容5.1 FMEA的开发时机5.1.1 FMEA为一份动态文件,应是:DFMEA:始于设计概念形成之时,更新于开发的各阶段更改之中,终于产品设计完成之前;针对设计意图并假定据此生产,考虑制造、维护和回收的需求。
PFMEA:在过程可行性分析阶段和生产工装准备到位之前开始,并考虑所有过程工序、产品特殊特性。
原则上一年更新一次,有投诉,变更或异常时等进行及时更新。
在下列情况应通过FMEA开发:➢新设计、新技术或新过程;➢对已有的设计或过程(含已有FMEA)的修改;➢将现有的设计或过程(含已有FMEA)用于新环境、场所或应用。
5.1.3 当产品仅为局部设计变化、工艺局部调整时可在原型FMEA文件中作高风险类的项目控制开发。
5.2 FMEA活动实施结合第五版FMEA手册要求,FMEA活动实施分为:规划和准备、结构分析、功能分析、失效分析、风险分析、优化措施、结果文件化等7个步骤。
规划和准备:本步骤工作核心内容为确定项目、项目计划、分析的范围/边界、基准FMEA的确定和选择。
fmea-msr对应的国际标准

在全球范围内,FMEA(Failure Mode and Effects Analysis,故障模式及影响分析)和MSR(Measurement System Analysis,测量系统分析)被公认为是生产和质量管理中至关重要的工具和方法。
针对这一主题,我们将深入探讨这两种工具在国际标准化方面的应用和发展。
1. FMEA(故障模式及影响分析)是一种系统性的方法,用于发现并消除产品或流程中的潜在故障,从而保证产品的质量和可靠性。
在国际标准化方面,FMEA得到了广泛的认可和应用。
ISO/TS 16949标准和本人AG(汽车工业行动小组)的FMEA手册是业界公认的FMEA标准,这些标准详细规定了FMEA的执行流程、方法和工具,使得FMEA成为了国际上广泛使用的先进质量管理工具。
2. MSR(测量系统分析)是另一个在国际标准化方面备受重视的工具。
它用于评估和确保生产中使用的测量系统的准确性和可靠性。
针对这一领域,国际上广泛应用的标准包括ISO 10012和ISO/TS 16949,这些标准规定了测量系统分析的流程和方法,确保了全球范围内的测量系统评估的一致性和可比性。
3. 国际标准化组织(ISO)和其他国际标准组织在FMEA和MSR领域的标准开发工作中,不断加强国际标准的协调和统一。
他们致力于确保各国之间的质量管理标准在内容和体系结构上的一致性,促进全球范围内品质管理的协调和发展。
总结而言,FMEA和MSR在国际标准化方面得到了广泛的应用和认可。
随着国际标准的不断完善和协调,这两种工具在全球范围内的应用将对产品生命周期各个阶段的质量管理产生重要的影响。
对于企业而言,深入理解和应用这两种工具,将有助于提升产品质量、降低成本,进而在市场竞争中获得更大的优势。
FMEA和MSR是在生产和质量管理过程中极其重要的工具和方法。
它们帮助企业发现潜在的故障和问题,并通过系统性的分析和评估来解决这些问题,从而提高产品的质量和可靠性。
FMEA风险评估(DPN)

FMEA风险评估(DPN)风险评估是一种用于识别和评估潜在风险的工具,对产品或过程进行风险分析,并制定相应的应对计划。
这样可以帮助组织预防和减少可能发生的问题,并提高产品或过程的质量和可靠性。
FMEA(Failure Mode and Effects Analysis)是一种常用的风险评估方法,被广泛应用于各个行业。
DPN方法(Design Process New)DPN方法是针对产品设计和开发过程中的风险评估而提出的。
它强调在设计过程中尽早识别和解决潜在的问题,以避免在后期开发过程中造成重大的影响。
FMEA风险评估步骤1. 识别潜在失效模式:对产品或过程进行系统性的分析,识别出可能发生的失效模式。
这些失效模式可以包括物理性失效、功能性失效、可靠性失效等。
识别潜在失效模式:对产品或过程进行系统性的分析,识别出可能发生的失效模式。
这些失效模式可以包括物理性失效、功能性失效、可靠性失效等。
2. 评估失效影响:对每个失效模式进行评估,分析其对产品或过程的影响程度。
可以考虑到人身安全、产品性能、生产效率等方面的影响。
评估失效影响:对每个失效模式进行评估,分析其对产品或过程的影响程度。
可以考虑到人身安全、产品性能、生产效率等方面的影响。
3. 确定失效原因:对每个失效模式进行分析,找出导致该失效的可能原因。
这可以帮助制定相应的预防和纠正措施。
确定失效原因:对每个失效模式进行分析,找出导致该失效的可能原因。
这可以帮助制定相应的预防和纠正措施。
4. 评估风险等级:将失效模式的影响程度和发生概率综合考虑,确定风险等级。
常用的评估指标包括风险优先数(RPN)等。
评估风险等级:将失效模式的影响程度和发生概率综合考虑,确定风险等级。
常用的评估指标包括风险优先数(RPN)等。
5. 制定应对计划:针对高风险等级的失效模式,制定相应的应对计划。
这可以包括改进设计、增加安全措施、加强质量控制等措施。
制定应对计划:针对高风险等级的失效模式,制定相应的应对计划。
FMEA严重性评估参考标准(中英文)
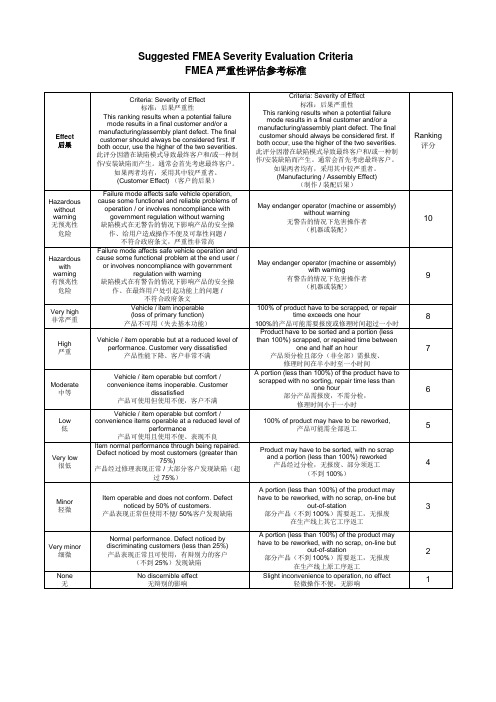
Level 级别
Probability 可能性
Very high 非常高
High 高
Persistent failures 缺陷持续不断
Frequent failures 缺陷频繁出现
Moderate 中等
Occasional failures 缺陷偶尔出现
Low 低
Remote 几乎不会
Relatively few failures 缺陷相对较少
or involves noncompliance with government regulation with warning
缺陷模式在有警告的情况下影响产品的安全操 作、在最终用户处引起功能上的问题 / 不符合政府条文 Vehicle / item inoperable (loss of primary function) 产品不可用(失去基本功能)
than 100%) scrapped, or repaired time between one and half an hour
产品须分检且部分(非全部)需报废、 修理时间在半小时至一小时间
A portion (less than 100%) of the product have to scrapped with no sorting, repair time less than one hour 部分产品需报废,不需分检, 修理时间小于一小时
11返工无报废在生产线上原工序返工2none无nodiscernibleeffect无辩别的影响slightinconveniencetooperationnoeffect轻微操作不便无影响1fmeaoccurrenceevaluationcriteriafmea机率性评估参考标准level级别probability可能性likelyfailurerates可能出现的缺陷机率dppm以一百万块板里的缺陷数计dppmppkranking评分veryhigh非常高persistentfailures缺陷持续不断100perthousandpieces5
FMEA严重度、频度和可探测度培训标准
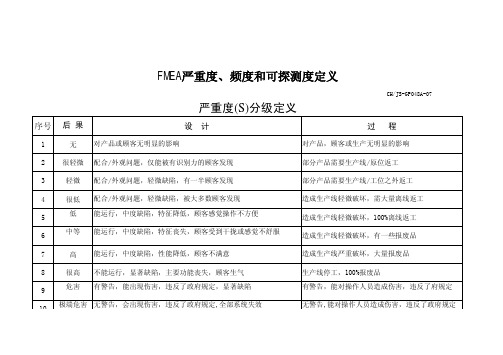
序号 后 果
严重度(S)分级定义
设计
CH/JS-GP048A-07
过程
1
无 对产品或顾客无明显的影响
对产品,顾客或生产无明显的影响
2 很轻微 配合/外观问题,仅能被有识别力的顾客发现
部分产品需要生产线/原位返工
3
轻微 配合/外观问题,轻微缺陷,有一半顾客发现
部分产品需要生产线/工位之外返工
现了缺陷.现行控制方法不能探测出失效原因
过程
现行控制能100%探测出失效模式,已知相似 过程的探测控制是可靠的,没理由漏掉缺陷 现行控制能很有效探测出失效模式, 90%、100%自动检测 现行控制能很有效探测出失效模式, 80%、100%自动检测 现行控制能很有效探测出失效模式,>70% 测量方便,应用SPC 现行控制可能探测出失效模式,>60% 测量不方便,应用SPC 现行控制可能探测出失效模式,>50% 测量不方便,未使用SPC 现行控制可能探测出失效模式,>40% 测量不方便,未使用SPC 现行控制不太可能探测出失效模式,<40% 目测 现行控制不太可能探测出失效模式,<25% 目测 无现行控制,顾客了现了缺陷,现行控制方法 不能探测出失效原因或模式
4
很低 配合/外观问题,轻微缺陷,被顾客感觉操作不方便
6
中等 能运行,中度缺陷,特征丧失,顾客受到干拢或感觉不舒服
造成生产线轻微破坏,需大量离线返工 造成生产线轻微破坏,100%离线返工 造成生产线轻微破坏,有一些报废品
7
高 能运行,中度缺陷,性能降低,顾客不满意
参考已证实的类似应用
8
高
设计人员很少的经验和/或能 相似过程经常出现失效
参考已证实的类似应用
(品管工具FMEA)-FMEA应用指导书
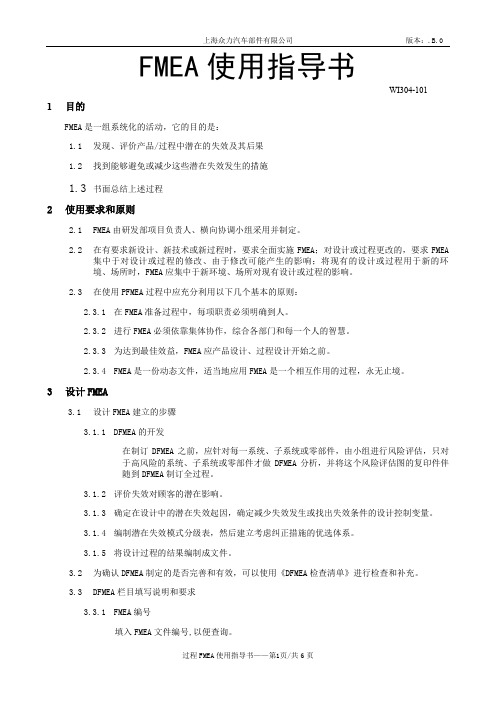
FMEA使用指导书WI304-1011目的FMEA是一组系统化的活动,它的目的是:1.1发现、评价产品/过程中潜在的失效及其后果1.2找到能够避免或减少这些潜在失效发生的措施1.3书面总结上述过程2使用要求和原则2.1FMEA由研发部项目负责人、横向协调小组采用并制定。
2.2在有要求新设计、新技术或新过程时,要求全面实施FMEA;对设计或过程更改的,要求FMEA集中于对设计或过程的修改、由于修改可能产生的影响;将现有的设计或过程用于新的环境、场所时,FMEA应集中于新环境、场所对现有设计或过程的影响。
2.3在使用PFMEA过程中应充分利用以下几个基本的原则:2.3.1在FMEA准备过程中,每项职责必须明确到人。
2.3.2进行FMEA必须依靠集体协作,综合各部门和每一个人的智慧。
2.3.3为达到最佳效益,FMEA应产品设计、过程设计开始之前。
2.3.4FMEA是一份动态文件,适当地应用FMEA是一个相互作用的过程,永无止境。
3设计FMEA3.1设计FMEA建立的步骤3.1.1DFMEA的开发在制订DFMEA之前,应针对每一系统、子系统或零部件,由小组进行风险评估,只对于高风险的系统、子系统或零部件才做DFMEA分析,并将这个风险评估图的复印件伴随到DFMEA制订全过程。
3.1.2评价失效对顾客的潜在影响。
3.1.3确定在设计中的潜在失效起因,确定减少失效发生或找出失效条件的设计控制变量。
3.1.4编制潜在失效模式分级表,然后建立考虑纠正措施的优选体系。
3.1.5将设计过程的结果编制成文件。
3.2为确认DFMEA制定的是否完善和有效,可以使用《DFMEA检查清单》进行检查和补充。
3.3DFMEA栏目填写说明和要求3.3.1FMEA编号填入FMEA文件编号,以便查询。
3.3.2项目名称填入所分析的系统、子系统或零件的名称、编号。
3.3.3设计责任部门填入整车厂、部门和横向协调小组。
如果知道,还应包括供方的名称。
纯化水系统风险评估(FMEA五分制法)
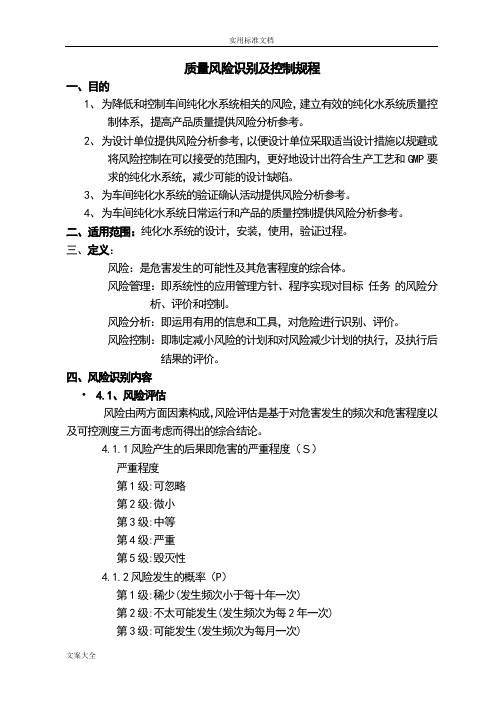
质量风险识别及控制规程一、目的1、为降低和控制车间纯化水系统相关的风险,建立有效的纯化水系统质量控制体系,提高产品质量提供风险分析参考。
2、为设计单位提供风险分析参考,以便设计单位采取适当设计措施以规避或将风险控制在可以接受的范围内,更好地设计出符合生产工艺和GMP要求的纯化水系统,减少可能的设计缺陷。
3、为车间纯化水系统的验证确认活动提供风险分析参考。
4、为车间纯化水系统日常运行和产品的质量控制提供风险分析参考。
二、适用范围:纯化水系统的设计,安装,使用,验证过程。
三、定义:风险:是危害发生的可能性及其危害程度的综合体。
风险管理:即系统性的应用管理方针、程序实现对目标任务的风险分析、评价和控制。
风险分析:即运用有用的信息和工具,对危险进行识别、评价。
风险控制:即制定减小风险的计划和对风险减少计划的执行,及执行后结果的评价。
四、风险识别内容• 4.1、风险评估风险由两方面因素构成,风险评估是基于对危害发生的频次和危害程度以及可控测度三方面考虑而得出的综合结论。
4.1.1风险产生的后果即危害的严重程度(S)严重程度第1级:可忽略第2级:微小第3级:中等第4级:严重第5级:毁灭性4.1.2风险发生的概率(P)第1级:稀少(发生频次小于每十年一次)第2级:不太可能发生(发生频次为每2年一次)第3级:可能发生(发生频次为每月一次)第4级:很可能发生(发生频次为每周一次) 第5级:经常发生(几乎每次都可能发生) 4.1.3风险发生时的可预知性(D)第1级:不可能预知第2级:不太可能预知第3级:可能预知第4级:很可能预知第5级:完全可预知4.2风险识别项目风险源风险详述风险可能导致的结果风险严重程度风险发生概率风险可预知性1 原水原水质量低含有大量泥砂,浑浊过滤器内石英砂使用期限缩短,进入活性炭过滤器的水质下降1 4 52 石英砂过滤器过滤器损坏石英砂进入活性炭过滤器中,降低活性炭过滤器效果,也可能损坏阀门2 1 13 活性炭过滤器过滤器损坏活性炭进入软化器中,使软化器不能正常工作2 1 14 软化器再生装置故障无法再生,影响一级水质3 2 2软化器泄漏未经软化的水进入一级反渗透膜,使一级水不3 1 1合格,也可能损坏一级膜或一级泵。
- 1、下载文档前请自行甄别文档内容的完整性,平台不提供额外的编辑、内容补充、找答案等附加服务。
- 2、"仅部分预览"的文档,不可在线预览部分如存在完整性等问题,可反馈申请退款(可完整预览的文档不适用该条件!)。
- 3、如文档侵犯您的权益,请联系客服反馈,我们会尽快为您处理(人工客服工作时间:9:00-18:30)。
• Detection, can it be detected if it goes wrong.
– P-Type controls- Preventing it from happening. – D- Type controls - Detect it if goes wrong.
Potential Cause of Failure
FMEA Purpose
• To reduce product or service concerns and to minimize the probability of defective product reaching the customer. • To identify potential failure modes and to rate the severity of their effects. • To identify the critical characteristics of the product or process. • To rank the order of potential design and process defects.
– – – – Next user. Ultimate user or customer. Product operation. Government regulations.
Severity Definition
• Severity is the assessment of the failure effects on the process as well as the product. • Severity rating apply to the effects and the effects only. • Severity assessment is focusing on both the process / operation and the product. • All causes of a failure mode having the same effect should be assigned the same severity ranking. • Severity ranking scale goes from 1 to 10.
RPN
Recommended Actions
Section 1: What Is FMEA
What is FMEA
• FMEA is the prefix of Potential Failure Mode and Effects Analysis. The word potential is omitted. • FMEA is a systematic method which identifies potential product problems in the following areas. – Product design. – Product manufacture. – Product use. • FMEA is developed by Chrysler,Ford,General Motors . • FMEA including DFMEA--Design FMEA & PFMEA--Process FMEA. • Based on SAE product characteristic, we will study PFMEA detailedly.
– Two Types of failure modes. • Failure to perform the required function. • Performs function poorly. • Performs a function that is not supposed to be there.
FMEA History
• Mid -60‟s: Started in the Aerospace Industries. • 1974: Navy created FMEA Standard. • 1976: US Department of Defense adopted an FMEA standard. • Late 70‟s: Automotive Industries started to use FMEA. • Early 80‟s: Micro Electronic Industry started to apply FMEA to assist in improving the “yield of memory devices”. • Mid 80‟s: Automotive industries started to apply FMEA to the manufacturing processes. • 90‟s: TQS 9000 recommended adoption of FMEA.
FMEA application in SAE
• Nonconforming prevention and correction • Failure analysis • QCC tools, major cause confirmation, action taking,and effect comparison • Others engineering area
Effects
• An effect of the failure mode that would be noticed or experienced at the next operation, at a subsequent operation, by any downstream user. • Consider:
Section 3: Elementary Concepts of FMEA
FMEA Concepts
• Function, what is supposed to happen here.
– What is the product or process objective.
• Failure Mode, what can go wrong here.
Current Controls
• Current controls are intended to prevent the cause of the failure from occurring, to detect the cause if it should occur, and to reduce the impacts of the failure effects. – For example: • SPC. • Fixture fool proofing. • Process DOE. • SE. approval. • Production validation. • Preventive maintenance program. • Gauge R-R study. • Operator training.
Process PFMEA Analysis Sheet
PFMEA
Process Analyzed _________________
Function
Potential Effect of Failure Mode Failure
Severity Cause of Occurrence Current Detection Failure Rate Process (1 - 10) (1- 10) Controls (1 - 10)
• Cause, how can it go wrong.
– Four types of possible causes. • Design related. • Manufacturing process related. • Application related. • Service related.
FMEA Concepts
• Effect, what happens when it goes wrong:
– Design possible effects. • Product end user. • Local user. • Other, in between users. – Process possible effects. • The product effects. • Process effects.
Failure Mode Sa rating corresponding to the seriousness of the effect of the potential failure mode. Severity Description (1) No effect on the system performance. (2) Very slight Effect. Nuisance fault noticed. (3) Slight Effect. Nuisance fault obvious. (4) Minor Effect. Chronic nuisance fault. (5) Moderate Effect. Nuisance repair required. (6) Significant Effect. Repair required. (7) Major Effect. Rework /repairs required. (8) Serious Effect. Equipment/very dissatisfied customer. (9) Very Serious Effect. Stop ship required. (10) Hazardous Effect, sudden failure , or non-compliance to regulations or liability issue.
• List all possible conceivable causes of each failure mode. • The list should be complete as possible so that corrective actions can be implemented effectively and timely. • It must be a process or manufacturing cause. • Use as much detail as possible to define the cause of the failure. • Consider: – Method, machinery, materials, people and environment.