2013年加工线OEE
oeko-tex 2013中文版
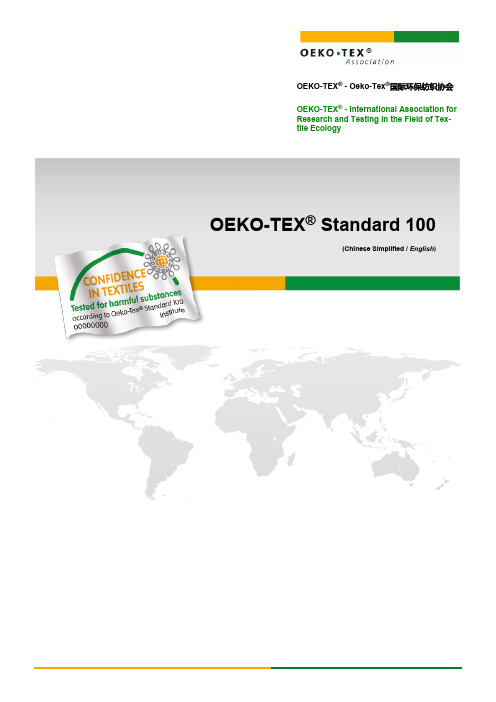
OEKO-TEX® - Oeko-Tex®国际环保纺织协会OEKO-TEX® - International Association forResearch and Testing in the Field of Tex-tile EcologyOEKO-TEX® Standard 100(Chinese Simplified / English)授权使用Oeko - Tex® Standard 100标签的一般和特殊条款General and special conditions for the authorisation to use the Oeko-Tex® Standard 100 mark内容Contents1目的1Purpose2适用范围2Applicability3条款及定义3Terms and definitions3.1有害物质 3.1Harmful substances3.2OEKO-TEX® Standard 100 标签 3.2OEKO-TEX® Standard 100 mark3.3生产商 3.3Manufacturer3.4销售商 3.4Distributor3.5产品名称 3.5Designation of product3.6产品组合 3.6Article group3.7产品类别 3.7Product classes3.8活性化学产品 3.8Active chemical products4条款4Conditions4.1产品特定要求 4.1Product specific requirements4.2使用生物活性产品的要求 4.2Requirements regarding the use of biological ac-tive products4.3使用阻燃产品的要求 4.3Requirements regarding the use of flame retard-ant products4.4申请 4.4Application4.5样品材料 4.5Sample material4.6承诺声明 4.6Declaration of commitment4.7检测 4.7Testing4.8质量控制 4.8Quality control4.9质量保证 4.9Quality assurance4.10符合性 4.10Conformity5标签5Marking5.1给予授权 5.1Granting of authorisation5.2授权限制 5.2Limit of authorisation5.3授权撤销 5.3Withdrawal of authorisation5.4标签类型 5.4Type of markingA1地址A1AdressesA2标签A2MarkA3包装指引A3Packing instructionsA4限量值A4Limit valuesA5个别物质A5Individual substances版本说明Impressum编辑Editor:OEKO-TEX®国际环保纺织协会International Association for Research and Testing inthe Field of Textile Ecology (OEKO-TEX®) Gotthardstr. 61Gotthardstr. 61P.O. Box 2156P.O. Box 2156CH-8027 Zürich (Switzerland)CH-8027 Zurich (Switzerland)出版Place of origin:Zurich (Switzerland)Zurich (Switzerland)印刷:Printing:自设复印系统Own copy system版本: 04/2013Edition: 04/2013€ 40.- / CHF 70.- / SEK 390.- / DKK 330.- / NOK 360.- / £ 34.- / Ft 6’100.-售价 / selling price(OEKO-TEX ®)出版的规范性文件,该协会的成员机构在附录一中列出。
数控机床oee计算方法(一)
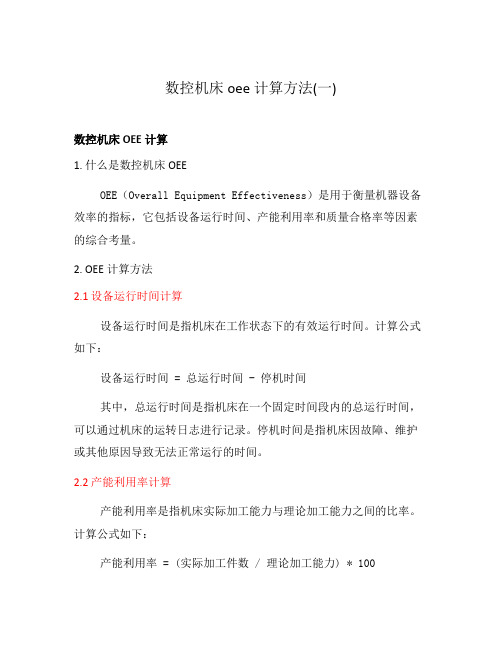
数控机床oee计算方法(一)数控机床OEE计算1. 什么是数控机床OEEOEE(Overall Equipment Effectiveness)是用于衡量机器设备效率的指标,它包括设备运行时间、产能利用率和质量合格率等因素的综合考量。
2. OEE计算方法2.1 设备运行时间计算设备运行时间是指机床在工作状态下的有效运行时间。
计算公式如下:设备运行时间 = 总运行时间 - 停机时间其中,总运行时间是指机床在一个固定时间段内的总运行时间,可以通过机床的运转日志进行记录。
停机时间是指机床因故障、维护或其他原因导致无法正常运行的时间。
2.2 产能利用率计算产能利用率是指机床实际加工能力与理论加工能力之间的比率。
计算公式如下:产能利用率 = (实际加工件数 / 理论加工能力) * 100实际加工件数是指在设备运行时间内机床实际加工的零件数量,理论加工能力是指在设备运行时间内机床理论上能够加工的最大零件数量。
2.3 质量合格率计算质量合格率是指机床加工零件中符合质量标准的比例。
计算公式如下:质量合格率 = (合格零件数量 / 总加工零件数量) * 100合格零件数量是指在设备运行时间内机床加工的符合质量标准的零件数量,总加工零件数量是指在设备运行时间内机床总共加工的零件数量。
3. OEE综合计算OEE综合计算是将设备运行时间、产能利用率和质量合格率三个方面综合考虑,得出一个综合评估指标。
计算公式如下:OEE = 设备运行时间× 产能利用率× 质量合格率OEE的取值范围为0~100,数值越高表示机床效率越高。
4. OEE计算的意义OEE计算可以帮助企业定量地评估机床设备的效率,并通过分析结果找出影响设备效率的关键因素。
通过优化设备运行时间、提高产能利用率和质量合格率,企业可以进一步提高生产效率,降低成本,提升市场竞争力。
5. 总结OEE计算是评估机床设备效率的重要工具,它能够帮助企业识别并改进影响设备效率的关键因素。
OEE的计算公式

OEE的计算公式OEE(Overall Equipment Effectiveness)是一种衡量设备效率和生产效果的关键性指标。
它是由美国自动化协会(American Productivity & Quality Center)提出并广泛应用于各类制造企业中。
设备的有效生产时间(Net Operating Time,也称为稼动时间)指的是设备在生产过程中的全部时间减去计划维修时间、预定停机时间和计划修整时间。
公式如下:稼动时间=总时间-计划维修时间-预定停机时间-计划修整时间设备的速度损失(Speed Loss)指的是设备在生产中由于速度低于设计速度而造成的损失时间。
这可能是由于设备故障、设备调试期间的运行速度下降、设备因为操作员的技术水平不高而无法达到最大速度等原因造成的。
公式如下:速度损失=稼动时间-设备实际运行时间设备的质量损失(Quality Loss)指的是由于生产过程中产生的次品和废品所导致的损失时间。
这可能是由于操作员技术不熟练、原材料质量问题、设备故障引起的废品等原因造成的。
公式如下:质量损失=稼动时间-合格产品产生的时间根据以上三个因素,可以计算出OEE的值。
OEE的计算公式如下:OEE=稼动时间×性能指标×质量指标其中性能指标(Performance Index)表示设备在生产中实际运行时间与设备理论运行时间的比值。
性能指标的计算公式为:性能指标=设备实际运行时间÷(设备理论运行时间×合格产品产生的时间)质量指标(Quality Index)表示合格产品产生的时间与设备实际运行时间的比值。
质量指标的计算公式为:质量指标=合格产品产生的时间÷设备实际运行时间将性能指标和质量指标代入OEE计算公式中,可以得到最终的OEE值。
OEE的计算公式

OEE是一个独立的测量工具,它用来表现实际的生产能力相对于理论产能的比率。
国际上对OEE的定义为:OEE是Overall Equipment Effectiveness(全局设备效率)的缩写,它由可用率(Availability time),表现性(Performance)以及质量指数(Quality)三个关键要素组成。
OEE的计算公式(不考虑设备加工周期的差异)=?OEE= 时间开动率×性能开动率×合格品率[1],[4]其中,时间开动率 = 开动时间/负荷时间而,负荷时间 = 日历工作时间-计划停机时间开动时间 = 负荷时间–故障停机时间–设备调整初始化时间(包括更换产品规格、更换工装模具、更换刀具等活动所用时间)性能开动率 = 净开动率×速度开动率而,净开动率 = 加工数量×实际加工周期/开动时间速度开动率 = 理论加工周期/实际加工周期合格品率 = 合格品数量/ 加工数量在OEE公式里,时间开动率反映了设备的时间利用情况;性能开动率反映了设备的性能发挥情况;而合格品率则反映了设备的有效工作情况。
反过来,时间开动率度量了设备的故障、调整等项停机损失,性能开动率度量了设备短暂停机、空转、速度降低等项性能损失;合格品率度量了设备加工废品损失。
例1: 设某设备1天工作时间为8h, 班前计划停机20min, 故障停机20min, 更换产品型号设备调整40min, 产品的理论加工周期为0.5min/件, 实际加工周期为0.8min/件, 一天共加工产品400件, 有8件废品, 求这台设备的OEE。
计算:负荷时间 = 480-20 = 460 min开动时间 = 460 – 20 – 40 = 400 min时间开动率 = 400/460 = 87%速度开动率 = 0.5/0.8 = 62.5%净开动率 = 400×0.8/400 = 80%性能开动率 = 62.5%×80% = 50%合格品率 = (400-8)/400 = 98%于是得到 OEE = 87%×50%×98% = 42.6%。
单台设备、生产线、多品种生产线三种OEE计算表

H2 不良损失 8.不良返修时间
H
不良损失时间H=H1+H论周期时间(理论C/T)
K
实际周期时间(实际C/T)=I/E
L
不良产品数量(报废)
M
不良返修数量(返修)
N
时间稼动率=(负荷时间-停止时间)/负荷时间=(C-D)/C=E/C
O
性能稼动率=理论C/T*总投入数/稼动时间=(J*I)/E=J/K
代号
项目
A
(工作时间)上班到下班的时间(包括加班)
B1
用餐时间
B2
工间休息时间
B3 计划损失 会议时间
B4 (停机(SD) 停工不生产时间
B5 损失) 设备点检、润滑及开展5S活动时间
B6
其他约定停止时间
B
计划停止时间B=B1+B2+B3+B4+B5+B6
C
设备负荷时间C=A-B
D1
1.设备故障时间(含换刀具)
P
良品率=(总投入数-不良数-返修数)/总投入数=(I-L-M)/I
OEE
OEE=N*O*P
510
660
30
30 20
50
30
460
630
70
50
30
70
80
390
550
0
0
390
550
0 418 0.8 1.1 8.36
84.8% 85.7% 98.0% 71.2%
0 200 0.8
10
87.3% 29.1% 95.0% 24.1%
0
0
0
0
0
0
0
0
0
OEE介绍及计算方法

OEE定义及计算公式
五﹑速度损失定义
速度损失时间分为两部分﹕ 1﹑速度降低 2﹑空转和小停顿 分别定义如下﹕ • 速度降低
机器操作中与理论速度的差异造成的损 失时间。 • 空转和小停顿损失
制程中由于小的停顿(比如断料)导致的 生产损失。
稼动时间(=负荷时间-停机时间)
时间稼动率 =
出勤时间
性能稼动率 = 理论周期*加工数量
稼动时间
为了区分速度降低﹑小停顿对性能稼动率的影响﹐将性能稼动率 拆分为纯稼动率和速度稼动率﹐分别表达速度降低的影响和小停顿的 影响。
OEE定义及计算公式
纯稼动率是指设备在稼动时间内﹐以一定速度保持稳定﹑连续运 转的程度。以一定之速度运转这并不是与理论速度比快或慢﹐即 使本身速度比较慢﹐但要看是否能在长时间内保持安定的速度运 转。所以可以衡量因小停顿引起的损失﹐或在每日报表上看不出 来之微缺损失。
性能 稼动 率
纯稼动率 =(实际周期时间×加工数量)/稼动时间×100%
=×
速度稼动率 =理论周期/实际周期×100%
速度稼动率是指速度的差﹐对设备应具备的能力﹐与实 际速度比率。也就是判断是否以规定的速度进行运转。如 果设备的速度降低﹐会有多少损失。
良品数
良品率 = 总产出量
OEE定义及计算公式
= 时间稼动率 ×性能稼动率 ×良品率
OEE三大
设 备
模换暖 具线机
空速 转度
不 良
要素对应 故 故 调 损 与 降
件
的损失 障 障 整 失 小 低
停
顿
综合设备效率是从上述的时间性﹑性能﹑良率观察后得到的使 用有效率﹐来整体性进行设备评估的标准。
(完整版)OEE基本概念
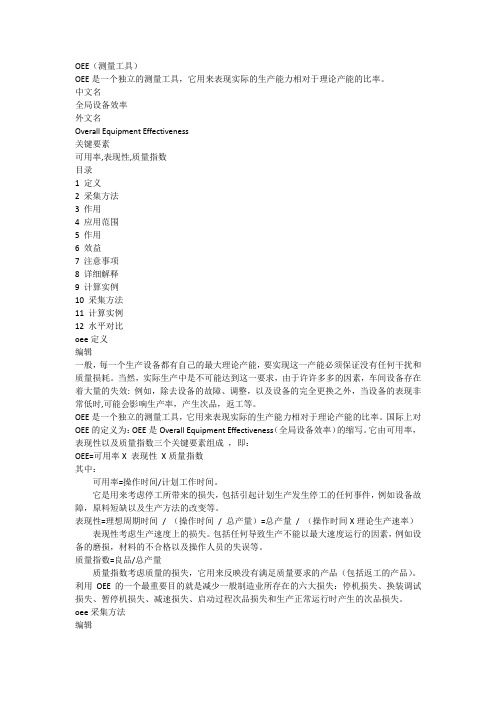
OEE(测量工具)OEE是一个独立的测量工具,它用来表现实际的生产能力相对于理论产能的比率。
中文名全局设备效率外文名Overall Equipment Effectiveness关键要素可用率,表现性,质量指数目录1 定义2 采集方法3 作用4 应用范围5 作用6 效益7 注意事项8 详细解释9 计算实例10 采集方法11 计算实例12 水平对比oee定义编辑一般,每一个生产设备都有自己的最大理论产能,要实现这一产能必须保证没有任何干扰和质量损耗。
当然,实际生产中是不可能达到这一要求,由于许许多多的因素,车间设备存在着大量的失效: 例如,除去设备的故障、调整,以及设备的完全更换之外,当设备的表现非常低时,可能会影响生产率,产生次品,返工等。
OEE是一个独立的测量工具,它用来表现实际的生产能力相对于理论产能的比率。
国际上对OEE的定义为:OEE是Overall Equipment Effectiveness(全局设备效率)的缩写。
它由可用率,表现性以及质量指数三个关键要素组成,即:OEE=可用率X 表现性X质量指数其中:可用率=操作时间/计划工作时间。
它是用来考虑停工所带来的损失,包括引起计划生产发生停工的任何事件,例如设备故障,原料短缺以及生产方法的改变等。
表现性=理想周期时间/ (操作时间/ 总产量)=总产量/ (操作时间X理论生产速率)表现性考虑生产速度上的损失。
包括任何导致生产不能以最大速度运行的因素,例如设备的磨损,材料的不合格以及操作人员的失误等。
质量指数=良品/总产量质量指数考虑质量的损失,它用来反映没有满足质量要求的产品(包括返工的产品)。
利用OEE的一个最重要目的就是减少一般制造业所存在的六大损失:停机损失、换装调试损失、暂停机损失、减速损失、启动过程次品损失和生产正常运行时产生的次品损失。
oee采集方法编辑OEE的计算虽然简单,但是,在实际的应用中,当与班次,员工,设备,产品等生产要素联系在一起时,便变得十分复杂,利用人工采集数据计算OEE显得麻烦费事,为了更有效的利用OEE这个工具,OEE数据采集信息化越来越成为人们关心的话题,OEE IMPACT是世界上最优秀的OEE系统,它具有自动化数据采集模块,可以轻松地获取有关设备的生产信息,为OEE提供最有价值的数据,同时,该系统也可以生成实时的生产信息报告,包括故障停工,在制品信息和OEE等。
OEE的计算公式

OEE的计算公式(不考虑设备加工周期的差异)OEE= 时间开动率×性能开动率×合格品率其中,时间开动率= 开动时间/负荷时间而,负荷时间= 日历工作时间-计划停机时间开动时间= 负荷时间–故障停机时间–设备调整初始化时间(包括更换产品规格、更换工装模具、更换刀具等活动所用时间)性能开动率= 净开动率×速度开动率而,净开动率= 加工数量×实际加工周期/开动时间速度开动率= 理论加工周期/实际加工周期合格品率= 合格品数量/ 加工数量在OEE公式里,时间开动率反映了设备的时间利用情况;性能开动率反映了设备的性能发挥情况;而合格品率则反映了设备的有效工作情况。
反过来,时间开动率度量了设备的故障、调整等项停机损失,性能开动率度量了设备短暂停机、空转、速度降低等项性能损失;合格品率度量了设备加工废品损失。
例1: 设某设备1天工作时间为8h, 班前计划停机20min, 故障停机20min, 更换产品型号设备调整40min, 产品的理论加工周期为0.5min/件, 实际加工周期为0.8min/件,一天共加工产品400件, 有8件废品, 求这台设备的OEE。
计算:负荷时间= 480-20 = 460 min开动时间= 460 –20 –40 = 400 min时间开动率= 400/460 = 87%速度开动率= 0.5/0.8 = 62.5%净开动率= 400×0.8/400 = 80%性能开动率= 62.5%×80% = 50%合格品率= (400-8)/400 = 98% 于是得到OEE = 87%×50%×98% = 42.6%。
有些企业还可以根据生产的实际, 用便于统计的数据来推算TPM例2.设备负荷时间a = 100h,非计划停机10h,则实际开动时间为b = 90h;在开动时间内,计划生产c = 1000个单元产品,但实际生产了d = 900个单元;在生产的e = 900个单元中,仅有f = 800个一次合格的单元。
综合设备效率OEE

为什么引进OEE
采用OEE指标的优点:
1、能使设备的技术管理与经济管理结合起来,可直
接真实地反映企业的技术经济效益。综合效率的高低能引
起领导重视,从而使各级员工建立“设备服务于生产”和“生产 靠设备”的观念;
2、影响综合效率的因素会涉及到设备的设计、制
造、检修、使用、质检、生产组织等各环节,体现了系统
从时间角度讲,OEE计算的是合格品的净生产时间(价 值开动时间)占总可用生产时间(负荷时间)的比例,其本
质就是实际合格产量与负荷时间内理论产量的比值。
为什么引进OEE
OEE由来和变迁
日本企业最早把提高设备综合效率作为TPM管理的主要目标
贯标的质量体系也把OEE作为持续改进的有效技术措施之一
在计算公式中,由时间开动率、性能开动率和合格品率来反映影响OEE
教育、训练:公司认定的企业内、外教育和训练必须参加而引 起的设备停机时间(例:外部教育、内部教育、预备役、民兵训练 等);
如何计算OEE
以下情况应归类于休止时间
停电(停水):电力供给(停水)中断引起的设备不能开 动的时间;
原材料供应:生产过程中由于原材料的品质、供应等 问题引起的生产不能持续进行导致设备停止的时间(管理 损失)。
1、设备利用率:(计算TEEP时用)
在整个日历时间中去除休止时间后的可利用时间所占的比例。
设备利用率=
日历时间-休止时间
日历时间
×100% =
负荷时间
日历时间 ×100%
总日历时间
计划停机时间(年修、定修、节假日) 非设备因素停机时间(停电、待料)
休止时间
负荷时间(总的可用生产时间)
如何计算OEE
如何计算OEE
基于工作抽样的OEE分析在缝纫线生产管理中的应用
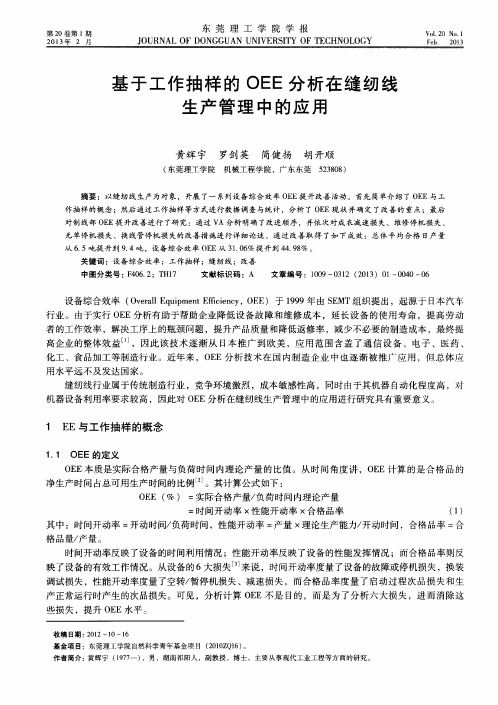
第 1期
黄辉宇 ,等 : 基 于工作抽样 的 O E E分析在缝 纫线生产管理 中的应用
4 1
1 . 2 工作抽 样 的概 念
工作抽样 ( w o r k S a m p l i n g )是利用数理统计 的原理 ,用随机抽样方法研究生产率 的一种技术 。它 又称 为 瞬时 观测 法 ,是在 一段 较 长 的时间 内 ,以随 机 的方式 对调 查对 象进 行 间断地 观测 ,并 按预 定 的 目 的整 理 、分 析所 调查 的资 料 ,最 后 得 出需 要 的结 果 J 。 由于 它 不是 全 数 调 查 ,所 以就 会 产 生 误差 ,这 又取决于抽样的数量 ( 即观测次数 ) 。抽样数越多 ,可靠性就越 高;反之 ,可靠性就越低。但是抽样次 数多 , 人力 、物力、财力的消耗将增加 ,因此就必须考虑可靠度与精度的问题 。
2 基于工作抽样 的制线部 OE E现状分 析
打线 是缝 纫线 生 产 的一个 最为 核心 生产 环节 ,直接影 响 到产 品 的产量 和 品质 。 目前 公 司制线 部生产 尼龙 线产 品有 1 0 1 个 锭 子机 器 ,而生 产 成衣线 产 品则 有 2 8 8个锭 子 机器 ,总 共有 3 8 9个 锭子 机 器 。经 调 查 发 现 ,由于种种 原 因 ,制线 部现 场 设备 存 在 大 量 的 损 失 与 浪 费 ,O E E整体 水 平 不 高 。下 面 分 别 通 过
第2 0 卷第 1 期
2 01 3 年 2 月
J OURN AL OF D ONGG UAN U NI VER S I T Y OF T E C HN0 L 0G Y
东 莞 理 工 学 院 学 报
V o 1 . 2 O N O . 1
OEEOPE时间构成及计算公式
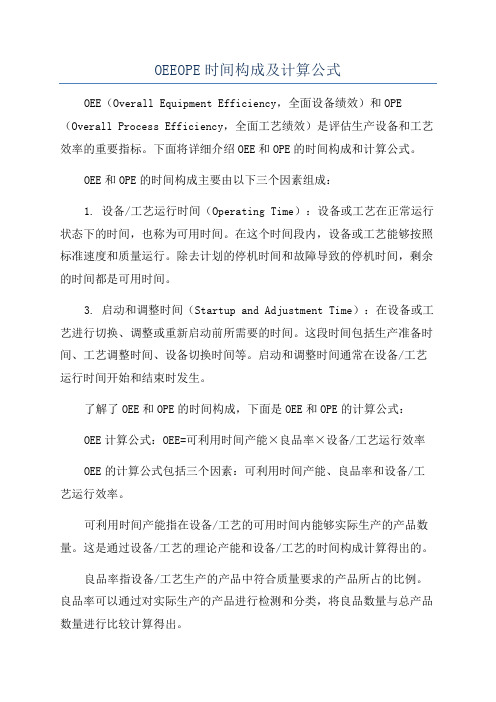
OEEOPE时间构成及计算公式OEE(Overall Equipment Efficiency,全面设备绩效)和OPE (Overall Process Efficiency,全面工艺绩效)是评估生产设备和工艺效率的重要指标。
下面将详细介绍OEE和OPE的时间构成和计算公式。
OEE和OPE的时间构成主要由以下三个因素组成:1. 设备/工艺运行时间(Operating Time):设备或工艺在正常运行状态下的时间,也称为可用时间。
在这个时间段内,设备或工艺能够按照标准速度和质量运行。
除去计划的停机时间和故障导致的停机时间,剩余的时间都是可用时间。
3. 启动和调整时间(Startup and Adjustment Time):在设备或工艺进行切换、调整或重新启动前所需要的时间。
这段时间包括生产准备时间、工艺调整时间、设备切换时间等。
启动和调整时间通常在设备/工艺运行时间开始和结束时发生。
了解了OEE和OPE的时间构成,下面是OEE和OPE的计算公式:OEE计算公式:OEE=可利用时间产能×良品率×设备/工艺运行效率OEE的计算公式包括三个因素:可利用时间产能、良品率和设备/工艺运行效率。
可利用时间产能指在设备/工艺的可用时间内能够实际生产的产品数量。
这是通过设备/工艺的理论产能和设备/工艺的时间构成计算得出的。
良品率指设备/工艺生产的产品中符合质量要求的产品所占的比例。
良品率可以通过对实际生产的产品进行检测和分类,将良品数量与总产品数量进行比较计算得出。
设备/工艺运行效率指设备/工艺在可用时间内以标准速度和质量运行的能力。
这可以通过实际运行时间与可用时间的比例计算得出。
OPE计算公式:OPE=设备/工艺运行时间/(设备/工艺运行时间+停机时间+启动和调整时间)OPE的计算公式表示设备/工艺运行时间在总运行时间中的占比。
通过计算OEE和OPE,可以评估设备或工艺的效率水平,并找出影响其效率的主要因素。
OEE

一OEE是全效率的简称,又称设备综合效率,它首先是一种度量方法,通过它可以度量一台设备或一条生产线的盈利能力。
对一台设备或一条生产线来说,越高的OEE就是最终产出好产品越多,从而使单位产品的成本降低。
OEE还是一个分析工具,运用OEE方法可以识别出体统地降低瓶颈工序设备的效率损失,使隐藏的或损失掉的产能释放出来。
二OEE=时间开动率×性能开动率×合格品率其中,(1)时间开动率(Availability)=开动时间/负荷时间,负荷时间=日历工作时间-计划停机时间,开动时间=负荷时间-故障停机时间-设备调整初始化时间(包括更换产品规格、更换工装模具、更换刀具等活动所用时间)。
(2)性能开动率(Performance Efficiency)=净开动率×速度开动率净开动率(Performance Efficiency)=加工数量×实际加工周期/开动时间速度开动率(Speed Efficiency)=理论加工周期/实际加工周期(3)合格品率(Quality)=合格品数量/加工数量在OEE的公式里,时间开动率反映了设备的时间利用情况,性能开动率反映了设备的性能发挥情况,而合格品率则反映了设备的有效工作情况。
2 OEE公式的本质OEE的本质实际上就是合格品的理论加工时间与负荷时间的百分比,因为我们展开OEE的计算公式有:设备综合效率OEE=时间开动率×性能开动率×合格品率=(开动时间/负荷时间)×(加工数量×实际加工量/开动时间)×(理论加工周期/实际加工周期)×(合格品数量/加工数量)=合格品数量×理论加工周期/负荷时间=合格品理论加工时间/负荷时间由此可见,OEE准确地告诉你设备的效率如何,设备真正用于加工合格品的时间是多少,即设备真正有多少时间是在创造价值的,从而利于人们找出生产环节中的损失。
在全员生产维修(TPM)中,世界级的维修水平要求达到以下目标:设备的时间开动率≥90%;性能开动率≥95%;合格品率≥99%;设备综合效率≥85%。
关于生产线的OEE(设备综合利用效能)
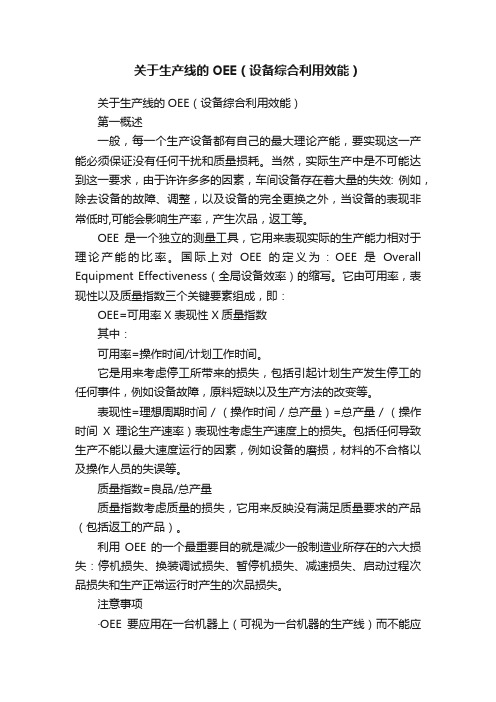
关于生产线的OEE(设备综合利用效能)关于生产线的OEE(设备综合利用效能)第一概述一般,每一个生产设备都有自己的最大理论产能,要实现这一产能必须保证没有任何干扰和质量损耗。
当然,实际生产中是不可能达到这一要求,由于许许多多的因素,车间设备存在着大量的失效: 例如,除去设备的故障、调整,以及设备的完全更换之外,当设备的表现非常低时,可能会影响生产率,产生次品,返工等。
OEE是一个独立的测量工具,它用来表现实际的生产能力相对于理论产能的比率。
国际上对OEE的定义为:OEE是Overall Equipment Effectiveness(全局设备效率)的缩写。
它由可用率,表现性以及质量指数三个关键要素组成,即:OEE=可用率X 表现性 X质量指数其中:可用率=操作时间/计划工作时间。
它是用来考虑停工所带来的损失,包括引起计划生产发生停工的任何事件,例如设备故障,原料短缺以及生产方法的改变等。
表现性=理想周期时间 / (操作时间 / 总产量)=总产量 / (操作时间X理论生产速率)表现性考虑生产速度上的损失。
包括任何导致生产不能以最大速度运行的因素,例如设备的磨损,材料的不合格以及操作人员的失误等。
质量指数=良品/总产量质量指数考虑质量的损失,它用来反映没有满足质量要求的产品(包括返工的产品)。
利用OEE的一个最重要目的就是减少一般制造业所存在的六大损失:停机损失、换装调试损失、暂停机损失、减速损失、启动过程次品损失和生产正常运行时产生的次品损失。
注意事项·OEE要应用在一台机器上(可视为一台机器的生产线)而不能应用在整个生产线或全厂上,这样才有意义。
·OEE要作为一系列一体化的综合关键业绩指标中的一部分来运用而不能孤立使用,否则将造成生产批次规模加大或有质量缺陷的产品。
·OEE必须与精益原则相符,要确保对OEE的计算不会导致浪费合理化、制度化,例如,绝不要允许给换线留出时间。
机加线稼动率及OEE

机加设备生产线,设备综合效率(OEE)及稼动时间计算方式:设备总体效率(OEE)=时间稼动率X性能稼动率X直通率时间稼动率=稼动时间/负荷时间X100%性能稼动率=标准CT X 生产数/稼动时间X100%直通率=良品数/生产数X100%OEE指标范围:卓越:OEE》80%,优秀:70%《OEE《79%,良好:55%《OEE《69%,一般:OEE《55%。
时间稼动率计算:最大操作时间A:设备理论上可以使用的最大时间;负荷时间B:最大操作时间扣除停机时间B=A-C;停机时间C:计划上的停机休息时间,例如休假、培训学习、设备保养等时间;稼动时间D:负荷时间扣除设备停止时间D=B-E;停止时间E:包括设备在生产批次之间的转换停止时间,现场生产过程中的异常处理时间,设备故障引起的异常停止及修复时间稼动率定义/设备稼动率(也称为时间稼动率)其计算公式:时间稼动率S=稼动时间D/负荷时间B=1-E/B=1-E/A-C(最大操作时间-停机损失时间-停止时间)最大操作时间-停机损失时间(概括起来说就是设备本身具备的最大生产时间扣除因为计划停机时间和生产过程异常引起的时间损失与设备最大理论生产时间扣除计划停机时间的比值百分比)。
在评价设备生产效率时,可能因为生产时间相同,计划停机时间相同但是设备生产效率不同而带来的设备整体生产效率评价上的不准确,所以引入了设备性能稼动率作为意向评价标准。
性能稼动率/实质稼动率/速度稼动率速度稼动率=基准周期时间/实际周期时间基准周期时间=设备原设计产出单位产量产品所需要的时间时间周期时间=目前设备时间生产单位产量产品所实际需要的时间实质稼动率=生产量X实际周期时间/稼动时间性能稼动率=速度稼动率X实质稼动率性能稼动时间=稼动时间X性能稼动率=稼动时间-性能损失时间产品直通率,既是单位产量的产品在设备生产加工过程中,在各个工序的质量检查中都OK,一次性通过整条生产线所占的比率,是用来衡量生产线生产性能及质量稳定性的指标。
OEE介绍和计算方法-oee介绍

O E E介绍和计算方法-o e e介绍(总12页)-CAL-FENGHAI.-(YICAI)-Company One1-CAL-本页仅作为文档封面,使用请直接删除OEE(Overall Equipment Effectiveness),即设备综合效率,其本质就是设备负荷时间内实际产量与理论产量的比值。
企业在进行OEE计算时常常遇到很多迷惑的问题,如工厂停水、停电、停气、停汽使设备不能工作,等待定单、等待排产计划、等待检查、等待上一道工序造成的停机,不知如何计算。
本文引入非设备因素停机的概念,修改了OEE的算法,使计算得到的OEE更能够真实反映设备维护的实际状况,让设备完全利用的情况由完全有效生产率这个指标来反映。
本文同时介绍了在不同情况下如何分析设备损失的PM分析流程。
1、 OEE表述和计算实例OEE= 时间开动率×性能开动率×合格品率其中,时间开动率 = 开动时间/负荷时间而,负荷时间 = 日历工作时间-计划停机时间开动时间 = 负荷时间–故障停机时间–设备调整初始化时间性能开动率 = 净开动率×速度开动率而,净开动率 = 加工数量×实际加工周期/开动时间速度开动率 = 理论加工周期/实际加工周期合格品率 = 合格品数量/ 加工数量在OEE公式里,时间开动率反映了设备的时间利用情况;性能开动率反映了设备的性能发挥情况;而合格品率则反映了设备的有效工作情况。
反过来,时间开动率度量了设备的故障、调整等项停机损失,性能开动率度量了设备短暂停机、空转、速度降低等项性能损失;合格品率度量了设备加工废品损失。
OEE还有另一种表述方法,更适用于流动生产线的评估, 即OEE= 时间开动率×性能开动率×合格品率而,时间开动率 = 开动时间/计划利用时间而,计划利用时间 = 日历工作时间-计划停机时间开动时间 = 计划利用时间–非计划停机时间性能开动率 = 完成的节拍数/计划节拍数其中,计划节拍数 = 开动时间/标准节拍时间合格品率 = 合格品数量/加工数量这与前述的OEE公式实际上是同一的。
OEE介绍
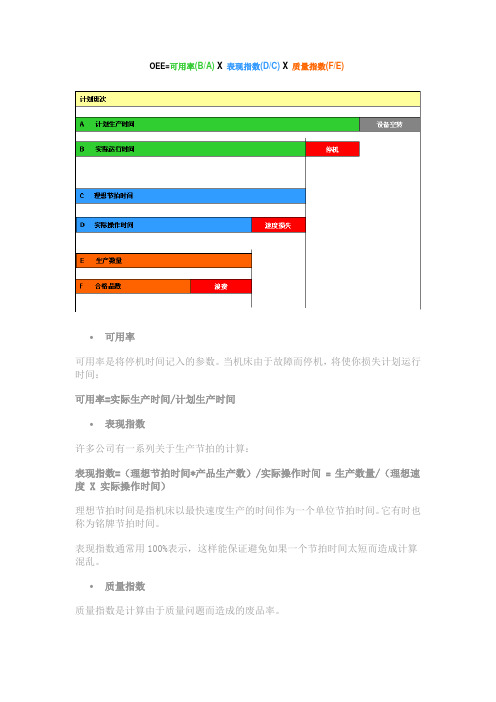
OEE=可用率(B/A) X 表现指数(D/C) X 质量指数(F/E)∙可用率可用率是将停机时间记入的参数。
当机床由于故障而停机,将使你损失计划运行时间:可用率=实际生产时间/计划生产时间∙表现指数许多公司有一系列关于生产节拍的计算:表现指数=(理想节拍时间*产品生产数)/实际操作时间= 生产数量/(理想速度 X 实际操作时间)理想节拍时间是指机床以最快速度生产的时间作为一个单位节拍时间。
它有时也称为铭牌节拍时间。
表现指数通常用100%表示,这样能保证避免如果一个节拍时间太短而造成计算混乱。
∙质量指数质量指数是计算由于质量问题而造成的废品率。
质量指数=合格品数/生产数量下面举一个例子来说明:假如下面是某车间一个班次的记录:从上面的数据,我们可以得出:计划生产时间=班次时间—计划中断=480—2 X 15=450(分钟)工作时间=计划时间—停工时间=420—47=373(分钟)良品=生产数量—次品=19271—423=18,848(件)从而:∙可用率=实际生产时间/计划生产时间=373/420=0.888(88.8%) ∙表现性=生产数量/(理想速度 X 工作时间)=19271/(60 X 373)=0.861(86.1%)∙质量指数=合格品数/生产数量= 18,848/19,271=0.978(97.8%)∙OEE=可用率 X 表现性 X 质量指数=0.888 X 0.861 X0.978=0.748(74.8%)根据OEE系统所提供的数据,你可以方便的知道自己工厂存在什么问题,例如,如果你的可用率在某一个时间段很低,说明在六大损失中和OEE可用率损失有关的故障太多,那么,显而易见,你应该把改善重点放在这些方面了!同样,如果质量指数或者表现性导致你的OEE水平降低,那么你就应该把目光放在和它们有关的问题点上。
在表一中,我们只列举了一些事件原因,其实它可以包括和生产有关的任何方面,因此,你可以对生产做到全面的管理和改善。
- 1、下载文档前请自行甄别文档内容的完整性,平台不提供额外的编辑、内容补充、找答案等附加服务。
- 2、"仅部分预览"的文档,不可在线预览部分如存在完整性等问题,可反馈申请退款(可完整预览的文档不适用该条件!)。
- 3、如文档侵犯您的权益,请联系客服反馈,我们会尽快为您处理(人工客服工作时间:9:00-18:30)。
第 1 页
OEE统计表 1,140 组别 加工5线 加工5线 加工5线 加工5线 加工5线 加工5线 加工5线 加工5线 加工5线 加工5线 加工5线 加工5线 加工5线 加工5线 加工5线 加工5线 加工5线 加工5线 加工5线 加工5线 加工5线 加工5线 加工5线 加工5线 加工5线 加工5线 加工5线 加工5线 加工5线 加工5线 加工5线 日期 班别 业务号 加工数量 (C) 0 0 0 0 0 0 0 0 0 0 0 0 0 0 0 0 0 0 0 0 0 0 0 0 0 0 0 0 0 0 0 良品 不良品 顺产时间 工作时间 产能 (秒) 目标数量 #DIV/0! #DIV/0! #DIV/0! #DIV/0! #DIV/0! #DIV/0! #DIV/0! #DIV/0! #DIV/0! #DIV/0! #DIV/0! #DIV/0! #DIV/0! #DIV/0! #DIV/0! #DIV/0! #DIV/0! #DIV/0! #DIV/0! #DIV/0! #DIV/0! #DIV/0! #DIV/0! #DIV/0! #DIV/0! #DIV/0! #DIV/0! #DIV/0! #DIV/0! #DIV/0! #DIV/0! 时间稼动 性能稼动 率 率 #DIV/0! #DIV/0! #DIV/0! #DIV/0! #DIV/0! #DIV/0! #DIV/0! #DIV/0! #DIV/0! #DIV/0! #DIV/0! #DIV/0! #DIV/0! #DIV/0! #DIV/0! #DIV/0! #DIV/0! #DIV/0! #DIV/0! #DIV/0! #DIV/0! #DIV/0! #DIV/0! #DIV/0! #DIV/0! #DIV/0! #DIV/0! #DIV/0! #DIV/0! #DIV/0! #DIV/0! #DIV/0! #DIV/0! #DIV/0! #DIV/0! #DIV/0! #DIV/0! #DIV/0! #DIV/0! #DIV/0! #DIV/0! #DIV/0! #DIV/0! #DIV/0! #DIV/0! #DIV/0! #DIV/0! #DIV/0! #DIV/0! #DIV/0! #DIV/0! #DIV/0! #DIV/0! #DIV/0! #DIV/0! #DIV/0! #DIV/0! #DIV/0! #DIV/0! #DIV/0! #DIV/0! #DIV/0! 日期:2012年1月 良品率 #DIV/0! #DIV/0! #DIV/0! #DIV/0! #DIV/0! #DIV/0! #DIV/0! #DIV/0! #DIV/0! #DIV/0! #DIV/0! #DIV/0! #DIV/0! #DIV/0! #DIV/0! #DIV/0! #DIV/0! #DIV/0! #DIV/0! #DIV/0! #DIV/0! #DIV/0! #DIV/0! #DIV/0! #DIV/0! #DIV/0! #DIV/0! #DIV/0! #DIV/0! #DIV/0! #DIV/0! OEE #DIV/0! #DIV/0! #DIV/0! #DIV/0! #DIV/0! #DIV/0! #DIV/0! #DIV/0! #DIV/0! #DIV/0! #DIV/0! #DIV/0! #DIV/0! #DIV/0! #DIV/0! #DIV/0! #DIV/0! #DIV/0! #DIV/0! #DIV/0! #DIV/0! #DIV/0! #DIV/0! #DIV/0! #DIV/0! #DIV/0! #DIV/0! #DIV/0! #DIV/0! #DIV/0! #DIV/0! 操作员 每小时产 出 备注
第 3 页
OEE统计表 1,140 组别 加工5线 日期 班别 业务号 加工数量 (C) 良品 不良品 顺产时间 工作时间 产能 (秒) 目标数量 #DIV/0! 时间稼动 性能稼动 率 率 #DIV/0! #DIV/0! 日期:2012年1月 良品率 #DIV/0! OEE #DIV/0! 操作员 每小时产 出 备注
=
第 4 页
第 2 页
OEE统计表 1,140 组别 加工5线 加工5线 加工5线 加工5线 加工5线 加工5线 加工5线 加工5线 加工5线 加工5线 加工5线 加工5线 加工5线 加工5线 加工5线 加工5线 加工5线 加工5线 加工5线 加工5线 加工5线 加工5线 加工5线 加工5线 加工5线 加工5线 加工5线 加工5线 加工5线 加工5线 加工5线 日期 班别 业务号 加工数量 (C) 0 0 0 0 0 0 0 0 0 0 0 0 0 0 0 0 0 0 0 0 0 0 0 0 0 0 0 0 0 0 0 良品 不良品 顺产时间 工作时间 产能 (秒) 目标数量 #DIV/0! #DIV/0! #DIV/0! #DIV/0! #DIV/0! #DIV/0! #DIV/0! #DIV/0! #DIV/0! #DIV/0! #DIV/0! #DIV/0! #DIV/0! #DIV/0! #DIV/0! #DIV/0! #DIV/0! #DIV/0! #DIV/0! #DIV/0! #DIV/0! #DIV/0! #DIV/0! #DIV/0! #DIV/0! #DIV/0! #DIV/0! #DIV/0! #DIV/0! #DIV/0! #DIV/0! 时间稼动 性能稼动 率 率 #DIV/0! #DIV/0! #DIV/0! #DIV/0! #DIV/0! #DIV/0! #DIV/0! #DIV/0! #DIV/0! #DIV/0! #DIV/0! #DIV/0! #DIV/0! #DIV/0! #DIV/0! #DIV/0! #DIV/0! #DIV/0! #DIV/0! #DIV/0! #DIV/0! #DIV/0! #DIV/0! #DIV/0! #DIV/0! #DIV/0! #DIV/0! #DIV/0! #DIV/0! #DIV/0! #DIV/0! #DIV/0! #DIV/0! #DIV/0! #DIV/0! #DIV/0! #DIV/0! #DIV/0! #DIV/0! #DIV/0! #DIV/0! #DIV/0! #DIV/0! #DIV/0! #DIV/0! #DIV/0! #DIV/0! #DIV/0! #DIV/0! #DIV/0! #DIV/0! #DIV/0! #DIV/0! #DIV/0! #DIV/0! #DIV/0! #DIV/0! #DIV/0! #DIV/0! #DIV/0! #DIV/0! #DIV/0! 日期:2012年1月 良品率 #DIV/0! #DIV/0! #DIV/0! #DIV/0! #DIV/0! #DIV/0! #DIV/0! #DIV/0! #DIV/0! #DIV/0! #DIV/0! #DIV/0! #DIV/0! #DIV/0! #DIV/0! #DIV/0! #DIV/0! #DIV/0! #DIV/0! #DIV/0! #DIV/0! #DIV/0! #DIV/0! #DIV/0! #DIV/0! #DIV/0! #DIV/0! #DIV/0! #DIV/0! #DIV/0! #DIV/0! OEE #DIV/0! #DIV/0! #DIV/0! #DIV/0! #DIV/0! #DIV/0! #DIV/0! #DIV/0! #DIV/0! #DIV/0! #DIV/0! #DIV/0! #DIV/0! #DIV/0! #DIV/0! #DIV/0! #DIV/0! #DIV/0! #DIV/0! #DIV/0! #DIV/0! #DIV/0! #DIV/0! #DIV/0! #DIV/0! #DIV/0! #DIV/0! #DIV/0! #DIV/0! #DIV/0! #DIV/0! 操作员 每小时产 出 备注
OEE统计表 1,140 组别 加工5线 加工5线 加工5线 加工5线 加工5线 加工5线 加工5线 加工5线 加工5线 加工5线 加工5线 加工5线 加工5线 加工5线 加工5线 加工5线 加工5线 加工5线 加工5线 加工5线 加工5线 加工5线 加工5线 加工5线 加工5线 加工5线 加工5线 加工5线 加工5线 加工5线 加工5线 7-11 7-11 白 晚 040-009 040-009 日期 班别 业务号 加工数量 (C) 0 0 0 410 317 0 0 0 0 0 0 0 0 0 0 0 0 0 0 0 0 0 0 0 0 0 0 0 0 0 0 410 317 0 0 610 530 610 530 70 70 良品 不良品 顺产时间 工作时间 产能 (秒) 目标数量 #DIV/0! #DIV/0! #DIV/0! 523 454 #DIV/0! #DIV/0! #DIV/0! #DIV/0! #DIV/0! #DIV/0! #DIV/0! #DIV/0! #DIV/0! #DIV/0! #DIV/0! #DIV/0! #DIV/0! #DIV/0! #DIV/0! #DIV/0! #DIV/0! #DIV/0! #DIV/0! #DIV/0! #DIV/0! #DIV/0! #DIV/0! #DIV/0! #DIV/0! #DIV/0! 时间稼动 性能稼动 率 率 #DIV/0! #DIV/0! #DIV/0! 100.00% 100.00% #DIV/0! #DIV/0! #DIV/0! #DIV/0! #DIV/0! #DIV/0! #DIV/0! #DIV/0! #DIV/0! #DIV/0! #DIV/0! #DIV/0! #DIV/0! #DIV/0! #DIV/0! #DIV/0! #DIV/0! #DIV/0! #DIV/0! #DIV/0! #DIV/0! #DIV/0! #DIV/0! #DIV/0! #DIV/0! #DIV/0! #DIV/0! #DIV/0! #DIV/0! 78.42% 69.78% #DIV/0! #DIV/0! #DIV/0! #DIV/0! #DIV/0! #DIV/0! #DIV/0! #DIV/0! #DIV/0! #DIV/0! #DIV/0! #DIV/0! #DIV/0! #DIV/0! #DIV/0! #DIV/0! #DIV/0! #DIV/0! #DIV/0! #DIV/0! #DIV/0! #DIV/0! #DIV/0! #DIV/0! #DIV/0! #DIV/0! 日期:2012年1月 良品率 #DIV/0! #DIV/0! #DIV/0! 100.00% 100.00% #DIV/0! #DIV/0! #DIV/0! #DIV/0! #DIV/0! #DIV/0! #DIV/0! #DIV/0! #DIV/0! #DIV/0! #DIV/0! #DIV/0! #DIV/0! #DIV/0! #DIV/0! #DIV/0! #DIV/0! #DIV/0! #DIV/0! #DIV/0! #DIV/0! #DIV/0! #DIV/0! #DIV/0! #DIV/0! #DIV/0! OEE #DIV/0! #DIV/0! #DIV/0! 78.42% 69.78% #DIV/0! #DIV/0! #DIV/0! #DIV/0! #DIV/0! #DIV/0! #DIV/0! #DIV/0! #DIV/0! #DIV/0! #DIV/0! #DIV/0! #DIV/0! #DIV/0! #DIV/0! #DIV/0! #DIV/0! #DIV/0! #DIV/0! #DIV/0! #DIV/0! #DIV/0! #DIV/0! #DIV/0! #DIV/0! #DIV/0! 40 36 操作员 每小时产 出 备注