甲醇装置运行中存在的问题及解决措施
360kt/a甲醇装置运行中存在的问题及解决措施
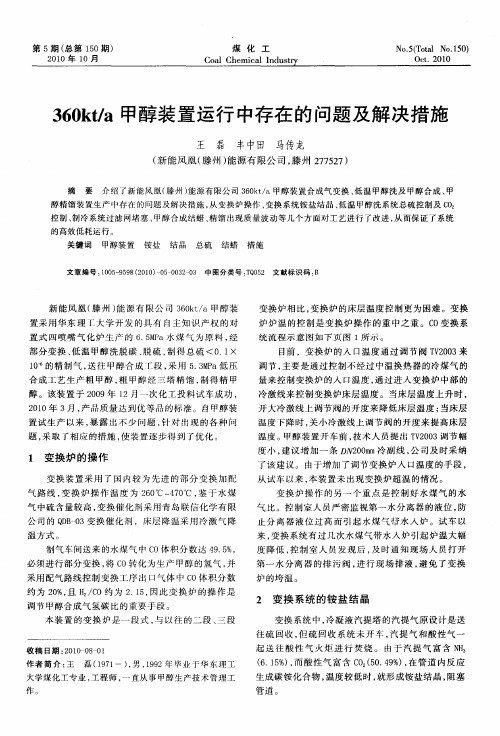
( 能 凤凰 ( 州 ) 新 滕 能源 有 限公 司 , 滕州 2 7 2 ) 7 5 7
摘 要
介绍 了新 能凤凰 ( 滕州 ) 源有限公 司 3 0 ta甲醇 装置合成气 变换 、 温 甲醇 洗及 甲醇合成 、 能 6k/ 低 甲
醇 精 馏 装 置 生 产 中存 在 的 问 题 及 解 决 措 施 , 变 换 炉 操 作 、 换 系 统 铵 盐 结 晶 、 温 甲醇 洗 系 统 总 硫 控 制 及 c 从 变 低 0
题, 采取 了相 应 的措 施 , 装 置 逐 步 得 到 了优 化 。 使
冷激线来控制变换炉床层温度 。当床层温度上升时 , 开大冷激线上调节阀的开度来 降低床层温度 ; 当床层
温 度 下 降 时 , 小 冷 激线 上 调 节 阀 的 开 度 来 提 高 床 层 关 温度 。 甲醇 装 置 开 车 前 , 术人 员 提 出 T2 0 调 节 幅 技 V03 度 小 , 议 增 加 一 条 D 2 0m冷 副 线 , 司 及 时 采 纳 建 N 0m 公 了该 建 议 。 由于 增 加 了调 节 变 换 炉 人 口温 度 的手 段 , 从 试 车 以来 , 装 置 未 出现 变 换 炉 超 温 的情 况 。 本 变 换 炉 操 作 的 另 一 个 重 点 是 控 制 好 水 煤 气 的 水
新 能 凤 凰 ( 州 ) 源 有 限 公 司 30 ta甲 醇 装 滕 能 6k / 置 采 用 华 东 理 丁大 学 开 发 的具 有 自主 知 识 产 权 的 对
置 式 四喷 嘴 气 化 炉 生 产 的 6 5 P . M a水 煤 气 为 原 料 , 经
变换 炉相 比, 变换 炉的床层温度控制更为 困难 。变换 炉炉温 的控制是 变换炉操作 的重 中之重 。C 0变换系
低温甲醇洗装置运行中出现的问题及解决措施

低温甲醇洗装置运行中出现的问题及解决措施低温甲醇洗装置是用于甲醇洗过程中分离和净化气体的设备,在运行过程中可能会出现一些问题。
下面将介绍一些常见的问题以及对应的解决措施:1. 甲醇泵出现堵塞问题:甲醇在低温条件下易结冰,导致甲醇泵堵塞,影响设备正常运行。
解决措施:使用加热方式对甲醇泵进行加热,防止结冰现象发生,定期清理泵体内积冰物。
2. 甲醇洗塔出现液位异常问题:甲醇洗塔的液位过高或过低,可能导致洗涤效果不佳或洗涤能力下降。
解决措施:检查洗塔的进出口阀门是否正常,调整进料流量和出料流量以控制液位;查找洗涤塔内是否有积水或其他杂质,清理洗塔内部;定期检查洗液的浓度,保证洗涤液与废气的充分接触。
3. 甲醇洗塔出现堵塞问题:在低温甲醇洗过程中,废气中的杂质可能会导致甲醇洗塔堵塞。
解决措施:定期清理洗塔内部的杂质,可以采用高压水进行清洗或者拆卸洗塔进行清理。
4. 甲醇回收系统出现故障:甲醇回收系统在循环过程中可能会出现泄漏或失效的问题,导致甲醇的回收效率降低。
解决措施:定期检查甲醇回收系统的密封性,确保系统正常运行;检查回收系统中的设备是否有损坏或磨损情况,及时更换和修复。
5. 甲醇洗液浓度不足:甲醇洗液浓度不足会导致洗涤效果下降。
解决措施:定期检测甲醇洗液的浓度,根据需要添加适量的甲醇;检查洗液循环系统的泵是否正常运行,确保洗液循环顺畅。
6. 甲醇洗装置能耗过高:如果能耗过高,可能会导致生产成本的增加。
解决措施:优化甲醇洗装置的运行参数,合理调整甲醇洗液的流量和温度,控制甲醇的使用量;采用节能设备进行能耗监测和控制,如换热器、节能泵等设备。
低温甲醇洗装置在运行过程中可能会出现一些问题,要根据具体情况采取相应的解决措施,并定期进行检查和维护,以保证设备的正常运行和洗涤效果的达到要求。
低温甲醇洗装置运行中出现的问题及解决措施
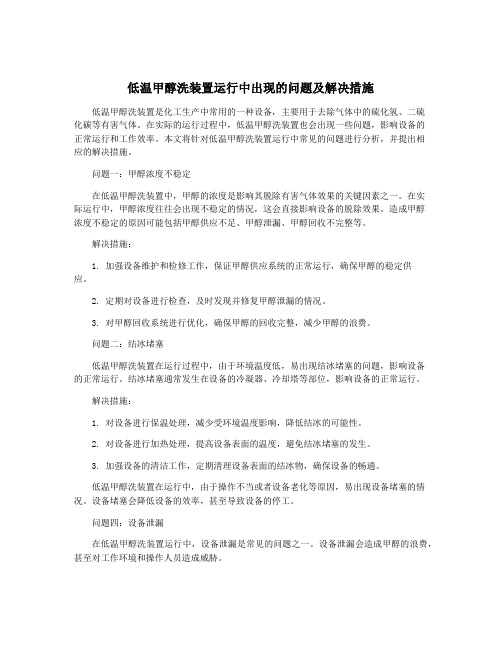
低温甲醇洗装置运行中出现的问题及解决措施低温甲醇洗装置是化工生产中常用的一种设备,主要用于去除气体中的硫化氢、二硫化碳等有害气体。
在实际的运行过程中,低温甲醇洗装置也会出现一些问题,影响设备的正常运行和工作效率。
本文将针对低温甲醇洗装置运行中常见的问题进行分析,并提出相应的解决措施。
问题一:甲醇浓度不稳定在低温甲醇洗装置中,甲醇的浓度是影响其脱除有害气体效果的关键因素之一。
在实际运行中,甲醇浓度往往会出现不稳定的情况,这会直接影响设备的脱除效果。
造成甲醇浓度不稳定的原因可能包括甲醇供应不足、甲醇泄漏、甲醇回收不完整等。
解决措施:1. 加强设备维护和检修工作,保证甲醇供应系统的正常运行,确保甲醇的稳定供应。
2. 定期对设备进行检查,及时发现并修复甲醇泄漏的情况。
3. 对甲醇回收系统进行优化,确保甲醇的回收完整,减少甲醇的浪费。
问题二:结冰堵塞低温甲醇洗装置在运行过程中,由于环境温度低,易出现结冰堵塞的问题,影响设备的正常运行。
结冰堵塞通常发生在设备的冷凝器、冷却塔等部位,影响设备的正常运行。
解决措施:1. 对设备进行保温处理,减少受环境温度影响,降低结冰的可能性。
2. 对设备进行加热处理,提高设备表面的温度,避免结冰堵塞的发生。
3. 加强设备的清洁工作,定期清理设备表面的结冰物,确保设备的畅通。
低温甲醇洗装置在运行中,由于操作不当或者设备老化等原因,易出现设备堵塞的情况。
设备堵塞会降低设备的效率,甚至导致设备的停工。
问题四:设备泄漏在低温甲醇洗装置运行中,设备泄漏是常见的问题之一。
设备泄漏会造成甲醇的浪费,甚至对工作环境和操作人员造成威胁。
低温甲醇洗装置运行中出现的问题及解决措施
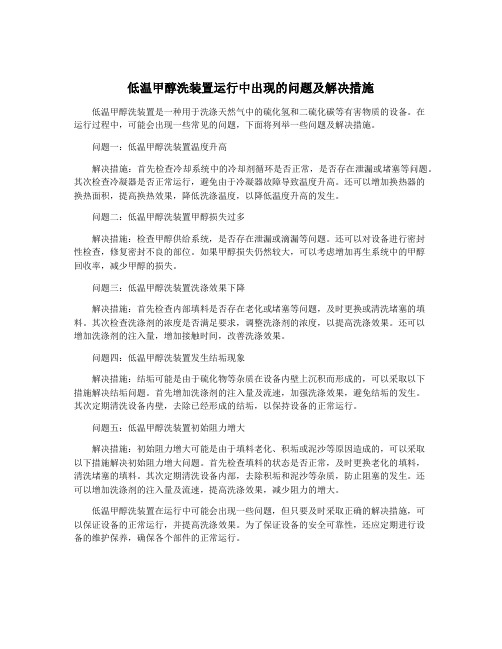
低温甲醇洗装置运行中出现的问题及解决措施低温甲醇洗装置是一种用于洗涤天然气中的硫化氢和二硫化碳等有害物质的设备。
在运行过程中,可能会出现一些常见的问题,下面将列举一些问题及解决措施。
问题一:低温甲醇洗装置温度升高解决措施:首先检查冷却系统中的冷却剂循环是否正常,是否存在泄漏或堵塞等问题。
其次检查冷凝器是否正常运行,避免由于冷凝器故障导致温度升高。
还可以增加换热器的换热面积,提高换热效果,降低洗涤温度,以降低温度升高的发生。
问题二:低温甲醇洗装置甲醇损失过多解决措施:检查甲醇供给系统,是否存在泄漏或滴漏等问题。
还可以对设备进行密封性检查,修复密封不良的部位。
如果甲醇损失仍然较大,可以考虑增加再生系统中的甲醇回收率,减少甲醇的损失。
问题三:低温甲醇洗装置洗涤效果下降解决措施:首先检查内部填料是否存在老化或堵塞等问题,及时更换或清洗堵塞的填料。
其次检查洗涤剂的浓度是否满足要求,调整洗涤剂的浓度,以提高洗涤效果。
还可以增加洗涤剂的注入量,增加接触时间,改善洗涤效果。
问题四:低温甲醇洗装置发生结垢现象解决措施:结垢可能是由于硫化物等杂质在设备内壁上沉积而形成的,可以采取以下措施解决结垢问题。
首先增加洗涤剂的注入量及流速,加强洗涤效果,避免结垢的发生。
其次定期清洗设备内壁,去除已经形成的结垢,以保持设备的正常运行。
问题五:低温甲醇洗装置初始阻力增大解决措施:初始阻力增大可能是由于填料老化、积垢或泥沙等原因造成的,可以采取以下措施解决初始阻力增大问题。
首先检查填料的状态是否正常,及时更换老化的填料,清洗堵塞的填料。
其次定期清洗设备内部,去除积垢和泥沙等杂质,防止阻塞的发生。
还可以增加洗涤剂的注入量及流速,提高洗涤效果,减少阻力的增大。
低温甲醇洗装置在运行中可能会出现一些问题,但只要及时采取正确的解决措施,可以保证设备的正常运行,并提高洗涤效果。
为了保证设备的安全可靠性,还应定期进行设备的维护保养,确保各个部件的正常运行。
低温甲醇洗装置运行中出现的问题及解决措施
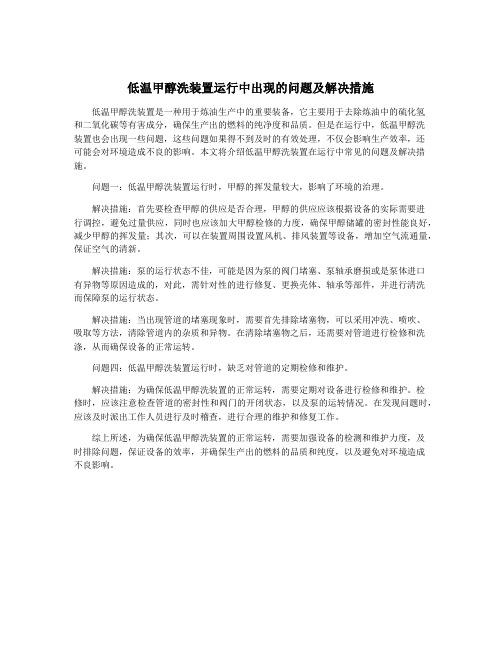
低温甲醇洗装置运行中出现的问题及解决措施低温甲醇洗装置是一种用于炼油生产中的重要装备,它主要用于去除炼油中的硫化氢和二氧化碳等有害成分,确保生产出的燃料的纯净度和品质。
但是在运行中,低温甲醇洗装置也会出现一些问题,这些问题如果得不到及时的有效处理,不仅会影响生产效率,还可能会对环境造成不良的影响。
本文将介绍低温甲醇洗装置在运行中常见的问题及解决措施。
问题一:低温甲醇洗装置运行时,甲醇的挥发量较大,影响了环境的治理。
解决措施:首先要检查甲醇的供应是否合理,甲醇的供应应该根据设备的实际需要进行调控,避免过量供应,同时也应该加大甲醇检修的力度,确保甲醇储罐的密封性能良好,减少甲醇的挥发量;其次,可以在装置周围设置风机、排风装置等设备,增加空气流通量,保证空气的清新。
解决措施:泵的运行状态不佳,可能是因为泵的阀门堵塞、泵轴承磨损或是泵体进口有异物等原因造成的,对此,需针对性的进行修复、更换壳体、轴承等部件,并进行清洗而保障泵的运行状态。
解决措施:当出现管道的堵塞现象时,需要首先排除堵塞物,可以采用冲洗、喷吹、吸取等方法,清除管道内的杂质和异物。
在清除堵塞物之后,还需要对管道进行检修和洗涤,从而确保设备的正常运转。
问题四:低温甲醇洗装置运行时,缺乏对管道的定期检修和维护。
解决措施:为确保低温甲醇洗装置的正常运转,需要定期对设备进行检修和维护。
检修时,应该注意检查管道的密封性和阀门的开闭状态,以及泵的运转情况。
在发现问题时,应该及时派出工作人员进行及时稽查,进行合理的维护和修复工作。
综上所述,为确保低温甲醇洗装置的正常运转,需要加强设备的检测和维护力度,及时排除问题,保证设备的效率,并确保生产出的燃料的品质和纯度,以及避免对环境造成不良影响。
甲醇合成装置优化运行总结
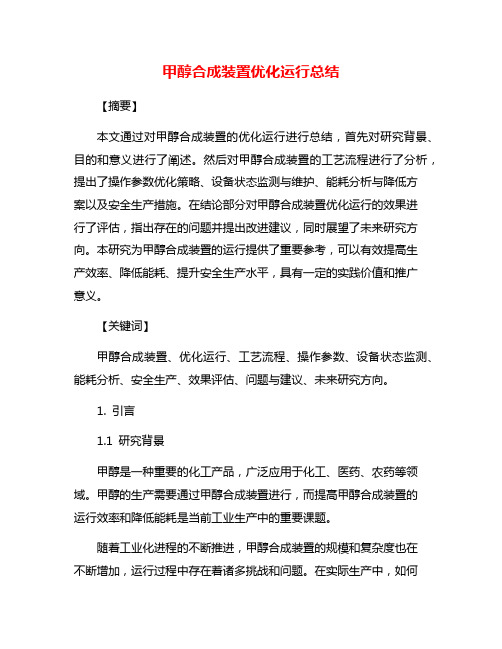
甲醇合成装置优化运行总结【摘要】本文通过对甲醇合成装置的优化运行进行总结,首先对研究背景、目的和意义进行了阐述。
然后对甲醇合成装置的工艺流程进行了分析,提出了操作参数优化策略、设备状态监测与维护、能耗分析与降低方案以及安全生产措施。
在结论部分对甲醇合成装置优化运行的效果进行了评估,指出存在的问题并提出改进建议,同时展望了未来研究方向。
本研究为甲醇合成装置的运行提供了重要参考,可以有效提高生产效率、降低能耗、提升安全生产水平,具有一定的实践价值和推广意义。
【关键词】甲醇合成装置、优化运行、工艺流程、操作参数、设备状态监测、能耗分析、安全生产、效果评估、问题与建议、未来研究方向。
1. 引言1.1 研究背景甲醇是一种重要的化工产品,广泛应用于化工、医药、农药等领域。
甲醇的生产需要通过甲醇合成装置进行,而提高甲醇合成装置的运行效率和降低能耗是当前工业生产中的重要课题。
随着工业化进程的不断推进,甲醇合成装置的规模和复杂度也在不断增加,运行过程中存在着诸多挑战和问题。
在实际生产中,如何科学合理地优化甲醇合成装置的运行,提高生产效率和质量,降低能耗和成本,保障生产安全,已成为当前甲醇行业亟待解决的问题。
为了更好地解决甲醇合成装置优化运行的问题,本文对甲醇合成装置的工艺流程进行了深入分析,探讨了操作参数优化策略、设备状态监测与维护、能耗分析与降低方案以及安全生产措施等方面,旨在为甲醇生产企业提供更有效的优化运行方案。
1.2 研究目的甲醇合成装置是重要的化工生产设备,其优化运行对降低生产成本、提高生产效率具有重要意义。
本次研究的目的在于通过对甲醇合成装置的工艺流程分析、操作参数优化策略、设备状态监测与维护、能耗分析与降低方案以及安全生产措施等方面的研究,探讨如何使甲醇合成装置的运行更加稳定、高效。
通过对甲醇合成装置优化运行的效果评估,及存在的问题与改进建议的分析,为今后的生产提供重要参考。
未来研究方向展望将在继续优化甲醇合成装置的运行模式、提高产品质量和生产效率的基础上,进一步探索更加环保和节能的生产工艺,为甲醇合成装置的长期可持续发展提供科学依据。
低温甲醇洗装置运行中出现的问题及解决措施

低温甲醇洗装置运行中出现的问题及解决措施低温甲醇洗装置是一种用于去除煤气中硫化氢和二氧化碳的设备,通常用于天然气净化工艺中。
在运行过程中,由于煤气成分复杂、工艺条件变化等原因,可能会出现一些问题。
本文将就低温甲醇洗装置运行中可能出现的问题进行分析,并提出相应的解决措施。
一、问题一:甲醇损耗过大甲醇在低温甲醇洗装置中起到溶解硫化氢和二氧化碳的作用。
如果甲醇损耗过大,不仅会增加生产成本,还会影响设备的正常运行。
甲醇损耗过大的原因可能有多种,包括:1. 煤气中硫化氢和二氧化碳含量过高,导致甲醇消耗过多;2. 操作不当,例如温度、压力控制不当导致甲醇挥发损失;3. 设备本身存在泄漏,导致甲醇损耗。
解决方式:1. 对原料煤气进行预处理,降低硫化氢和二氧化碳的含量;2. 对操作人员进行培训,加强操作规程的执行;3. 定期对设备进行检查和维护,及时发现并修复泄漏点。
二、问题二:结垢和结晶在低温甲醇洗装置中,甲醇会受到低温的影响,容易结晶或结垢,导致设备堵塞或性能下降。
1. 适当提高操作温度,避免甲醇结晶;2. 对设备进行定期清洗,避免结垢影响设备运行;3. 优化设备结构,设计合理的排污系统,避免结垢产生。
三、问题三:设备堵塞1. 设备运行中定期清理沉淀物;2. 增加过滤器,防止杂质进入设备引起堵塞;3. 提高操作技能,防止操作不当引起设备堵塞。
四、问题四:设备性能下降低温甲醇洗装置在长期运行中,可能会出现设备性能下降的问题,表现为去除硫化氢和二氧化碳效果降低。
1. 定期对设备进行检修和维护,保持设备的良好状态;2. 加强操作管理,避免操作不当引起设备性能下降;3. 对设备进行适当的改进和优化。
低温甲醇洗装置在运行中可能会出现各种问题,但只要我们加强设备管理、提高操作技能、定期维护保养,就能有效地解决这些问题,确保设备正常运行,保证生产安全和生产效率。
低温甲醇洗装置运行中出现的问题及解决措施
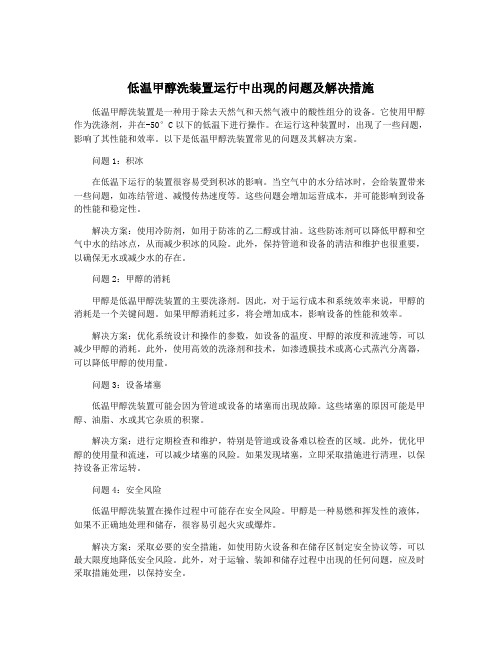
低温甲醇洗装置运行中出现的问题及解决措施低温甲醇洗装置是一种用于除去天然气和天然气液中的酸性组分的设备。
它使用甲醇作为洗涤剂,并在-50°C以下的低温下进行操作。
在运行这种装置时,出现了一些问题,影响了其性能和效率。
以下是低温甲醇洗装置常见的问题及其解决方案。
问题1:积冰在低温下运行的装置很容易受到积冰的影响。
当空气中的水分结冰时,会给装置带来一些问题,如冻结管道、减慢传热速度等。
这些问题会增加运营成本,并可能影响到设备的性能和稳定性。
解决方案:使用冷防剂,如用于防冻的乙二醇或甘油。
这些防冻剂可以降低甲醇和空气中水的结冰点,从而减少积冰的风险。
此外,保持管道和设备的清洁和维护也很重要,以确保无水或减少水的存在。
问题2:甲醇的消耗甲醇是低温甲醇洗装置的主要洗涤剂。
因此,对于运行成本和系统效率来说,甲醇的消耗是一个关键问题。
如果甲醇消耗过多,将会增加成本,影响设备的性能和效率。
解决方案:优化系统设计和操作的参数,如设备的温度、甲醇的浓度和流速等,可以减少甲醇的消耗。
此外,使用高效的洗涤剂和技术,如渗透膜技术或离心式蒸汽分离器,可以降低甲醇的使用量。
问题3:设备堵塞低温甲醇洗装置可能会因为管道或设备的堵塞而出现故障。
这些堵塞的原因可能是甲醇、油脂、水或其它杂质的积聚。
解决方案:进行定期检查和维护,特别是管道或设备难以检查的区域。
此外,优化甲醇的使用量和流速,可以减少堵塞的风险。
如果发现堵塞,立即采取措施进行清理,以保持设备正常运转。
问题4:安全风险低温甲醇洗装置在操作过程中可能存在安全风险。
甲醇是一种易燃和挥发性的液体,如果不正确地处理和储存,很容易引起火灾或爆炸。
解决方案:采取必要的安全措施,如使用防火设备和在储存区制定安全协议等,可以最大限度地降低安全风险。
此外,对于运输、装卸和储存过程中出现的任何问题,应及时采取措施处理,以保持安全。
甲醇装置危险因素分析及其防范措施

甲醇装置危险因素分析及其防范措施简介甲醇是一种常见的化学品,随着技术的发展,甲醇被广泛地应用于工业生产领域。
然而,甲醇有着较高的毒性和易燃性,甲醇装置的设计和运行存在一定的危险性。
本文将对甲醇装置的危险因素进行分析,并提出相应的防范措施。
甲醇装置的危险因素1.化学品泄漏甲醇是一种易挥发的化学品,容易发生泄漏,如不及时清理和处理,会对生产环境和工作人员造成一定的伤害。
2.反应失控甲醇在制造过程中需要进行化学反应,如果反应温度、压力、加热方式等控制不当,会导致反应失控,可能引发火灾、爆炸等严重事故。
3.静电火花甲醇在工业生产过程中产生的静电容易引起火花,从而引起甲醇自燃或爆炸事故。
4.设备故障甲醇装置中的设备无论是生产设备还是安全设备,如果发生故障,都会引发生产安全事故,例如:进料泄漏,仪表失灵,管道破裂等。
甲醇装置的防范措施1.加强装置的安全管理在甲醇装置运行过程中,应严格加强管理,制定相关策略和措施,减少危险的发生,确保生产、环境和员工的安全。
例如建立完善的安全工作体系,加强操作规程和监测控制等。
2.增加监测控制装置为了减少甲醇装置中产生事故的可能性,应增加监测控制装置,确保工厂运行安全可靠,如加装防爆控制器、温度控制器、液位传感器等。
3.加强人员培训和技能考核员工是防范甲醇装置事故的第一道防线,所以加强人员培训和技能考核,对员工进行工作现场的安全培训和技能操作考核,增强员工的安全意识。
如应急预案和安全演练等。
4.定期设备检测和维护定期检测和维护甲醇装置中的设备,确保设备良好的运行状态,设备维护应涵盖各种不同的设备类型,如泵、机器、仪器等。
这样可以保证设备的安全性和耐用性,避免因设备老化而导致的安全事故。
5.建立完善的预警机制建立完善的作业环境监测机制和预警机制,及时响应和处理突发事件和危险情况,加强管理人员对员工的指导和监督,提高企业的应急处置能力和反应速度。
结论甲醇装置是一个高危险性的化工生产领域,为确保生产安全和员工生命健康,需要采取具体的措施减少和避免危险因素的发生。
低温甲醇洗装置运行中出现的问题及解决措施
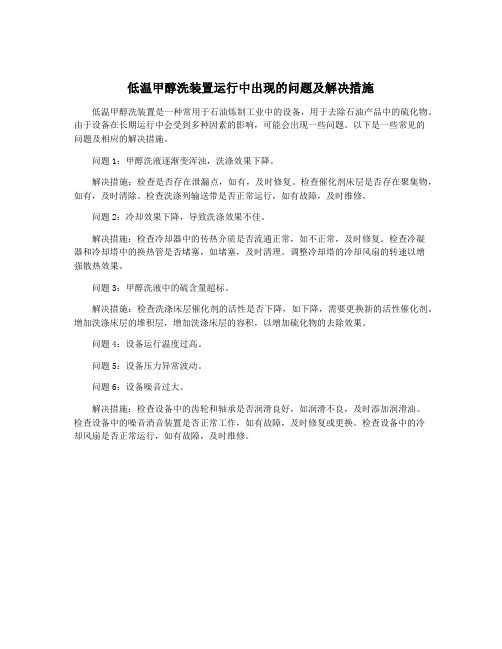
低温甲醇洗装置运行中出现的问题及解决措施
低温甲醇洗装置是一种常用于石油炼制工业中的设备,用于去除石油产品中的硫化物。
由于设备在长期运行中会受到多种因素的影响,可能会出现一些问题。
以下是一些常见的
问题及相应的解决措施。
问题1:甲醇洗液逐渐变浑浊,洗涤效果下降。
解决措施:检查是否存在泄漏点,如有,及时修复。
检查催化剂床层是否存在聚集物,如有,及时清除。
检查洗涤列输送带是否正常运行,如有故障,及时维修。
问题2:冷却效果下降,导致洗涤效果不佳。
解决措施:检查冷却器中的传热介质是否流通正常,如不正常,及时修复。
检查冷凝
器和冷却塔中的换热管是否堵塞,如堵塞,及时清理。
调整冷却塔的冷却风扇的转速以增
强散热效果。
问题3:甲醇洗液中的硫含量超标。
解决措施:检查洗涤床层催化剂的活性是否下降,如下降,需要更换新的活性催化剂。
增加洗涤床层的堆积层,增加洗涤床层的容积,以增加硫化物的去除效果。
问题4:设备运行温度过高。
问题5:设备压力异常波动。
问题6:设备噪音过大。
解决措施:检查设备中的齿轮和轴承是否润滑良好,如润滑不良,及时添加润滑油。
检查设备中的噪音消音装置是否正常工作,如有故障,及时修复或更换。
检查设备中的冷
却风扇是否正常运行,如有故障,及时维修。
低温甲醇洗装置运行中出现的问题及解决措施
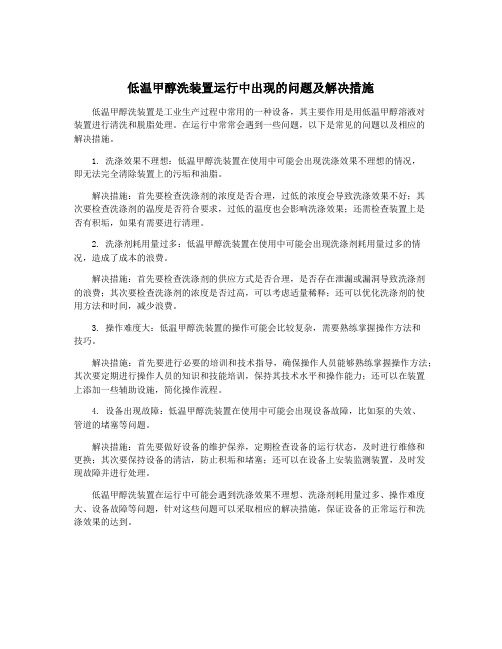
低温甲醇洗装置运行中出现的问题及解决措施低温甲醇洗装置是工业生产过程中常用的一种设备,其主要作用是用低温甲醇溶液对装置进行清洗和脱脂处理。
在运行中常常会遇到一些问题,以下是常见的问题以及相应的解决措施。
1. 洗涤效果不理想:低温甲醇洗装置在使用中可能会出现洗涤效果不理想的情况,即无法完全清除装置上的污垢和油脂。
解决措施:首先要检查洗涤剂的浓度是否合理,过低的浓度会导致洗涤效果不好;其次要检查洗涤剂的温度是否符合要求,过低的温度也会影响洗涤效果;还需检查装置上是否有积垢,如果有需要进行清理。
2. 洗涤剂耗用量过多:低温甲醇洗装置在使用中可能会出现洗涤剂耗用量过多的情况,造成了成本的浪费。
解决措施:首先要检查洗涤剂的供应方式是否合理,是否存在泄漏或漏洞导致洗涤剂的浪费;其次要检查洗涤剂的浓度是否过高,可以考虑适量稀释;还可以优化洗涤剂的使用方法和时间,减少浪费。
3. 操作难度大:低温甲醇洗装置的操作可能会比较复杂,需要熟练掌握操作方法和技巧。
解决措施:首先要进行必要的培训和技术指导,确保操作人员能够熟练掌握操作方法;其次要定期进行操作人员的知识和技能培训,保持其技术水平和操作能力;还可以在装置上添加一些辅助设施,简化操作流程。
4. 设备出现故障:低温甲醇洗装置在使用中可能会出现设备故障,比如泵的失效、管道的堵塞等问题。
解决措施:首先要做好设备的维护保养,定期检查设备的运行状态,及时进行维修和更换;其次要保持设备的清洁,防止积垢和堵塞;还可以在设备上安装监测装置,及时发现故障并进行处理。
低温甲醇洗装置在运行中可能会遇到洗涤效果不理想、洗涤剂耗用量过多、操作难度大、设备故障等问题,针对这些问题可以采取相应的解决措施,保证设备的正常运行和洗涤效果的达到。
低温甲醇洗装置运行中出现的问题及解决措施

低温甲醇洗装置运行中出现的问题及解决措施低温甲醇洗装置是一种常见的气体处理设备,用于去除天然气中的杂质和液态碳氢化合物,确保供应品质量。
在运行过程中,可能会出现一些问题。
接下来将讨论一些常见的问题及其解决措施。
问题1:甲醇泄漏低温甲醇洗装置运行过程中,可能出现甲醇泄漏。
这可能会对环境和人员造成危害,并影响设备的正常运行。
解决措施:- 定期检查设备和管道的密封性,确保没有泄漏点。
- 安装甲醇泄漏检测器,并确保其正常工作。
- 确保操作人员都经过培训,知道如何正确操作设备,以避免甲醇泄漏。
解决措施:- 确保提供足够的加热设备,以保持设备的温度在正常范围内。
- 定期检查设备和管道的绝热性能,修复破损的绝热层。
- 定期清理设备和管道,以防止结冰物堆积。
问题3:设备堵塞在低温甲醇洗装置中,可能会因为杂质的沉积而导致设备堵塞。
这会影响到设备的正常运行,并可能导致设备故障。
解决措施:- 确保使用高质量的过滤器,并定期更换过滤器。
- 定期对设备进行清洗和维护,以防止杂质积聚。
- 将天然气中的杂质控制在合理范围内,以减少对设备的损害。
解决措施:- 定期监测甲醇的消耗情况,确保甲醇消耗在合理范围内。
- 优化设备的操作参数,使设备能够在最佳工作条件下运行,并确保甲醇利用率最大化。
- 配备足够的甲醇储备,以应对突发情况。
低温甲醇洗装置在运行中可能会出现甲醇泄漏、设备结冰、设备堵塞和甲醇减少等问题。
通过定期检查设备的密封性、加热设备的工作状态,以及定期清洁设备和维护的方法,可以有效解决这些问题,确保设备能够正常运行,并提高设备的使用寿命。
低温甲醇洗装置运行中出现的问题及解决措施
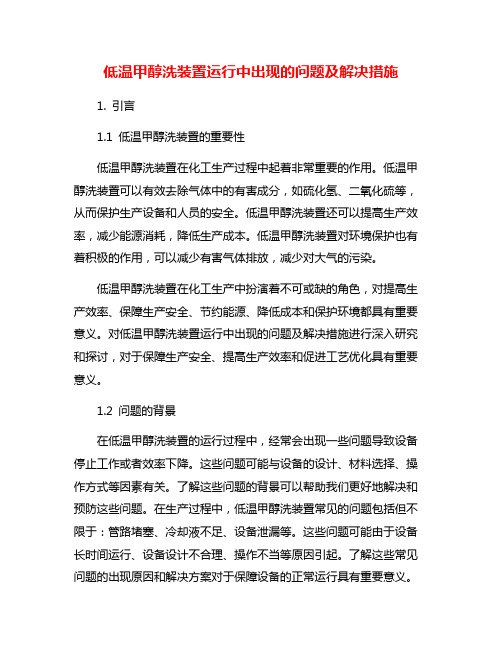
低温甲醇洗装置运行中出现的问题及解决措施1. 引言1.1 低温甲醇洗装置的重要性低温甲醇洗装置在化工生产过程中起着非常重要的作用。
低温甲醇洗装置可以有效去除气体中的有害成分,如硫化氢、二氧化硫等,从而保护生产设备和人员的安全。
低温甲醇洗装置还可以提高生产效率,减少能源消耗,降低生产成本。
低温甲醇洗装置对环境保护也有着积极的作用,可以减少有害气体排放,减少对大气的污染。
低温甲醇洗装置在化工生产中扮演着不可或缺的角色,对提高生产效率、保障生产安全、节约能源、降低成本和保护环境都具有重要意义。
对低温甲醇洗装置运行中出现的问题及解决措施进行深入研究和探讨,对于保障生产安全、提高生产效率和促进工艺优化具有重要意义。
1.2 问题的背景在低温甲醇洗装置的运行过程中,经常会出现一些问题导致设备停止工作或者效率下降。
这些问题可能与设备的设计、材料选择、操作方式等因素有关。
了解这些问题的背景可以帮助我们更好地解决和预防这些问题。
在生产过程中,低温甲醇洗装置常见的问题包括但不限于:管路堵塞、冷却液不足、设备泄漏等。
这些问题可能由于设备长时间运行、设备设计不合理、操作不当等原因引起。
了解这些常见问题的出现原因和解决方案对于保障设备的正常运行具有重要意义。
在本文中,我们将就低温甲醇洗装置运行中常见的问题及其解决措施进行详细探讨,希望能够为相关技术人员提供一些参考和帮助。
2. 正文2.1 常见问题及原因1. 低温甲醇洗装置运行中常见的问题之一是管道堵塞。
管道堵塞可能由于甲醇结晶、沉淀或异物堵塞而引起,导致设备停止运行。
2. 另一个常见问题是设备泵的失效。
泵失效可能是由于泵的磨损、密封件老化或泵体设计不合理等原因造成的,会影响设备的正常运转。
3. 操作人员的操作错误也是导致低温甲醇洗装置出现问题的原因之一。
操作不当可能导致设备过载、温度过高或压力过大,引发设备故障。
4. 低温甲醇洗装置的传感器故障也是常见问题之一。
传感器故障可能导致设备监控不准确,无法及时发现问题并进行处理,从而影响设备的正常运行。
低温甲醇洗装置运行中出现的问题及解决措施
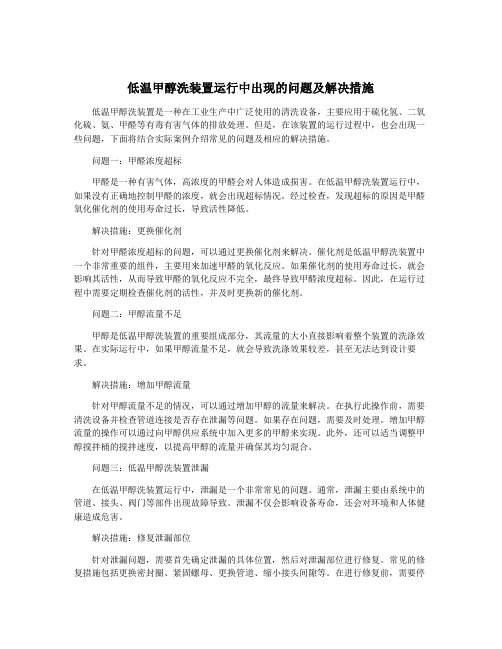
低温甲醇洗装置运行中出现的问题及解决措施低温甲醇洗装置是一种在工业生产中广泛使用的清洗设备,主要应用于硫化氢、二氧化硫、氨、甲醛等有毒有害气体的排放处理。
但是,在该装置的运行过程中,也会出现一些问题,下面将结合实际案例介绍常见的问题及相应的解决措施。
问题一:甲醛浓度超标甲醛是一种有害气体,高浓度的甲醛会对人体造成损害。
在低温甲醇洗装置运行中,如果没有正确地控制甲醛的浓度,就会出现超标情况。
经过检查,发现超标的原因是甲醛氧化催化剂的使用寿命过长,导致活性降低。
解决措施:更换催化剂针对甲醛浓度超标的问题,可以通过更换催化剂来解决。
催化剂是低温甲醇洗装置中一个非常重要的组件,主要用来加速甲醛的氧化反应。
如果催化剂的使用寿命过长,就会影响其活性,从而导致甲醛的氧化反应不完全,最终导致甲醛浓度超标。
因此,在运行过程中需要定期检查催化剂的活性,并及时更换新的催化剂。
问题二:甲醇流量不足甲醇是低温甲醇洗装置的重要组成部分,其流量的大小直接影响着整个装置的洗涤效果。
在实际运行中,如果甲醇流量不足,就会导致洗涤效果较差,甚至无法达到设计要求。
解决措施:增加甲醇流量针对甲醇流量不足的情况,可以通过增加甲醇的流量来解决。
在执行此操作前,需要清洗设备并检查管道连接是否存在泄漏等问题。
如果存在问题,需要及时处理。
增加甲醇流量的操作可以通过向甲醇供应系统中加入更多的甲醇来实现。
此外,还可以适当调整甲醇搅拌桶的搅拌速度,以提高甲醇的流量并确保其均匀混合。
问题三:低温甲醇洗装置泄漏在低温甲醇洗装置运行中,泄漏是一个非常常见的问题。
通常,泄漏主要由系统中的管道、接头、阀门等部件出现故障导致。
泄漏不仅会影响设备寿命,还会对环境和人体健康造成危害。
解决措施:修复泄漏部位针对泄漏问题,需要首先确定泄漏的具体位置,然后对泄漏部位进行修复。
常见的修复措施包括更换密封圈、紧固螺母、更换管道、缩小接头间隙等。
在进行修复前,需要停止相关设备的运行,并对泄漏部位进行必要的检查和测试。
甲醇装置运行中存在的问题及解决措施
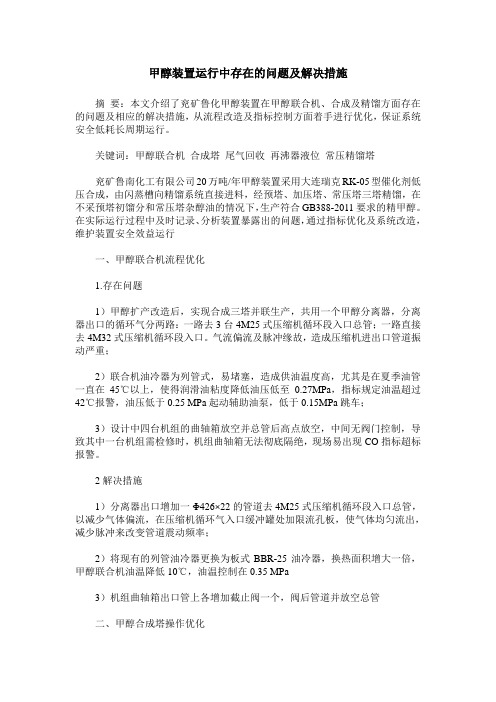
甲醇装置运行中存在的问题及解决措施摘要:本文介绍了兖矿鲁化甲醇装置在甲醇联合机、合成及精馏方面存在的问题及相应的解决措施,从流程改造及指标控制方面着手进行优化,保证系统安全低耗长周期运行。
关键词:甲醇联合机合成塔尾气回收再沸器液位常压精馏塔兖矿鲁南化工有限公司20万吨/年甲醇装置采用大连瑞克RK-05型催化剂低压合成,由闪蒸槽向精馏系统直接进料,经预塔、加压塔、常压塔三塔精馏,在不采预塔初馏分和常压塔杂醇油的情况下,生产符合GB388-2011要求的精甲醇。
在实际运行过程中及时记录、分析装置暴露出的问题,通过指标优化及系统改造,维护装置安全效益运行一、甲醇联合机流程优化1.存在问题1)甲醇扩产改造后,实现合成三塔并联生产,共用一个甲醇分离器,分离器出口的循环气分两路:一路去3台4M25式压缩机循环段入口总管;一路直接去4M32式压缩机循环段入口。
气流偏流及脉冲缘故,造成压缩机进出口管道振动严重;2)联合机油冷器为列管式,易堵塞,造成供油温度高,尤其是在夏季油管一直在45℃以上,使得润滑油粘度降低油压低至0.27MPa,指标规定油温超过42℃报警,油压低于0.25 MPa起动辅助油泵,低于0.15MPa跳车;3)设计中四台机组的曲轴箱放空并总管后高点放空,中间无阀门控制,导致其中一台机组需检修时,机组曲轴箱无法彻底隔绝,现场易出现CO指标超标报警。
2解决措施1)分离器出口增加一Φ426×22的管道去4M25式压缩机循环段入口总管,以减少气体偏流,在压缩机循环气入口缓冲罐处加限流孔板,使气体均匀流出,减少脉冲来改变管道震动频率;2)将现有的列管油冷器更换为板式BBR-25油冷器,换热面积增大一倍,甲醇联合机油温降低10℃,油温控制在0.35 MPa3)机组曲轴箱出口管上各增加截止阀一个,阀后管道并放空总管二、甲醇合成塔操作优化2013年4月,合成更换使用RK-05催化剂,升温还原后缓慢导入新鲜气,在较低压力、较低CO、CO2浓度下进行轻负荷运行,5月逐渐调整到滿负荷状况,转入正常生产。
低温甲醇洗装置运行中出现的问题及解决措施
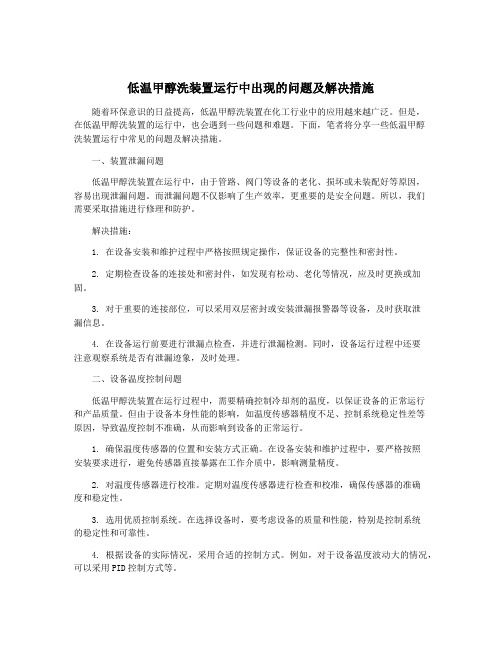
低温甲醇洗装置运行中出现的问题及解决措施随着环保意识的日益提高,低温甲醇洗装置在化工行业中的应用越来越广泛。
但是,在低温甲醇洗装置的运行中,也会遇到一些问题和难题。
下面,笔者将分享一些低温甲醇洗装置运行中常见的问题及解决措施。
一、装置泄漏问题低温甲醇洗装置在运行中,由于管路、阀门等设备的老化、损坏或未装配好等原因,容易出现泄漏问题。
而泄漏问题不仅影响了生产效率,更重要的是安全问题。
所以,我们需要采取措施进行修理和防护。
解决措施:1. 在设备安装和维护过程中严格按照规定操作,保证设备的完整性和密封性。
2. 定期检查设备的连接处和密封件,如发现有松动、老化等情况,应及时更换或加固。
3. 对于重要的连接部位,可以采用双层密封或安装泄漏报警器等设备,及时获取泄漏信息。
4. 在设备运行前要进行泄漏点检查,并进行泄漏检测。
同时,设备运行过程中还要注意观察系统是否有泄漏迹象,及时处理。
二、设备温度控制问题低温甲醇洗装置在运行过程中,需要精确控制冷却剂的温度,以保证设备的正常运行和产品质量。
但由于设备本身性能的影响,如温度传感器精度不足、控制系统稳定性差等原因,导致温度控制不准确,从而影响到设备的正常运行。
1. 确保温度传感器的位置和安装方式正确。
在设备安装和维护过程中,要严格按照安装要求进行,避免传感器直接暴露在工作介质中,影响测量精度。
2. 对温度传感器进行校准。
定期对温度传感器进行检查和校准,确保传感器的准确度和稳定性。
3. 选用优质控制系统。
在选择设备时,要考虑设备的质量和性能,特别是控制系统的稳定性和可靠性。
4. 根据设备的实际情况,采用合适的控制方式。
例如,对于设备温度波动大的情况,可以采用PID控制方式等。
三、设备堵塞问题低温甲醇洗装置在运行过程中,由于工作介质中含有颗粒物或杂质等物质,容易造成设备堵塞,影响到设备的正常运行。
1. 选择合适的滤芯或过滤器。
在设备安装中,应根据工作介质的特性选择合适的过滤器或滤芯,并定期更换。
低温甲醇洗装置运行中出现的问题及解决措施

低温甲醇洗装置运行中出现的问题及解决措施低温甲醇洗装置是石油化工行业中常见的一种设备,主要用于甲醇的生产和提纯过程中的洗涤工艺。
然而在该装置的运行过程中,可能会出现一些问题,需要及时解决。
本文将就低温甲醇洗装置运行中可能出现的问题及解决措施进行详细的介绍。
问题一:低温甲醇洗装置出现洗涤效果不佳的情况在低温甲醇洗装置的运行过程中,有时会出现洗涤效果不佳的情况,主要表现为洗涤后甲醇的纯度不符合要求,甚至出现某些杂质无法被有效去除的情况。
解决措施:首先需要对该问题进行细致的分析,可能的原因包括洗涤介质的温度、流量、浓度、洗涤塔的结构设计等方面。
针对具体情况,可以采取以下措施进行解决:1. 根据洗涤介质的性质和特点,调节洗涤塔的温度、流量和浓度,以保证洗涤效果。
2. 对洗涤塔的结构和设备进行检查,确保设备运行正常,不出现堵塞或泄漏等情况。
3. 对操作人员进行培训,提高他们对设备操作的熟练程度,避免操作不当导致效果不佳。
在低温甲醇洗装置的长时间运行过程中,可能会出现设备损坏或故障的情况,这将严重影响装置的正常运行和甲醇的洗涤过程。
解决措施:针对设备故障或损坏的情况,可以采取以下措施进行解决:1. 定期对设备进行检查和维护,确保设备处于良好的运行状态。
2. 对出现的故障进行及时的排查和修复,避免故障扩大影响设备的运行。
3. 对设备进行更新和维护,提高设备的使用寿命和稳定性。
在低温甲醇洗装置的运行过程中,可能会出现能源消耗过大的情况,导致生产成本增加,效益降低。
1. 调整设备的操作参数,减小能源的消耗,提高装置的能效。
2. 对设备的能源利用进行优化,改进设备的设计和工艺流程,降低能源的消耗。
3. 对设备进行更新和改造,采用新的节能技术和设备,提高设备的能效和降低能源的消耗。
在低温甲醇洗装置的运行过程中,可能会出现安全隐患,例如洗涤介质泄漏、设备堆积过厚、操作不当等问题,严重影响生产安全。
1. 对设备进行定期安全检查,排查潜在的安全隐患,及时进行整改和修复。
低温甲醇洗装置运行中出现的问题及解决措施

低温甲醇洗装置运行中出现的问题及解决措施低温甲醇洗装置是一种用于石油化工行业的重要设备,其主要功能是通过低温甲醇溶液对原油进行洗涤处理,以降低原油中的硫、氮等有害物质的含量,提高原油的质量。
在低温甲醇洗装置运行中,常常会出现各种问题,严重影响设备的正常运行和生产效率。
本文将就低温甲醇洗装置运行中常见的问题及解决措施进行详细介绍。
一、问题一:低温甲醇洗装置冷凝器传热效果不佳问题描述:低温甲醇洗装置中的冷凝器是用于冷却和凝结洗涤后的甲醇溶液中的水蒸气,使其重新形成液态甲醇并回收的重要设备。
在运行中,冷凝器传热效果不佳,导致冷凝效果下降,影响了洗涤和回收的效果。
解决措施:首先要对冷凝器进行彻底的清洗和检查,排除可能存在的污垢和堵塞,保证冷凝器的传热管道畅通。
其次要检查冷媒的流量和温度,调整冷媒的流量和温度,保证冷媒的质量和流量符合要求。
可以考虑增加冷凝器的散热面积或改善冷媒的循环方式,以提高冷凝器的传热效果。
二、问题二:低温甲醇洗装置沉淀槽结晶速度过慢解决措施:首先要优化沉淀槽的操作参数,包括调整温度、压力和搅拌速度等,以提高沉淀槽内的流动速度和混合效果。
其次可以考虑增加沉淀槽的深度和增加沉淀剂的投加量,以提高沉淀效果。
同时还可以考虑对沉淀槽进行升级改造,例如增加加热设备或增加沉淀槽的数量,以提高沉淀速度和效果。
三、问题三:低温甲醇洗装置甲醇溶液泵漏液严重问题描述:低温甲醇洗装置中的甲醇溶液泵用于输送和循环洗涤后的甲醇溶液,然而在运行中,甲醇溶液泵漏液严重,导致甲醇的损耗增加和设备的泄漏现象。
解决措施:首先要对甲醇溶液泵进行彻底的检查和维护,包括更换叶轮、密封圈和轴承等易损件,以保证泵的正常运转和密封性。
其次可以考虑增加泵的密封装置或改善泵的密封性能,以降低甲醇溶液泵的漏液率。
同时还可以考虑增加泵的备用件和增加定期检修的频率,以提高泵的可靠性和使用寿命。
解决措施:首先要对管道进行彻底的清洗和检查,排除可能存在的污垢和堵塞,保证管道的流通畅通。
新能凤凰甲醇装置存在的问题及解决措施
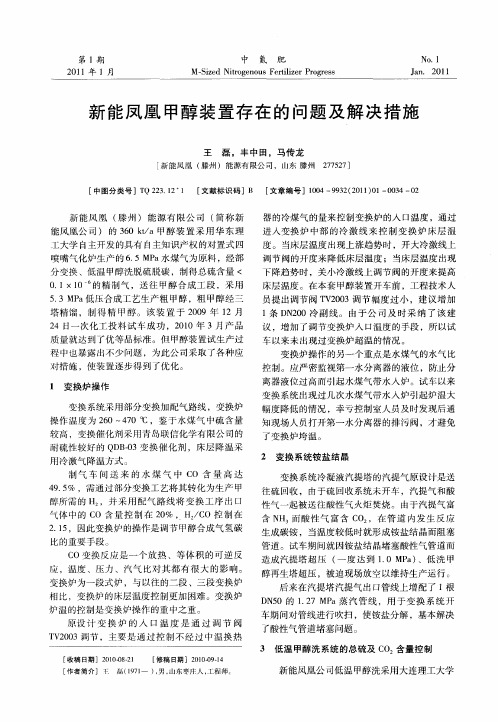
2 1 年 1月 01
中 氮
肥
No .1
M — ie to e o sFe t ie o r s Sz d Nir g n u ri z rPr g e s l
Hale Waihona Puke J n 2 1 a. 0 1
新 能 凤凰 甲醇 装 置存 在 的 问题 及解 决措 施
王 磊 ,丰 中田 ,马传 龙
・5・ 3
的具有 自主 知识产 权 的气 体净 化技 术 ,该 技术 具 有气体 净化 度高 、吸 收选 择性 好 、技术 成熟 、运
行 成本低 等 特 点 。低 温 甲醇 洗 为 物理 吸 收 过程 , 其 吸 收效 果 与压力 、温度 、循 环量 以及 吸收剂 甲
醇 的浓度 密切 相关 。
器 的冷煤气 的量来 控 制变换 炉 的入 口温 度 ,通 过 进入 变换 炉 中部 的冷 激 线 来 控 制 变换 炉 床层 温 度 。当床层 温度 出现 上涨趋 势时 ,开大 冷激线 上 调节 阀 的开 度来 降低床 层温度 ;当床层 温度 出现 下 降趋 势时 ,关小 冷激线 上调 节 阀的开度来 提 高 床 层温度 。在本套 甲醇装 置开 车前 ,工程 技术人 员 提 出调节 阀 T 2 0 节 幅 度过 小 ,建 议增 加 V 0 3调 1 D 2 0冷 副 线 。 由于 公 司及 时 采 纳 了该 建 条 N0
用 冷激气 降温 方式 。 制 气 车 间 送 来 的 水 煤 气 中 C 含 量 高 达 O 4 . % ,需 通过部分 变换 工艺将 其转 化为生 产 甲 95 醇所 需 的 H, ,并 采 用 配 气路 线 将 变 换 工 序 出 口 气体 中的 C 含 量 控 制 在 2 % ,H / O控 制 在 O 0 C 2 1 ,因此 变换炉 的操作是 调节 甲醇 合成气 氢碳 .5
低温甲醇洗装置运行中出现的问题及解决措施
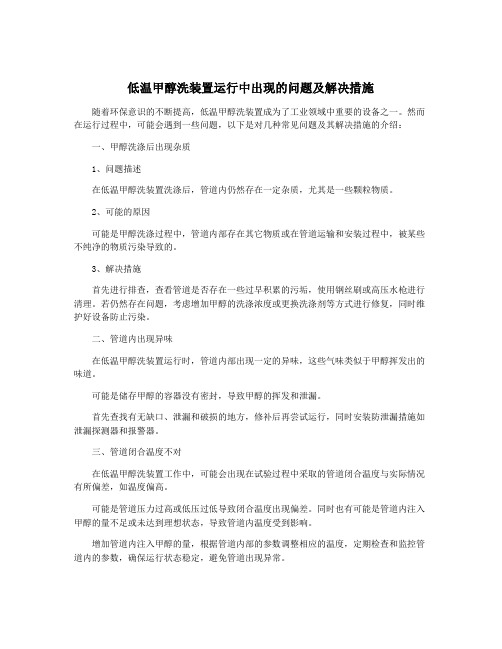
低温甲醇洗装置运行中出现的问题及解决措施
随着环保意识的不断提高,低温甲醇洗装置成为了工业领域中重要的设备之一。
然而在运行过程中,可能会遇到一些问题,以下是对几种常见问题及其解决措施的介绍:
一、甲醇洗涤后出现杂质
1、问题描述
在低温甲醇洗装置洗涤后,管道内仍然存在一定杂质,尤其是一些颗粒物质。
2、可能的原因
可能是甲醇洗涤过程中,管道内部存在其它物质或在管道运输和安装过程中,被某些不纯净的物质污染导致的。
3、解决措施
首先进行排查,查看管道是否存在一些过早积累的污垢,使用钢丝刷或高压水枪进行清理。
若仍然存在问题,考虑增加甲醇的洗涤浓度或更换洗涤剂等方式进行修复,同时维护好设备防止污染。
二、管道内出现异味
在低温甲醇洗装置运行时,管道内部出现一定的异味,这些气味类似于甲醇挥发出的味道。
可能是储存甲醇的容器没有密封,导致甲醇的挥发和泄漏。
首先查找有无缺口、泄漏和破损的地方,修补后再尝试运行,同时安装防泄漏措施如泄漏探测器和报警器。
三、管道闭合温度不对
在低温甲醇洗装置工作中,可能会出现在试验过程中采取的管道闭合温度与实际情况有所偏差,如温度偏高。
可能是管道压力过高或低压过低导致闭合温度出现偏差。
同时也有可能是管道内注入甲醇的量不足或未达到理想状态,导致管道内温度受到影响。
增加管道内注入甲醇的量,根据管道内部的参数调整相应的温度,定期检查和监控管道内的参数,确保运行状态稳定,避免管道出现异常。
低温甲醇洗装置的运行对于企业生产具有非常重要的作用,但其运行中出现问题也同样属于正常现象。
针对这些问题,应及时做出诊断并采取措施进行修复,确保设备的正常运转。
- 1、下载文档前请自行甄别文档内容的完整性,平台不提供额外的编辑、内容补充、找答案等附加服务。
- 2、"仅部分预览"的文档,不可在线预览部分如存在完整性等问题,可反馈申请退款(可完整预览的文档不适用该条件!)。
- 3、如文档侵犯您的权益,请联系客服反馈,我们会尽快为您处理(人工客服工作时间:9:00-18:30)。
甲醇装置运行中存在的问题及解决措施
摘要:本文介绍了兖矿鲁化甲醇装置在甲醇联合机、合成及精馏方面存在的问题及相应的解决措施,从流程改造及指标控制方面着手进行优化,保证系统安全低耗长周期运行。
关键词:甲醇联合机合成塔尾气回收再沸器液位常压精馏塔
兖矿鲁南化工有限公司20万吨/年甲醇装置采用大连瑞克RK-05型催化剂低压合成,由闪蒸槽向精馏系统直接进料,经预塔、加压塔、常压塔三塔精馏,在不采预塔初馏分和常压塔杂醇油的情况下,生产符合GB388-2011要求的精甲醇。
在实际运行过程中及时记录、分析装置暴露出的问题,通过指标优化及系统改造,维护装置安全效益运行
一、甲醇联合机流程优化
1.存在问题
1)甲醇扩产改造后,实现合成三塔并联生产,共用一个甲醇分离器,分离器出口的循环气分两路:一路去3台4M25式压缩机循环段入口总管;一路直接去4M32式压缩机循环段入口。
气流偏流及脉冲缘故,造成压缩机进出口管道振动严重;
2)联合机油冷器为列管式,易堵塞,造成供油温度高,尤其是在夏季油管一直在45℃以上,使得润滑油粘度降低油压低至0.27MPa,指标规定油温超过42℃报警,油压低于0.25 MPa起动辅助油泵,低于0.15MPa跳车;
3)设计中四台机组的曲轴箱放空并总管后高点放空,中间无阀门控制,导致其中一台机组需检修时,机组曲轴箱无法彻底隔绝,现场易出现CO指标超标报警。
2解决措施
1)分离器出口增加一Φ426×22的管道去4M25式压缩机循环段入口总管,以减少气体偏流,在压缩机循环气入口缓冲罐处加限流孔板,使气体均匀流出,减少脉冲来改变管道震动频率;
2)将现有的列管油冷器更换为板式BBR-25油冷器,换热面积增大一倍,甲醇联合机油温降低10℃,油温控制在0.35 MPa
3)机组曲轴箱出口管上各增加截止阀一个,阀后管道并放空总管
二、甲醇合成塔操作优化
2013年4月,合成更换使用RK-05催化剂,升温还原后缓慢导入新鲜气,在较低压力、较低CO、CO2浓度下进行轻负荷运行,5月逐渐调整到滿负荷状况,转入正常生产。
分析系统运行情况,发现吨甲醇耗新鲜气高达2600NM3,放空在6000 NM3/h,对使用初期触媒来说消耗偏高,
取样分析新鲜气气体成分符合(H2-CO2)/(CO+CO2)=2.05~2.15指标,而系统操作压力控制在4.0MPa,合成塔出口温度在216±1℃,对照上炉催化剂使用情况,指标控制偏低,甲醇合成是一个体积缩小的反应,加压对甲醇合成反应是有利的。
RK-05型催化剂使用温度是205~265℃,尽量维持催化剂床层在较低温度下操作,有利于延长催化剂的使用寿命。
综合催化剂产量和使用寿命等因素考虑,合成系统压力控制在4.4MPa,合成塔出口温度控制在224±1℃,最高月产甲醇20.63万吨,吨甲醇耗新鲜气高达2350NM3。
三、甲醇尾气流程优化
净化脱碳闪蒸气800NM3/h(CO:3.86% H2:36.95% CO2:45. 8%)及甲醇闪蒸槽闪蒸气500NM3/h(CO:8% H2:73% CO2:3%)均直接放空至大气中,甲醇驰放气(气量5000~12000 Nm3/h,氢气80.5%)送往氨净化的变换系统,由于驰放气中含有部分甲醇,易造成冷凝液中COD超标;驰放气温度低、波动大,易拉跨变换炉炉温,为避免变换炉炉温低造成氨净化系统的减量停车事故,需维持送氨净化驰放气量稳定,不得不稍开现场放空。
改造时,将净化脱碳闪蒸气和甲醇闪蒸槽闪蒸气送锅炉炉口进行焚烧,副产蒸汽并入系统使用。
两尾气管线在入炉前分别设置有阻火器、止回阀及放空管(调节阀控制)。
两路尾气的现场放空管仍保留,作为锅炉停车或紧急情况下的备用。
在甲醇水洗塔后新上一套膜分离氢回收装置,回收驰放气中的H2用于甲醇生产。
流程如下:驰放气先经预处理系统将其中夹带的液体分离,液体通过甲醇闪蒸槽送往精馏系统;气体进入套管式加热器加热到60℃左右,以保证进膜前的气体远离露点,气体经过加热器加热后,直接从上端侧面进入膜分离器。
氢气以较快的速率透过纤维膜丝,在纤维芯侧得到富氢产品,送往甲醇联合机入口多产甲醇;扩散速率较慢的组分N2、CO、CH4等则滞留在原料侧,送往氨净化产合成氨。
主要设备:分离器1台内装304材质除雾芯件,套管式加热器1台,膜分离器1套,控制系统兼容浙大中控;主要公用介质:0.4MPa(G)150℃低压蒸汽200 kg/h,0.4MPa(G)仪表空气3 Nm3/h,整套膜装置撬装方式提供,露天放置。
装置占地面积为3.0m(宽)×14.0m(长);最高处不超过5m。
两边各留出1m、膜的一端留出3m以供巡查及换膜时用。
膜分离装置运行稳定可靠,无须专人照看,H2回收率:≥87%、浓度:≥90%
四、精馏蒸汽冷凝液流程优化
精馏预塔、加压塔再沸器均采用1.3MPa蒸汽加热,通过控制冷凝液流量,即改变换热面积来控制温度,再沸器内冷凝液目前没有液位指示,只能人为判断,
液位过高,换热面积小温度提不起来;液位过低,潜热利用不彻底,蒸汽损失大,同时冷凝液在管内闪蒸出部分蒸汽,在管道内出现了蒸汽冷凝液和蒸汽的两相流,管线弯头、三通、变径处由于局部阻力大,受流动的冲刷影响最为严重,易出现管壁减薄产生泄漏影响安全运行
五、精馏常压塔流程优化
1存在问题
1)常压塔塔底废水只能分两路外送:一路去气化磨煤一路去污水处理厂,在系统开车时常压塔塔底废水醇含量较高,达30%左右;在系统停车检修时,第一遍水洗液废水醇含量更是高达50%左右,直接外送造成甲醇浪费
2)常压塔塔顶负压造成回流量波动,同时损坏泵密封,漏液
3)当回流槽/常压塔塔底液位低时,控制室人员只能手动关小泵出口调节阀,当泵出口流量小于泵的最小连续流量时,会造成泵的振动、噪声、汽蚀,从而使泵的零部件遭到破坏
5.2解决措施
1)在塔底废水泵出口增加一路去粗甲醇槽,当塔底废水中醇含量高时,将废水改送至粗甲醇槽,重新精馏
2)向常压塔回流槽补充N2,保持正压
3)泵出口增加回流管线,确保泵的最小连续流。