甲醇装置简介和重点部位及设备(通用版)
甲醇装置简介和重点部位及设备(通用版)

( 安全技术 )单位:_________________________姓名:_________________________日期:_________________________精品文档 / Word文档 / 文字可改甲醇装置简介和重点部位及设备(通用版)Technical safety means that the pursuit of technology should also include ensuring that peoplemake mistakes甲醇装置简介和重点部位及设备(通用版)一、装置简介(一)装置发展及类型以一氧化碳和氢为原料合成甲醇的生产技术始于20世纪20年代。
到50年代末,我国已掌握了甲醇和合成甲醇催化剂的制备技术。
60年代未,我国又实现了合成氨和合成甲醇的联合生产(简称联醇),联醇技术降低了合成氨和甲醇的生产成本。
20世纪60年代,世界上,低压法合成甲醇新工艺技术实现了工业化。
低压法由于其能耗低,逐步取代了原来的高压法合成甲醇工艺,并得到了快速发展。
80年代初,我国研制的低压合成甲醇催化剂已达到国际水平。
联醇工艺技术是合成氨生产过程中,利用合成氨原料气中一氧化碳、二氧化碳与氢气同时生产甲醇。
联醇工艺技术由于生产方式灵活、工艺简单、原料利用率高、成本低、效益好,在我国中型合成氨装置得到普遍的推广。
甲醇生产一般以天然气、轻油、重油、煤及某些加工过程中产生的尾气为原料。
制得的原料气通过净化,得到一氧化碳、二氧化碳与氢气,经合成生成甲醇。
典型的流程包括原料气制备、原料气净化、甲醇合成和粗甲醇精馏等工序。
甲醇装置生产工艺所采用的原料气制备与净化工艺,与合成氨装置相同或相类似。
原料气制备工艺类型一般有:煤(焦)固定床气化工艺;煤(焦)气流床气化工艺;渣油、水煤浆部分氧化制气工艺;烃类(轻油、天然气)蒸汽转化制气工艺。
气体净化工艺类型也与合成氨原料气净化工艺类型相同,一般根据原料气的组成不同而采用不同的脱硫、变换、脱碳工艺技术。
甲醇装置工艺概述
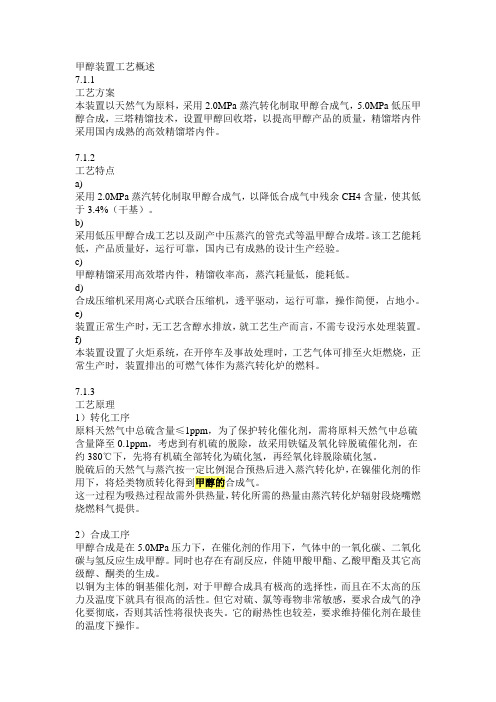
甲醇装置工艺概述7.1.1工艺方案本装置以天然气为原料,采用2.0MPa蒸汽转化制取甲醇合成气,5.0MPa低压甲醇合成,三塔精馏技术,设置甲醇回收塔,以提高甲醇产品的质量,精馏塔内件采用国内成熟的高效精馏塔内件。
7.1.2工艺特点a)采用2.0MPa蒸汽转化制取甲醇合成气,以降低合成气中残余CH4含量,使其低于3.4%(干基)。
b)采用低压甲醇合成工艺以及副产中压蒸汽的管壳式等温甲醇合成塔。
该工艺能耗低,产品质量好,运行可靠,国内已有成熟的设计生产经验。
c)甲醇精馏采用高效塔内件,精馏收率高,蒸汽耗量低,能耗低。
d)合成压缩机采用离心式联合压缩机,透平驱动,运行可靠,操作简便,占地小。
e)装置正常生产时,无工艺含醇水排放,就工艺生产而言,不需专设污水处理装置。
f)本装置设置了火炬系统,在开停车及事故处理时,工艺气体可排至火炬燃烧,正常生产时,装置排出的可燃气体作为蒸汽转化炉的燃料。
7.1.3工艺原理1)转化工序原料天然气中总硫含量≤1ppm,为了保护转化催化剂,需将原料天然气中总硫含量降至0.1ppm,考虑到有机硫的脱除,故采用铁锰及氧化锌脱硫催化剂,在约380℃下,先将有机硫全部转化为硫化氢,再经氧化锌脱除硫化氢。
脱硫后的天然气与蒸汽按一定比例混合预热后进入蒸汽转化炉,在镍催化剂的作用下,将烃类物质转化得到甲醇的合成气。
这一过程为吸热过程故需外供热量,转化所需的热量由蒸汽转化炉辐射段烧嘴燃烧燃料气提供。
2)合成工序甲醇合成是在5.0MPa压力下,在催化剂的作用下,气体中的一氧化碳、二氧化碳与氢反应生成甲醇。
同时也存在有副反应,伴随甲酸甲酯、乙酸甲酯及其它高级醇、酮类的生成。
以铜为主体的铜基催化剂,对于甲醇合成具有极高的选择性,而且在不太高的压力及温度下就具有很高的活性。
但它对硫、氯等毒物非常敏感,要求合成气的净化要彻底,否则其活性将很快丧失。
它的耐热性也较差,要求维持催化剂在最佳的温度下操作。
甲醇车间关键装置重点部位应急救援预案

甲醇车间关键装置、重点部位应急救援预案(ISO45001-2018/ISO14001-2015)1.0目的为保证甲醇车间关键装置、重点部位的操作、检修、仪表、电气等作业人员会识别和及时处理各种不正常现象及事故,特制订本预案。
2.0术语2.1关键生产装置为:2.1.1在易燃、易爆、易腐蚀、高温、高压、真空、深冷、剧毒等工艺条件下运行的装置。
2.1.2在生产系统中处于重要地位、生产操作对安全生产影响较大的其他装置和设施。
2.2重点部位为:2.2.1生产、储运、销售和使用易燃易爆危险化学品,高度和极度危害的化学介质和放射性物质,以及可能形成火灾、爆炸和化学品中毒的罐区、仓库、工段、岗位等场所。
2.2.2、对生产系统安全稳定运行起关键作用的公用工程系统。
3.0应急救援指在发生事故时,采用的消除、减少事故危害和防止事故恶化,最大限度降低事故损失的措施。
4.0预案指根据预测危险源、危险目标可能发生事故的类别,危害程度,而制定的事故应急救援方案,能及时、有效地统筹指导事故应急救援行动。
5.0关键装置、重点部位识别及应急措施名称事故名称应急预案生产工段、岗点气体泄漏穿戴劳保用品,关闭手机及其他通讯工具,禁止远离明火,同时上报公司应急救援指挥部火灾视情况处理,关闭电源,组织应急队伍进行扑救同时上报公司应急救援指挥部爆炸事故上报厂应急指挥部,组织应急队伍进行扑救,同时向附近消防部门请求支援储存区域气体泄漏穿戴劳保用品,关闭手机及其他通讯工具,禁止远离明火,同时上报公司应急救援指挥部火灾视情况处理,关闭电源,组织应急队伍进行扑救同时上报公司应急救援指挥部爆炸事故上报厂应急指挥部,组织应急队伍进行扑救,同时向附近消防部门请求支援储罐区域阀门泄漏正确穿戴劳保用品,关闭手机及其他通讯工具;关闭总阀门;.检修或更换阀门。
超压正确穿戴劳保用品:检查仪表;开启泄压阀门,同时报公司应急指挥部。
电机故障关停设备;切断线路总闸,检查线路:如电机故障,上报厂应急指挥部,组织人员修理。
甲醇合成装置工艺流程及关键控制点分析简介
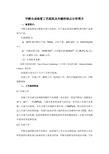
甲醇合成装置工艺流程及关键控制点分析简介一、装置简介:甲醇合成装置是以煤基合成气为原料,生产满足要求的MTO级甲醇产品和氢气产品。
(1)装置能力:a)MTO级甲醇日产量:5500t,小时产量:229.167t(以100%CH3OH 计)。
b)日输出氢气量:15456 Nm3,小时输出量644Nm3,(以99.5% H2计)。
(2)年操作小时:8000小时。
(3)专利技术来源:装置引进英国DPT(Davy Process Technology)公司的工艺包和JMC(Johnson Matthey Catalyst)催化剂。
(4)装置主要由以下几个工艺单元组成:压缩工序、合成工序、精馏工序、氢回收工序、蒸汽冷凝液回收工序、甲醇裂解制氢二、工艺流程简述2.1压缩工序压缩工序合成气压缩机和循环气压缩机。
来自界区(低温甲醇洗)的煤基合成气~30℃、~5.2MPaG,与膜分离来的富氢气混合后,依次进入合成气分离器、合成气压缩机,并在合成气压缩机中增压到~7.8MPaG。
增压后的合成气进入合成气净化预热器,用蒸汽加热并喷入锅炉给水以水解其中的COS,然后进入合成气净化槽,脱除残留的对合成催化剂有毒害的微量组份。
合成气净化槽中装填有净化催化剂。
2.2 合成工序甲醇合成回路由两个串联在一起的蒸汽上升式反应塔组成。
这种串联方式比传统流程在催化剂与设备投资上要更为经济。
甲醇合成塔为径向流反应器,气体通过装填在壳侧的催化剂,发生甲醇合成反应。
反应器内温度由管内上升的蒸汽控制。
副产蒸汽过热后送出界区。
来自合成气压缩机的净化后的合成气分为两股,其中大部分合成气和循环气混合,经过合成回路1号中间换热器加热后,进入1号甲醇合成塔进行甲醇合成反应。
甲醇合成反应在~280℃、~7.46MPaG下,在催化剂的作用下进行,该反应为放热反应。
主要的两个反应如下:CO + 2H2→ CH3OH + QCO2 + 3H2 → CH3OH + H2O + Q反应热副产~2.1MPaG的中压饱和蒸汽,经1号甲醇合成汽包分离后,进入装置内蒸汽总管。
甲醇的技术装备与设施
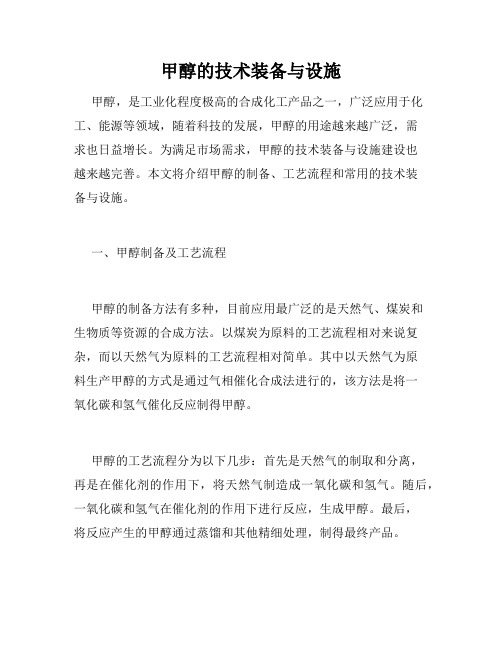
甲醇的技术装备与设施甲醇,是工业化程度极高的合成化工产品之一,广泛应用于化工、能源等领域,随着科技的发展,甲醇的用途越来越广泛,需求也日益增长。
为满足市场需求,甲醇的技术装备与设施建设也越来越完善。
本文将介绍甲醇的制备、工艺流程和常用的技术装备与设施。
一、甲醇制备及工艺流程甲醇的制备方法有多种,目前应用最广泛的是天然气、煤炭和生物质等资源的合成方法。
以煤炭为原料的工艺流程相对来说复杂,而以天然气为原料的工艺流程相对简单。
其中以天然气为原料生产甲醇的方式是通过气相催化合成法进行的,该方法是将一氧化碳和氢气催化反应制得甲醇。
甲醇的工艺流程分为以下几步:首先是天然气的制取和分离,再是在催化剂的作用下,将天然气制造成一氧化碳和氢气。
随后,一氧化碳和氢气在催化剂的作用下进行反应,生成甲醇。
最后,将反应产生的甲醇通过蒸馏和其他精细处理,制得最终产品。
二、甲醇的技术装备与设施1. 合成反应装置合成反应装置是甲醇制备工艺的核心设备之一,通常包括加气管、催化剂层和冷却水管等附件,它们的结构设计和装配工艺对甲醇合成反应的效果有重要影响。
目前从合成装置技术方面来看,常用的有固定床反应器、移动床反应器,流化床反应器等。
2. 精馏装置精馏装置是使甲醇精馏纯化、去除杂质的重要设备,包括粗精馏器、回流塔、精馏塔、加热系统、冷却系统等部分。
甲醇的精馏过程非常复杂,因此精馏塔的结构和操作控制至关重要。
通常采用的装置有常压塔、减压塔、等压塔和蒸汽回流塔等,其中蒸汽回流塔是目前甲醇精馏的主要方式。
3. 生产储罐生产储罐是指用于储存甲醇的设备,通常采用圆柱形或球形储罐,包括罐壁、罐盖、进气口、排出口、抽气口和检查孔等部分,有一定的环保和安全措施。
甲醇的储存需要安全性强且环保的设施,以免对人体和环境造成危害。
4. 废气回收设备甲醇合成过程会产生大量的废气,包括一氧化碳、二氧化碳、甲烷、氢气等物质。
因此,甲醇生产场地需要配置废气回收设备,用于收集和处理废气,减少对环境的污染和腐蚀。
甲醇合成装置工艺说明

甲醇合成装置工艺说明目录1 概述2 技术概况3 工艺技术方案选择4 工艺流程简述5 物料平衡6 消耗7 主要操作条件8 主要设备选型9 技术和设备来源10 节能11 三废排放12 装置占地13 定员1 概述甲醇合成装置将来自低温甲醇洗的净化气转化为粗甲醇。
拟采用德国Lurgi低压甲醇合成技术。
粗甲醇送往甲醇精馏装置,弛放气去氢回收装置,闪蒸气去燃料气管网。
甲醇合成装置处理能力为507344Nm3/h净化气,甲醇产量为230吨/小时(以100%甲醇计)。
2技术概况甲醇工业化始于20世纪初,1923年德国BASF公司首先建立了一套采用Zn-Cr催化剂、合成压力为30.0MPa、规模为300吨/年的高压法甲醇生产装置。
20世纪60年代,甲醇工业随着选择性好、低温活性高的铜基催化剂开发成功而取得重大进展。
1966年英国ICI 公司研制成功Cu-Zn-Al催化剂后,推出ICI低压甲醇合成工艺,在所属Billingham工厂建立了工业化装置。
1971年德国Lurgi公司成功开发出采用活性更高的Cu-Zn-Al-V催化剂的另一著名低压法工艺-Lurgi工艺。
此后,世界各大公司竞相开发了各具特色的低压法工艺技术。
与高压法工艺相比,低压法工艺在投资和综合技术经济指标方面都具有显著优势。
以天然气为原料的甲醇厂,高压法能耗达64.8GJ/t甲醇,而大型低压法装置为29.5~31.5GJ/t 甲醇。
1970年代后国外新建的大中型甲醇装置全部采用低压法,高压法渐趋淘汰。
高、低压法甲醇生产主要操作条件如下:随着1997年德国Lurgi公司大甲醇(MegaMethanol)概念的提出,甲醇技术逐渐向大型化发展,Lurgi,Davy,Topsoe等公司相继提出大甲醇技术,各种甲醇合成技术,主要体现在甲醇合成反应器的设计上。
2.1 Lurgi甲醇反应器传统的Lurgi甲醇反应器为列管等温反应器,其结构形式与管壳式换热器非常类似,列管内装填催化剂,管间为沸腾水。
甲醇合成的主要设备
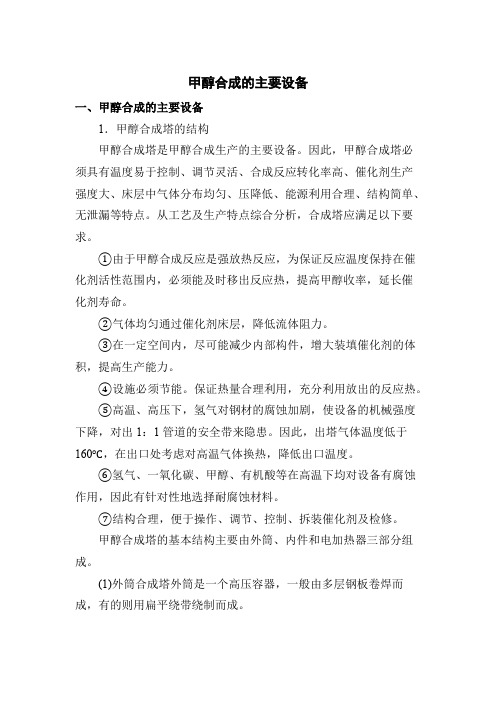
甲醇合成的主要设备一、甲醇合成的主要设备1.甲醇合成塔的结构甲醇合成塔是甲醇合成生产的主要设备。
因此,甲醇合成塔必须具有温度易于控制、调节灵活、合成反应转化率高、催化剂生产强度大、床层中气体分布均匀、压降低、能源利用合理、结构简单、无泄漏等特点。
从工艺及生产特点综合分析,合成塔应满足以下要求。
①由于甲醇合成反应是强放热反应,为保证反应温度保持在催化剂活性范围内,必须能及时移出反应热,提高甲醇收率,延长催化剂寿命。
②气体均匀通过催化剂床层,降低流体阻力。
③在一定空间内,尽可能减少内部构件,增大装填催化剂的体积,提高生产能力。
④设施必须节能。
保证热量合理利用,充分利用放出的反应热。
⑤高温、高压下,氢气对钢材的腐蚀加剧,使设备的机械强度下降,对出1:1管道的安全带来隐患。
因此,出塔气体温度低于160℃,在出口处考虑对高温气体换热,降低出口温度。
⑥氢气、一氧化碳、甲醇、有机酸等在高温下均对设备有腐蚀作用,因此有针对性地选择耐腐蚀材料。
⑦结构合理,便于操作、调节、控制、拆装催化剂及检修。
甲醇合成塔的基本结构主要由外筒、内件和电加热器三部分组成。
(1)外筒合成塔外筒是一个高压容器,一般由多层钢板卷焊而成,有的则用扁平绕带绕制而成。
(2)内件内件由催化剂筐和换热器两部分组成。
催化剂筐是填装催化剂进行合成反应的组合件。
换热器分两类,一是为满足开车时催化剂活性温度,对原料气进行加热的需要,可采用电加热器;二是对进出催化剂床层的反应气体进行热交换,以达到工艺生产要求。
①催化剂筐。
甲醇合成塔内件的设计主要是催化剂筐的设计,它的形式与结构需尽可能实现催化剂床层内最佳温度分布,一般连续冷管有自热式和外冷式两种结构。
自热式是利用反应热,用冷原料气为冷却剂,使催化剂床层降温,原料气体同时被加热。
自热式又分为单管逆流、双套管并流、三套管并流、单管并流以及U形管式。
外冷式是冷却剂采用其他介质进行冷却。
②换热器。
换热器的作用是回收合成气反应后的热量及提高冷原料气的温度。
甲醇合成的工艺流程和设备

甲醇合成的工艺流程和设备甲醇是一种重要的化工原料,广泛应用于化工、医药、食品等领域。
甲醇的合成工艺流程主要包括天然气制甲醇和煤制甲醇两种。
以下将以天然气制甲醇为例,介绍甲醇的合成工艺流程和设备。
1. 甲醇合成工艺流程甲醇的合成主要通过气相合成法进行,该方法通过一系列复杂的催化反应将一氧化碳和氢气合成甲醇。
具体的工艺流程如下:- 天然气→天然气净化→变化转换反应→合成气→合成气净化→合成气改质→甲醇合成→甲醇回收2. 甲醇合成设备甲醇合成设备主要包括催化反应器、冷凝器、分离塔等:- 催化反应器:将一氧化碳和氢气催化反应生成甲醇,需要具有较高的反应活性和选择性。
- 冷凝器:用于冷却和凝结合成气中的甲醇,使其形成液体甲醇。
- 分离塔:用于将液体甲醇从残余的气相中分离出来,保证甲醇的纯度和回收率。
3. 甲醇生产过程甲醇生产过程主要包括天然气的催化转变、合成气的制备、甲醇的合成和甲醇的回收等环节。
整个过程需要耗费大量的热能和电能,因此需要具备较为完备的能源设施和配套设备。
总的来说,甲醇的合成工艺流程较为复杂,需要涉及多个催化反应和分离过程,所需要的设备也比较繁杂。
企业在进行甲醇合成生产时,需要充分考虑到工艺流程和设备配置,确保生产过程的高效稳定。
甲醇是一种重要的化学品,其合成工艺的复杂性和对能源的依赖性使得甲醇工业在全球范围内备受关注。
天然气制甲醇是目前全球最为主流的甲醇生产工艺。
下面将详细介绍甲醇的合成工艺流程和设备,以及在甲醇生产过程中可能出现的关键技术和挑战。
4. 甲醇合成过程甲醇的合成工艺主要涉及以下几个过程:4.1 天然气制备合成气首先,天然气需要在天然气净化设备中进行净化处理,去除其中的硫化氢、二氧化碳和水等杂质。
通过石灰石和干燥剂的吸附、脱硫等处理,可使天然气达到合成气制备的要求。
然后,经催化转化反应,天然气中的甲烷和水蒸气进行高温反应,生成一氧化碳和氢气,形成合成气。
4.2 合成气的制备合成气是由一氧化碳和氢气所组成的气体混合物,它是甲醇合成的重要中间产物。
煤制甲醇设备一览表

煤制甲醇设备一览表一、引言煤是我国主要的能源资源之一,而甲醇作为一种重要的化工原料和清洁燃料,对于能源结构调整和环境保护具有重要意义。
煤制甲醇是将煤转化为甲醇的工艺过程,其关键在于煤制甲醇设备的选用和优化。
二、煤制甲醇设备一览表以下是煤制甲醇常用的设备一览表:1. 煤气化设备煤气化是将煤转化为合成气的过程,合成气中主要成分为一氧化碳和氢气,是煤制甲醇的原料。
常用的煤气化设备有固定床煤气化炉、流化床煤气化炉和煤浆气化炉等。
2. 合成气净化设备合成气中含有一定的杂质,需要进行净化处理。
常用的合成气净化设备有除尘器、除硫器、除氮器等。
3. 合成气变换设备合成气变换是将一氧化碳和氢气转化为甲醇的过程。
常用的合成气变换设备有催化剂床、换热器、压力容器等。
4. 甲醇分离设备甲醇分离是将合成气中的甲醇从其他组分中分离出来的过程。
常用的甲醇分离设备有精馏塔、吸收塔、萃取塔等。
5. 废气处理设备煤制甲醇过程中会产生一些废气,包括煤气化废气、合成气净化废气和甲醇生产废气等。
这些废气中含有一些有害物质,需要进行处理和净化。
常用的废气处理设备有除尘器、脱硫装置、脱氮装置等。
6. 热力设备煤制甲醇过程中需要进行能量转化和供应,因此需要热力设备。
常用的热力设备有锅炉、热交换器、蒸汽发生器等。
7. 辅助设备除了上述主要设备外,煤制甲醇还需要一些辅助设备来保障生产运行的顺利进行,如压缩机、泵站、储存设备等。
三、煤制甲醇设备选型和优化在煤制甲醇项目中,设备的选型和优化是至关重要的一环。
选用合适的设备可以提高生产效率、降低能耗、增加产品质量和降低环境污染。
优化设备结构和工艺参数可以进一步提高设备的性能和经济效益。
1. 设备选型设备选型需要考虑煤的性质、产量要求、工艺流程以及经济效益等因素。
不同类型的煤制甲醇工艺可能需要不同的设备选型,如煤气化方式的选择会影响煤气化设备的选用,而甲醇生产工艺的选择会影响合成气变换和甲醇分离设备的选用。
甲醇装置电气系统基本知识介绍
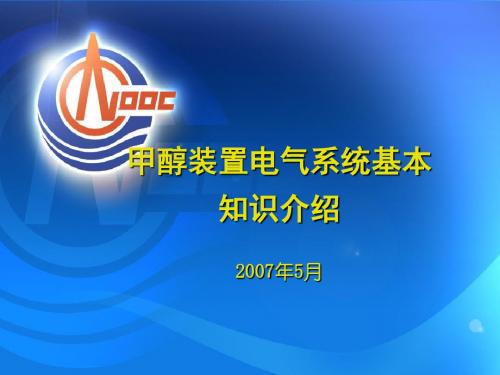
过75℃。
油浸变压器的绝缘等级为 A级,考虑到最高环境为40℃,则极限 工作温度为40+65=105℃。标准规定绕组连续维持在95℃时,可以
2019/2/8 11
保证变压器具有经济合理的使用寿命。根据相关标准规定变压器在 额定负荷时各部分充许温升,当周围最高温度为 40℃时,规定上层
油温温升为 55℃,通常要求变压器上层油温的温升不要长期超过超
2019/2/8 8
第二讲:电气系统的基本要素 一、概述
在工厂企业中,电力是现代化生产的主要动力。由于电能具有传 输迅速、变换方便、使用简单和便于远距离控制和测量等特点,因 此它的广泛应用,为实现生产自动化提供了良好条件。
在工厂中变配电所的作用是接受电能、变换电压和分配电能,而 配电所作用只是接受电能和分配电能。两者的区别主要在于变电所 安装有变换电压作用的电力变压器。所以在工厂企业中,根据容量 的大小、引入电压的高低,变、配电所可分为一次降压变电所、二 次降压变电所和配电所三种类型。 工厂变配电所的主要电气设备,包括电力变压器、高低压电器设 备、互感器、移相电容器、配电装置、电气测量仪表和继电保装置 等。这些电气设备构成了电气系统的基本要素。
2019/2/8 3
各类负荷对供电要求: (1)一级负荷:必须由保安电源供电(应急电源),直流保安负荷 由蓄电池供电。对于交流保安负荷凡用快速启动(一般不超过 15 秒 )柴油发电机可以满足要求者可以用其供电。不能满足要求者则需 要由不间断电源装置供电。
在化工企业中通常采用几种类型ห้องสมุดไป่ตู้安电源,通过相互配合满足工 艺装置要求。
2019/2/8 15
l
l
检查变压器器身有无渗漏油现象。 检查变压器上层油温。
甲醇装置简介

本工程的工艺装置包括:GE水煤浆气化、变换及热回收、低温甲醇洗、CO深冷分离及CO压缩、甲醇合成及压缩、甲醇精馏、甲醇中间罐区、硫回收、冷冻。
煤气化以神华化工煤为原料,采用三台直径3.2米气化炉,气化压力6.5MPa,两开一备,为保证装置年操作8000小时,渣水闪蒸系统设3套,与气化炉配套两开一备。
变换采用耐硫变换工艺,酸性气脱除装置采用低温甲醇洗脱硫脱碳工艺,生产甲醇的水煤气经CO部分变换后送低温甲醇洗净化装置,脱除了H2S和CO2后的合格的合成气送入甲醇合成装置。
甲醇合成装置采用国际上先进的甲醇合成技术,甲醇合成系统压力8.2MPa。
甲醇精馏采用节能型三塔精馏。
精馏塔采用规整填料塔。
甲醇通过新建的甲醇装置经中间罐区以管道输送至老醋酸装置罐区。
罐区有2个2000m3的精甲醇贮罐与2个2000m3的粗甲醇贮罐。
一氧化碳深冷分离装置采用Linde公司技术,分离出合格的一氧化碳送出界区,供醋酸装置使用。
分离出的富氢气返回与甲醇净化原料气混合,送甲醇合成装置。
制冷采用氨压缩制冷工艺。
硫回收装置采用三级克劳斯硫回收工艺。
回收酸性气中的硫,硫回收尾气经焚烧炉焚烧后送热电锅炉燃烧后去烟囱高空排放,以确保满足环保的要求。
中海石油天野化工20万吨甲醇装置简介

18
四、重要设备~中间罐区
中间罐区属公司一级重大危险源,共有四个贮罐,包括两个精醇 罐和两个粗醇缸,单个精醇罐容积为402立方米,单个粗醇罐容积为 866立方米。其作用有两个,一是临时储存甲醇合成生产的粗甲醇; 接受、储存、计量甲醇精馏工序生产的精甲醇,经检验合格后用泵送 往成品罐区中储存。
19
氧化锌脱硫是通过化学吸附来脱硫的,可以脱除无机硫,其化学 反应方程如下: H2S+ZnO→ZnS+H2O
氧化锌和硫化氢即使在常温下也可以反应生成性质稳定的硫化锌。
反应生成的硫化锌不能再生,因此氧化锌脱硫剂在使用一段时间后,随
着氧化锌含量的降低,硫化锌含量的升高,脱硫效果下降,氧化锌脱硫
剂需要定期更换
3
3
一、甲醇装置的原料及产品简介
天然气
序号 1 2 3 4 5 6
分析项目 CH4 C2H6 CO2 总硫
低位热能 温度
单位
实测值
设计值
mol% mol%
94-97 0.580-1.100
95.949 0.908
mol%
≤3.0
3.0
mg/Nm3
≤20
20
kJ/NM3 0C
33800-35800 环境温度
35058 25
4
4
一、甲醇装置的原料及产品简介
GB338-1992中华人民共和国国家标准工业甲醇产品质量标准
项目
指标
优等品
一级品
色度(钴-钼)
≤Leabharlann 5密度(200C)
g/cm3 0.791~0.792 0.791~0.793
温度范围(0.1MPa)
≤0C
64.0~65.5
甲醇装置教材(第三版)1

第八章甲醇装置教材目录第一节概述1.甲醇装置的组成及简介2.甲醇装置的技术简介2.1 甲醇合成技术简介2.2 PSA技术简介2.3 精馏技术简介2.4 甲醇中间罐区技术简介第二节甲醇的生产原理1.甲醇合成反应的物理化学原理1.1 甲醇合成反应的基本化学反应方程式1.2 化学反应的热效应和转化率2.甲醇合成热力学2.1甲醇合成的热力学分析2.2化学反应平衡3.甲醇合成反应动力学甲醇合成反应机理甲醇合成反应动力学影响甲醇合成的工艺因素及工艺条件4.变压吸附(PSA)提纯氢气的原理4.1 PSA技术分离H2的基本原理4.2 PSA装置常用的吸附剂特性5.甲醇精馏的原理第三节催化剂及化学品消耗1.催化剂的作用及要求2.催化剂的种类及性能2.1还原前主要化学组成2.2催化剂的类型2.3催化剂的性能及物理性质3.催化剂的使用3.1催化剂的活化3.2催化剂的使用3.3催化剂的钝化4.吸附剂5.碱液6.危险化学品的物理化学性质第四节工艺流程1.生产方案和装置的物料平衡1.1甲醇生产方案1.2变压吸附提纯氢气生产方案1.3物料平衡2.装置工艺流程描述2.1甲醇合成(5200)2.2 变压吸附(PSA)氢气提纯(5250)2.3 甲醇精馏(5300)2.4 甲醇中间罐区(5400)3.装置的工艺流程图4.主要工艺参数5.装置原材料及公用工程消耗5.1通常甲醇合成单元的操作条件和技术指标:5.2本装置的主要工艺参数:6.主产品和副产品规格6.1甲醇( 中间产品)6.2副产品(侧线抽出)6.3 送往聚丙烯装置的H2产品规格第五节主要生产设备1.本工段主要设备汇总表2.主要设备描述3.主要设备规格表第八章 甲醇装置第一节 概述1. 甲醇装置的组成及简介◆ 甲醇装置位于煤基烯烃项目生产装置区的中心区域,规划占地265mX135m =35775m 2,约合54亩。
◆ 甲醇装置由甲醇合成单元(5200单元)、PSA 氢气提纯单元(5250单元)、甲醇精馏单元(5300单元)和甲醇中间罐区(5400单元),共四个单元组成。
20万吨甲醇装置工艺简介

(1.824亿方天然气/年)。
7
7
序号 1 2 3 4 5 6
分析项目 CH4 C2H6 CO2 总硫
低位热能 温度
天然气
单位
实测值
设计值
mol% mol%
94-97 0.580-1.100
95.949 0.908
mol%
≤3.0
3.0
mg/Nm3
≤20
20
kJ/NM3 0C
33800-35800 环境温度
➢ 反应条件:温度855℃左右,压力2.53MPa,镍催化剂的催化作用下
进行转化反应。
➢ 反应方程如下:
CH4+H2O→CO+3H2 -205.66KJ/mol
CH4+2H2O→CO2+4H2 -164.69kJ/mol 同时发生CO的变换反应
CO+H2O→CO2+H2 +40.7KJ/mol
➢ 转化反应是吸热反应,其反应热由转化管外燃烧的天然气提供。
5
5
改进与提高
2011年以来,由于天然气供应不足停车两个月(2010年12月3日-2011 年2月9日),利用此次机会更换了新的进口触媒,不断的对甲醇工艺进 行思考探索,装置整体消耗出现了大幅度的降低,尤其是2011年7月消耗 创历史最低:1022NM3/T(车间计量987NM3/T )。节能减排相当有效每 月降低天然气用量36万立方米;每月降低大烧用量79.2万立方米;每月 减少排碳量282.85吨由于燃料气量降低,鼓、引风机负荷也降低了,两 台风机电流大约降低3安培。每月节电:17958KWH。 (突破了以前不能多补碳的操作难点)而且工况相当稳定,为深入研究 工况提供了可能。
甲醇装置工艺说明及工厂描述

第四章工艺说明及工厂描述4.1 装置组成本项目由工艺主装置、辅助装置、配套的公用工程、办公及生活设施和辅助工程组成。
其中承包商承担的主要有:4.1.1工艺主装置主要包括以下单元:(1)20000m3焦炉气气柜(2)焦炉气压缩(3)焦炉气粗脱硫和净化;(4)焦炉气二段加氢脱硫;(5)焦炉气纯氧转化及热回收;(6)合成气压缩;(7)甲醇合成;(8)甲醇精馏;(9)空分。
4.1.2辅助装置主要包括:(1)甲醇中间罐区;(2)甲醇成品罐区;(3)甲醇成品装车设施(含火车和汽车)(4)火炬。
4.1.3配套的公用工程主要包括:(1)循环水站(2)除氧水站(3)中央控制室(4)甲醇装置化验室(5)变配电所(6)化学消防和水消防等。
4.1.4 厂外工程(1)10kV四回电源进线;(2)去污水处理场的污水和循环水排水管线;(3)去孟沟的清净废水管线。
4.1.5办公及生活设施主要包括:综合楼(包括中央控制室、中央化验室)、浴室等。
4.1.6辅助工程主要包括:装置内的界区内道路和各种管网,照明、给排水设施,通讯设施,以及大门(门卫)及围墙等。
负责合同装置界区内的绿化。
其余部分由业主承担,例如铁路专用线、厂外管线、污水处理场等。
4.2 工艺描述4.2.1 推荐工艺流程的主要特点(1)空分采用液氧内压缩空气膨胀流程,即采用增压空压机+液氧泵+空气增压透平膨胀机并通过换热器系统的合理组织来取代外压缩流程氧压机。
针对用氧压力高,装置规模大的特点,选择这一流程是最安全可靠的,也经济合理。
(2)焦炉气压缩采用电机驱动的无油螺杆式压缩机对焦炉气进行二级压缩,该压缩机具有对气体的适应性强,能适应焦炉煤气中高焦油、高萘的特点;且没有气阀、活塞环等易损件,结构简单、紧凑,运转可靠,寿命长;还可保持气体的干净无油。
S的脱除效率可以保证在90%以上,同时可以脱除(3)用PDS湿法脱硫,H2部分有机硫、焦油和HCN。
(4)采用氧化铁干法粗脱硫的工艺,流程简单且操作简便,同时也除去了部分焦油。
甲醇生产装置操作 甲醇精制装置认知

主要设备介绍
03
工艺流程介绍工艺流程介绍 源自放视频:甲醇精制工艺流程介绍04
工艺特点
工艺特点
三塔精馏加回收塔工艺流程的主要特点是热能的合理利用。 双效精馏方法:将加压塔塔顶气相的冷凝潜热用作常压塔塔釜再沸器热源。 废热回收:
甲醇精制装置认知
甲醇精制装置认知
甲醇合成
甲醇精制
对粗甲醇进行纯化
目
CONTENTS
录
01 甲醇精制装置简述 02 主要设备介绍 03 工艺流程介绍 04 工艺特点 05 复杂控制说明
01
甲醇精制装置简述
甲醇精制装置简述
甲醇生产仿真软件是根据甘肃某化工厂年产20万吨甲醇项 目开发的。
甲醇精制采用四塔精馏工艺,包括预塔、加压塔、常压塔 及甲醇回收塔。这是甲醇精制的工艺流程图。
甲醇精制装置简述 甲醇精制的工艺流程图
02
主要设备介绍
主要设备介绍
设备
预塔(T701):主要作用除去粗甲醇中溶解 的气体(如CO2、CO、H2等)及低沸点组分 (如二甲醛、甲酸甲酯)
加压塔(T702)、常压塔(T703):精制 过程的主精馏塔,作用是除去水及高沸点杂 质(如异丁基油),同时获得高纯度的优质甲 醇产品。
(1)将转化工段的转化气作为加压塔再器热源 (2)加压塔辅助再沸器、预塔再沸器冷凝水用来预热进料粗甲醇; (3)加压塔塔釜出料与加压塔进料充分换热。
05
复杂控制说明
复杂控制说明
串级回路 的使用
液位与流量串级回路 温度与流量串级回路
在结构上,串级回路调节系统有两个闭合回路。主、副调节器 串联,主调节器的输出为副调节器的给定值,系统通过副调节 器的输出操纵调节阀动作,实现对主参数的定值调节。
化工设备关键装置、重点部位
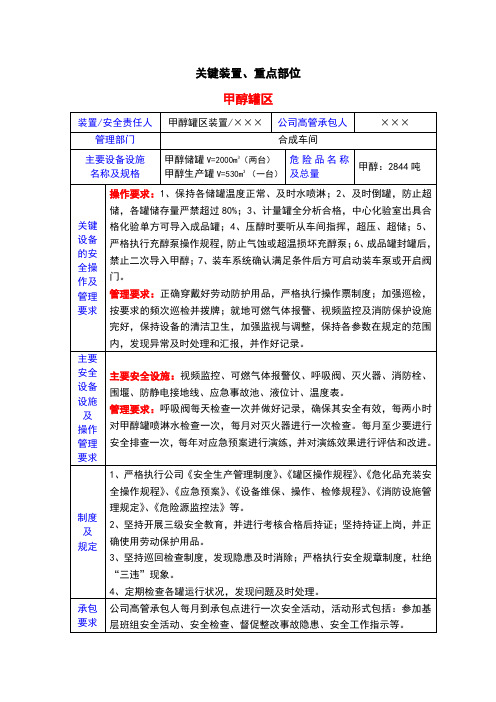
甲醇罐区装置/安全责任人甲醇罐区装置/×××公司高管承包人×××管理部门合成车间主要设备设施名称及规格甲醇储罐V=2000m3(两台)甲醇生产罐V=530m3 (一台)危险品名称及总量甲醇:2844吨关键设备的安全操作及管理要求操作要求:1、保持各储罐温度正常、及时水喷淋;2、及时倒罐,防止超储,各罐储存量严禁超过80%;3、计量罐全分析合格,中心化验室出具合格化验单方可导入成品罐;4、压醇时要听从车间指挥,超压、超储;5、严格执行充醇泵操作规程,防止气蚀或超温损坏充醇泵;6、成品罐封罐后,禁止二次导入甲醇;7、装车系统确认满足条件后方可启动装车泵或开启阀门。
管理要求:正确穿戴好劳动防护用品,严格执行操作票制度;加强巡检,按要求的频次巡检并拨牌;就地可燃气体报警、视频监控及消防保护设施完好,保持设备的清洁卫生,加强监视与调整,保持各参数在规定的范围内,发现异常及时处理和汇报,并作好记录。
主要安全设备设施及操作管理要求主要安全设施:视频监控、可燃气体报警仪、呼吸阀、灭火器、消防栓、围堰、防静电接地线、应急事故池、液位计、温度表。
管理要求:呼吸阀每天检查一次并做好记录,确保其安全有效,每两小时对甲醇罐喷淋水检查一次,每月对灭火器进行一次检查。
每月至少要进行安全排查一次,每年对应急预案进行演练,并对演练效果进行评估和改进。
制度及规定1、严格执行公司《安全生产管理制度》、《罐区操作规程》、《危化品充装安全操作规程》、《应急预案》、《设备维保、操作、检修规程》、《消防设施管理规定》、《危险源监控法》等。
2、坚持开展三级安全教育,并进行考核合格后持证;坚持持证上岗,并正确使用劳动保护用品。
3、坚持巡回检查制度,发现隐患及时消除;严格执行安全规章制度,杜绝“三违”现象。
4、定期检查各罐运行状况,发现问题及时处理。
承包要求公司高管承包人每月到承包点进行一次安全活动,活动形式包括:参加基层班组安全活动、安全检查、督促整改事故隐患、安全工作指示等。
- 1、下载文档前请自行甄别文档内容的完整性,平台不提供额外的编辑、内容补充、找答案等附加服务。
- 2、"仅部分预览"的文档,不可在线预览部分如存在完整性等问题,可反馈申请退款(可完整预览的文档不适用该条件!)。
- 3、如文档侵犯您的权益,请联系客服反馈,我们会尽快为您处理(人工客服工作时间:9:00-18:30)。
( 安全技术 )单位:_________________________姓名:_________________________日期:_________________________精品文档 / Word文档 / 文字可改甲醇装置简介和重点部位及设备(通用版)Technical safety means that the pursuit of technology should also include ensuring that peoplemake mistakes甲醇装置简介和重点部位及设备(通用版)一、装置简介(一)装置发展及类型以一氧化碳和氢为原料合成甲醇的生产技术始于20世纪20年代。
到50年代末,我国已掌握了甲醇和合成甲醇催化剂的制备技术。
60年代未,我国又实现了合成氨和合成甲醇的联合生产(简称联醇),联醇技术降低了合成氨和甲醇的生产成本。
20世纪60年代,世界上,低压法合成甲醇新工艺技术实现了工业化。
低压法由于其能耗低,逐步取代了原来的高压法合成甲醇工艺,并得到了快速发展。
80年代初,我国研制的低压合成甲醇催化剂已达到国际水平。
联醇工艺技术是合成氨生产过程中,利用合成氨原料气中一氧化碳、二氧化碳与氢气同时生产甲醇。
联醇工艺技术由于生产方式灵活、工艺简单、原料利用率高、成本低、效益好,在我国中型合成氨装置得到普遍的推广。
甲醇生产一般以天然气、轻油、重油、煤及某些加工过程中产生的尾气为原料。
制得的原料气通过净化,得到一氧化碳、二氧化碳与氢气,经合成生成甲醇。
典型的流程包括原料气制备、原料气净化、甲醇合成和粗甲醇精馏等工序。
甲醇装置生产工艺所采用的原料气制备与净化工艺,与合成氨装置相同或相类似。
原料气制备工艺类型一般有:煤(焦)固定床气化工艺;煤(焦)气流床气化工艺;渣油、水煤浆部分氧化制气工艺;烃类(轻油、天然气)蒸汽转化制气工艺。
气体净化工艺类型也与合成氨原料气净化工艺类型相同,一般根据原料气的组成不同而采用不同的脱硫、变换、脱碳工艺技术。
甲醇的合成工艺类型主要有高压法和低压两种:前者操作温度300-400℃,操作压力30-50MPa(表);后者操作温度220-250℃,操作压力5.0—8.0MPa(表)。
甲醇合成塔类型:按气体流向分有轴向塔和径向塔;按床层换热方式分有内部换热式、中间换热式和中间冷凝式。
甲醇精馏有常压法和加压法,以及双塔精馏和三塔精馏两种流程。
低压法合成甲醇工艺技术目前发展的方向是:采用活性高、转化率高、选择性好的甲醇合成催化剂;采用温差小、阻力小、反应温度易控制、热能回收率高的均温型合成塔;并不断提高热量利用率和合成气利用率,向低能耗方向发展。
(二)单元组成与工艺流程1.组成单元甲醇生产装置采用的原料种类不同,工艺流程不同,其组成单元也不同。
现介绍以天然气为原料,采用低压合成工艺技术的甲醇生产装置。
装置由硫化物脱除(简称脱硫)、天然气蒸汽转化制气(简称转化)、合成气压缩(简称压缩)、甲醇合成(简称合成)、粗甲醇精馏(简称精馏)5个单元组成。
各单元介绍如下:(1)脱硫天然气与氢气混合进行加氢反应,将天然气中的不饱和烃、有机硫化物转化为饱和烃、硫化氢。
再由氧化锌脱硫剂吸附除去原料中的硫化物。
如天然气中硫含量过高,则在脱硫单元中要增加预脱硫装置。
(2)转化天然气与蒸汽发生转化反应,得到含氢气、一氧化碳、二氧化碳、甲烷等的气体,并回眼热量产生中压蒸汽。
转化反应需要的热量由天然气和合成吹出气燃烧提供。
(3)压缩通过合成气压缩机将工艺气压力提高,补充入甲醇合成循环回路,并提供甲醇合成回路气体循环需要的动力。
(4)合成一氧化碳、二氧化碳与氢气在一定的压力、温度及催化剂存在下反应生成甲醇。
反应后的气体经换热,冷却分离出粗甲醇。
未反应的气体经加压后与新鲜气汇合,换热后回到合成塔。
(5)精馏粗甲醇通过精馏,除去水、不溶气体及杂质,得到精甲醇产品。
2.工艺流程工艺流程说明:工艺原则流程见图7—3(1)脱硫天然气经天然气压缩机升压到2.6MPa(表),与少量氢气混合后,进入转化炉对流段换热器,与烟气换热(开车时经开工加热炉加热),加热到350℃。
再进入加氢反应器,将天然气中少量不饱和烃及有机硫化物转化为饱和烃及硫化氢。
然后进入氧化锌脱硫槽吸附硫化氢,使天然气中硫含量降到<0.2mg/m3,脱硫后的天然气送到转化。
(2)转化脱硫后的气体与水蒸气混合,预热后进入转化炉炉管内,在镍催化剂作用下,进行甲烷与蒸汽转化反应,出口温度达820—860℃左右,出口气体中CH4含量达3%左右。
高温转化气再进入废热锅炉,回收热量,产生中压蒸汽。
转化气通过水加热器、换热器,进一步换热、降温后去压缩。
转化炉设有侧(或顶)壁烧嘴,由天然气和合成吹出气燃烧,提供转化反应需要的热量。
燃烧后的烟气通过废热锅炉及换热器,回收热量,并产生中压蒸汽。
(3)压缩转化来的合成气压力为2.OMPa(表),经合成气压缩机加压到6.5MPa(表),送到甲醇合成系统。
合成压缩机用中压蒸汽透平驱动。
合成气压缩机还有一个循环段,甲醇合成系统来的循环气经循环段升压后,与加压后的合成气混合一起送到甲醇合成系统。
(4)合成合成气压缩机出口合成气与循环气混合后进入热交换器,与合成塔出口高温气换热,温度上升到230℃,经开工加热器(正常生产停用)调节温度后进人合成塔。
反应后的循环气通过热交换器,温度降到90℃,经水冷器冷却到40℃,进人粗甲醇分离器,粗甲醇与循环气分离,分离后的循环气去循环段入口。
粗甲醇进入闪蒸槽,减压分离出气体后,送至粗甲醇储槽。
甲醇合成塔为管式合成塔,管内充填甲醇合成催化剂,合成反应产生的大量热量通过管间锅炉水蒸发,产生蒸汽回收。
为了排除合成回路中惰气,从循环段人口引出部分气体作为吹出气。
吹出气进入甲醇回收塔用水洗涤,回收粗甲醇后,送到转化炉作燃料。
吹出气也可送到其他装置,综合利用。
(5)精馏从粗甲醇槽来的粗甲醇换热后,进入轻馏分塔,塔底再沸器用蒸汽加热,进行蒸馏。
绝大部分轻组分杂质和一部分甲醇自塔顶蒸馏出来。
经冷凝后,大部分回流入轻馏分塔顶部,少部分排到杂醇油储槽,不冷凝气体放空。
塔底粗甲醇,由给料泵送到重馏分塔,进行蒸馏。
重馏分塔塔底再沸器用蒸汽加热,进行蒸馏。
塔顶甲醇蒸汽,经冷凝后,回流人塔顶部。
产品甲醇从塔上部塔板采出,经冷却后送到甲醇储槽。
从塔下部塔板处采出杂醇油,经冷却后排至杂醇油储槽。
塔底的废水经换热后,排至污水处理场。
以天然气为原料制得的合成气,气体中H2/CO+C02比例较高。
如有可供利用的二氧化碳气源,适当补充人合成气中后,可提高气体利用率,提高产量,降低消耗。
(三)化学反应过程1.脱硫烯烃、硫化物加氢反应如下:2.转化天然气与蒸汽转化反应如下:3,合成甲醇合成反应如下:(四)主要操作条件及工艺技术特点:1.主要操作条件因采用的原料、催化剂、设备不同,工艺操作条件不尽相同,表7—38列出主要操条件的范围。
2.工艺技术特点采用天然气蒸汽一段转化制气工艺技术,烟气及转化气的热量通过废热锅炉产生中压蒸汽回收。
脱硫采用加氢转化,氧化锌吸附脱硫技术,流程短。
合成采用低压甲醇合成工艺技术,压力低,动力消耗低。
催化剂采用高活性铜基催侣剂,其转化率高,对一氧化碳与二氧化碳比例要求不严,副反应少。
合成塔采用管式均温合成塔,该塔工艺控制简单、热量回收利用率高。
催化剂床层径向温差仅6—8℃,轴向几乎无温差,床层温度控制准确、均匀、稳定。
但合成塔结构复杂,装卸催化剂不太方便。
精馏采用常压双塔精馏流程,流程短,产品质量高。
(五)催化剂甲醇装置采用了加氢催化剂、硫吸收剂、转化催化剂、甲醇合成催化剂共四种。
催化剂由于型号、生产配方不同,其性能特性也不同。
催化剂一般组成见表7—39。
(六)原料及产品特性1.原材料特性原料为天然气(或适当补充二氧化碳气体),燃料为天然气(或加人吹出气)。
主要化学材料有氢氧化钠。
其安全特性见表7—40。
2.产品性质产品为甲醇,生产过程中还存在氢气、硫化氢、一氧化碳等中间产物。
其安全性质见表7—41。
二、重点部位及设备(一)重点部位1.转化系统转化系统由转化炉、废热锅炉以及燃料燃烧、烟气废热回收设备组成。
高温设备集中,转化炉炉膛温度高达1300℃,炉出口温度820℃,废热锅炉产生3.8MPa(表)中压蒸汽。
设备内工艺气体为CH4 、H2、CO、C02等,压力达2.6MPa(表)。
转化系统是装置中的高温区,其特点是高温、中压、易燃、易爆、有毒。
若设备发生超温,易造成设备损坏,工艺气体泄漏,而引发重大火灾、爆炸事故。
2.合成系统合成系统由合成塔、中压蒸汽汽包、热交换器、水冷器、粗甲醇分离器等压力设备组成。
设备内压力为6.2MPa(表)左右.设备内工艺介质为氢气、一氧化碳、二氧化碳、甲醇、甲烷等易燃、易爆、有毒气体。
由于压力高,设备发生泄漏,易造成火灾、中毒、爆炸事故。
如设备存在缺陷、超压、腐蚀等,在发生物理性爆炸时,还可发生化学爆炸,往往造成灾难性的后果。
(二)重点设备1.转化炉转化炉承担着将天然气与蒸汽发生反应制取原料气的任务。
其操作、运行是否正常影响到整个装置的安全运行,是装置中结构复杂,操作条件苛刻的关键设备。
转化炉由辐射段、对流段及燃料系统组成。
辐射段一般有上百根转化炉管,炉管内装填催化剂,天然气与水蒸气在炉管内反应。
炉管外用天然气燃烧形成的火焰直接加热,炉管外壁温度高达900—950℃,炉管内压力为2.6MPa(表),运行条件比较苛刻。
烟气进烟气废热锅炉,回收热量。
转化炉在生产中,如发生催化剂中毒、结碳,水碳比失调,燃料系统故障、炉管超温等都可造成事故。
如发生设备损坏、泄漏还可引发重大火灾、爆炸事故。
2.压缩透平机组甲醇装置有天然气压缩机和合成气压缩机两大机组,采用离心式多级压缩机组,用蒸汽透平驱动。
天然气压缩机压缩气体为天然气,出口压力约2.7MPa(表)。
合成气压缩机压缩气体为氢气、一氧化碳、二氧化碳、甲烷等,出口压力约6.5MPa(表),转速可达13000r /min。
大机组一般在高温、高压、高转速下运行,密封、润滑条件要求高,调节控制系统复杂。
运行中如发生喘振、气体带液、轴瓦磨损、密封损坏,轴位移高等都可造成机组故障o由于结构复杂,维护保养,检修安装要求高。
维护不当,检修安装未达到精度标准,也容易发生设备故障。
而两大机组均为单系列运行,无备用机组,任何一台机组的停机,都可造成全装置停车。
而且泄漏出来的氢气、一氧化碳、甲烷,天然气还可造成重大的火灾、爆炸、中毒事故。
3.合成塔合成塔是装置的主要设备,氢气与一氧化碳、二氧化碳在合成塔内反应生成甲醇。
工作压力6.2-6.5MPa(表),反应温度200-250℃。
管式合成塔管内充填合成催化剂,管间为强制循环的锅炉水,吸收合成反应热,产生3.7~4.1MPa(表)的中压蒸汽。