基于的汽车排气系统加速耐久试验载荷谱的研究
汽车冷却系统频域加速耐久试验方法研究
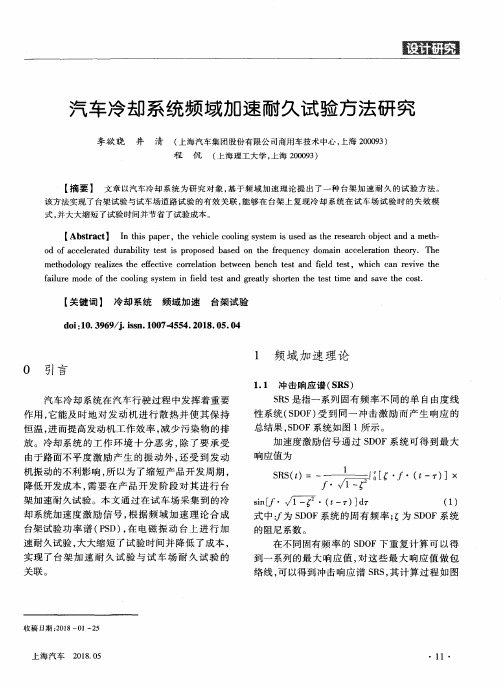
Bendat与 Rice提 lI_r ·种 山:接 }{1应 力 PSI)
该台 试验 PSD 址 · 『J}J的 ,否 则将 会 导 致 不能 复现 '}式年场 ] 或 ‘』Jl1述 过度
2 冷 却 系统 台架 加速 试 验
冷却 系统 傲 定
I , 以将 它 与车 架
胥做 一个整 体 ,符 s1)()F系统 的似设 条 件 。根据
I 述 频域 JJl】速 理论 结 合 录 到 的试 4==场 各 T
试验载 荷谱 总损 伤 试 车 场每 ·个 ‘I 况所 采
集 刮的载 荷谱 都会 对应 一 个 FDS 按 照 整 4 耐 久
试验 舰范 对 试车 场 各 FDS进 行 稳 加 ,可 以得
划 个总 的 FDS,总 的 FI)S包 含 了 存 试 车 场 进 行
一 个完整 的耐 久试验 规 范所 采 集 到载 荷 谱 的总 损
【关键词】 冷却系统 频域加速 台架试验
doi:10.3969/j.issn.1007-4554.2018.05.04
0 引 言
汽 车冷 却 系统 在 汽 车行 驶 过程 中发挥 着 重要 作 用 ,它能 及 时 地 对 发 动 机 进 行 散 热 并 使 其 保 持 恒 温 ,进 而 提高 发动 机 工 作效 率 ,减 少 污 染 物 的排 放 。冷 却 系统 的 工 作 环 境 十 分 恶 劣 ,除 了要 承 受 由于路 面不 平 度 激励 产 生 的振 动 外 ,还 受 到 发 动 机振 动 的不 利影 响 ,所 以为 了缩 短 产 品 开发 周 期 , 降低 开 发成 本 ,需 要 在 产 品开 发 阶段 对 其 进 行 台 架加 速 耐久试 验 。本 文 通 过 在试 车 场 采 集 到 的冷 却 系统加 速 度 激 励 信 号 ,根 据 频 域加 速 理 论 合 成 台架 试 验 功 率谱 (PSD),在 电 磁 振 动 台上 进 行 加 速耐 久试 验 ,大 大缩 短 了试 验 时 间并 降低 了成 本 , 实 现 了 台架 加 速 耐久 试 验 与 试 车 场 耐 久 试 验 的 关 联 。
基于GT-Power的汽车排气消声器的试验研究

义 重 大 。 排 气 消 声 器 的 设 计 要 建 立 在 与 发 动 机 耦 合 的 基础 上 , 但 是 由于发 动 机试 验成 本 比较高 , 因此 , 设 计
一
压 缩 比 1 0
缸径/ mm
缸 数及 排 列 直 列 四缸 行 程/ m m
冲程 数 四 冲程 连 杆 长 度 / m m
染源 , 而 国家 对 排 放 的标 准 愈 来 愈 严 格 , 这 使 得 消 声
器 的设计 要求 也越 来越 高 [ 1 - 2 ] 。一 款 设 计 合 理 的 消 声 器
对 提 升 整 车 NVH ( No i s e 、 Vi b r a t i o n、 Ha r s h n e s s ) 品 质 意
拟声源代替发动机 , 连 接 消 声 器进 行试 验 测 试 , 试 验 结果 表 明 , 测试 结果 与 仿 真 结 果基 本 一 致 。验 证 了仿 真软 件 的 可 靠性 ,
为 消声 器开 发提 供 快捷 的途 径 。
关键词 : 排气消声器 插入损 失 G T — P o w e r
能 分 析 以及 整 车 计 算 的 仿 真 环 境 , 所 有模 块 可 以互相 切换 , 集 成 为 一 体 。 GT — P o we r 可 以 提 供 各 种 针 对 汽 车 不 同层 次 的 物理 模 型 , 用户 可 以在 提 供 的模 型 基 础上
基于 G T — P o w e r 的汽车排 气消声器 的试验研究
口 刘一航 口 安
江 苏无 锡
伟
2 1 4 1 2 2
江 南 大 学 机械 工 程 学 院
摘
要: 利用 G T — P o w e r 软件 , 建 立 排 气消 声 器 与 发动 机 耦 合 模 型 , 计 算 得 到 消 声 器 的插 入 损 失 。 开发 一 款 装 置 作 为 模
汽车排气系统振动疲劳特性分析

汽车排气系统振动疲劳特性分析发布时间:2023-03-07T01:19:01.281Z 来源:《中国科技信息》2022年19期10月作者:窦海燕[导读] 排气系统是汽车整体的重要组成,由于不同因素的干扰导致排气系统管壁会出现不同程度的振动疲劳窦海燕安徽江淮汽车集团股份有限公司安徽合肥 230601摘要:排气系统是汽车整体的重要组成,由于不同因素的干扰导致排气系统管壁会出现不同程度的振动疲劳,因此,需要对汽车排气系统振动疲劳特性展开分析。
明确排气系统的基本特征,综合汽车的不同零部件,构建集成系统,同时要考虑到路面激励具有随机性,保证不同惯性力矩的平衡。
根据排气系统动态响应,完成总应力的集中性影响,考虑到振动特性等因素,获取疲劳参数,分析振动与疲劳特性之间的关系。
关键词:汽车;排气系统;振动疲劳特性排气系统在不同因素共同作用的影响下很容易产生裂纹。
排气系统运行过程中受到的较大振动,导致损伤不断叠加,最终排气系统疲劳程度加重一直到失效,而行车环境、舒适度等也会产生恶劣的变化,因此,需要进一步的分析汽车排气系统振动疲劳特性,这样既能够保障排气系统的使用寿命与质量,同时还能够获取更大的经济效益。
1考虑整车影响的排气系统力学模型排气系统与其他结构部分之间的关系具有相互影响相互促进的作用,因此,构建排气系统力学模型对于研究排气系统振动疲劳特性能够起到关键的效果。
通过排气系统力学模型考虑到整车的影响,能够更好地分解与简化排气系统。
排气系统在力学模型构建当中需要进行适当性简化,这样更加方便建模,同时要明确发动机的安全性,由于其铸造当中涉及到的材料等较多,需要一低阶模态的形式完成发动机机体的建设,并且还能够避免受到激励频率的影响。
悬置系统通常使用橡胶材质,模态频率与其他部位相比频率较低,而发动机悬置系统在模态频率的呈现上要明显的低于机体,这时候就能够将发动机机体进行适当的简化,成为刚体。
而由于轮胎能够保障汽车更为平稳的运行,增强乘车的舒适度,因此,轮胎就能够简化成为弹性元件。
汽车排气系统机械性能试验方法研究
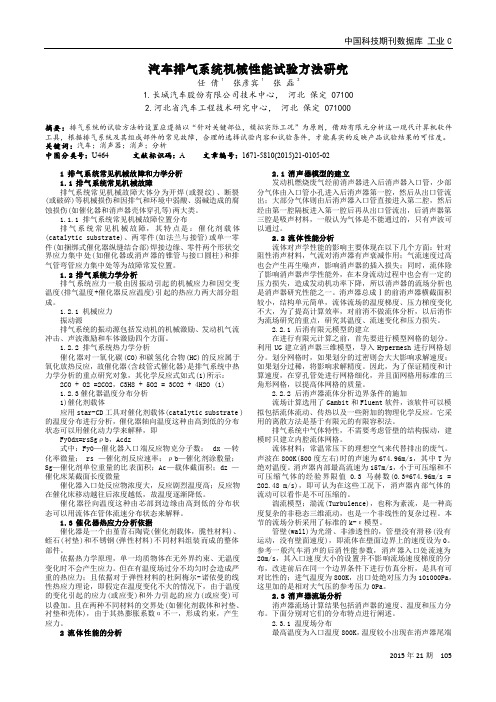
中国科技期刊数据库 工业C2015年21期 105汽车排气系统机械性能试验方法研究任 倩1 张彦宾1 张 磊21.长城汽车股份有限公司技术中心, 河北 保定 071002.河北省汽车工程技术研究中心, 河北 保定 071000摘要:排气系统的试验方法的设置应遵循以“针对关键部位,模拟实际工况”为原则,借助有限元分析这一现代计算机软件工具,根据排气系统及其组成部件的常见故障,合理的选择试验内容和试验条件,才能真实的反映产品试验结果的可信度。
关键词:汽车;消声器;消声;分析 中图分类号:U464 文献标识码:A 文章编号:1671-5810(2015)21-0105-021 排气系统常见机械故障和力学分析1.1 排气系统常见机械故障排气系统常见机械故障大体分为开焊(或裂纹)、断裂(或破碎)等机械损伤和因排气和环境中弱酸、弱碱造成的腐蚀损伤(如催化器和消声器壳体穿孔等)两大类。
1.1.1 排气系统常见机械故障位置分布排气系统常见机械故障,其特点是:催化剂载体(catalytic substrate)、两零件(如法兰与接管)或单一零件(如捆绑式催化器纵缝结合部)焊接边缘、零件两个形状交界应力集中处(如催化器或消声器的锥管与接口圆柱)和排气管弯管应力集中处等为故障常发位置。
1.2 排气系统力学分析排气系统应力一般由因振动引起的机械应力和因交变温度(排气温度+催化器反应温度)引起的热应力两大部分组成。
1.2.1 机械应力 振动源排气系统的振动源包括发动机的机械激励、发动机气流冲击、声波激励和车体激励四个方面。
1.2.2 排气系统热力学分析催化器对一氧化碳(CO)和碳氢化合物(HC)的反应属于氧化放热反应,故催化器(含歧管式催化器)是排气系统中热力学分析的重点研究对象,其化学反应式如式(1)所示:2CO + O2 =2CO2,C3H8 + 5O2 = 3CO2 + 4H2O (1) 1.2.3催化器温度分布分析 1)催化剂载体应用star-CD 工具对催化剂载体(catalytic substrate )的温度分布进行分析,催化器轴向温度这种由高到低的分布状态可以用催化动力学来解释,即Fy0dx=rsSg ρb ,Acdz式中:Fy0—催化器入口端反应物克分子数; dx —转化率微量; rs —催化剂反应速率;ρb —催化剂涂敷量;Sg —催化剂单位重量的比表面积;Ac —载体截面积;dz —催化床某截面长度微量催化器入口处反应物浓度大,反应剧烈温度高;反应物在催化床移动越往后浓度越低,故温度逐渐降低。
基于真实路谱的汽车疲劳寿命开发试验技术
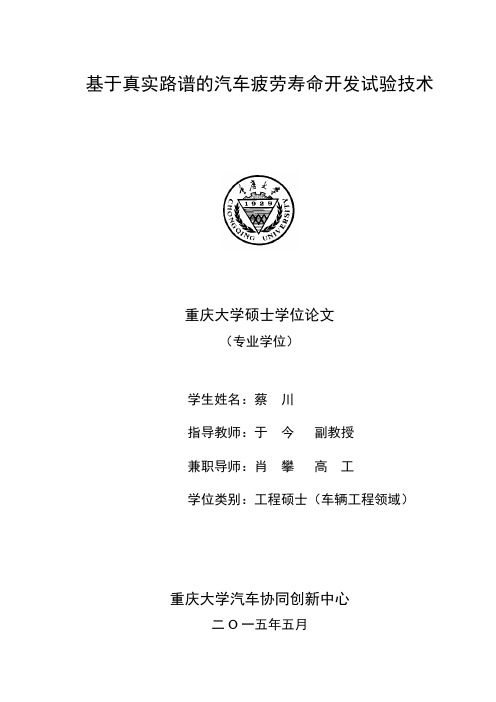
基于真实路谱的汽车疲劳寿命开发试验技术重庆大学硕士学位论文(专业学位)学生姓名:蔡*指导教师:于今副教授兼职导师:肖攀高工学位类别:工程硕士(车辆工程领域)重庆大学汽车协同创新中心二O一五年五月The development of automotive fatigue life test technique based on the real road loadspectrumA Thesis Submitted to Chongqing Universityin Partial Fulfillment of the Requirement forProfessional DegreeByCai ChuanSupervised by Assistant Prof.Yu JinPluralistic Supervised by Senior Eng.Xiao PanSpecialty:ME( Vehicle Engineering Field)Automotive Collabarative Innovation Center ofChongqing University , Chongqing, ChinaMay 2015中文摘要摘要随着人们生活水平的提高,人们对汽车的需求量也越来越大。
与此同时,人们对汽车的品质、性能、外形等各方面提出了更严苛的要求。
对于大多数人来说汽车的使用年限是其关注的重中之重。
这也是各大汽车厂商展示自己产品品质的关键。
汽车的疲劳耐久性设计不仅对汽车的使用寿命有积极的意义,同时也对汽车的安全可靠性有重大的意义。
它是汽车行业所面对的重大课题之一。
因而,各大汽车公司和科研院所积极展开了对汽车结构的疲劳耐久寿命的研究。
通常评估其疲劳寿命采用的方法大致有三种方法:实车道路试验、台架试验以及计算虚拟疲劳试验。
实车道路试验通过在强化路面上连续行驶来验证整车及其零部件的疲劳寿命,它在车辆开发阶段有着重要意义。
基于相对疲劳损伤谱的整车疲劳耐久试验加速方法研究

基于相对疲劳损伤谱的整车疲劳耐久试验加速方法研究李伟;端木琼;赵成刚【摘要】The authors propose a durability test acceleration method based on relative fatigue damage spectrum (RDS). Taking a vehicle as the research object, they acquire the spindle acceleration signal and shock-absorber displacement signal. They take the RDS of structural durability test procedures as a target to optimize the test proce-dure through optimizing algorithm. And under the premise of guaranteeing the RDS consistent, they try to shorten the test cycle as possible.%提出一种基于相对疲劳损伤谱的疲劳耐久试验加速方法。
以某轿车为研究对象,在试验场采集轴头加速度信号和减振器位移信号,以结构耐久性试验程序的相对疲劳损伤谱为目标,通过优化算法对试验程序进行优化,在保证相对疲劳损伤谱一致前提下,最大限度地缩短试验周期。
【期刊名称】《客车技术与研究》【年(卷),期】2016(038)002【总页数】4页(P46-48,55)【关键词】整车疲劳;耐久试验;相对疲劳损伤谱;加速方法【作者】李伟;端木琼;赵成刚【作者单位】中国汽车技术研究中心汽车工程研究院,天津 300300;中国汽车技术研究中心汽车工程研究院,天津 300300;中国汽车技术研究中心汽车工程研究院,天津 300300【正文语种】中文【中图分类】U467.4+97在整车开发流程中,车辆的疲劳耐久性是厂商重点关注的性能指标,直接影响到客户的满意度和车辆的三包成本。
周新_汽车排气系统耐久性分析
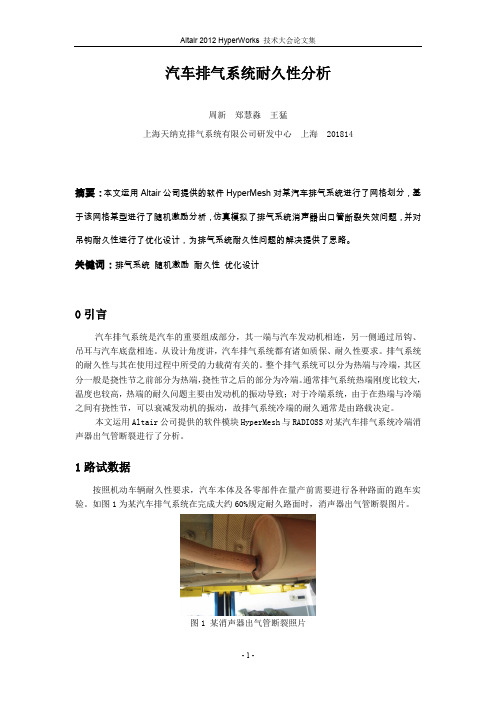
汽车排气系统耐久性分析周新郑慧淼王猛上海天纳克排气系统有限公司研发中心上海 201814摘要:本文运用Altair公司提供的软件HyperMesh对某汽车排气系统进行了网格划分,基于该网格某型进行了随机激励分析,仿真模拟了排气系统消声器出口管断裂失效问题,并对吊钩耐久性进行了优化设计,为排气系统耐久性问题的解决提供了思路。
关键词:排气系统随机激励耐久性优化设计0引言汽车排气系统是汽车的重要组成部分,其一端与汽车发动机相连,另一侧通过吊钩、吊耳与汽车底盘相连。
从设计角度讲,汽车排气系统都有诸如质保、耐久性要求。
排气系统的耐久性与其在使用过程中所受的力载荷有关的。
整个排气系统可以分为热端与冷端,其区分一般是挠性节之前部分为热端,挠性节之后的部分为冷端。
通常排气系统热端刚度比较大,温度也较高,热端的耐久问题主要由发动机的振动导致;对于冷端系统,由于在热端与冷端之间有挠性节,可以衰减发动机的振动,故排气系统冷端的耐久通常是由路载决定。
本文运用Altair公司提供的软件模块HyperMesh与RADIOSS对某汽车排气系统冷端消声器出气管断裂进行了分析。
1路试数据按照机动车辆耐久性要求,汽车本体及各零部件在量产前需要进行各种路面的跑车实验。
如图1为某汽车排气系统在完成大约60%规定耐久路面时,消声器出气管断裂图片。
图1 某消声器出气管断裂照片2有限元分析如图2为某汽车排气系统有限元模型。
该模型由一个挠性节、一个消声器、三个吊钩以及排气管组成。
其中挠性节用弹性单元模拟,消声器壳体及排气管用壳体单元模拟,实芯吊钩用实体单元模拟。
图2 汽车排气系统有限元模型由路试数据知:排气系统发生断裂的位置位于消声器出口端,断裂位置位于挠性节之后,故本计算主要考虑了路载是否是导致其失效的原因。
由于汽车排气系统在路试以及将来使用过程中,任意时刻的路载数据是不确定的,故本计算采集了排气系统在最恶劣路试阶段的一组数据,然后对数据进行了处理,进而对排气系统进行随机响应激励下的分析。
汽车消声器内压耐久性试验系统研制
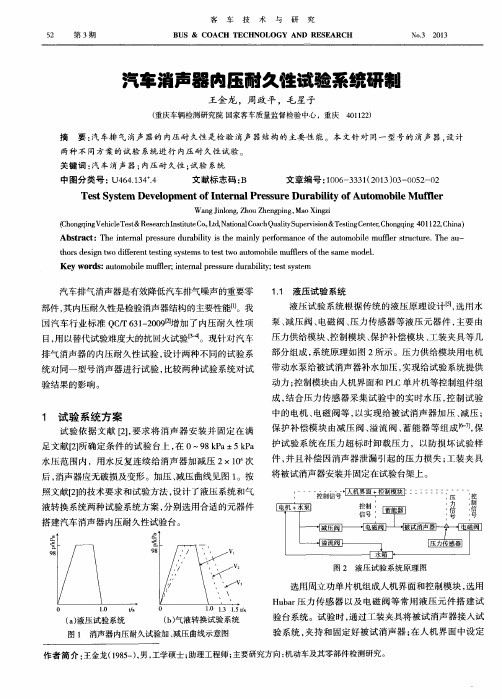
1 . 1 液压试验系统
液 压试验 系统根 据传统 的液 压原理设计[ 5 1 , 选 用水 泵、 减压 阀 、 电磁 阀 、 压力传感器 等液压元器 件 , 主要 由 压力供 给模块 、 控制模块 、 保护补偿模块 、 工装夹具 等几 部分组成 , 系统原理如图 2 所示 。压力供 给模块用 电机 带动水泵给被试 消声 器补水加 压 , 实现给试 验系统 提供 动力 ; 控制模块 由人机界面和 P L C单片机等控制组 件组
中的电机 、 电磁 阀等 , 以实现给被 试消声器加 压 、 减压 ; 保护 补偿模块 由减压 阀 、 溢流阀、 蓄能 器等组 成[ 6 - - 7 ] , 保
护试验 系统在压力 超标时卸载压 力 ,以防损 坏试验样
件, 并 且补偿 因消声器泄漏 引起 的压力损失 ; 工装夹具
将被试消声器安装并 固定在试验台架 上。
液转换 系统两种试验 系统方 案 , 分别选用 合适 的元器件
搭建汽 车消声器 内压耐久性试验台。
图 2 液 压 试 验 系 统原 理 图
选用周立功单 片机组成人机界面和控制模块 , 选用
H u b a r 压 力传感 器 以及 电磁 阀等 常用液压 元件搭 建试
( a ) 液压试验系统 ( b ) 气液转换试验系统
验 台系统。试 验时 , 通过 工装夹具将被试 消声 器接入试
图1 消声器内压耐久试验加 、 减压曲线示意 图
验 系统 , 夹持 和固定 好被试 消声器 ; 在人机 界面 中设 定
作者简介 : 王金龙 ( 1 9 8 5 一 ) , 男, 工学硕士 ; 助理 工程 师; 主要研究方 向: 机动车及其零部件检测研究。
汽车排气系统局部疲劳耐久性试验仿真分析

汽车排气系统局部疲劳耐久性试验仿真分析汽车排气系统是关键的发动机零部件,它负责将废气从发动机中排出。
同时,排气系统庞大的设计,包括排气管、消声器、吸气管等部分。
因此,汽车排气系统表现出良好的疲劳耐久性是必不可少的。
为了保证汽车排气系统的疲劳耐久性,研究人员最近进行了一项试验仿真分析。
在这篇文章中,我们将简要介绍该研究的目的和结果。
研究目的汽车排气系统的疲劳耐久性与排气管、消声器、吸气管等部分有关,这些部分在长时间使用中容易发生疲劳断裂。
因此,研究团队开发了一种试验仿真模型,以模拟汽车排气系统在工作过程中的实际使用情况。
他们的目标是通过分析模型得出新的设计指导方针,以满足汽车排气系统的疲劳耐久性标准。
试验设计研究人员使用有限元方法来模拟汽车排气系统的耐久性。
他们设计了一个模型,包括了汽车的发动机和排气系统,模型使用了500000个单元,每个单元尺寸约为2毫米。
这个模型可以模拟排气系统的疲劳过程,并预测其使用寿命和压力受力情况。
试验流程在试验中,研究人员向模型中输入压力和温度数据,以模拟排气系统在工作时的真实情况。
然后,他们根据不同的载荷条件,通过数值方法计算得到了排气系统在使用过程中的应力和变形情况。
结果分析通过试验,研究者发现最容易发生疲劳断裂的区域集中在排气管与消声器连接点、消声器与吸气管连接点等重要部位。
根据评估,路上反复行驶会再次摩擦并引起底部生锈,钢桶管内腐蚀和外部碰撞等因素也是当前排气系统容易疲劳的主要原因。
研究者还发现,加大零粉和碱性物质对中空铁管表面的腐蚀也会影响其耐久性。
研究者推荐在设计阶段应考虑强度增加的措施来提高汽车排气系统的疲劳耐久性。
本文介绍了一项研究,通过试验仿真分析汽车排气系统在工作过程中的实际情况,研究者运用有限元素方法,通过输入压力和温度数据,以模拟排气系统在工作时的真实情况,最终推荐在设计过程中考虑强度增加的措施,以提高汽车排气系统的疲劳耐久性。
该研究对汽车排气系统的设计和生产具有指导意义,可以指导汽车生产厂家改进其设计和制造工艺,提高汽车的性能和质量。
基于载荷谱的轿车后车身耐久性能分析

基于载荷谱的轿车后车身耐久性能分析柳亮;王峰;史建鹏【摘要】This paper focused on the rear part of the body's durability of the vehicle which developed by the technological center, the multi-body dynamics model was established to calculate the load spectral by extracting suspension attachment forces which measured by the six force measuring instrument. Then the BIW and weld finite element model was established followed. The fatigue analysis software FEMFAT was used to calculate the durability life and the analyzed durability results was marked with the competing vehicle and tests finally. This analysis proposed in this paper provides an effective way of BIW's durability prediction and improvement.%本文以中心开发的乘用车后车身的疲劳耐久特性作为研究对象,截取整车后半部分白车身建立有限元模型,以实测车轮六分力载荷谱经多体动力学仿真分析输出的后悬架安装点激励作为疲劳计算的载荷输入。
在此基础上,通过疲劳仿真分析软件FEMFAT分别对开发车与竞品车后车身疲劳寿命进行了对比分析,并将仿真分析结果与试验结果进行了对标,为该乘用车车身的设计开发及改进提供重要依据。
基于多参数特征保留的载荷谱加速耐久性编辑

(1.中国汽车工程研究院股份有限公司 重庆,401122) (2 重庆市汽车底盘性能工程技术研究中心 重庆,401122)
(3.河北工业大学机械工程学院 天津,300401)
摘要 为了得到时间更短加载效果相 同 的 加 速 耐 久 性 试 验 载 荷 谱,提 出 了 基 于 多 参 数 特 征 保 留 的 载 荷 谱 编 辑 方 法。该方法同时考虑载荷谱的损伤、功率谱密度以 及 统 计 参 数 等 信 息,对 零 部 件 载 荷 谱 的 时 间 进 行 压 缩。 以 汽 车 悬架螺旋弹簧的载荷谱为例,采用该方法进行缩减,同 时 从 多 个 参 数 特 征 方 面 与 传 统 的 基 于 损 伤 保 留 的 编 辑 方 法 所得到的载荷谱进行对比。为了进一步验证编辑 效 果,采 用 编 辑 谱 和 原 始 谱 对 弹 簧 进 行 疲 劳 仿 真。 结 果 表 明,该 方 法 能 够 有 效 缩 短 汽 车 零 部 件 的 载 荷 谱 ,可 得 到 与 原 始 载 荷 谱 具 有 相 同 加 载 效 果 的 编 辑 载 荷 谱 。
笔者提出的频域内兼顾多参数特征保留的载荷 谱 编 辑 方 法 ,同 时 考 虑 载 荷 谱 的 损 伤 、功 率 谱 密 度 以 及统计参数等维度 的 信 息,对 零 部 件 的 载 荷 谱 进 行 压 缩 ,得 到 时 间 更 短 、且 与 原 始 载 荷 谱 相 同 加 载 效 果 的编辑载荷谱。以 汽 车 悬 架 弹 簧 的 载 荷 谱 为 例,通 过采用所提出的编 辑 方 法 进 行 编 辑,同 时 采 用 时 域 方法对弹簧载荷谱 进 行 编 辑,从 多 个 参 数 特 征 对 编 辑前后载荷谱的变化情况进行对比。对汽车悬架弹
* 重庆市自然科学基金面上资助项目(cstc2019jcyj-msxmX0789);国家自然科学基金资助项目(51705128) 收 稿 日 期 :2018-08-16;修 回 日 期 :2019-03-06
某乘用车排气系统动力学研究的开题报告
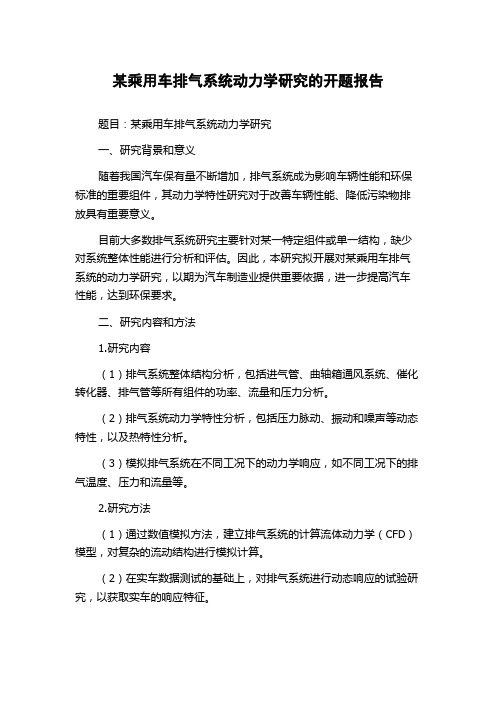
某乘用车排气系统动力学研究的开题报告题目:某乘用车排气系统动力学研究一、研究背景和意义随着我国汽车保有量不断增加,排气系统成为影响车辆性能和环保标准的重要组件,其动力学特性研究对于改善车辆性能、降低污染物排放具有重要意义。
目前大多数排气系统研究主要针对某一特定组件或单一结构,缺少对系统整体性能进行分析和评估。
因此,本研究拟开展对某乘用车排气系统的动力学研究,以期为汽车制造业提供重要依据,进一步提高汽车性能,达到环保要求。
二、研究内容和方法1.研究内容(1)排气系统整体结构分析,包括进气管、曲轴箱通风系统、催化转化器、排气管等所有组件的功率、流量和压力分析。
(2)排气系统动力学特性分析,包括压力脉动、振动和噪声等动态特性,以及热特性分析。
(3)模拟排气系统在不同工况下的动力学响应,如不同工况下的排气温度、压力和流量等。
2.研究方法(1)通过数值模拟方法,建立排气系统的计算流体动力学(CFD)模型,对复杂的流动结构进行模拟计算。
(2)在实车数据测试的基础上,对排气系统进行动态响应的试验研究,以获取实车的响应特征。
(3)应用MATLAB和AVL等软件进行数据处理和分析,对模拟和试验结果进行精准控制和模型验证。
三、预期结果和成果本研究将通过数值模拟和试验研究,深入分析某型号乘用车排气系统的动力学特性,预测排气系统在不同工况下的动力学响应,从而更加深入的了解排气系统性能瓶颈,提出改进建议。
预计取得的研究成果包括:(1)某型号乘用车排气系统CFD模拟分析的有效数据。
(2)排气系统功率、流量和压力分析的数据。
(3)排气系统动力学特性数据,包括压力脉动、振动和噪声等动态特性,以及热特性的分析数据。
(4)提出针对排气系统的改进方案和建议,优化汽车性能和环保标准。
四、研究进度和计划1.研究进度(1)前期工作:综合相关文献,调查不同组件的性能参数。
(2)中期工作:建立排气系统CFD模型,对复杂的流动结构进行模拟计算。
轻型柴油车排气后处理系统耐久性的研究

轻型柴油车排气后处理系统耐久性的研究徐正飞;张卫锋;资新运;何锦勇;杜小东;谭柏春【摘要】在北汽福田轻型柴油车上采用废气再循环+氧化催化器+微粒捕集器的降低柴油车排放技术路线,设计了一种燃油添加剂+起燃器+氧化催化器的微粒捕集器复合再生方案,进行了10万km耐久性试验.分析了微粒捕集器过滤效率变化规律和灰分对过滤体的影响;对比了发动机排放恶化和催化氧化剂老化对一氧化碳和碳氢化合物排放的影响;试验结果表明,催化氧化剂老化会导致排放超标,是系统应用主要难点.%A technology roadmap of EGR + DOC + DPF for reducing diesel vehicle emission is adopted for a light-duty diesel vehicle of Foton. A compound regeneration scheme of FBC + burner + DOC for DPF is devised, and a 100,000 km durability test is conducted. The changing law of the filtration efficiency of DPF and the effects of ash on filter are analyzed and the effects of engine emission deterioration and DOC aging on CO and HC emissions are compared. The results of test show that the aging of DOC can lead to excess emission and is the bottleneck of system application.【期刊名称】《汽车工程》【年(卷),期】2012(034)002【总页数】4页(P116-119)【关键词】微粒捕集器;氧化催化器;耐久性;排放【作者】徐正飞;张卫锋;资新运;何锦勇;杜小东;谭柏春【作者单位】军事交通学院汽车工程系,天津300161;军事交通学院汽车工程系,天津300161;军事交通学院汽车工程系,天津300161;军事交通学院汽车工程系,天津300161;军事交通学院汽车工程系,天津300161;军事交通学院汽车工程系,天津300161【正文语种】中文前言废气再循环(exhaust gas recirculation,EGR)+排气后处理是降低柴油机排放的主要路线之一。
某汽车排气系统的机械疲劳寿命仿真分析
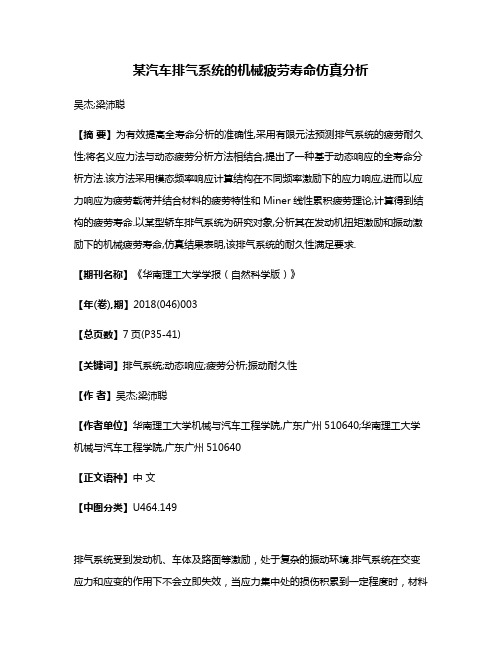
某汽车排气系统的机械疲劳寿命仿真分析吴杰;梁沛聪【摘要】为有效提高全寿命分析的准确性,采用有限元法预测排气系统的疲劳耐久性;将名义应力法与动态疲劳分析方法相结合,提出了一种基于动态响应的全寿命分析方法.该方法采用模态频率响应计算结构在不同频率激励下的应力响应,进而以应力响应为疲劳载荷并结合材料的疲劳特性和Miner线性累积疲劳理论,计算得到结构的疲劳寿命.以某型轿车排气系统为研究对象,分析其在发动机扭矩激励和振动激励下的机械疲劳寿命,仿真结果表明,该排气系统的耐久性满足要求.【期刊名称】《华南理工大学学报(自然科学版)》【年(卷),期】2018(046)003【总页数】7页(P35-41)【关键词】排气系统;动态响应;疲劳分析;振动耐久性【作者】吴杰;梁沛聪【作者单位】华南理工大学机械与汽车工程学院,广东广州510640;华南理工大学机械与汽车工程学院,广东广州510640【正文语种】中文【中图分类】U464.149排气系统受到发动机、车体及路面等激励,处于复杂的振动环境.排气系统在交变应力和应变的作用下不会立即失效,当应力集中处的损伤积累到一定程度时,材料出现疲劳裂纹直至断裂[1].消声器和管路连接处是耐久性分析的重点关注对象[2].为满足耐久性要求,工程上一般采取保守的结构设计并通过实车路试验证.为降低试验成本,有必要在正向开发阶段预测排气系统的疲劳寿命,甄别排气系统的寿命和疲劳损坏易发部位,进而优化结构设计.Meda等[3]分析了排气系统各部件耐久性的影响因素,并提出了相应的优化措施.Patil等[4]以发动机悬置处的加速度谱表征发动机动态激励,针对排气系统应力较大的部位进行了优化以提高耐久性.沈渡等[5]从振动幅值的角度判断发动机激励为主要激励源,采用准静态法计算排气系统在扭矩激励下的疲劳寿命.基于准静态法,文献[6- 7]通过数值计算模拟疲劳试验,优选消声器和挂钩设计方案.Zhang等[8]运用瞬态疲劳分析方法对比钢、铝两种材料的摩托车车架在同一路面激励下的寿命.赵天孟[9]综合考虑动态应力、热应力和应力集中,建立了排气系统的振动疲劳裂纹扩展模型.从现有文献来看,在排气系统总成、消声器分总成和挂钩等组件的疲劳寿命计算中,均将静力作用下的应力结果作为疲劳载荷,通过叠加单位正弦波得到疲劳应力循环.文中以某轿车排气系统为研究对象,通过自由模态试验修正有限元模型后,对排气系统的有限元模型施加动态正弦激励;基于频率响应分析方法提取排气系统总成各点的名义应力,并导入Fatigue疲劳分析软件,采用名义应力法分析两种激励源下的寿命及易损部位.1 排气系统的有限元模型及精度验证1.1 排气系统的有限元模型采用HyperMesh软件,以壳单元为主划分网格,壳体间使用VOLVO法建立焊缝单元[10],焊缝用4节点四边形或3节点三角形壳单元离散,单元厚度为等效焊喉厚度,单元法线指向焊缝外部.动力总成简化为质心质量单元,输入各项惯性参数.动力总成为三点支承,根据各悬置位置与角度建立弹簧阻尼单元.由于悬置间距远大于其尺寸,故只需输入悬置的各向平动刚度,粘性阻尼比为0.05.采用RIGID刚性单元,将发动机质心与各弹簧阻尼单元、球形法兰相连.排气系统的有限元模型如图1所示,含有65 791个节点,66 373个单元.图1 排气系统的有限元模型Fig.1 Finite element model of the exhaust system 1.2 有限元模型的精度验证对排气系统进行自由模态分析,以振型一致为原则,各阶模态频率的计算与测试结果对比见表1.表1 自由模态频率的计算值与试验值对比Table 1 Comparison of free modal frequencies between the computational and the experimental values阶次频率/Hz试验值计算值绝对误差/Hz相对误差/%114.3213.580.745.17216.5515.560.995.98328.7827.291.495.18439.4540.400.952.41556.4155.740.671.19669.8368.960.871.25780.7980.620.170.218121.35116.305.054.169151.78138.4013.388.8210168.77165.203.572.1211195.6 9196.901.210.61模态测试的置信因子MAC矩阵的非对角线元素最大为11.58%,小于工程要求的20%,说明自由模态试验有效且较为准确.表1中主要阶次(1~7阶)模态的计算绝对误差小于1.5 Hz,相对误差小于6%,模型精度满足工程实际要求.2 基于动态响应的全寿命分析2.1 全寿命分析常用的疲劳分析有全寿命分析、裂纹萌生分析和裂纹扩展分析.全寿命分析适用于高周疲劳问题,疲劳循环应力小于材料拉伸弹性极限、循环次数大于105.裂纹萌生分析和裂纹扩展分析适用于服役期间经历高应力、低循环(循环次数小于105)的疲劳问题[1],如计算发电站电机轴的使用寿命.全寿命分析采用名义应力法,对照材料的应力-寿命(S-N)曲线,结合疲劳累积损伤理论估算疲劳寿命,又称S-N法.排气系统的失效循环次数高,危险部位的名义应力在材料的弹性范围内,且材料为各向同性不锈钢材,所受载荷可近似为恒幅载荷且系统疲劳破坏是渐进、累积的过程,适宜进行全寿命分析,并可采用Miner法则[11](1)式中,N为总寿命,D为损伤和,Ni为材料各名义应力下的疲劳寿命,ni为材料各名义应力下的循环次数,l为变幅载荷应力水平级数.当D达到临界损伤和Df时,结构发生疲劳破坏.多数S-N曲线描述了应力循环特性r=-1下通过对试样施加对称循环载荷所获取材料疲劳极限与应力循环次数的关系.非对称载荷作用下的响应应力不能作为疲劳极限求取疲劳寿命.工程中通过平均应力修正来估算r不等于-1时的疲劳极限.循环特性r为(2)式中,σm为循环应力的平均应力,σa为循环应力的应力幅.高周疲劳循环预测常用Goodman直线模型对应力响应结果进行修正,其定义为(3)式中,σe为疲劳极限,σu为极限强度.2.2 准静态、动态应力计算对比分析以图2的单自由度无阻尼系统为例,计算准静态和动态应力结果并进行对比分析.图中,k为弹簧刚度,m为刚体质量.若载荷p(t)=p0sin(ωt)以准静态方式施加于系统,根据牛顿第二定律,建立运动微分方程:kx=p0sin(ωt)(4)图2 单自由度无阻尼系统Fig.2 An undamped single-degree-of-freedom system在t0时刻,易得xS=p0sin(ωt0)/k(5)σS=p0sin(ωt0)/S(6)若载荷p(t)=p0sin(ωt)以动态方式施加于系统,根据牛顿第二定律,建立运动微分方程:(7)两边同时作傅里叶变换,得-ω2mXO(jω)+kXO(jω)=p0XI(jω)(8)在t0时刻,易得(9)(10)式中:=ω/ωn,ωn为固有频率;xS、xD、σS、σD分别为系统在静态和动态激励下的位移、应力;XI(jω)、XO(jω)分别为激励和响应的傅里叶变换;S为质量块的底面积.仅当ω≪ωn时,≈0,此时σD≈σS,准静态应力近似为动态应力.工程上认为激励频率小于系统最低阶固有频率的1/10时,采用准静态有限元法分析能在满足工程预测精度的要求下提高计算效率.如文献[7]中,激励频率为10 Hz,远低于挂钩的一阶约束模态频率260 Hz,准静态仿真结果与实验结果一致性较好.当ω不满足ω≪ωn时,σD≠σS.如当ω=ωn时,=1,结构发生共振,σD≫σS,此时宜采用动态有限元法求解,虽然求解速度较准静态有限元法有所下降,但能有效提高全寿命分析的准确性.对比式(6)和式(10)可以看出,σD能够表征激励频率对应力的影响.3 排气系统的疲劳仿真分析3.1 排气系统的全寿命分析文献[5]对比了实车3WOT工况下发动机和车身的振动幅值,认为发动机激励是主要振源.四缸四冲程发动机振源主要为往复惯性力及其力矩和燃烧气体力[12].文中分别以发动机常用工况和极限工况下的扭矩作为等效力矩加载于质心处,如表2所示.表2 发动机的激励扭矩Table 2 Excitation torque of the engine工况转速/(r·min-1)扭矩/(N·m)常用工况2500130极限工况4000140根据式(11)计算,得到常用和极限工况下的二阶激励频率分别为83.3 Hz和133.3 Hz,介于排气系统第7和第9阶模态频率之间,不满足准静态分析条件.因此,文中选择动态有限元法的频率响应分析,相关基础理论详见文献[13].(11)式中,n为发动机转速,j为发动机缸数,为冲程系数,四冲程发动机对应=2.发动机为横置,于动力总成质心处施加绕Y轴的正弦激励.运用Nastran软件的模态频率响应分析[9]计算扭矩激励下排气系统的名义应力.将应力结果导入Fatigue 疲劳分析软件后,选择名义应力法,输入疲劳载荷信息与材料属性信息后进行全寿命分析,主要求解参数为存活率和名义应力修正.存活率是指以高斯分布表示可靠性时结构不发生失效的概率.为满足3σ原则,根据正态概率分布,将存活率设置为99%.由于加载的正弦激励为对称循环载荷,排气系统上各节点的名义应力呈对称循环变化,名义平均应力σm=0,根据式(3),应力幅σa即为疲劳极限σe,无须进行名义应力修正.由式(2)得循环特性r=-1,可对照S-N曲线来预测疲劳寿命.排气系统包含Q235和409L两种材料.Fatigue数据库中缺乏相关材料的S-N曲线,手动输入参数绘制各材料的S-N曲线,如图3所示[5].排气系统的频率响应分析和全寿命分析结果如图4、图5所示.从图4可以看出,两种工况下的应力最大点均出现在普通法兰两侧焊缝,分别为27.72 MPa和7.95 MPa,对应点的疲劳寿命分别为4.19×104s和1.64×108s,根据激励频率将单位换算为循环次数,分别为3.49×106和2.19×1010.文献[14]中焊缝无限寿命设计循环次数为2×106,上述两种工况下的循环次数均大于限值,说明发动机激励下排气系统的疲劳寿命满足要求.图3 排气系统材料的S-N曲线Fig.3 S-N curves of exhaust system materials图4 排气系统的应力云图Fig.4 Mean stress contour plot of the exhaust system图5 排气系统的疲劳寿命云图Fig.5 Fatigue life contour plot of the exhaust system3.2 消声器分总成的振动耐久性试验消声器分总成是排气系统的主要组成部分,其机械性能对总体疲劳寿命有直接的影响.因此,除考核发动机激励下的排气系统寿命外,还要通过振动耐久性试验检验消声器分总成的机械性能[15].文中研究对象为某乘用车,试验标准要求振动试验台的振动频率为33或67 Hz,对应振动加速度峰-峰值为30 m/s2,根据不同振动方向,振动时间分别为4 h(上下)、2 h(左右)、2 h(前后).消声器分总成按照整车上的使用状态安装在振动台上,如图6所示.图6 振动耐久性测试平台Fig.6 Vibration durability test rig试验中,消声器分总成按规定频率与幅值强迫振动,若在振动时间内不发生开裂、脱焊等损坏现象,则认为机械性能满足要求.如图7所示,使用RIGID单元代替安装支架,连接激励点和消声器分总成吊耳被动侧,避免安装支架的固有频率和激励频率耦合.在激励点施加强迫加速度正弦激励,幅值为15 m/s2,频率为33 Hz或67 Hz,频率响应分析结果如图8和表3所示.图7 振动耐久性分析模型Fig.7 Analysis model for the vibration durability将应力结果导入Fatigue,求解参数和材料疲劳属性与前面相同,应力时间历程为33和67 Hz的单位正弦波,全寿命分析结果如图9和表4所示.据此可以看出,在不同振动频率下,消声器分总成的振动寿命均大于规定的振动时间,说明消声器分总成的机械性能满足要求.图8 33 Hz正弦加速度激励的应力云图Fig.8 Mean stress contour plots of sinusoidal acceleration excitation at 33 Hz表3 正弦加速度激励的应力仿真结果Table 3 Simulation results of mean stress with sinusoidal acce-leration excitation频率/Hz方向位置应力/MPa上下后消右侧端盖16.2933左右前消侧挂钩焊缝5.13前后后消左侧挂钩焊缝5.98上下后消左侧挂钩焊缝2.6567左右后消右侧端盖0.48前后前消侧挂钩焊缝0.44对比消声器分总成在相同幅值频率、不同方向激励下的疲劳寿命,发现上下和前后方向的激励对耐久性的影响最大.这两组方向分别对应消声器分总成在汽车行驶过程中路面不平度引起的上下跳动以及车辆加速制动产生的前后移动.在现实中,汽车加速制动产生的移动加速度频率很低,因此,路面不平度是影响消声器振动耐久性的主要因素.由路面不平度产生激励的幅值虽然远小于发动机激励,但激励频带宽,可能与排气系统的固有频率耦合而引发共振,从而降低排气系统的疲劳寿命.图9 33 Hz正弦加速度激励的寿命云图Fig.9 Fatigue life contour plot of sinusoidal acceleration excitation at 33 Hz表4 正弦加速度激励的振动耐久性寿命仿真结果Table 4 Simulation results of vibration durability fatigue life with sinusoidal acceleration excitation频率/Hz方向位置寿命/h上下后消右侧挂钩焊缝24.78033左右前消侧挂钩焊缝3.310×106前后后消左侧挂钩焊缝1.102×103上下后消左侧挂钩焊缝1.325×10567左右后消右侧端盖5.410×109前后前消侧挂钩焊缝1.000×109 3.3 准静态有限元分析对比名义应力是影响疲劳寿命预测可信度的关键因素.应力分析结果与分析方法密切相关.2.2节通过算例分析了计算准静态应力和动态应力的区别.本节以发动机常用工况的扭矩激励为例,通过有限元分析对算例的计算结果进行验证.于有限元模型的发动机质心处施加绕Y轴的扭矩130 N·m,激励频率分别为0.00、1.00和15.56 Hz,结果如图10所示.图10 各激励频率下的应力云图Fig.10 Mean stress contour plot at different excitation frequencies对于一个无阻尼或只有模态阻尼的系统,准静态分析产生与0.00 Hz激励频率响应分析一致的结果.从图10可以看出,准静态分析结果与频率响应分析结果均不一致,应力最大值为78.26 MPa,峰值点出现在球形法兰螺栓孔.1.00 Hz激励频率小于系统最低阶固有频率的1/10,应力最大点和准静态分析结果相仿,幅值为78.47 MPa,出现在球形法兰螺栓孔,验证了准静态法的使用条件.激励频率为15.56 Hz时,与系统第2阶固有频率耦合,结构发生共振,应力幅值达367.90 MPa,大于准静态分析值,不满足主机厂家对排气系统应力小于150 MPa的要求.排气系统的应力分析结果与发动机激励的频率密切相关.在工程实际中,当激励频率远离系统最低阶固有频率时,才能使用准静态法分析系统的结构应力,否则仿真结果将偏离实际值.同时,产品设计应避免结构的固有频率与常用工况下的激励频率耦合,如在排气系统开发阶段通过模态分析优化设计,可避免在发动机怠速阶段发生共振.由于疲劳试验需要消耗大量的人力和时间成本,仿真结果在短期内无法进行试验验证.但文中所提出的仿真方法可以为排气系统的疲劳寿命预测和优化提供有益的借鉴.4 结论文中以一单自由度无阻尼系统为例,推导出准静态法和动态法的应力计算公式,根据公式中激励频率和固有频率的比值大小,分析了两种应力计算方法的适用范围.在排气系统的开发阶段,运用模态频率响应分析计算排气系统在发动机激励和振动激励下的名义应力,通过名义应力法进行全寿命分析,即可预测疲劳寿命和易损部位.分析结果表明,本排气系统的机械疲劳寿命满足要求,消声器分总成耐久性对上下方向激励的灵敏度较高.名义应力法以系统响应应力作为疲劳载荷,动态法应力分析能综合考虑激励幅值和频率,求解速度比准静态法有一定的下降,但能有效地提高全寿命分析的准确性.参考文献:[1] 周传月,郑红霞,罗慧强,等.MSC-Fatigue疲劳分析应用与案例 [M].北京:科学出版社,2005.[2] 庞剑,谌刚,何华.汽车噪声与振动:理论与应用[M].北京:北京理工大学出版社,2006.[3] MEDA L,LAWRENZ H,ROMZEK M,et al.Structural durability evaluation of exhaust system components [C]∥Proceedings of SAE 2007 World Congress & Exhibition.Detroit:SAE International,2007:1- 0467/1- 14.[4] PATIL S S,KATKAR V V.Approach for dynamic analysis of automotive exhaust system [C]∥Proceedings of SAE 2008 Commercial Vehicle Engineering Congress & Exhibition.Detroit:SAE International,2008:1- 2666/1- 7.[5] 沈渡,丁渭平,李洪亮,等.汽车排气系统疲劳耐久性的CAE分析研究 [J].汽车技术,2010(6):29- 33.SHEN Du,DING Weiping,LI Hongliang,et al.CAE ana-lysis study of automotive exhaust system fatigue durability [J].Automobile Technology,2010(6):29- 33.[6] 侯献军,郑灏,刘志恩,等.汽车排气系统局部疲劳耐久性试验仿真分析 [J].汽车技术,2011(3):41- 45.HOU Xianjun,ZHENG Hao,LIU Zhien,et al.Simulation and analysis of local fatigue durability test on vehicle exhaust system [J].AutomobileTechnology,2011(3):41- 45.[7] LIN Y,LI L G,CHENG Y.Fatigue design and analysis of the vehicle exhaust system’ hanger [C]∥Proceedings of SAE/KSAE 2013 International Powertrains,Fuels & Lubricants Meeting.Detroit:SAE International,2013:1- 2609/1- 7.[8] ZHANG L,LU C.Fatigue analysis of a motorcycle frame system based on a road test and the finite element method [J].Material Science Forum,2013,773/774:842- 850.[9] 赵天孟.汽车排气系统振动疲劳特性研究 [D].南宁:广西大学,2016.[10] 朱涛,高峰,张步良,等.汽车结构中焊缝疲劳寿命预估 [J].汽车技术,2006(10):37- 40.ZHU Tao,GAO Feng,ZHANG Buliang,et al.Fatigue life prediction of seam weld in the automotive structure [J].Automobile Technology,2006(10):37- 40.[11] 姚卫星.结构疲劳寿命分析 [M].北京:国防工业大学出版社,2003.[12] 徐兆坤,孙树亭,吴伟蔚,等.四缸内燃机振动分析及其对策 [J].噪声与振动控制,2007(6):50- 53.XU Zhao-kun,SUN Shu-ting,WU Wei-wei,et al.Vibration Analysis and the Location of Balance Shaft on Four Cylinder Engine [J].Noise and Vibration Control,2007(6):50- 53.[13] 田利思,李相辉,马越峰等.MSC Nastran动力分析指南 [M].北京:中国水利水电出版社,2012.[14] 黄小清,陆丽芳,何庭蕙.材料力学 [M].广州:华南理工大学出版社,2006.[15] 中华人民共和国工业和信息化部.汽车排气消声器总成技术条件和试验方法:QC/T 631—2009 [S].北京:中国计划出版社,2009.。
- 1、下载文档前请自行甄别文档内容的完整性,平台不提供额外的编辑、内容补充、找答案等附加服务。
- 2、"仅部分预览"的文档,不可在线预览部分如存在完整性等问题,可反馈申请退款(可完整预览的文档不适用该条件!)。
- 3、如文档侵犯您的权益,请联系客服反馈,我们会尽快为您处理(人工客服工作时间:9:00-18:30)。
253
能够代替原始信号做加速试验的浓缩信号必须 1) 浓缩信号产生的损伤值与原始信号产生的损 2) 浓缩信号和原始信号对样件产生的失效模式 为了避免在移去原始应变信号中损伤较小段以 :
基于 Glyphworks 的汽车排气系统加速 耐久试验载荷谱的研究
( 1. 江苏科技大学 能源与动力工程学院, 江苏 镇江 212003 ) 上海 201814 ) ( 2. 天纳克汽车工业中国研发中心, 要:在损伤等效和失效模式相同的前提下, 应用疲劳分析软件 Glyphworks, 对从试验场采集的汽车排气系统道路载荷
影响, 形式简单, 精度较高, 广泛应用于实际工程 N = 1/D = 1/ n ∑ N
l i i =1 i
(3)
a)e - DAQ 数据采集系统
e 式 (1 ~ 3) 中: ε a 为应变幅值; ε a 为弹性应变幅值;
p E 为弹性模 ε a 为塑性应变幅值; σ a 为应力幅值; 量; K' 为循环强度系数; n' 为循环应变硬化系数;
[ 1]
路载荷谱, 进而合成试验谱.
但其中存在太多的经验和估计因素, 很难作出确定 的损伤量化对比, 因此传统方法存在误差过大和不 确定性等问题. 文献 [2 ] 中通过对汽车道路耐久性试验及载荷
.
测道路载荷数据, 借助疲劳分析软件 Glyphworks, 重 点阐述了台架试验的加速试验谱的编辑过程, 提出 法, 并进行台架试验验证. 一套基于损伤等效的汽车排气系统加速耐久试验方
ε a = ε a + ε a = σ a / E +( σ a / K') 应变 - 寿命法曲线的表达式为:
e p
1 / n'
(1)
进行数据采集, 得到各种路面的载荷谱, 再对载荷
谱进行编辑, 得出台架试验的加速试验谱. 图 2 为 道路载荷数据采集系统. 图 3 为台架加速试验流程 图.
εa = εa e + εa p =
徐华平1 ,崔京宝2
摘
谱进行编辑. 得到预计试验时间和保留不同损伤量的台架试验加速载荷谱编辑结果, 并进行试验验证 . 结果表明: 与传统耐 关键词:排气系统;加速试验;损伤等效;试验谱编辑;应变寿命 中图分类号: U464 文献标志码:A 文章编号: 1673 - 4807 ( 2014 ) 03 - 0250 - 05 久试验方法相比, 该方法能在更短的时间内准确再现失效模式 .
计算一次. 图 6 中自左至右为窗口长度等于 1, 1. 5,
时间关系曲线簇, 窗口长度为 1 表示每 1 s 总损伤被
2. 78E - 6
a)雨流直方图
4
基于损伤等效的加速试验谱编辑
在实测的道路载荷谱中,Hale Waihona Puke 存在着大量对疲劳损第3 期
徐华平, 等:基于 Glyphworks 的汽车排气系统加速耐久试验载荷谱的研究
251
循环应力应变曲线, 将构件上的名义应力载荷谱转 换成危险部位的局部应力应变谱, 然后根据危险部
[ 5] 估 . 应变幅值 ε a 与对应的应力幅值 σ a 的关系式 为:
2
2. 1
道路载荷谱的采集与编辑
道路载荷谱的采集 排气系统上粘贴应变片后在指定的试车场地
位产生的 局 部 应 力 应 变 谱 来 进 行 疲 劳 寿 命 的 预
Xu Huaping1 ,Cui Jingbao2
Abstract:On the premise of the same failure mode and damage equivalence ,the loading spectra of the exhaust system of a passenger car were edited by using fatigue strength analysis software Glyphworks. Then both the test duration and fatigue editing were displayed with various damage retained , and validation test was conducted. Compared with traditional durability tests,the test duration and cost of our method were reduced markedly. Key words:exhaust system;accelerated test;damage equivalence ;test spectrum edit;E - N life 对于随机类的汽车排气系统载荷疲劳加速试 验, 传统做法是将试验载荷谱加以浓缩或强化, 或将 原始试验谱乘上一个强化系数, 以缩短试验时间
图4 Fig. 4
原始信号应变时间历程和损伤时间历程 Damage time history and strain time history 表1 原始信号寿命分析结果 Analysis of original signals life 值 6 221 1. 289E + 4 7. 760 37E - 5 501 图6 Fig. 6 损伤保留与时间保留关系曲线簇 140
b)损伤时间历程
Table 1
项目 应变循环数 预测寿命次数 预计试验时间 / h 总损伤值 信号长度 / s
个大小应变循环, 所产生损伤值为 7. 760 37E - 5, 若 时间为 501 h. 进行耐久试验, 预测寿命为 1. 289E + 4 个循环, 折合 图 5 为原始信号的雨流循环直方图和损伤分布
第 28 卷第 3 期 2014 年 6 月
Journal of Jiangsu University of Science and Technology ( Natural Science Edition)
江苏科技大学学报 ( 自然科学版)
Vol. 28 No. 3 Jun. 2014
10. 3969 / j. issn. 1673 - 4807. 2014. 03. 010 doi:
收稿日期: 2013 - 12 - 18
[ 4] 产生的局部循环塑性变形效应 . 其基本假设是: 若
作者简介:徐华平 (1979 —) , 男, 讲师, 研究方向为柴油机性能优化及排放控制. E-mail: xhp@ just. edu. cn
第3 期
徐华平, 等:基于 Glyphworks 的汽车排气系统加速耐久试验载荷谱的研究
台架加速试验流程
Flowchart of accelerated bench test
2. 2
应变 - 寿命法进行原始信号寿命分析. 汽车排气系 统局部疲劳耐久性试验重点考虑消声器和管路连
图1 Fig. 1 雨流计数法模型 Rain flow counting method
借助 Glyphworks 的疲劳 寿 命 分 析 模 块, 利用
1. 2
有明确的力学挖掘, 并具有较高的正确性, 也易于
[ 9] 实现自动化和程序化 . 图 1 为雨流计数法模型.
较好地反映随机加载的全过程. 该法在计数原则上
图2 Fig. 2
b) 应变片粘贴位置
道路载荷数据采集系统
Data acquisition system of road load
图3 Fig. 3
样所吸收的能量达到极限值时产生疲劳破坏, 且吸
Miner 从能量的角度出发, 作了如下假设: 试
σf ' b c (2 Ni ) + ε f( ' 2 Ni ) (2) E
收的能量与其循环数间存在着正比关系. Miner 累 积损伤理论忽略了加载次序及载荷间相互作用的
[ 6 - 7] 中 . Miner 线性损伤累积表达式为:
采集的时域应变信号进行预处理, 如去漂移、 去尖
图5 Fig. 5
原始信号时间历程的雨流直方图和损伤分布
b)损伤分布
Rain flow and damage histograms of strain history
3
a)应变时间历程
加速耐久试验谱编辑预估
在保证相当损伤的前提下, 尽可能缩短试验时
间是编辑加速耐久试验谱的目的, 这样做使得试验 时间缩短的同时更实现了试验资源的节省, 包括人 和保留时间长度之间的关系. 所以有必要通过对加 性. 图 6 为损伤保留与时间保留关系曲线簇. 力、 物力和费用等. 其难点在于如何确定保留损伤量 速试验谱的预估来检验加速试验谱编辑结果的正确
2, 2. 5, …, 5 的 9 个值的曲线, 从曲线图看出, 保留同 样的损伤值, 窗口长度越长, 编辑后的信号保留时间 越长, 因此, 文中选取最小窗口长度 1 进行加速耐久 试验谱的编辑. 表 2 是疲劳编辑预估结果.
表2 Table 2 时间保留 / % 10. 730 2. 497 3. 763 损伤保留 / % 100 90 95 损伤保留与时间保留关系预估结果 损伤流失 Predictive results of retaining damage and time 3. 59E - 9 1. 87E - 5
b 为疲劳 σ f ' 为疲劳强度系数; ε f ' 为疲劳延性系数; 强度指数; c 为疲劳延性指数; l 为载荷等级; n i 为各
[ 8] 劳寿命; N 为疲劳寿命; D 为疲劳总损伤 .
载荷水平下的循环次数; N i 为各载荷水平下的疲 雨流计数法 雨流计数法对应力应变迟滞回线逐个计数, 能
文中以某乘用车排气系统为研究对象, 通过实
谱驱动汽车台架耐久性试验的试验车辆响应信号和 台架信号的对比分析, 探讨了路谱驱动台架耐久性 试验的可行性. 文献 [3 ] 中提出了一种可用来采集大