汽车副车架衬套道路载荷谱缩减应用研究
乘用车副车架计算模态分析边界当量方法研究

乘用车副车架计算模态分析边界当量方法研究乘用车副车架的计算模态分析是一项重要的技术,可以用来评估车身的刚性和强度。
在该领域,边界当量方法是一种常用的近似方法,通过将实际加载替代为等效静态和动态力载荷,以简化计算过程。
本文将介绍乘用车副车架计算模态分析边界当量方法的研究进展,并探讨其优缺点。
边界当量方法的基本原理是将实际载荷替换为等效载荷,使得系统的动态响应与实际载荷下的响应一致。
该方法的优点在于可以简化计算过程,减少计算时间和成本。
此外,边界当量方法可以将动态载荷解决为对应的静态载荷,以简化结构分析。
边界当量方法的缺点在于,其计算结果可能会出现误差,因为实际载荷会随时间变化而产生变化,而静态边界当量方法无法精确模拟这种变化。
边界当量方法可以分为几种类型,包括静态和动态的方法。
静态边界当量方法使用最小和最大值的载荷范围来模拟实际载荷。
动态边界当量方法使用均方根振幅等参数来描述实际载荷的动态性。
此外,还有一些其他边界当量方法,例如基于统计学的方法,可以在不知道实际载荷的情况下对其进行近似估计。
乘用车副车架计算模态分析边界当量方法的研究领域广泛,包括对载荷的测量、建立边界当量模型以及验证模型精度等方面。
最近的研究还关注了不同载荷模拟方法的比较,以及不同设计方案的模态优化。
例如,研究表明使用动态边界当量方法可以获得更准确的结果,而基于统计学的方法可以在无法确定载荷的情况下进行设计。
总之,乘用车副车架计算模态分析边界当量方法是一种广泛应用的技术,其优点在于简化计算过程,在有限时间内获得较精确的结果。
然而,该方法的缺点需要注意,在设计过程中需要慎重考虑误差问题。
研究还需要进一步探讨如何将边界当量方法与优化设计相结合,以提高车身的性能和强度。
近年来,随着汽车市场的快速发展,乘用车副车架的设计已经受到了越来越多的关注。
在副车架的设计中,计算模态分析是一项重要的技术,可以评估车身的刚性和强度。
在计算模态分析中,边界当量方法是一种常用的技术,可以将实际载荷转换为等效载荷,从而简化计算过程。
某车型副车架衬套压出力偏小原因浅析
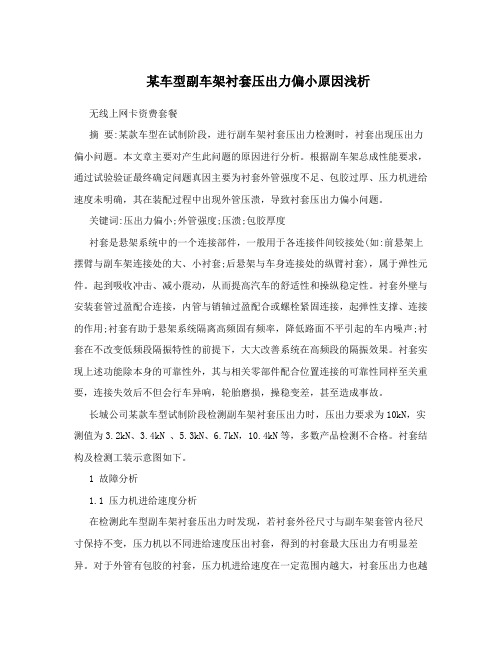
某车型副车架衬套压出力偏小原因浅析无线上网卡资费套餐摘要:某款车型在试制阶段,进行副车架衬套压出力检测时,衬套出现压出力偏小问题。
本文章主要对产生此问题的原因进行分析。
根据副车架总成性能要求,通过试验验证最终确定问题真因主要为衬套外管强度不足、包胶过厚、压力机进给速度未明确,其在装配过程中出现外管压溃,导致衬套压出力偏小问题。
关键词:压出力偏小;外管强度;压溃;包胶厚度衬套是悬架系统中的一个连接部件,一般用于各连接件间铰接处(如:前悬架上摆臂与副车架连接处的大、小衬套;后悬架与车身连接处的纵臂衬套),属于弹性元件。
起到吸收冲击、减小震动,从而提高汽车的舒适性和操纵稳定性。
衬套外壁与安装套管过盈配合连接,内管与销轴过盈配合或螺栓紧固连接,起弹性支撑、连接的作用;衬套有助于悬架系统隔离高频固有频率,降低路面不平引起的车内噪声;衬套在不改变低频段隔振特性的前提下,大大改善系统在高频段的隔振效果。
衬套实现上述功能除本身的可靠性外,其与相关零部件配合位置连接的可靠性同样至关重要,连接失效后不但会行车异响,轮胎磨损,操稳变差,甚至造成事故。
长城公司某款车型试制阶段检测副车架衬套压出力时,压出力要求为10kN,实测值为3.2kN、3.4kN 、5.3kN、6.7kN,10.4kN等,多数产品检测不合格。
衬套结构及检测工装示意图如下。
1 故障分析1.1 压力机进给速度分析在检测此车型副车架衬套压出力时发现,若衬套外径尺寸与副车架套管内径尺寸保持不变,压力机以不同进给速度压出衬套,得到的衬套最大压出力有明显差异。
对于外管有包胶的衬套,压力机进给速度在一定范围内越大,衬套压出力也越大。
根据以往车型开发经验,把压力机进给速度设定为5mm/s所检测的压出力比较符合实际产品使用性能要求。
1.2衬套与套管配合过盈量分析在衬套压脱力偏小的情况下,通常是衬套与套管的配合过盈量偏小造成的。
故在衬套外径为 59mm保持不变时,把套管内径尺寸分别调整为 59mm、 59mm、59mm,其对应的压出力见表1(单位:kN):[,&,&,&,&,&,&,&,&,&,&,&,&,&,&,&,&,&,&,&,&,&,&,&,&,&,&,&,&,&,&,&,&,&, &,&,&][ 序号内径595959][15.66.7127.723][24.65.9383.245][35.36.8195.951][45.55.0827.147][54.37.076.577][66.29.0934.249][74.73.0327.279][84.37.3726.147]从上表可得,三种产品所测压出力均不合格(要求?10kN),且没有明显差异。
基于DFSS的副车架衬套压出力优化设计
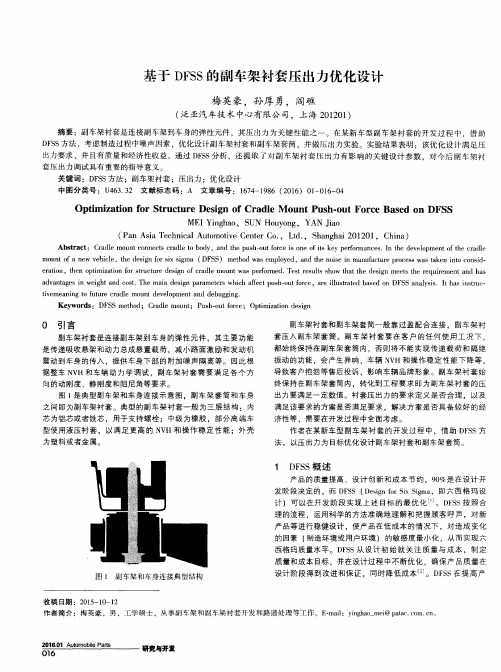
Optim ization for Structure Design of Cradle M ount Push—out Force Based on DFSS MEI Yinghao, SUN Houyong YAN Jiao
基 于 DFSS的 副 车架 衬套 压 出 力优化 设 计
梅 英 豪 ,孙厚 勇 , 阎礁
(泛亚 汽车技 术 中心有 限公 司 ,上 海 201201)
摘要 :副车架衬套 是连接副车架 到车身 的弹性元件 ,其压出力为关键性 能之一 。在某新车 型副车架衬套 的开发过 程中 ,借助 DFSS方法 ,考 虑制 造过程 中噪声 因素 ,优化设计副车架衬套和副车架套筒 ,并做压 出力实验 。实验结果表明 :该优化设 计满足压 出力要求 ,并且有质量和经 济性 收益 。通过 DFSS分析 ,还提取 了对副车 架衬套压 出力有影 响的关键设 计参数 .对 今后 副车架衬 套 压 出力 调 试 具 有 重 要 的 指 导 意 义 。
作者在某新车型副车架衬 套的开发 过程 中,借助 DFSS方 法 。以压 出力 为 目标优 化 设 计 副 车 架 衬 套 和副 车 架 套 筒 。
图 1 副车ห้องสมุดไป่ตู้架和车 身连接 典型 结构
1 DFSS概 述
产 品 的质 量 提 高 、设 计 创 新 和 成 本 节 约 。90%是 在 设 计 开 发 阶 段 决定 的 ,而 DFSS (Design for Six Sigma,即 六 西 格 玛 设 计 ) 可 以在 开 发 阶 段 实 现 上 述 目 标 的 最 优 化 … 。 DFSS按 照合 理 的 流 程 。运 用 科 学 的 方 法准 确 地 理 解 和 把 握 顾 客 呼 声 ,对 新 产 品等进行稳健设计 ,使产品在低 成本的情况下 ,对造成 变化 的 因素 (制 造 环 境 或 用户 环 境 ) 的 敏 感 度最 小 化 ,从 而 实现 六 西 格 玛 质量 水 平 。DFSS从 设 计 初 始 就 关 注 质 量 与 成 本 ,制 定 质量和成本 目标 ,并在设计过 程中不断优化 。确保产 品质 量在 设计阶段得到 改进 和保 证 。同时降低成本[2 3。DFSS在 提高产
基于实测载荷谱的副车架疲劳寿命估算方法

基于实测载荷谱的副车架疲劳寿命估算方法副车架是汽车底盘的一部分,是连接车轮、传动系统和悬架系统的主要构成部分。
它不仅要支撑整个汽车的重量,还要承受路况不良和载荷变化造成的负荷。
因此,副车架的疲劳寿命是汽车安全性和使用寿命的重要因素。
本文将讨论一种基于实测载荷谱的副车架疲劳寿命估算方法。
首先,测量和记录副车架在不同驾驶情况下的载荷变化。
它可以通过安装传感器来完成,该传感器可以记录副车架在不同路面、加速、刹车和转向等情况下的荷载。
这些测量结果可以作为载荷谱输入到疲劳寿命估算模型中。
其次,根据实验室测定得到的应力奋斗历程进行疲劳寿命试验,以获得副车架在该应力状况下的疲劳寿命。
然后可以使用疲劳寿命测试数据建立基于副车架所受载荷的疲劳寿命曲线,以估算不同载荷情况下副车架的疲劳寿命。
最后,将谱法理论应用于载荷谱中的副车架负载,得到当期载荷对应的等效疲劳载荷,并应用于副车架疲劳寿命曲线中以估算副车架的疲劳寿命。
根据所得到的结果,可以给出推荐的维护和更换周期。
然而,该方法存在的主要问题是,载荷谱的随机性质使得结果存在一定的误差。
此外,由于不同车辆的操作条件和使用环境不同,因此需要考虑实测数据的个体差异。
因此,建立一个可重复性高、可靠性强的疲劳寿命估算方法是当前研究的重点。
综上所述,随着计算机技术的不断发展,副车架的疲劳寿命估算方法将不断完善。
应在实践中运用合理的负载谱获取方法并结合疲劳寿命测试结果,以实现对汽车底盘的安全使用和长寿命的保障。
除了基于实测载荷谱的副车架疲劳寿命估算方法之外,还有一些其他方法可以用来评估副车架的疲劳寿命。
例如,可以使用计算机模型来模拟驾驶循环,并预测副车架在不同载荷下的应力状态。
它可以基于模拟结果建立疲劳寿命模型,以估算副车架的疲劳寿命。
此外,还可以使用裂纹扩展方法,以测定裂纹在副车架上扩展的速度。
通过中断试验,可以根据49CFR 393.207标准来估算副车架的疲劳状态,以确定是否需要维修或更换。
汽车副车架衬套道路载荷谱缩减应用研究
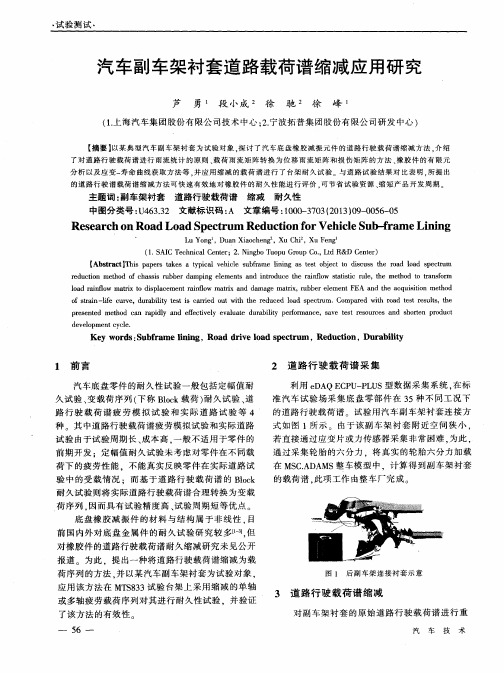
2 道 路 行 驶 载 荷 谱 采 集
利用 e D AQ E C P U — P L U S型 数据 采集 系统 . 在标
准 汽车试 验场 采 集底 盘零 部 件 在 3 5种不 同工 况 下 的道 路行 驶 载荷谱 试 验用 汽 车副 车架 衬套 连接 方
p r e s e n t e d me  ̄o d c a n r a p i d l y a n d e f f e c t i v e l y e v a l u a t e d u r a b i l i t y p e r f o m a r n c e ,s a v e t e s t r e s o u r c e s a n d s h o r t e n p r o d u c t
主 题词 : 副 车架衬 套
道 路行驶 载 荷谱
缩减
耐 久性
中图分 类号 : U 4 6 3 . 3 2 文献标 识 码 : A 文章 编 号 : 1 0 0 0 — 3 7 0 3 ( 2 0 1 3 ) 0 9 — 0 0 5 6 — 0 5
对轿车副车架设计与优化的研究洪磊

对轿车副车架设计与优化的研究洪磊发布时间:2023-05-31T11:36:09.668Z 来源:《中国电业与能源》2023年6期作者:洪磊[导读] 目前,轿车副车架设计质量提升,受到行业内关注。
本文将针对轿车载荷情况和典型工况设计情况,对轿车副车架设计开展优化,设计优化中应用三维CAD软件,提高设计质量。
最终完成构件的强度计算,借此分析优化设计后的轿车副车架优势。
研究发现,通过优化设计后的副车架可通过减小板材厚度的方式,实现车架减重的效果,进而提升轿车的整体性能。
本文关于轿车副车架性能优化的研究,可供其他同行工作参考。
宁波汇众汽车车桥制造有限公司 315033摘要:目前,轿车副车架设计质量提升,受到行业内关注。
本文将针对轿车载荷情况和典型工况设计情况,对轿车副车架设计开展优化,设计优化中应用三维CAD软件,提高设计质量。
最终完成构件的强度计算,借此分析优化设计后的轿车副车架优势。
研究发现,通过优化设计后的副车架可通过减小板材厚度的方式,实现车架减重的效果,进而提升轿车的整体性能。
本文关于轿车副车架性能优化的研究,可供其他同行工作参考。
关键词:副车架;优化设计;轿车引言:研究发现,汽车底盘性能很难兼顾舒适性、操控性,两者是相互矛盾的。
针对悬挂系统的设计,设计者会选用一些复杂结构来尽量保障操控性和底盘舒适性的平衡,而轿车副车架发挥的就是这方面的作用。
简单地说,副车架的作用显著,可看作前后车桥的骨架,属于轿车的重要构成。
传统副车架设计中应用的是承载式车身,这种方式会影响操作性能,随着副车架设计的完善,悬挂系统结构发生了改变,由散件变成了总成,操作中稍作调校便可实现良好匹配的效果。
基于这种结构的副车架设计,除了方便和优越性要得到保障以外,还要兼顾舒适性和悬挂刚度等具体需求。
1副车架的作用原理对于副车架来说,在设计中需满足性能需求,副车架的突出作用是控制路面震动的传入,借此增加行车的舒适性。
同时,借助副车架的设计,还可以强化悬挂系统连接刚度,从而提升安全性。
基于拓扑优化设计方法的轿车副车架轻量化研究的开题报告

基于拓扑优化设计方法的轿车副车架轻量化研究的开题报告一、选题背景随着汽车工业的发展,汽车的轻量化问题日益突出。
副车架作为汽车重要零部件之一,其质量对整车重量和燃油经济性有着重要的影响。
因此,如何在保证副车架性能的前提下实现轻量化是目前汽车制造企业和科研机构研究的重点之一。
拓扑优化设计方法作为一种新型的结构优化方法,已经被广泛应用于汽车结构轻量化领域,并取得了很大的成功。
二、研究目的和意义本文旨在研究基于拓扑优化设计方法的轿车副车架轻量化,探究在满足副车架承载能力和刚度的前提下,通过优化设计使副车架质量尽量减轻,从而提高汽车的燃油经济性和环保性能。
通过研究,可以为实现汽车轻量化提供理论参考和实践基础,促进汽车工业的可持续发展。
三、研究内容和方法1.对副车架的结构、工作原理、设计要求和轻量化技术进行研究和分析。
2.研究拓扑优化设计方法的基本理论和应用方法,设计并建立数学模型。
3.通过有限元分析软件进行副车架的模拟计算,建立副车架的有限元模型。
4.通过拓扑优化设计方法对副车架进行优化设计。
根据优化结果,利用CAD软件生成优化后的副车架模型,进行有限元分析和验证。
5.对比分析优化前后副车架的质量、刚度和承载能力等参数,并对优化结果进行评价和优化。
四、预期成果1.通过对副车架轻量化的研究和分析,得出副车架轻量化的可行性和优点。
2.通过拓扑优化设计方法对副车架进行优化设计,得到优化后的副车架模型。
3.通过对比分析,证明优化后的副车架在满足设计要求的前提下,质量得到了明显降低,且具备良好的刚度和承载能力。
4.为轿车副车架的轻量化提供理论依据和实践参考,为汽车工业的可持续发展做出贡献。
五、进度安排第1-2周:文献综述与调研;第3-4周:副车架的结构和轻量化技术分析;第5-6周:拓扑优化设计方法理论研究;第7-8周:建立副车架的有限元模型;第9-10周:拓扑优化设计并求解;第11-12周:CAD建模和有限元分析;第13-14周:对比分析和评价;第15-16周:撰写论文和答辩准备。
轿车副车架轻量化技术研究及应用

第17卷第5期塑性工程学报V。
1.17No.51111111望』Q堕基丛△垦12E£L垒苎!!竺!!羔堡丛g!盟堡垦垦!堕鱼!!!!:!!!!doi:10.3969/j.issn.1007—2012.2010.05.015轿车副车架轻量化技术研究及应用*(北京汽车研究总院,北京100021)张立玲黄黎叶子青林逸(密歇根大学,美国48109)赵红伟马正东摘要:文章将多.r况强度分析方法与拓扑优化技术相结合,制定了基于刚度日标及应力约束的轿车副午架结构优化分析流程,并对几种车型的副车架分别进行厂结构强度评价分析、轻昔化优化分析。
工程实际应用表明,采用多工况强度分析方法。
能够准确地预测副车架强度薄弱部位,CAE分析与试验结果吻合;采用拓扑优化方法,选取适当的优化参数,可以得到该文给f{j的减重约15%、符合制造工艺要求的实用减重方案,并适用于全新副车架的概念模型设计,具有较为重要的学术价值及工程实际意义。
关键词:轻量化;轿车副车架;拓扑优化;数值模拟中图分类号:U463.32文献标识码:A文章编号:1007—2012(2010)05-0071—05ResearchandapplicationoflightweighttechnologyforpassengercarsubframesZHANGLi-lingHUANGLiYEZi—qingLINYi(BeijingAutomotiveTechnologyCenter,Beijing100021China)ZHAOHong-weiMAZheng-dong(UniversityofMichigan,AnnArbor,MI48109,USA)Abstract:CAEanalysismethodsandproceduresofstructuraloptimizationforpassengercarsubframesweresetupbasedonmulti—pieloadcasesstrengthanalysismethodsandtopologyoptimizationtechnology,bywhichthestructuralstiffness。
某型汽车悬架衬套有限元与试验分析

s us pe ns l ● on bus l hi l ● ng s
Z HO N G Ha n w e n ,C HE N G u o d o n g ,B U J i l i n g , J I A N G Q i b i n
第2 2卷 增 刊 2
2 0 1 3年 1 0月
计 算 机 辅 助 工 程
Co mp u t e r Ai d e d En g i n e e r i n g
Vo 1 . 22 Su p p1 . 2 0c t .2 0l 3
文章编号 : 1 0 0 6—0 8 7 1 ( 2 0 1 3 ) s 2 — 0 1 9 2 — 0 6
e l e me n t a n a l y s i s r e s u l t s c a n h a v e a g o o d c o n s i s t e n c e wi t h t he t e s t r e s u l t s,wh i c h c a n i mpr o v e t he d e s i g n
0 引 言
近年来 , 汽 车的轻 量化设 计成 为一 种趋势 . 悬 架
件 中的柔 性连接 件 , 衬 套 对悬 架 的性 能 和 影 响 十分 重要 . 在 实际 的产 品设 计 中 , 希望 衬套 的刚度能 实现
某 型汽 车悬 架衬 套 有 限元 与 试 验分 析
钟 汉文 , 陈 国栋 , 1 、 继玲 , 姜 其 斌
( 株 洲 时代 新 材料 科技 股 份 有 限公 司 , 湖南 株洲 4 1 2 0 0 7 )
汽车道路模拟试验载荷谱的研究
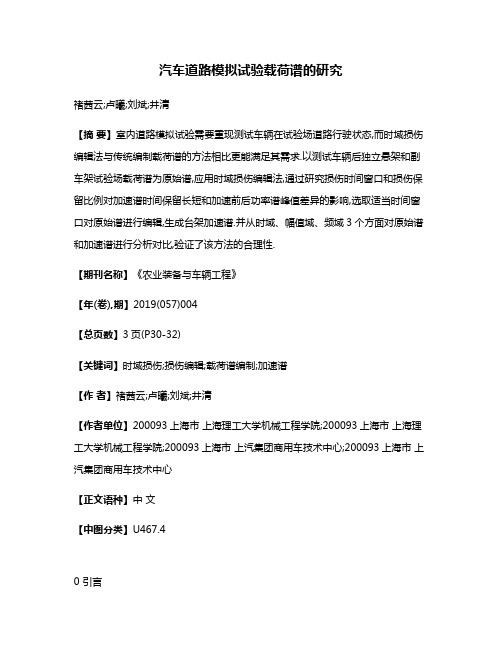
汽车道路模拟试验载荷谱的研究褚茜云;卢曦;刘斌;井清【摘要】室内道路模拟试验需要重现测试车辆在试验场道路行驶状态,而时域损伤编辑法与传统编制载荷谱的方法相比更能满足其需求.以测试车辆后独立悬架和副车架试验场载荷谱为原始谱,应用时域损伤编辑法,通过研究损伤时间窗口和损伤保留比例对加速谱时间保留长短和加速前后功率谱峰值差异的影响,选取适当时间窗口对原始谱进行编辑,生成台架加速谱.并从时域、幅值域、频域3个方面对原始谱和加速谱进行分析对比,验证了该方法的合理性.【期刊名称】《农业装备与车辆工程》【年(卷),期】2019(057)004【总页数】3页(P30-32)【关键词】时域损伤;损伤编辑;载荷谱编制;加速谱【作者】褚茜云;卢曦;刘斌;井清【作者单位】200093上海市上海理工大学机械工程学院;200093上海市上海理工大学机械工程学院;200093上海市上汽集团商用车技术中心;200093上海市上汽集团商用车技术中心【正文语种】中文【中图分类】U467.40 引言汽车的悬架与副车架作为底盘系统关键承载部件,其疲劳耐久性对整车的可靠性非常重要。
室内道路模拟试验[1]相比公共道路试验与试验场道路试验,除了具有可重复性高、不受环境因素影响的优点以外,还由于其本身编制时删除了试验场路面中的过渡路面以及损伤占比极小的工况,试验时间相比缩短了约80%,因此成为车辆快速验证的首选[2]。
汽车载荷谱特征包含幅值、频率、多通道加载相位与次序,道路模拟试验采用的载荷谱中需要包含上述特征。
传统的编制载荷谱的方法如增大载荷幅值或频率法、峰谷抽取法、程序块加载法,都已不能满足道路模拟试验的要求[3]。
国外学者目前已发表2种先进方法,Abdullah[4]等采用Wavelet Bump Extraction 算法保留大损伤频带的时间,删除小损伤的频带,从而得到加速谱;Abdullah[5]等还基于STFT( Short Time Fourier Transform) 方法编辑载荷谱,删除低于设定功率谱值的低幅值随机载荷,从而编制加速谱。
基于路谱载荷的副车架加速耐久台架试验的开发与应用
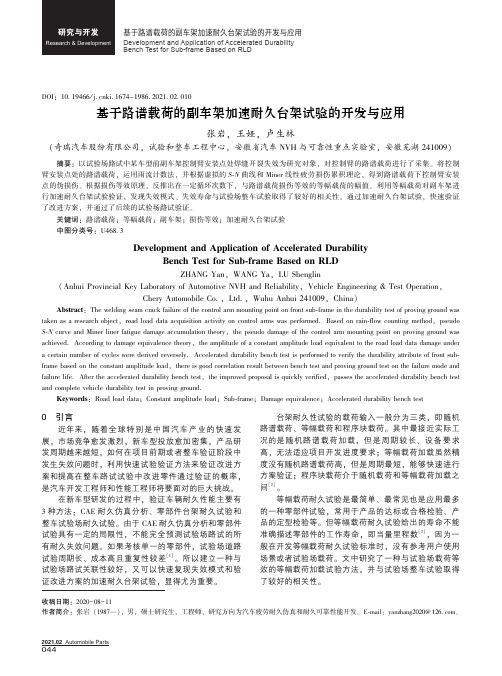
2021.02 Automobile Parts 044Automobile Parts 2021.020451㊀前副车架焊缝失效在试验场耐久路试中,当试验进行到一个寿命循环的98%时,发现前副车架右控制臂安装点处的焊缝端部发生开裂㊂开裂位置如图1所示㊂图1㊀前副车架焊缝开裂位置2㊀试验场路谱载荷采集2.1㊀控制臂上应变片布置方式焊缝开裂位置附近只有一个受力硬点:控制臂在副车架上的安装点,因此了解控制臂安装点处的试验场载荷尤为重要㊂为了获得前副车架控制臂安装点处的路谱载荷,首先要获取控制臂上的载荷,通常使用应变片来反映应变与载荷之间的关系㊂控制臂所受载荷以轴向拉压载荷为主,所以应变片贴于控制臂受力方向的对称面并组成全桥,此种应变片的布置方式可以补偿弯曲载荷,且对拉压载荷敏感,是测量轴向拉压载荷的常用布置方式㊂应变位置布置方式如图2所示㊂图2㊀控制臂上应变片布置2.2㊀左、右控制臂的标定标定就是获得力和应变之间的关系,是对载荷测量精度影响最为关键的步骤之一,一般只需做线性标定,标定还可以初步检验应变传感器的安装质量㊂完成控制臂应变片布置后,通过台架上的标准力传感器施加一定范围内的载荷,从而将应变测量转换为载荷的测量㊂标定过程如图3所示㊂标定时拉伸为正,压缩为负,左右控制臂的标定结果分别如图4和图5所示㊂图3㊀左右控制臂标定过程图4㊀左侧控制臂标定结果图5㊀右侧控制臂标定结果2.3㊀试验场路谱载荷采集控制臂的路谱载荷采集,选择与整车耐久路试相同的试验场进行,依据试验场耐久试验规范中包含的特征路面以及规范中通过每个特征路面的速度,对这些特征2021.02 Automobile Parts046图6㊀特征路面下控制臂载荷3㊀相关疲劳理论介绍3.1㊀S-N 曲线介绍在零件上所施加的载荷,由应力范围S r 或者应力幅S a 确定㊂应力范围被定义为一个循环中最大应力S max 和最小应力S min 之间的代数差:S r =S max -S min (1)应力幅等于应力范围的1/2:S a =S r 2=S max -S min2(2)通常采用对称的循环交变加载方式进行S -N 的疲劳试验㊂对称循环表示以零平均应力进行交变加载,平均应力S m 被定义为:S m =S max +S min2(3)典型的S -N 曲线公式为:S a =S ᶄf(2N f )b(4)Automobile Parts 2021.02047图7㊀路谱载荷雨流计数直方图2㊀计算伪损伤和等幅载荷的幅值在计算零件的损伤或寿命时,采用的是零件真实的应力应变,根据零件材料真实的S-N 曲线,计算出真实的损伤值㊂而在实际的工程实践中,从能量的角度出发,对各种信号,无论是力,力矩还是位移㊁加速度应力㊁应变都可认为是 广义应力 ,通过预先设定的虚拟的S-N 曲线,即可求得伪损伤[8]㊂定义一条虚拟的S-N 曲线:S a =S ᶄf(2N f )b其中S ᶄf =1ˑ105,b =-1/3㊂将雨流计数得到的一系列幅值不同的载荷代入式(4)中,就能得到每个幅值下的循环次数N f ,再将求得的N f 代入式(5)的疲劳损伤累计公式中,就可以得到控制臂在路谱载荷下的总损伤:D RLD =ðli =1n i /N i =529.06(6由损伤等效原理,路谱载荷下的总损伤D RLD 与等幅载荷下的总损伤D constant 相等,即:D RLD =D constant =529.06(7定义N constant =170000次为等幅载荷的循环次数㊂由式(4)和(5)可得公式:S constant =0.5ˑSᶄfD constant N constant()-b(8将S ᶄf =1ˑ105,b =-1/3,D constant =529.06,N constant =170000代入公式(8)中,可得:S constant =0.5ˑ100000ˑ529.06170000()-(-1/3)ʈ7300N其中S constant 为需要求得的等幅载荷的幅值[9]㊂图8㊀等幅载荷试验加载波形等幅幅值S constant =7300N ,加载目标循环次数N constant =170000次,均值S m =500N ,加载频率为5Hz ㊂副车架加速耐久台架试验加载示意图如图9所示㊂图9㊀副车架加载示意5 加速耐久台架试验验证5.1㊀加速耐久台架搭建约束副车架与车身的4个安装点,采用单轴作动缸加载,并用激光测距仪检测加载点处的位移,目的是为了监测副车架开裂失效的时间点,可以更准确地确定失效时的循环次数㊂加速耐久台架搭建如图10所示㊂2021.02 Automobile Parts048图10㊀加速耐久台架搭建加速耐久台架试验结果在完成183000次加载(108%)后,发现前副车架右控制臂安装点处的焊缝发生了开裂,与试验场路试中前副车架焊缝的开裂失效模式和失效寿命基本一致速耐久台架试验中副车架焊缝开裂如图11所示㊂图11㊀加速耐久台架试验中副车架焊缝关于台架试验与路试试验的失效模式㊁失效位置失效寿命和验证时间的对比结果见表1㊂表1㊀台架试验结果与路试试验结果对比试验种类失效模式失效位置失效寿命/%验证时间试验场焊缝开裂焊缝端部98706台架焊缝开裂焊缝端部10810从台架试验结果与路试试验结果的对比可以发现试验场副车架焊缝的失效模式㊁失效寿命与台架试验结图12㊀耐久失效问题台架验证及改进流程基于损伤等效㊁疲劳累计损伤,雨流计数法疲劳分析和伪损伤等理论和分析方法,将试验场路谱载荷等效为等幅载荷,经过试验验证后,发现施加等幅载荷的加速耐久台架试验的失效模式㊁失效寿命与试验场试验基本一致,相关性较好㊂台架试验的失效验证时间仅为试验场试验的加速耐久台架试验,可以大幅减少改进方案的验增加了改进后零件通过试验场整车试验的通过文中以副车架为研究对象,进行了副车架加速耐久试验的开发与应用,其他底盘零部件,转向节㊁转向拉杆等部件,都可以应用文中方法开发相应的加速耐久台架试验㊂基于损伤等效的加速耐久台架试验方法可以在耐久路试出现问题后,应用于改进方案的快速验也可以在项目开发前期,仅有底盘系统的物理样件Automobile Parts 2021.02049。
某轿车副车架的强度及疲劳有限元分析的开题报告
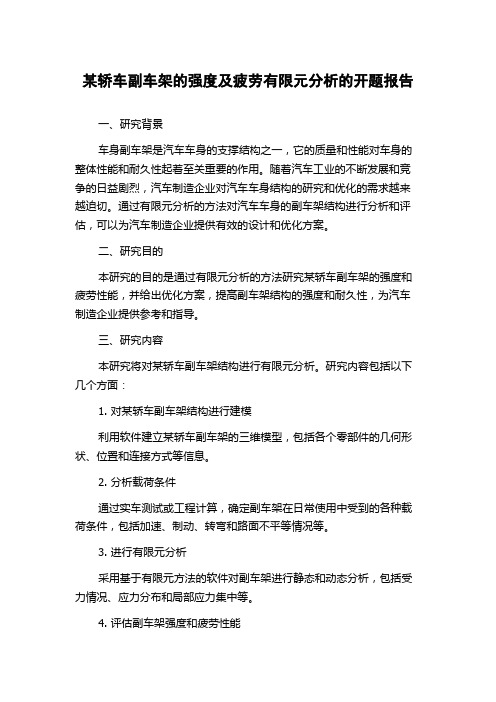
某轿车副车架的强度及疲劳有限元分析的开题报告一、研究背景车身副车架是汽车车身的支撑结构之一,它的质量和性能对车身的整体性能和耐久性起着至关重要的作用。
随着汽车工业的不断发展和竞争的日益剧烈,汽车制造企业对汽车车身结构的研究和优化的需求越来越迫切。
通过有限元分析的方法对汽车车身的副车架结构进行分析和评估,可以为汽车制造企业提供有效的设计和优化方案。
二、研究目的本研究的目的是通过有限元分析的方法研究某轿车副车架的强度和疲劳性能,并给出优化方案,提高副车架结构的强度和耐久性,为汽车制造企业提供参考和指导。
三、研究内容本研究将对某轿车副车架结构进行有限元分析。
研究内容包括以下几个方面:1. 对某轿车副车架结构进行建模利用软件建立某轿车副车架的三维模型,包括各个零部件的几何形状、位置和连接方式等信息。
2. 分析载荷条件通过实车测试或工程计算,确定副车架在日常使用中受到的各种载荷条件,包括加速、制动、转弯和路面不平等情况等。
3. 进行有限元分析采用基于有限元方法的软件对副车架进行静态和动态分析,包括受力情况、应力分布和局部应力集中等。
4. 评估副车架强度和疲劳性能根据有限元分析的结果,对副车架的强度和疲劳性能进行评估,并给出相应的评估指标。
5. 提出副车架结构优化方案根据分析结果和评估指标,提出副车架结构的优化方案,提高其强度和耐久性。
四、研究意义本研究的意义在于:1. 提高汽车副车架结构的强度和耐久性,保障其安全性和可靠性。
2. 为汽车制造企业提供有效的设计和优化方案,提高汽车竞争力。
3. 拓宽有限元分析的应用范围和方法,对有限元分析技术的发展具有一定的推动作用。
五、研究进度安排本研究的进度安排如下:第一阶段:文献调研和理论学习(2个月)第二阶段:副车架结构建模和载荷分析(2个月)第三阶段:有限元分析和结果分析(3个月)第四阶段:副车架强度和疲劳性能评估(1个月)第五阶段:副车架结构优化方案提出和总结(2个月)六、预期成果本研究预期达到的成果包括:1. 对某轿车副车架结构进行建模和有限元分析,并给出评估指标。
汽车零部件可靠性测评技术的发展与应用

10.16638/ki.1671-7988.2021.012.035汽车零部件可靠性测评技术的发展与应用宁世儒,张冠勇,庞方超(中汽研汽车检验中心(天津)有限公司,天津300300)摘要:随着汽车零部件可靠性验证已成为产品开发过程中越来越重要的一个环节,并占用了整车研发过程中的大量时间,因此迫切需要研发出更为高效的汽车零部件可靠性测评技术。
文章从编辑道路载荷谱、搭建疲劳耐久性台架试验以及虚拟仿真试验技术三个方面着手进行汽车零部件可靠性测评技术研究及应用现状阐述,并对未来车辆可靠性测评技术的发展方向进行展望,为实现汽车零部件产品开发流程的最优化,降低研发费用以及增强产品竞争力提供重要的理论支撑。
关键词:可靠性强化试验技术;道路载荷谱;可靠性台架试验;虚拟仿真试验技术中图分类号:U467 文献标识码:A 文章编号:1671-7988(2021)12-113-04Development and Application of Reliability StrengtheningTest Technology for Auto PartsNING Shiru, ZHANG Guanyong, PANG Fangchao( China Automotive Research Institute Automotive Inspection Center (Tianjin) Co., Ltd., Tianjin 300300 )Abstract: As the reliability verification of auto parts has become an increasingly important part of product development and takes up a lot of time in the vehicle parts development process, there is an urgent need to develop more efficient reliability evaluation technologies for auto parts. This paper starts to conduct auto parts reliability evaluation research and application status elaboration from three aspects: editing the road load spectrum, building reliability bench test and virtual simulation test technology, and looks forward to the future vehicle reliability evaluation technology, and provides important theoretical support for realizing the optimization of the development process of auto parts products, reducing R&D costs and enhancing product competitiveness.Keywords: Reliability enhancement test technology; Road load spectrum; Reliability bench test; Virtual simulation test technologyCLC NO.: U467 Document Code: A Article ID: 1671-7988(2021)12-113-04前言近年来,国内汽车市场结束了连续29年的增长奇迹,市场对于汽车产品的可靠性和安全性提出越来越高的标准和要求[1-2]。
汽车悬架衬套静动特性分析中缩径量影响研究

V ol 39No.1Feb.2019噪声与振动控制NOISE AND VIBRATION CONTROL 第39卷第1期2019年2月文章编号:1006-1355(2019)01-0126-05汽车悬架衬套静动特性分析中缩径量影响研究陈宝1,代正莉1,付江华1,陈哲明1,许言明2(1.重庆理工大学车辆工程学院,重庆400054;2.河北华密橡胶有限责任公司,河北邢台054000)摘要:为有效开展整车操稳性、平顺性的仿真研究,有必要对影响较大的汽车悬架衬套的静、动刚度范围进行精确设计及控制。
采用3阶Ogden 超弹性本构模型与3阶PRONY 级数黏弹性模型建立某汽车悬架减振器橡胶连接衬套超-黏弹性有限元模型,利用ABAQUS/Standard 有限元分析模块分别研究衬套缩径量大小与静、动刚度的关系,得到了不同缩径量下橡胶衬套静、动刚度曲线;结果显示,当缩径量小于0.6mm 时,橡胶衬套静、动刚度随缩径量的增加而增大并呈近似的线性关系;当缩径量大于0.6mm 后,静、动刚度随缩径量增大而增大的速率急剧变大而呈现非线性关系;研究表明,当缩径值达到一定程度后对橡胶衬套静、动刚度值的影响变大;最后通过试验测试发现有限元分析结果与测试结果相对误差在10%以内,证明考虑缩径量影响的汽车悬架衬套静动特性分析的正确性,这对车用橡胶衬套的设计与分析研究具有一定的指导意义。
关键词:振动与波;橡胶衬套;静/动刚度;超-黏弹性;有限元分析;缩径量中图分类号:TH703.63文献标志码:ADOI 编码:10.3969/j.issn.1006-1355.2019.01.024Influence of Contraction Amount on the Analysis of Static and Dynamic Characteristics of Automobile Suspension BushingsCHEN Bao 1,DAI Zhengli 1,FU Jianghua 1,CHEN Zheming 1,XU Yanming 2(1.Department of Vehicle Engineering,Chongqing University of Technology,Chongqing 400054,China;2.Hebei Huami Rubber Co.Ltd.,Xingtai 054000,Hebei China )Abstract :In order to effectively carry out the simulation research for the handling and riding performance of the vehicles,it is necessary to accurately design and control the static and dynamic stiffness ranges of the automotive suspension bushings.In this paper,the hyper-viscoelastic finite element model of a rubber bushing for an automotive suspension shock absorber is established using the 3rd order Ogden hyperelastic constitutive model and the 3rd order PRONY series viscoelastic model.The finite element analysis module ABAQUS /Standard is used to study the relationship between the radial contraction amount and the static and dynamic stiffness.The static and dynamic stiffness curves of the rubber bushings vs.different contraction amount are obtained.The results show that when the contraction amount is less than 0.6mm,the static and dynamic stiffness of the rubber bushing increases almost linearly with the increase of the contraction amount.When the contraction amount is greater than 0.6mm,the static and dynamic stiffness increases rapidly with the increase of the contraction amount.When the contraction amount reaches a certain level,its influence on the static and dynamic stiffness values of the rubber bushing becomes larger.Finally,the experimental results show that the relative error between the finite element analysis results and the test results is less than 10%.Thus,the correctness of the static and dynamic characteristics analysis of the automotive suspension bushings considering the influence of the contraction amount is proved.This study has a certain guiding significance for the design and analysis of rubber bushings for vehicles.Keywords :vibration and wave;rubber bushing;static and dynamic stiffness;super-viscoelastic;finite element analysis;radial contraction amount收稿日期:2018-07-13基金项目:电动轮总成多因素耦合对车辆系统动力学影响及其协同控制研究(cstc2018jcyjAX0109)作者简介:陈宝(1974-),男,山西省大同市人,教授,博士,从事汽车结构分析以及系统动力学研究。
某车型前副车架轻量化优化分析

某车型前副车架轻量化优化分析周丽杰【摘要】某款车型前副车架在设计阶段,进行结构耐久仿真分析时发现前副车架的焊缝疲劳存在开裂风险.利用OptiStruct的优化功能,对副车架进行灵敏度分析和尺寸优化设计,得到副车架的最优结构尺寸.优化后的副车架质量减少1.2%,且焊缝寿命提高64-85%.【期刊名称】《汽车实用技术》【年(卷),期】2019(000)006【总页数】2页(P156-157)【关键词】前副车架;OptiStruct;焊缝疲劳;轻量化;优化【作者】周丽杰【作者单位】爱驰汽车(上海)有限公司,上海200090【正文语种】中文【中图分类】U467引言对于新能源电动汽车来说,减轻重量,实现轻量化,对增加其行驶里程和提高车身的耐久性和安全性有着非常重要的意义,有目标地减轻汽车自身的重量就成为必然的途径。
同时作为有效的节能手段,汽车轻量化技术已经成为新能源电动汽车发展的重要方向之一,这也是新能源汽车发展的基础技术。
轻量化在电动汽车上的实现是一项极其具有挑战的机械工程,汽车轻量化是集多学科、多行业于一体的完整的系统,涵盖设计方法、材料科学、制造工艺等领域[1],需各部门间密切合作,具有协调统一的整体优化目标。
1 前副车架作用及轻量化副车架是汽车底盘的重要零部件之一,副车架的作用可以减少车辆的噪声与振动[2],同时还可以提高整车的刚度、强度和安全性,对于舒适性起到很重要的作用,所以其性能表现对于汽车而言是非常重要的。
副车架轻量化指的是减轻副车架本身的重量,在保证副车架的强度、振动特性与安全性的基础下,通过采用高强钢材料、结构拓扑优化、车型规格优化、减薄板料厚度等方式降低副车架质量。
2 前副车架基础版仿真分析前副车架由上片、下片、中塔内板、中塔外板、悬置加强板等部分组成,利用多套焊接工艺序完成组装,因此要求副车架的焊接质量是非常高的。
本论文所用的前副车架采用热轧高强度酸洗钢HZFB590。
(1)根据44种典型工况下的受力分析提取副车架各硬点位置所受力及力矩大小,对副车架进行静强度分析,基础版前副车架各工况最大应力为 505Mpa,满足小于其材料屈服强度要求。
某车副车架有限元分析与改进

某车副车架有限元分析与改进廖抒华;张旭;刘利【摘要】针对副车架安装状态实验模态与仿真约束模态误差太大,用车身安装点处局部动刚度导入弹性单元替代刚性约束的方法对模型进行修改,有限元模型精度得到改善,模态误差减少到可接受范围.在修正模型基础上,对副车架上关键点动刚度进行分析与改进,使动刚度不足的安装点满足目标要求,改善了安装点的动刚度特性,使副车架的结构更趋合理.【期刊名称】《汽车零部件》【年(卷),期】2017(000)012【总页数】4页(P46-49)【关键词】副车架;模型修正;模态;动刚度【作者】廖抒华;张旭;刘利【作者单位】广西科技大学汽车与交通学院,广西柳州545000;广西科技大学汽车与交通学院,广西柳州545000;广东海洋大学,广东湛江524000【正文语种】中文【中图分类】U46轿车副车架作为车桥与悬架的支撑,也是发动机的重要承载单元。
在车辆行驶过程中,副车架对来自路面的随机载荷和发动机的振动载荷进行衰减和隔离[1]。
通过模态性能分析,可以得出副车架结构的固有频率和固有振型,进而分析其动态响应频率,避免共振现象的产生[2-3]。
副车架自身的结构设计及其与安装件的连接强度对车辆的舒适性和行驶平顺性有重要的影响[4]。
副车架需要满足局部动刚度的要求,一些关键点(发动机后悬置安装点、摆臂安装点等)是向车身传递振动的主要来源,对车身的振动和疲劳破坏有重要影响,因此,分析这些关键点的动刚度具有重要意义[5]。
将在CATIA中建立的副车架几何模型导入HyperMesh中进行前处理,对该模型采用壳单元进行网格划分。
整个模型有12 786个节点,四边形Quad单元11 658个,Tria三角形单元458个,占壳单元3.8%。
对网格质量进行检查,Comp.QI值为0.03,小于工程要求Comp.QI值0.1,网格质量较好。
将实际厚度和材料属性赋予网格,材料属性如表1所示。
在该副车架中,有一些关键点,例如发动机悬置点、副车架安装点和摆臂安装点等,对这些点通过RBE2单元与孔周围的节点相连[6]。
- 1、下载文档前请自行甄别文档内容的完整性,平台不提供额外的编辑、内容补充、找答案等附加服务。
- 2、"仅部分预览"的文档,不可在线预览部分如存在完整性等问题,可反馈申请退款(可完整预览的文档不适用该条件!)。
- 3、如文档侵犯您的权益,请联系客服反馈,我们会尽快为您处理(人工客服工作时间:9:00-18:30)。
为得到橡胶材料的应变与寿命关系袁 利用图 6 所示的设备进行单轴拉伸疲劳试验袁 以获取不同工 程应变水平下的橡胶试片的疲劳寿命数据袁 再经拟 合得到最大主应变与试片寿命数据的函数关系遥 拟 合的应变要寿命曲线见图 7遥
试片
图 6 橡胶材料试片疲劳寿命试验设备
要 58 要
1.8
0.8
-0.2
104
105
渊c冤Z 向 副车架衬套三向力-位移曲线计算值与测试值对比
应变
+1.264伊100 +7.000伊10-1 +6.417伊10-1 +5.833伊10-1 +5.250伊10-1 +4.667伊10-1 +4.083伊10-1 +3.500伊10-1 +2.917伊10-1 +2.333伊10-1 +1.750伊10-1 +1.167伊10-1 +5.834伊10-2 +1.997伊10-6
通过雨流计数可得到道路行驶载荷谱载荷的雨 流载荷矩阵袁此矩阵包括幅值渊Range冤尧均值渊Mean冤 与循环次数渊Cycle冤袁如图 3 所示遥 其中每个 Block 载荷包含多个 Cycle曰 Block 载荷的大小由 Mean 值和 Range 值共同确定袁 在一定范围内动态变化遥 由此可知袁Block 载荷是一个范围值袁为便于后期橡 胶件有限元分析袁需要将此载荷范围值转换为定值袁 即将载荷 Mean 值转换为 Range 值袁 此方法类似金 属疲劳中的 Goodman 平均应力修正遥 根据实际工 程经验袁该衬套的转换公式为院修正的 Range 值=原
运藻赠 憎燥则凿泽院Subframe lining袁 Road drive load spectrum袁 Reduction袁 Durability
1 前言
汽车底盘零件的耐久性试验一般包括定幅值耐 久试验尧变载荷序列渊下称 Block 载荷冤耐久试验尧道 路行驶载荷谱疲劳模拟试验和实际道路试验等 4 种遥 其中道路行驶载荷谱疲劳模拟试验和实际道路 试验由于试验周期长尧成本高袁一般不适用于零件的 前期开发曰 定幅值耐久试验未考虑对零件在不同载 荷下的疲劳性能袁 不能真实反映零件在实际道路试 验中的受载情况曰 而基于道路行驶载荷谱的 Block 耐久试验则将实际道路行驶载荷谱合理转换为变载 荷序列袁因而具有试验精度高尧试验周期短等优点遥
106
107
寿命
图 7 橡胶材料典型应变-寿命曲线
拟合方程为院
Y =A窑XB
渊1冤
式中, Y 为疲劳评价参数袁 即最大主应变曰X 为疲
劳寿命曰A 尧B 为疲劳参数遥
疲劳参数 A 尧B 的拟合效果通过相关系数 R2 来
评估袁若 R2跃0.9 则认为具有较好的拟合度袁即 A 尧B
可用于疲劳寿命预测遥 本文所研究橡胶试片的疲劳
变矩阵曰
c. 通过橡胶材料的应变要寿命曲线袁将应变矩
阵转换为单个循环加载下的损伤矩阵曰
d. 将单个加载循环下的损伤矩阵乘以道路行
驶载荷谱矩阵中的总循环次数袁 得到全部道路行驶
载荷谱下的总损伤矩阵遥
3.6 橡胶件道路行驶载荷谱三向相位关系确定
在正常使用工况下袁 实际底盘橡胶件同时承受
X尧Y 尧Z 3 个平动方向的载荷渊特殊零件可能还需要
损伤矩阵
有
无
判断是否有相位联系
按照相关工况循环次数创 建有相位关系道路行驶载 荷谱的损伤矩阵
按照相关工况循环次数创 建没有相位关系道路行驶 载荷谱的损伤矩阵
通过损伤等效的方法 编辑 Block 矩阵
通过损伤等效的方法 编辑 Block 矩阵
编辑后的 Block 渊多轴及单轴冤
合并 Block 矩阵 渊多轴及单轴冤
10
测试
计算
5
0
-5
-10 -6 -4 -2 0 2 4 6 加载位移/mm
渊a冤X 向
要 57 要
窑试验测试窑
10
测试
计算
5
0
-5
图4
-10 -6 -4 -2 0 2 4 6 加载位移/mm
渊b冤Y 向
10
测试
5
计算
0
-5 -10
-15 -2-010 -8 -6 -4 -2 0 2 4 6
加载位移/mm
底盘橡胶减振件的材料与结构属于非线性袁目 前国内外对底盘金属件的耐久试验研究较多[1~3]袁但 对橡胶件的道路行驶载荷谱耐久缩减研究未见公开 报道遥 为此袁 提出一种将道路行驶载荷谱缩减为载 荷序列的方法袁并以某汽车副车架衬套为试验对象袁 应用该方法在 MTS833 试验台架上采用缩减的单轴 或多轴疲劳载荷序列对其进行耐久性试验袁 并验证 了该方法的有效性遥
周期遥连续时间历程的载荷谱通过损伤等效的方
式转化为 Block 载荷序列的缩减方法流程如图 2
所示遥
道路行驶载荷
雨流统计 渊载荷冤
雨流矩阵渊载荷冤
载荷转化 为位移
雨流矩阵渊位移冤
绘制 X/Y/Z 通道道路行驶 载荷谱载荷分布图袁 查找
X/Y/Z 通道相位关联性
零件 FEA 分析 应变寿命曲线
创建损伤矩阵及计 算单个寿命下的累 积损伤
副车架衬套的静态特性有限元分析过程为院首 先根据单轴拉伸尧 双等轴拉伸和平面拉伸获得橡胶 材料在不同应变下的应力-应变曲线袁 选取合适的 橡胶材料超弹性本构模型拟合得到模型参数曰 然后 在软件 ABAQUS 中对衬套主簧区域进行网格划分袁 赋予橡胶材料属性袁施加一定位移袁获得潜在疲劳失 效区域的位移-应变曲线[4]遥
参数 A 尧B 的拟合相关系数 R2=0.916袁所以疲劳参数
A 尧B 可用于橡胶疲劳分析遥
3.5 创建损伤矩阵
根据前述分析袁橡胶件的损伤矩阵创建步骤如下院
a. 首先对橡胶件进行 FEA 分析袁得到加载点
与零件应变集中区域的位移-应变曲线袁并利用3 次
多项式公式进行拟合曰
b. 通过 3 次多项式公式将位移矩阵转换为应
应பைடு நூலகம்=0.63
图 5 某工况下副车架衬套应变云图
3.4 橡胶材料应变要寿命曲线获取 目前袁 国内外对橡胶疲劳寿命的研究主要有 2
种方法[6]袁一是裂纹成核法袁即基于连续体力学理论 在给定某些量渊如应变和应力冤的时间历程下袁预测 裂纹晶核形成的寿命;二是裂纹扩展法袁即基于断裂 力学在给定特定裂纹的初始几何形状和能量释放率 历程的条件下袁 预测特定裂纹的扩展遥 裂纹成核方 法认为某一点应力或应变历程能决定材料的固有寿 命袁 为此采用裂纹成核法获取橡胶材料在不同应变 水平下的疲劳寿命袁即所谓的应变-寿命法遥
Range 值+2/3渣Mean 值渣遥
圆园13 年 第 9 期
600 500 400 300 200 100
0 50
载荷幅值/N
-5 875 4 950 3 875
图 3 道路行驶载荷谱载荷总雨流统计直方图
3.2 载荷转化为橡胶件位移 在副车架衬套设计阶段对其静态特性有明确要
求袁通过 X尧Y 尧Z 三向非线性力-位移曲线体现遥根据 转换得到的载荷矩阵中修正后的载荷 Range 值袁以 及有限元计算得到的橡胶件的力-位移曲线袁通过插 值得到橡胶件在不同力值下的位移遥 3.3 橡胶件应变计算
考虑扭转载荷冤袁该研究中的 Z 向为整车垂直方向袁
X 向为整车纵向袁Y 向为整车侧向袁三方向符合右手
定则袁 因此需要考虑道路行驶载荷谱中不同通道间
的载荷耦合情况遥
在考虑多通道载荷耦合情况时袁 由于道路行驶
载荷谱载荷信号具有明显的非周期性袁 无法采用通
常的相关函数来判断 3 个轴向载荷信号的相关性袁
因此袁应用线性回归方法袁通过计算各通道间的相关
要 56 要
2 道路行驶载荷谱采集
利用 eDAQ ECPU-PLUS 型数据采集系统袁在标 准汽车试验场采集底盘零部件在 35 种不同工况下 的道路行驶载荷谱遥 试验用汽车副车架衬套连接方 式如图 1 所示遥 由于该副车架衬套附近空间狭小袁 若直接通过应变片或力传感器采集非常困难袁为此袁 通过采集轮胎的六分力袁 将真实的轮胎六分力加载 在 MSC.ADAMS 整车模型中袁 计算得到副车架衬套 的载荷谱袁此项工作由整车厂完成遥
编辑后的 Block 渊单轴冤
否
否
满足总循环次数要求钥
是
最终的 Block矩阵
图 2 副车架衬套 Block 耐久试验道路行驶载荷谱缩减流程
3.1 道路载荷谱雨流统计 在试验场采集的道路行驶载荷谱是一种随机载
荷谱袁 而使零件产生疲劳损伤的主要因素是载荷的 峰谷值尧 均值和载荷循环次数遥 所以在对橡胶零件 进行疲劳分析时袁 需要用计数法对随机载荷进行统 计和分析袁 本文采用雨流计数法对橡胶件载荷进行 统计遥
图 1 后副车架连接衬套示意
3 道路行驶载荷谱缩减
对副车架衬套的原始道路行驶载荷谱进行重
汽车技术
窑试验测试窑
采样尧去均值及剪辑等编辑处理后得到衬套的载荷