基于实测载荷谱的白车身疲劳寿命计算
基于CAE方法车身疲劳耐久性研究

11 局部 应 变寿 命法 (—_ 方 法) . E N
局部 应变 寿命 法 ( - 法 ) EN 是继 名 义应 力 寿命 法 (- 法) SN ,也称 为裂 纹 萌生法 。许 多汽 车零 件 设 计 为在 使 用时 处 于塑性 应 变 ,但 SN 基 本上 忽 略 . 塑 性 , 因此 用 EN 方法 更为 合适 ,能更 为准 确 的 - 模 拟应 力 集 中等 现 象所 产 生 的局 部循 环 塑性 变 形
关键词 : 白车 身:道路载荷谱 ;疲劳耐久性 中图分类 号:U4 38 U 6 . 1 文献标识码 :A 文章编号 :17 -8 12 1) 1140 6. 2 4 1 7 6 24 0 (0 20 .0 .3
当前 , 随着汽 车 工业 的发展 ,消 费者 对产 品
的安全 性 和可 靠 性 的要 求越 来 越 高 。如何 将汽 车 这 样 复杂 的机 器 在 尽量 短 的时 间周 期 内保 质保 量 的研发 出来 ,并 且 能得 到 消费 者 的认 可 是摆在 所 有 汽车 研 发机 构面 前 的难 题 。 依 传 统 的设 计 观念 ,在 研 发过 程 中 ,需 通过 反 复 的样 件 试制 和 工程 样 车试 制 ,对 部件 、 白车 身进 行大 量 的台架 试验 和 整车 疲 劳耐 久 性试 验 , 从而 验证 所 设 计产 品 万无 一 失 。但 ,这 样 的方 法
过 程 中 的塑 性应 变分 布 及 其疲 劳寿 命 进行 评 估 ,
以期为 车辆 的前期 开 发设 计提 供 理论依 据 。
Mie nr累积损 伤 理论 。 nr从 能量 的角 度 出发 , Mie
做 了如下 假 设 :试样 所 吸 收 的能量 达 到极 限值 时
1 车 身疲 劳 分 析 方 法 的基 本 概 念
基于实测路谱的动力总成壳体疲劳寿命预测

AUTOMOBILE APPLIED TECHNOLOGY2018年第6期10. 16638/ki. 1671-7988. 2018. 06. 016基于实测路谱的动力总成壳体疲劳寿命预测翟文涛W,崔勇奎2,李瑞U(1.同济大学汽车学院,上海201804; 2.中国第一汽车股份有限公司技术中心,吉林长春130011)摘要:文章介绍了基于实测试验场道路载荷谱进行动力总成壳体疲劳寿命预测的方法,通过三向加速度传感器实测可靠性试验路面上动力总成壳体悬置点位置载荷谱数据,应用nCodeDesignKfe进行有限元分析软件,考虑对材料的S-N曲线进行修正,进行动力总成壳体模型疲劳寿命仿真预测。
根据预测的结果,得出动力总成壳体方案满足疲劳寿命仿真要求的结论。
并且得到的疲劳寿命云图,可以发现疲劳寿命薄弱位置,为结构设计和优化提供了一定的参考依据。
该方案通过了整车可靠性试验,验证了有限元分析的正确性。
关键词:动力总成壳体;载荷谱;疲劳分析;有限元分析中图分类号:U467文献标识码:B文章编号:1671-7988(2018)06-46-03Fatigue Analysis of Powertrain Shell based on the Measured Road SpectrumZhai Wentao1,2, Cui Yongkui2, Li Rui1,2(1.College of A utomotive Engineering TongjiUniversity,Shanghai201804;2.China FAW Co.,Ltd R&D Center,Jilin Changchun 130011 )Abstract: A fatigue analysis method of powertrain shell was introduced which was based on the measured road spectrum. The load spectrum data could be obtained by Three-way acceleration sensor when the truck ran on the test road.The fatiguelife of the structure was analyzed by nCode finite element analysis software.And the modification of the s-n curve of the material should be considered.lt was concluded that the powertrain shell scheme met the requirements of fatigue life by simulation results.The weak position was found which provided a good reference for the structure design and optimization of parts.Through the reliability test of the vehicle,the correctness of the finite element analysis is verified.Keywords: powertrain shell; load spectrum; fatigue analysis; finite element analysisCLC NO.: U467 Document Code: B Article ID: 1671-7988(2018)06-46-03刖g有限元分析方法在汽车方案设计中应用的越来越广泛。
浅谈某自卸车道路载荷谱采集与处理

根据相关规定,
使用相关的仪器设备对
整车进行试验路试,得 到 整 车 的 道 路 载 荷 谱 并 进 行
一系列的修正及后期的处理得到较为合理的道路载
荷谱。得到的载荷谱能够作为台架试验或者计算机
仿真分析的输入,
大大缩短了产品的研发周期,
降低
了成本,
带来了巨大的效益 [2]。
1
传感器的安装
载荷谱采集系统与传感器参考表 1 所示。
从而达到隔离现场干
计算和报表生成方面具有很强的灵活性。实时监视
每一个流量点 的 检 定 数 据、可 将 检 定 数 据 传 至 Mi
c
r
o
s
o
f
tEx
c
e
l电子 表 格 中,根 据 流 量 点 自 动 选 择 开
启不同的喷嘴组合,
完成检定过程。
[
参考文献]
[
临界流文丘里喷嘴
1] 全国流量计量技术委员会 .
尘、
防水处理;
在应变片表面涂抹特定胶水并粘贴胶
六分力传感器
布以防止测试过程中的脱落等。防护完成之后要对
六分力传感器是一个替代汽车轮辋中心部分的
传感器进行标定与调零,
并做进一步的检查与修改。
收稿日期:
2021-11-15
· 116 ·
Copyright©博看网. All Rights Reserved.
1
9 页)
· 117 ·
Copyright©博看网. All Rights Reserved.
李红艳,等 · 气体流量标准装置自动检定控制系统设计
3
技术指标
2022 年第 13 期
扰的目的。变频器 是 整 套 系 统 中 最 大 的 干 扰 源,可
基于随机载荷的白车身焊点疲劳寿命预测
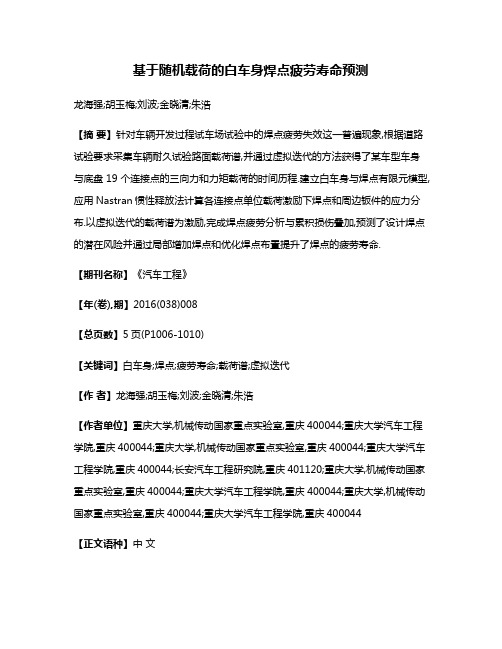
基于随机载荷的白车身焊点疲劳寿命预测龙海强;胡玉梅;刘波;金晓清;朱浩【摘要】针对车辆开发过程试车场试验中的焊点疲劳失效这一普遍现象,根据道路试验要求采集车辆耐久试验路面载荷谱,并通过虚拟迭代的方法获得了某车型车身与底盘19个连接点的三向力和力矩载荷的时间历程.建立白车身与焊点有限元模型,应用Nastran惯性释放法计算各连接点单位载荷激励下焊点和周边钣件的应力分布.以虚拟迭代的载荷谱为激励,完成焊点疲劳分析与累积损伤叠加,预测了设计焊点的潜在风险并通过局部增加焊点和优化焊点布置提升了焊点的疲劳寿命.【期刊名称】《汽车工程》【年(卷),期】2016(038)008【总页数】5页(P1006-1010)【关键词】白车身;焊点;疲劳寿命;载荷谱;虚拟迭代【作者】龙海强;胡玉梅;刘波;金晓清;朱浩【作者单位】重庆大学,机械传动国家重点实验室,重庆400044;重庆大学汽车工程学院,重庆400044;重庆大学,机械传动国家重点实验室,重庆400044;重庆大学汽车工程学院,重庆400044;长安汽车工程研究院,重庆401120;重庆大学,机械传动国家重点实验室,重庆400044;重庆大学汽车工程学院,重庆400044;重庆大学,机械传动国家重点实验室,重庆400044;重庆大学汽车工程学院,重庆400044【正文语种】中文电阻点焊以其高效率、低成本等突出优点被广泛应用于汽车等大规模薄板装配制造业,是车身装配制造关键技术之一。
通常,轿车白车身由5 000~7 000个焊点完成装配[1-2],大量的焊点不仅是白车身装配连接的需要,也是白车身承受扭转、颠簸、碰撞等条件下零部件之间载荷传递的主要途径。
由于点焊连接的离散性,在其连接位置形成几何突变,导致局部应力集中。
同时,点焊连接是复杂的物理化学过程,局部焊接板材瞬间加热熔化并以高达1 200℃/s的速度冷却形成焊核[3-4]。
该加工过程常常伴有不可避免的夹杂、孔隙[5-6]等缺陷残留在焊核区,从而影响焊点的连接强度和疲劳寿命。
基于实测道路谱的车身疲劳耐久性能改进

收稿日期:2019-12-02作者简介:张泽俊(1989 ),男,工程师,研究方向为车辆结构耐久性CAE分析㊂E⁃mail:csuftzhang@126 com㊂DOI:10 19466/j cnki 1674-1986 2020 04 004基于实测道路谱的车身疲劳耐久性能改进张泽俊,刘宗成,颜伏伍,王雪峰,冯广冬(东风小康汽车有限公司汽车技术中心,重庆402247)摘要:基于实测试验场道路载荷谱,结合多体虚拟迭代技术与CAE疲劳损伤分析技术再现某车型车身钣金和焊点疲劳失效㊂对车身结构进行改进,改进后的样车在后续可靠性试验中未出现车身疲劳失效问题㊂工程实践表明,该方法可用于车身开发过程中疲劳失效实际问题的改进,减少物理样车试验次数,节约开发成本㊂关键词:道路谱;白车身;虚拟迭代;损伤预测中图分类号:U463DurabilityImprovementofBIWBasedonMeasuredRoadSpectrumZHANGZejun,LIUZongcheng,YANFuwu,WANGXuefeng,FENGGuangdong(AutomotiveTechnicalCenter,DongfengSokonAutomobileCo.,Ltd.,Chongqing402247,China)Abstract:ThesheetmetalandweldingspotfatiguefailureinBIWwasreproducedbasedonthemeasuredroadloadspectrumandthecombinationmethodofvirtualiterationandCAEfatiguedamageanalysis.Thebodystructurewasimprovedbasedontheanalysisresults.AndthefatiguefailureinBIWnevershowedupinthesubsequentroadtests.Theengineeringpracticeindicatesthisapproachcanbeusedtoimprovethepracticalproblemsoffatiguefailure.Thetimesofexperimentcanbegreatlyreducedandalsothedevelopmentcostscanbesavedsignificantlyinthisway.Keywords:Roadspectrum;Whitebody;Virtualiteration;Fatiguedamageprediction0㊀引言面对日趋激烈的汽车市场,各大整车制造商不断延长整车质保里程或年限来提高产品竞争力,这样整车的疲劳耐久性能开发越来越受到重视㊂车身作为整车关键子系统之一,其耐久性能成为整车性能开发中的焦点之一[1]㊂车身是一切车身部件和底盘部件的安装基础,其结构和实际承受载荷的复杂多样性,给解决车身疲劳失效问题带来了极大的困难㊂一般是通过对样车进行可靠性道路试验和道路模拟试验来确保车辆达到耐久性能[2],但该手段存在开发周期长㊁资金投入大等问题㊂某新开发SUV车型,在整车道路模拟试验中,左右车身后门框处均出现钣金和焊点失效问题㊂通过试验场道路谱采集㊁建立多体动力学模型进行虚拟迭代并结合CAE疲劳分析技术,从仿真角度复现了车身疲劳失效问题,解决了车身开发过程中出现的疲劳失效问题,减少了开发成本及试验的盲目性,缩短了研发周期㊂1㊀车身失效情况简介及技术研究路线某SUV车型第一轮试制样车在整车四通道可靠性道路模拟试验完成63%时,发现左右后门框位置出现钣金开裂㊁焊点失效问题,如图1所示㊂检查发现裂纹断面存在磨损痕迹,说明车身左右侧后门框在试验小于63%时就出现了疲劳失效问题㊂意味着该SUV车身前期设计不能满足疲劳耐久性能要求,存在一定的安全隐患,需要对车身门框开裂位置进行优化设计,以达到指定的疲劳耐久性能㊂图1㊀车身门框失效通过实车在试验场采集载荷谱,并对采集的数据有效性进行检查,结合多体虚拟迭代技术和CAE分析技术再现物理试验疲劳失效点,并依据分析结果对车身结构进行改进㊂其技术路线如图2所示㊂图2㊀车身失效改进技术路线2 路谱采集及虚拟迭代2 1㊀采集工况简介采集车辆使用第一轮试制样车,在4个车轮上安装WFT六分力传感器,如图3(a)所示,采集车轮六分力信号;在车轮转向节轮心处安装加速度传感器,如图3(b)所示,采集轮心加速度信号;在前后车轮Topmount处安装加速度传感器,采集车身减震器塔顶处加速度信号;在前后减震器弹簧上布置应变计,测量前后弹簧应变信号;并安装GPS和陀螺仪,分别记录车辆行驶轨迹㊁车速和车身姿态㊂图3㊀车轮六分力传感器和轮心加速度传感器将样车配重至满载质量状态,依据路谱采集规范在某汽车试验场测量耐久试验路面(搓板路㊁卵石路㊁车身扭曲路等),GPS记录的车辆行驶轨迹如图4所示㊂图4㊀采集车辆行驶轨迹2 2㊀路谱采集结果及数据检查采集车辆布置传感器共计75个通道,各通道信号数据通过数据采集器记录和存储,每个样本采集3次㊂如图5所示,采集到的左后轮轮心的力和力矩㊂图5㊀采集到的左后轮轮心力和力矩在制动工况下,根据Fx和My的相互关系,可以判断采集到的六分力数据的正确性㊂如图6所示,左前轮在制动工况下Fx和My呈线性相关,且斜率在0 35左右,与轮胎的滚动半径一致㊂图6㊀制动力矩My和制动力Fx关系㊀㊀将采集到的4个车轮轮心Z向加速度做频谱分析,如图7所示,信号频率段主要集中在50Hz以下,与路面的激励频率一致,说明采集到的数据具备一定的有效性㊂图7㊀4个车轮轮心Z向加速度频谱2 3㊀多体虚拟迭代载荷分解采用多体虚拟迭代的方法获取车身各接附点的载荷,作为后续车身疲劳CAE分析的输入㊂将试验场采集到的载荷谱经过等效处理后,作为多体虚拟迭代的目标信号,搭建与采集样车状态一致的整车多体动力学模型,作为虚拟迭代的基础模型,如图8所示㊂图8㊀整车多体动力学模型虚拟迭代原理如图9所示,用白噪声驱动多体模型得到初始传递函数并求出反传递函数F-1,再根据试验采集的信号和反传递函数求得第一次迭代的驱动信号D1,该驱动信号再次驱动多体模型,可得到第一次的响应X1,对比X1与目标信号Xtarget,并修正公式(1)中的w,再迭代,直到满足收敛条件(Xn与Xtarget相对损伤值介于0 5 2之间[3])终止迭代㊂Dn+1=Dn+w㊃F-1㊃(Xtarget-Xn)(1)图9㊀虚拟迭代原理㊀㊀建立的多体动力学模型经过5次迭代后,迭代信号与目标信号的各通道相对损伤值范围在0 5 2之间,满足虚拟迭代精度要求㊂各次迭代收敛情况如图10所示㊂图10㊀各次迭代收敛情况通过最后一次迭代后,获取车身各接附点的力和力矩㊂图11所示为车身与后副车架连接左前接附点的力和力矩,获取的各接附点的载荷谱作为车身疲劳耐久CAE分析的输入㊂图11㊀车身与后副车架左前接附点力和力矩载荷谱3 车身疲劳CAE分析及疲劳失效再现3 1㊀车身疲劳CAE分析模型搭建搭建车身TB有限元模型,五门一罩㊁油箱㊁备胎㊁天窗等采用集中质量模拟,车身附件采用非结构质量NSM配重至钣金件上㊂车身焊点采用刚性梁Bar单元模拟[4],直径为6mm,梁单元与车身钣金件采用共节点方式连接㊂在车身18个接附点处加载六向单位载荷,共计108个通道,采用惯性释放法计算得到疲劳计算所需要的白车身结构应力场和焊点单元力场㊂3 2㊀车身疲劳损伤预测车身焊点刚性梁单元传递的力和力矩用来计算结构应力[5],基于计算的焊点结构应力对车身焊点进行疲劳损伤预测㊂焊点的材料采用Spot_Nugget_Generic和Spot_Sheel_Generic[6]㊂采用FKM法修正平均应力㊂将车身结构应力场导入疲劳分析软件,基于名义应力SN的方法,对车身进行疲劳损伤评估,其中平均应力修正采用Goodman法㊂由于车身几何形状复杂且受到多轴疲劳载荷作用,故采用临界平面法㊂临界平面法计算原理为过某点取n个等夹角的平面,对每个平面上的正应力和剪应力进行等效组合,对每个平面的等效应力计算损伤,然后取n个平面中最大损伤值为该点的损伤㊂根据车身中不同材料牌号建立不同材料的SN曲线㊂SN曲线可以通过试验获得,在缺少试验SN曲线时,可以根据材料的特性参数进行拟合得到SN曲线㊂对于母材,可以通过输入材料的抗拉极限UTS拟合得到材料应力寿命SN曲线[7],其拟合曲线如图12所示㊂图中参数SRI1㊁b1和b2通过公式(2) (5)计算得到㊂图12㊀基于UTS拟合的SN曲线SRI1=2ˑS2/(Nc1)b(2)b1=[log(S2)-log(S1)]log(Nc1)-3(3)b2=b1(2+b1)(4)S1=0 9ˑUTS;S2=0 357ˑUTS(5)式中:UTS为材料抗拉强度;S1为1000次循环下的应力幅值;S2为Nc1循环次数下的应力幅值;SRI1为循环1次即失效时的应力幅;b1和b2分别为SN曲线第一阶段和第二阶段的斜率;Nc1为SN曲线第一个拐点的循环次数,对于普通钢材材料Nc1一般取1ˑ106㊂设置好疲劳分析参数后,在疲劳分析软件中对车身焊点和钣金进行疲劳损伤计算,计算得到损伤结果如图13所示㊂可以看出:门框拐角处焊点的损伤均大于目标值1,最大损伤达到5 2(经验表明车身焊点损伤值高于1即存在失效风险);门框钣金的最大损伤为0 246(经验表明钣金处损伤值高于0 2即存在开裂风险)㊂分析结果表明:门框焊点㊁钣金失效位置与道路模拟试验失效位置一致㊂图13㊀车身焊点和钣金损伤计算结果3 3㊀车身结构改进依据上述分析结果,延长门槛梁加强板结构,并增加焊点,增加门框局部刚度,车身结构改进示意如图14所示㊂图14㊀车身结构改进示意对改进后的车身结构重新计算疲劳损伤,如图15所示㊂改进后的车身疲劳失效点的损伤远低于目标值,疲劳耐久性能得到显著提高㊂在后续的可靠性试验中,未发现门框处的焊点和钣金失效问题㊂图15㊀车身结构改进后损伤计算结果4㊀结束语以某白车身为研究对象,以实测试验场载荷谱作为多体虚拟迭代的输入,获取车身各硬点载荷谱,并结合CAE疲劳损伤预测方法,复现了可靠耐久试验中车身疲劳失效问题㊂针对车身失效位置提出了改进方案,改进后的车身失效位置的疲劳损伤值显著降低,并在后续的可靠耐久试验中未出现疲劳失效问题㊂实践表明,通过该方法预测的疲劳风险点与物理样车试验风险点比较吻合㊂该方法可用于车身开发过程中实际疲劳失效问题的改进,也可用于产品开发阶段车身的疲劳损伤预测,以此减少试验验证的盲目性,节约开发成本㊂参考文献:[1]黄金陵.汽车车身设计[M].北京:机械工业出版社,2007.[2]林育正,毛庆平.建立整车疲劳寿命分析技术的程序方法[J].车辆研测资讯,2005(3):20-27.[3]RYUS.Astudyonobtainingexcitationloadofvirtualtestlabusingvirtualiterationmethod[R].SAEPaper,2010-01-0011,2010.[4]龙海强,胡玉梅,刘波,等.基于随机载荷的白车身焊点疲劳寿命预测[J].汽车工程,2016,38(8):1006-1010.LONGHQ,HUYM,LIUB,etal.Fatiguelifepredictionforthespotweldsofbody⁃in⁃whitebasedonrandomloadings[J].AutomotiveEngineering,2016,38(8):1006-1010.[5]杜中哲,朱平,何俊,等.基于有限元法的轿车车身结构及焊点疲劳寿命分析[J].汽车工程,2006(10):944-947.DUZZ,ZHUP,HEJ,etal.FatiguelifeanalysisofcarbodystructureandspotweldbasedonFEM[J].AutomotiveEngineering,2006(10):944-947.[6]郜慧超.某重型载货汽车车架的疲劳分析及优化[D].北京:北京理工大学,2016.[7]毛显红,肖攀,陈建华,等.基于道路谱的汽车车身疲劳分析[J].计算机辅助工程,2011,20(2):75-78.MAOXH,XIAOP,CHENJH,etal.Automotivebodyfatigueanalysisbasedonroadspectrum[J].ComputerAidedEngineering,2011,20(2):75-78.L3级自动驾驶难落地?针对场景开发,发挥OTA价值是正解当前,L2级自动驾驶技术已经实现大规模的商业化运用,进一步向上突破,实现L3及以上自动驾驶汽车落地,成为了行业共同努力的方向㊂但同时也有一些车企宣称直接跃过L3级别,投入L4级自动驾驶的研发和量产㊂在自动驾驶领域,以腾讯为代表的软件和云服务提供方,对于量产落地的实现路径,有怎么样的投入和布局?日前,腾讯自动驾驶产品负责人王明明,分享了腾讯对自动驾驶落地应用的破局思路㊂从需求出发让用户早日体验到自动驾驶的便利性以用户的需求为出发点,提供场景化的自动驾驶服务,解决用户痛点,分场景㊁分需求逐步实现自动驾驶落地㊂解决高速场景中的自动驾驶,就可以在很大程度上满足用户解放双手的需求㊂另外,高速和封闭的城市快速路,道路地面标识相对清晰,路况相对简单,可以成为自动驾驶落地应用的第一步㊂除了高速和快速路,泊车也是在目前道路条件下可以比较快速实现的辅助驾驶场景㊂从2019年开始,腾讯自动驾驶团队针对高速及泊车场景进行了产品化开发,并预计在今年下半年推出针对这两种场景的自动驾驶量产解决方案,以分场景㊁分需求的方式逐步推动自动驾驶功能的量产落地㊂充分发挥腾讯的算法和云服务的优势,通过OTA让用户体验持续升级腾讯认为,实现数据闭环是自动驾驶系统不断优化的关键㊂在车辆硬件条件满足㊁算力保证的基础之上,腾讯可以结合自身的软件能力和云服务的优势,通过数据回传,尤其是cornercase的累积,实现算法的不断优化㊂经过OTA升级的方式更新软件,不断向用户开放更多自动驾驶能力,形成良性循环,为用户及车企合作伙伴带来持续的价值㊂软件定义汽车,差异化创造价值在数字化浪潮下,软件定义汽车的说法一再被提及,汽车电子软件爆炸式增长,随之而来的就是电子电气构架的变革㊂集中式架构取代传统的分布式架构,已经成为汽车电子电气架构公认的未来㊂集中式架构是方向,但是真正实现用一个或几个 大脑 来操控全车,面临着不少的挑战㊂硬件架构日趋相同,功能/体验的差异化更多通过软件的差异化实现㊂AI㊁大数据㊁云计算的发展,带来千人千面的定制化体验的潜力,使产品在硬件之外的增值变为可能㊂在这个过程中,腾讯希望聚焦自动驾驶软件,充分发挥自身的算法优势,提供模块化软件解决方案,做好数字化的工具箱,为合作伙伴提供助力㊂新基建推动产业互联网发展腾讯自动驾驶驶入快车道智慧出行领域,特别是自动驾驶产业链庞大且复杂,量产落地需要技术+政策+产业链共同驱动㊂腾讯一直在跟踪自动驾驶相关法规的进展,并力求在法规允许的范围内,为用户提供更好的产品体验㊂与此同时,腾讯也在积极推进法规建设㊂目前,腾讯正在与国家智能网联汽车(长沙)测试区㊁北京智能车联创新中心等行业机构密切合作,提升自动驾驶汽车的测试效率,共同探索测试评价的配套升级㊂自动驾驶和智能网联汽车领域将成为这一轮新基础建设加速的重点落地场景之一,腾讯自拥抱产业互联网以来,也早已布局了包含5G网络应用㊁车联网㊁自动驾驶等领域的智慧出行业务版图,连接丰富的出行服务生态,与政府部门㊁车企乃至整个汽车行业展开深入的合作,发挥自身的用户服务和生态连接能力,为智慧出行产业发展提供助力㊂(来源:互联网)。
基于实测载荷谱的副车架疲劳寿命估算方法

基于实测载荷谱的副车架疲劳寿命估算方法副车架是汽车底盘的一部分,是连接车轮、传动系统和悬架系统的主要构成部分。
它不仅要支撑整个汽车的重量,还要承受路况不良和载荷变化造成的负荷。
因此,副车架的疲劳寿命是汽车安全性和使用寿命的重要因素。
本文将讨论一种基于实测载荷谱的副车架疲劳寿命估算方法。
首先,测量和记录副车架在不同驾驶情况下的载荷变化。
它可以通过安装传感器来完成,该传感器可以记录副车架在不同路面、加速、刹车和转向等情况下的荷载。
这些测量结果可以作为载荷谱输入到疲劳寿命估算模型中。
其次,根据实验室测定得到的应力奋斗历程进行疲劳寿命试验,以获得副车架在该应力状况下的疲劳寿命。
然后可以使用疲劳寿命测试数据建立基于副车架所受载荷的疲劳寿命曲线,以估算不同载荷情况下副车架的疲劳寿命。
最后,将谱法理论应用于载荷谱中的副车架负载,得到当期载荷对应的等效疲劳载荷,并应用于副车架疲劳寿命曲线中以估算副车架的疲劳寿命。
根据所得到的结果,可以给出推荐的维护和更换周期。
然而,该方法存在的主要问题是,载荷谱的随机性质使得结果存在一定的误差。
此外,由于不同车辆的操作条件和使用环境不同,因此需要考虑实测数据的个体差异。
因此,建立一个可重复性高、可靠性强的疲劳寿命估算方法是当前研究的重点。
综上所述,随着计算机技术的不断发展,副车架的疲劳寿命估算方法将不断完善。
应在实践中运用合理的负载谱获取方法并结合疲劳寿命测试结果,以实现对汽车底盘的安全使用和长寿命的保障。
除了基于实测载荷谱的副车架疲劳寿命估算方法之外,还有一些其他方法可以用来评估副车架的疲劳寿命。
例如,可以使用计算机模型来模拟驾驶循环,并预测副车架在不同载荷下的应力状态。
它可以基于模拟结果建立疲劳寿命模型,以估算副车架的疲劳寿命。
此外,还可以使用裂纹扩展方法,以测定裂纹在副车架上扩展的速度。
通过中断试验,可以根据49CFR 393.207标准来估算副车架的疲劳状态,以确定是否需要维修或更换。
基于真实路谱的汽车疲劳寿命开发试验技术
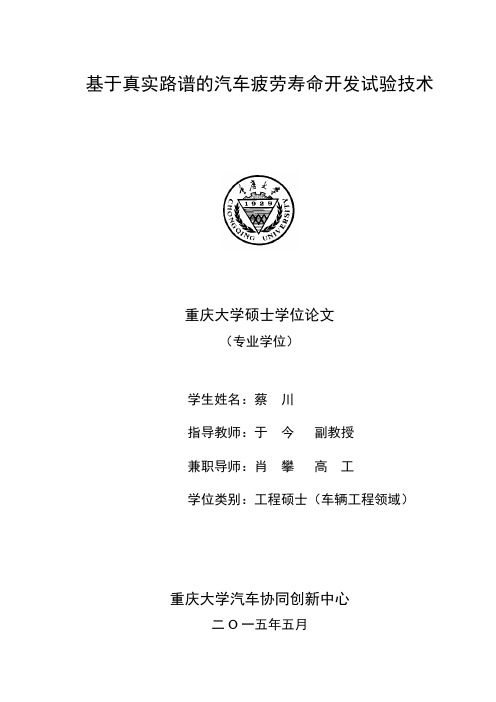
基于真实路谱的汽车疲劳寿命开发试验技术重庆大学硕士学位论文(专业学位)学生姓名:蔡*指导教师:于今副教授兼职导师:肖攀高工学位类别:工程硕士(车辆工程领域)重庆大学汽车协同创新中心二O一五年五月The development of automotive fatigue life test technique based on the real road loadspectrumA Thesis Submitted to Chongqing Universityin Partial Fulfillment of the Requirement forProfessional DegreeByCai ChuanSupervised by Assistant Prof.Yu JinPluralistic Supervised by Senior Eng.Xiao PanSpecialty:ME( Vehicle Engineering Field)Automotive Collabarative Innovation Center ofChongqing University , Chongqing, ChinaMay 2015中文摘要摘要随着人们生活水平的提高,人们对汽车的需求量也越来越大。
与此同时,人们对汽车的品质、性能、外形等各方面提出了更严苛的要求。
对于大多数人来说汽车的使用年限是其关注的重中之重。
这也是各大汽车厂商展示自己产品品质的关键。
汽车的疲劳耐久性设计不仅对汽车的使用寿命有积极的意义,同时也对汽车的安全可靠性有重大的意义。
它是汽车行业所面对的重大课题之一。
因而,各大汽车公司和科研院所积极展开了对汽车结构的疲劳耐久寿命的研究。
通常评估其疲劳寿命采用的方法大致有三种方法:实车道路试验、台架试验以及计算虚拟疲劳试验。
实车道路试验通过在强化路面上连续行驶来验证整车及其零部件的疲劳寿命,它在车辆开发阶段有着重要意义。
基于虚拟样机技术的微型客车白车身疲劳寿命分析

[] 6 史敬灼. 电动机伺服控制技术 [ . 步进 M] 北京 : 出版社 , 0 . 科学 2 6 0
第 6期
阮晓亮等: 基于虚拟样机技术的微型客车白车身疲劳寿命分析
17 9
动机 、 车身等子 系统经各种力学铰链 和减震 弹簧 、 阻尼器及橡胶 相应力和力矩的载荷时间历程 , 6 条 白车身载荷谱。 共 0 载荷提取 元 件连 接 而成 的 复杂 多体 系统 。基 于 动力 学 仿 真分 析平 台 点包括前悬架与车身相连处 、副车架与车身连接处及板簧前 、 后 A a  ̄ a, d m C r参考整车拓扑关系 , 按子结 构建模技术 , 已有模板 吊耳铰接处 , 在 部分载荷谱 , 如图 4 所示 。 基础上 通过输入该车型各组件的物理性 能参数 , 括其 质量 、 , 包 质心位置、 惯性主轴 、 转动惯量 、 惯性积等即可得到整车多体系统 动力学仿真模型。 除白车身外 , 为更好的反映该车的底盘 陛能 , 对 前悬挂横 向稳定杆和后板簧件均作柔性体处理 ,其 他部件为 刚 体。 最终建成整车虚拟样机模型 , 如图 1 所示 。 包括 6 3个部件 , 满 载质量为 10 k 。 0 g 8
析时 , 首先对白车身进行结构应力场计算 , 获取单位载荷下的弹性 应力应变响应,然后用近似修正法将弹性响应修正至弹塑性响应 ,
22 时域路 面生成模 型和载荷 谱的提取 .
0 0 O 0 0
在载荷历程作用下 参考汽车可靠『行驶试验方法( BI2 7 _0 中道路试验条 对照材料的疲劳 陛能数据和疲劳积累损伤理论 , 生 G ,1 6 8J ) 1 9
机 械 设 计 与 制 造
l6 9 文章编号 :O t 3 9 ( 0 20 — 16 0 lO 一 9 7 2 1 )6 0 9 — 3 Ma h n r De in c iey sg & Ma u a t r n f cu e
某铝制乘用车白车身疲劳寿命计算
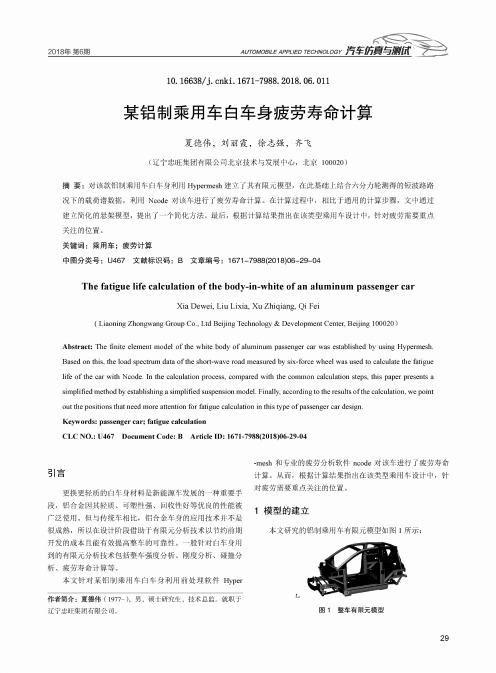
2018年第6期 AUTOMOBILE APPLIED TECHNOLOGY 汽辛仿真与‘10. 16638/ki. 1671-7988. 2018. 06. Oil某铝制乘用车白车身疲劳寿命计算夏德伟,刘丽霞,徐志强,齐飞(辽宁忠旺集团有限公司北京技术与发展中心,北京100020)摘要:对该款铝制乘用车白车身利用Hypermesh建立了其有限元模型,在此基础上结合六分力轮测得的短波路路 况下的载荷谱数据,利用N code对该车进行了疲劳寿命计算。
在计算过程中,相比于通用的计算步骤,文中通过 建立简化的悬架模型,提出了一个简化方法。
最后,根据计算结果指出在该类型乘用车设计中,针对疲劳需要重点 关注的位置。
关键词:乘用车;疲劳计算中图分类号:U467文献标识码:B文章编号:1671-7988(2018)06-29-04The fatigue life calculation of the body-in-white of an aluminum passenger carXia Dewei, Liu Lixia, Xu Zhiqiang, Qi Fei(Liaoning Zhongwang Group Co.,Ltd Beijing Technology&Development Center,Beijing100020)Abstract: The finite element model of the white body of aluminum passenger car was established by using Hypermesh.Based on this,the load spectrum data of the short-wave road measured by six-force wheel was used to calculate the fatigue life of the car with Ncode.In the calculation process,compared with the common calculation steps,this paper presents a simplified method by establishing a simplified suspension model.Finally,according to the results of t he calculation,we point out the positions that need more attention for fatigue calculation in this type of passenger car design.Keywords: passenger car; fatigue calculationCLC NO.: U467 Document Code: B Article ID: 1671-7988(2018)06-29-04引言更换更轻质的白车身材料是新能源车发展的一种重要手 段,铝合金因其轻质、可塑性强、回收性好等优良的性能被 广泛使用。
基于道路载荷谱的车身疲劳寿命改进研究
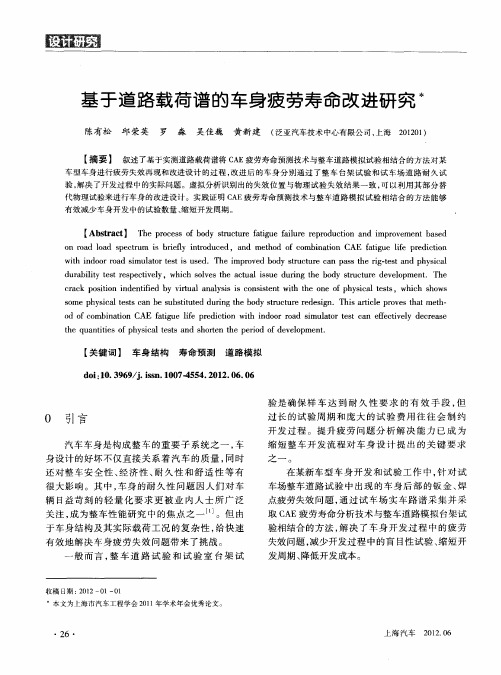
整 车室 内道 路 模 拟试 验 分 为轮 耦 合 型道路 模 拟 试验 和轴 耦 合型 道 路模 拟 试 验 两种 类 型 。失 效
位 置 的损 伤 贡献 分 析 结 果 表 明 , 身 失 效 位 置 处 车 占比 9 % 以上 的损 伤 发生在 以垂 向激励 为 主 的各 8 种 粗糙 路 面上 , 因此 本 课 题 中采 用 轮 耦 合 方 式 的
目
—
架试 验加 载信 号 驱 动 台架 , 各 监 测 点 处 采 集 应 在 变响 应信 号 , 后 与 实 际道 路 上 采 集 的 信 号进 行 然 比较 , 图 3所 示 , 算 出误 差 信 号 , 此 修 正 驱 如 计 据
动信 号并 再 次 完 成 加 载 , 此 循 环 下 去 。当迭 代 如 点 响应 与 目标 之 间 的 误 差 达 到 允 许 范 围之 内 时 ,
9 % 以 上 的粗 糙 路 面 采 集 的 信 号 进 行 迭 代 , 流 8 其
程 图见 图 2 。
1 代1 r嘉 模 _ 嚣 拟I . 迭- 1 - ' 膝 等
图 1 车 身 开 裂 研 究 技 术 路 线
2 1 典型 路面 道路 谱 采集 .
研 究 过 程 中采 用 虚拟 试 验 台 的形 式来 建 立 目 标 车辆 的耐 久 性 虚 拟 分 析 模 型 , 虚 拟 模 型 的边 该
界输 入 条件 为轮 轴 六 分 力 信 号 和轮 轴 位 移 信 号 , 而 此信 号必 须 通 过 实 车 的道 路 载 荷 谱 采 集 得 到 。
此外 , 虑 到后期 室 内道 路 模 拟 试 验 和 C E耐久 考 A
分 析 的需要 , 车 场 道 路 试 验 采 集 的 信 号 包 括 车 试
车身的模态分析及疲劳寿命计算

车身的模态分析及疲劳寿命计算毛彩菊1,王艳2【摘要】为了能够有效地分析车身的动态性能和疲劳寿命,利用有限元技术对车身进行了模态分析和疲劳寿命计算。
首先,总结了车身的有限元模型建立的措施;接着,归纳了模态分析和疲劳寿命计算的理论方法;然后,对车身进行了模态分析,求出了该车车身的前6阶固有频率和对应的振型,并进行了实验验证,提出了该车车身的动态性能。
最后,对该车车身进行了疲劳寿命计算,并且和实际情况比较吻合,为车身的进一步的优化设计提供了有利地理论依据。
【期刊名称】制造业自动化【年(卷),期】2011(033)011【总页数】5【关键词】车身;模态分析;疲劳分析0 引言随着对汽车舒适性要求的不断提高,汽车的振动逐渐成为人们所关注的重要指标之一。
对承载式轿车车身,其动力学特性很大程度地影响着整车的平顺性,用计算机分析以及通过试验辨识车身的动态性能,并根据实验结果提出相应的优化设计方案,是提高汽车平顺性的关键。
模态分析是动态分析的前提,是动态分析的主要组成部分。
对车身进行模态分析可以了解车身对激振力的响应,从而对车身优化设计方案的动态特性进行分析,是车身设计过程中关键的设计环节。
过去研究车身结构的模态特性通常利用试验模态方法,该方法的缺点是耗时多、实验方法复杂、实验耗资多,无法满足车身的设计和开发初期就对乘坐舒适进行控制和评价的要求。
有限元技术作为一种新兴的技术正在不断地发展,为车身的开发设计提供了有效的模态分析的方法,为控制车身的固有频率与振型提供了技术支持。
依据模态分析理论,对于大型的结构,只需求出前几阶固有频率和相应的振型,因为对车身动力特性影响最大的是低阶振动。
利用有限元分析平台ANSYS软件对车身进行模态分析,并对其动态特性进行评价。
另外,汽车的疲劳寿命计算也是提高整车性能重要因素,利用有限元技术对车身进行疲劳寿命评估是一种高效的方法,通过车身疲劳寿命的计算,可以为车身的优化设计提供有利的理论依据。
基于CAE方法车身疲劳耐久性研究

机电技术 2012年2月104作者简介:宋名洋(1981-),男,工程师,研究方向:虚拟仿真系统在整车研发中的应用和二次开发。
基于CAE 方法车身疲劳耐久性研究宋名洋(东南(福建)汽车工业有限公司研发中心,福建 福州 350119)摘 要:基于试验场实车测量的某乘用车在标准工况下的载荷谱数据,结合多体动力学计算、有限元的非线性强度分析和MSC. Fatigue 疲劳分析等多种CAE 分析手段,对该乘用车白车身在实测载荷谱作用下的疲劳寿命进行计算分析。
同时,总结出了一套符合真实工况的试验和虚拟分析相结合的白车身一体化疲劳分析流程。
关键词:白车身;道路载荷谱;疲劳耐久性中图分类号:U463.82 U461.7+1 文献标识码:A 文章编号:1672-4801(2012)01-104-03当前,随着汽车工业的发展,消费者对产品的安全性和可靠性的要求越来越高。
如何将汽车这样复杂的机器在尽量短的时间周期内保质保量的研发出来,并且能得到消费者的认可是摆在所有汽车研发机构面前的难题。
依传统的设计观念,在研发过程中,需通过反复的样件试制和工程样车试制,对部件、白车身进行大量的台架试验和整车疲劳耐久性试验,从而验证所设计产品万无一失。
但,这样的方法在导致整车的开发成本居高不下的同时,整个开发周期也很长,同时往往无法抓住“病根”,一旦批量化后会出现再次反复修改的现象。
为能有效的节省汽车研发成本、有效缩短汽车研发时间。
全球汽车业已在全面推行汽车有限元疲劳耐久性分析方法,通过有限元疲劳分析在产品设计初期对整车的强度耐久性进行预测,找到结构的薄弱环节,提出合理的改进方案。
在汽车工业相对发达的国家已经建立了适当的分析方法和流程,在产品的研发过程中发挥了越来越重要的作用。
目前,我国汽车行业有限元疲劳耐久性分析领域起步较晚、水平较低,严重滞后于我国汽车工业的发展速度。
因此,加快汽车领域有限元耐久性分析的研究和应用迫在眉睫。
本文以某车型前半车身疲劳耐久性为例,阐述了如何利用MSC.ADAMS 、LS-DYNA 以及MSC.Fatigue 软件E-N 法和Miner 累积损伤理论对汽车基于全仿真过程的疲劳耐久性分析,预测过程中的塑性应变分布及其疲劳寿命进行评估,以期为车辆的前期开发设计提供理论依据。
基于实测载荷谱的白车身疲劳寿命计算

基于实测载荷谱的白车身疲劳寿命计算
朱涛;宋健;李亮
【期刊名称】《汽车技术》
【年(卷),期】2009(000)005
【摘要】通过六分力轮测试系统实测了某型乘用车在试车场运行的载荷谱数据,以此作为输入,并综合有限元分析、多体动力学分析和疲劳分析等多种CAE手段,对该乘用车白车身在实测载荷谱作用下的疲劳寿命分布进行了计算分析.同时,给出了符合真实工况的试验与虚拟相结合的白车身一体化疲劳分析流程,该流程同样适用于底盘零部件的疲劳分析.
【总页数】4页(P8-11)
【作者】朱涛;宋健;李亮
【作者单位】清华大学,汽车安全与节能国家重点实验室;清华大学,汽车安全与节能国家重点实验室;清华大学,汽车安全与节能国家重点实验室
【正文语种】中文
【中图分类】U462.3+6
【相关文献】
1.某铝制乘用车白车身疲劳寿命计算 [J], 夏德伟;刘丽霞;徐志强;齐飞
2.基于实测载荷谱和仿真载荷谱的底盘疲劳分析及对比 [J], 荣兵;肖攀;周建文
3.实测道路载荷谱在新开发车型车身疲劳分析中的应用 [J], 宋自力; 徐余平
4.基于实测载荷谱的双叉臂悬架下摆臂疲劳寿命预测 [J], 马良灿;纪浩;符琳;李小
珊;覃宝海
5.基于实测数据的飞-续-飞疲劳载荷谱研究 [J], 霍文辉;孙小平;付友波
因版权原因,仅展示原文概要,查看原文内容请购买。
基于实测载荷的汽车变速器壳体疲劳寿命预测方法

基于实测载荷的汽车变速器壳体疲劳寿命预测方法
程凯华
【期刊名称】《汽车零部件》
【年(卷),期】2022()8
【摘要】汽车变速器壳体的疲劳寿命直接影响汽车传动系的疲劳可靠性,针对目前对汽车变速器壳体的疲劳寿命关注过少,未结合实际道路行驶负载导致无法准确地预估汽车变速器壳体的疲劳寿命。
运用有限元分析手段合理选取壳体应力测点,依托搭建的变速器壳体数据采集系统在某国内试验场实车采集动态载荷谱;依据频域特征分析对载荷进行数据处理,提取典型路面的特征值进行统计分析,运用雨流计数技术得到路面激励的雨流循环矩阵;之后对壳体的S-N曲线修正方法进行了深入分析与研究。
在此基础上,根据Miner线性损伤累计理论,准确预测了基于实际用户路面的变速器壳体的疲劳寿命约为1.258×10^(5) km,对壳体可靠性分析及局部结构优化具有重要的工程应用价值。
【总页数】5页(P6-10)
【作者】程凯华
【作者单位】招商局检测车辆技术研究院有限公司
【正文语种】中文
【中图分类】U467.3
【相关文献】
1.基于实测载荷谱的副车架疲劳寿命估算方法
2.基于实测路谱的动力总成壳体疲劳寿命预测
3.基于实测载荷谱的双叉臂悬架下摆臂疲劳寿命预测
4.基于实测载荷谱的电动汽车减速器齿轮疲劳寿命预测
5.基于实测载荷的收获机的风机疲劳寿命预测
因版权原因,仅展示原文概要,查看原文内容请购买。
基于载荷谱的电池包疲劳试验与计算方法

基于载荷谱的电池包疲劳试验与计算方法上官文斌;岳炼;吕辉;周孚鹏【期刊名称】《华南理工大学学报(自然科学版)》【年(卷),期】2024(52)3【摘要】电池包作为电动汽车的核心部件之一,对电动汽车的整车性能有着关键性的影响。
而在电动汽车的运行过程中,电池包会不断受到来自路面的持续性冲击力,造成电池包的疲劳损坏,对驾驶员和乘客的安全以及整车性能造成一定的影响。
本文以电动汽车电池包为研究对象,建立了电池包随机振动试验方法与疲劳寿命的计算方法。
先对振动台、工装夹具和电池包进行扫频分析,得到振动台台面、夹具空载端板、电池包与工装夹具连接端板处的加速度传感器的测量数值与输入扫频加速度值保持一致,验证振动信号的有效传递,确保输入的振动信号能够准确传递至电池包,然后开展电池包随机振动试验。
并对电池包进行了电芯性能检测、气密性检查、绝缘电阻检查和共振频率检查,得出电池包的损伤部位。
研究了电池包疲劳损伤计算方法,对电池箱、电池模组和电池包内各连接方式进行了精细化建模。
基于精细化模型,进行了电池包频响特性的计算。
基于计算得到的频响特性和实车路谱采集试验得到电池包随机振动载荷谱曲线,采用Goodman疲劳寿命估算方法和Miner 线性累积损伤法则,并结合电池包材料S-N曲线,对电池包进行了随机振动疲劳损伤分析。
试验得到的电池包结构损伤部位与分析得到的失效部位具有较好的一致性,证实了本文提出的疲劳损伤计算方法的准确性。
【总页数】7页(P50-56)【作者】上官文斌;岳炼;吕辉;周孚鹏【作者单位】华南理工大学机械与汽车工程学院;祥鑫科技股份有限公司【正文语种】中文【中图分类】U461.7【相关文献】1.基于试验场真实载荷谱的悬架疲劳试验研究2.基于实测载荷谱和仿真载荷谱的底盘疲劳分析及对比3.基于疲劳损伤谱的动力电池包振动标准分析*4.基于实测道路谱的纯电动轻卡电池包支架动态载荷仿真及疲劳分析5.基于实测载荷谱的板簧衬套载荷提取及台架疲劳试验因版权原因,仅展示原文概要,查看原文内容请购买。
基于实测载荷谱的C80车体疲劳寿命评估

基于实测载荷谱的C80车体疲劳寿命评估
张福田;辛民;陈萌;王曦;李强;邵文东;姚海
【期刊名称】《铁道机车车辆》
【年(卷),期】2017(037)001
【摘要】结合神华集团C80万吨列车车体载荷谱实测试验,编制了符合神华集团自有铁路线路特征的车体垂向、纵向、侧滚和扭转载荷谱.基于AAR标准中疲劳损伤计算方法和焊接接头疲劳特性,计算不同编组位置车辆关键部位损伤值,基于此评估C80车体关键部位疲劳寿命.通过对比载荷谱下损伤和实测应力损伤并优化载荷谱校准系数,使载荷谱符合实际工程运用要求.
【总页数】6页(P34-39)
【作者】张福田;辛民;陈萌;王曦;李强;邵文东;姚海
【作者单位】中国神华能源股份有限公司,北京100011;神华铁路货车运输有限责任公司,北京100011;北京交通大学机械与电子控制工程学院,北京100044;北京交通大学机械与电子控制工程学院,北京100044;北京交通大学机械与电子控制工程学院,北京100044;中车齐齐哈尔车辆有限公司大连研发中心,黑龙江齐齐哈尔161002;中车齐齐哈尔车辆有限公司大连研发中心,黑龙江齐齐哈尔161002
【正文语种】中文
【中图分类】U270.1+4
【相关文献】
1.基于英国标准的碳钢客车车体\r结构疲劳寿命评估 [J], 谢素明;苑忠华;张相宁
2.基于实测载荷谱和仿真载荷谱的底盘疲劳分析及对比 [J], 荣兵;肖攀;周建文
3.基于结构应力法的车体结构疲劳裂纹扩展与剩余寿命评估 [J], 杨海宾;朱涛;肖守讷;阳光武;杨冰
4.基于主S-N曲线法的车体疲劳寿命评估 [J], 陈秉智;滕飞
5.基于多体动力学模型的车身载荷谱获取及疲劳寿命评估 [J], 丁文敏
因版权原因,仅展示原文概要,查看原文内容请购买。
基于实测载荷谱的副车架疲劳寿命估算方法
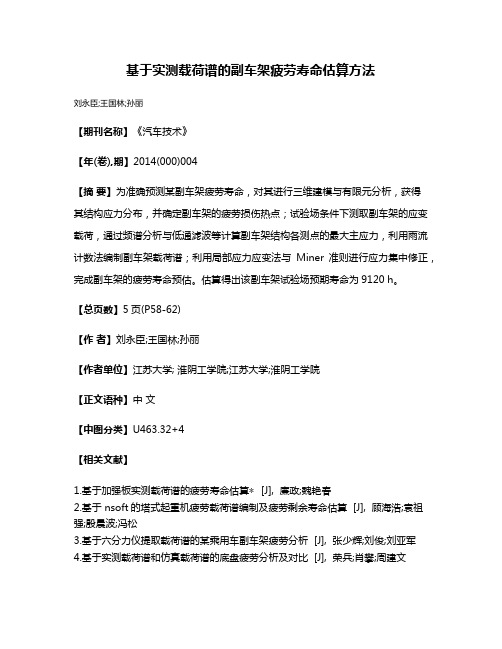
基于实测载荷谱的副车架疲劳寿命估算方法
刘永臣;王国林;孙丽
【期刊名称】《汽车技术》
【年(卷),期】2014(000)004
【摘要】为准确预测某副车架疲劳寿命,对其进行三维建模与有限元分析,获得
其结构应力分布,并确定副车架的疲劳损伤热点;试验场条件下测取副车架的应变载荷,通过频谱分析与低通滤波等计算副车架结构各测点的最大主应力,利用雨流计数法编制副车架载荷谱;利用局部应力应变法与Miner准则进行应力集中修正,完成副车架的疲劳寿命预估。
估算得出该副车架试验场预期寿命为9120 h。
【总页数】5页(P58-62)
【作者】刘永臣;王国林;孙丽
【作者单位】江苏大学; 淮阴工学院;江苏大学;淮阴工学院
【正文语种】中文
【中图分类】U463.32+4
【相关文献】
1.基于加强板实测载荷谱的疲劳寿命估算∗ [J], 廉政;魏艳春
2.基于 nsoft的塔式起重机疲劳载荷谱编制及疲劳剩余寿命估算 [J], 顾海浩;袁祖强;殷晨波;冯松
3.基于六分力仪提取载荷谱的某乘用车副车架疲劳分析 [J], 张少辉;刘俊;刘亚军
4.基于实测载荷谱和仿真载荷谱的底盘疲劳分析及对比 [J], 荣兵;肖攀;周建文
5.基于人工神经网络获取起重机当量载荷谱的疲劳剩余寿命估算方法 [J], 范小宁;徐格宁;王爱红
因版权原因,仅展示原文概要,查看原文内容请购买。
基于载荷谱的轿车后车身耐久性能分析

基于载荷谱的轿车后车身耐久性能分析柳亮;王峰;史建鹏【摘要】This paper focused on the rear part of the body's durability of the vehicle which developed by the technological center, the multi-body dynamics model was established to calculate the load spectral by extracting suspension attachment forces which measured by the six force measuring instrument. Then the BIW and weld finite element model was established followed. The fatigue analysis software FEMFAT was used to calculate the durability life and the analyzed durability results was marked with the competing vehicle and tests finally. This analysis proposed in this paper provides an effective way of BIW's durability prediction and improvement.%本文以中心开发的乘用车后车身的疲劳耐久特性作为研究对象,截取整车后半部分白车身建立有限元模型,以实测车轮六分力载荷谱经多体动力学仿真分析输出的后悬架安装点激励作为疲劳计算的载荷输入。
在此基础上,通过疲劳仿真分析软件FEMFAT分别对开发车与竞品车后车身疲劳寿命进行了对比分析,并将仿真分析结果与试验结果进行了对标,为该乘用车车身的设计开发及改进提供重要依据。
- 1、下载文档前请自行甄别文档内容的完整性,平台不提供额外的编辑、内容补充、找答案等附加服务。
- 2、"仅部分预览"的文档,不可在线预览部分如存在完整性等问题,可反馈申请退款(可完整预览的文档不适用该条件!)。
- 3、如文档侵犯您的权益,请联系客服反馈,我们会尽快为您处理(人工客服工作时间:9:00-18:30)。
基于实测载荷谱的白车身疲劳寿命计算
朱涛1 林晓斌2
1上海山外山机电工程科技有限公司
2英国恩科(nCode)国际有限公司上海代表处
基于实测载荷谱的白车身疲劳寿命计算
朱涛1 林晓斌2
1上海山外山机电工程科技有限公司
2英国恩科(nCode)国际有限公司上海代表处
摘要:汽车白车身疲劳分析由于缺乏真实载荷谱的输入而显得没有说服力,计算分析的结果往往与试车场或用户使用时发生的失效没有关联,这样导致了虚拟疲劳分析的强大作用无法发挥。
本文通过六分力轮测试系统实测了某型乘用车在试车场的载荷谱数据,以此作为输入,并综合了多种CAE手段,包括有限元网格划分、有限元分析、多体动力学分析和疲劳分析,对该乘用车的白车身在实测载荷谱作用下的疲劳寿命分布进行了计算分析,获得了有价值的结果。
同时给出了更符合真实工况的试验与虚拟相结合的白车身一体化疲劳分析流程。
关键词:白车身,虚拟疲劳分析,道路载荷谱,有限元网格划分,有限元分析,多
体动力学分析
1 前言
汽车结构疲劳的话题在当前各大整车制造企业越来越受到重视,几乎每种新开发的车型都需要考察其疲劳耐久性能。
以前传统的方法,汽车企业对于新车型疲劳寿命的评估都是利用实车在各道路试车场进行路试[1],该方式虽然是最直接且最准确的,但测试时间却十分冗长且耗费人力与经费甚巨,即使发现了问题往往也很难去修改。
近年来计算机软硬件的迅速发展,计算机辅助工程(CAE)分析技术在静态、碰撞、振动噪音等领域均有了相当不错的应用成果,但疲劳耐久性分析需要综合有限元应力分析和动力学载荷分析等专业技术,仍需花费非常大的计算量,且计算的准确性由于没有真实的道路载荷谱(RLD)作为计算输入而缺乏说服力。
本文针对上述问题,基于在国内汽车企业已经开始成熟运用的六分力轮测试技术实测获得的某乘用车在试车场的道路载荷谱数据[2],以此作为输入,驱动建立好的整车多刚体动力学仿真模型,获取作用在白车身各连接点上的载荷谱,同时对白车身进行有限元应力场分析。
综合上述结果,调用相应的疲劳损伤模型对白车身的疲劳寿命进行了计算,从而建立起一套较为可行的更符合真实工况的车辆疲劳寿命分析技术流程。
2 某型乘用车试车场道路载荷谱采集
2.1 测试工况简介
该试验用乘用车的四个车轮均安装六分力轮进行轴头上的三向力(Fx、Fy、Fz)和三向力矩(Mx、My、Mz)的测试,如图1所示。
道路载荷谱采集在某试车场进行,该试车场特征路面如图2示意。
车辆满载,测试工况为行驶一圈覆盖试车场所有特征路面的耐久性循环。
图1 安装了六分力轮的左前轮图2 试车场特征路面示意图
2.2 测试结果
测试共布置了24个通道,通过数据采集器记录存储下所有的载荷谱信号数据。
如图3所示为左前轮的六分力信号,共1720秒。
图3 采集到的左前轮六分力信号
3 白车身疲劳寿命计算
一般结构件在承受准静态随机载荷输入下的疲劳寿命计算流程如图4所示,可见输入包括该结构件在单位载荷下的应力/应变场结果、该结构件承受的载荷谱以及该结构件的材料疲劳性能参数,
即可调用相应的疲劳损伤模型进行该构件疲劳寿命的计算,计算结果将给出该几何结构形式和材料的构件在所承受的载荷谱作用下可能发生失效的危险部位和相应疲劳寿命的大小。
图4 结构疲劳寿命计算流程
3.1 整车多体动力学分析和载荷谱提取
显然,对白车身的疲劳寿命分析需要提供作用在白车身各连接点处的载荷谱,这里采用半实物方法,在多体动力学软件MSC.ADMAS平台上对该整车建立多体动力学模型,如图5所示。
以上述实测获得的四个车轮的六分力作为输入,驱动建立好的整车多体动力学模型运行一定时间长度,即可提取出作用在白车身各连接点上相应的力和力矩的时间历程。
如图6示意,给出某一个连接点处的三向载荷谱。
需要说明的是,由于整车多体动力学计算的限制,很难一次完成实测的1720秒时间长度的计算,同时出于考察各特征路面对车身结构疲劳的影响程度大小的目的,将实测载荷谱按各特征路面情况进行了分割,这里给出的是石块路面上的载荷谱,共40秒长度。
图5 建立的整车多体动力学模型图6 在石块路上提取的车身某连接点三向载荷谱
3.2 白车身有限元应力场分析
白车身有限元网格划分,静强度有限元计算已经是整车企业产品开发环节中应用非常成熟的CAE技术。
本文的分析是在有限元前后处理平台Altair HyperMesh和有限元求解器MSC.Nastran 中完成的,这里只给出前半车身的1/2对称局部模型及其在上述连接点处所承受的垂向单位载荷作用下的应力场分布结果,如图7所示。
图7 局部白车身模型及垂向单位载荷作用下的应力场
3.3 白车身疲劳寿命计算
所要进行疲劳分析的模型中包含有多种不同材料牌号和不同厚度的板材,这里用局部应变法(EN 法)损伤计算模型来对白车身进行疲劳寿命的计算,如图8所示给出其中一种主要材料的应变-寿命曲线(EN 曲线)。
图8 材料应变-寿命曲线 局部应变寿命法(E-N 法)是继名义应力寿命法(S-N 法)之后,广泛用于汽车结构件疲劳寿命计算的方法,它能很有效的计入缺口、焊缝、应力集中等现象所产生的局部循环塑性变形效应,该效应即循环应力-应变曲线,用式1表达。
E-N 法用幂函数形式表达为式2,也叫曼森-科芬方程。
迈纳线性损伤累积法则如式3所示,基于此法则结合循环应力-应变曲线和材料E-N 曲线即可计算承受随机载荷下的构件疲劳寿命[3]。
'
1/'(1)a a n e p a a a E K σσεεε⎛⎞=+=+⎜⎟⎝⎠L L
()''(2)2(2)f a a c
e p b a i
f i N N E
σεεεε=+=+L L 11,(l i i i n D N N D
===∑L L 3)
式中,a ε——应变幅值;e a ε——弹性应变幅值;p a ε——塑性应变幅值;a σ——应力幅值;E ——
弹性模量;——循环强度系数;——循环应变硬化指数;'K 'n 'f σ——疲劳强度系数;'
f ε——疲劳延性系数;
b ——疲劳强度指数;
c ——疲劳延性指数;——各应变水平下的循环次数;——各应变水平下的疲劳寿命;——总疲劳损伤;——疲劳寿命。
i n i N D N
以上述载荷谱、结构应力场结果和材料参数作为输入,在专业疲劳分析软件nCode DesignLife 平台上即可对该局部白车身模型进行疲劳寿命的计算,给出结果如图9所示。
可见该工况下的疲劳危险区域将主要集中在减振器支座处,提示需要在设计和工艺中对该部位引起重视。
图9 局部白车身疲劳计算结果
计算结果还可输出前5个危险区域的单元号和对应的寿命结果,如表1所示。
可见计算结果表明,最可能先发生失效的部位是22205号单元,其寿命值为输入的那段载荷谱还能重复5.652e4次。
表1 前5个危险区域单元号和寿命结果 危险区域 单元编号 寿命(Repeats )
1 22205 5.652e4
2 22206 6.218e4
3 22207 6.43e4
4 31541 7.287e5
5 31542 1.023e6
4 结论
随着汽车产品竞争日趋激烈,用户对产品质量的要求更加苛刻。
如果在设计阶段即对符合用户使用工况下的车辆疲劳耐久性能进行分析优化,及时发现问题并加以改进,显然能大大提升车辆的
品质、降低后期道路试验甚至用户使用时发生失效而产生的保修成本和声誉损失。
本文以某型乘用车的白车身为对象,通过实测获取了作用在车轮上的真实工况下的载荷谱,再通过多体动力学计算分解得到作用在白车身上的载荷谱,结合有限元分析的应力结果,即可对该结构进行基于实测载荷下的疲劳寿命分析计算,在此基础上还可进行各种结构、材料优化以及改型前后疲劳性能对比等分析工作。
这样的整车疲劳性能研究思路才能很好的满足上述需求,具有重要的工程意义。
5 参考文献
[1] 林育正, 毛庆平. 建立整车疲劳寿命分析技术的程序方法[J]. 车辆研测资讯, 2005, 3:20~27.
[2] 编辑委员会.汽车工程手册-试验篇.北京:人民交通出版社,2001.679~680.
[3] 徐灏.疲劳强度[M].北京:高等教育出版社,1988.
[4] 林晓斌. 机械产品的一体化抗疲劳设计[J]. CAD/CAM与制造业信息化, 2004, No.1-2:29~30.
[5] David Ensor, Chris Cook, Marc Birties. Optimizing Simulation and Test Techniques for Efficient Vehicle Durability Design and Development. SAE 2005-26-042.
[6] DesignLife User Manual. 2007. nCode International Ltd.。