机械零件疲劳寿命计算
03_疲劳强度计算
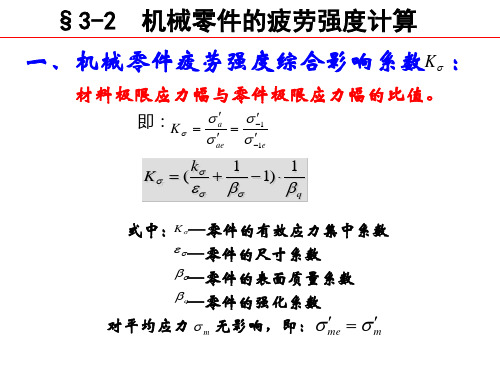
m
1 N0
n
m i
n
i
i 1
Sca
1 e
S
2. 当量循环次数Ne计算法:
取不稳定循环诸变应力中数值最大的应力或循环次
数最多的应力(对疲劳损伤影响最大的那个应力),
作为计算基准应力,而将诸变应力i所对应的循环次
数ni转化为当量循环次数Ne,使得应力循环Ne次后,
对材料所造成的损伤与诸应力i各自循环ni次对材料所
lim m ax ae m e s
按静应力计算:
M m e, ae M m, a
Sca
lim
m ax max
s m a
S
N
N
H
工作应力分布在: OAGH :疲劳强度计算 HGC :静强度计算
3.变应力的最小应力保持不变,即 min C(如受轴向变载荷的紧螺栓)
4)计算安全系数:Sca
lim
m ax max
S
零件的极限应力
lim m ax m e ae
零件的极限应力点的确定:
按零件的载荷变化规律不同分:
• 变应力的应力比保持不变,即:r = C • 变应力的平均应力保持不变,即:m = C • 变应力的最小应力保持不变,即:min = C
M m e, ae M m, a
1)如果此线与AG线交于M( me ,ae ),则有:
m e m
,
ae
1
m
K
lim m ax ae m e 1
K
K
m
Sca
lim
m ax max
1
K
K m m a
S
2)如果此线与GC线交于N( me ,ae ),则有:
03-02 机械零件的疲劳强度计算

3. 变应力的最小应力保持不变(σmin = C )
4. 应力的等效转化
公式中分子是材料的对称循环弯曲疲劳极限,分母看成是 一个与原来作用的不对称循环变应力等效的对称循环变应力。
• 应力的等效转化 :
• 计算安全系数为:
(2)单向不稳定变应力时零件的疲劳强度计算
• 不稳定变应力可分为非规律性的和规律性的两大类。 • 疲劳累积假说:Miner法则
(1)单向稳定变应力时机械零件的疲劳强度计算
计算零件疲劳强度的基本方法: • 零件危险截面上的σmax和σmin;
• 平均应力σm和应力幅σa
• 标出工作应力点M;
• 找出和工作应力 点相对应的疲劳 强度极限; • 计算零件工. 变应力的循环特性保持不变(r = C )
• 试验验证了假说的正确性:
(2)单向不稳定变应力时零件的疲劳强度计算
• 根据式(3-1a)可得:
• 不稳定变应力的计算应力:
• 设计准则:
• 强度条件:
(3)双向稳定变应力时零件的疲劳强度计算
1. 极限应力关系
2. 工作点 M
• M点的极限圆内,则为安 全的;
• M点在极限圆外,则一定 要破坏。
2. 变应力的平均应力保持不变(σm = C ) 3. 变应力的最小应力保持不变(σmin = C ) 4. 等效对称循环变应力 具体设计零件时,如果难于确定应力可能的变化规律, 在实践中往往采用r = C 时的公式。
1. 变应力的循环特性保持不变(r = C )
2. 变应力的平均应力保持不变(σm = C )
(3)双向稳定变应力时零件的疲劳强度计算
3. 计算安全系数
4. 不对称循环的变应力
(4)提高机械零件疲劳强度的措施
轴承寿命计算方法

轴承寿命计算方法轴承是机械传动中非常重要的零部件,其寿命的计算和预测对机械的可靠性和寿命具有重要的意义。
本文将介绍轴承寿命的计算方法,包括基本的理论原理、实验数据的统计处理以及运用寿命理论进行计算等内容。
1.轴承寿命的概念和分类轴承寿命指的是在特定工作条件下,轴承能够满足其要求并正常工作的时间。
通常来说,寿命是指从轴承开始使用到轴承失效的时间间隔。
根据轴承寿命的定义,可以将轴承寿命分为以下几种类型:(1)额定寿命:是指轴承在标准条件下可以正常工作的时间。
通常以满足一定故障率的时间为准。
(2)真实寿命:是指轴承工作在实际工况下的寿命,通常比额定寿命要短。
(3)经验寿命:是指根据实际工作情况和实验经验得到的一种估计值。
(4)相对寿命:是指相对于其他轴承的寿命。
通常根据平均故障率计算得到。
2.轴承寿命的理论计算轴承寿命的计算通常是基于寿命理论进行的。
目前使用较多的寿命理论包括极限额定寿命和疲劳寿命。
(1) 极限额定寿命:根据轴承的基本性能参数和工作条件,通过公式计算出轴承的额定寿命。
常用的公式包括L10、Lna、Lnm等。
L10寿命计算公式:L10=(C/P)³×(L10基准/H)或L10=(C/P)³×L10基准其中,L10为额定寿命,C为基本额定动载荷,P为轴承实际应力,L10基准为基准额定寿命,H为轴承的等效动负荷。
(2)疲劳寿命:考虑到实际工况下,轴承受到周期性载荷的作用,会出现疲劳破坏和寿命削减现象。
因此,疲劳寿命也是轴承寿命计算的重要方法。
疲劳寿命计算公式:Lh=(C/P)p×L10基准其中,Lh为疲劳寿命,C为基本额定动载荷,P为轴承实际应力,p 为疲劳指数,L10基准为基准额定寿命。
3.轴承寿命的实验数据统计为了得到准确的轴承寿命预测结果,需要根据实际工况下的轴承寿命进行数据的统计处理。
通常的数据统计方法包括寿命试验、故障统计和故障分析等。
机械零部件的疲劳寿命分析与优化设计

机械零部件的疲劳寿命分析与优化设计概述机械零部件的疲劳寿命分析和优化设计对于确保机械设备的可靠性和使用寿命至关重要。
疲劳失效是导致机械零部件损坏和事故的主要原因之一。
本文将介绍疲劳寿命的概念和常见分析方法,并探讨如何通过优化设计提高零部件的疲劳寿命。
疲劳寿命概念疲劳寿命是指机械零部件在循环应力的作用下失效之前能够承受的循环应力次数。
循环应力是指零部件在交变荷载作用下所受到的应力变化。
疲劳寿命可以通过应力-寿命(S-N)曲线来表示,该曲线描述了应力水平和所能承受的循环次数之间的关系。
疲劳分析方法1. 应力分析:对于机械零部件,必须首先进行应力分析,确定零部件在使用条件下所受到的应力水平和变化。
2. 材料特性分析:机械材料的疲劳寿命与其材料特性密切相关。
通过对材料的化学成分和热处理工艺等进行分析,可以确定材料的疲劳强度和寿命。
3. 循环载荷分析:确定作用在机械零部件上的循环载荷,包括振动载荷、冲击载荷等。
在实际情况中,往往会有多种载荷同时作用在零部件上,需要综合考虑不同载荷对疲劳寿命的影响。
4. 疲劳寿命预测:根据应力分析和材料特性,利用疲劳寿命预测模型,可以预测机械零部件在给定载荷下的疲劳寿命。
优化设计方法1. 材料选择:选择具有较高疲劳强度和寿命的材料,可以提高零部件的疲劳寿命。
例如,使用高强度钢材代替低强度钢材,可以提高零部件的抗疲劳能力。
2. 结构设计:通过优化零部件的结构设计,可以降低应力集中和应力变化幅度,从而延长疲劳寿命。
例如,合理设计零部件的圆角和倒角,可以缓解应力集中现象。
3. 表面处理:通过表面处理方法,如喷砂、磨削等,可以改善零部件表面的粗糙度和残余应力分布,提高疲劳强度。
4. 使用条件优化:调整机械设备的使用条件,如减小振动幅度、合理控制载荷大小等,可以减小零部件的疲劳应力,延长其寿命。
案例分析以一台发动机连接杆为例,进行疲劳分析和优化设计。
首先,进行应力分析并确定连接杆在使用条件下的应力水平和变化。
起重机传动零件疲劳计算基准载荷及载荷谱系数(0709)

起重机传动零件疲劳计算基准载荷及载荷谱系数*朱大林 郑小玲 方子帆摘要 本文讨论起重机传动零件疲劳计算方法问题。
讨论了区分机构和零件的载荷谱系数的必要性,指出应以零件的载荷谱作为零件疲劳计算的依据。
从实用的角度,提出以弹性振动最大载荷作为疲劳计算基准载荷并给出了相应的载荷谱系数定义。
本文还对零件的应力循环次数计算问题进行了分析。
关键词 起重机 机构 零件 疲劳计算 基准载荷 载荷谱系数1 引言起重机传动机构零部件的疲劳寿命计算是起重机设计的重要内容,起重机设计规范(GB3811-83)[1](以下简称规范)对此给出了一些原则规定。
起重机传动件的疲劳计算方法原则上与一般机械零件相同,但由于起重机的工作特点,决定了其零件的疲劳计算具有以下两个特点:1) 零件承受的载荷是变幅交变载荷,并具有随机变化的特性,从而使起重机零件的疲劳计算必须引入应力谱或载荷谱的概念,采用变幅疲劳的计算方法。
零件疲劳计算的依据是零件的载荷谱,而规范给出的是机构的载荷谱,对零件的载荷谱问题并未叙及。
2) 零件的应力循环次数通常小于材料的基本循环次数N 0,属于有限寿命疲劳计算。
这就要求正确计算零件的应力循环次数,对此,规范的规定也不尽完善。
本文将就以上问题进行讨论,并提出笔者的建议。
2 起重机传动零件疲劳计算与载荷谱规范采用名义应力法和疲劳损伤的线性累积理论,规定了起重机传动零件的疲劳计算方法,推荐的计算公式为:eq rk n σσ≤/Ⅰ (1)式中,σeq —考虑变幅应力和有限寿命的零件等效应力;σrk —考虑循环特性和应力集中后的零件无限寿命疲劳强度限;n Ⅰ—疲劳计算安全系数。
规范规定,零件的等效应力σeq 根据零件承受的等效载荷计算,对传动零件,等效载荷计算公式为:T eq =k n k m T Ⅰmax (2)式中,T Ⅰmax —机构启动时零件的静力矩与刚体惯性力矩之和;k m —载荷系数,m m m k K =,K m 为载荷谱系数;k n —有限寿命系数,n m k N N =/0,(N<N 0);N 0—材料的基本应力循环次数;N —机构零件的工作应力循环次数;当k n k m 〉1时,取k n k m =1 。
03-02 机械零件的疲劳强度计算讲解
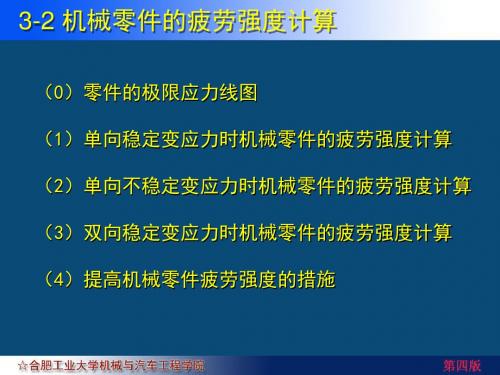
• 尽可能地减小或消除零件表面可能发生的初始裂纹的尺
寸,对于延长零件的疲劳寿命有着比提高材料性能更为
显著的作用。
(3)双向稳定变应力时零件的疲劳强度计算
3. 计算安全系数
4. 不对称循环的变应力
(4)提高机械零件疲劳强度的措施
• 尽可能降低零件上的应力集中的影响
• 可采用减荷槽来降低应力集中的作用;
(4)提高机械零件疲劳强度的措施
• 选用疲劳强度高的材料;
• 提高材料疲劳强度的热处理方法及强化工艺;
• 提高零件的表面质量;
3-2 机械零件的疲劳强度计算
(0)零件的极限应力线图 (1)单向稳定变应力时机械零件的疲劳强度计算 (2)单向不稳定变应力时机械零件的疲劳强度计算 (3)双向稳定变应力时机械零件的疲劳强度计算 (4)提高机械零件疲劳强度的措施
(0)零件的极限应力线图
1. 材料的极限应力线图 2. 零件的极限应力线图
(1)单向稳定变应力时机械零件的疲劳强度计算
计算零件疲劳强度的基本方法: • 零件危险截面上的σmax和σmin;
• 平均应力σm和应力幅σa
• 标出工作应力点M;
• 找出和工作应力 点相对应的疲劳 强度极限; • 计算零件工作的 安全系数。
(1)单向稳定变应力时机械零件的疲劳强度计算
1. 变应力的循环特性保持不变(r = C )
3. 变应力的最小应力保持不变(σmin = C )劳极限,分母看成是 一个与原来作用的不对称循环变应力等效的对称循环变应力。
• 应力的等效转化 :
• 计算安全系数为:
(2)单向不稳定变应力时零件的疲劳强度计算
• 不稳定变应力可分为非规律性的和规律性的两大类。 • 疲劳损伤累积假说:Miner法 则
机械疲劳强度的计算公式

机械疲劳强度的计算公式引言。
机械疲劳强度是指材料在受到交变载荷作用下所能承受的最大应力,是评价材料抗疲劳性能的重要指标之一。
在工程设计中,准确计算机械疲劳强度对于保证产品的可靠性和安全性至关重要。
本文将介绍机械疲劳强度的计算公式及其相关知识。
机械疲劳强度的概念。
机械疲劳强度是指材料在受到交变载荷作用下所能承受的最大应力。
在实际工程中,材料往往会受到交变载荷的作用,例如机械零件在运转过程中会受到交变载荷的作用,这时就需要考虑材料的疲劳强度。
疲劳强度与材料的抗拉强度、屈服强度等力学性能密切相关,但又有所不同。
疲劳强度是在交变载荷作用下,材料发生疲劳破坏的最大应力,而抗拉强度、屈服强度是在静态载荷作用下,材料发生破坏的最大应力。
机械疲劳强度的计算公式。
机械疲劳强度的计算公式是根据材料的疲劳试验数据和疲劳寿命曲线来确定的。
根据疲劳试验数据,疲劳强度与静态强度之比的数值在0.3~0.9之间。
常用的机械疲劳强度计算公式有双曲线法、极限应力法、应力循环法等。
双曲线法是一种常用的机械疲劳强度计算方法,其计算公式如下:\[ S_e = S_u \cdot (1 k \cdot \log(N_f)) \]其中,\( S_e \)为机械疲劳强度,\( S_u \)为材料的抗拉强度,\( k \)为常数,\( N_f \)为疲劳寿命。
极限应力法是另一种常用的机械疲劳强度计算方法,其计算公式如下:\[ S_e = \frac{1}{2} \cdot S_u \cdot (1 + \frac{1}{n}) \]其中,\( n \)为材料的应力循环指数。
应力循环法是根据材料在交变载荷下的应力循环曲线来计算疲劳强度的方法。
其计算公式如下:\[ S_e = \frac{1}{2} \cdot S_u \cdot (1 + R \cdot K_f) \]其中,\( R \)为载荷比,\( K_f \)为应力比例系数。
以上三种方法都是根据材料的疲劳试验数据和疲劳寿命曲线来确定机械疲劳强度的计算公式,不同的方法适用于不同的材料和载荷情况。
第六章 机器设备的寿命估算

第六章机器设备的寿命估算知识框架第一节磨损寿命一、典型的磨损过程【提示】由设备磨损规律的分析可知:1.如果设备使用合理,加强维护,可以延长设备正常使用阶段的期限,保证加工质量并提高经济效益。
2.对设备应该进行定期检查。
为了避免使设备遭到破坏,在进入第三阶段之前就进行修理,不是等到发生急剧磨损后才修理。
阶段特点磨损方程初期阶段时间很短,磨损速度很快。
S=S min+t(S0-S min)/△t(Ⅰ)(0≤t≤△t1)正常阶段(Ⅱ)磨损速度缓慢,情况稳定,磨损量随时间均匀的增加,二者成为线性关系,曲线中的AB段是一条斜直线。
S=S0+(t-△t1)·tga=S0+(t-△t1)·△t1≤t≤△t1+△t2急剧阶段(Ⅲ)磨损速度加快,磨损量急剧上升,造成机器设备的精度、技术性能和生产效率明显下降—第二节疲劳寿命理论及应用一、材料强度的衡量指标比例极限应力和应变、力和变形成线性关系的最大应力,用σp表示弹性极限保持弹性变形的最大应力,超过它就不再仅仅是弹性变形,还有塑性变形,用σe 表示屈服极限开始出现屈服现象的应力,所谓屈服,就是负荷不再增加,但试件还在继续伸长的这种现象。
屈服极限用σs表示强度极限材料拉断前的最大应力,也叫做抗拉强度,用σb表示断裂负荷试件断裂处的负荷二、许用应力定义许用应力是机械设计中,允许零件或构件承受的最大应力值。
公式对于塑性材料(大多数结构钢、铝合金等):对于脆性材料(高强度钢、铸铁等):三、疲劳及疲劳寿命【提示】根据应力循环次数分为高周疲劳和低周疲劳,在机械工程中最常见的疲劳是高周疲劳。
锅炉受到的是低周疲劳。
【小结1】水平起始点M对应的应力值σ叫做疲劳极限。
①疲劳极限:是可以承受无限次应力循环而不会发生疲劳破坏的最大应力。
②疲劳极限比材料静强度极限要低得多。
【小结2】对应M点的横坐标叫做循环基数,用符号N0来表示,N0一般是10,但是对于具体的材料、具体的循环特征,N0有所不同。
机械零件疲劳寿命计算

机械零件疲劳寿命计算机械零件的疲劳寿命是指在特定工作条件下,零件在循环加载下发生疲劳破坏之前能够承受的循环次数。
疲劳寿命的计算对于机械设计和工程应用至关重要,它能够帮助工程师评估零件的可靠性和使用寿命,从而指导设计和维护工作。
疲劳寿命的计算是基于疲劳强度和应力循环数之间的关系。
疲劳强度是指材料在循环加载下发生疲劳破坏的能力,而应力循环数则是指零件在工作过程中所经历的应力循环次数。
根据材料的疲劳强度曲线和应力循环数,可以计算出零件的疲劳寿命。
要计算疲劳寿命,首先需要确定零件所受的应力循环数。
这可以通过对零件的工作条件进行分析和测量来获取。
例如,在机械设备中,可以通过传感器检测零件的应力变化,并将其转换为应力循环数。
同时,还需要了解材料的疲劳强度曲线,该曲线描述了材料在不同应力水平下的疲劳强度。
根据疲劳强度曲线和应力循环数,可以得到零件的疲劳强度。
疲劳强度可以通过应力循环数与疲劳强度曲线的交点来确定。
在交点处,表示零件所受的应力循环数达到材料的疲劳强度,超过该循环数则可能导致零件的疲劳破坏。
疲劳寿命的计算还需要考虑到一些影响因素,例如应力集中、温度、湿度等。
应力集中是指零件中存在的应力集中点,这些点会导致应力集中并降低零件的疲劳寿命。
温度和湿度可以影响材料的力学性能,进而影响零件的疲劳寿命。
除了上述因素,材料的品质也对疲劳寿命有着重要的影响。
材料的制造工艺、组织结构和化学成分等因素都可以影响材料的疲劳性能。
因此,在计算疲劳寿命时,还需要考虑材料的品质和特性。
为了提高机械零件的疲劳寿命,工程师可以采取一些措施。
首先,可以通过改变零件的几何形状来减小应力集中,从而提高零件的疲劳强度。
其次,可以选择高强度的材料,提高零件的抗疲劳能力。
此外,还可以采用表面处理技术,如渗碳、氮化等,来增加零件的表面硬度和耐磨性,进而延长零件的疲劳寿命。
机械零件的疲劳寿命计算是机械设计和工程应用中的重要任务。
通过合理计算疲劳寿命,可以评估零件的可靠性和使用寿命,为机械设计和维护提供指导。
第2章机械零件的疲劳强度计算机械设计课件
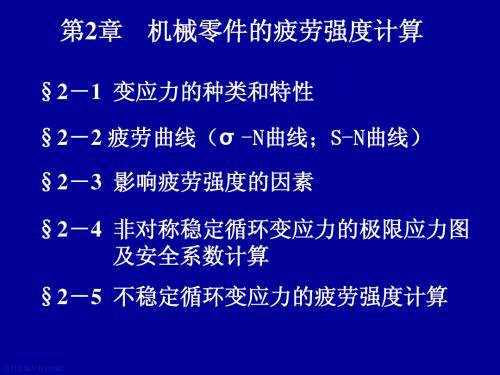
作σ
自用盘编号JJ321002
r∞
,通常用N0次数下的σ r取代,σ r值由实验得到。
σ
rN
轻合金材料的循环基数通常取为: N0≈2.5×108 σ
r
0
N0
N
图2—5 轻合金材料的σ—N曲线 N0称为循环基数,对应的疲劳极限σ r称为该材料的疲
劳极限。 对于钢材:当HB≤350时:N0≈106~107;
α
σ
、α
τ
——理论应力集中系数,查教材P39 ~ P41附表
自用盘编号JJ321002
3—1 ~ 附表3—3或查手册和其它资料。 若一个剖面上有几个不同的应力集中源,则零件的疲劳 强度由各kσ (kτ )中的最大值决定。
3、尺寸效应的影响 材料的疲劳强度极限是对一定尺寸的光滑试件进行实验 得出的,考虑到零件尺寸和试件的尺寸不同,其疲劳强度 也不一样,故引入一个尺寸系数ε: 1d 1d 直径d的 ; 1 1 标准试件的 εσ 、ετ的值可查教材P42 ~ P43附图3—2、3—3,附 表3—7或查手册及有关资料。 4、表面质量的影响 零件表面的加工质量,对疲劳强度也有影响,加工表面 的粗糙度值越小,应力集中越小,疲劳强度越高。因此引 入一个表面质量系数β 来考虑零件表面的加工质量不同对 疲劳强度的影响。 β可查教材P44附图3—4
max
自用盘编号JJ321002
min r max
称r为应力循环特性,表示了变应力 的变化性质。
σa σ r=-1
r=-1 t
σ
r=0 t t r=+1 t + σm
t 左边区域: σ 压应力为主, Ⅱ区: 零件在压缩 - 1 < r <0 变应力时破 σ 坏的情况较 Ⅰ区: 少,故不予 0 <r <+ 1 以分析。 45° - σm σ 0 0
疲劳强度计算

疲劳强度计算一、变应力作用下机械零件的失效特征1、失效形式:疲劳(破坏)(断裂)——机械零件的断裂事故中,有80%为疲劳断裂。
2、疲劳破坏特征:1)断裂过程:①产生初始裂反(应力较大处);②裂纹尖端在切应力作用下,反复扩展,直至产生疲劳裂纹。
2)断裂面:①光滑区(疲劳发展区);②粗糙区(脆性断裂区)(图2-5)3)无明显塑性变形的脆性突然断裂4)破坏时的应力(疲劳极限)远小于材料的屈服极限。
3、疲劳破坏的机理:是损伤的累笱4、影响因素:除与材料性能有关外,还与γ,应力循环次数N ,应力幅a σ主要影响 当平均应力m σ、γ一定时,a σ越小,N 越少,疲劳强度越高二、材料的疲劳曲线和极限应力图疲劳极限)(N N γλτσ—循环变应力下应力循环N 次后材料不发生疲劳破坏时的最大应力称为材料的疲劳极限疲劳寿命(N )——材料疲劳失效前所经历的应力循环次数N 称为疲劳寿命1、疲劳曲线(N γσ-N 曲线):γ一定时,材料的疲劳极限N γσ与应力循环次数N 之间关系的曲线0N —循环基数 γσ—持久极限1)有限寿命区当N <103(104)——低周循环疲劳——疲劳极限接近于屈服极限,可接静强度计算 )10(1043≥N ——高周循环疲劳,当043)10(10N N ≤≤时,N γσ随N ↑→N σσ↓2)无限寿命区,0N N ≥ γγσσ=N 不随N 增加而变化γσ——持久极限,对称循环为1-σ、1-τ,脉动循环时为0σ、0τ注意:有色金属和高强度合金钢无无限寿命区,如图所示。
3)疲劳曲线方程))10(10(043N N ≤≤C N N m m N =⋅=⋅0γγσσ——常数∴疲劳极限:γγγσσσ⋅==N m N K NN 0 (2-9) m N NN K 0=——寿命系数 几点说明:①0N 硬度≤350HBS 钢,7010=N ,当7010=>N N 时,取7010==N N ,1=N K≥350HBS 钢,70701025,10)25~10(⨯=>⨯=N N N 时,取701025⨯==N N ,1=N K有色金属,(无水平部分),规定当71025⨯>N 时,取701025⨯==N N②m —指数与应力与材料的种类有关。
机械设计中的疲劳寿命估算

机械设计中的疲劳寿命估算疲劳寿命估算是机械设计中一个重要的任务,它能够帮助工程师评估机械零件在长期使用过程中可能发生的疲劳破坏。
合理的疲劳寿命估算可以减少机械故障的发生,提高机械设备的可靠性和安全性。
本文将从疲劳寿命的定义、影响因素以及估算方法三个方面进行探讨。
一、疲劳寿命的定义疲劳寿命是指机械零件在循环加载下能够承受的次数,即在特定的载荷条件下,零件发生疲劳破坏前所经历的循环次数。
一般来说,疲劳寿命的表达方式为Nf,单位可以是次数、小时或循环。
二、影响疲劳寿命的因素1.应力水平:应力是导致疲劳破坏的主要原因之一,较高的应力水平会导致疲劳寿命的显著缩短。
2.材料性能:材料的强度、韧性等性能对疲劳寿命有着重要影响。
一般来说,强度较高、韧性较好的材料疲劳寿命相对较长。
3.工作环境:工作环境的恶劣程度、温度、湿度等因素也会对零件的疲劳寿命产生影响。
在腐蚀性环境中工作的零件疲劳寿命通常更短。
4.载荷类型:对于不同类型的载荷,疲劳寿命也会有所不同。
多变载荷和单纯应力载荷下的疲劳寿命表现不同。
5.几何形状:零件的形状、尺寸以及表面质量等也会对疲劳寿命造成一定影响。
三、疲劳寿命估算方法1.基于SN曲线的估算方法:SN曲线是疲劳寿命估算方法中最为常用的一种方法。
它通过试验得到零件在不同循环次数下的应力水平,进而建立起应力水平与疲劳寿命之间的关系曲线。
根据实际工况下的应力水平,可以通过插值或外推的方法预估零件在特定条件下的疲劳寿命。
2.统计学方法:统计学方法是一种基于概率统计理论的疲劳寿命估算方法,它考虑到了不确定性因素对疲劳寿命的影响。
通过统计样本数据,建立概率密度函数或累积分布函数,从而得到零件在一定概率范围内的疲劳寿命。
3.有限元方法:有限元方法是一种基于数值模拟的疲劳寿命估算方法。
它通过建立零件的有限元模型,并考虑材料本构关系和载荷工况,利用有限元软件对零件的应力分布进行分析,从而计算出疲劳寿命。
总结:疲劳寿命估算是机械设计中不可忽视的一环,它可以帮助工程师评估零件的使用寿命和可靠性。
机械零件的工作能力和计算准则
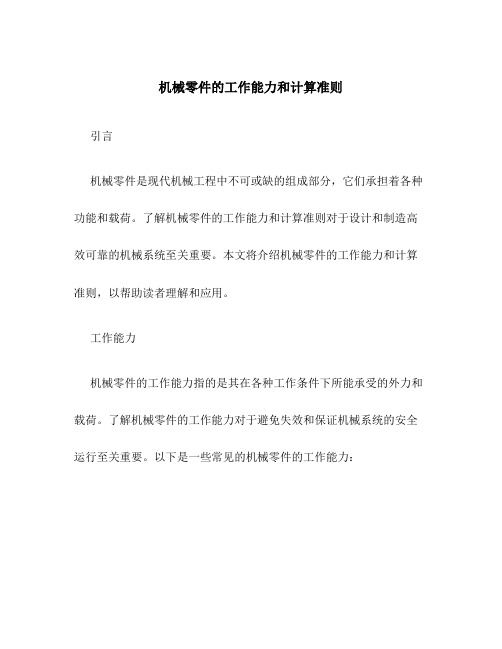
机械零件的工作能力和计算准则引言机械零件是现代机械工程中不可或缺的组成部分,它们承担着各种功能和载荷。
了解机械零件的工作能力和计算准则对于设计和制造高效可靠的机械系统至关重要。
本文将介绍机械零件的工作能力和计算准则,以帮助读者理解和应用。
工作能力机械零件的工作能力指的是其在各种工作条件下所能承受的外力和载荷。
了解机械零件的工作能力对于避免失效和保证机械系统的安全运行至关重要。
以下是一些常见的机械零件的工作能力:1. 钢材的抗拉强度钢材的抗拉强度是指其在拉伸过程中所能承受的最大外力。
在设计机械零件时,需要确保所选用的钢材的抗拉强度能够满足实际工作条件下的外力要求。
2. 轴承的承载能力轴承是机械系统中常见的零件,它们承担着支撑和传递载荷的任务。
轴承的承载能力是指其在工作过程中能够承受的最大载荷。
在选择和设计轴承时,需要考虑所需承载能力以及预计的工作条件。
3. 齿轮的承载能力齿轮是传动系统中重要的元件,它们负责传递动力和承受转矩。
齿轮的承载能力是指其在工作过程中能够承受的最大转矩。
在设计齿轮时,需要确保其承载能力能够满足实际工作条件下的转矩要求。
为了保证机械零件的工作能力,我们可以使用一些计算准则来评估其在各种工作条件下的性能。
以下是常见的机械零件计算准则:1. 安全系数安全系数是指机械零件的实际工作能力与设计要求之间的比值。
通常,我们会给机械零件设置一个合适的安全系数,以确保其在工作过程中有足够的余量。
安全系数的选取应考虑到工作条件和材料性能等因素。
2. 疲劳寿命疲劳寿命是指机械零件在连续循环加载下能够承受的次数。
疲劳寿命与工作负载、材料强度和设计几何形状等因素有关。
通过计算疲劳寿命,可以评估机械零件在实际工作条件下的寿命。
应力分析是用于评估机械零件受力情况的一种方法。
通过应力分析,可以计算出机械零件在工作过程中所受到的应力,进而评估其工作能力。
常见的应力分析方法包括有限元分析和解析计算等。
结论机械零件的工作能力和计算准则对于设计和制造可靠的机械系统至关重要。
疲劳寿命计算

疲劳分析的数值计算方法及实例第一节引 言零件或构件由于交变载荷的反复作用,在它所承受的交变应力尚未达到静强度设计的许用应力情况下就会在零件或构件的局部位置产生疲劳裂纹并扩展、最后突然断裂。
这种现象称为疲劳破坏。
疲劳裂纹的形成和扩展具有很大的隐蔽性而在疲劳断裂时又具有瞬发性,因此疲劳破坏往往会造成极大的经济损失和灾难性后果。
金属的疲劳破坏形式和机理不同与静载破坏,所以零件疲劳强度的设计计算不能为经典的静强度设计计算所替代,属于动强度设计。
随着机车车辆向高速、大功率和轻量化方向的迅速发展,其疲劳强度及其可靠性的要求也越来越高。
近几年随着我国铁路的不断提速,机车、车辆和道轨等铁路设施的疲劳断裂事故不断发生,越来越引起人们的重视。
疲劳强度设计及其研究正在成为我国高速机车车辆设计制造中的一项不可缺少的和重要的工作。
金属疲劳的研究已有近150年的历史,有相当多的学者和工程技术人员进行了大量的研究,得到了许多关于金属疲劳损伤和断裂的理论及有关经验技术。
但是由于疲劳破坏的影响因素多而复杂并且这些因素互相影响又与构件的实际情况密切相关,使得其应用性成果尚远远不能满足工程设计和生产应用的需要。
据统计,至今有约90%的机械零部件的断裂破坏仍然是由直接于疲劳或者间接疲劳而引起的。
因此,在21世纪的今天,尤其是在高速和大功率化的新产品的开发制造中,其疲劳强度或疲劳寿命的设计十分重要,并且往往需要同时进行相应的试验研究和试验验证。
疲劳断裂是因为在零件或构件表层上的高应力或强度比较低弱的部位区域产生疲劳裂纹,并进一步扩展而造成的。
这些危险部位小到几个毫米甚至几十个微米的范围,零件或构件的几何缺口根部、表面缺陷、切削刀痕、碰磕伤痕及材料的内部缺陷等往往是这种危险部位。
因此,提高构件疲劳强度的基本途径主要有两种。
一种是机械设计的方法,主要有优化或改善缺口形状,改进加工工艺工程和质量等手段将危险点的峰值应力降下来;另一种是材料冶金的方法,即用热处理手段将危险点局部区域的疲劳强度提高,或者是提高冶金质量来减少金属基体中的非金属夹杂等材料缺陷等局部薄弱区域。
机械零件的疲劳强度计算

机械零件的疲劳强度计算1.疲劳强度计算基础疲劳强度计算的基础是疲劳试验数据。
通过疲劳试验,可以得到不同应力水平下的应力与循环寿命的关系,即疲劳试验曲线。
然后通过统计方法,计算出零件在极限寿命设计条件下的疲劳强度。
2.标准疲劳曲线标准疲劳曲线是指确定零件疲劳强度的一种方法。
根据标准疲劳曲线,可以通过查表或计算,得到具体应力水平下的寿命和强度。
3.应力集中系数机械零件在实际工作中常常存在应力集中现象。
应力集中系数是考虑应力集中对零件疲劳强度影响的一个修正系数。
根据零件形状和载荷条件,可以确定相应的应力集中系数,从而修正零件的疲劳强度。
4.疲劳裕度系数疲劳裕度系数是指零件的实际应力与允许应力之比。
疲劳裕度系数是确定零件设计是否合理的一个重要参数。
如果疲劳裕度系数小于1,说明零件存在疲劳强度不足的风险;如果疲劳裕度系数大于1,说明零件在设计寿命内连续运行是安全的。
5.SN曲线法SN曲线法是一种常用的疲劳强度计算方法,通过试验或经验得到不同应力水平下的应力与寿命关系,即SN曲线。
通过与实际应力相比较,可以得到零件的寿命。
6.工程应力法工程应力法是一种简化的疲劳强度计算方法。
该方法根据零件在实际工况中的应力分布情况,选择合适的应力部位,计算得到平均应力,然后根据SN曲线法得到寿命。
7.有限元分析方法有限元分析方法是一种基于数值模拟的疲劳强度计算方法。
通过建立零件的有限元模型,并给定边界条件和载荷条件,可以计算出零件的应力分布情况。
然后通过与SN曲线法相结合,得到零件的疲劳寿命。
总之,机械零件的疲劳强度计算是一个复杂的工作,需要深入研究零件的应力分布、载荷条件、材料性能以及疲劳试验数据等方面,综合运用不同的计算方法和理论,以保证零件在实际工作条件下的安全性和可靠性。
机械设计基础中的材料疲劳与寿命分析
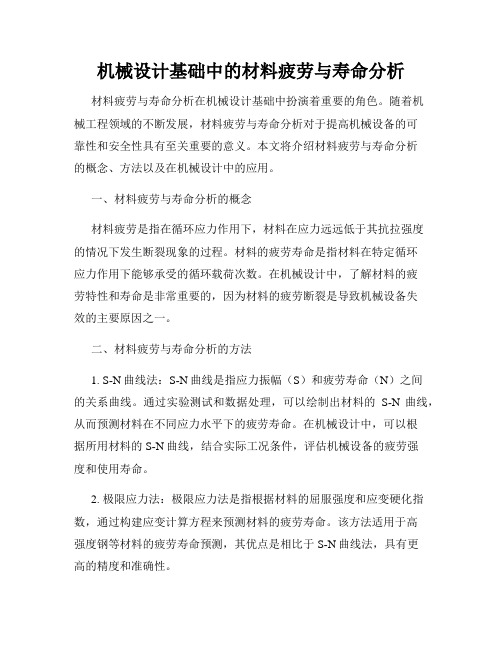
机械设计基础中的材料疲劳与寿命分析材料疲劳与寿命分析在机械设计基础中扮演着重要的角色。
随着机械工程领域的不断发展,材料疲劳与寿命分析对于提高机械设备的可靠性和安全性具有至关重要的意义。
本文将介绍材料疲劳与寿命分析的概念、方法以及在机械设计中的应用。
一、材料疲劳与寿命分析的概念材料疲劳是指在循环应力作用下,材料在应力远远低于其抗拉强度的情况下发生断裂现象的过程。
材料的疲劳寿命是指材料在特定循环应力作用下能够承受的循环载荷次数。
在机械设计中,了解材料的疲劳特性和寿命是非常重要的,因为材料的疲劳断裂是导致机械设备失效的主要原因之一。
二、材料疲劳与寿命分析的方法1. S-N曲线法:S-N曲线是指应力振幅(S)和疲劳寿命(N)之间的关系曲线。
通过实验测试和数据处理,可以绘制出材料的S-N曲线,从而预测材料在不同应力水平下的疲劳寿命。
在机械设计中,可以根据所用材料的S-N曲线,结合实际工况条件,评估机械设备的疲劳强度和使用寿命。
2. 极限应力法:极限应力法是指根据材料的屈服强度和应变硬化指数,通过构建应变计算方程来预测材料的疲劳寿命。
该方法适用于高强度钢等材料的疲劳寿命预测,其优点是相比于S-N曲线法,具有更高的精度和准确性。
三、材料疲劳与寿命分析在机械设计中的应用材料疲劳与寿命分析在机械设计中具有重要的应用价值。
首先,通过针对所用材料的疲劳特性进行分析,可以为机械设备的设计提供参考依据。
例如,在设计机械零部件时,可以根据材料的疲劳寿命选择合适的材料,并进行必要的工艺处理,以提高机械设备的疲劳强度和使用寿命。
其次,材料疲劳与寿命分析可以帮助预测机械设备在特定工况条件下的寿命。
通过分析材料的S-N曲线或者应变计算方程,可以估计机械设备在实际使用中的疲劳寿命。
这对于机械设备的维护和保养至关重要,可以避免因材料疲劳导致的突然故障和损坏。
此外,材料疲劳与寿命分析还可以帮助改进机械设备的设计。
通过分析材料在疲劳断裂前的应力分布和变形特征,可以找到机械零部件的薄弱环节,并进行结构优化和改进。
机械零件的疲劳寿命分析及寿命预测
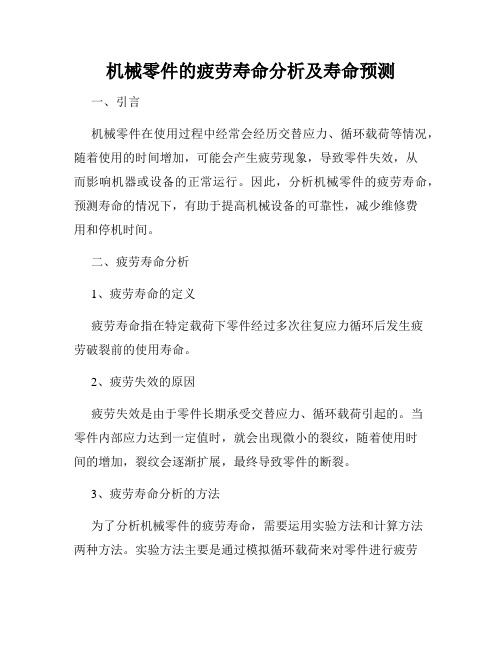
机械零件的疲劳寿命分析及寿命预测一、引言机械零件在使用过程中经常会经历交替应力、循环载荷等情况,随着使用的时间增加,可能会产生疲劳现象,导致零件失效,从而影响机器或设备的正常运行。
因此,分析机械零件的疲劳寿命,预测寿命的情况下,有助于提高机械设备的可靠性,减少维修费用和停机时间。
二、疲劳寿命分析1、疲劳寿命的定义疲劳寿命指在特定载荷下零件经过多次往复应力循环后发生疲劳破裂前的使用寿命。
2、疲劳失效的原因疲劳失效是由于零件长期承受交替应力、循环载荷引起的。
当零件内部应力达到一定值时,就会出现微小的裂纹,随着使用时间的增加,裂纹会逐渐扩展,最终导致零件的断裂。
3、疲劳寿命分析的方法为了分析机械零件的疲劳寿命,需要运用实验方法和计算方法两种方法。
实验方法主要是通过模拟循环载荷来对零件进行疲劳试验,得出疲劳寿命。
计算方法则通过分析零件的几何形状、材料性能、工作载荷等参数,利用数学方法计算出疲劳寿命。
4、疲劳寿命分析的步骤(1)确定零件的工作载荷和工况,根据实际情况确定零件受到的应力类型以及循环载荷的大小。
(2)确定零件的应力范围,根据零件工作载荷和材料的弹性模量计算出应力范围。
(3)计算疲劳强度系数,疲劳强度系数是指材料的疲劳极限(抗疲劳强度)与实际应力范围之间的比值,它是评估疲劳寿命的关键因素。
(4)应用材料疲劳曲线和极限疲劳循环次数得出零件的疲劳寿命。
三、寿命预测1、寿命预测方法为了预测机械零件的寿命,需要了解材料的疲劳强度曲线和应力分布等参数。
因此,寿命预测方法的主要任务是建立一个与材料和工况有关的模型,并利用该模型进行寿命预测。
2、寿命预测模型寿命预测模型是通过分析材料的疲劳性能和预处理实验数据得出的。
根据预处理数据和材料性质,可建立一个基于概率的寿命模型,以预测未来所需的寿命。
3、寿命预测的应用寿命预测可用于评估机械零件的耐久性,避免零件在使用过程中出现过载和振动等问题。
通过预测零件的寿命,可以及时采取相应的维护措施,延长机器的使用寿命。
零件疲劳强度

疲劳极限σr来近似代表ND和 σr∞,则有限寿命期内:
s
m rN
N
s
m r
N
0
C
s rN
m
N0 N
s
r
kNs r
kN—寿命系数, kN m N0 / N; 验常数 m—疲劳曲线实
机械零件的疲劳强度
三、极限应力线图(等寿命疲劳曲线)
机械零件材料的疲劳特性除用s-N曲线表示外,还可用极限应力线图
M
o
G N'
N
C σm
对于工作应力点N,当载荷加大到使应力达到N点时,将产生静力破坏,
S s m ax s m s a s s s max s m s a s m s a
机械零件的疲劳强度
3、最小应力为常数min=C (紧螺栓) σa
当载荷加大到使应力达到M‘ 时刚好 要产生 疲劳破坏,故安全系数S为:
来描述。该曲线表达了不同循环特性时疲劳极限的特性。
在工程应用中,常将等寿命曲线用直线来近似替代。
σa
A'
D' G'
σ-1 σ0/2
45º
45º
o σ0/2
σS σB
B
C σm
A′点:对称循环疲劳极限点 D′点:脉动循环疲劳极限点 B点:强度极限点 C点:屈服极限点
机械零件的疲劳强度
三、材料极限应力线图
se tg
Ks
2Ks s
kNs0 / 2
Ks
σ-1e
σ0e/2
o
kNσ0/2
C σm
σS
机械零件的疲劳强度
五、单向稳定变应力时的疲劳强度计算