数字化成形与制造
数字化成形与制造(双语)教案
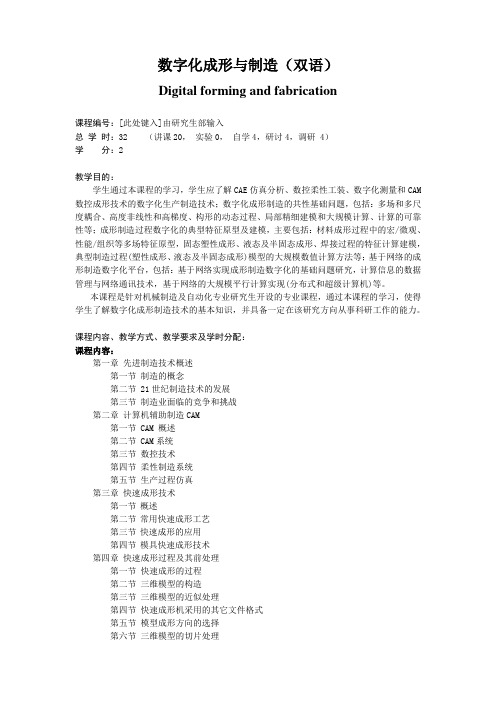
数字化成形与制造(双语)Digital forming and fabrication课程编号:[此处键入]由研究生部输入总学时:32 (讲课20,实验0,自学4,研讨4,调研 4)学分:2教学目的:学生通过本课程的学习,学生应了解CAE仿真分析、数控柔性工装、数字化测量和CAM 数控成形技术的数字化生产制造技术;数字化成形制造的共性基础问题,包括:多场和多尺度耦合、高度非线性和高梯度、构形的动态过程、局部精细建模和大规模计算、计算的可靠性等;成形制造过程数字化的典型特征原型及建模,主要包括:材料成形过程中的宏/微观、性能/组织等多场特征原型,固态塑性成形、液态及半固态成形、焊接过程的特征计算建模,典型制造过程(塑性成形、液态及半固态成形)模型的大规模数值计算方法等;基于网络的成形制造数字化平台,包括:基于网络实现成形制造数字化的基础问题研究,计算信息的数据管理与网络通讯技术,基于网络的大规模平行计算实现(分布式和超级计算机)等。
本课程是针对机械制造及自动化专业研究生开设的专业课程,通过本课程的学习,使得学生了解数字化成形制造技术的基本知识,并具备一定在该研究方向从事科研工作的能力。
课程内容、教学方式、教学要求及学时分配:课程内容:第一章先进制造技术概述第一节制造的概念第二节 21世纪制造技术的发展第三节制造业面临的竞争和挑战第二章计算机辅助制造CAM第一节 CAM 概述第二节 CAM系统第三节数控技术第四节柔性制造系统第五节生产过程仿真第三章快速成形技术第一节概述第二节常用快速成形工艺第三节快速成形的应用第四节模具快速成形技术第四章快速成形过程及其前处理第一节快速成形的过程第二节三维模型的构造第三节三维模型的近似处理第四节快速成形机采用的其它文件格式第五节模型成形方向的选择第六节三维模型的切片处理第五章工程数据处理技术第一节数表程序化第二节数表公式化第三节线图程序化第四节工程中的曲线与曲面第六章数据交换格式、协议与技术第一节数据交换格式与协议综述第二节 XML技术第三节 3XSL技术第四节 VRML技术第五节 WAP技术教学方式:课堂讲授:现代数字化成形技术(包括快速成形、模拟仿真技术等)、数字化制造技术(包括工艺过程设计自动化以及虚拟制造技术)、制造系统综合自动化技术(分布式数控系统、柔性制造系统、计算机集成制造系统以及智能制造系统)的特点。
数字化设计与制造技术研究

数字化设计与制造技术研究随着信息技术的高速发展,数字化设计与制造已经成为工业制造领域中的一项重要技术。
数字化设计与制造技术,是利用计算机和数字技术,将工业制造过程中的物理、化学、数学等科学方法结合起来,以达到高效、高质量、低成本、高精度的生产目标。
数字化设计与制造技术主要包括三个方面:数字化制造、数字化设计和数字化建模。
一、数字化制造数字化制造就是将设计完成的二维图形或三维模型文件通过计算机控制的数控设备进行机械加工、焊接、切割、折弯等生产制造工艺的一种新型制造技术。
其主要特点是对加工参数、加工路径和各种制造工艺进行数值化计算和处理。
数字化制造的优点是可以大大提高制造效率、降低生产成本、提高生产质量、精度和准确度。
数字化制造技术可以应用在航空航天、汽车制造、工业机器人、模具制造和精密制造等领域。
二、数字化设计数字化设计是利用计算机技术,将手工图纸转化成计算机二维或三维模型,以达到设计效率高、成本低、效果好的目的的一种工业设计方法。
数字化设计可以有效解决手工绘图过程中的精度问题、效率问题和高成本问题。
数字化设计主要应用于各种产品的开发设计、模具设计、工艺设计、建筑设计、城市规划和环境规划等领域。
三、数字化建模数字化建模是由数字图像处理技术、计算机图形学技术、计算机辅助设计技术和虚拟现实技术相结合的一种模拟生产工艺流程的技术。
数字化建模可以对任意形状的物体进行模拟设计和测试,从而达到提高产品开发的效率、降低产品制作成本和提高产品质量的目的。
数字化建模的应用范围非常广泛,可用于汽车、船舶、飞机、机器人等机械制造行业,也可用于建筑、城市规划等领域。
数字化设计与制造技术的研究重点是数字化化生产制造过程和数字化设计过程中的各个关键技术。
其中数字化设计的研究主要是针对三维数模的形成和建模方式、界面设计、参数化和自动化设计等内容。
而数字化制造的研究则涉及到数控加工技术和仿真制造技术。
未来数字化设计与制造技术的发展趋势,应该向着实现开放化、可扩展、可配置化和智能化的方向发展。
数字化制造中的快速成型技术研究与应用
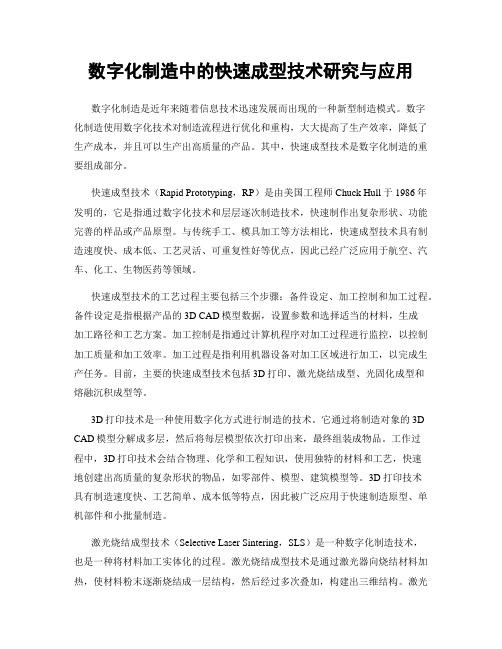
数字化制造中的快速成型技术研究与应用数字化制造是近年来随着信息技术迅速发展而出现的一种新型制造模式。
数字化制造使用数字化技术对制造流程进行优化和重构,大大提高了生产效率,降低了生产成本,并且可以生产出高质量的产品。
其中,快速成型技术是数字化制造的重要组成部分。
快速成型技术(Rapid Prototyping,RP)是由美国工程师Chuck Hull于1986年发明的,它是指通过数字化技术和层层逐次制造技术,快速制作出复杂形状、功能完善的样品或产品原型。
与传统手工、模具加工等方法相比,快速成型技术具有制造速度快、成本低、工艺灵活、可重复性好等优点,因此已经广泛应用于航空、汽车、化工、生物医药等领域。
快速成型技术的工艺过程主要包括三个步骤:备件设定、加工控制和加工过程。
备件设定是指根据产品的3D CAD模型数据,设置参数和选择适当的材料,生成加工路径和工艺方案。
加工控制是指通过计算机程序对加工过程进行监控,以控制加工质量和加工效率。
加工过程是指利用机器设备对加工区域进行加工,以完成生产任务。
目前,主要的快速成型技术包括3D打印、激光烧结成型、光固化成型和熔融沉积成型等。
3D打印技术是一种使用数字化方式进行制造的技术。
它通过将制造对象的3D CAD模型分解成多层,然后将每层模型依次打印出来,最终组装成物品。
工作过程中,3D打印技术会结合物理、化学和工程知识,使用独特的材料和工艺,快速地创建出高质量的复杂形状的物品,如零部件、模型、建筑模型等。
3D打印技术具有制造速度快、工艺简单、成本低等特点,因此被广泛应用于快速制造原型、单机部件和小批量制造。
激光烧结成型技术(Selective Laser Sintering,SLS)是一种数字化制造技术,也是一种将材料加工实体化的过程。
激光烧结成型技术是通过激光器向烧结材料加热,使材料粉末逐渐烧结成一层结构,然后经过多次叠加,构建出三维结构。
激光烧结成型技术具有制造速度快,精度高,纹理细,材料可塑性强等优点,因此被广泛应用于汽车、军工、医疗器械等领域的快速制造领域。
机械制造中的数字化工艺与制造技术
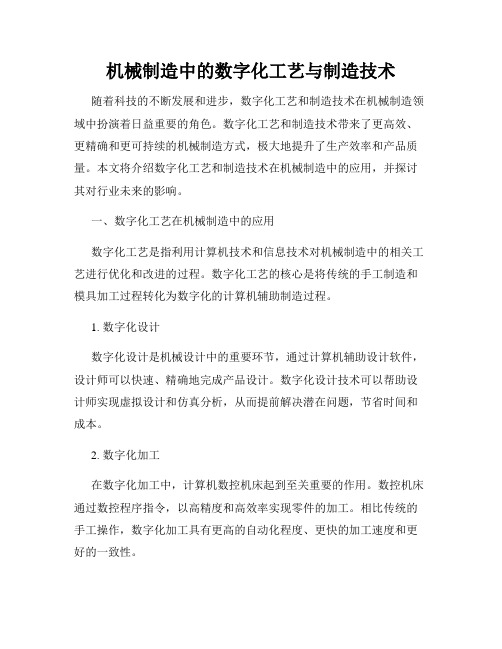
机械制造中的数字化工艺与制造技术随着科技的不断发展和进步,数字化工艺和制造技术在机械制造领域中扮演着日益重要的角色。
数字化工艺和制造技术带来了更高效、更精确和更可持续的机械制造方式,极大地提升了生产效率和产品质量。
本文将介绍数字化工艺和制造技术在机械制造中的应用,并探讨其对行业未来的影响。
一、数字化工艺在机械制造中的应用数字化工艺是指利用计算机技术和信息技术对机械制造中的相关工艺进行优化和改进的过程。
数字化工艺的核心是将传统的手工制造和模具加工过程转化为数字化的计算机辅助制造过程。
1. 数字化设计数字化设计是机械设计中的重要环节,通过计算机辅助设计软件,设计师可以快速、精确地完成产品设计。
数字化设计技术可以帮助设计师实现虚拟设计和仿真分析,从而提前解决潜在问题,节省时间和成本。
2. 数字化加工在数字化加工中,计算机数控机床起到至关重要的作用。
数控机床通过数控程序指令,以高精度和高效率实现零件的加工。
相比传统的手工操作,数字化加工具有更高的自动化程度、更快的加工速度和更好的一致性。
3. 数字化检测数字化工艺在机械制造的质量检测环节也起到了重要作用。
传感器和计算机系统的应用,使得零件的尺寸、外形和性能可以被准确地检测和分析。
数字化检测技术提高了产品质量的稳定性和可靠性,避免了人工检测的偏差和误差。
二、制造技术在机械制造中的应用制造技术是指从材料处理到成品制造的全过程中所涉及的各种技术和方法。
制造技术是数字化工艺的具体体现,是实现数字化工艺目标的手段和工具。
1. 先进材料制造技术的发展离不开先进材料的应用。
新型材料的研发和应用,如高强度合金、复合材料和纳米材料,使得机械制造的品质和性能得到了极大的提升。
2. 3D打印技术3D打印技术是一种快速原型制作技术,它通过逐层堆积材料来制造零件和成品。
3D打印技术具有设计灵活性高、制造成本低、生产周期短的特点,让机械制造业迈向了个性化定制和小批量生产的新时代。
3. 智能制造智能制造是数字化工艺和制造技术的最高形态,它将传统的机械制造与信息技术、通信技术和人工智能相结合,实现了工厂的自动化、柔性化和智能化。
数字化设计与制造3篇

数字化设计与制造数字化设计与制造数字化设计与制造是指借助计算机技术和数学方法来完成产品设计和生产制造的一种技术手段。
它实现了设计与生产环节的无缝对接,从而可以实现快速、高效、精确的产品设计和生产制造。
数字化设计与制造在现代工业生产中已经得到广泛应用,它不仅能够提高生产制造效率,还能够提高产品质量和降低生产成本。
数字化设计与制造的发展历程数字化设计与制造起源于20世纪70年代,当时计算机技术的发展还很初期。
那时的设计和制造过程主要是手工作业,大量的人工操作和繁琐的测量是不可避免的。
到了20世纪80年代后期,计算机技术开始成熟,三维建模软件和计算机辅助制造(CAM)系统开始应用于设计和制造过程中。
到了21世纪,数字化设计与制造技术得到了快速的发展,随着计算机技术的不断进步和互联网的普及,数字化设计与制造技术的应用范围越来越广泛,从最初的机械设计到后来的电子产品设计、建筑设计等,涉及的领域不断扩大,技术也不断升级。
数字化设计与制造技术的发展推动了现代工业的快速发展。
数字化设计与制造的优势数字化设计与制造的优势主要是体现在以下几个方面:1. 可以实现快速设计:传统的设计方法需要手工制图和测量,非常耗时费力,而数字化设计可以使用CAD软件等计算机辅助工具快速完成设计,提高设计效率。
2. 可以提高产品质量:数字化设计可以借助计算机进行仿真分析,帮助设计师更好地了解产品的性能和质量状况,从而进行优化设计。
3. 可以提高生产效率:数字化制造可以使用CAM系统完成生产加工,避免了手工加工的低效率和高误差率,提高了生产效率。
4. 可以降低生产成本:数字化制造可以精确控制加工过程,避免浪费资源和材料,从而降低生产成本,并提高生产效益。
数字化设计与制造的发展趋势数字化设计与制造技术的发展趋势主要表现在以下几个方面:1. 智能化:数字化设计与制造技术在未来可能会发展成为智能设计和智能制造,借助人工智能、机器人技术等,实现更加智能化、高效化的设计和制造。
基于多点数字化成形装备的智能制造服务技术研究
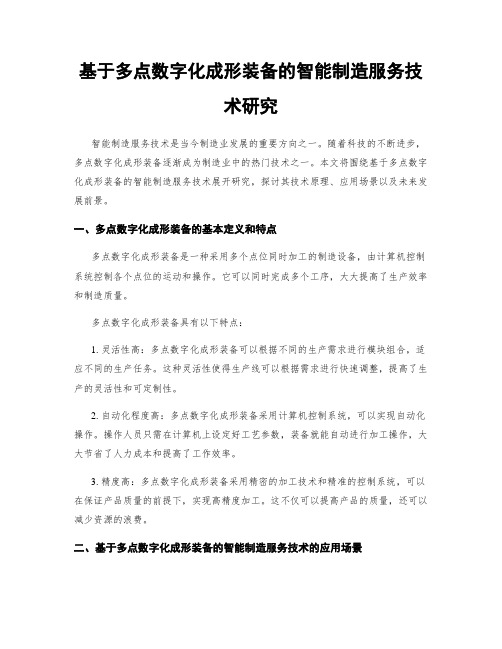
基于多点数字化成形装备的智能制造服务技术研究智能制造服务技术是当今制造业发展的重要方向之一。
随着科技的不断进步,多点数字化成形装备逐渐成为制造业中的热门技术之一。
本文将围绕基于多点数字化成形装备的智能制造服务技术展开研究,探讨其技术原理、应用场景以及未来发展前景。
一、多点数字化成形装备的基本定义和特点多点数字化成形装备是一种采用多个点位同时加工的制造设备,由计算机控制系统控制各个点位的运动和操作。
它可以同时完成多个工序,大大提高了生产效率和制造质量。
多点数字化成形装备具有以下特点:1. 灵活性高:多点数字化成形装备可以根据不同的生产需求进行模块组合,适应不同的生产任务。
这种灵活性使得生产线可以根据需求进行快速调整,提高了生产的灵活性和可定制性。
2. 自动化程度高:多点数字化成形装备采用计算机控制系统,可以实现自动化操作。
操作人员只需在计算机上设定好工艺参数,装备就能自动进行加工操作,大大节省了人力成本和提高了工作效率。
3. 精度高:多点数字化成形装备采用精密的加工技术和精准的控制系统,可以在保证产品质量的前提下,实现高精度加工。
这不仅可以提高产品的质量,还可以减少资源的浪费。
二、基于多点数字化成形装备的智能制造服务技术的应用场景基于多点数字化成形装备的智能制造服务技术在许多行业中都有广泛的应用,包括航空航天、汽车制造、医疗器械等。
1. 航空航天领域:多点数字化成形装备可以用于航空航天领域的零部件制造和维修。
由于航空航天领域对产品质量和精度要求极高,多点数字化成形装备的高精度加工和自动化操作能够满足这种需求。
2. 汽车制造领域:多点数字化成形装备可以用于汽车制造领域的车身板件制造。
多点数字化成形装备可以根据客户需求进行快速定制和生产,提高了汽车制造的灵活性和生产效率。
3. 医疗器械领域:多点数字化成形装备可以用于医疗器械领域的高精度零部件制造。
医疗器械对产品的质量要求极高,多点数字化成形装备可以保证产品的高精度和一致性,确保产品的质量和安全性。
机械制造中的数字化设计与制造

机械制造中的数字化设计与制造数字化设计与制造是现代机械制造领域中的重要趋势,它通过使用数字化技术和工具来优化产品设计、生产流程和制造过程,提高生产效率和质量。
在传统的机械制造中,设计和制造往往是分开进行的,设计师设计产品后通过图纸传递给制造人员进行制造,这种方式存在信息传递不畅、沟通效率低、成本高等问题。
而数字化设计与制造的出现,打破了这种传统的局限,将设计和制造整合在一起,实现了全流程的数字化化和智能化。
首先,数字化设计与制造通过CAD(计算机辅助设计)、CAM(计算机辅助制造)等软件工具的应用,实现了产品设计和制造过程的数字化。
设计师可以在CAD软件中将产品的三维模型细化设计,通过虚拟仿真来验证产品设计的可行性,优化产品结构和性能。
而制造人员可以在CAM软件中将三维设计模型转化为加工程序,实现数控加工,提高加工精度和效率。
这种数字化设计方式不仅减少了传统手工绘图和纸质文档的使用,提高了设计和制造的效率,同时也减少了人为因素引起的错误,提高了产品的质量和一致性。
其次,数字化设计与制造还可以实现产品数据的共享和协同。
传统的设计和制造过程中,设计师和制造人员之间信息交流不畅,往往存在信息遗漏和误解的情况。
而数字化设计与制造可以将产品数据存储在统一的数据库中,设计师、制造人员和其他相关人员可以随时访问和共享这些数据,实现信息的实时更新和传递。
这样可以有效避免信息传递中的问题,提高沟通效率,减少误差发生的可能性。
此外,数字化设计与制造还可以实现产品定制化和个性化生产。
传统的机械制造往往采用大规模生产,产品设计和制造比较标准化,无法满足消费者个性化需求。
而数字化设计与制造可以实现快速的产品设计和定制化生产,根据客户需求快速调整产品设计,实现小批量、高混合度的生产。
这种定制化生产模式不仅可以提高产品的市场竞争力,还可以降低库存和生产成本,提高企业的盈利能力。
总的来说,数字化设计与制造是现代机械制造领域中的重要趋势,它将设计和制造整合在一起,实现了全流程的数字化化和智能化。
数字化设计与制造技术
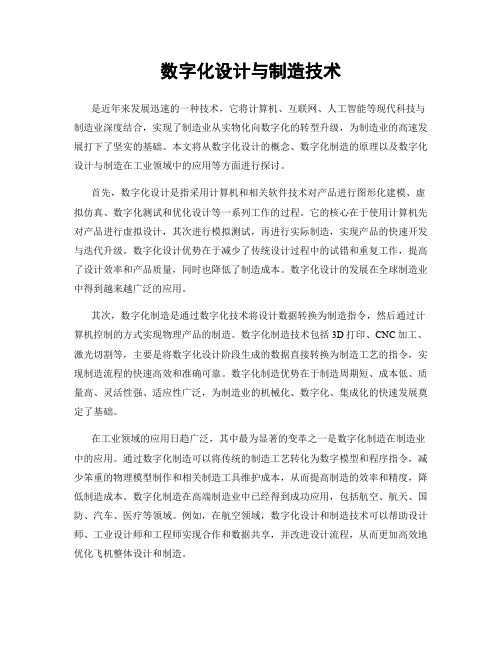
数字化设计与制造技术是近年来发展迅速的一种技术,它将计算机、互联网、人工智能等现代科技与制造业深度结合,实现了制造业从实物化向数字化的转型升级,为制造业的高速发展打下了坚实的基础。
本文将从数字化设计的概念、数字化制造的原理以及数字化设计与制造在工业领域中的应用等方面进行探讨。
首先,数字化设计是指采用计算机和相关软件技术对产品进行图形化建模、虚拟仿真、数字化测试和优化设计等一系列工作的过程。
它的核心在于使用计算机先对产品进行虚拟设计,其次进行模拟测试,再进行实际制造,实现产品的快速开发与迭代升级。
数字化设计优势在于减少了传统设计过程中的试错和重复工作,提高了设计效率和产品质量,同时也降低了制造成本。
数字化设计的发展在全球制造业中得到越来越广泛的应用。
其次,数字化制造是通过数字化技术将设计数据转换为制造指令,然后通过计算机控制的方式实现物理产品的制造。
数字化制造技术包括3D打印、CNC加工、激光切割等,主要是将数字化设计阶段生成的数据直接转换为制造工艺的指令,实现制造流程的快速高效和准确可靠。
数字化制造优势在于制造周期短、成本低、质量高、灵活性强、适应性广泛,为制造业的机械化、数字化、集成化的快速发展奠定了基础。
在工业领域的应用日趋广泛,其中最为显著的变革之一是数字化制造在制造业中的应用。
通过数字化制造可以将传统的制造工艺转化为数字模型和程序指令,减少笨重的物理模型制作和相关制造工具维护成本,从而提高制造的效率和精度,降低制造成本。
数字化制造在高端制造业中已经得到成功应用,包括航空、航天、国防、汽车、医疗等领域。
例如,在航空领域,数字化设计和制造技术可以帮助设计师、工业设计师和工程师实现合作和数据共享,并改进设计流程,从而更加高效地优化飞机整体设计和制造。
数字化设计和制造技术的快速发展和应用需要建立稳定的生态系统和优良的产业生态,包括高效的数字化设计工作站、标准化的设计数据和指令传输协议、定制化的数字化制造设备等。
装备制造中数字化设计与制造技术研究

装备制造中数字化设计与制造技术研究一、引言随着科技的迅猛发展和进步,数字化技术在装备制造领域中也被广泛应用,数字化设计和制造技术正成为装备制造行业的重要的发展方向。
数字化技术的应用使装备制造企业能够更快速、更高效、更精确地完成各项工作,在质量效益以及成本费用上达到了更好的平衡。
本文将阐述数字化设计与制造技术在装备制造中的应用和优势。
二、数字化设计在装备制造中的应用1.数字化建模技术数字化建模技术是数字化设计的基础,是将实体对象通过数字化手段转换为"虚拟对象",以确保整个建模过程的精确性。
数字化建模技术的应用,大大降低了装备设计制图时的误差率,提高了生产效率。
常见的基于CAD(计算机辅助设计)软件的数字化建模技术可以在制造前进行一些较为复杂的更改或纠错,可以大大提高装备制造工艺的可控性和生产效率。
2.数值分析技术数值分析技术(Numerical Analysis)是将工程物理现象描述为有限的数学方法,然后通过计算机数值计算的方法来求解物理现象的行为、规律和数值的一种分析方法。
在制造过程中,利用数值分析模拟装备在使用过程中的运行状态,可以更准确地了解装备运行的情况,在信誉、安全性、性能、寿命等方面提高了装备的实用价值。
通过数模与实验的方法评估装备的可靠性,可以有效地降低生产过程中的试验费用。
三、数字化制造在装备制造中的应用1.智能制造系统在数字化制造系统中,企业可以通过智能化研发、智能化生产、智能化服务等方面,来打破传统制造模式里面的弊端,使制造过程变更智能、灵活、高效等。
数字化制造技术可以通过建立智能化装备制造系统、采用智能传感器系统、制定规模化的智能生产计划等方面,提高装备制造的生产力和质量。
智能制造系统可以在减少浪费物质资源、提高制造的自动化程度、减少能源消耗等方面发挥重要的作用,是数字化制造技术的发展方向之一。
2.数字化制造技术的应用数字化制造技术可以将设备制造的各个环节通过数字化手段联系在一起,从而实现装备制造的信息化、数字化。
模具数字化设计与制造工艺
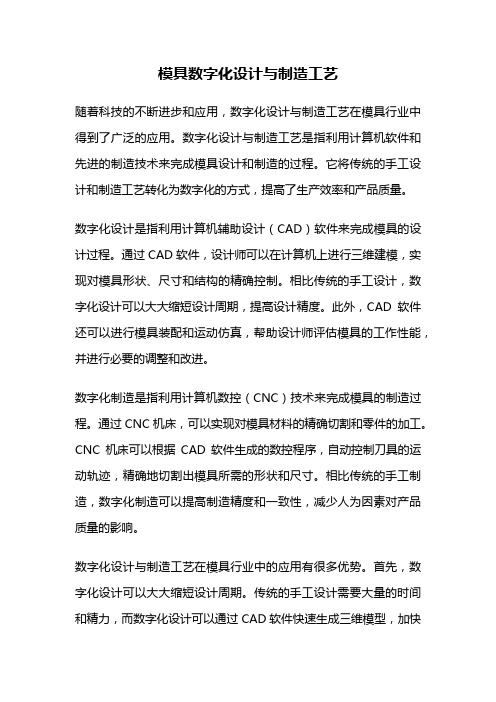
模具数字化设计与制造工艺随着科技的不断进步和应用,数字化设计与制造工艺在模具行业中得到了广泛的应用。
数字化设计与制造工艺是指利用计算机软件和先进的制造技术来完成模具设计和制造的过程。
它将传统的手工设计和制造工艺转化为数字化的方式,提高了生产效率和产品质量。
数字化设计是指利用计算机辅助设计(CAD)软件来完成模具的设计过程。
通过CAD软件,设计师可以在计算机上进行三维建模,实现对模具形状、尺寸和结构的精确控制。
相比传统的手工设计,数字化设计可以大大缩短设计周期,提高设计精度。
此外,CAD软件还可以进行模具装配和运动仿真,帮助设计师评估模具的工作性能,并进行必要的调整和改进。
数字化制造是指利用计算机数控(CNC)技术来完成模具的制造过程。
通过CNC机床,可以实现对模具材料的精确切割和零件的加工。
CNC机床可以根据CAD软件生成的数控程序,自动控制刀具的运动轨迹,精确地切割出模具所需的形状和尺寸。
相比传统的手工制造,数字化制造可以提高制造精度和一致性,减少人为因素对产品质量的影响。
数字化设计与制造工艺在模具行业中的应用有很多优势。
首先,数字化设计可以大大缩短设计周期。
传统的手工设计需要大量的时间和精力,而数字化设计可以通过CAD软件快速生成三维模型,加快设计速度。
其次,数字化制造可以提高制造精度和一致性。
通过CNC机床的精确控制,可以保证模具的形状和尺寸的一致性,提高产品的质量稳定性。
此外,数字化设计与制造还可以实现模具的自动化生产,减少人力成本,提高生产效率。
在数字化设计与制造工艺的应用过程中,还需要解决一些技术难题。
首先是CAD软件的选择和使用。
不同的CAD软件具有不同的功能和特点,需要根据具体需求选择合适的软件,并培训设计师掌握相关技术。
其次是CNC机床的操作和维护。
CNC机床是一种复杂的设备,需要专业的操作和维护人员来保证其正常运行。
此外,数字化设计与制造还需要建立完善的数据管理系统,确保设计和制造数据的安全和可追溯性。
计算机辅助设计与制造的数字化造型技术
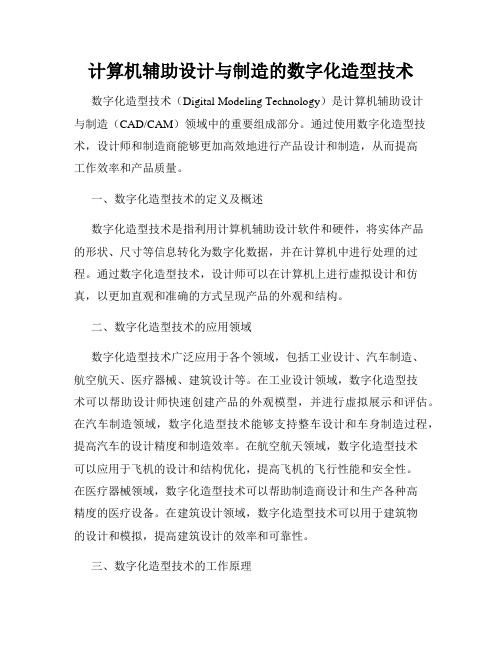
计算机辅助设计与制造的数字化造型技术数字化造型技术(Digital Modeling Technology)是计算机辅助设计与制造(CAD/CAM)领域中的重要组成部分。
通过使用数字化造型技术,设计师和制造商能够更加高效地进行产品设计和制造,从而提高工作效率和产品质量。
一、数字化造型技术的定义及概述数字化造型技术是指利用计算机辅助设计软件和硬件,将实体产品的形状、尺寸等信息转化为数字化数据,并在计算机中进行处理的过程。
通过数字化造型技术,设计师可以在计算机上进行虚拟设计和仿真,以更加直观和准确的方式呈现产品的外观和结构。
二、数字化造型技术的应用领域数字化造型技术广泛应用于各个领域,包括工业设计、汽车制造、航空航天、医疗器械、建筑设计等。
在工业设计领域,数字化造型技术可以帮助设计师快速创建产品的外观模型,并进行虚拟展示和评估。
在汽车制造领域,数字化造型技术能够支持整车设计和车身制造过程,提高汽车的设计精度和制造效率。
在航空航天领域,数字化造型技术可以应用于飞机的设计和结构优化,提高飞机的飞行性能和安全性。
在医疗器械领域,数字化造型技术可以帮助制造商设计和生产各种高精度的医疗设备。
在建筑设计领域,数字化造型技术可以用于建筑物的设计和模拟,提高建筑设计的效率和可靠性。
三、数字化造型技术的工作原理数字化造型技术的工作原理主要包括三个主要步骤:数据采集、数据处理和数据输出。
1. 数据采集:数字化造型技术主要通过激光扫描、光学测量、三维扫描等技术手段,将实体产品的形状、尺寸等信息转化为数字化数据。
具体的数据采集方法根据具体的应用需求而定。
2. 数据处理:在数据采集完成后,需要对采集到的原始数据进行处理和整理。
这包括数据清理、数据修正、数据重建等操作。
数据处理的目的是对原始数据进行优化和精确化,以确保后续的数字建模和仿真能够准确反映实体产品的特征。
3. 数据输出:数据输出是指将处理后的数字模型数据输出到计算机辅助设计软件中进行后续操作。
数字化制造与先进制造技术的融合与发展
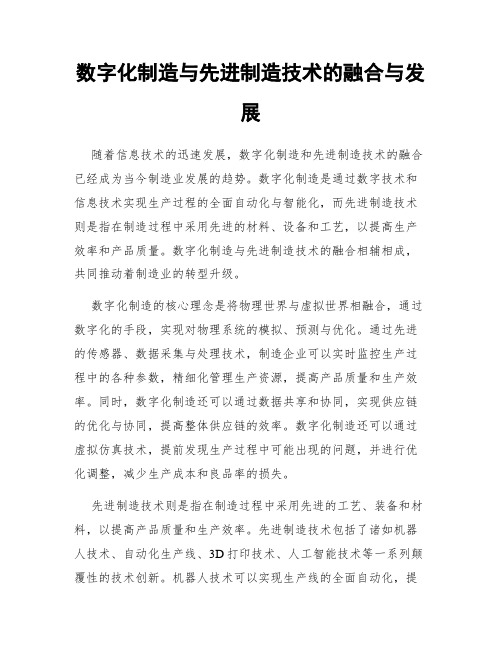
数字化制造与先进制造技术的融合与发展随着信息技术的迅速发展,数字化制造和先进制造技术的融合已经成为当今制造业发展的趋势。
数字化制造是通过数字技术和信息技术实现生产过程的全面自动化与智能化,而先进制造技术则是指在制造过程中采用先进的材料、设备和工艺,以提高生产效率和产品质量。
数字化制造与先进制造技术的融合相辅相成,共同推动着制造业的转型升级。
数字化制造的核心理念是将物理世界与虚拟世界相融合,通过数字化的手段,实现对物理系统的模拟、预测与优化。
通过先进的传感器、数据采集与处理技术,制造企业可以实时监控生产过程中的各种参数,精细化管理生产资源,提高产品质量和生产效率。
同时,数字化制造还可以通过数据共享和协同,实现供应链的优化与协同,提高整体供应链的效率。
数字化制造还可以通过虚拟仿真技术,提前发现生产过程中可能出现的问题,并进行优化调整,减少生产成本和良品率的损失。
先进制造技术则是指在制造过程中采用先进的工艺、装备和材料,以提高产品质量和生产效率。
先进制造技术包括了诸如机器人技术、自动化生产线、3D打印技术、人工智能技术等一系列颠覆性的技术创新。
机器人技术可以实现生产线的全面自动化,提高生产的稳定性和一致性。
3D打印技术则可以将设计概念直接转化为实物,减少制造过程中的浪费和环境的破坏。
人工智能技术可以通过数据分析和智能决策,实现对生产过程的优化与管理。
数字化制造和先进制造技术的融合与发展,将为制造业带来深远的影响。
首先,数字化制造和先进制造技术的应用,将大大提高制造业的生产效率和产品质量。
通过对生产过程的全面监控和优化,可以减少生产过程中的浪费和资源消耗,提高生产线的利用率和产品的一致性。
其次,数字化制造和先进制造技术的应用,将推动制造业的转型升级。
通过数字化制造和先进制造技术的引入,可以实现传统制造业向智能制造业的转变,提高企业的竞争力和核心竞争力。
再者,数字化制造和先进制造技术的应用,将推动制造业向服务型制造业的发展。
大型飞机结构件数字化制造与成形技术

大型飞机结构件数字化制造与成形技术一、概述1. 大型飞机结构件制造技术的重要性随着航空产业的飞速发展,大型飞机的制造技术也得到了空前的发展。
而在飞机制造过程中,结构件的制造是至关重要的一环,其质量和精度直接影响着飞机的安全性和航空运输的效率。
数字化制造与成形技术在大型飞机结构件制造中发挥着至关重要的作用。
二、大型飞机结构件数字化制造技术2. 数字化设计技术数字化设计技术是大型飞机结构件制造的第一步,它通过计算机辅助设计软件,实现了对飞机结构件的设计、优化和改进。
相比传统设计方法,数字化设计技术具有设计周期短、效率高、精度高等优势,能够有效地提高飞机的设计质量和生产效率。
3. 数字化扫描技术数字化扫描技术是大型飞机结构件制造中的重要技术手段之一。
通过激光扫描仪等设备,可以实现对飞机结构件的快速、精准的三维扫描,将实体物体转化为数学模型,为后续的数字化制造提供了精确的数据基础。
4. 数控加工技术在大型飞机结构件的制造中,数控加工技术是不可或缺的一环。
通过数控机床、数控车床等设备,可以实现对结构件的高精度加工,保证了结构件的尺寸和形状的精准度。
5. 3D打印技术3D打印技术作为一种革命性的数字化制造技术,也在大型飞机结构件制造中得到了广泛应用。
通过3D打印技术,可以实现对复杂结构件的快速制造,大大缩短了制造周期和降低了制造成本。
三、大型飞机结构件成形技术6. 复合材料成形技术大型飞机结构件的重量和强度要求非常高,因此复合材料成形技术成为了制造这些结构件的重要手段。
通过真空成型、压缩成型等技术,可以实现对复合材料的成型,使其具备较高的力学性能和表面质量。
7. 热成形技术对于一些金属结构件来说,热成形技术是制造高强度、复杂形状结构件的有效方法。
通过加热和塑性变形,可以实现对金属材料的成形,提高其强度和塑性。
8. 精密成形技术大型飞机结构件的成形工艺要求非常高,需要保证结构件的尺寸精度和表面质量。
精密成形技术通过模具设计、成形工艺优化等手段,实现了对结构件的高精度成形,满足了飞机的使用要求。
多点数字化成形装备在船舶制造中的应用案例研究
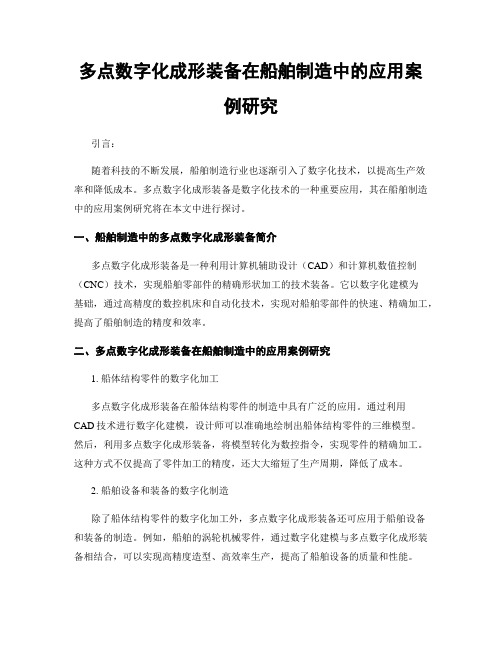
多点数字化成形装备在船舶制造中的应用案例研究引言:随着科技的不断发展,船舶制造行业也逐渐引入了数字化技术,以提高生产效率和降低成本。
多点数字化成形装备是数字化技术的一种重要应用,其在船舶制造中的应用案例研究将在本文中进行探讨。
一、船舶制造中的多点数字化成形装备简介多点数字化成形装备是一种利用计算机辅助设计(CAD)和计算机数值控制(CNC)技术,实现船舶零部件的精确形状加工的技术装备。
它以数字化建模为基础,通过高精度的数控机床和自动化技术,实现对船舶零部件的快速、精确加工,提高了船舶制造的精度和效率。
二、多点数字化成形装备在船舶制造中的应用案例研究1. 船体结构零件的数字化加工多点数字化成形装备在船体结构零件的制造中具有广泛的应用。
通过利用CAD技术进行数字化建模,设计师可以准确地绘制出船体结构零件的三维模型。
然后,利用多点数字化成形装备,将模型转化为数控指令,实现零件的精确加工。
这种方式不仅提高了零件加工的精度,还大大缩短了生产周期,降低了成本。
2. 船舶设备和装备的数字化制造除了船体结构零件的数字化加工外,多点数字化成形装备还可应用于船舶设备和装备的制造。
例如,船舶的涡轮机械零件,通过数字化建模与多点数字化成形装备相结合,可以实现高精度造型、高效率生产,提高了船舶设备的质量和性能。
3. 船舶管道系统的数字化设计与制造在船舶管道系统的设计与制造中,多点数字化成形装备同样起到了重要作用。
通过将CAD软件与多点数字化成形装备相结合,可以实现对船舶管道系统的全面数字化设计和生产。
这种方式不仅使得管道系统的设计更加准确和合理,还提高了管道系统的安装效率和可靠性。
4. 船舶模型的数字化制造船舶模型是船舶制造中的一个重要环节,通过制作船舶模型,可以对船舶的外形和结构进行验证。
利用多点数字化成形装备,可以将数字化建模转化为实际的船舶模型,从而实现对船舶的仿真和验证工作。
这种方式不仅减少了制作船舶模型的时间和成本,还提高了模型的精度和真实性。
多点数字化成形装备在体育用品制造中的应用研究
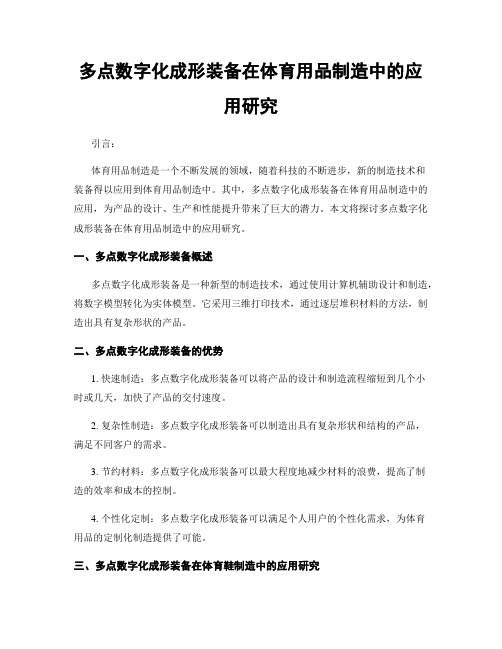
多点数字化成形装备在体育用品制造中的应用研究引言:体育用品制造是一个不断发展的领域,随着科技的不断进步,新的制造技术和装备得以应用到体育用品制造中。
其中,多点数字化成形装备在体育用品制造中的应用,为产品的设计、生产和性能提升带来了巨大的潜力。
本文将探讨多点数字化成形装备在体育用品制造中的应用研究。
一、多点数字化成形装备概述多点数字化成形装备是一种新型的制造技术,通过使用计算机辅助设计和制造,将数字模型转化为实体模型。
它采用三维打印技术,通过逐层堆积材料的方法,制造出具有复杂形状的产品。
二、多点数字化成形装备的优势1. 快速制造:多点数字化成形装备可以将产品的设计和制造流程缩短到几个小时或几天,加快了产品的交付速度。
2. 复杂性制造:多点数字化成形装备可以制造出具有复杂形状和结构的产品,满足不同客户的需求。
3. 节约材料:多点数字化成形装备可以最大程度地减少材料的浪费,提高了制造的效率和成本的控制。
4. 个性化定制:多点数字化成形装备可以满足个人用户的个性化需求,为体育用品的定制化制造提供了可能。
三、多点数字化成形装备在体育鞋制造中的应用研究1. 个性化设计:多点数字化成形装备可以根据客户的个人需求,制造出符合其足部特征的个性化鞋垫和鞋面。
2. 减震性能:通过使用多点数字化成形装备,可以将不同硬度的材料组合到鞋底中,提高鞋子的减震性能,从而保护运动员的脚部。
3. 减轻重量:多点数字化成形装备可以制造出轻量化的鞋底和鞋面,减轻运动员的负重,提高运动表现。
4. 提高稳定性:多点数字化成形装备可以通过局部加厚或增加支撑结构的方式,提高鞋子的稳定性,降低运动损伤的风险。
四、多点数字化成形装备在球拍制造中的应用研究1. 材料选择:多点数字化成形装备可以根据不同球拍的要求,选择不同的材料进行制造,以实现強度、耐用性和灵活性的平衡。
2. 结构优化:通过多点数字化成形装备,可以将材料堆积成球拍的各个部位,根据运动员的需求进行结构优化,提高球拍的性能。
数字化生产制造与创新
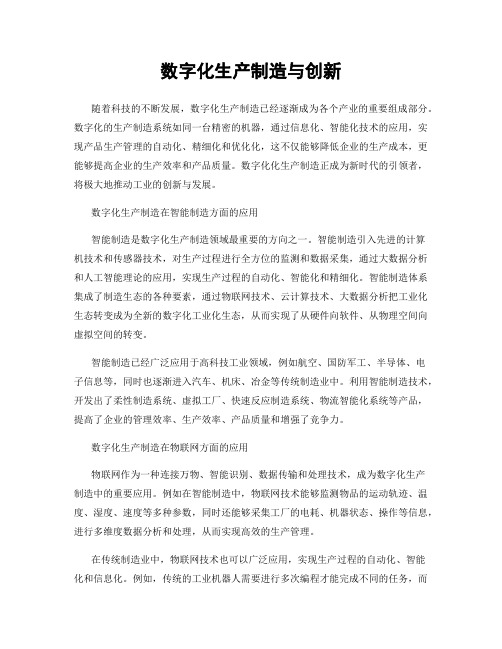
数字化生产制造与创新随着科技的不断发展,数字化生产制造已经逐渐成为各个产业的重要组成部分。
数字化的生产制造系统如同一台精密的机器,通过信息化、智能化技术的应用,实现产品生产管理的自动化、精细化和优化化,这不仅能够降低企业的生产成本,更能够提高企业的生产效率和产品质量。
数字化化生产制造正成为新时代的引领者,将极大地推动工业的创新与发展。
数字化生产制造在智能制造方面的应用智能制造是数字化生产制造领域最重要的方向之一。
智能制造引入先进的计算机技术和传感器技术,对生产过程进行全方位的监测和数据采集,通过大数据分析和人工智能理论的应用,实现生产过程的自动化、智能化和精细化。
智能制造体系集成了制造生态的各种要素,通过物联网技术、云计算技术、大数据分析把工业化生态转变成为全新的数字化工业化生态,从而实现了从硬件向软件、从物理空间向虚拟空间的转变。
智能制造已经广泛应用于高科技工业领域,例如航空、国防军工、半导体、电子信息等,同时也逐渐进入汽车、机床、冶金等传统制造业中。
利用智能制造技术,开发出了柔性制造系统、虚拟工厂、快速反应制造系统、物流智能化系统等产品,提高了企业的管理效率、生产效率、产品质量和增强了竞争力。
数字化生产制造在物联网方面的应用物联网作为一种连接万物、智能识别、数据传输和处理技术,成为数字化生产制造中的重要应用。
例如在智能制造中,物联网技术能够监测物品的运动轨迹、温度、湿度、速度等多种参数,同时还能够采集工厂的电耗、机器状态、操作等信息,进行多维度数据分析和处理,从而实现高效的生产管理。
在传统制造业中,物联网技术也可以广泛应用,实现生产过程的自动化、智能化和信息化。
例如,传统的工业机器人需要进行多次编程才能完成不同的任务,而利用物联网技术,工业机器人能够通过传感器自主感知周围环境和工件的位置,从而自动调整工作模式和轨迹,实现一机多能的自动化生产模式。
数字化生产制造在工业4.0方面的应用工业4.0是数字化生产制造中的一个重要概念,是数字化生产制造向集成化和智能化的发展。
数字化成型与制造
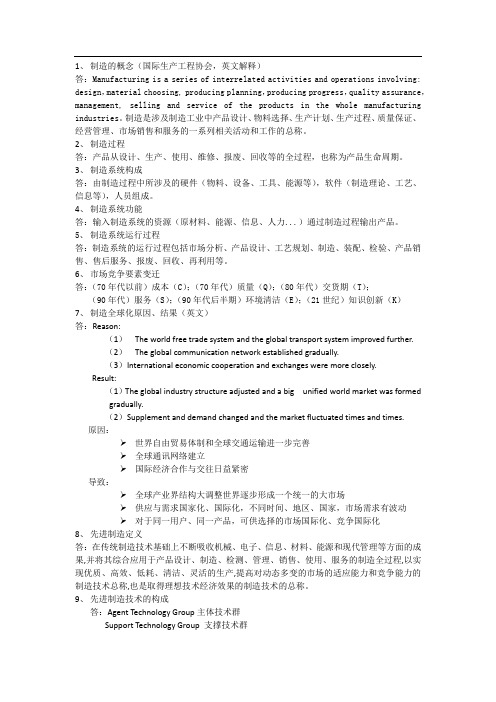
1、制造的概念(国际生产工程协会,英文解释)答:Manufacturing is a series of interrelated activities and operations involving: design,material choosing, producing planning,producing progress,quality assurance,management, selling and service of the products in the whole manufacturing industries。
制造是涉及制造工业中产品设计、物料选择、生产计划、生产过程、质量保证、经营管理、市场销售和服务的一系列相关活动和工作的总称。
2、制造过程答:产品从设计、生产、使用、维修、报废、回收等的全过程,也称为产品生命周期。
3、制造系统构成答:由制造过程中所涉及的硬件(物料、设备、工具、能源等),软件(制造理论、工艺、信息等),人员组成。
4、制造系统功能答:输入制造系统的资源(原材料、能源、信息、人力...)通过制造过程输出产品。
5、制造系统运行过程答:制造系统的运行过程包括市场分析、产品设计、工艺规划、制造、装配、检验、产品销售、售后服务、报废、回收、再利用等。
6、市场竞争要素变迁答:(70年代以前)成本(C);(70年代)质量(Q);(80年代)交货期(T);(90年代)服务(S);(90年代后半期)环境清洁(E);(21世纪)知识创新(K)7、制造全球化原因、结果(英文)答:Reason:(1)The world free trade system and the global transport system improved further.(2)The global communication network established gradually.(3)International economic cooperation and exchanges were more closely.Result:(1)The global industry structure adjusted and a big unified world market was formedgradually.(2)Supplement and demand changed and the market fluctuated times and times.原因:世界自由贸易体制和全球交通运输进一步完善全球通讯网络建立国际经济合作与交往日益紧密导致:全球产业界结构大调整世界逐步形成一个统一的大市场供应与需求国家化、国际化,不同时间、地区、国家,市场需求有波动对于同一用户、同一产品,可供选择的市场国际化、竞争国际化8、先进制造定义答:在传统制造技术基础上不断吸收机械、电子、信息、材料、能源和现代管理等方面的成果,并将其综合应用于产品设计、制造、检测、管理、销售、使用、服务的制造全过程,以实现优质、高效、低耗、清洁、灵活的生产,提高对动态多变的市场的适应能力和竞争能力的制造技术总称,也是取得理想技术经济效果的制造技术的总称。
飞机大型覆盖件的数字化成形制造技术

《冲压工艺及模具设计》大作业大型覆盖件成型工艺及模具**:***班级:成型072成绩:飞机大型覆盖件的数字化成形制造技术飞机作为一种常见的航空工具,其制造技术复杂,工艺流程多,零件数目巨大,而其最主要的外部构件却是整体成型,然后组装起来成飞机表面的覆盖件,其在飞机制造行业的学名是蒙皮。
蒙皮是构成飞机气动外形的外表零件,其尺寸大、品种多、外形复杂、批量小,主要采用拉伸成形工艺,其先进程度是衡量一个国家飞机制造能力和水平的重要标志。
现代制造技术的普及使数字化成形制造技术在航空制造领域不断推广和应用,使飞机蒙皮从传统的经验型向科学型制造模式转变。
飞机蒙皮数字化成形工艺是一个综合CAD工艺设计系统、CAE仿真分析、数控柔性工装、数字化测量和CAM数控成形技术等先进制造技术而成的数字化生产制造技术。
基于数字化柔性工装的飞机蒙皮数字化成形制造技术,是基于柔性多点拉形模具、柔性夹持定位和数控切边构成的可重构柔性工装的全数字量传递的蒙皮制造技术。
其主要的工作流程如下所述:一、模具型面CAD工艺设计系统在蒙皮的常规制造工艺中,包括设计模具型面、编制工艺流程、制造拉形模具、拉形、测量、切边等工序,其中模具型面的设计是整个工艺流程的关键环节,其需要根据蒙皮零件形状增加工艺补充面,设计模具型面,为拉形模具的制造提供依据。
国内外CAE软件固化了零件模具设计及成形仿真流程,用户能方便地操作从零件几何数据导入、模具生成到成形仿真CAE等固化流程。
为了规范化、流程化整体化蒙皮模具的设计流程,提高快速研制、加工和生产的能力,我国科学家综合多年的飞机蒙皮拉形工艺研究工作,构建了蒙皮CAD工艺设计系统框架,继而通过艰苦的努力,基于法国达索公司的CATIA 软件CAA平台,开发了模具型面CAD数字化工艺设计系统。
二、蒙皮拉形CAE仿真及回弹补偿优化技术蒙皮拉形过程的数值模拟分析,可以方便快速地确定各种参数对金属塑性流动的影响,预测蒙皮零件在成形中是否产生起皱、破裂等缺陷,计算回弹对零件形状、尺寸的影响,为设计者提供了进行工艺分析和模具设计的科学依据,减少或消除试拉和反复调形次数、改善产品质量,为传统制造模式向数字化方向转变奠定了基础。
数字化设计与制造技术3篇

数字化设计与制造技术第一篇:数字化设计与制造技术的发展数字化设计与制造技术已成为现代制造业的重要组成部分,它的出现改变了传统的制造方式和产品设计,极大地提高了生产效率和质量。
数字化设计与制造技术包括多个方面,如CAD、CAM、CAE等,它们的协同作用实现了制造业的数字化化、网络化、智能化。
数字化设计技术是指利用计算机和相关软、硬件进行产品设计的方法和技术,它将产品设计过程转化为数字化过程。
CAD(计算机辅助设计)是数字化设计技术的主要手段之一,它利用计算机软件来辅助人们完成产品的设计。
与手工设计相比,CAD具有快速、精确、易修改等优点,大大提高了产品设计的效率和准确性。
数字化制造技术是指利用计算机和相关软、硬件进行产品加工的方法和技术,它将产品制造过程转化为数字化过程。
CAM(计算机辅助制造)是数字化制造技术的主要手段之一,它通过对CAD模型的处理,生成数控程序,实现产品加工自动化。
数字化制造技术的应用,不仅提高了生产效率,而且还能保证产品的精度和一致性。
数字化仿真技术是指利用计算机对产品在使用过程中所受到的各种载荷和环境因素进行模拟,验证产品设计的可靠性和优化设计方案的方法和技术。
CAE(计算机辅助工程)是数字化仿真技术的主要手段之一,它能够对机械、电力、流体等各种领域的产品进行模拟仿真,辅助设计人员进行设计验证和优化,提高了产品设计的质量。
总之,数字化设计与制造技术是制造业数字化化的重要手段,它的应用将提高制造效率和质量,推动制造业向更高水平迈进。
第二篇:数字化设计与制造技术在制造业中的应用数字化设计与制造技术在制造业中得到广泛应用,改变了传统的制造方式,提高了生产效率和质量,具有重要的推动作用。
数字化设计与制造技术的应用领域包括机械加工、电子制造、航空航天等多个行业。
在机械加工领域,数字化设计与制造技术的应用可以实现机械加工过程的数字化化和自动化。
利用CAD软件,可以快速、精确地完成机械零部件的设计。
多点数字化成形技术的发展及应用
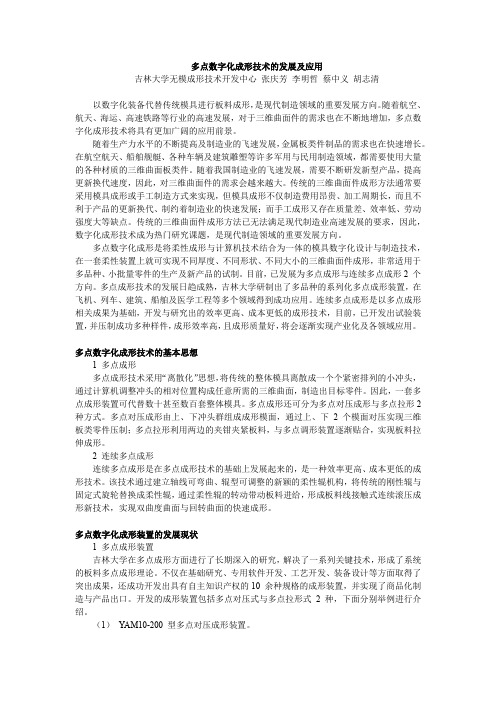
多点数字化成形技术的发展及应用吉林大学无模成形技术开发中心张庆芳李明哲蔡中义胡志清以数字化装备代替传统模具进行板料成形,是现代制造领域的重要发展方向。
随着航空、航天、海运、高速铁路等行业的高速发展,对于三维曲面件的需求也在不断地增加,多点数字化成形技术将具有更加广阔的应用前景。
随着生产力水平的不断提高及制造业的飞速发展,金属板类件制品的需求也在快速增长。
在航空航天、船舶舰艇、各种车辆及建筑雕塑等许多军用与民用制造领域,都需要使用大量的各种材质的三维曲面板类件。
随着我国制造业的飞速发展,需要不断研发新型产品,提高更新换代速度,因此,对三维曲面件的需求会越来越大。
传统的三维曲面件成形方法通常要采用模具成形或手工制造方式来实现,但模具成形不仅制造费用昂贵、加工周期长,而且不利于产品的更新换代、制约着制造业的快速发展;而手工成形又存在质量差、效率低、劳动强度大等缺点。
传统的三维曲面件成形方法已无法满足现代制造业高速发展的要求,因此,数字化成形技术成为热门研究课题,是现代制造领域的重要发展方向。
多点数字化成形是将柔性成形与计算机技术结合为一体的模具数字化设计与制造技术,在一套柔性装置上就可实现不同厚度、不同形状、不同大小的三维曲面件成形,非常适用于多品种、小批量零件的生产及新产品的试制。
目前,已发展为多点成形与连续多点成形2 个方向。
多点成形技术的发展日趋成熟,吉林大学研制出了多品种的系列化多点成形装置,在飞机、列车、建筑、船舶及医学工程等多个领域得到成功应用。
连续多点成形是以多点成形相关成果为基础,开发与研究出的效率更高、成本更低的成形技术,目前,已开发出试验装置,并压制成功多种样件,成形效率高,且成形质量好,将会逐渐实现产业化及各领域应用。
多点数字化成形技术的基本思想1 多点成形多点成形技术采用“离散化”思想,将传统的整体模具离散成一个个紧密排列的小冲头,通过计算机调整冲头的相对位置构成任意所需的三维曲面,制造出目标零件。
- 1、下载文档前请自行甄别文档内容的完整性,平台不提供额外的编辑、内容补充、找答案等附加服务。
- 2、"仅部分预览"的文档,不可在线预览部分如存在完整性等问题,可反馈申请退款(可完整预览的文档不适用该条件!)。
- 3、如文档侵犯您的权益,请联系客服反馈,我们会尽快为您处理(人工客服工作时间:9:00-18:30)。
北京科技大学数字成形与制造论文题目:玻璃瓶的数字化测量与制造单位:北京科技大学学号:作者:专业名称:机械工程完成时间: 2014年6月11日玻璃瓶的数字化成形与制造1.玻璃瓶的早期制作方法在现代入的日常生活中,玻璃瓶是一种不可或缺的东西。
在超市里,我们到处可见各类啤酒瓶、葡萄酒瓶、各种饮料瓶、果酱蜂蜜瓶、婴儿用的牛奶瓶、汽水或酒等以及各种逗人喜爱的化妆玻璃瓶。
在医院里可见大小不一的各类药品、输液瓶等。
玻璃瓶的玲珑剔透,晶莹明亮,空灵时尚、新奇多姿确使人见人爱。
它的化学稳定性又是其他材料无可匹敌的。
在公元前15世纪埃及已经能制造各种颜色的有美丽花纹的瓶子。
但是当时是在泥罐里溶制的,玻璃都不透明。
到了中世纪,玻璃工业在意大利兴盛起来,特别是威尼斯最为发达。
为了垄断玻璃瓶的生产和价格,威尼斯当局把所有的玻璃工厂迁到姆拉诺岛上,付以玻璃工人高薪,但严禁他们与外界接触。
不久,威尼斯玻璃业得到迅猛发展,其制作工艺在世界玻璃业处于领先地位。
他们制造的玻璃瓶精品迭出,畅销世界。
一个世纪前,玻璃瓶是靠肺活量制造出来的。
工匠用一根管子的末端收集一玻璃溶液,把管子伸进模子里,然后用嘴吹气,直到吹出一个玻璃瓶的形状。
1820年法国的一家玻璃厂(Baccarat)第一次使用压缩空气用于制瓶。
从此吹制玻璃瓶摆脱了用人的肺部。
1851年第一届伦敦世博会上,一共消费了一百万个玻璃瓶,丰要是用来装矿泉水、各种饮料等。
可见当时玻璃瓶的使用己趋于大众化。
但是在人工吹制时,料泡不是100%可用的,吹完后吹管上的一段玻璃就浪费掉。
美国在1882年理论阐明压-吹法的工艺,英国在1885年发明了吹-吹法的工艺,此二项工艺的发明,使玻璃液100%的得到利用.同时为今后制瓶工业的半自动化、自动化打开了道路。
在早期人们吹制玻璃瓶是没有模具的,工匠们用嘴吹,用手转动,做成瓶子,其做成的瓶子尺寸、形状不一。
好在当时的人要求不高,只要瓶子不坏、不漏均认为好瓶。
后来发展为木头制成的模具,它的内表面粗糙,尺寸也不统一。
1811年英国发明了金属模子,1821年英国发明了二瓣金属模子组成了一个整体的玻璃瓶。
1847年美国申请使铸铁模具专利,但直到1866年铸铁模具使用了冷却风后,才取得了良好的效果,玻璃瓶的尺等技术指标得到保证。
2.玻璃瓶数字化生产1890-1915人半自动制瓶机时代的到柬,它采用了压吹法或是吹吹法的工艺。
1903年美国O-I公司制造成功世界上第一台全自动制瓶机,每分钟21-24只瓶,并且申请专利。
它在1904年8月2日得到专利批准,供料机它能从窑炉料道里,能自动地供出一块一块的料滴.然后传递到制瓶机里。
它是将制瓶机直接取料分开.从而提高了效牢1925年在哈特福德诞生了第一台行列式制瓶机(I S制瓶机),该机分成若干个独立的组,每一组均町单独停机和换模,操作管理十分方便,当时采用的工艺是吹一吹法。
30年代末I.S制瓶机开始采用一种新的工艺,即压一吹法,1939年出现了四组职滴料的LS制瓶机,1950年出现了五组双滴料的1.S制瓶机。
1952年罗朗(Roitant)R7转盘式的制瓶机问世,1953年出现了六组双滴料的I.S制瓶机.1961年R7制瓶机开始采用积滴料,1966年罗朗S10转盘式的制瓶机问世.1967年I.S制瓶机发展成三渍料,1970年出现了八组般浦料的I.S制瓶机,同时研制成功分料机构,1972年出现了八组三滴料I S制瓶机,同时研制成功电子定时系统,1974年出现了十组职滴料I.S制瓶机,70年代中期西德海叶公司小口瓶压一吹法研制成功.1978年S10转盘式制瓶机采用双滴料,1979年出现了十组三滴料的I S制瓶机,1982年安装了第~台十组凹滴料的I.S制瓶机,1983年轴向冷却系统研制成功,80年代中期一些组合而成的十二组、十A组LS制瓶机相继出现在世界上一些著名的玻璃瓶罐生产90年代制瓶机电子定时系统计算机化。
2000年以后制瓶机与冷端联合实行制瓶数据化。
为了保证玻璃瓶的质量,仅仅采用人工目测的方法是不够的,在上世纪40年代。
人们就研究用机器,自动检验玻璃瓶的缺陷。
经过几十年的努力.采用机、电、光等现代技术,研发成功了自动检验机,它可以高速检验出}.几种典型玻璃瓶的缺陷.每分钟可检验120个玻璃瓶。
(见图13、图14早期的与现代化的自动捡验机)在30年代左右.人们发现玻璃瓶的一些缺陷,难咀用制瓶机械或模具来解释从而促进了制瓶工艺以及制瓶热传导的研究。
人们更重视料道玻璃液的均化以及料道温度的控制从早期人工吹制玻璃瓶,到第一台自动制瓶机每分钟生产24个玻璃瓶.再到现在每分钟生产700个玻璃瓶的生产线。
2000年以后制瓶机与冷端开始联合实行制瓶数字化。
在30年代左右,人们发现玻璃瓶的一些缺陷,难以用制瓶机械或模具来解释,从而促进了制瓶工艺以及制瓶热传导的研究。
人们更重视料道玻璃液的均化以及料道温度的控制,同时对冷气模具温度也进行了深入的研究,从而提高了玻璃瓶质量,满足了市场与顾客的要求,也使产品合格率大为提高。
现在通常认为玻璃成分、模具技术(材质、设计、制造和修理)和成型过程热交换是成功制瓶的三要素,要制作出高质量的玻璃瓶,这三者都必须置于完全控制之下。
从配合料加进窑炉那一刻开始,直到瓶子从退火炉炉膛出来的全过程是热交换过程;配合料在玻璃窑炉中,玻璃瓶在退火炉中是一个热交换过程;熔融的玻璃进入料道,直至制瓶机做出瓶子送到退火炉口是又一个热交换过程,这就是所谓成型过程的热交换。
成型过程热交换控制技术即成型过程热工控制技术,由于它对制作高质量玻璃瓶的重要作用而备受玻璃瓶制造者的关注,坚持不懈地从各方面着手进行改进,使之不断有所发展。
2.1料道温度的”智能”控制料道操作对制瓶机所生产的瓶子质量有很大影响。
料道操作的主要任务是掌握玻璃液在料道中的温度变化,合理地进行冷却、加热,匀化玻璃液的温度和成分,使之达到符合制瓶机做瓶要求的状态。
为了获得最佳结果,在生产过程中,操作人员随时观察料滴从流料孔滴落的情况。
如果料滴保持垂直下落,表明料滴温度已处于均匀状态。
如果料滴前部较冷料滴从流料孔流出时将向前弯曲则需进行调整(降低料道温度或提高料盆的玻璃料温度),使料滴达到垂直悬挂,把此时料道各控温区和料盆的温度记录下来,作为生产该特定产品时应保持的温度数据。
同时还要把达到所需温度时各加热区混合气的合适压力数值和冷却风蝶阀手轮的位置记录下来,作为生产特定产品的操作依据。
在安装了温度自动控制的料道上,较之人工控制的料道温度控制的效果显然要好得多。
但人工干预的成分依然很大(当外界条件变化时需由人工改变设定)。
由于控制环路的增加,使得通过设定值的人工调节以获得最佳控制效果变得更为复杂和困难。
况且,即使在设定上下了很大的功夫,现行控制系统自身所能作出的反应也是很有限的。
有鉴于此,近年来国外已研制出一种对干扰的影响有预测能力并能自行改变设定的新系:料道温度的计算机智能控制系统。
它不是一种传统概念的控制系统而是对传统控制系统的管理。
它只是作“决定”,而“执行”仍是交由传统控制系统的控制器。
智能计算机的程序由大量的解析料道操作的算法功能组成,来自实际料道的操作数据为这些算法提供数据。
因此,计算机程序是针对特定的料道研制的。
该系统在普通的PC总线上运行,可与别的具有完全的读/ 写通讯能力的中心控制系统(上位机)或别的控制器联网。
智能控制系统对操作数据连续进行统计分析,以辨别换品种的不同阶段,使用操作知识和料道的响应,对换品种的每个阶段要求的操作条件进行预测,按需要加热或冷却,以尽快达到新的设定点,而不去理会由于玻璃液流变化或其它因素造成的温度参数的短时间的变化。
2.2制瓶冷却风自动控制的改进除了在料道这一热交换器中进行热交换之外,成型过程中的另一个热交换是在制瓶机和输瓶机上进行的,对制瓶冷却风的自动控制是玻璃瓶成型过程热工控制技术的另一项不可忽视的内容。
模具的冷却是成型机控制的三个关键因素之一。
制瓶冷却风源来自鼓风机提供的空气。
早期的制瓶冷却风系统,每台制瓶机配备1台风机,或多台制瓶机共用1台风机。
冷却风管穿过制瓶机下面联结到制瓶机的每个分部和输瓶机,风管上装有手动阀,用于手动启闭单独分部的冷却风,还有附加的支管用来提供固定板冷却风,附加支管上也配备了手动阀用空气做冷却风源。
调节冷却能力的途径有两个:一是改变空气的温度,这是很不现实的。
二是通过改变压力调节空气量,这是目前实际采用的。
但改变压力的同时,也就改变了穿过模子的空气的速度,这将有可能引起模具冷却流型的变化。
因此,当要求的冷却风量已经适合,冷却风的压力已经选定,希望保持这个压力不变,以免干扰空气穿过模具的速度。
保持制瓶机冷却风压力不变的简单的压力控制系统已经使用多年,其做法是由一个电动执行机构带动鼓风机入口风闸,由一个压力传感器测鼓风机出口压力。
当个别分部或多机系统中的整台机关或开引起冷却风压变化时,压力控制器的输出经电动执行机构改变鼓风机入口风闸位置,以保持冷却风压不变。
由于空气流量是温度的函数,故随着季节变换、早晚气温的不同,使穿过模具的空气温度变化,导致对模具冷却能力的改变。
为保持冷却能力不变而去控制空气的温度显然是不可取的,另一种做法是通过改变压力来进行补偿。
因此,对早期的制瓶机冷却风系统的改进之一是把模具冷却风和制瓶的其它冷却风、固定板和输瓶带的冷却风分离,装设单独的模具冷却风机,并采用带温度补偿的冷却风压力自控。
系统对冷却风压力的控制方式不变,但鼓风机出口的一个温度传感器向控制器提供温度数值作为微调压力的设定值。
对制瓶机冷却风系统的另一项改进是对同一台固定风压的鼓风机供风的固定板和输瓶带分别由单独的控制器控制风压。
目前已在国内多条瓶罐玻璃生产线上投运的是美国O.B.公司的制瓶冷却风自控系统。
3.玻璃瓶的反求反求工程是针对消化吸收先进技术的一系列分析方法和应用技术的组合,它是以先进产品设备的实物、软件(图纸、程序、技术文件等)或影像(图片、照片等)作为研究对象,应用现代设计理论方法、生产工程学、材料学和有关专业知识进行系统深入的分析和研究,探索掌握其关键技术,进而开发出同类的先进产品。
反求工程含义广泛,包括设计反求、工艺反求、管理反求等。
实物反求是以产品为依据,对有关产品的设计原理、结构、材料、工艺装配、包装使用等进行分析研究,研制开发出与原型产品相同或相似的新产品。
因此,这是一个认识产品、再现产品或创造性地开发产品的过程。
三维光学扫描系统是将光栅条纹投影到物体表面,由CCD将拍摄到的条纹图像输入到计算机中,然后根据条纹按照曲率变化的形状利用相位法和三角法等精确地计算出物体表面每一点的空间坐标(X、Y、Z),生成三维的可输出色彩信息(R、G、B)的彩色面点云数据,可用于逆向-T程及快速成型以及工业设计、人体数字化、文物数字化等领域。