铸件分析报告
铸造缺陷质量分析报告

铸造缺陷质量分析报告标题:铸造缺陷质量分析报告摘要:本次报告对一批铸造件的缺陷进行了详细分析,并提供了解决方案,以提高铸件的质量和可靠性。
通过对缺陷的分类、原因分析和改进措施的制定,本报告的目标是降低缺陷率、提高产品质量,并为企业的生产过程提供指导。
一、引言铸造工艺是一种常见且重要的金属加工方式,但由于多种因素的影响,铸造件常常出现各种缺陷。
本报告对以下几种常见铸造缺陷进行了分析:气孔、砂眼、夹渣和缩孔。
二、缺陷分类和特征1. 气孔:气孔是铸造件内部的圆形或椭圆形气体空洞,在表面上通常呈孔状。
这种缺陷的特征是大小不一、分布不均匀,并且可能与材料中的气体分离有关。
2. 砂眼:砂眼是在铸造件表面形成的小凹陷或孔穴,并且通常有砂粒残留。
这种缺陷的主要原因是在型腔填充过程中砂芯未能完全固化或砂芯破裂。
3. 夹渣:夹渣是铸造件内部存在金属残留或其他非金属杂质的缺陷。
它通常表现为呈条状、点状或块状分布的较暗色物质。
4. 缩孔:缩孔是在铸造件中形成的不完全填充的孔洞,通常位于较厚的截面部分。
这种缺陷的主要原因是在凝固过程中金属收缩引起的。
三、缺陷原因分析1. 气孔:气孔的形成主要与以下因素有关:金属液中溶解的气体、型腔设计不合理、浇注过程中液态金属的气体浸润和释放等。
解决方案包括采取适当的除气处理、改进型腔设计、控制浇注工艺等。
2. 砂眼:砂眼通常与砂芯制备和浇注过程中的温度、浇注速度等相关。
解决方案包括优化砂芯制备工艺、调整浇注参数以及改善浇注系统设计等。
3. 夹渣:夹渣的原因主要与金属液的净化和过滤不足、浇注过程中金属液与非金属杂质的接触等有关。
解决方案包括加强净化处理、使用过滤器、改进浇注工艺等。
4. 缩孔:缩孔的形成与金属凝固收缩不平衡、铸造温度过低、浇注过程中金属液的顺流速度等相关。
解决方案包括优化浇注工艺、控制冷却速度等。
四、改进措施根据对缺陷原因的分析,提出了以下改进措施:1. 加强除气处理:通过采用真空或压力浇注等技术,有效去除金属液中的气体;2. 优化砂芯工艺:提高砂芯的强度和温度稳定性,避免砂芯破裂;3. 加强金属液净化:采用有效的净化剂和过滤器,去除金属液中的杂质;4. 调整浇注参数:合理控制浇注温度和速度,确保金属液充满型腔;5. 优化冷却过程:控制冷却速度,减少金属凝固收缩引起的缺陷。
铸件成本分析报告

铸件成本分析报告铸件成本分析报告一、引言铸件成本是指生产一件铸件所需的材料、人力、设备以及其他费用。
铸件作为一种常见的制造工艺,广泛应用于汽车、航空航天、机械制造等行业。
了解铸件成本对于企业合理控制成本、提高生产效率和竞争力至关重要。
本报告旨在分析铸件成本,从而为企业管理者制定有效的成本控制策略提供依据。
二、铸件成本的构成1. 材料成本:铸件的材料成本主要包括金属原料和砂型材料。
金属原料的成本可以通过计算材料的重量和单价得出,而砂型材料的成本则需要考虑砂型的用量和成本。
2. 人工成本:铸件生产过程需要一定数量的工人参与,包括操作工、检查员等。
人工成本主要包括工资、社会保险和福利等费用。
3. 设备成本:铸件生产中需要使用各种生产设备,包括熔炼炉、造型设备、清理设备等。
设备成本主要包括设备的购置费、维护费和能耗费用。
4. 工装夹具成本:铸件生产中还需要使用一些工装夹具来保证铸件的质量和生产效率。
工装夹具成本主要包括夹具的购置费、维护费用和使用寿命等。
5. 其他成本:铸件生产中可能还需要考虑一些其他费用,如研发费用、运输费用、管理费用等。
三、铸件成本分析方法1. 分步分析法:按照铸件生产的不同阶段分步分析成本。
将成本按照材料成本、人工成本、设备成本等分类统计,然后根据各个成本项的比例计算出总成本。
2. 直接成本法:将所有与铸件生产直接相关的成本作为直接成本,包括材料成本、人工成本、设备成本和工装夹具成本等。
通过直接成本可以了解到每一件铸件的具体成本。
3. 间接成本法:将与铸件生产间接相关的成本归入间接成本,如研发费用、运输费用、管理费用等。
通过间接成本的分析可以了解到铸件生产所需的其他费用和资源占用情况。
四、铸件成本控制策略1. 优化材料成本:通过选择合适的金属材料和砂型材料,合理控制材料的用量和成本,同时可以考虑对废料进行回收再利用,节约成本。
2. 提高生产效率:通过改进生产工艺、优化生产流程,提高生产效率,减少人工成本和设备成本。
铸件分析报告
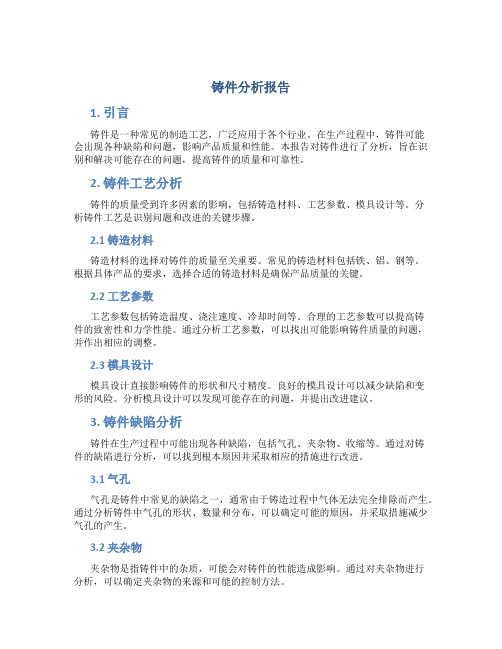
铸件分析报告1. 引言铸件是一种常见的制造工艺,广泛应用于各个行业。
在生产过程中,铸件可能会出现各种缺陷和问题,影响产品质量和性能。
本报告对铸件进行了分析,旨在识别和解决可能存在的问题,提高铸件的质量和可靠性。
2. 铸件工艺分析铸件的质量受到许多因素的影响,包括铸造材料、工艺参数、模具设计等。
分析铸件工艺是识别问题和改进的关键步骤。
2.1 铸造材料铸造材料的选择对铸件的质量至关重要。
常见的铸造材料包括铁、铝、钢等。
根据具体产品的要求,选择合适的铸造材料是确保产品质量的关键。
2.2 工艺参数工艺参数包括铸造温度、浇注速度、冷却时间等。
合理的工艺参数可以提高铸件的致密性和力学性能。
通过分析工艺参数,可以找出可能影响铸件质量的问题,并作出相应的调整。
2.3 模具设计模具设计直接影响铸件的形状和尺寸精度。
良好的模具设计可以减少缺陷和变形的风险。
分析模具设计可以发现可能存在的问题,并提出改进建议。
3. 铸件缺陷分析铸件在生产过程中可能出现各种缺陷,包括气孔、夹杂物、收缩等。
通过对铸件的缺陷进行分析,可以找到根本原因并采取相应的措施进行改进。
3.1 气孔气孔是铸件中常见的缺陷之一,通常由于铸造过程中气体无法完全排除而产生。
通过分析铸件中气孔的形状、数量和分布,可以确定可能的原因,并采取措施减少气孔的产生。
3.2 夹杂物夹杂物是指铸件中的杂质,可能会对铸件的性能造成影响。
通过对夹杂物进行分析,可以确定夹杂物的来源和可能的控制方法。
3.3 收缩收缩是铸件冷却过程中普遍存在的问题。
铸件冷却时可能会发生体积收缩和变形,影响铸件的尺寸精度和形状。
通过分析收缩问题,可以找到可能的原因,并采取相应的措施进行改进。
4. 铸件质量改进措施针对铸件分析中发现的问题和缺陷,可以采取一系列的质量改进措施,以提高铸件的质量和可靠性。
4.1 优化工艺参数根据铸造材料和具体产品要求,对工艺参数进行优化调整,以提高铸件质量。
例如,调整铸造温度、浇注速度和冷却时间等。
铸铜件材质报告
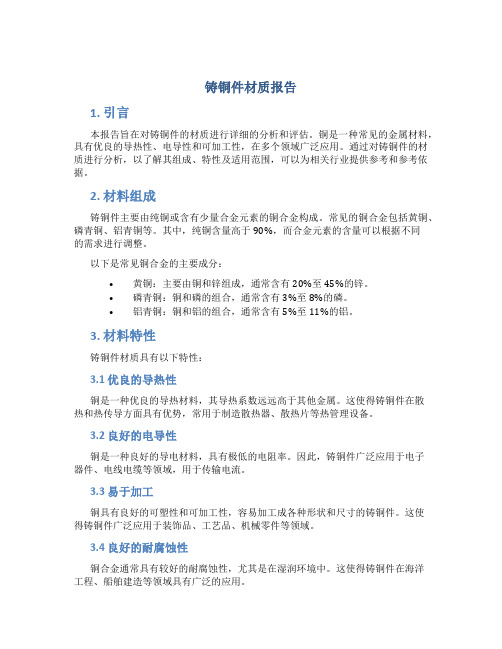
铸铜件材质报告1. 引言本报告旨在对铸铜件的材质进行详细的分析和评估。
铜是一种常见的金属材料,具有优良的导热性、电导性和可加工性,在多个领域广泛应用。
通过对铸铜件的材质进行分析,以了解其组成、特性及适用范围,可以为相关行业提供参考和参考依据。
2. 材料组成铸铜件主要由纯铜或含有少量合金元素的铜合金构成。
常见的铜合金包括黄铜、磷青铜、铝青铜等。
其中,纯铜含量高于90%,而合金元素的含量可以根据不同的需求进行调整。
以下是常见铜合金的主要成分:•黄铜:主要由铜和锌组成,通常含有20%至45%的锌。
•磷青铜:铜和磷的组合,通常含有3%至8%的磷。
•铝青铜:铜和铝的组合,通常含有5%至11%的铝。
3. 材料特性铸铜件材质具有以下特性:3.1 优良的导热性铜是一种优良的导热材料,其导热系数远远高于其他金属。
这使得铸铜件在散热和热传导方面具有优势,常用于制造散热器、散热片等热管理设备。
3.2 良好的电导性铜是一种良好的导电材料,具有极低的电阻率。
因此,铸铜件广泛应用于电子器件、电线电缆等领域,用于传输电流。
3.3 易于加工铜具有良好的可塑性和可加工性,容易加工成各种形状和尺寸的铸铜件。
这使得铸铜件广泛应用于装饰品、工艺品、机械零件等领域。
3.4 良好的耐腐蚀性铜合金通常具有较好的耐腐蚀性,尤其是在湿润环境中。
这使得铸铜件在海洋工程、船舶建造等领域具有广泛的应用。
3.5 优美的外观铜合金具有良好的颜色和质感,在许多情况下可以用作装饰材料。
铸铜件可以通过抛光、喷涂等方式进行表面处理,以提高外观效果。
4. 适用范围由于铸铜件材质的特性,其在多个领域具有广泛的应用。
以下是一些常见的应用领域:1.机械工程:铸铜件可用于制造各种机械零件,如齿轮、轴承、活塞等,以满足高强度和耐磨损的要求。
2.电子工程:铸铜件广泛应用于电子器件的制造,如电路板、散热片、导热模组等,以提供良好的导热和散热性能。
3.航空航天:铸铜件可用于制造飞机发动机零部件、导航仪器等,其优良的导热性和耐腐蚀性在航空航天领域中得到广泛应用。
Q345铸件失效分析报告

Q345铸件失效分析报告
发表时间:2015-05-29T16:41:36.320Z 来源:《工程管理前沿》2015年第7期供稿作者:周亮[导读] 高强大体积混凝土不仅要保证实现强度,尤其要预防开裂,尽可能提高密实性,降低水化热。
周亮(江苏省特种设备安全监督检验研究院徐州分院江苏徐州 221007)某厂一铸钢件在使用过程中发生断裂,应企业要求,对其宏观形貌、化学成分、金相组织、硬度、冲击性能、微观组织等进行分析。
线切割取样位置如图1所示。
1、宏观形貌及断口分析(1)整体检查图1为该断裂铸件的宏观形貌。
图2为铸件内外表面腐蚀情况。
经检查发现,该铸件除断口外,有4条明显裂缝,如图所示。
另外,该铸件内外表面腐蚀严重,多处地方存在明显生锈和剥落,如图2所示。
3、金相组织分析
分别对裂纹处试样及冲击试样进行金相检测,参考GB/T 8493-1987《一般工程用铸造碳钢金相》,经打磨、抛光后,用4%硝酸酒精腐蚀,100倍观察,所得金相照片如图10、11所示。
其金相组织为魏氏体+块状铁素体+珠光体。
6、结论
(1)由于Q345作为铸件使用时没有对应的标准或者相近材料作为参照对比,企业也没提供产品执行的技术指标,因此本分析报告只
能给出相对应的测试结果,供分析参考。
其中:C%- ,Si%- ;Mn%- ,P%- ,S%- ,Ni%- ,Cr%- ;金相组织为魏氏体+块状铁
素体+珠光体;硬度平均值为HV 113.06;冲击功AkV为7.0J,冲击韧性ak为8.8J;(2)铸件在使用过程中受到较大冲击力,产生裂缝并导致断裂;(3)铸件存在大量铸造缺陷,致使其性能下降。
手工铸造实验报告总结(3篇)
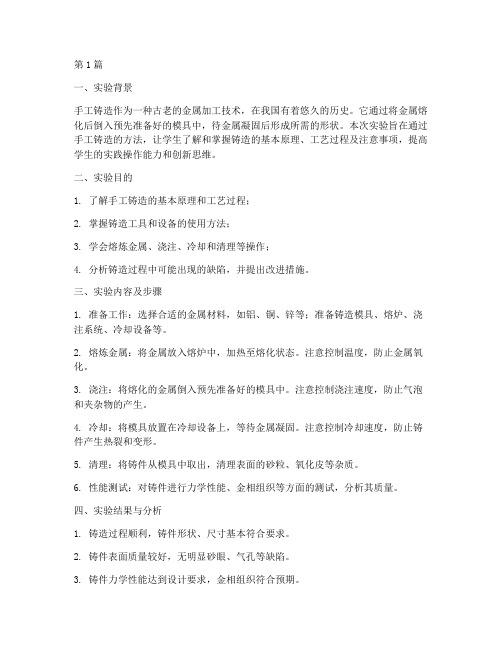
第1篇一、实验背景手工铸造作为一种古老的金属加工技术,在我国有着悠久的历史。
它通过将金属熔化后倒入预先准备好的模具中,待金属凝固后形成所需的形状。
本次实验旨在通过手工铸造的方法,让学生了解和掌握铸造的基本原理、工艺过程及注意事项,提高学生的实践操作能力和创新思维。
二、实验目的1. 了解手工铸造的基本原理和工艺过程;2. 掌握铸造工具和设备的使用方法;3. 学会熔炼金属、浇注、冷却和清理等操作;4. 分析铸造过程中可能出现的缺陷,并提出改进措施。
三、实验内容及步骤1. 准备工作:选择合适的金属材料,如铝、铜、锌等;准备铸造模具、熔炉、浇注系统、冷却设备等。
2. 熔炼金属:将金属放入熔炉中,加热至熔化状态。
注意控制温度,防止金属氧化。
3. 浇注:将熔化的金属倒入预先准备好的模具中。
注意控制浇注速度,防止气泡和夹杂物的产生。
4. 冷却:将模具放置在冷却设备上,等待金属凝固。
注意控制冷却速度,防止铸件产生热裂和变形。
5. 清理:将铸件从模具中取出,清理表面的砂粒、氧化皮等杂质。
6. 性能测试:对铸件进行力学性能、金相组织等方面的测试,分析其质量。
四、实验结果与分析1. 铸造过程顺利,铸件形状、尺寸基本符合要求。
2. 铸件表面质量较好,无明显砂眼、气孔等缺陷。
3. 铸件力学性能达到设计要求,金相组织符合预期。
4. 部分铸件出现轻微的热裂现象,经分析,可能是冷却速度过快或模具设计不合理所致。
五、实验总结1. 手工铸造是一种重要的金属加工方法,具有操作简便、成本低廉等优点。
2. 在实验过程中,要严格遵守操作规程,确保实验安全。
3. 熔炼金属时,要注意控制温度,防止金属氧化。
4. 浇注过程中,要控制浇注速度,避免气泡和夹杂物的产生。
5. 冷却过程中,要控制冷却速度,防止铸件产生热裂和变形。
6. 铸造模具的设计对铸件质量有很大影响,要充分考虑模具的刚度和强度。
7. 通过本次实验,使学生掌握了手工铸造的基本原理和工艺过程,提高了实践操作能力。
铝合金压铸件市场分析报告

铝合金压铸件市场分析报告1.引言1.1 概述铝合金压铸件是一种应用广泛的铝合金制品,它具有轻量化、高强度、耐腐蚀等优点,被广泛应用于汽车、航空航天、电子通讯等领域。
本报告旨在对铝合金压铸件市场进行全面的分析,包括市场概况、发展趋势、竞争格局等方面的研究,旨在为行业相关人士提供决策参考。
通过对市场的深入分析,可以帮助企业把握行业发展动向,寻找机遇,应对挑战,实现可持续发展。
1.2 文章结构文章结构本报告主要包括引言、正文和结论三个部分。
引言部分将对铝合金压铸件市场进行概述,介绍本报告的结构和目的,以及总结本报告所涉及的内容。
正文部分将详细分析铝合金压铸件市场的概况,包括市场规模、行业发展趋势和市场竞争格局等方面的内容。
结论部分将总结本报告的主要发现,展望铝合金压铸件市场的未来发展前景,并对整个报告进行总结概括。
1.3 目的:本报告的目的是对铝合金压铸件市场进行深入分析,以更好地了解市场的概况、发展趋势和竞争格局。
通过对市场的研究,我们旨在为相关行业提供可靠的市场信息和数据支持,帮助决策者制定更科学的发展策略。
同时,本报告还旨在为投资者提供决策参考,为企业制定未来发展规划提供依据。
通过对铝合金压铸件市场的全面分析,我们希望能够为行业发展和企业经营提供有益的帮助,促进行业的健康发展和可持续增长。
1.4 总结总结:通过对铝合金压铸件市场的深入研究分析,我们可以得出一些重要结论。
首先,铝合金压铸件市场正面临着快速增长的发展趋势,这得益于汽车、航空航天等行业的不断发展和需求增加。
其次,市场竞争格局日益激烈,企业需要不断提高技术水平和产品质量,以保持竞争力。
最后,在未来的市场前景展望中,铝合金压铸件市场有望继续保持稳步增长的态势,但同时也面临着技术创新、环保要求等挑战,企业需要做好准备并寻求发展机遇。
通过本报告的分析,可以为相关企业提供参考和指导,帮助他们更好地把握市场动态和发展方向。
2.正文2.1 铝合金压铸件市场概况铝合金压铸件市场概况铝合金压铸件是一种用铝合金为原料,通过压铸工艺制造而成的零部件,广泛应用于汽车、航空航天、电子通讯、军工等领域。
合金铸造实验报告总结(3篇)

第1篇一、实验目的本次合金铸造实验旨在通过实际操作,使学生了解和掌握合金铸造的基本原理、工艺流程以及影响铸造质量的因素。
通过实验,使学生能够熟练运用铸造技术,提高实际操作能力,为今后的工作打下坚实的基础。
二、实验内容1. 合金熔炼:了解不同合金的熔点、熔炼方法以及熔炼过程中的注意事项。
2. 合金铸造:学习铸型制作、浇注、冷却、脱模等铸造工艺。
3. 铸造缺陷分析:观察和分析实验中出现的铸造缺陷,如缩孔、裂纹、夹杂物等,了解其产生原因和预防措施。
4. 铸造性能测试:对铸造样品进行力学性能、金相组织等方面的测试,评估铸造质量。
三、实验过程1. 合金熔炼:按照实验要求,选取合适的合金材料,通过电弧炉进行熔炼。
在熔炼过程中,注意控制熔炼温度、熔炼时间以及熔体保护措施,以确保合金成分的均匀性。
2. 铸型制作:根据样品形状和尺寸,选用合适的铸型材料,制作出符合要求的铸型。
在铸型制作过程中,注意铸型的刚度、透气性和尺寸精度。
3. 浇注:将熔炼好的合金液倒入铸型中,注意控制浇注速度和温度,避免产生浇注缺陷。
4. 冷却与脱模:根据合金性质和铸型材料,确定合理的冷却速度。
冷却过程中,注意防止铸件变形和裂纹。
待铸件冷却至室温后,进行脱模。
5. 铸造缺陷分析:对实验中出现的铸造缺陷进行观察和分析,总结产生原因,并提出预防措施。
6. 铸造性能测试:对铸造样品进行力学性能、金相组织等方面的测试,评估铸造质量。
四、实验结果与分析1. 合金熔炼:实验过程中,成功熔炼了多种合金,如铝合金、铜合金等。
通过控制熔炼温度和熔炼时间,确保了合金成分的均匀性。
2. 铸型制作:根据实验要求,制作出符合要求的铸型,保证了铸件的尺寸精度和形状。
3. 铸造缺陷:在实验过程中,出现了一些铸造缺陷,如缩孔、裂纹、夹杂物等。
通过分析,发现这些缺陷主要是由熔炼、铸型制作、浇注、冷却等因素引起的。
针对这些缺陷,提出了相应的预防措施。
4. 铸造性能:对铸造样品进行力学性能、金相组织等方面的测试,结果表明,实验中铸造的合金具有良好的性能。
铸造仿真分析报告

铸造仿真分析报告1. 引言本文档为铸造仿真分析的报告,根据实际铸造工艺和仿真数据,对铸件的铸造过程进行了分析和评估。
通过仿真分析,可以提供准确的铸造工艺参数和辅助决策,从而优化铸造工艺,提高产品质量,降低生产成本。
本报告将详细介绍铸造仿真所涉及的模型、材料和分析结果,供相关人员参考。
2. 铸造模型在铸造仿真分析中,我们选择了某个具体的铸造模型进行仿真。
该模型是由CAD软件建模生成的三维几何模型,包括铸件和模具。
模具的形状和尺寸与真实情况一致,并考虑了芯子的位置和形状。
同时,还考虑了其他辅助结构和装备,如浇口、浇道和支撑结构等。
3. 材料参数在仿真分析中,材料参数是非常重要的输入。
通过实验和研究,我们得到了铸造材料的各种物理和力学参数。
这些参数包括材料的热尺寸、导热系数、比热容和机械性能等。
在铸造过程中,这些参数将直接影响到铸件的温度分布和变形情况。
4. 工艺参数铸造工艺参数是指在铸造过程中控制和调节的参数,如浇注温度、浇注速度、浇注方向和冷却时间等。
这些参数对于铸造过程的控制非常重要,能够直接影响铸件的质量和性能。
5. 仿真结果根据铸造模型和输入的材料参数和工艺参数,进行了铸造仿真。
通过仿真软件的模拟计算,得到了一系列的仿真结果。
这些结果包括铸件的温度分布、凝固曲线、应力分布和变形情况等。
这些结果能够直观地展示铸造过程的物理特性和工艺效果。
6. 结果分析根据仿真结果,我们对铸件的铸造过程进行了详细的分析。
根据温度分布,可以判断出铸件的凝固过程和热传导情况。
通过应力分布和变形情况,可以评估铸件的内部质量和外观形态。
同时,还可以根据仿真结果对铸造工艺参数进行优化和调整,以改善铸件的质量和性能。
7. 结论通过铸造仿真分析,我们得到了铸件的详细铸造过程和相关的物理特性。
通过分析模型和仿真结果,我们可以对铸造工艺参数进行优化和调整,以提高铸件的质量和效率。
此外,仿真分析还可以帮助我们预测和解决一些潜在的问题,如热裂纹和变形等。
铸件失效分析报告

铸件失效分析报告引言铸件是常用的金属成型工艺之一,广泛应用于各个领域的机械制造中。
然而,在使用过程中,铸件可能会出现失效现象,例如裂纹、变形、断裂等。
本报告旨在对铸件失效进行分析,找出失效的原因,并提出相应的建议。
一、失效描述在实际使用中发现某些铸件出现断裂现象。
断裂表现为铸件上出现明显的裂纹,并伴随着变形。
这些断裂的位置主要集中在铸件的连接处,例如焊接缝或连接孔。
二、失效原因分析经过对失效铸件的观察和分析,结合相关理论知识,我们初步推断铸件失效的原因可能是以下几个方面:1.材料问题:铸件可能使用了低质量的材料或者材料存在质量问题,导致其力学性能不符合要求,易发生断裂。
2.设计问题:铸件的设计可能存在缺陷,如圆角半径不足、壁厚变化过大等,导致应力集中,增加了断裂的风险。
3.制造问题:铸件的制造过程可能存在问题,例如铸型不完善、铸造温度控制不当等,造成铸件内部存在缺陷,从而降低了其强度。
4.使用问题:铸件在使用过程中可能受到了异常的外力载荷作用,或者受到了腐蚀、疲劳等环境因素的影响,导致断裂。
三、实验分析为了进一步确认铸件失效的原因,我们进行了一系列的实验分析。
首先,我们对失效铸件的材料进行了化学成分分析。
结果显示,铸件所使用的材料与设计要求的标准材料存在差异,材料中掺杂了较高含量的夹杂物,这可能是材料强度下降的主要原因。
进一步进行金相组织分析后发现,失效铸件的金相组织存在明显的缺陷和非均匀性。
部分区域存在晶界偏析和孔隙等缺陷,这些缺陷对铸件的强度和韧性具有显著的负面影响。
同时,我们对失效铸件的断口进行了扫描电镜观察。
观察结果显示,断裂面上存在明显的沿晶裂纹,这表明铸件可能存在应力集中的问题。
此外,断裂面上还发现了一些细小的颗粒,初步判断为夹杂物或者金属氧化物,这些颗粒的存在进一步加剧了铸件的脆性。
四、建议和改进措施基于对失效铸件的分析结果,我们提出了以下建议和改进措施:1.选择合适的材料:铸件的材料应符合设计要求的标准,并经过相关质量检测,避免选用低质量的材料。
- 1、下载文档前请自行甄别文档内容的完整性,平台不提供额外的编辑、内容补充、找答案等附加服务。
- 2、"仅部分预览"的文档,不可在线预览部分如存在完整性等问题,可反馈申请退款(可完整预览的文档不适用该条件!)。
- 3、如文档侵犯您的权益,请联系客服反馈,我们会尽快为您处理(人工客服工作时间:9:00-18:30)。
280 380 327 331 347 313 30.64
281.0 379.0 331.0 331.0 341.0 317.0 误差
1.41 375 363 1.41 317 331 5.66 255 260 0.00 341 321 8.49 341 341 5.66 287 285 9.3% 318.1 38.64
370 320 258 336 334 280 317
368 324 260 338 338 278 38.87
369.0 322.0 259.0 337.0 336.0 279.0 误差
1.41 2.83 1.41 1.41 2.83 1.41 12.3%
测量结果(转子产品硬度数据)
实物测量的偏差确认(4个点测量 中心部位、端面)
262.0 2.83 360 313.0 2.83 328 318.0 1.41 260 342.0 1.41 321 331.0 1.41 331 313.0 1.41 280 误差 8.4% 313.33 15HB
362 320 262 325 333 278 35.08
361.0 324.0 261.0 323.0 332.0 279.0 误差
★硬度计修理前的1302028的平均与其他产品的平均差值在4.3HB左右,所以可以判断修理有效。 ★作为参考,借用其他公司的打击式硬度计测量1302017的结果为268、285HB,幅度相同
容川出货检查方法变更
现有检查方法
KING 硬 测量设备 端面 度 测量位置 测 测量数量 每个批次1个样品,1处 量 每个批次1处
转子
零件名 复绕轮 曳引轮 曳引轮 转子 数量 10 31 12 36
6PCS
判定结果 OK OK OK ---
2处
2次
备注 2件特别采用
序号
1件特别采用 29件合格7件不合格
转子产品的硬度要求为240~260HB,36件产品中有7件测量结果为310HB左右
测量位置
端部;30mm 中间;55mm
測定位置
铸件产品分析报告
2013年4月10日
目录
测量方法问题点及改善 测量结果 容川出货检查方法变更 富士达受入检查方法变更 统一检测标准与方法
测量方法问题点及改善(1)
硬度计的校正
①把量具固定在产品上实施校 正(有很大的误差)
②量具的压力无法达到3000kg
校正、测定顺序 不明确 设备点检不足
测量结果(数据)
校正测定数据
试验片硬度 GE KING 578HLG 284HB 合格范围 578±6HLG 284±3% 5次测量数据
575,577,575, 578,575 283,283,285, 282,282
平均值 576.25HLG 283HB
差异 1.75HLG 1.0HB
误差 0.31% 0.35%
GE &KING 中心部位 GE 全检 4个位置 有问题时用KING
改善后检查方法
GE &KING 中心部位,避开冷铁 GE全检 1个位置
KING 每批次抽样3件,测4个位置
每个批次1PC 球化率 GB标准判定结果
每个批次1PC,1个位置 球化率 GB标准判定结果
统一检测标准与方法
减少意见分歧,达成共识。 GE硬度计将由富士达提供(约60天)。 GE硬度计提供前请使用KING硬度计测量。 GE硬度计提供前请测量端面部位。 检测方法注意事项 ★测量位置需打磨2~2.5mm后测量。 ★测量点需避开冷铁位置,测量4个位置时,每个测量点之间 需分隔90度。 ★一个产品4个测量点之间的硬度差需在15HB以内。 ★不能测量中间值时,上限规格值为“上限+中间规格值 X5%”或SIFT+15HB。
1.41 273 280 5.66 388 385 1.41 338 336 2.83 337 336 1.41 334 327 1.41 320 322 11.2% 331.3 33.7
276.5 386.5 337.0 336.5 330.5 321.0 误差
4.95 2.12 1.41 0.71 4.95 1.41 10.2%
偏差
3
转子
&0679SAR001
7
1301015 1212006 HB220~260 1212007 1302028 1302017 264 260 HB240~260 1302014 311 315 (硬度差15以 1302016 317 319 内) 1302030 343 341 1302022 330 332 1302023 312 314 平均值 313.2 26.29 端面与中心部差异
上限规格值=上限+中间规格值X5%是因为考虑了KING的测量误差
推进计划
星期一 4月8日 星期三 4月10日 星期五 4月12日 星期一 4月15日 星期三 4月17日 星期五 4月19日
双方沟通
4月22日 4月24日
GE订购
4月26日
生产启动
4月29日 5月1日 5月3日
5月6日
5月8日
5月10日
改善后检查方法
GE 中心部位,避开冷铁
每个批次全检1个位置
每个批次抽样3件,测量4个位置
每个批次1处
组织检查
球化率 碳素大小
数据
球化率 GB标准判定结果
照片
测量硬度的位置不要喷涂油漆,且在旁边位置标注测量数值。
富士达受入检查方法变更
现有检查方法
硬 测量设备 度 测量位置 测 测量数量 量 组织检查
5月13日
5月15日
5月17日
开始交货
5月20日 5月22日 5月24日 5月27日 5月29日
定期交流
5月31日
定期交流
6月3日 6月5日 6月7日 6月10日 6月12日 6月14日
定期交流
6月17日 6月19日 6月21日 6月24日 6月26日 6月28日
GE提供
标准统一
货期确认
供应商名称 芜湖市容川机电科技有限公司 芜湖市容川机电科技有限公司 芜湖市容川机电科技有限公司 芜湖市容川机电科技有限公司 芜湖市容川机电科技有限公司 芜湖市容川机电科技有限公司 芜湖市容川机电科技有限公司 芜湖市容川机电科技有限公司 芜湖市容川机电科技有限公司 芜湖市容川机电科技有限公司 芜湖市容川机电科技有限公司 芜湖市容川机电科技有限公司 芜湖市容川机电科技有限公司 芜湖市容川机电科技有限公司 芜湖市容川机电科技有限公司 芜湖市容川机电科技有限公司 芜湖市容川机电科技有限公司 芜湖市容川机电科技有限公司 芜湖市容川机电科技有限公司 芜湖市容川机电科技有限公司 芜湖市容川机电科技有限公司 芜湖市容川机电科技有限公司 芜湖市容川机电科技有限公司 芜湖市容川机电科技有限公司 芜湖市容川机电科技有限公司 芜湖市容川机电科技有限公司 芜湖市容川机电科技有限公司 部品号 &0382SAK001 &0679SAR001 &0619SFJ001 &0682SBE001 &0651SAA001 &0619SFH001 &0633SAM001 &0679SAR001 &0619SFH001 &0619SFJ001 &0619SFH001 &0619SFJ001 &0682GAJ001 &0633SAP001 &0679SAV001 &0682SBG001 &0651SAB001 &0633SAN001 &0679SAS001 &0682SBF001 &0619SFJ001 &0679SAR001 &0682SBE001 &0651SAA001 &&0678SAA001 &0619SFH001 &0633SAM001 部品名 绳轮素材 转子 端盖 绳轮素材 制动臂 编码器盖(毛坯) 机座毛坯 转子 编码器盖(毛坯) 端盖 编码器盖(毛坯) 端盖 绳轮毛坯 机座 转子 曳引轮 制动臂 箱体 转子 曳引轮 端盖 转子 绳轮素材 制动臂 制动靴 编码器盖(毛坯) 机座毛坯 数量 4 57 57 57 112 56 56 2 4 4 5 5 15 3 3 3 14 4 4 4 100 100 100 200 34 100 100 交期 20130221 20130207 20130207 20130207 20130207 20130207 20130207 20130120 20130228 20130228 20130310 20130310 20130207 20130315 20130315 20130315 20130315 20130315 20130315 20130315 20130410 20130410 20130410 20130410 20130410 20130410 20130410 交期再确认 订单日期 20121211 20130114 20130114 20130114 20130114 20130114 20130114 20130115 20130117 20130117 20130120 20130120 20130120 20130221 20130221 20130221 20130221 20130221 20130221 20130221 20130222 20130222 20130222 20130222 20130222 20130222 20130222 供应商承认日期 20130329 20130329 20130329 20130329 20130322 20130322 20130322 20130329 20130418 20130527 20130322 20130329 20130329 20130329 20130329 20130329 20130329 20130329 20130329 20130329 20130410 20130410 20130410 20130410 20130410 20130410 20130410 未入库数 1 28 35 28 92 31 37 2 4 4 5 5 4 3 3 3 14 4 4 4 100 100 100 200 34 100 100