工厂配料称量误差标准
混凝土配料秤(称重系统)检定规程
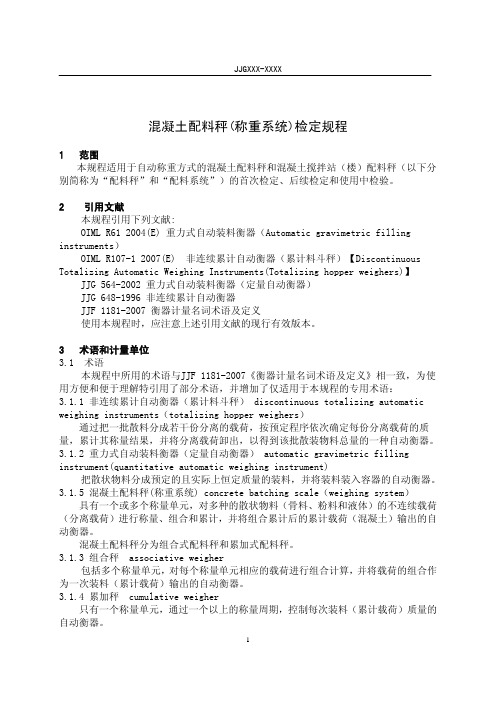
置零准确度
静态称量
偏载
鉴别力
7.3.3 物料检定
+
+
+
注:“+”表示应检项目,“-”表示可不检项目。
7.3 检定方法 7.3.1 外观检查
5 计量性能要求 5.1 准确度等级
配料秤的准确度等级划分为4个等级,用符号表示为:0.5,1,2, 5。 5.2 最大允许误差 5.2.1 自动称量
最大允许误差应是表1中累计载荷(装料)质量的百分数,可将其化整到最接近于 累计分度值(dt)的相应值。最大允许误差不适用于小于最小累计载荷(Σmin) 的装料。
3
JJGXXX-XXXX
给料装置的设计应能保证物料流量充足且稳定。
6.5 安装
配料秤应装配完整,并在使用位置固定。应保证无论是检定,还是实际使用,其
自动称量是相同的。
6.6 说明性标志
在配料秤的某一个醒目位置,有下列说明性标志。
·计量器具制造许可证的标志、编号
·配料秤的名称
·制造厂名称或商标
·配料秤的型号和序列号
表 1 自动称量的最大允许误差 MPE
准确度等级
累计载荷(装料)质量的百分数(%)
检定
使用中
0.2
0.4%
0.5%
0.5
0.8%
1.0%
1
1.6%
2.0%
2
4.0%
5.0%
注:若需要,可表中的数值化整到最接近的分度值倍数
5.2.2 静态称量 静态称量的最大允许误差应符合表2的规定。
2
JJGXXX-XXXX
公式,可得:
P=(100+0.5-0.3)kg=100.2kg
配料秤校正标定方法(试行)

配料秤校正标定方法(试行)配料是水泥生产最重要的环节,其优劣决定了产品质量的好坏和生产效益的高低,而配料皮带秤作为主要设备,在物料的输送过程中要完成对物料的称重,其准确度、可靠性和稳定性是控制的关键,为此须定期对配料秤进行校正和标定。
一、空称去皮配料秤在首次安装时、调节皮带张紧度或更换皮带后、更换传感器后、标定系数与正常比偏差±10%时,均应执行空称去皮程序。
其步骤如下:1、打死下料插板,空称运行5分钟,检查称体灵活性,皮带运行情况,计量托辊、十字簧片和传感器的接触面;2、现场仪表做好各参数记录,进入去皮程序后去皮;3、记录好去皮后参数,查找变化原因。
4、停下称体,挂码标定,校重量传感器线性。
根据传感器的量程选择挂码重量,最多挂码重量不得少于传感器量程的70%,根据线性比,至少取五个不同重量点标定,挂码重量与仪表显示重量相比,测试重量传感器的线性。
其误差范围不得大于1%。
二、实物标定工具:磅秤、秒表、计算器、接料盒(斗车)、铁锹、扫把等配料秤实物标定是利用在生产时实测流量,周期为每周一次,由分厂和电仪工段、质控处共同完成,标定步骤如下:1、检查称体运行情况:包括称体计量称架的灵活性;传感器、托辊、皮带运行状态是否良好;物料下料稳定性,仪表数据稳定性,在各项指标运行正常后方能开始标称;2、准备好计量相关器具,校好计量小磅秤;检查下料翻板的灵活,有无漏料等;3、现场仪表做好各参数记录,通知中控,进入实物标定程序;4、在正常运行时,标定人在打开翻板的同时按下秒表(尽量做到同步,减少人为误差),控制好接料时间和接料量,流量小于20T/H的称接料时间为皮带运行一圈,流量在20~40T/H之间的称接料时间为皮带运行3/4圈,流量大于40T/H的称接料时间为皮带1/2圈,收集完取的料称量,计算的流量值和仪表流量值比较,至少两次标定后按计算误差修改参数,在复测一次。
注:根据公司粉磨工艺会要求规定,此类大流量标定为每月一次,其它时候标定取料时间不得低于30S.5、标定完成记录各参数,如显示流量、实际瞬时流量、接料时长、实际物料重量、变频器频率、标定系数等,建立台账,掌握配料秤运行状态供以后对比和更好的查找问题。
工程混凝土配料秤的校准方法
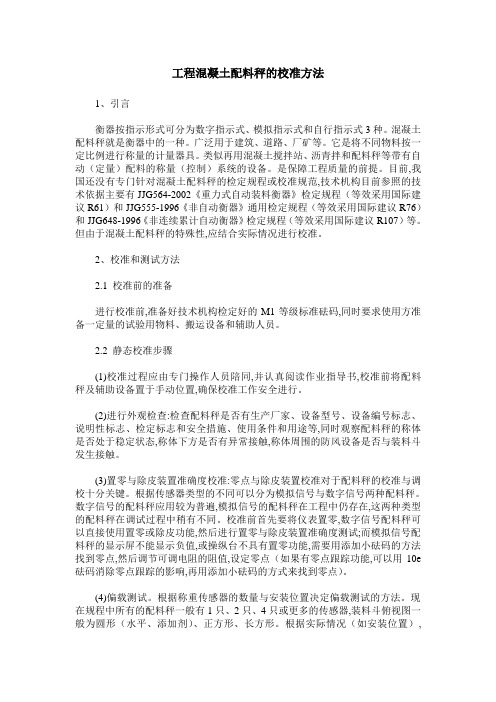
工程混凝土配料秤的校准方法1、引言衡器按指示形式可分为数字指示式、模拟指示式和自行指示式3种。
混凝土配料秤就是衡器中的一种。
广泛用于建筑、道路、厂矿等。
它是将不同物料按一定比例进行称量的计量器具。
类似再用混凝土搅拌站、沥青拌和配料秤等带有自动(定量)配料的称量(控制)系统的设备。
是保障工程质量的前提。
目前,我国还没有专门针对混凝土配料秤的检定规程或校准规范,技术机构目前参照的技术依据主要有JJG564-2002《重力式自动装料衡器》检定规程(等效采用国际建议R61)和JJG555-1996《非自动衡器》通用检定规程(等效采用国际建议R76)和JJG648-1996《非连续累计自动衡器》检定规程(等效采用国际建议R107)等。
但由于混凝土配料秤的特殊性,应结合实际情况进行校准。
2、校准和测试方法2.1 校准前的准备进行校准前,准备好技术机构检定好的M1等级标准砝码,同时要求使用方准备一定量的试验用物料、搬运设备和辅助人员。
2.2 静态校准步骤(1)校准过程应由专门操作人员陪同,并认真阅读作业指导书,校准前将配料秤及辅助设备置于手动位置,确保校准工作安全进行。
(2)进行外观检查:检查配料秤是否有生产厂家、设备型号、设备编号标志、说明性标志、检定标志和安全措施、使用条件和用途等,同时观察配料秤的称体是否处于稳定状态,称体下方是否有异常接触,称体周围的防风设备是否与装料斗发生接触。
(3)置零与除皮装置准确度校准:零点与除皮装置校准对于配料秤的校准与调校十分关键。
根据传感器类型的不同可以分为模拟信号与数字信号两种配料秤。
数字信号的配料秤应用较为普遍,模拟信号的配料秤在工程中仍存在,这两种类型的配料秤在调试过程中稍有不同。
校准前首先要将仪表置零,数字信号配料秤可以直接使用置零或除皮功能,然后进行置零与除皮装置准确度测试;而模拟信号配料秤的显示屏不能显示负值,或操纵台不具有置零功能,需要用添加小砝码的方法找到零点,然后调节可调电阻的阻值,设定零点(如果有零点跟踪功能,可以用10e 砝码消除零点跟踪的影响,再用添加小砝码的方式来找到零点)。
031原料药车间称量、配料岗位标准操作规程

1 目的制定中药车间、综合制剂车间、原料药车间称量、配料岗位的标准操作规程,规范称量、配料岗位人员的具体操作。
2 范围适用于中药车间、综合制剂车间、原料药车间称量、配料岗位的操作过程。
3 职责3.1中药车间、综合制剂车间、原料药车间称量、配料岗位负责实施。
3.2生产技术部、质量部负责监督。
4 内容4.1生产前准备4.1.1 岗位操作人员按照《人员进出生产区更衣标准操作规程》更衣后进入一般生产区或洁净区。
4.1.2 检查:操作间、设备及房间的清洁和状态标识牌;有无前次生产清场合格证正/副本,并在有效期内;设备有无“完好”标志和“已清洁”标志;计量器具有无“计量合格证”,并在有效期内;使用工具是否完好;容器具是否有“已清洁”标志。
检查岗位相关文件及生产记录是否齐全。
环境是否符合要求。
4.1.3 根据批生产指令到物料暂存间领取物料,领取时,认真核对品名、批号、数量、检验报告单等信息。
按物料品名、批号码放整齐。
4.1.4 在器具暂存间领取在清洁效期内的不锈钢桶,内衬洁净塑料袋。
山 东 百 维 药 业 有 限 公 司文件名称 称量、配料岗位标准操作规程文件编号:PM-SOP-031-00起 草 人: 起草日期: 部门:生产技术部审 核 人: 审核日期: 生产副总 页码 1/4 审 核 人: 审核日期: 质量部 版 本 号 00 批 准 人: 批准日期:质量副总生效日期颁发部门 质量部分发部门质量副总、生产副总、质量部、生产技术部、生产车间。
4.1.5 在门前生产标识牌上填写生产品种的相关信息; 4.2 操作过程: 4.2.1 配料4.2.1.1 称量前磅秤调零(一般区配料称量用磅秤或电子称),电子秤、电子天平开机预热15min-20min 后用标准砝码校验,并填写校验记录。
4.2.1.2 将计量器具空载,调至水平并调零。
根据批生产指令、批生产记录进行配料。
4.2.1.3 根据配料量选取合适的计量器具,称量时一人称量,另一人复核。
电子配料秤的单次称量相对误差
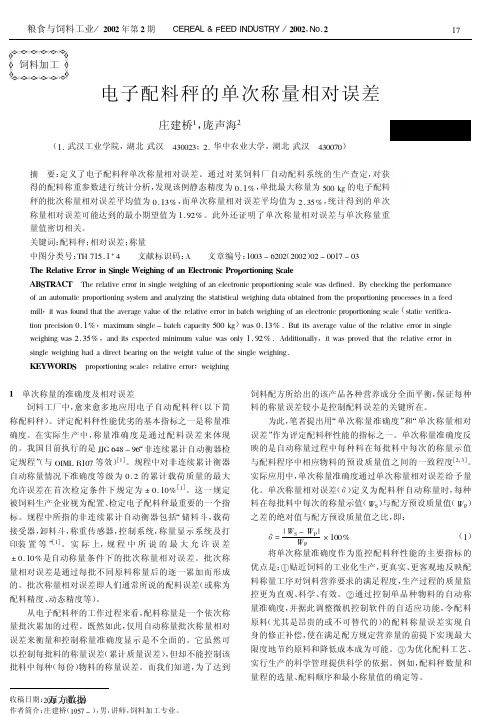
"
"
. 3 0
偏差 $ 为 ( !) $ ’ # ’-& 3 8 8 ’ # ’’& & ! " "13& 这里, ! 反映的是 13& 次单次称量条件下单次称量相对 $ ( !)8 误差的估计值; $ 反映的是 13& 个单次称量相对误差的分散 程度; 是平均值! 的 9 类标准不确定度 (用统计方法得 $ ( !) 出的不确定度) , 反映的是平均值! 分布的分散程度。 如果取置信概率 % 8 ’ # 7!, 查 ’ 分布 ’ : & 8 ! 6 % 8 13%,
整个配料工序采用计算机控制。在生产的同时, 计算机 对称量时间、 称量品种、 称量重量、 称量误差等相关参数同步 记录。在查定的 3’ 批配料称量生产记录中, 单次称量累计 (%) 对原始记录数据逐一计算单次称量相 13& 次。根据公式 对误差。将 13& 个单次称量的原始记录数据按相对误差 ( !) 值由小到大重新排列并进行统计。可以得到: 在 13& 次单次 称量的相对误差中, 相对误差不同值的有 %%! 个, 相对误差 的平均值为 & + 1!, 。其中相对误差为 ’ 的有 &1 个, 相对误 差的最大值为 &-, 。13& 个单次称量相对误差的数量分布 见表 -。 本例 13& 个单次称量相对误差的样本平均值! 为 % ! % 13& ! 8 ! "! ! !" 8 ’ # ’&1 ! " 8 13& ! 8% "8% 13& 个单次称量相对误差的样本标准偏差 $ 为 % ! % 13& & & ( ( !" 6!) 8 13% ! !" 6!) 8 ’ + ’-& 3 ! 6 %"! 8% "8% 13& 个单次称量相对误差的样本平均值 ! 分布的标准 $8
重量偏差允许范围
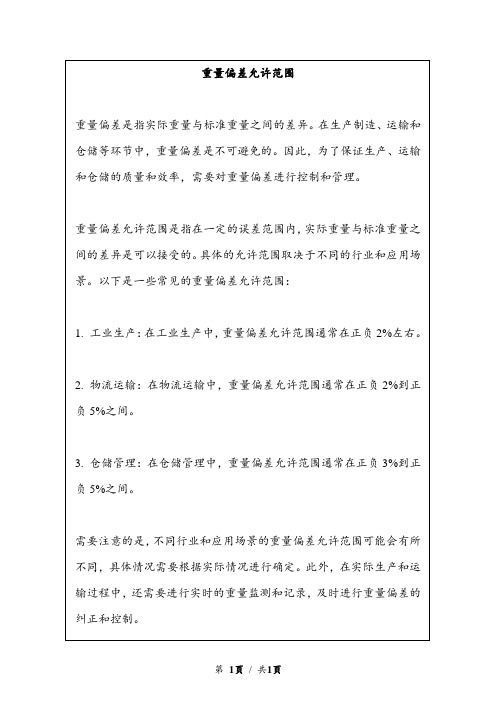
重量偏差允许范围
重量偏差是指实际重量与标准重量之间的差异。
在生产制造、运输和仓储等环节中,重量偏差是不可避免的。
因此,为了保证生产、运输和仓储的质量和效率,需要对重量偏差进行控制和管理。
重量偏差允许范围是指在一定的误差范围内,实际重量与标准重量之间的差异是可以接受的。
具体的允许范围取决于不同的行业和应用场景。
以下是一些常见的重量偏差允许范围:
1. 工业生产:在工业生产中,重量偏差允许范围通常在正负2%左右。
2. 物流运输:在物流运输中,重量偏差允许范围通常在正负2%到正负5%之间。
3. 仓储管理:在仓储管理中,重量偏差允许范围通常在正负3%到正负5%之间。
需要注意的是,不同行业和应用场景的重量偏差允许范围可能会有所不同,具体情况需要根据实际情况进行确定。
此外,在实际生产和运输过程中,还需要进行实时的重量监测和记录,及时进行重量偏差的纠正和控制。
第1页/ 共1页。
lcs配料称标准
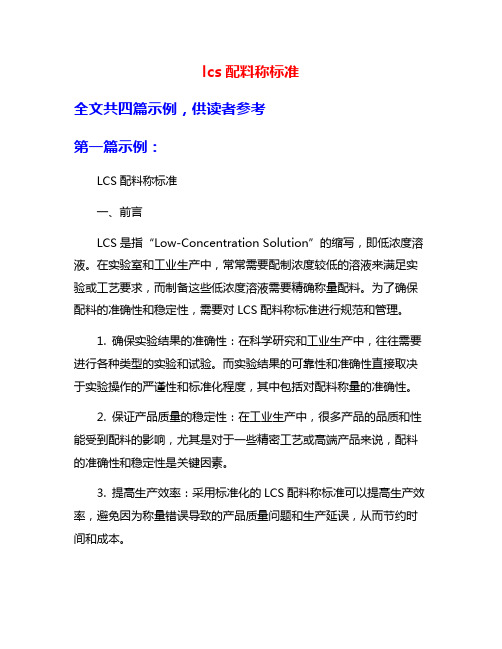
lcs配料称标准全文共四篇示例,供读者参考第一篇示例:LCS配料称标准一、前言LCS是指“Low-Concentration Solution”的缩写,即低浓度溶液。
在实验室和工业生产中,常常需要配制浓度较低的溶液来满足实验或工艺要求,而制备这些低浓度溶液需要精确称量配料。
为了确保配料的准确性和稳定性,需要对LCS配料称标准进行规范和管理。
1. 确保实验结果的准确性:在科学研究和工业生产中,往往需要进行各种类型的实验和试验。
而实验结果的可靠性和准确性直接取决于实验操作的严谨性和标准化程度,其中包括对配料称量的准确性。
2. 保证产品质量的稳定性:在工业生产中,很多产品的品质和性能受到配料的影响,尤其是对于一些精密工艺或高端产品来说,配料的准确性和稳定性是关键因素。
3. 提高生产效率:采用标准化的LCS配料称标准可以提高生产效率,避免因为称量错误导致的产品质量问题和生产延误,从而节约时间和成本。
1. 确定配料称量的精度要求:根据实验或生产的需要确定配料称量的精度要求,一般来说,LCS溶液的精确度要求比较高,通常要求误差在0.1%以内。
2. 确定配料称标的单位:根据实验或生产的需要确定配料称标的单位,一般来说,常用的称量单位有克、毫克、微克等。
3. 确定称量方法和工具:根据配料称量的性质和要求确定称量方法和工具,一般来说,常用的称量方法有天平称量、分注管称量等,工具有电子天平、瓶口分注器等。
4. 制定称量规程和操作规范:根据实验室或生产车间的具体情况,制定配料称标的规程和操作规范,明确称量的步骤和操作要求,加强对操作人员的培训和管理。
1. 配料称标的标准化:建立健全的LCS配料称标准规范体系,明确配料称标的要求、方法、程序和责任,确保每一次称量都能够符合标准要求。
2. 设备的维护和校准:定期对配料称标使用的设备进行维护和校准,保持设备的良好状态和准确度,确保称量的准确性和可靠性。
3. 资料的记录和管理:建立配料称标的档案记录系统,记录每一次称量的配料信息、操作人员、日期、时间等关键信息,便于查证和追溯。
1公斤以下重量的误差标准

1公斤以下重量的误差标准根据不同的物品和应用场景而有所不同。
根据国家重量标准,对于粮食、蔬菜、水果等每公斤价值在6元内的物品,称重1公斤以下的允许20克的误差。
对于肉、蛋、禽、海产品、糕点、糖果、调味品类等,每公斤价值在6元至30元以内的物品,称重为0.5公斤的允许1克的误差,称重为0.5公斤以上至2公斤的允许2克的误差,称重在2公斤以上至5公斤的允许3克的误差。
需要注意的是,具体情况可能会受到不同因素的影响,如物品的性质、计量设备的精度等。
因此,在实际操作中,应根据具体的要求和条件来确定相应的误差标准。
以上信息仅供参考,如需了解更多信息,建议查阅国家相关标准文件或咨询行业专业人士。
拌合站材料计量允许误差

拌合站材料计量允许误差
对于拌合站的材料计量允许误差,一般根据相关标准和规定而定。
以下是一些常见的计量允许误差范围参考:
1. 水泥:允许误差通常在±1%以内。
2. 砂子和骨料:允许误差通常在±2%以内。
3. 水:允许误差通常在±1%以内。
4. 外加剂:允许误差通常在±3%以内。
需要注意的是,这些允许误差范围只是一般参考值,具体的计量允许误差应根据相关的国家标准、行业标准或项目规范确定。
在实际操作中,应严格按照相关标准和规定进行计量,并定期进行检定和校准,以确保拌合站的生产质量和工程质量。
不同称量段的最大允许误差

不同称量段的最大允许误差哎呀,大家好!今天咱们来聊聊“不同称量段的最大允许误差”这个话题。
你可能觉得这听起来有点晦涩,不太容易理解。
但咱们生活中随时随地都在接触这些东西,就像你去买水果称重,或者在厨房里量点调料一样,多少都会用到一些“误差”吧!今天我们就来简单明了地捋一捋这些“误差”背后的玄机。
什么叫“不同称量段”?其实就是根据你称的东西重量的不同,误差的标准也不一样。
你想象一下,如果你称一个一克重的小小药丸,和称一个十公斤重的西瓜,误差肯定是不一样的,对吧?一个微小的药丸,哪怕误差大一点也没啥影响,但那个十公斤的西瓜,稍微一偏差,可能就要少给你几块,或者多给你几块。
懂了吧?这就是“称量段”带来的区别。
我们说的“最大允许误差”,说白了就是每次称重时,给定的“允许”范围。
你可以理解为,就像考试的分数,错一点没关系,只要不超出规定的标准,大家都能接受。
假如你去买苹果,商贩说“这个苹果称重准确,最多误差不超过五克”,那如果你买了个五百克的苹果,它的实际重量可能是495克,也可能是505克,只要在这个范围内,大家都能心安理得地接受。
这就是“最大允许误差”。
说到这里,咱们再来聊聊这些“误差”的具体计算。
嗯,你看,称重的误差并不是一成不变的,它和你称的物品的重量直接相关。
如果称得越重,误差的比例就越小。
举个例子,假如你称一个1000克的重物,最大允许误差可能是2克;而如果是称50克的小物品,误差可能就大一些,可能是0.5克。
有没有觉得这就像是人一样,体重大的人不容易犯错,轻的容易出错?哈哈,开玩笑啦,毕竟谁都可能犯错,尤其是我这种经常跑题的人。
其实说到这,你可能有个疑问:“哎,那这个误差会不会让我买到的东西少了或者多了?”嗯,老实说,误差本身并不意味着欺诈。
毕竟每一台秤都有它的容忍度,这种误差范围是经过设计和测试的,商家可不是故意坑你。
不过,如果你真的觉得有问题,也可以要求商家重新称量。
就像买菜一样,买的多了,大家开心,买得少了,你就能少花点钱,哈哈,是不是?但这里面有个小陷阱,商家可能会故意选择一些轻一点的秤,或者在称量过程中偷偷“掉点水分”,所以对这误差的理解很重要。
拌和站粉料误差范围

拌和站粉料误差范围
拌和站是指专门用于混合水泥、砂子、石子等材料制作混凝土的设备。
在混凝土生产过程中,粉料是非常重要的一个组成部分。
粉料误差范
围是指在混凝土生产过程中,由于各种因素的影响,粉料实际用量与
设计用量之间存在的误差范围。
一般来说,拌和站粉料误差范围应该控制在正负2%以内。
具体来说,如果设计用量为1000kg的话,那么实际使用的粉料应该控制在
980kg到1020kg之间。
这个误差范围可以通过以下几个方面进行控制:
1. 设备精度:拌和站设备本身应该具有一定的精度保证。
例如,在计
量仪表方面,应选择高品质、高稳定性的仪表,并进行定期校验和维护。
2. 原材料质量:为了保证混凝土生产过程中的粉料误差范围不超过正
负2%,必须对原材料进行严格检验和筛选。
例如,在进货时应检查原材料是否符合国家标准,并对其进行化验分析,以确保其质量符合要求。
3. 操作技能:拌和站操作人员应具备一定的技能和经验,能够熟练掌
握设备的操作方法,并且在生产过程中能够根据实际情况进行调整和
处理。
4. 生产管理:拌和站生产过程应该进行全面的管理。
例如,在生产过
程中应建立完善的记录系统,对每一批混凝土原材料使用量进行记录,并严格按照工艺流程进行操作。
总之,控制拌和站粉料误差范围是保证混凝土质量稳定性的重要环节。
只有通过科学、规范、严谨的生产管理,才能够达到这一目标。
国家称量器具误差范围

国家称量器具误差范围
国家称量器具误差范围是指器具在正常使用条件下测量结果与真实值之间的误差范围。
根据国际标准ISO 9001-2015《质量
管理体系标准》和国家标准《量具技术规范》的规定,国家称量器具的误差范围应在规定的允许误差范围内。
具体的国家称量器具误差范围取决于其所属的类别和测量范围。
例如,常见的称量器具包括千分秤、百分秤、万分秤等,其允许误差范围通常为最大允许误差的一半。
即,若一个器具的最大允许误差为±0.01克,其误差范围通常为±0.005克。
此外,国家称量器具还需定期进行校准和检验,以确保其测量结果的准确性和可靠性。
校准和检验的频率和方法也受到国家标准的规定。
对于一些特殊用途的称量器具,如衡器和质量流量计等,其误差范围和校准要求可能会更加严格。
需要注意的是,不同国家和地区可能存在不同的标准和规定,对于国家称量器具误差范围的具体要求可能会有所不同。
因此,在使用国家称量器具时,应参考并遵守所在地区的相关法规和标准。
ZD37物料数量允许误差标准
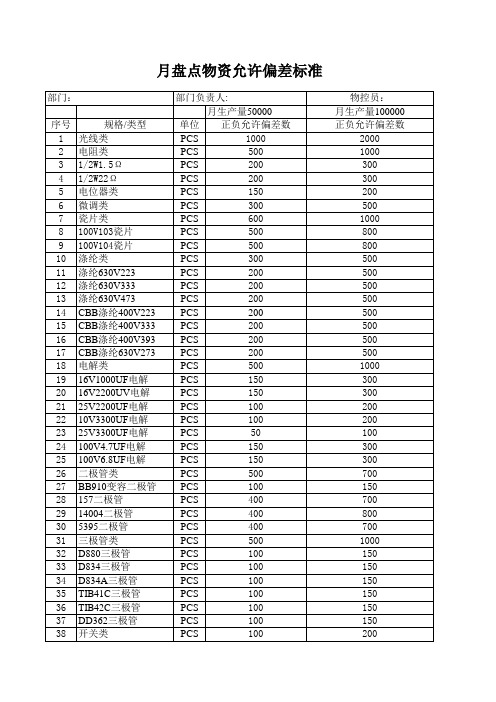
部门: 序号 1 2 3 4 5 6 7 8 9 10 11 12 13 14 15 16 17 18 19 20 21 22 23 24 25 26 27 28 29 30 31 32 33 34 35 36 37 38 规格/类型 光线类 电阻类 1/2W1.5Ω 1/2W22Ω 电位器类 微调类 瓷片类 100V103瓷片 100V104瓷片 涤纶类 涤纶630V223 涤纶630V333 涤纶630V473 CBB涤纶400V223 CBB涤纶400V333 CBB涤纶400V393 CBB涤纶630V273 电解类 16V1000UF电解 16V2200UV电解 25V2200UF电解 10V3300UF电解 25V3300UF电解 100V4.7UF电解 100V6.8UF电解 二极管类 BB910变容二极管 157二极管 14004二极管 5395二极管 三极管类 D880三极管 D834三极管 D834A三极管 TIB41C三极管 TIB42C三极管 DD362三极管 开关类 部门负责人: 月生产量50000 单位 正负允许偏差数 PCS 1000 PCS 500 PCS 200 PCS 200 PCS 150 PCS 300 PCS 600 PCS 500 PCS 500 PCS 300 PCS 200 PCS 200 PCS 200 PCS 200 PCS 200 PCS 200 PCS 200 PCS 500 PCS 150 PCS 150 PCS 100 PCS 100 PCS 50 PCS 150 PCS 150 PCS 500 PCS 100 PCS 400 PCS 400 PCS 400 PCS 500 PCS 100 PCS 100 PCS 100 PCS 100 PCS 100 PCS 100 PCS 100 物控员: 月生产量100000 正负允许偏差数 2000 1000 300 300 200 500 1000 800 800 500 500 500 500 500 500 500 500 1000 300 300 200 200 100 300 300 700 150 700 800 700 1000 150 150 150 150 150 150 200
饲料检测结果判定的允许误差标准

饲料检测结果判定的允许误差标准《饲料检测结果判定的允许误差》标准《GB/T18823—2002饲料检测结果判定的允许误差》标准饲料质量监督检测部门和饲料生产部门对饲料产品质量检测结果判定是否合格时使用。
饲料产品只有检测结果超出(低于或高于)本标准所规定的允许误差范围,才能判定该产品确实不合格。
饲料质量检测结果判定的允许误差见表1、表2、表3的规定。
表1饲料一般营养指标检测结果判定允许误差测定营养指标/(%) 允许误差(绝项目对误差)/(%)水分 <5 +0.25~10 +0.3>10~15 +0.4>15~20 +0.5>20~30 +0.6>30~40 +0.8>40 +1.0粗蛋<5 -0.3白质 5~10 -0.4>10~15 -0.6>15~20 -0.8>20~25 -1.0>25~30 -1.1>30~40 -1.2>40~50 -1.3>50~60 -1.4>60~70 -1.5>70 -1.6粗脂<2 -0.2肪 2~3 -0.3>3~4 -0.4>4~6 -0.5>6~9 -06>9~12 -0.7>12~15 -0.8>15 -1.0 粗纤<3 +0.4 维 3~5 +0.6>5~7 +0.8>7~9 +1.0>9~12 +1.2>12~15 +1.4>15 +1.6 测定营养指标/(%) 允许误差(绝项目对误差)/(%) 粗灰<5 +0.1 分 5~7 +0.2>7~9 +0.3>9~11 +0.4>11~13 +0.5>13~16 +0.6>16~20 +0.7>20 +0.8 钙镁 <0.5 ?0.1 0.5~1 ?0.15>1~2 ?0.2>2~3 ?0.3>3~4 ?0.4>4~5 ?0.6>5~10 ?0.9>10~15 ?1.2>15 ?1.5总磷 <0.5 -0.1>0.5~1 -0.15>1~2 -0.2>2~3 -0.3>3~4 -0.4>4~5 -0.6>5~10 -0.9>10~15 -1.2>15 -1.5 食盐 <0.3 ?0.05 >0.3~1 ?0.1>1~2 ?0.2>2~3 ?0.3>3~4 ?0.4>4~5 ?05>5 ?0.6 赖氨<0.5 -0.1 酸、蛋0.5~1 -0.15 氨酸>1~2 0.25>2~3 -0.4>3~4 -0.55>4~5 -0.7>5~8 -0.9>8 -1.2 色氨<0.2 -0.04 酸 0.2~0.5 -0.08>0.5~1 -0.12>1~2 -0.2>2~3 -0.3>3 -0.4注1:“+”号表示营养指标值加上允许误差值(高限值),即小于或等于该值时为合格。
饲料配料系统配料精度误差分析
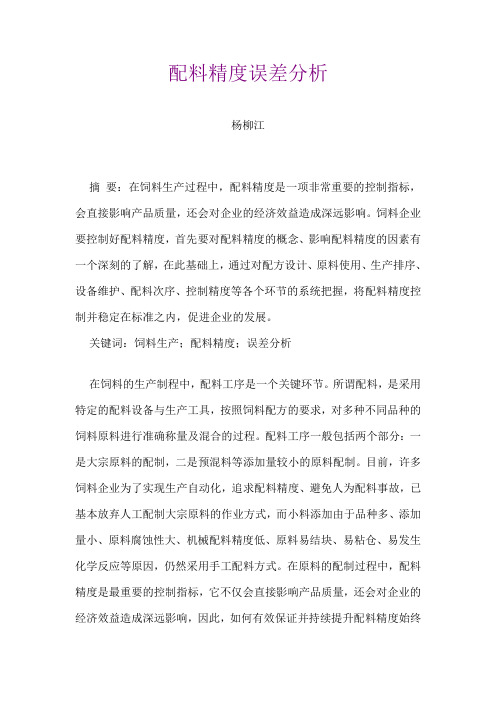
配料精度误差分析杨柳江摘要:在饲料生产过程中,配料精度是一项非常重要的控制指标,会直接影响产品质量,还会对企业的经济效益造成深远影响。
饲料企业要控制好配料精度,首先要对配料精度的概念、影响配料精度的因素有一个深刻的了解,在此基础上,通过对配方设计、原料使用、生产排序、设备维护、配料次序、控制精度等各个环节的系统把握,将配料精度控制并稳定在标准之内,促进企业的发展。
关键词:饲料生产;配料精度;误差分析在饲料的生产制程中,配料工序是一个关键环节。
所谓配料,是采用特定的配料设备与生产工具,按照饲料配方的要求,对多种不同品种的饲料原料进行准确称量及混合的过程。
配料工序一般包括两个部分:一是大宗原料的配制,二是预混料等添加量较小的原料配制。
目前,许多饲料企业为了实现生产自动化,追求配料精度、避免人为配料事故,已基本放弃人工配制大宗原料的作业方式,而小料添加由于品种多、添加量小、原料腐蚀性大、机械配料精度低、原料易结块、易粘仓、易发生化学反应等原因,仍然采用手工配料方式。
在原料的配制过程中,配料精度是最重要的控制指标,它不仅会直接影响产品质量,还会对企业的经济效益造成深远影响,因此,如何有效保证并持续提升配料精度始终是饲料机械制造厂家与饲料企业要面对的课题。
本文重点讨论在现存的各种配料工艺及设备状况下影响配料精度的原因,以及在生产工艺与设备固定的情况下,如何有效提升生产现场的配料精度。
1 配料精度的概念配料精度就是要将配料误差控制在一定范围之内。
配料精度分为静态精度与动态精度。
静态精度是指在静止状态下(即配料完成后),实际配料量与设计配料量之间的误差值。
动态精度是指在动态状态下(即配料过程中),实际配料量与设计配料量之间的误差值。
在现阶段,国家标准为静态0.1% FS,动态0.3% FS(FS = Full Scale,满量程)。
2 控制配料精度的意义2.1 配料误差对成本造成的批次效应表1 猪浓缩饲料配方表1是一个猪浓缩饲料配方。
包装车间包装计量偏差表

为规范包装操作过程,控制包装过程风险,提高成品包装重量的稳定性,对
1、包装车间可根据包装成品的最大允许偏差来选择相应的称量工具,包括机械磅称,电子称等,所选用计量工具精度必须满足称量精度的要求。
例如;
﹙1﹚称重1.0~5.0公斤的物料,必须使用精确到5克以内的电子称或机械磅称来称量;
﹙2﹚称重5.1~30.0公斤的物料,必须使用精确到10克以内的电子称或机械磅称来称量;
﹙3﹚称重30.1~50.0公斤的物料,必须使用精确到50克以内的电子称或机械磅称来称量;
﹙4﹚称重50.1~100.0公斤的物料,必须使用精确到100克以内的电子称或机械磅称来称量;
﹙5﹚称重100.1~500.0公斤的物料,必须使用精确到500克以内的电子称或机械磅称来称量;
2、所有包装原始记录单的记录以实际包装的数量填写,禁止假填、虚填、错填、漏填写包装原始记录单;
编制:审核:批准:
1。
配料称实验报告

一、实验目的1. 理解配料称的工作原理和操作方法。
2. 掌握配料称的校准过程和精度测试方法。
3. 通过实际操作,提高对配料称在实际生产中的应用能力。
4. 学习并运用质量控制理论,确保配料过程的准确性。
二、实验仪器与材料1. 配料称一台2. 配料容器若干3. 待称物料(如:面粉、糖、盐等)4. 电子秤一台5. 秤盘若干6. 计时器一台7. 记录本和笔三、实验步骤1. 准备阶段- 检查配料称的电源和信号线是否完好,确保仪器正常工作。
- 将待称物料放置在配料容器中,确保物料表面平整,便于称量。
- 打开配料称,预热至正常工作温度。
2. 校准阶段- 将电子秤放置在配料称上,调整电子秤至零位。
- 打开配料称,进行自检,确保仪器无故障。
- 使用标准砝码对配料称进行校准,记录校准结果。
3. 配料操作- 根据配方要求,输入所需配料的种类和数量。
- 启动配料称,将物料逐个放入配料容器中。
- 观察配料称的显示屏,确保物料重量准确。
- 当配料完成时,关闭配料称,记录实际配料重量。
4. 精度测试- 使用电子秤对配料容器中的物料进行称重,记录实际重量。
- 计算配料称的称量误差,分析误差原因。
5. 实验总结- 对实验过程进行总结,包括操作步骤、结果分析、注意事项等。
- 提出改进措施,提高配料称的精度和效率。
四、实验结果与分析1. 校准结果- 校准后,配料称的精度达到±0.1g,满足实验要求。
2. 配料结果- 实验过程中,配料称准确地将物料配至所需重量,误差在±0.2g以内。
3. 精度测试结果- 精度测试结果显示,配料称的称量误差在±0.5g以内,符合国家标准。
五、实验结论1. 配料称是一种高精度、自动化程度高的配料设备,广泛应用于食品、化工、医药等行业。
2. 配料称的操作简单,易于掌握,能够提高配料效率,降低人工成本。
3. 通过实验,验证了配料称的精度和可靠性,为实际生产提供了有力保障。
六、实验反思1. 在实验过程中,应严格按照操作规程进行,确保配料称的正常工作。
- 1、下载文档前请自行甄别文档内容的完整性,平台不提供额外的编辑、内容补充、找答案等附加服务。
- 2、"仅部分预览"的文档,不可在线预览部分如存在完整性等问题,可反馈申请退款(可完整预览的文档不适用该条件!)。
- 3、如文档侵犯您的权益,请联系客服反馈,我们会尽快为您处理(人工客服工作时间:9:00-18:30)。
10kg-50kg(含)
±50g
4
>50kg
±100g
油脂类 注
1
0-100kg(含)
±1kg
使用抽油系统抽料
2
>100kg
±2kg
使用抽油系统抽料
鲜货、泡菜类原料
序号
重量范围
误差值
备 注
1
0-10kg(含)
±50g
2
>10kg
±100g
2
非限量粉类添加剂
±1g
除限量添加剂外
3
0--3kg(含)
±5g
4
3kg-10kg(含)
±10g
5
10kg-30kg(含)
±30g
6
30kg-50kg(含)
±50g
7
>50kg
±100g
半固体、液体原料
序号
重量范围
误差值
备 注
1
液体类添加剂
±5g
包含花椒油树脂、辣椒红、香精等
2
0-10kg(含)
±30g
原料称量误差标准
一、目的
为统一原料在配制过程的误差标准,规范人员操作,特制定本标准。
2、适用范围
适用于配料过程中原料称量的误差要求。
3、职责
1、各工厂配料车间按照标准要求执行、管理;
2、工厂QC负责日常监督查核。
4、称量标准要求
固体、粉类原料
序号
重量范围
误差值
备 注
1
限量粉类添加剂
±0.2g
山梨酸钾、干贝素(琥珀酸二钠)、茶多酚、二氧化硅、乳酸链球菌素等