浅谈电镀后处理脱水常见问题及解决方法
电镀行业企业存在问题及相应整改措施
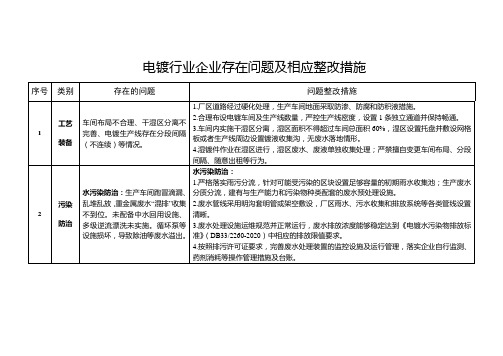
降耗 带出液回收装置,未配备中水回 用单级漂洗或直接冲洗等落后工艺。
用设施等问题。
3.加强废水重复利用,减少废水排放量,鼓励中水回用设施建设。
序号 类别
存在的问题
问题整改措施
厂容厂貌差,生产工艺流程图、
4
环境 管理
废水走向图、废气走向图未上墙。 部分电镀流水线、电镀槽等生产 设备未在明显位置悬挂防腐标志
1.定期委托具有监测资质的单位开展环境监测,监测频次、因子符合规范要求。 2.建设地下水监测井,实施定期巡查,开展地下水水质监测。
牌。
车间硫酸、液碱储罐围堰高度不 1.编制突发环境事件应急预案(或综合应急预案且包含突发环境事件应对内容)且及时更
环境 够导致不能满足应急要求;事故 新。 5
风险 废水外溢厂界对周边环境造成影 2.电镀企业应设置应急事故水池,事故废水应急池容量应满足事故状态下收集泄漏物料,
电镀行业企业存在问题及相应整改措施
序号 类别
存在的问题
问题整改措施
1.厂区道路经过硬化处理,生产车间地面采取防渗、防腐和防积液措施。
1
善、电镀生产线存在分段间隔 (不连续)等情况。
2.合理布设电镀车间及生产线数量,严控生产线密度,设置 1 条独立通道并保持畅通。 3.车间内实施干湿区分离,湿区面积不得超过车间总面积 60%,湿区设置托盘并敷设网格 板或者生产线周边设置镀液收集沟,无废水落地情形。 4.湿镀件作业在湿区进行,湿区废水、废液单独收集处理;严禁擅自变更车间布局、分段
药剂消耗等操作管理措施及台账。
序号 类别
存在的问题
问题整改措施
大气污染防治:
1.所有电镀生产线统一落实大包围、全封闭集气,确因生产工艺需要无法全封闭的,废气
电镀常见不良问题点分析及对策
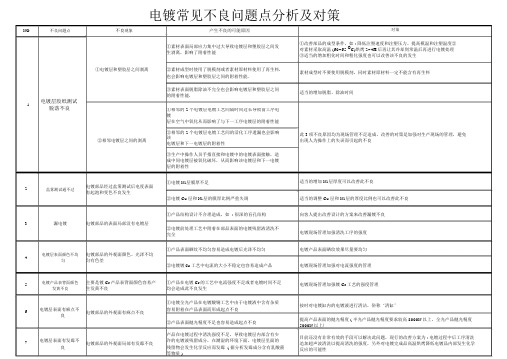
电镀常见不良问题点分析及对策NO.不良问题点不良现象产生不良的可能原因①素材表面局部应力集中过大导致电镀层和塑胶层之间发生剥离,影响了附着性能①电镀层和塑胶层之间剥离②素材成型时使用了脱模剂或者素材原材料使用了再生料.也会影响电镀层和塑胶层之间的附着性能.③素材表面脱脂除油不完全也会影响电镀层和塑胶层之间电镀层胶纸测试的附着性能.1脱落不良①相邻的 2个电镀层电镀工艺间隔时间过长导致前工序电镀层在空气中氧化从而影响了与下一工序电镀层的附着性能②相邻电镀层之间的剥离②相邻的 2个电镀层电镀工艺间的活化工序遗漏也会影响该电镀层和下一电镀层的附着性对策①改善部品的成型条件,如 : 降低注塑速度和注塑压力、提高模温和注塑温度②对素材采取高温 (60~65 O C)烘烤2~4H后再让其冷却到常温后再进行电镀处理③适当的增加粗化时间和粗化强度也可以改善该不良的发生素材成型时不要使用脱模剂,同时素材原材料一定不能含有再生料适当的增加脱脂、除油时间此3项不良原因均为现场管理不足造成,改善的对策是加强对生产现场的管理,避免出现人为操作上的失误而引起的不良2 3 4 5 6 7③生产中操作人员手指直接和电镀中的电镀表面接触,造成中间电镀层被氧化破坏,从而影响该电镀层和下一电镀层的附着性电镀部品经过盐雾测试后电度表面①电镀 Ni层膜厚不足盐雾测试通不过有起泡和变色不良发生②电镀 Cu层和Ni层的膜厚比例严重失调①产品结构设计不合理造成,如 : 很深的盲孔结构漏电镀电镀部品的表面局部没有电镀层②电镀前处理工艺中附着在部品表面的电镀残留液清洗不完全电镀部品的外观面颜色、光泽不均①产品表面晒纹不均匀容易造成电镀后光泽不均匀电镀层表面颜色不均匀匀有色差②电镀镀C u工艺中电流的大小不稳定也容易造成产品电镀产品表背面颜色主要是镀 Cr产品表背面颜色容易产①产品在电镀 Cr的工艺中电流强度不足或者电镀时间不足发黄不良生发黄不良均会造成此不良发生①电镀全光产品在电镀酸铜工艺中由于电镀液中含有杂质电镀层表面有麻点不电镀部品的外观面有麻点不良容易附着在产品表面而形成起点不良良②产品表面抛光精度不足也容易造成起点不良产品在电镀过程中清洗强度不足,导致电镀层内部含有少电镀层表面有发霉不电镀部品的外观面局部有发霉不良许的电镀液残留成分,在潮湿的环境下面,电镀层里面的良残留物会发生化学反应而发霉 ( 据分析发霉成分含有乳酸菌等物质 )适当的增加 Ni层厚度可以改善此不良适当的调整 Cu层和Ni层的厚度比例也可以改善此不良向客人提出改善设计的方案来改善漏镀不良电镀现场管理加强清洗工序的强度电镀产品表面晒纹效果尽量要均匀电镀现场管理加强对电流强度的管理电镀现场管理加强镀 Cr工艺的强度管理按时对电镀缸内的电镀液进行清洁,俗称‘清缸’提高产品表面的抛光精度 ( 半光产品抛光精度要求较高 8000N以上,全光产品抛光精度5000N以上)目前还没有非常有效的手段可以解决此问题,现行的改善方案为 : 电镀过程中后工序清洗追加超声波清洗以提高清洗的强度,另外对电镀完成品高温烘烤降低电镀品内部发生化学反应的可能性。
电镀加工出现问题的原因及解决办法
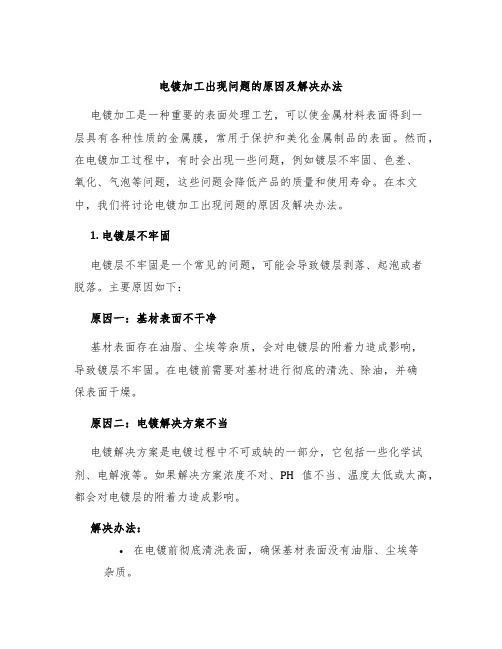
电镀加工出现问题的原因及解决办法电镀加工是一种重要的表面处理工艺,可以使金属材料表面得到一层具有各种性质的金属膜,常用于保护和美化金属制品的表面。
然而,在电镀加工过程中,有时会出现一些问题,例如镀层不牢固、色差、氧化、气泡等问题,这些问题会降低产品的质量和使用寿命。
在本文中,我们将讨论电镀加工出现问题的原因及解决办法。
1. 电镀层不牢固电镀层不牢固是一个常见的问题,可能会导致镀层剥落、起泡或者脱落。
主要原因如下:原因一:基材表面不干净基材表面存在油脂、尘埃等杂质,会对电镀层的附着力造成影响,导致镀层不牢固。
在电镀前需要对基材进行彻底的清洗、除油,并确保表面干燥。
原因二:电镀解决方案不当电镀解决方案是电镀过程中不可或缺的一部分,它包括一些化学试剂、电解液等。
如果解决方案浓度不对、PH值不当、温度太低或太高,都会对电镀层的附着力造成影响。
解决办法:•在电镀前彻底清洗表面,确保基材表面没有油脂、尘埃等杂质。
•在电镀解决方案中,加入一些添加剂,例如促进剂、增容剂等,来增强电镀层的附着力。
2. 镀层色差在电镀过程中,有时会出现镀层色差的问题,主要原因如下:原因一:电解液浓度不均电解液浓度的不均匀会导致镀层颜色不均匀。
例如,电解液中某些添加剂如果浓度过高或者过低,都可能导致镀层颜色的不同。
原因二:镀层表面存在缺陷镀层表面存在气泡、孔洞等缺陷也会导致镀层颜色不均匀。
解决办法:•定期检查电解液浓度,确保其均匀。
•彻底清洗基材的表面,确保表面无污染和缺陷。
3. 氧化问题氧化是电镀过程中另一个常见的问题,可以影响镀层的附着力和外观。
主要原因如下:原因一:电解液中的氧化物电解液中含有氧化物,而这些氧化物经常与电解液中的金属离子发生反应,从而导致镀层表面氧化。
原因二:镀层表面缺氧缺乏足够的电解气体氧分子也会导致金属离子表面氧化。
解决办法:•检查电解液中氧化物的含量,并确定其是否应该加入或减少。
•向电解液中添加抗氧化剂。
电镀常见的问题及解决方案

电镀常见的问题及解决方案
电镀过程中可能出现的问题及其解决方案如下:
1.针孔或麻点:这是由于前处理不良、有金属杂质、硼酸含量太少、镀液温度太低等原因造成的。
可以使用润湿剂来减小影响,并严格控制镀液维护及流程。
2.结合力低:如果铜镀层未经活化去氧化层,铜和镍之间的附着力就差,会产生镀层剥落现象。
因此,在电镀前应对基材进行适当的预处理,如酸洗、活化等。
3.镀层脆、可焊性差:这通常是由于有机物或重金属物质污染造成的。
添加剂过多会使镀层中夹带的有机物和分解产物增多,此时可以用活性炭处理或电解等方法除去重金属杂质。
4.镀层发暗和色泽不均匀:有金属污染可能是造成这一问题的原因。
应尽量减少挂具所沾的铜溶液,并在发现污染时立即处理。
5.镀层烧伤:这可能是由于硼酸不足、金属盐的浓度低、工作温度太低、电流密度太高、PH值太高或搅拌不充分等原因造成的。
需要检查并调整相关工艺参数,确保其处于合适的范围。
6.沉积速率低:PH值低或电流密度低都可能导致沉积速率低。
应检查并调整镀液的PH值和电流密度,以优化沉积速率。
7.其他问题:如辅助阳极的铜条未与生产板长度一致或已发粗,不允许再使用。
全板及图形镀后板需在24小时内制作下工序。
图形镀上板戴细纱手套,下板戴棕胶手套,全板上板戴橡胶手套,下板戴干燥的粗纱手套。
在处理电镀问题时,需要综合考虑多个因素,包括镀液成分、设备状况、操作条件等。
如遇到难以解决的问题,建议寻求专业人士的帮助。
电镀整流机常见故障常见电镀故障的分析和纠正方法
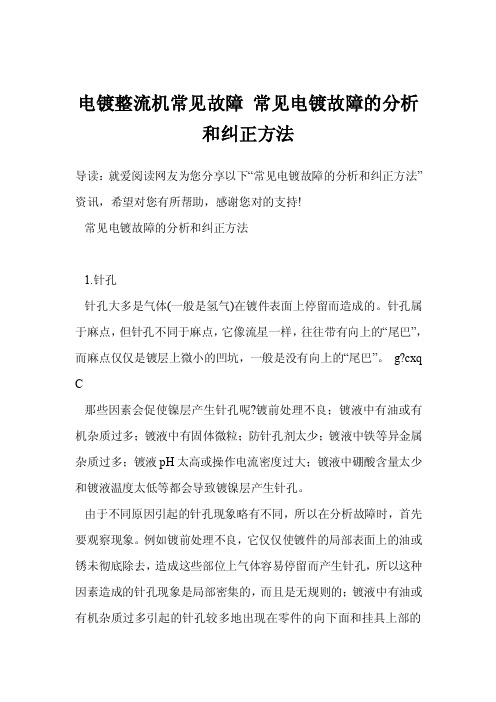
电镀整流机常见故障常见电镀故障的分析和纠正方法导读:就爱阅读网友为您分享以下“常见电镀故障的分析和纠正方法”资讯,希望对您有所帮助,感谢您对的支持!常见电镀故障的分析和纠正方法1.针孔针孔大多是气体(一般是氢气)在镀件表面上停留而造成的。
针孔属于麻点,但针孔不同于麻点,它像流星一样,往往带有向上的“尾巴”,而麻点仅仅是镀层上微小的凹坑,一般是没有向上的“尾巴”。
g?cxq C那些因素会促使镍层产生针孔呢?镀前处理不良;镀液中有油或有机杂质过多;镀液中有固体微粒;防针孔剂太少;镀液中铁等异金属杂质过多;镀液pH太高或操作电流密度过大;镀液中硼酸含量太少和镀液温度太低等都会导致镀镍层产生针孔。
由于不同原因引起的针孔现象略有不同,所以在分析故障时,首先要观察现象。
例如镀前处理不良,它仅仅使镀件的局部表面上的油或锈未彻底除去,造成这些部位上气体容易停留而产生针孔,所以这种因素造成的针孔现象是局部密集的,而且是无规则的;镀液中有油或有机杂质过多引起的针孔较多地出现在零件的向下面和挂具上部的零件上,镀液中固体微粒产生的针孔较多地出现在零件的向上面;防针孔剂太少造成的针孑L在零件的各个部位都有,镀液中铁杂质过多,pH值过高和阴极电流密度较大引起的针孔较多地出现在零件的尖端和边缘(即高电流密度处),硼酸含量太少产生的针孔较多地出现在零件的下部,镀液温度过低造成的针孔是稀少的,也是零件各个部位都有可能出现的。
”F? Rh)%; $-s8tc(通过观察现象,可以初步判断造成针孔的部分原因,然后再进一步试验。
例如零件的局部表面上有密集的针孔,从现象来看,好像是前处理不良造成的,那么究竟是不是这个原因呢?可以取一批零件,进行良好的前处理后直接镀镍,假使经这样处理后所得的镀层上没有针孔,那么原来的针孔是镀前处理不良造成的。
否则就是其他方面的原因。
镀液的温度、pH值和阴极电流密度,比较容易检查,所以可首先检查和纠正。
镀液中是否缺少十二烷基硫酸钠,从平时向镀液中补充十二烷基硫r >s酸钠的情况就能基本确定,如难以确定时,可以向镀液中加入/L十二烷基硫酸钠后进行试镀,若这样所得的镀层上针孔现象没有改善,那就不是缺少十二烷基硫酸钠,可能是镀液中的杂质或硼酸太少引起的,这就可按前述的方法,用小试验分析故障原因,然后按试验所得的结果讲行纠正。
电镀不良的一些情况和解决方法

电镀不良的一些情况和解决方法电镀不良对策镀层品质不良的发生多半为电镀条件,电镀设备或电镀药水的异常,及人为疏忽所致.通常在现场发生不良时比较容易找出塬因克服,但电镀后经过一段时间才发生不良就比较棘手.然而日后与环境中的酸气,氧气,水分等接触,加速氧化腐蚀作用也是必须注意的.以下本章将对电镀不良的发生塬因及改善的对策加以探讨说明.1.表面粗糙:指不平整,不光亮的表面,通常成粗白状(1)可能发生的塬因: (2)改善对策:1.素材表面严重粗糙,镀层无法覆盖平整. 1.若为素材严重粗糙,立即停产并通知客户.2.金属传动轮表面粗糙,且压合过紧,以至于压伤. 2.若传动轮粗糙,可换备用品使用并检查压合紧度.3.电流密度稍微偏高,部分表面不亮粗糙(尚未烧焦) 3.计算电流密度是否操作过高,若是应降低电流4.浴温过低,一般镀镍才会发生) 4.待清晰度回升再开机,或降低电流,并立即检查温控系统.5.PH值过高或过低,一般镀镍或镀金(过低不会)皆会发生. 5.立即调整PH至标准范围.6.前处理药液腐蚀底材. 6.查核前处理药剂,稀释药剂或更换药剂2.沾附异物:指端子表面附着之污物.(1)可能发生的塬因: (2)改善对策:1.水洗不干净或水质不良(如有微菌). 1.清洗水槽并更换新水.2.占到收料系统之机械油污. 2.将有油污处做以遮蔽.3.素材带有类似胶状物,于前处理流程无法去除. 3.须先以溶剂浸泡处理.4.收料时落地沾到泥土污物. 4.避免落地,若已沾附泥土可用吹气清洁,浸透量很多时,建议重新清洗一次.5.锡铅结晶物沾附 5.立即去除结晶物.6刷镀羊毛?纤维丝 6.更换羊毛?并检查接触压力.7.纸带溶解纤维丝. 7.清槽.8.皮带脱落屑. 8.更换皮带.3.密着性不良:指镀层有剥落.起皮,起泡等现象.(1)可能发生的塬因: (2).改善对策:1.前处理不良,如剥镍. 1.加强前处理.2.阴极接触不良放电,如剥镍,镍剥金,镍剥锡铅. 2.检查阴极是否接触不良,适时调整.3.镀液受到严重污染. 3.更换药水4.产速太慢,底层再次氧化,如镍层在金槽氧化(或金还塬),剥锡铅. 4,电镀前须再次活化.5.水洗不干净. 5.更换新水,必要时清洗水槽.6.素材氧化严重,如氧化斑,热处理后氧化膜. 6.必须先做除锈及去氧化膜处理,一般使用化学抛光或电解抛光.7.停机化学置换反应造成. 7.必免停机或剪除不良品8,操作电压太高,阴极导电头及镀件发热,造成镀层氧化. 8.降低操作电压或检查导线接触状况9,底层电镀不良(如烧焦),造成下一层剥落. 9.改善底层电镀品质.10.严重.烧焦所形成剥落 10.参考NO12处理对策.4.露铜:可清楚看见铜色或黄黑色于低电流处(凹槽处)(1)可能发生塬因: (2)改善对策:1.前处理不良,油脂,氧化物.异物尚未除去,镀层无法析出. 1.加强前处理或降低产速2.操作电流密度太低,导致低电流区,镀层无法析出. 2.重新计算电镀条件.3镍光泽剂过量,导致低电流区,镀层无法析出 3.处理药水,去除过多光泽剂或更新.4.严重刮伤造成露铜. 4.检查电镀流程,(查参考NO5)5.未镀到. 5.调整电流位置.5刮伤:指水平线条状,一般在锡铅镀层比较容易发生.(1)可能发生的塬因: (2)改善对策:1.素材本身在冲压时,及造成刮伤. 1.停止生产,待与客户联系.2.被电镀设备中的金属制具刮伤,如阴极头,烤箱定位器,导轮等. 2.检查电镀流程,适时调整设备和制具.3.被电镀结晶物刮伤. 3.停止生产,立即去除结晶物.6.变形(刮歪):指端子形状已经偏离塬有尺寸或位置.(1)可能发生的塬因: (2)改善对策:1.素材本身在冲压时,或运输时,即造成变形. 1.停止生产,待与客户联系.2.被电镀设备,制具刮歪(如吹气.定位器,振荡器,槽口,回转轮) 2.检查电镀流程,适时调整设备和制具.3.盘子过小或卷绕不良,导致出入料时刮歪 3.停止生产,适时调整盘子4.传动轮转歪, 4.修正传动轮或变更传动方式.7压伤:指不规则形状之凹洞可能发生的塬因:改善对策:1)本身在冲床加工时,已经压伤,镀层无法覆盖平整2)传动轮松动或故障不良,造成压合时伤到 1)停止生産,待与客户联2)检查传动机构,或更换备品8白雾:指镀层表面卡一层云雾状,不光亮但平整可能发生的塬因:1)前处理不良2)镀液受污染3)锡铅层爱到酸腐蚀,如停机时受到锡铅液腐蚀4)锡铅药水温度过高5)锡铅电流密度过低6)光泽剂不足7)传致力轮脏污8)锡铅电久进,産生泡沫附着造成改善对策:1)加强前处理2)更换药水并提纯污染液3)避免停机,若无法避免时,剪除不良4)立即检查温控系统,并重新设定温度5)提高电流密度6)补足不泽剂传动轮7)清洁传动轮8)立即去除泡沫9针孔:指成群、细小圆洞状(似被钟扎状)可能发生的塬因:改善对策:1.操作的电流密度太 1.降低电流密度2.电镀溶液表面张力过大,湿润剂不足。
教你电镀故障引起原因与排除方法
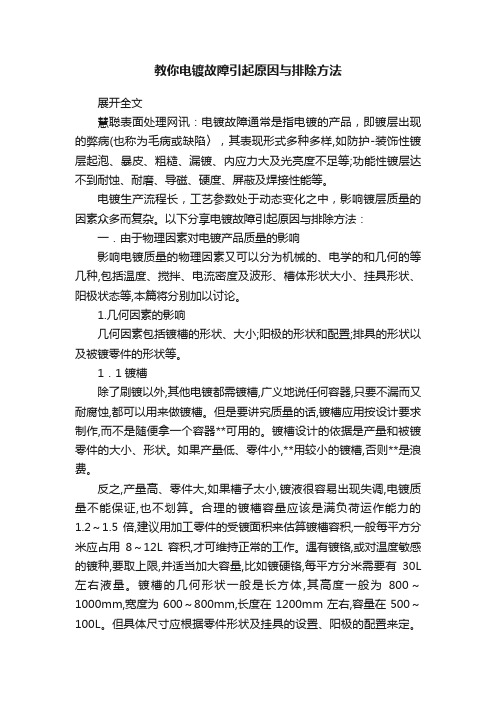
教你电镀故障引起原因与排除方法展开全文慧聪表面处理网讯:电镀故障通常是指电镀的产品,即镀层出现的弊病(也称为毛病或缺陷〉,其表现形式多种多样,如防护-装饰性镀层起泡、暴皮、粗糙、漏镀、内应力大及光亮度不足等;功能性镀层达不到耐蚀、耐磨、导磁、硬度、屏蔽及焊接性能等。
电镀生产流程长,工艺参数处于动态变化之中,影响镀层质量的因素众多而复杂。
以下分享电镀故障引起原因与排除方法:一.由于物理因素对电镀产品质量的影响影响电镀质量的物理因素又可以分为机械的、电学的和几何的等几种,包括温度、搅拌、电流密度及波形、槽体形状大小、挂具形状、阳极状态等,本篇将分别加以讨论。
1.几何因素的影响几何因素包括镀槽的形状、大小;阳极的形状和配置;排具的形状以及被镀零件的形状等。
1.1镀槽除了刷镀以外,其他电镀都需镀槽,广义地说任何容器,只要不漏而又耐腐蚀,都可以用来做镀槽。
但是要讲究质量的话,镀槽应用按设计要求制作,而不是随便拿一个容器**可用的。
镀槽设计的依据是产量和被镀零件的大小、形状。
如果产量低、零件小,**用较小的镀槽,否则**是浪费。
反之,产量高、零件大,如果槽子太小,镀液很容易出现失调,电镀质量不能保证,也不划算。
合理的镀槽容量应该是满负荷运作能力的1.2~1.5倍,建议用加工零件的受镀面积来估算镀槽容积,一般每平方分米应占用8~12L容积,才可维持正常的工作。
遇有镀铬,或对温度敏感的镀种,要取上限,并适当加大容量,比如镀硬铬,每平方分米需要有30L 左右液量。
镀槽的几何形状一般是长方体,其高度一般为800~1000mm,宽度为600~800mm,长度在1200mm左右,容量在500~100L。
但具体尺寸应根据零件形状及挂具的设置、阳极的配置来定。
一般以中间为阴极、两侧为阳极的配置为标准。
零件应浸入在镀液中,距液面5~10cm,下端距槽底应10~20cm,阴极(零件)与阳极的距离应在15~20cm,尤其在没有搅拌时,阴阳极距离要拉大一些。
电镀加工出现问题的原因及解决办法

电镀加工出现问题的原因及解决办法对于电子设备厂家来说,在进行电子加工活动的时候,电镀加工处理是少不的,电镀加工处理工艺中可能消失各种问题,给生产带来不便.电镀加工不平整是一个常见问题,下面来了解一下它消失的缘由:1、电镀件毛坯表面过于粗糙或不好。
过于粗糙的表面要各到优质的沉积电镀层相对更困难,特殊是一些压铸不良的产品就不能得到合格的电镀层。
一些素材表面的缺陷在电镀之前不能发觉与修复,良品率相对低些。
2、电镀加工工艺不合理或电镀时间不够。
比如塑料电镀在镀铜的时间太短电流太小,铜件电镀直上镍电镀时镀光亮镍的时间短或电流太小。
3、电镀液性能差,整平性能不好。
如光亮硫酸铜所用的材料杂质多,组成成分含量不对,所使用的光亮剂质量不好,都不能有良好的填平性能。
4、电镀件在前处理部分不良,如五金电镀件镀底铜或底镍层不良或有附着有机膜层等。
另外还会消失电镀加工渗漏的问题,无锡华友微电子有限公司在该行业已有15年的历史,已形成了肯定规模,具备肯定的加工力量,并拥有丰富的阅历,下面它给我们解析下如何防止苏州电镀加工活动中的渗漏问题。
1、严防镀液加温过高。
当镀液加温过高时,镀液会加速蒸发和分解,气雾中含有高浓度的溶质成分。
这时会严峻污染环境,尤其是酸、碱气雾,氰化物和铬雾对环境的影响和人体危害会更大。
2、严格防止镀液被排风机吸走。
当电镀加工中,排风机配备不当,镀液液位过高,这时镀液简单被吸走,在槽盖未启开之前尤为严峻,既引起环境污染,又会造成镀液损耗,消失这种状况时要准时实行措施予以解决,如降低镀液液位,调整吸风口宽度等。
3、防止镀槽、加温(冷却)管渗漏造成污染。
电镀槽或加温(冷却)管渗漏往往会造成严峻污染,其渗漏缘由随制造材料及不同镀种各有区分。
电镀污泥干燥机常见故障分析及解决方法

电镀污泥干燥机常见故障分析及解决方法电镀污泥干燥机是用于处理电镀废水中的污泥的设备。
由于其长时间运转和高温环境,常会显现故障。
本文将从机器保养、设备故障两个方面,认真分析其常见故障及解决方法。
一、机器保养1. 定期清理滚筒电镀污泥干燥机的滚筒是干燥的关键部件,定期清理滚筒能够保证其工作顺畅。
假如滚筒上长时间积聚了污泥,不仅简单堵塞,还简单损坏滚筒的表面,从而影响其干燥效果和使用寿命。
2. 维护传动系统电镀污泥干燥机的传动系统包括减速机、皮带和链条等部件。
这些部件长时间运转后简单显现松动、断裂等故障,影响设备的工作效果。
因此,定期检测并维护传动系统,可以延长设备的使用寿命,提高生产效率。
3. 清洗电控系统电镀污泥干燥机的电控系统是保证设备正常工作的紧要部分。
假如电控系统长时间不清洗,会积累很多灰尘和杂质,导致电气元器件渐渐老化,进而影响设备的正常运转。
因此,我们建议每隔一段时间对电控系统进行清洗保养。
二、设备故障1. 电机启动无力电镀污泥干燥机的电机启动无力是常见故障之一,原因有很多种,如电网电压过低、电机本身故障或者传动系统磨损等。
解决方法如下:•检查电网电压是否正常,若过低则需进行电源升压处理;•检查电机是否受损,如有受损的地方则需要更换电机;•检查传动系统,如有磨损则需要进行维护和修理或更换。
2. 滚筒漏气电镀污泥干燥机的滚筒紧要是通过加热器进行干燥的,但是假如滚筒显现漏气现象,则影响干燥效果。
滚筒漏气的原因可能是滚筒本身存在问题,如焊缝处缺陷,也可能是加热器和滚筒之间的接头处未密封好。
这种故障处理方法如下:•对滚筒进行检查,确认漏气原因;•如为滚筒本身问题,则需对滚筒焊缝处进行修补,保证其密封性;•如为加热器和滚筒之间接头处未密封好,则需重新进行密封,以确保两者之间的气密性。
3. 温度掌控问题电镀污泥干燥机的温度掌控很关键,假如温度超过规定范围或不匹配,则会影响设备的干燥效果。
导致这种故障的原因可能是温度掌控器损坏、温度传感器显现故障或传热介质不通畅等问题。
电镀加工出现问题的原因及解决办法
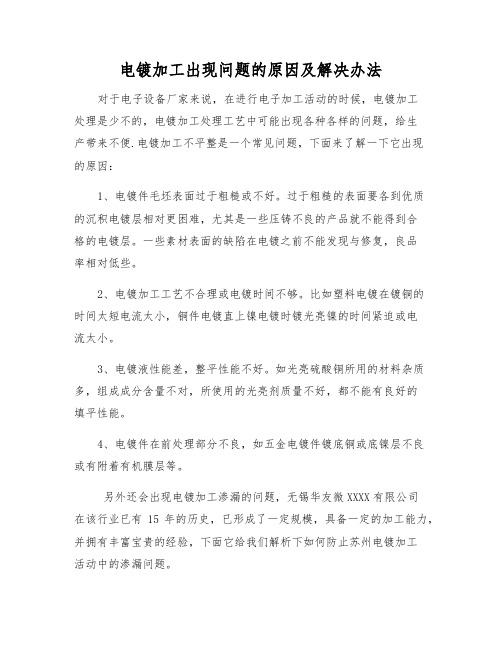
电镀加工出现问题的原因及解决办法对于电子设备厂家来说,在进行电子加工活动的时候,电镀加工处理是少不的,电镀加工处理工艺中可能出现各种各样的问题,给生产带来不便.电镀加工不平整是一个常见问题,下面来了解一下它出现的原因:1、电镀件毛坯表面过于粗糙或不好。
过于粗糙的表面要各到优质的沉积电镀层相对更困难,尤其是一些压铸不良的产品就不能得到合格的电镀层。
一些素材表面的缺陷在电镀之前不能发现与修复,良品率相对低些。
2、电镀加工工艺不合理或电镀时间不够。
比如塑料电镀在镀铜的时间太短电流太小,铜件电镀直上镍电镀时镀光亮镍的时间紧迫或电流太小。
3、电镀液性能差,整平性能不好。
如光亮硫酸铜所用的材料杂质多,组成成分含量不对,所使用的光亮剂质量不好,都不能有良好的填平性能。
4、电镀件在前处理部分不良,如五金电镀件镀底铜或底镍层不良或有附着有机膜层等。
另外还会出现电镀加工渗漏的问题,无锡华友微XXXX有限公司在该行业已有15年的历史,已形成了一定规模,具备一定的加工能力,并拥有丰富宝贵的经验,下面它给我们解析下如何防止苏州电镀加工活动中的渗漏问题。
1、严格防范镀液加温过高。
当镀液加温过高时,镀液会加速蒸发和分解,气雾中含有高浓度的溶质成分。
这时会严重污染环境,尤其是酸、碱气雾,氰化物和铬雾对环境的影响和人体危害会更大。
2、严格防止镀液被排风机吸走。
当电镀加工中,排风机配备不当,镀液液位过高,这时镀液容易被吸走,在槽盖未启开之前极为严重,既引起环境污染,又会造成镀液损耗,出现这种情况时要及时采取措施予以解决,如降低镀液液位,调整吸风口宽度等。
3、防止镀槽、加温(冷却)管渗漏造成污染。
电镀槽或加温(冷却)管渗漏往往会造成严重污染,其渗漏原因随制造材料及不同镀种各有区别。
电镀常见故障原因与排除[宝典]
![电镀常见故障原因与排除[宝典]](https://img.taocdn.com/s3/m/8906ce48302b3169a45177232f60ddccda38e6b9.png)
常见故障原因与排除3.导电不良4.铬酸含量太低5.三价铬或异金属杂质过多6.有硝酸根存在3. 检查线路4. 补充铬酐5. 电解法除去6. 用电解法镀层脱落1.镀铬过程中断电2.阴极电流密度过大3.底层镍钝化或底镀层上有油1. 检查线路2. 降低电流密度3. 加强前处理镀层表面粗糙1. 底镀层本身较粗糙2. 镀液中有微细固体粒子3. 硫酸含量过低4. 阴极电流密度过大1.加强底层质量2.过滤3.提高硫酸含量4.降低电密度氯化物酸性镀锌常见故障原因与排除方法故障现象故障原因故障排除方法镀层起泡结合力不好1.镀前处理不良2.添加剂过多3.硼酸过低4.阴极电流密度过大1.加强前处理2.用活性炭吸附3.补充硼酸4.降低电流密度镀层粗糙1.锌含量过高2.DY添加剂含量偏少3.温度过高4.镀液中有固体微粒1. 析成分,冲稀镀液2. 补充DY添加剂3. 采用冷冻设备,控制温度正常值4. 加强过滤镀层上出现黑色条纹或斑点1.前处理不良2.阴极电流密度过大3.镀液中氯化物太少4.有机杂质过多5.有较多的铜铅杂质1.加强除油除锈2.降低电流密度3.分析成份,提高氯化物含量4.建议用双氧水活性炭处理5.加入0.5-1克/升锌粉镀层容易烧焦1.氯化物含量不够2.锌含量低3.DY柔软剂不够4.PH太高1.分析成分,提高氯化物含量2.分析成分,提高锌含量3.补充柔软剂4.用稀盐酸调PH至5.5-6. 2低电流区镀层灰暗1.镀液温度过高2.DY添加剂含量太少3.镀液中有铜/铅杂质1.采用冷冻设备,控制温度正常值2.补充添加剂3.加入0.5-1克/升锌粉或加除杂水镀层光泽差1.镀液中DY添加剂太少2.温度太高3.PH太高或太低1.补充DY添加剂0.1-0.2毫升/升2. 采用冷冻设备,控制温度正常值3. 用稀盐酸调PH至5.5-6.2氰化物镀锌常见故障原因与排除方法故障现象故障原因故障排除方法镀层结合力不好 1.前处理不良 1. 加强前处理。
电镀处理中的电镀故障分析与排除

电镀处理中的电镀故障分析与排除随着工业化程度的逐步提高,电镀处理如今已经变得越来越常见。
电镀处理技术在现代工业生产中拥有着广泛的应用,尤其是在电子、汽车、航空等领域中都有着广泛的运用。
电镀处理能够使金属表面具备防腐、耐磨、美化、导电、抗氧化、增加光泽等功能,因此也成为了现代工业中不可缺少的一环。
而在电镀处理中,难免会遇到各种电镀故障,如何准确地判断故障原因,排除故障,是我们在电镀处理过程中需要面临的问题。
本文将从电镀故障产生的原因和种类、电镀故障的分析方法和处理措施等几个方面来展开阐述。
一、电镀故障的产生原因和种类1. 电镀异质金属在电镀处理过程中,电镀池中的异质金属是产生电镀故障的主要原因之一。
异质金属能够进入电镀池中并污染电极板,导致电极板出现气孔、颗粒等缺陷。
同时,由于异质金属的存在,电极板表面的颜色和光泽也会受到影响。
2. 电流不稳定电流不稳定也会导致电镀故障的发生。
而电流不稳定的原因主要包括电源电压、电源输出电流、电极板与电源之间的接触等。
3. 水和空气的污染在电镀池中,水和空气中的污染物也会污染电极板,并导致电镀故障的发生。
这些污染物包括微生物、异物、有机物等。
这些污染物能够附着在电极板上,污染表面,导致表面出现不均匀的颜色、凹凸不平等问题。
二、电镀故障的分析方法1. 观察外观观察电极板表面的外观可以获得很多线索。
通常情况下,电极板出现的问题,如颜色、水泡、气孔等,都能够通过观察表面得到反应。
通过观察外观,我们可以初步判断故障出现的位置以及与何种因素有关。
2. 检测电流稳定性在电镀处理过程中,电流的稳定性是至关重要的。
检测电流的稳定性可以通过对电源电压和电源负载电流的波动进行分析。
如果电压和电流波动较大,说明电流不稳定,那么就需要对电源进行维护或更换。
3. 化学分析在一些特殊情况下,我们需要进行化学分析来检测电镀故障的原因。
这种方法主要适用于难以通过外观观察或电容法检测得到的故障原因。
电镀产生问题原因及对策
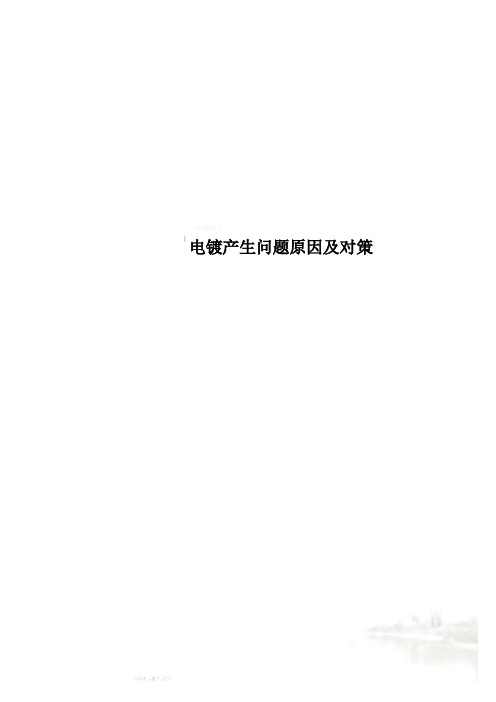
电镀产生问题原因及对策塑料制品表面电镀故障之成因及对策一、预处理及化学镀故障的排除待续!或全部沉积不实际生产中都有可能遇到化学镀沉积不上或覆盖不全的现象。
其成因及对策为:上镀层(1)若将经过活化处理后的制品侵入化学镀液中,制品表面根本不发生化学变化,则表明活化不良。
应检查敏化液和活化液的配比是否适宜,操作条件是否得当。
如果敏化或活化温度太低或时间太短,应适当提高温度及延长处理时间。
对于采用胶体钯进行活化处理的制品,制品不沉积不上镀层,还需要考虑解胶是否完全。
若解胶不足,应适当调整解胶溶液配比或提高溶液温度。
(2)若反应只在制品表面局部进行,同时沉积的镀层很光亮,但覆盖不全,组份。
粗化时,制品表面不能过蚀。
d、活化不良。
应及时调整敏化和活化液的组分或换用新液。
e、制品表面出现海绵状化学镀层。
应调制适宜的镀液并降低其沉积速度。
(2)表面线状起泡。
其成因及对策:a、粗化不良。
应适当调整粗化液的配比。
b、制品表面有残留的脱模剂。
应在制品成型时尽量避免使用脱模剂。
c、制品表面有杂质点。
应在制品成型时防止产生这一缺陷。
(3)浇口处起泡。
其成因及对策:a、制品成型时注射压力太高或浇口尺寸设计不当。
应适当调整成型条件及模具设计。
露塑点(4)镀镍溶液中放针孔剂不足或胶质太多。
应适当调整。
(5)制品成型时模具表面光洁度太差。
应对模具表面进行抛光或电镀处理, 提高其表面光洁度。
化学沉铜层表 沉铜层表面若产生能擦去的褐色粉末时,电镀亮层就会影响亮铜层的结合面浮有褐色粉力。
其产生原因及处理方法如下: 末(1)化学沉铜液已分解失效,铜离子在还原过程中生成的铜原子被氧化,使之变成氧化铜,而氧化铜有成为还原铜的结晶核心,使镀液浑浊不清。
应适当降低镀液的pH 值至10左右,并过滤镀液,用比色法补充镀液。
黑色粉化反应速度太快,使镍的结晶粗末松,沉镍层产生结合力差的黑色粉末镍。
对此,应分析和调整沉镍液中镍离子的含量,并合理控制溶液温度及pH值。
电镀产生问题原因及对策
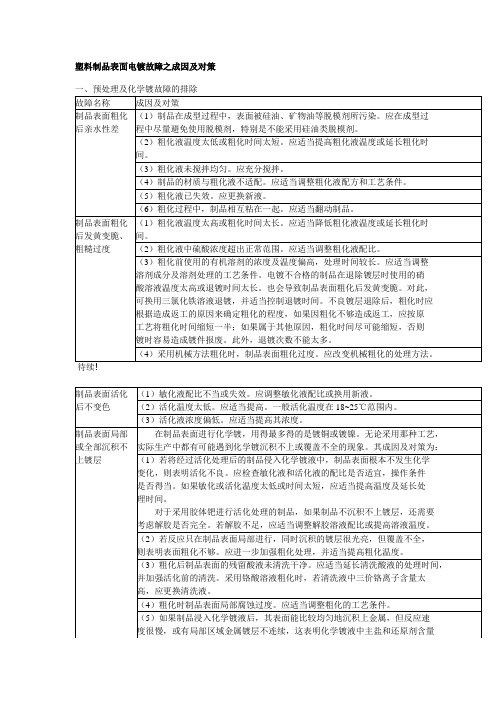
塑料制品表面电镀故障之成因及对策完二、电镀故障的排除的方法来检查镀层的热稳定性能。
在试验中选用得高低温度范围和循环次数,是根据制品的使用条件和环境确定的。
如汽车上使用的零件,在进行冷热循环试验时,先将镀件放入85℃的烘箱中保温1h,取出后在室温中放置15min,然后再放入40℃条件下1h,最后再在室温中放置15min。
如此循环4次,如果镀层表面状态和结合力均无变化则为合格所谓剥离试验,是在制品电镀的样片上切取1!2cm宽的镀层,橇起一头,用垂直于基体的力拉镀层,并测定剥离镀层时所需的力,其单位为kg/cm。
一般剥离在0.45kg/cm以上则为合格。
由于制品成型条件对镀层结合力影响的因素相当复杂,处理较为困难,尚未完待续完!完四、光亮硫酸盐铜常见故障的排除五、焦磷酸盐闪镀铜常见故障的排除完八、氰化镀铜合金故障的排除完完十一、ABS制品表面电镀故障的排除一、ABS制品表面酸性镀铜故障的排除复杂形状塑料大件电镀麻点产生的原因及对策董兴华摘要从工艺试验和实际生产方面找出了复杂形状塑料大件电镀产生麻点的主要原因,分析了产生麻点的各种因素,提出了减少麻点产生的办法和消除对策。
关键词塑料件电镀麻点对策新研制的电熨斗,有空心手柄、商标凸耳、大平面面积的侧身、散热窗、大穴内空、螺孔、凹槽、盲孔、通孔、非镀绝缘等部位,上壳为ABS塑料,形状复杂,受镀面积10 dm2。
常规塑料件电镀的工艺弊病很多,分析如下:1 麻点产生之因麻点的产生,主要来源于:(1)基材缺陷;(2)镀液;(3)工艺;(4)挂勾。
1.1 基材缺陷基材产生的麻点由模具精度和成型工艺及操作等造成,分布无规则。
轻微的缺陷孔,可通过电镀的填平将其减轻。
稍轻的缺陷孔,可机械抛磨后进行电镀。
严重的缺陷孔,视用户要求酌情处理。
1.2 镀液及其相关性(1)镀液性能差。
镀液成分含量改变,如酸铜中CuSO4过低,氯离子过高,光亮剂失调(S类光亮剂),表面活性剂过少。
(2)镀液污染。
电镀工艺常见故障和处理方法

Trouble Shooting Indexz电金工艺z碳膜工艺z电铜工艺z图像转移工艺z蚀板工艺z喷锡(热风整平)工艺z线路油墨工艺z电镍工艺z有机保焊膜工艺z压板工艺z沉铜(PTH)工艺z银浆贯孔工艺z电锡工艺z湿绿油工艺一、版权说明关於这个【Trouble Shooting】软件 的版权我想一定是属於 中国PCB技术网 所有,其中如果有同行要直接引用本软件则要与我联系,一般情况下我也希望此软件 在我们同行中广泛传播!但如果要用於商业用途则我们就要认真商量一个方案了!当然这其中的文章版权就是文章和作者和来自 的不同网站!如果我转录的这些文章,相关网站或作者不允许录入到这个软件中,请与我们联系,我们会立即删除并表示道歉!二、注册说明这是一个完全免费的软件,当然我们是想知道这个软件到哪里去了!如果你想要告诉我们,请用这三种方法:1、用EMAIL与我联系。
2、在就是技术网站上留言,并留下EMAIL地址。
3、寄一封书信给我们。
无论何种方法都请写明你的姓名、职业、使用此软件的用途等等。
如果你能对此软件进行一些有建设性的 评价,那我们首先感谢!如果你使用了此软件,觉得对你有一定的帮助,想寄一点钱给我们,那我们非常感激!!三、如何联系我们EMAIL:94TECH@OICQ:9371469网址:三、特别感谢本制程TROUBLE SHOOTING的内容基本上来自己《印制电路工艺》教课书。
此教程为国家信息产业部岗位培训的指定教材。
内容丰富,适用於行业培训。
在此特别感谢!◎ Copyright©2001-2002 ◎ 版权所有©2001-2002 中国PCB技术网◎电镀金工艺◎镀金层常见故障和纠正方法故障可能原因纠正方法低电流区发雾①温度太低②补充剂不足①调整温度到正常值②添加补充剂③有机污染④PH太高③活性炭处理④用酸性调整盐调低PH中电流区发雾,高电流区呈暗褐色①温度太高②阴极电流密度太高③PH太高④补充剂不够⑤搅拌不够⑥有机污染①降低操作温度②降低电流密度③用酸性调整盐调低PH④添加补充剂⑤加强搅拌⑥活性炭过滤高电流区烧焦①金含量不足②PH太高③电流密度太高④镀液比重太低⑤搅拌不够①补充金盐②用酸性调整盐调低PH③调低电流密度④用导电盐提高比重⑤加强搅拌镀层颜色不均匀①金含量不足②比重太低③搅拌不够④镀液被Ni,Cu等污染①补充金盐②用导电盐调高比重③加强搅拌④清除金属离子污染,必要时更换溶液板面金变色(特别是在潮热季节)①镀金层清洗不彻底②镀镍层厚度不够③镀金液被金属或有机物污染④镀镍层纯度不够⑤镀金板存放在有腐蚀性的环境中①加强镀后清洗②镍层厚度不小于2.5微米③加强金镀液净化④加强清除镍镀液的杂质⑤镀金层应远离腐蚀气氛环境保存,其变色层可浸5-15%H2SO4除去镀金板可焊性不好①低应力镍镀层太薄②金层纯度不够③表面被污染,如手印④包装不适当①低应力镍层厚度不小于2.5微米②加强镀金液监控,减少杂质污染③加强清洗和板面清洁④需较长时间存放的印制板,应采用真空包装镀层结合力不好①铜镍间结合力不好②镍金层结合力不好①注意镀镍前铜表面清洁和活化②注意镀金前的镍表面活化③ 镀前清洗处理不良④ 镀镍层应力大③ 加强镀前处理④ 净化镀镍液,通小电流或炭处理◎ Copyright ©2001-2002 ◎ 版权所有©2001-2002 中国PCB技术网 ◎碳膜电路制造技术◎碳膜印制板常见故障及纠正方法序号 故障 产生原因排除方法1碳膜方阻偏高1.网版膜厚太薄2.网目数太大3.碳浆粘度太低4.固化时间太短5.固化抽风不完全6.固化温度低7.网印速度太快1.增大网膜厚度2.降低选择的网目数3.调整碳浆粘度4.延长固化时间5.增大抽风量6.提高固化温度7.降低网印速度 2碳膜图形渗展1.网印碳浆粘度低2.网印时网距太低3.刮板压力太大4.刮板硬度不够1.调整碳浆粘度2.提高网印的网距3.降低刮板压力4.调换刮板硬度3碳膜附着力差1.印碳膜之间板面未处理清洁2.固化不完全3.碳浆过期4.电检时受到冲击5.冲切时受到冲击1.加强板面的清洁处理2.调整固化时间和温度3.更换碳浆4.调整电检时压力5.模具是否在上模开槽4碳膜层针孔1.刮板钝2.网印的网距高3.网版膜厚不均匀4.网印速度快5.碳浆粘度高1.磨刮板的刀口2.调整网距3.调整网版厚度4.降低网印速度5.调整碳浆粘度6.刮板硬度不够 6.更换刮板硬度◎ Copyright©2001-2002 ◎ 版权所有©2001-2002 中国PCB技术网◎酸性电镀铜工艺◎酸性镀铜常见故障及处理故障可能原因纠正方法镀层与基体结合力差镀前处理不良加强和改进镀前处理镀层烧焦①铜浓度太低②阳极电流密度过大③液温太低④阳极过长⑤图形局部导致密度过稀⑥添加剂不足①分析并补充硫酸铜②适当降低电流密度③适当提高液温④阳极就砒阴极知5-7CM⑤加辅助假阴极或降低电流⑥赫尔槽试验并调整镀层粗糙有铜粉①镀液过滤不良②硫酸浓度不够③电流过大④添加剂失调①加强过滤②分析并补充硫酸③适当降低④通过赫尔槽试验调整台阶状镀层氯离子严重不足适当补充局部无镀层①前处理未清洗干净②局部有残膜或有机物①加强镀前处理②加强镀前检查镀层表面发雾有机污染活性炭处理低电流区镀层发暗①硫酸含量低②铜浓度高③金属杂质污染④光亮剂浓度不当或选择不当①分析补充硫酸②分析调整铜浓度③小电流处理④调整光亮剂量或另选品种镀层在麻点、针孔①前处理不干净②镀液有油污③搅拌不够④添加剂不足或润湿剂不足⑤加强镀前处理⑥活性炭处理⑦加强搅拌⑧调正或补充镀层脆性大①光亮剂过多①活性炭处理或通电消耗② 液温过低③ 金属杂质或有机杂质污染② 适当提高液温③ 小电流处理和活性炭处理金属化孔内有空白点① 化学沉铜不完整② 镀液内有悬浮物③ 镀前处理时间太长,蚀掉孔内镀层① 检查化学沉铜工艺操作② 加强过滤③ 改善前处理孔周围发暗(所谓鱼眼状镀层)① 光亮剂过量② 杂质污染引起周围镀层厚度不足③ 搅拌不当① 调整光亮剂② 净化镀液③ 调整搅拌阳极表面呈灰白色 氯离子太多 除去多余氯离子阳极钝化① 阳极面积太小② 阳极黑膜太厚① 增大阳极面积至阴极的2倍② 检查阳极含P是否太多◎ Copyright ©2001-2002 ◎ 版权所有©2001-2002 中国PCB技术网 ◎光化学图像转移(D/F)工艺◎D/F常见故障及处理(1)干膜与覆铜箔板粘贴不牢(2)干膜与基体铜表面之间出现气泡原因解决方法1)干膜储存时间过久,抗蚀剂中溶剂挥发。
电镀废水处理中的问题及措施分析
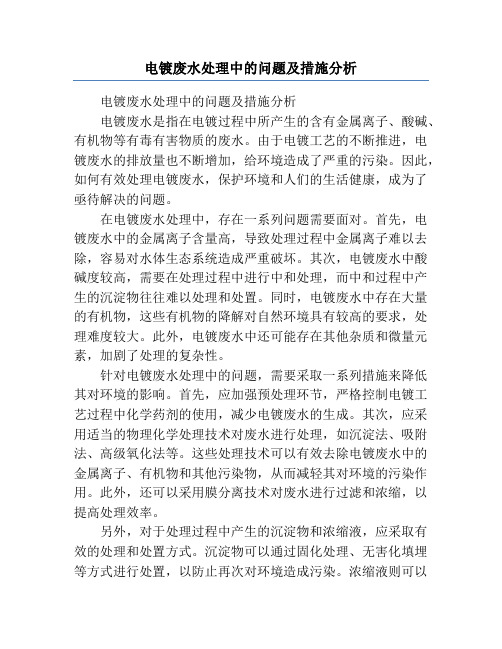
电镀废水处理中的问题及措施分析电镀废水处理中的问题及措施分析电镀废水是指在电镀过程中所产生的含有金属离子、酸碱、有机物等有毒有害物质的废水。
由于电镀工艺的不断推进,电镀废水的排放量也不断增加,给环境造成了严重的污染。
因此,如何有效处理电镀废水,保护环境和人们的生活健康,成为了亟待解决的问题。
在电镀废水处理中,存在一系列问题需要面对。
首先,电镀废水中的金属离子含量高,导致处理过程中金属离子难以去除,容易对水体生态系统造成严重破坏。
其次,电镀废水中酸碱度较高,需要在处理过程中进行中和处理,而中和过程中产生的沉淀物往往难以处理和处置。
同时,电镀废水中存在大量的有机物,这些有机物的降解对自然环境具有较高的要求,处理难度较大。
此外,电镀废水中还可能存在其他杂质和微量元素,加剧了处理的复杂性。
针对电镀废水处理中的问题,需要采取一系列措施来降低其对环境的影响。
首先,应加强预处理环节,严格控制电镀工艺过程中化学药剂的使用,减少电镀废水的生成。
其次,应采用适当的物理化学处理技术对废水进行处理,如沉淀法、吸附法、高级氧化法等。
这些处理技术可以有效去除电镀废水中的金属离子、有机物和其他污染物,从而减轻其对环境的污染作用。
此外,还可以采用膜分离技术对废水进行过滤和浓缩,以提高处理效率。
另外,对于处理过程中产生的沉淀物和浓缩液,应采取有效的处理和处置方式。
沉淀物可以通过固化处理、无害化填埋等方式进行处置,以防止再次对环境造成污染。
浓缩液则可以进行再利用,以提高资源的利用效率和经济效益。
此外,还应加强电镀工艺的改进和优化,减少废水的排放。
通过改进电镀液的组成和工艺参数的调整,可以降低废水产生的量和污染物的含量,从根本上减轻废水处理的负担。
最后,还应建立健全的监督和管理制度,加强对电镀企业的环保监管,确保其按照相关法规和标准进行废水排放和处理。
同时,也要加强宣传和教育,提高企业和公众对电镀废水处理的认识和重视程度,形成共同的环保意识和责任。
电镀废水处理过程存在问题分析和解决办法.

电镀废水处理过程存在问题分析和解决办法电镀是全球三大高污染工业之一,随着科技的发展,电镀工业的规模也随之发展,排放废水量越来越大。
由于电镀废水危害性大、毒性大、具有积累作用,因而对生态环境的破坏作用巨大,远远超过其它种类的污染。
因此,对电镀废水进行处理,对处理效果进行监督管理,就显得非常重要。
对任何一项废水处理工艺,一方面要考虑它的处理效果,另一方面,还应考虑它的经济效益。
节省投资,节约能源,提高经济效益,节省运行费用,这是进行废水处理前必须考虑的问题。
一、电镀废水处理过程存在的问题及原因分析(一设备投资过大,处理成本高。
一个企业投入几百万用于购置处理设备,然而实际处理的效果却不稳定,达标的情况也不稳定,并且消耗药剂的成本也高。
采用焦亚硫酸钠法、亚硫酸钠法的企业,就药剂的成本来说均在5.0~6.5元每平方米废水,对于塑料电镀厂而言,药剂成本为每平方米废水至少十元人民币。
假如计算设备人工费、测试监测费、折旧费等费用,每平方米废水处理的成本就更高。
这就是阻碍现今的电镀企业认真对待废水处理问题的最根本、最直接的原因。
因而,研制开发一种设备,投资省,流程短,适用性强,操作简单,处理时间短,处理效果好,性能稳定,处理成本低的混合废水处理的技术,是尽可能杜绝并避免现实中把设备当摆设,处理时偷工减料、偷排、处理不彻底等一系列现象的最实际有效的方法。
(二处理效果不够理想。
经过多年研究,现有多种废水处理技术(硫酸亚铁法、焦亚硫酸钠法、亚硫酸钠法、离子交换法、铁~焦炭法、电解法等。
目前,在实际生产中,港台企业采用亚硫酸钠法、焦亚硫酸钠法较多,内地企业采用铁~焦炭法、硫酸亚铁法的较多;离子交换法和电解法因为管理和运行的效果不如人所愿,近些年来在实际运用中比较罕见。
但在实际运用中硫酸亚铁法、焦亚硫酸钠法、亚硫酸钠法等方案,pH值和投料量难以控制。
一旦投料超标,浪费材料不说,成本也有所增加,而且又会增加出水中COD的值,如果过多的投料,还容易形成络离子,就算加碱也难以沉淀。
- 1、下载文档前请自行甄别文档内容的完整性,平台不提供额外的编辑、内容补充、找答案等附加服务。
- 2、"仅部分预览"的文档,不可在线预览部分如存在完整性等问题,可反馈申请退款(可完整预览的文档不适用该条件!)。
- 3、如文档侵犯您的权益,请联系客服反馈,我们会尽快为您处理(人工客服工作时间:9:00-18:30)。
浅谈电镀后处理脱水常见问题及解决方法
电镀后的最后一道工序是脱水干燥。
这道工序相对于前面各个工序来讲没有那么复杂与技术含量,在一般的人看来也就是过几格水而已,不算什么技术。
如果不重视它,也许出现问题往往就在这道工序上,也要给予重视,不能忽视。
一般表现出来的现象是工件由上到下出现一道水迹。
一些形状复杂的工件,在其螺丝孔里残留的电镀液烘烤后缓慢散发出来,表现轻微的就流出一道污痕,表现严重的是周围镀层都被腐蚀掉(比如镀青铜),这样的工件一般是不合格的,达不到客人要求,只能作返工处理,所以处理不好,既耽误货期,又浪费大量人力物力。
对于这个问题的解决,我们一般采取的方法有一下几个方法:
一)采用超纯水电镀工件清洗干净与否,最重要的莫过于需要水质洁净,如果后处理水质不干净,水的硬度高、含有大量盐分、微生物等,清洗后的工件表面状况会非常糟糕,如出现工件颜色变色,大量污迹等。
水质问题一般工厂都能做到,都是利用反渗透+离子交换装置解决,经过处理后水的电导率一般在5Ω/cm3-以下,有的甚至更低,电导率越低越好,使用一段时间后电导率升高则需要对离子交换进行再生处理。
二)增加辅助装置一些复杂的工件一般可以辅助一些吹、吸设备,利用压缩空气吹扫,可以轻松吹除一些挂得比较牢固的工件表面水珠,特别是光面比较大的工件效果特佳。
对一些仅挂钩在挂具上的工件则只能采取吸取的方法。
如果还采取吹扫则工件都被吹掉,弄
花。
这种方法对一些有孔位工件尤为适用,比如讲吸尘器改装前面吸嘴,可以很好解决一些藏水工件。
三)加温对漂水过程中最后两槽水适当进行加温,一般讲温度控制在60度左右,但温度不宜过高,过高的温度会使水分蒸发越快,提取操作也不安全。
温度提高水的表面张力降低,一方面加速水脱离工件表面,另外带着一定热量的工件在进入隧道炉干燥时有一定帮助作用,可以加快温度的提升,在热风的吹扫下水珠很容易脱离工件表面。
四)采取脱水油这个方法在以前使用得比较多,例如采取多级无水乙醇脱水,脱水防锈油等,这个方法对电镀后处理工件清洗不适用,在此不作讨论。
五)添加脱水剂采取以上方法可以对一些简单的电镀工件表面水珠轻松去除,但是对于一些复杂的工件则同样表现得不得力,上述方法增加很多的人力物力,如果在漂水槽中添加一点脱水剂,则对后面的清洗效果有很大的提升。
脱水剂是由多种表面活性剂、缓蚀剂等复合而成的。
它的最大特点就是能够快速在工件表面形成一层疏水膜,将大量水置换掉并起防变色作用,从而大大减轻后面吹、吸等方法的劳动量。
使用脱水剂的最大弱项是:如果使用不当或使用劣质脱水剂,一些工件经过喷力架,力架与工件表面的结合力低,力架硬度大大降低,失去保护作用,稍经过摩擦、刮划,力架很容易脱掉,这也是不可取的。
只有采取质量良好的脱水剂则可避免出现此类问题。
目前市面上个别厂家开发的电镀后处理专用脱水剂完全可以满足这种要求,用量少,脱水效率高,脱水后表面无尘点,与力架结合力好等特点。
经过多家工厂试用,反映较好。
对于在五金电镀中有关后处理脱水一事,有更好的方法或建议,希望大家可以多加讨论,分享工作经验。
以上仅是自己的一点工作经验,如有不当之处还望大家批评指正。
2012年8月。