基于知识的精铸模具智能化设计方法
CAE技术实现先进铸造设备的远程智能监控

CAE技术实现先进铸造设备的远程智能监控CAE技术实现先进铸造设备的远程智能监控随着科技的发展,先进铸造设备的远程智能监控引起了人们的广泛关注。
在传统的铸造过程中,操作员需要亲身前往设备现场进行监测和控制,不仅费时费力,而且存在一定的安全隐患。
而借助于计算机辅助工程(Computer-Aided Engineering, CAE)技术,可以实现铸造设备的远程智能监控,提高生产效率、降低生产成本、提升产品质量和生产安全。
一、CAE技术概述CAE技术是指利用计算机辅助进行工程分析和设计的一种方法。
它通过数值模拟、计算机仿真等手段,实现对物理过程的预测、优化和控制。
在铸造领域,CAE技术可以模拟铸造过程中的流体力学、传热学、固相变形学等物理现象,帮助工程师更好地理解和控制铸造过程。
二、远程智能监控的意义远程智能监控是指通过远程控制和监测设备,在不同的时间和空间,实现对先进铸造设备的操作和管理。
它可以提供实时数据、检测设备状态和故障预警等功能,有效地提高了生产效率和设备利用率。
远程智能监控还可以减少人为因素对铸造过程的干扰,提高产品质量和生产安全。
三、CAE技术在远程智能监控中的应用1. 数值模拟与优化通过CAE技术,可以对铸造设备进行数值模拟,预测和优化铸造过程中的温度、流速、气流等参数。
同时,借助于优化算法,可以寻找最佳的工艺参数组合,提高铸件的成形质量和机械性能。
这些模拟和优化结果可以通过远程智能监控系统进行实时更新和传输,为操作员提供及时的参考和决策依据。
2. 传感器与数据采集远程智能监控系统通过传感器可以实时采集铸造设备的工作状态和环境参数,如温度、压力、振动等。
这些数据经过采集、处理和传输后,可以在远程终端进行监测和分析。
在发生异常或故障时,系统可以通过警报和预警信息通知操作员,及时采取措施,减少停机时间,提高生产效率。
3. 远程控制与故障诊断在远程智能监控系统中,操作员可以通过终端设备远程控制铸造设备的开关、运行状态等。
铸造加工在智能制造中的应用

铸造加工在智能制造中的应用随着科技的不断发展和智能化方向的不断深入,铸造加工作为一种传统工艺被不断赋予了新的生命力。
在智能制造的过程中,铸造加工成为了一个必不可少的环节,大大推动了工业的发展。
本文将会阐述铸造加工在智能制造中的应用,探究铸造加工在智能化领域的优势和发展方向。
1. 铸造加工在智能制造中的优势铸造加工在智能制造中具有多个优势,其中最显著的一个是铸造加工具有高度的自动化程度。
在传统的铸造加工过程中,往往需要人工进行各种操作才能够完成制造,效率低下且受制于工人技术水平。
但是在智能化制造中,铸造加工使用数字化信息化技术,从制造流程的概念设计到数控加工的各项参数都可以通过计算机进行自动化管理,不仅实现了生产过程的高度自动化,同时也提升了生产效率和生产质量。
另一个优势是铸造加工可以快速适应生产速度和生产量的变化。
作为工业制造的一个重要环节,铸造加工需要能够应对生产过程中产量、型号、品质等多方面的不确定性。
在智能化制造的过程中,不仅可以根据生产需要及时的进行生产调整,更可以进行数量的快速扩张和变更,满足市场的需求,快速响应市场的变化。
2. 铸造加工在智能化制造中的发展方向随着工业的不断发展,铸造加工在智能化制造中的应用也在不断的创新和发展。
在智能制造领域发展的过程中,铸造加工除了在生产流程和生产技术上在不断进行优化,还是在不断地推动产业转型和升级。
其一,虚拟化的铸造加工技术。
虚拟化技术是一种应用广泛的数字化技术。
应用虚拟化技术可以通过软件模拟仿真,在计算机上对整个生产过程进行模拟、优化,实现生产过程的全数字化和自动化。
在智能化制造中,虚拟化的铸造加工技术可以通过人工智能、机器学习等技术,让整个生产过程更加自主、高效和智慧化。
其二,与大数据的融合。
大数据以其高速度、高容量、高复杂性、高价值的特点,成为新技术、新商业模式、新应用场景的重要支撑。
在智能化制造中,铸造加工与大数据的融合将成为一个热点,可以通过数据的收集、分析、挖掘,提高生产过程的智能化、高质量、高效率。
模具设计与制造中的智能化技术应用

模具设计与制造中的智能化技术应用随着科技的不断发展,智能化技术在各个行业中得到了广泛应用,模具设计与制造也不例外。
智能化技术的应用使得模具设计与制造更加高效、精确,并且大大提高了生产效率。
本文将从智能化技术在模具设计与制造中的应用入手,探讨其对行业的影响。
首先,智能化技术在模具设计中的应用使得设计更加精确。
传统的模具设计往往需要经验丰富的设计师进行手工绘图,容易出现尺寸不准确、结构复杂等问题。
而智能化技术的应用,如计算机辅助设计(CAD)软件,能够帮助设计师更加准确地绘制模具图纸,避免了人为因素的干扰,提高了设计的精度。
其次,智能化技术在模具制造中的应用使得生产更加高效。
在传统的模具制造中,需要大量的人力、时间和物力投入,生产周期长,成本高。
而智能化技术的应用,如数控机床、机器人等设备的使用,使得模具制造过程自动化程度更高,能够大大提高生产效率,减少人力和物力的浪费,降低生产成本。
此外,智能化技术在模具设计与制造中的应用还带来了更多的创新。
传统的模具设计与制造往往受限于人力和设备的限制,创新性不高。
而智能化技术的应用,如虚拟现实技术、3D打印技术等,使得设计师能够更加自由地进行创意设计,并且能够快速制造出模具样品,验证设计的可行性。
这种创新性的应用使得模具设计与制造更加灵活多样,能够满足各种不同需求。
然而,智能化技术在模具设计与制造中的应用也面临一些挑战。
首先是技术更新换代的问题。
智能化技术的发展非常迅速,新技术层出不穷,模具设计师和制造者需要不断学习和更新知识,以适应新技术的应用。
其次是安全性的问题。
智能化技术的应用需要涉及到大量的数据和信息,如果不加以保护,就有可能被黑客攻击或者泄露,造成严重的损失。
为了克服这些挑战,模具设计与制造者需要加强技术培训,提高自身的技术水平和应用能力。
同时,加强信息安全意识,加强网络安全防护,保护好企业的核心技术和数据。
综上所述,智能化技术在模具设计与制造中的应用带来了诸多的好处,使得设计更加精确,生产更加高效,创新更加多样。
基于知识推理的导向器叶片单元体精铸模具分模技术研究
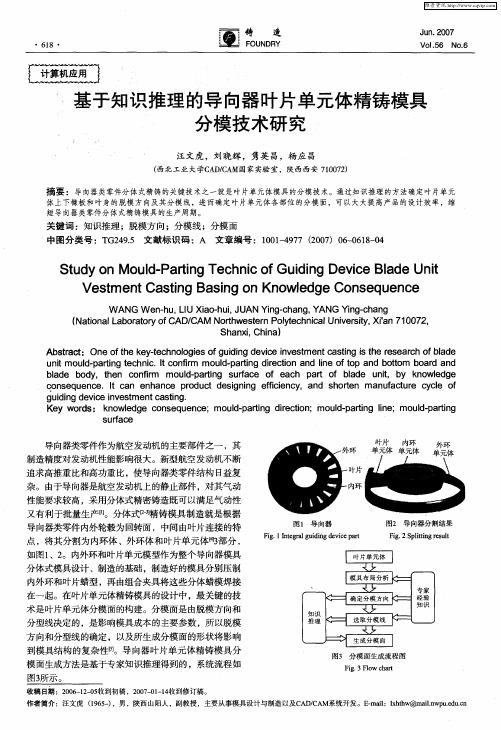
导 向器类零件作为航空发 动机 的主要部 件之一 ,其
制造精度对发动机性能影 响很 大。新型航 空发动机不 断 追求高推重 比和高功重 比 ,使导 向器类零件 结构 日益复 杂 。由于导 向器是航空发动机上 的静 止部件 ,对其气动 性能要求较高 ,采用分体式精 密铸造 既可以满足气动性 又有利 于批量生 产【 I ] 。分体 式 精 铸模具 制造就 是根据 导 向器类零件 内外轮毂 为回转面 ,中间 由叶片连接 的特 点 ,将其 分割为 内环体 、外 环体 和叶 片单 元体 部分 , 如 图1 。内外环和叶片单元模 型作 为整个 导 向器模具 、2 分体式模具设计 、制造 的基础 ,制造好 的模 具分别压制
短导 向器 类零件分体式精铸模具的生产周 期。
关 键词 :知识推 理 ;脱模方 向 ;分模线 ;分模 面 中图分 类号 :T 4 . 文献 标识 码 :A 文章 编 号 :10 —97 (0 7 60 1—4 G29 5 0 147 20 )0— 680
St d n Mo l- rigTe h i fGudn vc a e Unt u y o ud- t c nco iig De ie Bld i Pa n
Ab t c . On f h e -e h oo iso udig d vc n e t e t a t g i te rs arh o ld sr t a e o e k y t c n lge f i n e ie iv sm n s i h e e c fba e t g c n s u i m o l— a ig t c nc I c n r mo l— a ig d r cin a d l e o o n ot m O r n nt ud p r n e h i.t o f m t i ud p r n i t n i f p a d b t t e o n t o b ad a d ba e o y t e c n i ld b d , h n O f m m o l— a ig uf c o e c p r f ld u i b k o e g r ud p r n s r e f a h a o ba e nt y n wld e t a t , i d h r n t ua t r c ce o c n e u n e I c n n a c p o u t d sg ig fce c an s o e man f c u e y l f o s q e c t a e h n e r d c e inn e f in y g iig d vc v s me t a t g ud n e i i e t n s i e n c n
基于知识推理的导向器类零件精铸模具单元体智能切分

W ANG e - n - h n , ANG i, Ln ZHANG u Jn
( ai a L b rtr f A / AM, r we tr oye h ia U i ri , i n7 0 2 N t n l a oaoyo D C o C Not se nP l c nc l n es y X’ 1 7 h t v t a 0 S a x, i ) h n iChn a
得 到的 内外环和 叶片单元模 型 .如 图2 示 。内外环和 所
零件 通常都 采用 精 密铸造 工艺 完 成 。因此 ,精 密铸 造
导 向器 蜡 型 的设 计 和 制造 定 型则 必 然 成 为重 巾之 重 。 目前 ,导 向器类 零件 蜡 型 的获得 可采用快 速 成型制 造
叶片 单元 模 型作 为 整个 导 向器模 具 分 体 式模 具设 计 、
Ab ta t On ft e k yt c n Ige fg iig d vc v s me tc sig i g tn ne n l ig s rc : e o e —e h OO is o udn e ie i e t n a t s et g it r a n , h n n i r e t r a ig a d ba e u i b piig it g a udn e ie p r f rwa - od d sg .Gan d xe n lr n ld nt y s lt ne r l iig d vc a o x m l e in n tn g t ie p r m e e ie p rig ln o g iig e ie h o g e p e sn e p r n e n wld e y aa t r d a n pa e f udn d vc t r u h x r s ig x e i c k o e g b z t e m ah ma i e s nn n sa l h d sa l o n a in f rm a hnn udn e ie p r s fl te t r a o ig a d e t bi e t be f u d t o c iig g iig d vc a wi y c s o t t a de a t . n x c l y Ke ywors: it g a ud n e iep r p r me e ie a ig pa e iv sm e t a t g de d ne r l iig d vc a ; a a t r d p r n ln ;n e t n s i i g t z t c n
模具设计制造过程的智能化技术

模具设计制造过程的智能化技术1 .智能CAD 和智能NC 的实质传统的CA 瓜心AM 系统仅仅是趁立在计算机图形学的基础上的。
随着人工智能技术的发展,人们就试图用它来解决以前无法解决的工程领域问题,智能CAD ( Intelligence CAD , ICAD )和智能NC ( Intelligence NC , INC ;也称Intelligence CAM , ICAM )就是在这种背景下提出的。
如果说传统CAD / CAM 是解决工程问题的一种简化方法,那么智能CAD 和智能NC 实质就是在计算机处理过程中考虑了各种复杂的工艺问题,力图在一种拟实环境下用计算机处理原来只有人类才有可能解决的问题。
模具CAD / CAM 是CAD / CAM 技术最早的应用领域之一,由于模具设计制造技术是一门经验性很强的技术,涉及许多专业领域的经验知识,这一过程的智能化技术研究也是人工智能技术的一个很重要的分支。
2 .产品建模过程中工艺特征模型的表示、抽取与识别技术产品建模就是通过某种模式将设计过程计算机化,依靠计算机进行分析和计算,最后获得设计结果的过程。
产品模型的建立是CAD 的关键技术之一,实际上也是实现模具设计制造智能系统的关键,是设计制造过程中各个环节的知识与信息传递的基础。
当前产品信息模型正沿着几何模型、特征模型和集成化产品模型等方向发展。
特征定义一个零件(或部件)的几何描述的工程意义,它们可以是关于功能、行为或制造的定义等。
特征是与应用相关的,它们可以支持产品活动不同过程、不同层次的需求,实现这些过程之间的信息传递。
特征建模技术实际上就是在非几何的工艺信息和几何信息之间建立起可以沟通的信息桥梁,是工艺特征模型自动抽取与识别的基础。
它也是〔’Ax 智能化集成过程中工艺集成的关键,并为集成化产品建模提供重要的愈考。
而集成化产品建模的一个主要方面就是将专家的设计经验和设计过程的有关知识,表示在产品信息模型中,为实现模具设计制造智能化、自动化提供足够的信息.因此在模具设计制造智能系统中应采用集成化产品模型,而其甲工艺特企模型的表示、抽取与识别技术是关键。
叶片精铸模具设计中标准件智能化选用方法研究

实现 了人工选择参 数 ,系统 自动生成零件 的功能 ,但
是还需要设计人 员进行标 准件种类 和尺寸的选择 ;同 时模具设计人员还要手工生成模具 活块 的槽 腔结构 。
创建特征库 ,建立利用特征库 中的各种 特征组 成某类 零 件的过程化描述 ,表 达出此类零件 的构形 信息 ,它 是 此类零 件在零 件库中的实 际存储形 式 ,称 之为零 件 特性文 件 ( 由建 库 工 具 中 的 特 性 文 件 解 释 程 序 解 释) 。具体 的参数 可驱动 库 中零件模 式具 体化 ,产生
N r w s r oy c n a U i r t,X ’n7 0 7 . C ia ot et nP l eh i l nv sy i a 0 2 h e t c ei 1 hn )
Ab ta t h x rsin o n wld ea d tea po c os d r atslcinb sd O h n wld eW 8d srb di r- sr c :T ee pe s fk o e g n h p ra h t t adp r ee t ae Ntek o e g a ec e np o n a o i e cso iin—c sig mod d s n,a d terao igmeh dw sgv n Th d uaiainpo rm tu tr sit d cd A f meo e at l e i n g n h e snn to a ie . emo lr t rga srcu ewa nr u e . r f h z o o a t itlg n ee t gmeh di h t d r at fba epe iin—modd sg igw gv nb yo tgaigat ca tlg n e nel e tslci to tesa adp r o ld rcs i n n n o l einn 聃 ie ywa f ne rt ri ilnel e c i n i f i i w t o lo ulig3 aa t zf nga h l rr. ev r c t ne a lsw r f rdt aiaeteef in ya dpa t ai i to rb i n D p rmer a o rp i ay T e f ai x mpe e ofe ovl t h fce c n rci ly h f d i i b h i i o e e d i c t
模具的发展以及智能制造的实现
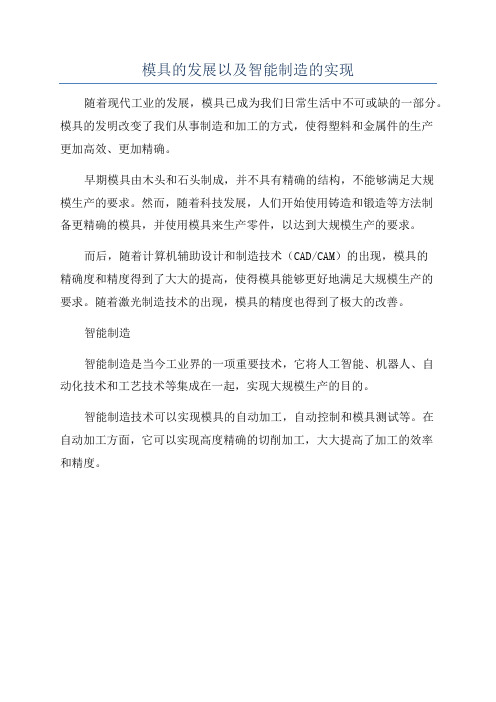
模具的发展以及智能制造的实现
随着现代工业的发展,模具已成为我们日常生活中不可或缺的一部分。
模具的发明改变了我们从事制造和加工的方式,使得塑料和金属件的生产
更加高效、更加精确。
早期模具由木头和石头制成,并不具有精确的结构,不能够满足大规
模生产的要求。
然而,随着科技发展,人们开始使用铸造和锻造等方法制
备更精确的模具,并使用模具来生产零件,以达到大规模生产的要求。
而后,随着计算机辅助设计和制造技术(CAD/CAM)的出现,模具的
精确度和精度得到了大大的提高,使得模具能够更好地满足大规模生产的
要求。
随着激光制造技术的出现,模具的精度也得到了极大的改善。
智能制造
智能制造是当今工业界的一项重要技术,它将人工智能、机器人、自
动化技术和工艺技术等集成在一起,实现大规模生产的目的。
智能制造技术可以实现模具的自动加工,自动控制和模具测试等。
在
自动加工方面,它可以实现高度精确的切削加工,大大提高了加工的效率
和精度。
提高铸造工艺自动化水平的设计方案

提高铸造工艺自动化水平的设计方案提高铸造工艺自动化水平的设计方案1. 引言铸造工艺是制造业中重要的加工方法之一,然而传统的铸造工艺存在着工人劳动强度大、生产效率低、质量难以保证等问题。
为了解决这些问题,提高铸造工艺的自动化水平显得非常重要。
本文将介绍一种设计方案,旨在提高铸造工艺自动化水平,从而提高生产效率和质量稳定性。
2. 设备自动化首先,对铸造工艺的设备进行自动化改造是非常重要的一步。
可以引入自动化设备,如机器人、自动化传送带等,来替代传统的人工操作。
这样可以降低工人劳动强度,提高工作效率。
此外,还可以利用传感器和控制系统对设备进行监测和控制,实现铸造工艺参数的自动调整,并及时报警处理异常情况,以提高质量稳定性。
3. 数据采集与分析其次,通过采集和分析数据,可以对铸造工艺进行优化和改进。
利用传感器和数据采集系统,实时采集设备运行状态、温度、压力等各方面的数据,并将其存储在数据库中。
然后,通过建立合适的数据分析模型,对数据进行分析和挖掘,找出影响铸造质量和生产效率的关键因素。
基于这些分析结果,可以针对性地调整铸造工艺参数,提高产品质量和生产效率。
4. 远程监控与控制此外,借助互联网和信息技术的发展,可以实现对铸造工艺的远程监控和控制。
通过网络连接设备和控制系统,可以实时监控铸造工艺的各项指标,并实现远程控制和调整。
这样,不仅可以减少人工巡检和调整的工作量,还可以及时响应和处理异常情况,提高生产效率和产品质量的稳定性。
5. 人机协作虽然设备的自动化能够提高铸造工艺的效率和质量,但完全依赖自动化设备也会存在一些问题。
因此,人机协作也是提高铸造工艺自动化水平的重要方面。
在设计方案中,可以充分考虑工人与自动化设备的配合,如提供人机界面,使工人能够方便地监控和调整设备运行状态;同时提供培训和技术支持,使工人能够掌握自动化设备的操作技能。
这样可以最大程度地发挥人和机器的优势,提高铸造工艺的生产效率和稳定性。
知识系统设计及其在压铸模智能cad中的应用

知识系统设计及其在压铸模智能cad中的应用
一、知识系统设计
知识系统设计是一种十分有效的让计算机获得信息和智能、模式识别和判断能力的高
级信息技术,指令计算机是有关知识,把相关知识组织在一起,形成一个模式,然后再利
用这个模式进行推理和处理,得出某些结论来。
它可以代表知识的发现、学习、表达、应
用和总结等诸方面的内容与技术。
知识系统设计是一个系统化的方法,借助这种方法,可以用结构化科学的方法来存储,管理和分享相关的知识,如基础知识、方法、技术、流程等,以便合理的使用或组合它们,以产出新的知识。
二、压铸模智能CAD中的应用
压铸模是一种非常复杂的部件,它的设计通常需要反复修改才能得到一个满意的结果。
在这种情况下,知识系统设计技术尤其有效。
知识系统设计允许分析压铸模结构(如冷芯、冷垫和模块),并具有建立工程分析模型这一功能,并可以利用系统知识将其反馈到压铸
模设计过程中。
此外,CAD系统也可以根据客户提供的加工要求,自动找到压铸模的最合
理方案。
结合知识系统设计和CAD技术,可以实现预测和优化的功能,为客户提供高质量的压
铸模。
它可以有效的简化设计过程,大大改善模具的设计与制造的效率,有效的降低客户
的成本。
总之,知识系统设计技术是实现智能压铸模CAD的重要技术,它可以有效运用于整个
压铸模设计和制造生产过程中,为客户提供高效、高质量的产品服务。
基于知识的精铸模具智能化设计方法
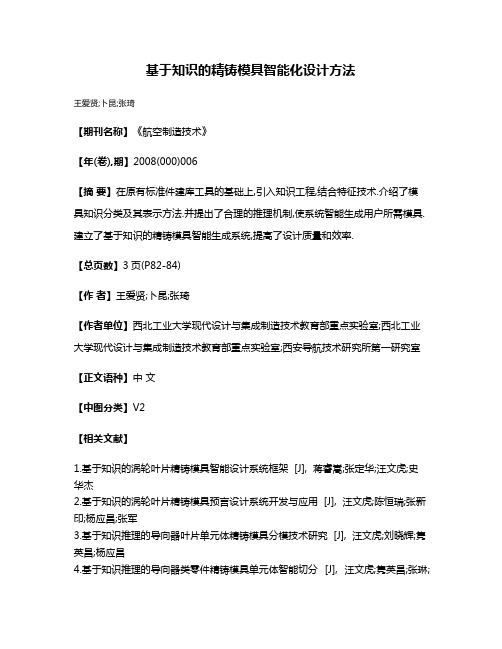
基于知识的精铸模具智能化设计方法
王爱贤;卜昆;张琦
【期刊名称】《航空制造技术》
【年(卷),期】2008(000)006
【摘要】在原有标准件建库工具的基础上,引入知识工程,结合特征技术.介绍了模具知识分类及其表示方法.并提出了合理的推理机制,使系统智能生成用户所需模具.建立了基于知识的精铸模具智能生成系统,提高了设计质量和效率.
【总页数】3页(P82-84)
【作者】王爱贤;卜昆;张琦
【作者单位】西北工业大学现代设计与集成制造技术教育部重点实验室;西北工业大学现代设计与集成制造技术教育部重点实验室;西安导航技术研究所第一研究室【正文语种】中文
【中图分类】V2
【相关文献】
1.基于知识的涡轮叶片精铸模具智能设计系统框架 [J], 蒋睿嵩;张定华;汪文虎;史华杰
2.基于知识的涡轮叶片精铸模具预言设计系统开发与应用 [J], 汪文虎;陈恒瑞;张新印;杨应昌;张军
3.基于知识推理的导向器叶片单元体精铸模具分模技术研究 [J], 汪文虎;刘晓辉;隽英昌;杨应昌
4.基于知识推理的导向器类零件精铸模具单元体智能切分 [J], 汪文虎;隽英昌;张琳;
张军
5.基于知识模板的涡轮叶片精铸模设计方法研究 [J], 周桐;汪文虎;贾丽萍;杨俊臣因版权原因,仅展示原文概要,查看原文内容请购买。
模具设计的创新思维方法
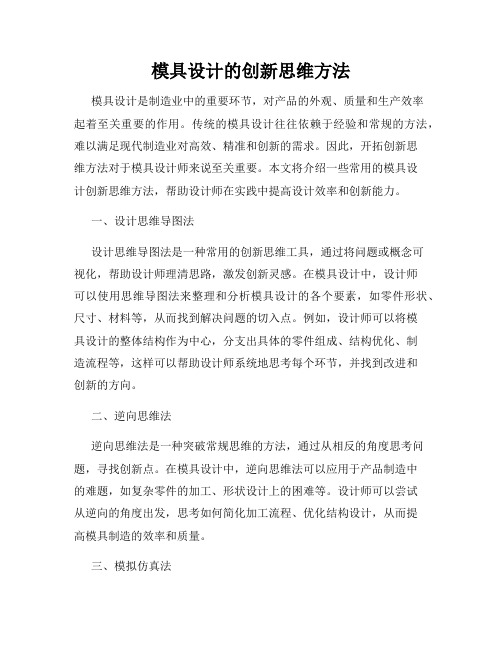
模具设计的创新思维方法模具设计是制造业中的重要环节,对产品的外观、质量和生产效率起着至关重要的作用。
传统的模具设计往往依赖于经验和常规的方法,难以满足现代制造业对高效、精准和创新的需求。
因此,开拓创新思维方法对于模具设计师来说至关重要。
本文将介绍一些常用的模具设计创新思维方法,帮助设计师在实践中提高设计效率和创新能力。
一、设计思维导图法设计思维导图法是一种常用的创新思维工具,通过将问题或概念可视化,帮助设计师理清思路,激发创新灵感。
在模具设计中,设计师可以使用思维导图法来整理和分析模具设计的各个要素,如零件形状、尺寸、材料等,从而找到解决问题的切入点。
例如,设计师可以将模具设计的整体结构作为中心,分支出具体的零件组成、结构优化、制造流程等,这样可以帮助设计师系统地思考每个环节,并找到改进和创新的方向。
二、逆向思维法逆向思维法是一种突破常规思维的方法,通过从相反的角度思考问题,寻找创新点。
在模具设计中,逆向思维法可以应用于产品制造中的难题,如复杂零件的加工、形状设计上的困难等。
设计师可以尝试从逆向的角度出发,思考如何简化加工流程、优化结构设计,从而提高模具制造的效率和质量。
三、模拟仿真法模拟仿真法是一种通过计算机辅助设计软件进行模拟分析的方法,可以模拟出真实环境下的各种工况和情况,帮助设计师评估设计方案的可行性和优劣。
在模具设计中,设计师可以利用仿真软件模拟零件成型过程中的变形、应力分布等,从而准确评估模具的稳定性和性能。
通过模拟仿真,设计师可以快速评估多个设计方案的优劣,降低设计风险,提高设计效率和创新能力。
四、开放式创新法开放式创新法是一种借鉴外部资源和思维的方法,通过与其他行业、领域的专家进行交流和合作,获取新的创意和知识。
在模具设计中,设计师可以积极参与各类展会、研讨会,与其他相关行业的设计师、工程师进行交流和合作,从而了解最新的技术和工艺,拓宽设计思路,激发创新灵感。
此外,设计师还可以利用互联网等开放式平台,加入相关行业的社交圈,通过分享和交流获取创意和灵感,提高设计的创新性和前瞻性。
注塑模具数字化设计与智能制造研究
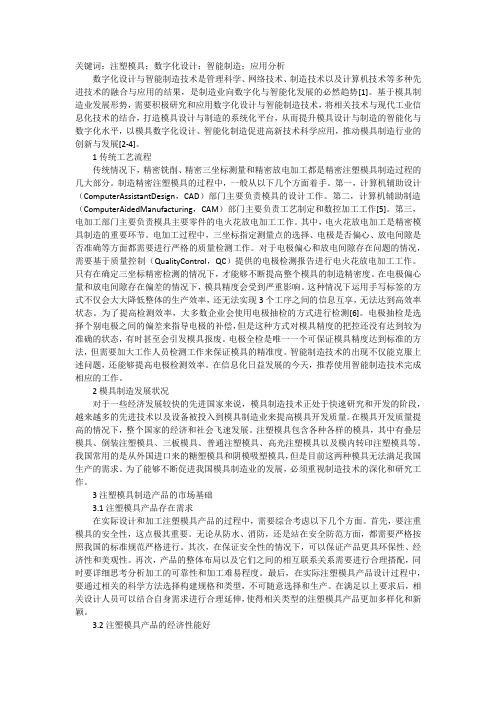
关键词:注塑模具;数字化设计;智能制造;应用分析数字化设计与智能制造技术是管理科学、网络技术、制造技术以及计算机技术等多种先进技术的融合与应用的结果,是制造业向数字化与智能化发展的必然趋势[1]。
基于模具制造业发展形势,需要积极研究和应用数字化设计与智能制造技术,将相关技术与现代工业信息化技术的结合,打造模具设计与制造的系统化平台,从而提升模具设计与制造的智能化与数字化水平,以模具数字化设计、智能化制造促进高新技术科学应用,推动模具制造行业的创新与发展[2-4]。
1传统工艺流程传统情况下,精密铣削、精密三坐标测量和精密放电加工都是精密注塑模具制造过程的几大部分。
制造精密注塑模具的过程中,一般从以下几个方面着手。
第一,计算机辅助设计(ComputerAssistantDesign,CAD)部门主要负责模具的设计工作。
第二,计算机辅助制造(ComputerAidedManufacturing,CAM)部门主要负责工艺制定和数控加工工作[5]。
第三,电加工部门主要负责模具主要零件的电火花放电加工工作。
其中,电火花放电加工是精密模具制造的重要环节。
电加工过程中,三坐标指定测量点的选择、电极是否偏心、放电间隙是否准确等方面都需要进行严格的质量检测工作。
对于电极偏心和放电间隙存在问题的情况,需要基于质量控制(QualityControl,QC)提供的电极检测报告进行电火花放电加工工作。
只有在确定三坐标精密检测的情况下,才能够不断提高整个模具的制造精密度。
在电极偏心量和放电间隙存在偏差的情况下,模具精度会受到严重影响。
这种情况下运用手写标签的方式不仅会大大降低整体的生产效率,还无法实现3个工序之间的信息互享,无法达到高效率状态。
为了提高检测效率,大多数企业会使用电极抽检的方式进行检测[6]。
电极抽检是选择个别电极之间的偏差来指导电极的补偿,但是这种方式对模具精度的把控还没有达到较为准确的状态,有时甚至会引发模具报废。
浅析注塑模具数字化工艺与智能制造运用

浅析注塑模具数字化工艺与智能制造运用摘要:智能化、数字化技术的有效运用,提高了制造产业的工作效率。
为了提高注塑模的功能性,相关人员需要意识到数字化工艺和智能制造技术的应用优势,通过不断规范智能制造的流程及标准,在发挥出新兴技术应用作用的过程中进行创新,提高产品的生产质量,也能保证制造流程更为科学。
基于此,文章就注塑模具数字化工艺与智能制造运用措施进行了分析。
关键词:注塑模具;数字化工艺;智能制造引言:数字化技术、智能制造技术融合了多种技术的操作优势,它可利用科学的、智能的、网络实践技术进行实践作业,通过确定符合标准的注塑模具操作步骤和操作体系,再根据产品的使用要求确定模具设计与制造的相关标准,搭建智能化的操作平台,也能提高注塑模具本身的质量。
另外,相关人员也要结合制造产业的作业标准确定技术的应用思路,通过做好技术的创新与优化,凸显出数字化技术的应用优势。
一、注塑模具数字化工艺与智能制造技术基本概述注塑模具数字化工艺与智能化制造技术是基于制造产业的发展需求而创新的技术模式,该技术符合西方工业的生产,故在发达国家的应用也相对广泛。
虽然国内在注塑模具数字化、智能化技术应用相对较晚,但是相关人员可以结合注塑模具的生产、使用要求确定科学的应用标准,做好技术的融合与创新,符合高新技术的应用趋势[1]。
目前,注塑模具已经融合了三维立体化设计技术、虚拟装配技术、自动化检测及模具检测技术的应用优势,故相关人员需要在保证整体生产技术质量的过程中搭建智能化的生产程序,也能完善模具加工、生产的标准。
二、注塑模具产品应用的市场需求在注塑模具设计、生产、制造过程中,相关人员需要综合考量模具产品的使用要求,再根据注塑模具的功能性、设计标准确定相关市场需求,提高注塑模具应用的有效性。
具体来讲,需要满足以下要点:第一,相关人员要尽可能保证模具的安全性,尤其是要满足产品的防水功能、消防功能需求,并站在产品的安全防范相关安全性问题。
模具数控自动编程设计技巧

模具数控自动编程设计技巧摘要现代的模具设计生产中,通常运用SolidWorks、MasterCAM等CAD/CAM软件先进行产品的3D图形设计,然后根据产品的特点设计模具结构,确定模具型芯、分模面和抽芯结构等,生成模具型芯实体图和工程图,最后根据模具型芯的特点,拟定数控加工工艺,输入加工参数,生成加工程序并输送到数控机床的控制系统进行自动化加工。
这些步骤是现代化模具设计生产的过程和趋势。
它使复杂模具型芯的生产简化为单个机械零件的数控自动化生产,全部模具设计和数控加工编程过程都可以借助CAD/CAM软件在计算机上完成。
它改变了传统的模具制造手段,有效地缩短了模具制造周期,大大提高了模具的质量、精度和生产效率。
关键词SolidWorks;模具;设计1零件分析如图1所示的是三角凸台注塑件产品[16] ,零件材料为ABS,材料的收缩率为5‰,注塑件产品的厚度为2mm。
三角凸台的凸模的分型面为产品的下表面,凸模的材料为锻造铝合金6061,凸模的尺寸设计依据产品尺寸设计,然后将比例缩小2mm的产品厚度。
至于调整材料的收缩率,通过刀具补偿值来统一调整获得凸模尺寸,而且与其从设计角度和制造角度相比,在制造过程中通过调整刀具长度值要比设计容易实现。
2 工艺分析工件材料为锻造铝合金6061,原牌号为LD30,是最常见的。
铝合金与大部分钢材和铸铁材料相比,具有一个明显的优点:较低的屈服强度。
因此,加工中需要的切削力较低,可以在刀具不发生过量磨损的情况下提高切削速度和进料比。
3 工艺方案的确定该凸模零件由多个曲面组成,对表面粗糙度要求较高。
采用球状刀加工之后有加工痕迹存在,通过手工修模达到所需要求。
因此,留有0.1mm的加工余量,由手工研磨到所需的粗糙度要求。
在数控加工前,工件在普通机床上完成6个面的铣削。
为确保三角凸台分型面的质量,解决分型面在粗加工时可能受损的问题,在分型面上留有0.1mm的磨削余量。
考虑到分型面预留的磨削量,对刀后将G54坐标中的Z值抬高0.1mm。
智能铸造技术

智能铸造技术嘿,咱今儿就来说说这智能铸造技术!你说这智能铸造技术啊,就像是一个超级厉害的魔法师,能把那些普通的材料变得神奇无比。
咱就打个比方吧,以前铸造就像是摸着石头过河,全靠经验和感觉,有时候运气不好,出来的东西那叫一个差强人意。
可现在有了智能铸造技术,那就完全不一样啦!它就像给铸造过程装上了一双火眼金睛,能精准地控制每一个环节,让一切都变得有条不紊。
你想想啊,以前工人师傅们得在高温、嘈杂的环境里辛苦劳作,汗流浃背的。
现在呢,智能铸造技术能帮他们省不少力气呢!它能自动调整参数,让铸造出来的产品质量更高、更稳定。
这不是挺好的嘛!而且啊,智能铸造技术还能大大提高生产效率呢!以前要花好长时间才能完成的任务,现在可能一下子就搞定了。
这就好比是坐火箭和骑自行车的区别,那速度,简直了!你说这智能铸造技术这么厉害,那它是不是就没有缺点啦?嘿嘿,那可不一定哦!就像人无完人一样,智能铸造技术也可能会有一些小瑕疵。
比如说,要是程序出了问题,那可就麻烦啦!不过这也不用担心,咱们聪明的技术人员总会有办法解决的嘛。
再说说这智能铸造技术的发展前景,那可真是一片光明啊!随着科技的不断进步,它肯定会变得越来越厉害。
说不定以后啊,我们都能用上智能铸造技术制造出来的超级厉害的产品呢!到时候,咱们的生活肯定会变得更加便利、更加美好。
智能铸造技术就像是一股强大的力量,推动着制造业不断向前发展。
它让我们看到了未来的无限可能,让我们对生活充满了期待。
咱可不能小瞧了它,得好好支持它、发展它,让它为我们的生活带来更多的惊喜和改变。
你说是不是这个理儿?反正我是这么觉得的!这智能铸造技术啊,绝对是个了不起的好东西,咱得好好利用它,让它为我们的生活增光添彩!。
注塑模具数字化设计与智能制造技术

注塑模具数字化设计与智能制造技术摘要:在注塑模具的制造领域中,对数字化设计与智能制造技术进行研究,不仅能够帮助注塑模具制造业对相关技术人员进行有效的培养,还能在整体上提升我国注塑模具制造领域的整体技术水平,具有十分深远的意义。
基于此,本文首先概述了注塑模具数字设计及智能制造技术,对注塑模具智能加工岛的制造工艺流程及内容进行了介绍,重点强调了注塑模具的工艺设计。
并借助大数据技术、信息技术和自动化技术等先进技术,体现注塑模具制造的智能化和工艺性分析,进而实现对模具制造领域中人才培育方向的正确引领。
关键词:注塑模具;数字化设计;智能制造技术;分析引言:在注塑模具生产制造过程中,数字化设计和智能制造技术是十分重要的项目内容之一。
其是制造技术、计算机技术、信息技术、管理科学等多方先进技术通过协调、融合得到的结果。
针对当前模具制造领域的发展现状来看,数字化设计和智能制造技术必然是其今后发展的首要趋势。
因此,模具制造产业应在实际的制造过程中加强对数字化设计和智能制造技术的探究和应用,以成功构建出现代化的注塑模具制造系统平台,从而提高注塑模具制造过程中的数字化和智能化水平,进一步带动注塑模具制造产业的可持续发展。
1.注塑模具、数字化设计和智能制造技术的概述1.1注塑模具注塑模具在本质上是一种在生产塑胶制品中用到的工具,其能够保证塑胶制品在生产中的结构完整性和尺寸精度。
一般情况下,在对形状复杂且对尺寸精度要求较高的塑胶部件进行生产时使用,采用的是将注塑成型的加工方式,利用注塑机将已经融化的塑料摄入到模具内,之后通过冷却固化则能得到成型的产品[1]。
注塑模具的分类较多,可以从多个不同的方面对其类型进行划分,例如从其成型特点进行划分可以将其分为热固性注塑模具和热塑性注塑模具;而从溢料方式的差异可以将其分为溢式、半溢式、不溢式这三种。
1.2数字化设计和智能制造技术注塑模具的数字化设计和智能制造技术主要指的是,在注塑模具的制造过程中,通过对数字化设计和智能制造技术来完成注塑模具的设计工作。
模具智能化要点

模具智能化要点
模具智能化是一种新兴的技术手段,主要用于加强模具制造过程中的自动化和智能化程度,提高模具制造的效率和质量。
下面是模具智能化的要点:
1. 智能化设计:通过使用CAD和CAM等数字化设计和制造工具,实现模具设计的自动化和智能化,提高设计效率和质量。
2. 智能化制造:采用新型材料、先进的制造设备和自动化加工技术,提高模具制造的精度和效率,并减少制造成本。
3. 智能化监控:通过传感器和物联网技术,实现对模具制造过程中的各个环节的实时监控和预警,及时发现和解决问题,提高制造质量和效率。
4. 智能化维护:采用智能化维护技术,对模具设备进行远程监控和管理,及时排除故障,延长设备寿命,降低维护成本。
5. 智能化服务:通过建立模具服务平台,实现模具生命周期内的全面服务,包括设计、制造、维护和升级等,提供一站式的模具解决方案。
综上所述,模具智能化的要点主要包括智能化设计、制造、监控、维护和服务,这些要点旨在提高模具制造的自动化程度和智能化水平,进一步提升制造效率和质量。
- 1、下载文档前请自行甄别文档内容的完整性,平台不提供额外的编辑、内容补充、找答案等附加服务。
- 2、"仅部分预览"的文档,不可在线预览部分如存在完整性等问题,可反馈申请退款(可完整预览的文档不适用该条件!)。
- 3、如文档侵犯您的权益,请联系客服反馈,我们会尽快为您处理(人工客服工作时间:9:00-18:30)。
航空制造技术・2008年第6期学术论文RESEARCH基于知识的精铸模具智能化设计方法*MethodofKnowledge ̄basedIntelligentizedDesignforPrecisionCastingMold西北工业大学现代设计与集成制造技术教育部重点实验室王爱贤卜昆张琦[摘要]在原有标准件建库工具的基础上,引入知识工程,结合特征技术,介绍了模具知识分类及其表示方法,并提出了合理的推理机制,使系统智能生成用户所需模具。
建立了基于知识的精铸模具智能生成系统,提高了设计质量和效率。
关键词:基于知识模具特征智能化[ABSTRACT]Basedontheoriginaltoolforbuildingstandardpartlibrary,theknowledgeengineer-ingisintroduced.Combiningwiththefeaturetechnolo-gy,themoldknowledgeclassificationanditsrepresen-tationareintroduced.Areasonablereasoningmecha-nismisputforward,sothattheintelligentizedsystemgeneratesthemoldrequiredbyusers.Theknowledge ̄basedintelligentgenerationsystemfortheprecisioncastingmoldisestablished.Thedesignqualityandeffi-ciencyareimproved.Keywords:Knowledge ̄basedMoldFeatureIntelligentization涡轮叶片精铸模具的设计与制造是当代航空发动机研制生产中的关键技术难题,它的优化设计,是进一步缩短研制周期、提高产品精度、保证质量的关键。
而模具设计是一种经验性较强的设计,设计人员在长期工作中积累的经验、知识对模具设计有重要影响,所以在通用标准件库中不能完全体现模具知识。
在模具设计中引入知识工程可以消除单独的标准件库在模具设计使用中的不足,结合设计经验进行组合、提炼,建立基于知识的模具设计系统是现代模具设计的发展方向。
叶片精铸模具中常用件和标准件的形状、尺寸选取、空间相对位置关系和结构本身都体现了一定的模具设计知识;通过对大量的叶片模具结构进行分析,提取特征,利用西北工业大学卜昆老师开发的建库工具[1]建立叶片零件的标准件库和常用件库,并对公式、表格、图形、规则等各种表示形式的精铸模具知识(包括理论知识和设计经验)进行处理,运用合理的推理机制,结合“中小型航空发动机信息集成技术应用研究”项目中基于知识的精铸模具优化设计导向软件开发及应用,建立了模具标准件智能化设计的整体框架,进而实现了精铸模具的智能生成。
1基于知识的系统流程基于知识的模具智能生成系统,是在卜昆开发的建库工具的基础上,应用C语言,结合UG二次开发技术UG/OpenAPI,在VC++环境下实现的。
由用户输入毛坯尺寸和模具种类信息,系统通过建立的知识库,提取出与相应毛坯和模具种类相关的知识,并经过推理,自动计算出所需零件的参数,运用建库工具和UG用户操作界面接口,自动生成零件实体(利用UIstyler实现),再根据知识库中空间位置关系,生成用户所需模具,系统流程见图1。
系统的知识库包括零件的属性、特征、参数信息、空间位置关系等,分别以表格、图形、公式的形式体现,推理机制是针对不同模具的类型和尺寸,经过大量的实例模具研究,由提取的知识规则而编制的选取原则,经过推理,很快找到与所需模具相匹配的零件*本课题为航空科技任务:中小型航空发动机信息集成技术应用研究(项目编号:41801150202)。
西安导航技术研究所第一研究室推理机制设计用毛坯用户界面标准件实体建库工具传送标准件参数叶片模具设计系统内部接口模具标准件设计知识图1系统流程图Fig.1Systemflowchart82学术论文RESEARCH参数,利用由建库工具生成的标准件库,系统读入参数,自动生成零件实体,再根据知识库中零件扫描文件信息(包括零件的空间位置关系),进而生成模具。
2精铸模具知识分类和表示2.1知识分类在航空发动机叶片精铸模具设计过程中,可以根据模具设计特点将知识分为:数据层次上相关领域的描述性知识、设计经验中的规则、客观事实性的常识性知识和具体系统运行中的过程性知识。
描述性知识指的是各种对象及其类型和性质,如模具零件名称、属性等;规则是指与模具设计过程相关联的因果关系的动态知识,一般以“if…then…”形式出现,如“if(模具为导向叶片内型)then(模具结构为锁紧机构)”;另外还有常识性知识,例如在导向叶片内型模具设计中上下盖板要比模具毛坯长度宽,主要是为了便于操作;过程性知识为零件在设计过程中的构形信息以及与用户的交互信息等,体现在程序设计中。
2.2知识表示(1)描述性知识表示。
描述性知识在概念上和功能上的层次深浅是不一样的,而框架式表示方法能够层次化、模块化地表示了对象的所有属性及所处的状态以及与其他对象的关系,所以采用框架式表示方法表示描述性知识。
系统中标准件(常用件)的框架构造如下:框架名:<标准件或常用件名称>;参数名称:标准件描述文件所需参数名称;参数值数组:存储描述文件中需要赋值的参数;参数尺寸系列数组:存储标准件尺寸系列数据(仅标准件中存在);标准件的主参数尺寸(系列)数据:存储于标准件库数据表格文件中。
标准件框架中的参数值由两部分组成:一部分参数是从内部系统中获得的零件毛坯尺寸;另一部分参数是由推理机制根据产生式规则知识推理得出的。
例如,关于“导向叶片内型模具上盖板”的框架描述如下:框架名:<tcover>(上盖板);类属:<内型模具锁紧机构>;类型:(常用件,标准件);参数名称:<L,B,H,d1,d2,uh,…>(其中L、B、H分别为毛坯的长、宽、高,d1指上盖板直径,d2指上盖板内径,uh指上盖板厚度);参数值数组:对<L,B,H,d1,d2,uh,…>的赋值;结构类型:(非槽腔结构)。
(2)规则知识的表示。
由于规则知识具有因果性,并且模具设计中主要的规则是根据模具毛坯尺寸以及其他辅助信息来获得所需标准件的参数值,有其不确定性,所以一般采用产生式规则中的“if…then…”形式表示。
例如:If(模具毛坯高度为H)then(锁紧块高度为ceil(2H/3)……),表示为了确保锁紧,锁紧块的高度必须要大于等于模具毛坯高度的2/3,类似的规则还包括内型模具的锁紧机构中上下盖板的厚度等参数的选择。
(3)过程性知识表示。
过程性知识包括不同模具的零件和结构种类知识、典型结构的零件种类知识。
结合UG二次开发函数功能和界面设计,对不同类型的模具在不同的对话框中分开考虑和处理;典型结构零件的种类知识则是在程序内部对其各组成零件依次通过推理生成。
3关键技术3.1典型结构处理模具中有一些典型结构,即指设计人员在长期工作中总结出的完成某一种或几种独立功能模具零件的组合形式。
为了处理方便,把各类组合件按其完成的功能分成各类典型结构,其蕴含的知识具有层次性,它由标准件、非标件按照一定的空间位置关系组合而成,同时典型结构与模具毛坯也具备一定的位置关系。
因此典型结构设计中的知识包括具体零件的描述性知识、零件的结构性知识和过程性知识,在系统中分别体现在框架结构体、零件特性文件和主控程序中,由这些知识综合作用共同生成典型结构。
例如,在内型模具的典型结构———锁紧机构中,上盖板、底板、套筒、螺杆属于非标常用件,定位销属于标准件,由它们按照一定的空间位置关系组合而成典型结构。
其中各零件均由若干特征组合而成,其知识用结构和零件特性文件表示出来;并且上盖板和底板的空间位置要分别位于模具毛坯的上下两端,它们的参数值受模具毛坯尺寸的约束而唯一确定。
对于定位销来说,它的尺寸选取受到底板参数的限制,同时还应该是定位销标准件尺寸系列中存在的值。
系统在生成锁紧机构时,根据过程知识依次推理生成锁紧机构的零件。
3.2标准件和非标件选取时的处理在系统自动生成模具零件过程中,由模具毛坯到832008年第6期・航空制造技术航空制造技术・2008年第6期学术论文RESEARCH成形模具,是一种正向推理机制。
系统首先搜索生成模具的条件,根据条件属性检索与之相适应的规则,再将设计条件值与该规则的条件值相匹配,最终的解是建库工具所需的标准件型号和参数值。
系统搜索到模具所需零件后,首先要判断该零件是否为标准件。
标准件在行业标准中有尺寸系列,参数值是离散的,所以在系统中经过推理机制得到的参数值,除了要与其他零件尺寸配合外还必须要选取尺寸系列中的值;而非标件得到尺寸后只要经过圆整即可。
标准件与非标件选取示意图见图2。
4运行实例系统智能生成模具过程如图3所示。
用户在选择不同的模具种类后系统弹出对话框,提示用户选择毛坯,用户输入毛坯的长、宽、高参数后,系统会自动生成与之相应尺寸的模具实体。
图4为系统生成的锁紧机构。
当选择所要建立的模具为内型模具锁紧机构后,系统调用获取模具毛坯尺寸参数的程序,按照用户输入的毛坯尺寸参数,自动生成符合要求的锁紧机构。
5结论本课题在标准件的建库工具基础上,引入了知识,并用产生式与框架式相结合的方法来表示模具蕴含的规则,系统经过推理,智能化生成用户所需模具,实现了模具的智能化设计。
本系统有其扩展性,并已应用到基于知识的精铸模具优化设计导向软件开发及应用项目中,在模具设计中大大提高了设计效率。
参考文献[1]卜昆,王金凤.基于CATIA的三维参数化图形库建库工具设计与开发.机械科学与技术,1999,18(1):170 ̄172.[2]陈靖芯,李红,徐晶,等.基于知识的智能化设计方法及其实现.农业机械学报,2003,34(4):109 ̄112.[3]陈军,石晓祥,赵震,等.KBE关键技术及其在现代模具智能设计中的应用.锻压技术,2003,28(4):47 ̄50.[4]赵震,彭颖红.KBE在冲压工艺设计中的应用.模具技术,2001(4):59 ̄61,64.[5]李凯岭,张月蓉.基于KBS的注射模具CAD技术的研究.模具技术,2004(3):3 ̄6.(责编晓霏)图3系统智能生成模具过程Fig.3Intelligentmoldgenerationprocessofthesystem图4系统生成的锁紧机构Fig.4Lockmechanismgeneratedbythesystem图2系统对标准件与非标件的处理Fig.2Standardpartsandnon ̄standardpartsprocessedbythesystem计算零件参数尺寸系列值获取模具毛坯尺寸零件是否标准件?零件尺寸圆整将参数写入相关的零件描述文件建库工具生成所要的零件实体标准件尺寸系列参数知识查找标准件尺寸系列参数中匹配的尺寸系列是标准件参数值与毛坯的尺寸间的关联知识非84。