改变电机转速下皮带轮适用外径尺寸计算公式
【2017年整理】电机皮带轮转速计
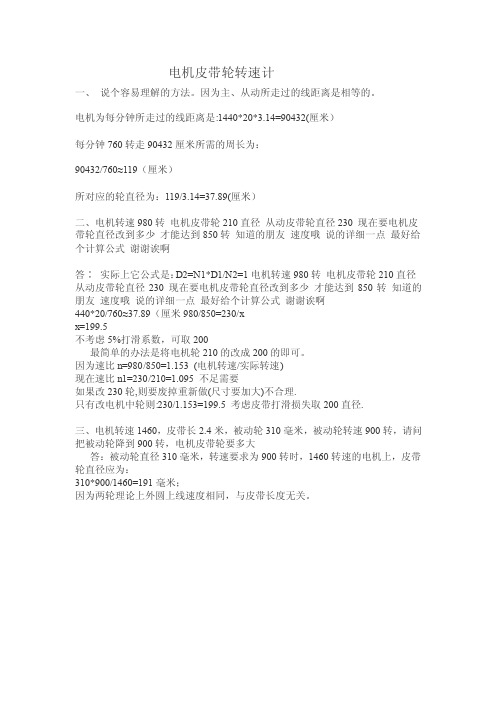
电机皮带轮转速计一、说个容易理解的方法。
因为主、从动所走过的线距离是相等的。
电机为每分钟所走过的线距离是:1440*20*3.14=90432(厘米)每分钟760转走90432厘米所需的周长为:90432/760≈119(厘米)所对应的轮直径为:119/3.14=37.89(厘米)二、电机转速980转电机皮带轮210直径从动皮带轮直径230 现在要电机皮带轮直径改到多少才能达到850转知道的朋友速度哦说的详细一点最好给个计算公式谢谢诶啊答∶实际上它公式是:D2=N1*D1/N2=1电机转速980转电机皮带轮210直径从动皮带轮直径230 现在要电机皮带轮直径改到多少才能达到850转知道的朋友速度哦说的详细一点最好给个计算公式谢谢诶啊440*20/760≈37.89(厘米980/850=230/xx=199.5不考虑5%打滑系数,可取200最简单的办法是将电机轮210的改成200的即可。
因为速比n=980/850=1.153 (电机转速/实际转速)现在速比n1=230/210=1.095 不足需要如果改230轮,则要废掉重新做(尺寸要加大)不合理.只有改电机中轮则:230/1.153=199.5 考虑皮带打滑损失取200直径.三、电机转速1460,皮带长2.4米,被动轮310毫米,被动轮转速900转,请问把被动轮降到900转,电机皮带轮要多大答:被动轮直径310毫米,转速要求为900转时,1460转速的电机上,皮带轮直径应为:310*900/1460=191毫米;因为两轮理论上外圆上线速度相同,与皮带长度无关。
电厂分散控制系统故障分析与处理作者:单位:摘要:归纳、分析了电厂DCS系统出现的故障原因,对故障处理的过程及注意事项进行了说明。
为提高分散控制系统可靠性,从管理角度提出了一些预防措施建议,供参考。
关键词:DCS故障统计分析预防措施随着机组增多、容量增加和老机组自动化化改造的完成,分散控制系统以其系统和网络结构的先进性、控制软件功能的灵活性、人机接口系统的直观性、工程设计和维护的方便性以及通讯系统的开放性等特点,在电力生产过程中得到了广泛应用,其功能在DAS、MCS、BMS、SCS、DEH系统成功应用的基础上,正逐步向MEH、BPC、ETS和ECS方向扩展。
皮带轮比计算公式

皮带轮比计算公式皮带传动是一种常见的机械传动方式,它通过皮带轮的转动来传递动力。
在实际的工程应用中,我们需要计算皮带轮的比值,以便确定传动系统的工作性能。
本文将介绍皮带轮比的计算公式,并讨论其在工程设计中的应用。
皮带轮比的定义。
皮带轮比是指两个相邻皮带轮的直径比值。
在传动系统中,通过改变皮带轮的直径比,可以实现不同的传动比例,从而满足不同的工作需求。
皮带轮比通常用字母“i”表示,其计算公式如下:i = (D1 / D2)。
其中,i表示皮带轮比,D1表示大皮带轮的直径,D2表示小皮带轮的直径。
皮带轮比的计算。
在实际的工程设计中,我们常常需要根据传动系统的要求来计算皮带轮的比值。
计算皮带轮比的步骤如下:1. 确定传动比例,根据传动系统的要求,确定所需的传动比例。
传动比例通常由工作负载、转速和功率等参数决定。
2. 确定大、小皮带轮的直径,根据传动比例和已知的参数,计算出大、小皮带轮的直径。
通常情况下,可以根据所需的传动比例和已知的参数来计算出大、小皮带轮的直径。
3. 计算皮带轮比,根据上述公式,计算出大、小皮带轮的直径比值,得到皮带轮比。
皮带轮比的应用。
皮带轮比的计算在工程设计中具有重要的应用价值。
通过合理的皮带轮比设计,可以实现传动系统的高效工作,并满足不同工作条件下的需求。
以下是皮带轮比在工程设计中的应用:1. 传动系统设计,在传动系统的设计过程中,通过计算皮带轮比,可以确定合适的传动比例,从而实现传动系统的高效工作。
2. 功率传递,通过控制皮带轮比,可以实现不同功率的传递。
根据工作负载和转速等参数,可以确定合适的皮带轮比,从而实现功率的有效传递。
3. 转速调节,通过改变皮带轮比,可以实现传动系统的转速调节。
根据工作需求,可以调整皮带轮比,从而实现不同转速下的工作。
4. 节能设计,合理的皮带轮比设计可以实现传动系统的节能工作。
通过优化传动比例,可以降低传动系统的能耗,从而实现节能设计。
结论。
皮带轮比的计算公式可以帮助工程师确定传动系统的传动比例,从而实现传动系统的高效工作。
皮带计算标准公式

皮带计算标准公式一、 条件,皮带长度L ,巷道倾角β,运输能力(一般取350或400)A ,带速V (一般取1.6,2,2.5,3.15,常用2),松散度γ(一般取1),煤的堆积角度a ,倾角系数C ,最大块度Amax (一般为300-400之间),货断面系数K ,上托辊间距L ’(1-1.5m 一般取1.2m ),下托辊间距L ”(2-3,一般2.5或3),上托单位重量q G ’(一般取9.2kg/m ) ,下托单位重量q G “(2.5m 时4.4kg/m ;3m 时为3.7kg/m ),胶带每米重量q d ,(1000mm 取11.4kg ,800mm 取10.8),运行阻力系数ω′胶带抗拉强度BGX (一般1000mm 取14000N/cm ,10000 N/cm ),输送带安全系数M ′2、胶带宽度计算0.43)m ==(运输能力A=350-400 载货断面系数K=458 松散度γ=1 倾角系数C=0.9 带速V=23、对皮带进行块度效验 B ≥2Amax+2004、胶带运行阻力与胶带张力计算①运行阻力计算:取运行阻力系数ω′=0.05,ω″=0.025每米物料重量q=Q/(3.6×V)=Wzh=g(q+qd + qg′) Lω′cosβ+g(q+qd) L sinβ= (N)W K =g (qd+ qg″) Lω″cosβ± g qdL sinβ(上运为加,下运为减)= (N)②胶带张力计算ˋ1 1′用逐点计算法求胶带个点张力S 2≈S1S 3=1.04S2S 4=1.04S3=1.042S1=1.08 S1S 5=S4+Wk=1.042S1+WK=1.08 S1+WKS6=1.04S5=1.043S1+1.04Wk=1.12 S1+1.04WkS 7=S6+Wzh=1.043S1+1.04Wk+Wzh=1.12 S1+1.04Wk+WzhS8≈S9=1.04S7=1.044S1+1.042Wk+1.04Wzh=1.17S1+1.08Wk+1.04Wzh2′、按摩擦传动条件考虑摩擦力备用系数列方程,得:S 9=S1(1+((e uα-1)/m″))=S1(1+((e0.2×8.225-1)/1.15))=4.663 S1S9=1.17 S1+1.08WK+1.04WZH3′联立1′2′ S9=4.663S1解得:S1=(N) S5= (N)S2=(N) S6= (N)S 3=(N) S7= (N)S4=(N) S8≈S9= (N)4、胶带悬垂度与强度的验算(1)悬垂度验算:重段最小张力S6=N按悬垂度要求重段允许的最小张力为:Smin=5×(q+q d)Lg′×g×cosβ=NSmin<S6胶带悬垂度满足要求(2)胶带强度验算:胶带允许承受的最大张力为:Smax=BGX/M′=1000000/9=111111NSmax>S9 因此胶带强度满足要求5、牵引力与电机功率输送机主轴牵引力为:W0=S9-S1+0.04(S9+S1)=(N)电动机功率为:N=W0×V/1000η= KW考虑15%的备用功率,电机功率为:N=1.15×=KW SPJ 型皮带机满足要求。
电动机皮带轮转速计算公式
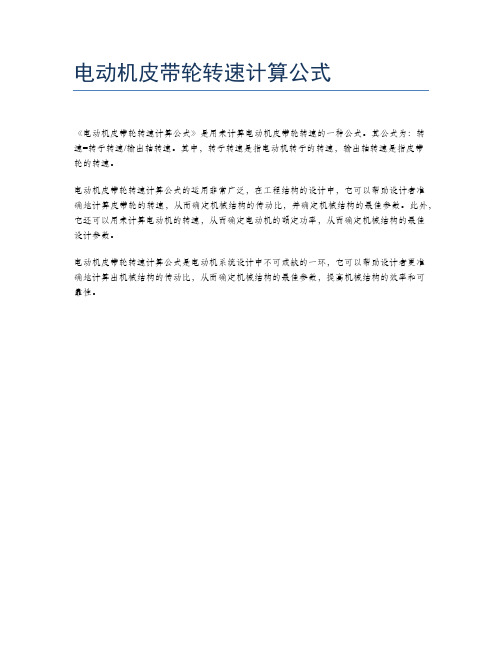
电动机皮带轮转速计算公式
《电动机皮带轮转速计算公式》是用来计算电动机皮带轮转速的一种公式。
其公式为:转速=转子转速/输出轴转速。
其中,转子转速是指电动机转子的转速,输出轴转速是指皮带
轮的转速。
电动机皮带轮转速计算公式的运用非常广泛,在工程结构的设计中,它可以帮助设计者准确地计算皮带轮的转速,从而确定机械结构的传动比,并确定机械结构的最佳参数。
此外,它还可以用来计算电动机的转速,从而确定电动机的额定功率,从而确定机械结构的最佳设计参数。
电动机皮带轮转速计算公式是电动机系统设计中不可或缺的一环,它可以帮助设计者更准确地计算出机械结构的传动比,从而确定机械结构的最佳参数,提高机械结构的效率和可靠性。
电机皮带轮换算表

电机皮带轮换算表介绍电机皮带轮换算表的作用与意义电机皮带轮换算表的定义电机皮带轮换算表是一种用于计算电机传动比例的工具,它基于电机皮带轮的直径和齿数之间的关系。
通过使用这个换算表,我们可以方便地确定不同直径或齿数的电机皮带轮之间的换算比例。
电机皮带轮换算表的作用电机皮带轮换算表的主要作用是帮助工程师和技术人员在设计与维护电机传动系统时计算合适的换算比例。
通过准确选择电机皮带轮的尺寸,我们可以实现以下目标:1.传递扭矩:电机皮带轮的尺寸决定了传递到工作负载上的扭矩,适当选择合适的换算比例可以确保电机与负载之间的匹配,避免因负载扭矩过大或过小而导致的故障。
2.控制转速:电机皮带轮的尺寸也影响了传动系统的转速。
通过合理选择电机皮带轮的换算比例,我们可以调整输出转速,使其符合工作要求。
3.节约能源:通过选择合适的电机皮带轮换算比例,我们可以优化传动效率,减少能源消耗。
这对于大型工业设备和生产线上的电机传动系统特别重要。
电机皮带轮换算表的使用方法了解电机皮带轮参数在使用电机皮带轮换算表之前,我们首先需要了解电机皮带轮的直径和齿数等参数。
这些参数可以从电机和传动系统的技术手册、标签及相关图纸中获取。
确定传动系统要求然后,我们需要明确传动系统的要求,包括所需的工作转速和扭矩。
这些要求通常可以从设计规范、工艺流程或产品手册中得到。
查找换算比例接下来,根据电机皮带轮的参数和传动系统的要求,我们可以查找电机皮带轮换算表,并根据表中提供的数据选择合适的换算比例。
这些表通常按照不同电机型号和规格进行分类,以便更方便地查找所需信息。
应用换算比例找到合适的换算比例后,我们可以根据公式或图表上的指示,计算并选择合适的电机皮带轮尺寸。
这些计算通常涉及到电机轴之间的转速比、齿数比和直径比等参数。
考虑其他因素在应用换算比例时,我们还需要考虑其他因素,如传动带的类型、传动效率、工作环境和设备的可靠性等。
这些因素会影响我们的选型和换算结果,因此需要全面考虑。
皮带轮及皮带选型计算

9.75
P:传递的功率 KA:工 况系数,此处取1.3
2 选定带型
3 传动比
i
i= n1/n2
4 小带轮基准直径 dd1 mm
SPA 1.41 140
n1:小带轮转速 n2:大 带轮转速
0.01 宜选较大直径§ε值
5 大带195.67 190 按表取标准值
a
a0
Ld
Ld0 2
1
180o
d2
a
d1
57.3o
z
Pd
P1 P1 K Kl
10.56 1500 1999.21 740.40 176.13
1.68
v 一般不得低于5m/s
740
根据结构要求确定 前 <a0<后
2000 由表选取相近的Ld
1.06 Kl:带长修正系数
0.99 Kα:小带轮包角修正系数
5.4 根据带型、dd1和n1确定
0.13 2
根据带型、dd1和i查表
Kα:小带轮包角修正系数 Kl:带长修正系数
1061
SPA 140 38 × 2 190 42 × 2 SPA 2000 × 2
6 带速
v
m/s v = πdp1n1/(60×1000)
7 初定轴间距
a0
mm
8 所需基准长度 Ld0 mm
9 实际轴间距
a
mm
10 小带轮包角
α1 。
11 单根V带传递功率 P1 KW
12
传动比i≠1额定 功率增量
△P1
13 V带的根数
z
231
2
Ld0 2a0 2
dd1 dd2
dd2 dd1 4 a0
各种同步带轮的计算公式

各种同步带轮的计算公式同步带轮的节圆直径计算:Dp=p×Z/∏Dp:节径Z :齿数∏:圆周率同步带轮实际外圆直径计算:De= Dp-2δDp:节径δ:节顶距同步带轮中心距及同步带节线长计算L’:近似皮带节线长C :两轴的中心距Dp :大带轮的节径dp :小带轮节径中心距的确定B= L – 1.57 (Dp + dp)L:皮带节线长带轮径向允许跳动量(单位:MM)表3带轮外径允许跳值≤203.20 0.13>203.20 0.13+[(带轮外径-203.20)x0.005]圆弧齿轮传动设计步骤:1) 简化设计:根据齿轮传动的传动功率、输入转速、传动比等条件,确定中心距、模数等主要参数。
如果中心距、模数已知,可跳过这一步。
2) 几何设计计算:设计和计算齿轮的基本参数,并进行几何尺寸计算。
3) 强度校核:在基本参数确定后,进行精确的齿面接触强度和齿根弯曲强度校核。
4) 如果校核不满足强度要求,可以返回带轮端面允许跳动量公差(单位:MM)表2带轮外径允许跳动量≤101.60 0.1>101.60~254.00 带轮外径x0.001>254.00 0.25+[(带轮外径-254.00)x0.005]梯形齿同步带、轮选型圈额定功率KWT形齿同步带、轮选型图额定功率KWHTD型(圆弧形齿)同步带、轮选型图额定功率KW同步带的选型方法步骤1 确定设计时的必要条件1机械种类 2传动动力 3负载变动程度4一日工作时间 5小带轮的转速 6旋转比(大带轮齿数/小带轮齿数) 7暂定轴间距 8带轮直径极限 9其他使用条件【步骤2-a】计算设计动力……MXL/XL/L/H/S□M/MTS□M系列时●设计动力(Pd)=传动动力(Pt) M过负载系数(Ks)·请根据原动机额定动力计算传动动力(Pt)。
(原本根据施加在皮带上的实际负载进行计算较为理想)·过负载系数(Ks)=Ko+Kr+Ki Ko: 负载补偿系数(表1) Kr: 旋转比补偿系数(2) Ki: 惰轮补偿系数(表3)电机选型说明无刷直流电机无刷直流电机采用电子部件替代传统电刷换相器,保留了直流电机的优良调速特性,低速力矩大,调速范围宽,电机体积小效率高,同时克服了直流电机电刷容易打火特点无级调速,调速范围较宽,其调速比可达到1:50,1:100或更高相对有刷直流和交流变频,具有更高的工作转速电机采用高性能永磁材料,高能密度设计,相对于交流异步电机体积明显减小,效率高,转矩大电机采用高热容技术设计,电机温升低电机采用拉伸铝合金外壳,外观精美,传热性好在额定转速范围内保持恒转矩启动转矩大,过载能力强,运行平稳,低噪声反馈方式采用开关霍尔,低线数码盘或无位置传感器方式相关术语额定功率:无刷直流电机运行在额定转速下,输出额定转矩时输出的功率额定功率=额定转速(rpm)x额定转矩(N.m)x2x3.14/60=额定转速(rpm)x额定转矩(N.m)/9.55额定转速:无刷直流电机在额定负载下能长时间运行的最大速度额定转矩:无刷直流电机在长时间稳定运行条件下可以输出的最大转矩无刷直流电机有关参数环境温度--0℃- +50℃环境湿度--<85%RH绝缘等级--B级耐振动/耐冲击--0.5/2.5G链轮链条的选择方法选择滚轮链条时应把握以下7个条件。
皮带轮计算公式
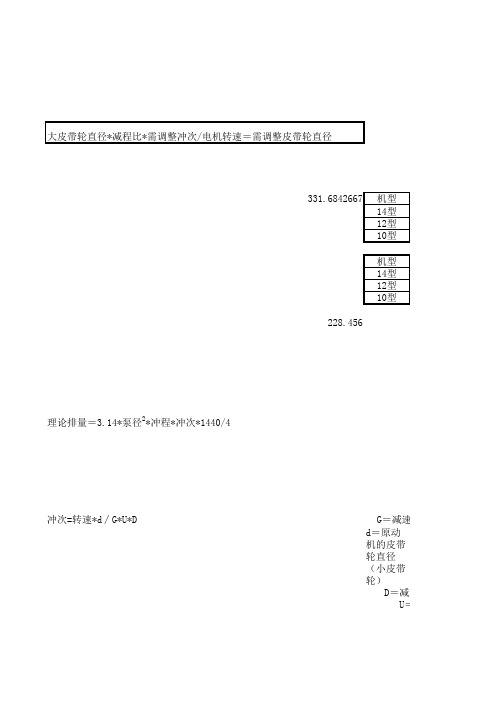
皮带轮长度计算

皮带轮长度计算皮带轮长度计算是在机械设计和传动中常见的计算方法之一。
皮带轮长度是指皮带围绕在两个皮带轮上的长度,它的计算涉及到皮带的长度、轮边直径以及皮带的拉紧方式等因素。
要计算皮带轮长度,我们需要知道皮带的长度。
皮带的长度通常可以通过以下公式计算得到:皮带长度(L)= (π/2)×((D1+D2)/2 + 2C)+ ((D1-D2)^2 /(4C)+ C^2)^0.5其中,π为圆周率,D1和D2分别为两个皮带轮的直径,C为两个皮带轮中心距离的一半。
我们需要考虑皮带的拉紧方式对皮带长度的影响。
常见的皮带拉紧方式有三种:固定轴距、固定中心距和固定皮带长度。
在固定轴距的情况下,皮带长度计算公式为:皮带长度(L)= (π/2)×(D1+D2)/2 + 2C在固定中心距的情况下,皮带长度计算公式为:皮带长度(L)= (π/2)×(D1+D2)/2 + 2C + ((D1-D2)^2 /(4C)+ C^2)^0.5在固定皮带长度的情况下,皮带长度计算公式为:皮带长度(L)= (π/2)×(D1+D2)/2 + 2C - ((D1-D2)^2 /(4C)+ C^2)^0.5除了以上的计算方法,如果需要考虑其他因素,如皮带的弯曲半径、拉紧装置的弹性等,还可以采用近似计算或者通过专业软件进行计算。
在实际应用中,皮带轮长度的计算对于正确选择和设计传动系统至关重要。
合理选择皮带轮长度不仅可以确保传动的稳定性和可靠性,还可以提高传动效率和延长传动部件的使用寿命。
总结起来,皮带轮长度的计算是一项复杂而重要的工作,需要考虑多个因素并运用相应的公式和计算方法。
只有在准确计算皮带轮长度的基础上,才能进行合理的传动设计和选型,从而满足机械传动的要求。
游梁式抽油机冲次与电机转速、电机皮带轮直径关系式的推导

与冲程参数相比, 冲次调整简单、 易于实现, 因此冲次调整是实际 速为曲柄轴转速, 即其减速比可表示为:
生产中最常用的调参办法 。理论研究发现 , 存在一个恰当的冲
抽油机减速比= 电动机转速, 曲柄轴转速
( 4 )
次, 既能满足抽油机液量要求, 又不至于素统效率过低。这个恰 由上述分析知, 曲柄转速即为冲次。综合( 3 ) 式和( 4 ) 式即得 当的冲次是多少, 要根据油井与地层的侧排协调关系、 产液量情 到关系式( 5 ) : t :・ 、
.
转经皮带传送 , 将动力传给减速箱输入车 畦 I , 输入轴将动力传给中 较复杂 ; 另外 , 通过改变减速箱皮带轮直径的大小对调整冲次的
间轴 , 中间轴将 动力传给输出轴 ( 由于输 轴、 中间轴和输 出轴 齿 效果不 明显 , 且 受到减速 箱外形尺寸的限制较大 。所以现场一般
轮逐 渐增大 , 所 以角速度在逐渐减小 ) , 输 拙轴将减速后的动 力再 通过改变 电机转速和 电机皮带轮直径I 拘 大 小来调整冲次 。
X - 大学学报, 2 0 1 1 .
轮齿数。若某抽油机减速箱输入轴齿数为Z 1 , 左右旋齿数为Z 2 ,
中间轴 齿数为z 3 , 输 出轴齿数为z 4 , 那么 :
【 3 ] 吉效科, 李宁会等. 抽油机参数优化技术探讨[ J 】 . 长江大学
学报, 2 0 1 0 .
减速 箱一级减 速比= 从动轮 的齿数/ 主 动轮 的齿数= Z 2 / Z 1 , 二
传给 曲柄, 带动曲柄做低速运动, 再通过 曲柄一  ̄k r l : 一 游梁的四连 三 、 结论及认识
杆 机构, 使驴头带动井下抽油泵做低速上卞往复运动。
皮带轮转速计算公式
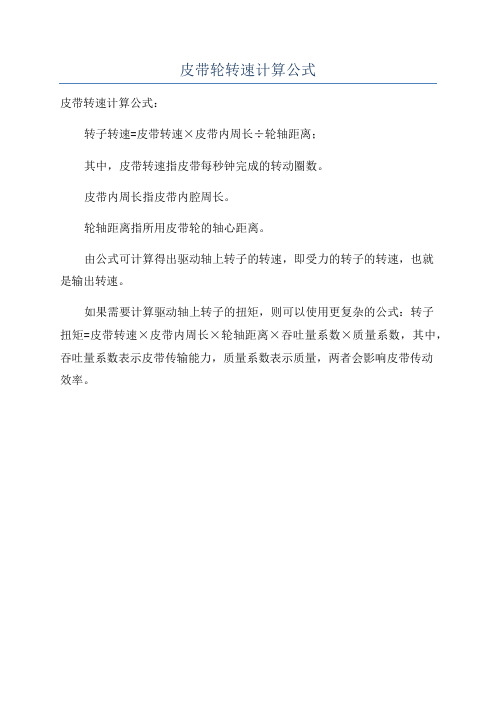
皮带轮转速计算公式
皮带转速计算公式:
转子转速=皮带转速×皮带内周长÷轮轴距离;
其中,皮带转速指皮带每秒钟完成的转动圈数。
皮带内周长指皮带内腔周长。
轮轴距离指所用皮带轮的轴心距离。
由公式可计算得出驱动轴上转子的转速,即受力的转子的转速,也就
是输出转速。
如果需要计算驱动轴上转子的扭矩,则可以使用更复杂的公式:转子
扭矩=皮带转速×皮带内周长×轮轴距离×吞吐量系数×质量系数,其中,吞吐量系数表示皮带传输能力,质量系数表示质量,两者会影响皮带传动
效率。
皮带轮计算
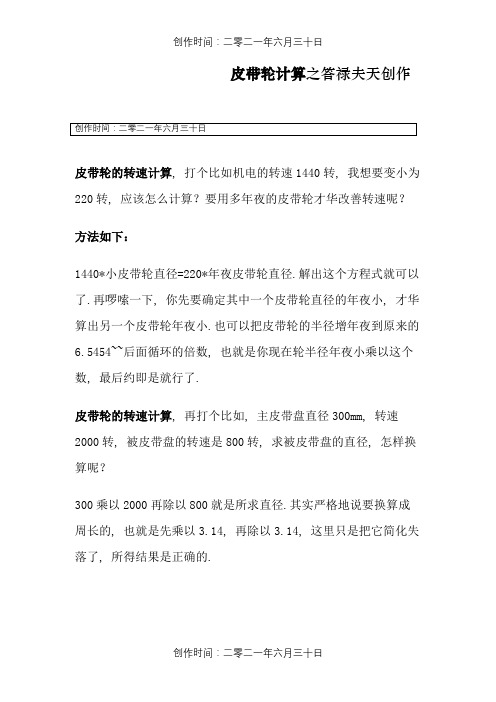
皮带轮计算之答禄夫天创作
皮带轮的转速计算, 打个比如机电的转速1440转, 我想要变小为220转, 应该怎么计算?要用多年夜的皮带轮才华改善转速呢?方法如下:
1440*小皮带轮直径=220*年夜皮带轮直径.解出这个方程式就可以了.再啰嗦一下, 你先要确定其中一个皮带轮直径的年夜小, 才华算出另一个皮带轮年夜小.也可以把皮带轮的半径增年夜到原来的6.5454~~后面循环的倍数, 也就是你现在轮半径年夜小乘以这个数, 最后约即是就行了.
皮带轮的转速计算, 再打个比如, 主皮带盘直径300mm, 转速2000转, 被皮带盘的转速是800转, 求被皮带盘的直径, 怎样换算呢?
300乘以2000再除以800就是所求直径.其实严格地说要换算成周长的, 也就是先乘以3.14, 再除以3.14, 这里只是把它简化失落了, 所得结果是正确的.
主动轮直径310毫米, 转速要求为900转时, 1460转速的机电上, 皮带轮直径应为:
310*900/1460=191毫米;
皮带轮的线速度怎么计算皮带轮的直径怎么计算
公式如下:
主动轮转速为:A
主动轮直径为:a
主动轮转速为:B
主动轮直径为:b
a/b*A=B 百变不离其中
线速/(轮直径X3.14X机电转速/蜗轮皮带轮直径/减速机速比)=机电皮带轮直径。
延伸机计算公式
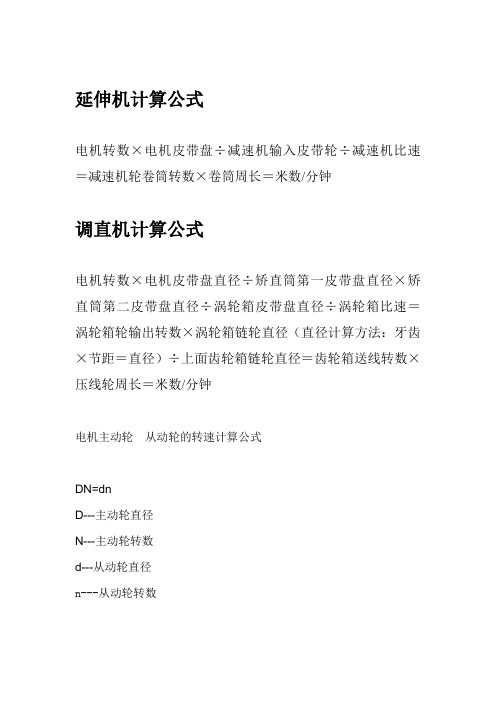
延伸机计算公式
电机转数×电机皮带盘÷减速机输入皮带轮÷减速机比速=减速机轮卷筒转数×卷筒周长=米数/分钟
调直机计算公式
电机转数×电机皮带盘直径÷矫直筒第一皮带盘直径×矫直筒第二皮带盘直径÷涡轮箱皮带盘直径÷涡轮箱比速=涡轮箱轮输出转数×涡轮箱链轮直径(直径计算方法:牙齿×节距=直径)÷上面齿轮箱链轮直径=齿轮箱送线转数×压线轮周长=米数/分钟
电机主动轮从动轮的转速计算公式
DN=dn
D---主动轮直径
N---主动轮转数
d---从动轮直径
n---从动轮转数。
皮带轮速比计算公式
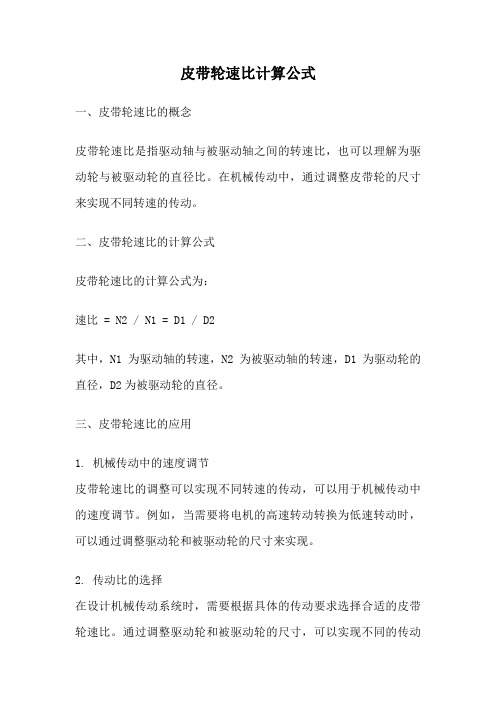
皮带轮速比计算公式
一、皮带轮速比的概念
皮带轮速比是指驱动轴与被驱动轴之间的转速比,也可以理解为驱动轮与被驱动轮的直径比。
在机械传动中,通过调整皮带轮的尺寸来实现不同转速的传动。
二、皮带轮速比的计算公式
皮带轮速比的计算公式为:
速比 = N2 / N1 = D1 / D2
其中,N1为驱动轴的转速,N2为被驱动轴的转速,D1为驱动轮的直径,D2为被驱动轮的直径。
三、皮带轮速比的应用
1. 机械传动中的速度调节
皮带轮速比的调整可以实现不同转速的传动,可以用于机械传动中的速度调节。
例如,当需要将电机的高速转动转换为低速转动时,可以通过调整驱动轮和被驱动轮的尺寸来实现。
2. 传动比的选择
在设计机械传动系统时,需要根据具体的传动要求选择合适的皮带轮速比。
通过调整驱动轮和被驱动轮的尺寸,可以实现不同的传动
比,以满足不同的工作需求。
3. 皮带传动系统的设计
在设计皮带传动系统时,需要根据所需的传动比和转速来选择合适的驱动轮和被驱动轮。
通过计算皮带轮速比,可以确定合适的轮径,从而满足传动系统的要求。
4. 动力传递的优化
在某些情况下,为了优化动力传递效果,可以通过调整皮带轮速比来实现。
例如,在汽车发动机中,通过调整曲轴和飞轮的尺寸,可以改变转速和扭矩的传递比例,从而提高动力输出的效果。
四、总结
皮带轮速比是机械传动中常用的参数,用于调整传动系统的转速和传动比。
通过计算皮带轮速比,可以选择合适的轮径,满足传动系统的要求,并优化动力传递效果。
在实际工程中,合理应用皮带轮速比可以提高机械传动系统的效率和性能。
皮带轮计算之欧阳科创编
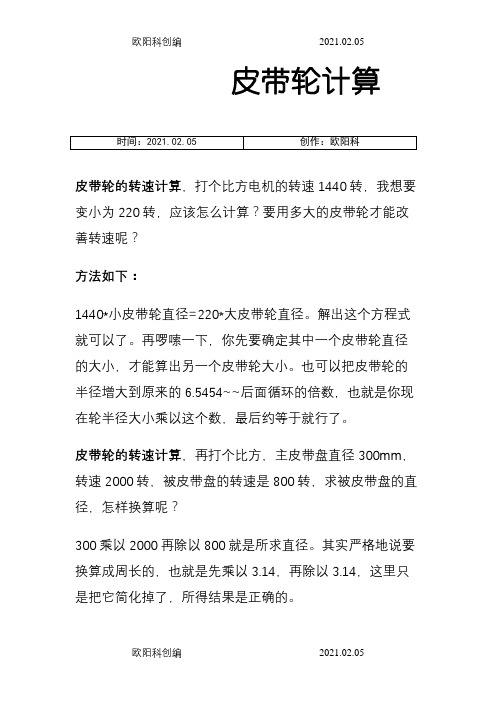
皮带轮计算
皮带轮的转速计算,打个比方电机的转速1440转,我想要变小为220转,应该怎么计算?要用多大的皮带轮才能改善转速呢?
方法如下:
1440*小皮带轮直径=220*大皮带轮直径。
解出这个方程式就可以了。
再啰嗦一下,你先要确定其中一个皮带轮直径的大小,才能算出另一个皮带轮大小。
也可以把皮带轮的半径增大到原来的6.5454~~后面循环的倍数,也就是你现在轮半径大小乘以这个数,最后约等于就行了。
皮带轮的转速计算,再打个比方,主皮带盘直径300mm,转速2000转,被皮带盘的转速是800转,求被皮带盘的直径,怎样换算呢?
300乘以2000再除以800就是所求直径。
其实严格地说要换算成周长的,也就是先乘以3.14,再除以3.14,这里只是把它简化掉了,所得结果是正确的。
被动轮直径310毫米,转速要求为900转时,1460转速的电机上,皮带轮直径应为:310*900/1460=191毫米;
皮带轮的线速度怎么计算皮带轮的直径怎么计算
公式如下:
主动轮转速为:A
主动轮直径为:a
被动轮转速为:B
被动轮直径为:b
a/b*A=B 百变不离其中
轮直径X3.14X电机转速X电机皮带轮直径/涡轮皮带轮直径/减速速度比=锯条速度
轮直径X3.14X电机转速X电机皮带轮直径/锯条速度/减速速度比=涡轮皮带轮直径
线速/(轮直径X3.14X电机转速/蜗轮皮带轮直径/减速机速比)=电机皮带轮直径。
皮带轮转速计算公式
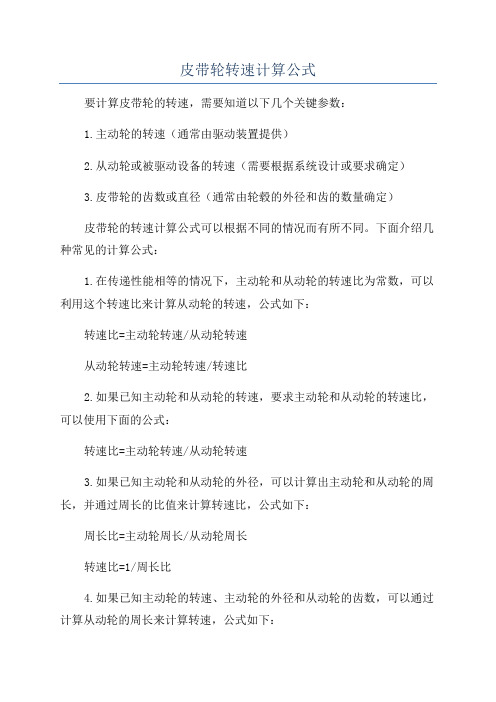
皮带轮转速计算公式
要计算皮带轮的转速,需要知道以下几个关键参数:
1.主动轮的转速(通常由驱动装置提供)
2.从动轮或被驱动设备的转速(需要根据系统设计或要求确定)
3.皮带轮的齿数或直径(通常由轮毂的外径和齿的数量确定)
皮带轮的转速计算公式可以根据不同的情况而有所不同。
下面介绍几种常见的计算公式:
1.在传递性能相等的情况下,主动轮和从动轮的转速比为常数,可以利用这个转速比来计算从动轮的转速,公式如下:
转速比=主动轮转速/从动轮转速
从动轮转速=主动轮转速/转速比
2.如果已知主动轮和从动轮的转速,要求主动轮和从动轮的转速比,可以使用下面的公式:
转速比=主动轮转速/从动轮转速
3.如果已知主动轮和从动轮的外径,可以计算出主动轮和从动轮的周长,并通过周长的比值来计算转速比,公式如下:
周长比=主动轮周长/从动轮周长
转速比=1/周长比
4.如果已知主动轮的转速、主动轮的外径和从动轮的齿数,可以通过计算从动轮的周长来计算转速,公式如下:
从动轮周长=2π×从动轮外径×从动轮齿数
从动轮转速=主动轮转速×从动轮周长/主动轮周长
上述计算公式仅适用于一般情况下皮带轮的转速计算。
在实际应用中,还需要考虑皮带的伸长、滑动、弯曲等因素对转速的影响。
此外,还需要
根据具体的设备设计和工作条件,选择合适的皮带轮和驱动装置。
总之,对于皮带轮的转速计算,需要根据系统的具体情况和要求确定
适用的计算公式,并结合实际情况进行计算和调整。
皮带皮带轮计算

pd = K A P
(5-23) 载荷变动小, 每天工作大于 16 小时, 轻载启动, 取 K A =1.2; K A —工况系数, P — 传递的功率,P =3.0KW
p d = K A P =1.2 3.0 =3.6KW
(2)根据 p d 和转速 n1 选取普通 V 带 查机械设计 (孙志礼主编)图 3-12,选 A 型 V 带。[32] (3)传动比 i 由于采用变频器控制转速,且考虑到立轴尺寸,传动比可定为 i = 0.9 。 (4)带轮基准直径 查机械设计(孙志礼主编)表 3-6,取 d d =75 mm, d a =80.5mm。 (5)带速 V (m/s)
K —小带轮包角修正系数,查表得 K =1 ;
K L —带长修正系数,查表得 K L =0.96 ;
代入数据,得 z =3.50,考虑到污泥的性质变化会影响载荷的波动及离心机 转子较大的转动惯量,为安全起见,并取整,令 z =4 。 V 带最多使用根数见表 5-2。
V 带型号
zቤተ መጻሕፍቲ ባይዱmax
Y
Z
(9)带轮包角 ( °)
= 180°
(10)单根 V 带的基本额定功率 P1 (kw) 由传动设计手册查得: 带轮基准直径 d d =75mm,带轮转速 n1 = 3000 r/min=366.52 rad/s 时,A 型 V 带单 根基本额定功率为: P0 =1.07 kw (11)单根 V 带的基本额定功率增量 P0 单根 V 带的基本额定功率增量
FQ 2 F0 zSin
1
2
(5-29) 代入数据得, FQ = 544.08N。 (15)带轮的结构和尺寸(查机械设计手册) A 型槽型; 基准宽度 bd =11.0mm; 槽深 h=11.5mm 基准线上槽深 ha =2.8mm; 基准线下槽深 h f =8.7mm; 槽间距 e =15 0.3 mm; 槽边距 f min =9mm,取 f =11.5mm;