04-特种铸造
第四节特种铸造概要

消失模铸造
消失模
增大了铸件结构设计的自由度:许多在普通砂型铸造中 难以铸造的铸件结构在实型铸造中不存在任何问题,可以 铸造的铸件结构在采用实型铸造后壁厚减少,整体重量 减轻约15%
消失模铸造应用: 特别适合于形状复杂铸件的生产,适用范 围广,不但适合于生产各类合金 (包括灰铸铁、球墨铸 铁以及除低碳钢以外的铸钢,还包括铝、镁、铜合 金),而且不受铸件结构、尺寸、重量和批量限制。
4)生产批量不受限制,单件、小批、大批量生产均可。
5)缺点:材料贵,工艺过程繁杂,生产周期长.
应用: 最适合高熔点合金精密铸件的成批,大量生产;形 状,复杂、难以切削的小零件,大批量生产。
目前在汽车、机床、气轮机、航空、兵器等领域得到 广泛应用。如:汽轮机叶片,风动工具,滚刀等。
二、实型铸造(消失模铸造)
生产率低于压铸。
适用范围:
一般用来大量生产铝合金、镁合金的精密铸件,包括 缸体、缸盖、活塞、曲轴箱等等,也能铸造其它各种合金, 包括铜合金甚至球铁,如QT曲轴、铜合金螺旋浆等。
六、离心铸造
将液态合金浇入高速旋转(250~1500r/min)的铸型中, 使液态合金在离心力作用下填充铸型并凝固的铸造方法。 1、离心铸造的生产方式: 1)离心铸造是在离心铸造机上进行的,其过程是:将金 属型型腔清理干净,喷涂料,铸型旋转,浇入定量金属液, 待一定时间后停止旋转,取出铸件。 2)按离心铸造旋转轴的位置分为: 立式:铸型绕垂直轴旋转,用于生产圆环铸件; 卧式:铸型绕水平轴旋转,用于生产管类和套类铸件。 离心铸造的铸型主要使用金属型,也可以用砂型。
熔模铸造
金属型铸造
压力铸造
低压铸造
比较项目
适用金属
任意
不限制,以铸钢 不限制,以有色合 铝、锌、镁等低熔 以有色合金为主,
特 种 铸 造

二、金属型铸造
金属型铸造是指将液态 金属浇入金属铸型中获得铸 件的工艺。金属铸型有多种 形式,如垂直分型式、水平 分型式和复合型式等,其中 垂直分型式使用方便,应用 最广。
1,2—左右半型;3—底型;4,5,6—分块 金属砂芯;7,8—销孔金属砂芯
图6-23 铸造铝活塞的金属铸型
与砂型铸造相比,金属型铸造具有以下特点。
室;7—压射活塞;8—铸件
图6-24 卧式冷挤压铸机的工作过程示意图
与砂型铸造相比,压力铸造具有以下特点。
(1)铸件的表面质量和尺寸精度高,一般可以不经机械加工而直接 使用。
(2)铸件的强度和硬度较高。 (3)可以压铸形状复杂的薄壁铸件。 (4)压铸件中可嵌铸其他材料,如钢、铸铁、铜合金、钻石等,可 以节省贵重材料和机械加工工时。 (5)压力铸造的生产效率较高,但压铸设备成本高、生产周期长。 (6)压铸件容易产生气孔,不宜进行大余量的切削加工和热处理。
四、低压铸造
低压铸造是指液态金属在较低的压力(一般0.02~0.06 MPa)下, 自下而上地充填型腔并凝固而获得铸件的工艺。
1—铸型;2—密封盖;3—坩埚;4—金属液;5—升液管 图6-25 低压铸造的工艺过程
与砂型铸造相比,低压铸造具有以下特点。
(1)适应性强。由于浇注及凝固时的压力可以人为控制,所以适用 于金属型、砂型、树脂壳型、熔模壳型等铸型。
(1)实现了“一型多铸”。 (2)铸件的精度与表面粗糙度有所改善。 (3)铸件的力学性能高。 (4)金属型铸造的局限性。
三、压力铸造
压力铸造是指液态金属在高压作用下快速充填金属型腔,并在压力下 凝固成铸件的铸造工艺。压力铸造的两大特点是高压和高速充型。
(a)
(b)
(c)
04铸造工程学-特种铸造

6
不限
1.6~50
3.2~100
7~9
7~9
1000
不限
铸件尺寸公差与铸件基本尺寸有关,此外,还和合金种类 铸造方法有关
合金种类铸 黑色金属 铜合金 轻金属合金 造方法
砂型手工造型
砂型及其造型及壳型
11-15
8-10
10-15
8-10
9-13
7-9
金属型铸造
压力铸造
7-9
国内暂无
7-9
6-8
6-8
④劳动条件得到显著改善。
• (2)缺点 ①金属型的制造成本高、生产周期长。 ②铸造工艺要求严格,否则容易出现浇不足、冷隔、裂 纹等铸造缺陷,而灰铸铁件又难以避免白口缺陷。 ③金属型铸件的形状和尺寸还有着一定的限制。 2)金属型铸造适用范围 适用于形状不太复杂的尺寸精度要求较高的中小型铸 件,特别适合铝合金、镁合金件的生产。航空工业上 用于生产有特殊要求的复杂件。
• (3)铸件的强度和硬度都较高。因为铸件的冷却速度快,又 是在压力下结晶,其表层结晶细密,如抗拉强度比砂型铸 造提高25%~30%。 • (4)压铸的生产率较其它铸造方法均高。如我国生产的压铸 机生产能力为50~150次/h。最高可达500次/h。 • 2)缺点 • (1)压铸设备投资大,制造压型费用高、周期长,只有在大 量生产条件下经济上才合算。 • (2)压铸高熔点合金(如铜、钢、铸铁)时,压型寿命很低, 难以适应。 • (3)由于压铸的速度极高,型腔内气体很难排除,厚壁处的 收缩也很难补缩,致使铸件内部常有气孔和缩松。因此, 压铸件不宜进行较大余量的切削加工,以防孔洞的外露。
(3)蜡模组装 熔模铸件一般均较小,为提高生产率、降低成本,通常 将若干个蜡模焊在 一个预先制好的浇口棒上构成蜡模 组,从而可实现一型多铸。 2)型壳制造 它是在蜡模组上涂挂耐火材料,以制成具有一定强度的耐 火型壳的过程。由于型壳的质量对铸件的精度和表面粗糙 度有着决定性的影响,因此结壳是熔模铸造的关键环节。 (1)浸涂料 将蜡模组置于涂料中浸渍,使涂料均匀地覆盖在蜡模 组的表层。涂料是由耐火材料(如石英粉)、粘结剂(如 水玻璃、硅酸乙酯等)组成的糊状混合物。这种涂料
第4讲特种铸造

提高了金属的充填能力,有利于形成轮廓清晰, 表面光洁的铸件; – 铸件组织致密,机械性能高; – 金属收得率高(80%~98%)。
© 2006 金工教研室
机械制造基础
© 2006 金工教研室
机械制造基础
© 2006 金工教研室
机械制造基础
卧式离心铸造机
© 2006 金工教研室
机械制造基础
大型管件
© 2006 金工教研室
机械制造基础
更大的管道
© 2006 金工教研室
机械制造基础
最大重量
达几公斤 到十多吨
离心铸件最大直径可 达3米,最大长度8米
© 2006 金工教研室
机械制造基础
立 式 离 心 铸 造 机
© 2006 金工教研室
© 2006 金工教研室
机械制造基础
金属型铸造
© 2006 金工教研室
机械制造基础
金属型铸造的四种分型方式
© 2006 金工教研室
机械制造基础
金属型铸造的缺点和不足
1. 生产成本高,适合大批量生产 2. 铸件易形成浇不足和开裂等缺陷, 3. 工艺过程参数控制严格 4. 采用金属型生产的铸件重量和形状方面
© 2006 金工教研室
机械制造基础
比较
产量
铸件制造成本(元/件) 砂型 金属型 熔模 压力
100
1.75
6.02
6.25 18.75
1000 0.62 1.23 2.67 1.95
10000 0.33 0.37 1.93 0.50
100000 0.30 0.29 1.80 0.16
© 2006 金工教研室
特种铸造
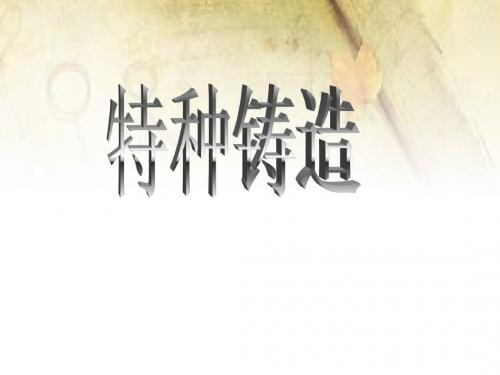
3、压力铸造
• 压力铸造使用的设备是压铸机,由动型、 定型以及压室等组成。可移动的压铸型部 分叫动型。安装在压铸机固定板上且固定 不动的压铸型部分叫定型,其中有浇注系 统与压室相通。压铸型用耐热的合金工具 钢制成,加工质量要求很高,需经严格的 热处理。 (铸造过程)
特点及应用范围
(1)压铸件尺寸精度高,表面质量好,一般不需机 加工即可直接使用。 (2)压力铸造在快速、高压在成型,可压铸出形状 复杂、轮廓清晰的薄壁精密铸件,铝合金铸件最 小壁可达0.5mm,最小壁孔径直径为0.7mm。 (3)铸件组织致密,力学性能好,其强度比沙型铸 件提高25%~40%。 (4)生产率高,劳动条件好。 (5)设备投资大,铸型制造费用高,周期长。
概念:
• 特种铸造是指与砂型铸造不同的其它铸造 方法。 • 常用的特种铸造方法有熔模铸造、金属型 铸造、压力铸造、离心铸造等。
1、熔模铸造
• 熔模铸造是用易熔材料制成模样,然后用 造型材料将其表面包覆,经过硬化后再将 模样熔去,从而制成无分型面的铸型壳, 最后经浇注而获得铸件的方法。 • 由于熔模广泛采用蜡质材料来制造,所以 熔模离心铸造是将液体金属浇入高速旋转的铸 型中,使其在离心力作用下凝固成形的铸 造方法。 • 铸造过程
特点及应用范围:
• (1)铸件在离心力作用下结晶,组织致密,无缩 孔、缩松、气孔、夹渣等缺陷,力学性能好。 • (2)铸造圆形中空铸件时,可省去型芯和浇注系 统,简化了工艺,节约了金属。 • (3)便于制造双金属铸件,如钢套镶铸铜衬。 • (4)离心铸造内表面粗糙,尺寸不易控制,需要 加大加工余量来保证铸件质量,且不适宜易偏析 的合金。
• 熔模铸造的工艺过程:
• 压型 注蜡 • 蜡模组 • 脱蜡、焙烧 • 完成
特种铸造的特点和应用

特种铸造的特点和应用特种铸造是指在普通铸造工艺的基础上,通过改变材料、工艺和设备等方面的参数,以满足特殊要求的铸造工艺。
特种铸造具有独特的特点和广泛的应用。
特种铸造的特点主要体现在以下几个方面:1. 材料选择多样化:特种铸造可以根据不同的要求选择不同的材料,如高温合金、耐腐蚀材料等,以满足特殊工作环境下的使用需求。
2. 工艺参数可调性强:特种铸造可以通过调整工艺参数,如温度、压力、速度等,来控制铸造过程中的凝固组织、缺陷和性能等,以获得符合要求的铸件。
3. 设备要求高:特种铸造通常需要使用特殊的设备和工具,如真空熔炼炉、真空铸造设备等,以保证铸造过程的精确控制和高质量的铸件。
4. 铸件质量高:特种铸造可以通过优化工艺参数和材料选择,使铸件具有优异的性能,如高强度、高耐热、高耐蚀等,以满足特殊工作条件下的使用要求。
特种铸造的应用范围广泛,涉及到多个行业和领域,以下是一些常见的应用领域:1. 航空航天工业:特种铸造在航空航天工业中得到广泛应用,如用于制造发动机叶片、涡轮盘、航空航天结构件等,以满足高温、高压、高速等复杂工作环境下的使用要求。
2. 能源工业:特种铸造在能源工业中的应用很多,如用于制造核电设备的反应堆压力容器、核燃料包壳等,以满足高温、高压、辐射等特殊条件下的使用要求。
3. 化工工业:特种铸造在化工工业中的应用主要是制造耐腐蚀材料的设备和部件,如耐酸泵、耐腐蚀阀门等,以满足复杂的介质和工作环境下的使用要求。
4. 汽车工业:特种铸造在汽车工业中广泛应用于发动机、变速器、悬挂系统等关键部件的制造,以提高汽车的性能和可靠性。
5. 铁路工业:特种铸造在铁路工业中主要应用于制造高速列车的车轮、车架等关键部件,以满足高速、高荷载等特殊工况下的使用要求。
特种铸造的发展对于提高工业生产的技术水平和产品质量具有重要意义。
通过不断改进特种铸造工艺和材料,可以满足各行各业对于高性能、高可靠性铸件的需求,推动相关行业的发展和进步。
铸造工程学-特种铸造
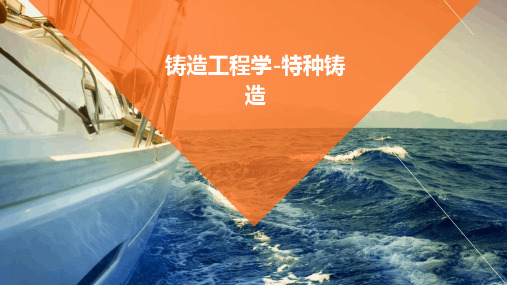
应用先进的传感器和检测技术对铸造过程进行实 时监控和数据采集,为生产优化和质量控制提供 依据。
大数据与人工智能技术
利用大数据分析和人工智能技术对铸造过程进行 优化和控制,实现精益生产和智能化决策。
05 特种铸造质量控制与检测
质量影响因素分析
原材料质量
特种铸造对原材料的成分、纯净度和 组织结构有严格要求,原材料质量直
热处理设备
对铸件进行退火、正火、淬火等热处理,改善其力学性能和加工 性能。
表面处理设备
采用喷涂、电镀、化学处理等方法对铸件表面进行防护和装饰, 提高其耐腐蚀性和美观度。
自动化与智能化技术应用
1 2 3
自动化生产线
实现铸造生产全过程的自动化,包括熔炼、造型、 浇注、清理等工序,提高生产效率和产品质量稳 定性。
低压铸造
01
02
03
定义
低压铸造是在低压气体作 用下,使液态金属由下而 上地充填型腔并凝固成形 的铸造方法。
工艺流程
合模→升液→充型→增压 →保压→卸压→开模取件 。
特点
铸件组织致密,力学性能 高,可铸造大型复杂薄壁 铸件,适用于铝合金等有 色金属的铸造。
离心铸造
定义
离心铸造是将液态金属浇 入旋转的铸型中,在离心 力作用下充填铸型和凝固 成形的铸造方法。
造型与制芯技术
3D打印技术
01
通过逐层堆积材料的方式构建三维模型,可快速制造出复杂形
状的砂型和芯子。
机器人造型
02
利用机器人进行自动造型,提高生产效率和造型精度。
陶瓷型芯制造技术
03
采用陶瓷材料制造型芯,具有高温稳定性、耐磨损等优点,适
用于高精度铸件生产。
特 种 铸 造
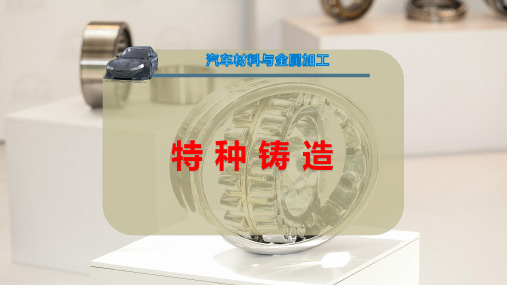
特种铸造
•
为获得高质量、高精度的铸件,提高生产率,人们在砂型铸
造的基础上,创造了多种其它的铸造方法;通常把这些有别于砂型铸
造的其他铸造方法通称为特种铸造。
•
金属型铸造
定义:金属型铸造是指利用金属材料制成铸型,在重力作用下将熔融
金属浇注到铸型中制造铸件的一种铸造方法,也称永久型铸造。
•
特点和应用:
用下充填型腔并凝固成形的铸造方法。
•
特点和应用:
•
1.离心力改善了补缩条件,缩孔等缺陷减少;
•
2.改善金属的流动性,提高了充型能力;
•
3.简化了中空圆柱形铸件的生产过程;
•
4.成分偏析严重,尺寸难以控制;
•
5.特别适于横截面呈圆柱的铸件生产。
•
连续铸造
定义:是指将熔融金属连续不断地浇注到被成为结晶器的特殊容器中,
填型腔并凝固而获得铸件的一种铸造方法。
•
特点和应用:
•
1.充型压力和充型速度易于控制,气孔、夹渣较少;
•
2.铸型散热快,组织致密,机械性能好;
•
3.无需冒口设置,金属利用率高;
•
4.铸件尺寸精度高,表面光洁;
•
5.适于生产质量要求高的铝镁等有色金属铸件。
•
离心铸造
定义:是指将液态金属浇入高速旋转的铸型中,使金属在离心力的作
•
特点和应用:
•
1.浇注时间短,易于机细化,耐磨、耐蚀性好;
•
3.铸件尺寸精度高,表面光洁;
•
4.凝固速度快,排气困难,易形成疏松和缩孔;
•
5.模具成本高,铸件尺寸受限;
•
6.适于有色金属薄壁复杂铸件的大批量生产。
4特种铸造

a) 水平分型式
b) 垂直分型式 金属型的种类
c) 复合分型式
二、金属型的铸造工艺
1、喷刷涂料 、 2、金属型应保持一定的工作温度 、 3、适合的出型时间 、
三、金属型铸造的特点和适用范围
1、优点: 、优点: (1)一型多铸,便于实现机械化和自动化生产,有 )一型多铸,便于实现机械化和自动化生产, 利于提高生产率; 利于提高生产率; (2)铸件精度和表面质量比砂型铸造显著提高; )铸件精度和表面质量比砂型铸造显著提高; (3)结晶组织致密,铸件的力学性能显著提高; )结晶组织致密,铸件的力学性能显著提高; (4)劳动条件显著改善。 )劳动条件显著改善。 2、缺点: 、缺点: (1)金属型制造成本高、生产周期长; )金属型制造成本高、生产周期长; (2)铸造工艺要求严格,易出现浇不足、冷隔、裂 )铸造工艺要求严格,易出现浇不足、冷隔、 纹等铸造缺陷; 纹等铸造缺陷; (3)金属型铸件的形状和尺寸有一定限制。 )金属型铸件的形状和尺寸有一定限制。 3、使用范围:铜、铝合金不复杂铸件的大批量生产, 铝合金不复杂铸件的大批量生产, 、使用范围: 如铝活塞、气缸盖、油泵壳体、铜瓦、 如铝活塞、气缸盖、油泵壳体、铜瓦、衬套
1、优点: 、优点: (1)铸件精度和表面质量较其它铸造方法均高; )铸件精度和表面质量较其它铸造方法均高; (2)可压铸形状复杂的薄壁件,或直接铸出小孔、螺纹、齿轮 )可压铸形状复杂的薄壁件,或直接铸出小孔、螺纹、 等; (3)铸件的强度和硬度都较高; )铸件的强度和硬度都较高; (4)压铸的生产率较其它铸造方法均高。 )压铸的生产率较其它铸造方法均高。 (5)便于采用镶铸(镶嵌法) )便于采用镶铸(镶嵌法) 2、缺点: 、缺点: (1)压铸设备投资大,制造压型费用高、周期长,用于大批量 )压铸设备投资大,制造压型费用高、周期长, 生产; 生产; (2)压铸高熔点合金时,压型寿命很低; )压铸高熔点合金时,压型寿命很低; (3)由于压铸速度高,铸件内部易产生气孔和缩松; )由于压铸速度高,铸件内部易产生气孔和缩松; (4)压铸件不能用热处理方法来提高性能。 )压铸件不能用热处理方法来提高性能。 3、应用:铝、镁、锌合金铸件生产,如汽缸体、箱体、喇叭外 锌合金铸件生产,如汽缸体、箱体、 、应用: 化油器等。 壳、化油器等。
特种铸造的特点和应用

特种铸造的特点和应用
特种铸造是指用于生产特定形状、特定材料和特定性能的铸件的一种铸造方法。
它与普通铸造相比,具有以下特点:
1. 高精度:特种铸造可以实现精确的铸造尺寸和形状,确保铸件的准确性和一致性。
2. 材料性能优异:特种铸造可以选择特殊的合金材料,以满足特定的工程要求,如高强度、高耐热、高耐腐蚀等。
3. 复杂结构:特种铸造可以实现复杂的内部结构和形状,如薄壁铸件、空腔结构、内部通道等,以满足特定的功能需求。
4. 原型快速制造:特种铸造可以用于快速制造原型铸件,以便于产品开发和设计验证。
特种铸造在各个领域有着广泛的应用,主要包括以下几个方面:
1. 航空航天领域:特种铸造可用于生产航空发动机、航天器零部件等高性能铸件,满足航空航天行业对材料性能和复杂结构的要求。
2. 石油化工领域:特种铸造可用于生产石油化工设备的耐腐蚀铸件、高温耐热铸件,如阀门、泵体、换热器等。
3. 汽车工业:特种铸造可用于生产发动机缸盖、曲轴、刹车卡钳等汽车零部件,以提高汽车的性能和安全性。
4. 电力工业:特种铸造可用于生产电力设备的零部件,如涡轮叶片、导叶、涡轮壳体等。
5. 医疗器械领域:特种铸造可用于生产医疗器械的复杂零部件,如人工关节、牙科植入物等,满足医疗器械对材料生物相容性和结构形状的要求。
总之,特种铸造在各个领域都发挥着不可替代的作用,为实现复杂结构和高性能的铸件提供了有效的解决方案。
第四章 特种铸造

金属型铸造的特点
可承受多次浇注,便于实现机械化生产
铸件精度和表面质量高(铝合金铸件的尺寸公 差等级可达IT7~IT9,表面粗糙度可达Ra3.2~12. 5um) 铸件的结晶组织致密,机械性能高
金属型成本高,生产周期长
铸造工艺严格, 易出现浇不足、冷隔、裂纹 铸件的形状和尺寸受一定的限制
组合金属型结构
金属型和砂型,在性能上有显著的区别
1.透气性差 2.导热性好 3.没有退让性 金属型的这些特点决定了它在铸件形成过程中有自 己的规律。
金属型铸造工艺
金属型的预热(预热温度一般不低于150°C)
金属型导热性好/液体金属冷却快,铸件易出现 冷隔、浇不足、气孔等缺陷。同时保护铸型。
也称气化模铸造,国际上称EPC工艺。 真空实型铸造, 用泡沫模型代替金属或木模,造 型后模样不取出,呈实体型腔,浇注时模样气化消失而 得到铸件。
预发泡
模型成型
模型簇组合
浸涂
浇注
消失模铸造的工艺过程
► (1)制造泡沫塑料模
►
a.制备消失模材料 需经预发泡—将珠粒密度 大(1.05g/cm3)的原材料及发泡剂,经过 蒸汽加热、抽真空,获得符合要求的低密度 珠粒、残留发泡剂含量及适当粒度的珠粒的 处理过程。(主要的消失模材料有:可发性 聚苯乙烯(EPS),适用于灰铸铁、球墨铸 铁和有色合金铸件等;可发性聚甲基丙烯甲 酯(EPMMA),适用于球墨铸铁和铸钢件等。 这类泡沫塑料的特点:密度小 (0.015~0.025g/cm3),发气量小、导热 系数小、产生气体及残留物少、资源丰富、
4.可以制造各种合金材质的铸件,尤其适用于高熔点、难切削合金 的小型复杂铸件的生产
金属型铸造
又称硬模铸造,将液体金属浇入金属铸型,获得 铸件的一种铸造方法。铸型是用金属制成,可以反复 使用多次。金属型的结构有多种形式,(a)是水平 分型式金属型,多用于生产薄壁轮状铸件;(b)为 垂直分型式金属型,广泛应用于复杂铝合金铸件。
特种铸造

1 . 基本工艺过程 请看影片
31
32
2 . 特点及应用范围 优点: ⑴陶瓷型高温时变形小,铸件尺寸精度和表 面粗糙度与熔模铸造相似。 ⑵陶瓷材料耐高温,故也可浇注高熔点合金。 ⑶陶瓷型铸件的尺寸几乎不受限制,如铸件 重量可从几千克到数吨。 ⑷在单件、小批生产条件下,需要的投资少、 生产周期短,在一般铸造车间较易实现。
14 -2
二 . 特点和范围 特点: (1)铸件的尺寸精度高,表面粗糙度值小。 (IT11----13、Ra6.3---1.6) (2)可压铸出形状复杂的薄壁件和镶嵌件。
(3)铸件的强度和硬度较高。 (4)压铸的生产率比其它铸造方式都高。 一般为50----150次/小时,最高达500次/小时。
21
低压铸造的 组成
22
23
24
§5 离心铸造 离心铸造---将液态合金浇入高速旋转的铸型 中,使液态合金在离心力作用下填充铸型并 凝固的铸造方法。 一 .离心铸造的基本方式 离心铸造是在离心铸造机上进行的,按旋转 轴的位置分为:立式和卧式。 基本原理:
25
26
27
28
二.特点和 适用范围 优点: (1)不用设置浇注系统和型芯。 (2)铸件组织致密,缺陷少。 (3)合金充型能力强,便于生产流动性差及 薄壁件。 (4)便于生产双金属铸件。如:
铸铝活塞
6
铸型的种类:按分型面的方位分为整 体式、垂直分型式、 水平分型式、和 复合式。 铸型材料:一般多数用铸铁或铸钢 。 型芯材料:组合芯采用钢材,其它芯 有的用钢,有的用砂芯。 合箱、开箱方式:自动或半自动的连 杆机构
7
二 . 铸造工艺
1. 喷刷涂料: (1)减缓铸件的冷却速度; (2)防止高温金属液对型壁的直接冲刷。 (3)利用涂料有一定的蓄气、排气能力, 防止气孔。 2 .使金属铸型保持一定的温度; 3 . 适合的出型时间; 4 . 防止铸铁件产生白口;
特种铸造介绍范文

特种铸造介绍范文特种铸造是一种高技术含量的铸造工艺,在工业领域中起到了至关重要的作用。
它是一种通过将金属或其他材料熔化后,借助于铸型,将熔化后的材料注入到铸型中,然后通过冷却固化的过程,使其成型的工艺过程。
特种铸造在实际应用中有很广泛的应用范围,如航空航天、汽车、石油化工、冶金、能源等行业,对于提高产品质量、延长使用寿命、降低生产成本等方面起到了重要作用。
首先,特种铸造采用了先进的材料,如高温合金、高强度合金等。
这些材料在一般的铸造工艺中很难实现。
而特种铸造可以通过精细的工艺参数控制,使复杂形状的零部件得以实现。
例如,航空发动机叶片、燃烧室壁板等复杂结构的零部件,利用特种铸造可以实现高质量的生产。
其次,特种铸造具有高精度、高一致性的特点。
在特种铸造过程中,可以通过控制浇注温度、流量、浇注速度等参数,使得产品的尺寸精度得到保证。
同时,特种铸造还可以减少焊接、组装等工序,提高零部件的一致性和性能稳定性。
另外,特种铸造还能够实现零废料生产,节约资源。
在传统的铸造工艺中,往往需要进行大量的修理、修整工序,产生大量的废料。
而特种铸造可以在铸造过程中实现高效率的铸造,减少修整工艺,降低废料的产生。
此外,特种铸造还可以实现大规模、快速生产的需求。
通过合理的设计和工艺参数的控制,可以实现高效率的铸造生产。
这对于一些大规模生产的行业来说,具有重要的意义。
例如,汽车发动机缸体、汽车轮毂等产品,利用特种铸造工艺可以实现高效率、高一致性的生产。
综上所述,特种铸造在现代工业中具有重要的应用价值。
它不仅可以实现高精度、复杂形状零部件的生产,还可以减少废料的产生,提高产品的一致性和性能稳定性。
随着科技的不断发展和进步,特种铸造会在未来的工业生产中发挥更加重要的作用。
特种铸造及应用范围

特种铸造及应用范围特种铸造是指应用特殊材料、特殊工艺或特殊设备进行铸造生产的铸造方法。
由于特种铸造具有广泛的应用范围和独特的技术特点,因此在诸多领域中得到了广泛的应用。
首先,特种铸造在航空航天领域中具有重要的地位。
在航空航天工业中,要求零部件具有较高的强度、耐高温、耐腐蚀等特殊性能。
特种铸造技术能够满足这些要求,因此在航空航天领域内被广泛应用。
例如,特种铸造技术可以用于生产发动机叶片、涡轮盘等高温部件,以及飞机舵面等结构部件。
其次,特种铸造在能源领域也起着重要的作用。
特种铸造技术可以用于生产核电站中的核燃料座和反应堆压力容器等部件。
同时,在风力发电领域,特种铸造技术可以用于生产大型风力发电机组轮毂、风叶等关键零部件。
此外,特种铸造还可以应用于石油装备制造,例如石油钻井平台和海底油气管道等部件的生产。
另外,在汽车制造领域,特种铸造也得到了广泛应用。
汽车发动机中的缸体、曲轴等关键零部件,以及车轮、差速器壳体等结构部件,都可以通过特种铸造技术进行生产。
特种铸造技术不仅可以提高零部件的强度和耐磨性,还可以实现零部件的轻量化设计,提高整车的燃油经济性。
此外,特种铸造还在军事工业中发挥着重要作用。
军事装备对零部件的要求通常较高,需要具备较高的强度、耐磨性、耐腐蚀性等特殊性能。
特种铸造技术可以满足这些要求,因此在军事装备制造中得到了广泛应用。
例如,特种铸造技术可以用于生产坦克炮塔、弹头、导弹外壳等关键零部件。
最后,特种铸造还在工程机械领域中得到了广泛应用。
工程机械常常需要承受较大的载荷和振动,因此需要具备较高的强度和韧性。
特种铸造技术可以通过合金配方的优化和特殊工艺的应用,提供高强度、高韧性的零件。
例如,特种铸造技术可以用于生产挖掘机的斗齿、履带链轮等耐磨零部件,以及起重机的滚筒、起重机钩等承载零部件。
综上所述,特种铸造具有广泛的应用范围。
在航空航天、能源、汽车制造、军事工业和工程机械等领域中,特种铸造技术都发挥着重要的作用。
特种铸造

成形工艺基础
13
§3金属型铸造
又称:永久型铸造 在重力作用下将熔融金属 浇入金属型而获得铸件的方法。 特点和适用范围:
1.生产率高 金属型可“一型多铸”,易于实 现机械化和自动化生产。 2.铸件精度和表面质量高,加工余量减小。
3.铸件力学性能好,因冷却快,故组织致密。
成形工艺基础 14
4.劳动条件好,减少了硅尘危害和环境污染.
成形工艺基础 8
压力铸造
回到主页
镶嵌件的应用
成形工艺基础 9
回到主页
压力铸造
成形工艺基础
10
5.压铸机费用高,压铸模具制造成本高,工 艺准备周期长,不适用单件小批量生产。
6. 压铸件不宜热处理,并尽量避免切削加 工 。(为什么?)
答:由于压铸的金属液注入和凝固速度过快, 型腔气体难以及时完全排出,壁厚处难以进行补 缩,故铸件内部易存有气孔、缩孔和缩松等铸造 缺陷。 所以,不宜热处理。
成形工艺基础 17
5.不适合比重偏析大的合金及铝、镁等金属.
离心铸造适用于大批量生产管、筒类铸件, 如铁管、筒套、缸套、双金属钢背铜套,轮盘类 铸件,如泵轮、电机转子等。
成形工艺基础
18
离心铸造
回到主页
立式
卧式
成形工艺基础
19
离心铸造
回到主页
特点: •制造筒形件时省去型芯,浇注系统;
•适用于生产薄壁件;
成形工艺基础
22
§6 磁型铸造
磁型铸造
回到主页
成形工艺基础
23
第四章 铸造
磁型铸造
基本工艺过程 磁 丸
回到主页
造 型
激磁、浇注
落丸
气化模
成形工艺基础
- 1、下载文档前请自行甄别文档内容的完整性,平台不提供额外的编辑、内容补充、找答案等附加服务。
- 2、"仅部分预览"的文档,不可在线预览部分如存在完整性等问题,可反馈申请退款(可完整预览的文档不适用该条件!)。
- 3、如文档侵犯您的权益,请联系客服反馈,我们会尽快为您处理(人工客服工作时间:9:00-18:30)。
成形工艺基础
2
3.铸件合金种类不受限制,钢、铸铁和有 色合金均可。
4.生产工序复杂,生产周期长。
5.原材料价格贵,铸件成本高。
6.铸件不能太大、太长,否则蜡模易变形。
熔模铸造是一种少无切削的先进的精密铸造工艺。
它最适合25kg以下的高熔点、难以切削成形的合
金铸件的大批量生产。广泛应用于航天、
成形工艺基础
成形工艺基础
17
5.不适合比重偏析大的合金及铝、镁等金属.
离心铸造适用于大批量生产管、筒类铸件, 如铁管、筒套、缸套、双金属钢背铜套,轮盘类 铸件,如泵轮、电机转子等。
成形工艺基础
18
离心铸造
立式
成形工艺基础
回到主页
卧式
19
离心铸造
回到主页
特点: •制造筒形件时省去型芯,浇注系统; •适用于生产薄壁件; •可以生产双金属铸件; •容易产生比重偏析缺陷,内表面粗糙
5.金属型透气差、无退让性、铸件冷却快, 易生缺陷。
用于大批量生产铝合金活塞、气缸体、铜合 金轴瓦,及铁合金铸件等。
工艺措施:
•喷刷涂料 •保证合适的工作温度 •严控开型时间 •防止产生白口铸铁
成形工艺基础
15
§4离心铸造
将金属液浇入绕水平、倾斜或立轴旋转的铸型, 在离心作用下凝固成铸件的铸造方法。
成形工艺基础
卧式
16
特点与应用:
1.生产空心旋转铸件时,可以省去型芯、浇 注系统和冒口。
2.补缩条件好,使铸件致密,力学性能好(?)
在离心力作用下,密度大的金属液被推往外 壁。而密度小的气体、熔渣向自由表面移动,形 成自外向内的顺序凝固。
3.便于浇注“双金属轴套和轴瓦”。
4.铸件内表面粗糙,尺寸误差大,质量差。
成形工艺基础
第4章 特种铸造
1
§1熔模铸造
熔模铸造又称失蜡铸造,用易熔材料如蜡料 制成模样,在模样上包覆若干层耐火涂料,制成型 壳,熔出模样后经高温焙烧即可浇注的铸造方法.
特点与应用:
1.铸件的精度高,表面粗糙度低(IT12~10、 Ra12.5~1.6μm)
2.可铸出形状复杂的薄壁铸件,如铸件上的 凹槽(宽>3mm),小孔( >2.5mm)均可直接铸出。
3
飞机、汽轮机、燃汽轮机叶片、泵轮、复杂刀 具、汽车、拖拉机和机床上的小型铸件生产。
没有分型面
成形工艺基础
4
熔模铸造
生产工艺过程
生产工艺过程
蜡模制造 结壳 脱蜡 焙烧、造型和浇注
压型
浸涂料
耐火材料
热水法 加热800~1000°C
高压粘蒸结汽剂法
焙烧
蜡模压制 撒砂 蜡模组装 硬化
化学硬化 干燥处理
成形工艺基础
11
低压铸造
❖ 特点:
(1)充型平稳;
(2)压力和充型速度可调;
(3)浇注系统简单、金属 利用率高;
(4)铸件轮廓清晰,机械 性能较高;
(5)生产率高,劳动条件 好。
成形工艺基础
12
低压铸造
回到主页
特点: •充型压力和速度便于控制,适用于各种铸型; •力学性能好; •金属利用率高,可达90~98%,; •充型能力强,适用大型薄壁件; •容易实现;
成形工艺基础
20
陶瓷型铸造
砂套造型 灌浆与胶结 起模与喷烧 焙烧与合箱
§5陶瓷型铸造
基本工艺过程
成形工艺基础
回到主页
21
陶瓷型铸造
回到主页
特点: •精度高,适合高熔点合金; •铸件大小不受限制,可以从几十千克到数吨; •投资少,周期短; •不适合于大批量、重量轻或形状复杂铸件。
成形工艺基础
22
磁型铸造
成形工艺基础
8
压力铸造
回到主页
镶嵌件的应用
成形工艺基础
9
压力铸造
成形工艺基础
回到主页
10
5.压铸机费用高,压铸模具制造成本高,工 艺准备周期长,不适用单件小批量生产。
6. 压铸件不宜热处理,并尽量避免切削加 工 。(为什么?)
答:由于压铸的金属液注入和凝固速度过快, 型腔气体难以及时完全排出,壁厚处难以进行补 缩,故铸件内部易存有气孔、缩孔和缩松等铸造 缺陷。 所以,不宜热处理。
成形工艺基础
13
§3金属型铸造
又称:永久型铸造 在重力作用下将熔融金属 浇入金属型而获得铸件的方法。 特点和适用范围:
1.生产率高 金属型可“一型多铸”,易于实 现机械化和自动化生产。
2.铸件精度和表面质量高,加工余量减小。 3.铸件力学性能好,因冷却快,故组织致密。
成形工艺基础
14
4.劳动条件好,减少了硅尘危害和环境污染.
600~700°C 浇注
成形工艺基础
落砂和清理
打碎型壳 落砂
去浇口、毛刺 清理
5
§2压力铸造
简称压铸:熔融金属在高压下高速充型,并 在压力下凝固的铸造方法。
1. 压铸的压力(压射比压)可达 30~70MPa(300~700大气 压)
2. 充型速度可达5~100m/s 3. 充型时间为0.05~0.2s,最
短时间只有千分之几秒。
高压、高速是压铸的两大特点
成形工艺基础
6
成形工艺基础
7
特点与应用:
1.生产效率高,便于实现自动或半自动化。
2.铸件的精度高,表面粗糙度低。
3.铸件高压高速下结晶,故晶粒细小,表层 紧实,铸件的强度、硬度高。
4.便于采用嵌铸,又称镶铸法
嵌铸是将各种金属或非金属的零件嵌放在压 铸型中,在压铸时与压铸件铸合成一体。
§6 磁型铸造
回到主页
成形工艺基础
23
磁型铸造
基本工艺过程 磁丸
造型
激磁、浇注
气化模
成形工艺基础
金属熔化Βιβλιοθήκη 回到主页落丸 铸件
24
磁型铸造
成形工艺基础
回到主页
特点: •设备简单,无污染; •造型、清理方便; •不需要起模,精度高。
25