ANSYS_Workbench_电磁场分析例子
ansys workbench电磁场仿真完整例子
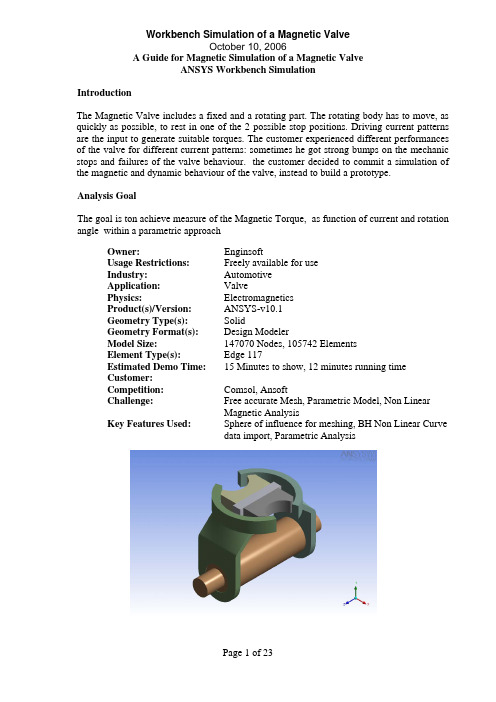
IntroductionThe Magnetic Valve includes a fixed and a rotating part. The rotating body has to move, as quickly as possible, to rest in one of the 2 possible stop positions. Driving current patterns are the input to generate suitable torques. The customer experienced different performances of the valve for different current patterns: sometimes he got strong bumps on the mechanic stops and failures of the valve behaviour. the customer decided to commit a simulation of the magnetic and dynamic behaviour of the valve, instead to build a prototype.Analysis GoalThe goal is ton achieve measure of the Magnetic Torque, as function of current and rotation angle within a parametric approachOwner:EnginsoftUsage Restrictions:Freely available for useIndustry:AutomotiveApplication:ValvePhysics:ElectromagneticsProduct(s)/Version:ANSYS-v10.1Geometry Type(s):SolidGeometry Format(s): Design ModelerModel Size:147070 Nodes, 105742 ElementsElement Type(s): Edge 117Estimated Demo Time:15 Minutes to show, 12 minutes running timeCustomer:Competition:Comsol,AnsoftChallenge:Free accurate Mesh, Parametric Model, Non LinearMagnetic AnalysisKey Features Used:Sphere of influence for meshing, BH Non Linear Curvedata import, Parametric AnalysisSteps and Points to Convey.Picture Guide.Start ANSYS Workbench Environment, and choose “New Geometry”.Importing of external geometrySet the desired length unit: meters.01) Click “File > Open > Import External Geometry File”.02) Click on “Generate” in order to confirm the importation of the geometry.The geometry regards a magnetic valve.Steps and Points to Convey.Picture Guide.Create a Parametric, Relative Rotation between two groups of bodies01) Create a local coordinate system (plane 4) by clicking on the “New Plane” icon in the tool bar.02) In “Details of Plane4 >. Type” choose from face in order to select the surface of interest. 03) Choose the space to the right of “Base Face” in Details of Plane4 and select the surface indicated in light blue in the plot at right.The local coordinate system “Plane 4” is now visible, centered on a face vertex04) In “Details of Plane4 >. Transform 1 (RMB)” insert an offset along X axis of –0.00825 m.05) In “Details of Plane4 >. Transform 1 (RMB)” insert an offset along Y axis of 0.0015 m.06) Click Generate to create Plane4Create another plane (Plane5).07) In “Details of Plane5 > Type” choose from plane. Base plane should be set to Plane4.08) In “Details of Plane5 >. Transform 1 (RMB)” insert a rotation about Z axis of 30°. 09) Click Generate to create Plane5.Steps and Points to Convey. Picture Guide.The local coordinate system “Plane 5” is now visible.10) From the tool bar menu, select “Tools > Freeze”.The freezing operation is indicated when bodies are displayed with transparency.11) From the tool bar menu, select “Create > Body Operation” set “Type” to “Move” click on the box to the right of Bodies.12) Select the bodies highlighted at right (use the Ctrl button to select multiple entities) and click Apply.Steps and Points to Convey.Picture Guide.13) In “Details of BodyOp1” choose the box to the right of “Source Plane” and pick on Plane4 in the Tree Outline.14) In a similar fashion, set “Destination Plane” to Plane5.Then click on “Generate” to move the parts as shown at right.ENCLOSURE definition01) From the tool bar menu, select “Tools >Enclosure” in order to insert a control volume cylindrically shaped and aligned to Y axis. Set the Cushion to 0.0375 m and set “Merge Parts?” to “Yes”.02) Click Generate to create the enclosureIn the “Outline” tree the just created enclosure is now visible.Steps and Points to Convey Picture GuideEnclosure is visible in the “Model View”window.CREATE the WINDING COIL01) In the Tree Outline, Open “1 Part, 7 Bodies > Part”. RMB on the last Solid in the list and choose “Hide Body” in the drop down menu. This will allow access to the surfaces of the imported geometry for forthcoming picking operations.02) Create a new plane (Plane6)03) In “Details of Plane6 >. Type” choose “From Face”.04) Click on the box to the right of “Base Face” and select the surface shown at right.05) In “Details of Plane6 >. Transform 1 (RMB)” insert an offset along Z axis of –0.0231 m.Click on Generate to create Plane6.06) With Plane6 now active, go to the tool bar and choose “New Sketch”.07) Select “Sketch1” in the “Tree Outline”.Steps and Points to Convey Picture Guide Sketching mode for winding coil generation08) Pick the Sketching tab at the bottom of theTree Outline09) Select “Circle” in the “Draw” window andchoose the center (origin of Plane6) and anarbitrary poin some distance away from thecenter to create a circle.10) Pick the Dimensions button at the bottom ofthe Sketching Toolboxes pane and choose“Radius”.11) Click on the circle and another arbitrarylocation for the radial dimension marker.12) In “Details of Sketch1”, modify the radiusR1 to be 0.00775 m.The sketch is now visible in the “Graphics”window.13) From the tool bar select “Concept > LineFrom Sketches”. Choose the circle and clickApply in the box to the right of “Base Objects”in “Details of Line1”. “Operation” should be setto “Add Material”.Click Generate.14) Choose the Line Body in the Tree Outline.15) In “Details of Line Body” set:•“Winding Body > Yes”•“Number of Turns” = 1•“CS Length” = 0.022 m•“CS Length” = 0.00375 mSteps and Points to ConveyPicture Guide16) From the tool bar, select “View > Show Cross Sections Solids”. The new winding body should appear as it does in the figure to the right.ANGLE as PARAMETER01) In the “Tree Outline” select “Plane5”02) Make the rotation about Z axis as parameter by clicking on the box to the left of “FD1, Value 1”.03) Rename the parameter as “angle”.Steps and Points to Convey.Picture Guide.04) From the tool bar, select “Tools > Options>Common Settings>Geometry Import”. Remove “DS” from the field to the right of “Personal Parameter Key” to remove the DS prefix naming convention restriction for importing parameters. Click OK.GO IN SIMULATIONIn the “[Project]” window, select “New Simulation”.In the “[Simulation]” window, the “Outline” tree should be as in figure.Steps and Points to ConveyPicture GuideMaterials Properties DefinitionSelect “Data” in the tool bar to open the “[Engineering Data]” window.Materials Properties Definitionchange defaults of STRUCTURAL STEEL01) Select “Structural Steel” and click on “Add/Remove Properties” in the “Electromagnetics” field and unselect the following items:- “Relative Permeability” - “Resistivity”02) Check the box to the left of “B-H curve” and click OK.03) Say “Yes” to the “Remove Material Properties” box that appears.04) Open excel file “bh1.xls” and copy the two data columns (highlight them with the mouse cursor and type Cntl-C).Steps and Points to ConveyPicture Guide05) Click the icon depicting an xy plot to the right of “B-H Curve”06) LMB on the 2 (second row) of the “Magnetic Flux Density vs. Magnetic Field Intensity” table and press “Ctrl +V” to paste the two column data from the .xls file.07) Click on the B-H Curve icon at the lower right.The curve should appear as shown at right.NEW Material definition IRONRMB on “Materials (2)” in the tree and choose “Insert New Material”. RMB on “New Material”, choose Rename and change the name of the new material to Iron. Define BH data as before but this time use data from “bh2.xls” file.NEW Material definition NEODYMIUM01) Define a New material named “Neodymium”.02) Among Electromagnetics properties let active just: “Linear Hard Material”: 03) Insert the following data:• Cohercive Force: 7.9577 e5 A/m • Residual Induction 1.2 T01) Return to the Simulation Tab02) In the Outline Tree, open Geometry>Part and use the Cntl button to select both of the RIC9512_105 items. The parts should be highlighted as shown at right.03) In Details of “Multiple Selection”, changematerial from “Structural Steel” to “Iron”Steps and Points to ConveyPicture Guide04) Select the part shown at right.05) Change material from “Structural Steel” to “Neodymium”MESH01) Select the coil support solid (see figure)02) RMB on “Mesh” on the tree to insert a sizing control: Element Size 2e-303) Insert another sizing control , 1e-3, referred to 5 bodies as in the following picture. It may help to hide the 4th solid (the “air enclosure) in the Outline tree to simplify selecting these parts.Steps and Points to ConveyPicture Guide5 bodies for sizing setting n.204) In the Outline tree, RMB on Model and insert a “Coordinate Systems” branch. RMB on the Coordinate Systems branch and insert (define) a new Coordinate System. Choose “Origin” in the Details of “Coordinate System” pane, select the surface shown at right, and click Apply.05) RMB on Mesh in the Outline to insert a third sizing control:For “Type”, choose “Sphere of Influence”• Sphere Center: Coordinate System (defined just before) • Radius 1.5e-2 • Element size 5e-4Areas to be applied are the following (10 areas)Steps and Points to ConveyPicture Guide10 Areas where to apply the Sphere of Influence sizing control06) Click on Mesh -> Preview MeshThe Mesh should result as in figure, if the “Air” solid enclosure body is hideLOADSSet the Conductor Current value in details window related to “Conductor Winding Body”: 1000 ABOUNDARY CONDITIONSRMB on Environment in the tree and insert a Magnetic Flux Parallel object. Use the Cntl button to select the 3 exterior surfaces of the enclosure and click Apply.Steps and Points to Convey.Picture Guide.POSTPROCESSING SETTINGS01) Insert under the “Solution” tree the following output requests: • Total Flux Density • Total Flux Intensity 02) Select 3 bodies as in figure03) Insert a “Directional Force/Torque” output request with details:• In Details of “Directional Force/Torque” pane, change “Global Coordinate System” to “Coordinate System” (this is the user-defined coordinate system centered on the top surface of the permanent magnet).• Set Orientation to Y Direction (rotation axis)04) repeat Directional Force/Torque Request for both X and Z axis direction05) By a right click under the Solution Tree Insert a “Solution Information” request to monitor the run during the solutionSOLVE01) Highlight the Environment tree tosee/check all Boundary & Loads previously defined.02) Click on the “SOLVE” Icon to launchthe run.Solution times takes about 12 minutes on a 2.8 Ghz single processor 32bit PCSteps and Points to ConveyPicture GuideREVIEW RESULTS01) See the Total Flux of Magnetic results 02) Set up a Vector Image of the MagneticField03) After Vector Image settings show a Vector Plot of Magnetic Field03)See the Magnetic Force distribution, Yaxis direction, on the requested parts. 04)The same for X, Z directions05)Activate the view from Y Global Axis06)Define a “Slice Plane”07)Draw the slice plane trace at nearlyalong the Y global direction08)View from the X Global direction09)Activate “show elements” and show themagnetic fieldSteps and Points to Convey Picture GuideSET UP A PARAMETRIC ANALYSIS01) Click on “Model”02) Click on CAD Parameters Detail toactivate the “angle” as a parameter. Thiswill be the first INPUT parameter.03) Click on Environment and Duplicate byright click04) Activate the Conductor Current Value asparameter. This is the second INPUTparameter n.2.05) Activate the Torque value in Y directionas OUTPUT parameter (ThirdParameter)06)Click on “Solution” of Environment 2and then click on Parameter Manager 07)Set up many cases as you like, forexample with 4 current values, 3 values other than the previously solved.。
ANSYSWorkbench电磁场分析例子共38页
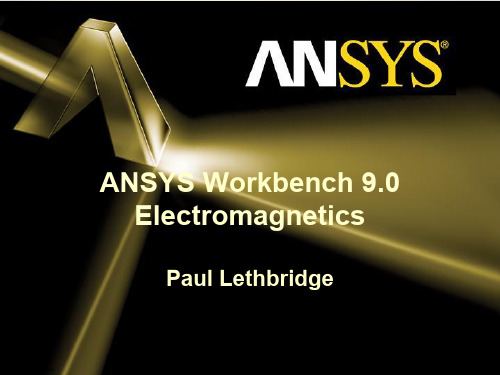
ANSYS, Inc. Proprietary
Contents
Workbench Electromagnetics
– Workbench Emag Roadmap
– Design Modeler
• Enclosure Symmetry • Winding bodies • Winding Tool
• Workbench v9.0 is the first release with electromagnetic analysis capability. – Support solid and stranded (wound) conductors – Automated computations of force, torque, inductance, and coil flux linkage. – Easily set up simulations to compute results as a function of current, stroke, or rotor angle.
– Up to 3 three symmetry planes can be specified. – Full or partial models can be included in the Enclosure. – During the model transfer from DesignModeler to Simulation, the enclosure feature with symmetry planes forms two kinds of named selections:
– Winding Bodies: Used to represent wound coils for source excitation. The advantage of these bodies is that they are not 3D CAD objects, and hence simplify modeling/meshing of winding structures.
ANSYSWorkbench电磁场分析例子
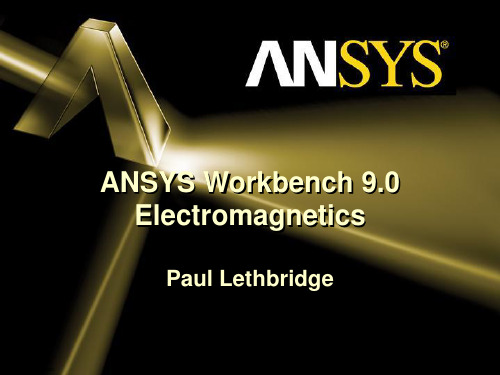
© 2004 ANSYS, Inc.
ANSYS, Inc. Proprietary
Winding Options - Skew
– Simulation
© 2004 ANSYS, Inc.
ANSYS, Inc. Proprietary
Winding Bodies & Tool
• Feature: Design Modeler (DM) includes two new tools to allow a user to easily create current carrying coils:
– Winding Bodies: Used to represent wound coils for source excitation. The advantage of these bodies is that they are not 3D CAD objects, and hence simplify modeling/meshing of winding structures.
Winding cross-section displayed
© 2004 ANSYS, Inc.
A line body can be promoted to a winding body. Turns and cross-section (CS) dimensions are entered
ANSYS, Inc. Proprietary
– Upon “attach to Simulation”, Winding Bodies are assigned as Conductor bodies.
ansysworkbench电磁场仿真完整例子
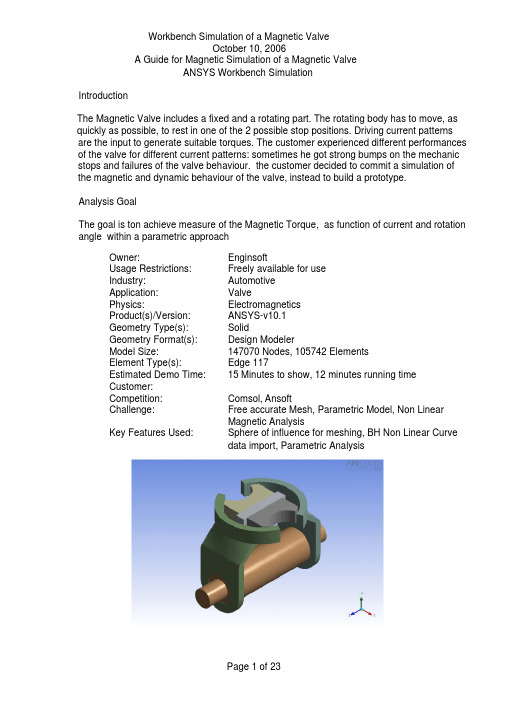
IntroductionThe Magnetic Valve includes a fixed and a rotating part. The rotating body has to move, as quickly as possible, to rest in one of the 2 possible stop positions. Driving current patterns are the input to generate suitable torques. The customer experienced different performances of the valve for different current patterns: sometimes he got strong bumps on the mechanic stops and failures of the valve behaviour. the customer decided to commit a simulation of the magnetic and dynamic behaviour of the valve, instead to build a prototype.Analysis GoalThe goal is ton achieve measure of the Magnetic Torque, as function of current and rotation angle within a parametric approachOwner:EnginsoftUsage Restrictions:Freely available for useIndustry:AutomotiveApplication:ValvePhysics:ElectromagneticsProduct(s)/Version:ANSYS-v10.1Geometry Type(s):SolidGeometry Format(s): Design ModelerModel Size:147070 Nodes, 105742 ElementsElement Type(s): Edge 117Estimated Demo Time:15 Minutes to show, 12 minutes running timeCustomer:Competition:Comsol, AnsoftChallenge:Free accurate Mesh, Parametric Model, Non LinearMagnetic AnalysisKey Features Used:Sphere of influence for meshing, BH Non Linear Curvedata import, Parametric AnalysisSteps and Points to Convey. Picture Guide. Start ANSYS Workbench Environment, andchoose “New Geometry”.Importing of external geometrySet the desired length unit: meters.01) Click “File > Open > Import ExternalGeometry File”.02) Click on “Generate” in order to confirm theimportation of the geometry.The geometry regards a magnetic valve.Steps and Points to Convey. Picture Guide. Create a Parametric, Relative Rotationbetween two groups of bodies01) Create a local coordinate system (plane 4)by clicking on the “New Plane” icon in the toolbar.02) In “Details of Plane4 >. Type” choose fromface in order to select the surface of interest.03) Choose the space to the right of “Base Face” in Details of Plane4 and select the surfaceindicated in light blue in the plot at right.The local coordinate system “Plane 4” is nowvisible, centered on a face vertex04) In “Details of Plane4 >. Transform 1(RMB)” insert an offset along X axis of –0.00825 m.05) In “Details of Plane4 >. Transform 1(RMB)” insert an offset along Y axis of 0.0015m.06) Click Generate to create Plane4Create another plane (Plane5).07) In “Details of Plane5 > Type” choose fromplane. Base plane should be set to Plane4.08) In “Details of Plane5 >. Transform 1(RMB)” insert a rotation about Z axis of 30°.09) Click Generate to create Plane5.Steps and Points to Convey. Picture Guide. The local coordinate system “Plane 5” is nowvisible.10) From the tool bar menu, select “Tools >Freeze”.The freezing operation is indicated when bodiesare displayed with transparency.11) From the tool bar menu, select “Create >Body Operation” set “Type” to “Move” click onthe box to the right of Bodies.12) Select the bodies highlighted at right (usethe Ctrl button to select multiple entities) andclick Apply.Steps and Points to Convey. Picture Guide.13) In “Details of BodyOp1” choose the box tothe right of “Source Plane” and pick on Plane4in the Tree Outline.14) In a similar fashion, set “Destination Plane” to Plane5.Then click on “Generate” to move the parts asshown at right.ENCLOSURE definition01)From the tool bar menu, select “Tools >Enclosure” in order to insert a controlvolume cylindrically shaped and alignedto Y axis. Set the Cushion to 0.0375 mand set “Merge Parts?” to “Yes”.02)Click Generate to create the enclosureIn the “Outline” tree the just created enclosure isnow visible.Steps and Points to Convey Picture Guide Enclosure is visible in the “Model View” window.CREATE the WINDING COIL01) In the Tree Outline, Open “1 Part, 7 Bodies> Part”. RMB on the last Solid in the list andchoose “Hide Body” in the drop down menu.This will allow access to the surfaces of theimported geometry for forthcoming pickingoperations.02) Create a new plane (Plane6)03) In “Details of Plane6 >. Type” choose“From Face”.04) Click on the box to the right of “Base Face” and select the surface shown at right.05) In “Details of Plane6 >. Transform 1(RMB)” insert an offset along Z axis of –0.0231 m.Click on Generate to create Plane6.06) With Plane6 now active, go to the tool barand choose “New Sketch”.07) Select “Sketch1” in the “Tree Outline”.Steps and Points to Convey Picture Guide Sketching mode for winding coil generation08) Pick the Sketching tab at the bottom of theTree Outline09) Select “Circle” in the “Draw” window andchoose the center (origin of Plane6) and anarbitrary poin some distance away from thecenter to create a circle.10) Pick the Dimensions button at the bottom ofthe Sketching Toolboxes pane and choose“Radius”.11) Click on the circle and another arbitrarylocation for the radial dimension marker.12) In “Details of Sketch1”, modify the radiusR1 to be 0.00775 m.The sketch is now visible in the “Graphics” window.13) From the tool bar select “Concept > LineFrom Sketches”. Choose the circle and clickApply in the box to the right of “Base Objects” in “Details of Line1”. “Operation” should be setto “Add Material”.Click Generate.14) Choose the Line Body in the Tree Outline.15) In “Details of Line Body” set:?“Winding Body > Yes” ?“Number of Turns” = 1?“CS Length” = 0.022 m?“CS Length” = 0.00375 mSteps and Points to Convey Picture Guide 16) From the tool bar, select “View > ShowCross Sections Solids”. The new winding bodyshould appear as it does in the figure to the right.ANGLE as PARAMETER01) In the “Tree Outline” select “Plane5” 02) Make the rotation about Z axis as parameterby clicking on the box to the left of “FD1, Value1”.03) Rename the parameter as “angle”.Steps and Points to Convey. Picture Guide.04) From the tool bar, select “Tools >Options>Common Settings>Geometry Import”.Remove “DS” from the field to the right of“Personal Parameter Key” to remove the DSprefix naming convention restriction forimporting parameters. Click OK.GO IN SIMULATIONIn the “[Project]” window, select “NewSimulation”.In the “[Simulation]” window, the “Outline” treeshould be as in figure.Steps and Points to Convey Picture GuideMaterials Properties DefinitionSelect “Data” in the tool bar to open the“[Engineering Data]” window.Materials Properties Definitionchange defaults of STRUCTURAL STEEL01) Select “Structural Steel” and click on“Add/Remove Properties” in the“Electromagnetics” field and unselect thefollowing items:-“Relative Permeability” -“Resistivity” 02) Check the box to the left of “B-H curve” andclick OK.03) Say “Yes” to the “Remove MaterialProperties” box that appears.04) Open excel file “bh1.xls” and copy the twodata columns (highlight them with the mousecursor and type Cntl-C).Steps and Points to Convey Picture Guide 05) Click the icon depicting an xy plot to theright of “B-H Curve”06) LMB on the 2 (second row) of the“Magnetic Flux Density vs. Magnetic FieldIntensity” table and press “Ctrl +V” to paste thetwo column data from the .xls file.07) Click on the B-H Curve icon at the lowerright.The curve should appear as shown at right.NEW Material definition IRONRMB on “Materials (2)” in the tree and choose“Insert New Material”. RMB on “NewMaterial”, choose Rename and change the nameof the new material to Iron. Define BH data asbefore but this time use data from “bh2.xls” file.NEW Material definition NEODYMIUM01) Define a New material named“Neodymium”.02) Among Electromagnetics properties letactive just: “Linear Hard Material”:03) Insert the following data:?Cohercive Force: 7.9577 e5 A/m?Residual Induction 1.2 TAssign MAT PROPS to parts01) Return to the Simulation Tab02) In the Outline Tree, open Geometry>Partand use the Cntl button to select both of theRIC9512_105 items. The parts should behighlighted as shown at right.03) In Details of “Multiple Selection”, change material from “Structural Steel” to “Iron” Steps and Points to Convey Picture Guide04) Select the part shown at right.05) Change material from “Structural Steel” to “Neodymium” MESH01) Select the coil support solid (see figure)02) RMB on “Mesh” on the tree to insert asizing control:Element Size 2e-303) Insert another sizing control , 1e-3, referredto 5 bodies as in the following picture. It mayhelp to hide the 4th solid (the “air enclosure) inthe Outline tree to simplify selecting these parts.Steps and Points to Convey Picture Guide 5 bodies for sizing setting n.204) In the Outline tree, RMB on Model andinsert a “Coordinate Systems” branch. RMB onthe Coordinate Systems branch and insert(define) a new Coordinate System. Choose“Origin” in the Details of “Coordinate System” pane, select the surface shown at right, and clickApply.05) RMB on Mesh in the Outline to insert a thirdsizing control:For “Type”, choose “Sphere of Influence” ?Sphere Center: Coordinate System(defined just before)?Radius 1.5e-2?Element size 5e-4Areas to be applied are the following (10 areas)Steps and Points to Convey Picture Guide 10 Areas where to apply the Sphere of Influencesizing control06) Click on Mesh -> Preview MeshThe Mesh should result as in figure, if the “Air” solid enclosure body is hideLOADSSet the Conductor Current value in detailswindow related to “Conductor Winding Body”:1000 ABOUNDARY CONDITIONSRMB on Environment in the tree and insert aMagnetic Flux Parallel object. Use the Cntlbutton to select the 3 exterior surfaces of theenclosure and click Apply.Steps and Points to Convey. Picture Guide.POSTPROCESSING SETTINGS01) Insert under the “Solution” tree thefollowing output requests:?Total Flux Density?Total Flux Intensity02) Select 3 bodies as in figure03) Insert a “Directional Force/Torque” outputrequest with details:?In Details of “Directional Force/Torque” pane, change “Global CoordinateSystem” to “Coordinate System” (this isthe user-defined coordinate systemcentered on the top surface of thepermanent magnet).?Set Orientation to Y Direction (rotationaxis)04) repeat Directional Force/Torque Requestfor both X and Z axis direction05) By a right click under the Solution TreeInsert a “Solution Information” request tomonitor the run during the solutionSOLVE01)Highlight the Environment tree tosee/check all Boundary & Loadspreviously defined.02)Click on the “SOLVE” Icon to launchthe run.Solution times takes about 12 minutes on a 2.8 Ghz single processor 32bit PCSteps and Points to Convey Picture GuideREVIEW RESULTS01)See the Total Flux of Magnetic results02)Set up a Vector Image of the MagneticField03) After Vector Image settings show aVector Plot of Magnetic Field03)See the Magnetic Force distribution, Yaxis direction, on the requested parts.04)The same for X, Z directions05)Activate the view from Y Global Axis06)Define a “Slice Plane” 07)Draw the slice plane trace at nearlyalong the Y global direction08)View from the X Global direction09)Activate “show elements” and show themagnetic fieldSteps and Points to Convey Picture GuideSET UP A PARAMETRIC ANALYSIS01)Click on “Model” 02)Click on CAD Parameters Detail toactivate the “angle” as a parameter. Thiswill be the first INPUT parameter.03)Click on Environment and Duplicate byright click04)Activate the Conductor Current Value asparameter. This is the second INPUTparameter n.2.05)Activate the Torque value in Y directionas OUTPUT parameter (ThirdParameter)06)Click on “Solution” of Environment 2and then click on Parameter Manager07)Set up many cases as you like, forexample with 4 current values, 3 valuesother than the previously solved.。
ANSYSWorkbench电磁场分析例子
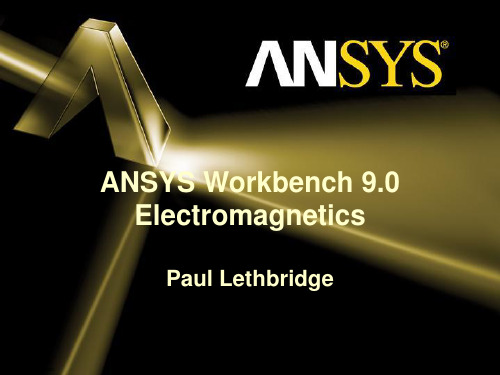
© 2004 ANSYS, Inc.
ANSYS, Inc. Proprietary
Winding Bodies & Tool
• Feature: Design Modeler (DM) includes two new tools to allow a user to easily create current carrying coils:
– Winding Bodies: Used to represent wound coils for source excitation. The advantage of these bodies is that they are not 3D CAD objects, and hence simplify modeling/meshing of winding structures.
– Upon “attach to Simulation”, Winding Bodies are assigned as Conductor bodies.
– Winding Tool: Used to create more complex coils for motor windings. The Winding Tool uses a Worksheet table format to drive the creation of multiply connected Winding Bodies. Or a user can read in a text file created by MSExcel.
– Design Modeler
• Enclosure Symmetry • Winding Bodies • Winding Tool
ANSYSWorkbench电磁场分析例子精品文档
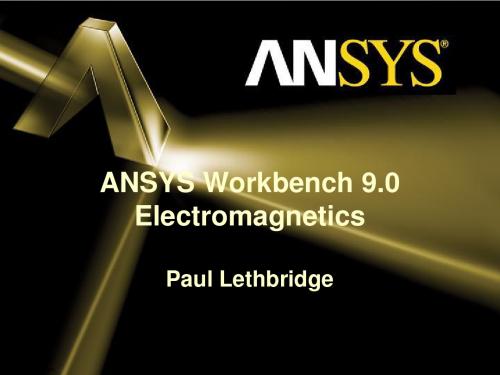
• Benefits: Very easy to use, rapid creation of coil windings.
© 2004 ANSYS, Inc.
ANSYS, Inc. Proprietary
Winding Bodies
Tangent orientation vector (blue arrow) defines direction of current.
• Fill Tool: Released at 9.0 (Beta at 8.1). Similar function to enclosure, but only fills interior cavities.
© 2004 ANSYS, Inc.
Example of a hemispherical enclosure around an electromagnet
– Simulation
© 2004 ANSYS, Inc.
ANSYS, Inc. Proprietary
Winding Bodies & Tool
• Feature: Design Modeler (DM) includes two new tools to allow a user to easily create current carrying coils:
ANSYS, Inc. Proprietary
Workbench Emag Markets
Target markets: • Solenoid actuators • Permanent magnet devices • Sensors • Rotating Electric machines
– Synchronous machines – DC machines – Permanent magnet machines
ANSYS电磁场分析例子
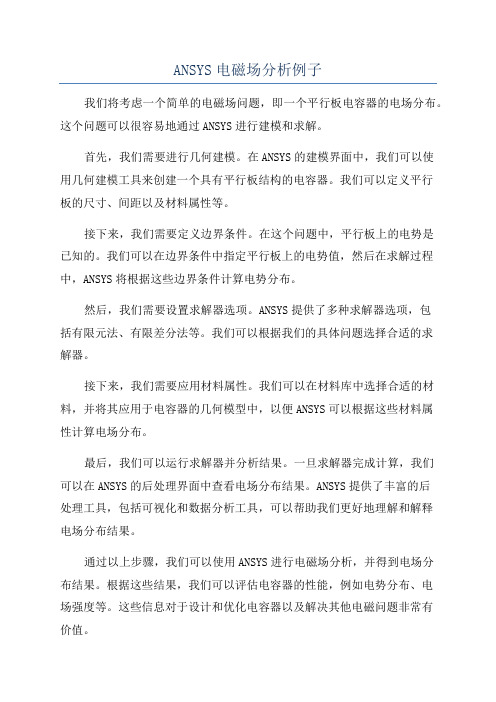
ANSYS电磁场分析例子我们将考虑一个简单的电磁场问题,即一个平行板电容器的电场分布。
这个问题可以很容易地通过ANSYS进行建模和求解。
首先,我们需要进行几何建模。
在ANSYS的建模界面中,我们可以使用几何建模工具来创建一个具有平行板结构的电容器。
我们可以定义平行板的尺寸、间距以及材料属性等。
接下来,我们需要定义边界条件。
在这个问题中,平行板上的电势是已知的。
我们可以在边界条件中指定平行板上的电势值,然后在求解过程中,ANSYS将根据这些边界条件计算电势分布。
然后,我们需要设置求解器选项。
ANSYS提供了多种求解器选项,包括有限元法、有限差分法等。
我们可以根据我们的具体问题选择合适的求解器。
接下来,我们需要应用材料属性。
我们可以在材料库中选择合适的材料,并将其应用于电容器的几何模型中,以便ANSYS可以根据这些材料属性计算电场分布。
最后,我们可以运行求解器并分析结果。
一旦求解器完成计算,我们可以在ANSYS的后处理界面中查看电场分布结果。
ANSYS提供了丰富的后处理工具,包括可视化和数据分析工具,可以帮助我们更好地理解和解释电场分布结果。
通过以上步骤,我们可以使用ANSYS进行电磁场分析,并得到电场分布结果。
根据这些结果,我们可以评估电容器的性能,例如电势分布、电场强度等。
这些信息对于设计和优化电容器以及解决其他电磁问题非常有价值。
总结起来,ANSYS电磁场分析是一种强大的工具,可以用于解决各种电磁问题。
通过几何建模、边界条件设置、求解器选项设置、应用材料属性和结果分析等步骤,我们可以使用ANSYS获得准确和可靠的电场分布结果,为问题的解决和优化提供有力支持。
ANSYS-Workbench-9.0电磁学教程实例(英文ppt)剖析
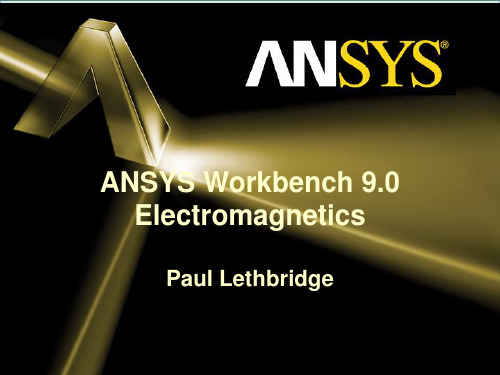
Fill Feature
• The Fill feature create a new frozen body to fill the space occupied by a hole or cavity.
• Useful for interior cavity electromagnetic applications.
• A skew angle may be identified for the coil winding slots • Many motor designs employ a skewed coil form.
© 2004 ANSYS, Inc.
ANSYS, Inc. Proprietary
Winding Slot Clash Detection
• Benefits: Very easy to use, rapid creation of coil windings.
© 2004 ANSYS, Inc.
ANSYS, Inc. Proprietary
Winding Bodies
Tangent orientation vector (blue arrow) defines direction of current.
• Workbench v9.0 is the first release with electromagnetic analysis capability. – Support solid and stranded (wound) conductors – Automated computations of force, torque, inductance, and coil flux linkage. – Easily set up simulations to compute results as a function of current, stroke, or rotor angle.
- 1、下载文档前请自行甄别文档内容的完整性,平台不提供额外的编辑、内容补充、找答案等附加服务。
- 2、"仅部分预览"的文档,不可在线预览部分如存在完整性等问题,可反馈申请退款(可完整预览的文档不适用该条件!)。
- 3、如文档侵犯您的权益,请联系客服反馈,我们会尽快为您处理(人工客服工作时间:9:00-18:30)。
A line body can be promoted to a winding body. Turns and cross-section (CS) dimensions are entered
© 2004 ANSYS, Inc. ANSYS, Inc. Proprietary
Winding Tool
Winding Bodies
© 2004 ANSYS, Inc.
ANSYS, Inc. Proprietary
Winding Table File
• Each Winding has a Winding Table File associated with it. • The Winding Table File can be created directly in DM • The Winding Table File can be exported to or imported from a text file. • Each row corresponds to a created Winding Body
© 2004 ANSYS, Inc.
ANSYS, Inc. Proprietary
Winding Tool
Each Winding consists a number of related Winding Bodies. The related Winding Bodies are shown in the Parts/Bodies branch:
© 2004 ANSYS, Inc. ANSYS, Inc. Proprietary
Fill Feature
• The Fill feature create a new frozen body to fill the space occupied by a hole or cavity. • Useful for interior cavity electromagnetic applications.
© 2004 ANSYS, Inc.
ANSYS, Inc. Proprietary
Enclosure Symmetry
•Feature: The Enclosure feature now supports symmetry models when the enclosure shape is a box or a cylinder:
– Design Modeler
• Enclosure Symmetry • Winding Bodies • Winding Tool
– Simulation
© 2004 ANSYS, Inc.
ANSYS, Inc. Proprietary
Workbench Emag Roadmap
• LF Emag capability will be exposed over several release cycles: – 3D Magnetostatics (9.0) – 3D Current conduction (10.0) – 3D Electrostatics Circuit elements – Time transient & 2D • Workbench v9.0 is the first release with electromagnetic analysis capability. – Support solid and stranded (wound) conductors – Automated computations of force, torque, inductance, and coil flux linkage. – Easily set up simulations to compute results as a function of current, stroke, or rotor angle. • Workbench Emag capability is mapped to & accessed via:
ANSYS, Inc. Proprietary
Winding Tool Example
Winding 1 highlighted with rotor
Complete DC Motor model
© 2004 ANSYS, Inc.
ANSYS, Inc. Proprietary
Winding Options
ANSYS Workbench 9.0 Electromagnetics
Paul Lethbridge
© 2004 ANSYS, Inc.
ANSYS, Inc. Proprietatromagnetics
– Workbench Emag Roadmap
– Synchronous machines – DC machines – Permanent magnet machines
© 2004 ANSYS, Inc.
ANSYS, Inc. Proprietary
Contents
Workbench Electromagnetics
– Workbench Emag Roadmap
Complex coil windings may be created using the Winding Tool: • The Winding Tool inserts a “Winding#” into the model tree. • A “Details” view is used for geometric placement.
• Coils may have different radii between IN & OUT slots • Multiple coils may be stacked in the same slot
© 2004 ANSYS, Inc.
ANSYS, Inc. Proprietary
Winding Options - Skew
– Design Modeler
• Enclosure Symmetry • Winding bodies • Winding Tool
– Simulation
© 2004 ANSYS, Inc.
ANSYS, Inc. Proprietary
Enclosure & Fill Tools
Design Modeler (DM) includes two features to allow a user to create a volumetric “field” body associated with a solid model. • Enclosure tool: Released at 8.0. This tool is used to completely enclose the bodies of a model in a material typically required for an Emag analysis.
– ANSYS Emag (stand alone or enabled task) – ANSYS Multiphysics license keys.
ANSYS, Inc. Proprietary
© 2004 ANSYS, Inc.
Workbench Emag Markets
Target markets: • Solenoid actuators • Permanent magnet devices • Sensors • Rotating Electric machines
– Up to 3 three symmetry planes can be specified.
– Full or partial models can be included in the Enclosure. – During the model transfer from DesignModeler to Simulation, the enclosure feature with symmetry planes forms two kinds of named selections: – Open Domain – Symmetry Plane
© 2004 ANSYS, Inc.
ANSYS, Inc. Proprietary
Contents
Workbench Electromagnetics
– Workbench Emag Roadmap
– Design Modeler
• Enclosure Symmetry • Winding bodies • Winding Tool
– Simulation
© 2004 ANSYS, Inc.
ANSYS, Inc. Proprietary
Winding Bodies & Tool
• Feature: Design Modeler (DM) includes two new tools to allow a user to easily create current carrying coils: – Winding Bodies: Used to represent wound coils for source excitation. The advantage of these bodies is that they are not 3D CAD objects, and hence simplify modeling/meshing of winding structures. – Upon “attach to Simulation”, Winding Bodies are assigned as Conductor bodies. – Winding Tool: Used to create more complex coils for motor windings. The Winding Tool uses a Worksheet table format to drive the creation of multiply connected Winding Bodies. Or a user can read in a text file created by MSExcel.