108-1003-001;中文规格书,Datasheet资料
V23074A1002A403;中文规格书,Datasheet资料

101-2013, Rev. 0113Datasheets and product specification ac-Datasheets and product data is subject to the Datasheets, product data, ‘Definitions’ sec-Micro Relay A/VFMA1) The values apply to a resistive or inductive load with suitable spark suppression and atmaximum 13.5VDC for 12VDC or 27VDC for 24VDC load voltages.2) For a load current duration of maximum 3s for a make/break ratio of 1:10.3) Current and time are compatible with circuit protection by a typical automotive fuse. Relay will make, carry and break the specified current.4) See chapter Diagnostics of Relays in our Application Notes or consult the internet at /appnotes/5) Electrical endurance data are only valid for the variants with resistor.6) Not applicable for polarity reverse loads like powerwindowsn High current version with limiting continuous current 30A at 85°C n Pin assignment according to ISO 7588 part 3n Customized versions on request– 24VDC versions with special contact gap – Integrated components (e.g. diode) – Customized marking– Special covers (e.g. notches, release features) – For latching version refer to Micro Relay Latching – For low noise version refer to Micro Relay Low Noise – For high current version refer to part number table Typical applicationsCross carline up to 30A for example: ABS control, blower fans, cooling fan, door control, door lock, fuel pump, heated front screen, immobilizer, interior lights, seat control, seatbelt pretensioner, sun roof, trunk lock, valves, window lifter, wiper control.Max. DC load breaking capacityLoad limit curve 1: arc extinguishes during transit time (CO contact).Load limit curve 2: safe shutdown, no stationary arc (NO contact).Load limit curves measured with low inductive resistors verified for 1000 switching events.Contact DataForm A – StandardForm C Form A – HCContact arrangement 1 form A, 1 NO 1 form A, 1 NO 1 form C, 1 CO 1 form C, 1 CO 1 form A, 1 NORated voltage 12VDC 24VDC 12VDC 24VDC 6) 12VDCLimiting continuous current, form A/form B NO/NC NO/NC 23°C 30A 30A 30/20A 30/20A 35A 85°C 25A 25A 25/15A 25/15A 30A 125°C 10A 10A 10/8A 10/8A 15ALimiting making current 1)2), A/B (NO/NC) 120A 120A 120/40A 120/20A 120ALimiting breaking current 30A 20A 30/15A 20/10A 30A Limiting short-time current,overload current, ISO 8820-33) 1.35 x 25A, 1800s 1.35 x 25A, 1800s 1.35 x 30A, 1800s 2.00 x 25A, 5s 2.00 x 25A, 5s 2.00 x 30A, 5s 3.50 x 25A, 0.5s 3.50 x 25A, 0.5s 3.50 x 30A, 0.5s 6.00 x 25A, 0.1s 6.00 x 25A, 0.1s 6.00 x 30A, 0.1s Jump start test 24VDC for 5min conducting nominal current at 23°C Contact material silver based Min. recommended contact load 4) 1A at 5VDC Initial voltage drop NO contact at 10A, typ./max. 15/200mV NC contact at 10A, typ./max. 20/250mV Frequency of operation 6 ops./min (0.1Hz)Electrical endurance 5)resistive load at 14VDC >1x105 ops. >1x105 ops. >1x105 ops.25A 25A (NO) 30A resistive load at 28VDC >1x105 ops. >1x105 ops. 15A 15A (NO) >1x105 ops. 10A (NC)Mechanical endurance typ. 107 ops. F074_fcw1_bwFVFMA_fcw1c201-2013, Rev. 0113Datasheets and product specification ac-Datasheets and product data is subject to the Datasheets, product data, ‘Definitions’ sec-Other DataEU RoHS/ELV compliance compliant Ambient temperature -40 to +125°C Climatic cycling with condensation, EN ISO 6988 6 cycles, storage 8/16h Temperature cycling, IEC 60068-2-14, Nb 10 cycles, -40/+85°C (5°C/min) Damp heat cyclic,IEC 60068-2-30, Db, Variant 1 6 cycles, upper air temp. 55°C Damp heat constant,IEC 60068-2-3 (78), Ca 56 days Category of environmental protection, IEC 61810 RT I – dustproof Degree of protection, IEC 60529 IP54 Corrosive gas IEC 60068-2-42 10±2cm 3/m 3 SO 2, 10 days IEC 60068-2-43 1±0.3cm 3/m 3 H 2S, 10 days Vibration resistance (functional) IEC 60068-2-6 (sine sweep) 10 to 500Hz min. 5g 8) Shock resistance (functional) IEC 60068-2-27 (half sine) min. 20g 11ms 8) Drop test, free fall, IEC 60068-2-32 1m onto concrete Terminal type plug-in, QC Cover retention axial force 150N pull force 150N push force 200N Terminal retention pull force 100N push force 100N resistance to bending 10N 9) force applied to side 10N 9) torque 0.3Nm Weight approx. 16 to 20g (0.5 to 0.7oz)Packaging unit Micro A 480 pcs. VFMA 600 pcs.8) No change in the switching state >10µs. Valid for NC contacts, NO contact values significantly higher.9) Values apply 2mm from the end of the terminal. When the force is removed, the terminal must not have moved by more than 0.3mmAccessoriesFor details see datasheetConnectors for Micro ISO RelaysCoil DataCoil voltage range 12/24VDCCoil versions, DC coil Coil Rated Operate Release Coil Rated coil code voltage voltage voltage resistance 7) power 7) VDC VDC VDC Ω±10% W 001 12 7.2 1.6 119 1.20 002 24 14.4 3.6 430 1.34 005 12 7.2 1.6 144 1.00 F 12 7.2 1.2 90 1.60 H 24 14.4 3.6 430 1.34All figures are given for coil without pre-energization, at ambient temperature +23°C.7) Without components in parallel.Insulation DataInitial dielectric strength between open contacts 500VAC rms between contact and coil 500VAC rms Load dump testISO 7637-1 (12VDC), test pulse 5 Vs=+86.5VDC ISO 7637-2 (24VDC), test pulse 5Vs=+200VDCNOD1 form A, 1 NO with diodeNOR1 form A, 1 NO with resistorTerminal Assignment COD1 form C, 1 CO with diodeCOR1 form C, 1 CO with resistor5435435353Does not take into account the temperature rise due to the contact currentE = pre-energization.Does not take into account the temperature rise due to the contact current E = pre-energization Coil operating range301-2013, Rev. 0113Datasheets and product specification ac-Datasheets and product data is subject to the Datasheets, product data, ‘Definitions’ sec-View of the terminals (bottom view)Quick connect terminal similar to ISO 8092-1.Micro A: Terminals without holes401-2013, Rev. 0113Datasheets and product specification ac-Datasheets and product data is subject to the Datasheets, product data, ‘Definitions’ sec-Product code structureTypical product code V23074 -A 1 001 -A4 02Type V23074 Micro Relay A Version A Standard H High current Coil suppression 1 Resistor 2 Diode Coil 001 12VDC 002 24VDC00512VDC for high current versionContact material -A4 Silver based -A5 Silver based for high current version Contact arrangement 02 1 form A, 1 NO031 form C, 1 COProduct code structureTypical product codeVFMA -1 1 F 4 1 -S01Type VFMA VFMA Series Version 1 Standard Contact arrangement 1 1 form A, 1 NO 5 1 form C, 1 COCoil F 12VDC H 24VDC Contact material 4 Silver based 7Silver based for high current versionTerminals 1 Plug-in Coil suppression S01 ResistorOther types on request.This list represents the most common types and does not show all variants covered by this datasheet.分销商库存信息: TE ConnectivityV23074A1002A403。
AC108_Datasheet_V1.1

BSH108,215;中文规格书,Datasheet资料

BSH108N-channel enhancement mode field-effect transistorRev. 02 — 25 October 2000Product specification1.DescriptionN-channel enhancement mode field-effect transistor in a plastic package using TrenchMOS™1 technology.Product availability:BSH108 in SOT23.2.Featuress TrenchMOS™ technology s Very fast switching s Logic level compatiblesSubminiature surface mount package.3.Applicationss Battery management s High speed switchs Low power DC to DC converter.4.Pinning information1.TrenchMOS is a trademark of Royal Philips Electronics.Table 1:Pinning - SOT23, simplified outline and symbolPin Description Simplified outlineSymbol1gate (g)SOT232source (s)3drain (d)MSB003Top view123sdgMBB0765.Quick reference dataTable 2:Quick reference dataSymbol Parameter Conditions Typ Max Unit V DS drain-source voltage (DC)T j=25to150°C−30VI D drain current (DC)T sp=25°C; V GS=5V− 1.9AP tot total power dissipation T sp=25°C−0.83W T j junction temperature−150°C R DSon drain-source on-state resistance V GS=10V; I D=1A77120mΩV GS=5V; I D=1A102140mΩ6.Limiting valuesTable 3:Limiting valuesIn accordance with the Absolute Maximum Rating System (IEC 60134).Symbol Parameter Conditions Min Max Unit V DS drain-source voltage (DC)T j=25to150°C−30VV DGR drain-gate voltage (DC)T j=25to150°C; R GS=20kΩ−30VV GS gate-source voltage (DC)−±20VI D drain current (DC)T sp=25°C; V GS=5V;Figure2and3− 1.9AT sp=100°C; V GS=5V;Figure2− 1.2AI DM peak drain current T sp=25°C; pulsed; t p≤10µs;Figure3−7.5AP tot total power dissipation T sp=25°C;Figure1−0.83W T stg storage temperature−65+150°C T j operating junction temperature−65+150°C Source-drain diodeI S source (diode forward) current (DC)T sp=25°C−0.83AI SM peak source (diode forward) current T sp=25°C; pulsed; t p≤10µs− 3.3AV GS ≥5VFig 1.Normalized total power dissipation as afunction of solder point temperature.Fig 2.Normalized continuous drain current as afunction of solder point temperature.T sp =25°C; I DM is single pulse.Fig 3.Safe operating area; continuous and peak drain currents as a function of drain-source voltage.03aa170204060801001200255075100125150175P der T sp(o C)(%)03aa25204060801001200255075100125150175I der T sp (o C)(%)P der P totP tot 25C °()----------------------100%×=I der I DI D 25C °()------------------100%×=03aa8010-310-210-111010-1110102V DS (V)I D (A) D.C.100ms10msR DSon =V DS /I D1mst p =10µs 100µs T sp =25o Ct pt p TPtTδ =7.Thermal characteristics7.1Transient thermal impedanceTable 4:Thermal characteristicsSymbol ParameterConditionsValue Unit R th(j-sp)thermal resistance from junction to solder point mounted on a metal clad substrate;Figure 4150K/W R th(j-a)thermal resistance from junction to ambientmounted on a printed circuit board;minimum footprint350K/WMounted on a metal clad substrate.Fig 4.Transient thermal impedance from junction to solder point as a function of pulse duration.03aa7910-111010210310-510-410-310-210-1110t p (s)Z th(j-sp)(K/W)single pulseδ=0.50.20.10.050.02t pt p TPtTδ =8.CharacteristicsTable 5:CharacteristicsT j=25°C unless otherwise specifiedSymbol Parameter Conditions Min Typ Max Unit Static characteristicsV(BR)DSS drain-source breakdown voltage I D=10µA; V GS=0VT j=25°C3040−VT j=−55°C27−−VV GS(th)gate-source threshold voltage I D=1mA; V DS=V GS;Figure9T j=25°C1 1.52VT j=150°C0.5−−VT j=−55°C−− 3.2VI DSS drain-source leakage current V DS=24V; V GS=0VT j=25°C−0.01 1.0µAT j=150°C−−10µA I GSS gate-source leakage current V GS=±10V; V DS=0V−10100nA R DSon drain-source on-state resistance V GS=10V; I D=1A;Figure7and8T j=25°C−77120mΩV GS=5V; I D=1A;Figure7and8T j=25°C−102140mΩT j=150°C−170240mΩDynamic characteristicsg fs forward transconductance V DS=10V; I D=1A;Figure112 4.5−SQ g(tot)total gate charge V DD=15V; V GS=10V; I D=5A;Figure14− 6.410nC Q gs gate-source charge−0.5−nC Q gd gate-drain (Miller) charge− 1.3−nC C iss input capacitance V GS=0V; V DS=10V; f=1MHz;Figure12−190−pF C oss output capacitance−70−pF C rss reverse transfer capacitance−50−pF t d(on)turn-on delay time V DD=10V; R L=10Ω; V GS=10V; R G=6Ω−3−ns t r rise time−8−ns t d(off)turn-off delay time−15−ns t f fall time−26−ns Source-drain diodeV SD source-drain (diode forward) voltage I S=0.83A; V GS=0V;Figure13−0.8 1.2Vt rr reverse recovery time I S=1A; dI S/dt=−100A/µs; V GS=0V;V DS=25V −25−nsQ r recovered charge−20−nCT j =25°C T j =25°C and 150°C; V DS >I D ×R DSonFig 5.Output characteristics: drain current as afunction of drain-source voltage;typical values.Fig 6.Transfer characteristics: drain current as afunction of gate-source voltage; typical values.T j =25°CFig 7.Drain-source on-state resistance as a functionof drain current; typical values.Fig 8.Normalized drain-source on-state resistancefactor as a function of junction temperature.03aa8100.511.522.533.544.5500.20.40.60.811.2 1.4 1.6 1.82V DS (V)I D(A) 3 V2 V2.2 V 2.4 V 2.6 VV GS = 2.8 V3.4 V T j = 25 o C5 V10 V 03aa8300.511.522.533.544.5500.511.522.533.54V GS (V)I D (A)V DS > I D X R DSonT j = 25 o C150 o C03aa8200.050.10.150.20.250.30.350.40.450.50.511.522.533.544.55I D (A)R DSon(Ω)V GS = 10 V T j = 25 o C 3 V5 V2.2 V2.4 V2.6 V2.8 V3.4 V03aa2700.20.40.60.81.01.21.41.61.82.0-60-202060100140180T j(o C)aa R DSonR DSon 25C °()---------------------------=I D =1mA; V DS =V GS T j =25°C; V DS =5VFig 9.Gate-source threshold voltage as a function ofjunction temperature.Fig 10.Sub-threshold drain current as a function ofgate-source voltage.T j =25°C and 150°C; V DS >I D ×R DSon V GS =0V; f =1MHzFig 11.Forward transconductance as a function ofdrain current; typical values.Fig 12.Input,output and reverse transfer capacitancesas a function of drain-source voltage; typical values.03aa3300.511.522.5-60-202060100140180maxtypminV GS(th)T j (o C)(V)03aa360.511.522.53maxtyp minI DV GS (V)10-610-510-410-310-210-1(A)03aa8401234567800.511.522.533.544.55I D (A)g fs (S)V DS > I D X R DSonT j = 25 o C150 o C03aa861010210310-1110102V DS (V)C iss , C oss , C rss (pF)C issC ossC rssT j =25°C and 150°C; V GS =0V I D =0.5A; V DD =15V; T j =25°CFig 13.Source (diode forward) current as a function ofsource-drain (diode forward) voltage; typical values.Fig 14.Gate-source voltage as a function of gatecharge; typical values.03aa8500.511.522.533.544.5500.20.40.60.811.2 1.4V SD (V)I S (A)150 o CT j = 25 o CV GS = 0V03ab100123456789101112131415012345678910Q G (nC)V GS (V)I D = 0.5 A T j = 25 o CV DD = 15 V9.Package outlineFig 15.SOT23.UNIT A 1max.b p c D E e 1H E L p Q w v REFERENCESOUTLINE VERSION EUROPEAN PROJECTIONISSUE DATE 97-02-2899-09-13IECJEDEC EIAJmm0.10.480.380.150.093.02.81.41.20.95e 1.92.52.10.550.450.10.2DIMENSIONS (mm are the original dimensions)0.450.15SOT23TO-236ABb pD e 1eAA 1L pQdetail XH EE w M v M ABAB 01 2 mmscaleA 1.10.9cX123Plastic surface mounted package; 3 leadsSOT2310.Revision historyTable 6:Revision historyRev Date CPCN Description022*******-Product specification; second version; supersedes Rev.01 of 20000906.Correction to diode I S; see Table 3 “Limiting values”0120000906-Product specification.分销商库存信息: NXPBSH108,215。
BLF888A,112;中文规格书,Datasheet资料

RF performance in a common source 860 MHz narrowband test circuit f1 = 860; f2 = 860.1 860 858 858 DVB-T (8k OFDM) 858 858
[1] [2] [3] Measured at = 10 %; tp = 100 s. Measured [dBc] with delta marker at 4.3 MHz from center frequency. PAR (of output signal) at 0.01 % probability on CCDF; PAR of input signal = 9.5 dB at 0.01 % probability on CCDF.
Graphic symbol
BLF888A (SOT539A)
1 2 5 3 3 4 4 5 1
2
sym117
BLF888AS (SOT539B) 1 2 3 4 5 drain1 drain2 gate1 gate2 source
[1]
1
2 5
1
3
4
3 5 4
2
sym117
[1]
Connected to flange.
[1] [2]
Conditions VGS = 0 V; ID = 2.4 mA VDS = 10 V; ID = 240 mA VGS = 0 V; VDS = 50 V VGS = VGS(th) + 3.75 V; VDS = 10 V VGS = 10 V; VDS = 0 V VGS = VGS(th) + 3.75 V; ID = 8.5 A VGS = 0 V; VDS = 50 V; f = 1 MHz VGS = 0 V; VDS = 50 V; f = 1 MHz VGS = 0 V; VDS = 50 V; f = 1 MHz
NOIH2SM1000S-HHC;中文规格书,Datasheet资料

NOIH2SM1000AHAS2 Image SensorINTRODUCTIONScopeThis ICD version is generated after qualification campaign closure. This specification details the ratings, physical, geometrical, electrical and electro-opticalcharacteristics, and test- and inspection-data for the High Accuracy Star Tracker (HAS2) CMOS active pixel image sensor (CMOS APS).The device described in this document is protected by US patent 6,225,670 and others.Component Type ValuesTable 10 on page 8 provides a summary of the type variants of the basic CMOS image sensor. The complete list of specifications for each type variant is given in Detailed Specifications on page 9.All specifications in Detailed Specifications on page 9 are given at 25 ±3°C, under nominal clocking and bias conditions. Exceptions are noted in the ‘Remarks’ field. Maximum RatingTable 11 on page 9 specifies the maximum ratings. Do not exceed these ratings at any times, during use or storage. Physical Dimension and Geometrical Information Figure 2 on page 24 shows the physical dimensions of the assembled component. The geometrical information in Figure 4 on page 25 describes the position of the die in the package.Pin AssignmentFigure 5 on page 26 contains the pin assignment. The figure contains a schematic drawing and a pin list. A detailed functional description of each pin is available in Pin List on page 36.Soldering InstructionsSoldering is restricted to manual soldering only. No wave or reflow soldering is allowed. For manual soldering, the following restrictions are applicable:•Solder 1 pin on each of the four sides of the sensor.•Cool down for a minimum period of 1 minute before soldering another pin on each of the four sides.•Repeat soldering of 1 pin on each side, including a 1 minute cool down period.Handling PrecautionsThe component is susceptible to damage by electro-static discharge. Therefore, use suitable precautions for protection during all phases of manufacture, testing, packaging, shipment, and any handling. Follow these guidelines:•Always manipulate devices in an ESD controlled environment.•Always store the devices in a shielded environment that protects against ESD damage (at least a non-ESD generating tray and a metal bag).•Always wear a wrist strap when handling the devices and use ESD safe gloves.•The HAS2 is classified as class 1A (JEDEC classification - [AD03]) device for ESD sensitivity. For proper handling and storage conditions, refer to the ON Semiconductor application note AN52561.Limited WarrantyON Semiconductor’s Image Sensor Business Unit warrants that the image sensor products to be delivered hereunder, if properly used and serviced, will conform to Seller’s published specifications and will be free from defects in material and workmanship for two (2) years following the date of shipment. If a defect were to manifest itself within two (2) years period from the sale date, ON Semiconductor will either replace the product or give credit for the product.Return Material Authorization (RMA)ON Semiconductor packages its image sensor products in a clean room environment under strict handling procedures and ships all image sensor products in ESD-safe, clean-room-approved shipping containers. Products returned to ON Semiconductor for failure analysis should be handled under these same conditions and packed in its original packing materials, or the customer may be liable for the product.Storage InformationThe components must be stored in a dust-free and temperature-, humidity-and ESD-controlled environment.•Store devices in special ESD-safe trays such that the glass window is never touched.•Close the trays with EDS-safe rubber bands.•Seal the trays in an ESD-safe conductive foil in clean room conditions.•For transport and storage outside a clean room, pack the trays in a second ESD-save bag that is sealed in cleanroom.Additional InformationThe HAS sensor is subject to the standard European export regulations for dual use products. A Certificate of Conformance will be issued upon request at no additional charge. The CoC refers to this document. Additional screening tests is done on request at additional cost.The following data is delivered by default with FM sensors:•Sensor calibration data •Temperature calibration data •Certificate of Conformance to this detailed specification•Visual inspection report•Bad pixel mapITAR InformationThe NOIH2SM1000A is an ITAR-free component.Table 1. ORDERING INFORMATIONMarketing Part Number Description Package NOIH2SM1000T-HHC HAS2 Mono, Flight Model, Level 284-pin JLCC NOIH2SM1000A-HHC HAS2 Mono, Engineering ModelNOIH2SM1000S-HHC HAS2 Mono, Flight Model, Level 1NOIH2SM1000A-HWC HAS2 Mono Windowless, Engineering ModelNOIH2SM1000S-HWC HAS2 Mono Windowless, Flight Model, Level 1ORDERING CODE DEFINITIONO = OptoN = ON SemiconductorHAS2M=MonoH= JLCCCommercial Temperature Range 1000M HS = Standard Process1.0 MP Resolution A= Engineering Model H= BK7G18 GlassI I = Image Sensors H CN O H2S A −S= Flight Model, Level 1T= Flight Model, Level 2W= WindowlessAPPLICABLE DOCUMENTSThe following documents form part of this specification:Table 2. APPLICABLE DOCUMENTSNo.Reference Title Issue DateAD01ESCC Generic Specification 9020Charge Coupled Devices, Silicon, Photosensitive2March 2010AD02001-06225(Note 1)Electro-optical test methods for CMOS image sensors E October, 2008AD03JESD22-A114-B Electrostatic Discharge (ESD) Sensitivity Testing HumanBody Model (HBM)B June, 2000AD04APS2-FVD-06-003Process Identification Document for HAS22February, 2008 AD05001-49283Visual Inspection for FM devices1January, 2008 AD06001-49280HAS2 FM Screening2June, 20091.This specification will be superseded by the ESCC basic specification 25000, which is currently under development. The current referenceis an internal ON Semiconductor procedure and is a confidential document.2.Lot acceptance and screening are based on ESCC 9020 issue 2. Please note that Lot Acceptance and Screening on page 6 − is valid forthe Flight Model Level 1 devices. For more information on Flight Model 1 Windowless devices, please contact imagesensors@DETAILED INFORMATIONDeviations from Generic SpecificationLot acceptance and screening are based on ESCC 9020 issue 2. See Lot Acceptance and Screening on page 6 for more information.Mechanical RequirementsDimension CheckThe dimensions of the components specified here is checked and must comply with the specifications and the tolerances indicated in Figure 2 on page 24 Geometrical CharacteristicsThe geometrical characteristics of the components specified here is checked and must comply with the specifications and tolerances given in Figure 2 on page 24 and Figure 3 on page 25WeightThe maximum weight of the components specified here is specified in Table 14 on page 9Materials and FinishesThe materials and finishes is as specified in this document. Where a definite material is not specified, a material which enables the components to meet the performance requirements of this specification must be used. See Note 2. CaseThe case is hermetically sealed and must have a ceramic body and a glass window.Table 3. CASEType JLCC−84Material Black Alumina BA−914 Thermal expansion coefficient7.6 x 10−6/KHermeticity< 5 x 10−7 atms. cm3/s Thermal resistance(Junction to case)3.633°C/WLead Material and FinishTable 4. LEAD MATERIAL AND FINISHLead Material KOVAR1e Finish Nickel, min 2 m m2nd Finish Gold, min 1.5 m mWindowThe window material is a BK7G18 glass lid with anti-reflective coating applied on both sides.The optical quality of the glass must have the specifications in Table 15 on page 9.The anti reflective coating has a reflection coefficient less than 1.3% absolute and less than 0.8% on average, over a bandwidth from 440 nm to 1100 nm.Level 2 versus Level 1 differencesHAS2 Level 2 devices are differing from Level 1 devices in Lot Acceptance and Screening on page 6•100% screening is applied with burn-in limited to 168 hinstead of 240 h as for Level 1.•Assembly process is based on ESA qualified process (same procedures and materials)•Devices will be fully tested at room temperature, electrical testing at 85 degrees is limited to power consumption measurements only.•X/Y dye placement is relaxed to +/- 200 m m.•Mismatching between odd and even columns in Direct Readout is allowed but shall stay in the limit of127LSB.•The defect and particles specification will be the same as for the Engineering Model - NOIH2SM1000A-HHC – with the exception of the defective columns which are not allowed in the Level 2 devices. Refer to Table 10“Type Variant Summary” on page 8.•Endurance testing during wafer LAT is limited to a 1000 h burn in instead of 2000 h and will be performed on 3 un-screened parts instead of 6.•Prior to endurance testing and total dose testing, a stabilization bake of 48 hrs, followed by a 168 hrs burn-in, shall be performed.•During wafer LAT, the Electro-optical measurements is limited on 2 parts (1 from endurance testing and 1 from radiation testing) instead of 6.•For each assembly batch (manufacturing-lot), 2 screened devices will be made available for a DPA test. An assembly batch is defined as a group of parts which have been assembled within a time window of less than one week. The DPA devices can be rejected devices (glass lid cosmetic defects, electrical defects,…) but has to be screened through the same thermal steps as the HAS2 “level2”. The DPA test will be carried out by ON Semiconductor as a customer courtesy.Prior to DPA testing, the following tests are performed: Solderability and Resistance to Solvents (marking permeability).NOTE:As the glass lid removal is a best effort activity, the DPA test cannot be 100% guaranteed.•Pictures and defect maps are not included in the data pack, but will be made available upon request.•Assembly lot acceptance testing is not performed.Data PackEach set of devices will have a data pack which will be made available to the customer. The data pack consists of:•CoC form referring to the applicable specification •Calibration data •Screening Report•Life Test Report and Radiation (Total Dose) Test Report for each wafer lot •Electrical Test Report •Spectral response data •Visual Inspection Report •DPA Test ReportMarkingGeneralThe marking must consist of lead identification and traceability information.Lead IdentificationAn index to pin 1 must be located on the top of the package in the position defined in Figure 2 on page 24. The pin numbering is counter clock-wise, when looking at the top-side of the component.Traceability InformationEach component must be marked such that complete traceability is maintained.The component must have a number as follows:Figure 1. Product MarkingXXXXX = Specific Device Code A = Assembly Location WL = Wafer Lot YY = YearWW = Work WeekNNNN = Serial NumberTable 5. PACKAGE MARK DECODEROrderable Part Number Package Mark: Line 1Package Mark: Line 2Package Mark: Line 3NOIH2SM1000T-HHC NOIH2SM1000T -HHC_NNNN AWLYYWW NOIH2SM1000A-HHC NOIH2SM1000A -HHC_NNNN AWLYYWW NOIH2SM1000S-HHC NOIH2SM1000S -HHC_NNNN AWLYYWW NOIH2SM1000A-HWC NOIH2SM1000A -HWC_NNNN AWLYYWW NOIH2SM1000S-HWCNOIH2SM1000S-HWC_NNNNAWLYYWWwhere NNNN- serialized number controlled manually by ON Semiconductor, BELGIUM where DD-MM-YYYY represents the lot assembly date NOIH2SM1000T-HHC has a Minimum Order Quantity of 10Electrical and Electro −optical MeasurementsElectrical and Electro −optical Measurements at Reference TemperatureThe parameters to be measured to verify the electrical and electro-optical specifications are given in Table 18 on page 13 and Table 27 on page 23. Unless otherwise specified, the measurements must be performed at a environmental temperature of 22 ±3°C.For all measurements, the nominal power supply, bias,and clocking conditions apply. The nominal power supply and bias conditions are given in Table 28 on page 23; thetiming diagrams in Figure 35 on page 47 and Figure 37 on page 49.NOTE:The given bias and power supply settings implythat the devices are measured in ‘soft-reset’condition.Electrical and Electro −optical Measurements at High and Low TemperatureTable 19 on page 14 and Table 20 on page 15 list the parameters to be measured to verify electrical and electro-optical specifications. Unless otherwise specified,the measurements must be performed at –40 (–5 +0) °C and at +85 (+5 –0) °C.Circuits for Electrical and Electro−optical Measurements Circuits for performing the electro−optical tests in Table18 on page13 and Table 27 on page 23 are shown in Figure 49 on page 59 to Figure 52 on page 59.Burn−in TestParameter Drift ValuesThe parameter drift values for power burn-in are specified in Table 21 on page 17. Unless otherwise specified, the measurements must be conducted at an environmental temperature of 22 ±3°C and under nominal power supply, bias, and timing conditions.Do not exceed the parameter drift values. In addition to these drift value requirements, do not exceed the limit values of any parameter, as indicated in Table 18 on page13 Conditions for High Temperature Reverse Bias Burn-in Not ApplicableConditions for Power Burn-inThe conditions for power burn-in is specified in Table 24 on page 19 of this specification.Electrical Circuits for High Temperature Reverse Bias Burn-inNot ApplicableElectrical Circuits for Power Burn-inCircuits to perform the power burn-in test are shown in Figure 48 on page 58 and Figure 49 on page 59 of this specification.Environmental and Endurance TestsElectrical and Electro-optical Measurements on Completion of Environmental TestThe parameters to be measured on completion of environmental tests are listed in Table 25 on page 20. Unless otherwise stated, the measurements must be performed at a environmental temperature of 22 ±3°C. Measurements of dark current must be performed at 22 ±1°C and the actual environmental temperature must be reported with the test results.Electrical and Electro-optical Measurements At Intermediate Point During Endurance TestThe parameters to be measured at intermediate points during endurance test of environmental tests are listed in Table 25 on page 20. Unless otherwise stated, the measurements must be performed at an environmental temperature of 22 ±3°C.Electrical and electro-optical Measurements on Completion of Endurance TestThe parameters to be measured on completion of endurance tests are listed in Table 25 on page 20. Unless otherwise stated, the measurements must be performed at a environmental temperature of 22 ±3°C.Conditions for Operating Life TestThe conditions for operating life tests must be as specified in Table 24 on page 19 of this specification.Electrical Circuits for Operating Life TestCircuits for performing the operating life test are shown in Figure 49 on page 59 and next ones of this specification. Conditions for High Temperature Storage TestThe temperature to be applied must be the maximum storage temperature specified in Table 11 on page 9 of this specification.Total Dose Radiation TestApplicationThe total dose radiation test must be performed in accordance with the requirements of ESCC Basic Specification 22900.Parameter Drift ValuesThe allowable parameter drift values after total dose irradiation are listed in Table 22 on page 18 . The parameters shown are valid after a total dose of 42 KRad and 168h/100°C annealing.Bias ConditionsContinuous bias must be applied during irradiation testing as shown in Figure 49 on page 59 and next ones of this specification.Electrical and Electro-optical MeasurementsThe parameters to be measured, prior to, during and on completion of the irradiation are listed in Table 27 on page23 of this specification. Only devices that meet the specification in Table 18 on page 13 of this specification must be included in the test samples.Lot Acceptance and ScreeningThis section describes the Lot Acceptance Testing (LAT) and screening on the HAS2 FM devices. All tests on device level must be performed on screened devices (see Table 9 on page 7)Wafer Lot AcceptanceThis is the acceptance of the silicon wafer lot. This must be done on every wafer lot that is used for the assembly of flight models.Table 6.Test Test Method Number of Devices Test Condition Test Location Wafer processingdata reviewPID NA NA ON Semiconductor SEM ESCC 21400 4 naked dies NA Test houseTotal dose test ESCC 22900 3 devices42 krad, not to exceed3.6 krad/hr Test house by ON SemiconductorEndurance test MIL-STD-883 Method 1005 6 devices2000h at +125°C Test houseBefore and after total dose test and endurance test:•Electrical measurements before and after at high, low, and room temperature. See Table 18 on page13, Table 19 on page 14 and Table 20 on page 15 of this specification.•Visual inspection before and after•Detailed electro-optical measurements before and after Glass Lot AcceptanceTransmission and reflectance curves that are delivered with each lot must be compared with the specifications in Table 15. Three glass lids are chosen randomly from the lot and measured in detail. The results are compared with Figure 5 on page 26.Package Lot Acceptance•Five packages are chosen randomly from the lot and measured in detail. The results are compared with Figure 2 on page 24.•A solderability test is covered in the assembly lot acceptance tests (Table 7)Table 7. ASSEMBLY LOT ACCEPTANCETest Test Method Number ofDevices Test Condition Test LocationSpecial assembly house inprocess controlAssembly House Bond strength test MIL-STD-883 method 20112D Assembly HouseAssembly house geometrical datareviewReview All CYSolder ability MIL-STD883, method 20033D Test House Terminal strength MIL-STD 883, method 2004Marking permanence ESCC 24800Geometrical measurements PID All CY Temperature cycling MIL-STD 883, method 10105Condition B50 cycles–55°C / +125°CTest House Moisture resistance JEDEC Std. Method A101-B240 h at 85°C / 85%Test HouseTable 7. ASSEMBLY LOT ACCEPTANCETestTest LocationTest ConditionNumber of DevicesTest MethodDPADie shear test MIL-STD-883 method 20194N/A Test House Bond pull testMIL-STD-883 method 2011All wiresTest HouseNOTE:As the glass lid is removed from the packageprior to DPA, the results of the DPA cannot be guaranteed.Before and after the following tests are done:•Electrical measurements conform to Table 18 on page 13 of this specification •Detailed visual inspection •Fine leak test + gross leak testFine- and gross-leak tests must be performed using the following methods:Fine Leak test : MIL-STD-883, Test Method 1014,Condition AGross Leak test : MIL-STD-883, Test Method 1014,Condition CThe required leak rate for fine leak testing is 5x 10−7atms.cm 3/sTable 8. PERIODIC TESTINGTestTest MethodNumber of DevicesTest ConditionTest Location Mechanical shock MIL-STD 883, method 20022 B - 5 shocks, 1500 g – 0.5 ms – ½ sine, 6 axesTest House Mechanical vibration MIL-STD 883, method 20072A - 4 cycles, 20 g 80 to 2000 Hz, 0.06 inch 20 to 80 Hz, 3 axesTest HouseDPADie shear test MIL-STD-883 method 20192N/A Test House Bond pull testMIL-STD-883 method 2011All wiresTest HouseNOTE:As the glass lid is removed from the packageprior to DPA, the results of the DPA cannot be guaranteed.Periodic testing is required every two years. Before and after the following tests are done:•Electrical measurements conform to Table 18 on page 13•Detailed visual inspection •Fine leak test + gross leak testFine- and gross-leak tests must be performed using the following methods:Fine Leak Test : MIL-STD-883, Test Method 1014,Condition AGross Leak Test : MIL-STD-883, Test Method 1014,Condition CThe required leak rate for fine leak testing is 5x 107atms.cm 3/sTable 9. SCREENINGNo.TestTest MethodNumber of DevicesTest Condition Test Location 1HCRT Electrical measurements001-53958AllHT +85°C LT –40°C RT +25°CON Semiconductor2Visual inspection001-49283 + ICD All ON Semiconductor 3Die placement measurements Internal proc.All ON Semiconductor 4XRAYESCC 20900All Test House 5Stabilization bake MIL-STD-883 method 1008All 48h at 125°C Test House 6Fine leak testMIL-STD-883 method 1014AllATest HouseTable 9. SCREENING7Gross leak test MIL-STD-883 method 1014All C Test HouseTest House 8Temperature cycling MIL-STD-883 method 1010All B - 10 cycles–55°C +125°C 9Biased Burn-in ICD All240 h at +125°C ON Semiconductor 10Mobile Particle Detection MIL-STD-883 method 2020All A Test House 11Fine leak test MIL-STD-883 method 1014All A Test House 12Gross leak test MIL-STD-883 method 1014All C Test HouseON Semiconductor 13HCRT Electrical measurements001-53958All HT +85°CLT –40°CRT +25°C 14Final Visual Inspection001-49283 + ICD All ON SemiconductorTABLES AND FIGURESSpecification TablesTable 10. TYPE VARIANT SUMMARYHAS2 Type Variants Engineering Model Flight Model Optical quality (see Optical Quality − Definitions on page 67)Dead pixels10020Bright pixels in FPN image5020Bad pixels in PRNU image15050Bad columns50Bad rows50Bright pixel clusters2 adjacent bright pixels2524 or more adjacent bright pixels100DSNU defects at 22 dec BOL12001000DSNU defects at 22 dec EOL15001250 Particle contaminationFixed particles outside focal plane N/A N/AMobile particles > 20 m m00Fixed particles on focal plane > 20 m m00Mobile particles > 10 m m and < 20 m m2010Fixed particles on focal plane > 10 m m and < 20 m mParticles < 10 m m N/A N/AWafer lot acceptance (see section Wafer Lot Acceptance on page 6)NO YesGlass lot acceptance (see section Glass Lot Acceptance on page 6)NO Yes Assembly lot acceptance (Table 7 on page 6)NO Yes Periodic testing (Table 8 on page 7)NO Yes Screening (Table 9 on page 7)NO Yes Calibration data NO YesVisual Inspection + particle mapping NO YesTable 11. MAXIMUM RATINGSNo.Characteristic Min Typ Max Unit Remarks1Any supply voltage except VDD_RES–0.5 3.3+7.0V2Supply voltage at VDD_RES–0.5 3.3+5.0V 3.3 V for normal operation; up to5V for increased full well capacity.3Voltage on any input terminal–0.5 3.3Vdd + 0.5V4Soldering temperature NA NA260°C Hand soldering only; See Solder-ing Instructions on page 1 5Operating temperature–40NA+85°C6Storage temperature–55NA+125°CStresses exceeding Maximum Ratings may damage the device. Maximum Ratings are stress ratings only. Functional operation above the Recommended Operating Conditions is not implied. Extended exposure to stresses above the Recommended Operating Conditions may affect device reliability.Detailed Specifications − All Type VariantsTable 12. GENERAL SPECIFICATIONSNo.Characteristic Min Typ Max Unit Remarks1Image sensor format N/A1024 x 1024N/A pixels2Pixel size N/A18N/A m m3ADC resolution N/A12N/A bit10-bit accuracy at 5 Msamples/secTable 13. SILICON PARTICLE CONTAMINATION SPECIFICATIONSNo.Characteristic Min Typ Max Unit Remarks1Optical quality: Particle max size N/A N/A20m m See Type Variant Summary onpage 8Table 14. MECHANICAL SPECIFICATIONSNo.Characteristic Min Typ Max Unit Remarks1a Flatness of image area NA7.4NA m m Peak-to-peak at 25 ±3°CSpecified by the foundry over anentire 8-inch wafer 1b Flatness of glass lid NA90150m m Towards ceramic package2Mass7.77.858.0g3Total thickness 3.2 3.3 3.4mm Package + epoxy + glass lid4a Die position, X offset NA NA0.1mm Die in center of cavity4b Die position, Y offset NA NA0.1mm Die in center of cavity5Die position, parallelism vs window Die position, parallelism vs backside –0.10.10.10.1mm6Die position, Y tilt–0.100.1°7Die position, X tilt–0.100.1°8Die – window distance0.250.30.35mmTable 15. GLASS LID SPECIFICATIONSNo.Characteristic Min Typ Max Unit Remarks 1a XY size26.7 x 26.726.8 x 26.826.9 x 26.9mm1b Thickness 1.4 1.5 1.6mmTable 15. GLASS LID SPECIFICATIONSNo.RemarksUnitMaxTypMinCharacteristic2a Spectral range for optical coating ofwindow440NA1100nm2b Reflection coefficient for window NA<0.8<1.3%Over bandwidth indicated in 2a3Optical quality:Scratch max widthScratch max numberDig max sizeDig max number N/A N/A1056025m mTable 16. ENVIRONMENTAL SPECIFICATIONSNo.Characteristic Min Typ Max Unit Remarks1Operating temperature–40NA+85°C2Storage temperature–55NA+125°C Lower storage temperatures (up to–80°C) have been tested and thedevice survives, but this is not afully qualified temperature.3Sensor total dose radiation tolerance N/A42N/A krad (Si)Tested for functionality up to300krad, 42 krad is guaranteed4Sensor SEL threshold with ADC enabled NA NA>110MeV cm3mg-1Equivalent LET valueTable 17. ELECTRICAL SPECIFICATIONSNo Characteristic Min Typ Max Unit Remarks1Total power supply current stand-by1618.521mA2Total power supply current, operational353740mA ADC at 5 MHz sampling ratemeasured3Power supply current to ADC, operational: analog + digital 171921mA ADC at 5 MHz sampling ratemeasured4Power supply current to image core,operational1415.517mA5Input impedance digital input3NA NA M W6Input impedance ADC input3NA NA M W7Output amplifier voltage range 2.2 2.45 2.6V8Output amplifier gain setting 0NA1NA–Nominal 1measured reference9Output amplifier gain setting 1 1.9 2.1 2.3–Nominal 2relative to setting 010Output amplifier gain setting 2 3.8 4.1 4.4–Nominal 4relative to setting 011Output amplifier gain setting 37.27.78.2–Nominal 8relative to setting 012Output amplifier offset setting 00.860.93 1.0V0 decodes to middle value 13Output amplifier offset setting 31 1.30 1.35 1.40V14Output amplifier offset setting 320.430.510.6V15Output amplifier offset setting 630.800.90 1.0V16ADC ladder network resistance NA 1.8NA k W Typical value17ADC differential nonlinearity NA711lsb18ADC integral nonlinearity NA818lsb分销商库存信息: ONSEMINOIH2SM1000S-HHC。
3590S-2-502L;3590S-2-102L;3590S-2-103L;3590S-2-203L;3590S-1-502L;中文规格书,Datasheet资料

Specifi cations are subject to change without notice.Customers should verify actual device performance in their specifi c applications.*RoHS Directive 2002/95/EC Jan. 27, 2003 including annex and RoHS Recast 2011/65/EU June 8, 2011.Stop Strength..............................................................................................................................................................................45 N-cm (64 oz.-in.) minimum Mechanical Angle ...........................................................................................................................................................................................3600 ° +10 °, -0 °Torque (Starting & Running) ................................................................................................................................0.35 N-cm (0.5 oz.-in.) maximum (unsealed) 1.1 N-cm (1.5 oz.-in.) maximum (sealed) Mounting ..............................................................................................................................................................................55-80 N-cm (5-7 lb.-in.) (plastic) 90-113 N-cm (8-10 in.-lb.) (metal)Shaft Runout......................................................................................................................................................................................0.13 mm (0.005 in.) teral Runout ...................................................................................................................................................................................0.20 mm (0.008 in.) T.I.R.Shaft End Play ...................................................................................................................................................................................0.25 mm (0.010 in.) T.I.R.Shaft Radial Play ...............................................................................................................................................................................0.13 mm (0.005 in.) T.I.R.Pilot Diameter Runout .......................................................................................................................................................................0.08 mm (0.003 in.) T.I.R.Backlash ............................................................................................................................................................................................................1.0 ° maximum Weight ........................................................................................................................................................................................................Approximately 19 G Terminals ................................................................................................................................................................................................Solder lugs or PC pins Soldering ConditionManual Soldering...........................................................96.5Sn/3.0Ag/0.5Cu solid wire or no-clean rosin cored wire; 370 °C (700 °F) max. for 3 seconds Wave Soldering ...................................................................................96.5Sn/3.0Ag/0.5Cu solder with no-clean fl ux; 260 °C (500 °F) max. for 5 seconds Wash processes .......................................................................................................................................................................................Not recommended Marking .....................................Manufacturer’s name and part number, resistance value and tolerance, linearity tolerance, wiring diagram, and date code.Ganging (Multiple Section Potentiometers) ......................................................................................................................................................1 cup maximum Hardware ............................................................................................................One lockwasher and one mounting nut is shipped with each potentiometer.NOTE: For Anti-rotation pin add 91 after confi guration dash number. Example: -2 becomes -291 to add AR pin.1At room ambient: +25 °C nominal and 50 % relative humidity nominal, except as noted. 2Consult manufacturer for complete specifi cation details for resistances below 1k ohms.BOLDFACE LISTINGS ARE IN STOCK AND READILY AVAILABLETHROUGH DISTRIBUTION. FOR OTHER OPTIONS CONSULT FACTORY.ROHS IDENTIFIER: L = COMPLIANTRecommended Part Numbers(Printed Circuit)(Solder Lug)(Solder Lug)Resistance (Ω)Resolution (%)3590P-2-102L 3590S-2-102L 3590S-1-102L 1,000.0293590P-2-202L 3590S-2-202L 3590S-1-202L 2,000.0233590P-2-502L 3590S-2-502L 3590S-1-502L 5,000.0253590P-2-103L 3590S-2-103L 3590S-1-103L 10,000.0203590P-2-203L 3590S-2-203L 3590S-1-203L 20,000.0193590P-2-503L 3590S-2-503L 3590S-1-503L 50,000.0133590P-2-104L3590S-2-104L3590S-1-104L100,000.009*Ro H S C O MP L I A N T/Panel Thickness Dimensions(For Bushing Mount Only)1.60 +.08/-.03(.063 +.003/-.001)DIA.ANTI-ROTATION PINAnti-rotation pin hole is shown at six o'clockposition for reference only. The actual location isdetermined by the customer's application. Referto the front view of the potentiometer to see thelocation of the optional A/R pin.Panel thickness and hole diameters arerecommended for best fit. However, customersmay adjust the dimensions to suit their specificapplication.Product DimensionsSpecifi cations are subject to change without notice.Customers should verify actual device performance in their specifi c applications.REV. 06/12 MOUNTING SURFACE-2, -4, -6, -8 Confi gurations-1, -3, -5, -7 Confi gurationsRecommended PCB LayoutHOLE DIAMETER5.08(.200)5.08(.200)6.99(.275)SchematicTOLERANCES: EXCEPT WHERE NOTED.508 .127DECIMALS: .XX ±(.02),.XXX ±(.005)FRACTIONS: ±1/64MMDIMENSIONS:(IN.)Shaft & Bushing Confi gurations(Bushing - DxL, Shaft - D):(-1) Plastic Bushing (3/8 ” x 5/16 ”)and Shaft (.2480 + .001, - .002)(-2) Metal Bushing (3/8 ” x 5/16 ”)and Shaft (.2497 + .0000, - .0009)(-3) Sealed, Plastic Bushing (3/8 ” x 5/16 ”)and Shaft (.2480 + .001, - .002)(-4) Sealed, Metal Bushing (3/8 ” x 5/16 ”)and Shaft (.2497 + .0000, - .0009)(-5) Metric, Plastic Bushing (9 mm x 7.94 mm)and Shaft (6 mm + 0, - .076 mm)(-6) Metric, Metal Bushing (9 mm x 7.94 mm)and Shaft (6 mm + 0, - .023 mm)(-7) Metric, Sealed, Plastic Bushing (9 mm x7.94 mm) and Shaft (6 mm + 0, - .076 mm)(-8) Metric, Sealed, Metal Bushing (9 mm x7.94 mm) and Shaft (6 mm + 0, - .023 mm)Terminal Styles“P” Terminal Style“S” Terminal Style/分销商库存信息:BOURNS3590S-2-502L3590S-2-102L3590S-2-103L 3590S-2-203L3590S-1-502L3590S-2-104L 3590S-1-203L3590S-2-501L3590S-2-202L 3590S-1-503L3590S-2-503L3590S-1-104L 3590S-291-102L3590S-291-203L3590S-291-502L 3590S-1-201L3590S-1-501L3590S-2-101L 3590S-2-201L3590P-1-102L3590P-1-103L 3590P-1-201L3590P-1-502L3590S-1-102L 3590S-1-103L3590S-2-252L3590P-291-501L 3590P-2-102L3590P-2-201L3590P-2-203L 3590P-2-502L3590S-1-202L3590S-6-102L 3590S-6-201L3590S-6-202L3590S-6-203L 3590S-6-501L3590P-1-104L3590S-6-502L 3590S-4-102L3590S-4-103L3590S-4-202L 3590S-4-203L3590S-4-502L3590S-8-102L 3590S-8-103L3590S-8-202L3590P-2-104L 3590P-4-103L3590P-4-202L3590S-6-503L 3590S-6-104L3590S-4-104L3590P-4-503L 3590P-4-104L3590S-2-5023590S-1-102 3590S-1-1033590S-1-1043590S-1-203 3590S-1-5023590S-1-5033590S-2-102 3590S-2-1033590S-2-1043590S-2-203 3590S-2-5033590S-1-2023590S-2-202 3590S-2-501。
FJY3002R;中文规格书,Datasheet资料

TinyBoost™ TinyBuck™ ® TinyLogic TINYOPTO™ TinyPower™ TinyWire™ TruTranslation™ μSerDes™ ® UHC UniFET™ VCX™ Wire™
DISCLAIMER FAIRCHILD SEMICONDUCTOR RESERVES THE RIGHT TO MAKE CHANGES WITHOUT FURTHER NOTICE TO ANY PRODUCTS HEREIN TO IMPROVE RELIABILITY, FUNCTION OR DESIGN. FAIRCHILD DOES NOT ASSUME ANY LIABILITY ARISING OUT OF THE APPLICATION OR USE OF ANY PRODUCT OR CIRCUIT DESCRIBED HEREIN; NEITHER DOES IT CONVEY ANY LICENSE UNDER ITS PATENT RIGHTS, NOR THE RIGHTS OF OTHERS. THESE SPECIFICATIONS DO NOT EXPAND THE TERMS OF FAIRCHILD’S WORLDWIDE TERMS AND CONDITIONS, SPECIFICALLY THE WARRANTY THEREIN, WHICH COVERS THESE PRODUCTS. LIFE SUPPORT POLICY FAIRCHILD’S PRODUCTS ARE NOT AUTHORIZED FOR USE AS CRITICAL COMPONENTS IN LIFE SUPPORT DEVICES OR SYSTEMS WITHOUT THE EXPRESS WRITTEN APPROVAL OF FAIRCHILD SEMICONDUCTOR CORPORATION. As used herein: 1. Life support devices or systems are devices or systems which, (a) are intended for surgical implant into the body or (b) support or sustain life, and (c) whose failure to perform when properly used in accordance with instructions for use provided in the labeling, can be reasonably expected to result in a significant injury of the user. PRODUCT STATUS DEFINITIONS Definition of Terms Datasheet Identification Advance Information Preliminary Product Status Formative or In Design First Production Definition This datasheet contains the design specifications for product development. Specifications may change in any manner without notice. This datasheet contains preliminary data; supplementary data will be published at a later date. Fairchild Semiconductor reserves the right to make changes at any time without notice to improve design. This datasheet contains final specifications. Fairchild Semiconductor reserves the right to make changes at any time without notice to improve design. This datasheet contains specifications on a product that has been discontinued by Fairchild Semiconductor. The datasheet is printed for reference information only.
BYV32EB-200,118;中文规格书,Datasheet资料
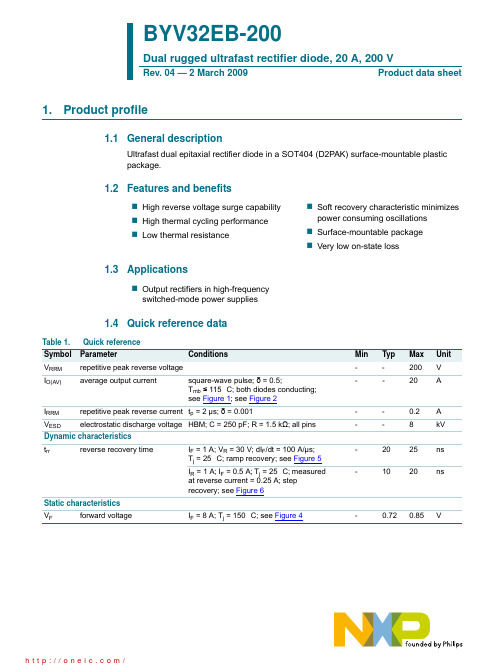
BYV32EB-200Dual rugged ultrafast rectifier diode, 20 A, 200 VRev. 04 — 2 March 2009Product data sheet 1.Product profile1.1General descriptionUltrafast dual epitaxial rectifier diode in a SOT404 (D2PAK) surface-mountable plasticpackage.1.2Features and benefitsHigh reverse voltage surge capability High thermal cycling performanceLow thermal resistance Soft recovery characteristic minimizes power consuming oscillationsSurface-mountable packageVery low on-state loss1.3ApplicationsOutput rectifiers in high-frequencyswitched-mode power supplies1.4Quick reference dataTable 1.Quick referenceSymbol Parameter Conditions Min Typ Max Unit V RRM repetitive peak reverse voltage--200VI O(AV)average output current square-wave pulse; δ=0.5;T mb≤115°C; both diodes conducting;see Figure 1; see Figure 2--20AI RRM repetitive peak reverse current t p=2µs; δ=0.001--0.2AV ESD electrostatic discharge voltage HBM; C = 250 pF; R = 1.5 kΩ; all pins--8kV Dynamic characteristicst rr reverse recovery time I F=1A; V R=30V;dI F/dt=100A/µs;T j=25°C; ramp recovery; see Figure 5-2025nsI R=1A;I F=0.5A;T j=25°C; measuredat reverse current = 0.25 A; steprecovery; see Figure 6-1020nsStatic characteristicsV F forward voltage I F=8A; T j=150°C; see Figure 4-0.720.85V2.Pinning information[1]it is not possible to make a connection to pin 2 of the SOT404 package3.Ordering informationTable 2.Pinning information Pin Symbol Description Simplified outline Graphic symbol1A1anode 1SOT404 (D2PAK)2K cathode [1]3A2anode 2mbKmounting base; cathodemb132sym125Table 3.Ordering information Type number PackageName DescriptionVersion BYV32EB-200D2PAK plastic single-ended surface-mounted package (D2PAK); 3 leads (onelead cropped)SOT4044.Limiting valuesTable 4.Limiting values In accordance with the Absolute Maximum Rating System (IEC 60134).Symbol ParameterConditionsMin Max Unit V RRM repetitive peak reverse voltage-200V V RWM crest working reverse voltage -200V V R reverse voltage DC-200V I O(AV)average output currentsquare-wave pulse; δ=0.5; T mb ≤115°C; both diodes conducting; see Figure 1; see Figure 2-20A I FRM repetitive peak forward currentδ=0.5; t p =25µs; T mb ≤115°C; per diode -20A I FSMnon-repetitive peak forward currentt p =8.3ms; sine-wave pulse; T j(init)=25°C; per diode-137A t p =10ms; sine-wave pulse; T j(init)=25°C;per diode-125A I RRM repetitive peak reverse currentδ=0.001; t p =2µs -0.2A I RSM non-repetitive peak reverse current t p =100µs-0.2A T stg storage temperature -40150°C T j junction temperature-150°C V ESDelectrostatic discharge voltageHBM; C = 250 pF; R = 1.5 k Ω; all pins -8kV5.Thermal characteristics6.CharacteristicsTable 5.Thermal characteristics Symbol ParameterConditionsMin Typ Max Unit R th(j-mb)thermal resistance from junction to mounting base with heatsink compound; both diodes conducting -- 1.6K/W with heatsink compound; per diode; seeFigure 3-- 2.4K/W R th(j-a)thermal resistance from junction to ambientminimum footprint FR4 board -50-K/WTable 6.Characteristics Symbol Parameter ConditionsMin Typ Max Unit Static characteristicsV F forward voltage I F =8A; T j =150°C; see Figure 4-0.720.85V I F =20A; T j =25°C -1 1.15V I Rreverse currentV R =200V; T j =25°C -630µA V R =200V; T j =100°C-0.20.6mADynamic characteristics Q r recovered charge I F =2A; V R =30V;dI F /dt =20A/µs -812.5nC t rrreverse recovery timeI F =1A; V R =30V;dI F /dt =100A/µs; ramp recovery; T j =25°C; see Figure 5-2025ns I F =0.5A; I R =1A; measured at reverse current = 0.25 A; step recovery; T j =25°C; see Figure 6-1020nsV FRforward recovery voltageI F =1A; dI F /dt =10A/µs; see Figure 7--1V7.Package outlinePlastic single-ended surface-mounted package (D2PAK); 3 leads (one lead cropped)SOT404Fig 8.Package outline SOT404 (D2PAK)8.Revision historyTable 7.Revision historyDocument ID Release date Data sheet status Change notice SupersedesBYV32EB-200_420090302Product data sheet-BYV32E_SERIES_3 Modifications:•The format of this data sheet has been redesigned to comply with the new identityguidelines of NXP Semiconductors.•Legal texts have been adapted to the new company name where appropriate.•Package outline updated.•Type number BYV32EB-200 separated from data sheet BYV32E_SERIES_3BYV32E_SERIES_320010301Product specification-BYV32E_SERIES_2 BYV32E_SERIES_219980701Product specification-BYV32EB_SERIES_1 BYV32EB_SERIES_119960801Product specification--9.Legal information9.1Data sheet status[1]Please consult the most recently issued document before initiating or completing a design.[2]The term 'short data sheet' is explained in section "Definitions".[3]The product status of device(s) described in this document may have changed since this document was published and may differ in case of multiple devices. The latest product status information is available on the Internet at URL .9.2DefinitionsDraft — The document is a draft version only. The content is still under internal review and subject to formal approval, which may result in modifications or additions. NXP Semiconductors does not give any representations or warranties as to the accuracy or completeness ofinformation included herein and shall have no liability for the consequences of use of such information.Short data sheet — A short data sheet is an extract from a full data sheet with the same product type number(s) and title. A short data sheet is intended for quick reference only and should not be relied upon to contain detailed and full information. For detailed and full information see the relevant full data sheet, which is available on request via the local NXP Semiconductors sales office. In case of any inconsistency or conflict with the short data sheet, the full data sheet shall prevail.9.3DisclaimersGeneral — Information in this document is believed to be accurate andreliable. However, NXP Semiconductors does not give any representations or warranties, expressed or implied, as to the accuracy or completeness of such information and shall have no liability for the consequences of use of such information.Right to make changes — NXP Semiconductors reserves the right to make changes to information published in this document, including withoutlimitation specifications and product descriptions, at any time and without notice. This document supersedes and replaces all information supplied prior to the publication hereof.Suitability for use — NXP Semiconductors products are not designed, authorized or warranted to be suitable for use in medical, military, aircraft, space or life support equipment, nor in applications where failure ormalfunction of an NXP Semiconductors product can reasonably be expected to result in personal injury, death or severe property or environmentaldamage. NXP Semiconductors accepts no liability for inclusion and/or use of NXP Semiconductors products in such equipment or applications and therefore such inclusion and/or use is at the customer’s own risk.Applications — Applications that are described herein for any of these products are for illustrative purposes only. NXP Semiconductors makes no representation or warranty that such applications will be suitable for the specified use without further testing or modification.Quick reference data — The Quick reference data is an extract of theproduct data given in the Limiting values and Characteristics sections of this document, and as such is not complete, exhaustive or legally binding. Limiting values — Stress above one or more limiting values (as defined in the Absolute Maximum Ratings System of IEC 60134) may cause permanent damage to the device. Limiting values are stress ratings only and operation of the device at these or any other conditions above those given in theCharacteristics sections of this document is not implied. Exposure to limiting values for extended periods may affect device reliability.Terms and conditions of sale — NXP Semiconductors products are sold subject to the general terms and conditions of commercial sale, as published at /profile/terms , including those pertaining to warranty, intellectual property rights infringement and limitation of liability, unlessexplicitly otherwise agreed to in writing by NXP Semiconductors. In case of any inconsistency or conflict between information in this document and such terms and conditions, the latter will prevail.No offer to sell or license — Nothing in this document may be interpreted or construed as an offer to sell products that is open for acceptance or the grant, conveyance or implication of any license under any copyrights, patents or other industrial or intellectual property rights.9.4TrademarksNotice: All referenced brands, product names, service names and trademarks are the property of their respective owners.10.Contact informationFor more information, please visit: For sales office addresses, please send an email to: salesaddresses@Document status [1][2]Product status [3]DefinitionObjective [short] data sheet Development This document contains data from the objective specification for product development.Preliminary [short] data sheet Qualification This document contains data from the preliminary specification.Product [short] data sheetProductionThis document contains the product specification.11.Contents1Product profile. . . . . . . . . . . . . . . . . . . . . . . . . . .11.1General description . . . . . . . . . . . . . . . . . . . . . .11.2Features and benefits. . . . . . . . . . . . . . . . . . . . .11.3Applications . . . . . . . . . . . . . . . . . . . . . . . . . . . .11.4Quick reference data . . . . . . . . . . . . . . . . . . . . .12Pinning information. . . . . . . . . . . . . . . . . . . . . . .23Ordering information. . . . . . . . . . . . . . . . . . . . . .24Limiting values. . . . . . . . . . . . . . . . . . . . . . . . . . .35Thermal characteristics . . . . . . . . . . . . . . . . . . .46Characteristics. . . . . . . . . . . . . . . . . . . . . . . . . . .47Package outline. . . . . . . . . . . . . . . . . . . . . . . . . .68Revision history. . . . . . . . . . . . . . . . . . . . . . . . . .79Legal information. . . . . . . . . . . . . . . . . . . . . . . . .89.1Data sheet status . . . . . . . . . . . . . . . . . . . . . . . .89.2Definitions. . . . . . . . . . . . . . . . . . . . . . . . . . . . . .89.3Disclaimers. . . . . . . . . . . . . . . . . . . . . . . . . . . . .89.4Trademarks. . . . . . . . . . . . . . . . . . . . . . . . . . . . .810Contact information. . . . . . . . . . . . . . . . . . . . . . .8Please be aware that important notices concerning this document and the product(s)described herein, have been included in section ‘Legal information’.© NXP B.V.2009.All rights reserved.For more information, please visit: For sales office addresses, please send an email to: salesaddresses@分销商库存信息: NXPBYV32EB-200,118。
PBRP123YT,215;中文规格书,Datasheet资料

Min
VCBO
collector-base voltage
open emitter
-
VCEO
collector-emitter voltage
open base
-
VEBO
emitter-base voltage
open collector
-
VI
input voltage
positive
-
negative
δ=1 0.75
0.50 0.33
0.20
0.10
0.05
0.02 0.01
10
006aab002
10−1
10−5
10−4
10−3
10−2
10−1
1
10
102
103
tp (s)
Ceramic PCB, Al2O3 standard footprint
Fig 4. Transient thermal impedance from junction to ambient as a function of pulse duration for SOT23 (TO-236AB); typical values
Version SOT23
4. Marking
Table 4. Marking codes Type number PBRP123YT
VLF4012AT-4R7M1R1;VLF4012AT-100MR79;VLF4012AT-3R3M1R3;VLF4012AT-2R2M1R5;中文规格书,Datasheet资料
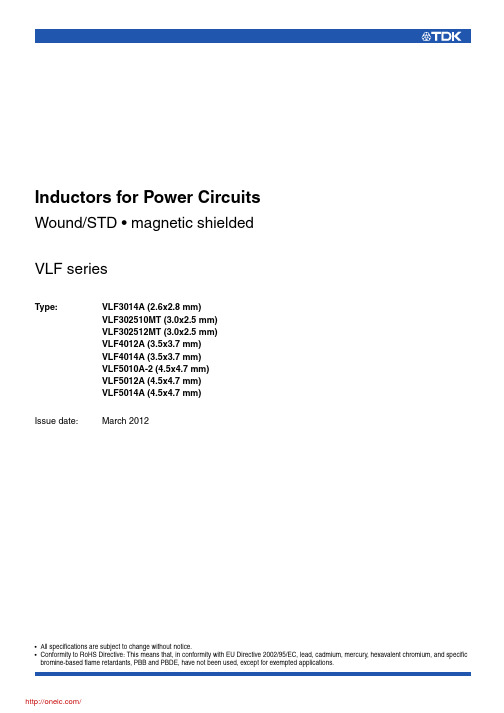
Inductance tolerance(%) ±30 ±20 ±20 ±20 ±20 ±20 ±20
Test frequency (kHz) 100 100 100 100 100 100 100
DC resistance( ) max. 0.054 0.1 0.15 0.2 0.31 0.46 1.20 typ. 0.047 0.091 0.13 0.1R7
2.8±0.2
1.4max. Dimensions in mm
RECOMMENDED PC BOARD PATTERN
1.2 2.1 3.4 Dimensions in mm
Inductance [at 1/2 Idc1]3 (µH) 1 2.2 3.3 4.7 6.8 10 22
• All specifications are subject to change without notice.
/
001-04 / 20120310 / e531_vlf
(3/17)
Inductors for Power Circuits Wound/STD • Magnetic Shielded
Part No. VLF3014AT-1R0N1R7 VLF3014AT-2R2M1R2 VLF3014AT-3R3M1R0 VLF3014AT-4R7MR90 VLF3014AT-6R8MR72 VLF3014AT-100MR59 VLF3014AT-220MR37
1
SHAPES AND DIMENSIONS
VLF-MT Series VLF302510MT
With the VLF302510MT Series, a DC to DC converter with topclass voltage conversion efficiency for similar size products was achieved by optimizing the magnetic material and configuration. These products are optimal for use as choke coils in switching power supplies such as those in mobile devices requiring spacesaving design. FEATURES • Miniature size Mount area: 3.02.5mm Low profile: 1.0mm max. height • Generic use for portable DC to DC converter line. • High magnetic shield construction should actualize high resolution for EMC protection. • The products contain no lead and also support lead-free soldering. • The products is halogen-free. • It is a product conforming to RoHS directive. APPLICATIONS Smartphones, cellular phones, DSCs, DVCs, HDDs, LCD displays, compact power supply modules, etc. SHAPES AND DIMENSIONS
PUMH20,115;中文规格书,Datasheet资料

1.Product profile1.1General descriptionNPN/NPN resistor-equipped transistors.1.2FeaturesBuilt-in bias resistors Simplifies circuit design Reduces component countReduces pick and place costs1.3ApplicationsLow current peripheral driver Control of IC inputsReplaces general-purpose transistors in digital applications1.4Quick reference dataPEMH20; PUMH20NPN/NPN resistor-equipped transistors; R1 = 2.2 k Ω, R2 = 2.2 k ΩRev. 04 — 15 November 2009Product data sheetTable 1.Product overviewType number Package NPN/PNP complement PNP/PNP complement NXPJEITA PEMH20SOT666-PEMD20PEMB20PUMH20SOT363SC-88PUMD20PUMB20Table 2.Quick reference data Symbol ParameterConditions Min Typ Max Unit V CEO collector-emitter voltage open base--50V I O output current (DC)--100mA R1bias resistor 1 (input) 1.54 2.2 2.86k ΩR2/R1bias resistor ratio0.811.22.Pinning information3.Ordering information4.Marking[1]* = -: made in Hong Kong * = p: made in Hong Kong * = t: made in Malaysia * = W: made in ChinaTable 3.PinningPin Description Simplified outlineSymbol1GND (emitter) TR12input (base) TR13output (collector) TR24GND (emitter) TR25input (base) TR26output (collector) TR1001aab555645132sym063Table 4.Ordering informationType number Package NameDescriptionVersion PEMH20-plastic surface mounted package; 6 leads SOT666PUMH20SC-88plastic surface mounted package; 6 leadsSOT363Table 5.Marking codesType numberMarking code [1]PEMH206K PUMH20H7*5.Limiting valuesTable 6.Limiting valuesIn accordance with the Absolute Maximum Rating System (IEC 60134).Symbol Parameter Conditions Min Max UnitPer transistorV CBO collector-base voltage open emitter-50VV CEO collector-emitter voltage open base-50VV EBO emitter-base voltage open collector-10VV I input voltagepositive-+12Vnegative-−10VI O output current (DC)-100mAI CM peak collector current-100mAP tot total power dissipation T amb≤ 25 °CSOT363[1]-200mWSOT666[1][2]-200mW T stg storage temperature−65+150°CT j junction temperature-150°CT amb ambient temperature−65+150°CPer deviceP tot total power dissipation T amb≤ 25 °CSOT363[1]-300mWSOT666[1][2]-300mW[1]Device mounted on a FR4 printed-circuit board, single-sided copper, tin-plated and standard footprint.[2]Reflow soldering is the only recommended soldering method.6.Thermal characteristics[1]Device mounted on a FR4 printed-circuit board, single-sided copper, tin-plated and standard footprint.[2]Reflow soldering is the only recommended soldering method.7.CharacteristicsTable 7.Thermal characteristics Symbol ParameterConditionsMinTypMaxUnitPer transistorR th(j-a)thermal resistance from junction to ambient in free air SOT363[1]--625K/W SOT666[1][2]--625K/WPer device R th(j-a)thermal resistance from junction to ambient in free air SOT363[1]--416K/W SOT666[1][2]--416K/WTable 8.CharacteristicsT amb = 25 °C unless otherwise specified.Symbol ParameterConditions Min Typ Max Unit Per transistorI CBO collector-base cut-off currentV CB = 50 V; I E = 0 A --100nA I CEOcollector-emitter cut-off current V CE = 30 V; I B = 0 A --1μA V CE = 30 V; I B = 0 A; T j =150°C --50μA I EBO emitter-base cut-off current V EB = 5 V; I C = 0 A --2mAh FE DC current gain V CE = 5 V; I C = 20 mA 30--V CEsat collector-emitter saturation voltage I C = 10 mA; I B = 0.5 mA --150mV V I(off)off-state input voltage V CE = 5 V; I C = 1 mA - 1.20.5V V I(on)on-state input voltage V CE = 0.3 V; I C = 20 mA2 1.6-V R1bias resistor1 (input) 1.54 2.2 2.86k ΩR2/R1bias resistor ratio 0.81 1.2C ccollector capacitanceV CB = 10 V; I E = i e = 0 A; f =1MHz -- 2.5pF8.Package outline9.Packing informationTable 9.Packing methodsThe indicated -xxx are the last three digits of the 12NC ordering code.[1]Type number Package Description Packing quantity30004000800010000 PEMH20SOT666 2 mm pitch, 8 mm tape and reel---315-4 mm pitch, 8 mm tape and reel--115--PUMH20SOT363 4 mm pitch, 8 mm tape and reel; T1[2]-115---1354 mm pitch, 8 mm tape and reel; T2[3]-125---165[1]For further information and the availability of packing methods, see Section12.[2]T1: normal taping[3]T2: reverse taping10.Revision historyTable 10.Revision historyDocument ID Release date Data sheet status Change notice SupersedesPEMH20_PUMH20_420091115Product data sheet-PEMH20_PUMH20_3 Modifications:•This data sheet was changed to reflect the new company name NXP Semiconductors,including new legal definitions and disclaimers. No changes were made to the technicalcontent.•Figure 5 “Package outline SOT363 (SC-88)”: updatedPEMH20_PUMH20_320050214Product data sheet-PUMH20_2PUMH20_220040414Product specification-PUMH20_1PUMH20_120031016Product specification--11.Legal information11.1Data sheet status[1]Please consult the most recently issued document before initiating or completing a design. [2]The term ‘short data sheet’ is explained in section “Definitions”.[3]The product status of device(s) described in this document may have changed since this document was published and may differ in case of multiple devices. The latest product status information is available on the Internet at URL .11.2DefinitionsDraft — The document is a draft version only. The content is still under internal review and subject to formal approval, which may result in modifications or additions. NXP Semiconductors does not give any representations or warranties as to the accuracy or completeness ofinformation included herein and shall have no liability for the consequences of use of such information.Short data sheet — A short data sheet is an extract from a full data sheet with the same product type number(s) and title. A short data sheet is intended for quick reference only and should not be relied upon to contain detailed and full information. For detailed and full information see the relevant full data sheet, which is available on request via the local NXP Semiconductors sales office. In case of any inconsistency or conflict with the short data sheet, the full data sheet shall prevail.11.3DisclaimersGeneral — Information in this document is believed to be accurate andreliable. However, NXP Semiconductors does not give any representations or warranties, expressed or implied, as to the accuracy or completeness of such information and shall have no liability for the consequences of use of such information.Right to make changes — NXP Semiconductors reserves the right to make changes to information published in this document, including withoutlimitation specifications and product descriptions, at any time and without notice. This document supersedes and replaces all information supplied prior to the publication hereof.Suitability for use — NXP Semiconductors products are not designed, authorized or warranted to be suitable for use in medical, military, aircraft, space or life support equipment, nor in applications where failure ormalfunction of an NXP Semiconductors product can reasonably be expected to result in personal injury, death or severe property or environmentaldamage. NXP Semiconductors accepts no liability for inclusion and/or use of NXP Semiconductors products in such equipment or applications and therefore such inclusion and/or use is at the customer’s own risk.Applications — Applications that are described herein for any of these products are for illustrative purposes only. NXP Semiconductors makes no representation or warranty that such applications will be suitable for the specified use without further testing or modification.Limiting values — Stress above one or more limiting values (as defined in the Absolute Maximum Ratings System of IEC 60134) may cause permanent damage to the device. Limiting values are stress ratings only and operation of the device at these or any other conditions above those given in theCharacteristics sections of this document is not implied. Exposure to limiting values for extended periods may affect device reliability.Terms and conditions of sale — NXP Semiconductors products are sold subject to the general terms and conditions of commercial sale, as published at /profile/terms , including those pertaining to warranty, intellectual property rights infringement and limitation of liability, unlessexplicitly otherwise agreed to in writing by NXP Semiconductors. In case of any inconsistency or conflict between information in this document and such terms and conditions, the latter will prevail.No offer to sell or license — Nothing in this document may be interpreted or construed as an offer to sell products that is open for acceptance or the grant, conveyance or implication of any license under any copyrights, patents or other industrial or intellectual property rights.Export control — This document as well as the item(s) described herein may be subject to export control regulations. Export might require a prior authorization from national authorities.Quick reference data — The Quick reference data is an extract of theproduct data given in the Limiting values and Characteristics sections of this document, and as such is not complete, exhaustive or legally binding.11.4TrademarksNotice: All referenced brands, product names, service names and trademarks are the property of their respective owners.12.Contact informationFor more information, please visit: For sales office addresses, please send an email to: salesaddresses@Document status [1][2]Product status [3]DefinitionObjective [short] data sheet Development This document contains data from the objective specification for product development. Preliminary [short] data sheet Qualification This document contains data from the preliminary specification. Product [short] data sheetProductionThis document contains the product specification.13.Contents1Product profile. . . . . . . . . . . . . . . . . . . . . . . . . . 11.1General description . . . . . . . . . . . . . . . . . . . . . 11.2Features. . . . . . . . . . . . . . . . . . . . . . . . . . . . . . 11.3Applications . . . . . . . . . . . . . . . . . . . . . . . . . . . 11.4Quick reference data . . . . . . . . . . . . . . . . . . . . 12Pinning information. . . . . . . . . . . . . . . . . . . . . . 23Ordering information. . . . . . . . . . . . . . . . . . . . . 24Marking. . . . . . . . . . . . . . . . . . . . . . . . . . . . . . . . 25Limiting values. . . . . . . . . . . . . . . . . . . . . . . . . . 36Thermal characteristics . . . . . . . . . . . . . . . . . . 47Characteristics. . . . . . . . . . . . . . . . . . . . . . . . . . 48Package outline. . . . . . . . . . . . . . . . . . . . . . . . . 69Packing information . . . . . . . . . . . . . . . . . . . . . 610Revision history. . . . . . . . . . . . . . . . . . . . . . . . . 711Legal information. . . . . . . . . . . . . . . . . . . . . . . . 811.1Data sheet status . . . . . . . . . . . . . . . . . . . . . . . 811.2Definitions. . . . . . . . . . . . . . . . . . . . . . . . . . . . . 811.3Disclaimers. . . . . . . . . . . . . . . . . . . . . . . . . . . . 811.4Trademarks. . . . . . . . . . . . . . . . . . . . . . . . . . . . 812Contact information. . . . . . . . . . . . . . . . . . . . . . 813Contents. . . . . . . . . . . . . . . . . . . . . . . . . . . . . . . 9Please be aware that important notices concerning this document and the product(s)described herein, have been included in section ‘Legal information’.© NXP B.V.2009.All rights reserved.For more information, please visit: For sales office addresses, please send an email to: salesaddresses@分销商库存信息: NXPPUMH20,115。
SQT-103-01-F-D;SQT-106-01-LM-D;SQT-110-03-F-D;SQT-120-01-F-S;中文规格书,Datasheet资料
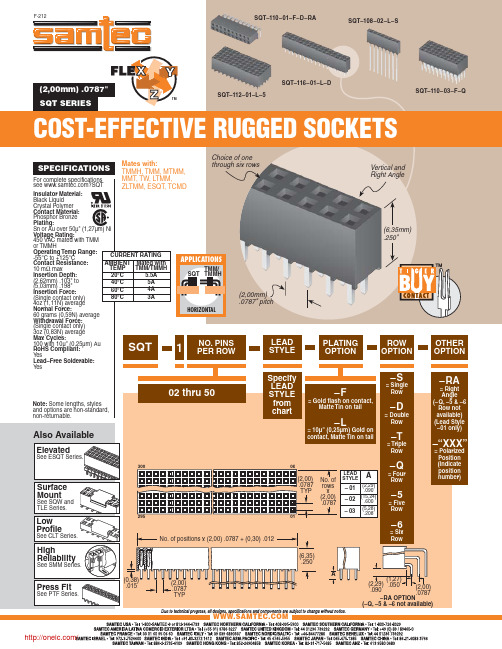
SPECIFICATIONS
For complete specifications see ?SQT
Mates with: TMMH, TMM, MTMM, MMT, TW, LTMM, ZLTMM, ESQT, TCMD
Choice of one through six rows
SQT-106-01-LM-D SQT-112-01-F-D SQT-110-01-L-Q
SQT-110-03-F-D SQT-107-01-L-T SQT-125-01-F-D
(2,29) .050 .090
(2,00) .0787
–RA OPTION
(–Q, –5 & –6 not available)
/
分销商库存信息:
SAMTEC SQT-103-01-F-D SQT-120-01-F-S SQT-110-01-LM-Q SQT-116-01-S-D
TMM/ SQT TMMH
HORIZONTAL
(2,00mm) .0787" pitch
1
NO. PINS PER ROW
LEAD STYLE
(6,35mm) .250"
PLATING OPTION
ROW OPTION
Note: Some lengths, styles and options are non-standard, non-returnable.
20°C
5.5A
(2,62mm) .103" to (5,03mm) .198" Insertion Force: (Single contact only)
40°C
5A
60°C
ESW105,ESW108,ESW105-ML,ESW108-ML,ESW105-SL,ESW108-SL, 规格书,Datasheet 资料

U C T I N F O R M A T I O N B &B E L E C T R O N I C SESW105 and ESW108 Series5 & 8 Port,Ultra Compact Industrial Ethernet SwitchesFunctional DescriptionDesigned to fit many applications, theESW105 and ESW108 series are more than just an Ethernet switch with a great low pricing. They are plug-and-play industrial Ethernet Switches with an ultra compact IP30 DIN rail case, 6 way mountable panel brackets, LEDs for Power, (Link / Speed / Activity for each port), 12 to 36 VDC and 10 to 24 VAC power inputs with removable terminal blocks. These switches are perfect for any applications that require special protection from hash environments.Choose a switch with five or eight copper ports, or a combination of copper and fiber ports. Multi-mode fiber models extend range up to 2 km. Single-mode fiber models extend range up to 20 km. All models require an external power supply (sold separately).The switch ships with 4 panel mount clips giving the user 6 different ways to panel mount the unit.Features✓ Designed to meet (Heavy) IndustrialEnvironments - EN61000-6-2 Certifications ✓ Ultra Compact design - Less than 1 inch wide ✓ Shock, Vibration, Free Fall Tested ✓ LC Single and Multi mode fiber ports ✓ 10/100M, full/half duplex, MDI/MDI-X (Auto-negotiate)✓ Supports IEEE 802.3, 802.3u, and 802.3x standards ✓ Industrial IP30 rated DIN rail case with 6different Panel mount options ✓ Dual power inputs, 12 to 36 VDC and 10 to 24 VAC ✓ 2K MAC addressesWe also offer a full line of Fiber Optic and RJ-45Patch CablesU C T I N F O R M A T I O N B &B E L E C T R O N SpecificationsTechnologyStandards:IEEE802.3, 802.3u, 802.3xProcessing Type: Store and forward with IEEE802.3x full duplex, non-blocking flow control Flow Control:IEEE802.3x flow control, back pressure flow control Packet buffer memory: 64K bytesAddress Table Size 2K MAC AddressesInterfaceRJ45 Ports: 10/100BaseT(X) auto negation, Full/Half duplex, auto MDI/MD-X Fiber Ports: 100BaseFX, (multi-mode or single–mode with LC connectors) LED Indicators: Power, (Link / Speed / Activity for each port)Fiber OpticsFiber Type Distance Wavelength Transmit PowerReceive Sensitivity Multi-mode 2 km 1310 nm Neg. 23.5 to Neg. 14 dBm ≤ Neg. 35 dBm Single-mode 20 km 1310 nmNeg. 15 to Neg. 8 dBm≤ Neg. 35 dBmPowerEnvironmentalInput Voltage12 to 36 VDC and 10 to 24 VAC Op. Temperature -10 to 60 C (14 to 140 F) Power Consumption 4.00 W Max Storage Temperature -40 to 80 C (-40 to 176 F)Humidity 10 to 95% Non-condensing Input Connection Removable Terminal Block MTBF200,000 hoursProtection Reverse Polarity Protection MTBF Calculation Parts count reliability predictionMechanicalRegulatory ApprovalsEnclosureIP30 DIN mount metal case CE, FCC, Dimensions (5 ports)H 100mm x W 25mm x D 75mm ( 3.94in x 0.98in x 2.95in) RoHS Dimensions (8 ports)H 145mm x W 24mm x D 75mm (5.71in X 0.94in x 2.95in)Installation35 mm DIN or 6 way panel mountU C T I N F O R M A T I O N B &B E L E C T R O NESW108-xx SeriesESW105-xx Series。
AD9273BSVZ-50;AD9273BSVZ-25;AD9273BBCZ-25;AD9273BSVZ-40;AD9273BBCZ-40;中文规格书,Datasheet资料

/
CLK+ CLK–
AD9273 TABLE OF CONTENTS
Features .............................................................................................. 1 Applications ....................................................................................... 1 General Description ......................................................................... 1 Functional Block Diagram .............................................................. 1 Revision History ............................................................................... 2 Product Highlights ........................................................................... 3 Specifications..................................................................................... 4 AC Specifications.......................................................................... 4 Digital Specifications ................................................................... 8 Switching Specifications .............................................................. 9 ADC Timing Diagrams ................................................................. 10 Absolute Maximum Ratings.......................................................... 11 Thermal Impedance ................................................................... 11 ESD Caution ................................................................................ 11 Pin Configuration and Function Descriptions ........................... 12 Typical Performance Characteristics ........................................... 15 Equivalent Circuits ......................................................................... 19 Theory of Operation ...................................................................... 21 Ultrasound .................................................................................. 21 Channel Overview ..................................................................... 22 Input Overdrive .......................................................................... 25 CW Doppler Operation............................................................. 25 TGC Operation ........................................................................... 27 ADC ............................................................................................. 31 Clock Input Considerations ...................................................... 31 Serial Port Interface (SPI) .............................................................. 38 Hardware Interface..................................................................... 38 Memory Map .................................................................................. 40 Reading the Memory Map Table .............................................. 40 Reserved Locations .................................................................... 40 Default Values ............................................................................. 40 Logic Levels ................................................................................. 40 Outline Dimensions ....................................................................... 44 Ordering Guide .......................................................................... 45
Z515中文资料(Intel)中文数据手册「EasyDatasheet - 矽搜」
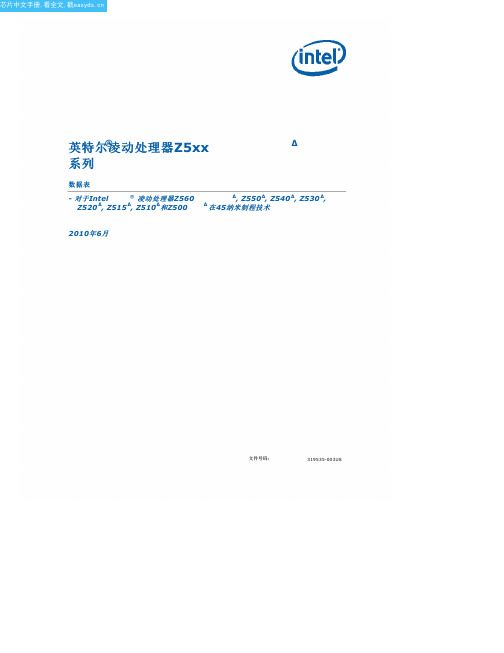
UNLESS O THERW ISE AGREED IN W RITING BY INTEL, THE INTEL PRO DUCTS ARE NO T DESIGNED NO R INTENDED FO R ANY APPLICATIO N IN W HICH THE FAILURE O F THE INTEL PRO DUCT CO ULD CREATE A SITUATIO N W HERE PERSO NAL INJURY O R DEATH MAY O CCUR.
Contact your local Intel sales office or your distributor to obtain the latest specifications and before placing your product order. Copie s of docum ents which have an orde r num be r and are re fere nce d in this docum ent, or othe r Inte l lite rature , m ay be obtaine d
EV2011;中文规格书,Datasheet资料

ContentsSection Page No.Introduction1Functional Description1Contents2EV2011 Connections2EV2011 Configuration2Installing the User Interface Program3Using the EV2011 Program3Main Menu3Output Control Screen4Monitor Screen4Display Program Screen6Data Logging7Measure V OS Screen8Appendix A:AP11 User's Guide9Appendix B:Troubleshooting10Appendix C:EV2011 Schematic11 IntroductionThe bq2011Gas Gauge IC provides battery capacity monitoring in a single16-pin SOIC or DIP package.The EV2011Evaluation Board provides a useful means to test bq2011functionality and easily interface with the de-vice over the RS-232port of a PC.The bq2011features:n Battery capacity monitoring functionsn LED display of available chargen DQ serial I/O port communications functions Functional DescriptionThe EV2011provides functional evaluation of the bq2011 IC on a PCB.The actual implementation of a bq2011-based design will be significantly smaller in size.See the bq2011data sheet(July1994C or later)for bq2011 specifications.Power SourceThe bq2011derives its V CC from either an external source or from the battery connected to the BAT+(J1) and BAT–(J2)terminal blocks.Refer to Table4in Us-ing the bq2010—A Tutorial for Gas Gauging for the proper size of R16as part of the V CC regulation.The EV2011Evaluation Board is shipped with a301KΩre-sistor for R16.Current PathThe bq2011uses a sense resistor(R15)on the negative terminal of the battery to measure charge and discharge of the battery.This resistor may be changed if necessary.The system load is connected between the BAT+(J1)and RET–(J2)terminal blocks(see the schematic in AppendixC).Parameter ProgrammingThe EV2011is programmed by the MODE and PFC pro-gramming pins.The programming pins determine:n Programmed full countn Scale factorn Display mode1EV2011Gas Gauge EvaluationBoard 12/96Rev.C BoardEV2011 ContentsEach package contains the following items:1EV2011 PC BoardThis includes the bq2011sample,current regulator, programming jumpers,battery divider resistors, and the PC serial port interface.1EV2011 DQ/RS-232 Cable1EV2011 (v2.0) User Interface Program Diskette This program runs on any AT-compatible computer equipped with a standard RS-232(COM1,COM2, COM3,or COM4)serial port,and provides the user with a complete menu-driven system to control, monitor,and log data from the EV2011Evaluation Board.The User Interface Program communicates with the bq2011over the DQ serial I/O port using the RS-232interface.Please check to make sure that all items are present and in good condition.If you have any problems,please con-tact your Benchmarq representative or call Benchmarq at214-407-0011.EV2011 ConnectionsThe connections for the EV2011are described below. Please refer to the attached schematic in conjunction with these descriptions.JP1–JP8Battery cell divider.JP1-JP6are usedto divide the battery voltage by5to10.JP7and JP8are user-definable,but areconfigured for11and12cells on thisboard.JP9V CC supply.This jumper is used to se-lect the V CC supply for the bq2011.WhenJP9is on B(near Q1),the supply is takenfrom the BAT+input and is regulated bythe bq2011and Q1.When JP9is on L(near D12),the V CC supply is provided byLBAT+.If V CC is supplied by LBAT+,itmust not exceed the specified V CC voltagerange in the bq2011data sheet.JP11PFC programming pins.This jumpercan be set low,high impedance,or high.Ifthe jumper is between the middle pin andlow,PFC is set low.If the jumper is re-moved,the PFC is high impedance,or Z.If the jumper is between the middle pinand high,PFC is set high.JP10MODE selection jumper.If the jumperis between the middle pin and V CC,thedisplay mode is relative.If the jumper isbetween the middle pin and MODE,thedisplay mode is absolute.If the jumper isremoved,no display is available.DSP Display input(DISP pin).DSP is con-nected in parallel with the push-buttonswitch S1provided on the EV2011board.An external switch configuration can bemade using DSP.When the EV2011isfloating and detects charging or dis-charging,the LED outputs are active toreflect the charge state.When the DISPinput is pulled low,the LEDs reflects thecharge state.EV2011 ConfigurationThe EV2011Evaluation Board may be used with or without the DQ/RS-232Interface Program.The Evalua-tion Board should first be configured before connecting the battery or the RS-232cable.Step1Connecting the power supplyThe EV2011can operate from power pro-vided by the battery being monitored orfrom LBAT+.Set the battery divider(JP1–JP8)to the correct number of bat-tery cells prior to connecting the battery.If the bq2011will be powered from thebattery,connect JP9to B.If the bq2011will be powered from an external supply,connect JP9to L.Important:Connectthe battery ONLY after setting JP1-JP8and JP9.Step3Connecting the RS-232cableConnect the cable provided to the serialport of any PC.Please ensure no mem-ory-resident programs use this serialport.Step4Connecting the loadThe external load is connected betweenBAT+and RET-(J2)on the EV2011.Asense resistor(R15)is in series with thenegative terminal of the battery.TheEV2011board is supplied with a0.005,1%3W resistor.Please ensure that thedischarge load does not exceed the V SRspecification for the bq2011.R15may bechanged to a different-value resistor.2Rev.C Board EV2011Installing the User Interface ProgramThe User Interface Program(named“EV2011”)runs on any PC-compatible computer.The program may be run from the disk provided,or it may be installed on any di-rectory on the computer's hard disk.To run the program from the hard disk,simply copy all the files from the disk supplied to the hard disk.All the files should re-side in the same directory.The User Interface Program installs a driver to control the DQ/RS-232interface.This driver asks which COM port is connected to the EV2011Evaluation board.If communication is not established with the EV2011 board,the Main Menu does not appear.Please refer to Appendix B(Troubleshooting)if the program does not establish communication with the EV2011.The EV2011uses the PC-AT real-time clock to provide the proper bit timing for serial communication with the bq2011.The modem control lines are used as the single-wire serial interface to the bq2011.Any TSR that uses the PC real-time clock affects the operation of the EV2011.For proper operation,the EV2011should not be operated from a DOS shell program.If the PC is a notebook or portable type,it may be config-ured to save battery power by adjusting the clocks ac-cording to the activity under way.Configure the notebook to run in“High Performance”mode for reliable communication between the EV2011and the PC.The EV2011UIP terminates if communication with the EV2011board is lost.Start the User Interface Program as follows:C>EV2011Using the EV2011 ProgramEV2011is a menu-driven program.Almost all of the functions and entries are made by positioning the high-lighted cursor on the function desired and pressing the ENTER key,or by typing a value and then pressing the ENTER key.Key functions are as follows:ARROWkeysUse the arrow keys to move the high-lighted cursor around the screen.ENTERkeyPress the ENTER key to select the valuecurrently being displayed for a parameter,or to perform a function selected by thehighlighted cursor.ESCAPEkeyPress the ESCAPE key to escape from anyfunction back to the main menu,or to es-cape from any parameter value screen backto the menu displaying that parameter.F3key Press the F3key to display a help file forthe selected function or parameter. Main MenuThe Main Menu appears after the EV2011program has started.If this menu does not appear,communication with the EV2011has not been established;please refer to Appendix B(Troubleshooting)if the EV2011does not display the Main Menu.The Main Menu shows six functions that may be activated;see e the cursor keys(arrow keys)to position the highlighted cursor over the function to be activated and press the ENTER key.For help,press the F3key,and a help note about the function appears.Press the ESCAPE key to exit from the EV2011program.3EV2011Rev.C BoardBenchmarq BQ2011Evaluation Board Main Menu(v2.0)<Initialize><Monitor><Output Control><Data Log><Display Program><Measure Vos>Please enter SR value B in Display Program for Proper OperationESC to exit program F3for HelpFigure 1. Main MenuThe Main Menu functions are as follows:<Initialize>Sends a reset command to the bq2011.<Output Control>Activates a screen from which the LEDs can be controlled.<Monitor>Activates a screen from which the bq2011activity is monitored on a real-time basis. <Data Log>Allows entering a file name to whichbq2011data will be logged,and the log-ging period in seconds.When the log isactivated,the display changes to theMonitor screen with a top display of:Logging Record:xx<Display Program>Activates a screen showing the current program settings for the bq2011.<Measure V OS>This allows the user to determine the ap-parent offset voltage of the bq2011under test.A minimum of2minutes is required to complete the V OS measurement,which has a resolution of±0.15mV per2minutes.Output Control ScreenThis screen controls the bq2011LEDs;see Figure2. Press the space bar to toggle the LED OFF and ON. Pressing the push-button switch activates the display. The bq2011LED output returns to normal on exiting this screen.Monitor ScreenThis screen monitors real-time changes of the bq2011; see Figure 3.The program continually updates the monitor screen.As conditions change,the new values are displayed.Time Time of day in HH:MM:DD,24-hour nota-tion.Empty/Full This indicates the current value for GG inthe TMPGG register of the bq2011.Thecapacity value is giventh steps.Date Current date in MM/DD/YY notation.NAC NAC register values multiplied by thescale value and divided by the sense re-sistor value to give mAH.LMD Last Measured Discharge expressed interms of mAH.This is the8-bit LMD reg-ister value multiplied by the scale valuetimes256and divided by the sense resis-tor to give mAH.Sense Resis-tor ValueThis is the sense resistor value from theProgramming menu.Average V SRCurrentThis is the average battery current.TimeRemainingDuring discharge only,this is the time re-maining at the average current(NAC/Avg.V SR current)DigitalFilter SettingThis is the value of the digital magnitudefilter.Temp Step This is a display of the active tempera-ture step,which ranges from0(for tem-peratures<-30°C)to12for temperatures>80°C).Activity This indicates the charging/dischargingactivity occurring with the battery.CHARGE is displayed if the battery ischarging,while DISCHARGING is dis-played if the battery is being discharged,or if it is idle(no charging taking place).OVERLOAD is displayed if the voltagedrop across the sense resistor exceeds the 4Rev.C BoardBenchmarq BQ2011Evaluation Board Output Control ScreenOutput PinsLED Display LED1:OFF/ON LED2:OFF/ONLED Display LED3:OFF/ON LED4:OFF/ONLED Display LED5:OFF/ONESC to main menuFigure 2. Output Control ScreenEV2011V SR1threshold.Please note that the ap-dependent,and may take some time after the application of a charging current or a discharge load depending on the PFC and scale selected,and the rate of charge or discharge being applied.VSR Step This is the value of the V SR current step as defined in the bq2011data sheet.GG StepThis is the lower four bits of the TMPGG register that correspond to the current NAC value relative to either the LMD or the original programmed full count (as determined by PROG 1-4).The GG step is reported as a step number from 0to 15,with step 0available capac-ity from 0to offull,and 15represent-ing available from full to full.Charge RateIndicates whether the present charge is TRICKLE or FAST depending on thestate of the charge rate (CR)bit in FLGS2.EDVThis is the state of the EDV flag.The EDV flag latches ON if V SB drops below the EDV threshold value.It remains latched until charging is detected,at which time it is cleared.Battery RemovedThis is the state of the battery removed flag.It is set (BRM =yes)if one of the conditions indicating battery removed oc-curs.This flag is reset when the battery is replaced.ValidDischargeThis is the state of the VDQ bit in FLGS1.VDQ =yes if the bq2011is charged until NAC =LMD.VDQ =no indi-cates the present discharge is not valid for LMD update.Full CountThis value is the contents of the Full Count register.This value times 16is the5EV2011Benchmarq BQ2011Evaluation Board Real-Time Monitor ScreenTime:99:99:99EMPTY ****_____FULL Date:99/99/99NAC:99999mAHLMD:99999mAHSense Resistor Value:XXX ΩAvg Vsr Current:±9999mATime remaining:9999min.Digital Filter Setting:+0.50mV=Vsrd -0.40mV=Vsrq Temp Step:XX Activity:XXXXX Vsr Current Step:XX GG Step:XX Charge Rate:XXXX First EDV:XXX Batt.Rem'vd:XXX Valid Discharge:XXXFull Count:XXXBatt.Repl'd:XXXCapacity Inaccurate:XXX Capacity Inaccurate Count:XXXFLGS1:XX X X X _X _FLGS2:X X X X___X C B B C V N E N C D D D N N N O H R R I D /D /R R R R ///V G PM Q U VU210U U U L S1DESC to main menu F1to modify NAC F2to modify LMDFigure 3. Real-Time Monitor ScreenRev.C Boardnumber of times that NAC has counted up to LMD after a valid discharge.Battery Replaced This is the state of the battery replaced flag.It is set(BRP=yes)if the battery valid condition returns after setting the battery removed flag.The battery re-placed flag is cleared if the battery is dis-charged to the EDV1level or if it is charged to NAC=LMD.This flag is set after a EV2011initialization.Capacity Inaccurate This is the state of the capacity inaccu-rate bit in FLGS1.It is set(CI=yes)to indicate that the battery capacity has not been updated during the last64charge cycles.Capacity Inaccurate Count This is the number of charge cycles be-tween an LMD update.This counter is reset to zero when NAC=LMD after a valid LMD update.FLGS1This indicates the present state of theFLGS1resistor.FLGS2This indicates the present state of theFLGS2resistor.Modifying NAC and LMDIt is possible to change the values of the NAC and LMD parameters from the screen using the F1and F2func-tion keys as follows.Changing NAC(F1)1)Press the F1 key.The NAC field is highlighted.2)Enter the value in mAH and press the ENTERkey to store the value.Note:Changing NAC disqualifies a subsequent LMD update.Changing LMD(F2)1)Press the F2 key.The LMD field is highlighted.2)Enter the value in mAH and press the ENTERkey to store the value.Display Program ScreenThis menu is accessed by selecting the<Display Pro-gram>function on the Main Menu.The Display Pro-gram Screen represents the state of the bq2011 programming pins;see Figure4.To change the bq2011 programming,reconfigure jumpers MODE and PFC and 6Rev.C BoardBenchmarq BQ2011Programming ScreenSense Resistor:0.005ΩScale Factor:1/80Display Full:RELATIVE PFC Count:XXXXPFC(mVH):XXXX mVHSelf-Discharge Battery Capacity:9999mAHRate:1/64NAC/dayProgramming Pin ConfigurationLED Drive***PFC***ESC to main menu F3for HelpFigure 4. Programming MenuEV2011initialize the bq2011.The reset allows the bq2011to read the program pins.Sense Resistor Enter the value of sense resistor in ohms. Typical values range from0.001to 0.005Ω.The sense resistor value is used by the EV2011UIP to develop meaningful infor-mation in terms of A,mA,and mAH in re-lation to battery capacity and current. The default value is0.005.Values from 0.001to0.256are saved in the battery ID RAM byte of the bq2011.Values greater than0.256must be re-entered each time EV2011is started.Scale Factor Select the scale factor from the available scales using JP11.Like the sense resistor,the scale factor is used to develop meaningful information for the programmed full count tables,battery full,and available capacity indications.Display Full Use JP10to choose between RELATIVE and ABSOLUTE full reference for the LED display.PFC Select the programmed full count usingJP11.Note that the selected PFC and thesense resistor value are used to determinethe initial battery full capacity(mAh)rep-resented by the PFC.Battery Capacity This display indicates the battery capac-ity represented by dividing the PFC by the sense resistor.In practice,picking a PFC and sense resistor that provide a battery full value slightly lower than (within5%)the rated battery capacity is recommended.Program-ming Pin Configura-tion This indicates the display mode as either LED DRIVE by MODE or V CC.The PFC pin state is shown as L,Z,H.Please refer to the bq2011data sheet for more infor-mation.Data LoggingThe data log is activated from the Main Menu by select-ing the Data Log function.A filename to be used and the log sample period must be entered.For example: Log Data to Filename:<filename.ext>Enter Sample Period(10sec or greater):<xx>Opening Data Log FileWhen the data log is started,the Monitor Screen dis-plays the number of the current log record between thetime and date fields at the top of the screen.To termi-nate the data log,press the ESCAPE key.The file is closed and data logging is terminated.The data log record contains fields of ASCII data sepa-rated by tab characters.The field names and descrip-tions in record order follow.TIME Time record written in secondsLMD LMD value in mAHNAC NAC value in mAHAvg.DischargeCurrentAverage V SR battery currentFLAGS1Binary setting of FLAGS1flags:Bit Meaning0Not used1EDV flag state2Not used3VDQ (valid discharge)4Capacity inaccurate5Battery removed flag state6Battery replaced flag state7Charge active flag stateFLAGS2Binary setting of FLAGS2flags:Bit Meaning0Overload flag state1–3Not used4–6Discharge rate7Charge rateThe log records should be readable by most spreadsheet programs.7EV2011Rev.C BoardMeasure V OS ScreenThis screen is used to measure the V OS of the bq2011; see Figure5.A minimum of120seconds are required to perform this test.Pressing the ESC key terminates thetest in progress.Operating the test for a longer period increases the resolution of the test.A“beep”signals test completion.8Benchmarq EV2011Evaluation Board VO SMeasurementPresent DMF Setting+0.50mV=Vsrd-0.40mV=VsrqCurrent Threshold(DMF(mv)/Rsns):XXXXmADo you want to test Vos?:Y/NCalculated Vos:Vos XXXmV,over last xxxx secondsElapsed time:XXXX seconds**Note:There must be no charge/discharge activity on the bq2011for this testto be valid.Running the test for a longer period of time increasesthe Vos measurement resolution.This test requires a minimumof2minutes before any value is displayed.ESC to main menuFigure 5. VOS Measurement ScreenEV2011Rev.C BoardAppendix A:AP11 User's GuideThe AP11utility(AP11.EXE)is used to communicate with the bq2011on a register basis.AP11uses a driver to communicate with the EV2011over serial port on a PC-AT personal computer.AP11The AP11utility is started by executing AP11.EXE.After AP11is started,the following prompt is displayed: Select COM Port<1234>CommandsThe user can respond with various commands at the prompt.Pressing“Q”causes the program to terminate.–>?Pressing the?key displays following menu:These commands may be used to send or receive data from the EV2011.–>AIf A is entered in response to–>,then a break bit is sent to the EV2011.This may be used to restart the commu-nication if a problem appears.If the prompt does not re-turn immediately,then proper communication has not been established;please refer to Appendix B for trouble-shooting procedures.–>R#If R#is entered in response to–>,where#is an applica-ble address in HEX format,AP11returns the value at that location from the EV2011.The addresses are de-fined in the bq2011data sheet.For example:–>R03causes the display to show:R03=##where##is the current NAC value in HEX format.Address00is used to read and display all readable reg-isters.–>S#If S#is entered in response to–>,where#is a valid bq2011address in HEX format,AP11continuously reads and displays the value at that location.The ad-dressed are defined in the bq2011data sheet.For exam-ple:–>S03causes the display to show:Address3=##after XXX.XX sec.where##is the value at location03and XXX.XX isthe number of seconds between changes in thisvalue.–>W#=**If W#=**is entered in response to–>,where#is an ap-plicable address in HEX format and**is the value to be written,AP11writes the value to that location.The ad-dresses are defined in the bq2011data sheet.For exam-ple:–>W05=A0causes the program to write A0in location05hex(LMD register).9EV2011Rev.C BoardThe following commands are available:?This display is shown.A Send break.Q Quit and return to DOS.R#Read at address#.S#Scan at address#.W#=**Write at address#value**.Appendix B:Troubleshooting If the EV2011Main Menu does not appear after starting EV2011,then communication to the bq2011has not been established.Please check the following:1.Confirm the proper serial port is being used.2.Confirm the battery divider is properly set for thenumber of cells in the battery pack.3.Confirm JP9is properly set for either an externalsupply through LBAT+(J1)or the microregulator.JP9on B enables the microregulator,while JP9on L enables LBAT+.If the battery divider on JP1–JP8is not set properly,the bq2011will not op-erate,and the EV2011UIP or AP11will not work.4.Confirm the battery is attached between BAT+andBAT–(J1and J2).5.Push S1.SEG1LED should be on indicating thatthe bq2011is properly powered.6.If the LED is not on,check the battery voltage onpin16of the bq2011to determine if it is above3Vbut below6.5V.7.If the LED is on,and the EV2011Main Menu stilldoes not appear,try using AP11to establish com-munication.Appendix A describes AP11.8.If communication cannot be established usingAP11,the problem is either the RS-232port in thePC or the EV2011interface section.Please contactBenchmarq if the interface section is not workingproperly on the EV2011board.10Rev.C Board EV2011分销商库存信息: TIEV2011。