828D调试步骤(精)
828D调试步骤(精)

一系统参数后台:Alt+N或者shift+报警键1、通用数据10000【0】X(定义机床坐标轴的名称10000【1】Z(同上10000【2】SP(同上10000【3-5】自由轴的名称(无定义轴的名称X1、Y1、A1、B1、SP等等11310 手轮反向11346 手轮脉冲移动实际距离2、通道机床参数20050【0-3】0(定义通道内的几何轴20060【0-3】0(同上20070【0】1(通道内有效的机床轴号20070【1】2(同上20070【2】3(同上20070【3-4】0(同上20080【0】X(通道内有效的机床轴名20080【1】Z(同上20080【2】SP(同上20080【3-4】0(同上20700 0(未回参考点NC启动停止为13、轴参数通过“轴+”“轴-”更换轴,使用的同性质轴同时更改30100【5】1(模拟给定输出到轴控接口30110【1】1-驱动器号对于X轴(定义速度给定端口30110【2】2-驱动器号对于Z轴(同上30130【0】1(给定值输出类型,同时更改30220 同30110,实际值:驱动器号(定义位置反馈接口30240 1-实际值(编码器反馈类型,同时更改,1-相对编码器/2-仿真轴/4-绝对编码器30300 1(定义“回转轴”对于SP30310 1(回转轴取模转换,对于SP30320 1(取模360度位置显示,1为有效,对于SP31020 2048(每转的编码器线数,对于SP31030 10(丝杠螺距31040 1-直接测量系统32110 1-实际值(反馈记性:1/-131050【0-5】1(减速箱丝杠端齿轮齿数31060【0-5】5(减速箱电机端齿轮齿数32000 3000(最大轴速度,同时更改32010 2500(点动方式快速速度32100 电机转向(1/-132110 反馈极性(1/-132450 反向间隙补偿,回参考点后补偿生效(单位mm 36100 负方向软限位(单位mm,一般为负值36110 正方向软限位(单位mm,一般为正值设定主轴步骤如下:30300 1-定义为主轴(0-坐标轴/1-主轴30310 1-回转轴取模转换30320 1-取模360度位置显示(1-有效/0-无效35000 1-定义机床轴为主轴35100 实际值(最高主轴转速35110【0-5】主轴各档最高转速35120【0-5】主轴各档最低转速35130【0-5】主轴各档最高转速限制35140【0-5】主轴各档最低转速限制36200【0-5】各档速度监控的门限值带直接编码器的模拟量主轴30110 1-给定值模块号30220 1-编码器模块号30230 2-编码器信号端口号31000 实际值(0-编码器/1-光栅尺31010 实际值(光栅尺节点距离31020 实际值(编码器没转脉冲数NCK复位上电二驱动调试见手册14510【16】1H(用户数据车床14512【18】8H(用户数据K1使能。
828D新机开机调试

目录一、安全检查 (2)二、出厂设置 (2)三、设定语言、日期 (3)四、开启外部设备 (3)五、自动升级驱动 (4)六、轴分配 (5)七、传输PLC (7)八、传输报警文本和制造商循环 (9)九、系统数据设定 (9)十、绝对值回零设定 (9)十一、伺服自动优化 (9)十二、镭射补偿 (9)一、安全检查●目测设备的下列项目:–机械结构是否正确,电气连接是否安全–电源是否接好,输入电压是否正确稳定–屏蔽层和接地是否接好●接通控制系统,在“Nor mal startup”的模式中启动系统:HMI 上出现初始画面后,表明控制系统已启动。
二、出厂设置启动控制系统操作步骤:1. 控制系统接通后,启动时会出现以下提示:2. 在 3 秒钟内,按下<SELECT>键。
3. 然后依次按下:菜单扩展键、HSK2(水平软键 SK2)、 VSK2(垂直软键 SK2)4. “Setup men u”显示在屏幕上,“Normal startup”被选为缺省设置。
选择功能Normal startup系统正常启动。
Reload saved user data系统从系统 CF 卡上载入其中保存的用户数据,软键“数据存储”。
Install从用户 CF 卡或 U 盘上安装系统 CF 卡的升级程序。
softwareupdate/backup三、设定语言、日期设置语言操作步骤:1. 选择操作区域“启动”。
2. 按下右侧“CHANGE LANGUAGE”软键。
3. 选择simplified chinese 简体中文。
4. 按下软键“确认”结束输入,立即转化成为中文界面。
设置日期和时间操作步骤:1. 选择操作区域“启动”。
2. 按下“HMI”软键。
3. 按下“日期时间”软键。
打开窗口“日期/时间”。
4. 在“格式”栏中选择需要的日期和时间的显示格式。
5. 按下软键“确认”结束输入。
新的日期或时间被接收并在“当前”栏的第一行中显示。
828D调试步骤(精)
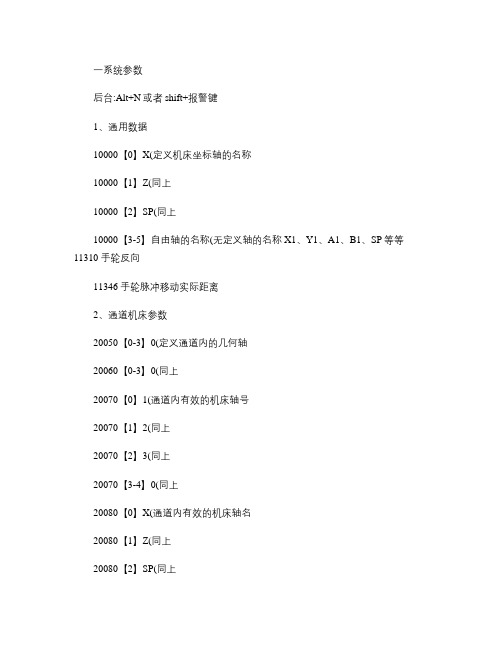
一系统参数后台:Alt+N或者shift+报警键1、通用数据10000【0】X(定义机床坐标轴的名称10000【1】Z(同上10000【2】SP(同上10000【3-5】自由轴的名称(无定义轴的名称X1、Y1、A1、B1、SP等等11310 手轮反向11346 手轮脉冲移动实际距离2、通道机床参数20050【0-3】0(定义通道内的几何轴20060【0-3】0(同上20070【0】1(通道内有效的机床轴号20070【1】2(同上20070【2】3(同上20070【3-4】0(同上20080【0】X(通道内有效的机床轴名20080【1】Z(同上20080【2】SP(同上20080【3-4】0(同上20700 0(未回参考点NC启动停止为13、轴参数通过“轴+”“轴-”更换轴,使用的同性质轴同时更改30100【5】1(模拟给定输出到轴控接口30110【1】1-驱动器号对于X轴(定义速度给定端口30110【2】2-驱动器号对于Z轴(同上30130【0】1(给定值输出类型,同时更改30220 同30110,实际值:驱动器号(定义位置反馈接口30240 1-实际值(编码器反馈类型,同时更改,1-相对编码器/2-仿真轴/4-绝对编码器30300 1(定义“回转轴”对于SP30310 1(回转轴取模转换,对于SP30320 1(取模360度位置显示,1为有效,对于SP31020 2048(每转的编码器线数,对于SP31030 10(丝杠螺距31040 1-直接测量系统32110 1-实际值(反馈记性:1/-131050【0-5】1(减速箱丝杠端齿轮齿数31060【0-5】5(减速箱电机端齿轮齿数32000 3000(最大轴速度,同时更改32010 2500(点动方式快速速度32100 电机转向(1/-132110 反馈极性(1/-132450 反向间隙补偿,回参考点后补偿生效(单位mm 36100 负方向软限位(单位mm,一般为负值36110 正方向软限位(单位mm,一般为正值设定主轴步骤如下:30300 1-定义为主轴(0-坐标轴/1-主轴30310 1-回转轴取模转换30320 1-取模360度位置显示(1-有效/0-无效35000 1-定义机床轴为主轴35100 实际值(最高主轴转速35110【0-5】主轴各档最高转速35120【0-5】主轴各档最低转速35130【0-5】主轴各档最高转速限制35140【0-5】主轴各档最低转速限制36200【0-5】各档速度监控的门限值带直接编码器的模拟量主轴30110 1-给定值模块号30220 1-编码器模块号30230 2-编码器信号端口号31000 实际值(0-编码器/1-光栅尺31010 实际值(光栅尺节点距离31020 实际值(编码器没转脉冲数NCK复位上电二驱动调试见手册14510【16】1H(用户数据车床14512【18】8H(用户数据K1使能。
828d主轴定位,回零,NC调试

主轴定位1.更换完主轴后,主轴需要重新定位2.首先在TMS下旋转主轴,然后执行M19定位主轴,此时主轴的位置可能是偏离换刀位置的,需要将主轴调整到换刀的位置(用千分表定位)3.查看系统显示的主轴的角度位置,并将此位置输入到MD34090中,重启系统。
4.通过M19对主轴进行定位,查看主轴是否在换刀位置。
35500=0时,主轴不选择也可以使用G01指令主轴换挡激活信号:一档DB380*.DBX2000.二档DB380*.DBX2000.1电机回零1绝对值编码器电机回零2将对应轴移动到零点位置3将对应轴的机床数据MD34210[0]更改为14选择回零状态,选择对应的轴,按“+”即可回零,回零后机床坐标会变为0.0mm5同时MD34210[0]会变为2.6增量编码器电机回零7通常增量编码器电机回零是,按“+”键后,对应的轴会向正方向移动,当挡块压到回零开关后,会反向移动,当挡块离开回零开关后,编码器找到零位。
8常见问题1:按“+”键后,该轴向负向移动,然后报警找不到零位。
原因:回零开关被压死。
9常见问题2:加工的工件尺寸,或大一个螺距的尺寸,或小一个螺距的尺寸。
处理:将回零挡块换个位置,或者将回零开关换个位置(向前或者后移动一点点)。
顺序回参考点1.除了按轴+/-向移动键让各轴回参考点外,还可以激活通道中的回参考点信号(DB3200.DBX1.0)让各轴按顺序回参考点。
2.各轴回参考点的顺序在轴机床数据MD34110 中设定。
建议铣床MD34110[Z]=1,MD34110[X]=2,MD34110[Y]=2,既Z 轴先回参考点,然后X 轴和Y 轴同时回参考点;车床MD34110[X]=1,MD34110[Z]=2,既X 轴先回参考点,然后Z 轴回参考点。
3.注:应在机床说明中注明操作安全提示,确保回零过程中无干涉,不碰撞。
NC调试MD30130 给定值输出类型0模拟轴;1实际轴MD30240编码器类型0 没有编码器;1增量编码器; 4绝对值编码器传动系统参数设置:MD31030 LEADSCREW_PITCH mm * 丝杠螺距MD31050 DRIVE_AX_RATIO_DENUM[0...5] * 电机端齿轮齿数(减速比分母)MD31060 DRIVE_AX_RATIO_NOMERA[0...5] * 丝杠端齿轮齿数(减速比分子)注意:对于主轴,索引号为[0]的减速比分子和分母均无效。
828四轴系统调试步骤
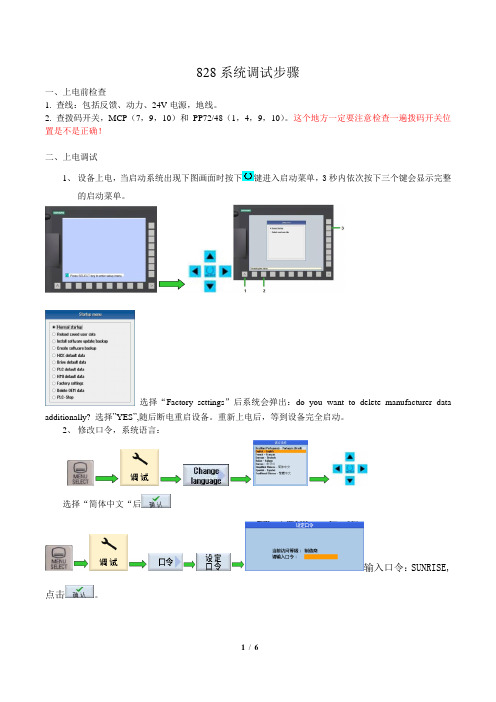
828系统调试步骤一、上电前检查1. 查线:包括反馈、动力、24V电源,地线。
2. 查拨码开关,MCP(7,9,10)和PP72/48(1,4,9,10)。
这个地方一定要注意检查一遍拨码开关位置是不是正确!二、上电调试1、设备上电,当启动系统出现下图画面时按下键进入启动菜单,3秒内依次按下三个键会显示完整的启动菜单。
选择“Factory settings”后系统会弹出:do you want to delete manufacturer data additionally? 选择”YES”,随后断电重启设备。
重新上电后,等到设备完全启动。
2、修改口令,系统语言:选择“简体中文“后输入口令:SUNRISE,点击。
3、 激活MCP 及PP72/48D搜索参数12986[0]=-1,12986[6]= -1。
4、 使用“PLC Programming Tool “软件连接828PLC 系统,下载PLC 控制程序。
4.1如上图所示:A :双击“通讯”在弹出的通讯设定对话框B:通讯参数:828系统PLC 地址:192、168、215、1。
电脑上的IP 地址选择自动获取。
C :更改TCP/IP 网卡,双击此处在弹出的对话框中,选择当前电脑启用的网卡。
D:以上三步设置结束后,双击刷新,此处会显示绿色的字体“828D ”,此时表明已经和828的PLC 建立了通讯,可以进行下载和上传程序了。
4.2 下载PLC 程序,下载程序时会出现如下对话框。
默认只下载PLC 程序和数据块的初始值。
如果要下载数据块的实际值,请勾选“数据模块”复选框。
ABCD如果只是对程序做了简单的修改,可以选择在RUN模式下下载;如果程序做了较大的改动或者新建了数据块,则必须在STOP模式下下载。
第一次下载时选择STOP模式。
4.3 程序下载成功后,点击启动PLC运行状态。
等待PLC重新启动运行后,观察MCP各按键指示灯状态。
若指示灯全部闪烁,则说明MCP板与PLC的通讯没有建立,请检查MCP背板的拨码开关位置和参数12986[6]设置是否正确。
828d主轴定位,回零,NC调试

828d主轴定位,回零,NC调试主轴定位1.更换完主轴后,主轴需要重新定位2.⾸先在TMS下旋转主轴,然后执⾏M19定位主轴,此时主轴的位置可能是偏离换⼑位置的,需要将主轴调整到换⼑的位置(⽤千分表定位)3.查看系统显⽰的主轴的⾓度位置,并将此位置输⼊到MD34090中,重启系统。
4.通过M19对主轴进⾏定位,查看主轴是否在换⼑位置。
35500=0时,主轴不选择也可以使⽤G01指令主轴换挡激活信号:⼀档DB380*.DBX2000.⼆档DB380*.DBX2000.1电机回零1绝对值编码器电机回零2将对应轴移动到零点位置3将对应轴的机床数据MD34210[0]更改为14选择回零状态,选择对应的轴,按“+”即可回零,回零后机床坐标会变为0.0mm5同时MD34210[0]会变为2.6增量编码器电机回零7通常增量编码器电机回零是,按“+”键后,对应的轴会向正⽅向移动,当挡块压到回零开关后,会反向移动,当挡块离开回零开关后,编码器找到零位。
8常见问题1:按“+”键后,该轴向负向移动,然后报警找不到零位。
原因:回零开关被压死。
9常见问题2:加⼯的⼯件尺⼨,或⼤⼀个螺距的尺⼨,或⼩⼀个螺距的尺⼨。
处理:将回零挡块换个位置,或者将回零开关换个位置(向前或者后移动⼀点点)。
顺序回参考点1.除了按轴+/-向移动键让各轴回参考点外,还可以激活通道中的回参考点信号(DB3200.DBX1.0)让各轴按顺序回参考点。
2.各轴回参考点的顺序在轴机床数据MD34110 中设定。
建议铣床MD34110[Z]=1,MD34110[X]=2,MD34110[Y]=2,既Z 轴先回参考点,然后X 轴和Y 轴同时回参考点;车床MD34110[X]=1,MD34110[Z]=2,既X 轴先回参考点,然后Z 轴回参考点。
3.注:应在机床说明中注明操作安全提⽰,确保回零过程中⽆⼲涉,不碰撞。
NC调试MD30130 给定值输出类型01MD30240编码器类型0 没有编码器;1增量编码器; 4绝对值编码器传动系统参数设置:MD31030 LEADSCREW_PITCH mm * 丝杠螺距MD31050 DRIVE_AX_RATIO_DENUM[0...5] * 电机端齿轮齿数(减速⽐分母)MD31060 DRIVE_AX_RATIO_NOMERA[0...5] * 丝杠端齿轮齿数(减速⽐分⼦)注意:对于主轴,索引号为[0]的减速⽐分⼦和分母均⽆效。
828D新机开机调试
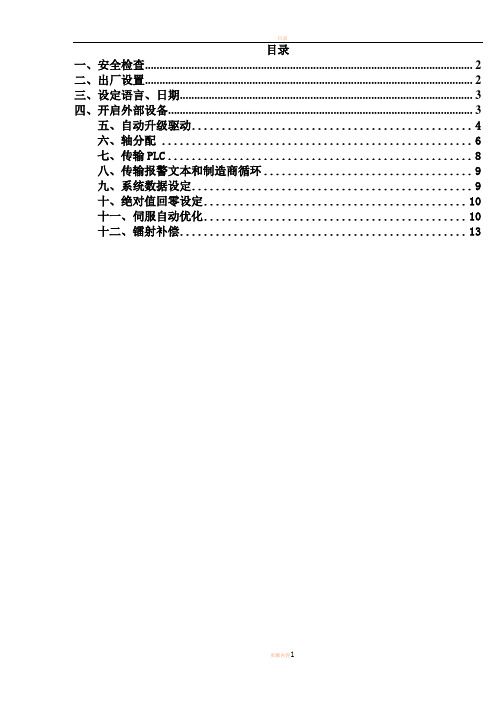
目录一、安全检查 (2)二、出厂设置 (2)三、设定语言、日期 (3)四、开启外部设备 (3)五、自动升级驱动 (4)六、轴分配 (6)七、传输PLC (8)八、传输报警文本和制造商循环 (9)九、系统数据设定 (9)十、绝对值回零设定 (10)十一、伺服自动优化 (10)十二、镭射补偿 (13)一、安全检查●目测设备的下列项目:–机械结构是否正确,电气连接是否安全–电源是否接好,输入电压是否正确稳定–屏蔽层和接地是否接好●接通控制系统,在“Nor mal startup”的模式中启动系统:HMI上出现初始画面后,表明控制系统已启动。
二、出厂设置启动控制系统操作步骤:1. 控制系统接通后,启动时会出现以下提示:2. 在 3 秒钟内,按下<SELECT>键。
3. 然后依次按下:菜单扩展键、HSK2(水平软键 SK2)、 VSK2(垂直软键 SK2)4. “Setup men u”显示在屏幕上,“Normal startup”被选为缺省设置。
选择功能Normal startup系统正常启动。
Reload saved user data系统从系统 CF 卡上载入其中保存的用户数据,软键“数据存储”。
Installsoftwareupdate/backup从用户 CF 卡或 U 盘上安装系统 CF 卡的升级程序。
三、设定语言、日期设置语言操作步骤:1. 选择操作区域“启动”。
2. 按下右侧“CHANGE LANGUAGE”软键。
3. 选择simplified chinese 简体中文。
4. 按下软键“确认”结束输入,立即转化成为中文界面。
设置日期和时间操作步骤:1. 选择操作区域“启动”。
2. 按下“HMI”软键。
3. 按下“日期时间”软键。
打开窗口“日期/时间”。
4. 在“格式”栏中选择需要的日期和时间的显示格式。
5. 按下软键“确认”结束输入。
新的日期或时间被接收并在“当前”栏的第一行中显示。
828D 调试顺序

S i n u m e r i k 828DSINUMERIK 828D 第 1 页 B068调试顺序单元描述:Sinumerik 828D CNC 控制系统是为了中等机床刀具市场而开发的。
在中等机床刀具市场中,除了通过外接CAD /CAM 类型的系统进行编程,也需要在机床上编程。
这些被大量销售的机床应该展示出相似的工作特性。
调试工程师通过执行已定义的调试步骤来保证这种相似性。
B068 单元目标:在完成本单元的学习之后,您将能够按照已定义的调试步骤配置并调试带主轴以及附加了第四轴的3轴铣削机床。
该步骤是保证机床安装的兼容性及质量的必要手段。
驱动配置(调试工具) NC 轴分配 第二节准备控制系统 第三节第四节第五节第六节NC 机床数据 第七节硬件及软件要求/调试顺序 配置MCP 及外围设备 轴使能 第八节驱动优化 第九节数据管理 第十节B068目录:第二节硬件及软件要求/调试顺序批注 1. 工具/软件安装单元B0022. 加载标准数据控制系统必须加载默认数据以便根据机床工艺类型设置默认机床数据(铣削/车削)。
在调试过程中,选择打开控制系统,等待控制系统显示以下窗口。
在3秒钟之内,按“请选择SELECT键进入setup菜单控制系统显示基本“Set-up”菜单,根据下图中的数字顺序选择按键以显示高级“Start-up”菜单。
请选择SELECT键进入setup菜单u2B068第 4 页选择“Yes”确认执行操作。
第三节允许控制系统完全调试,这个过程最多需要5分钟。
控制系统前面板上的绿色将常准备控制系统批注如果系统未使用所需的语言,可修改语言。
设置口令以使能待查看及修改的机床数据等。
建议使用密码 - “SUNRISE”, 然后按“确认”软键。
使用“取消报警”键确认报警号铣削机床已经加载标准数据并且被配置为在激活额外的轴之前,必须确保选件可用。
按以下顺序使用软键以查看/激活许可证:B068第 6 页第三节输入值1并选择“复位 (po)”软键以激活选件。
828D新机开机调试

规程,熟悉紧急停止按钮和安
钮、指示灯等操作界面,帮助
全防护装置。
操作人员了解机床的运作原理
。
3 模拟操作
4 实际加工
在模拟环境下进行操作练习,
在实际加工过程中,指导操作
熟悉机床的各个操作步骤,掌
人员进行零件加工,并进行实
握基本操作技能。
时指导和答疑,帮助操作人员
巩固操作技能。
总结及建议
调试过程顺利
软件安装与设置
软件下载 1
确保下载官方软件,避免恶意软件。
安装程序 2
运行安装程序,并根据提示进行操作。
激活授权
3
输入授权码,激活软件使用权限。
配置参数 4
根据机床型号和加工需求,设置软件参数。
安装完成后,需要进行软件参数的配置。例如,设置机床型号、加工精度、切削速度等参数。确保这些参数与实际机床相匹配,以便软件能够正常 运行。
检查机床各部件
机床本体
检查机床本体是否存在裂纹、变形、腐蚀等缺 陷。
传动系统
检查传动轴、齿轮、链条等部件是否有磨损、 松动等现象。
液压系统
检查液压油缸、油管、阀门等是否泄漏、堵塞 。
电气系统
检查电线、接线盒、开关等是否有破损、接触 不良。
电气系统检查
电源线连接
检查电源线是否牢固连接, 确保电源线没有损坏或松动 。连接过程中需要注意极性 ,避免接反。
新机开机调试顺利完成,设备各 项功能正常运行。
工艺参数优化
对加工参数进行优化,提升加工 效率和零件质量。
定期维护保养
建议定期进行机床维护保养,确 保设备运行稳定。
安全操作
操作人员需严格遵守安全操作规 程,避免发生安全事故。
828D调试流程
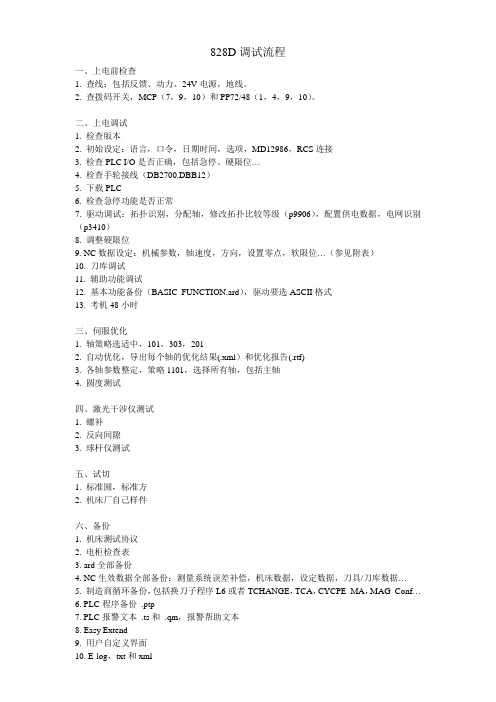
828D调试流程一、上电前检查1. 查线:包括反馈、动力、24V电源,地线。
2. 查拨码开关,MCP(7,9,10)和PP72/48(1,4,9,10)。
二、上电调试1. 检查版本2. 初始设定:语言,口令,日期时间,选项,MD12986,RCS连接3. 检查PLC I/O是否正确,包括急停、硬限位…4. 检查手轮接线(DB2700.DBB12)5. 下载PLC6. 检查急停功能是否正常7. 驱动调试:拓扑识别,分配轴,修改拓扑比较等级(p9906),配置供电数据,电网识别(p3410)8. 调整硬限位9. NC数据设定:机械参数,轴速度,方向,设置零点,软限位…(参见附表)10. 刀库调试11. 辅助功能调试12. 基本功能备份(BASIC_FUNCTION.ard),驱动要选ASCII格式13. 考机48小时三、伺服优化1. 轴策略选适中,101,303,2012. 自动优化,导出每个轴的优化结果(.xml)和优化报告(.rtf)3. 各轴参数整定,策略1101,选择所有轴,包括主轴4. 圆度测试四、激光干涉仪测试1. 螺补2. 反向间隙3. 球杆仪测试五、试切1. 标准圆,标准方2. 机床厂自己样件六、备份1. 机床测试协议2. 电柜检查表3. ard全部备份4. NC生效数据全部备份:测量系统误差补偿,机床数据,设定数据,刀具/刀库数据…5. 制造商循环备份,包括换刀子程序L6或者TCHANGE,TCA,CYCPE_MA,MAG_Conf…6. PLC程序备份.ptp7. PLC报警文本.ts和.qm,报警帮助文本8. Easy Extend9. 用户自定义界面10. E-log,txt和xml11. 系统许可证备份.Alm12. 优化测试结果截图13. 圆度测试结果截图14. PLC IO地址15. 机床操作说明:MCP自定义键说明,M代码功能说明,PLC报警文本内容说明,PLC 数据MD14510说明,刀库操作说明16. 照片:机床、电柜、试切17. 试切件程序附表:常用机床数据传动系统参数MD32100 AX_MOTION_DIR 轴运动方向(不是反馈极性)MD31030 LEADSCREW_PITCH 丝杠螺距MD31040 ENC_IS_DIRECT[0]…[1] 直接测量系统MD31050 DRIVE_AX_RA TIO_DENOM[0]...[5] 负载变速箱分母MD31060 DRIVE_AX_RA TIO_NUMERA[0]...[5] 负载变速箱分子轴速度MD32000 MAX_AX_VELO 最大轴速度MD32010 JOG_VELO_RAPID 点动方式快速速度MD32020 JOG_VELO 点动速度MD36200 AX_VELO_LIMIT[0]...[5] 速度监控的门限值主轴相关MD35010 GEAR_STEP_CHANGE_ENABLE 齿轮级改变使能MD35110 GEAR_STEP_MAX_VELO[0]...[5] 主轴各档最高转速MD35120 GEAR_STEP_MIN_VELO[0]...[5] 主轴各档最低转速MD35130 GEAR_STEP_MAX_VELO_LIMIT[0]...[5] 主轴各档最高转速限制MD35140 GEAR_STEP_MIN_VELO_LIMIT[0]...[5] 主轴各档最低转速限制SD43200 SA_SPIND_S 通过VDI 进行主轴起动时的速度返回参考点MD34010 REFP_CAM_DIR_IS_MINUS 负方向返回参考点MD34020 REFP_VELO_SEARCH_CAM 寻找参考点开关的速度MD34040 REFP_VELO_SEARCH_MARKER 寻找零脉冲的速度MD34060 REFP_MAX_MARKER_DIST 寻找零标记的最大距离MD34070 REFP_VELO_POS 返回参考点的定位速度MD34100 REFP_SET_POS 参考点(相对于机床坐标系)的位置MD34110 REFP_CYCLE_NR 返回参考点次序MD34200 ENC_REFP_MODE[0]…[1] 返回参考点模式MD34210 ENC_REFP_STA TE[0]…[1] 绝对值编码器调试状态MD11300 JOG_INC_MODE_LEVELTRIGGRD 返回参考点触发方式软限位MD36100 POS_LIMIT_MINUS 第一软限位负向MD36110 POS_LIMIT_PLUS 第一软限位正向优化MD32200 POSCTRL_GAIN[0]...[5] 位置环增益MD32810 EQUIV_SPEEDCTRL_TIME[0]...[5] 速度控制环等效时间常数MD32640 STIFFNESS_CONTROL_ENABLE 动态刚性控制MD32420 JOG_AND_POS_JERK_ENABLE 手动和定位方式下轴加加速度限制使能MD32430 JOG_AND_POS_MAX_JERK 手动方式下轴加加速度最大值MD32431 MAX_AX_JERK[0]…[4] 自动方式下轴加加速度最大值MD32432 PA TH_TRANS_JERK_LIM[0]…[4] 轨迹控制时程序段过渡处轴加加速度最大值刀库管理MD20270 CUTTING_EDGE_DEFAULT 未编程时刀具刀沿的默认设置MD20310 MC_TOOL_MANAGEMENT_MASK 激活不同类型的刀具管理MD52270 MCS_TM_FUNCTION_MASK 刀库管理功能。
828D调试步骤(精)

一系统参数后台:Alt+N或者shift+报警键1、通用数据10000【0】X(定义机床坐标轴的名称10000【1】Z(同上10000【2】SP(同上10000【3-5】自由轴的名称(无定义轴的名称X1、Y1、A1、B1、SP等等11310 手轮反向11346 手轮脉冲移动实际距离2、通道机床参数20050【0-3】0(定义通道内的几何轴20060【0-3】0(同上20070【0】1(通道内有效的机床轴号20070【1】2(同上20070【2】3(同上20070【3-4】0(同上20080【0】X(通道内有效的机床轴名20080【1】Z(同上20080【2】SP(同上20080【3-4】0(同上20700 0(未回参考点NC启动停止为13、轴参数通过“轴+”“轴-”更换轴,使用的同性质轴同时更改30100【5】1(模拟给定输出到轴控接口30110【1】1-驱动器号对于X轴(定义速度给定端口30110【2】2-驱动器号对于Z轴(同上30130【0】1(给定值输出类型,同时更改30220 同30110,实际值:驱动器号(定义位置反馈接口30240 1-实际值(编码器反馈类型,同时更改,1-相对编码器/2-仿真轴/4-绝对编码器30300 1(定义“回转轴”对于SP30310 1(回转轴取模转换,对于SP30320 1(取模360度位置显示,1为有效,对于SP31020 2048(每转的编码器线数,对于SP31030 10(丝杠螺距31040 1-直接测量系统32110 1-实际值(反馈记性:1/-131050【0-5】1(减速箱丝杠端齿轮齿数31060【0-5】5(减速箱电机端齿轮齿数32000 3000(最大轴速度,同时更改32010 2500(点动方式快速速度32100 电机转向(1/-132110 反馈极性(1/-132450 反向间隙补偿,回参考点后补偿生效(单位mm 36100 负方向软限位(单位mm,一般为负值36110 正方向软限位(单位mm,一般为正值设定主轴步骤如下:30300 1-定义为主轴(0-坐标轴/1-主轴30310 1-回转轴取模转换30320 1-取模360度位置显示(1-有效/0-无效35000 1-定义机床轴为主轴35100 实际值(最高主轴转速35110【0-5】主轴各档最高转速35120【0-5】主轴各档最低转速35130【0-5】主轴各档最高转速限制35140【0-5】主轴各档最低转速限制36200【0-5】各档速度监控的门限值带直接编码器的模拟量主轴30110 1-给定值模块号30220 1-编码器模块号30230 2-编码器信号端口号31000 实际值(0-编码器/1-光栅尺31010 实际值(光栅尺节点距离31020 实际值(编码器没转脉冲数NCK复位上电二驱动调试见手册14510【16】1H(用户数据车床14512【18】8H(用户数据K1使能。
828D开机调试流程

828D开机调试流程做完后请在“□”处打勾一、上电前检查条目详细内容备注1 查线□动力线、反馈线接牢,顺序无误□驱动模块间的直流母线、24V母线□24V电源线□所有设备独立接地2 拨码开关二、上电调试 条目详细内容备注1初始设定□ 设置系统语言为中文Chinese请参见简明调试手册3.4章节□ 输入制造商□令:SUNRISE请参见简明调试手册3.2章节□ 设置系统时间请参见简明调试手册3.3章节□ 进入选项界面,检查激活的选项请参见简明调试手册3.6章节□ 激活PP72/48,设置MD12986[0]=-1 有第二块I/O 板时需设置MD12986[1]=-1;请参见简明调试手册3.5章节 □ 激活MCP ,设置MD12986[6]=-1 使用自制机床操作面板时保持MD12986[6]=112 □ 设置RCS 远程诊断访问权限2检查系统软件版本□ V. + SP + HF3监控PLC I/O 点状态□ 监控IB115的状态,如果为0则代表MCP 不正常。
因为IB115的低5位是西门子MCP 进给倍率开关的地址,格雷码开关是不会出现全0状态的。
□ 输入点:急停开关、硬限位开关、报警信号点… □ 输出点:EP 、OFF1、OFF3使能…□ 手轮接线状态:摇手轮时监控DB2700.DBB12(手轮1脉冲计数),如果数值有变化说明手轮接线无误。
4下载PLC 程序□STOP 模式下载,下载后重启系统5PLC 基本功能调试□ MCP 功能是否正常 □ 急停、硬限位功能是否正常 □ 加EP ,OFF1,OFF3使能是否正常 □ 手轮轴选,增量是否正常6 驱动调试□ 拓扑识别请参见简明调试手册5.2章节□修改拓扑比较等级为中级:控制单元数据p9906=1如不修改会影响批量调试;请参见简明调试手册5.2章节□ 配置供电数据,输入电压380V请参见简明调试手册5.3章节□ 电网识别,设置供电数据p3410=5请参见简明调试手册5.3章节□ 分配轴:设置MD30110为电机动力线所在的驱动编号 设置MD30220为电机反馈线所在的驱动编号 设置MD30130=1,激活电机的给定信号设置MD30240=1或4,激活电机的反馈信号。
828D车床模拟量主轴加进给轴全闭环调试

828D车床模拟量主轴加进给轴全闭环调试——828D进给轴的第三编码器调试前言:对于模拟主轴的直接编码器,我们在应用时需要把它叠加到一个进给轴上。
通常的使用方法,是我们把它配置为一个进给轴的第二编码器,在使用时主轴从这个进给轴的第二编码器读取数据。
但当设备所有轴都为全闭环时,就没有第二编码器可为模拟主轴使用。
所以我们介绍使用进给轴第三编码器的方法实现车床模拟量主轴编码器加进给轴全闭环的调试。
实验原理:在Z轴上配置三个编码器,其中第三编码器作为模拟主轴的直接编码器,828D系统默认的驱动报文格式136或116传递的是轴第一编码器和第二编码的信号,改用118的报文格式可以传输轴编码器2和3的信息给系统;系统侧就可以读取Z 轴编码器2和3的值(系统只能接受两套反馈,驱动可以接受三套反馈),然后我们通过NC参数设置,将Z轴编码器2作为Z轴系统的反馈1,编码器3作为Z轴系统的反馈2,再将其中一个反馈分配给模拟量主轴使用,这样就完成了调试要求。
116报文与118报文中状态字的区别调试设备:试验硬件 数量 详细信息828D BASIC T 1 软件版本04.04.SP1电源模块 1 非调节型电源模块 (SLM)电机模块 1 双轴模块电机 2 1FK7 同步电机外接编码器 3 1Vpp 2500线 (X轴第二测量)EnDat 512线(Z轴第二测量)TTL 1024线(Z轴第三测量或主轴的直接测量)SMC 3 SMC20、SMC20、SMC30各一个注:用两个同步电机作为X,Z 轴,主轴为模拟轴。
硬件连接示意图如下:说明:Motor Enc X为X 轴电机编码器;Direct X为X轴第二编码器;Motor Enc Z为Z 轴电机编码器;Direct Z为Z轴第二编码器;Direct Spi为SP 轴编码器调试步骤:1、硬件连接好后,系统自动进行拓扑识别。
在拓扑识别完成后,HMI 上会出现”Alarm201331: Topology:Component not assigned to a drive object, Component no.for the encoder interface”。
828D调试流程

828D调试流程调试是软件开发过程中非常重要的一部分,它可以帮助开发人员识别和修复软件中的错误和缺陷。
在调试过程中,开发人员需要使用一定的方法和策略来有效地定位和解决问题。
下面是一个基本的828D调试流程,包括以下几个步骤:1.确认问题:在开始调试之前,开发人员需要与用户或测试人员沟通,了解出现的问题并尽可能详细地描述。
在确认问题之后,与用户或测试人员一起分析问题,确保所有相关信息都已经收集和理解。
2.复现问题:为了准确地定位问题,开发人员需要尽可能准确地复现问题。
这可以通过使用相同的环境、数据和条件来实现。
如果无法复现问题,可能需要进一步了解可能的原因以及如何重现问题。
3.分析代码:一旦问题被复现,开发人员可以开始分析代码以查找问题。
这包括查看相关的日志文件、调试信息、错误报告以及相关代码段。
开发人员应该借助调试工具和技术来帮助定位问题,例如断点调试、日志输出、性能分析等。
4.突出关键点:在分析代码时,开发人员需要特别关注可能与问题相关的关键点。
这可能是问题发生的地方,也可能是其他可能引起问题的代码段。
开发人员可以使用调试工具来逐步执行代码,并观察其行为以找出问题所在。
5.排除可能的原因:在找到问题所在之后,开发人员需要进一步排除其他可能的原因。
这可能包括与其他模块的交互、并发问题、内存管理问题、网络问题等。
开发人员可以使用一些常见的调试技巧来定位和排除这些潜在的原因。
6.修复问题:一旦问题被定位和确认,开发人员可以开始解决问题。
这可能包括修复代码中的错误、重新设计或优化算法、增加异常处理、修改配置文件等。
修复后,开发人员需要进行一系列的测试以确保问题得到解决。
7.测试和验证:在修复问题之后,开发人员需要进行测试和验证,以确保问题已经完全解决。
这可能包括单元测试、集成测试、系统测试等。
如果问题没有完全解决,开发人员需要返回到调试过程中,重新分析并修复问题。
8.文档和总结:在调试过程完成后,开发人员需要将整个过程进行文档化和总结。
828D调试步骤

一系统参数后台:Alt+N或shift+报警键1、通用数据10000【0】X(概念机床坐标轴的名称)10000【1】Z(同上)10000【2】SP(同上)10000【3-5】自由轴的名称(无概念轴的名称X一、Y一、A一、B一、SP等等)11310 手轮反向11346 手轮脉冲移动实际距离二、通道机床参数20050【0-3】0(概念通道内的几何轴)20060【0-3】0(同上)20070【0】1(通道内有效的机床轴号)20070【1】2(同上)20070【2】3(同上)20070【3-4】0(同上)20080【0】X(通道内有效的机床轴名)20080【1】Z(同上)20080【2】SP(同上)20080【3-4】0(同上)20700 0(未回参考点NC启动停止为1)3、轴参数通过“轴+”“轴-”改换轴,利用的同性质轴同时更改30100【5】1(模拟给定输出到轴控接口)30110【1】1-驱动器号关于X轴(概念速度给定端口)30110【2】2-驱动器号关于Z轴(同上)30130【0】1(给定值输出类型,同时更改)30220 同30110,实际值:驱动器号(概念位置反馈接口)30240 1-实际值(编码器反馈类型,同时更改,1-相对编码器/2-仿真轴/4-绝对编码器)30300 1(概念“回转轴”关于SP)30310 1(回转轴取模转换,关于SP)30320 1(取模360度位置显示,1为有效,关于SP)31020 2048(每转的编码器线数,关于SP)31030 10(丝杠螺距)31040 1-直接测量系统32110 1-实际值(反馈记性:1/-1)31050【0-5】1(减速箱丝杠端齿轮齿数)31060【0-5】5(减速箱电机端齿轮齿数)32000 3000(最大轴速度,同时更改)32010 2500(点动方式快速速度)32100 电机转向(1/-1)32110 反馈极性(1/-1)32450 反向间隙补偿,回参考点后补偿生效(单位mm)36100 负方向软限位(单位mm,一样为负值)36110 正方向软限位(单位mm,一样为正值)设定主轴步骤如下:30300 1-概念为主轴(0-坐标轴/1-主轴)30310 1-回转轴取模转换30320 1-取模360度位置显示(1-有效/0-无效)35000 1-概念机床轴为主轴35100 实际值(最高主轴转速)35110【0-5】主轴各档最高转速35120【0-5】主轴各档最低转速35130【0-5】主轴各档最高转速限制35140【0-5】主轴各档最低转速限制36200【0-5】各档速度监控的门限值带直接编码器的模拟量主轴30110 1-给定值模块号30220 1-编码器模块号30230 2-编码器信号端口号31000 实际值(0-编码器/1-光栅尺)31010 实际值(光栅尺节点距离)31020 实际值(编码器没转脉冲数)NCK复位上电二驱动调试见手册14510【16】1H(用户数据)车床14512【18】8H(用户数据)K1使能。
- 1、下载文档前请自行甄别文档内容的完整性,平台不提供额外的编辑、内容补充、找答案等附加服务。
- 2、"仅部分预览"的文档,不可在线预览部分如存在完整性等问题,可反馈申请退款(可完整预览的文档不适用该条件!)。
- 3、如文档侵犯您的权益,请联系客服反馈,我们会尽快为您处理(人工客服工作时间:9:00-18:30)。
一系统参数
后台:Alt+N或者shift+报警键
1、通用数据
10000【0】X(定义机床坐标轴的名称
10000【1】Z(同上
10000【2】SP(同上
10000【3-5】自由轴的名称(无定义轴的名称X1、Y1、A1、B1、SP等等11310 手轮反向
11346 手轮脉冲移动实际距离
2、通道机床参数
20050【0-3】0(定义通道内的几何轴
20060【0-3】0(同上
20070【0】1(通道内有效的机床轴号
20070【1】2(同上
20070【2】3(同上
20070【3-4】0(同上
20080【0】X(通道内有效的机床轴名
20080【1】Z(同上
20080【2】SP(同上
20080【3-4】0(同上
20700 0(未回参考点NC启动停止为1
3、轴参数通过“轴+”“轴-”更换轴,使用的同性质轴同时更改
30100【5】1(模拟给定输出到轴控接口
30110【1】1-驱动器号对于X轴(定义速度给定端口
30110【2】2-驱动器号对于Z轴(同上
30130【0】1(给定值输出类型,同时更改
30220 同30110,实际值:驱动器号(定义位置反馈接口
30240 1-实际值(编码器反馈类型,同时更改,1-相对编码器/2-仿真轴/4-绝对编码器
30300 1(定义“回转轴”对于SP
30310 1(回转轴取模转换,对于SP
30320 1(取模360度位置显示,1为有效,对于SP
31020 2048(每转的编码器线数,对于SP
31030 10(丝杠螺距
31040 1-直接测量系统
32110 1-实际值(反馈记性:1/-1
31050【0-5】1(减速箱丝杠端齿轮齿数
31060【0-5】5(减速箱电机端齿轮齿数
32000 3000(最大轴速度,同时更改
32010 2500(点动方式快速速度
32100 电机转向(1/-1
32110 反馈极性(1/-1
32450 反向间隙补偿,回参考点后补偿生效(单位mm 36100 负方向软限位(单位mm,一般为负值
36110 正方向软限位(单位mm,一般为正值
设定主轴步骤如下:
30300 1-定义为主轴(0-坐标轴/1-主轴
30310 1-回转轴取模转换
30320 1-取模360度位置显示(1-有效/0-无效
35000 1-定义机床轴为主轴
35100 实际值(最高主轴转速
35110【0-5】主轴各档最高转速
35120【0-5】主轴各档最低转速
35130【0-5】主轴各档最高转速限制
35140【0-5】主轴各档最低转速限制
36200【0-5】各档速度监控的门限值
带直接编码器的模拟量主轴
30110 1-给定值模块号
30220 1-编码器模块号
30230 2-编码器信号端口号31000 实际值(0-编码器/1-光栅尺31010 实际值(光栅尺节点距离31020 实际值(编码器没转脉冲数NCK复位上电
二驱动调试
见手册
14510【16】1H(用户数据车床14512【18】8H(用户数据K1使能。