材料成型第4章铸造工艺设计
东大材料成型课程设计

东大材料成型课程设计一、课程目标知识目标:1. 理解并掌握材料成型的基本原理,包括铸造、焊接、塑性加工等;2. 学习并了解不同材料的成型特性及适用范围;3. 掌握材料成型过程中常见缺陷的类型及成因。
技能目标:1. 能够运用材料成型原理,设计简单的成型工艺流程;2. 能够分析并解决材料成型过程中出现的问题;3. 能够运用所学知识,对实际材料成型工艺进行评价和优化。
情感态度价值观目标:1. 培养学生对材料成型技术的兴趣,激发探索精神;2. 培养学生严谨的科学态度,注重实践操作与理论知识的结合;3. 增强学生的团队协作意识,提高沟通与表达能力。
分析课程性质、学生特点和教学要求,本课程旨在帮助学生在掌握材料成型基本知识的基础上,提高实践操作能力和解决实际问题的能力。
课程目标具体、可衡量,以便学生和教师能够清晰地了解课程的预期成果。
通过本课程的学习,使学生能够在实际工作中运用所学知识,为我国材料成型技术的发展做出贡献。
二、教学内容1. 材料成型基本原理:包括铸造、焊接、塑性加工等成型方法的工作原理及特点;- 教材章节:第一章《材料成型技术概述》- 内容列举:铸造原理、焊接原理、塑性加工原理。
2. 材料成型工艺及设备:介绍不同材料的成型工艺及所使用的设备;- 教材章节:第二章《材料成型工艺与设备》- 内容列举:铸造工艺及设备、焊接工艺及设备、塑性加工工艺及设备。
3. 材料成型缺陷分析:分析材料成型过程中常见缺陷的类型、成因及解决办法;- 教材章节:第三章《材料成型缺陷及质量控制》- 内容列举:铸造缺陷、焊接缺陷、塑性加工缺陷。
4. 材料成型工艺设计:学习如何设计简单的成型工艺流程,并进行优化;- 教材章节:第四章《材料成型工艺设计》- 内容列举:工艺流程设计方法、工艺参数优化。
5. 实践教学环节:组织学生进行实际操作,巩固所学知识,提高解决实际问题的能力;- 教材章节:第五章《材料成型实践》- 内容列举:铸造实践、焊接实践、塑性加工实践。
【材料成型原理--铸造】第4章 液态金属凝固过程中的传热与传质
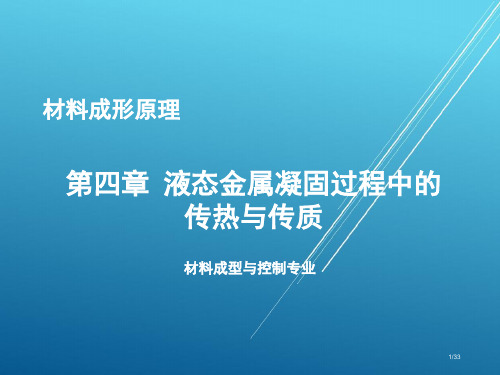
• 2、模型建立
• 温度TL时,开始凝固: • 固 度k相0C:0。百分数dfS;溶质浓
• 液相:溶质浓度几乎不变, 为C0。 • 温度降到T*时,
• 固 数f相S;:溶质浓度C*S;百分
•
液相:溶质浓 数fL。
度
C*L;百
分
28/33
• 当dfSf)S界,溶面这质处些浓固溶度相质增增将加加均d百C匀*L分扩,量散则为到:d整fS个时液,相排中出,溶使质剩量余为液(相C*(L-C1*S-) • (C*L-C*S)dfS=(1-fS)dC*L
30/33
31/33
32/33
33/33
34/33
35/33
• (二)固相无扩散,液相只有有限扩散(无对流或搅拌) 的溶质再分配
• 1、假设: • (1)合金单相凝固; • (2)固相无扩散(接近实际情况); • (3)液相有限扩散(无对流、搅拌); • (4)固液相线为直线,k0为常数; • (5)试样很长,单向放热,平面推进。
• 该两式为平衡凝固时溶质再分配的数学模型。
19/33
CS
1
C0k0 f S (1 k0 )
CL
k0
C0 f L (1 k0 )
• 3、验证 (1)开始凝固时 • 初始条件:fS0,fL1 • 则:CS=k0C0;CL=C0 (2)凝固结束时 • 初始条件:fS1,fL0 • 则:CS=C0;CL=C0/k0
凝固时间与凝固层厚度的平方成正比。
计算结果与实际接近。
适合大平板和结晶间隔小的铸件。
14/33
• 3、“折算厚度”法则
R2 t
K2
R V1 为铸件折算厚度或铸件模数。
A1
铸造工艺毕业设计

铸造工艺毕业设计【篇一:铸造工艺毕业论文】毕业论文题目浅谈铸造工艺与品质检查姓名所在系别专业班级学号指导教师日期摘要:为了提高铸件的可靠性、适用性;提高产品在市场上的竞争能力,对铸件质量的要求不断提高。
铸件质量的概念也发生了相应的变化,“质量”的含义至少包含两个方面的内容:一是产品质量,即铸件满足用户要求的程度;或按其用途在使用中应取得的功效,这功效是反映铸件结构特征、材质的工作特性和物理力学特性的总和,是评价铸件质量水平和技术水平的基本指标。
二是工程质量,指的是铸制毛坯和铸制零件的生产过程对产品质量的保证程度,即铸件在具体使用条件下的可靠性。
这一指标在相当大的程度上决定于前述的功效指标,还与稳定性、耐用性和工艺性等指标有关。
标准是由国家承认的标准制订单位批准的对各种产品(铸件)规格、材料规格、试验方法、术语定义或推荐的工艺方法的规定。
我国的国家标准是由国家技术监督局批准并颁行的,有关铸件质量的各种标准一经接纳、贯彻与实施,可取得明显的效果和效益。
国际标准是由国际标准化组织批准并颁行的。
我国是国际标准化组织的主要成员国之一,按国家现行的政策,国际标准可以等效地视为国家标准。
关键词:铸件质量;提高铸件品质;稳定性;耐用性目录引言 (3)第一章铸件质量标准 (4)1.1 铸件精度标准 (4)第二章铸件缺陷分类 (6)2.1铸件缺陷 (6)2.2废品与铸件质量 (11)2.3 修补与缺陷防止 (11)第三章铸造过程中的质量控制技术................................. 错误!未定义书签。
3.1影响铸件质量的因素 (12)3.2 技术准备过程的质量控制 (13)3.2.1质量标准的制定 (13)3.2.2铸件设计 (14)3.2.3铸造工艺、工装设计及验证 (15)3.3生产工艺过程的质量控制 (15)3.3.1原材料的质量控制 (15)3.3.2设备及工装的质量控制 (16)3.3.3 工艺过程的质量控制 (16)第四章铸件质量检测技术与缺陷诊断方法 (17)4.1铸件外观质量检测 (17)4.1.1 铸件形状和尺寸检测 (17)4.2 铸件内在质量检测 (17)4.3 铸件质量无损检测技术 (18)结论 ......................................................................... 18 参考文献???????????????????????????????..19 答谢。
材料成型第4章_铸造工艺设计1.答案

(2)尽量使铸件重要加工面或大部分加 工面、加工基准面放在一个砂型内,减少 错箱、披缝和毛刺,提高铸件精度。
床身铸件,其顶部平面为加工基准面。 图中方案a在妨碍起模的凸台处增加了外部型芯,因采用整模造型使加工 面和基准面在同一砂箱内,铸件精度高,是大批量生产时的合理方案。 若采用方案b,铸件若产生错型将影响铸件精度,但在单件、小批生产条 件下,铸件的尺寸偏差在一定范围内可用划线来矫正,故在相应条件下方 案b仍可采用。
25
方案1要考虑采用活块造型或加外型芯才能铸造; 方案2则省去了活块造型或加外型芯。
26
使铸件全部或大部分放在同一砂型
尽量使加工基准面与大部分 加工面在同一砂型内
不合理
合理
尽量使加工基准面与大部分 加工面在同一砂型内
27
(3)使型腔和主要型芯位于下箱,以便于造型、下 芯、合型和检查型腔尺寸。
于垂直或倾斜位置。图为油盘铸件的合理浇注位 置。
图4-2b 大面积薄壁铸件浇注位置
(4)对于容易产生缩孔的铸件,应使厚的 部分放在铸型的上部或侧面,以便在铸件 厚壁处直接安置冒口,使之实现自下而上 的定向凝固
铸钢卷扬筒,浇注时厚端放在上部是合理的; 反之,若厚端放在下部,则难以补缩。
23 图4-2-1 有热节的浇注位置
铸件的造型位置由分型面决定,而铸件的浇注位 置与造型位置通常是一致的。
浇注位置和分型面对铸件质量及铸造工艺都有很 大影响。
选择原则:着眼于控制铸件的凝固顺序
估计到铸件发生缺陷的可能
1.浇注位置的选择原则
(1) 铸件的重要加工面或主要工作面应朝下或位于 侧面,避免砂眼、气孔和夹渣
因为铸件的上表面容易产生砂眼、气孔、夹渣等缺陷,组 织也不如下表面致密。如果这些加工面难以朝下,则应尽 力使其位于侧面。当铸件的重要加工面有数个时,则应将 较大的平面朝下。
滑动轴承座铸造工艺设计

材料成型技术基础课程设计设计题目院系:机械工程学院专业:机械设计制造及自动化班级:姓名:学号:指导老师:时间:滑动轴承座铸造工艺设计摘要砂型铸造在机械制造业中占有非常重要的地位,不受质量、尺寸、材料种类及生产批量的限制。
而用于装轴瓦的部分总称壳件其上半部称为轴承盖下半部称为滑动轴承座。
本次对滑动轴承座进行设计。
滑动轴承座大多用铸铁制造材料为HT200或ZG200ZG400承受载荷大的采用铸钢或钢板焊接结构。
广泛应用于冶金矿山输送系统环保设备等。
滑动轴承座在铸造过程中有严格的技术要求。
本文通过对滑动轴承座的研究得出滑动轴承座的铸造工艺。
关键词:砂型铸造技术要求铸造工艺目录摘要第1章绪论 (1)1.1课程设计的意义 (1)1.2设计题目的提出 (1)第2章材料的确定 (3)第3章结构工艺分析 (4)第4章工艺方案的设计 (5)4.1 铸型种类方法确定 (5)4.2 型芯结构及其制造 (5)4.3 分型面的筛选 (5)4.4 铸造位置及浇注口的确定 (6)第5章铸件工艺参数确定 (7)5.1 加工余量 (7)5.2 起模斜度及圆角确定 (10)5.3 收缩量选择 (10)5.4型芯及型芯头选择 (10)5.5 冒口尺寸确定 (10)附录总结第一章绪论1.1课程设计的意义材料成形技术种类较多,应用广泛,生产效率高,是现代制造业的基础。
而课程设计是学生学完了材料成形技术基础课程后对这本书进一步了解的练习性的教学环节,是学习深化与升华的重要过程,是对学生综合素质与工程实践的能力培养应在指导教师指导下独立完成一项给定的设计任务,编写符合要求的设计说明书,并正确绘制有关图表。
在课程设计工作中,应综合运用多学科的理论、知识与技能,分析与解决工程问题。
应学会依据技术课题任务,进行资料的调研、收集、加工与整理和正确使用工具书培养学生掌握有关工程设计的程序、方法与技术规范,提高工程设计计算、图纸绘制、编写技术文件的能力培养学生掌握实验、测试等科学研究的基本方法锻炼学生分析与解决工程实际问题的能力。
材料成型工艺基础——铸造

机器造型铸件精度高,余量小;手工造型误差大,余量 也大。灰铸铁加工余量小,铸钢加工余量大。
(3) 拔模斜度
(4) 铸造圆角 圆角半径一般约为相交两壁平均厚度的1/4
(5) 型芯头
型芯头的作用:定位、支撑和固定砂芯
(6) 最小铸出孔及槽
最小铸出孔直径 灰口铸铁件 12~15 15~30 30~50 铸钢件 30~50 50
(2) 对于一些需要补缩的铸件,为防止铸件产生缩孔、缩松的 缺陷,应使铸件较厚的部位放在铸型的上部或侧面。 (3) 应将面积较大的薄壁部位置于铸型下部,或使其倾斜位置
(4) 铸件的大平面应朝下
2. 分型面的选择 (1)分型面应选在铸件的最大截面处。
(2)应尽量减少分型面的数量,并尽可能选择平面分型。
(2) 冷裂 冷裂的特征是:裂纹细小,呈连续直线状,缝内有金属 光泽或轻微氧化色。 冷裂的防止: 1)使铸件壁厚尽可能均匀; 2)采用同时凝固的原则; 3)对于铸钢件和铸铁件,必须严格控制磷的 含量,防止冷脆性。
作 业
1.铸件的凝固应遵循什么基本原则?优缺点是 什么?各适用于什么范围? 2.在生产中,为什么要选择共晶成分、近共晶 成分或凝固温度范围小的合金作为铸造合金?
2)给定成分的铸件,缩孔和缩松的总容积是一定值,适 当增大铸件的冷却速度可促进缩松向缩孔转化; 3)合金收缩越大,铸件的缩孔体积越大; 4)浇注温度越高,液态收缩越大,缩孔的体积越大; 5)缩孔和缩松总是存在于铸件的最后凝固部位。如果铸 件设计壁厚不均匀,则在厚壁处易于出现缩孔或缩松。
2)缩孔和缩松的防止 防止缩孔和缩松常用的工艺措施就是控制铸件的凝固
提高25~30%,但伸长率有所下降。
(3) 可压铸出形状复杂的薄壁件。 (4) 生产率高。国产压铸机每小时可铸
铸造工艺设计
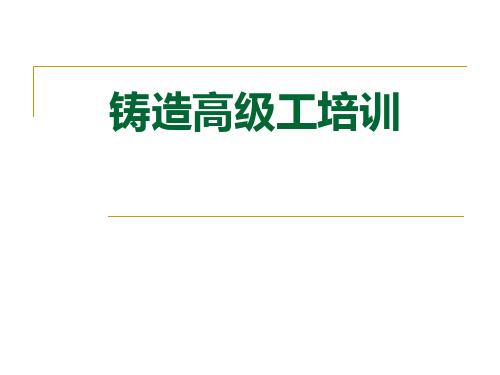
铸件设计步骤:
①功用设计;②依铸造经验修改和简化设计;③冶金设计(铸件材 质的选择和适用性)④考虑经济性。
审查零件图的作用:
①审查零件结构是否符合铸造工艺的要求。②在既定的零件结构下, 考虑铸造过程中可能出现的主要缺陷,在工艺设计中采取防止措施。
总体设计原则:
在满足使用要求的前提下,尽可使制模、造型、造芯、合箱和清理 等过程简化。
分 型 面: 指铸型的分割或装配面。
正确设置浇注位置和分型面是完成造型、取模、设置浇 冒系统和安装砂芯的需要。
浇注位置的选择
浇注位置:
是指浇注时铸件在铸型中所处的位置。
铸件
铸件
铸件
浇注位置的选择
(1) 重要加工面应处于型腔低面或位于侧面 (2) 大平面应朝下 (3) 面积较大的薄壁部分置于铸型下部或使其处于垂直或倾 斜位置 (4) 容易产生缩孔的铸件,应将厚大部分放在分型面附近的 上部或侧面
铸件图( 毛坯图)
铸件图的画法及尺寸标注:
(1) 按照铸造工艺图及产品图绘制铸件图。
(2)铸件图应表明下列内容:铸件毛面上的 加工定位点(面)、夹紧点(面),加工余量, 拔模斜度,分型面,内浇口和冒口残余,铸件全 部形状和尺寸,未注明的圆角、璧厚,涂漆种类, 铸件允许的缺陷说明等项。
铸件图( 毛坯图)
注意事项
(6)所标注的各种工艺尺寸或数据,不要盖住产品 图上的数据,应方便工人操作,符合工厂的实际条 件。 例如标注拔模斜度,对于手工木模,则应尽量 标注尺寸(毫米)或比例(1/50); 对于金属模则应标注角度,而且所注角度应和 工厂常用铣刀角度相对应。
铸造工艺图纸
铸造工艺图中的符号及表示方法(序)
铸造生产的工艺流程
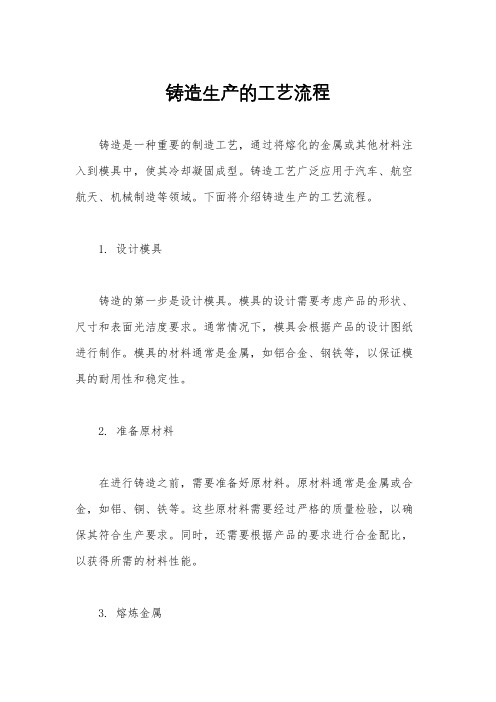
铸造生产的工艺流程铸造是一种重要的制造工艺,通过将熔化的金属或其他材料注入到模具中,使其冷却凝固成型。
铸造工艺广泛应用于汽车、航空航天、机械制造等领域。
下面将介绍铸造生产的工艺流程。
1. 设计模具铸造的第一步是设计模具。
模具的设计需要考虑产品的形状、尺寸和表面光洁度要求。
通常情况下,模具会根据产品的设计图纸进行制作。
模具的材料通常是金属,如铝合金、钢铁等,以保证模具的耐用性和稳定性。
2. 准备原材料在进行铸造之前,需要准备好原材料。
原材料通常是金属或合金,如铝、铜、铁等。
这些原材料需要经过严格的质量检验,以确保其符合生产要求。
同时,还需要根据产品的要求进行合金配比,以获得所需的材料性能。
3. 熔炼金属一旦原材料准备就绪,就需要将金属熔化。
这通常是通过高温熔炉来完成的。
熔炼过程需要严格控制温度和熔炼时间,以确保金属的纯度和均匀性。
在熔炼过程中,还需要添加合金元素,以调整金属的化学成分。
4. 浇铸一旦金属熔化完成,就可以进行浇铸。
在浇铸过程中,熔化的金属被注入到预先设计好的模具中。
浇铸需要注意浇注速度和压力,以确保金属充分填充模具,并避免气孔和缺陷的产生。
同时,还需要控制浇注温度,以避免金属在模具中过早凝固。
5. 冷却凝固一旦金属注入模具中,就需要进行冷却凝固。
在这个过程中,金属会逐渐从液态转变为固态,并最终成型。
冷却时间通常取决于金属的种类和厚度,需要根据实际情况进行调整。
6. 脱模当金属完全凝固后,就可以进行脱模。
脱模是将成型的金属制品从模具中取出的过程。
这个过程需要小心操作,以避免损坏产品表面。
通常情况下,还需要进行后续的去毛刺、打磨等表面处理工艺。
7. 检验和修整最后一步是对铸造产品进行检验和修整。
检验需要对产品的尺寸、形状、表面质量等进行严格检查,以确保产品符合设计要求。
如果发现缺陷或不合格的地方,还需要进行修整或重新铸造。
总结铸造生产的工艺流程包括模具设计、原材料准备、熔炼金属、浇铸、冷却凝固、脱模、检验和修整等多个环节。
材料成形技术基础知识点总结
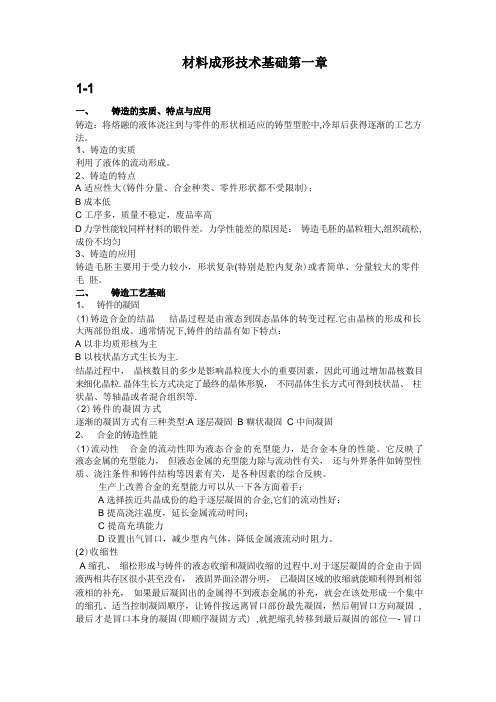
铸造:将熔融的液体浇注到与零件的形状相适应的铸型型腔中,冷却后获得逐渐的工艺方法。
1、铸造的实质利用了液体的流动形成。
2、铸造的特点A 适应性大(铸件分量、合金种类、零件形状都不受限制);B 成本低C 工序多,质量不稳定,废品率高D 力学性能较同样材料的锻件差。
力学性能差的原因是:铸造毛胚的晶粒粗大,组织疏松, 成份不均匀3、铸造的应用铸造毛胚主要用于受力较小,形状复杂(特别是腔内复杂)或者简单、分量较大的零件毛胚。
1、铸件的凝固(1)铸造合金的结晶结晶过程是由液态到固态晶体的转变过程.它由晶核的形成和长大两部份组成。
通常情况下,铸件的结晶有如下特点:A 以非均质形核为主B 以枝状晶方式生长为主.结晶过程中,晶核数目的多少是影响晶粒度大小的重要因素,因此可通过增加晶核数目来细化晶粒. 晶体生长方式决定了最终的晶体形貌,不同晶体生长方式可得到枝状晶、柱状晶、等轴晶或者混合组织等.(2)铸件的凝固方式逐渐的凝固方式有三种类型:A 逐层凝固B 糊状凝固C 中间凝固2、合金的铸造性能(1)流动性合金的流动性即为液态合金的充型能力,是合金本身的性能。
它反映了液态金属的充型能力,但液态金属的充型能力除与流动性有关,还与外界条件如铸型性质、浇注条件和铸件结构等因素有关,是各种因素的综合反映。
生产上改善合金的充型能力可以从一下各方面着手:A 选择挨近共晶成份的趋于逐层凝固的合金,它们的流动性好;B 提高浇注温度,延长金属流动时间;C 提高充填能力D 设置出气冒口,减少型内气体,降低金属液流动时阻力。
(2)收缩性A 缩孔、缩松形成与铸件的液态收缩和凝固收缩的过程中.对于逐层凝固的合金由于固液两相共存区很小甚至没有,液固界面泾渭分明,已凝固区域的收缩就能顺利得到相邻液相的补充,如果最后凝固出的金属得不到液态金属的补充,就会在该处形成一个集中的缩孔。
适当控制凝固顺序,让铸件按远离冒口部份最先凝固,然后朝冒口方向凝固, 最后才是冒口本身的凝固(即顺序凝固方式) ,就把缩孔转移到最后凝固的部位—- 冒口中去,而去除冒口后的铸件则是所要的致密铸件。
材料成型技术-铸造四(冒口设计)

4)煤气加热冒口; )煤气加热冒口; 5)电弧加热冒口; )电弧加热冒口;
6)发热保温冒口: 发热保温冒口: 利用保温剂和发热剂等专门材料制成发热套, 保温剂和发热剂等专门材料制成发热套 利用保温剂和发热剂等专门材料制成发热套,构成冒口 型腔内表面,浇注后发热套材料产生化学反应激烈发热, 型腔内表面,浇注后发热套材料产生化学反应激烈发热, 使冒口金属液温度提高,凝固时间延长。 使冒口金属液温度提高,凝固时间延长。
冒口设计
一、冒口的作用 1、冒口:铸型中能储存一定的金属液,可对铸件进行 冒口:铸型中能储存一定的金属液, 补缩的专门工艺“空腔”称之为冒口。 补缩的专门工艺“空腔”称之为冒口。 铸件在凝固过程中需要补偿的体积变化有: 铸件在凝固过程中需要补偿的体积变化有: 铸型的胀大(体积膨胀) (1)铸型的胀大(体积膨胀) (2)金属液的液态收缩(高温到低温) )金属液的液态收缩(高温到低温) 金属的凝固收缩(液态到固态) (3)金属的凝固收缩(液态到固态)
冒口设计
3.冒口的设计内容 选择冒口的形状及安放位置; (1)选择冒口的形状及安放位置; 初步确定冒口的数量; (2)初步确定冒口的数量; 计算冒口的尺寸; (3)计算冒口的尺寸; 校核冒口的补缩能力; (4)校核冒口的补缩能力; 校核工艺出品率。 (5)校核工.冒口的类型: 冒口的类型: 按位置分类:顶冒口和边冒口; 1)按位置分类:顶冒口和边冒口; 2)按覆盖情况分类:明冒口和暗冒口。 按覆盖情况分类:明冒口和暗冒口。
三 、 冒口的有效补缩距离
冒口的有效补缩距离:致密的冒口作用区与致 冒口的有效补缩距离: 密的末端区之和称为冒口的有效补缩距离, 密的末端区之和称为冒口的有效补缩距离,即 冒口区+ b = 冒口区+末端区 = c + e 如果被补缩部分的长度大于这个距离, 如果被补缩部分的长度大于这个距离,就 会产生缩孔和缩松;小于b时铸件才是健全的。 会产生缩孔和缩松;小于b时铸件才是健全的。 冒口有效补缩距离是指长度方向的, 冒口有效补缩距离是指长度方向的,实际 上冒口的补缩作用是一个范围。 上冒口的补缩作用是一个范围。 以圆柱冒口为例:以冒口中心为圆心, 以圆柱冒口为例:以冒口中心为圆心,用 冒口半径加上有效补缩距离为半径做圆,圆内 冒口半径加上有效补缩距离为半径做圆, 就是冒口的有效补缩范围 有效补缩范围。 就是冒口的有效补缩范围。
材料成型工艺学二复习思考题
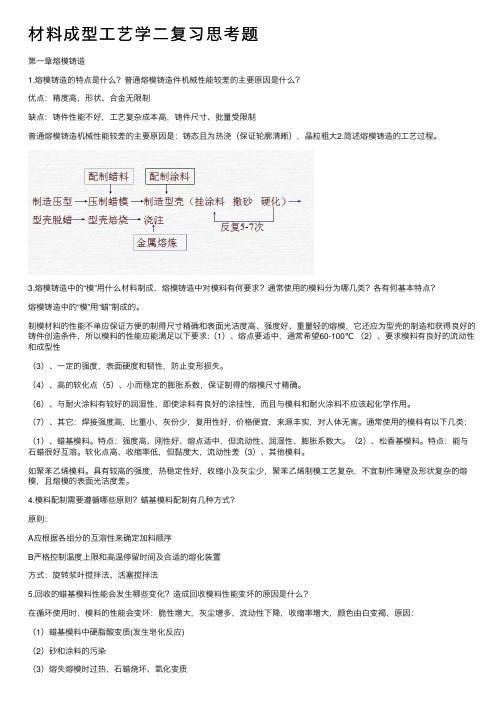
材料成型⼯艺学⼆复习思考题第⼀章熔模铸造1.熔模铸造的特点是什么?普通熔模铸造件机械性能较差的主要原因是什么?优点:精度⾼,形状、合⾦⽆限制缺点:铸件性能不好,⼯艺复杂成本⾼,铸件尺⼨、批量受限制普通熔模铸造机械性能较差的主要原因是:铸态且为热浇(保证轮廓清晰),晶粒粗⼤2.简述熔模铸造的⼯艺过程。
3.熔模铸造中的“模”⽤什么材料制成,熔模铸造中对模料有何要求?通常使⽤的模料分为哪⼏类?各有何基本特点?熔模铸造中的“模”⽤“蜡”制成的。
制模材料的性能不单应保证⽅便的制得尺⼨精确和表⾯光洁度⾼、强度好、重量轻的熔模,它还应为型壳的制造和获得良好的铸件创造条件,所以模料的性能应能满⾜以下要求:(1)、熔点要适中,通常希望60-100℃(2)、要求模料有良好的流动性和成型性(3)、⼀定的强度,表⾯硬度和韧性,防⽌变形损失。
(4)、⾼的软化点(5)、⼩⽽稳定的膨胀系数,保证制得的熔模尺⼨精确。
(6)、与耐⽕涂料有较好的润湿性,即使涂料有良好的涂挂性,⽽且与模料和耐⽕涂料不应该起化学作⽤。
(7)、其它:焊接强度⾼,⽐重⼩,灰份少,复⽤性好,价格便宜,来源丰实,对⼈体⽆害。
通常使⽤的模料有以下⼏类:(1)、蜡基模料。
特点:强度⾼、刚性好、熔点适中,但流动性、润湿性、膨胀系数⼤。
(2)、松⾹基模料。
特点:能与⽯蜡很好互溶。
软化点⾼、收缩率低,但黏度⼤,流动性差(3)、其他模料。
如聚苯⼄烯模料。
具有较⾼的强度,热稳定性好,收缩⼩及灰尘少,聚苯⼄烯制模⼯艺复杂,不宜制作薄壁及形状复杂的熔模,且熔模的表⾯光洁度差。
4.模料配制需要遵循哪些原则?蜡基模料配制有⼏种⽅式?原则:A应根据各组分的互溶性来确定加料顺序B严格控制温度上限和⾼温停留时间及合适的熔化装置⽅式:旋转浆叶搅拌法、活塞搅拌法5.回收的蜡基模料性能会发⽣哪些变化?造成回收模料性能变坏的原因是什么?在循环使⽤时,模料的性能会变坏:脆性增⼤,灰尘增多,流动性下降,收缩率增⼤,颜⾊由⽩变褐,原因:(1)蜡基模料中硬脂酸变质(发⽣皂化反应)(2)砂和涂料的污染(3)熔失熔模时过热,⽯蜡烧坏、氧化变质6.哪⼏种处理⽅法可以使旧的蜡基模料的性能得到⼀定程度的恢复?(1)盐酸(硫酸)处理法(2)活性⽩⼟处理法(3)电解法7.熔模铸造的型壳是如何制造的(由哪三个基本步骤组成)?熔模铸造制造⼀般铸件时型壳需要涂挂⼏层?型壳的制造⼯艺:涂覆涂料→撒砂→⼲燥硬化8.熔模铸造制造型壳时可以采⽤哪⼏种粘结剂,各种粘结剂有何特点?它们的硬化机理是什么,⼯业上分别采⽤什么⽅法硬化?第⼀种是硅酸⼄脂⽔解液。
材料成型与工艺课后答案 1-3,1-4
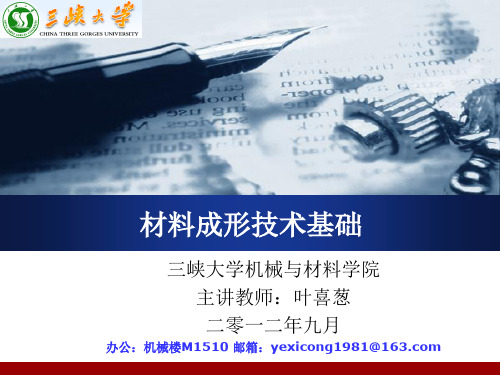
铸造工艺图:铸造工艺图是利用各种工 艺符号,把制造模样和铸型所需的资料, 直接绘在零件图上的图样。
它是制造模样和铸型,进行生产准备和铸件检验的依 据——基本工艺文件 收缩余量
工 浇注位置 艺 方 分型面的选择 案
工 加工余量 艺 参 起模斜度 数 铸造圆角 型芯及芯头
浇 组成及作用 注 常见类型 系 统 冒口
2)铸件的大平面应朝下,减少辐射,防开裂夹渣。
3)面积较大的薄壁部分应置于铸型下部或垂直、 倾斜位置。防止产生浇不足、冷隔。
4)易形成缩孔的铸件,较厚部分置于上部或 侧面。考虑安放冒口利于补缩。
5) 应尽量减少型芯的数量。
6)要便于安放型芯、固定和排气。
Back to page-4
浇注位置
较大的铸件,宜将内浇道
从铸件薄壁处引入,以利 铸件同时凝固,减少铸件 的内应力、变形,防止裂 纹产生。
二、浇注位置的选择-六点注意
浇注位置:浇注时铸件在铸型中所处的空间位置;浇 注位置对铸件质量及铸造工艺都有很大影响。选择时应考 虑如下原则:
选择原则:
1)铸件的重要加工面和受力面应朝下或位于侧面, 避免砂眼气孔和夹渣。
1)冒口就近设在铸件热节的上方或侧旁; 2) 冒口尽量设在铸件最高、最厚的部位,对低处的热节增设补 贴或使用冷铁。 3)冒口不应设在铸件重要的、受力大的部位,以防晶粒粗大降 低力学性能。 4)冒口位置不要选在铸造应力集中处,应注意减轻对铸件的收 缩阻碍,以免引起裂纹。 5)尽量用一个冒口同时补缩几个热节或铸件 6)冒口布置在加工面上,可借加工精整铸件表面,零件外观质 量好。 7)对不同高度上的多个冒口,应用冷铁使各个冒口的补缩范围 相隔开
起模斜度的大小根据立壁的高度、造型方法和模样材料来 确定:立壁愈高,斜度愈小;外壁斜度比内壁小;机器造型 的一般比手工造型的小;金属模斜度比木模小。具体数据可 查有关手册。一般外壁为3º ~ 15°,内壁为3°~10°。
铸造工艺设计

课程设计的内容
铸造工艺设计的主要内容,包括: 1.铸造工艺图 2.铸造工艺卡 3.铸型装配图 4.铸件图(毛坯图) 5.模样图 6.芯盒图 7.砂箱图 8.模板图(模板装配图)
铸造基本过程
一.设计铸造工艺图: 铸造工艺图是铸造行业所特有的
一种图纸,它规定了铸件的形状和尺寸, 也规定了铸件的基本生产方法和工艺过 程,以便模具制造、造型、检验和技术 存档。将已确定的各项工艺设计内容, 用不同颜色和符号描绘在产品零件图纸 上或用文字注明在图纸上。
(2)工艺方案的确定 铸造工艺性分析可不考虑,详细分析、说明以下 内容的设计依据: ①浇注位置的确定:写明设计的依据,选择几种可 行的方案,优缺点分析; ②分型面的选择:写明确定的依据,选择几种可行 的方案,优缺点分析; ③砂芯分块:芯头尺寸与结构,验算; ④铸造工艺参数的选择:各工艺参数选择的依据, 书、页、表;
四、填写铸造工艺卡
铸造工艺卡片 零件图号 炉内配料 产品型号 设计材质
金属 材料
造 型 和 制 芯 型 芯 材 料
零件 净重
联铸 件数
工艺文件代号 共 页 零件名称 铸件毛 型 内 重 铸件数 砂型类别 (干潮型) 造型方法 (机器、手工) 涂料 烘干次 数
第 页 浇注系统重
砂箱和模板 芯板 图号 规 格 (长.宽. 上砂箱 高) 中砂箱 下砂箱 模板 芯盒数 砂型 砂芯 类别 重量 类 别 重量 类别
封闭式浇注系统适合中小型铸铁件 开放式浇注系统适合易氧化的有色金属件、球铁件
及柱塞包浇注的中大型铸钢件。
确定浇注系统的结构与布置:内浇口的引入
位置,浇口杯、直浇道、横浇道、内浇道等的 结构;
浇注系统的计算:包括铸件毛重、浇注时间、
铸造成形技术-铸造工艺设计

①[分型面应选择最大截面处]:
②[分型面的选择应尽量简化工序]:
[ 活块造型三维动画分析] [pro/E活块造型三维动画分析]
[砂芯代替活块三维动画分析] [pro/E砂芯代替活块三维动画分析]
③[分型面应尽量平直]:
右图为采用平直 分型面的造型图
④[基准面放在同一个砂箱中]:
加工基准面放在同一个砂箱中,以避免产生错箱披缝 和毛剌,降低铸件精度和增加清理工作量。
⑤[尽量减少分型面]:
二箱造型动画的动图演示: 观看影像 三箱造型动画的动图演示: 观看影像
材料成型技术基础
铸造成形技术(三)
童幸生 2004年8月
铸造工艺设计
浇注位置的选择原则 分型面的选择原则 铸造工艺参数的确定 铸件三维造型工艺分析
浇注位置的选择原则
铸造工艺设计是根据铸件结构特点、 技术要求、生产批量、生产条件等,确 定铸造方案和工艺参数,绘制图样和标 注符号,编制工艺卡和工艺规范等。其 主要内容包括制订铸件的浇注位置、分 型面、浇注系统,确定加工余量、收缩 率和起模斜度,设计砂芯等。
② [铸件宽大平面应朝下]:
大平面铸件应朝下:这是因为在浇注过程中,熔融金属对型腔上表面的 强烈辐射,容易使上表面型砂急剧地膨胀而拱起或开裂,在铸件表面造成 夹砂结疤缺陷
③ [面积较大的薄壁部分应置于铸型下部或垂直]:
面积较大的薄壁部分应置于铸型下部或垂直、倾斜位置: 如箱盖铸件, 将薄壁部分置于铸型上部,易产生浇不足、冷隔等缺陷。改置于铸型于下 部后,可避免出现缺陷。
铸造成型工艺过程

铸造成型工艺过程铸造是一种常见的金属成型工艺,广泛应用于各个行业,如汽车、航空航天、机械制造等。
铸造成型工艺通过将金属融化,倒入铸型中,经过冷却固化后,得到所需的零件或产品。
下面将详细介绍铸造成型工艺的步骤和注意事项,以便帮助读者了解和运用该工艺。
首先,铸造成型工艺的第一步是设计和制作铸模。
铸模是铸造的重要工具,它决定了最终产品的形状和尺寸。
在设计铸模时,要考虑材料的流动性、收缩率、气孔等因素,以确保最终产品的质量。
制作铸模可以采用传统的木模、石膏模,也可以使用更高精度的金属模具。
接下来是准备材料和设备。
根据所需产品的要求,选择适当的金属材料,并将其加热到熔点。
常用的金属包括铝合金、铜合金、铸铁等。
同时,将制作好的铸模放置在铸造设备中,通常是砂型或金属型。
然后进行金属融化和熔炼。
将选定的金属材料放入熔炉中,加热至熔点以上,使其融化成液态。
在熔炉中加入剂和合金,以调整材料的化学成分和性质。
熔炼是铸造过程中非常重要的一步,需要稳定的温度控制和适当的搅拌,以保证金属液的均匀性和纯度。
接下来就是铸注,也就是将融化的金属倒入铸模中。
在倒注过程中,要注意控制倒注速度和温度,以免形成气孔或裂纹。
同时,要避免气泡和杂质的混入,可采用真空铸造或压力铸造等方法提高产品质量。
倒注完成后,待金属冷却固化,即可取出铸件。
冷却时间取决于金属的类型和厚度。
通常,较大的铸件需要更长的冷却时间。
一旦铸件冷却完全,可以从铸模中取出,并进行后续的加工处理,如修整、研磨、清洁等。
最后,进行产品的检验和质量控制。
铸造成型工艺中,检验是非常重要的一环,可以采用金相分析、物理性能测试等方法检测产品的性能和质量。
通过合格的质检,可以确保产品符合设计要求并达到客户的需求。
总结来说,铸造成型工艺是一种重要的金属加工工艺,具有广泛的应用前景。
在应用该工艺时,需要注意设计和制作铸模、准备材料和设备、金属融化和熔炼、倒注和铸件冷却、产品检验和质量控制等多个步骤。