Dynaform分析报告_要求_格式
dynaform报告
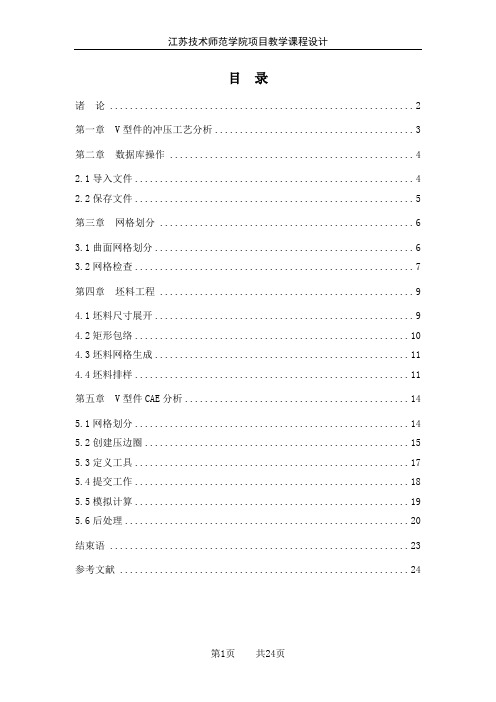
目录诸论 (2)第一章 V型件的冲压工艺分析 (3)第二章数据库操作 (4)2.1导入文件 (4)2.2保存文件 (5)第三章网格划分 (6)3.1曲面网格划分 (6)3.2网格检查 (7)第四章坯料工程 (9)4.1坯料尺寸展开 (9)4.2矩形包络 (10)4.3坯料网格生成 (11)4.4坯料排样 (11)第五章 V型件CAE分析 (14)5.1网格划分 (14)5.2创建压边圈 (15)5.3定义工具 (17)5.4提交工作 (18)5.5模拟计算 (19)5.6后处理 (20)结束语 (23)参考文献 (24)诸论Dynaform是由美国ETA公司与LSTC公司共同推出的针对板料成形的数值模拟的专业软件,是目前该领域中应用最广泛的CAE软件之一。
它可以预测成形过程中板料的破裂、起皱、减薄、划痕、回弹,评估板料的成形性能,从而为板料成形工艺及模具设计提供帮助;可以用于工艺及模具设计涉及的复杂板成形问题;还包括板成形分析所需的与CAD软件的接口、前后处理、分析求解等所有功能。
本文简述了CAE技术在V型件冲压成形中的应用,通过对拉延工序进行冲压成形模拟分析,提前预知成形缺陷,并采取有效措施,进行工艺参数的调整与优化。
实践证明,分析计算缩短了模具制造周期,减少了模具调试次数,节约了生产成本。
第一章 V型件的冲压工艺分析本文采用V型件形状如图1-1所示,材料为B170P1,厚度1.2mm,整体来看,具有材料较薄,外形尺寸不大,深度较大,成型较困难,有可能出现破裂或起皱等缺陷,因此可先进行CAE分析,观察成型情况。
图 1-1 V型件第二章数据库操作2.1导入文件在桌面上双击图标,进入Dyanform操作界面如图2.2所示。
图2-1操作界面选择“BSE”→“Preparation”→“Import”导入菜单项,将需要分析的V型件的IGS格式的模型文件导入到数据库中,如图2-2所示。
图2-2导入文件2.2保存文件点击下拉菜单“File”→“Save as”,然后命名为“v1.df”,点击“保存”。
dynaform分析报告

Dynaform分析报告1. 引言本文旨在对Dynaform进行分析,并提供一种基于“step by step thinking”的思考方式。
首先,我们将介绍Dynaform的概念和用途,然后分析其功能特点,并提供一些使用Dynaform的最佳实践。
2. 概述Dynaform是一种表单设计与管理工具,可以帮助用户创建各种类型的表单,并对表单数据进行管理和分析。
通过Dynaform,用户可以轻松地设计出符合自身需求的表单,并实现高效的数据收集与分析。
3. 功能特点3.1 表单设计Dynaform提供了丰富的表单设计功能,用户可以通过简单的拖放操作来创建各种表单元素,如文本框、下拉菜单、复选框等。
同时,Dynaform还支持对表单进行样式定制,使表单能够符合用户的品牌形象。
3.2 数据收集与管理通过Dynaform,用户可以方便地收集表单数据,并对数据进行管理。
Dynaform提供了数据验证功能,可以确保收集到的数据的准确性和完整性。
用户可以通过设置条件和规则,对表单数据进行自动化处理,如计算、筛选、转换等。
3.3 数据分析与报告Dynaform还提供了强大的数据分析与报告功能。
用户可以通过简单的操作,生成各种类型的报告,如柱状图、折线图、饼图等。
通过这些报告,用户可以直观地了解表单数据的分布和趋势,从而做出更加明智的决策。
4. 使用最佳实践4.1 设计清晰的表单在使用Dynaform设计表单时,应该注意保持表单的清晰和简洁。
避免添加过多的表单元素,以免给用户带来困惑。
同时,应该合理地布局表单元素,使其易于填写和理解。
4.2 设置数据验证规则为了确保数据的准确性和完整性,应该在Dynaform中设置合适的数据验证规则。
根据表单的特点和需求,可以设置必填字段、数据格式要求等规则,以防止用户填写错误或不完整的数据。
4.3 开展数据分析Dynaform提供了丰富的数据分析功能,用户应该充分利用这些功能,对收集到的数据进行分析和挖掘。
dynaform实验报告

机电与能源实验中心实 验 报 告实验名称冲压工艺及模具设计实验 专业班级 机制091 姓 名 学 号 30906010宁波理工实验项目名称:基于Dynaform的圆筒形零件拉深成形模拟报告人:学号:3090601专业/班级:机制091实验时间:2012.10.17 指导教师:一、实验目的与要求【实验目的】1.掌握Dynaform板材成形CAE分析的基本方法。
2.掌握基于Dynaform的拉深成形方法,能进行后处理分析。
【实验题目与要求】筒形件拉深,直径为学号后三位加100,深度为直径的2.5倍,凸缘宽度为半径的35%。
前处理文件名为,学号_姓名拼音首字母,其它自定。
如学号为3090611138的张三同学,筒形件直径为238mm,前处理文件名为:3090611138_zs.df 。
模拟完成后,写模拟分析报告,两周内交班长。
请班长按学号先后清理整齐,上交。
要求必须写清楚下面内容:1. 模拟条件:零件名称、厚度t=2、材料DQSK36、成形条件自行优化(成形方式,速度等)。
标出零件尺寸。
2.修改成形参数,优化结果。
研究有无压边力的影响,压边力大小的影响;3. 结果:●给出dynaform变形网格图。
●给出变形完成(最后一帧)的成形极限图(Forming Limit Diagram);●给出变成完成(最后一帧)的厚度变化图(Thickness);●给出压边力曲线;二、实验方法、步骤、内容(样例)1.利用三维造型软件对待分析的产品进行三维建模,如图1所示。
图1三维建模2.将模型保存为*.igs格式,导入Dyanform,并进行网格划分,如图2所示。
图2划分网格模型3.设置Dynaform的前处理模拟类型_Double action______,板材厚度__2____,工序类型__拉伸_____;零件材料_DQSK___36_____;工具运动速度_____5000_____;压边圈闭合速度____2000______;压边力___200000________;4.启动后处理,并查看结果;a)最后一帧的成形极限图,如图3所示。
模具设计制造DYNAFORM实验指导书

板料成形CAE分析及排样上机指导书黄玉萍编王菲茹审南昌航空大学飞行器制造工程系二○一零年十月板料成形CAE分析及排样一、实验目的和要求:1、认识板料成形CAE软件Dyanform的操作界面;2、了解板料成形CAE分析的基本方法和思路;3、掌握坯料排样的基本方法,输出排样报告。
二、实验设备计算机、DYNAFORM(V5.2)三、实验内容1、板料成形CAE分析2、坯料排样四、实验步骤练习一、板料成形CAE分析1、Dynaform界面简介在桌面上双击DF5.2图标,进入Dyanform操作界面(如图1)。
图1 Dynaform界面快捷键:CTRL+鼠标左键旋转;CTRL+鼠标右键缩放2、导入零件模型,保存文件打开下拉菜单File->Import,如图2所示,在F:\dynaform\BLANK_CAE目录下分别导入文件punch.igs,binder.igs,die.igs和bl an k.igs。
图2 导入、保存文件菜单导入上述文件后,点击Save As 在F:\BLANK_CAE\STU目录下,以姓名作为文件名,保存文件*.df。
图3 导入文件窗口图4 库文件保存窗口3、更改零件层名打开下拉菜单Parts->Edit,对应不同的零件更改层名,改好层名后保存文件。
图5 修改层名窗口4、进行网格划分打开DFE-->Preparation菜单(如图6所示),进入模面工程界面,点击MESH TOOL,进入网格划分窗口,如图7所示,修改相应的参数,点击OK后点击Apply按钮进行网格划分。
依次对Punch,Die,和Binder进行网格划分。
打开BSE--> Preparation菜单,进入坯料工程界面,点击PART MESH进行坯料网格划分,经网格划分后的零件如图8所示。
图6 DFE菜单图7 网格划分操作界面图8 网格化后的零件5、定义工具和坯料材料(1)定义工具打开Tools-->Define Tools菜单,进入工具定义窗口(如图9所示)。
dynaform拉伸件实验报告

杯形件拉深有限元分析报告
1、几何模型
凸模
压边圈
坯料
凹模
凸模尺寸Φ18mm,模具间隙取1.1t。
坯料直径Φ50mm
压边圈内径为Φ24mm,外径为Φ54mm
2、材料模型和性能参数
材料选用DQSK低碳钢,板料厚度1mm。
屈服准则采用三参数Barlat—Lian各向异性屈服函数。
本构关系如下:
板料力学性能参数表
3、接触类型以及边界条件
接触类型:forming-one-way-surface-to-surface。
动态摩擦系数取0,静态摩擦系数0.125。
4、模拟结果分析:
厚度变化:
厚度云图
成形件厚度分布规律
不同点在不同时刻厚度变化板料厚度对成形性能的影响
摩擦系数对成形性的影响
模具圆角半径对成形性的影响
压边力大小对成形性的影响。
Dynaform控制参数分析

8.2选择Drawbead的相应位置
8.3选择格Drawbead阻力系数
如图所示位置:5,7,16为40% 15为30% 13和9位10% 其余设为5%
锁定drawbead
• 选择所有的drawbead • 选择Die或者Binder上 • 投影并锁定
9.控制参数界面说明
IX. 控制参数:
时间步长和CPU数量
凸模和凹模分别参照产品上表面 (下表面) 和 下表面 (上表面) .如果之前只有其中的一个模 面上表面或者中面或者下表面.使用几何等距 的方式.
Outer Top Middle Tipping Middle
Inner
Bottom
三种设置
传统设置 快速设置 自动设置
具有最大限度的灵活性。 可以添加任意多个辅助 工具,同时也可以定义 简单的多工序成形。但 是设置非常繁琐,用户 需要仔细定义每一个细 节。很容易出错 需要更多的设置时间, 不易于初学者学习,易 出错 手工定义运动、载荷曲 线,可任意修改,但是 不做正确性检查
网格细分参数
隐式计算参数
DYNAFORM/AutoSetup
X.
总结:
Click the Summary… button on the bottom of the mainly GUI The Summary tree list will list all the information of the current setup The user should check that the time of each stage is not Zero. Or the program will warning and can’t be output the dyn file
冲压dynaform分析

《DYNAFORM-3D盒型件的正向拉深成型模拟》实验报告
六、实验结果分析
采用成形极限图(FLD)对成形件的质量进行分析。
冲压成形极限是指板料在冲压加工中所能达到的最大变形程度。
成形极限包含两方面的因素:变形区的变形极限和传力区的承载能力。
成形极限所研究的范围主要是以伸长为主的变形。
对板料冲压来说,厚度方向的应力很小,可以忽略不计,一般都认为是平面应力状态。
以最大主应变作纵坐标,以最小主应变作横坐标,即可绘出成形极限图。
如应变在界限曲线以上,零件将发生破裂;应变在界限曲线以下,零件将成形成功。
dynaform报告

一、任务分析本次有限元分析汽车门板拉深件,零件如图1所示,要求一次冲压成型,请设置合适的冲压参数分析没有拉裂与起皱。
图1 汽车门板拉深件二、有限元分析模型建立1 凸模的建立1)根据冲压件的形状建立凸模如图2所示:图2 冲压件凸模2)对凸模进行网格分析,具体参数选择如下:网格类型:tool mesh,最大尺寸:5mm,最小尺寸0.5mm,弦高误差0.15mm,角度:20度,间隙公差2.5mm。
凸模图层OFFSET01 4,图层摘要:单元数目:4480;四边形单元数目:4112;三角形单元数目:368最小单元编号:8537;最大单元编号:13016:节点数目:4382;最小节点编号:8589;最大节点编号:129702 凹模的建立1)根据冲压件与凹模形状设置凹模如图3所示:图3 冲压件凹模2)对凹模进行网格分析,设置参数如下:网格类型:tool mesh,最大尺寸:5mm,最小尺寸0.5mm,弦高误差0.15mm,角度:20度,间隙公差2.5mm。
凹模图层C001V000 1,图层摘要如下曲面数目:107单元数目:6508;四边形单元数目:6070;三角形单元数目:438最小单元编号:1;最大单元编号:6508:节点数目:6395;最小节点编号:1;最大节点编号:64053 压边圈的建立1)根据冲压件与凹模的形状设置压边圈如图4所示:图4 冲压件压边圈2)对压边圈进行网格化处理,具体参数选择如下:网格类型:tool mesh,最大尺寸:5mm,最小尺寸0.5mm,弦高误差0.15mm,角度:20度,间隙公差2.5mm。
压边圈图层OFFSET00 3,图层摘要如下曲面数目:6单元数目:2028;四边形单元数目:1958;三角形单元数目:70最小单元编号:6509;最大单元编号:8536:节点数目:2183;最小节点编号:6406;最大节点编号:8588三、坯料大小的计算及排样1 坯料反求1)此次板料的材料选择为:HSLA350 T36 ,板料的厚度为:1.5mm ,根据冲压件的形状进行反求,反求形状如图5所示:图5 坯料反求形状2)对反求的坯料进行修边,再加上距离为20mm的压边距离,最终的坯料如图6、图7所示:图6 冲压件坯料修边量图7 冲压件最终坯料3)对压边圈进行网格化处理,具体参数选择如下:网格类型:tool mesh,最大尺寸:3mm,最小尺寸0.5mm,弦高误差0.15mm,角度:20度,间隙公差2.5mm。
DYNAFORM分析过程
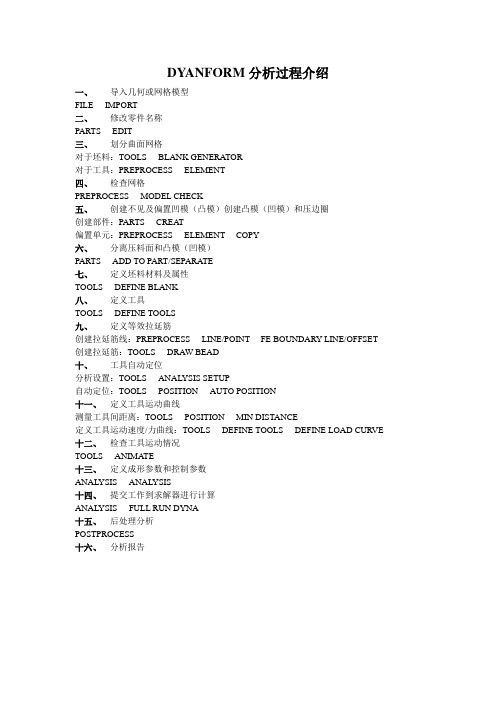
DYANFORM分析过程介绍一、导入几何或网格模型FILE----IMPORT二、修改零件名称PARTS----EDIT三、划分曲面网格对于坯料:TOOLS----BLANK GENERATOR对于工具:PREPROCESS----ELEMENT四、检查网格PREPROCESS----MODEL CHECK五、创建不见及偏置凹模(凸模)创建凸模(凹模)和压边圈创建部件:PARTS----CREAT偏置单元:PREPROCESS----ELEMENT----COPY六、分离压料面和凸模(凹模)PARTS----ADD TO PART/SEPARATE七、定义坯料材料及属性TOOLS----DEFINE BLANK八、定义工具TOOLS----DEFINE TOOLS九、定义等效拉延筋创建拉延筋线:PREPROCESS----LINE/POINT----FE BOUNDARY LINE/OFFSET 创建拉延筋:TOOLS----DRAW BEAD十、工具自动定位分析设置:TOOLS----ANAL YSIS SETUP自动定位:TOOLS----POSITION----AUTO POSITION十一、定义工具运动曲线测量工具间距离:TOOLS----POSITION----MIN DISTANCE定义工具运动速度/力曲线:TOOLS----DEFINE TOOLS----DEFINE LOAD CURVE 十二、检查工具运动情况TOOLS----ANIMATE十三、定义成形参数和控制参数ANAL YSIS----ANAL YSIS十四、提交工作到求解器进行计算ANAL YSIS----FULL RUN DYNA十五、后处理分析POSTPROCESS十六、分析报告。
CAE分析报告

Fቤተ መጻሕፍቲ ባይዱrming process:The blank gravity(重力状态)
10
The binder closing(压边圈闭合)
11
85mm to the draw home
75mm to the draw home
12
65mm to the draw home
55mm to the draw home
17
附页
供应商可自行填入其他重要内容,包括结论以及改 进方案等
18
5
Thinning Ratio Analysis(坯料减薄率分布图) 注:破裂起皱区域要显示出来
零件最大减薄率(或 则最大厚度)云图分 级显示
零件增厚率(或则最小厚度)
6
Wrinkle Analysis : Mean stress (平均应力分布图:起皱判断) 注:仅对DYNAFORM
最大值为材料屈服强度
云图8级显示, 红色表示起皱风 险极高,黄色表 示有一定风险。
最小值为负的材料抗拉强度 7
Wrinkling Criterion Plot(起皱趋势) 注:仅对AUTOFORM
8
Forming Limit Diagram 成型极限图( 必须显示出零件有起皱和破裂的区域)
FLD0:0.35
FLD图必须显示清晰,且对 于DYNAFORM,必须在此页 注明FLD0值。FLD安全裕度 推荐10%-20%
SIMULATION PACKAGE
DYNAFORM () AF SHELL ()
PAMSTAMP () AF MEMBRANCE ( )
Project (项目名称) Part No. (零件号) Part Name (零件名称) Analyst (分析员): Date (日期) SIM Version (模拟文件版本)
基于dynaform软件的方盒零件成型分析

2.1 凹模零件(die)的定义 ..........................................................................7 2.1.1 操作流程 ..................................................................................................7 2.2 凸模零件(punch)的定义 ......................................................................8 2.2.1 具体操作 ..................................................................................................8 2.3 压扁圈零件(binder)的定义 ................................................................8 2.3.1 具体操作 ...................................................................................................8 2.3.2 定位模具结构........................................................................................ 10
dynaform筒形件实验报告

CAE实验报告作者: 学号:学院(系):机械工程专业: 机械制造及自动化题目: 基于dynaform的筒形件冲压成型仿真2013年 4 月1.CAE在研究领域的应用CAE软件从60年代初在工程上开始使用到今天,已经历了40多年的发展历史,其理论和算法都经历了从蓬勃发展到日趋成熟的过程,现已成为在航空、航天、机械和土木结构等众多领域中的产品结构设计时必不可少的数值计算工具。
随着计算机技术的不断发展,CAE系统的功能和计算精度也随之有了很大提高。
计算时可采用CAD技术来建立几何模型,通过前处理完成分析数据的输入,求解得到的计算结果可以通过CAD技术生成形象的图形输出,如生成位移、应力、应变分布的等值线图、彩色云图,以及随机械载荷变化的动态显示图等。
这些结果可有效用于产品质量分析,为工程应用提供实用的依据。
DYNAFORM软件是由美国ETA公司和LSTC公司联合开发的用于板料成形模拟的专用软件包,可方便地求解板料成形工艺及模具设计涉及的复杂问题,是目前该领域中应用最为广泛的CAE软件之一。
它可以预测板料成形过程中的破裂、起皱、减薄和回弹,评估板料的成形性能,为板料成形工艺及模具设计提供帮助,可以显著减少模具设计时间及试模周期,从而提高产品品质和市场竞争力。
目前,DYNAFORM软件已在世界各大汽车、航空、钢铁公司以及众多的大学和科研单位得到了广泛的应用;自进入中国以来,DYNAFORM软件已在长安汽车、南京汽车、上海宝钢、中国一汽、上海汇众汽车公司和洛阳一拖等知名企业得到了成功应用。
2.确定CAE分析对象圆筒形零件的冲压成型过程是一个较为复杂的受力变形过程,其最终的成型结果好坏与否凸模冲压速度、压边圈压力大小及其加载曲线有很大关系。
本次试验采用dynaform专业板料成型分析软件来分析给定条件下的圆筒件冲压成型过程的受力与变形,根据结果分析其中问题以及有待改进的地方。
3. 问题描述为了分析圆筒形件的冲压成型过程,并从分析结果中给出防止出现零件缺陷的措施,现给定筒形件冲压模型,材料选用铝合金AA6009,毛坯厚度1.0mm,模具接触间隙1.0mm,凸模冲压速度5000mm/s,压边圈压力200000N。
基于Dynaform软件的壳体零件成形模拟分析【毕业作品】

基于Dynaform软件的壳体零件成形模拟分析摘要壳体零件是我们日常生活中必不可少的一部分,像平常常见的肥皂盒,矿泉水的盖子,手机套都是的,随着科技日新月异的发展,人们的生活条件越来越好,对生活质量也有着更高的要求,追求着个性化,传统的制作工艺已经不能满足人们对物质文化的需求。
科技在发展,社会在进步。
掌握一门实用的技能可以使自己在竞争激烈的社会中得以站稳脚跟。
Dynaform是一款美国公司研发,对成形零件进行工艺分析的CAE软件。
在拉伸成形分析方面有着独特之处,也是最容易上手的分析软件之一。
有关壳类零件成形工艺,通过冲头,凹模,版料以及压边料的运动情况,用ETA来观察成形过程,通过修改参数变量来控制成形结果,通过多次试验,得到最佳数据。
首先通过ug导入模型,导入的是面,厚度,材料等等可以在软件中自行修改。
如果分析结构不够精准,将会给生产带来巨大麻烦。
本文通过有限元分析软件dynaform对壳类成形零件进行冲压拉伸模拟,希望通过一系列的模拟来论述一些思路,验证一些壳类零件相关数据的影响。
关键词:壳体零件;Dynaform;有限元分析前言 (1)1.第一章DYNAFORM软件介绍 (2)1.1 基本资料及主要应用范围 (2)2.第二章壳类零件拉伸成形前处理 (3)2.1 导入模型零件编辑名 (3)2.2曲线网格划分 (4)2.3 自动设置 (6)2.4 定义BLANK (6)2.5 定义DIE (8)2.6 定义PUNCN (9)2.7 定义BINDER (10)2.8工序参数设置 (10)第三章后处理 (13)3.1 模拟分析 (13)总结 (17)致谢 (18)参考文献 (19)附录 (20)最近几年我国的重工业,机械制造业领域迅猛发展,尤其是这个机械行业。
自从“十五”计划实施,我国机床消费纪录连创新高,大陆市场的机床消费总额和进口额已连续8年排名世界第一,远超世界其它大国,想要成为令全瞩目的机床消费大国,那么作为一个在世界消费领域上发挥重要作用的大国,我国必须从各个方面确保国家的独立自主地位,不能被他国技术资源制约。
dynaform 分析

基于Dynaform盒形件冲压成形仿真研究生姓名: ___ ____学号: _ __学科、专业:机械制造及其自动化 _导师: _基于Dynaform盒形件冲压成形仿真摘要:Dynaform是基于有限元理论建立的成形模拟和分析软件。
拉深成形是一种常见的成形方法,它的实质在于凸缘部分材料的转移和塑性变形,拉深过程中制件的主要失效形式有起皱和破裂。
文章基于Dynaform分析引起起皱的各种因素以及对盒形件拉深成形质量造成的影响,可弥补拉深模具经验设计的不足,缩短模具的设计周期,并对类似产品的模具设计具有一定的借鉴作用。
关键词: Dynaform; 有限元分析;盒形件一、前言冲压成形是现代工业的一种重要的加工成形方法,它广泛应用于汽车、航天等领域,是一个包括了几何、材料以及边界条件非线性的复杂力学过程[1]。
由于冲压件成形力学过程的复杂性,使得依靠实际经验和反复修模、试模,进行模具设计的传统方法既费时又费力。
将计算机模拟引入冲压模具的设计过程中,是现代模具设计发展的必然。
Dynaform板料成形软件,可以预测成形过程中板料的裂纹、起皱、减薄、划痕、回弹,评估板料的成形性能,从而为板料成形工艺及模具设计提供帮助[2]。
它将在缩短模具设计周期和改善产品成形质量等方面发挥极其重要的作用。
盒形件是典型的板料冲压成形制品,在其拉深成形过程中,坯料的凸缘部分是主要变形区,凸缘变形区在切向压应力的作用下,可能产生失稳,其特征表现为凸缘边缘的材料产生皱折。
轻微的起皱可以通过凸凹模间隙来调整,仅在拉深件侧壁上留下皱痕; 但严重的起皱将不能满足制件的尺寸精度和使用要求,并且会导致坯料成形时不能顺利通过凸凹模间隙而造成拉裂失效。
影响拉深件起皱的主要因素有: (1) 是否采用压边装置以及压边力是否合适; (2) 材料的机械性能,如材料弹性模量E、毛坯相对厚度t/D等; ( 3) 拉深成形时的阻力大小[3]。
二、盒形基准件模型的建立(1)320X200,底部圆角R15,边圆角R5,高度H35,拔模斜度3°(2)根据零件尺寸设计模型如图:设置上平面倒角半径R10,文件保存为IGS后缀文件。
dynaform成型研究分析

计算机仿真技术研究报告论文(设计)题目计算机仿真技术研究报告作者所在系别材料工程系作者所在专业材料成型及控制工程作者所在班级B09811作者姓名宋明明作者学号200940xxxxx指导教师姓名赵军指导教师职称讲师完成时间2012 年12 月北华航天工业学院教务处制目录一、喷雾器滤液槽成型研究•••••••••••••• 1二、厨房洗菜盆成型研究••••••••••••••• 5三、自拟件成型研究•••••••••••••••••9四、小轴套成型研究•••••••••••••••••13五、钣金反拉深件成型研究••••••••••••••17六、自拟二次拉深件成型研究•••••••••••••22七、冲压弯曲件成型研究•••••••••••••••26八、液压胀形件成型研究•••••••••••••••30一、喷雾器滤液槽成型研究1.1零件结构分析1.1.1建立三维模型图1为零件的三维模型图图11.1.2结构分析此件名为喷雾器滤液槽,底部有许多小孔,后侧壁上有两个大孔,厚度为1mm,材料为铝材,适合拉深成形。
在进行dynaform划分网格时需要把这些孔进行填补修整。
1.2模具设计下图2为喷雾器滤液槽的拉深模具及压边圈(外围很大的一片即为压边圈)。
压边圈很大是为了保证能够完全压住坯料,防止其起皱。
划分网格后的模具如图3。
图2 图31.3冲压工艺分析1.3.1材料特性分析此材料为AA6009,属于铝材,主要应用在汽车车身板上。
6×××系列铝板材主要含有镁和硅两种元素,故集中了4×××系列和5×××系列的优点。
铝是一种轻金属,其化合物在自然界中分布极广,地壳中铝的含量约为8%(重量),仅次于氧和硅,居第三位。
在金属品种中,仅次于钢铁,为第二大类金属。
铝的导电性、延展性良好,应用范围十分广泛。
铝及铝合金与其它一般特性,铝及铝合金其它金属材料相比,具有以下一些特点:1、密度小。
Dynaform计算机仿真技术研究报告

计算机仿真技术研究报告原文标题计算机仿真技术研究报告作者所在系别作者所在专业作者所在班级作者姓名作者学号指导教师姓名指导教师职称完成时间2013 年12 月北华航天工业学院教务处制目录内容摘要 (2)第1章冲压件仿真 (3)1.1喷雾器滤液槽仿真1.1.1.零件结构分析与模具设计 (3)1.1.2.冲压工艺分析 (3)1.1.3.冲压结果分析 (4)1.2厨房洗菜盆仿真1.2.1.零件结构分析与模具设计 (7)1.2.2.冲压工艺分析 (8)1.2.3.冲压结果分析 (8)1.3自拟冲压件仿真1.3.1.零件结构分析与模具设计 (12)1.3.2.冲压工艺分析 (12)1.3.3.冲压结果分析 (13)第2章二次拉伸冲压件仿真 (17)2.1小轴套仿真2.1.1.零件结构分析与模具设计 (17)2.1.2.冲压工艺分析 (17)2.1.3.第一次拉伸冲压结果分析 (17)2.1.4.第二次拉伸冲压结果分析 (20)2.2钣金反拉深件仿真2.2.1.零件结构分析与模具设计 (23)2.2.2.冲压工艺分析 (23)2.2.3.第一次拉伸冲压结果分析 (24)2.2.4.第二次拉伸冲压结果分析 (26)2.3自拟二次拉深件仿真2.3.1.零件结构分析与模具设计 (29)2.3.2.冲压工艺分析 (30)2.3.3.第一次拉伸冲压结果分析 (30)2.3.4.第二次拉伸冲压结果分析 (33)第3章冲压弯曲件仿真 (37)3.1零件结构分析与模具设计 (37)3.2.冲压工艺分析 (37)3.3.弯曲结果分析 (37)第4章液压胀形件仿真 (41)4.1零件结构分析与模具设计 (41)4.2.冲压工艺分析 (41)4.3.胀形结果分析 (41)内容摘要本文章是基于Dynaform计算机仿真软件的分析及应用,通过对冲压件,二次拉伸件,弯曲件,胀形件的计算机仿真,通过对零件结构的分析,对模具的分析,对冲压工艺的分析,对冲压结果如破坏极限、应力、应变、厚度与金属流动的分析,找出了零件成型过程中可能出现的缺陷,并针对不同的缺陷根据实际生产的需要提出了不同的解决方法。
冲压综合实验报告1 - Dynaform
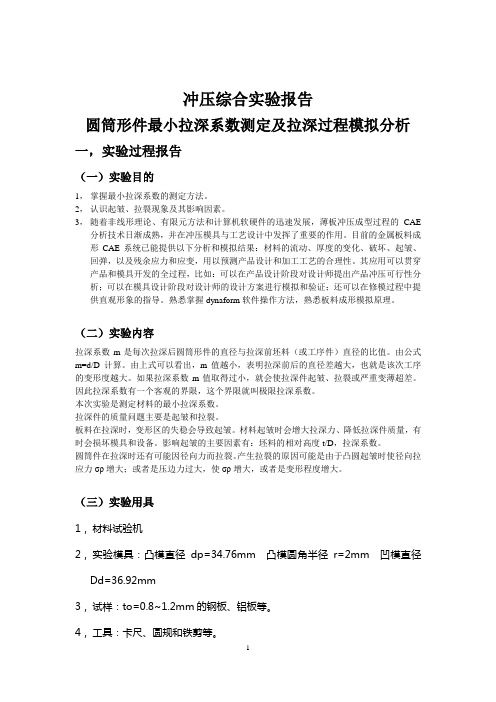
冲压综合实验报告圆筒形件最小拉深系数测定及拉深过程模拟分析一,实验过程报告(一)实验目的1,掌握最小拉深系数的测定方法。
2,认识起皱、拉裂现象及其影响因素。
3,随着非线形理论、有限元方法和计算机软硬件的迅速发展,薄板冲压成型过程的CAE 分析技术日渐成熟,并在冲压模具与工艺设计中发挥了重要的作用。
目前的金属板料成形CAE系统已能提供以下分析和模拟结果:材料的流动、厚度的变化、破坏、起皱、回弹,以及残余应力和应变,用以预测产品设计和加工工艺的合理性。
其应用可以贯穿产品和模具开发的全过程,比如:可以在产品设计阶段对设计师提出产品冲压可行性分析;可以在模具设计阶段对设计师的设计方案进行模拟和验证;还可以在修模过程中提供直观形象的指导。
熟悉掌握dynaform软件操作方法,熟悉板料成形模拟原理。
(二)实验内容拉深系数m是每次拉深后圆筒形件的直径与拉深前坯料(或工序件)直径的比值。
由公式m=d/D计算。
由上式可以看出,m值越小,表明拉深前后的直径差越大,也就是该次工序的变形度越大。
如果拉深系数m值取得过小,就会使拉深件起皱、拉裂或严重变薄超差。
因此拉深系数有一个客观的界限,这个界限就叫极限拉深系数。
本次实验是测定材料的最小拉深系数。
拉深件的质量问题主要是起皱和拉裂。
板料在拉深时,变形区的失稳会导致起皱。
材料起皱时会增大拉深力、降低拉深件质量,有时会损坏模具和设备。
影响起皱的主要因素有:坯料的相对高度t/D,拉深系数。
圆筒件在拉深时还有可能因径向力而拉裂。
产生拉裂的原因可能是由于凸圆起皱时使径向拉应力σρ增大;或者是压边力过大,使σρ增大,或者是变形程度增大。
(三)实验用具1,材料试验机2,实验模具:凸模直径dp=34.76mm 凸模圆角半径r=2mm 凹模直径Dd=36.92mm3,试样:to=0.8~1.2mm的钢板、铝板等。
4,工具:卡尺、圆规和铁剪等。
5,实验地点:材料馆243教室(四)实验步骤1,将剪下的圆形试片夹紧在凹模和压边圈之间,并保证试片与凹模中心重合。
DF分析结果

客户名称 模具编号 *** *** 产品名称 分析人员 *** 汤向星
DYNAFORM材料参数
材料模型 材质*料厚 密度 杨氏模量 泊松比 硬化规律(指数)
36#
替代料 BIF340*2.5T
7.830000e-009
DYNAFORM模拟参数
(1)压料方式:内限位,脱料板接触材料后静止 (2)板料尺寸:
第一工程成型极限图(注:红色处破裂)
第一工程厚度分布图
第二工程成型极限图(注:红色处破裂)
第二工程厚度分布图
2.070000e+005
2.800000e-001
K=648 N=0.22
初始屈服应力 (指数硬化准则)
Barlat屈服面指数
各项异性指数
拉伸强度,极限
抗拉强度,屈服
断裂伸长率
Байду номын сангаас
E0= SPI=
M=6
R0=1.87 R45=1.27 R90=2.17
270--350MPA
> = 210
> = 0.38
dynaform分析流程

dynaform分析流程DYNAFORM 5.7分析应用规范Preprocessor 前处理一、工具网格划分maxsize:20~30mm;chordal dev.:0.1 ;angle:10 其他参数采取默认。
工具网格的数量也直接影响到计算度。
二、网格检查与修补工具网格检查内容包括:1. boundary 2. over lap element 3. auto platenormal以上3项内容是必须要进行检查的,其他内容,如需要可进行简单检查。
在工具网格检查时,可以出现没有修补的网格,但不能出现退化单元、突出工具形面的单元,重叠单元。
好的工具网格是进行准确分析、减少计算时间和使计算能够顺利进行的前提。
在网格修补工具中有auto repair工具,该工具可以对整个工具进行自动修补,但修补后的工具会与实际工具存在偏差,因此该功能只能使用在局部很小的范围,而不能采用该功能对工具进行一次性修补。
三、板料网格划分在划分板料网格时,若采用真实筋模拟,此时所关心的工具网格圆角应为拉延筋的R角,一般拉延筋圆角半径R为3mm左右。
根据dyna要求,为使板料在成形后能够很好的反映出工具形面,尤其是小圆角处的形状特征,即让板料能与工具模面贴合性好,则在关心的圆角处至少应该有3个网格单元。
因此,采用最高划分等级4级,在板料初期划分网格时应为8mm。
(板料网格大小=(8/3)R)四、工具定义采用setup/auto setup模块。
按照要求逐步填写工具即可。
注意:工具行程一定要设置合理,避免空行程,影响计算速度。
Process 设置:单动拉延:Closing阶段:Drawing阶段:Duration设置:die采用travel或者until home类型。
双动拉延:Closing 阶段:Duration设置:dieControl设置:采用真实筋进行dynaform分析时,计算时间很长。
因此可以先采用粗略分析,尽量使零件在2小时左右就能得到大致结果。
- 1、下载文档前请自行甄别文档内容的完整性,平台不提供额外的编辑、内容补充、找答案等附加服务。
- 2、"仅部分预览"的文档,不可在线预览部分如存在完整性等问题,可反馈申请退款(可完整预览的文档不适用该条件!)。
- 3、如文档侵犯您的权益,请联系客服反馈,我们会尽快为您处理(人工客服工作时间:9:00-18:30)。
[Dynaform分析报告要求]
模拟底面有凹坑的盒形件,盒形件长为学号后二位数字加一百,宽为长的一半,高为宽的一半。
前处理文件名为,学号_姓名拼音首字母。
其它自定。
如学号为10609010789的张三同学,盒形件长为189mm。
前处理文件名为:10609010789_zs.df 。
模拟完成后,写模拟分析报告,打印装订,两周内交班长。
请班长按学号先后清理整齐,上交。
要求必须写清楚下面内容:
1. 模拟条件:零件名称、厚度、材料、成形条件(成形方式,速度等)。
标出零件主要尺寸。
2. 结果:
●给出dynaform变形网格图。
第一步,中间一步,最终步。
第一步,要求标出坯料主要尺寸,最后一步,要求标出产品主要
尺寸。
●给出变形完成(最后一帧)的成形极限图(Forming Limit Diagram);
●给出变成完成(最后一帧)的厚度变化图(Thickness);
●给出压边力曲线;
3. 简要分析
4. 工艺优化措施,并重复模拟,直到得出满意结果(报告只写第一次模拟,及最后一次模拟。
)
[Dynaform分析报告格式]
重庆理工大学
报告名称Dynaform板料成形模拟
姓名黎毅
学号10709010313
日期2010.10.25
1、模拟条件
计算机软件、硬件、Dynamform分析软件
产品名:盒形件,厚度1mm
材料:DQSK,材料特性用Belytschko-Tsay,材料性能………
成形条件:单动,成形速度,5000mm/s,静摩擦系数为0.1,行程52mm,压边力20T,材料选用37号,材料特性用Belytschko-Tsay。
………
产品外表面主要尺寸:
2. 结果
给出dynaform变形网格图。
第一步,中间一步,最终步。
第一步,要求标出坯料主要尺寸,最后一步,要求标出产品主要尺寸。
给出变形完成(最后一帧)的成形极限图(Forming Limit Diagram);
给出变成完成(最后一帧)的厚度变化图(Thickness);
给出压边力曲线
3.简要分析
从以上结果可看出,本产品。
4. 工艺优化措施,并重复模拟,直到得出满意结果(报告只写第一次模拟,及最后一次模拟。
)
工艺优化措施:变压边力,变坯料大小,变凹模圆角等。
并再次模拟。