通钢超薄热带轧制过程中的新工艺与控制过程中的新技术
通钢超薄热带轧制过程中的新工艺与控制过程中的新技术
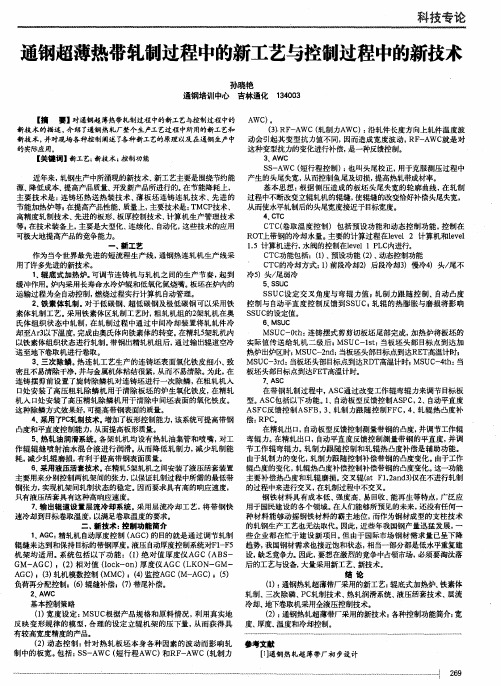
通钢超薄热带轧制过程中的新工艺与控制过程中的新技术
通钢培训 中 心 孙晓艳 吉林通化 1 3轧制过程中的新工艺与控制过程中的 AWC)。 新 技 术 的描述 , 介绍了 通钢热 轧厂整 个生产工艺过 程 中所用的新工艺和 ( 3 ) . RF — A WC( 轧制 力A WC ): 沿轧 件长 度方 向上 轧件 温 度波 新技术, 并对现 场各 种控制 阐述 了 各种 新J - E的原理 以及在 通钢生产 中 动 会 引起 其 变 型抗 力值 不 同 , 因而 造成 宽 度波 动 , R F — A WC 就 是 对 的实际应 用。 这 种变 型抗 力的变 化进行 补偿 , 是 一种反馈控 制。
【 关键词】 新工艺; 新技术; 控制功能
3 .AW C
S S — A WC ( 短 行程 控 制 ) : 也 叫头尾 校 正 , 用于克 服 测压 过 程 中 近年来 , 轧钢生产中所涌现的新技术、 新工艺主要是 围绕节约能 产生 的头 尾失宽 , 从 而控制 鱼 尾及切 损 , 提 高热 轧带成 材率 。 源、 降低成本、 提高产品质量、 开发新产品所进行的。 在节能降耗上, 基本思想: 根据侧压造成 的板坯头尾失宽的轮廓曲线, 在轧制 主要技术是 : 连铸坯热送热装技术、 薄板坯连铸连轧技术、 先进的 过程中不断改变立辊轧机的辊缝 , 使辊缝的改变恰好补偿头尾失宽, 节能 加 热 炉等 ; 在 提高 产品性能 、 质量上 , 主 要技 术是 : T MC P 技术、 从而 使水平轧 制后 的头尾 宽度 接近 于 目标宽 度。 4、C TC 高精 度 轧制 技 术 、 先 进 的板 形 、 板 厚控制 技 术 、 计算 机 生产 管 理技 术 等; 在 技术 装 备上 , 主要 是大 型化 、 连 续化 、 自动化 , 这些 技术 的应 用 C TC ( 卷取温度控制)包括预设功能和动态控制功能 , 控制在 可极大地提高产品的竞争能力。 RO T A = 带钢的冷却水量。 主要的计算过程在l e v e l 2 计算机和l e v e l 新 工艺 1 . 5 计算 机进 行, 水 阀的控 制在 l e v e l I P L C 内进 行。 作 为 当今 世界 最先 进 的短 流 程 生产 线 , 通钢 热连 轧 机 生产 线 采 C TC 功能包括:( I ) 、 预设功能 ( 2 ) 、 动态控制功能 。 C TC 的 冷却 方 式 : 1 ) 前 段冷 却2 ) 后段 冷 却3 )慢 冷4 )头 / 尾不 用 了许多先 进 的新技 术 。 1 . 辊 底 式 加热 炉 。 可调 节 连铸 机 与 轧 机 之 间的 生 产节 奏 , 起 到 冷 5 )头/ 尾 弱冷 5. SS UC 缓 冲 作用 。 炉 内采用长 寿 命 水冷 炉辊 和低 氧化 氮烧 嘴 。 板 坯在 炉 内的 运 输 过程 为全 自动控 制 , 燃 烧 过程 实行 计算 机 自动管 理 。 S S UC 设 定 交 叉 角度 与 弯 辊 力 值 ; 轧 制 力跟 随 控 制 ,自动 凸度 2 . 铁素体轧制。 对于低碳钢、 超低碳钢及极低碳钢可以采用铁 控制与自动平直度控制反馈Ns s uc; 轧辊的热膨胀与磨损将影响 素体轧制工艺。 采用铁素体区轧制工艺时, 粗轧机组的2 架轧机在奥 S S UC 的设定 值 。 6 M SU C 氏体组织状态中S E N, 在轧制过程中通过 中间冷却装置将轧轧件冷 却至At 3 以下温度, 完成由奥氏体向铁素体的转变。 在精轧5 架轧机内 MS U C - 0 t h: 连铸摆式剪剪切板坯尾部完成 , 加 热炉将板坯的 以铁 素 体组 织状 态 进行 轧制 。 带 钢 出精 轧机 组 后 , 通 过输 出辊道 空冷 实际值传送给轧机二级后I MS UC -I s t : 当板坯头部 目 标 点到达加 送 至地下卷 取机 进行 卷取 。 热炉出炉区时 MS UC - 2 n d : 当板坯头部 目 标点到达RE T 高温计时l 3 三次除鳞 。 热连轧工艺生产的连铸坯表面氧化铁皮细小、 致 MS UC - 3 r d : 当板 坯头 部 目标 点到达 RD T 高温计 时 } MS UC 一 4 t h : 当 密且 不易清 除干 净, 并 与金属 机体 粘结 很紧 , 从 而不 易清除 。 为此 , 在 板坯 头部 目 标 点 到达 F E T高温计 时。 7 、AS C 连铸 摆 剪 前设 置了旋 转 除 鳞机 对 连铸 坯 进行 一 次 除 鳞 , 在 粗轧 机 入 口处安装了高压粗轧除鳞机用于清除板坯的炉生氧化铁皮 , 在精轧 在带钢轧制过程中, AS C 通过改变工作辊弯辊力来调节 目 标 板 机 入 口处 安 装 了高压 精 轧 除鳞 机 用 于清 除 中间坯 表 面的 氧化 铁 皮 。 型。 A S C 包 括 以下功 能 。 1 、自 动 板 型反馈 控制 AS P C, 2 、 自动平 直 度 这种 除 鳞方 式 效果 好, 可提 高带 钢表 面的 质量 。 A S F C 反馈 控 ̄ AS F B, 3 、 轧 制 力跟 随 控 制 F F C , 4 、 轧 辊 热 凸度 补 4 采用了P C ¥ L 制技术。 增加了板形控制能力, 该系统可提高带钢 偿 : R P C 。 凸度和平直度控制能力, 从面提高板形质量。 在精轧出口, 自动板型反馈控制测量带钢的凸度, 并调节工作辊 5 热轧油润滑系统 。 各架轧机均设有热轧油集管和喷嘴, 对工 弯辊 力。 在精轧出口, 自动平直度反馈控制测量带钢的平直度, 并调 轧制力跟随控制和轧辊热凸度补偿是辅助功能 。 作辊辊缝 喷射 油水混合液进行润滑。 从而降低S L S U 力, 减 少轧制能 节工作辊弯辊 力。 由于轧制 力 的变化 , 轧制 力跟 随控 制补 偿 带钢 的凸度 变化 。 由于工作 耗, 减少轧辊磨损, 有利于提高带钢表面质量。 轧辊 热 凸度补 偿控 制补 偿 带钢 的凸度 变化 。 这 一功能 6 . 采用液压活套技术。 在精轧5 架轧机之间安装了液压活套装置 辊 凸度 的变 化 , 主要用来分别控制两机架间的张力, 以保证轧制过程中所需的最低带 主要补偿热凸度和轧辊磨损。 交叉辊( a t F 1 , 2 a n d 3 ) 仅在不进行轧制 钢 张 力, 实 现机 架 间轧制 状态 的稳 定 。 因而 要求具 有 高 的响应 速 度, 的过程 中来进行 交叉 , 在 轧制过 程 中不 交叉 。 只有液压活套具有这种高响应速度。 钢铁 材 料具 有成 本低 、 强度 高 、 易 回收 、 能 再 生等 特 点, 广泛 应 7 . 输 出辊 道设 置 层 流冷 却 系统 。 采 用 层流 冷 却 工艺 , 将 带 钢快 用 于 国民建设 的各 个 领域 。 在人们 能够 所 预见 的未来 , 还没有任 何一 种 材 料 能 够动 摇钢 铁 材料 的霸 主地 位 , 而 作为钢 材成 型 的 支柱 技 术 速冷却到目标卷取温度, 以满足卷取温度的要求。 =. 新技 术 : 控 制 功 能简 介 的 轧钢 生产 工艺 也无 法取 代 。 因此 , 近些 年 我 国钢 产 量迅 猛 发 展 , 一 1 . A G C : 精轧 机 自 动 厚度 控制 ( AG C ) 的 目的就 是 通 过 调节 轧制 些 企 业 都 在忙 于建 设 新 项 目。 但 由于 国际市场 钢 材 需 求量 已呈下 降 辊 缝来 达 到和 保持 目 标 的 带钢 厚度 。 液 压 自动厚 度控 制系统 对F I - F 5 趋势 , 我 国钢材 需 求也 接近 饱和 状 态 , 相 当一 部分 都 是低 水平重复 建 机架均适用。 系 统 包 括 以下 功 能 :( I ) 绝 对 值 厚 度仪 A GC ( AD S - 设, 缺乏竞争力。 因此, 要想在激烈的竞争中占领市场 , 必须要淘汰落
浅谈轧钢生产中应用的新技术新工艺

浅谈轧钢生产中应用的新技术新工艺近年来,轧钢生产中所涌现的新技术、新工艺主要是围绕节约能源、降低成本、提高产品质量、开发新产品所进行的。
这些技术的应用可极大地提高产品的竞争能力。
一、以节能降耗为目标的新技术1.连铸坯热送热装技术连铸坯热送热装技术是指在400℃以上温度装炉或先放入保温装置,协调连铸与轧钢生产节奏,然后待机装入加热炉。
在轧钢采用的新技术中热送热装效益明显,主要表现在:大幅度降低加热炉燃耗,减少烧损量,提高成材率,缩短产品生产周期等。
连铸坯热送热装技术的实现还需要以下几个条件:(1)质量合格的连铸板坯;(2)工序间的协调稳定;(3)相关技术设备要求,如采用雾化冷却、在平面布置上尽可能缩短连铸到热轧之间的距离、通过在输送辊道上加设保温罩及在板坯库中设保温坑等;(4)采用计算机管理系统。
根据国内目前的实际情况分析,需要继续推广该技术,己经采用的轧机应当在提高水平上下功夫。
通过加强管理保证该技术的连续使用,不断提高热装率和提高热装温度,同时进行必要的攻关,解决由于采用热装技术以后,产生的产品质量不稳定问题。
2.薄板坯连铸连轧技术薄板坯连铸连轧是20 世纪80 年代末实现产业化的新技术,是钢铁生产近年来最重要的技术进步之一。
根据国外的统计,目前薄板坯连铸连轧生产线可以生产的品种主要有:低碳钢、低合金钢、普通管线钢、可热处理钢、弹簧钢、工具钢、电工钢、耐磨钢和部分不锈钢等。
现在,薄板坯连铸连轧厂可以覆盖大多数的热轧带钢的品种范围,但是一些高性能要求和高附加值的品种还不能生产。
国外正在进行扩大品种的研究工作,希望在短时间内能够使薄板坯连铸连轧的产品覆盖更多传统轧机生产的热轧带钢。
目前的发展工作主要集中在低碳和超低碳深冲钢的生产、高牌号管线钢的生产、高强度钢的生产等几个方面。
增加薄板坯连铸连轧品种所采取的主要措施归结起来主要有:改进电炉原料结构,普遍进行铁水预处理,加强钢水精炼,配备真空精炼设备,从根本上改善钢水的纯净度;改进结晶器的结构;二冷普遍采用轻(软)压下技术,并根据钢种、铸速对二冷区域轻(软)压下的起、终点、压下量及压下速率进行智能化控制;加大铸坯厚度以增加压缩比,提高浇铸过程中结晶器液面的稳定性;进行粗轧;多次高压水除鳞;进行铁素体轧制等7 个方面。
新一代控制轧制和控制冷却技术与创新的热轧过程

新一代控制轧制和控制冷却技术与创新的热轧过程王国栋作者单位:文摘:针对传统控制轧制控制冷却(TMCP)技术存在的问题,提出了以超快冷为核心的新一代的TMCP 技术,并详述了作为实现新一代TMCP 技术核心手段的超快冷技术的科学内涵和工业装备开发情况。
关键词:钢;热轧;新一代控制轧制和控制冷却;超快冷;强化东北大学王国栋摘要:针对传统控制轧制控制冷却(TMCP)技术存在的问题,提出了以超快冷为核心的新一代的TMCP 技术,并详述了作为实现新一代TMCP 技术核心手段的超快冷技术的科学内涵和工业装备开发情况。
关键词:钢;热轧;新一代控制轧制和控制冷却;超快冷;强化New generation TMCP and innovative hot rollingprocessWANG Guo-dong( Northeastern University )Abstract:A new-generation TMCP(thermo-mechanical control process) with ultra fast cooling as core technique was suggested instead of the conventional TMCP in which some problems are to be solved. Describes the ultra fast cooling technique theoretically and relevant equipment developed for commercial applications in detail.Key words:steel;hot rolling;new generation TMCP;ultra fast cooling;strengthening1 新一代NG-TMCP 的科学内涵1.1 传统TMCP控制轧制和控制冷却技术,即TMCP,是20 世纪钢铁业最伟大的成就之一。
浅谈轧钢生产中的新技术应用

浅谈轧钢生产中的新技术应用1. 引言1.1 引言轧钢是一种重要的金属加工工艺,广泛应用于各种工业领域。
随着科技的不断发展,新技术在轧钢生产中的应用也日益普及。
数字化技术、自动化设备、机器学习、智能制造以及材料科学等方面的技术不断涌现,为轧钢生产带来了许多变革和提升。
在本文中,我们将深入探讨这些新技术在轧钢生产中的具体应用。
数字化技术的应用可以实现生产过程的精细化管理和优化,提高生产效率和质量。
自动化设备的应用可以减少人力投入,提高生产线的稳定性和持续性。
机器学习技术的应用可以帮助预测生产过程中的问题并及时调整生产参数。
智能制造的应用可以实现生产过程的智能化控制和优化。
材料科学的应用可以研究新材料的应用及在轧钢生产中的效果。
通过对这些新技术在轧钢生产中的应用进行深入探讨,我们可以更好地理解和把握轧钢生产的发展方向和趋势,推动轧钢行业的持续发展和提升。
2. 正文2.1 数字化技术在轧钢生产中的应用数字化技术在轧钢生产中的应用已经成为行业发展的趋势。
通过数字化技术的应用,可以实现生产过程的智能化、自动化,提高生产效率和产品质量。
在轧钢生产中,数字化技术主要包括实时监控系统、智能控制系统、大数据分析等方面的应用。
实时监控系统可以实时监测轧钢生产过程中各个环节的参数,包括温度、压力、速度等,实时反馈给操作人员,确保生产过程的稳定性和安全性。
这样可以避免因为人为操作不当而导致的生产事故,提高生产效率。
智能控制系统可以根据实时监测的数据,自动调节轧机的工作参数,实现轧钢过程的自动化控制。
这样可以降低人工干预的误差,提高产品的一致性和质量。
大数据分析可以通过对历史数据的挖掘和分析,找出生产过程中的潜在问题和改进空间,为生产决策提供科学依据。
通过大数据分析,可以实现轧钢生产过程的优化和智能化。
数字化技术在轧钢生产中的应用可以提高生产效率、降低生产成本,同时提升产品质量和市场竞争力。
随着技术的不断发展,数字化技术将在轧钢生产中发挥越来越重要的作用。
浅谈轧钢生产中的新技术应用
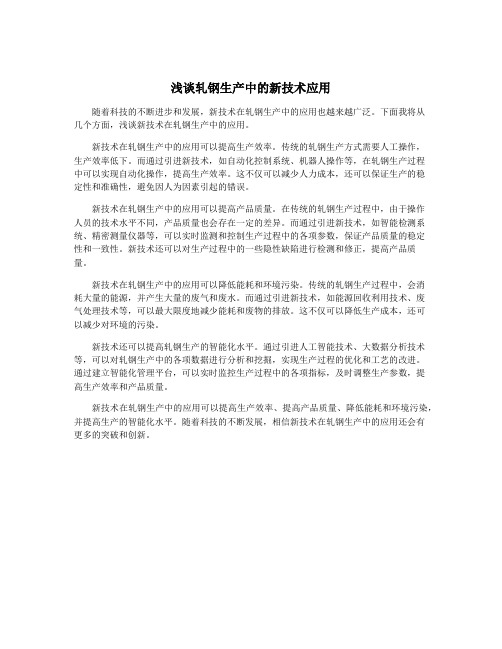
浅谈轧钢生产中的新技术应用随着科技的不断进步和发展,新技术在轧钢生产中的应用也越来越广泛。
下面我将从几个方面,浅谈新技术在轧钢生产中的应用。
新技术在轧钢生产中的应用可以提高生产效率。
传统的轧钢生产方式需要人工操作,生产效率低下。
而通过引进新技术,如自动化控制系统、机器人操作等,在轧钢生产过程中可以实现自动化操作,提高生产效率。
这不仅可以减少人力成本,还可以保证生产的稳定性和准确性,避免因人为因素引起的错误。
新技术在轧钢生产中的应用可以提高产品质量。
在传统的轧钢生产过程中,由于操作人员的技术水平不同,产品质量也会存在一定的差异。
而通过引进新技术,如智能检测系统、精密测量仪器等,可以实时监测和控制生产过程中的各项参数,保证产品质量的稳定性和一致性。
新技术还可以对生产过程中的一些隐性缺陷进行检测和修正,提高产品质量。
新技术在轧钢生产中的应用可以降低能耗和环境污染。
传统的轧钢生产过程中,会消耗大量的能源,并产生大量的废气和废水。
而通过引进新技术,如能源回收利用技术、废气处理技术等,可以最大限度地减少能耗和废物的排放。
这不仅可以降低生产成本,还可以减少对环境的污染。
新技术还可以提高轧钢生产的智能化水平。
通过引进人工智能技术、大数据分析技术等,可以对轧钢生产中的各项数据进行分析和挖掘,实现生产过程的优化和工艺的改进。
通过建立智能化管理平台,可以实时监控生产过程中的各项指标,及时调整生产参数,提高生产效率和产品质量。
新技术在轧钢生产中的应用可以提高生产效率、提高产品质量、降低能耗和环境污染,并提高生产的智能化水平。
随着科技的不断发展,相信新技术在轧钢生产中的应用还会有更多的突破和创新。
钣金加工过程中轧制工艺的改进与创新

钣金加工过程中轧制工艺的改进与创新钣金加工是一种将金属板材通过剪切、翻边、折弯、冲压等工艺加工成各种形状的工艺过程。
其中,轧制是一种常见的钣金加工工艺,主要用于将金属板材通过辊筒的压迫来改变其形状和尺寸。
随着钣金加工技术的不断发展,轧制工艺也在不断改进与创新,以提高生产效率、减少生产成本,满足市场的需求。
首先,轧制工艺在设备方面的改进与创新。
传统的轧制设备主要采用水平轧制,其工作原理是通过两组辊筒的压迫将金属板材压制成所需的形状。
然而,由于水平轧制存在一些局限性,如轧制力不稳定、工作精度低等问题,制约了其在生产中的应用。
近年来,垂直轧制技术的出现解决了这些问题。
垂直轧制将金属板材垂直放置,通过上、下两组辊筒的压迫来实现轧制。
相对于水平轧制,垂直轧制具有轧制力稳定、工作精度高的优点,适用于对较高精度要求的产品生产。
其次,轧制工艺在材料方面的改进与创新。
传统的轧制工艺主要适用于金属板材的加工,但对于一些新型复合材料,传统轧制工艺则显得力不从心。
针对这一问题,研究人员提出了热轧与冷轧相结合的复合轧制工艺。
该工艺通过先将复合材料进行热轧处理,使其软化后再进行冷轧,以实现更精细、更复杂的形状加工。
这种复合轧制工艺不仅适用于复合材料的加工,还能有效提高生产效率和工作精度。
此外,轧制工艺在自动化方面的改进与创新。
传统的轧制工艺主要依靠操作人员控制设备进行加工,存在生产周期长、工作效率低等问题。
为了提高生产效率和降低人工成本,研究人员引入了自动化控制技术。
通过自动化控制系统对轧制设备进行精确控制,可以实现自动运行、自动调节等功能,提高生产效率和工作精度。
同时,还可以通过数据采集和分析来实现生产过程的监控和控制,以及对生产数据的统计和分析,为企业提供决策依据。
最后,轧制工艺在环保方面的改进与创新。
传统的轧制工艺在生产过程中会产生大量的粉尘和废水废气,对环境造成严重污染。
为了减少污染,研究人员提出了绿色轧制技术。
绿色轧制技术主要通过改变工艺参数和设备结构,减少废弃物的产生,提高资源利用率。
超薄热带生产线提速轧制工艺的改进与实践

间『。但 试 生产 以来 , 了在使 用 半无 头 轧制 时采 2 1 除
用提速 轧 制 ,在 单块 轧制 时均没 有采用 该 项技术 ,
这主 要是 由于受 设备传 动 系统 的影 响, 几个 主要产
品 的轧制速 度一 直没 有达 到实 际最佳状 态 , 很大 的
质 量重要 的工艺参 数 。 于薄 规格产 品 , 对 厚度越 薄 ,
p a t eh s n r me td b fe meo l fr n e a d s v d r l n m ea d c a a . h r u t n p r a a e n r ci a c e ne u r i f c i t mil u a c n a e o l g t o l s T e p o ci e y h sb e i i n g o d
兰 圭蔓 塑
——
. 界 j 世
,
s j z com sz
维普资讯
加热 炉缓冲 时 间紧张 , 给公 司全年 达产 带来 极大 困缓 冲 时间 , 为 增
通 过 与 外方 交流 以及 参照 其 他 国 内外板 带 轧 制 经验 , 们需要对 压 下分配 进行优 化 。通过 更改 我 压 下 我们 既可 以保 证产 品厚度 也 可 以保 持张 力 的 恒 定 。大 量实 践证 明对第 1 架 ( ) 用 大压 下 机 R1采 可 减轻 后面机 架 的轧制 负荷 , 微调后 几架 轧机压 下 则 可 以实现提速 , 持秒 流量相 等 。并且压 下 的优 保 化 可 以 由二 级 自适应 控 制在 线 作 微量 调整 或 通 过 自学 习功 能进 行优 化 。 鉴 于 以上 研 究我 们 可得 出提速 时 的轧制 动态
系统安全 的前提 下, 通过更改轧制工艺, 提高了轧制速度 , 加快 了轧制节奏 , 实践效果 证明: 新工艺可节省轧制单卷
轧钢生产中新工艺新技术的应用探究

轧钢生产中新工艺新技术的应用探究摘要:我国社会发展迅速,推动了钢铁生产行业的发展,生产工艺越来越先进。
轧钢技术以及产品性能也有较大程度提升。
轧钢生产对于社会经济发展具有直接影响。
本文对于轧钢生产环节新技术和工艺的发展现状做出阐述,并对其在加工生产环节实践应用深度剖析。
关键词:轧钢生产;新工艺;技术应用引言:在社会各领域的发展过程,需要消耗大量钢材,对于轧钢生产品质以及技术应用要求更高。
以往轧钢生产工艺及技术的应用,生产出产品可能和现实需求不相符。
因此,需要结合市场需求,探索轧钢生产全新工艺和技术的应用思路,不断提高轧钢品质,提高生产企业核心竞争力。
一、轧钢生产期间设备和工艺的发展(一)设备方面我国轧钢生产设备的应用方面主要有如下几种:第一,热轧生产线,能够实现连续生产,并且生产过程节能性良好,生产流程紧凑,能够保证连铸、轧钢各工序无缝衔接。
第二,集成宽厚板的轧制生产线,需要使用国内外联合设计生产工艺,引进国外设备,才能完成生产;第三,大型冷轧生产线,像酸洗冷轧就是其中之一,该生产线的运用,对于轧钢工艺以及生产技术多方面发展有直接影响。
(二)技术方面轧钢生产期间,新技术的应用包括节能均温炉,能够实现多元化生产棒线材,既可生产带肋钢筋,还能生产特殊的钢棒与线材,需要将生产期间环境温差考虑其中,确保铸钢环节和轧制工艺运用衔接顺利。
利用DROF生产线,能够有效缩短生产距离,并将产品向缓冲区送入,通过无坯之后,将产品放入轧制机器内,若此环节温度和要求不符,即可自动剔除,确保轧钢品质[1]。
二、轧钢生产中新工艺和新技术的应用(一)品质保证工艺1.TCMP技术在轧钢生产环节,PMCP技术的应用也称机械热控制,具体来讲即指对于金属的奥氏体转化全程加以控制,最终对于金属内部形态以及组织分布综合控制。
轧钢生产时,可按照钢材C曲线,对于温度和加热速率全面控制。
通过“炉、水、空”等不同冷却技术的不同速率控制,获得轧钢终组织。
浅谈轧钢生产中的新技术应用
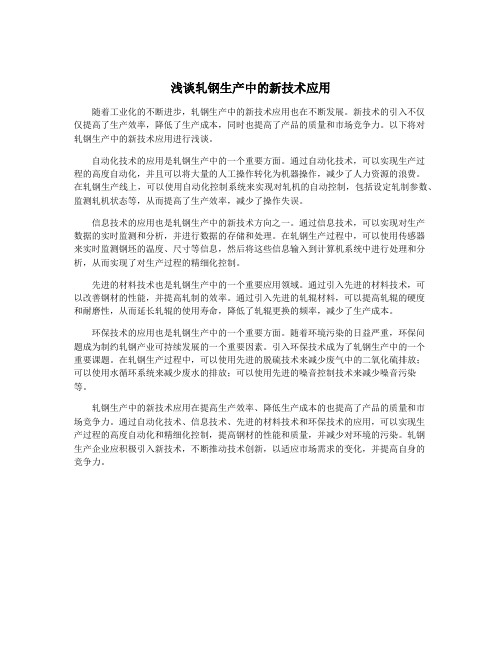
浅谈轧钢生产中的新技术应用随着工业化的不断进步,轧钢生产中的新技术应用也在不断发展。
新技术的引入不仅仅提高了生产效率,降低了生产成本,同时也提高了产品的质量和市场竞争力。
以下将对轧钢生产中的新技术应用进行浅谈。
自动化技术的应用是轧钢生产中的一个重要方面。
通过自动化技术,可以实现生产过程的高度自动化,并且可以将大量的人工操作转化为机器操作,减少了人力资源的浪费。
在轧钢生产线上,可以使用自动化控制系统来实现对轧机的自动控制,包括设定轧制参数、监测轧机状态等,从而提高了生产效率,减少了操作失误。
信息技术的应用也是轧钢生产中的新技术方向之一。
通过信息技术,可以实现对生产数据的实时监测和分析,并进行数据的存储和处理。
在轧钢生产过程中,可以使用传感器来实时监测钢坯的温度、尺寸等信息,然后将这些信息输入到计算机系统中进行处理和分析,从而实现了对生产过程的精细化控制。
先进的材料技术也是轧钢生产中的一个重要应用领域。
通过引入先进的材料技术,可以改善钢材的性能,并提高轧制的效率。
通过引入先进的轧辊材料,可以提高轧辊的硬度和耐磨性,从而延长轧辊的使用寿命,降低了轧辊更换的频率,减少了生产成本。
环保技术的应用也是轧钢生产中的一个重要方面。
随着环境污染的日益严重,环保问题成为制约轧钢产业可持续发展的一个重要因素。
引入环保技术成为了轧钢生产中的一个重要课题。
在轧钢生产过程中,可以使用先进的脱硫技术来减少废气中的二氧化硫排放;可以使用水循环系统来减少废水的排放;可以使用先进的噪音控制技术来减少噪音污染等。
轧钢生产中的新技术应用在提高生产效率、降低生产成本的也提高了产品的质量和市场竞争力。
通过自动化技术、信息技术、先进的材料技术和环保技术的应用,可以实现生产过程的高度自动化和精细化控制,提高钢材的性能和质量,并减少对环境的污染。
轧钢生产企业应积极引入新技术,不断推动技术创新,以适应市场需求的变化,并提高自身的竞争力。
轧钢生产中新工艺新技术的应用

轧钢生产中新工艺新技术的应用摘要:改革开放后,我国的经济得到突飞猛进的发展。
而钢铁工业,在国家的发展中起到了至关重要的作用。
钢的用途非常广泛,尤其是轧钢技术,它在机械生产和设备制造中起到了举足轻重的作用。
基于此,本文以轧钢生产为例,阐述其生产过程中应用新工艺、新技术对我国钢铁行业的重要价值体现,仅供参考。
关键词:轧钢生产;新工艺;新技术;应用分析引言:近几年,钢铁制品的需求不断增长。
在此背景下,我国钢铁工业的发展日益受到重视。
传统的生产工艺和技术已不能适应当前钢铁生产水平和性能的要求。
而新工艺、新技术的涌现,可以很好地弥补这一缺陷。
因此,对各种新工艺、新技术的运用进行分析是十分必要的。
一、节能工艺及技术(一)薄板坯连铸连轧薄板坯连铸连轧是一种典型的新型工艺,在生产高强度钢、超低碳深冲钢、高标号管线钢等领域都有广泛应用。
从该新技术的使用效果来看,采用薄板坯连铸连轧技术在轧钢生产中具有很好的节能效果。
薄板坯连铸连轧技术包括 ISP、CSP等几个常见的工艺类型。
在这些项目中, ISP最初是在意大利某公司建立和投入使用的。
本工艺主要是利用直弧型铸机、平移式二辊轧机等设备来完成。
ISP生产线长度大约180米,采用这种工艺生产的效率大约为30分钟(钢液到卷筒)。
CSP主要是用来制造超低碳钢,碳钢,0.8 mm以下。
(二)高温低氧燃烧在钢铁锻造炉的生产中,常规的生产方法有以下缺点:燃烧时会引起高温(600~700℃),但有关规定的排烟温度应<150℃,说明此工艺存在热量损耗问题。
高温低氧燃烧技术是以降低热耗为目的而发展起来的一项新技术。
该技术的节能机理是:采用喷射方式将燃油与高温、低氧的助燃剂混在一起,促进两者的充分混合。
在燃烧过程中,由于高温、低氧等助燃剂的作用,可以使燃油达到蓄热燃耗,从而使烟气的排放温度下降。
与传统的制程技术相比,本发明具有以下优点:一是节约能源。
在燃烧时,采用高温、低氧的助燃剂,可以使烟道中的余热得到充分的回收,从而降低了热能的损耗。
轧钢生产中的新技术应用分析

轧钢生产中的新技术应用分析摘要:近些年来,国家经济实力增长迅速,科技水平不断提高,各领域的技术研究也取得了较大进步。
就现阶段的分析来看,在节能减排的绿色生产环境下,钢铁的生产需要强调高效率、低成本,必须要进行生产工艺的改造和创新,因此在轧钢的生产中需要不断的应用新技术和工艺来实现对传统工艺的改善。
研究新技术、新工艺在轧钢生产过程中的利用价值,并对技术规范利用做强调,这于实践生产有突出指导意义。
本文以分析轧钢生产中的新技术合理应用策略作为主要的目的,从而有效提升轧钢生产中新技术应用的总体水平。
关键词:轧钢生产;新技术;应用策略1轧钢生产状况分析1.1热轧宽带轧钢生产线热轧宽带轧钢生产线在目前的钢材生产实践中有着非常普遍的利用,这是我国自主研发的,通过对传统中薄板连铸连轧技术的优化而改进的现代轧钢新技术成果。
对热轧宽带轧钢生产工艺的具体利用做分析可知其具有非常显著的完整性,而且在应用实践中具有高效性,在规模化、连续化生产实践中表现出了突出价值。
就生产线的具体利用来看,其工艺流程整体比较的紧凑,能够实现连铸和轧钢工序的有效连接。
简言之,热轧宽带轧钢生产线作为我国配自主研发的轧钢生产工作,在目前的实践应用中表现出了突出价值,所以其应用受到了青睐。
1.2集成宽厚板的生产线集成宽厚板的生产线在目前的轧钢生产实践中也有比较普遍的利用。
就该生产线而言,其构建与我国引进的国外关键轧钢设备有密切的关系。
我国在引进关键轧钢设备之后通过对设备性能和特点的分析,结合了我国轧钢先进技术成果,并在不断探索和研究的基础上最终整合而成了新型的轧钢生产线技术,便是集成宽厚板的生产线。
就此生产线的具体利用来看,其主要在管线钢板、结构钢板以及石油储备用钢等产生的生产实践中进行利用。
总的来讲,集成宽厚板的生产线在轧钢生产过程中,其应用范围具有针对性和专业性,所以在实践中需要做好生产线的具体应用分析。
1.3大型冷连轧的生产线大型冷连轧的生产线在目前的轧钢生产实践中利用也比较的普遍。
浅谈轧钢生产中的新技术应用
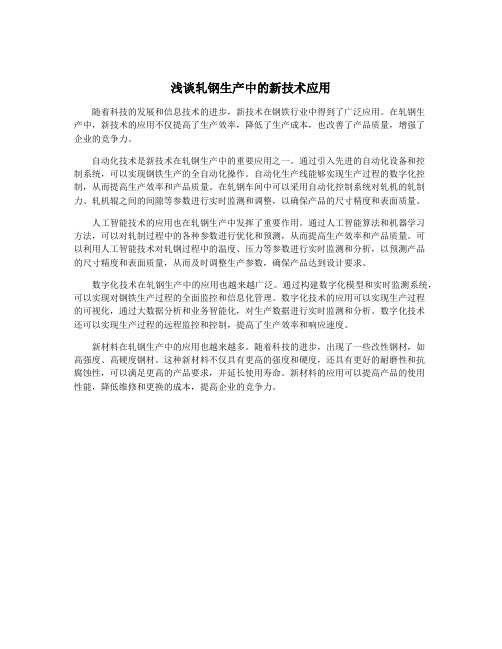
浅谈轧钢生产中的新技术应用随着科技的发展和信息技术的进步,新技术在钢铁行业中得到了广泛应用。
在轧钢生产中,新技术的应用不仅提高了生产效率,降低了生产成本,也改善了产品质量,增强了企业的竞争力。
自动化技术是新技术在轧钢生产中的重要应用之一。
通过引入先进的自动化设备和控制系统,可以实现钢铁生产的全自动化操作。
自动化生产线能够实现生产过程的数字化控制,从而提高生产效率和产品质量。
在轧钢车间中可以采用自动化控制系统对轧机的轧制力、轧机辊之间的间隙等参数进行实时监测和调整,以确保产品的尺寸精度和表面质量。
人工智能技术的应用也在轧钢生产中发挥了重要作用。
通过人工智能算法和机器学习方法,可以对轧制过程中的各种参数进行优化和预测,从而提高生产效率和产品质量。
可以利用人工智能技术对轧钢过程中的温度、压力等参数进行实时监测和分析,以预测产品的尺寸精度和表面质量,从而及时调整生产参数,确保产品达到设计要求。
数字化技术在轧钢生产中的应用也越来越广泛。
通过构建数字化模型和实时监测系统,可以实现对钢铁生产过程的全面监控和信息化管理。
数字化技术的应用可以实现生产过程的可视化,通过大数据分析和业务智能化,对生产数据进行实时监测和分析。
数字化技术还可以实现生产过程的远程监控和控制,提高了生产效率和响应速度。
新材料在轧钢生产中的应用也越来越多。
随着科技的进步,出现了一些改性钢材,如高强度、高硬度钢材。
这种新材料不仅具有更高的强度和硬度,还具有更好的耐磨性和抗腐蚀性,可以满足更高的产品要求,并延长使用寿命。
新材料的应用可以提高产品的使用性能,降低维修和更换的成本,提高企业的竞争力。
轧钢生产中新工艺新技术及应用策略分析

轧钢生产中新工艺新技术及应用策略分析作者:武鹏文来源:《知识文库》2018年第15期轧钢生产中,新工艺新技术具有重要作用,能确保轧钢质量,提高轧钢生产效率。
目前主要的新工艺新技术包括连铸坯热送热装技术、高温低氧燃烧技术、热机械控制工艺、柔性轧制技术。
随着技术创新发展,高性能低能耗技术、智能化技术、绿色环保技术将会得到广泛应用,有利于促进轧钢生产效率和产品质量提升。
轧钢生产是钢铁生产的关键环节。
加强该项工作,提高产品质量和生产效率,不仅有利于确保产品综合性能,同时还有利于更好满足人们生产生活需要。
因此,作为钢铁企业,在轧钢生产中应该顺应时代发展趋势,注重工艺新技术应用,促进产品质量提升,使其更好满足工业生产需要。
1 轧钢生产中新工艺新技术的作用1.1 确保轧钢质量提高轧钢质量,这是钢铁生产的重要目标。
但部分钢铁企业新工艺新技术应用存在不足,忽视工艺创新,制约产品质量提升。
为转变这种情况,制定有效的发展计划和措施,重视新工艺新技术应用,能有效指导产品生产,有利于推动产品质量提升,使其更好满足生产生活需要。
1.2 提高轧钢生产效率如果忽视新技术和新工艺应用,必然会制约产品质量提升。
作为钢铁生产企业,在生产中应该创新思想观念,提高产品生产效率,将新工艺和新技术应用到产品生产之中。
从而有效规范和引导产品生产,促进轧钢生产效率提升,也为钢铁企业发展注入生机与动力。
2 轧钢生产中新工艺新技术的应用策略2.1 连铸坯热送热装技术钢铁加热工艺分为预热、加热和均热三个环节,连铸坯热送热装技术在实际应用中,省去预热和加热两个环节,从而降低钢铁生产周期,让轧钢过程变得紧凑,有利于提高生产效率,节约资源能源,降低对周围环境的破坏。
此外,预热和加热流程的省去,还显著减少燃料的燃烧量,有利于节约成本。
应用该技术时,其中最为关键的环节是确保炼钢与连铸顺利衔接。
工作人员要制定科学合理的生产控制计划,建立坯件保温罩、双步进梁式加热炉等设施,采用连铸坯缓冲措施确保产品质量。
轧钢生产中的新技术应用分析

100科学技术Science and technology轧钢生产中的新技术应用分析贾维海(凌源钢铁集团有限责任公司,辽宁 朝阳 122500)摘 要:我国钢铁产业发展势头较为迅猛,其中粗钢产量已经位于世界领先地位,但精钢生产工艺水平以及产量却稍显落后,部分企业仍然存在着对产品生产质量有所忽视的发展弊端,为保证冶金轧钢行业振兴质量,生产精细化发展属于必然之举。
低附加值、高成本以及高能耗等问题,均是我国钢铁行业发展需要解决的困境。
为妥善解决各项问题,突破行业发展瓶颈,对生产新技术展开研究,借助技术优势提升产品质量与能耗控制水平,显得极为重要。
关键词:轧钢生产;新技术;应用中图分类号:TG335 文献标识码:A 文章编号:11-5004(2020)18-0100-2收稿日期:2020-09作者简介:贾维海,男,生于1982年,汉族,山东寿光人,研究生,工程师,研究方向:棒材生产技术研究。
1 轧钢生产技术发展的现状分析对于国内而言,在轧钢生产技术研究方面取得了很多的成果,研发的速度不断加快,各种不同类型的新产品得以研制出来,其中会运用到下述不同类型的轧制工艺,具体如下:①半无头轧制工艺。
融合了其中的众多先进技术。
②超薄规格轧制工艺。
将从热到冷作为主要的宗旨。
③钢轨、热处理轧制工艺的说明。
当发挥出喷风冷却作用后,能获得良好的成效。
④管控冷却工艺。
通过将集管层流冷却作为主要的工艺,并且还需要科学借助压力喷射冷却技术,可以达到良好的处理效果。
⑤基于数学模型下轧制工艺的说明。
通过研发有关调优宽带钢冷连轧数学模型系统之后,经过连续轧制处理,有效发挥出钢冷连轧机柔性轧制的良好作用。
⑥板形管控工艺。
既扩大了有关极限规格的范围,又加快了较高等级钢质量的管控工艺开发速度。
2 轧钢生产技术的发展与应用2.1 高温低氧燃烧技术在轧钢生产中高温低氧燃烧指的是:燃料在较低氧气浓度中充分燃烧或者在较高温度的环境中充分燃烧。
在高温低氧燃烧中,燃料的燃烧过程并不是静态火焰,是一个动态反应,在节能环保方面具有突出优势,加热时间大量减少,燃料节约达到百分之五十,实现了轧钢生产效率的提高。
钢筋加工中的新技术与新方法

钢筋加工中的新技术与新方法钢筋加工是建筑行业中关键的环节之一,对整个工程质量和建筑安全至关重要。
在传统的钢筋加工过程中,人工操作是主要手段,然而随着科技的发展和社会的进步,不断涌现出新的技术和方法,对钢筋加工的效率和质量提出了更高的要求。
本文将探讨一些应用于钢筋加工中的新技术和新方法,并分析其应用前景。
一、3D打印技术在钢筋加工中的应用潜力3D打印技术作为新兴技术,正在逐渐应用于实际生产中,钢筋加工领域也不例外。
传统的钢筋加工过程需要通过模具进行定型,但随着3D打印技术的发展,可以直接将钢筋打印成所需的形状,不仅可以提高加工效率,还可以大大节省人力和物力成本。
此外,3D打印技术还可以实现形状复杂的结构,在某些特殊工程中具有独特的优势。
然而,目前3D打印技术在钢筋加工中面临一些挑战。
首先,3D打印设备和材料的成本仍然相对较高,需要进一步降低成本才能推广应用。
其次,现有的3D打印设备只能打印小型的构件,对于大型工程来说还存在局限性。
最后,3D打印技术的标准和规范还不够完善,需要进一步研究和制定相关规范,以确保打印出的钢筋符合工程质量要求。
二、机器人在钢筋加工中的应用现状及前景展望随着机器人技术的不断进步,越来越多的机器人应用于钢筋加工中。
相比传统的人工操作,机器人具有高精度、高效率、高安全性的特点,可以提高钢筋加工的质量和效率。
目前,机器人在钢筋切割、弯曲、焊接等环节都有应用。
在钢筋切割方面,传统的切割方式多是采用火焰或割炬,除了时间长、操作复杂之外,还存在着安全隐患。
而机器人在切割中具有高速、高精度和安全可控的优势,可以快速完成切割任务,减少人力成本,提高工作效率。
在钢筋弯曲方面,传统的弯曲方式多是采用手工操作,不仅费时费力,而且无法保证弯曲的精度。
而机器人在弯曲中可以通过预定程序完成复杂的操作,不仅可以提高效率,还可以保证弯曲的精度和一致性。
在钢筋焊接方面,机器人可以精确控制焊接路径和焊接参数,避免了人工焊接中的误差和不稳定性,可以提高焊接质量和效率。
冶金轧钢生产新技术解析

冶金轧钢生产新技术解析冶金轧钢是指将金属块材和连续铸坯经过一系列的轧制工序,通过调整轧制工艺参数和采用新技术,使金属材料具备所需的力学性能和外观质量。
近年来,随着科技的进步和应用技术的不断更新,冶金轧钢生产中出现了一些新技术,下面我们将对其中的一些新技术进行解析。
第一种新技术是连铸轧制技术。
传统的冶金轧钢生产中,铸造工艺和轧制工艺是分开进行的,而连铸轧制技术通过一次连续的工艺流程,将铸坯直接轧制成带钢或薄板。
这种技术不仅能够提高生产效率,还能够减少能耗和原材料浪费,提高产品的质量和利用率。
第二种新技术是挤轧技术。
挤轧是指利用挤压力将金属材料从一个截面变形为另一个截面的轧制工艺。
相比于传统的冷轧和热轧工艺,挤轧具有能耗低、生产效率高、产品品质好等优点。
挤轧技术能够制备高精度、高强度和高塑性的金属材料,广泛应用于航空、航天、汽车和建筑等领域。
第三种新技术是微量合金化技术。
微量合金化是指向金属材料中加入极少量的合金元素,用于调整金属材料的化学成分和组织结构,从而改善材料的力学性能和外观质量。
通过微量合金化技术,可以提高材料的强度、延展性、抗腐蚀性和耐磨性等性能,满足不同工程应用的需求。
第四种新技术是智能化轧机技术。
随着信息技术和自动化技术的快速发展,智能化轧机技术逐渐应用于冶金轧钢生产中。
智能化轧机技术通过采集各种传感器的信号,实时监测和控制轧机的工艺参数和设备状态,实现轧制工艺的自动调整和生产过程的实时控制。
这种技术能够提高产品的质量稳定性和生产的精确度,减少人为因素的干扰,提高生产效率。
冶金轧钢生产中的新技术不断涌现,主要包括连铸轧制技术、挤轧技术、微量合金化技术和智能化轧机技术等。
这些新技术的应用能够提高生产效率,降低能耗和原材料浪费,提高产品的质量和利用率,推动冶金轧钢生产向高效、智能和可持续发展的方向发展。
超薄规格热轧板卷稳定轧制及板形控制技术

超薄规格热轧板卷稳定轧制及板形控制技术栗建辉;田亚强【摘要】唐钢UTSP生产线通过对板坯温度控制、压下分配、轧制速度、板形控制等进行研究和实践,开发了薄板坯连铸连轧生产线辊底式加热炉蓄热式燃烧技术与超薄规格板卷稳定轧制技术,提升了板形控制能力,提高了超薄规格板卷轧制稳定性和板形质量,实现了薄板坯连铸连轧生产线1.0 mm超薄规格热轧板卷的大批量稳定生产。
通过技术升级和改造,目前1.0 mm超薄规格单轧程产量可达555 t,规格比例达到60%以上,且带钢板形及表面质量满足品种开发和产品质量要求。
【期刊名称】《金属世界》【年(卷),期】2014(000)004【总页数】6页(P56-61)【作者】栗建辉;田亚强【作者单位】河北联合大学河北省现代冶金技术重点实验室,河北唐山063009; 河北钢铁股份有限公司唐山分公司,河北唐山063009;河北联合大学河北省现代冶金技术重点实验室,河北唐山063009【正文语种】中文薄板坯连铸连轧生产线具有超薄规格产品生产的技术优势,但由于超薄规格热轧板卷生产技术难度高,国内薄板坯连铸连轧生产线的产品规格主要集中在1.6 mm以上,韩国东部制铁公司薄板坯连铸连轧生产线(FTSR)的产品规格集中在1.4 mm 以上,也未实现超薄规格热轧板卷的大批量稳定生产。
唐钢UTSP生产线在原有设备、工艺基础上,通过应用对板坯温度控制、压下分配、轧制速度、板形控制等进行研究,开发了薄板坯连铸连轧生产线辊底式加热炉蓄热式燃烧技术与超薄规格板卷稳定轧制等先进技术,提高了超薄规格板卷轧制稳定性和板形质量,实现了1.0 mm超薄规格热轧板卷的大批量稳定生产,适应了当前市场的需求。
UTSP生产线工艺流程及关键装备、技术唐钢1810线于2001年引进的UTSP薄板坯连铸连轧生产线,是国内第一条应用半无头轧制工艺的热轧带钢生产线,生产线的布置如图1所示,其连铸采用意大利DANIELI公司的FTSC连铸机,生产厚度65~90 mm铸坯;加热炉采用美国BRICMONT公司的辊底式均热炉,炉长230.195 m;轧机采用2RM+5FM布置,粗轧机由意大利DANIELI公司设计,精轧机由日本三菱重工设计,具有动态PC和ORG功能;卷取区采用了IHI株式会社设计制造的高速飞剪、双地下卷取机。
浅谈轧钢生产中的新技术应用

浅谈轧钢生产中的新技术应用轧钢是一种重要的金属加工过程,是将不同形状和尺寸的金属材料通过机械压力改变其截面形状和尺寸的过程。
随着科学技术的不断发展,轧钢生产中也不断出现新技术的应用。
首先,控制轧制参数的技术。
在传统的轧钢生产过程中,轧制参数很难被有效控制,常常会导致轧制品质下降,浪费能源和原材料。
而现代的轧制工艺采用了先进的计算机辅助控制系统,通过对轧制参数进行精确计算和调整,实现对轧制过程的精确控制,提高了产品的质量和加工效率。
例如采用自适应控制技术,可以在轧制过程中根据轧制速度和温度变化自动调整轧制参数,避免了出现生产过程中的偏差。
其次,智能化生产技术的应用。
随着工业自动化水平的不断提高,智能化生产技术在轧钢生产中的应用也越来越广泛。
例如利用激光技术测量坯料的形状和尺寸,通过数字化的方式实现对原材料和成品的自动化检测和调整,提高了生产效率和品质稳定性。
第三,绿色环保性能技术在轧钢生产中的应用。
随着社会对环境保护的重视程度的不断提高,轧钢生产中采用环保型技术已经成为现代轧钢生产的趋势。
例如采用采用清洗垃圾泵系统,集中回收和处理重金属、有害气体等工业废气和废水,降低环境污染。
同时,绿色制造理念在轧钢生产过程中的应用,例如采用降低能耗、减少废品率、回收利用等手段,实现了生产过程中的节能、降耗和环保目标。
最后,材料科学技术的应用。
轧制生产过程中,原材料的材料科学特性对生产质量和工艺效率起着重要作用。
因此,通过采用先进的材料科学技术研究和开发新型原材料,可以提高轧制生产过程中的有效性和性能优化程度。
例如,针对高强度钢管的轧制,采用微合金化技术,可以提高钢管的强度和韧性,减轻钢管的重量,提高了产品的性能和市场竞争力。
总之,随着科学技术的不断发展,轧钢生产中的新技术应用为轧制工艺的性能优化和加工效率提高提供了有力的支撑,同时也为整个工业制造业的发展注入了新的动力。
- 1、下载文档前请自行甄别文档内容的完整性,平台不提供额外的编辑、内容补充、找答案等附加服务。
- 2、"仅部分预览"的文档,不可在线预览部分如存在完整性等问题,可反馈申请退款(可完整预览的文档不适用该条件!)。
- 3、如文档侵犯您的权益,请联系客服反馈,我们会尽快为您处理(人工客服工作时间:9:00-18:30)。
通钢超薄热带轧制过程中的新工艺与控制过程中的新技术
[摘要]对通钢超薄热带轧制过程中的新工艺与控制过程中的新技术的描述,介绍了通钢热轧厂整个生产工艺过程中所用的新工艺和新技术,并对现场各种控制阐述了各种新工艺的原理以及在通钢生产中的实际应用。
【关键词】新工艺;新技术;控制功能
近年来,轧钢生产中所涌现的新技术、新工艺主要是围绕节约能源、降低成本、提高产品质量、开发新产品所进行的。
在节能降耗上,主要技术是:连铸坯热送热装技术、薄板坯连铸连轧技术、先进的节能加热炉等;在提高产品性能、质量上,主要技术是:TMCP技术、高精度轧制技术、先进的板形、板厚控制技术、计算机生产管理技术等;在技术装备上,主要是大型化、连续化、自动化,这些技术的应用可极大地提高产品的竞争能力。
一、新工艺
作为当今世界最先进的短流程生产线,通钢热连轧机生产线采用了许多先进的新技术。
1、辊底式加热炉。
可调节连铸机与轧机之间的生产节奏,起到缓冲作用。
炉内采用长寿命水冷炉辊和低氧化氮烧嘴。
板坯在炉内的运输过程为全自动控制,燃烧过程实行计算机自动管理。
2、铁素体轧制。
对于低碳钢、超低碳钢及极低碳钢可以采用铁素体轧制工艺。
采用铁素体区轧制工艺时,粗轧机组的2架轧机在奥氏体组织状态中轧制,在轧制过程中通过中间冷却装置将轧轧件冷却至Ar3以下温度,完成由奥氏体向铁素体的转变。
在精轧5架轧机内以铁素体组织状态进行轧制。
带钢出精轧机组后,通过输出辊道空冷送至地下卷取机进行卷取。
3、三次除鳞。
热连轧工艺生产的连铸坯表面氧化铁皮细小、致密且不易清除干净,并与金属机体粘结很紧,从而不易清除。
为此,在连铸摆剪前设置了旋转除鳞机对连铸坯进行一次除鳞,在粗轧机入口处安装了高压粗轧除鳞机用于清除板坯的炉生氧化铁皮,在精轧机入口处安装了高压精轧除鳞机用于清除中间坯表面的氧化铁皮。
这种除鳞方式效果好,可提高带钢表面的质量。
4、采用了PC轧制技术。
增加了板形控制能力,该系统可提高带钢凸度和平直度控制能力,从面提高板形质量。
5、热轧油润滑系统。
各架轧机均设有热轧油集管和喷嘴,对工作辊辊缝喷射油水混合液进行润滑。
从而降低轧制力,减少轧制能耗,减少轧辊磨损,有利于提高带钢表面质量。
6、采用液压活套技术。
在精轧5架轧机之间安装了液压活套装置主要用来分别控制两机架间的张力,以保证轧制过程中所需的最低带钢张力,实现机架间轧制状态的稳定。
因而要求具有高的响应速度,只有液压活套具有这种高响应速度。
7、输出辊道设置层流冷却系统。
采用层流冷却工艺,将带钢快速冷却到目标卷取温度,以满足卷取温度的要求。
二、新技术:控制功能简介
1、AGC:精轧机自动厚度控制(AGC)的目的就是通过调节轧制辊缝来达到和保持目标的带钢厚度。
液压自动厚度控制系统对F1-F5机架均适用。
系统包括以下功能:(1)绝对值厚度仪AGC(ABS-GM-AGC);(2)相对值(lock-on)厚度仪AGC(LKON-GM-AGC);(3)轧机模数控制(MMC);(4)监控AGC (M-AGC);(5)负荷再分配控制;(6)辊缝补偿;(7)带尾补偿。
2、AWC
基本控制策略
(1)宽度设定:MSUC根据产品规格和原料情况,利用真实地反映变形规律的模型,合理的设定立辊机架的压下量,从而获得具有较高宽度精度的产品。
(2)动态控制:针对热轧板坯本身各种因素的波动而影响轧制中的板宽。
包括:SS-AWC(短行程AWC)和RF-AWC(轧制力AWC)。
(3)RF-AWC(轧制力AWC):沿轧件长度方向上轧件温度波动会引起其变型抗力值不同,因而造成宽度波动,RF-AWC就是对这种变型抗力的变化进行补偿,是一种反馈控制。
3、AWC
SS-AWC(短行程控制):也叫头尾校正,用于克服测压过程中产生的头尾失宽,从而控制鱼尾及切损,提高热轧带成材率。
基本思想:根据侧压造成的板坯头尾失宽的轮廓曲线,在轧制过程中不断改变立辊轧机的辊缝,使辊缝的改变恰好补偿头尾失宽,从而使水平轧制后的头尾宽度接近于目标宽度。
4、CTC
CTC(卷取温度控制)包括预设功能和动态控制功能,控制在ROT上带钢的冷却水量。
主要的计算过程在level 2 计算机和level 1.5 计算机进行,水阀的控制在level 1 PLC内进行。
CTC功能包括:(1)、预设功能(2)、动态控制功能
CTC的冷却方式:1)前段冷却2)后段冷却3)慢冷4)头/尾不冷5)头/尾弱冷
5、SSUC
SSUC设定交叉角度与弯辊力值;轧制力跟随控制、自动凸度控制与自动平直度控制反馈到SSUC;轧辊的热膨胀与磨损将影响SSUC的设定值。
6、MSUC
MSUC-0th:连铸摆式剪剪切板坯尾部完成,加热炉将板坯的实际值传送给轧机二级后;MSUC-1st:当板坯头部目标点到达加热炉出炉区时;MSUC-2nd:当板坯头部目标点到达RET高温计时;MSUC-3rd:当板坯头部目标点到达RDT 高温计时;MSUC-4th:当板坯头部目标点到达FET高温计时。
7、ASC
在带钢轧制过程中,ASC通过改变工作辊弯辊力来调节目标板型。
ASC包括以下功能。
1、自动板型反馈控制ASPC,2、自动平直度ASFC反馈控制ASFB,3、轧制力跟随控制FFC,4、轧辊热凸度补偿:RPC。
在精轧出口,自动板型反馈控制测量带钢的凸度,并调节工作辊弯辊力。
在精轧出口,自动平直度反馈控制测量带钢的平直度,并调节工作辊弯辊力。
轧制力跟随控制和轧辊热凸度补偿是辅助功能。
由于轧制力的变化,轧制力跟随控制补偿带钢的凸度变化。
由于工作辊凸度的变化,轧辊热凸度补偿控制补偿带钢的凸度变化。
这一功能主要补偿热凸度和轧辊磨损。
交叉辊(at F1,2and3)仅在不进行轧制的过程中来进行交叉,在轧制过程中不交叉。
钢铁材料具有成本低、强度高、易回收、能再生等特点,广泛应用于国民建设的各个领域。
在人们能够所预见的未来,还没有任何一种材料能够动摇钢铁材料的霸主地位,而作为钢材成型的支柱技术的轧钢生产工艺也无法取代。
因此,近些年我国钢产量迅猛发展,一些企业都在忙于建设新项目。
但由于国际市场钢材需求量已呈下降趋势,我国钢材需求也接近饱和状态,相当一部分都是低水平重复建设,缺乏竞争力。
因此,要想在激烈的竞争中占领市场,必须要淘汰落后的工艺与设备,大量采用新工艺、新技术。
结论
(1):通钢热轧超薄带厂采用的新工艺:辊底式加热炉、铁素体轧制、三次除磷、PC轧制技术、热轧润滑系统、液压活套技术、层流冷却、地下卷取机采用全液压控制技术。
(2):通钢热轧超薄带厂采用的新技术:各种控制功能简介:宽度、厚度、温度和冷却控制。