PPW-7中文资料
PanelView Plus 7 Performance终端产品目录说明书

Technical DataPanelView Plus 7 Performance TerminalsCatalog Numbers 2711P-T7C22D9P , 2711P-T7C22D9P-B, 2711P-T7C22A9P , 2711P-T7C22A9P-B, 2711P-B7C22D9P , 2711P-B7C22D9P-B, 2711P-B7C22A9P, 2711P-B7C22A9P-B, 2711P-T9W22D9P , 2711P-T9W22D9-B, 2711P-T9W22A9P , 2711P-T9W22A9P-B, 2711P-T10C22D9P , 2711P-T10C22D9P-B, 2711P-T10C22A9P, 2711P-T10C22A9P-B, 2711P-B10C22D9P , 2711P-B10C22D9P-B, 2711P-B10C22A9P , 2711P-B10C22A9-B, 2711P-T12W22D9P , 2711P-T12W22D9P-B, 2711P-T12W22A9P , 2711P-T12W22A9P-B, 2711P-T15C22D9P , 2711P-T15C22D9P-B, 2711P-T15C22A9P , 2711P-T15C22A9P-B, 2711P-B15C22D9P , 2711P-B15C22D9P-B, 2711P-B15C22A9P , 2711P-B15C22A9P-B, 2711P-T19C22D9P , 2711P-T19C22D9P-B, 2711P-T19C22A9P , 2711P-T19C22A9P-BSummary of ChangesThe PanelView™ Plus 7 Performance terminals are operator interface devices. They monitor and control devices that are attached to ControlLogix® and CompactLogix™ 5370controllers on an EtherNet/IP network. Animated graphic and text displays provide operators a view into the operating state of a machine or process. Operators interact with the control system by using touch screen or keypad input.TopicPage Environmental Specifications 2Certifications 3Technical Specifications 4Product Dimensions 7Accessories 8HMI Software 9Additional Resources10TopicPage Updated system memory to 512 MB RAM and 512 MB storage.Updated user memory to 80 MB, approx, nonvolatile storage for applications.4, 5, 62Rockwell Automation Publication 2711P-TD009C-EN-P - July 2016PanelView Plus 7 Performance TerminalsFeatures include the following:•FactoryTalk® View Machine Edition software, version 8.1, provides a familiar environment for creating HMI applications•Windows CE operating system with desktop access for configuration and third-party applications •Connection to ControlLogix or CompactLogix 5370 controllers•Ethernet communication that can support Device Level Ring (DLR), linear, or star network topologies•W eb browser, Microsoft file viewers, text editor, PDF viewer, remote desktop connection, and media player on the terminal desktopEnvironmental SpecificationsThis table lists environmental specifications for the PanelView Plus 7 Performance terminals.AttributeValueTemperature, operating (1)(1)The 19-inch terminals (2711P-T19C22D9P , 2711P-T19C22D9P-B, 2711P-T19C22A9P , and 2711P-T19C22A9P-B) are rated up to 50 °C (122 °F) operating temperature.0…55 °C (32…131 °F)Temperature, nonoperating-25…+70 °C (-13…+158 °F)Heat dissipation (2)(2)Typical BTU measurements were taken at 25 °C (77 °F).7-in. DC (touch, and touch with keypad), 51 BTU (typical)7-in. AC (touch, and touch with keypad), 53 BTU (typical)9-in. DC, 55 BTU (typical)9-in. AC, 58 BTU (typical)10-in. DC (touch, and touch with keypad), 51 BTU (typical)10-in. AC (touch, and touch with keypad), 56 BTU (typical)12-in. DC, 60 BTU (typical)12-in. AC, 67 BTU (typical)15-in. DC (touch, and touch with keypad), 61 BTU (typical)15-in. AC (touch, and touch with keypad), 68 BTU (typical)19-in. DC, 114 BTU (typical)19-in. AC, 119 BTU (typical)Altitude, operating 2000MRelative humidity 5…95% without condensation Vibration 0.012 pk-pk, 10…57 Hz 2 g peak at 57…500 Hz (3)(3)The 15-inch and 19-inch terminals (2711P-T15C22D9P , 2711P-T15C22D9P-B, 2711P-T15C22A9P , 2711P-T15C22A9P-B, 2711P-B15C22D9P , 2711P-B15C22D9P-B,2711P-B15C22A9P , 2711P-B15C22A9P-B, 2711P-T19C22D9P , 2711P-T19C22D9P-B, 2711P-T19C22A9P , 2711P-T19C22A9P-B) are rated to: 0.006 in. pk-pk, 10...57 Hz, 1 g peak at 57...640 Hz.Shock, operating 15 g at 11 ms Shock, nonoperating 30 g at 11 msEnclosure ratingsNEMA and UL Type 12, 13, 4X, also rated IP66 as Classified by ULRockwell Automation Publication 2711P-TD009C-EN-P - July 20163PanelView Plus 7 Performance TerminalsCertificationsThis table lists certifications for the PanelView Plus 7 Performance terminals.Certification (1)(1)When marked. See the Product Certification link at /global/certification/overview.page for Declarations of Conformity, Certificates, and othercertification details.ValuecULuscULus Listed Industrial Control Equipment for use in Hazardous Locations (E10314) per standards ANSI / ISA 12.12.01 and CSA C22.2 No. 213. rated:•Class I, Div 2, Groups A, B, C, DEnclosure type ratings per UL50 and CSA C22.2 No. 94.2-07. Enclosure ingress protection classified by UL per IEC 60529.CE (EMC)European Union 2004/108/EC EMC Directive, compliant with:•EN 61000-6-2; Industrial Immunity •EN 61000-6-4; Industrial Emissions •EN 61131-2; Programmable ControllersCE (LVD)European Union 2006/95/EC Low Voltage Directive, compliant with:•EN 61131-2; Programmable Controllers RCM Australian Radiocommunications Act, compliant with:•AS/NZS CISPR 11; Industrial Emissions RoHS China RoHS, Turkey RoHS, European RoHS KCC Certificate of complianceEtherNet/IPODVA conformance tested to EtherNet/IP specifications4Rockwell Automation Publication 2711P-TD009C-EN-P - July 2016PanelView Plus 7 Performance TerminalsTechnical SpecificationsThe tables in this section provide technical specifications for the PanelView Plus 7 Performance terminals.PanelView Plus 7 Performance 7-in and 9-in TerminalsAttribute 7-in. Touch2711P--T7C22D9P , 2711P--T7C22D9P-B (1)2711P-T7C22A9P , 2711P-T7C22A9P-B (1)Catalog numbers with a -B extension denote terminals that exclude the Allen-Bradley brand marking. Customers can put their own brand labels on these terminals.7-in. Touch with Keypad2711P-B7C22D9P , 2711P-B7C22D9P-B (1)2711P-B7C22A9P , 2711P-B7C22A9P-B 9-in. Touch2711P-T9W22D9P, 2711P-T9W22D9P-B (1)2711P-T9W22A9P , 2711P-T9W22A9P-BOperator input Touch Touch with keypadTouchDisplay type TFT Color Display size, diagonal 6.5-in.9-in. widescreen Viewing area (W x H)132 x 99 mm (5.2 x 3.9 in.)196 x 118 mm (7.7 x 4.6 in.)Display resolution 640 x 480 VGA, 18-bit color graphics 800 x 480 WVGA, 18-bit color graphics Aspect ratio 4:3 5:3Brightness, typical 300 cd/m 2 (Nits)Backlight lifeWhite light-emitting diode, solid-stateLife: 50,000 h min at 40 °C (104 °F) to half-brightness, backlight is not replaceable Touch screenAnalog resistiveActuation rating: 1 million presses Operating force: 100 grams Battery (real-time clock backup)Accuracy: +/-2 minutes per month.Battery life: 4 years min at 25 °C (77 °F)Replacement: CR2032 lithium coin cellMemory:•System •User •512 MB RAM and 512 MB storage•80 MB, approx, nonvolatile storage for applicationsSecure Digital (SD) card slot One SD card slot for external storage; supports cat. no. 1784-SD x cardsUSB ports:•Host •Device •Two USB high-speed 2.0 host ports (type A) support removable flash drives for external storage •One high-speed 2.0 device port (type B) that will be functional in a future releaseOperating system Windows CE with Extended Features and MS Office Viewers (includes FTP , VNC client server, ActiveX controls, PDF reader, third-party device support)Ethernet ports Two 10/100Base-T, Auto MDI/MDI-X Ethernet ports that support Device Level Ring (DLR), linear, or star network topologies Software FactoryTalk View Studio for Machine Edition, FactoryTalk ViewPoint, version 2.6 or laterElectrical Input voltage 24V DC nom (18…30V DC)100…240V AC 24V DC nom (18…30V DC)100…240V AC 24V DC nom (18…30V DC)100…240V AC Power consumption 50 W max(2.1 A at 24V DC)105VA 50 W max(2.1 A at 24V DC)105VA 50 W max(2.1 A at 24V DC)105VA Power supply Supports (SELV) and (PELV) 24V DC supplies (2)(2)DC-powered terminals support safety extra low voltage (SELV) and protective extra low voltage (PELV) 24V DC power supplies such as cat. nos. 1606-XLP95E, 1606-XLP100E, 2711P-RSACDIN.—Supports (SELV) and (PELV) 24V DC supplies (2)—Supports (SELV) and (PELV) 24V DC supplies (2)—Mechanical Weight, approx 1.2 kg (2.65 lb) 1.47 kg (3.25 lb) 1.58 kg (3.48 lb)Dimensions, approx (H x W x D)170 x 212 x 69.6 mm 6.69 x 8.35 x 2.74 in.179 x 285 x 69.6 mm 7.05 x 11.22 x 2.74 in.190 x 280 x 69.6 mm 7.48 x 11.02 x 2.74 in.Cutout dimensions, approx (H x W)142 x 184 mm 5.59 x 7.24 in.142 x 237 mm 5.59 x 9.33 in.162 x 252 mm 6.38 x 9.92 in.Rockwell Automation Publication 2711P-TD009C-EN-P - July 20165PanelView Plus 7 Performance TerminalsPanelView Plus 7 Performance 10-in and 12-in TerminalsAttribute 10-in. Touch2711P-T10C22D9P, 2711P-T10C22D9P-B (1)2711P-T10C22A9P , 2711P-T10C22A9P-B (1)Catalog numbers with a -B extension denote terminals that exclude the Allen-Bradley brand marking. Customers can put their own brand labels on these terminals.10-in. Touch with Keypad2711P-B10C22D9P , 2711P-B10C22D9P-B (1)2711P-B10C22A9P , 2711P-B10C22A9P-B 12-in. Touch2711P-T12W22D9P , 2711P-T12W22D9P-B (1)2711P-T12W22A9P , 2711P-T12W22A9P-B Operator input Touch Touch with keypadTouchDisplay type TFT Color Display size, diagonal 10.4-in.12.1-in.Viewing area (W x H)211 x 158 mm (8.3 x 6.2 in.)261 x 163 mm (10.3 x 6.4 in.)Display resolution 800 x 600 SVGA, 18-bit color graphics 1280 x 800 WXGA, 18-bit color graphics Aspect ratio 4:316:10Brightness, typical 300 cd/m 2 (Nits)Backlight lifeWhite light-emitting diode, solid-stateLife: 50,000 h min at 40 °C (104 °F) to half-brightness, backlight is not replaceable Touch screenAnalog resistiveActuation rating: 1 million presses Operating force: 100 grams Battery (real-time clock backup)Accuracy: +/-2 minutes per month.Battery life: 4 years min at 25 °C (77 °F)Replacement: CR2032 lithium coin cellMemory:•System •User •512 MB RAM and 512 MB storage•80 MB, approx, nonvolatile storage for applicationsSecure Digital (SD) card slot One SD card slot for external storage; supports cat. no. 1784-SD x cardsUSB ports:•Host •Device •Two USB high-speed 2.0 host ports (type A) support removable flash drives for external storage •One high-speed 2.0 device port (type B) that will be functional in a future releaseOperating system Windows CE with Extended Features and MS Office Viewers (includes FTP , VNC client server, ActiveX controls, PDF reader, third-party device support)Ethernet ports Two 10/100Base-T, Auto MDI/MDI-X Ethernet ports that support Device Level Ring (DLR), linear, or star network topologies Software FactoryTalk View Studio for Machine Edition, FactoryTalk ViewPoint, version 2.6 or laterElectrical Input voltage 24V DC nom (18…30V DC)100…240V AC 24V DC nom (18…30V DC)100…240V AC 24V DC nom (18…30V DC)100…240V AC Power consumption 50 W max(2.1 A at 24V DC)105VA 50 W max(2.1 A at 24V DC)105VA 50 W max(2.1 A at 24V DC)105VA Power supply Supports (SELV) and (PELV) 24V DC supplies (2)(2)DC-powered terminals support safety extra low voltage (SELV) and protective extra low voltage (PELV) 24V DC power supplies such as cat. nos. 1606-XLP95E, 1606-XLP100E, 2711P-RSACDIN.—Supports (SELV) and (PELV) 24V DC supplies (2)—Supports (SELV) and (PELV) 24V DC supplies (2)—Mechanical Weight, approx 2.28 kg (5.03 lb) 2.58 kg (5.69 lb) 2.54 kg (5.60 lb)Dimensions, approx (H x W x D)252 x 297 x 69.6 mm 9.92 x 11.69 x 2.74 in.252 x 385 x 69.6 mm 9.92 x 15.16 x 2.74 in.240 x 340 x 69.6 mm 9.69 x 13.39 x 2.74 in.Cutout dimensions, approx (H x W)224 x 269 mm 8.82 x 10.59 in.224 x 335 mm 8.82 x 13.19 in.218 x 312 mm 8.58 x 12.28 in.6Rockwell Automation Publication 2711P-TD009C-EN-P - July 2016PanelView Plus 7 Performance TerminalsPanelView Plus 7 Performance 15-in and 19-in TerminalsAttribute 15-in. Touch2711P-T15C22D9P , 2711P-T15C22D9P-B (1)2711P-T15C22A9P , 2711P-T15C22A9P-B (1)Catalog numbers with a -B extension denote terminals that exclude the Allen-Bradley brand marking. Customers can put their own brand labels on these terminals.15-in. Touch with Keypad2711P-B15C22D9P, 2711P-B15C22D9P-B (1)2711P-B15C22A9P , 2711P-B15C22A9P-B 19-in. Touch2711P-T19C22D9P , 2711P-T19C22D9P-B (1)2711P-T19C22A9P, 2711P-T19C22A9P-B Operator input Touch Touch with keypadTouchDisplay type TFT Color Display size, diagonal 15-in.19-in.Viewing area (W x H)304 x 228 mm (12.0 x 9.0 in.)376 x 301 mm (14.8 x 11.9 in.)Display resolution 1024 x 768 XGA, 18-bit color graphics 1280 x 1024 SXGA, 18-bit color graphics Aspect ratio 4:35:4Brightness, typical 300 cd/m 2 (Nits)Backlight lifeWhite light-emitting diode, solid-stateLife: 50,000 h min at 40 °C (104 °F) to half-brightness, backlight is not replaceable Touch screenAnalog resistiveActuation rating: 1 million presses Operating force: 100 grams Battery (real-time clock backup)Accuracy: +/-2 minutes per month.Battery life: 4 years min at 25 °C (77 °F)Replacement: CR2032 lithium coin cellMemory:•System •User •512 MB RAM and 512 MB storage•80 MB, approx, nonvolatile storage for applicationsSecure Digital (SD) card slot One SD card slot for external storage; supports cat. no. 1784-SD x cardsUSB ports:•Host •Device •Two USB high-speed 2.0 host ports (type A) support removable flash drives for external storage •One high-speed 2.0 device port (type B) that will be functional in a future releaseOperating system Windows CE with Extended Features and MS Office Viewers (includes FTP , VNC client server, ActiveX controls, PDF reader, third-party device support)Ethernet ports Two 10/100Base-T, Auto MDI/MDI-X Ethernet ports that support Device Level Ring (DLR), linear, or star network topologies Software FactoryTalk View Studio for Machine Edition, FactoryTalk ViewPoint, version 2.6 or laterElectrical Input voltage, DC 24V DC nom (18…30V DC)100…240V AC 24V DC nom (18…30V DC)100…240V AC 24V DC nom (18…30V DC)100…240V AC Power consumption, DC 50 W max(2.1 A at 24V DC)105VA 50 W max(2.1 A at 24V DC)105VA 50 W max(2.1 A at 24V DC)105VA Power supply Supports (SELV) and (PELV) 24V DC supplies (2)(2)DC-powered terminals support safety extra low voltage (SELV) and protective extra low voltage (PELV) 24V DC power supplies such as cat. nos. 1606-XLP95E, 1606-XLP100E, 2711P-RSACDIN.—Supports (SELV) and (PELV) 24V DC supplies (2)—Supports (SELV) and (PELV) 24V DC supplies (2)—Mechanical Weight, approx 3.69 kg (8.14 lb) 4.14 kg (9.13 lb) 5.62 kg (12.40 lb)Dimensions, approx (H x W x D)318 x 381 x 69.6 mm 12.52 x 15.00 x 2.74 in 329 x 484 x 69.6 mm 12.95 x 19.06 x 2.74 in 411 x 485 x 69.6 mm 16.18 x 19.09 x 2.74 in Cutout dimensions, approx (H x W)290 x 353 mm 11.42 x 13.90 in290 x 418 mm 11.42 x 16.46 in383 x 457 mm 15.08 x 17.99 inRockwell Automation Publication 2711P-TD009C-EN-P - July 20167PanelView Plus 7 Performance TerminalsProduct DimensionsThe table provides product dimensions. The 10.4-inch touch and combination keypad with touch devices are shown for illustrative purposes. All other terminal sizes look similar.PanelView Plus 7 Performance Dimensions - 10.4-in. ModelProduct Dimensions - PanelView Plus 7 Performance TerminalsTerminal Size Input Type Height (a)mm (in.)Width (b)mm (in.)Overall Depth (c)mm (in.)Mounted Depth (d)mm (in.)6.5-in.Key/touch 179 (7.05)285 (11.22)69.6 (2.74)63.6 (2.50)Touch 170 (6.69)212 (8.35)9-in.Touch 190 (7.48)280 (11.02)10.4-in.Key/touch 252 (9.92)385 (15.16)Touch 252 (9.92)297 (11.69)12.1-in.Touch 246 (9.69)340 (13.39)15-in.Key/touch 329 (12.95)484 (19.06)Touch 318 (12.52)381 (15.00)19-in.Touch411 (16.18)485 (19.09)TIPWhen mounted in a panel, the front of the bezel extends less than 6.36 mm (0.25 in.) from the front of the panel.b8Rockwell Automation Publication 2711P-TD009C-EN-P - July 2016PanelView Plus 7 Performance TerminalsAccessoriesThe tables in this section list accessories for the PanelView Plus 7 Performance terminals.Protective OverlaysPower Supplies and Power Terminal BlocksMounting HardwareSecure Digital (SD) CardsBattery ReplacementCat. No.(1)(1)Three overlays are shipped with each catalog number.Display Size Operator Input Touch Key and Touch2711P-RGT7SP 6.5-in.•2711P-RGB7P •2711P-RGT9SP 9-in. (wide)•2711P-RGT10SP 10.4-in.•2711P-RGB10P •2711P-RGT12SP 12.1-in. (wide)•2711P-RGT15SP 15-in.•2711P-RGB15P •2711P-RGT19P19-in.•Cat. No.DescriptionQuantity1606-XLP95E DIN rail power supply, 24…28V DC output voltage, 95 W 11606-XLP100E DIN rail power supply, 24…28V DC output voltage, 100 W 12711P-RSACDIN DIN rail power supply, AC-to-DC, 85…265V AC, 47…63 Hz 12711P-RTBAP 3-pin AC power terminal block 102711P-RTBDSP3-pin DC power terminal block10Cat. No.Description Quantity 2711P-RMCP (1)(1)Catalog number 2711P-RMCP mounting levers are used with PanelView Plus 7 Performance terminals. Do not use gray mounting levers; they are notcompatible with PanelView Plus 7 Performance terminals.Mounting levers (black)16Cat. No.Description 1784-SD1 1 GB SD card 1784-SD2 2 GB SD card2711C-RCSDUSB to SD adapter for SD cardCat. No.DescriptionQuantity2711P-RY2032Lithium coin cell battery, CR2032 equivalent1Rockwell Automation Publication 2711P-TD009C-EN-P - July 20169PanelView Plus 7 Performance TerminalsHMI SoftwareAll PanelView Plus 7 terminals are configured with FactoryTalk View Studio software and have an integrated runtime system called FactoryTalk View Machine Edition Station.Machine Edition Station runs projects that are developed with FactoryTalk View Studio software and is included on all PanelView Plus 7 terminals.Two versions of FactoryTalk View Studio software support application development for PanelView Plus 7 terminals.Y ou can import PanelView Standard/PanelBuilder® 32 and PanelView applications into FactoryTalk View Studiosoftware as Machine Edition applications by using the Machine Edition Import Wizard. The Import Wizard steps you through a few options such as scaling to a new screen resolution size, and then converts objects, text, tags, and communication configurations to ones that are available in Machine Edition.FactoryTalk ViewPoint software, an add-on to FactoryTalk View Studio software, allows plant managers, production supervisors, system integrators, and other key stakeholders to view and control real-time plant floor operations remotely from a web browser. FactoryTalk ViewPoint enabled displays are fully scalable and animated in the browser. The remote user can also view displays that are not the active display of the terminal.Each PanelView Plus 7 terminal contains one license that supports one client connection to the terminal. No additional software is required.For a complete list of available HMI software, visit /rockwellsoftware .Cat. No.(1)(1)To order localized versions of the software, replace EN in the catalog number with DE for German, FR for French, JP for Japanese, or ZH for Chinese.Description9701-VWSTMENEFactoryTalk View Studio for Machine Edition software - Configuration software for developing and testingmachine-level human machine interface (HMI) applications. Includes RSLinx® Enterprise and KEPServer Enterprise software.9701-VWSTENEFactoryTalk View Studio software - Configuration software for developing and testing machine-level and supervisory-level human machine interface (HMI) applications.10Rockwell Automation Publication 2711P-TD009C-EN-P - July 2016PanelView Plus 7 Performance TerminalsAdditional ResourcesThese documents contain more information about related products from Rockwell Automation.Y ou can view or download publications at /global/literature-library/overview.page . T o order paper copies of technical documentation, contact your local Allen-Bradley distributor or Rockwell Automation sales representative.ResourceDescriptionPanelView Plus 7 Performance Terminals User Manual, publication 2711P-UM008 Provides instructions on how to install, configure, and operate the PanelView Plus 7 Performance terminals.Industrial Automation Wiring and Grounding Guidelines, publication 1770-4.1 Provides general guidelines on how to install a Rockwell Automation industrial system.Product Certifications website, /global/certification/overview.pageProvides declarations of conformity, certificates, and other certification details.PanelView Plus 7 Performance Terminals Notes:Rockwell Automation Publication 2711P-TD009C-EN-P - July 201611Allen-Bradley, CompactLogix, ControlLogix, FactoryTalk, PanelBuilder, PanelView, LISTEN. THINK. SOLVE, Rockwell Automation, Rockwell Software, and RSLinx are trademarks of Rockwell Automation, Inc.Trademarks not belonging to Rockwell Automation are property of their respective companies.Publication 2711P-TD009C-EN-P - July 2016Supersedes Publication 2711P-TD009B-EN-P - May 2016Copyright © 2016 Rockwell Automation, Inc. All rights reserved. Printed in the U.S.A.Rockwell Automation SupportUse the following resources to access support information.Documentation FeedbackY our comments will help us serve your documentation needs better. If you have any suggestions on how to improve this document, complete the How Are W e Doing? form at /idc/groups/literature/documents/du/ra-du002_-en-e.pdf .Technical Support CenterKnowledgebase Articles, How-to Videos, FAQs, Chat, User Forums, and Product Notification /knowledgebase Local Technical Support Phone NumbersLocate the phone number for your /global/support/get-support-now.page Direct Dial CodesFind the Direct Dial Code for your product. Use the code to route your call directly to a technical support /global/support/direct-dial.page Literature LibraryInstallation Instructions, Manuals, Brochures, and Technical /literature Product Compatibility and Download Center(PCDC)Get help determining how products interact, check features and capabilities, and find associated /global/support/pcdc.pageRockwell Otomasyon Ticaret A.Ş., Kar Plaza İş Merkezi E Blok Kat:6 34752 İçerenköy, İstanbul, T el: +90 (216) 5698400Rockwell Automation maintains current product environmental information on its website at /rockwellautomation/about-us/sustainability-ethics/product-environmental-compliance.page .。
OP07中文资料_数据手册_参数

绝对大额定值超过工作自由空气温度范围(除非另有说明) (1) MIN MAX单元 V CC + (2) 0 22电源电压 V V CC- (2) -22 0 差 分输入电压 (3) ±30 V V 我 输入电压范围(任一输入) (4) ±22 V 输出短路持续时间 (5)无限 T J操作虚拟结温度 150 C引线温 度距离壳体1.6毫米(1/16英寸),持续10秒 260 C (1)强调绝对大额定值以外列出的可能会导致设备永久性损坏.这些是压力评级只 有在这些或任何其他超出建议的操作条件下的条件下才能操作设备不暗示条件.暴露在绝对大额定条件下可能会影响器件的可靠性. (2) 除非另有说明,所有的电压值都是相对于V CC + 和V CC- 之间的中点 . (3)差分电压相对于IN处于IN + - . (4)输入电压的 大小决不能超过电源电压的大小或15 V,取其小者. (5)输出可能短路到地或任何一个电源. 7.2处理评级参数定义 MIN MAX单元 T STG存储温度范围 -65 150 C人体模型(HBM),根据ANSI / ESDA / JEDEC JS-001,全部 0 1000 (1)静电的 V (ESD) V卸货带电器 件型号(CDM),根据JEDEC规范JESD22- 0 1000 C101,所有引脚 (2) (1) JEDEC文件JEP??155指出,500V HBM允许采用标准 ESD控制过程进行安全制造. (2) JEDEC文件JEP??157指出,250V CDM允许使用标准ESD控制过程进行安全制造. 7.3推荐的操作条件 超过工作自由空气温度范围(除非另有说明) MIN MAX单元 V CC + 3 18电源电压 V CC- -3 -18 V V IC共模输入电压 V CC± =±15 V -13 13 T A.操作自由空气温度 0 70 C 7.4热量信息 温度计 (1) D P单元 RθJA结到环境热阻 97 85 °C / W (1)有关传统和新型散热指 标的更多信息 OP07Y精密运算放大器 SLOS099B - 1983年10月 - 修订于1996年8月五邮政信箱655303 ? 达拉斯,得克萨斯州75265 经营特色,V CC ±= ± 15 V,T A = 25°C参数测试 OP07C OP07D单元参数条件? MIN TYP MAX MIN TYP MAX单元 F = 10HZ 10.5 10.5 √ VN等效输入噪 声电压 F = 100HZ 10.2 10.3内华达州/ √HZ的 F = 1KHZ 9.8 9.8 VN(PP)峰峰值等效输入噪声电压 F = 0.1HZ至10HZ 0.38 0.38 μV F = 10HZ 0.35 0.35 √在等效输入噪声电流 F = 100HZ 0.15 0.15 PA / √HZ的 F = 1KHZ 0.13 0.13 IN(PP)峰峰值等效输入噪声电流 F = 0.1HZ 至10HZ 15 15 PA的 SR摆率 RL≥2KΩ 0.3 0.3 V /微秒 ?除非另有说明,所有特性均在开环条件下以零共模输入电压进行测量. 电气特 性,V CC ±= ± 15 V,T A = 25°C(除非另有说明)参数测试条件? OP07Y单元参数测试条件? MIN TYP MAX单元 VIO输入失调电 压 RS = 50Ω 60 150 μV输入失调电压的长期漂移见注6 0.5 μV/月偏移调整范围 RS = 20KΩ,见图1 ±4毫伏 IIO输入失调电流 0.8 6 NA 的 IIB输入偏置电流 ±2 ±12 NA的 VICR共模输入电压范围 ±13 ±14 V RL≤10KΩ ±12 ±13 VOM峰值输出电压 RL≤2KΩ ±11.5 ±12.8 V RL≤1KΩ ±12 AVD大信号L≤500KΩ 400 AVD大信号差分电压放大 VO = ±10 V, RL = 2KΩ 120 400 B1单位增益带宽 0.4 0.6兆赫 RI输入电阻 7 31中号 Ω CMRR共模输入电阻 VIC =±13 V, RS = 50Ω 94 110 D B KSVS电源电压抑制比( ΔVCC/ΔVIO) VCC ±=±3 V至±18 V, RS = 50Ω 7 32 μV/ V PD功
PP牌号与熔指大全(PP牌号下)

PP-纤维类型号产地熔指g/10min特性及用途T30S 西太/有机抚顺/天津华北/大庆齐鲁/青岛茂名/兰化2.5-3.5用于膜丝、纺织膜丝线、地毯背衬T30S辽宁华锦 3.2编制带丝,用于包装,地毯背衬,人工草坪,捆扎绳,包装绳及其他应用C30S辽宁华锦6流延膜生产工艺生产的编织带丝,捆扎绳,绳,单丝用于刷子和扫帚,针织土工布F401盘锦/兰港 2.5-3用于编织袋、打包带,及一些小制品PP022有机/前郭3用于膜丝、纺织膜丝线及地毯背衬S1003燕山/赛科/独山子3.2用于窄带、扁丝5004辽阳石化 2.6-4.4适用于切制薄膜(扁丝)、单丝、复丝HP550J中海壳牌 3.2曾用名T30S;可用于拉丝、纤维及注塑成型F501韩国晓星兰化/兰港3用于编织袋、包装用绳,作业安全性H0305G印度信诚3用于编织袋、包装用绳H5300韩国湖南 3.5用于包装袋、绳子5014大韩油化 3.5用于编织袋、包装用绳S30S辽宁华锦 1.8编制带丝,流延膜或管膜生产工艺,用于包装,工业纤维,捆扎绳、包装绳、单丝应用Y-130韩国湖南 3.5纱纤维级、平纱级,高韧性、高伸张率;用于包装袋、捆扎带、纤维纱、草坪等6531M马来大腾2用于绳、带、纺织袋H730F韩国SK 3.5用于绳、带、纺织袋、防水布SY130韩国湖南 3.5高韧性、高伸长率;用于包装带、捆扎带H430韩国LG 3.5用于膜丝、编织膜丝线及地毯背衬等3365美国3高韧性、高伸长率;用于包装带、捆扎带HP450J韩国大林3用于膜丝、编织膜丝线及地毯背衬等HP502N中海壳牌12曾用名F30S,用于纤维、地毯等HP550R中海壳牌25曾用名Z30S,用于纤维、连续纤维、非连续纤维等Z30S大连西太22-27低速纺短纤维,用于BCF-CF复丝Z30S大连有机11-20纺丝类Z30S华北一炼25适用于中速到高速纺生产的细旦膨化丝,连续丝、长丝Z30S抚顺乙烯20均聚物,用于长丝、丙纶、丙纶短纤维.Z30S 新彊独山子22-28均聚物,用于长丝、丙纶、丙纶短纤维.Z30S辽宁华锦25低旦尼尔BCF、CF和短纤,中高纺速生产线上生产的BCF丝用于地毯,CF丝用于捆扎绳,扶手,包装等Z21S辽宁华锦25用于高速生产线生产的窄份资料分布牌号,低旦尼尔,纺粘型无纺布,用于尿布,医用卫生品,也可用于优质纱和BCF丝。
SOP-MW-007 车床操作说明

创亿欣
精密电子股份有限公司
车床
操作说明
文件编号SOP-MW-007日期2008/02/20
页数1/1 版次A2
1.打开机器电源,检查各转动部分有无异常;
2.准备待加工的工件及图纸,依加工要求选择适合的刀具;
3.安装刀具并确认锁紧;
4.用适合的方法装夹工件:一般圆形工件用三爪卡盘,方形工件用四爪卡盘,加工较长
的工件时,要使用尾架,中心架及跟刀架装夹,加工长工件转速不能太快;
5.装夹完成时,装夹用扳手要随手拿下;
6.按加工要求调整机床转速及进给速度;
7.开动主轴,待主轴接近设定转速时,扳动进给手柄正式加工;
8.加工螺纹时,按螺距要求调整挂轮;
9.开动主轴,用螺纹开合手柄加工,左手操纵螺纹开合手柄,右手操纵中拖板;
10.打开冷却水,调整好冲水位置;
11.加工过程中,要测量尺寸是否达到预定要求,以及早发现设定错误并修正;
12.加工到要求位置时,松开进给手柄或螺纹开合手柄;
13.加工中心孔或中心孔攻牙时,诮将钻头或丝攻装在尾架上,待主轴接近设定转速时,
推动尾架进给加工;
14.待主轴完全停止时,移开刀具,测量尺寸;
15.加工铜件时,切屑要用另外的容器收集,确保与铁屑分开,以方便废料处理;
16.作业完成,清洁工作台面,下班前断开电源,清洁设备。
核准:制定:陈锦柏2011-10-20。
NEO-7M中文版
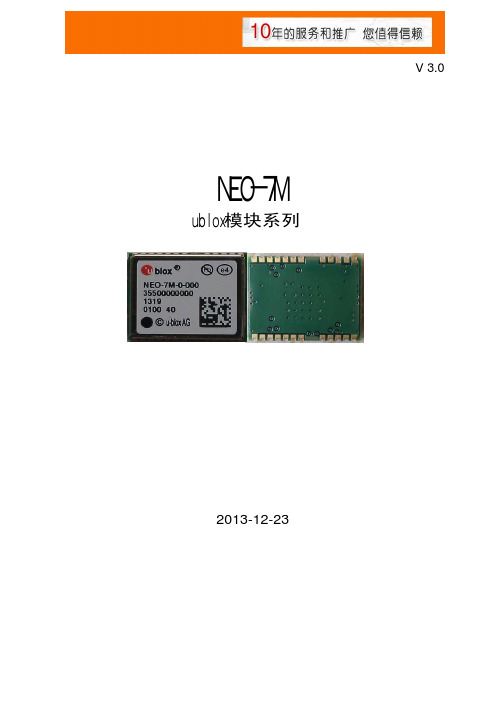
NEO-7Mublox模块系列V 3.0深圳市鹏城润发电子有限公司2013-12-23目 录1.产品描述.................................................................................................................-2- 2.产品型号编码规则..................................................................................................-3- 3.产品用应用范围及优点...........................................................................................-4- 4.技术特性................................................................................................................-5- 5.模块工作原理.........................................................................................................-6- 6.模块信号测试图和模块RF 射频图............................................................................-7- 6.1模块信号测试图...........................................................................................-7- 6.2模块RF 射频图...........................................................................................-7- 7.模块管脚分配........................................................................................................-8- 8.推荐应用电路.......................................................................................................-10- 9.模块设计注意事项................................................................................................-11- 10.模块焊盘尺寸.....................................................................................................-12- 11.NMEA 0183 协议. (13)11.1 GGA................................................................................................-14- 11.2 GLL.................................................................................................-15- 11.3 GSA ...............................................................................................-15- 11.4 GSV................................................................................................-16- 11.5 RMC...............................................................................................-17- 11.6 VTG. (17)12.经纬度转换....................................................................................................-18- 13-19- 14.产品包装.......................................................................................................-20- .SMT 温度曲线图.. (21)15.贴片注意事项................................................................................................NEO-7MGPS 产品名称1. 产品描述:模块是一个低功耗主芯片的超小外型GPS 接收模组,该产品采用了新一代U-blox 芯片,超高灵敏度,具备全方位功能,能满足专业定位的严格要求。
WASP7使用手册

W a t e r Q u a l i t y A n a l y s i s S i m u l a t i o n P r o g r a m(W A S P)V e r s i o n7.1Watershed and Water Quality ModelingTechnical Support CenterUS EPAOffice of Research DevelopmentNational Exposure Research LaboratoryEcosystems Research DivisionAthens, GATable of Contents INTRODUCTION (1)USING WASP6 INPUT FILES WITH WASP7 (1)S YSTEM D ETERMINATION (1)B OUNDARY C ONDITION U PDATE (2)USER INTERFACE ENHANCEMENTS (2)G ENERAL L AYOUT (2)Restart File (3)Hydrodynamic Linkage File (4)Internal Kinematic Wave Flow Routing (4)External Hydrodynamic Linkage (6)Hydraulic Geometry (8)Solution Technique (11)S EGMENT I NFORMATION (12)Length (12)Width (12)Slope (12)Segment Roughness (13)T IME S ERIES I MPORT/SQL (13)Sources (15)Defer Import (21)Import (23)Execute Queries (24)WASP N ETWORK T OOL (25)Control File (26)Segment Information File (27)Flow File (27)Load File (27)Boundary File (27)O UTPUT C ONTROL D ATABASE (27)Comma Separated Value File (28)UTILITY PROGRAMS (28)HYDROLINK (29)HYDROLINK_BMD (29)EUTROPHICATION MODEL ENHANCEMENTS (30)O VERVIEW (30)BOD (30)B ENTHIC A LGAE (31)S OLIDS (31)L IGHT E XTINCTION (31)Background (32)Algal (32)Solids (32)DOC (32)D ETRITUS (33)R EAERATION (33)Dam Reaeration (33)Table of FiguresFigure 1 WASP 7 State Variable Selection (2)Figure 2 Interface Main Screen (3)Figure 3 WASP Simulation Parameters Screen (4)Figure 4 Link-Node Hydrodynamic Linkage with WASP (7)Figure 5 WASP Segment Definition Screen for Kinematic Wave Function (12)Figure 6 Time Series Import from External Files (14)Figure 7 Import Time Series Control Screen (15)Figure 8 Time Series External Source Selection Dialog (16)Figure 9 External Worksheet or Database File Selection (17)Figure 10 Example Excel Spreadsheet Example for External Data Source (18)Figure 11 Database Query Grid for Time Series Extraction (19)Figure 12 Time Field Selection (20)Figure 13 Result Field Selection (21)Figure 14 Defer Import Option for Time Series (22)Figure 15 Defer Import Indicator (23)Figure 16 Time Series Import Function Dialog (24)Figure 17 Time Series Conversion from Deferred to Imported (25)Figure 18 WASP Network Import Control File Selection (26)Figure 19 Output Control Screen (28)Table of TablesTable 1 Comparison of Hydraulic Exponents (10)Table 2 Dam Reaeration Water Quality Coefficient (33)Table 3 Dam Reaeration Dam Type Definition (33)IntroductionThe purpose of this document is to provide a brief description of the new features and algorithms available in WASP version 7.1. This release of WASP represents one of the largest sets of improvements in the model over the past 10 years. Enhancements to the eutrophication model have been made to directly support the TMDL program. Major enhancements have been made to the user interface to make it easier for the user to take eternal data and bring it into the model.The user will have to go through a series of steps to use previous versions of WASP 6.x with this new version. It should be noted that the user has the option of leaving WASP6 installed on their computer. Installing WASP7 will not affect this installation, nor will the WASP6 installation affect WASP7.Using WASP6 Input Files with WASP7The WASP user interface stores version information in the WIF files that allows for easy updating of input files when new releases are made. With the release of WASP 7 in the eutrophication model there are additional state variables. The user needs to make decisions on whether to consider and using these new state variables, the user will have to go into two data entry screen to make decisions.System DeterminationWhen the user opens a previous version of a WASP eutrophication input file additional state variables are available to the user. By default these state variables are simulated, in most cases this should not cause a problem but does increase the computational burden. For additional information on the new state variables available in WASP 7 see Eutrophication Model Enhancements section. If the user is not interested in using the new state variables, the systems should be set to Bypassed.Figure 1 WASP 7 State Variable SelectionBoundary Condition UpdateBecause there are additional state variables in WASP 7, when a previous version of WASP is read into the program there will not be boundary information specified for the new state variables. Before the input file will work correctly in WASP 7 boundary information must be specified. To do this you must open the flow screen, because WASP determines all boundary segments from the flow, exchange screens or the hydrodynamic linkage file. You do not have to change any information in these screens, just open the screens and then click Okay. WASP will create boundary condition information for all of the new state variables setting the concentration to zero.User Interface EnhancementsWhile the general layout of the user interface has not changed very much, there are some subtle changes that the user needs to be made aware. Any new functionality that has been added to the interface will be documented in other sections of the release notes.In previous versions of WASP the time was entered with AM/PM designation. Because of problems with the Microsoft language packs translating the AM/PM time designation the time fields in WASP have been converted to military time (00:00 to 24:00). Previously created WASP input files will be converted and displayed in military time automatically once brought into WASP 7.General LayoutThe general layout has not changed much since the previous version; a couple of icons have been changed and/or moved. The icon used to load the graphical post processor hasbeen moved out to the right away from the execute button. This was done because users were selecting execute instead of post process and the model would start to run over writing the output files.The Validate input file icon has been removed; it was very difficult to continue coding of this function keeping track of updates in the model and the interface. More effort was placed in the model code to track most of the input errors that can cause the model to crash. Basically, there is only one input error that we are aware of that will cause the model to crash. When developing input time series for the model, whether it is timestep, print interval, loads, boundaries, flows, and environmental time functions the user must make sure the first time entry exactly matches the start date and time of the model simulation as specified on the parameterization screen.Figure 2 Interface Main ScreenRestart FileThe methods used by WASP to read and create restart files have changed substantially in this version. In previous versions the user would have selected Create Restart File, for WASP to write the final conditions of the simulation to an output file. This is true for the current version as well. If the user wants to restart a simulation with the final conditions of previous simulation this radio must be set (Figure 3). At the end of the WASP simulation a restart file with the same name as the WIF except with the extension *.RST will be saved. With the current release of WASP if the user wants to use a restart file they simple click on the Load Restart File button, this will allow the user to browse to whatever restart file they want to use. Once the file is selected and the user clicks on theOkay button, the restart file is opened up and segment volumes and state variable initial conditions are reset to the values in the user selected *.RST file.Figure 3 WASP Simulation Parameters ScreenHydrodynamic Linkage FileIf the user selects a hydrodynamic linkage file option, WASP expects the file to be previously created and in the appropriate format. WASP7 only recognizes one file format for hydrodynamic linkage files. There is a utility program (HYDROLINK.EXE) that should be used to convert previously created hydrodynamic linkage files to the appropriate file format. See Section HYDROLINK for more details on the new file format.Internal Kinematic Wave Flow RoutingFor one-dimensional, branching streams or rivers, kinematic wave flow routing is a simple but realistic option to drive advective transport. The kinematic wave equation calculates flow wave propagation and resulting variations in flows, volumes, depths, and velocities throughout a stream network. This well-known equation is a solution of the one-dimensional continuity equation and a simplified form of the momentum equation that considers the effects of gravity and friction:Continuity equation:Momentum equation:where Q is volumetric flow, m3/sec, A is cross-sectional area, m2, g is acceleration of gravity, m/sec2, S0 is the bottom slope, and S f is the friction slope. Manning’s equation iswhere n is the Manning friction factor, v is water velocity, m/sec, and R is hydraulic radius, m. From the simplified momentum equation, S0 can be equated to S f. Hydraulic radius can be expressed as cross-sectional area divided by width, B, in m. Substituting these into the Manning’s equation and rearranging terms gives flow as a function of bottom slope, cross-sectional area, and width:Substituting this expression into the continuity equation and differentiating A with respect to time gives the kinematic wave differential equation:WASP7 solves this kinematic wave equation for each segment in a stream network using a 4-step Runga-Kutta numerical technique.To implement kinematic wave routing, the user must select this option in the Data Input (gears) screen. In the Flows screen, the upstream inflow, each tributary inflow, and any flow withdrawals must be completely described by continuity path functions and inflow time functions as discussed in the previous section. In the Segments screen, the user must specify channel length (m), width (m), minimum depth (m), slope (m/m), and Manning’s friction factor for each segment in the network.External Hydrodynamic LinkageRealistic simulations of unsteady transport in rivers, reservoirs, and estuaries can be accomplished by linking WASP7 to a compatible hydrodynamic simulation. This linkage is accomplished through an external “hyd” file chosen by the user at simulation time. The hydrodynamic file contains segment volumes at the beginning of each time step, and average segment interfacial flows during each time step. WASP7 uses the interfacial flows to calculate mass transport, and the volumes to calculate constituent concentrations. Segment depths and velocities may also be contained in the hydrodynamic file for use in calculating reaeration and volatilization rates.Before using hydrodynamic linkage files with WASP, a compatible hydrodynamic model must be set up for the water body and run successfully, creating a hydrodynamic linkage file with the extension of *.hyd. This is an important step in the development of the WASP input file because the hydrodynamic linkage file contains all necessaray network and flow information.When Hydrodynamic Linkage is selected in the Data Set Parameters screen, the user cannot provide any additional surface flow information. When you are ready to begin the development of a WASP input deck, simply open the hydrodynamic linkage file from within the data preprocessor. The hydrodynamic linkage dialog box allows the user to browse and select a hydrodynamic linkage file. The data preprocessor will open the hydrodynamic interface file and extract the number of segments, the starting and ending time. The data processor will also determine the set of boundary segments (segments that receive flow from outside the model network) and set the boundary concentrations to 1.0 mg/L. Once a hydrodynamic linkage file is selected in the data preprocessor, WASP has enough information to execute a simple test run with no loads or kinetics enabled. This step is recommended to test the network and transport integrity. If the simulation is run for a sufficient duration, concentrations should approach 1.0 mg/L throughout the network. If you are getting a number other than 1 mg/L, you may have to use a different time step in the hydrodynamic model. This is especially true if the concentrations are oscillating between large and small numbers, a clear indication of numerical instability. WASP has the ability to get hydrodynamic information from a host of hydrodynamic models. If a hydrodynamic model does not support the WASP linkage it is relativestraightforward to create a hydrodynamic linkage file (see Appendix X for file format). The hydrodynamic models that currently support the WASP7.x file format are: EFDC (three dimensions), DYNHYD (one dimension branching), RIVMOD (one dimension no branching, CE-QUAL-RIV1 (one dimension branching), SWMM/Transport (one dimension branching, SWMM/Extran (one dimension branching)The first step in the hydrodynamic linkage is to develop a hydrodynamic calculational network that is compatible with the WASP7 network. The easiest linkage is with link-node hydrodynamic models that run on equivalent spatial networks. An example is given in Figure 4. Note that each WASP7 segment corresponds exactly to a hydrodynamic volume element, or node. Each WASP7 segment interface corresponds exactly to a hydrodynamic link, denoted in the figure with a connecting line.Figure 4 Link-Node Hydrodynamic Linkage with WASPThe hydrodynamic model calculates flow through the links and volume within the nodes. Within the hydrodynamic model, the user must specify the water quality time step, or the number of hydrodynamic time steps per water quality time step. The hydrodynamic model must then write out node volumes at the beginning of each water quality time step, and average link flows during each water quality time step. The user in the hydrodynamic model or in an external interface program must supply a network map such as the one in Figure 4. This map is used to create a hydrodynamic file that WASP7 can read and interpret. The hydrodynamic model DYNHYD5, supplied with WASP7, contains subroutines to produce a proper WASP7 hydrodynamic file.It is important to note that the hydrodynamic model has additional nodes outside of the WASP7 network. These additional nodes correspond to WASP7 boundaries, denoted by nominal segment number "0." These extra hydrodynamic nodes are necessary because while flows are calculated only within the hydrodynamic network, WASP7 requires boundary flows from outside its network.Multidimensional hydrodynamic models can also be linked to WASP7. A compatible two-dimensional network is illustrated in Figure 4. For the beginning of each water quality time step, the volumes within a WASP7 segment must be summed and written to the hydrodynamic file. For the duration of each water quality time step, flows across the WASP7 segment boundaries must be averaged. All of the averaged flows across a boundary must then be summed and written to the hydrodynamic file. Again, it is important to note the presence of hydrodynamic elements outside the WASP7 network generating boundary flows. The preprocessor will determine the boundary segments from reading the hydrodynamic linkage file. The user will then be able to enter concentrations associated with each of these boundaries.To implement the hydrodynamic linkage, the user must specify Hydrodynamic Linkage and select a previously created hydrodynamic linkage file. Following the choice of a proper file, the hydrodynamic file will reset the simulation time step. The time steps read in will be ignored but must still be entered, as this is where the user specifies the ending time for the simulation. Similarly, water column segment volumes will be read from the hydrodynamic file. The user must nevertheless enter volumes for each segment in the usual location. During the simulation, flows and volumes are read every time step. Hydraulic GeometryA good description of segment geometry as a function of flow conditions can be important in properly using WASP7 to simulate rivers. For flow option 3, velocity and depth are computed within the hydrodynamic model, and are read by WASP7. For flow options 1 and 2, a set of user-specified hydraulic discharge coefficients can be entered in that defines the relationship between velocity, depth, and stream flow in the various segments. This method, described below, follows the implementation in QUAL2E (Brown and Barnwell, 1987). In WASP7, these segment velocities and depths are only used for calculations of reaeration and volatilization rates; they are not used in the transport scheme.Discharge coefficients giving depth and velocity from stream flow are based on empirical observations of the stream flow relationship with velocity and depth (Leopold and Maddox, 1953). It is important to note that these coefficients are only important when calculating reaeration or volatilization. The velocity calculations are not used in time of travel, and will not affect the simulation of tracers. The equations relate velocity, channel width, and depth to stream flow through power functions:Equation 1 Hydraulic Coefficients Q a = V bEquation 2Q c = D bEquation 3Q e = B fwhere:D is average depth, mB is average width, ma, b, c, d, e, and f are empirical coefficients or exponentsGiven that area is a function of average width (B) and average depth (D),Equation 4B D =Ait is clear from continuity that:Equation 5Q e) c (a = )Q (e )Q (c )Q (a = B D U = A U = Q f + d + b f d b •••••••and, therefore, the following relationships hold:Equation 61 = e c aEquation 71 = f + d + bWASP7 only requires specification of the relationships for velocity, Equation 1, anddepth, Equation 2; the coefficients for Equation 3 are implicitly specified by Equation 6and Equation 7.These options can be put into perspective by noting that, for a given specific channelcross-section, the coefficients (a, c, e) and exponents (b, d, f) can be derived fromManning’s equation. For example, if a channel of rectangular cross-section is assumed, then width (B) is not a function of stream flow (Q), the exponent (f) is zero (0.00) and the coefficient (e) is the width of the rectangular channel (B). By noting that hydraulic radius (R) is approximately equal to depth (D) for wide streams and that A = D B, the discharge coefficients for rectangular cross sections can be shown to be 0.4 for velocity and 0.6 for width.Leopold et al. (1964) have noted that stream channels in humid regions tend towards a rectangular cross-section because cohesive soils promote steep side slopes whereas noncohesive soils encourage shallow sloped, almost undefined banks.Table 1 Comparison of Hydraulic ExponentsChannel Cross-Section Exponent for(b) VelocityExponentFor (d)DepthExponent for (f)WidthRectangular 0.400.600.00Average of 158 U.S. Gaging Stations 0.43 0.45 0.12Average of 10 Gaging Stations on RhineRiver 0.430.410.13Ephemeral Streams in Semiarid U.S. 0.34 0.36 0.29Table 1 compares hydraulic exponents for a rectangular channel with data reported byLeopold et al. (1964). Note that the average velocity exponent is relatively constant forall channel cross sections. The major variation occurs as a decrease in the depth exponentand concomitant increase in the width exponent as channel cross-sections change fromthe steep side slopes characteristic of cohesive soils to the shallow slopes of arid regionswith noncohesive soils.For bodies of water such as ponds, lakes, and reservoirs, velocity and depth may not be afunction of flow. For these cases, both the velocity and depth exponents (b and d) can bechosen to be zero (0.00). Because Q to the zero power is equal to one (1.0), thecoefficients a and c must be the velocity and depth, i.e.,IF b = 0.0 THEN a = V, andIF d = 0.0 THEN c = D.When the depth exponent is zero, WASP7 will adjust segment depths with segmentvolumes assuming rectangular sides.For site-specific river or stream simulations, hydraulic coefficients and exponents mustbe estimated. Brown and Barnwell (1987) recommended estimating the exponents (b andd) and then calibrating the coefficients (a and c) to observed velocity and depth. Theexponents may be chosen based on observations of channel shape noted in areconnaissance survey. If cross sections are largely rectangular with vertical banks, thefirst set of exponents shown should be useful. If channels have steep banks typical ofareas with cohesive soils, then the second set of exponents is appropriate. If the stream is in an arid region with typically noncohesive soils and shallow sloping banks, then the last set of exponents is recommended.The key property of the channel that should be noted in a reconnaissance survey is the condition of the bank slopes or the extent to which width would increase with increasing stream flow. Clearly the bank slopes and material in contact with the stream flow at the flow rate(s) of interest are the main characteristics to note in a reconnaissance. This gives general guidance but it should be noted that values are derived for bankful flows. Even in streams with vertical banks, the low flows may be in contact with a sand bed having shallow sloped, almost nonexistent banks more representative of ephemeral streams in semi-arid areas.With the release of WASP 7, the model is capable of internally calculating hydrodynamics in that travel time and wave propagation is calculated in the model using the kinematic wave formulation. This is a significant improvement to the transport component of WASP when it comes to one dimensional networks. The model uses channel slope, width, depth, flow and roughness to calculate water movement. For most stream and small river systems (one dimensional) the kinematic wave formulation can be used instead of external linkage to hydrodynamic models such as EPD-RIV1 and DYNHYD.The assumptions for the kinematic wave formulation is one dimensional flow, the flows may diverge (branch) and then re-join. The model calculates flow wave propagation and resulting variable flows, volumes, depths, and velocities throughout the network. The default is a rectangular channel shape unless user specifies hydraulic coefficients in the depth and velocity multiplier and exponents in the segment definition screen. The user can specify time-variable upstream and tributary inflows. These inflows can come from USGS gauges, user estimations or watershed models. The user would be responsible for providing the following segment information to parameter the segment (See Segment Information Figure 5):•length (m), width (m), initial depth (m)•hydraulic exponents set to 0•bottom slope (m/m)•Manning’s roughness coefficientSolution TechniqueThe user now has the ability to select the model solution technique to be used during the simulation. Currently there are only 2 solution techniques that can be selected: 1) Euler – which is the traditional solution technique that has been in WASP since its inception, 2) COSMIC Flux Limiting – this solution technique is typically used when WASP is linked to multi-dimensional hydrodynamic models like EFDC.Segment InformationThe segment information screen has been modified to allow the user to put information into the model that is required by the kinematic wave formulation. It should be noted that if the kinematic wave option is not being used this information is not needed. The new information needed by the kinematic wave formulation is: Segment Length, Segment Width, Segment Slope, and Segment Roughness. Whether or not if the kinematic wave option is being used, if the user does not specify a segment volume, but segment length, width and depth are specified WASP will calculate the volume.Figure 5 WASP Segment Definition Screen for Kinematic Wave FunctionA bug has been fixed in pasting segment information into the segment screen; the preprocessor will not longer insert the blank row of segment information at the bottom. If the user wants to paste segment descriptions/names, and these descriptions have spaces the user should place the segment description in quotes (i.e. “I 20 Bridge”).LengthThe segment length describes the bottom length of the segment from the start and end of the segment. This information should be entered in meters.WidthThe segment width describes the average segment width across the whole length of the segment. This information should be entered in meters.SlopeThe segment slope describes the average slope down the whole length of the segment. This is a dimensionless term which should be calculated as meters/meters.Segment RoughnessThe segment bottom roughness describes the Manning’s n coefficient for the segment being described.Time Series Import/SQLAnother major enhancement to the user interface is to allow the user to query/retrieve information from external data sources. These external data sources can be things such as database files (Paradox, Dbase, Access, etc.) or spreadsheet files (Excel). The user interface allows the user to attach to these external files and bring the time series data into the model without using the conventional cut and paste methods. Furthermore, using a graphical user interface the user has the ability to develop SQL queries that are used to subset the external file to get to the particular data that is needed for the time series being defined in WASP. If the user is working with very large datasets, the user can set a radio button that will cause the interface to execute the query steps one by one “drilling” or sub-setting the data make it more efficient to work with. Figure 3 illustrates a typically time series entry screen (WASP Boundary Conditions), to initiate an import the user needs to click on the Import Button.Figure 6 Time Series Import from External FilesOnce the user selects import time series a data query form is presented (Figure 7). The user can select various file types in which to import data. The user should use the browse button to open the file selection dialog box, the path and filename is stored in the WIF file once selected and saved.Figure 7 Import Time Series Control ScreenSourcesFrom the file dialog window the user will be presented with a typical windows file selection interface. The user can set the file type filter by using the drop down menu at the bottom of the dialog box. This also specifies the types of external data file types available to the user. A list of the file types are described below:1.DBF – this is a conventional dBase file format. dBase files are standard withESRI products and many third party software packages support this file format.Spreadsheet programs like Excel, Lotus 123 and Quattro have the ability to create these files.2.XLS – this is a standard Microsoft Excel spreadsheet file. WASP can handle aspreadsheet with many sheets associated with the data. It is best to arrange the data that you want to pull into WASP in a columnwise fashion.3.MDB – this is a standard Microsoft Access database file. WASP can handleAccess database files that have multiple tables within the MDB. The user will have the ability to select which table to extract data.4.DB – this is a standard Corel Paradox database file format. This is the same filetype that the graphical post processor MOVEM reads to obtain observed data.。
pp7公差与测量技术

任务一 滚动轴的概述
图7-1 小齿轮轴部分装配图
任务一 孔和轴的极限与配合
(3)轴承的游隙为基本组径向游隙。
任务二
滚动轴承配合件公差及合理选用
(5)轴为实心或厚壁钢制轴。
(6)外壳为铸钢或铸铁。
任务二
滚动轴承配合件公差及合理选用
7-4 轴承外圈轴与外壳孔配合常用工程带关系图
注:Δdmp表示轴承外圈单一平面平均外径的偏差
任务二
滚动轴承配合件公差及合理选用
二、滚动轴承的配合选择
公差带。
任务二
滚动轴承配合件公差及合理选用
7-4 轴承内圈孔与轴颈配合的常用公差带
注:Δdmp表示轴承内圈单一平面平均内孔直径的偏差。
任务二
滚动轴承配合件公差及合理选用
该公差带适用场合
(1)轴承外形尺寸符合GB/T 273.3—1999《滚动轴承 向心 轴承 外形尺寸总方案》的规定。
(2)轴承的精度等级为0级和6(6x)级。
轴承的正确运转很大程度上取决于轴承与轴、孔的配合质量 。为了使滚动轴承具有较高的定心精度,通常轴承内外圈的配合
都偏紧,但为了防止因内圈的弹性胀大和外圈的收缩导致轴承内
部间隙变小,甚至完全消除,并产生过盈,影响轴承正常运转。 同时也为了避免内外圈材料产生较大的应力,致使轴承使用寿命 降低,所以选择时不仅要遵循轴承与轴颈、外壳孔正确配合的一
任务一 滚动轴的概述
二、滚动轴承的公差等级及应用
1.滚动轴承的公差等级
Taranis Q X7 用户手册说明书
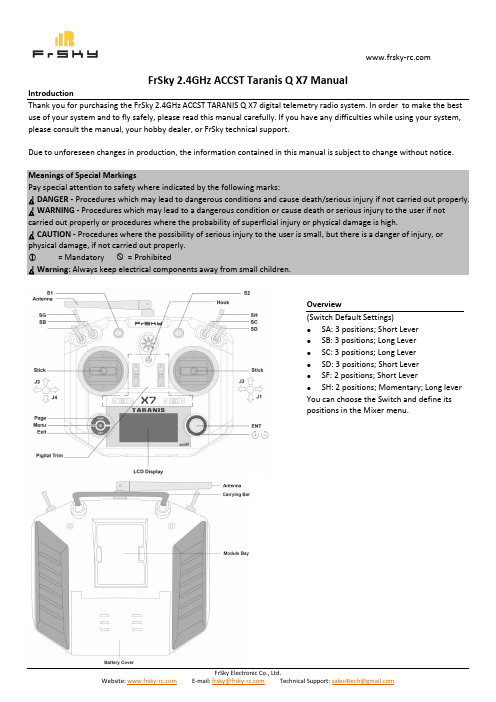
FrSky 2.4GHz ACCST Taranis Q X7 ManualIntroductionThank you for purchasing the FrSky 2.4GHz ACCST TARANIS Q X7 digital telemetry radio system. In order to make the best use of your system and to fly safely, please read this manual carefully. If you have any difficulties while using your system, please consult the manual, your hobby dealer, or FrSky technical support.Due to unforeseen changes in production, the information contained in this manual is subject to change without notice.Meanings of Special MarkingsPay special attention to safety where indicated by the following marks:△!DANGER - Procedures which may lead to dangerous conditions and cause death/serious injury if not carried out properly. △!WARNING - Procedures which may lead to a dangerous condition or cause death or serious injury to the user if not carried out properly or procedures where the probability of superficial injury or physical damage is high.△!CAUTION - Procedures where the possibility of serious injury to the user is small, but there is a danger of injury, or physical damage, if not carried out properly. = Mandatory = Prohibited△!Warning: Always keep electrical components away from small children.Overview(Switch Default Settings) ● SA: 3 positions; Short Lever ● SB: 3 positions; Long Lever ● SC: 3 positions; Long Lever ● SD: 3 positions; Short Lever ● SF: 2 positions; Short Lever ● SH: 2 positions; Momentary; Long lever You can choose the Switch and define its positions in the Mixer menu.SpecificationsModel Name: Taranis Q X7Operating Voltage Range: 6~15V (2S, 3S Lipos are acceptable)Operating Current: 210mA maximum (both RF module and backlit are on)Operating Temperature: -10~45℃Backlight LCD Screen: 128*64 outdoor readable LCDModel Memories: 60 (extendable by SD card)Compatibility: FrSky X series, D series and V8-II series receivers (plus other receivers if an external module is used) Features● Quad Ball Bearing Gimbals● Receiver Match● Audio Speech Outputs (values, alarms, settings, etc.)● Antenna Status Detection and Adjustment● Real-time Flight Data Logging ● Receiver Signal Strength Indicator (RSSI) Alerts ● Super Low Latency● Smart Port Supported● Vibration Alerts△! Cautions on handling antenna✠Do not touch the antenna during operation. Doing so could interfere with transmission, causing a crash.✠Do not carry the transmitter by the antenna. The antenna wire could break and prevent transmission.✠Do not pull the antenna forcefully. The antenna wire could break and prevent transmission.Rotating AntennaThe antenna can be rotated 180 degrees and angled 90degrees. Forcing the antenna further than this can causedamage to the antenna. The antenna is not removable.Angle adjustment of the antennaThe antenna rotation and angle can be adjusted. Theantenna features week radio signal in the forward directionand strong radio signal in the sideways directions. Adjust theantenna angle to match your flying style.△! Notes and Warnings for Battery (Not provided)Model Setup for Taranis Q X7 Internal RF ModuleThe internal RF module of FrSky Taranis Q X7 is newly developed by FrSky under the name of XJT.Enter the MODEL SETUP menu (for details, refer to the Guide included on the SD card, or download it from FrSky website).Step 1: Set the Mode for Taranis Q X7 Internal RFRefer to the table below and set the Taranis Q X7 to the mode corresponding to your receiver (D8, D16 or LR12 ).Mode of Taranis Q X7 Compatible ReceiversNumber of Output servoChannels D8 V8-II series in D mode (V8FR-II, V8R7-II, V8R4-II, VD5M, etc.) D series (D8R-II plus, D8R-XP, D6FR, D4R-II, etc.)8D16 X series (X8R, etc.) Up to 16 LR12 L series (L9R, etc.) 12Note: older V8 receivers are not supported by the internal module but can be used with an external DJT module in V8 mode.Step 2: Set the Channel RangeThe internal RF module of Taranis Q X7 supports up to 16 output servo channels. The channel range is configurable, and needs double check before use.Step 3: Set the Receiver NumberWhen you create a new model, the system will assign you a receiver number automatically, but this can be easily changed. The range of the receiver number is 00-63, with the default number being 01 (use 00 is not recommended). Once the receiver is set to the desired number and is bound to the Taranis Q X7, the bind procedure will not need to be repeated✠ Please connect a battery in the battery compartment before use. ✠ The voltage range should be DC 6-15V. ✠ Be careful not to drop the battery.✠ Don't pull the battery wires as this could produce, short-circuits and cause the battery to explode.✠ Do not remove the battery from the TARANIS Q X7 transmitter while the voltage warning is blinking as this could cause iinternal settings and memories to be destroyed.✠ Do not use the transmitter if a “Backup Error” warning occurs. Battery Connector Polarity Ensure that the battery connector polarity is correct when connecting batteries into the battery compartment, otherwise the Taranis Q X7 might not be powered on.unless the receiver number is changed, In this case, either set the receiver number to the previous one, repeat the bind procedure.Step 4: BindBind refers to Taranis Q X7 binding mode. M ove the cursor to “Bind”, press ENTER button, the cursor will flash and the speaker will beep to remind you that the RF module has entered the bind mode. Then put your receiver into binding mode and finish the bind procedure (refer to the receiver’s manual for details).Press Enter or EXIT to exit.Step 5: Set Failsafe modeThere are 4 failsafe modes: No Pulse, Hold, Custom, Receiver (this mode only used above opentx-v2.0.0 firmware).● No Pulse: on loss of signal the receiver produces no pulses on any channel. To use this type, select it in the menu and wait 9 seconds for the failsafe to take effect.● Hold: the receiver continues to output the last positions before signal was lost. To use this type, select it in the menu and wait 9 seconds for the failsafe to take effect.● Custom: pre-set to required positions on lost signal. Move the cursor to “Set” and press ENTER, you will see FAILSAFE SETTING screen below. Move the cursor to the channel you want to set failsafe on, and press ENTER. When moving the corresponding sticks or switches, you will see the channel bar moving. Move the channel bar to the place you want for failsafe and long press ENTER to finish the setting. Wait 9 seconds before the failsafe takes effect.●Receiver: set the failsafe on the receiver(see receiver instructions) in D16 or LR12 mode, select it in the menu and wait 9 seconds for the failsafe to take effect.Notice:The above instructions do not apply to D-series receivers, which require the internal RF module of Taranis Q X7 to be in D8 mode. For these receivers, failsafe must be set on the receiver side (see receiver instructions)●SBUS port always outputs, No Pulse could not perform properly on it. Set “Hold” or “Custom” for SBUS port.Step 6: RangeRange refers to Taranis Q X7 range check mode. A pre-flight range check should be done before each flying session. Move the cursor to “Range” and press ENTER. In range check mode, t he effective distance will be decreased to 1/30. Press Enter or EXIT to exit.Model Setup for Taranis Q X7 External RF ModuleThe external RF module can be powered on or off by software. The setup process is the same as that for the internal RF . If you use other brand RF module than FrSky, please choose PPM mode.CEThe product may be used freely in these countries: Germany, UK, Italy, Spain, Belgium, Netherlands, Portugal, Greece, Ireland, Denmark, Luxembourg, Austria, Finland, Sweden, Norway and Iceland.France: the law permits the emission band 2400 to 2483.5 MHz with the limitation of transmission power of 100 mW (reduced to 10 mW between 2454 and 2483.5 MHz for outdoor flying).FCC Statement§ 15.19 Labelling requirements.This device complies with part 15 of the FCC Rules. Operation is subject to the following two conditions: (1) This device may not cause harmful interference, and (2) this device must accept any interference received, including interference that may cause undesired operation.§ 15.21 Information to user.Any Changes or modifications not expressly approved by the party responsible for compliance could void the user's authority to operate the equipment.§ 15.105 Information to the user.Note: This equipment has been tested and found to comply with the limits for a Class B digital device, pursuantto part 15 of the FCC Rules. These limits are designed to provide reasonable protection against harmfulinterference in a residential installation. This equipment generates uses and can radiate radio frequency energy and, if not installed and used in accordance with the instructions, may cause harmful interference to radiocommunications. However, there is no guarantee that interference will not occur in a particular installation. If this equipment does cause harmful interference to radio or television reception, which can be determined by turning the equipment off and on, the user is encouraged to try to correct the interference by one or more of the following measures:-Reorient or relocate the receiving antenna.-Increase the separation between the equipment and receiver.-Connect the equipment into an outlet on a circuit different from that to which the receiver is connected. -Consult the dealer or an experienced radio/TV technician for help.* RF warning for Portable device:The device has been evaluated to meet general RF exposure requirement. The device can be used in portable exposure condition without restriction.FLYING SAFETY△! Warning: To ensure the safety of yourself and others, please observe the following precautions. Have regular maintenance performed . Although your TARANIS Q X7 protects the model memories with non-volatile EEPROM memory (which does not require periodic replacement) and of a battery, it still should have regular check-ups for wear and tear. We recommend sending your system to your FrSky Service Center annually during your non-flying-season for a complete check-up and service. Always pay partic ular attention to the flying field’s rules , as well as the presence and location of spectators, the wind direction, and any obstacles on the field. Be very careful flying in areas near power lines, tall buildings, or communication facilities as there may be radio interference in their vicinity.At the flying field To prevent possible damage to your radio gear, turn the power switches on and off in the proper sequence: If you do not turn on your system on and off in this order, you may damage your servos or control surfaces, flood your engine, or in the case of electric-powered or gasoline-powered models, the engine may unexpectedly turn on and cause a severe injury. Make sure your transmitter can’t tip it over. If it is knocked over, the throttle stick may be accidentally moved, causing the engine to speed up. Also, damage to your transmitter may occur. In order to maintain complete control of your aircraft it is important that it remains visible at all times. Flyingbehind large objects such as buildings, grain bins, etc. must be avoided. Doing so may interrupt the radio frequency link to the model, resulting in loss of control. ✠ Do not grasp the transmitter's antenna during flight. Doing so may degrade the quality of the radio frequency transmission and could result in loss of control. ✠ As with all radio frequency transmissions, the strongest area of signal transmission is from the sides of the transmitter's antenna. As such, the antenna should not be pointed directly at the model. If your flying style creates this situation, easily move the antenna to correct this situation Before taxiing, be sure to extend the transmitter antenna to its full length.A collapsed antenna will reduce your flying range and cause a loss of control. It is a good idea to avoid pointing the transmitter antenna directly at the model, since the signal is weakest in that direction.1. Pull throttle stick to idle position, or otherwise disarm your motor/engine.2. Turn on the transmitter power and allow your transmitter to reach its home screen.3. Confirm the proper model memory has been selected.4. Turn on your receiver power.5. Test all controls. If a servo operates abnormally, don’t attempt to fly until you determine the cause of theproblem. (For PCM systems only: Test to ensure that the Failsafe settings are correct by waiting at least 2 minutes after adjusting then, turning the transmitter off and confirming the proper surface/throttle movements. Turn the transmitter back on.) 6. Start your engine. 7. Complete a full range check. 8. After flying, bring the throttle stick to idle position, engage any kill switches or otherwise disarm your motor/engine. 9. Turn off receiver power.Don’t fly in the rain! Water or moisture may enter the transmitter through the antenna or stick openings and cause erratic operation or loss of control. If you must fly in wet weather during a contest, be sure to cover your transmitter with a plastic bag or waterproof barrier. Never fly if lightning is expected.Secure Digital (SD) Memory Card Handling InstructionsThe MicroSD card (TF Card) (not provided with Taranis Q X7) can store various files, such as model data, music, sound files, pictures and text. The card is locked when it is pushed in all the way in. To remove the card, push in on the card again, it will pop out allowing you to remove it .If model data generated by a transmitter with a new software version is copied to an one with older software, the transmitter may not operate correctly. Before copying the model data, update the destination transmitter to the new software version.Do not expose the MicroSD card to dirt, moisture, water or fluids of any kind. ✠ Never remove the MicroSD card or turn off power while entering data.✠ Never store the MicroSD card where it may be subject to strong static electricity or magnetic fields. ✠ Do not expose the MicroSD card to direct sunlight, excessive humidity or corrosive environments. ✠Be certain to insert the MicroSD card in the correct direction.Read data from a PCMusic and image files edited by a PC can be transferred onto the MicroSD card and used on your TARANIS Q X7 transmitter. Equipment for reading and writing MicroSD cards is available at most electronics stores.Stored dataThe life of the MicroSD card is limited due to the use of Flash memory. If you have a problem saving or reading data such as picture data after a long period of use you may need to purchase a new MicroSD card. ∙ We are not responsible for, and cannot compensate for any failure to the data stored in the memory card for any reason. Be sure to keep a backup of your models and data in your MicroSD card. ∙ TARANIS Q X7 transmitters and MicroSD cards use non-volatile memory devices so that the data stored is retained, even without a backup battery. Nevertheless, it is good practice to back up the data in the transmitter to the MicroSD card. The clock for the transmitter does depends on the lithium battery, which may need to be replaced occasionally.UpdatesFrSky is continuously adding features and improvements to our radio systems. Updating (via the MicroSD card in Taranis Q X7) is easy and free. To get the most from your new transmitter, please check the download section of the FrSky website , for the latest update firmware and how-to guide.﹡The currently pre-installed firmware of FrSky Taranis Q X7 is modified from OpenTX firmware, improved and well tested by FrSky and the developing union.﹡More information about OpenTX can be found on: .△! Warning Be sure to turn off the power of the transmitter before inserting or removing a MicroSD card. ✠ As the MicroSD card is a precision device, do not use excessive force when inserting.。
运算放大器OP07中文手册

Ric Common Mode Input Resistance 共模输入电阻
-
12 -
GΩ
0
±1
Input Common Mode Voltage Range 输入共模电压范 Vicm 围 0℃ ≤ Tamb ≤ +70℃
±13 ±13
3.5 -
V
12
Common Mode Rejection Ratio (Vi =Vicm min)共模 100
0℃ ≤ Tamb ≤ +70℃ RL =2KΩ ±11
Slew Rate 转换率(RL =2KΩ,CL = 100pF)
-
Gain Bandwidth Product 带宽增益(RL =2KΩ,CL = -
100pF, f = 100kHz)
Supply Current -(no load) 电源电流(无负载) ≤ Tamb ≤ +70℃ VCC = ±3V
VCC Vid Vi Tope r
Supply Voltage 电源电压 Differential Input Voltage 差分输入电压 Input Voltage 输入电压
Operating Temperature 工作温度
Tstg Storage Temperature 贮藏温度
电气特性 虚拟通道连接= ± 15V , Tamb = 25 ℃(除非另有说明)
Value 数值 Unit 单位
±22 ±30 ±22 -40 +105 -65 +150
V V V to ℃
to ℃
Sym Parameter 参数及测试条件
最小 典 最 Unit
bol 符号
Input Offset Voltage 输 入 失 调 电 压 0℃ ≤ Tamb ≤
op07cdr中文资料

op07cdr中⽂资料OUT+OFFSET N2IN?IN+OFFSET N1132861Features3DescriptionThese devices offer low offset and long-term stability ?Low Noiseby means of a low-noise,chopperless,?No External Components Requiredbipolar-input-transistor amplifier circuit.For most ?Replace Chopper Amplifiers at a Lower Cost applications,external components are not required for offset nulling and frequency compensation.The ? Wide Input-Voltage Range:0to ±14V (Typ)true differential input,with a wide input-voltage range ?Wide Supply-Voltage Range:±3V to ±18Vand outstanding common-mode rejection,provides maximum flexibility and performance in high-noise 2Applicationsenvironments and in noninverting applications.Low bias currents and extremely high input impedances ?Wireless Base Station Control Circuits are maintained over the entire temperature range. Optical Network Control Circuits InstrumentationDevice Information (1)Sensors and Controls PART NUMBER PACKAGE (PIN)BODY SIZEPrecision FiltersSO (8) 6.20mm ×5.30mm OP07xSOIC (8) 4.90mm ×3.91mm PDIP (8)9.81mm ×6.35mm(1)For all available packages,see the orderable addendum atthe end of the data sheet.4Simplified SchematicAn IMPORTANT NOTICE at the end of this data sheet addresses availability,warranty,changes,use in safety-critical applications,intellectual property matters and other important disclaimers.PRODUCTION DATA.找电⼦元器件上宇航军⼯OP07C,OP07DSLOS099G–OCTOBER1983–REVISED NOVEMBER2014Table of Contents9.2Functional Block Diagram (7)1Features (1)9.3Feature Description (7)2Applications (1)9.4Device Functional Modes (7)3Description (1)10Application and Implementation (8)4Simplified Schematic (1)10.1General Application (8)5Revision History (2)10.2Typical Application (8)6Pin Functions (3)11Power Supply Recommendations (10)7Specifications (4)12Layout (11)7.1Absolute Maximum Ratings (4)12.1Layout Guidelines (11)7.2Handling Ratings (4)12.2Layout Example (11)7.3Recommended Operating Conditions (4)13Device and Documentation Support (12)7.4Thermal Information (4)13.1Related Links (12)7.5Electrical Characteristics (5)13.2Trademarks (12)7.6Operating Characteristics (6)13.3Electrostatic Discharge Caution (12)8Typical Characteristics (6)13.4Glossary (12)9Detailed Description (7)14Mechanical,Packaging,and Orderable9.1Overview (7)Information (12)5Revision HistoryChanges from Revision F(January2014)to Revision G Page ?Added Applications,Device Information table,Pin Functions table,Handling Ratings table,Thermal Information table,Typical Characteristics,Feature Description section,Device Functional Modes,Application andImplementation section,Power Supply Recommendations section,Layout section,Device and DocumentationSupport section,and Mechanical,Packaging,and Orderable Information section (1)Changes from Revision E(May2004)to Revision F Page ?Deleted Ordering Information table (1)2Submit Documentation Feedback Copyright?1983–2014,Texas Instruments IncorporatedProduct Folder Links:OP07C OP07D12348765OFFSET N1IN?IN+V CC?OFFSET N2V CC+OUT NCD OR P PACKAGE(TOP VIEW)NC ?No internal connectionOP07C,OP07DSLOS099G –OCTOBER 1983–REVISED NOVEMBER 20146Pin FunctionsPin FunctionsPINTYPE DESCRIPTIONNAME NO.IN+3I Noninverting input IN–2I Inverting input NC5—Do not connectOFFSET N11I External input offset voltage adjustment OFFSET N28I External input offset voltage adjustment OUT 6O Output V CC +7—Positive supply V CC –4—Negative supplyCopyright ?1983–2014,Texas Instruments Incorporated Submit Documentation Feedback3Product Folder Links:OP07C OP07DOP07C,OP07DSLOS099G–OCTOBER1983–REVISED NOVEMBER201411Power Supply RecommendationsThe OP07is specified for operation from±3to±18V;many specifications apply from0°C to70°C.CAUTIONSupply voltages larger than±22V can permanently damage the device(see theAbsolute Maximum Ratings).Place0.1-µF bypass capacitors close to the power-supply pins to reduce errors coupling in from noisy or high impedance power supplies.For more detailed information on bypass capacitor placement,refer to the Layout Guidelines.10Submit Documentation Feedback Copyright?1983–2014,Texas Instruments IncorporatedProduct Folder Links:OP07C OP07D。
WM 中文资料

1
输入限幅器/电平自动控制(ALC)..................................... 25 ALC 芯片保护 .......................................................29 噪声门............................................................. 29 输出信号线路....................................................... 30 数字重放(DAC)线路................................................ 30 数字 Hi-Fi DAC 音量(增益)控制.....................................31 DAC 5 路均衡器 .....................................................32 DAC 3D 放大 ........................................................32 音量推动........................................................... 32 5 路图表均衡器 .....................................................34 3D 立体声放大 ......................................................36 模拟输出........................................................... 36 左和右通道混合器................................................... 36 耳机输出(LOUT1 和 ROUT1)..........................................39 扬声器输出(LOUT2 和 ROUT2)........................................41 零交叉间歇时间..................................................... 44 OUT3/OUT4 混合和输出 ...............................................44 输出使能........................................................... 48 过热保护........................................................... 48 未使用的模拟输入/输出.............................................. 48 数字音频接口....................................................... 51 主属和从属操作模式................................................. 51 音频数据模式....................................................... 51 音频接口控制....................................................... 54 环回............................................................... 54 压缩............................................................... 54 音频采样率......................................................... 55 主时钟和锁相环(PLL).............................................. 56 通用的输入/输出.................................................... 57 输出开关选择(插座检测)........................................... 58 控制接口........................................................... 59 控制模式选择和 2 线模式地址.........................................59 3 线串行控制模式 ...................................................59 2 线串行控制模式 ...................................................59 芯片复位........................................................... 60 电源............................................................... 60 推荐的上电/断电顺序................................................ 60 电源管理........................................................... 61 通过减少过采样率节省电能........................................... 61 VMID............................................................... 61 BIASEN............................................................. 61 源电流估算......................................................... 61
OP07作用详解

修订历史
2010年3月—修订版A至修订版B 修改格式 ..................................................................................... 通篇 更改“简介”部分和“单电源供电”部分 ........................................ 1 更改图2和图4 .................................................................................. 3 更改“更低的电源电流”部分......................................................... 4 更改“输入端无箝位二极管”部分及图10 ................................... 5 更改图14和图16 .............................................................................. 6 更改“高出输入端3 V”部分 ........................................................... 7
V2 R7 100Ω
GAIN = 100 (V2 – V1)
AD589
N D1
2
U1 V–
1
1/4 OP747
R2 200Ω RTD 100Ω
V1 R5 26.7kΩ R8 2.55MΩ R9 6.19kΩ R12 1MΩ U4
R4 10.1kΩ
U3 1/4 OP747 R15 1MΩ
VOUT
1/4 OP747
WiFi 7 壁挂型套装说明书

KIT CONTENTS Your WiFi 7 wall mount kit includes the following:• Wall mount bracket*• Anchor screw pack •Device screw pack*White bracket included in kit RBEWM-10000S. Black bracket included in kit RBEWMB-10000S.For installation instructions, see the reverse side of this document.Quick Start GuideWall Mount KitFor selectandWiFi 7 devices© NETGEAR, Inc.NETGEAR and the NETGEAR Logo are trademarks ofNETGEAR, Inc. Any non‑NETGEAR trademarks are used for reference purposes only.July 2023NETGEAR, Inc. 350 East Plumeria Drive San Jose, CA 95134, USA NETGEAR INTERNATIONAL LTD Floor 6, Penrose Two, Penrose Dock, Cork, T23 YY09, Ireland REGULATORY AND LEGALSi ce produit est vendu au Canada, vous pouvez accéder à ce document en français canadien à /support/download/.(If this product is sold in Canada, you can access this document in Canadian French at /support/download/.)For regulatory compliance informationincluding the EU Declaration of Conformity, visit /about/regulatory/.See the regulatory compliance document before connecting the power supply.For NETGEAR’s Privacy Policy, visit /about/privacy‑policy.By using this device, you are agreeing to NETGEAR’s Terms and Conditions at/about/terms‑and‑conditions. If you do not agree, return the device to your place of purchase within your return period.Applicable to 6 GHz devices only: Only use the device indoors. The operation of 6 GHz devices is prohibited on oil platforms, cars, trains, boats, and aircraft, except that operation of this device is permitted in large aircraft while flying above 10,000 feet. Operation of transmitters in the 5.925‑7.125 GHz band is prohibited for control of or communications with unmanned aircraft systems.SUPPORT AND COMMUNITYGet your questions answered and access the latestdownloads at /support, and check out our NETGEAR Community at .STEP 1 ‑ MOUNT BRACKET STEP 2 ‑ PREPARE CABLES STEP 3 ‑ MOUNT DEVICE STEP 4 ‑ ATTACH CABLESIMPORTANT: Only install the wall mountvertically on a wall. Do not install the wallmount horizontally or on a ceiling.*Orbi WiFi 7 router installation shown for illustrative purposes.。
7英寸角空气沙子说明书

OPERATOR’S MANUAL FOR 7 in. Angle Air SANDER 4,500 RPMOriginal InstructionsModel No. EATAS70S1P1) General Industry Safety & Health Regulations, Part 1910, OSHA 2206, available from: Superinten-dent of Documents; Government Printing Office; Washington DC 204022) Safety Code for Portable Air Tools, ANSI B186.1 available from: American National Standards Institute, Inc.; 1430 Broadway; New York, New York 100183) State and Local Regulations.WarningAlways wear eye protection when operating or performing maintenance on this tool.Always turn off the air supply and disconnect the air supply hose before installing, removing or adjust-ing any accessory on this tool, or before performing any maintenance on this tool.Improper operation or maintenance of this product could result in serious injury and property damage. Read and understand all warnings and operation instructions before using this equipment.4041382928112526222423212049040103024803051617181514195051473943423337363534121109080713064546313230Item No Part No.Description Qty.01AP-70001#LW MAIN SHAFT CASING1 02AP-70002MAIN SHAFT1 03BB-62011BALL BEARING2 04AP-70004BEVEL PINION1 05AP-70005BEARING SUPPORT1 06AP-70006ARBOR1 07BB-62032BALL BEARING1 08AP-70008BEVEL GEAR1 09AP-70009SET NUT1 11BB-06082BALL BEARING2 12BWW-0608WAVE WASHER1 13AP-70013ARBOR BEARING1 14AP-70014DISTANCE NUT1 15AP-70015INTERNAL GEAR1 16AP-70016IDLER SPINDLE1 17NR-35240NEDDLE ROLLER3 18AS-70018IDLER GEAR3 19HD-12022WASHER1 20BB-60002BALL BEARING1 21HD-12019FRONT END PLATE1 22HD-12018CYLINDER1 23AS-70023ROTER1 24HD-12016ROTER BLADE4 25HD-12014REAR END PLATE1 26SP-30060SPRING PIN1 28VP-70011BEARING CAP1 29HD-12001#LW-EMAX MOTOR HOUSING1 30AP-70030BUSHING1 31VP-70035VALVE STEM1 32DG-40058O-RING1 33VP-70037VALVE STEM1 34AP-70034AIR REGULATOR1 35ORP-0080O-RING1 36ORP-0120O-RING1 37VP-70C41VALVE SCREW1 38AR-38005#BC THROTTLE LEVER1 39SP-25220SPRING PIN1 40HD-12002INLET BUSHING1 41ORP-0180O-RING1 42PG-38043PLUG1 43ORP-0040O-RING1 45VP-70042PAD1 46VP-70I43PAD NUT1 47AP-70C47HANDLE1 48AP-70048SPACER COLLAR1 49AS-70049SUN GEAR1 50AG-70057WRENCH(B)1 51DG-14043WRENCH(A)1Model Number Free Speed(rpm)Spindle Size Pad SizeProduct Net WeightPound (kg)Heightin. (mm)Lengthin. (mm)AirConsumptionscfm (LPM)EATAS70S1P4,5005/8-11 UNC7 in. 4.30 (1.96) 4.21 (107)13.0 (330) 38 (1075) Specifications subject to change without prior notice.The actual exposure values and amount of risk or harm experienced to an individual is unique to each situation and depends upon the surrounding environment, the way in which the individual works, the particular material being worked, work station design as well as upon the exposure time and the physical condition of the user. EMAX™ cannot be held responsible for the consequences of using declared values instead of actual exposure values for any individual risk assessment.Further occupational health and safety information can be obtained from the following websites:https://osha.europa.eu/en (Europe); (USA)The tool is intended to be operated as a hand held tool. It is always recommended that the tool be used when standing on a solid floor. It can be in any position but before any such use, the operator must be in a secure position having a firm grip and footing and be aware that the tool can develop a torque reaction. See the section “Safety Information”.Use a clean lubricated air supply that will give a measured air pressure at the tool of 90 psig (6.2 bar) when the tool is running with the lever fully depressed. It is recommendedto use an approved 3/8 in. (10 mm) x 25 ft (8 m) maximum length airline. It is recommended that the tool be connected to the air supply as shown in Figure 1.Do not connect the tool to the airline system without incorpo-rating an easy to reach and operate air shut off valve. The air supply should be lubricated. It is strongly recommended that an air filter, regulator and lubricator (FRL) be used as shown in Figure 1 as this will supply clean, lubricated air at the correct pressure to the tool. Details of such equipment can be obtained from your supplier. If such equipment is not used then the tool should be manually lubricatedTo manually lubricate the tool, disconnect the airline and put 2 to 3 drops of suitable pneumatic Airbase synthetic air tool oil must be used for lifetime warranty. Part# OIL012 into the hose end (inlet) of the machine. Reconnect tool to the air supply and run tool slowly for a few seconds to allow air to circulate the oil. If the tool is used frequently, lubricate it on a daily basis or lubricate it if the tool starts to slow or lose power.It is recommended that the air pressure at the tool be 90 PSI (6.2 Bar) while the tool is running so the maximum RPM is not exceeded. The tool can be ran at lower pressures but should never be ran higher than 90 PSI (6.2 Bar). If ran at lower pres-sure the performance of the tool is reduced.Figure 11) Read all instructions before using this tool. All operatorsmust be fully trained in its use and aware of these safety requirements. All service and repair must be carried out by trained personnel.2) Never direct air at yourself or anyone else.3) Install air fitting into inlet bushing of tool.4) Always remove the air supply to the tool before fitting,adjusting or removing the abrasive/accessory.5) Always wear required safety equipment when using thistool.6) When operating always place the tool on the work thenstart the tool. Always remove the tool from the workbefore stopping. This will prevent gouging of the workdue to excess speed of the abrasive/accessory.7) Always adopt a firm footing and/or position and be awareof torque reaction developed by the tool.8) Use only correct spare parts.9) Always ensure that the workpiece is firmly fixed to pre-vent its movement.10) Check hose and fittings regularly for wear. Do not carrythe tool by its hose; always be careful to prevent the tool from being started when carrying the tool with the airsupply connected.11) Dust can be highly combustible. Keep working areaclean.12) Dust from some work processes can cause cancer, birthdefects or other respiratory diseases. Risk assessmentof these hazards and implementation of appropriatecontrols is essential.13) Direct the exhaust so as to minimized disturbance of dustin a dust filled environment14) Do not operate the tool in explosive atmospheres, suchas in the presence of flammable liquids, gases, or dust.The abrasives are able to create sparks when workingmaterial, resulting in the ignition of the flammable dustor fumes.15) Do not exceed maximum recommended air pressure.Use safety equipment as recommended.16) The tool is not electrically insulated. Do not use wherethere is a possibility of coming into contact with liveelectricity, gas pipes, water pipes, etc. Check the area of operation before operation.17) Take care to avoid entanglement with the moving partsof the tool with clothing, ties, hair, cleaning rags, etc. Ifentangled, it will cause the body to be pulled towards the work and moving parts of the machine and can be verydangerous.18) Keep hands away from rotating or accessories, spindlesor other moving parts during use.19) If the tool appears to malfunction, remove from use im-mediately and arrange for service and repair.20) Do not allow the tool to free speed without taking precau-tions to protect any persons or objects from the loss ofthe abrasive/accessory.21) Do not allow tool to free run for an extended period oftime as this will shorten its life.Year Standard WarrantyOur Standard warranty covers defects or failures in workmanship or materials in our air tools 2 years from the date of purchase. EMAX will repair or replace; at their discretion any defective part or unit which proves to be defective. This warranty does not cover incidental/consequential damages and failures due to misuse, abuse or normal wear and tear.Any modification, repair or repair attempts not authorized are not covered under this warranty. Shipping for warranty claims are included in this warranty for the first 90 days.*Limited Extended Lifetime WarrantyOur LIMITED EXTENDED LIFETIME WARRANTY is our no questions asked warranty. It covers defects or failures in workmanship or materials in our air tools for the life of the tool. EMAX will repair or replace; at their discretion any defective part or unit which proves to be defective. This warranty does not cover incidental/consequential damages and failures due to misuse, abuse or normal wear and tear (sanding pads and discs, chisels, tips, needs, nozzles, etc).ANY MODIFICATION, REPAIR OR REPAIR ATTEMPTS NOT AUTHORIZED ARE NOT COVERED UNDER THIS WARRANTY.SHIPPING FOR WARRANTY CLAIMS ARE INCLUDED IN THIS WARRANTY FOR THE FIRST 90 DAYS.3 SIMPLE STEPS TO QUALIFY FOR YOUR EXTENDED LIFETIME AIR TOOL WARRANTY:1. Register your air tool purchase at , be sure to have youroriginal receipt of purchase in hand for important information needed in your registry.2. Write a review on the site where you purchased your air tool3. Send us a screen shot or photograph of your review to***************************************************************************. For warranty claims or more information call EMAX directly at: 1-866-294-4153EMAX PHONE: 1-866-294-4153。
抗振型涡街流量计参数
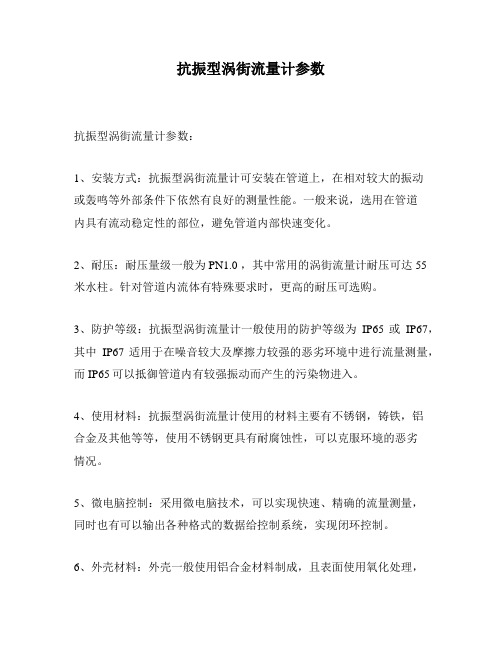
抗振型涡街流量计参数
抗振型涡街流量计参数:
1、安装方式:抗振型涡街流量计可安装在管道上,在相对较大的振动
或轰鸣等外部条件下依然有良好的测量性能。
一般来说,选用在管道
内具有流动稳定性的部位,避免管道内部快速变化。
2、耐压:耐压量级一般为PN1.0 ,其中常用的涡街流量计耐压可达55米水柱。
针对管道内流体有特殊要求时,更高的耐压可选购。
3、防护等级:抗振型涡街流量计一般使用的防护等级为IP65或IP67,其中IP67适用于在噪音较大及摩擦力较强的恶劣环境中进行流量测量,而IP65可以抵御管道内有较强振动而产生的污染物进入。
4、使用材料:抗振型涡街流量计使用的材料主要有不锈钢,铸铁,铝
合金及其他等等,使用不锈钢更具有耐腐蚀性,可以克服环境的恶劣
情况。
5、微电脑控制:采用微电脑技术,可以实现快速、精确的流量测量,
同时也有可以输出各种格式的数据给控制系统,实现闭环控制。
6、外壳材料:外壳一般使用铝合金材料制成,且表面使用氧化处理,
不仅防止了外部污染物进入,而且降低了介质温度对流量测量精度的影响。
7、企业标准:根据国家标准GB/T 1227-1993,抗振型涡街流量计必须符合“流量计的电气及放大性能”的要求,以确保在振动环境下正确的响应流量变化。
pzd和pkw
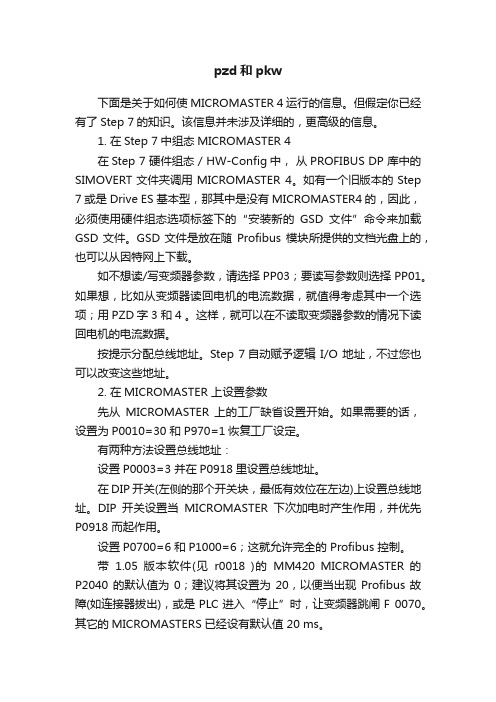
pzd和pkw下面是关于如何使MICROMASTER 4 运行的信息。
但假定你已经有了Step 7的知识。
该信息并未涉及详细的,更高级的信息。
1. 在Step 7中组态MICROMASTER 4在Step 7 硬件组态 / HW-Config中,从PROFIBUS DP 库中的SIMOVERT文件夹调用MICROMASTER 4。
如有一个旧版本的Step 7或是Drive ES 基本型,那其中是没有MICROMASTER4的,因此,必须使用硬件组态选项标签下的“安装新的GSD文件”命令来加载GSD文件。
GSD文件是放在随Profibus 模块所提供的文档光盘上的,也可以从因特网上下载。
如不想读/写变频器参数,请选择PP03;要读写参数则选择PP01。
如果想,比如从变频器读回电机的电流数据,就值得考虑其中一个选项;用PZD字 3 和 4 。
这样,就可以在不读取变频器参数的情况下读回电机的电流数据。
按提示分配总线地址。
Step 7自动赋予逻辑I/O 地址,不过您也可以改变这些地址。
2. 在MICROMASTER 上设置参数先从MICROMASTER 上的工厂缺省设置开始。
如果需要的话,设置为P0010=30 和P970=1恢复工厂设定。
有两种方法设置总线地址:设置P0003=3 并在P0918里设置总线地址。
在DIP开关(左侧的那个开关块,最低有效位在左边)上设置总线地址。
DIP开关设置当MICROMASTER下次加电时产生作用,并优先P0918 而起作用。
设置P0700=6 和P1000=6;这就允许完全的 Profibus 控制。
带1.05 版本软件(见r0018 )的MM420 MICROMASTER 的P2040 的默认值为 0;建议将其设置为 20,以便当出现 Profibus 故障(如连接器拔出),或是PLC进入“停止”时,让变频器跳闸F 0070。
其它的MICROMASTERS已经设有默认值 20 ms。
- 1、下载文档前请自行甄别文档内容的完整性,平台不提供额外的编辑、内容补充、找答案等附加服务。
- 2、"仅部分预览"的文档,不可在线预览部分如存在完整性等问题,可反馈申请退款(可完整预览的文档不适用该条件!)。
- 3、如文档侵犯您的权益,请联系客服反馈,我们会尽快为您处理(人工客服工作时间:9:00-18:30)。
Alternate Configuration
E
L
3.17 max.
L ± 0.8 1705 22.3 22.3 35.3 47.7 47.7
W ± 0.8 6.99 7.87 9.65 9.65 9.65 12.7
600V 300V 1000 2000 3000 600 Volts 10x1000µsec
General Note
Welwyn Components reserves the right to make changes in product specification without notice or liability. All information is subject to Welwyn’s own data and is considered accurate at time of going to print. A subsidiary of TT electronics plc Issue B · 03.02
25 40
65 PPW-2
PPW-15
© Welwyn Components Limited Bedlington, Northumberland NE22 7AA, UK Telephone: +44 (0) 1670 822181 · Facsimile: +44 (0) 1670 829465 · Email: info@ · Website: 116
Power Derating
100 80 PPW-3, 5, 7, 10 % Rated Load 60 150 40 20 0 0 50 100 150 200 Ambient Temperature (°C) 250
Max. Recommended Ambient Operating Temperature 150°C
Electrical Data
PPW-2 Power rating at 25°C Resistance range watts 2 PPW-3 3 PPW-5 5 PPW-7 7 PPW-10 10 PPW-15 15 0R1 to 5K ohms 0R1 to 1K6 0R1 to 1K6 0R1 to 1K6 0R1 to 2K5 0R1 to 5K
1000V 500V 1000 2000 3000 1000 Volts 10x360µsec
*10 microseconds – Maximum rise time to peak voltage. 360 or 1000 microseconds - minimum decay time to one half peak.
Please note: When ordering the alternate configuration please add an ‘A’ after the part number (ie. PPW-3A)
Lighting Surge Capabilities for PPW-2
Resistive range 1R to 9R9 10R to 29R9 30R to 99R 100R to 1K6 ohms 10 x 1000* 250V 500V 600V 1000V 10 x 360* 650V 850V 1000V 1500V
© Welwyn Components Limited · Bedlington, Northumberland NE22 7AA, UK
Telephone: +44 (0) 1670 822181 · Facsimile: +44 (0) 1670 829465 · Email: info@ · Website:
Issue B · 03.02
115
元器件交易网
Semi-Precision Power Wirewound Resistors
PPW Series
Welwyn Components
Physical Data
Dimensions (mm)
Standard Configuration
d W H 25.4 min
元器件交易网
Semi-Precision Power Wirewound Resistors
PPW Series
Welwyn Components
• Ideal for pulse and surg5 watts • Resistance to 0R1 ohms to 5K ohms • ±3%, ±2% or ±1% tolerance • ±20 ppm/°C TCR
H ± 0.8 6.99 7.87 8.89 8.89 8.89 12.7
d dia. 0.8 0.8 0.8 0.8 0.8 0.8
E ± 0.8 8.134 9.65 10.4 11.9 11.9 12.7
Temperature Rise
Hot Spot Temperature (°C) 250 200 150 100 50 0 0 20 40 60 80 100 120 % Rated Load PPW-15 PPW-10 PPW-7 PPW-5 PPW-3 PPW-2