采用深度分析法分析模具内的流动特性
压铸模流分析分析报告

压铸模流分析分析报告目录压铸模流分析分析报告 (1)引言 (1)背景介绍 (1)目的和意义 (2)压铸模流分析概述 (3)压铸模流分析的定义 (3)压铸模流分析的作用 (4)压铸模流分析的方法 (4)压铸模流分析的关键步骤 (5)模型建立 (5)材料参数设定 (6)网格划分 (7)求解器选择 (8)结果分析 (9)压铸模流分析的应用案例 (10)案例一:汽车零部件压铸模流分析 (10)案例二:电子产品外壳压铸模流分析 (11)案例三:家电产品压铸模流分析 (12)压铸模流分析的优势和局限性 (13)优势 (13)局限性 (14)结论 (14)对压铸模流分析的总结 (14)对未来研究的展望 (15)引言背景介绍压铸模流分析是一种重要的工程分析方法,用于评估和优化压铸模具的设计和制造过程。
随着工业技术的不断发展和进步,压铸模流分析在压铸行业中的应用越来越广泛。
通过模拟和分析压铸过程中的流动、凝固和收缩等关键参数,可以帮助工程师们更好地理解和控制压铸过程,提高产品质量和生产效率。
压铸是一种常用的金属成型工艺,广泛应用于汽车、航空航天、电子、家电等行业。
在压铸过程中,液态金属被注入到模具中,经过凝固和冷却后形成所需的零件或产品。
然而,由于压铸过程中涉及到复杂的流动和凝固现象,模具设计和制造过程中存在许多挑战和难题。
在传统的压铸模具设计中,通常需要通过试模和试产的方式来验证模具的可行性和性能。
这种方法不仅费时费力,而且成本高昂。
而压铸模流分析则可以在模具制造之前,通过计算机模拟和分析来预测和评估模具的性能。
通过模拟压铸过程中的流动、凝固和收缩等关键参数,可以帮助工程师们更好地理解和控制压铸过程,提高产品质量和生产效率。
压铸模流分析的核心是数值模拟方法,通过建立数学模型和计算流体力学(CFD)方法来模拟和分析压铸过程中的流动和凝固现象。
通过对模具结构、材料和工艺参数等进行优化,可以提高产品的成型质量和生产效率。
注塑模具的模流分析

注塑模具的模流分析注塑模具的模流分析是指在注塑模具设计阶段,通过模具的数值模拟计算和分析,得出注塑成型过程中的流动状态。
模流分析可以帮助制造商预测并优化注塑成型过程,以确保产品质量和生产效率。
下面将介绍注塑模具的模流分析的重要性、分析内容及步骤,并分享一些模流分析的实际应用案例。
一、注塑模具模流分析的重要性1.预测成型缺陷通过模流分析,可以预测成型缺陷,如短射、气泡、翘曲等,帮助制造商在实际生产前就能够发现潜在的问题并加以改进,减少不良品率。
2.优化模具结构模具结构对注塑成型过程的影响很大,通过模流分析可以确定最佳的模具结构,如冷却系统的设计、料斗和浇口的位置等,从而提高成型效率和产品质量。
3.提高产品质量模流分析能够帮助设计师预测和优化填充过程,从而避免成型缺陷,提高产品质量。
4.节约成本通过模流分析可以调整注塑工艺参数,如注射速度、注射压力等,达到最佳注塑效果,减少成本。
二、注塑模具模流分析的内容1.塑料材料流动模拟模流分析可预测塑料在模腔内部的流动速度、温度分布和填充情况,以及预测和防止可能出现的缺陷,如短射、气泡、翘曲等。
2.模具温度分析通过模流分析,可以优化模具的冷却系统设计,确保模具在注塑过程中能够保持合适的温度,提高成型效率和产品质量。
3.油压分析注塑模具中的油压对模具的开合速度和稳定度影响很大,模流分析可以帮助设计师优化油压系统,确保模具运行平稳。
三、注塑模具模流分析的步骤1.准备模具CAD模型和相关参数首先需要准备注塑模具的CAD模型及相关参数,如材料特性、注射机参数等。
2.进行模型网格划分将模具CAD模型划分成网格,以便进行计算和分析。
3.设置材料和物理参数设置塑料材料的流变性能和热物理参数。
4.设定模具填充流动条件设定注塑过程中的注射速度、压力、温度等参数。
5.进行模流计算和分析通过计算机软件进行模流计算和分析,得出注塑成型过程中的填充情况、温度分布、压力分布等信息。
6.优化设计和参数调整根据模流分析结果,对模具结构和工艺参数进行优化和调整,以改进产品质量和生产效率。
压铸模流分析讲义

压铸模流分析讲义一、引言压铸是一种常用的金属成形工艺,广泛应用于汽车、摩托车、航空航天等领域。
而在压铸过程中,模具的设计和模流分析是非常重要的环节,能够对压铸件的质量和成形效果起到关键的影响。
本讲义将介绍压铸模流分析的基本原理、流程和应用。
二、压铸模流分析的原理1.流动性分析原理:通过数值模拟方法,计算金属液在模穴中的流动速度、填充压力和温度分布等,并结合模具结构特点预测模具充填过程中的缺陷,如气孔、冷隔、夹杂等。
2.凝固性分析原理:根据金属液的凝固特性,分析模具结构对液态金属凝固过程的影响,预测可能出现的缺陷,如热裂纹、收缩缺陷等。
3.温度场分析原理:通过计算得到金属液在模具中的温度分布,进一步预测可能出现的缺陷。
4.应力变形分析原理:根据模具在铸造过程中的受力情况,分析金属液对模具的应力和变形,预测可能出现的变形和裂纹。
三、压铸模流分析的流程1.模型导入:将要分析的压铸模的三维CAD模型导入流体动力学(CFD)软件中。
2.网格划分:对导入的CAD模型进行网格划分,将模型划分为若干个网格单元,用于模拟流体的流动。
3.材料参数设置:设置金属液的物性参数,如密度、黏度、比热等,并将其导入CFD软件。
4.界面边界条件设置:设置金属液与模具壁之间的界面条件,如润滑和传热系数等。
5.操作条件设置:设置压铸过程中的操作参数,如压力、速度、温度等。
6.数值模拟:基于数值方法,对模具进行流动性、凝固性、温度场、应力变形等方面的模拟。
7.结果分析:根据模拟结果,对流动性、凝固性、温度场、应力变形等方面进行分析和评估。
8.优化设计:根据分析结果,对模具的结构和工艺参数进行优化设计,以改善铸件质量。
9.结果验证:通过样品试铸,验证优化后的模具设计和工艺参数是否能够达到预期效果。
四、压铸模流分析的应用1.优化模具结构设计:通过分析流动性、凝固性和应力变形等方面,可以找出模具设计中存在的问题,并提出相应的改进方案,以提高铸件的质量和生产效率。
塑料模流分析-塑料流动分析

塑料流动分析熔融的热塑性塑料呈现黏弹性行为(viscoelastic behavior),亦即黏性流体与弹性固体的流动特性组合。
当黏性流体流动时,部分驱动能量将会转变成黏滞热而消失;然而,弹性固体变形时,会将推动变形的能量储存起来。
日常生活中,水的流动就是典型的黏性流体,橡胶的变形属于弹性体。
除了这两种的材料流动行为,还有剪切和拉伸两种流动变形,如图4-1 (a)与(b)。
在射出成形的充填阶段,热塑性塑料之熔胶的流动以剪切流动为主,如图4-1(c)所示,材料的每一层元素之间具有相对滑动。
另外,当熔胶流经一个尺寸突然变化的区域,如图4-1(d),拉伸流动就变得重要多了。
图4-1 (a)剪切流动;(b)拉伸流动;(c)模穴内的剪切流动(d)充填模穴内的拉伸流动热塑性塑料承受应力时会结合理想黏性流体和理想弹性固体之特性,呈现黏弹性行为。
在特定的条件下,熔胶像液体一样受剪应力作用而连续变形;然而,一旦应力解除,熔胶会像弹性固体一样恢复原形,如图4-2 (b)与(c)所示。
此黏弹性行为是因为聚合物在熔融状态,分子量呈现杂乱卷曲型态,当受到外力作用时,将允许分子链移动或滑动。
然而,相互纠缠的聚合物分子链使系统于施加外力或解除外力时表现出弹性固体般的行为。
譬如说,在解除应力后,分子链会承受一恢复应力,使分子链回到杂乱卷曲的平衡状态。
因为聚合物系统内仍有分子链的交缠,此恢复应力可能不是立即发生作用。
图4-2 (a)理想的黏性液体在应力作用下表现出连续的变形;(b)理想的弹性固体承受外力会立刻变形,于外力解除后完全恢复原形;(c)热塑性塑料之熔胶就像液体一样,在剪切应力作用下而连续变形。
然而,一旦应力解除,它就像弹性固体一般,部分变形会恢复原形。
4-1 熔胶剪切黏度熔胶剪切黏度(shear viscosity)是塑料抵抗剪切流动的阻力,它是剪切应力与剪变率的比值,参阅图4-3。
聚合物熔胶因长分子链接构而具有高黏度,通常的黏度范围介于2~3000 Pa(水为10-1 Pa,玻璃为1020 Pa)。
流体力学实验装置的流体流动特性分析方法

流体力学实验装置的流体流动特性分析方法流体力学实验装置的设计和分析对于研究流体流动的性质和特性具有重要意义。
在科学研究和工程应用中,通过合理的设计和准确的分析,可以更好地理解流体的特性,优化流体流动过程,提高工程效率。
本文将针对流体力学实验装置的流体流动特性分析方法展开讨论。
一、实验装置的基本结构流体力学实验装置通常由流体注入口、流动通道、压力传感器、流速测量装置等基本组成部分构成。
在实验过程中,通过控制流体注入口的流量和速度,可以实现对流动速度和流体压力的调节,从而对流体流动特性进行研究。
二、流体流动特性的参数分析1. 流体速度分布流体速度分布是描述流体流动特性的重要参数之一。
通过在不同位置上测量流体速度,可以分析流体在流动过程中的变化规律。
其中,流速分布的均匀性和稳定性对于流体流动的稳定性和可控性具有重要影响。
2. 流体压力分布流体在流动过程中会产生压力变化,而流体的压力分布则反映了流体流动的受力情况。
通过在流体流动通道上设置压力传感器,可以实时监测流体压力的变化,并分析流体流动的受力状态。
三、流体流动特性的分析方法1. 数值模拟分析法数值模拟是一种常用的分析流体流动特性的方法。
通过建立流体力学模型,采用数值计算方法对流体流动过程进行模拟,可以得到流速、压力等参数的数值解,从而揭示流体流动的特性。
2. 实验测试分析法实验测试是验证和分析数值模拟结果的重要手段。
通过在流体力学实验装置上进行实验测试,可以获得真实的流体流动数据,并与数值模拟结果进行对比分析,验证模拟的准确性和可靠性。
四、流体流动特性分析的应用流体流动特性的分析方法在工程领域有着广泛的应用。
例如,在航空航天领域,可以通过分析飞行器的流体流动特性,优化飞行器的空气动力学性能;在能源领域,可以通过分析液体或气体在管道中的流动特性,提高能源传输效率等。
综上所述,流体力学实验装置的流体流动特性分析方法对于研究流体流动具有重要的意义。
通过合理的设计和精确的分析,可以更好地理解流体的运动规律,为工程实践和科学研究提供有力支撑。
浅析模流分析

模流分析给热流道定点位减少了不少风险,收到广大热流道企业和模具企业的好评,模流分析工程师勤勤恳恳的工作也收到了业内人士的一度部塑料的流动路径进行分析的一个结果报告。模流分析的作用是在理想状态下对产品的成型做一个注塑模拟,以此来协助确定方案。模流分析可以模拟出在一定的锁模力,注塑压力,温度,路径大小,进浇点位,水路排布等理想环境下的成型状况。一般的分析主要是分析产品的熔接痕位置,产品是否饱满,压力是否合理,锁模力能否达到,产品的翘曲变形是否很大,点位是否合适。如果要加入水路分析,这个工作量就会大很多,一般的电脑配置也不足以完成这个庞大的工作量。世界上最精确的模流分析是于实际操作温差不超过2度的,这也是业内人士透露给艾贝斯的消息。
压铸模流分析分析报告

压铸模流分析分析报告
一、模具结构分析
通过对模具结构进行分析,可以确定模具的开合方式、浇注系统设计以及冷却系统设置等方面的参数。
在模具结构设计方面,需要考虑到金属充填的流态,避免产生二次气孔和翻砂现象,同时还需要保证金属的充填速度和压力等因素。
二、模具温度分析
模具温度对于铸件的质量有很大的影响,过高或过低的模具温度都会导致铸件出现缺陷。
通过模流分析可以对模具温度进行分析,可以帮助优化冷却系统的设计,保证模具表面均匀的温度分布,以提高铸件的质量。
三、金属流动分析
金属充填过程是压铸过程中的关键环节,通过模流分析可以模拟和分析金属在模具中的流动情况。
可以通过分析金属流动速度、充填时间和充填压力等参数,对模具结构和浇注系统进行优化设计,以提高铸件的充填性能。
四、缺陷分析
通过模流分析,可以模拟和分析金属在模具中的凝固过程,进而预测铸件中可能出现的缺陷情况,如气孔、缩孔、翻砂等。
通过这些分析可以提前发现潜在的缺陷问题,从而对模具结构和工艺进行改进,以提高铸件的质量。
五、优化建议
根据分析结果,可以得出针对模具结构和工艺的优化建议,以提高铸件的质量和生产效率。
建议可能包括改善浇注系统设计、调整模具温度、优化冷却系统设置等方面。
综上所述,压铸模流分析分析报告是对压铸模具结构、温度、金属流动和缺陷等方面进行模拟和分析,并给出相应的优化建议。
通过该分析可以提高铸件的质量,减少缺陷的产生,优化生产过程,提高生产效率。
注塑模具的模流分析
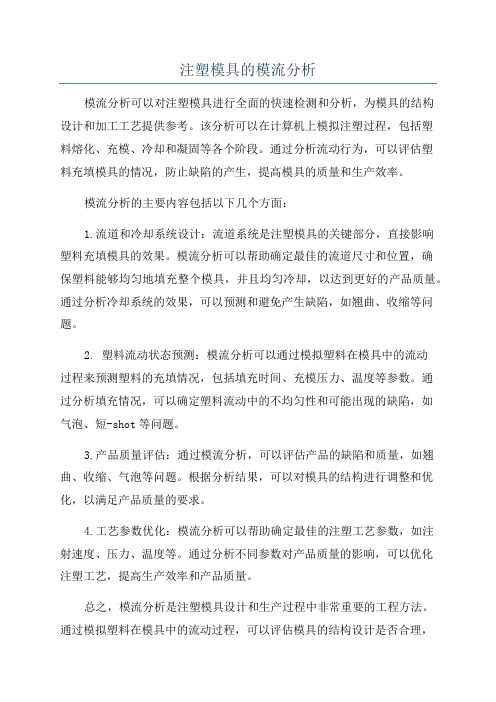
注塑模具的模流分析
模流分析可以对注塑模具进行全面的快速检测和分析,为模具的结构
设计和加工工艺提供参考。
该分析可以在计算机上模拟注塑过程,包括塑
料熔化、充模、冷却和凝固等各个阶段。
通过分析流动行为,可以评估塑
料充填模具的情况,防止缺陷的产生,提高模具的质量和生产效率。
模流分析的主要内容包括以下几个方面:
1.流道和冷却系统设计:流道系统是注塑模具的关键部分,直接影响
塑料充填模具的效果。
模流分析可以帮助确定最佳的流道尺寸和位置,确
保塑料能够均匀地填充整个模具,并且均匀冷却,以达到更好的产品质量。
通过分析冷却系统的效果,可以预测和避免产生缺陷,如翘曲、收缩等问题。
2. 塑料流动状态预测:模流分析可以通过模拟塑料在模具中的流动
过程来预测塑料的充填情况,包括填充时间、充模压力、温度等参数。
通
过分析填充情况,可以确定塑料流动中的不均匀性和可能出现的缺陷,如
气泡、短-shot等问题。
3.产品质量评估:通过模流分析,可以评估产品的缺陷和质量,如翘曲、收缩、气泡等问题。
根据分析结果,可以对模具的结构进行调整和优化,以满足产品质量的要求。
4.工艺参数优化:模流分析可以帮助确定最佳的注塑工艺参数,如注
射速度、压力、温度等。
通过分析不同参数对产品质量的影响,可以优化
注塑工艺,提高生产效率和产品质量。
总之,模流分析是注塑模具设计和生产过程中非常重要的工程方法。
通过模拟塑料在模具中的流动过程,可以评估模具的结构设计是否合理,
并预测可能出现的缺陷和问题。
这对于提高模具的质量和生产效率非常关键。
塑料成型中的流动行为分析与优化

塑料成型中的流动行为分析与优化塑料成型是一种广泛应用于制造业的工艺,它通过将塑料材料加热熔化后注入模具中,经过冷却固化后获得所需的产品形状。
在这个过程中,塑料的流动行为起着至关重要的作用。
本文将对塑料成型中的流动行为进行分析与优化。
一、塑料的流动行为塑料的流动行为是指在注塑过程中,塑料材料在模具中的流动特性。
它受到多种因素的影响,包括塑料材料的性质、温度、压力等。
塑料材料的性质决定了其流动性能,不同种类的塑料具有不同的流动性能。
温度对塑料的流动性能也有重要影响,一般来说,温度越高,塑料的流动性能越好。
压力是控制塑料流动的重要参数,适当的压力可以促进塑料的流动,但过高的压力会导致塑料的挤出。
二、流动行为分析为了更好地理解塑料的流动行为,可以通过数值模拟的方法进行分析。
数值模拟可以模拟塑料在注射过程中的流动情况,通过计算流体动力学方程和热传导方程,得到塑料在模具中的流动速度、温度分布等信息。
通过分析这些信息,可以评估塑料的充填情况和熔体的冷却效果,进而优化注射工艺。
三、流动行为优化优化塑料的流动行为是提高注射成型质量的关键。
在流动行为分析的基础上,可以通过以下几个方面来进行优化。
1. 模具设计优化:模具的设计对塑料的流动行为有重要影响。
合理的模具结构可以减少塑料的流动阻力,提高充填效果。
同时,通过设置合适的冷却系统,可以提高熔体的冷却速度,减少产品的收缩变形。
2. 工艺参数优化:工艺参数对塑料的流动行为有直接影响。
通过调整注射速度、压力、温度等参数,可以控制塑料的流动性能,提高产品的表面质量和尺寸精度。
3. 材料选择优化:不同种类的塑料材料具有不同的流动性能。
根据产品的要求和工艺的特点,选择合适的塑料材料可以改善流动行为,提高成型效果。
4. 模具表面处理优化:模具表面的处理也会影响塑料的流动行为。
通过表面涂层、抛光等处理方法,可以减少塑料在模具表面的粘附,提高产品的充填效果。
通过对塑料成型中的流动行为进行分析与优化,可以提高产品的质量和生产效率。
模具设计中的流动分析与注塑成型质量研究
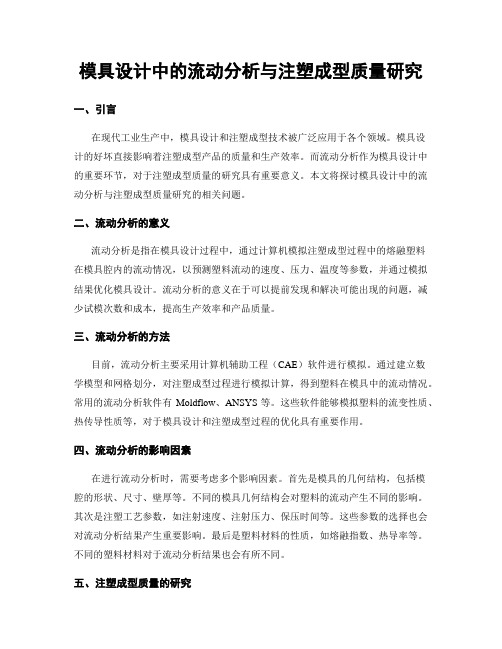
模具设计中的流动分析与注塑成型质量研究一、引言在现代工业生产中,模具设计和注塑成型技术被广泛应用于各个领域。
模具设计的好坏直接影响着注塑成型产品的质量和生产效率。
而流动分析作为模具设计中的重要环节,对于注塑成型质量的研究具有重要意义。
本文将探讨模具设计中的流动分析与注塑成型质量研究的相关问题。
二、流动分析的意义流动分析是指在模具设计过程中,通过计算机模拟注塑成型过程中的熔融塑料在模具腔内的流动情况,以预测塑料流动的速度、压力、温度等参数,并通过模拟结果优化模具设计。
流动分析的意义在于可以提前发现和解决可能出现的问题,减少试模次数和成本,提高生产效率和产品质量。
三、流动分析的方法目前,流动分析主要采用计算机辅助工程(CAE)软件进行模拟。
通过建立数学模型和网格划分,对注塑成型过程进行模拟计算,得到塑料在模具中的流动情况。
常用的流动分析软件有Moldflow、ANSYS等。
这些软件能够模拟塑料的流变性质、热传导性质等,对于模具设计和注塑成型过程的优化具有重要作用。
四、流动分析的影响因素在进行流动分析时,需要考虑多个影响因素。
首先是模具的几何结构,包括模腔的形状、尺寸、壁厚等。
不同的模具几何结构会对塑料的流动产生不同的影响。
其次是注塑工艺参数,如注射速度、注射压力、保压时间等。
这些参数的选择也会对流动分析结果产生重要影响。
最后是塑料材料的性质,如熔融指数、热导率等。
不同的塑料材料对于流动分析结果也会有所不同。
五、注塑成型质量的研究通过流动分析,可以得到注塑成型过程中的塑料流动情况。
根据流动分析结果,可以预测出可能出现的缺陷,如短射、气泡、翘曲等。
同时,还可以通过优化模具设计和注塑工艺参数,减少或消除这些缺陷。
注塑成型质量的研究旨在提高产品的尺寸精度、表面质量和力学性能,以满足不同行业的需求。
六、案例分析以汽车零部件的注塑成型为例,进行案例分析。
在汽车行业中,注塑成型是生产零部件的常用方法。
通过流动分析,可以优化模具设计和注塑工艺参数,提高产品的表面质量和力学性能。
注塑件模流分析范文

注塑件模流分析范文注塑件模流分析是指在注塑生产过程中对注塑件模具进行流道设计和流动分析,以优化产品的成型性能和生产效率。
注塑件模流分析可以帮助设计师在开始制造模具之前预测和解决潜在的模具设计问题,提高模具制造效率和产品质量。
注塑模流分析主要包括以下几个方面:1.模具流道设计:模具流道的设计是影响注塑件成型质量的重要因素之一、通过流道设计,可以控制注塑料在模具中的流动速度和流动方向,避免气泡、缩痕等缺陷的产生。
模具流道的设计要尽量减小注塑料在流动过程中的剪切力和热应力,以保证注塑料的充填性和保压性。
2.塑料材料选择:不同的注塑件需要选择不同的塑料材料,而塑料材料的性能也会影响注塑过程中的流动性能。
比如,高粘度的塑料需要较长的注塑时间和较高的注塑温度,否则容易出现流动不畅、射嘴堵塞等问题。
因此,在注塑件模流分析中,需考虑塑料材料的熔融指数、热稳定性、流变性能等因素,以选择合适的注塑材料。
3.模具温度控制:模具温度的设置对注塑件的成型效果有重要影响。
在注塑件模流分析中,需要通过流动分析确定最佳的模具温度。
过高的模具温度可能导致塑料材料过早熔化,造成射嘴堵塞或烧结;而过低的模具温度则可能导致塑料材料不充分熔化,造成充填不充分或有空洞的缺陷。
因此,在注塑件模流分析中,需要对模具进行温度场分析和热耦合分析,以确定最佳的模具温度。
4.模具结构设计:模具结构的设计也是注塑件模流分析的重要内容之一、注塑模具的结构要尽量简单,以降低成本和加工难度,同时要保证注塑件的成型质量。
在注塑件模流分析中,需对模具进行固态流动分析、模具冷却分析等,以确定最佳的模具结构。
比如,在注塑产品成型过程中,可以通过在模具上设置冷却通道来提高注塑件的冷却速度,减少产品变形。
总结起来,注塑件模流分析是一项非常重要的工作,可以为注塑件的设计和生产提供科学依据。
通过对注塑件模具进行流道设计和流动分析,可以预测和解决潜在的设计问题,提高产品的成型性能和生产效率,降低生产成本,提高产品质量。
模具冷却通道的流体动力学

模具冷却通道的流体动力学一、模具冷却通道的流体动力学概述模具冷却通道是模具设计中的重要组成部分,其主要作用是在注塑或铸造过程中快速、均匀地将模具内的热量传递到冷却介质中,以实现模具的快速冷却。
流体动力学作为研究流体运动规律的科学,在模具冷却通道设计中扮演着至关重要的角色。
通过深入研究流体动力学,可以优化冷却通道的设计,提高冷却效率,缩短生产周期,提升产品质量。
1.1 模具冷却通道的流体动力学特性模具冷却通道的流体动力学特性主要包括流体的流动状态、流动速度、压力分布、温度场分布等。
这些特性直接影响冷却通道的冷却效果和模具的使用寿命。
流体的流动状态可以分为层流和湍流,其中湍流状态下的换热效率更高。
流动速度的快慢决定了热量传递的速率,而压力分布则影响流体的流动方向和速度。
温度场的分布则直接关系到冷却的均匀性和效率。
1.2 模具冷却通道的设计原则在设计模具冷却通道时,需要遵循以下原则:首先,冷却通道应尽可能均匀地分布在模具的各个部位,以实现热量的均匀传递;其次,冷却通道的形状和尺寸应根据模具的具体形状和生产需求进行优化设计;再次,冷却通道的布局应考虑到流体动力学的特性,以确保流体的流动顺畅,避免产生涡流和死区;最后,冷却通道的材料选择也应考虑到其热传导性能和耐腐蚀性能。
二、模具冷却通道的流体动力学分析方法模具冷却通道的流体动力学分析是确保冷却通道设计合理性的关键步骤。
通过采用不同的分析方法,可以预测流体在冷却通道中的流动行为,评估冷却效果,从而指导冷却通道的优化设计。
2.1 数值模拟方法数值模拟是当前应用最广泛的流体动力学分析方法之一。
通过建立流体流动的数学模型,利用计算机软件进行数值求解,可以模拟流体在冷却通道中的流动状态、速度场、压力场和温度场。
数值模拟方法具有灵活性高、适应性强、成本相对较低等优点,但同时也存在计算精度受限于网格划分和计算方法等局限性。
2.2 实验测试方法实验测试是通过在实际或模拟的冷却通道中进行流体流动测试,直接测量流体的流动速度、压力、温度等参数,以验证数值模拟结果的准确性和评估冷却通道的实际冷却效果。
注塑模具的模流分析

塑 膠 材 料 簡 介
ABS : Techno ABS 810
1. -·O 2. 固 3. 顶 温 4. ¢¡G 温 5. ¢¡j 温 6. Yj 温 0.95489 1.0541 87.0 50.0 220.0 280.0 g/cm³ g/cm³ deg.C deg.C deg.C deg.C 7. .j 8. 5j 9. .G 10. 5G 11.53V^ 12.53V 温 温 温 温 200.0 240.0 30.0 70.0 50000 0.3 deg.C deg.C deg.C deg.C 1/s MPa
產 品 模 型 簡 介
產品長寬高約為724*40*61mm,大部分肉厚較爲均勻,基本肉厚為3.0mm。其中10mm和 14mm為流道呎吋。
分 析 模 型 簡 介
對此類產品,可使用Moldflow有限元分析網格中的Fusion(雙層面網格)或Midplane(中 性層網格)進行分析,分析結果一致。前者取外殼雙層網格,外表形狀与3D模型相同, 前處理時間較短,但網格數目是後者的兩倍以上,分析時間較長;後者取中間單層網格, 局部區域形狀需做等效處理,前處理時間較長,但分析時間較短。本分析採用前者。
循環周期溫度變化全屏后即可播放動畫充填壓力左圖為充填保壓切換時所需的注射壓力壓力适中達8035mpa但對所使用的180t注左圖的彩色線表示縫合線位置其中圈示的縫合綫較爲明顯
Moldflow模流分析報告 Moldflow模流分析報告
标 题: OOP 制 作 人: Henry 客户名称: 客户名称: 联盛 审 查 人: Henry 2007-06日 期: 2007-06-12
分 析 說 明
如下圖的產品,對尺寸精度要求較高。採用ABS的塑膠以熱流道成型,產品結構已確 定,客戶希望通過調整澆註繫統來優化産品的翹區,因此藉以Moldflow模流分析驗證是否 可行。 因Moldflow材料數據庫内ABS塑膠很多,故在分析中使用物性較爲相似的Techno ABS 810的ABS塑膠來代替,在數值上會与實際試模有差異,但趨勢是一致的。此報告中以這 種方案進行分析。
采用深度分析法分析模具内的流动特性

采用深度分析法分析模具内的流动特性newmaker 来源:MM现代制造CAE Services Corporation公司是一家Moldflow模内流动性分析咨询公司,它通过一个深度分析方法来分析熔液在模具内的流动性问题,该公司已为Moldflow模内流动性分析提供了20多年的咨询服务。
最近,PM Mold公司在为其客户Cessna Aircraft公司生产模具时,碰到了一个复杂的模压成型程序问题,于是该公司帮助PM Mold模具公司解决了这个问题。
PM Mold公司是一家为汽车、电器、航空和家电市场提供注塑模成型和模具制造服务的公司。
提供包括从模具的设计概念,一直到注塑、二次压注和模内纹饰(IMD)的生产等各种服务。
目前,该公司内有20台注塑压力,工作吨位28~500t不等。
Larry Hauck先生是PM Mold公司的总经理,他查看了各种操作的情况。
Cessna公司与PM Mold公司签订了合同,由其为Cessna公司生产Cessna Mustang飞机内的内饰注塑件。
于是Hauck先生与CAE Services公司取得了联系,让该公司对这类零件的模具内流动性进行分析。
Hauck先生说:“我们要求CAE Services司对该项目相关的所有零件进行模具注入、包装和冷却等方面的分析。
”采用Moldflow由于Cessna公司对Hauck先生及其团队所承接的塑料件生产提出了严格的质量要求,因此Hauck先生和Cessna公司一致同意采用Moldflow模内流动性分析法进行分析。
Hauck 先生说:“所有元件的尺寸、形状及其他细节都必须符合要求。
我们认为采用Moldflow模内流动性分析法具有最大的优越性,可以获得合适的浇口和冷却位置。
其所有的元件外观漂亮,零件的表面达到了A级水平。
对这些零件来说,美学是非常重要的。
正是这个原因,我们才与CAE Services公司合作。
”Hauck先生承认,他无法确信这种分析方法是否可达到100%的精确。
注塑模具加工前的重要步骤之模流分析

注塑模具加工前的重要步骤之模流分析
注塑模具开模之前需要进行模流分析,这有助于在生产开始前预测制造问题。
模具流动分析软件是使用特定的塑料和零件设计来模拟注射成型周期,对可制造性的设计进行了评价。
在注塑模具加工前做模流分析具有哪些优势?
◆模流分析有助于在模具制造前降低风险。
◆纠正潜在的模具结构问题
◆确定合适的壁厚
◆模具潜在问题的排除
◆确定最佳浇口的位置
◆调整为充分的拐角半径
◆为期望的结果找出最好的材料
Mitigate risk before production begins
Mold flow analysis helps to mitigate risk and create a successful mold from the start. It helps designers to:
correct potential cosmetic and structural problems
determine the appropriate wall thickness troubleshoot potential problem areas of the mold identify optimal gate locations
adjust for ample corner radius
create even and clean edges
identify the best material for the desired outcome create a successful mold from the start。
产品模流分析

方案一(流动分析结果) 方案一(流动分析结果)
注塑时间: 红色区域为最后填充区域.整个 注塑时间:2.231S,红色区域为最后填充区域 整个 红色区域为最后填充区域 流动平衡优秀,在不考虑其他因素前提下, 流动平衡优秀,在不考虑其他因素前提下,胶口 位置合理。 位置合理。 按F5可以自动播放 可以自动播放
无冷却系统情况下。 注:无冷却系统情况下。
方案一( 方向变形 方向变形) 方案一(Z方向变形
无冷却系统情况下。 注:无冷却系统情况下。
方案一小结
由以上分析结果可以知道, 点进胶的方式 点进胶的方式, 由以上分析结果可以知道,2点进胶的方式,对于填充上来 基本上可以满足,注塑压力跟时间,稍微有点偏多, 说,基本上可以满足,注塑压力跟时间,稍微有点偏多,会 在产品中心位置产生一明显的熔接痕, 在产品中心位置产生一明显的熔接痕,而且使用顺序控制也 无法调节。 无法调节。 变形方面,在不考虑冷却因素的前提下,Z方向上的变形 变形方面,在不考虑冷却因素的前提下, 方向上的变形 量比较大。可以针对性的在模具设计上做补偿。 量比较大。可以针对性的在模具设计上做补偿。
方案一(气穴位置图 方案一(气穴位置图)
注意气穴位置的排气设计。 注意气穴位置的排气设计。
方案一(产品的总变形 方案一(产品的总变形)
无冷却系统情况下。 注:无冷却系统情况下。
方案一( 方向变形 方向变形) 方案一(X方向变形
无冷却系统情况下。 注:无冷却系统情况下。
方案一( 方向变形 方向变形) 方案一(Y方向变形
方案二(产品的总变形 方案二(产品的总变形)
无冷却系统情况下。 注:无冷却系统情况下。
方案二( 方向变形 方向变形) 方案二(X方向变形
无冷却系统情况下。 注:无冷却系统情况下。
很全的模流分析诠释

很全的模流分析诠释很赞的模流分析诠释一流动分析部分1 Fill time result填充时间填充时间显示了模腔填充时每隔一定间隔的料流前锋位置。
每个等高线描绘了模型各部分同一时刻的填充。
在填充开始时,显示为暗蓝色,最后填充的地方为红色。
如果制品短射,未填充部分没有颜色。
使用:制品的良好填充,其流型是平衡的。
一个平衡的填充结果:所有流程在同一时间结束,料流前锋在同一时间到达模型末端。
这个意味着每个流程应该以暗蓝色等高线结束。
等高线是均匀间隔,等高线的间隔指示了聚合物的流动速度。
宽的等高线指示快速的流动,而窄的等高线指示了缓慢的填充。
查看项目:确认填充行为的显示状况。
短射—在填充时间结果上,短射将显示为半透明的,查看流动路径的末端是否有半透明区域。
关于3D模型, 可以使用未填充的模穴(短射)结果来检查是否在制品的内部存在未充填的部分。
滞流—如果填充时间结果显示一些区域上的云图有很近的间隔,将产生滞流。
如果一个薄区域在制品完全填充之前冻结滞流会导致短射。
过保压—如果填充时间结果显示某个流程的流程之前完成,将显示过保压。
过保压会导致高的制品重量、翘曲和不均匀的密度分布。
熔接线和气穴—在填充时间结果上重叠熔接线结果可以确定其存在,熔接线会导致结构和视觉上的缺陷。
气穴—在填充时间结果上重叠气穴结果可以确认其存在,气穴会导致结构和视觉上的缺陷。
跑道效应—跑道效应会导致气穴和熔接线,查看气穴和熔接线的位置及数量。
2 Pressure at velocity/pressure switchover resultV/P切换时刻的压力该结果从流动分析产生,显示了通过模型内的流程在从速度到压力控制切换点的压力分布。
使用:在填充开始前,模腔内各处的压力为零(或者为大气压,绝对压力)。
熔料前沿到达的位置压力才会增加,当熔料前沿向前移动填充后面的区域时压力继续增加,此取决于该位置与熔料前沿的长度。
各个位置的压力不同促使聚合物熔料的填充流动,压力梯度是压力差除以两个位置间的距离。
大尺寸复合材料注塑件模流分析

大尺寸复合材料注塑件模流分析摘要:随着近现代工业和科技的快速发展,注塑模具的技术水平也不断提高,仅仅依靠技术工人的经验乃至直观判断来完成设计工作已经不能满足生产的需要,企业也更加重视采用现代技术来辅助注塑模具的设计工作。
本文对注塑成型CAE技术进行了介绍,并对大尺寸复合材料注塑件模流进行了分析。
关键词:大尺寸复合材料注塑件;模流分析;CAE设计1.注塑成型CAE技术简介1.1 CAE技术概念及在注塑成型中的应用塑料在注塑成型的过程中要经历一系列复杂的过程,涉及众多的流体学、力学和热能变化过程,采用现在常用的CAE技术进行过程模拟,将塑料在注塑成型的过程中以及在模腔中的一系列流动过程仿真出来,并在此基础上进行分析,能够大大提高注塑成型设计工作的效率。
CAE技术指的是工程设计中的计算机辅助工程,既可以对设计物体进行动态分析,也可以进行静态分析,使用非常方便。
利用CAE技术对模具浇注过程中的温度、压力等参数进行计算、预测,其结果对于改进注塑工艺的系统以及浇注过程的技术参数具有非常重要的意义。
同时还可以利用CAE技术对可能发生的塑件翘曲进行预测,在模具浇注之前就可以采取一定的补救措施。
1.2CAE技术与注塑成型优化设计的关系目前,可以进行CAE设计的辅助软件非常多,其中使用范围比较广的就是Moldflow。
利用CAE技术进行注塑成型优化设计的技术前提就是对材料注塑过程中的压力、温度、应力、冷却时间等一系列的物理参数进行计算以及人工设置。
现在进行优化设计的一般过程可以分为划分网格、获得浇口的最佳位置、设置材料一系列的工艺参数、进行流动分析、重新更改方案、对多个方案进行综合技术比较、选择最佳设计方案等一系列过程。
以注塑模浇口的优化设计分析为例:采用CAE平台软件进行一系列的设置之后,首先对制件的浇口位置进行预分析,在此基础上,结合模具设计的相关技术理论,不断优化浇口的位置,然后进行充填和翘曲因素分析,最后根据显示的结果,确定浇口的最佳设计位置,完成整个设计过程。
压铸模流分析讲义

压铸模流分析讲义模具流动性分析是压铸模流分析的关键环节。
通过模具流动性分析,可以预测模具填充过程中可能出现的缺陷,如短流、冷隔、气孔等,并针对性地进行模具设计和优化。
模具流动性分析通常使用计算流体力学(CFD)方法来模拟设备中的铝液流动,通过计算和显示铝液在模腔中的压力、速度、温度和液面高度等参数的分布情况,以评估模具的填充性能。
此外,模具流动性分析还可以进一步分析铝液在填充过程中的温度场、应力场和凝固形态等,以预测可能导致缺陷的原因和位置。
压铸模具设计优化是通过模具流动性分析的结果对模具的结构和形状进行调整,以提高模具的填充性能和铸件质量。
在模具设计优化中,常用的方法包括增加给铝液的进场路线,减小液态金属在流动过程中的变形和浊流等。
例如,可以通过设计合理的浇口和浇注系统,使铝液能够均匀流动并避免在模腔中产生气隙,从而减少模具填充过程中的缺陷。
此外,在模具设计优化中还可以采用一些先进的材料和涂层技术,以提高模具的耐磨性和导热性,从而进一步降低模具的使用成本。
模具热平衡控制是压铸模流分析的另一个重要方面。
在压铸模具的填充过程中,由于铝液的高温和高压作用,模具会受到严重的热应力,从而导致模具的变形和损坏。
为了解决这个问题,可以通过模具热平衡控制来降低模具的温度梯度和热应力。
模具热平衡控制的主要方法包括采用合理的冷却系统和冷却通道,以提高模具的散热能力和温度均匀性。
此外,还可以采用一些热障涂层和陶瓷材料,以提高模具的抗高温性能和热传导性能。
总之,压铸模流分析是一项非常重要的模具设计和优化技术。
通过模具流动性分析、压铸模具设计优化和模具热平衡控制,可以预测和减少压铸模具制造过程中的缺陷和损坏,提高铸件的质量和生产效率。
随着计算机仿真技术的不断进步,压铸模流分析将在压铸模具制造中发挥越来越重要的作用。
- 1、下载文档前请自行甄别文档内容的完整性,平台不提供额外的编辑、内容补充、找答案等附加服务。
- 2、"仅部分预览"的文档,不可在线预览部分如存在完整性等问题,可反馈申请退款(可完整预览的文档不适用该条件!)。
- 3、如文档侵犯您的权益,请联系客服反馈,我们会尽快为您处理(人工客服工作时间:9:00-18:30)。
采用深度分析法分析模具内的流动特性
newmaker 来源:MM现代制造
CAE Services Corporation公司是一家Moldflow模内流动性分析咨询公司,它通过一个深度分析方法来分析熔液在模具内的流动性问题,该公司已为Moldflow模内流动性分析提供了20多年的咨询服务。
最近,PM Mold公司在为其客户Cessna Aircraft公司生产模具时,碰到了一个复杂的模压成型程序问题,于是该公司帮助PM Mold模具公司解决了这个问题。
PM Mold公司是一家为汽车、电器、航空和家电市场提供注塑模成型和模具制造服务的公司。
提供包括从模具的设计概念,一直到注塑、二次压注和模内纹饰(IMD)的生产等各种服务。
目前,该公司内有20台注塑压力,工作吨位28~500t不等。
Larry Hauck先生是PM Mold公司的总经理,他查看了各种操作的情况。
Cessna公司与PM Mold公司签订了合同,由其为Cessna公司生产Cessna Mustang飞机内的内饰注塑件。
于是Hauck先生与CAE Services公司取得了联系,让该公司对这类零件的模具内流动性进行分析。
Hauck先生说:“我们要求CAE Services司对该项目相关的所有零件进行模具注入、包装和冷却等方面的分析。
”
采用Moldflow
由于Cessna公司对Hauck先生及其团队所承接的塑料件生产提出了严格的质量要求,因此Hauck先生和Cessna公司一致同意采用Moldflow模内流动性分析法进行分析。
Hauck 先生说:“所有元件的尺寸、形状及其他细节都必须符合要求。
我们认为采用Moldflow模内流动性分析法具有最大的优越性,可以获得合适的浇口和冷却位置。
其所有的元件外观漂亮,零件的表面达到了A级水平。
对这些零件来说,美学是非常重要的。
正是这个原因,我们才与CAE Services公司合作。
”
Hauck先生承认,他无法确信这种分析方法是否可达到100%的精确。
Hauck先生说:“我当时希望我们能够获得约50%的精确度,浇口的二次加工和重复试验是必要的。
令我惊喜的是,初步获得的结果完全出乎意外。
不管采用什么分析,我们没有碰到任何问题。
”模拟的结果几乎100%的与真是结果相吻合。
为执行这个项目,Cessna公司愿意为Moldflow模内流动性分析法做出投资。
当Hauck先生及其团队表示他们能够满足Cessna公司的质量和美学要求时,CAE Services公司的工程设计经理Tim Lankisch先生清楚地表明,Moldflow模内流动性分析法可以帮助他们达到Cessna公司的要求。
因此,该客户同意增加费用。
项目的细节问题
为了执行这个项目,PM Mold公司与CAE Services公司签订了有关进行模具注入、包装和冷却分析的合同。
CAE Services公司独家使用Moldflow‟s Plastics Insight(MPI)模内流动性分析软件,用于零件和模具的深度设计模拟分析。
通过适当的学习、培训和彻底的了解模压成型工艺以及模具的设计和应用诀窍,MPI模内流动性分析软件可以精确地模拟塑料的流动性、包装、模具冷却、零件收缩率、热注塑、气体辅助注塑、共注吹塑,以及补偿注塑过程中造成的翘曲度。
关于这些项目,Lankisch先生这样说:“在工具受到限制的条件下,应确保其内部的均衡注入(图1)。
我们想要确定浇口的数量和位置,以及确定是否需要在不易看到的区域改变纹路。
”
图1 可见浇口的布置和流道尺寸的确定保证了均衡的注入
“分析费用是合理的。
”Hauck先生解释说,“为了执行Cessna公司的项目,采用Moldflow 模内流动性模拟方法可节省客户的二次重复加工等二次费用,以免零件模压成型后的元件
无法工作。
”他还说,这些分析是必要的,因为客户提出的生产时间比较紧迫,没有足够的时间对任何元件进行二次加工。
他补充说:“如果我们不得不使用传统的重复试验法,那么采用这种分析方法的费用显然要比前者少得多。
采用那种传统的策略必定会延长生产时间,这可能会造成客户的流失。
” Cessna公司的项目顺利地向着预定目标进展,没有出现任何问题,也没有延缓生产。
Hauck先生解释说:“客户十分高兴和满意,我们与他们之间的关系还在继续向前发展。
”
PM Mold公司与CAE Services公司的合作时间约6个星期,CAE Moldflow模内流动性分析专家共分析了约12个Cessna公司的零件。
Hauck先生说:“我们与CAE Services公司的合作非常愉快,所有专家的专业知识非常丰富,对我们的帮助很大。
”
“到目前为止,PM Mold公司自己还没有Moldflow模内流动性分析软件。
”Hauck先生说。
该公司可能会根据客户零件的要求购置这款软件。
从目前的情况来看,Hauck先生将根据过去的经验,决定什么时候通过外协来获得Moldflow模内流动性分析软件。
“如果零件是属于我们以前没有碰到过的新零件,或是零件的外观要求非常高,那么我们将会选用Moldflow模内流动性分析软件。
如果我们需要大批量生产高外观要求的模具,我们将会考虑采用这款软件。
”
做出的投资
对于那些不愿意为Moldflow模内流动性分析支付费用的客户,MP Mold公司的工程师们将与他们的客户讨论,共同确定浇口的位置。
“如果浇口的位置不够准确,PM Mold公司通常会为浇口的再次加工承担费用。
”Hauck先生说,“那种情况使我有更多的机会宣传Moldflow 模内流动性分析法。
”在模具制造后,改变浇口位置所需的相关费用约为1000~4000美元,这取决于零件和浇口的类型。
其他与这些问题相关的更加需要考虑的是影响其生产进度、劳务配置和机床超时工作的有关费用。
由于这些原因,越来越多的MP Mold公司客户都愿意为这种分析做出投资,当然这取决于不同的项目情况(图2)。
图2 冷却回路的效率可以通过冷却分析进行评价
“客户的早期介入对任何特定MPI项目的成功都十分关键。
我们不在真空中进行Moldflow 模内流动性分析。
对于模具应该如何制造,每家公司都有自己的规程。
然而,当你们互相合作时,您就能够以更快的速度解决问题。
”除了面对面的会谈之外,Lankisch先生与他的团队还会举行在线会议,保证使每个与项目有关的人员,在同一时刻集中讨论同一问题。
Lankisch先生解释说:“我们进行了几千次的模拟试验,有很好的理由认为,我们是Moldflow 模内流动性咨询领域的先驱。
我们能够进行快速而精确的分析,能够预见客户的需要,PM Mold公司也不例外。
”
从一个咨询公司的发展前景来看,Lankisch先生认为,对任何特定分析所要求的标准可以保证达到最佳的结果。
他说:“这个标准的大部分应归结于对期望值的管理。
像PM Mold 公司这样的新客户多次告诉我们,他们需要Moldflow模内流动性分析软件,但是他们不知道可以从结果中获得什么。
一般来说,他们的客户委托我们承办这项工作,即使他们并不知道分析数据会给他们带来些什么。
因此,我们有责任对我们的客户进行审核,并详细地了解他们希望从分析中获得一些信息。
”
CAE Services公司的销售副总裁Mark Solberg先生说:“我们的目标是…从第一次开始就做好一切事情。
‟这个方法最终为我们的客户节约了费用。
我们的首要目标是取消反复试验,降低客户的费用,创造价值。
为我们的客户创造价值就是我们最终的目标。
”
在竞争激烈的全球市场中,许多美国制造商的业务逐渐流向远东国家。
现在,PM Mold公司正在采取措施,以保证其目前的客户群。
该公司正在提供具有更高附加值的服务,如项目管理、Moldflow模内流动性分析,及对他们的产品提供技术支持。
Hauck先生最后总结说:“PM Mold公司将为其提供的所有产品和服务保证质量和价值,这就是他们工作的标准。
”(end)。