into操作手册
清洗机操作手册说明书
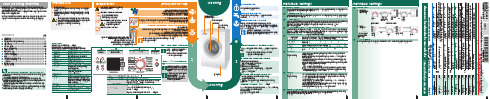
31.Activate thesetting mode for signal volume•1 step, the Press and +1 step, Set to •Button signalsInformation signalsSet the 1 stepSet the volume**you may need toselect the function several times.2.Set thevolume for ...skippage 10Detergent for main wash,water softener, bleach, stain remover fabric softener, starchdoor handleService flap**If the active Additional functions and options buttons Press WashingCancelling the programmeProgrammes at high temperatures:–Cool washing:–Press Programme selector for switching the machine on and off and for selecting the programme. Can be turned in either direction.All buttons are sensitive and need only to be touched lightly.Press and hold the option button for an automatic run8consumption consumptionTake care not to trap items of laundry between the washing machine door and the rubber seal.Laundry with varying degrees of soilinglight SoakingPour soaking agent/detergent into compartment selector to Starching Starching is possible in all wash programmes if liquid starch is used. Pour starch into the partment in accordance with the manufacturer's instructions (rinse first if necessary).10Cleaning the detergent drawer ...... if it contains detergent or fabric softener residues.ʑʑThis should not be necessary if the correct detergent dosage has been used. If it is necessary, however, proceed according to the descaling agent manufacturer's instructions. Suitable descalers can be obtained via our website or model-dependentDisconnect the mains plug .No solvents.11Detergent solution pumpTurn the programme selector to Drainage hose at the siphonTurn the programme selector to 1.2.Filter in the water supplyProduct number Production numberTrust the manufacturer's competence. Turn to us.You will thereby ensure that the repairs are performed by trained service personnel equipped with original spare parts.en operating instructionsWashing machine WAS32471SNObserve the safety instructions on page 8.Read these instructions and the separate installation instructions before operating the washing machine.page 10Detergent for main wash, water softener, bleach, stain removerfabric softener, starch3door handleService flap**If the active Additional functions and options buttons Press WashingCancelling the programmeProgrammes at high temperatures:–Cool washing:–Press Programme selector for switching the machine on and off and for selecting the programme. Can be turned in either direction.All buttons are sensitive and need only to be touched lightly.Press and hold the option button for an automatic run1.Activate thesetting mode forsignal volume• 1 step, the Press and + 1 step,Set to •Button signals Information signalsSet the 1 step Set the volume**you may need toselect the functionseveral times.2.Set thevolume for ...skipLaundry with varying degrees of soilinglightSoakingPour soaking agent/detergent into compartmentselector toStarchingStarching is possible in all wash programmes if liquid starch is used. Pour starch into thepartment in accordance with the manufacturer's instructions (rinse first if necessary).810Cleaning the detergent drawer ...... if it contains detergent or fabric softener residues.ʑʑThis should not be necessary if the correct detergent dosage has been used. If it is necessary, however, proceed according to the descaling agent manufacturer's instructions. Suitable descalers can be obtained via our website or model-dependentDisconnect the mains plug .No solvents.11Detergent solution pumpTurn the programme selector to Drainage hose at the siphonTurn the programme selector to 1.2.Filter in the water supplyProduct number Production numberTrust the manufacturer's competence. Turn to us.You will thereby ensure that the repairs are performed by trained service personnel equipped with original spare parts.en operating instructionsObserve the safety instructions on page 8.Read these instructions and the separate installationinstructions before operating the washing machine.。
支付宝英文操作手册
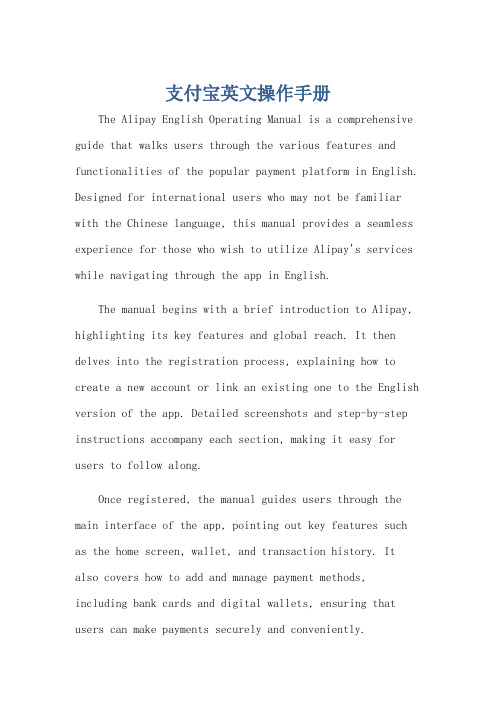
支付宝英文操作手册The Alipay English Operating Manual is a comprehensive guide that walks users through the various features and functionalities of the popular payment platform in English. Designed for international users who may not be familiar with the Chinese language, this manual provides a seamless experience for those who wish to utilize Alipay's services while navigating through the app in English.The manual begins with a brief introduction to Alipay, highlighting its key features and global reach. It then delves into the registration process, explaining how to create a new account or link an existing one to the English version of the app. Detailed screenshots and step-by-step instructions accompany each section, making it easy for users to follow along.Once registered, the manual guides users through the main interface of the app, pointing out key features such as the home screen, wallet, and transaction history. It also covers how to add and manage payment methods,including bank cards and digital wallets, ensuring that users can make payments securely and conveniently.The manual goes into detail about Alipay's various services, including online shopping, bill payments, and money transfers. It explains how to use Alipay to shop online, paying for goods and services securely with just a few clicks. It also covers how to use Alipay to pay bills such as utility bills and credit card payments, making it easier for users to manage their finances.For those interested in sending and receiving money, the manual provides a comprehensive guide to Alipay's money transfer features. It explains how to send money to friends or family, both domestically and internationally, as well as how to request money from others. The manual also covers Alipay's security features, such as face recognition and fingerprint payment, ensuring that users' transactions are protected at all times.In addition to its core features, the manual also introduces users to Alipay's loyalty programs and rewards system. It explains how to earn points and redeem them for discounts and special offers, helping users save money while enjoying the convenience of Alipay.Throughout the manual, emphasis is placed on the importance of security and privacy. Users are advised to keep their login information confidential and to regularly update their security settings to protect their accounts from unauthorized access.Overall, the Alipay English Operating Manual is an invaluable resource for international users who want to fully utilize the features and functionalities of the popular payment platform. With its detailed instructions and easy-to-follow screenshots, it provides a seamless experience for those who wish to navigate through Alipay in English.**支付宝英文操作手册详解**支付宝英文操作手册是一份全面指导用户以英文使用这款热门支付平台各项功能和特性的手册。
奇力速工業股份有限公司电动起子控制器操作手册说明书

電動起子控制器操作手冊OPERATION AND MAINTENANCE MANUALSKP-40BHL-800N(In: AC 115V/230V Out: DC 40V)奇力速工業股份有限公司KILEWS INDUSTRIAL CO., LTD.Important safety information enclosed.Read all these instructions before placing tool in service or operation this tool and save these instructions. It is the responsibility of theemployer to place the information in this manual into the hands of the operator. Failure to observe the following warnings could resultin injury. When using electric tools, Basic safety precautions should always be followed to reduce the risk of fire, electric shock andpersonal injury, including the following :1. Important Safety Instructions2. Operations Cautions3. Grounding Instructions4. Installation Instructions5. Specifications6. Servicing7. Steps to switch voltage was shown as below pictures :1Find the voltage switch on the backside of power controller (besure turn off poewr first)2 Release both screws and tack out the protect cover3 Move the red thick side to switch to the correct voltage4 Replace the protect cover and retighten both screwsWARNING!Read all instructions Failure to follow all instructions listed below may result in electric shock fire and/or serious injure. The term “power tool” in all of the warning listed below refer to your mains operated (corded) power tool or battery operated (cordless) power tool.SA VE THESE INSTRUCTIONS1) Electrical Safetya) Keep work area clean and well lit. Cluttered and dark areas invite accidents.b) Do not operate power tools in explosive atmosphere, such as in the presence of flammable liquids, gases or dust. Power toolscreat sparks which may ignite the dust of fumes..c) Keep children, and bystanders away while operating a power tool. Distractions can cause you to lose control.2) Electrical Safetya) Power tool plugs must match the outlet. Never modify the plug in any way. Do not use any adapter plugs with earthed(grounded) power tools. Unmodified plugs and matching outlets will reduce risk of electric shock.b) Avoid body contact with earthed or grounded surfaces such as pipes, radiators, ranges and refrigerators. There is an increased risk of electric shock if your body is earthed or grounded.c) Don’t expose power tools to rain or wet conditions. Water entering a power tool will increase the risk of electric shock.d) Do not abuse the cord. Never use the cord to carrying, pulling or unplugging the power tool. Keep cord away from heat, oil, sharp edges or moving parts. Damaged or entangled cords increase the risk of electric shock.e) When operating a power tool outdoors, use an extension cord suitable for outdoor use. Use of cord suitable for outdoor use reduces the risk of electric shock .3) Personal Safetya) Stay alert, watch what you are doing and use common sense when operating a power tool. Do not use power tool while you are tired or under the influence of drugs, alcohol, or medication. A moment of inattention while operating power tools may result in serious personal injury.b) Use safety equipment. Always wear eye protection. Safety equipment such as dust mask, non-skid safety shoes, hard hat, or hearing protection used for appropriate conditions will reduce personal injuries.c) Avoid accidental starting. Ensure the switch is in the off position before plugging in. Carrying power tools with your finger on the switch or plugging in power tools that have the switch on invites accidents.d) Remove any adjusting keys or wrench before turning the power tool on. A wrench or a key that is left attached to a rotating part of the power tool may result in personal injury.e) Do not overreach. Keep proper footing and balance at all times. This enables better control of the power tool in unexpected situations.f) Dress properly. Do not wear loose clothing or jewellery. Keep your hair,clothing, and gloves away from moving parts. Looseclothes, jewellery, or long hair can be caught in moving partsg) If devices are provided for the connection of dust extraction and collection facilitys, ensure these are connected and properly used. Use of these devices can reduce dust related hazards.4) Power tool Use and Carea) Do not force the power tool. Use the correct power tool for your application. The correct power tool will do the job better and safer at the rate for which it was designed.b) Do not use power tool if switch does not turn it on or off. Any power tool that cannot be controlled with the switch is dangerous and must be repaired.c) Disconnect the plug from the power source before making any adjustments, changing accessories, or storing the power tools. Such preventive safety measures reduce the risk of starting the power tool accidentally.d) Store idle power tools out of reach of children and do not allow persons unfamiliar with the power tool or these instructions to operate the power tool. Power tools are dangerous in the hands of untrained users.e) Maintain power tools. Check for misalignment or binding of moving parts, breakage of parts and any other condition that may affect the power tools operation. If damaged, have the power tool repaired before use. Many accidents are cause by poorly maintained power tools.g) Use the power tools, accessories and tool bits ect., in accordance with these instructions and in the manner intended for the particular type of power tool, taking into account the working conditions and the work to be performed. Use of the power tool for operations different from intended could result in a hazardous situation.5) SERVICEa) Have your power tool serviced by qualified repair person using only indentical replacement parts, This will ensure that thesafety of the power tool is maintained.Additional information shall be providea)Instruction for putting into use1.Setting-up or fixing power tool in a stable position as appropriate for power tools which can be mounted on a support.2.Assembly3.Connection to power supply, cabling, fusing, socket type and earthing requirements.4.Illustrated description of functions.5.Limitations on ambient conditions.6.List of contents.b)Operating Instructions.1.Setting and testing.2.Tool changing.3.Clamping of work.4.Limits on size of work piece.5.General instructions for use.c)Maintenance and servicing.1.Regular cleaning, maintenance, and lubrication.2.Servicing by manufacture or agent, list of addresses.3.List of user-replaceable parts.4.Special tools which may be required.1. Please read the operating manual thoroughly and comply with safety regulation to operate this Multi-Function Controller.2. Please grasp the plug of power cord while plugging in or out the plugs of connecting cord of Electric Screwdriver and powercord.3. Please fix the power controller to avoid any danger of pulling and dragging the power cord.4. Do not near oil, chemical materials or heated objects, also please be alert not to scratch the power cord by sharp object.5. This type of Controller can only be applied to Kilews Electric Screwdriver with Counter. Do not use Electric ScrewdriverController on other types of machinery.6. In case of the Controller is overheated or overloaded with maximum current rating of fuse, the high-speed fuse will be melt downand cut off the power. If the Controller continues to jump off or has an abnormal switching reaction, please stop the operation immediately and send back the Controller for repair.7. When Electric Screwdriver is running, if slides Forward/Reverse Switch instantly, device will generate the protection program toforce Electric Screwdriver stop.8. Please do not disassemble Electric Screwdriver casually and try to repair it by self.9. When Controller is not in use, please turn the main power switch OFF and unplug the power.10. The electric frequency will be lower when the voltage is adjusted as Lo or below 32V,so the torque of the electric screwdriverscan't be worked out except below scale of 4.WARNING!DO NOT OPERATE THIS TOOL WITHOUTPROTECTIVE EARTH CONNECTEDT he tool should be grounded while in use to protect the operator from electric shock. The tool is equipped with a three-conductor cordand three-prong grounding-type plug to fit the proper grounding-type receptacle. The green (or green and yellow) conductor in the cord is the grounding wire. Never connect the green (or green and yellow) wire to a live terminal.Green and yellow----- Earth Blue ------ Neutral Brown ------ Live1. Use the controller voltage recommended in the specification of this manul.2. When using a commercial power supply be sure to set up circuit and safety breakers. You must also properly ground the mechanisms.3. The temperature and humidity should be kept at appropriate levels.4. Do not set up the power supply in a room that has poor ventilation and where it may be exposed to dust and metallic flakes.5. Do not put heavy object on top of power supply or pile thing on it.6. Attach the power supply securely to a flat, stable surface. If the power supply is put ahigh place, take special care to ascertain that there is no danger of it falling.7. Keep bystanders away. Do not permit unauthorized personnel to operate this controller. 8. Do not set up the power supply near high voltage machinery or in an excessively noisyenvironment.9. Avoid setting up or storing the power supply in wet or oily environments or where it might be exposed to corrosive or flammable gases.10. We emphasize that the power supply should be placed in stable, fixed location.SA VE THESE INSTRUCTIONThe use of other than genuine KILEWS replacement parts may result in decreased controller performance and increased maintenance, and may invalidate all warranties.NOTICEMaintenance and Inspection :1. The controller must be operated in top condition, one day working hour must be not more than eight hours.2. Please note don’t let the controller get over heated, every minute use 10~15 screws to operate.3. The frequency use of this electric screw driver is over eight hours a day, still it needs periodically testing and treatment. Every 5-6 months.ModelSKP-40BHL-800NInput AC 115V / 230V / 6.3A 50/60HzOutput DC 40V/30V , 9A/360WDuty Cycle 1s ON / 3s OFFPower Consumption 360W Outside Dimensions (mm)213*133*68(mm) Weight(kg)1.8 (main body)Suitable ModelSKD-TBK30LF ;SKD-TBK35LF ;SKD-TBK50LF ;SKD-TBK70L SKD-TBN60L ;SKD-TBN90L ;SKD-TBN120L ;SKD-TBN180LSKD-RBK60;SKD-RBK90;SKD-RBK120;SKD-RBK180;SKD-RBK120F ;SKD-RBK180F ;SKD-RBK250;SKD-RBK250F ;SKD-RBK350;SKD-RBK500SKD-BK960;SKD-BK960F ;SKD-BK990;SKD-BK9120SKD-TBNK30LF ;SKD-TBNK35LF ;SKD-TBNK50LF ;SKD-TBNK70L SKD-TBNK60L ;SKD-TBNK90L ;SKD-TBNK120L ;SKD-TBNK180L SKD-RBNK60;SKD-RBNK90;SKD-RBNK120;SKD-RBNK180 SKD-RBNK120F ;SKD-RBNK180F ;SKD-RBNK250;SKD-RBNK350;SKD-RBNK500 SKD-BNK960;SKD-BNK960F ;SKD-BNK990;SKD-BNK91201.The use of other than genuine KILEWS replacement parts may Result in decreased tool performance and increasedmaintenance, and may invalidate all warranties.2.All repairs and maintenance of this tool and its word must be performed by an authorized service center.3.KILEWS is not responsible for customer modification of tools for applications on which KILEWS was not consulted.4.Repairs should by made only by authorized, trained personnel. Consult your nearest KILEWS authorized service center.5.It is the responsibility of the employer to place the information in this manual into the hands of the operator.DO NOT ATTEMPT TO REPAIR THIS EQUIPMENTAll repairs and maintenance of the Controller and its cordmust be performed by authorized service centerCAUTIONSA VE THESE INSTRUCTIONSDO NOT DESTROY操作前請閱讀全部說明(內附零件分解圖)警 告為了安全起見,在使用電動螺絲起子控制器前請詳閱電動螺絲起子控制器操作說明書,且務必依照說明書指示操作,並注意所有的警示重要安全說明事項1. 使用電動螺絲起子控制器說明書規定的電壓。
72-9185 TENMA AC电流紧贴式测量器操作手册说明书

72-9185TENMA AC CURRENT CLAMPOPERATOR’S MANUALPlease read this manual and all important safety information before switching the unit on.SAFETY NOTES:•Do not exceed the maximum allowable input range of any function.•Set the function switch OFF when the meter is not in use.INTRODUCTIONThe AC A Current Clamp is a transducer which will allow your AC Voltage multimeter to measure electrical current up to 400 amps AC, with a frequency response to 50/60Hz. When measuring current with this clamp, there is no need to break a circuit or to affect the isolation.NOTE: Keep the clamp jaw fully closed to ensure the correct readings during current test.APPLICATION PROCEDURES1. Insert the black banana plug into the COMjack and the red banana plug into the V jackof any multimeter with a minimum inputimpedance of 10k ohms.2. Set the power switch from “OFF” to thedesired range, 4A (output: 100mV/A) 40A(output: 10mV/A) or 400A (1mV/A) position.The green LED will light to indicate that theclamp is switched on.3. For current measurement below 4A, set theunit to 4A range and set the multimeter to400mV or 600mV AC range for AC currentmeasurements.4. Clamp the jaws around the current-carryingconductor and interpret the readingaccording to Step 3 above.5. When 40A range of clamp unit is selected,the measured current value in A.For example, if the multimeter reads 100mV, the measuredcurrent is 100mV/(10mV/A)=10A.When 400A range is selected, the measured current value in A. For example, if the multimeter reads 100mV, the measured current is 100mV/(1mV/A)=100A.Non-Contact AC Voltage Measurements1. Touch the probe tip, near the jaw opening, to ornear the suspected hot conductor or insert into thehot side of the electrical outlet.2. If AC voltage is present, the detector LED willilluminate.NOTE: The conductors in electrical cord sets areoften twisted. For best results, rub the probetip along a length of the cord to assureplacing the tip in close proximity to the liveconductor.NOTE: The detector is designed with high sensitivity.Static electricity or other sources of energymay randomly trip the sensor. This is normaloperationOPERATOR SAFETY1. Do not clamp around conductors withvoltages equal to or exceeding 600V DC or 600V rms AC.2. To avoid physical injury, never conductmeasurements on bare conductors or conductors with cracked or frayed insulator.SPECIFICATIONSGENERALCaptured Conductor Size: Φ30mm maximum Operating Temperature: 0°C to 50°C, 70% R.H. Storage Temperature: -20°C to +70°C, 80% R.H. Battery Type: Two “AAA” 1.5V BatteryELECTRICAL (At 23±5°C, 70% R.H. maximum) Effective Measurement Range4A (output: 100mV/A): rms AC for 400mV or 600mV range of the multimter.40A (output: 10mV/A): rms AC for 400mV or 600mV range of the multimter.400A (output: 1mV/A): rms AC for 400mV or 600mV range of the multimeter.AccuracyCurrent Clamp Accuracy:AC range : 4A (50/60Hz)0~4.00AAC: ± (2.5% +0.1A)ACA range: 40A (50/60Hz)0~40.0AAC: ± (2.5% +0.1A)ACA range: 400A (50/60Hz)0~400AAC: ± (2.8% +0.5A)SAFETY INFORMATIONThe instrument complies with class II, overvoltage CAT III - 600V of the EN 61010-1, and EN 61010-2-032 stardards. Pollution degree 2 in accordance with IEC 664 indoor use. If the equipment is used in a manner not specified, the protection provided by the equipment may beimpaired.72-9185。
Decanter安全指南和操作手册说明书

2Safety instructions2.1GeneralRead these safety instructions and this manual carefully before attempting to start, operate or service the decanter.Failure to comply with these safety instructions and this manual can result in serious injury or death, property damage and/or damage to the decanter.The decanter must be operated, cleaned, dismantled and/or assembled only by trained personnel who are over the age of 18 and have read and fully understand the instructions in this manual.2.2Limitations of Use••If the decanter is operated with flammable, toxic or hazardous process media, it is the plant operator’s responsibility to ensure that the installation and operational procedures take into account all hazards associated with this operation.•The decanter must not be operated at feed temperatures outside the limits stated in the technical specification for the decanter and marked on the nameplate for the decanter.•The decanter must not be operated at a speed exceeding the maximum speed stated in the technical specification for the decanter and marked on the nameplate for the decanter.•The decanter must not be operated at full bowl speed if the density of the compacted wetted solids phase exceeds the value stated on the nameplate of the decanter. If the decanter is used to separate high-density solidmatter, the operating speed must be reduced according to separateinstructions, which must be obtained from Alfa Laval.2Safety instructions2.3Potentially Explosive AtmosphereATEX decanters comply with the European ATEX directive 94/9/EC and is clearly marked with an Ex plate located next to the decanter name plate.The Ex plate marking is used to identify the ATEX category of compliance and intended zone of operation. See the table below.Marking on EX plate II 2G IIB b c T3II 3G IIB c T3 ATEX category Category 2 - Gas Category 3 - GasAllowed in Zone 1 and 2Zone 2•The ATEX declaration of conformity for the decanter only covers the decanter in the original configuration as delivered from Alfa Laval.•The user of the decanter must have a formal routine for regular cleaning and visual inspection of the condition of the decanter for faults andleakages. Any build-up of solids in the decanter casing must be removed.•Maintenance work on the decanter in any zone must under no circumstances be carried out before it is ensured that an explosiveatmosphere does not exist at the work place. This must be ensured by the user with a “permission to work” system. The work permit system must also specify when and how the maintenance work can be safely carried out.•For decanters processing flammable feed it is not allowed to disassembly or remove any of the decanter covers or other parts of the decanter before it is ensured by purging and ventilation that an explosive atmosphere does not exist inside or in the vicinity of the decanter.•The decanter must not be modified in any way and only correct original spare parts must be used.Safety instructions2 2.4Installation Requirements•Do not attempt to start the decanter before the decanter has been installedaccording to the requirements in the installation manual for the decanterand compliance with such requirements has been verified.•Ensure that piping, funnels and their connections are closed and securedbefore the decanter is put into operation.•Ensure that the voltage and frequency of the electrical motors and electricalequipment corresponds to the information given in the technicalspecification and the labels on the equipment.•Ensure that the main and back drive motors are rotating in the correctdirection. The direction of rotation for the decanter rotor is indicated byarrows on the decanter.•If drive motors are replaced or reconditioned, check that the voltage andfrequency of the reconditioned or new motor corresponds to the data for theoriginal motor as stated in the technical specification.•Always confirm that the operating bowl speed of the decanter correspondsto the technical specification of the decanter.•Check all warning and alarm functions of the control system regularly andat least once a year.2Safety instructions2.5Starting and Operating the Decanter•Before any instance of starting the decanter, inspect the decanter to confirm that it is in good working condition as specified in this Section.•Do not start or operate the decanter if damage or severe wear is observed on any of the rotating components, the cover, decanter frame, the electrical components or other critical parts.•Do not start or operate the decanter if the insulation on the electrical cabling is damaged or if any electrical connections are loose.•Do not start the decanter before all covers and guards are closed and properly secured according to the instructions.•Do not start the decanter before connections for feed to the decanter and the outlets from the decanter are closed and secured.•Do not start or operate the decanter with open outlets, or with outlet openings that are accessible by hand, as process material may leave the decanter at high speed and at high temperature.•Do not start the decanter with frozen or hard material in the decanter as it can create heavy unbalances.•Do not operate the decanter with vibration levels exceeding the limit values stated in this manual.•Do not operate the decanter with bearing temperatures exceeding the temperature limits in this manual.•Always use hearing protection in proximity to an operating decanter. The sound pressure level at the decanter can exceed the limits for long time exposure 80 dB(A) and short time exposure 85 dB(A).•Do not operate the decanter at full speed for more than 2 hours without feeding product or flushing with water since this may cause heating of the decanter, and in some cases unforeseen wear to the decanter.•Always reduce the main speed of the decanter and the differential speed of the decanter if the decanter for practical reasons cannot be completelystopped and will run in idle mode without feed.•Never start the feed pump or flush the decanter before opening the discharge valves or starting the discharge pumps, including any conveying means for the liquid and solids phases.•Immediately stop feed flow to the decanter if discharge pumps or conveying means for the liquid and solids phases leaving the decanter are stopped, or any of the outlets from the decanter are blockedSafety instructions2 2.6Stopping the Decanter•Always stop the decanter using the normal controlled stop and ensure thatall solids inside the decanter bowl are scrolled out since this may otherwisecreate a heavy unbalance when the decanter is next started.•The use of emergency stop should be limited to emergency situations only..•If the decanter is stopped as an emergency or by an alarm or power failure,be aware that solids can be present inside the bowl that can create a heavyunbalance at the next start. I can be required to dismantling of the bowl forcleaning before next start.•Note that due to the high moment of inertia it can take 15 minutes or morebefore a decanter comes to a complete stand still. Do not open or removecovers before ensuring that the decanter is at a complete stand still,electrically isolated, locked and clearly marked. See Section Disassemblyand Assembly.2.7Maintaining the Decanter•The instructions for regular maintenance, cleaning and lubrication of thedecanter must always be followed.•The decanter installation must be checked on a regular basis according tothe Maintenance section of this manual.•All warning labels on the decanter must be in good condition and replacedif they are damaged.•The nameplate on the decanter must be in good condition and replaced if itis not legible or is no longer securely attached to the machine.•All parts of the rotating assembly must be regularly inspected for wear andtear and kept in perfect condition. This includes, but is not limited to, allbowl parts, all bolted connections on the bowl, the gearbox adapterconnection and the conveyor. The inspections should occur no lessfrequently than the intervals set forth in the maintenance tables in thismanual. See Section Maintenance.•If visible wear, corrosion or cracks are observed on any of the bowlassembly parts, the decanter shall be stopped immediately and the plantoperator shall contact Alfa Laval for maintenance to ensure that theequipment can be operated safely. Inspection for wear and tear isincreasingly important the longer that the decanter is in operation.2.8Disassembly and Assembly•Do not attempt disassembly until the decanter has come to a completestand still, the main power is shut off, and the disconnected main switch islocked with a safety lock.2Safety instructions•Verify with the plant operator whether the decanter or rotating assembly contains process material which can be a health risk, and ensure that any waste can be safely handled and disposed.•Follow general safety instructions for workshop and use the required personal protection equipment.•Never work on a hot decanter. Surface temperatures must be below 40°C/ 104°F and all parts must have had enough time to cool down beforedisassembly is started.•Use designated lifting tools with the correct lifting capacity for lifting bowl, conveyor, frame and entire decanter.•Lift all parts from their balance points and ensure that lifting slings cannot slide or move during lifting.•Slings may be used for short distance lifts in a workshop but general safety rules for slings must be followed and slings must have the correct lifting capacity. Under no circumstances should slings be wrapped around bearing housings or paring disk parts.•Always use protective gloves and be observant when disassembling the decanter. The decanter parts may have sharp edges due to wear.•Always use eye protection when removing the gearbox oil plug or opening the gearbox in the event the gearbox has overpressurised.2.9Repair•Major repairs to the decanter must not be made without first consulting Alfa Laval. In no circumstances should weld repairs, or other alterations bemade to bowl shells, bowl hubs, gearbox adapter, shafts, or other rotating parts without prior written approval and instructions from Alfa Laval.•Alfa Laval will not be responsible for any injury to persons or damage to property if genuine parts are not used for the decanter.•Alfa Laval cannot be held responsible for any injury to persons or damage to property if unauthorized repairs are made to the decanter.•Interchange of bowl parts may affect balancing condition of the decanter and must only be carried out by specialists from Alfa Laval and with original parts.。
OMRON NB-series 可编程终端操作说明手册说明书
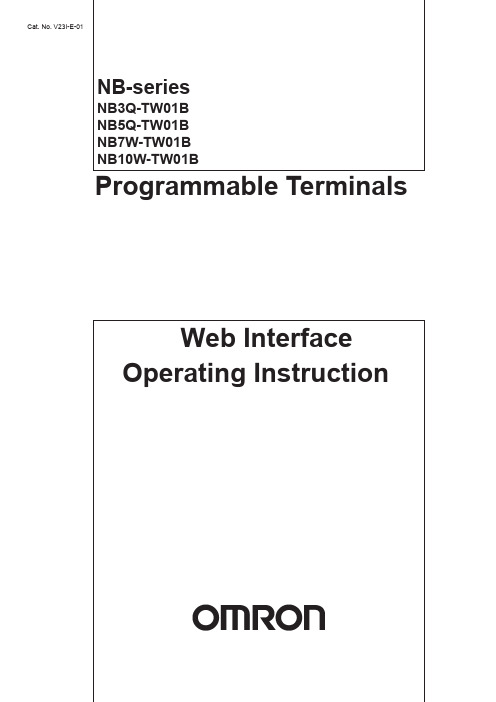
Cat. No. V23I-E-01NB-seriesNB3Q-TW01BNB5Q-TW01BNB7W-TW01BNB10W-TW01BProgrammable Terminals©OMRON, 2013All rights reserved. No part of this publication may be reproduced, stored in a retrieval system, or transmitted, in any form, or by any means, mechanical, electronic, photocopying, recording, or otherwise, without the prior written permission of OMRON.No patent liability is assumed with respect to the use of the information contained herein. Moreover, because OMRON is constantly striving to improve its high-quality products, the information contained in this instruction is subject to change without notice. Every precaution has been taken in the preparation of this instruction.Nevertheless, OMRON assumes no responsibility for errors or omissions. Neither is any liability assumed for damages resulting from the use of the information contained in this publication.NB-seriesNB3Q-TW01BNB5Q-TW01BNB7W-TW01BNB10W-TW01BProgrammable TerminalsWeb Interface Operating Instruction Manual September 2013IntroductionThis instruction describes only the configuration and settings required to use NB Web Interface.Please be sure to read and fully understand related manuals including NB-series manual beforeusing the NB series Programmable Terminal, and read this instruction when using NB Web Interface.Copyright and TrademarkSystem names and product names used in this instruction are the trademarks or registeredtrademarks of their respective companies.Notation and TerminologyIndicate the additional information on operation, descriptions or settings.2NB-series Programmable Terminals Web Operating Instruction Manual (OMSQ-ISV(01) 0362(3/21)ContentsIntroduction (2)Contents (3)1 Overview (4)1-1 What is NB Web Interface? (4)1-2 What NB Web Interface Can Do (5)1-3 Operating Environments (6)1-3-1 Necessary NB Series Configuration (6)1-3-2 Necessary Network Environments (6)1-3-3 Necessary Web Browser (6)2 Using NB Web Interface (7)2-1 Connection Method (7)2-1-1 PT Settings (7)2-1-2 Connecting a Web Browser to a PT (7)3 The Functions of NB Web Interface (9)3-1 A List of the Functions of NB Web Interface (9)3-2 Menu Screen (10)3-3 Monitor Screen (11)3-3-1 Monitor Screen (11)3-3-2 Updating a Screen Display (11)3-3-3 Specifying the Display Image Format of the Monitor Screen (12)3-3-4 Not Using the User Authentication (12)3-4 Operation Screen (13)3-4- 1 Operation Screen (13)3-4-2 Reloading Screen Display (14)4 NB Web Interface Settings (15)4-1 NB Web Interface Settings (15)4-1-1 Configuration Screen (15)4-1-2 NB Web Interface Settings (16)5 Authentication settings (18)5-1 Change user name and password (18)5-2 Default user name and password Restoration (18)6 Troubleshooting (19)6-1 Error Messages (19)Revision History List (20)NB-series Programmable Terminals Web Operating Instruction Manual(OMSQ-ISV(01) 0362(3/21))31 OverviewThis section describes an overview of the functions of NB Web Interface. This also describes the OperatingEnvironments for NB Web Interface.1-1 What is NB Web Interface?NB Web Interface is a function that monitors a screen that an NB-series HMI displays using a web browser on apersonal computer connected via Ethernet to an NB-series HMI (Programmable Terminal called “the PT”).NB Web Interface has the following functions.Monitors a PT screen at the site using a web browser.Operates a PT screen at the site using a web browser.4NB-series Programmable Terminals Web Operating Instruction Manual (OMSQ-ISV(01) 0362(3/21)1-2 What NB Web Interface Can DoThis section contains the usage examples of NB Web Interface.Remote MonitoringNB Web Interface allows users to check error and alarm details displayed on the PT by accessing the enduser’s PT from a web browser. Also when users instruct an operator, users can check work done by theoperator using a web browser.Remote OperationUser can access the PT using a web browser. From a web browser, it is possible to remote control the PT. NB-series Programmable Terminals Web Operating Instruction Manual(OMSQ-ISV(01) 0362(3/21))51-3 Operating EnvironmentsThe following shows the system configuration for connecting a PT on a network to a personal computer usingNB Web Interface.1-3-1 Necessary NB Series ConfigurationNB-series PT ModelsAny of the following NB-series is required to use NB Web Interface.NB Model Lot No.09X13M or aboveNB3Q-TW01BNB5Q-TW01BNB7W-TW01BNB10W-TW01BWhen the NB model above do not have web server function, please use NB-Manager version 1.30 or above toupdate the kernel and file system, for operation detail, please refer to [4-4 System Operate] of NB seriesNB-Designer Operation Manual.NB Designer VersionThe following version of the system program must be installed in your NB-series in order to use the NB WebInterface.NB Designer Version ( including NB Manager)Version 1.30 or later*In the NB-Manager, if there is “Web Interface Operation” option on the left side, it means this NB-Managersupports web server function.*For download the application programs, please access your local Omron website, If local site cannot be found,please access Omron IA global site "/ "at first and select the area where you are.1-3-2 Necessary Network EnvironmentsYour NB-series must be able to be connected to a personal computer via one of the following Ethernet standardin order to use the NB Web Interface.Standard10Base-T or 100Base-TX1-3-3 Necessary Web BrowserThe following web browsers can show a PT screen on a personal computer.Web browserMicrosoft Internet Explorer Ver.8Microsoft Internet Explorer Ver.9Safari (IOS.6x)6NB-series Programmable Terminals Web Operating Instruction Manual (OMSQ-ISV(01) 0362(3/21)2 Using NB Web InterfaceThis section explains how to connect a PT to a web browser on a personal computer using NB Web Interface.2-1 Connection MethodThis section explains a PT how to connect to a web browser on a computer using NB Web Interface. This document uses Windows 8 and Microsoft Internet Explorer Ver.9 as an example. For details on the operating system, the setting of the web browser and operation methods, refer to manuals for each product.2-1-1 PT SettingsTo use NB Web Interface, the following settings must be made in the project of NB.1. Use NB-Designer, open the project which will be download to the PT, add bit button component in theframe, set type to “Alternate” in the bit button property, and set the address to LB9175. 2. Compile and download the project to PT.3. Click the bit button on the PT to switch ON of address LB9175.2-1-2 Connecting a Web Browser to a PTThis section explains how to connect a Web Browser to a PT. 1. Start a web browser. 2. Input the following URL.http://(PT IP Address)/For example, when the PT IP Address is “192.168.0.1”:to 3 The Functions of NB Web Interface .ScreenURLMonitor Screen http://(PT IP Address)/monitor.html Operation Screen http://(PT IP Address)/operation.html Configuration Screen http://(PT IP Address)/config.html Menu Screenhttp://(PT IP Address)/menu.html3. The login screen will be displayed.7NB-series Programmable Terminals Web Operating Instruction Manual (OMSQ-ISV(01) 0362(3/21))ReferenceThe NB Web Interface login uses the Basic Authentication defined by the HTTP.It is possible to set whether to use the user authentication login screen or not when displaying Monitor Screen. Refer to 4 NB Web Interface Settings for the settings. 4. Enter the user name and password.The factory settings for the user name and password are as follows.User name default PassworddefaultReferenceThe user name and password can be changed by NB-Manager, for details please refer to 5 Authentication settings .5. ClickOK Button. The menu screen will be displayed.Item DescriptionMonitorMonitors the screen currently displayed on the PT . OperationMonitors the screen currently displayed on the PT .Operates the PT screen by mouse clicking the web browser.Configuration Make settings related to NB Web Interface.Details on each screen are explained in 3 The Functions of NB Web Interface .ReferenceThe initial screen can be changed by setting. For details on the setting, refer to 4 NB Web Interface Settings .NB-series Programmable Terminals Web Operating Instruction Manual (OMSQ-ISV(01) 0362(3/21)83 The Functions of NB Web InterfaceThis section explains the functions of NB Web Interface.3-1 A List of the Functions of NB Web InterfaceNB Web Interface has the following functions (screens).Detail ContentMenu screen The menu screen of NB Web Interface.Monitor screen Monitors the screen currently displayed on the PT.Operation screen Monitors the screen currently displayed on the PT.Also operates the PT screen by mouse clicking the web browser.Configuration screen Make settings related to NB Web Interface.ReferenceFor Configuration screen, refer to 4 NB Web Interface Settings.The Menu screen displays the following screen.ItemDescriptionMenu screenDisplays a list of the NB Web Interface screens. Clicking will jump to each screen.Microsoft product screen shot(s) reprinted with permission from Microsoft Corporation.3-3-1 Monitor ScreenThe Monitor screen is used to display a PT screen.It displays the screen as follow. (e.g.)No.Item Description1Monitor Screen Displays a PT screen.2Latest Captured Displays the date and time when a PT screen was read. ReferenceA PT screen cannot be operated with the Monitor screen.To operate a screen, please enter into the Operation screen.To hide the Latest Captured time, should be set in configuration page. For details on the setting, refer to 4 NB Web Interface Settings.3-3-2 Updating a Screen DisplayThe Monitor Screen periodically reads a screen displayed on the PT and updates the screen in a certain interval set in the Configuration screen. (Default: 15 seconds) For details on the setting, refer to 4 NB Web Interface Settings.3-3-3 Specifying the Display Image Format of the Monitor ScreenNB Web Interface displays a Windows BMP, JPEG or PNG format image of a PT screen on a web browser. To select one of the formats, make a setting in the Configuration screen.ReferenceThe display picture format settings in the Configuration screen will also be used for the Operation screen. 3-3-4 Not Using the User AuthenticationIt is possible to set whether or not to use the user authentication (Login screen display) when directly specifying a URL to open the Monitor screen. For details on the setting, refer to 4 NB Web Interface settings.3-4 Operation Screen3-4-1 Operation ScreenThe Operation screen is used to display the PT screen and operate the screen. The Operation screen displays the following screen. (e.g.)Item DescriptionOperation screenDisplays the PT screen.Allows the user to operate the PT screen by clicking the web browser.ReferenceIt is possible to prohibit operating the PT screen from the PT while operating the PT screen from the Operation screen. For details, refer to 4 NB Web Interface Settings .3-4-2 Reloading Screen DisplayThe Operation screen periodically reads a screen displayed on the PT and updates the display. The reload interval can be set in the Configuration screen (Default: 3 seconds).It is also possible to set the time from when the user mouse clicks until the Operation screen reads a PT screen and updates the display. (Default: 1 second).For details on the setting, refer to 4 NB Web Interface Settings.ReferenceThe Reload Interval in the Monitor screen and Reload Interval in the Operation screen are independent from each other. Thus, they must be set separately.4 NB Web Interface SettingsThis section explains the NB Web Interface settings.4-1 NB Web Interface Settings4-1-1 Configuration ScreenThe Configuration Screen is used to make settings for NB Web Interface. 1. Display the Configuration screen.No. Item Description1 Setting Items Settings for NB Web Interface.For details on the settings, refer to 4-1-2 NB Web Interface Settings . 2 apply Reflects the setting changes in NB Web Interface. 3 save Reflects the setting changes in NB Web Interface. Also saves those changes in the PT. 4 default Returns all settings to the default settings.5resetCancels the setting changes currently being input, and returns to the settings before change.(return to the last valid settings)2. Set each item, then click apply or save button.3. A window stating of configuration done is displayed.4. When three seconds elapsed after “Configuration Done” screen is displayed, the window automaticallydisplays a screen set for Initial Page.4-1-2 NB Web Interface SettingsSetting items in the Configuration screen are explained here.Monitor SettingItem Description Correspondingscreen Reload Interval Set the time from when the Monitor screen reads a PT screenuntil when it next reads the NB screen. Between 2 and 99seconds can be set. (Default: 15 seconds)Monitor screenDisplay Pic Format Set which images format used when a PT screen istransferred. There are three formats can be select: BMP, JPEGand PNG. (Default: BMP)-Checked: Use-Unchecked: Not useWhen PNG images are used, user can set the compressionlevel for PNG formats in the option “Compression Level”.Monitor screen, Operation screenPNG Compression Level Set the compression level for creating PNG data. Between0(Compression non destructive) and 8(Highest compressionrate) can be set. (Default: 3)Only enable when selected PNG format in “Display PicFormat”.Monitorscreen,OperationscreenDisplay Date and Time Set whether to display the date and time when the PT scre enis captured on the bottom of Monitor screen. (Defau lt:Selected)-Checked: Displayed-Unchecked: Not displayedMonitor screenUse Authentication Set whether to use the user authentication or not whenspecifying a URL for Monitor screen. (Default: Unchecked)-Checked: User authentication used-Unchecked: User authentication not usedMonitor screenOperation SettingItem Description CorrespondingscreenReload Interval Set the time from when Monitor screen reads an NB screen t owhen it reads the next NB screen. Between 2 and 99seconds can be set. (Default: 3 seconds)Operation screenDelay After Click Set the time from when mouse is clicked to when an NBscreen is read. Between 0 and 99 seconds can be se t.(Default: 1 second)Operation screenDisable Touch Panel Set whether or not to accept inputs at the PT while theOperation screen is being shown. (Default: Unchecked)-Checked: Not accept touch inputs-Unchecked: Accept touch inputs Operation screen refer :note1note1: If user checked “Disable Touch Panel” option and entered the operation screen in browser then disconnect Ethernet cable, NB will waiting 5min for touch control restoration.Server SettingItem Description Correspondingscreen Page Title Set the web page title of up to 64 characters. (Default: NBWeb Interface name and its version) Only support ASCII.All screensInitial Page Set a screen shown when “http://(PT IP address)/” is specifiedas a URL and when the Configuration screen is clos ed.(Default: Menu)-TCP Port Specify the TCP port number that NB Web Interface u ses.Port numbers 80, 8080, and between 49152 and 65535 ca nbe input. (Default: 80)When this setting is changed, NB Web Interface will cut theconnection, and wait to connect using the specified portnumber.Note: Safari browser cannot use 65535 for port number.All screensUser JavaScript Set whether to use JavaScript for screen reloading andscreen operation. (Default: Checked)-Checked: Use-Unchecked: Not use Monitor scre en, Operation screenReferenceIf an invalid value such as a value out of the range is inputted in any fields in the Configuration screen and the “apply” or “save” button is clicked, the value before change will be set in the corresponding fields. If the TCP Port setting is changed, NB Web Interface will cut the connection temporarily. Specify a port number and re-connect from a web browser.For example, specify a URL as follows:When the PT IP Address is 192.168.0.1 and the set port number is 8080. The URL should be input in browser is: http://192.168.0.1:8080/ (Input “:port number” after the IP address). If 80(default) is set as the port number, it don’t needs to be specified.5 Authentication settings5-1 Change user name and password1. Connect NB terminal to PC then open NB-Manager.2. In NB-Manager select “Web Interface Operation” on the left side, the setting page will be displayed on theright side.3. Input new user name, password, confirm password and click “Save Set”, the new login data has beenregistered in NB.Note: 1. Maximum length of user name and password is 32 char.2. User name and password only support English letters and Arabic numerals.ReferenceFor connecting NB with PC, please refer to chapter 2-3 Connecting of NB-series with PC of NB series Setup Manual.5-2 Default user name and password RestorationIf user wants to restore the default user name and password just click “Default” button then click “Save Set”button.Default login data:User Name defaultPassword default6 TroubleshootingThis section explains the troubleshooting measures when errors occur in NB Web Interface.6-1 Error MessagesThis section describes error messages displayed during using NB Web Interface and their countermeasures.Message Cause Countermeasure401 Authorization Required In the user authentication screen, anincorrect user name or password is entered.Enter the correct user name and password.404 Not Found The specified URL is incorrect.Specify the correct URL.NB Image Cannot properly transfer image data from thePT to a web browser. This occurs due to anexcessive network load or with som ebrowsers.Click Refresh Button on the web browser.Cannotfind server or DNS error An attempt was made to connect to a PTmodel that does not support the NB WebInterface.Cannot connect to a model that does no tsupport the NB Web Interface. Forinformation on models that support the NBWeb Interface, refer to 1-3-1 Necessary NBSeries Configuration.Not set bit register LB9175 to ON.Set bit register LB9175 to ON.The specified IP address in a URL isincorrect.Check the PT IP address. Then specify thecorrect IP address.Othererror messages An excessive load is applied to the networkor PT.Wait a while and try again.19NB-series Programmable Terminals Web Operating Instruction Manual(OMSQ-ISV(01) 0362(3/21))Revision History ListRev Date Revision contents1.002013-09-3 Original Production20NB-series Programmable Terminals Web Operating Instruction Manual (OMSQ-ISV(01) 0362(3/21)Terms and Conditions of SaleCertain Precautions on Specifications and UseOMRON CANADA, INC. • HEAD OFFICEToronto, ON, Canada • 416.286.6465 • 866.986.6766 • OMRON ELECTRONICS DE MEXICO • HEAD OFFICEMéxico DF • 52.55.59.01.43.00 •01-800-226-6766•**************OMRON ELECTRONICS DE MEXICO • SALES OFFICEApodaca,N.L.•52.81.11.56.99.20•01-800-226-6766•**************OMRON ELETRÔNICA DO BRASIL LTDA • HEAD OFFICE São Paulo, SP , Brasil • 55.11.2101.6300 • .brOMRON ARGENTINA • SALES OFFICE Cono Sur • 54.11.4783.5300OMRON CHILE • SALES OFFICE Santiago • 56.9.9917.3920OTHER OMRON LATIN AMERICA SALES 54.11.4783.5300Authorized Distributor:V23I-E-01 04/14 Note: Specifications are subject to change. © 2014 Omron Electronics LLC Printed in U.S.A.Automation Control Systems• Machine Automation Controllers (MAC) • Programmable Controllers (PLC) • Operator interfaces (HMI) • Distributed I/O • Software Drives & Motion Controls• Servo & AC Drives • Motion Controllers & Encoders Temperature & Process Controllers • Single and Multi-loop ControllersSensors & Vision• Proximity Sensors • Photoelectric Sensors • Fiber-Optic Sensors • Amplified Photomicrosensors • Measurement Sensors • Ultrasonic Sensors • Vision SensorsIndustrial Components• RFID/Code Readers • Relays • Pushbuttons & Indicators• Limit and Basic Switches • Timers • Counters • Metering Devices • Power SuppliesSafety• Laser Scanners • Safety Mats • Edges and Bumpers • Programmable Safety Controllers • Light Curtains • Safety Relays • Safety Interlock SwitchesOMRON AUTOMATION AND SAFETY • THE AMERICAS HEADQUARTERS • Chicago, IL USA • 847.843.7900 • 800.556.6766 • OMRON EUROPE B.V. • Wegalaan 67-69, NL-2132 JD, Hoofddorp, The Netherlands. • +31 (0) 23 568 13 00 • www.industrial.omron.eu。
Parker产品操作手册说明书

Operating ManualThank you for your choice of Parker product. Please read this operating manual carefully and use the product correctly. Keep this operating manual in case questions arise about this product in the future. If this operating manual becomes unreadable or lost, consult our distributors or Parker sales offices.For Safety UseThe following safety precautions are provided to prevent damage and injury to personnel and to provide instructions on the correct usage of this product. These precautions are classified into 3 categories: “CAUTION”, ”WARNING”, and “DANGER” according to the severity of possible injury or damage and the likelihood of such injury or damage. Be sure to comply with all precautions. Also comply with safety regulations such as JIS B 8370(*1), Industrial Safety and Health Law, and High Pressure Gas Safety Law, and ISO 4414(*2).Danger:Indicates an impeding hazardous situation whichmay arise due to improper handling or operationand could result in serious personal injury or death.Warning:Indicates a potentially hazardous situation which may arise due to improper handling or operationand could result in serious personal injury or death.Caution:Indicates a potentially hazardous situation which may arise due to improper handling or operationand could result in personal injury or property-damage-only accidents.*1 JIS B8370 : General Rules for Pneumatic Systems*2 ISO 4414: Pneumatic fluid power recommendations for the application of equipment totransmission control system.● This product is designed for air blowgun.Do not use it for other purposes.● Use compressed air from an air compressor.Do not use air from a high pressure tank or any other gas.● Do not blow air from air blowgun towards personnel or animals.Direct air blow or substance blown by air blow can potentially cause injury for humans or animals.● Wear safety glasses and ear plugs.Regardless of the use of this product, wear safety glasses and earplugs when operating an air blowgun. Without proper protection, injury to eyes due to blown dust or noise induced deafness would be potentially caused.● Do not disassemble or modify this product.Disassembling or modification may causes safety accidents in addition to operation failure.● Attach a pipe fitting or joint properly.If a pipe fitting or joint are attached improperly, it may cause danger such as hose whip due to unplugged piping. Confirm the connection of hose, tube or coupler joint is tight as well as the connection to this product prior to use.● Do not use for medical equipment or cooking equipmentThis product contains a small amount of lubricant. If there is concern for contamination due to lubricant, do not use.SpecificationsFluid Compressed air Pressure Range 0.35 to 0.8MPaMaximum Flow *1 1300L/min (@0.5MPa) Ambient Temperature*210 to 50℃ Pulse Adjustment Range5 to 15HzPort SizeIN Rc1/4OUTR1/4Weight155g*1 “Maximum Flow” in this case is the flow capacity of this product,and actual flow consumption is depending on the attached air blowgun.*2 If the temperature is under the specified temperature, pulse blowmay be unstable. In this case, please use it as continuous blow temporally for a while to reach specified temperature. This product works correctly within the specified ambient temperature.Connection≪取付例≫1. Before Piping, thoroughly flush the inside of each pipe toremove chips, machining oil, and dust etc. If sealing tape is used for the thread, leave 1.5 to 2 thread turns unwrapped. Do not use liquid sealant. It has possibility to contaminate the product and may cause malfunction.Push-in fitting or joint such as coupler(Sold Separately) Air Saver Unit for Air Blowgun“Air Saver Module” HASV08R9IM-E009-aIssued :Jan.14.2016Air blowgun“Air Saver Module”HASV08R Reference blowgun:Parker LegrisPart Number: 0659 00 13(Sold Separately)WarningCaution<Example of attachment>2.When installing piping or a joint, prevent contamination of chips or sealing agent. Also tightening torque should be within the range indicated below.Port Size Tightening Torque (N ・m)R ・Rc1/412 to 143.An air filter (Nominal filtration rating of 5 micron or smaller) must be placed upstream of piping. There is no need for additional lubrication.4. Attach the piping towards the direction of air flow described on the body. If it is opposite direction, this product does not work.5.This product must be attached directly to an air blow gun. If connected with any part such as coupler, it has the possibility to decrease the capability due to pressure loss.6.This product is not water & drip proof. Do not install this product in a place with direct water contact (rain, etc). Also install this product in a place without dew condensation or direct sunlight.Product Function[Pulse Adjustment Screw]This is a throttle valve for pulse ON time adjustment (Approx.5 to 15 Hz). When tightening this screw clockwise with flat-bladedscrewdriver, the air ON time will be longer. When loosening the screw counter clockwise, the air ON time will be shorter. The air OFF time is fixed for approx. 30ms. Adjust the air ON time in accordance with using air blowgun or object. Control angle is approx. single rotation of the screw. When tightening at the end of clockwise, it will stop air output, however it is not malfunction.[Pulse/ Continuous Switching Button]Press this button when requiring continuous blow. When pushing this button, air blows continuously. To keep continuous blow, press this button and turn the button 90 degrees. To release from this mode, press this button and turn counter clockwise for pulse blow mode.DimensionsNotes for Usage● Discharge drain from upstream air filter periodically. If periodic drain discharge is difficult, Parker recommends setting up an air filter with automatic drain.● Maintenance compressor periodically. If sludge, which isproduced in compressor oil, enters pneumatic equipment, it will cause operation failure of pneumatic equipment. Coalescing filter removes oil and sludge which cannot be removed by air filter. Parker recommends setting up a coalescing filter.Effect of Pulse BlowIn many factories, air blow accounts for more than 50% of total compressed air consumption. Pulse blow can be a measure forsaving energy by reducing the consumption of compressed air while maintaining the same capability of air blow operation.・Hole machining, tap, chip removing of complex shape work ・Removing stuck dust or viscous liquid ・Blowing at narrow space・Reducing load of compressor ・Energy saving activityPulse blow is especially effective for works listed above, however it is not for all applications. There is a possibility to reduce the removal effectiveness depending on the air blowgun. Parker recommends attaching to an air blowgun that has nozzle diameter bigger than I.D.2mm and low pressure loss.Also, for the case of using reduced pressure for air supply, installing this product without regulator enables a low energy loss circuit, which provides improved blow effectiveness compared to the current circuit.Kuroda Pneumatics Ltd(Parker Hannifin Automation Division Japan)10243 Kamakazu, Asahi city, Chiba 289-2505, JapanE-mail:********************10HzWhen screwing, seal tape may enters the product and cause malfunction.Leave space of 1.5 -2 turnsUse half width seal tape. It may reduce cost as well. Cut with knife.(Not good)(Good) Air Blow Gun Connecting Port (R1/4)Pulse Control Trimmer[Note] ● Please contact our distributors or Parker for after-sales service. ● Please keep this operating manual.15HzPressure Supply Port (Rc1/4)Vent HolePulse/ContinuousSwitching ButtonFlow Flow Current Circuit Pulse Blow A i r C o n s u m p t i o n L /m i nA i r C o n s u m p t i o n L /m i nTime (sec)Time (sec) Pulse Adjustment Screw (ON Time Control)Pulse/ Continuous Switching button Time Time。
操作手册OperationManual
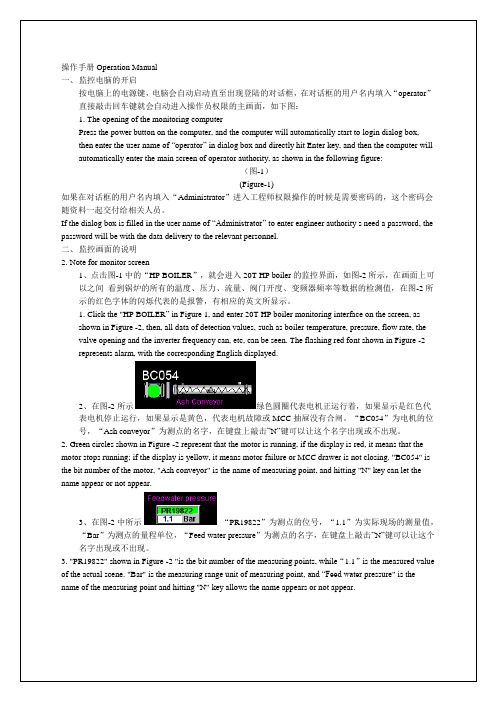
4. "Drum level HH / Drum level H" shown in Figure 2 represents the water level of the drumand alarmfor excessively height, and these two strings of English letters isflashing.The height of drum water level is +50, and +150 means excessively high, low is -50, -150 means excessively low (This value is the basis for the emergency stop for the boiler)
操作手册Operation Manual
一、监控电脑的开启
按电脑上的电源键,电脑会自动启动直至出现登陆的对话框,在对话框的用户名内填入“operator”直接敲击回车键就会自动进入操作员权限的主画面,如下图:
1. The opening of the monitoring computer
Press the power button on the computer, and the computer will automatically start to login dialog box, then enter the user name of“operator”in dialog box and directly hit Enter key, and then the computer will automatically enter the main screen of operator authority, as shown in the following figure:
海康威视DVR设备操作手册说明书

Step 17. Enter Alarm 1 Enable/Disable Submenu Press d to display flashing DSBL / ENBL .Step 18. Enable Alarm 1 SubmenuIf flashing ENBL is displayed, press a , if DSBL is displayed,press b until ENBL is displayed, then press d to store and go to the next menu item.Step 19. Select the Deviation Control Type Submenu Press d . If flashing _DEV Deviation is displayed press a ,otherwise press b until flashing _DEV is shown. Now press d to store and go to next menu item.Step 20. Select the Latched Type SubmenuPress d . If flashing UNLT Unlatched is displayed press a ,otherwise press b until UNLT is displayed.Press d to store and advance to next menu item.Step 21. Select the Normally Open Type of Contact Closure SubmenuPress d . If flashing N.o.Normally Open is displayed,press a , otherwise press b until N.o.is displayed. Press d to store and advance to next menu item.Step 22. Select the Above Type of Active Submenu Press d . If flashing ABoV Above is displayed, press a ,otherwise press b until ABoV is displayed. Press d to store and advance to next menu item.Step 23. Enable Alarm 1 at Power On (A.P.oN )Press d . If flashing ENBL is displayed, press a , otherwise press b until ENBL is displayed. Press d to store and advance to next menu item.Step 24. Enter Alarm 1 High SubmenuPress a twice to skip ALR.L Alarm 1 Low value. ALR.L is for below & ALR.H for above.Step 25. Set the Alarm 1 High value (ALR.H )Press d . Press b or c until value to set the display to 002.0. Press d to save.Step 26. Enter the Alarm 2 MenuThe display will show ALR2the top menu for Alarm 2.Repeat steps from 17 to 25 to set for Alarm 2 the same conditions as for Alarm 1.Step 27. Skip the Loop Break Time Menu (LOOP )Press a to go to the OUT1Output 1 Menu item.Step 28. Configuration the Output 1 MenuSet Alarm 1 Disabled (Step 18) to be able to Enable Output 1.Step 29. Configuration of Display Color Selection Press a until the COLR Display Color Selection Menu appears on the Display. Configure COLR as N.CLR /GRN (green), 1.CLR / RED (red), 2.CLR /AMBR (amber). Please refer to the operator’s manual if needed.For color change on Setpoints refer to Owners Manual Section 2.MQS4007/0411SPECIFICATIONSENSOR SPECIFICATIONSRelative Humidity Accuracy/Range:±2% for 10 to 90%±3% for 5 to 10% and 90 to 95%±4% for 0 to 5% and 95 to 100%Non-linearity : ±3%Hysteresis: ±1% RH Response Time :8 sec, tau 63%Repeatability : ±0.1%Resolution : 0.1%, 12bitTemperature Accuracy/Range*:±0.5°C for 5 to 45°C (±1°F for 41 to 113°F); up to ±1.5°C for -40 to 5°C and 45 to 124°C (up to ±2.7°F for -40 to 41°F and 113 to 257°F)*NOTE:extended temp range is for Probe only, the Controller’s operating temp is 0-50°CResponse Time : 5 to 30 sec, tau 63%Repeatability : ±0.1°C Resolution : 0.1°C, 14 bit METER SPECIFICATIONS Display:4-digit, 9-segment LED, •10.2 mm (0.40")Red, green, and amber programmable colors for setpoint and temperature units.Output 1†:Relay 250 Vac @ 3 A Resistive Load,SSR, Pulse Output 2†:Relay 250 Vac @ 3 A Resistive Load,SSR, Pulse †Only with -AL Limit Alarm optionOptions:Communication RS-232 / RS-485or Excitation:24 Vdc @ 25 mAExc. not available for Low Power OptionLine Voltage/Power:90 - 240 Vac ±10%,50 - 400 Hz*, or 110 - 375 Vdc, 4 W* No CE compliance above 60 HzLow Voltage Power Option:12 - 36 Vdc or 24 Vac** ±10%, 3 W**Units can be powered safely with 24 Vac but No Certification for CE/UL are claimed.Dimensions:25.4 H x 48 W x 126.3 D mm (1.0 x 1.89 x 5")Weight:127 g (0.28 lb)Approvals:CE per EN61010-1:2001It is the policy of OMEGA to comply with all worldwide safety and EMC/EMI regulations that apply.OEMGA is constantly pursuing certification of its products to the European New Approach Directives.OMEGA will add the CE mark to every appropriate device upon certification.The information contained in this document is believed to be correct, but OMEGA Engineering,Inc.accepts no liability for any errors it contains, and reserves the right to alter specifications without notice.TRADEMARK NOTICE:®,®,, andare Trademarks ofOMEGA ENGINEERING, INC.®This Quick Start Reference provides informationon setting up your instrument for basic operation.The latest complete Communication and OperationalManual as well as free Software and ActiveX Controlsare available at /specs/iseriesor on the CD-ROM enclosed with your shipment. SAFETY CONSIDERATIONThe instrument is a panel mount device protected in accordance with EN61010-1:2001. Remember that the unit has no power-on switch. Building installation should include a switch or circuit-breaker that must be compliant to IEC 947-1 and 947-3.SAFETY:•Do not exceed voltage rating on the label located onthe top of the instrument housing.•Always disconnect power before changing signal andpower connections.•Do not use this instrument on a work bench withoutits case for safety reasons.•Do not operate this instrument in flammable orexplosive atmospheres.•Do not expose this instrument to rain or moisture. EMC:•Whenever EMC is an issue, always use shielded cables.•Never run signal and power wires in the same conduit.•Use signal wire connections with twisted-pair cables.•Install Ferrite Bead(s) on signal wire close to theinstrument if EMC problems persist.MOUNTINGPanel Mounting Instruction:ing the dimensions from the panel cutout diagramshown above, cut an opening in the panel.2.Insert the unit into the opening from the front of thepanel, so the gasket seals between the bezel and thefront of the panel.3.Slide the retainer over the rear of the case and tightenagainst the backside of the mounting panel.。
730 DuN 操作手册说明书

730DuN操作手册目录1一致性声明5 2注册声明6 3拆箱73.1打开泵包装73.2包装丢弃73.3检验73.4组件清单73.5存放74泵返修须知8 5蠕动泵-综述9 6保修10 7安全须知11 8规格参数148.1规范148.2重量148.3泵头选项159安装建议169.1一般建议169.2注意事项1610泵的操作1810.1小键盘布局与按键ID1810.2启动与停止1910.3使用上下键1910.4最大转速1910.5改变转动方向1911连接电源2011.1导线颜色编码2111.2US NEMA模块接线2112启动检查表22 13控制线路2313.1上部D型接头2313.2下部D型接头2313.3标准25针D型接头:输入与输出2313.4标准-25针D型接头:供电限值3113.5N模块(标准型及SCADA型)3113.6标准型N模块3213.7SCADA型N模块3613.8标准9针D型接头RS23238 14首次开启泵4214.1选择显示语言4214.2首次启动默认设置42 15重复启动泵45 16模式菜单46 17手动4717.1启动4717.2停止4717.3增加和降低流量4817.4MAX(最大转速)功能(仅限于手动模式)48 18流量校准4918.1设置流量校准49 19模拟模式5219.1模拟信号校准5319.2校准输入15419.3设置高信号值5519.4设置高流量校准5619.5设置低信号值5619.6设置低流量校准5719.7校准缩放输入5919.8设置高信号值6119.9设置高流量校准6219.10设置低信号值6219.11设置低流量校准6320网络模式6520.1网络设置6520.2协议6520.3泵的编号6520.4波特率6620.5停止位6620.6保存网络设置67 21MemoDose模式6821.1配置MemoDose6821.2设置流量6821.3恢复中断加注6921.4主加注量7021.5手动定量分装73 22主菜单7522.1安全设置7522.2常规设置8322.3控制设置9222.4配置输出9322.5配置输入9622.6帮助97 23故障排除9823.1检漏9923.2错误代码9923.3技术支持100 24驱动维护101 25驱动器备件102 26泵头更换10326.1泵头更换103 27软管更换10527.1连续软管10527.2软管单元105 28订购信息10728.1蠕动泵订货号10728.2软管及软管单元订货号10828.3泵头配件110 29性能数据11429.1720R、720RE、720R/RX和720RE/REX性能数据114 30商标116 31免责声明117 32发布历史1181一致性声明2注册声明Watson-Marlow Ltd Falmouth Cornwall TR11 4RU EnglandIn accordance with the Machinery Directive 2006/42/EC that if this unit is to be installed into a machine or is to be assembled with other machines for installations, it shall not be put into service until the relevant machinery has been declared in conformity. We hereby declare that:Peristaltic PumpSeries: 530, 630 and 730 cased pumpsthe following harmonised standards have been applied and fulfilled for health and safety requirements:Safety of Machinery – EN ISO 12100Safety of Machinery – Electrical Equipment of Machines BS EN 60204-1 Quality Management System – ISO 9001and the technical documentation is compiled in accordance with Annex VII(B) of the Directive. We undertake to transmit, in response to a reasoned request by the appropriate national authorities, relevant information on the partly completed machinery identified above. The method of transmission shall be by mail or email.The pump head is incomplete and must not be put into service until the machinery into which it is to be incorporated has been declared in conformity with the provisions of the Directive. Person authorised to compile the technical documents:Andrew Green, Design & Engineering Director, Watson-Marlow Ltd. Place and date of declaration: Watson-Marlow Ltd, 31.07.2015 Responsible person:Simon Nicholson, Managing Director, Watson-Marlow LtdDeclaration of Incorporation3拆箱3.1打开泵包装仔细打开所有零件包装,保留包装,直到您确认所有组件均存在且状态良好。
RC411操作员手册说明书
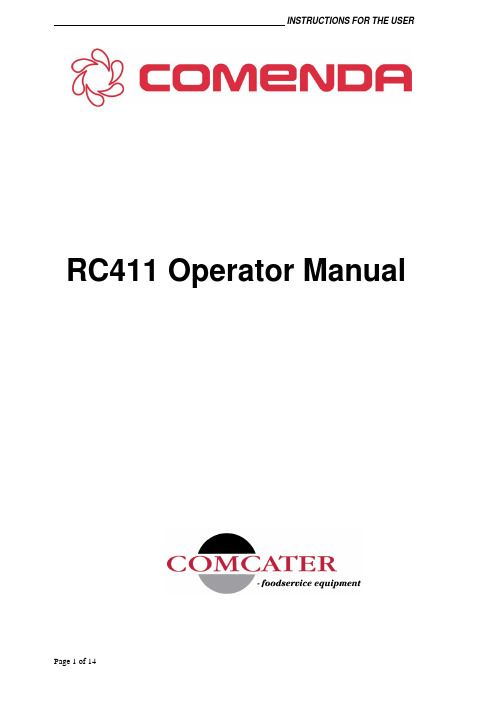
RC411 Operator ManualFOREWORD1.Read the instructions contained in the enclosed booklet carefully, because it contains important information on installation, operation and maintenance safety. Store this booklet carefully for any further consultation by other operators.2.Having removed the packing material, check that all the equipment is present.If there is any doubt, do not use it and contact qualified personnel.The packing elements (plastic bags, foam polystyrene, nails, etc.) should be kept away from children, because they are dangerous.3.Before switching the equipment on, make sure that the model plate data conforms to that of the electrical and water distribution network.4.Installation should be carried out by qualified personnel according to the manufacturer's instructions.5.This equipment should be destined to the use which it has been conceived for. Any other application should be considered improper and consequently dangerous.6.The equipment should only be used by personnel trained for its use.7.Operators must strictly follow all hygienic requirements in the handling of clean dishware and cutlery.8.Do not leave the machine in an environment at temperatures lower than 0°C.9.The protection of the machine is IP X4, therefore it should not be washed with high pressure directed water jets.10.Qualified personnel only can access the control panel, after having disconnected the machine from the primary current supply.11.The appliance is made according to EEC 89/336 regarding radio noise suppression and electromagnetic compatibility.12.According to EEC directive nr.23 of 19/02/1973 and the law of actuation nr.791 of 18/10/1987, our appliances are built-up according to the good technique norms in force in Italy and abroad.13.Noise level of the machine, less than 63dB(A)INSTRUCTIONS FOR USECONTROL PANELH3Q1H2H2Pilot lamp "machine READY"H3Pilot lamp "machine WORKING"Q1 Main switchOFFGREEN MachineRED Machine ON / Wash cycleselectorS9CycleOPERATION AND USE1. Before washing make sure that:•the wall-mounted on/off switch is switched on;•the water tap is open;•water is present in the distribution network;•the pump protection filters are installed in their respective positions;•the overflow in inserted;•all rotating parts are free;•the rinse aid dispenser is full;•make sure that dishware is in good conditions as it may cause cleaning difficulty and haven bacteria.2. Press the "Q1" button (RED) to enable the automatic wash tank filling and the consequent triggering of the heating element.3. As soon as visual indicator "H2" is ON; pour about 30 gr. of detergent directly into the tank, paying attention to distribute it uniformly on the filters, the quantity being according to supplier's instructions. Add 15 gr. every 7 cycles to achieve a concentration of 1,5gr/lt. In order to respect our environment, use only the correct amount of detergent.When using chlorinated detergent, it is suggested to use an automatic dispenser; otherwise, brownish spots might appear on the surfaces due to chlorine reactions. Detergent should always be placed near the pump filter.4. Then, introduce the glasses or the cups to wash, after having removed the solid waste and having placed them into the proper racks. The cups and the glasses should be turned upside down, while the cutlery should be put vertically into the proper container, and the same applies to dishware.5. Press the "S9" button to select the wash cycle according to conditions of•(pos.short cycle with normally dirty dishes;•(pos.long cycle with particularly dirty dishes or deep dishes 6. Close the door for the wash cycle start.The end of which will be indicated by the switching off of the "H3" lamp.standards, guaranteeing a final rinse at 85°C. Wash cycle automatically lengthened if final rinse temperature is not reached. When this auto-cycle intervenes and the cycle is pro-longed, after 8 minutes the "H3" indicator flashes to indicate this intervention and the cycle continues (water supply temperature is likely to be the problem, otherwise contact an assistance centre since it is a rinse water heating intervention.). Turn off the machine to remove this alarm.7. Remove the rack and slightly incline it to permit a perfect drain; allow dishware to dry and after having washed one’s hands, handle the rack in order not to touch the dishware inside then place the rack on hygienically clean shelves.8. At the end of washing, with the machine off (Q1 – GREEN pos.), empty out the tank by taking out the overflow tube, then close the door and with the machine on (Q1 – RED pos.).for a few minutes to wash the machine. Then again with the machine off and wait until the tank is completely emptyAt this point, the tank filter can be taken out, in order to be washed, then replace it with the overflow in its place.For any further information concerning equipment cleaning, read chapter "USEFUL SUGGESTIONS".turning off the main supply through the general wall switch and close the water supply.INSTRUCTIONS DURING THE WASHING1) Do not plunge bare hands into the water containing the detergent. If this happens, wash them immediately and abundantly with fresh water.2) When the machine is operating, do not open the door too rapidly.3) Use only specific anti-foaming detergents.4) Disconnect the equipment in case the machine is out of order or it does not work properly. For the repairs consult a technical assistance centre authorised by the manufacturer and ask only for an original spare parts.5) Never modify the thermostat settings.6) Check that lamp "H2" is on.7) Wash tank water should be changed at least twice a day or according to daily wash requirements.8) Do not subject clean dishware to any further cleansing treatment such as brushes or drying towels.If these instructions are not followed, the safety of the equipment can be compromised.USEFUL SUGGESTIONS1) MAINTENANCEIMPORTANT: Before carrying out the cleaning and maintenance operations, disconnect the equipment from the electric supply.Frequently check and clean the nozzles. The frequency of this operation will depend on the quantity of residues, which may result in an unsatisfactory washing result.♦For the inside and outside cleaning of the machine, do not use corrosive products such as sodium hypochlorite (bleach) savelling water and hydrochloric acid, acids, steel wool or steel brushes.♦The presence of calcium and magnesium salt in the water can compromise machine performance, thus ask qualified personnel to remove the deposits periodically.♦In order to avoid some oxidation risks, or chemical reactions, generally the stainless steel surfaces have to be well cleaned.2) OPTIMAL RESULTS:A possible wash deficiency can be noticed when residue remains.Marks can be caused by an insufficient rinse: in this case checkthat the rinse nozzles are clean and that there is sufficient water supply pressure.In case of dishware residue check that:•the washing nozzles are clean•the water temperature is around 60°C•there is detergent•the pump suction filter is clean•the racks are suitable for the dishes and cutlery that are to be washed•the position of the cutlery and the dishes in the racks are correct3) TEMPORARY MACHINE NON-USEIn case the machine is stopped for some weeks, it is recommended before closing it to fill the tank and run the machine with clean water, then empty it out, in order to avoid the forming of bad odour and that any residue remains in the pump.If necessary repeat this operation until the water leaving the machine is clean. If the machine is stopped for many weeks, it is recommended to oil the stainless steel surfaces with paraffin oil and to discharge the water from the boiler and the electric pump.4) SANITIZING THE MACHINESanitizing the machine at least once a week is of the utmost importance in order to guarantee hygiene even when the machine is not in use.It is advisable to use a disinfecting product suggested by an authorised detergent dealer.The use of this product will satisfy hygienic requirements, even during machine non use.Before switching off the machine run the machine briefly with cleanwater.5) HARD WATER CONDITIONSIf a hard water supply is present, mineral deposits will form within the machine and also on dishware.In order to avoid the above conditions a periodic removal of these deposits is necessary.The frequency and method of this operation upon consultation by your detergent supplier.INSTALLATION AND MAINTENANCEINSTRUCTIONSThe following instructions are addressed to qualified personnel the only one authorised to carry out checks and repairs, if any.The manufacturer declines any responsibility in the case of interventions made by a non-qualified personnel or the use of spare parts other than those supplied by the Manufacture.INSTALLATIONDuring installation, carry out proper machine levelling, which is a prerequisite for a correct operation thereof (max. tolerance 2°).In order to prevent any damage caused by steam going out of the machine, make sure that the surrounding materials do not deteriorate in its presence. After machine installation check thermostat settings, booster 85°C, tank 60°C.1) ELECTRICAL CONNECTIONThe electrical safety of this equipment is only assured if it is connected as follows. It is necessary to connect the equipment to an effective earthing as specified by the electrical safety regulations in force. Check that this basic requirement is complied with, in case of any doubt ask for a careful check of the installation by a qualified personnel. In the case the earthing is not efficient there will be a dispersion due to the suppresser.The machine shall be included in a correctly dimensioned equipotential, whose effectiveness is to be very tight in accordance to the procedures set for in the applicable safety standards. The connection shall be performed through a screw marked by the plate near the rear side of the appliance.The manufacturer declines any responsibility for any damages caused by lack of an effective ground installation. For the electrical power supply have available a wall circuit breaker switch with multiple phase protection according the following table with contact aperture distance, equal to or not exceeding 3mm and a supply cable no less than 2.5mm².kW 230/240V∼ 230/240V3N∼3∼ 400/415V7,75kW 40A 25A 16A5,45W 32A 16A 16A3,10kW 16AFor other supplies the cable cross section and the circuit breaker switch must be calculated according to voltage and length of cabling. If cabling too long adjust cable size to Amp rating; do not pull on supply cable or install it under tension. If cable needs to be replaced use type H07RN-F.2) WATER CONNECTIONInstall a 55°C water tap in a well accessible place, terminating in a 3/4" fitting, which the pipe strainer and inlet hose shall be connected to. Carefully comply with any national or regional regulations in force.The operating pressure should be neither less than 2 bars or greater that 4 bars (200/400 kPa). If water pressure is inferior then 2 bar, a pressure increase pump is necessary. If water pressure exceeds 4 bar, a pressure reducer is necessary.In order to obtain best results, it is suggested that the water supply have a hardness not greater that 8 Clarke.3) WATER DRAINArrange a water drain towards the floor with siphon and connect the machine with the flexible tube given with the machine, so that it leans towards the drain. Moreover, make sure that the hose does not have constrictions.Make sure that the building drain tubing withstands temperatures up to 70°C.4) RINSE AID DOSAGEMake sure that rinse aid suction hose is correctly installed in its proper container. The dosage is automatic with the adjusting of the screw "I", which after screwing to a full stop unscrew two turns. At this point the machine automatically takes the necessary liquid for every rinse: during the washing operations, check that the liquid of the container does not run short.For filling the dosing tube, start the machine without plugging the overflow in: at that point switch the machine on and off. Repeat this operation several times at intervals of few seconds, until the rinse aid reaches the injector. Wait until the machine reaches the correct temperature (lamp "H2" on). Make some empty cycles, then try to wash: if the objects washed show some drops, this means that the rinse aid is insufficient. On the contrary, the presence of marks can mean that there is too much rinse aid or the water is too hard. The regulation can change according to the kind of rinse aid.5) DETERGENT DOSAGE (for machines with built-in detergent dispenser)With the screw on the side of the detergent pump, close completely the product intake, and then slowly open the screw until the desired intake quantity has been reached. The correct quantity is indicated by the detergent supplier. Check that the intake of the pipe during the rinse cycle is as preset. (1cm = 1g approximately). Maximum intake or delivery distance: 2 meters.6) LOADING AND UNLOADING OF THE MACHINEFor the transportation of the machine from the delivery point to the final installation position, use a fork lift or adequate lifting equipment used by authorised staff. Lift the machine by its frame, taking care that any protruding parts are not damaged (discharges, wiring etc.).7) MACHINE DISMANTLINGAt the end of its normal lifetime, the machine has to be taken apart according to the local regulations in force by separating the components as follows: • metal parts: hood, platforms, frames, filters• electrical parts: motors, remote control switches, microswitches, wiring • plastic parts: racks, connections • rubber parts: tubes, sleevesENERGY CONSUMPTIONModel Wash tank capacity (l) Rinse waterconsumpt. (l)Tankheater (W)Rinse heater (W)Wash pump (W)Total electric load (W)Output in racks per hour with 55°C inlet waterOutput in racks per hour with 12°C inlet waterRC41121 3,5 2000MAX7000750MAX 775030/20 20In the event of low water supply temperature, the will be a subsequent machine output drop.WIRING DIAGRAMC1 Anti noise filterC3 CondensatorheaterE2 BoosterE3 TankheaterH2 Pilot lamp machine readyH3 Pilot lamp machine workingKE2 Booster heater contactorKE2b Safety contactor of booster heaterM2 Rinse pump (if required)M3 Wash pumpM5 Drain pump (if required)MD Detergent dispenser (if required)switchQ1 MainswitchS1 DoorS2 PressureswitchS9 Cycle selection push buttonthermostatSE2 BoosterSE2a Booster thermostatSE2b Booster safety thermostatthermostatSE3 TankSE3b Tank safety thermostatY1 Rinse solenoid valveX1 JunctionThe manufacturer declines any responsibility for any printing errors contained in this booklet. The manufacturer also reserves the right to make any modifications to its products that do not affect the basic characteristics thereof.。
Tennant V-WD-27 V-WD-62 V-WD-72 操作手册说明书

Operator manual操作手册ChinaPLDC04180-00Wet & Dry Vacuum CleanerV-WD-27V-WD-62V-WD-72ENCNTo view, print or download theparts manual, visit:Model Part No.:1244332 V-WD-27, CN (220-240 V)1244337 V-WD-62, CN (220-240 V)1244342 V-WD-72, CN (220-240 V)ENINTRODUCTIONThis manual is furnished with each new model.It provides necessary operation and maintenance instructionsRead all instructions before using this machine.This machine will provide excellent service. However, the best results will be obtained at minimum costs if:• The machine is operated with reasonable care.• The machine is maintained regularly - per the maintenanceinstructions provided.• The machine is maintained with manufacturer supplied orequivalent parts.T o view, print or download manuals online visit /manualsUNPACKING MACHINECarefully check machine for signs of damage. Report damages at once to carrier. Check machine contents to ensure all parts and accessories are included. Contact distributor or T ennant for missing items.INTENDED USEThis wet & dry vacuum cleaner is intended for commercial use, for example in hotels, schools, hospitals, shops, offices and rental businesses. The machine is suitable for picking up dry non-flammable dust and debris and liquids in an indoor environment. It is not suitable for picking up hazardous liquids or materials. Donot use this machine other than described in this manual.Do not dispose of electrical equipment into household waste! ccording to the European Directive 2012/19/EU on waste, electrical and electronic equipment (WEEE) and its incorporation into national law, electrical equipment that is no longer suitable for use must be separately collected and sentfor recovery in an environmental-friendly manner.Always remember to recycle.TENNANT CLEANING SYSTEM & EQUIPMENT (Shanghai) CO. LTDBuilding 1, No. 3777, Cao Ying Road Shanghai 201712People’s Republic of China Specifications and parts are subject to change without notice.Original Instructions. Copyright ©2019 T ennant Company.All rights reserved.INSTRUCTIONS THAT MUST BE STRICTL Y FOLLOWED - SAFE USERead carefully the manual before use, in order towork safely.Warning: Before operating, the appliance must be correctly assembled as described in manual. Check that all the equippedfiltering elements are in place and efficient.-This appliance must be kept out of the reach ofchildren, of people with reduced physical, sensory or mental abilities or lacking of experience and knowledge.-CAUTION: Children must be kept under control, do not allow children to use the appliance as a toy.-WARNING: Users must be properly trained to use the machine.-CAUTION: Components used in packaging (ex: plastic bags) can be dangerous; keep away from children, animals and people not aware of their actions.-T o correctly dispose of the packaging follow your local disposal ordinance.-Make sure the voltage of power source is the same as indicated on the rating plate of the vacuum cleaner. Verify that the outlet is compatible with the plug. Power cord must always be unrolled before using the appliance. Do not use the power cord coiled.-Do not handle/use plug or appliance with wet hands. -Do not pick up anything that can damage the filtering elements (such as glass, metal etc.).-Do not use the power cord to move or lift the machine. -Never immerse the machine in water and never use a pressure washer to clean the machine.-Do not use this appliance beyond 2000 m (6560 ft) above sea level.-WARNING: This machine is not suitable for picking up dangerous dust.-CAUTION: Don’t pick up flammable, incandescent, explosive or toxic dust/blends. Maximumtemperature allowed is 40°C (104°F).Warning: Any application not described in this manual is potentially dangerous,therefore it must be avoided.Warning: Do not leave a working machine unsupervised. Always unplug the machine if the appliance is not working. Keep awayfrom children and from people not aware of their actions.-WARNING: This appliance must be used on a levelsurface to prevent from rolling. Do not operate, move or store appliance on a sloping plane.-WARNING: This appliance must be stored indoor and in a dry area.-WARNING: Keep hands, feet, ears, loose clothing, hair and all parts of the body (human or animals) away from openings.-WARNING: Use only original spare parts. Using other accessories might compromise the operator’s safety.-Warning: This machine is not suitable for picking up dust in environments where electro-static discharges or spark can cause damages to electronic components and persons.-Only an authorized service centre can replace power cord of the appliance.V-WD-27V-WD-62V-WD-72Voltage 220-240 V 220-240 V 220-240 V Frequency 50-60 Hz 50-60 Hz 50-60 Hz Motor Power 1100 W 2200 W 3300 W Max Airflow 200 m 3/h400 m 3/h600 m 3/h Max Water lift 2.380 mmH 2O 2.380 mmH 2O 2.380 mmH 2O T ank Capacity 27 L 62 L 72 L Power cord length 8,5 m 8,5 m 8,5 m Weight7,8 kg 18,5 Kg 23,4 Kg Sound Pressure Level Lp(A) [dBA]71,275,479,0Hand-arm vibration < 2,5 m/s²< 2,5 m/s²< 2,5 m/s²Construction class II II II ProtectionIPX4IPX4IPX4TECHNICAL SPECIFICATIONSEN Warning: Do not tamper or modify theappliance. Failure to comply with theseinstructions could result in severepersonal injury or death. Tampering will void thewarranty.The manufacturer refuses all responsibilityfor damages or injuries due to improperuse of the machine or in case of failure tofailure to comply with the instructions given inthis manual.Always disconnect power cord frompower source after operating and beforeservicing. After every use and beforesending the appliance to a service center, it mustbe thoroughly cleaned and tank rinsed out toavoid hazard.-Do routine maintenance. Inspect gaskets seals,plastic parts, filters, switches and replace thosewhich have begun to leak or are damaged.-Using a machine with a damaged power cord couldresult in an electrocution. Check the cord lookingfor cuts, cracks or aging signs and replace it, if it’snecessary.-Do not use an extension cord with this machine.-Only an authorized service center can do reparationor maintenance of the appliance. Use only originalspare parts.-T o keep the appliance fully functional it is necessaryto clean main polyester filter by shaking it after everyuse and replacing filter bag if it’s full.-Clean every part of the appliance after each use:empty the tank, shake the filters, replace filteringbag if it’s full and clean the machine with a dampcloth before storing the vacuum cleaner.-WARNING: In case of foam or liquid leak turn off theappliance immediately.-WARNING: In case overturning, lift the appliance inthe upright position before switching the motors off.-Don’t pick up water from sink or tub. Do not useappliance as a pump to clean out clogged drains,sinks, or other plumbing fixtures. The appliance isintended for vacuuming air and water mixtures.-Do not use or pick up aggressive soaps, they coulddamage the appliance.WARNING: The float valve will stop thevacuuming when the tank is full of liquidsor if machine overturns; ensure float valveis installed and operating properly before use.-WARNING: Do not use outdoors or in a coldenvironment.-During a power quality disturbance of the facilitieselectrical grid, this appliance may cause temporarydrops in voltage.DRY PICK UP (PAGE 6)1. Insert main polyester filter into the tank (Fig. 1).2. Mount the motor head on top of tank and lock itwith latches (Fig. 3).3. Push vacuum hose into hose inlet (Fig. 4).4. Attach wand and desired tool to hose ends (Fig.5).5. If your vacuum is equipped with vacuum bag,slide vacuum bag over the deflector (Fig. 7).6. Plug power cord into a properly grounded outletand turn appliance on (Fig. 6).WET PICK UP (PAGE 6)1. Remove main polyester filter from the tank (Fig.2).2. Mount the motor head on top of tank and lock itwith latches (Fig. 3).3. Push vacuum hose into hose inlet (Fig. 4).4. Attach wand and hoses to hose end (Fig. 5).5. Attach squegee floor tool to the other end.6. Plug power cord into a properly grounded outletand turn appliance on (Fig. 6).COMPONENTS DESCRIPTION (PAGE 6)A - Motor headB - On/Off SwitchC - LatchesD - InletE - T ankF - Castor wheelsG - Main polyester filter. Use only for dry pick up(not for wet pick up).H - Float valveI - Vacuum hoseJ - Power cordK - Wand Clip (only V-WD-62)L - Two-piece wandM - Hose nozzleN - Crevice toolO - Round brushP - T ool adaptor (only V-WD-62 and 72)Q - Squeegee floor toolR - Brush floor toolS - Upholstery tool (only V-WD-27)T - Trolley (only V-WD-62 and 72)CN简介每款新型号机器都配有本手册。
AphaJET into-操作手册简体中文版

电流消耗:
最大 0.5A 230V,1.0A 110V
显示屏:
10.4 英寸,彩色,800x600(XVGA),可移除(除了 AJ into)
喷头:
145x40x40mm, 晶振加热器,喷嘴快门
喉管:
4 米,显示屏连接管 4 米
可选安装 UPS: 不间断的电源供给(电源桥接故障大约 2 分钟)
接口:
RS232/USB(仅存储设备)/以太网/4 个输出/8 个输入
硬件:
主板:
控制油墨系统
基板:
中央控制系统
加密狗:
evo/tempo/pico/into/light/standard/professional/染料墨/颜料墨
软件:
嵌入式操作系统 WIN CE<->不是电脑上的 Windows
page6
...
page28
alphaJET evo-family 结构与功能
连续喷墨的原理 导电油墨通过集成泵从喷嘴流出,从而形成一条墨线.超声波变频器将电子信号变成机械振 动,并将墨线分裂一颗颗的小墨滴.墨滴通过充电电极时会被充电(带+/-电),充电后经过 高压偏转板,相应的转移带电墨滴,这一过程决定了墨滴在基材上的位置。
page13
Example applications Wellen nutrients factory, Krefeld, D
Printing the expiry date on baking powder bags
page14
Example applications Zentis confectionary factory, Aachen, D
.子公司设在荷兰
.在全球范围内超过 30 家销售和服务代理商
操作指导手册 英文
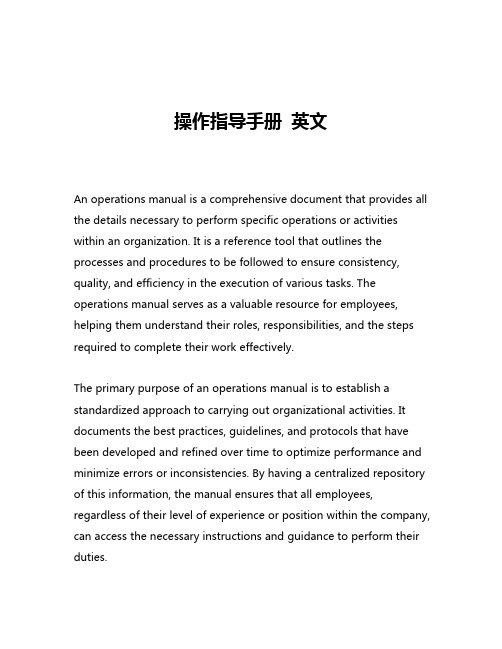
操作指导手册英文An operations manual is a comprehensive document that provides all the details necessary to perform specific operations or activities within an organization. It is a reference tool that outlines the processes and procedures to be followed to ensure consistency, quality, and efficiency in the execution of various tasks. The operations manual serves as a valuable resource for employees, helping them understand their roles, responsibilities, and the steps required to complete their work effectively.The primary purpose of an operations manual is to establish a standardized approach to carrying out organizational activities. It documents the best practices, guidelines, and protocols that have been developed and refined over time to optimize performance and minimize errors or inconsistencies. By having a centralized repository of this information, the manual ensures that all employees, regardless of their level of experience or position within the company, can access the necessary instructions and guidance to perform their duties.One of the key benefits of an operations manual is its ability to promote consistency across the organization. When all employees follow the same set of procedures, it helps to maintain a high level of quality and reliability in the organization's outputs. This consistency is particularly important in industries where compliance with regulations or standards is crucial, such as healthcare, finance, or manufacturing. The operations manual serves as a tool to ensure that all processes are executed in accordance with the established policies and guidelines, reducing the risk of non-compliance or errors.Moreover, an operations manual can be an invaluable resource for training and onboarding new employees. By providing a comprehensive overview of the organization's operations, the manual can help new hires quickly understand their roles and responsibilities, and how their work fits into the larger organizational context. This can significantly reduce the time and resources required to get new employees up to speed, as they can refer to the manual for guidance and reference as they become acclimated to their new environment.In addition to promoting consistency and facilitating training, an operations manual can also contribute to the overall efficiency of an organization. By documenting the step-by-step procedures for completing various tasks, the manual can help employees work more efficiently and effectively, reducing the likelihood of mistakes orunnecessary duplication of effort. This can lead to cost savings, improved productivity, and a more streamlined workflow.The content and structure of an operations manual can vary depending on the size, industry, and specific needs of the organization. However, there are typically several key components that are common to most operations manuals:1. Introduction: This section provides an overview of the purpose and scope of the operations manual, as well as any relevant background information about the organization or the specific operations being covered.2. Organizational Structure and Roles: This section outlines the organizational hierarchy, the roles and responsibilities of each department or team, and the lines of reporting and communication within the organization.3. Policies and Procedures: This is the most extensive section of the manual, detailing the step-by-step processes and procedures for carrying out various operational tasks. This may include information on procurement, inventory management, customer service, human resources, and any other relevant operational functions.4. Quality Control and Assurance: This section outlines theorganization's quality control measures, including any inspection or testing protocols, as well as the procedures for addressing and resolving any quality-related issues or non-conformances.5. Emergency and Contingency Plans: This section provides guidance on how to respond to unexpected events or emergencies, such as natural disasters, equipment failures, or security breaches, to ensure the continuity of operations.6. Appendices and Reference Materials: This section may include additional resources, such as forms, templates, checklists, or contact information, that employees can refer to as needed.Developing and maintaining an effective operations manual requires a collaborative effort across the organization. It is essential to involve key stakeholders, such as subject matter experts, department heads, and frontline employees, to ensure that the manual accurately reflects the organization's current practices and addresses the needs of all users. Regular reviews and updates are also crucial to keep the manual current and relevant as the organization evolves and adapts to changing circumstances.In conclusion, an operations manual is a critical tool for organizations of all sizes and industries. By providing a comprehensive and standardized guide to operational processes and procedures, themanual can help to promote consistency, efficiency, and quality in the execution of various tasks. Whether for training new employees, ensuring compliance with regulations, or optimizing workflow, the operations manual is an invaluable resource that can contribute to the overall success and resilience of an organization.。
Dynisco PT303应变片压力变送器操作手册说明书

providing a window into the processPT303 Strain Gage Pressure Transmitter Operating ManualExplosion proof pressure transmitter with integrated amplifier for use in hazardous environmeentsproviding a window into the processTable of ContentsContent Page IconGeneralNotes on safety Technical data Function Transport/delivery Assembly Commissioning Maintenance Troubleshooting35611 1112 141617providing a window into the process1. General1.1 Important information 1.2 Copyright 1.3 Explanation of icons 1.4 Abbreviations 1.5 Correct use 1.6 User’s obligations1.1 Important informationThis manual applies to the PT303 only. It must be kept near the equipment in a readily and immediately accessible location at all times.The content of this manual must be read, understood and followed in all points by all relevant people. This applies in particular to the notes on safety. Following the safety instructions will help to prevent accidents, defects and malfunctions.DYNISCO will not be held liable for any injury, loss or damage resulting from failure to follow the instructions in this manual.If malfunctions occur in spite of having followed the operating instructions, please contact the DYNISCO customer service department (see chapter 8, Maintenance).This applies in particular during the warranty period.344455providing a window into the process1.2 CopyrightCopyright law requires that this manual be used for inhouse purposes only.All reproduction, even partially and for in-house purposes, requires the approval of DYNISCO. This manual may not be forwarded to third parties.1.3 Explanation of iconsThe manual uses icons to indicate information pertaining to safety:Risk of destruction or damage to equipment, machines or installationsGeneral danger to life or limbSpecific danger to life or limbYou MUST do thisThe safety instructions are provided again in the individual chapters of the manual.1.4 AbbreviationsThe following abbreviations are used:OM Operating manualPT pressure transmitterf.s.of full scaleproviding a window into the process1.5 Correct useThe PT303 is designed for measuring pressure in explosive atmospheres (Class I, Division 1, Groups A, B, C & D) as part of a larger overall system. It contains an integrated signal amplifier. The PT303 pressure transmitter can be used in media temperatures up to 170°F. If the pressure transmitter is used in other applications, the safety and accident prevention regulations specific to that application must be followed.1.6 User’s obligationsThe operator or owner of the larger overall system, e.g. a machine, is responsible for following the safety and accident prevention regulations that apply to the specific application.2. Notes on safetyThe operator or owner of the larger overall system is responsible forfollowing the safety and accident prevention regulations that applyto the specific application.Mounting and electrical connection of the PT must be done by specialistswith EMC training, following all applicable regulations, and inpressureless, voltage-free condition with the machine switched off.The machine must be secured against being switched back on! Ambienttemperature for the electronics housing max. +170°F.Higher temperatures can result in damage and malfunction. Do not installthe pressure transmitter in places where this temperature is exceeded.providing a window into the processExplosion hazard!Deviation of the supply voltage from the value given in the technical specifications, or false polarity, can damage the pressure transmitter and cause malfunctions that can pose a risk of explosion. Operate with a power supply with the following specifications when employing the pressure 0 - 5 Vdcoutput:Do not lay connecting cables in the direct vicinity of cables carrying higher voltage or used to switch inductive or capacitive loads.3. Technical Data3.1 Ordering guide 3.1.1 Ordering guide for PT3033.2 Ordering example 3.3 Safety related specifications 3.4 Performance characteristics 3.4.1 Accuracy 3.5 Wiring/Electrical Termination 3.6 Pressure ranges 3.6.1 Max. Overload 3.6.2 Natural frequency 3.7 Electrical Data 3.8 Weight 3.9 Dimensions 677777899999103.1 Ordering guideThe exact meanings of the letter/digit combinations are given in the corresponding sections of chapter 3.providing a window into the process3.1.1 Ordering guide for pt3033.2 Example for Ordering3.3 Safety Related SpecificationsFM approvals Class I, Division 1 Groups A, B, C & D 3.4 Performance CharacteristicsPT303-X3.4.1 Accuracy±0.25% of full scale (Including Linearity, hysterisis and repeatability)providing a window into the process3.5 Wiring/Electrical TerminationThe electrical termination of the PT303 is 72” of four conductor sheilded cable, #22 AWG conductors, with 1/2-14 NPT conduit fitting.Color FunctionRed Signal +Black Signal -White Excitation +Green Excitation -Fig. 3-1 Typical Wiring Diagramproviding a window into the process3.6 Pressure Ranges(A) PT303-15 0-15(A) PT303-30 0-30(A) PT303-50 0-50(A) PT303-75 0-75(A) PT303-1C 0-100(A) PT303-1.1C 0-110(A) PT303-1.75C 0-175(A) PT303-2C 0-200(A) PT303-2.5C 0-250(A) PT303-3C 0-300(A) PT303-4C 0-400(A) PT303-5C 0-500(A) PT303-7.5C 0 - 750(A) PT303-1M 0-1,000(A) PT303-1.5M 0-1,500(A) PT303-2M 0-2,000(A) PT303-2.5M 0-2,500(A) PT303-3M 0-3,000(A) PT303-5M 0-5,000(A) PT303-7.5M 0-7,500(A) PT303-10M 0-10,0003.6.1 Max Overload (Without influencing Operation Data)3.6.2 Frequency Response3.7 Electrical Data3.8 WeightPT303 2x rated pressure> 2000 Hz-3.5 poundsConfiguration 4-arm Wheatstone bridge strain gauge with int. amplifier Output signal 4-wire 0 -5 Vdc Supply voltage +/- 12 Vdc for FM approved explosion proof modelsproviding a window into the process3.9 DimensionsFig. 3-2 PT303 Mechanical Drawingproviding a window into the process4. Function4.1 Construction 4.2 Description of functions 4.1 ConstructionThe PT303 are General Electric standards.The main advantages are:• thermal stability• resistance to aggressive media 11114.2 Description of FunctionsThrough a closed, direct contact measurement system, the PT furnishes an electrical signal that is proportional to the pressure of the media. The pressure is applied by the medium on the measuring diaphragm. The deflection of the measuring diaphragm changes the resistance of the strain gauge bonded to the measuring diaphragm. The strain gauge is a Wheatstone bridge. Depending on the model, the integratedamplifier generates an electrical signal (Vdc) proportional to the pressure.5. Transport / delivery5.1 Transport / packing / transport damage 5.2 Storage 5.3 Scope of delivery 121212ESD sensitive component. Electrostatic discharge may damage the PT. Take ESD precautions.providing a window into the process5.1 Transport/packing/transport damage - Do not let the PT be damaged by other items during transit.- Use only the original packaging.- Report transport damage to DYNISCO immediately in writing.5.2 Storage - Store the PT in original packaging only.- Protect against dust and moisture.5.3 Scope of delivery- Pressure Transmitter - Calibratoin Sheet- Operating manual with declaration of conformity6. Assembly6.1 Mounting the Pressure Transmitter 6.2 Electrical connection 6.3 Connection assignments 131314Ambient temperature for the electronics housing max. +170°F.Higher temperatures can result in damage and malfunction.Do not install the pressure transmitter in places where this temperature is exceeded.providing a window into the process6.1 Mounting the Pressure Transmitter6.2 Electrical ConnectionMounting and electrical connection of the PT must be done by specialists with EMC training, following all applicable regulations, and in pressureless, voltage-free, intrinsically safe condition with the machine switched off.The machine must be secured against being switched back on!ESD sensitive component. Electrostatic discharge may damage the PT. Take ESD precautions.Before mounting the PT, check the process connection carefully.Before mounting the PT, ensure that the process connection is free from media.To prevent the PT from sticking permanently in the process connection,coat the threadsection of the transmitter with high temperature resistant grease or a suitable parting agent.Always use a torque wrench when screwing the PT in and out. Do not apply the tool to the housing or housing / electrical connection!• Screw the PT into the process connection and tighten.Mounting and electrical connection of the PT must be done by specialists with EMC training, following all applicable regulations, and in pressureless, voltage-free, condition with the machine switched off.The machine must be secured against being switched back on!providing a window into the processDo not lay connecting cables in the direct vicinity of cables carrying highervoltage or used to switch inductive or capacitive loads.ESD sensitive component. Electrostatic discharge may damage the PT. TakeESD precautions.6.3 Connection Assignments7. Commissioning7.1 Supply VoltageConduit / LeadsRed Signal +Black Signal -White Excitation +Green Excitation -7.1 Supply voltage7.2 Calibration7.3 Zero adjustment7.4 OperationPlease read the entire manual prior to installation and use. Maximum excitation is 28 Vdc. Rated excitation is +/- 12 Vdc. Recommended warmup is 15 minutes. Explosion hazard!Deviation of the supply voltage from the value given in the technical specifications, or false polarity, candamage the pressure transmitter and cause malfunctions that can pose a risk of explosion.14151515providing a window into the process7.2 Calibration7.3 Zero Adjustment7.4 OperationCalibrate in pressureless state and at room temperature. Other ambient temperatures will corrupt the signal. Use an adjustment screwdriver!The adjustment is made at two potentiometer screws in the cover section of the elec-tronic housing.• Remove the cap screws from the potentiometers.• Connect a meter or suitable instrument to the signal output to verify the settings.• Adjust zero at potentiometer adjusting zero screw and verify on meter.For PT303, adjust zero at operating temperature!• Wait until a steady operating temperature is reached at the pressure sensor.• Adjust zero at potentiometer adjusting zero screw and verify on the meter.• Replace the cover screws on the potentiometers.Operating temperature at the PT diaphragm max. 170°F. Higher temperatures will damage the PT.Ambient temperature for the electronics housing max. 170°F. Higher temperatures can result in damage and malfunction.Do not install the pressure transmitter in places where this temperature is exceeded.providing a window into the process8. Maintenance8.1 Maintenance8.1 Maintenance 8.2 Repair/disposal 8.3 Warranty Mounting and electrical connection of the PT must be done by specialists with EMC training, following all applicable regulations, and in pressureless, voltage-free condition with the machine switched off.The machine must be secured against being switched back on!Burn hazard!The PT can be very hot when removed.Wear protective gloves!ESD sensitive component. Electrostatic discharge may damage the PT. Take ESD precautions.Always remove the PT before cleaning the machine with abrasives or steel wire brushes or suchlike.Removing the transmitter if the medium is in solidified condition can damage the diaphragm of the PT.Do not clean the screw-in section of the PT with hard objects. This will damage the PT!Always use a torque wrench applied to the designated hexagon collar when screwing the PT in and out. Do not apply the tool to the housing or housing/electrical connection!161717providing a window into the process• Remove the PT.• Carefully clean the PT/process connection of the transmitter with a soft cloth, while the medium is still malleable.8.2 Repair/DisposalPlease send defective PTs to your DYNISCO representative.For addresses, see the back cover of the operating manual.8.3 WarrantyThis DYNISCO product is warranted under terms and conditions set forth in the DYNISCO web pages. Go to and click “warranty” at the bottom of any page for complete details.9. Troubleshootingproviding a window into the processDyniscoLLC38 Forge ParkwayFranklin, MA 02038USATel: +1 508 541 9400Fax: +1 508 541 9436Email:********************Dynisco Extrusion1291 19th St Ln NWHickory, NC 28601Tel: 828-326-9888Fax: 828-326-8882Email:********************Dynisco Polymer Test Westgate II730 Hemlock Road Morgantown, PA 19543Sales & Service:Tel: 508-541-9400Fax: 508-541-6206Email:******************Dynisco Europe GmbH Wannenäckerstraße 2474078 Heilbronn DeutschlandTel: +49 7131 2970Fax:+49 7131 23260Email:*************************Dynisco Instruments S.a.r.l. 466, rue du Marché Rollay 94500 Champigny sur Marne FranceTel: +33 1 4881 8459Fax: +33 1 4881 8334Email:*************************Dynisco.s.r.l.Via Adriatico, 2/220162 MilanoItaliaTel: +39 02 661 01733Fax: +39 02 661 02908 Email:************************Dynisco UK Ltd.Silver Birches Business Park Aston Road, Bromsgrove Worcestershire B60 3EU Great BritainTel: +44 1527 577077Fax: +44 1527 577070 Email:********************* Dynisco SPOL, S.R.O.cp. 579756 55 Dolni BecvaCzech RepublicTel: +42 0571 647228Fax: +42 0571 647224 Email:*********************.czDynisco B.V.Muziekplein 67PO Box 666NL-5400 AR UdenThe NetherlandsTel: +31 413 250665Fax: +31 413 260548Email:**********************。
mysql数据库操作手册

MySQL是一种流行的开源关系型数据库管理系统(RDBMS),广泛应用于Web应用程序和其他各种类型的软件开发项目。
以下是MySQL数据库的基本操作手册,包括数据库的创建、表的操作、数据的插入和查询等。
1. 连接到MySQL服务器mysql -u 用户名-p在提示下输入密码以连接到MySQL服务器。
如果在本地服务器上,可以省略-h主机名。
2. 创建数据库CREATE DATABASE 数据库名;3. 选择数据库USE 数据库名;4. 创建表CREATE TABLE 表名(列1 数据类型,列2 数据类型,...);5. 查看表结构DESC 表名;6. 插入数据INSERT INTO 表名(列1, 列2, 列3, ...)V ALUES (值1, 值2, 值3, ...);7. 查询数据SELECT 列1, 列2, ...FROM 表名WHERE 条件;8. 更新数据UPDATE 表名SET 列1 = 值1, 列2 = 值2, ...WHERE 条件;9. 删除数据DELETE FROM 表名WHERE 条件;10. 基本查询-查询所有数据SELECT * FROM 表名;-查询满足条件的数据SELECT * FROM 表名WHERE 条件;-查询并排序SELECT * FROM 表名ORDER BY 列名[ASC|DESC];-聚合函数SELECT COUNT(*), A VG(列名), MAX(列名), MIN(列名), SUM(列名)FROM 表名;这只是MySQL数据库的一些基础操作。
对于更复杂的查询、索引、事务等方面的操作,需要更深入的学习和理解。
MT-40系列生物显微镜操作手册说明书

MT-40 Series Biological MicroscopeManualThis manual expatiates the using method, troubleshooting and maintenance about MT-40 series biological microscope. Please study this manual thoroughly before operating, and keep it with the instrument. The manufacturer reserves the rights to the modifications by technology development. On the basis of operation ensured, technical specifications may be subject to changes without notice.Contents MT-40 Series Before Use1. Components (1)2. Assembling (3)2-1 Assembling Scheme (3)2-2 Assembling Steps (4)3. Operation (6)3-1 Set Illumination (6)3-2 Place the Specimen Slide (6)3-3 Adjust the Focus (7)3-4 Adjust the Focusing Tension (7)3-5 Adjust the Interpupillary Distance (7)3-6 Adjust the Field Diaphragm (Iris Diaphragm Koehler Illuminator Condenser Optional) (8)3-7 Adjust the Aperture Diaphragm (8)3-8 Use the Oil Objective (100X) (9)3-9 Use the Filter (9)3-10 Replace the Fuse (10)4. Technical Specifications (11)4-1 MT-40 Series Biological Microscope Technical Parameters (11)4-2 Parameters of objective (11)5. Troubleshooting (12)1. Operation Notice1. As the microscope is a high precision instrument, always operate it with care, and avoid physical shake during the operation.2. Do not expose the microscope in the sundirectly, either not in the high temperature, damp, dust or acute shake. Make sure the worktable is flat and horizontal.3. When moving the microscope, use both hands to hold its back hand-clasping ① and the front base ②, and lay it down carefully (see Fig. 1). ★ It will damage the microscope by holding the stage, focusing knob or head when moving.4. When working, the surface of condenser will be very hot. Make sure there is enough room for the heat dissipating around the condenser ③ (see Fig. 2).5. Connect the microscope to the ground to avoid lightning strike.6. For safety, make sure the power switch ④ is at “0” (off) and power it off before replacing the bulb or fuse, and wait until the lamp cools down (see Fig. 2).★ Bulb selected only: Single 3W LED light.7. Wide voltage range is supported as 100~240V . Additional transformer is not necessary. Make sure the voltage is in this range.8. Use the special wire supplied by our company.Fig. 1Fig. 22. Maintenance1. Wipe the lens gently with a soft tissue. Carefully wipe off the oil marks and fingerprints on the lens surfaces with a tissue moistened with a small amount of 3:7 mixture of alcohol and ether or dimethylbenzene.★ As the alcohol and ether is flammable, don’t place these chemical near to fire or fire source. For example, when turning on or turning off the electrical device, please use these chemical in a ventilated place.2. Don’t use organic solution to wipe the surfaces of the other components. Please use the neutral detergent if necessary.3. If the microscope is damped by liquid when using, please power it off immediately and wipe it dry.4. Never disassemble the microscope, otherwise the performance will be affected or the instrument will be damaged.5. After using, cover the microscope with a dust cover.3. Safety SignSign Signification Study the instructions before use. Unsuitable operation would lead to person hurt or instrument faulty. | Main switch ON OMain switch OFF- 1 -- 2 -- 3 -- 4 -- 5 -- 6 -- 7 -3-3 Adjust the Focus1. Move the objective 4X to the light path.2. Observe the right eyepiece with right eye. Rotate the coarse focusing knob until the ① image appears (see Fig. 10).3. Rotate the fine focusing knob ③ for clear details.★The position screw ② can stop the objective touching the clips.3-4 Adjust the Focusing TensionIf the handle is very heavy when focusing or the specimen leaves the focus plane after focusing or the stage declines itself, please adjust the tension adjustment ring ① (see Fig. 11).To tighten the focusing arm, rotate the tension adjustment ring ① according to the arrowhead pointed; to loosen it in the reverse direction.3-5 Adjust the Interpupillary DistanceWhen observe with two eyes, hold the base of the prism and rotate them around the axis until there is only one field of view.“。
操作手册 (中英文)

操作手册Operation Manual一、监控电脑的开启按电脑上的电源键,电脑会自动启动直至出现登陆的对话框,在对话框的用户名内填入“operator”直接敲击回车键就会自动进入操作员权限的主画面,如下图:1. The opening of the monitoring computerPress the power button on the computer, and the computer will automatically start to login dialog box, then enter the user name of “operator” in dialog box and directly hit Enter key, and then the computer will automatically enter the main screen of operator authority, as shown in the following figure:(图-1)(Figure-1)如果在对话框的用户名内填入“Administrator”进入工程师权限操作的时候是需要密码的,这个密码会随资料一起交付给相关人员。
If the dialog box is filled in the user name of “Administrator” to enter engineer authority s need a password, the password will be with the data delivery to the relevant personnel.二、监控画面的说明2. Note for monitor screen1、点击图-1中的“HP BOILER”,就会进入20T HP boiler的监控界面,如图-2所示,在画面上可以之间看到锅炉的所有的温度、压力、流量、阀门开度、变频器频率等数据的检测值,在图-2所示的红色字体的闪烁代表的是报警,有相应的英文所显示。
tidb操作手册
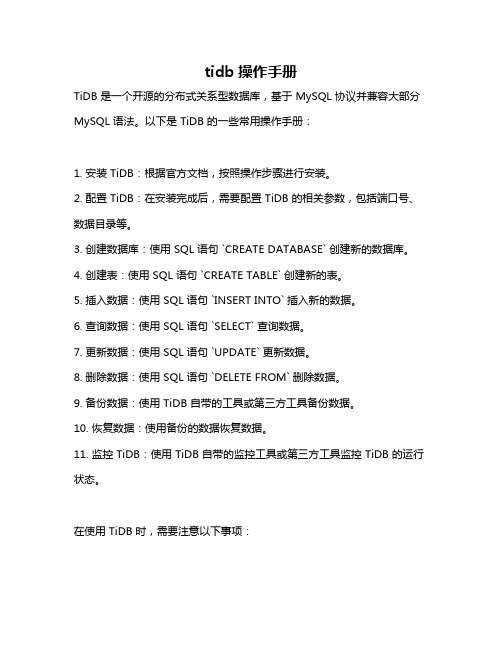
tidb操作手册
TiDB 是一个开源的分布式关系型数据库,基于 MySQL 协议并兼容大部分MySQL 语法。
以下是 TiDB 的一些常用操作手册:
1. 安装 TiDB:根据官方文档,按照操作步骤进行安装。
2. 配置 TiDB:在安装完成后,需要配置 TiDB 的相关参数,包括端口号、数据目录等。
3. 创建数据库:使用 SQL 语句 `CREATE DATABASE` 创建新的数据库。
4. 创建表:使用 SQL 语句 `CREATE TABLE` 创建新的表。
5. 插入数据:使用 SQL 语句 `INSERT INTO` 插入新的数据。
6. 查询数据:使用 SQL 语句 `SELECT` 查询数据。
7. 更新数据:使用 SQL 语句 `UPDATE` 更新数据。
8. 删除数据:使用 SQL 语句 `DELETE FROM` 删除数据。
9. 备份数据:使用 TiDB 自带的工具或第三方工具备份数据。
10. 恢复数据:使用备份的数据恢复数据。
11. 监控 TiDB:使用 TiDB 自带的监控工具或第三方工具监控 TiDB 的运行状态。
在使用 TiDB 时,需要注意以下事项:
1. TiDB 是分布式数据库,需要考虑数据的分片和复制。
2. TiDB 的 SQL 语法与 MySQL 基本兼容,但也有一些差异,需要注意。
3. 在使用过程中,需要关注 TiDB 的性能和稳定性,及时调整配置参数。
4. 在生产环境中,需要做好数据备份和恢复的准备。
5. 需要关注 TiDB 的版本更新情况,及时升级以获得更好的性能和稳定性。
Sarad Radon Vision 操作手册说明书

Setting the clock (initial operation or after battery removal for longer periods)Download the software Radon Vision and the USB driver from our website (www.sarad.de) and install both on your computer.the manual of Radon Vision on our website.Sampling Turn on the display by button (B) and set the slide switch (D) to the right. The first measured results will be presented after four hours (Avg = Average of the whole measurement, 24h = average of the last 24 hours). The display will alternate between temperature/humidity and Radon automatically. The unit records the readings every four-hours. When operated from battery, the display turns off after 30 seconds. Use button (B) to turn it on again. Another keystroke turns on the backlight. If Radon 3concentration exceeds 300Bq/m , the red LED (A) starts blinking (four consecutive flashes each four seconds). To cancel a measurement, shift the slide switch (D) into the left position.Hints for battery and mains power operationThe Radon Scout Home can be operated several months by battery. Here are some tips for a long-lasting battery operation: Use batteries of best quality brand that are especially optimized for long term use and low power consumption.Reduce usage of display and backlight.In case of low battery the red indicator (A) starts blinking, one single flash each four seconds. The measurement continues for a few days but it is impossible to start a new measurement. Remove discharged batteries immediately. Do not dispose batteries in domestic waste. You are legally obliged to return them to the appropriate waste collection centres. The internal clock will be sustained for a couple of minutes during battery replacing. For mains power operation, use always a wall adapter with USB connector. Do not use the USB port of a computer for power supply.Selection of the right place of measurementDo not expose the instrument to permanent shocks or vibrations. Place the unit stationary in that room where you will stay most frequently. Avoid heat sources or radiofrequency emitting devices (e.g. mobile phones, microwave stoves, DECT phones or base stations) in the immediate surrounding of the instrument. The distance from the wall should be more than 25cm (10inches) because the wall itself could be the reason for an increased Radon concentration.Further processing of measured resultsMeasured values of the previous eight years are stored in the instrument (circular memory structure). The measured data can be read through the USB port (C) and shown, exported or printed by Radon Vision. Refer software manual (SARAD website) to findout the complete functionality of Radon Vision. Manual Radon Scout HomeThank you for the purchase of a Radon Scout Home. The instrument hasbeen designed for long-term indoor measurements of the Radonconcentration. The manufacturer cannot guarantee for damages that willresult from use other than intended. Please read the manual carefullybefore operating the unit.Set the slide switch (D) into theleft position (sampling stopped)Unscrew both screws (E) at the rear of the instrument Remove rear panel by slightly tilting on theupper rounding Insert/replace the batteries (AAA/LR6) on the left and right (bottom first – check polarity)03/2020 - SARAD GmbH www.sarad.de 1E D C A BEN。
- 1、下载文档前请自行甄别文档内容的完整性,平台不提供额外的编辑、内容补充、找答案等附加服务。
- 2、"仅部分预览"的文档,不可在线预览部分如存在完整性等问题,可反馈申请退款(可完整预览的文档不适用该条件!)。
- 3、如文档侵犯您的权益,请联系客服反馈,我们会尽快为您处理(人工客服工作时间:9:00-18:30)。
KBA-Metronic 关于我们:.在德国Veitshochheim 有近40年的产品研发、设计及市场运作。
.客户公认的标识行业解决专家,如在食品制造、自动化、医药工程、机械制造、电子工程及建筑材料领域。
.全球联网的销售和服务代理。
公司:KBA-Metronic GmbH 喷码标识系统.高宝-美创立致力于印刷和标识设备的研发、生产和销售。
.高宝-美创立是印刷和标识技术的领导者 .保证精密、可靠的品质。
.极富创新精神。
.保证所有系统组装完成来自同一地方。
1.纲要:.中型制造企业 .超过300名员工 .公司创建于1972年.公司总部设在Veitshochheim (法伊茨赫希海姆) .子公司设在荷兰.在全球范围内超过30家销售和服务代理商 .从1996年开始具备ISO9001证明 .从2004年开始成为KBA 集团成员.在2005年3月开始更名为KBA-Metronic 股份公司.2010年开始分为两家公司,分别为KBA-Metronic GmbH 喷码标识系统制造公司和KBA-MetroPrintalphaJET 发展历史.在德国法伊茨赫希海姆超过25年的研发,设计,制造和市场引领,特殊的喷印应用及喷码标识行业解决方案。
.作为KBA AG的附属公司,我们是可持续的为集团公司的成功作出贡献1987-1994 1992-2001 1999-2011 2011alphaJETA alpha JET B alphaJET C alpha JET evoalphaJET C alphaJET C-HS alphaJET C4 alpha JET E alpha JET evo alphaJET tempo alphaJET into alphaJET pico新一代 alphaJET evo家族新的连续性油墨喷码机- 新一代缩小了配件和软件的兼容性alphaJET evo家庭alphaJET evo:食品,包装,电子,自动化,管材等行业alphaJET tempo:线缆,管道,管材,饮料,烟草等行业alphaJET pico: 线缆,医药,化妆品,烟草等行业alphaJET into:食品,饮料和烟草,医药,包装等行业alphaJET into.alphaJET into=所有领域的基本应用.适合在多功能市场领域的标识,如:食品,饮料,烟草,医药,包装.10.4英寸触控屏.1*RS232接口.信号灯或远程连接器可选.打开四个螺丝就可看到电子部分.简化的电源供给(没有备用电池功能).简化的底板产品特色:以下列出的是实际中与在连续式喷码机市场中竞争对手的比较:.更快的连续式喷码机(evo和tempo分别比C型要快10%和40%).48点阵喷印高度(professional 版本).最低的溶剂消耗(在温度20℃时候,使用55u喷嘴,消耗1.2ml/h,70u喷嘴,消耗1.6ml/h).紧凑和稳定的油墨系统.最低的维护成本.最广泛的油墨类型.最小的几何打印头.可拆除的,可旋转的操作终端.大尺寸彩色触摸屏.有最广泛的条形码.有大量的特殊功能.很高的防护等级(IP65).简易的操作.可选配不间断电源技术参数:重量:大约27kg+4kg操作终端外壳:不锈钢320mmx320x510(含操作终端的为700)mm防护等级: IP65工作温度: 5℃--45℃工作湿度:相应湿度最大90%,无冷凝噪音:噪音<60 dB(A)电源供给: 86V-264V(+/- 10%) 广泛的电源供给 50/60赫兹电流消耗:最大0.5A 230V,1.0A 110V显示屏: 10.4英寸,彩色,800x600(XVGA),可移除(除了AJ into)喷头: 145x40x40mm, 晶振加热器,喷嘴快门喉管: 4米,显示屏连接管4米可选安装UPS:不间断的电源供给(电源桥接故障大约2分钟)接口: RS232/USB(仅存储设备)/以太网/4个输出/8个输入硬件:主板:控制油墨系统基板:中央控制系统加密狗: evo/tempo/pico/into/light/standard/professional/染料墨/颜料墨软件:嵌入式操作系统WIN CE<->不是电脑上的WindowsalphaJET evo 特色浏览.最简易的操作通过一个操作终端或者PC(WYSIWYG). 没有废气排放(低废气排放)因为有溶剂回收系统 因此溶剂消耗会降到最低.1-4(6)行打印(喷印分解:垂直32(48)点阵).在字符单个宽度为2.5mm的时候喷印速度最高6.7米/秒(evo)和10米/秒(tempo).喷头简易合宜,并可以任意位置安装.可以安装到所有的产品线上.可以与相关联的机械设备实行网络联机.通过full unit可以用来操作别台机器(或和别台机器同步化).也可以通过外部设备同步结合X、Y轴系统、图像处理、产品分离装置或条码扫描仪alphaJET evo家庭喷印可能之应用.true type文本.有效期.批号,条码,图形标志,班次,递增、序列号.自动的时间,Julian日期(light机型不适用),时间.二维码(light机型不适用).数据库喷印(可选).WSM(DMS) 计米软件(light机型不适用).列表喷印(只有professional适用).变量数据通过以太网,USB和RS232…alphaJET evo家庭可喷印的材质.纸板,折叠纸盒,吸卡,纸.标签.箔 .玻璃 .有机物质 .食品 .塑料 .橡胶产品 .金属 .电路板可集成的应用.产品线.标签机.包装机.特殊设备.uda FORMAXX .独立单元(离线式)可用的油墨.标准墨(MEK,Ethanol-Aceton, Ethanol).颜料墨(白,黄,蓝绿色等).PVC墨.特殊墨:可喷印在食品上的墨水变色油墨高温油墨可喷印蛋的食用墨氟氯烷墨(附着力好)抗苯墨不褪色墨紫外线可读墨…必须确保机台使用原装的美创立油墨和溶剂喷印控制软件仅供standard 和professional机台WSM(DMS)连续模式下的距离测量系统(德国:WSM)是记录喷印开始到下一个喷印开始的距离(如果没有WSM功能,只能输入第一个文本喷印结束到第二个文本喷印开始之间的距离).因为这个,就有可能实现在连续喷印模式下,不同长度的不同位置上喷印的准确性.OPS 顺着喷印的方向每个点的喷印位置都会被测量,等再次喷印的时候,会由上个点的喷印位置继续喷印。
FTC (飞行时间补偿)墨滴的飞行时间(5-8ms取决于喷印头与物体的距离)被用于依时间计算出正确的开始喷印位置,这个点位置是依照产品的速度来的(取1m/s来计算取近似值)Textlist 定期打印不同标签 *仅供professional版本二维码喷印应用示范:Example applicationsBremer Werk für Montagesysteme (BWM), DCoding of cell phone cases: moving of the printheadtransverse to the transport direction of the cell phone casesExample applicationsWellen nutrients factory, Krefeld, DPr inting the expiry date on baking powder bagsExample applicationsZentis confectionary factory, Aachen, DExample applicationsEggebeck (KVE) potato handler, DExample applicationsCreaton brickworks in Wertingen, DPrinting a white brick securing band having an approx.1 m long black own advertDifficulties:Securing band is very fast=> because of this, Metronic hasdesigned a kind of memory device,that causes the band to run slowerand to overrun a little.Example applicationsCreaton brickworks in Guttau-Kleinsaubernitz, DExample applicationsNestle in Berlin, DPrinting the expiry date on cardboard boxes操作案例电缆引导装置操作案例汽车轮胎标记操作案例打印样品(标准应用)操作案例样品打印(标准应用)操作案例打印样品(圆形标记)操作案例打印样品:标记二维码周边设备:电缆引导装置规格:尺寸:包括喷头长400mm x 宽160mmx300mm 材料:镀铝及V2A电缆直径:最小1mm ,最大20mm喷印速度:单行喷印(5*5矩阵)最大6m/s 喷印开始:经由测量距离或时间间隔喷印选择:输出标记,数据,标志,数字,文本等等 喷印影像:自由编排(1-3行) 电缆引导装置为圆形电缆,与alphaJET 配合使用, .电缆直径1-20mm .易于整合.精确的喷印位置 .电缆引导无抖动.喷印引向位置和喷头离电缆的距离可经由支架调整 .安装一个同步器可监测运行速度及距离 .在alphaJET 上直接评估测量距离 .一道屏障,阻止电缆来回移动 .能够整合到所有的产线设备上 .其他电缆格式的快速切换alphaJET客户.Aida card.Alcatel.BDF (Beiersdorf).BMW.Bosch.Creaton.FCI. Fränkische Rohrwerke .Gretag (Kodak).HEW Kabel.Intersnack.Leoni Kabel.Nestle.Pirelli.Reemtsma.Rehau.Siemens.VDO.Zentis...alphaJET evo-family结构与功能连续喷墨的原理导电油墨通过集成泵从喷嘴流出,从而形成一条墨线.超声波变频器将电子信号变成机械振动,并将墨线分裂一颗颗的小墨滴.墨滴通过充电电极时会被充电(带+/-电),充电后经过高压偏转板,相应的转移带电墨滴,这一过程决定了墨滴在基材上的位置。
结构与功能连续喷墨的原理超声波换能器:将电信号直接转换成机械振动油墨供应喷嘴在充电电极内墨点分离充电电极:给分离的墨点充电墨点分离必须发生在充电电极,因为只有在分离时才能充电检测电极:检测从充电电极来的墨点充电情况高压偏极板(+)高压偏极板(-)HV最大值HV最小值HV0-100%结构与功能 连续喷墨的原理高压偏极板(+)可调整,必须控制在3000-6000V ,取决于喷头与喷印物体间的距离.充电电极:给分离的墨点充电回流口:回收没有使用的油墨到油墨系统超声波换能器:将电信号直接转换成机械振动检测电极:检测从充电电极来的墨点充电情况 高压偏极板(-)喷头:概述A 喷头盖 1 上偏转板 2充电检测槽 3充电槽 4喷嘴 5喷嘴快门 6下偏转板 7回流孔.尺寸: 40x40x145mm(长X 宽X 高) .喷头位置可以任意安装 .易清洗.喷头有快速发条可以快速打开和关闭 .喷头加热器使墨滴形成均匀.内置LED 灯和放大镜,可以更清晰的观察到墨滴的状况 .喷头快插 .无需外接气源油墨系统—alphaJET family.模块化和易于访问.高品质,耐用的部件造就了高可用性.维护简便,省时.高效但节能Array .标配溶剂回收系统.没有油墨和溶剂盒.没有油墨代码混合桶+溶剂回收系统 回流滤芯溶剂传感器 真空泵空气滤芯压力泵压力缓冲器压力泵前过滤器主滤芯真空泵阀块2压力传感器阀块1 +V1油墨阀供墨系统图表介绍图表介绍:机身.尺寸320x320x700mm(长x宽x高),已包含终端操作.时尚的设计.不锈钢机身.IP65的防护等级.工作温度5℃--45℃.电阻式触摸屏,可以被拆除和倾斜(除了alphaJET into)外部连接(概要)分配: A:电源线(广泛的电源供给)B:外接气管,6/4mm,可选装1 :主开关2:USB接口3:com1口4:com2口5:网线接口RJ45(evo light除外) 6:终端操作器接口7:远程端口(evo light除外)8:警报输出接口:外接警报器9:产品感应器/同步器接口10:产品感应器/同步器接口11:I/O接口12:信号栈(自选安装)外部连接(概要)明细远程端口2针警报输出端口4针产品感应器同步器端口7针产品感应器同步器端口7针自选信号输入或输出16针外部连接明细:机器提供两个平行的7PIN插座分别用于光眼(传感器)和同步器,它们可以插在任何一个7PIN插座上。