JAX500 600 DHZ系列说明书
TH9520 磁性元器件综合分析系统使用说明书
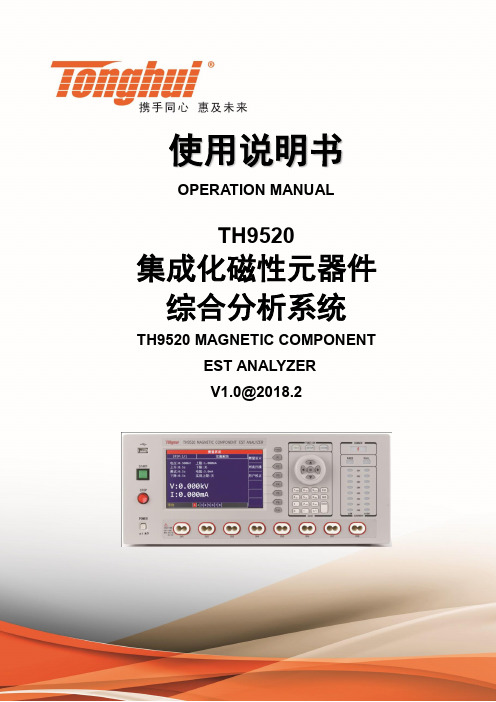
使用说明书OPERATION MANUALTH9520集成化磁性元器件综合分析系统TH9520 MAGNETIC COMPONENTEST ANALYZER***********目录第1章概述................................................................................................................................. 1-11.1引言................................................................................................................................. 1-11.2使用条件 ......................................................................................................................... 1-21.2.1 电源 .............................................................. 1-21.2.2 环境温度与湿度...................................................... 1-21.2.3 预热................................................................ 1-21.2.4 几点注意问题........................................................ 1-21.3体积与重量...................................................................................................................... 1-31.4安全要求 ......................................................................................................................... 1-31.4.1 绝缘电阻............................................................ 1-31.4.2 绝缘强度............................................................ 1-31.4.3 泄漏电流............................................................ 1-41.5电磁兼容 ......................................................................................................................... 1-41.5.1 电源瞬态敏感度按GB6833.4的要求。
海康威视 LVRD500 系列非接触雷达水位传感器说明书
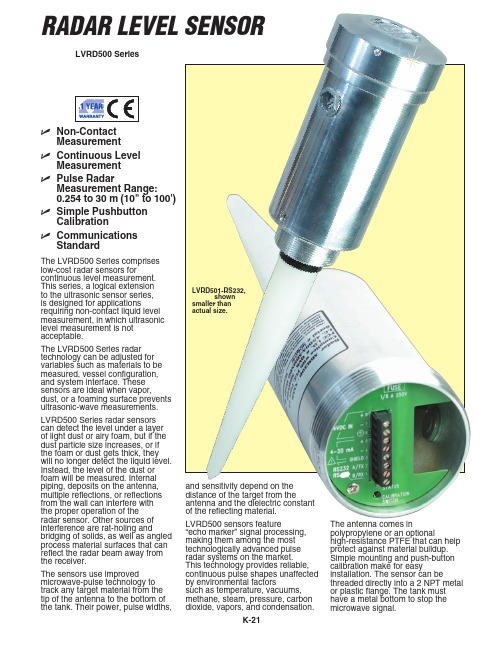
81,7(' 67$7(6 ZZZRPHJDFRP 7&20(*$
6WDPIRUG &7
&$1$'$ ZZZRPHJDFD /DYDO 4XHEHF 7&20(*$
communication device
Accessories
Conduit Entry: 1⁄2 NPT standard
Model No. Price
Description
Mounting: 2 NPT, or optional sanitary 2" tri-clamp Housing: Aluminum or optional
DPi8 CNi833
$240 310
1⁄8 DIN process meter 1⁄8 DIN controller with relays
316 SS
FW-205
250
Reference Book: The Consumer Guide to
Ingress Protection: NEMA 4 (IP65)
Power Options:
AC: 115 Vac, 60 Hz or 230 Vac, 50 Hz (±20%), 1.7 VA
DC: 12 to 30 Vdc (optional), @ 0.07 A max, 24 Vdc
R load = (Vs–6)/24 mA
Output: 4 to 20 mA, 6.1 μA resolution; 750 Ω (isolated on 4-wire models only); optional RS232 or RS485 communications port
高能点火装置

XDH高能点火装置(点火器、屏蔽电缆、点火枪)使用说明书安装、使用产品前,请阅读使用说明书徐州燃烧控制研究院有限公司高能点火装置1 概述1.1产品特点本系列产品属低压电容放电装置,具有放电电压低、火花能量大、外形体积小、操作方便、安全可靠、耐腐蚀等优点。
1.2主要用途及适用范围装置适应多种不同燃料的点火能量要求,广泛用于电力、石化、冶金、航空、航天等点火领域。
1.3型号的组成及其代表意义装置的型号标记由企业名称代号、产品名称代号、产品主参数及结构、特性代号4部分组成。
图示如下:结构、特性代号:T为手提型、F为信号反馈型、B 为Ex隔爆型、Z为充电直流便携型;L为铝铸造外壳;C为冲压外壳。
产品主参数:贮能能量,J;产品名称代号:高能点火装置;企业名称代号:徐州燃烧控制研究院有限公司。
2 工作原理本系列点火装置由XDH点火器、XDZ点火枪及XDL屏蔽电缆组成。
交流工频220V或110V,通过升压整流变换成直流脉动电流,对贮能电容充电。
当电容器充满时,放电电流经放电管、扼流圈、屏蔽电缆等传输至点火枪半导体电嘴,形成高能电弧火花。
当点火装置停止工作时,电容器上的剩余电荷通过泄放电阻泄放。
(见附图1)3 技术特性3.1主要参数3.2 主要性能用户应依据燃料的种类按下表正确选用点火装置的贮能等级。
贮能等级 2 焦耳6焦耳20焦耳100焦耳配用点火装置XDH-2 XDH-6 XDH-20 XDH-100 适用燃料种类可燃气可燃气、轻油轻油、原油原油、重渣油4 外形及安装尺寸(见附图4)5 安装、调试5.1点火器用螺栓紧固件水平或垂直安装牢固;5.2装置应保护接地或保护接零;5.3屏蔽电缆两端的螺母分别和点火器的输出端及点火枪输入端的螺纹旋接,两端必须拧紧,紧密贴合中心电极;如果电极间存有间隙,则会引起中心电极的放电烧熔;(见附图2)5.4点火枪电嘴端应伸入燃料区浓度最密处;依据稳燃器的回流和油枪喷射角的具体情况确定L,经验值取100~200mm;(见附图3)5.5装置安装、调试后,接通电源应能可靠发火;当电源电压过低,发火频率慢时,调整变压器次级输出焊接线,使次级电压升高;当电源电压过高,发火频率快时,调整变压器次级输出焊接线,使次级电压降低。
上海仪集仪表有限公司(国产ABB系列)JAX-ME智能执行器操作说明
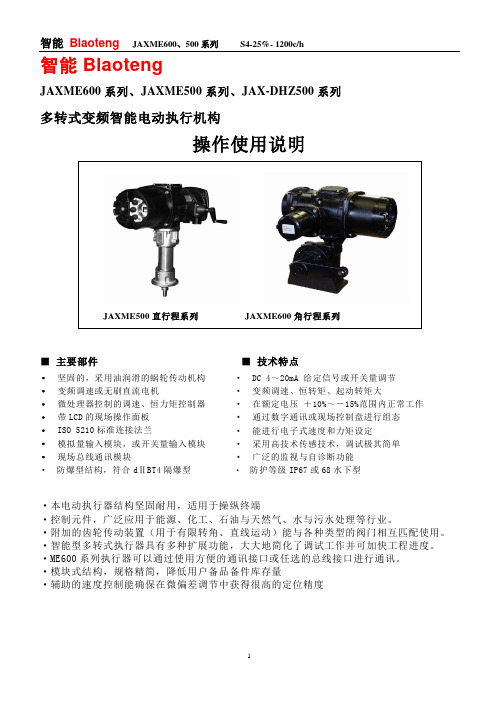
智能BlaotengJAXME600系列、JAXME500系列、JAX-DHZ500系列多转式变频智能电动执行机构操作使用说明·本电动执行器结构坚固耐用,适用于操纵终端·控制元件,广泛应用于能源、化工、石油与天然气、水与污水处理等行业。
·附加的齿轮传动装置(用于有限转角、直线运动)能与各种类型的阀门相互匹配使用。
·智能型多转式执行器具有多种扩展功能,大大地简化了调试工作并可加快工程进度。
·ME600系列执行器可以通过使用方便的通讯接口或任选的总线接口进行通讯。
·模块式结构,规格精简,降低用户备品备件库存量·辅助的速度控制能确保在微偏差调节中获得很高的定位精度上海仪集仪表有限公司(国产ABB系列)目录1、适用范围 (2)2、安全注意事项 (2)3、技术参数 (2)4、菜单结构和基本参数设定 (2)5、电气连接原理图 (8)6、通讯接口 (9)7、故障与意外情况处理 (11)8、隔爆产品注意事项 (13)9、JAXME600d系列输出扭矩参数表………………………………………… 14~1510、JAXME600d系列产品安装尺寸基本参数表…………………………… 16-1711、JAXME500d系列输出推力参数表................................................18~20 12.JAXME500d系列产品安装尺寸基本参数表................................. 21-22 13、产品型号命名及附言 (23)1.本操作说明书适用范围a)本操作说明适用范围为软件版本1.02的Blaoteng JAXME600/500全系列产品,也可供、JAXDHZ-500多回转系列产品使用参考。
b)适用于隔爆型,的JAXME600“d”角行程电动执行机构系列、JAXME500“d”直行程电动行机构系列,也可用于JAX-DHZ多回转智能电动执行机构系列产品的使用说明。
HYBRID 600 使用说明书
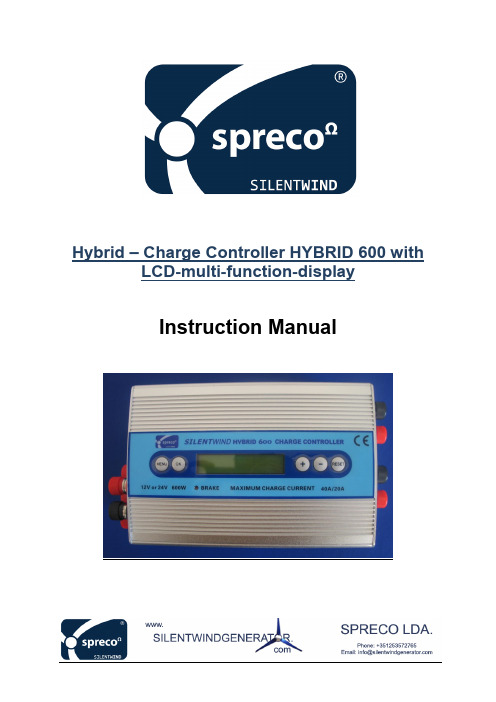
Hybrid – Charge Controller HYBRID 600 with LCD-multi-function-displayInstruction ManualCongratulations, you have bought a high-quality SPRECO hybrid charge regulator HYBRID 600Before first using this gadget please carefully read this manual .General information:The Silentwind-Charge-Regulator HYBRID 600 is a combined wind and solar charge regulator with an inbuilt micro-controller. The Silentwind-charge-controller HYBRID 600 was especially developed for the Silentwind Generator and enables you additionally to install solar panels up to a wattage of 180 Watt peak or to a max. current of 10A.Consumers with a maximum current of 10 Amps that are connected to the deepcycle output can be automatically switched off or on by a deep cycle protection function.All operating parameters can be seen on an LCD-display.You can adjust the charge regulator with 5 touch keys on the right and left of the LCD-display.A LED´s on top of the controller additionally informs you about the operating status “brake active”.A LED on top of the case, below the LCD-display, additionally informs about the either manually or automatically activated brake function.A thermically switched vent provides the correct operating temperature.The Silentwind Generator generates 3phase AC-voltage. In the charge controller AC is transformed to DC. 12 or 24 voltage is automatically detected after the first installation. All types of lead batteries (Gel, AGM and acid) can be charged.The suitable maximum charge voltage - depending on the type of battery - must be adjusted in the Setup.The charge-controller isAdvice:Please keep in mind that liquid acid batteries can emit dangerous explosive gas. If the place where you mount the charge controller is close to these batteries, ensure efficient ventilation. Gel or AGM batteries are normally maintenance free and do not emit gas if properly charged.Always make sure charge controller is mounted in a dry and as cool as possible place.Inhaltsverzeichnis:1.wiring diagramm42.technical data4ponents of the charge controller63.1frontside63.2backside73.3LCD –display73.4LED –indicator74.mounting the charge controller54.1mounting by holding brackets54.2mouting in a slurry wall trench55.Cable– cross section86.installation and Connection of the charge controller87.connecting solar panels108.programming charge controller119.programming instruction129.1.operating keys129.2.battery voltage and charge current129.3.charge cut-off voltage139.4.charge amount in ampere hours (Ah)139.5.charge amount in kilowatt hours (kWh)139.6.current charging power149.7consumer settings149.8brake adjustments159.9generator voltage1610.troubleshooting171.wiring diagramm2.Technical datahybrid-charge controller type HYBRID 600 Battery system voltage (automatically detected)12 or 24 Volt Max. power input of the wind generator600 WMax. current input of the wind generator30AMax. power input of the solarpanel180WpMax. current input of the solarpanel10AMax. open circuit voltage input of the solarpanel50VDCMax. total charge current 40 AMax. switch off current at LOAD-output (Load)10 AMax.voltage adjustable for the battery types acid, gel or AGM Dimensions (LxWxH) in mm190 x 120 x 65 Weight1,15 kg Suitable for acid, gel and AGM Warranty24 monthsFeaturesThermically switched vent automatically Cable connection screw terminals Ø 7mm Integrated electronic brake charge limitation Integrated manual brake switch storm brakeLCD-display of all relevant working data W, A, V/Ah, kWh LED shows the operating status brake activeLED for brake function LED occurs =brake activatedponents of the charge controller3.1FrontsideOn the front of the charge controller there are screw terminals to connect the battery. There are also screw terminals for the automatically switched load output (user output) as well as the brake switch to activate manually the brake function.Please note that the brake switch in position “I” means that the brake is activated / switched on manually, but it does not mean that the wind generator is switched on.The brake switch does not totally stop the blade rotation. The blades will still turn slowly. If the brake is manually or electronically activated, the LED “brake” will lit up. The brake switch should be manually activated in case of storm, maintenance or if you want to work close by the Silentwind Generator.For automatic brake mode please switch position “0” (“RELEASE”)Front view:3.2BacksideOn the backside of the charge controller there are screw terminals to connect the wind generator and the solar panels.Rear view:3.3LCD-DisplayOn the top of the charge controller there is an LCD-display that is necessary to adjust the charge controller and that shows you all operating data during the working process.3.4LED-indicationThe LED (brake) shows you that the charge controller has activated the electronic brake function or that the manual brake switch is switched on.4.Mounting the charge controllerThe charge controller can be mounted in various cways. We suggest these possibilities:4.1Mounting with holding plates (brackets)picture 1:Mount the charge controller with the enclosed holding plates as shown in picture 1. Use suitable screws - depending on the mounting material. Screws are not included in delivery.4.2Mounting in a slurry wall trenchpicture 2:As you can see from picture 2 there are 4 mounting holes on the back of the charge controller. Use filister head screws with appropriate (suitable) diameter and screw them into the mounting surface according to the measurements shown in the picture above. Don´t screw them completely into the mounting surface. Place the mounting holes over the screws and slide the charge controller into the 4 slurry wall trenches. Screws are not included in delivery.5.Cable cross sectionAs you can see from the wiring diagram in paragraph 1a 3-pole cable with suitable cross section must be wired from the Silentwind-Generator to the charge controller. The charge power gets from the charge controller to the batteries through two wires (on the AC entrance through three wires) Therefore the cross section of the two wires on the DC output should be larger, we recommend a minimum cross section of 10mm2.See below table to find the correct cable cross section:System voltage 12 VoltDistance fromwindgenerator to thecharge controller in m0 - 910 – 1920 – 2930 – 4445 – 6970 – 110Cable cross section mm2AWG610108166254352501Distance from the chargecontr. to the battery in m0 - 910 – 1920 – 2930 – 4445 – 6970 – 110Cable cross section mm2AWG 108166254352------------System voltage 24 VoltDistance fromwindgenerator to thecharge controller in m0 - 910 – 1920 – 2930 – 4445 –6970 – 110Cable cross section mm2AWG 2.514412610108166254Distance from the chargecontr. to the battery in m0 - 910 – 1920 – 2930 – 4445 – 6970 –110Cable cross section mm2AWG 108166254352------------6.Installation and connection of the charge controller:The charge controller should be mounted close to the battery in a ventilated and cool location which enables you to read the information shown on the LCD display and to operate the manual brake switch easily.Safety advice:Especially acid batteries can emit gas when charging. Therefore the charge controller must not be installed close to those batteries. In case of high concentration of dangerous gas there is a risk of explosion. Please note the safety regulations, -advice of the battery producer.If the acid batteries are equipped with ventilation pipes to the exterior or if the storage room of the batteries is otherwise ventilated, the charge controller can be installed close to the batteries.Please find a sketch of the wiring diagram in the paragraph 1 of this manual.Make sure that you fix the wires properly to prevent them from getting loose due to vibrations. Fix the plastic screw nuts sufficiently to ensure electric contact.We recommend the use of the enclosed wire kits3 x H07V-K 4mm2, red (input of 3 phases of the wind generator)1 x H07V-K 6mm2, red (output "+" to battery)1 x H07V-K 6mm2, black (output "-" to battery)Connect the free end of the connecting wire with your wires coming from the wind generator and the battery with suitable insulating screw joints.In case you do not use the connecting wires we recommend the use of crimp type cable sockets to fix your wires directly to the charge controller. After having fixed the crimp type cable sockets with the bared wires these can be fixed to the cable sockets.It is most important that you first connect the charge controller to the battery with the right polarity.Attention:On the output of the charge controller there must not be an additional brake switch ! In case there is such a brake switch due to the previousinstallation of a wind generator this must be removed.Please connect the enclosed fuse (50Amp.) close to the battery in the positive wire. The fuse is only included in delivery if you buy a wind generator (not only a charge controller).Attention:The confusion of Plus and Minus will definitely destroy your charge controller. In that case warranty is gone.After the connection of the battery you can connect the load output, the Silentwind Generator and -if required- a solarpanel. On the 3-phase output wires of the Silentwind you need not to pay attention to polarity.If you want to connect 24 volt batteries to the charge controller, make sure that the voltage of the batteries is above 20 Volt. Otherwise the charge controller will detect a 12 volt battery system.If you install this system after having used another windgenerator with a stop switch, make sure that this switch is deactivated or removed.If there is sufficient windspeed when connecting the Silentwind Generator, this will immediately generate electric power at the end of the 3 AC-wires without being connected to the charger. Therefore we recommend to block the Silentwind Generator blades with a rope before connecting the wires to the charger. The 3 AC output wires must be connected to the 3 screw terminals on the back of the charge regulator. (see paragraph 3.2). In a 3 phase AC system the connection order / polarity does not matter.In case you want to connect additional solarpower (max. 180Wp or 10A) to the charge controller, this should be done by using the PV screw terminals.Please make always sure that you do not confuse polarity. You can find the connection diagram in paragraph 7.7.Connecting solar panelsThe charge controller Hybrid 600 is a hybrid controller both for wind and solar energy. Solar panels with a max power of 180 Wp / 10 A can be connected, See technical details page 4.Connect the solar panels according to the following sketch.12 volt system:24 volt system:8.Programming charge controllerBefore first using the charge controller it must be adjusted to the type of battery (acid, gel, AGM) you want to use (see paragraph 9).At first you have to programme the max. possible voltage according to the instructions of the battery manufacturer in step “Charge Off” ( paragraph 9.3). Secondly you have to programme the requested switch off current at the step “Break On” (paragraph 9.8).We also recommend to make use of the additional adjustments according to your individual requirements.If the point of maximum voltage is reached, the Silentwind Generator will stop for 20 minutes.The break mode of the charge regulator generates internal rising temperatures that are thermically detected. Therefore the break time of the Silentwind Generator will be increased in high wind speeds until the internal temperature is reduced by the automatically switched vent.For this reason the charge controller should be installed on a place as cool as possible. Never install the controller at direct solar radiation or sunlight.A special feature of this charge controller is that you can programme the break function. If the maximum possible voltage – according to the type of battery – is reached, the charge controller will switch of the Silentwind Generator. Additionally the maximum charge current can be adjusted (see chapter settings page 12)This means that the Silentwind Generator can also be operated with a larger battery capacity. If a large battery capacity is discharged, a higher charge current will flow in high wind speeds. As you can set the maximum charge current you can prevent overheating of the charge controller. As described in step “Break On” you can reduce the max. charge current according to the requirements.Advice:If the capacity of the batteries is less than 150 Ah, or old batteries have lost their original capacity, the point of max. voltage can be reached very fast although the battery is not fully charged yet. In this case it can be useful to connect an electric consumer to the Load-output, as this will reduce the voltage and thus prevent that the break mode is activated too early.9.Programming instruction9.1Operating keysThe charge regulator has 5 operating keys on the top:∙ With the menu key you move through the menu.∙ With the OK key you move back.∙ with the "+" and "-" keys you can change the different parameters∙ With the RESET key the inbuilt micro-processor is restarted, your settings will not be resetted.9.2Battery voltage and charge currentThe system-voltage is automatically detected as soon as the charge regulator is connected to the battery.Please only connect batteries that are sufficiently charged. If the battery of a 24V system is discharged, it is possible that the charge controller detects a 12 V system. After the first connection the display shows the following data:The display shows:Hybrid NL = 12V system voltageHybrid NH = 24V system voltageIn the display mode you can see above the battery voltage and the charge current. The total current (wind and solar) is shown.9.3Charge cut-off voltageIn the display mode shown above …charge off“you can set the max. possible voltage of your battery with the buttons “+” and “-“ . Please note the instructions of the manufacturer of the batteries. The maximum possible voltage is dependent on the system voltage (12/24V) and the type of battery (acid, Gel or AGM)9.4Charge amount in Ampere hours (Ah)Charge shows how many ampere-hours (Ah) have been charged into your battery. This is updated every 10 seconds.9.5Charge amount in Kilowatt hours(kWh)Charge shows you the amount of kWh have been loaded into the battery. This parameter is updated every 10 seconds.9.6Current charging powerThis shows you the wattage flowing at the moment (incl. Solar-power).9.7Consumer settingsYou can also connect a consumer to the screw terminals of the load output and define when the consumer should be switched on and off. The consumer is called user in the picture above. This shows you how many amphours the user has taken.With the button …+“ and …-… you can define the voltage when the charge regulator should switch off the consumer. Please note that this must not be higher than10 Amp.User on defines the voltage when the consumer can be switched on again. As the voltage of the battery increases when switching off the consumer this will steadily switch on and off the load output if this value is not high enough. This function can also be used with smaller batteries.. So that the charge voltage is not detected too fast, you can connect a consumer additionally. This avoids that the brake will be activated too early.This setting shows how much amps the consumer that is connected to the load output is using.9.8Brake adjustmentWith +/- you can set the current when you want to stop the Silentwind Generator. This prevents overheating, especially with big battery banks and high loading currents. This function can also be used to reduce the RPM of the Silentwind Generator.You can calculate the max. charge current value as follows: The max. power of the Silentwind Generator 400Watts divided by the max. cut-off voltage e.g. 14,4Volt at a AGM battery. The max. possible charge current in this example is 400VA / 14,4V = 27,7Amp.Breaktime:With this setting you can programme the period of time that you want to stop the Silentwind. The longer you programme the time, the longer the first break intervals will take. This procedure will heat up the inbuilt brake resistores resulting in a permanent brake mode until the vent has cooled down. Therefore this time should not be programmed below 50sec.9.9Generator voltage:! Reference voltage - only relevant for service purposes !If the charge controller is correctly connected, the manual break switch on the front of the charge controller can be switched in position “0”. The Silentwind Generator will then start to turn faster until the charging process starts.The charge controller now starts operating and monitors all special settings that you have programmed according to the type of battery and the instructions of the battery manufacturer (see examples for settings).Saftey advice:Please never disconnect the battery wires while the Silentwind Generator is charging. This will immediately destroy the charge controller. If you want to measure the current flowing, an amp-meter must be installed in the positive battery wire. Mind the polarity of the amp-meter. The flowing current can be seen at the LCD-display. Notices10.TroubleshootingThe blades of your Silentwind Generator are turning too slowly∙ The manual stop switch of the charge controller is in position …I“ (“BRAKE”).∙ Connecting the wires possibly caused a short circuit between the wires.∙ The wind speed is too low.∙ The fuse connected to the battery is gone.∙ Your Silentwind Generator or the charge regulator has an internal problem.Please contact your dealer.In order to find the mistake you have to check the installation chain starting at the 3 wires of the Silentwind Generator connected to the charge controller. In case the Silentwind Generator does now start (without connection to the charge controller) the failure is between charge regulator and battery. BE CAREFULL, don´t touch the end of the cables because of the electric power that occurs at these ends. If the Silentwind Generator continues to turn slowly, the failure is between charge controller and Silentwind Generator.Mind the recommended cross section of the wire as well as the recommended minimum capacity of the battery that you want to charge.If the Silentwind Generator generates too little power∙ The wind speed is too low, see the performance diagrams shown in the manual of the Silentwind.The wind speed measured on top of the mast ishigher than at the position of the wind generator!∙ Turbulences by obstacles in the wind direction or the location isunsuitable, mast to short.∙ The wire cross section is not in line with the lenght of the wires installed.(see page 3).∙ The battery-capacity is below 100Ah so that the maximum possible voltage is generated too fast.∙ The battery is too old and has lost capacity so that the maximum power voltage is achieved too fast.Enjoy collecting regenerative power. You contribute protecting the environment and saving your money !Your Spreco Team edition: October 2011。
Alpha500使用说明书(PDF文件)

Alpha 500系列说明书一.注意事项一.注意事项a500系统在使用上非常简单,但在操作时必须注意其安全性,唯有在正确的操作 下,才能增加工作效益,提升生产力。
※以下几点事项,操作者必须严格遵守:1. 请勿任意更改发射机及接收机密码。
2. 经常检查发射机外壳及按键,发现破损应立即更换。
3. 随时注意并检查发射机电压,如没电压或电压不足请立即更换二颗碱性电池(注意电池极性)。
4. 工作前,务必检查紧急停止键是否正常。
5. 任何不正常情况发生时,不可先关闭电源,应立即按紧急停止键。
6. 在300米范围内,避免使用同一频道之遥控器。
7. 在电压不足或视线不佳的情况下,不得使用遥控器。
8. 使用者不得任意变更控制,调整及使用方法。
9. 维修或有调整需求应由具有发射机维修专长之技术人员执行直接监督及负责。
10.使用者不得任意置换零件(如电晶体、振荡器....等)。
11.低功率及射频管理规则:⑴ 依第七条至第九条型式审认或审验合格之低功率射频电机,厂商或使用人不得擅自改变频率、加大功率,外接十四条规定以外之天线或变更原设计之 功能。
⑵ 低功率射频电机之使用不得干扰合法通信,经发现有干扰现象时应停止,并改善至无干扰时方得继续使用。
低功率射频电机需忍受合法通信或工业、 科学及医疗用,辐射性电机之干扰。
⑶ 低功率射频电机之产销厂商或使用人违反擅自使用或变更无线频率、电功率者,依电信法相关条文之规定处罚。
“ 0 ”抑制“ 1 ”不抑制“ 0 ”抑制“ 1 ”不抑制“ 0 ”一般动作“ 1 ”自保持“ 0 ”抑制“ 1 ”不抑制“ 0 ”抑制“0”双继电器动作“ 00 ”一般动作“10”启动3速功能“ 0 ”抑制“ 0 ”一般动作“ 1 ”自保持“ 0 ”一般动作“ 1 ”自保持“ 1 ”不抑制“ 0 ”一般动作“ 1 ”自保持“ 0 ”一般动作“ 1 ”自保持“ 0 ”一般动作“ 1 ”自保持“1”单继电器动作“ 01 ”自保持“ 0 ”一般动作“ 1 ”自保持“0”双继电器动作“1”单继电器动作“ 0 ”一般动作“0”双继电器动作“1”单继电器动作“ 1 ”不抑制“ 0 ”一般动作“ 1 ”自保持“ 0 ”一般动作“ 1 ”自保持“ 00 ”一般动作“ 01 ”自保持“10”启动3速功能“ 0 ”一般动作“ 1 ”自保持“ 0 ”一般动作“ 1 ”自保持Alpha 580 指拨开关功能板(按键排列请参考第4-5页)指拨位置 注一:不可设定,需强制设定为“ 0 ” ※以上出厂设定值均为“ 0 ”DIP2- 2&39Alpha580C-1&RES 1RES 2Alpha580A/B/C/D/E 功能扩充DIP2-7DIP2-810 1&2(2速) 1&2(2速)7&87 Alpha 580E 98Alpha 580C-2Alpha 580D DIP2-2DIP2-3DIP2-4DIP2- 5&6DIP2-4DIP2-2,3,4DIP2-1DIP2-17&89&10107&81&2(2速)Alpha 580B 987Alpha 580A9DIP2-2DIP2-4DIP2-1DIP2-3DIP2-3DIP2-4DIP2-5DIP2-6DIP2-15&67&8按 键机 型1&2DIP2-1DIP2-23&4 出厂设定值为“0”(注一)DIP2-2拨至“ 1 ”才有效用DIP2-2拨至“ 1 ”才有效用于Alpha580A/B/C/D/E 之标准下并无此功能,需特别另外订做。
AT500 600安装调试操作手册

AT500/600磁致伸缩液位/界位变送器安装调试操作手册目录一、存放 (3)二、安装和启动 (3)2.1 接线 (3)2.2 确定4Ma和20Ma设定点 (4)2.3 倒置安装 (4)2.4 高/低报警点设定 (4)2.5 4MA/20MA交直流微调 (5)三、故障处理信息 (7)3.1 正确上电 (7)3.2 输出稳定性 (7)一.存放如果需要,应该存放在优于安装条件的环境温度下并置于室内,不能超出以下范围:温度范围:-40-65℃湿度范围:0--100% R.H. 无冷凝二.安装和启动注意:在安装AT500/600浓缩(简易)型磁致伸缩变送器时,探管是与一套特氟隆套圈一体运送的,另有一套不锈钢套圈单独装在一个袋子里。
特氟隆套圈只应用于低压场合,最于高压场合只能用不锈钢套圈。
2.1接线连接导线到1/2"电器接口,然后用18线规的双绞线连接变送器外壳,用适当的导线密封装置以排除可能渗透的潮气。
变送器按以下方式回路供电:# Terminal Block+:24 VDC(+14VDC最小到+36VDC最大)# Terminal Block-:共同端/电流表# Terminal Block :电流表# Terminal Block:接地(确认接地正确,以排除可能存在的干扰)2.2确定4MA和20MA设定点本产品是无须日常标定的电子变送器。
如果需要重新标定,可以使用右图标出的开关点按照以下步骤标定:设定4MA/0%点-使罐内物位为0%-把磁棒放置于X处两秒钟进入标定模式-把磁棒从X处移动到Z处设置0点(4MA),这一步是通过检查输出是4.00MA来确定的。
设定20MA/100%点-使罐内物位为100%-把磁棒放置于X处两秒钟进入标定模式-把磁棒从X处移动到S处设置满量程点(20MA),这一步是通过检查输出是20.00MA来确定的。
注:以上步骤可以根据需要任意重复。
2.3倒置安装如果需要,变送器输出可以通过以下步骤倒转(注:使4-20Ma输出倒转)使物位在50%处(+or-10%)-把磁棒放置于X处两秒钟进入标定模式-把磁棒从X处移动到Z处设置0点(4MA)这一步是通过检查输出是4.00MA来确定的。
DAHL 500系列燃料过滤器说明书
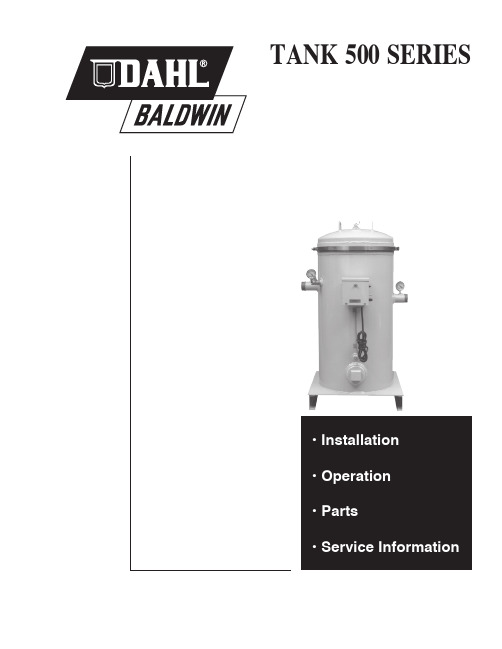
• Installation • Operation • Parts• Service InformationTANK 500 SERIESA non-restrictive check valve should be installed on the DAHL INLET to prevent loss of prime. See Figure 2B.1. Select a location in the fuel line between the fuel tank and the fuel pump.2. Install the DAHL unit on the vacuum (suction) side of all fuel pumps in a convenient location for servicing3. Install the fuel line with a check valve from the fuel tank to the DAHL unit INLET using appropriate non-galvanized fittings.4. Install the fuel line from the DAHL unit OUTLET to the INLET of the transfer or fuel pump.iLter ounted Bove ueL torAge Ank FIGURE 2BThe warning light in the instrument panel box on the 500-BP operates on standard 110 volt electricity. The warning light in the instrumentd. e LectricAL r equirementS for 500-BP _______________________________panel box on the 500-BP22 operates on 220 volt electricity. An optional warning buzzer on 500-BP (EC-005 OBS) is available.The DAHL 500 Series unit can also be used for fuel recycling to maintain high fuel purity for stored fuels and for blending of diesel fuel with used crankcase oil from diesel equipment. If thesee. r ecycLing & B Lending ___________________________________________functions are desired, they may be incorporated into the system through the addition of valves. See Figure 4 and the OPERATION section for recycling and blending instructions.Arine ontinuouS PerAtion ___________________________________3OPERATIONAs water is separated from the fuel, it accumulates in the sump. DAHL 500-BP is equipped with an electronic water sensor system.When water reaches the level of the sensing probe, the warning light (and optional buzzer) will activate. This indicates that approximately 11 gallons of water has collected. These electronic alarms turn themselves off when the sump is drained.SERVICENOTE: The probe should be cleaned monthly to remove coatingswhich can interfere with sensing dependability. See PROBE CLEANING.Check the water and contaminant level in the sump daily — particularly if no water sensor probes are installed.Periodically recycle the fuel through the DAHL 500 Series unit to purge water and contaminants from the storage tank.1. If your unit is equipped with a water sensor probe, plug it in.2. Close valves marked 1, 3, 4 and 7 in Figure 4.3. Open valves marked 2, 5 and 6.4. Start the fuel flow through the DAHL 500 Series unit. Start the pump motor and adjust the pump by-pass valve (number 3 on Figure 4) to the desired flow. Opening the valve decreases the flow.5. Check the water level occasionally. See the SERVICE section for instructions on draining water.6. Recycling time may be determined by fuel quantity. The maximum flow through a DAHL 500 Series unit is 1800 gph or 30 gpm with valve number 4 closed. Estimate the recycling time in minutes by dividing gallons of fuel by 30.r ecycLing _______________________________________________________FIGURE 4Most diesel engine manufacturers have tested and approved the blending of diesel fuel with used crankcase oil on a 20:1 ratio. (Do not exceed 5% oil in blend.)Once blended, the mixture is filtered and contaminants are removed. The blended fuel is then recycled back to the fuel storage tank for use. The used crankcase oil has now become valuable diesel fuel.Caution: NEVER use crankcase oil from gasoline engines forblending. Use diesel equipment waste oil only.Caution: The maximum ratio for blending used oil is one part oilto twenty parts of diesel fuel. NEVER EXCEED THIS RATIO.u Se of B Lended f ueL ______________________________________________To calculate:1. If the quantity of used oil is known, multiply by 20 to find the minimum quantity of diesel fuel to be used.2. If the quantity of diesel fuel is known, divide by 20 to find the maximum quantity of crankcase oil to add.DOUBLE-CHECK ALL CALCULATIONSFOR ACCURACY.NOTE: Cold oil is viscous, difficult to blend and shortens filterelement life. Consider warming it. If the vacuum gauge reading exceeds 20 inches, do not operate the DAHL unit. See the TROUBLESHOOTING section.To operate the DAHL 500 Series unit as a blender:1. If your unit is equipped with a water sensor probe, plug it in.2. Close valves marked 1, 3, 4 and 7 in Figure 4.3. Open valves marked 2, 5 and 6.4. Start the fuel flow through the DAHL 500 Series unit. Start the pump motor and adjust the pump by-pass valve (number 3 on Figure 4) to the desired flow. Opening the valve decreases the flow.B Lending ________________________________________________________5. Open the oil valve (number 7 on Figure 4) to begin mixing.6. Blending is complete when the calculated quantities are blended (approximately 7-8 minutes per gallon of oil.) A more efficient mixture, which will prolong filter element life, is obtained by injecting the oil slower and allowing a longer recycling period of time.1. Shut the pump off or set the valves to by-pass the DAHL unit.2. If no pressure is indicated on the inlet vacuum gauge, open the top air vent valve.3. Open the sump drain valve and drain all of the water.d rAining w Ater ___________________________________________________4. Close the sump drain valve.5. Prime the DAHL unit as instructed in the PRIMING METHODS section.1. Plug the water sensor probe models into an appropriate power source.2. Start the fuel flow through the DAHL unit by starting the pump or closing the DAHL unit by-pass valve. (See Figure 1.)S tArt -uP ________________________________________________________3. Check the system for leaks. If any problems develop, see the TROUBLESHOOTING section.4SERVICE (Cont’d.)Clean the probe with a dry cloth monthly to get dependable service.1. Unplug the DAHL unit and stop the fuel flow through the unit.2. Remove the probe nut and wire.3. Drain the tank, if needed.4. Remove the probe. (If the tank is not drained, plug the 1/4 inch NPT hole immediately.)5. Clean the probe tip with a clean dry cloth and replace.P roBe c LeAning ___________________________________________________6. Prime the DAHL unit as instructed in the PRIMING METHODS section.7. Replace the wire. Plug in the DAHL unit and turn the fuel flow on.8. Test the light bulb. See the PROBE AND LIGHT FUNCTION section.A. Head Pressure — If the storage tank is higher than the DAHL unit, head pressure (not to exceed 15 psi) can be used to prime the filter.1. Open the top air vent valve.2. Make sure the side and bottom drain valves are closed.3. Open the fuel supply shut-off valve.4. When diesel fuel comes out at the air vent valve, close the valve. The unit is now primed and ready.B. Manual and Pump Filling - If no head pressure is available, filling with a funnel or a pump is recommended.1. Open the top air vent valve.P riming m ethodS __________________________________________________2. Make sure the side and bottom drain valves are closed.3. a) Funnel Filling: Remove the primer plug and fill.b) Pump Filling: Attach a pump line to the 1/2 inch side drain valve. Pump slowly. Do not exceed 15 psi.4. Fill the unit with approximately 55 gallons or until the fuel comes out the air vent valve.5. a) If Filled by Funnel: Replace the primer plug. Use a thread sealer.b) If Filled by Pump: Close the 1/2 inch side drain valve.6. Close the top air vent.TROUBLESHOOTING1. DAHL unit not full of fuel — Prime the DAHL unit as instructed in the PRIMING METHODS section.2. Vent or drain valve is open.3. By-pass system is still open.4. Fuel supply shut-off valve is still closed.d AhL u nit w iLL n ot P rime __________________________________________5. Fittings are loose. Check and tighten.6. O-ring is defective. Apply grease to o-ring before installing.7. Pump operation is in wrong rotation. Change rotation if necessary.1. Refer to DAHL UNIT WILL NOT PRIME section.2. Inlet or outlet valve is closed.3. Filter elements are plugged. Check vacuum gauge reading and replace elements if needed.i nSufficient f ueL f Low _____________________________________________4. Viscosity is too high. Warm the fuel.5. Plumbing is undersized or restricted.DAHL f ilter e lements s hould b e c hanged w hen t he O UTLET vacuum gauge reads 20 inches of mercury while operating, or at the pump manufacturer’s specification, whichever is lower.The INLET gauge will indicate pressure during operation and should not exceed 15 psi on a typical installation with the fuel tank above the DAHL unit. See Figure 2.1. Shut the pump off or set the valves to by-pass the DAHL unit.2. Open the side drain valve. Drain off approximately 14 gallons of diesel fuel so that the fuel level is at the bottom of the filter elements. (Open the top air vent to assist in draining.)3. Remove the lid clamp and the lid. Tap with a rubber mallet if necessary.f iLter e Lement r ePLAcement ________________________________________4. Unscrew the filter element retainers and remove contaminated elements with a turning motion.5. Replace the filter element and retainers. Make priming easier by partially filling the housing with clean fuel at this time.6. Coat the O-ring with a heavy lubricant and re-install.7. Install the lid and the clamp. Be sure arrows on the lid and the housing are aligned for best fit.NOTE: Make sure both flanges are inside the clamp lids. Tapthe clamp with a rubber mallet while tightening fasteners until the clamp begins to tighten equally around the housing. Do not over-tighten.8. Prime the DAHL unit as instructed in the PRIMING METHODS section.Sump cleaning is required when too many large contaminants have accumulated for the sump drain valve to handle.1. Shut the pump off or set the valves to by-pass the DAHL unit.2. Open the top air vent valve.3. Drain the unit completely (approximately 55 gallons). A sump assist is a time-saver — attach it to the 3/4 inch sump drain valve.c LeAning the S umP ________________________________________________4. Remove the sump clean-out plug and flush the sump out with a small pump.5. Clean the probe as discussed in the PROBE CLEANING section.6. Replace clean-out plug using a thread sealer.7. Prime the DAHL unit as instructed in the PRIMING METHODS section.MODEL 500 SPECIFICATIONSRecommended Flow Rate:Single Model 500 Series ..............1,800 GPH (U.S.) (6,813 LPH) Double Model 500 Series ..........3,600 GPH (U.S.) (13,626 LPH) Multiple Unit: ....................................................Multiply Flow Rate and Sump Capacity by Number of Units Maximum Flow Rate:Single Model 500 Series ..............1,920 GPH (U.S.) (7,268 LPH) Double Model 500 Series ..........3,840 GPH (U.S.) (14,536 LPH)Flow Resistance: ........................................................1.0 In. Mercury Maximum Working Pressure:.................................15 PSI (103 kPa)Temperature Range: .......................-60° to +250°F (-50° to +121°C)Port Thread: .........................................................................2 In. NPT Overall Height:........................................................47 In. (1,194 mm)Width: ..................................................................28 1/2 In. (724 mm)Depth: .........................................................................22 In. (559 mm)Platform Base: ..................................24 x22 In. (609.6 x 558.8 mm)Tank Diameter: ..........................................................20 In. (508 mm)Shipping Weight: .......................................287-289 lbs. (130-131 kg)Element Removal Clearance: ...................................10 In. (254 mm)Sump Capacity: ....................................11 U.S. Gallons (41.6 Liters)Vacuum: .................................................................28 1/2 In. Mercury Seal Material: ..........................................................................Buna N Element Number:501 .........................................................................2 Micron Element 501-W* .................................................................10 Micron Element 501-30 ..................................................................30 Micron Element* Standard with Unit Unless Stated.500 SERIES SINGLE UNITS500 Diesel Fuel Filter/Water Separator500-BPDiesel Fuel Filter/Water Separator with Water Sensor Warning Light Kit — Equipped with a 110 Volt Electrical Connector.500-BP22 Diesel Fuel Filter/Water Separator with Water SensorWarning Light Kit — Equipped with a 220 Volt Electrical Connector. (For Overseas Operation)500 SERIES DOUBLE MANIFOLD UNIT500-MFVBP 22 Double Manifold Diesel Fuel Filter/Water Separatorwith Shut-Off Valves — Allows for continuous operation and Water Sensor Warning Light Kit — Equipped with a 220 Volt Electrical Connector. (For Overseas Operation)TROUBLESHOOTING (Cont’d.)The sensing probe should be cleaned monthly for dependable service. Refer to the PROBE CLEANING section.1. Check the power supply.2. Check the light bulb activation.a) If the probe is already removed, attach the probe wire and touch the probe tip to an unpainted surface on the DAHL unit.b) If the probe is installed, take a piece of wire and touch the wire to the probe nut and to an unpainted surface on the DAHL unit.P roBe And L ight f unction __________________________________________3. If warning light does not activate:a) Turn off the electrical power.b) Check for a burned out bulb. Replace with an EC-112 OBS light bulb if needed.c) Check, tighten or replace loose or broken wires.d) Check the optional warning buzzer. Replace if defective.e) Check to assure the transformer is functioning properly.1 1 1 In. Primer Plug2 100-30 1 Air Bleed Valve3 2 Attached Handle4 7 Element Retainer5 500-15 1 20 In. O.D. O-Ring6 500-12 1 20 In. Seal Clamp7 501,-W*,-30 7 Filter Element (7 Req.)8 85-P, 85-V 2 Vacuum/Pressure Gauge (2 Req.)9 1 20 In. Body 10 1 Depressurizer Cone 11 1 Water Sensor Probe 12 1 3/4 In. Drain Valve 13 1 4 In. Clean-Out Plug 14 1 Conical Baffle 15 1 1/2 In. Drain Valve 16 1 Water Sensor Probe 1 Replacement Light Bulb 17 1 20 In. LidIf no number appears in the Order Number column, the item is notavailable separately.5Form 4500 (R 9/13) © 2017 Baldwin Filters, a Parker Hannifin company Printed in U.S.A.WARNING: These products can expose you to chemicals, including Diisononyl Phthalate, Carbon black extracts, Nickel, 1,3 Butadiene, Ethylene Oxide, Epichlorohydrin, which are known to the State of California to cause cancer, and Bisphenol-A, Ethylene Glycol, Ethylene Oxide, 1,3 Butadiene, Epichlorohydrin, which are known to the State of California to cause birth defects or other reproductive harm. For more information go to .。
RUGGED GEEK INTELLIBOOST 600A 紧急启动器使用说明说明书
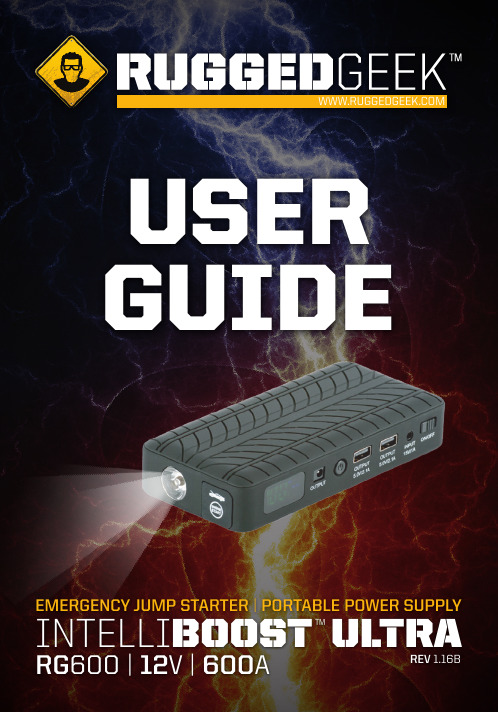
INTELLI BOOST ™ ULTRA EMERGENCY JUMP STARTER | PORTABLE POWER SUPPLYUSER GUIDEREV 1.16BWELCOMEWelcome to your new RUGGED GEEK™INTELLIBOOST™ULTRA RG600 Emergency Jump Starter and Personal Power Supply.Your next generation Lithium Ion Jump Starter features class-leading construction, exclusive INTELLIBOOST™ cables and a unique design perfected in North America for the ultimate in safety and convenience.We are excited by the versatility, features and safety offered by the RG600 and encourage you to read through the owner’s manual to ensure trouble free and safe operation.IMPORTANT:For updates to this manual, additional support, product-use videos and more please visit us at .PACKAGE CONTENTS(1) LAPTOP CHARGING CABLE(8) LAPTOP CHARGING TIPS(1) 4-IN-1 USB CABLE(1) CAR CHARGER (1) WALL CHARGER(1) INTELLIGENT JUMP STARTER | PORTABLE POWER SUPPLY & INTELLIBOOST JUMPER CABLESPRODUCT FEATURES(1) LED FLASHLIGHT(2) JUMP STARTER OUTPUT(3) LCD SCREEN(4) LAPTOP OUTPUT(5) CIRCLE BUTTON(6) 5.0V/2.1A USB OUTPUTS(7) 15V/1A INPUT(8) POWER SWITCH(5)(8)(7)(6)(4)(3)(2)(1)PROBLEM CAUSE SOLUTIONThe INTELLIBOOST cables won’t stop beeping and I can’t get it to boost my vehicle.The INTELLIBOOST cables havedetected an error.Reset the INTELLIBOOST cablesby unplugging them from theRG600 and disconnect thecables from the battery youwere attempting to boost. Plugthe cables back into the RG600prior to connecting them to thevehicle in need of boost.The light on the INTELLIBOOST cable won’t turn green, but they are connected properly.The cables do not detect asufficient draw.For the majority of vehicles,simply turning the vehicle to“ACC” or Accessory mode willinitiate enough of a draw to turnthe light green and allow you toboost. For certain lower drawvehicles without any accessorydraw, often just attempting tostart the vehicle will initiatethe draw needed. If that stilldoes not work, it is possible thedraw sensed from the vehicleis not compatible with theINTELLIBOOST feature. On thesevehicles, often turning on a lightor other type of draw, may work.I connected the INTELLIBOOST cables to the wrong terminals on the battery of the vehicle I am boosting and now the light is red and it’s beeping, did I wreck it?Reverse polarity connection ofthe booster cablesDon’t worry... you are safe.The INTELLIBOOST cables aredesigned to not spark or causeany damage if the cables areaccidentally hooked up inreverse. Simply connect thecables properly using the stepsoutlined in this manual.I have my USB device plugged in, but it won’t charge?No power is being output fromthe RG600.Ensure the proper cable is beingutilized. Ensure the switch isin the “on” position and the“power” circle button has beenpressed to initiate charge.TROUBLESHOOTINGSPECIFICATIONSBATTERY TYPE:LITHIUM IONBATTERY CAPACITY:11.1v / 35.52 whBATTERY CYCLE LIFE:1000+LED LIFE:100,000 HOURSPEAK CURRENT RATING:600AOPERATING TEMPERATURE:-22°F(-30°C)TO+122°F(+50°C) INPUT (CHARGING) VOLTAGE:15V,1AOUTPUT VOLTAGE (JUMP STARTER):12VOUTPUT VOLTAGE (USB):2@5V,2.1AOUTPUT VOLTAGE (LAPTOP):12V/16V/19V, 2A/3.5A/3.5A SIZE (L x W x H):6.3”(16cm)x2.9”(7.4cm)x1.3”(3.3cm) WEIGHT (WITHOUT CABLES):15.3 oz(435 gm)1) Connect the power cord to designated power socket.2) Remove the dust cap from tire valve and keep in a secure location while not in use.3) Carefully remove the air hose from the side of the compressor and screw the valve connector in place. Make sure the valve is correctly connected, and not over tightened.4) Press the ‘ON’ switch and the compressor will automatically start to inflate the tire.5) Periodically pause the compressor to allow a steady tire pressure reading to be taken.6) Once the correct tire pressure has been reached, switch the unit off, disconnect it from the tire valve, and place the dust cap back on the tire valve.OPERATING INSTRUCTIONSUSING THE ADAPTORSStep 1: Choose the compatible adaptor and screw it into the valve connector.Step 2: Press the ‘ON’ switch and the compressor will automatically start to inflate the item.Step 3: Periodically pause the compressor to allow a steady pressure reading to be taken.INCLUDES THE FOLLOWING ADAPTERS(1) NEEDLE ADAPTOR FOR SPORTS BALLS(2) PRESTA ADAPTOR FOR BICYCLE TIRES(3) NOZZLE ADAPTOR FOR INFLATABLES(1)(2)(3)TECHNICAL SPECIFICATIONS POWER INPUT: DC 12VMAXIMUM PRESSURE: 150 PSIMAXIMUM CURRENT: 4AUNLOADED CURRENT: <2.5AMAXIMUM VOLUME: .53CFM / 15L PER MININFLATION SPEED: LESS THAN 10 MINUTES TO INFLATE TIREFROM 0 TO 30 PSIWORKING TEMPERATURE: -22°F (-30°C°) TO +122°F(+50°C) PRESSURE GAUGE DISPLAY: ANALOG: READING IN PSI & BAR LIGHT: 1 LEDSIZE (L x W x H): 4.3” (10.9cm) X 2.0” (5.1cm) X 3.7” (9.4cm) ACCESSORIES: THREE ADAPTORSMODEL NO: RG150WARRANTY & SUPPORTRugged Geek (“RG”) warrants that its RG600 (“The Product”) will be free from defects in material and workmanship for a period of twelve (12) months from the date of purchase (the “”Warranty Period””). For defects reported during the Warranty Period, RG will, at its discretion, and subject to RG’s technical support analysis, either repair or replace any Product sold by RG that contains such a defect. Replacement parts and products will be new or serviceably used, comparable in function and performance to the original part and warranted for the remainder of the original Warranty Period.THE FOREGOING LIMITED WARRANTY IS IN LIEU OF AND EXCLUDES ALL OTHER WARRANTIES NOT EXPRESSLY SET FORTH HEREIN, WHETHER EXPRESS OR IMPLIED BY OPERATION OF LAW OR OTHERWISE, INCLUDING, BUT NOT LIMITED TO, ANY IMPLIED WARRANTIES OF MERCHANTABILITY OR FITNESS FOR A PARTICULAR PURPOSE.RG’S LIABILITY UNDER THIS LIMITED WARRANTY IS EXPRESSLY LIMITED TO REPLACEMENT (IN THE FORM AND UNDER THE TERMS ORIGINALLY SHIPPED), OR TO REPAIR, WHETHER SUCH CLAIMS ARE FOR BREACH OF WARRANTY OR FOR NEGLIGENCE. RG SHALL NOT BE LIABLE FOR ANY INCIDENTAL, CONSEQ UENTIAL, OR SPECIAL LOSSES, DAMAGES OR EXPENSES OF ANY KIND, INCLUDING, WITHOUT LIMITATION, ANY SUCH LOSSES, DAMAGES, OR EXPENSES ARISING DIRECTLY OR INDIRECTLY FROM THE SALE, HANDLING, OR USE OF THE PRODUCT FROM ANY OTHER CAUSE RELATING THERETO, OR FROM PERSONAL INJURY OR LOSS OF PROFIT.Some states do not allow the exclusion or limitation of incidental or consequential damages or length of an implied warranty so the above limitation(s) or exclusion(s) may not apply. This Limited Warranty gives you specific legal rights and you may also have other legal rights which vary from state to state.This Limited Warranty is made to the original purchaser from RG and does not extend to any other person or entity and is not assignable. It is the obligation of the original purchaser to forward the Product, with the proof of purchase, to RG.THE COSTS OF TRANSPORTING PRODUCTS TO RG FOR WARRANTY SERVICE IS THE RESPONSIBILITY OF THE ORIGINAL PURCHASER. THIS LIMITED WARRANTY IS VOID UNDER THE FOLLOWING CONDITIONS:1. The Product is misused, subjected to careless handling, or operated under conditions of extreme temperature, shock, or vibration beyond RG’s recommendations for safe and effective use.2. The Product has not been installed, operated, charged, or maintained in accordance with approved procedures.3. The Product is disassembled, altered, or repaired by anyone, except RG.4. The electrical connections to either the AC input or any of the DC outputs of the jump starter are modified.5. The Product is subject to improper storage or accidental damage.6. The original purchaser fails to provide the original bill of sale.THIS LIMITED WARRANTY DOES NOT COVER:1. Normal wear and tear.2. Cosmetic damage that does not affect functionality.3. Products where the purchase date is undeterminable.FOR ADDITIONAL WARRANTY INFORMATION AND TO REGISTER YOUR PRODUCT, PLEASE VISIT OUR WEBSITE AT AND CLICK ON “SUPPORT”. YOU MAY ALSO EMAIL US DIRECTLY AT **************************.TO CHECK OUT OUR OTHER COOL PRODUCTS, OR FOR ADDITIONAL PRODUCT USAGE INFORMATION AND VIDEOS, PLEASE VISIT:。
Catphan500-600manual
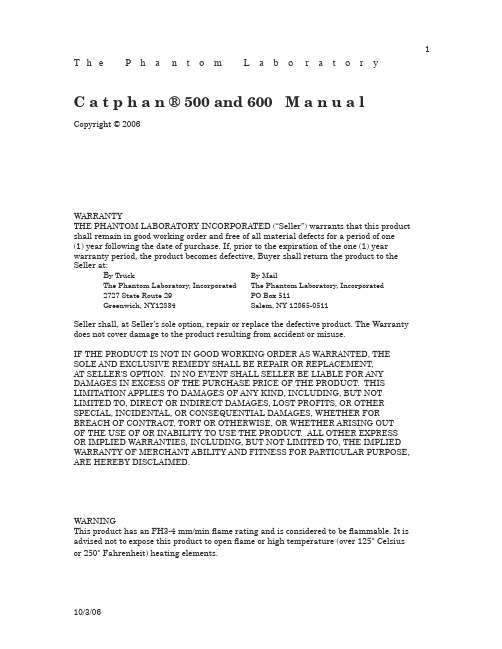
1 T h e P h a n t o m L a b o r a t o r yC a t p h a n ® 500 and 600 M a n u a lCopyright © 2006WARRANTYTHE PHANTOM LABORATORY INCORPORATED (“Seller”) warrants that this product shall remain in good working order and free of all material defects for a period of one(1) year following the date of purchase. If, prior to the expiration of the one (1) year warranty period, the product becomes defective, Buyer shall return the product to theSeller at:B y Truck By MailThe Phantom Laboratory, Incorporated The Phantom Laboratory, Incorporated2727 State Route 29 PO Box 511Greenwich, NY12834 Salem, NY 12865-0511Seller shall, at Seller’s sole option, repair or replace the defective product. The Warranty does not cover damage to the product resulting from accident or misuse.IF THE PRODUCT IS NOT IN GOOD WORKING ORDER AS WARRANTED, THESOLE AND EXCLUSIVE REMEDY SHALL BE REPAIR OR REPLACEMENT,AT SELLER’S OPTION. IN NO EVENT SHALL SELLER BE LIABLE FOR ANY DAMAGES IN EXCESS OF THE PURCHASE PRICE OF THE PRODUCT. THIS LIMITATION APPLIES TO DAMAGES OF ANY KIND, INCLUDING, BUT NOTLIMITED TO, DIRECT OR INDIRECT DAMAGES, LOST PROFITS, OR OTHER SPECIAL, INCIDENTAL, OR CONSEQUENTIAL DAMAGES, WHETHER FORBREACH OF CONTRACT, TORT OR OTHERWISE, OR WHETHER ARISING OUTOF THE USE OF OR INABILITY TO USE THE PRODUCT. ALL OTHER EXPRESSOR IMPLIED WARRANTIES, INCLUDING, BUT NOT LIMITED TO, THE IMPLIED WARRANTY OF MERCHANT ABILITY AND FITNESS FOR PARTICULAR PURPOSE, ARE HEREBY DISCLAIMED.WARNINGThis product has an FH3-4 mm/min flame rating and is considered to be flammable. It is advised not to expose this product to open flame or high temperature (over 125° Celsiusor 250° Fahrenheit) heating elements.10/3/0623 T h e P h a n t o m L a b o r a t o r yCatphan® ManualContentsWarranty 1Introduction 5Multi-Slice CT by David Goodenough, Ph.D. 6Initial phantom positioning 8Illustration of Catphan® models 9Incremental phantom modules positioning 10Phantom position verification 11CTP401 and CTP404 modules 12Patient alignment system check 13Scan slice geometry (slice width) 14Scan incrementation 15Circular symmetry 16Spatial linearity of pixel size verification 16Spherical acrylic contrast targets 16Sensitometry (CT number linearity) 17CTP591 Bead Geometry Module 18CTP528 High resolution module with 21 line pair per cm gauge and point source 19 Bead point source for point spread function and MTF 19Use of automated scanner MTF programs 20Bead point source (slice sensitivity profile) 2121 Line pair per centimeter high resolution gauge 22CTP515 Low contrast module with supra-slice and subslice contrast targets 23CTP486 Image uniformity module 25Installation and removal of test modules 27Optional phantom annuli 28Optional phantom housings 29Dose Phantoms 30Sample quality assurance program 31Automated computer analysis program 31Bibliography 3245 IntroductionThe Phantom Laboratory and physicist, David J. Goodenough, Ph.D., are continually developing and researching new tests and modifications for the Catphan® phantoms.The test objects that make up the current Catphan® models embody more than aquarter century of scientific evaluation and field experience. This manual outlines the applications of each module contained in the Catphan® 500 and 600 phantoms.We do not make specific recommendations on the content of your quality assurance program, because each medical imaging facility has its own unique set of requirements.A sample program is provided to give you ideas for possible program content. We suggesta review of local governing regulations, manufacturers’ specifications and the needs ofyour radiologists and physicists before developing your CT quality assurance program.The Catphan® instructional video, which illustrates the phantom setup and scanning ofthe different Catphan® sections, is also available.If you have any additional questions please contact The Phantom Laboratory at:Phone: 800-525-1190 or 518-692-1190Fax: 518-692-3329email: sales@Additional product information is available at: 6Multi-Slice CTby David J. Goodenough, Ph.D.At the request of The Phantom Laboratory I have put together this summary forphysicists who are familiar with CT image performance measurements and have not had experience with multi-slice CT scanners.Multi-slice uses the same basic approach to image reconstruction as axial single slice CT. Both modalities use the data from the detectors (positioned 360° around the patient) to reconstruct the axial patient images. The key difference between axial single slice CT and multi-slice is the axial image produced by single slice CT is developed from a single row of detectors, and the axial image made from a multi-slice scanner uses segments from several rows of detectors. With a multi-slice scan, as the patient moves through the gantry and the tube rotates around the patient, the detector rows utilized change as the patient and gantry move (see sketch on the next page).Additional variables in reconstruction result as the patient slice moves from one row of detectors to the next and the scanner reconstructs the images based on weightedaverages between the relevant rows. In this way, multi-slice CT is analogous to spiral or helical single slice CT, but where the reconstruction is obtained from the combined slices rather than the interpolation between the readings of a single moving slice. Now add in focal spot variables and a little scatter to define in more detail the challenges and variables included in the reconstruction of a multi-slice image.Because in spiral mode each multi-slice image is reconstructed from an ensemble of data taken in different positions across the beam and from different detector rows, the overall image quality differences between images are minimal. In the spiral mode each slice represents data as seen from all detector rows in a sense a kind of averaging of detector row positions. However, if you use a multi-slice “step and shoot” mode, where each of the slices may be created from a single detector row (or rows depending on the selected slice thickness) with a consistent collimation, the differences between the slices will be evident. Step and shoot mode in a multi-slice CT scanner is operated like a conventional axial scanner by imaging with a fixed table position and then moving the table to the next position before imaging the next section of the phantom with a fixed table position.For example, with a step and shoot 8 slice scan it is expected that the middle slicenumbers 4 and 5 will have better uniformity than outer slice numbers 1 and 8 because of the scanner x-ray beam geometry. However, if 1 and 8 or 4 and 5 are not similar, this may indicate a problem with the scanner.When assessing a scanner with a step and shoot mode, it is important to cover the full detector width with the selected test objects. If the test object is narrower than the slice, the table will need to be incremented between scanning sequences so the object can be scanned by all active rows of the detector.I recommend scanning through the entire phantom using different multi-slice spiralprotocols for performance evaluations, as well as using the step and shoot approach for the bead ramps where slice geometry and the MTF can be measured for each slice and uniformity section where the signal to noise and uniformity of each slice (detector row) can be evaluated.7This simplified illustration of a multi-slice sequence shows how the slices are reconstructed with information for different detector rows. The imaging sequence of thefirst selected slice (slice 1) of the patient begins when slice 1 moves over detector row A.As the tube continues to rotate and the patient continues to move through the gantry,slice 1 is picked up by the detectors in row B. At the same time slice 2, which was outside the detector view, is picked up by the detectors in row A. This sequence continues untilthe last selected region of the patient has passed through all the active detector rows.8Initial phantom positioningThe Catphan® phantom is positioned in the CT scanner by mounting it on the case.Place the phantom case on the gantry end of the table with the box hinges away from the gantry. It is best to place the box directly on the table and not on the table pads.Open the box, rotating the lid back 180°. If you are using an annulus, additional weight will need to be placed in the box to counterweigh the phantom. The patient straps can be used for additional stability.Remove the phantom from the box and hang the Catphan® from the gantry end of the box. Make sure the box is stable with the weight of the phantom and is adequatelycounterweighed to prevent tipping.Use the level and adjusting thumb screws to level the Catphan®. Once the phantom is level, slide the phantom along the end of the box to align the section center dots on the top of the phantom with the x axis alignment light.Use the table height and indexing drives to center the first section’s (CTP401 or CTP404, Slice Geometry) alignment dots on the side and top of the phantom with the scanner alignment lights.The z axis scan alignment position can be selected from the localizer scan, by centering the slice at the intersection of the crossed wire image created by the slice width ramps.Scan the first section (CTP401 or CTP404) and check the image for proper alignment as illustrated in the Phantom position verification section.9 Illustration of Catphan® 500 and 600 modelsCatphan® 500Catphan® 60010Incremental phantom module positioningThe Catphan® phantoms are designed so all test sections can be located by precisely indexing the table from the center of section 1 (CTP401 or CTP404) to the center of each subsequent test module. This design eliminates the need to remount the phantom once the position of section 1 (CTP401 or CTP404) has been verified. The indexing distances from section 1 are listed below. Additional illustrations on the preceeding page show the test modules and their index spacing. Phantom position and alignment verification is described on the next page.Catphan® 500 test module locations:Module Distance from section 1 centerCTP401CTP528, 21 line pair high resolution 30mmCTP528. Point source 40mmCTP515, Subslice and supra-slice low contrast 70mmCTP486, Solid image uniformity module 110mm Catphan® 600 test module locations:Module Distance from section 1 centerCTP404CTP591 Bead geometry 32.5mmCTP528, 21 line pair high resolution 70mmCTP528. Point source 80mmCTP515, Subslice and supra-slice low contrast 110mmCTP486, Solid image uniformity module 150mmPhantom position verificationBy evaluating the scan image of section 1 (CTP401 or CTP404) the phantom’s position and alignment can be verified. The section contains 4 wire ramps which rise at 23° angles from the base to the top of the module. The schematic sketches below indicate how the ramp images change if the scan center is above or below the z axis center of the test module. The use of the scanner’s grid image function may assist in evaluation ofphantom position.In this image the x, y symmetry of the centered ramp images indicates proper phantom alignment.When the ramps are evenly rotated clockwise from center, the phantom is too far into the gantry.When the ramps are evenly rotated counter-clockwise from center, the phantom needs to be moved toward the gantry. Poor alignment with the z axis is indicated when the ramps are not symmetrical in lenghts and rotation. If misalignment is indicated by the scan image, the phantom should be repositioned to obtain proper alignment and then rescanned. If the images of the repositioned phantom duplicate the original misalignment indications, the scanner’s alignment lights may require adjustment (contact your local service engineer).Once correct alignment has been established, you can proceed with the tests.CTP401 Module with slice width, sensitometry and pixel sizeCTP404 Module with slice width, sensitometry and pixel sizePatient alignment system checkThe laser, optical, and mechanical patient alignment system can be checked for accuracy. Align the white dots on the phantom housing with the alignment lights as discussedin Initial phantom positioning. The scanned image should show good alignment as discussed in Phantom position verification.For measuring the z axis alignment accuracy, measure from the center of the ramp image to the part of the ramp which aligns with the center of the phantom and sensitometry samples. Multiply the distance A by 0.42 to determine the z axis alignment light accuracy. To evaluate x and y accuracy, measure from the center of the phantom to the center of the scan field by use of the grid function or knowledge of the central pixel location.The accuracy of the localizer, pilot or scout view can be checked. To check this function perform a localization scan of the phantom. Align an axial scan at the crossing point of the wire ramps. Scan this axial cut and check the misalignment as discussed above.Scan slice geometry (slice width)Section 1 has two pairs of 23° wire ramps: one pair is oriented parallel to the x axis; the other pair to the y axis. These wire ramps are used to estimate slice width measurements and misalignment errors as previously discussed.Measuring slice width with the 23° wire ramps. The ramp angle is chosen tooffer trigonometric enlargement of 2.38 in the x-y image plane.To evaluate the slice width (Zmm), measure the Full Width at Half Maximum (FWHM) length of any of the four wire ramps and multiply the length by 0.42:(Zmm) = FWHM * 0.42To find the FWHM of the wire from the scan image, you need to determine the CT number values for the peak of the wire and for the background.To calculate the CT number value for the maximum of the wire, close down the CT “window” opening to 1 or the minimum setting. Move the CT scanner “level” to the point where the ramp image just totally disappears. The CT number of the level at this position is your peak or maximum value.To calculate the value for the background, use the region of interest function to identify the “mean” CT number value of the area adjacent to the ramp.Using the above CTvalues, determine the half maximum:First calculate the net peak... (CT # peak - background = net peak CT #) Calculate the 50% net peak... (net peak CT # ÷ 2 = 50% net peak CT #) Calculate the half maximum CT number...(50% net peak CT # + background CT # = half maximum CT #)Now that you have determined the half maximum CTnumber, you can measure the full width at half maximum of the ramp. Set the CT scanner level at the half maximumCT value and set your window width at 1. Measure the length of the wire image to determine the FWHM. Multiply the FWHM by 0.42 to determine the slice width.Schematic illustration of two sequential 5mm scans superimposed. L1 isthe center point on the 23° ramp in the first scan image and L2 is thecenter point on the 23° ramp on the second image.Scan incrementationUse the wire ramps to test for proper scanner incrementation between slices, and for table movement.Scan section 1 using a given slice width, (e.g. 5mm). Increment the table one slice width (e.g. 5mm) and make a second scan. Establish the x and y coordinates for the center of each ramp image. Calculate the distance between these points and multiply by the 23° ramp angle correction factor of 0.42.0.42(L1 - L2) = scan incrementationThis test can also be used to test table increment accuracy. Scan the section and increment the table 30mm in and out of the gantry and scan again. The ramp centers should be the same on both images.0.42(L1 - L2) = 0Circular symmetry of display systemThe circular phantom sections are used to test for circular symmetry of the CT image, including calibration of the CT display system. If an elliptical image is produced, the x-y balance of the image display system should be adjusted.Measuring spatial linearity in x and y axes.Spatial linearity of pixel size verificationThis section has four holes (one with a Teflon pin). These 3mm diameter holes are positioned 50mm on center apart. By measuring from center to center the spatial linearity of the CT scanner can be verified. Another use is to count the number of pixels between the hole centers, and by knowing the distance (50mm) and number of pixels, the pixel size can be verified.The Teflon pin is used for identification and orientation only. The ability to change the Teflon pin position enables organizations with more than one Catphan® phantom to identify their phantoms by images of the first section.Spherical acrylic contrast targetsThe section has five acrylic spheres located in a 30mm diameter circular pattern. These spheres are used to evaluate the scanner’s ability to image volume averaged spheres. The sphere diameters are 2, 4, 6, 8, and 10mm.Sensitometry (CT number linearity)Four or seven high contrast sensitometric targets surround the wire slice thickness ramps. Three are made from the commercial plastics: Teflon, acrylic and low density polyethylene (LDPE). The fourth is air. These targets range from approximately+1000 H to -1000 H.The monitoring of sensitometry target values over time and can provide valuable information, indicating changes in scanner performance.Linear attenuation coefficient µ [units cm-1]KEV Teflon Delrin Acrylic Polystryrene Water LDPE PMP Air40 0.556 0.327 0.277 0.229 0.240 0.209 0.189 050 0.447 0.283 0.244 0.209 0.208 0.191 0.173 060 0.395 0.260 0.227 0.196 0.192 0.181 0.164 062 0.386 0.256 0.224 0.194 0.190 0.179 0.162 064 0.380 0.253 0.221 0.192 0.188 0.178 0.160 066 0.374 0.251 0.219 0.191 0.186 0.177 0.160 068 0.370 0.248 0.217 0.189 0.184 0.175 0.158 070 0.363 0.245 0.215 0.188 0.182 0.174 0.157 072 0.359 0.243 0.214 0.186 0.181 0.172 0.155 074 0.355 0.240 0.211 0.185 0.179 0.171 0.155 076 0.351 0.238 0.210 0.184 0.178 0.170 0.154 078 0.346 0.236 0.208 0.183 0.177 0.168 0.152 080 0.342 0.234 0.207 0.180 0.175 0.167 0.151 090 0.328 0.225 0.199 0.175 0.170 0.163 0.147 0100 0.315 0.218 0.194 0.170 0.165 0.158 0.143 0Nominal material formulation and specific gravityMaterial Formula Specific Gravity* Electron Density (1023e/g) CT # est. Air 75%N, 23.2%O, 1.3%A 0.00 3.007 -1000 PMP [C6H12(CH2)] 0.83 3.435 -200 LDPE [C2H4] 0.92 3.429 -100 Water [H2O] 1.00 3.343 0 Polystryrene [C8H8] 1.05 3.238 -35 Acrylic [C5H8O2] 1.18 3.248 120 Delrin™ Proprietary 1.41 3.209 340 Teflon [CF2] 2.16 2.889 990 Contrast Scale (CS) is formally defined asCS = µm (E) - µw (E)CT m (E) – CT w (E)where m is reference medium, and w is water, and E is the effective energy of the CT beam.Alternatively, CS = µ1 (E) - µ2 (E)CT1 (E) – CT2 (E)where 1,2 are two materials with low z effective, similar to water (eg. acrylic & air).*For sensitometry inserts The Phantom Laboratory purchases a multiple year supply of material from a single batch. Samples of the purchased material are then measured to determine the actual specific gravity.CTP591 Bead Geometry ModuleThe Bead Geometry Module contains 3 pairs of opposed ramps and 2 individual beads. Two of the ramp pairs have 0.28mm diameter beads, spaced 1mm on center in the z direction. The other ramp pair has 0.18mm diameter beads, spaced 0.25mm on centerin the z direction. The 2 individual beads are 0.28mm and 0.18mm in diameter. A 50µ diameter tungsten wire is located 6cm from the center of the module. The wire and beads create point spreads that can be used to calculate the MTF (see the CTP528 section of this manual).The bead ramps can be used to measure the slice width of single or multiple slices following several different methods.•count the beads and multiply by the z axis increment•plot the ssp of the beads (see CTP528 section for additional information)•compare the bead maximum net CT # in thick and thin slices. Thin slice thickness = (( thick slice max net CT#) ÷ (thin slice max net CT#)) *(thick slice width)•z axis length at the full width at half maximum of a bead in a sagital or coronal image •full width at half max for a best-fit curve of the max points of the bead net values in a slice image.Note: Net value = (CT# of the bead) - (CT# of the background)CTP528 High resolution module with 21 line pair per cm gauge and point sourceThis section has a 1 through 21 line pair per centimeter high resolution test gaugeand two impulse sources (beads) which are cast into a uniform material. The beads are positioned along the y axis 20mm above or below the phantom’s center and 2.5 and 10mm past the center of the gauge in the z direction. On older CTP528 modules the bead is aligned in the z axis with the gauge.Bead Point Source for point spread function and MTFUse the impulse source to estimate the point source response function of the CT system. Print out a digitized image of the area surrounding the impulse source. Use the numerical data to determine the two-dimensional array of the CT values arising from the impulse source.The FWHM of the point spread function is determined from the best-fit curve of the point spread function numerical data.The average of several different arrays of impulse response functions is calculated to obtain the average point spread function of the system. These numerical values are used in conjunction with the Fourier Transform Program to provide an estimate of the two-dimensional spatial frequency response characteristics of the CT system (MTF). Illustration is on the next page.The tungsten carbide bead has a diameter of 0.011” or 0.28mm. Because the bead is subpixel sized it is not usually necessary to compensate for its size. However, some MTF programs are designed to compensate for it.PSFCTnumbersLine spread functionRelative position, x axisThe above illustration shows how by summing the columns (y axis) of numbers in the point spread function (PSF) the line spread function (LSF) for the x axis is obtained.0.00.51.00.80.60.40.30.20.10.90.73.0 6.09.012.00.0MTFSpatial Frequency (1/cm)The MTF curve results from the Fourier transform of the LSF data. Generallyit is easiest to use automated software for this operation. Some CT scanners are supplied with software which can calculate the MTF from the Catphan® bead images. Independent software is listed in the Current automated programs available section of the manual.Use of automated scanner MTF programsMany manufacturers include automated MTF software in the standard scanner software packages. Because the bead is cast into an epoxy background which has a different density than water, the software must accept an input for the background. The point size of .28mm must also be selected. While a sphere does produce a different density profile than a cross section of a wire or cylinder, the actual difference is not usually significant in current CT scanners.Bead point source for slice sensitivity profileThe bead in this module can be used to calculate the slice sensitivity profile (SSP).reconstruction. The length of the object at the Full Width at Half Maximum signal indicates the SSP. This measurement can be easily obtained on some systems, by making a sagittal or coronal reconstruction through the bead. The bead image in these reconstructions will appear as a small line. By setting the FWHM (use the same technique described in the Scan slice geometry section) measuring the z axis length of the bead image to obtain the SSP.If the scanner does not have the ability to measure z axis lengths in the sagittal or coronal planes, a SSP can be made by incrementing or spiraling the slice through the bead and reconstructing images in positive and negative table directions from the bead (using the smallest available increments) and plotting the peak CT number of the bead image in each slice. The FWHM measurement can then be made from the plotted CTvalues of the bead as a function of z axis table position.21 Line pair per centimeter high resolution gauge The 21 line pair/cm gauge has resolution tests for visual evaluation of high resolution ranging from 1 through 21 line pair/cm. The gauge accuracy is ± 0.5 line pair at the 21 line pair test and even better at lower line pair tests.The gauge is cut from 2mm thick aluminum sheets and cast into epoxy. Depending on the choice of slice thickness, the contrast levels will vary due to volume averaging. Line Pair/cm Gap SizeLine Pair/cm Gap Size 10.500 cm110.045 cm20.250 cm120.042 cm 30.167 cm130.038 cm40.125 cm140.036 cm 50.100 cm150.033 cm 60.083 cm160.031 cm 70.071 cm170.029 cm 80.063 cm180.028 cm 90.056 cm190.026 cm 100.050 cm200.025 cm 210.024 cmCTP515 low contrast module with supra-slice and subslice contrast targetsThe low contrast targets have the following diameters and contrasts:Supra-slice target diameters Subslice target diameters2.0mm3.0mm3.0mm 5.0mm4.0mm 7.0mm5.0mm 9.0mm6.0mm7.0mm8.0mm9.0mm15.0mmNominal target contrast levels.3%.5%1.0%Since the target contrasts are nominal, the actual target contrasts need to be determined before testing specific contrast performance specifications. The actual contrast levels are measured by making region of interest measurements over the larger target, and in the local background area. To determine actual contrast levels, average the measurements made from several scans. It is important to measure the background area adjacent to the measured target because “cupping” and “capping” effects cause variation of CT numbers from one scan region to another. Position the region of interest to avoid the target edges. The region of interest should be at least 4 x 4 pixels in diameter. Because low contrast measurements are “noisy” it is advisable to calculate the average of the multiple measurements made from several scans. Carefully monitor the mAs setting becausethe photon flux will improve with increased x-ray exposure. Use the size of the targets visualized under various noise levels to estimate information on contrast detail curves.All of the targets in each contrast group are cast from a single mix to assure that the contrast levels will be the same for all targets.The equation below can be used to convert the measured contrasts and diameters to other specified contrasts and diameters.(Measured Contrast) * (smallest diameter discernible) ≅ Constantexample: 5mm diameter @ 0.3% ≅ 3mm diameter @ 0.5%Along with the supra-slice (targets with z axis dimension longer than most maximum slice width) the CTP515 low contrast module includes subslice targets (targets withz axis length smaller than some of the usual slice width). The subslice targets are arranged in the inner circle of tests in the module.Subslice Supra-sliceThe subslice targets are cast from the same mix as the 1.0% supra-slice targets. Because they are from the same mix in the evaluation of the actual subslice target contrast the supra-slice targets can be used to establish contrast values. The subslice targets have z axis lengths of 3, 5, and 7mm and diameters of 3, 5, 7, and 9mm.The evaluation of subslice target readability is helpful in understanding the scanner’s different spiral imaging settings and how the settings will affect the ability to visualize small objects with low contrasts from their background.。
JAX-9B中文操作说明书
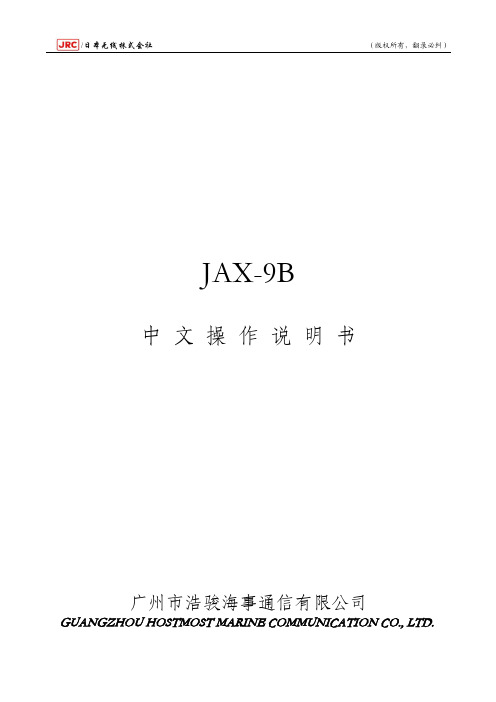
/日本无线株式会社 (版权所有,翻录必纠)JAX-9B中 文 操 作 说 明 书广州市浩骏海事通信有限公司 GUANGZHOU HOSTMOST MARINE COMMUNICATION CO., LTD.说 明为了使客户很快进入该设备的操作,我们参考原版英文说明书摘取了主要部份的操作说明进行了简单的翻译。
如有不详之处,请参考原英文说明书,以原厂家英文说明书为准。
目 录一、名称和功能---------------------------------------------------------------------------------- 11.1 电源开关-------------------------------------------------------------------------------------- 1 1.2 操作面板-------------------------------------------------------------------------------------- 1 1.3 控制旋钮-------------------------------------------------------------------------------------- 5 1.4 记录纸开盖旋钮------------------------------------------------------------------------------ 51.5 LCD显示--------------------------------------------------------------------------------------- 6二、基本操作---------------------------------------------------------------------------------------82.1 选择和设置接收频率(自动选择)------------------------------------------------------ 8 2.2 记录模式--------------------------------------------------------------------------------------- 9 2.3 接收传真--------------------------------------------------------------------------------------- 11 2.4 注册频道--------------------------------------------------------------------------------------- 18 2.5 定时程序记录--------------------------------------------------------------------------------- 21 2.6 与广播和接收相关的附加功能------------------------------------------------------------ 26 2.7 一般传真的功能设置------------------------------------------------------------------------ 31 2.8 报警显示-------------------------------------------------------------------------------------- 33第一章 名称和功能1.1 电源开关电源开关装在JAX-9B背面。
Bosch 500 Series Induction Cooktop 产品说明书

Power of Back Left heating element (in boost)
3,700 W
Power of Back Right heating element
2,600 W
Power of Back Right heating element (in boost)
3,700 W
Power of Front Right heating element
17 power levels for each cooking zone
Each cooking zone has an Independent countdown timer
SpeedBoost® – adds even more power to speed up the cooking process
Warranties: Please see Use & Care manual or Bosch website for statement of limited warranty.
For more information on our entire line of products, go to /us or call 1-800-944-2904
Features & Benefits
Induction – faster than gas and electric cooktops. Precise cooking, easy cleaning and more efficient
11" cooking zone for larger pots and pans
© BSH Home Appliances Corporation. All rights reserved. Bosch is a registered trademark of Robert Bosch GmbH.
22.DZ500 使用说明书

DZ500 型防喷器移动系统
DZ550
使用说明书
宝鸡鸿祥石油机电技术研究所
电话:(0917)3463571 传真 邮编:721006
手机:13991726902
Email:liuyujie2100@
地址:陕西省宝鸡市火炬路 4 号
目录
1、 概述……………………………………………………2 2、 形式与基本参数………………………………………2 3、 结构与特点…………………………………………2‐3 4、 安装与调试……………………………………………3 5、 操作、保养与安全……………………………………4 6、 易损件清单……………………………………………5 图一、吊装示意图………………………………………………6 图二、DZ‐400、DZ‐500、DZ‐550 防喷器移动装置………7 图三、液压原理图……………………………………………8
1
DZ-400、DZ-500、DZ-550 防喷器移动系统 使用说明书
1、概述
DZ-400、DZ-500、DZ-550 防喷器移动系统是为满足用户安装、拆卸
防喷器的需要而设计的,采用全液压控制,可用于大、中型钻井设
备。其主要功能为:移动单个防喷器进行安装或移动组合好的防喷
器组进行安装。该防喷器移动系统具有防爆、操作简单、可靠、安
Max.W.P.Hydr. System MPa
Max. Flow Hydraulic System
7.3 图三液压原理图
5
6
7
8
DZ-400
DZ-500 BOP Handling System
DZ-550
Operation Manual
Baoji Hongxiang petroleum Electro-mechanics Tech.lnst.
DH系列说明书

* 准备运行
1、再次检查是否有运输损害,如有损害,请联系:400-693-5886 2、参考所有注意事项 3、把洁净的柴油或煤油注入油箱后旋紧油箱盖(至少加油至油箱深度的二分之一以上)。在特别寒冷的季节,可以在
柴油中掺入部分煤油减少燃油粘度。 重要提示:第一次加油或者加热器长时间存放后油箱中会有凝结水,可以打开油箱底部的放油口排空冷凝水。 4、确认加热器附近没有易燃物质,且加热器进出风口未受阻。
* 安装
加热器带有轮子和手柄架。轮子以及其他配件都可以在包装箱内找到。在货箱中您可以找到以下配件: ①.一个暖风机机身并装有手柄架; ②.一个轮轴支架; ③.一个轮轴; ④.两个轮子; ⑤.四个螺丝钉; ⑥.四个螺钉帽; ⑦.八个垫片; ⑧.两个销子; ⑨.一本说明书; ⑩.一张质保卡。
按照以下步骤安装暖风机(见下图)
■调压重要提示:
问题:
调节: 问题: 调节:
加热器没有连续的火焰 加热器有烟或者有柴油味道 前罩板没有变红 气泵压力过低 顺时针方向旋动调压螺丝增加气泵压力 火焰喷出燃烧室 逆时针方向旋动调压螺丝减少气泵压力
◎ 日检 1、 通常检查 查看加热器部件是否松脱或者损坏。检查螺丝螺母是否会由于震动或者剧烈搬运产生松动。加热器损
使用说明及保养手册
适用型号
DH20M,DH20,DH40 请仔细阅读说明书:务必阅读并遵守说明书中指令。请把说明书保管好以备今后使用。未阅读说明书的人不能安装、 调试、操作本设备。
燃油热风机
警告:如果不能准确遵守该手册中的指令,错误使用本设备可能会引起火灾、爆炸并 由此产生财产损失、人身伤害等!
﹣请勿在设备附近储存或者使用汽油及其它挥发性易燃物 ﹣仅由专业人员进行维修
适用于中国地区的警告: 仅使用三爪插头,连接带地线电源!
SMC EX500系列减 wireless 系统操作手册说明书
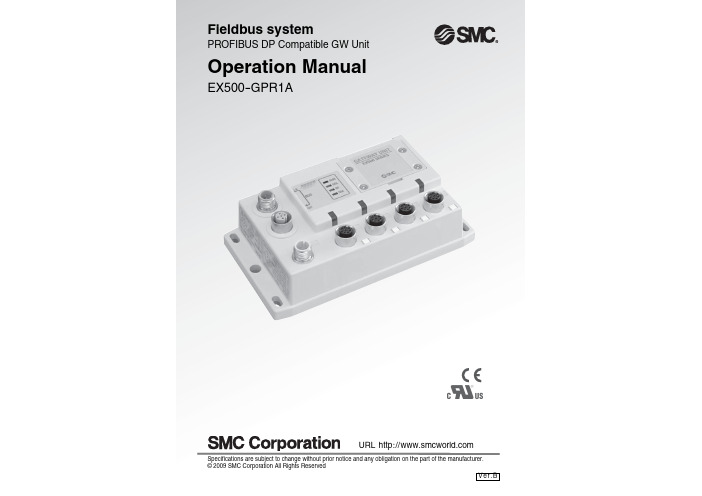
Specifications are subject to change without prior notice and any obligation on the part of the manufacturer.Thank you for purchasing the SMC reduced wiring system EX500 series.Please read this instruction manual carefully and understand the contents before use so that you can operate this unit safely and correctly.Please keep this manual handy for future reference.SAFETY ..........................................................................................................2Product Summary............................................................................................5EX500Part Names...................................................................................................6Dimensions...................................................................................................7Installation.....................................................................................................7Specification..................................................................................................8Wiring..........................................................................................................10Display/Switch setting.................................................................................17SI UnitPart Names.................................................................................................20Dimensions.................................................................................................21Mounting/Wiring..........................................................................................22Specification................................................................................................23Display........................................................................................................24Input Unit ManifoldPart Names.................................................................................................25Dimensions. (26)Installation...................................................................................................27Specification................................................................................................28Wiring..........................................................................................................29Display........................................................................................................30EX9 Series General Purpose Output BlockPart Names.................................................................................................31Dimensions.................................................................................................32Mounting.....................................................................................................33Wiring..........................................................................................................34Specification................................................................................................36Display .......................................................................................................37Option............................................................................................................38Troubleshooting (39)Appendix Table (40)OPERATORThis instruction manual has been written for those who have knowledge of machines and equipments that use reduced wiring system as well as thesufficient knowledge to assemble, operate, and maintain such devices.Before performing assembly, operation and/or maintenance, please read this manual carefully and understand the contents.ContentsTo facilitate recycling, this manual is printed using biodegradable soy ink, which can easily be de-inked.This manual is printed in the "non-water system", which does not output toxic liquid waste.The body of unit and this manual contain the essential information for the protection of users and others from possible injury and property damage and to ensure correct handling.Please check that you fully understand the definitions of the following messages ( symbols ) before going on to read the body of this manual, and always follow the instructions.Please also read the instruction manuals etc. of related machines and equipments andBefore performing maintenance:Turn off power supply.Stop air supply, exhaust compressed air in piping, and confirm the release to atmosphere.Otherwise injury can result.Follow the instructions given below when handling your reduced wiring system. Otherwise a damage or failure to cause a malfunction can result.Operate the reduced wiring system at the specified voltage.Reserve space for maintenance.Do not remove any name plate or label.Do not drop, hit or apply an excessive shock to the unit.Follow the specified tightening torque.Do not apply any excessive force to cables by repeated bending, tensioning or placing a heavy object on the cables.Connect wires and cables correctly.Do not perform any wiring work while the power is on.Do not use the reduced wiring system on the same wiring route as the power line or high voltage line.Confirm the insulation of wiring.Perform the power supply wiring by dividing into two lines ---- one is for power supply for output and the other is for power supply for input and control.Take sufficient measures against noise such as noise filter when incorporating the reduced wiring system into a machine or equipment.Mount a terminal plug or a waterproof cap on each unused M12 connector for input/output ( communication connector, communication ports A - D, and power supply for input and control).Take sufficient shielding measures when operating the product in any of the following places. ( 1 ) A place where noise due to static electricity etc. is generated( 2 ) A place of high electric field strength( 3 ) A place where exposure to radioactivity is possible( 4 ) A place near power cableDo not operate the product in a place where there is a source of surge.Use a surge absorbing element built-in type to directly drive the load that generates surge voltage such as solenoid valve.Prevent any foreign matter such as remnant of wires from getting inside the product when opening the station number switch protective cover.Install the reduced wiring system in a place free from vibration and impact.Operate the product in the specified ambient temperature range.Do not use in a place to be affected by the radiant heat from a surrounding heat source.Set the DIP switch and rotary switch by using a sharp-pointed watchmakers screwdriver etc. Perform the maintenance regularly.Conduct an appropriate functional inspection after completing the maintenance.Do not use chemicals such as benzin and thinner to clean the product.System configurationBranch cableInput unit manifoldManifold valvewith SI unitThe reduced wiring system is connected to various kinds of fieldbus realizes the reduced wiring and decentralized installation of I/O devices . The signals to/from fieldbus are exchanged by GW unit, and the signals to/from decentralized I/O devices are collected and delivered by GW unit.The maximum number of connections of manifold valve/Input unit manifold is16/branch x 4 branches = 64 points each for output and input.As the cables with connectors are used for all wirings among devices, the system complies with the IP65 environment.Note1: For wiring method, refer to subsection "Wiring" ( page 10 ) of section "EX500" in this manual.Note2: For display and setting method, refer to subsection "Display/Switch Setting" ( page 17 ) of section "EX500" in this manual.49.9136461160EX500 bodyC u to u t Dimensions for Mo u nting (Tolerance: 0.2)4 M5*Installation ( unit:mm )Thread mountingSecure at four positions with screws with head diameter of 5.2 or more and threadBasic specificationsHigher-level busProtocol PROFIBUS DP ( EN50170 ) Bus interface EIA RS-485Transmission rate Transmission distance 9.6/19.2/45.45/93.75/187.5/500kbps, 1.5/3/6/12Mbps Refer to the following.Freeze mode/Sync mode SupportedID Number1405 ( hexadecimal )Transmission distanceFor the communication wiring, use a PROFIBUS DP compatible twisted pair cable with shield. The maximum cable length depends on the transmission rate and the cable type to use. The following table shows the values when cable Type A ( see Note ) is used. Transmissionrate [kbps]9.619.245.4593.75187.550015003000600012000 Cable length [m]12001000400200100Wire diameter0.64mm or moreCorecross-section0.34mm2ormoreNote: Cable Type A specificationLower-level busNote: Total value of maximum current consumption and maximum load current of input devices to connect.Pollution degree Pollution degree 2 Operating ambient temp5o C to 45o C Storage ambient temp-25o C to 70o C Enoironmental specificationsThe wirings are described in the following order.Po w er s u pply connector Po w er s u pply for o u tp u tPo w er s u pply for inp u t andcontrolC o m m u n i c a t i o n c o n n e c t o rN N RxD/TxD N RxD/TxD N RxD/TxD P RxD/TxD P 0+240+24Gro u V V V V COM AV V V VCOM DN N Gro u Internal circuitCommunication wiring1Aligning the key groove with the IN-side communication connector ( 5-pin, plug ) ofGW unit, plug the PROFIBUS DP communication cable ( socket ).Tighten the lock nut on cable side by turning it clockwise by hand.Confirm that the connector portion does not move.Similar to the above, connect the other communication cable ( plug ) to the OUT-side communication connector ( 5-pin, socket ) of GW unit.Cable connectionConnect the communication cable with M12 connector to the M12 reversecommunication connector. For the cable to use, refer to "Appendix Table" ( page 40 ) in this manual.Pin layout and connection diagram of cable with PROFIBUS DP communication connectorConnect the cable with PROFIBUS DP communication connector to the communication connector of GW unit.2531415423OUTI NCommon to IN side and OUT sidePower supply wiring2Connect the power supply connector cable to the power supply connector of GW unit.There are two types of cables different in connector shape ----straight type and angle type. With this cable, the power is supplied to the output devices such as solenoid valve,and the input devices such as sensor, and for control. Therefore, there is no need to supply the power to other units individually.When selecting the power supply, refer to "Handling precautions" ( page 3 ) in this manual.24351Socket Connector Pin Layo u tSeparate wiring for power supply for solenoid valves/output and for input and control of GW/SIBoth single power supply and two power supply systems can be adopted, however, the wiring shall be made separately ( for solenoid valves/output and for input and controlling GW/SI ) for either system.A. Two power supply systemBranch wiring ( wiring to communication ports )3For wiring with solenoid valves or input devices, connect the branch cable with M12connector to communication ports A - D.There are two types of cables different in connector shape ----straight type and angle type. As each cable contains power supply wire, there is no need to supply the power to solenoid valves or input devices individually.Cable connectionAligning the key groove with theconnector ( socket ) of GW unit, plug inthe cable ( plug ).575Socket Connector Pin Layo u t Pl u g Connector Pin Layo u tTighten the lock nut on cable side by turning it clockwise by hand.Confirm that the connector portion doesnot move.For GW unit – Manifold valve – Input unit manifold configurationTwo communication connectors in SI unit and one communication connector in Input unit are installed respectively.To the communication connector ( C2 ) or ( 1 ) of SI unit, connect the branch cable with M12 connector from GW. To the communication connector ( C1 ) or ( 0 ), connect the branch cable with M12 connector from Input unit.To the communication connector of Input unit, connect the branch cable with M12connector from SI unit.G W u nitnit Connector (C1) / (0)Connector (C2) / (1)For GW unit – Input unit manifold configurationTo the communication connector of Input unit, connect the branch cable with M12connector from GW unit.G W u nitL=300, 500, 1000, 3000, 5000 (mm)GATEWAY UNITEX500 SERIESDIABF SOL RU N COM A COM B COM C COM DOUTI NBUSO I B U SF R P Settings for display1819Switch settingOpen the station number switch protective cover and set the switches with a sharp-pointed watchmakers screwdriver etc.Address setting switches 1,2 and 3 ( SW1,SW2 and SW3 )These switches can set the node address. The settings of each switch are as shown in the table below. The addresses up to 32 stations ( without repeater ) or 126 stations( with repeater ) can be set per segment.S W 2S W 310010S W 11Bus terminator switch ( SW4 )This switch can set the bus terminator.iths terminator itho u ts terminator itho u ts terminator2021The SI unit is the unit to communicate with GW unit in combination with manifold valve.It can be used with SV series valves, VQC series valves and S0700 series valves.In addition, this unit is able to operate solenoid valves, relays. etc. in combination with EX9 series general purpose output block. For how to use it, refer to section "EX9 Series General Purpose Output Block" ( page 31 ) in this manual.S V series1.SI unit for SV series valves ( EX500-S 01 )mon to EX500-S 01/EX500-QNote1: For wiring method, refer to subsection "Wiring" ( page 10 ) of section "EX500" in thismanual.Note2: For display, refer to "Display" ( page 24 ) in section "SI Unit" in this manual.1.SI unit for SV series valves ( EX500-S01 )2.SI unit for VQC/S0700 series valves ( EX500-Q 01 )( EX500-Q 02 )2223The mounting and removing methods of SI unit are as shown below.For branch wiring method, refer to subsection "Wiring" ( page 10 ) of section "EX500"in this manual. As the power to output devices such as solenoid valve is supplied by branch wiring ( branch cable with M12 connector ), there is no need to supply power individually.Note 1For mounting/installation methods of solenoid valve, manifold, etc., refer to thecatalogs, instruction manuals, technical data, etc. of each valve series.When connecting general purpose output block only, refer to subsection "Mounting"( page 33 ) of section "EX9 Series General Purpose Output Block" in this manual.Note 2M3 28: 4 pcs.( Pl u s-min u s slot ro u nd head scre w )assem blyu pply/exhau st b lock b lyM3 10: 2 pcs.scre w ( w3.Applicable valve seriesFor detailed specifications of solenoid valve and manifold, refer to the catalogs, operation manuals, technical data, etc. of each valve series.SV1000/2000/3000/4000VQC1000/2000/4000S07002425Po wComm u SI unit for SV series valves ( EX500-S01 )Po w er LEDCommu nication LEDSI unit for VQC/S0700 series valves ( EX500-Q)Common to EX500-S01/EX500-QThe Input unit manifold consists of Input unit, input block (s), end block and DIN rail.The input block up to 8 can be connected ( 16 points ).Any combination of input blocks ( for M8 connector, M12 connector and 8-point-integrated type ) is acceptable.Note1: For wiring method, refer to subsection "Wiring" ( page 29 ) of section "Input UnitManifold" in this manual.Note2: For display, refer to "Display" ( page 30 ) in section "Input Unit Manifold" in this manual.Figure shows the configuration when only input blocks for M8 connector are connected.Do not mix sensor input specifications ( PNP and NPN ) .NoteWhen only input blocks for M8 connector are connectedWhen only input blocks of 8-point-integrated type are connectedWhen only input blocks for M12 connector are connectedConnect each connector of Input unit, input blocks,and end block ( portion indicated by arrow in thefigure to the right ).Holding with hands so that there will be no gapbetween blocks, place the jointed unit and blocks onDIN rail.Tighten the bolts of Input unit and end block tosecure the jointed unit and blocks to DIN rail.Be sure to tighten the bolts by proper tighteningtorque. ( Tightening torque: 0.6Nm )321Installation2627Specifications for Input unitSpecifications for input blockBranch wiringFor wiring method, refer to subsection "Wiring" ( page 10 ) of section "EX500" in thismanual. To input devices such as sensor, the power is supplied through the branchwiring ( branch cable with M12 connector ). Therefore, there is no need to supply thepower to them individually.M12 BlockSensor wiringConnect sensors to the sensorconnectors of input block.Pin layout of sensor connectorNote: Internal wiring of M12 input block and key position for mounting sensor connectorNo. 2 pins of M12 input block connectors arewired to each other’s sensor signal input pins( No. 4 pins ) internally.This wiring enables direct input of signals fromtwo points combined into one cable throughconcentric connector etc.When connecting sensors, confirm thespecification of output signal carefully.Otherwise malfunction can result.The key position for mounting sensorconnector is as shown to the right. Considerthis key position when selecting sensor.283031Input block up to 8 can be connected ( 16 points ).Input numbers are 0 - 15 from Input unit side.246810Inp u t u nit 121413579111315The EX9 series general purpose output block is the unit to operate solenoid valve, relay,etc. in combination with VQC series valve and applicable SI unit.There are two types ---- one type is for low wattage load ( EX9-OET1 or EX9-OET2 ) that outputs signals by receiving power supply from SI unit, and the other type is for highwattage load ( EX9-OEP1 or EX9-OEP2 ) that outputs signals by receiving power supply from outside. The type for high wattage load is used in combination with the power block ( EX9-PE1 ) connected with external power supply. As the low-wattage-load type is powered from SI unit, the wattage of load is limited to 1.0W ( Note1 ). For a load up to 12W, use the power block and the high-wattage-load type.Note1: When connected with EX500 series.1.EX9-OET1/EX9-OET2/EX9-OEP1/EX9-OEP2V SI u nit forV ( EX500-Q 02 )Note1: For wiring method, refer to subsection "Wiring" ( page 34 ) of section "EX9 SeriesGeneral Purpose Output Block" in this manual.Note2: For display, refer to subsection "Display" ( page 37 ) of section "EX9 Series GeneralPurpose Output Block" in this manual.32332.EX9-PE1VSI u nit forgeneral p o u tp u t b Dimensions ( unit:mm )1.EX9-OET1/EX9-OET2/EX9-OEP1/EX9-OEP22.EX9-PE1Note1: For wiring method, refer to subsection "Wiring" ( page 34 ) of section "EX9 SeriesGeneral Purpose Output Block" in this manual.Note2: For display, refer to subsection "Display" ( page 37 ) in section "EX9 Series GeneralPurpose Output Block" in this manual.M3 18 : 2 pcs.cap scre w( w u tp u t b locku rpose lock ( EX500-Q 02 )L dimensionsThe mounting and removing methods of each SI unit are as shown below.Dimensions when general purpose output block is connectedThe above dimensions show those when one unit of power block ( width: 21mm ) is combined. For details, refer to the instruction manuals, technical data, etc. of EX9series general purpose output block.Note3435Output wiringConnect output devices to the output connectors.EX9-OET1/EX9-OET2/EX9-OEP1/EX9-OEP2 output connectorsNC: Not connectedTwo outputs are available with only output connector No. 0.M12, 5-pin, reverse key, socketPower supply wiringWhen combining EX9-OEP1 ( or EX9-OEP2 ) and EX9-PE1 and using external power supply, connect the power supply to the power input connector of EX9-PE1.When selecting power supply, refer to "Handling precautions" ( page 3 ) in this manual.EX9-PE1 power supply connector No.0reverse key, plugNote: Each signal of connector No.0 is connected to corresponding signal of connector No.1.The pins whose applications are shown in brackets [ ], are prepared supplementarily and not used normally.2531415423Po w er s u pply connector N o.0Po w er inp u t connector No.1Keep the waterproof cap mounted on power supply connector No.0 while using EX9-PE1. This connector is prepared supplementarily and not used normally.NotePl u g connector pin layo u t13452Pin allgnment and connection drawing of the Output CablePin allgnment and connection drawing of the Power Supply Cable36371.EX9-OET1/EX9-OET2/ EX9-OEP1/EX9-OEP2Note:To be used in combination with EX9-PE1.For detailed specifications, refer to the instruction manuals, technical data, etc. of EX9series general purpose output block.2.EX9-PE11.EX9-OET1/EX9-OET2/EX9-OEP1/EX9-OEP2Settings for display2.EX9-PE138TroubleshootingBranch cable with M12 connectorFor details, refer to subsection "Wiring" ( page 10 ) in section "EX500" in this manual.1Ho w to order:Power supply connector cableFor details, refer to subsection "Wiring" ( page 10 ) of section "EX500" in this manual.2Ho w to order: Terminal PlugConnected to C1 ( or 0 ) of SI unit when Input unit manifold is unused. ( If this terminal plug is not used, COM LED of GW unit does not light on. )5Ho w to order: EX500-AC000-SWaterproof capMounted on unused ports of GW unit, input block, power block and output block.The proper use of this waterproof cap can achieve IP65 Enclosure. ( The waterproof caps are delivered together with each input block as accessories. )6Ho w to order: EX500-A Overall systemHo w to order: EX9-7b le length(L)0100301[m]3[m]Ho w to order: Output cableFor details, refer to subsection "Wiring" ( page 34 ) of section "EX9 series General Purpose Output Black " in this manual.3Power supply cable(for power input connector of Power block)For details, refer to subsection "Wiring" ( page 34 ) of section "EX9 series General Purpose Output Black " in this manual.44041PROFIBUS DP compatible communicationCable with PROFIBUS DP communication cable/connector/terminal plugAppendix Table。
美国美国发布公司产品E9500工业汽油发电机操作手册说明书

WARNINGDO NOT OPERATE EQUIPMENT UNTIL READING & UNDERSTANDING OPERATOR’S MANUAL!TABLE OFCONTENTSSafety ................................................................................................................................................................................................ 2 Operation .......................................................................................................................................................................................... 6 Maintenance and Troubleshooting . (8)Specification & 1The following signal words and meanings are intended to explain the level of risk associated with this productIndicates a hazard which, if not avoided WILL result in death or serious injury.Indicates a hazard which, if not avoided, could result in death or serious injury.Indicates a hazard which, if not avoided, could result in minor or moderate injury.IMPORTANT WARNING SYMBOLSOperator’s ManualToxic FumesStore in Dry PlaceKeep DryGround GeneratorFireHot SurfacesProper LiftingGround ProperlyMANUFACTURER SHALL NOT BE RESPONSIBLE FOR ANY CONSEQUENCES RESULTING FROM IMPROPER USE OF THIS EQUIPMENT. THE OPERATOR IS REQUIRED TO READ THE ENTIRE CONTENTS OF THIS MANUAL BEFORE ATTEMPTING TO OPERATE THE UNIT. IF THE OPERATOR DOES NOT COMPLETELY UNDERSTAND THE INSTRUCTIONS AND ALL OF THE HAZARDS OF OPERATING THIS UNIT AFTER READING THIS MANUAL, OPERATOR MUST CALL THE FACTORY TO ANSWER THESE QUESTIONS TO OPERATOR’S COMPLETE SATISFACTION BEFORE PROCEEDING.• READ AND COMPLETELY UNDERSTANDENTIRE CONTENTS OF THIS OPERATOR’S MANUAL AND BECOME FAMILIAR WITH THE UNIT BEFORE ATTEMPTING TO START USING THIS EQUIPMENT! IT IS YOUR RESPONSIBILITY TO KNOW ITS APPLICATIONS,LIMITATIONS, AND HAZARDS! CALL THE FACTORY WITH ANY QUESTIONS.• A MINIMUM OF THREE (3) FEET OF CLEARANCE ON ALL SIDES IS REQUIRED.• THIS UNIT IS ONLY TO BE USED FOR ITS INTENDED PURPOSE, ANY OTHER APPLICATIONS COULD VOID WARRANTY.• USER ACCEPTS RESPONSIBILITY FOR INJURIES AND/OR DAMAGE RESULTING FROM OT HER APPLICATIONS.• INSPECT UNIT PRIOR TO USE FOR ANY UNSAFE CONDITIONS.• FOLLOW ALL CODES FOR THE SAFE OPERATION OF THIS EQUIPMENT, BOTH LOCAL AND FEDERAL• ONLY PEOPLE THAT ARE WELL ACQUAINTED WITH THE RULES OF SAFE OPERATION SHOULD USE THE GENERATOR.• KEEP CHILDREN AWAY FROM THE UNIT.• WEAR SAFETY GLASSES AND HEARING PROTECTION.• DO NOT STAND ON THE UNIT OR ATTEMPT TO USE IT AS A HAND HOLD.• REPLACE OR REPAIR ANY DEFECTIVE PARTS BEFORE USING.• DO NOT FILL FUEL TANK IF ENGINE IS HOT.• THE ENGINE GOVERNOR IS PRESET. DO NOT TAMPER WITH THE SETTING. EXCESSIVELY FAST SPEEDS WILL SEVERELY SHORTEN THE LIFE OF THE ENGINE AND MAY BE HAZARDOUS.FOR OUTDOOR USE ONLYNEVER USE THIS UNIT INSIDE OF ANY BUILDING, ENCLOSURE OR A RECREATION VEHICLE (RV). NO MODIFICATIONS WILL ELIMINATE THE DANGER OF POSSIBLE CARBON MONOXIDE POISONING, FIRE OR EXPLOSIONWARNINGS AND CAUTIONSIN THIS MANUAL AND OR DECALS AND TAGS ON THE UNIT ARE NOT ALL INCLUSIVE. IT WOULD BE IMPOSSIBLE TO ANTICIPATE EVERY CIRCUMSTANCE THAT MIGHT INVOLVE A HAZARD HANDLING.TO PREVENT SERIOUS INJURY FROM ACCIDENTAL OPERATION: Turn the UNIT OFF AND DISCONNECT THE BATTERY to prevent accidental starting.•GENERATORS PRODUCE A VERY POWERFUL VOLTAGE THAT CAN CAUSE EXTREMELY DANGEROUS ELECTRICAL SHOCK. AVOID CONTACT WITH BARE WIRES, TERMINALS, ETC. NEVER PERMIT AN UNQUALIFIED PERSON TO OPERATE OR SERVICE THE GENERATOR.•NEVER HANDLE ANY KIND OF ELECTRICAL CORD OR DEVICE WHILE STANDING IN WATER, WHILE BAREFOOT, WITH WET HANDS OR WHEN FEET ARE WET. DANGEROUS ELECTRICAL SHOCK COULD RESULT.•THE NATIONAL ELECTRIC CODE REQUIRES THAT THE FRAME AND EXTERNAL CONDUCTIVE PARTS BE PROPERLY CONNECTED TO AN APPROVED EARTH GROUND. LOCAL ELECTRICAL CODES MAY VARY. CHECK WITH AN ELECTRICIAN FOR LOCAL GROUNDING REQUIREMENTS.•USE A GROUND FAULT CIRCUIT INTERRUPTER IN ANY DAMP OR HIGHLY CONDUCTIVE AREA SUCH AS METAL DECKING OR STEEL WORK.•DO NOT USE WORN, BARE, FRAYED OR OTHERWISE DAMAGED ELECTRICAL CORDS OR WIRING WITH THE GENERATOR. A DEFECTIVE CORD MAY RESULT IN ELECTRICAL SHOCK OR MAY CAUSE DAMAGE TO EQUIPMENT.•DO NOT EXPOSE UNIT TO EXCESSIVE MOISTURE,DIRT OR CORROSIVE VAPORS. UNIT MUST BE OPERATED ON A LEVEL SURFACE •ONLY OPERATE THIS UNIT OUTSIDE WITH ADEQUATE VENTILATION. THIS GENERATOR’S EXHAUST PRODUCES CARBON MONOXIDE GAS THAT CAN CAUSE UNCONSCIOUSNESS OR EVEN DEATH.•NEVER STORE A GENERATOR WITH FUEL IN THE TANK WHERE FUEL VAPORS COULD BE IGNITED BY A FLAME, SPARK, OR PILOT LIGHT FROM AN APPLIANCE SUCH A SA FURNACE, WATER HEATER, OR CLOTHESDRYER.•ALWAYS ALLOW A MINIMUM OF 3 FEET OF CLEARANCE ON ALL SIDES FOR VENTILATION WHILE UNIT IS OPERATING. ALLOW 3 FEET OF CLEARANCE FROM ALL COMBUSTIBLES.•GENERATOR MUST ALWAYS BE STOPPED OR STARTED WITH ALL LOADS DISCONNECTED. START THE ENGINE AND LET IT STABILIZE BEFORE CONNECTING ANY LOADS. DISCONNECT ALL LOADS BEFORE SHUTTING DOWN THE GENERATOR.•NEVER INSERT ANY OBJECT THROUGH THE COOLING SLOTS OF THE ENGINE. YOU COULD DAMAGE THE UNIT OR CAUSE INJURY.NEVER OPERATE THE GENERATOR:•IN WET OR RAINY CONDITIONS•IN AN ENCLOSED COMPARTMENT•IF CONNECTED DEVICES OVERHEATAir Conditioning Unit (12,000 btu) 1700Impact Wrench 500 Battery Charger 500*Jet Pump800 Belt Sander 100Lawn Mower1200 Chain Saw 1200Light Bulb100 Coffee Maker 900Microwave Oven 700 Air Compressor (1HP)2000*Milk Cooler 1100 Air Compressor (3/4HP)1800Oil Burner on Furnace 300 Air Compressor (1/2HP)1400Oil Fired Space heater (140,000 BTU) 400 Curling iron 700Oil Fired Space heater (85,000 BTU) 225 Freezer 700Oil Fired Space heater (30,000 BTU) 150 Disc Sander 1200*Airless Paint Sprayer (1/3 HP)600 Edge Trimmer 500Handheld airless Paint Sprayer 150 Electric nail gun1200Radio 50 Electric Range 1600Slow Cooker 200 Furnace Fan (1/3HP) 1200*Submersible Pump (1-1/2 HP) 2800 Hair Dryer1200*Submersible Pump (1 HP) 2000 Hand Drill1200*Submersible Pump (1/2 HP) 1500 Television 500Sump Pump 600CAUTIONDO NOT ATTEMPT TO START THE ENGINE BEFORE CHECKING OILWARNINGDO NOT OVERFILL! LEAVE ROOM FORFUEL E XPANSION. N EVER FILLFUEL INDOORS. NEVER FILL FUELWHEN ENGINE IS HOT OR RUNNING.DO N OT S MOKE O R F ILLCAUTIONDO NOT CLEAN AIR FILTER WITHANY TYPE OF D ETERGENT.1. Place generator on a level surface.2. Clean area around oil fill opening.3. Remove the dipstick.4. Wipe the dipstick clean.5. Reinsert dipstick and check oillevel.6. DO NOT OVERFILL6. CLOSE OIL CAP.7. Change oil as published1. Remove cover panel.2. Loosen wing nut and remove airfilter cover3. Never wash air cleaner with anykind of detergent or cleaning sol-vent.4. Air filter should be changed ifengine performance decreases orcolor of exhaust changes.5. Never run engine without air filter.This will cause rapid engine wear.1. Fill with gasoline fuel only2. Clean area around fuel cap.3. Remove fuel cap.4. Add fuel to fuel tank.5. DO NOT overfill. Do not fill abovethe red plug inside the fuel tankfilter (this allows for fuel expansion)6. Replace fuel cap.7.Wipe up any spilled fuel.STARTING THE ENGINE MANUAL START• CHECK OIL AND GAS FOR PROPER LEVELS• TURN FUEL VALVE TO THE ONPOSITION(FIGURE #3)• TURN IGNITION SWITCH TO THE ON POSITION• SLIDE CHOKE LEVER TO THE ON/CHOKEPOSITION• GRIP RECOIL STARTER AND PULL BRISKLY• ONCE STARTED RETURN CHOKE LEVER TO THE OFF/RUN POSITION.• LET ENGINE STABILIZE BEFORE HOOKING UP ANY ELECTRICAL APPLIANCESELECTRIC START• BE SURE UNIT IS AT A LEVEL, WELL VENTILATED POSITION• CHECK FLUIDS FOR PROPER LEVELS.• TURN ON FUEL VALVE. (FIGURE #3)• SLIDE CHOKE LEVER TO THE ON/CHOKEPOSITION• TURN THE IGNITION KEY TO THE “START”POSITION.• ONCE ENGINE HAS STARTED, RETURN THE KEY TO THE “ON” POSITION.• RETURN CHOKE TO OFF/RUN POSITION.• LET ENGINE STABILIZE AND WARM UP FOR AT LEAST 3 MINUTES BEFORE ATTACHING ANYAPPLIANCES.• MAKE SURE DEVICES TO BE CONNECTED ARE IN GOOD WORKING ORDER AND IN THE “OFF”POSITION BEFORE CONNECTING TO THESTOPPI NG T H E E NG I N E• TURN OFF ALL E LECTRICAL DEVICESCONNECTED TO THE GENERATOR.• WARNING: DO NOT START OR STOPGENERATOR WITH ELECTRICAL DEVICESPLUGGED IN.• ALLOW THE GENERATOR ENGINE TO RUN AT A‘NO LOAD’ CONDITION FORSEVERAL MINUTES TO STABILIZEINTERNAL ENGINE TEMPERATURE BEFORESTOPPING.• TURN THE KEY ON THE CONTROL PANEL TO THE “OFF” POSITION.• TURN FUEL VALVE TO THE “OFF” POSITION.• KEEP THE GENERATOR CLEAN AND DRY.USE A DAMP CLOTH TO CLEAN EXTERIORSURFACES.REMOVE CAKED ON DIRT WITH ASOFT BRUSH.• N E V E R S P R A Y W I T H WATER. WATER WILL CAUSE ELECTRICAL SHORTS IN Fuel tank should never be filled indoors. Avoid spilling fuel on hotGASOLINE GENERATOR ENGINES REQUIRE 38OUNCES OF 10W/30 TYPE API SJ or HIGHERMAINTENANCE SCHEDULEDAILY MONTHLY 3 MONTHS 6 MONTHS Check Air Filter xCheck For Oil Leaks x xReplace Air Filter xChange Oil x*First oil change should be after 5 hours. After initial break-in period change oil every (30) hours.batteries give off explosive hydrogen Avoid smoking, open flames, sparks or any otherWhen working on the generator, always disconnect cable from the battery. Also disconnect spark plus wireHot oil may cause burns. Allow engine to cool before draining oil. AvoidPage 8AMERICAN FAB INC TRAVELERS REST, SCPage 10Remote StartingThe ignition key has to be in the run position to operate the remote.Battery DrainWhen the unit is not operating always keep the ignition key in the “OFF”position to avoid battery drain and accidental starting!240 VOLT RECEPTACLEWARRANTYAmerican Fab equipment is warranted to be free from defects in material and workmanship for a period of120v 20 amp Receptacle1- L14-30 Receptacle 1- L14-30 Auxiliary plug Circuit Breaker Protection 74 Db. @ 10’Electric Start \ Manual Recoil 420cc Gasoline Engine Steel Sleeve Cylinder 12.3 Gallon Fuel TankApprox. Run Time 24 hrs @ 50% LoadCopper Windings Single Phase 60Hz Low Oil Shut Down Oil Capacity 32 oz 12v DC ConnectorSize: L-29” W-30” H-31” Net Weight: 360lbLockable Toolbox Compartments Hex Key LocksEngine Warranty – 2 years Equipment Warranty – 1 year Battery- 230 CCA Lawn and Garden batteryManufactured by:American Fab Inc.P.O. Box 1027WARRANTY。
梅思安说明书
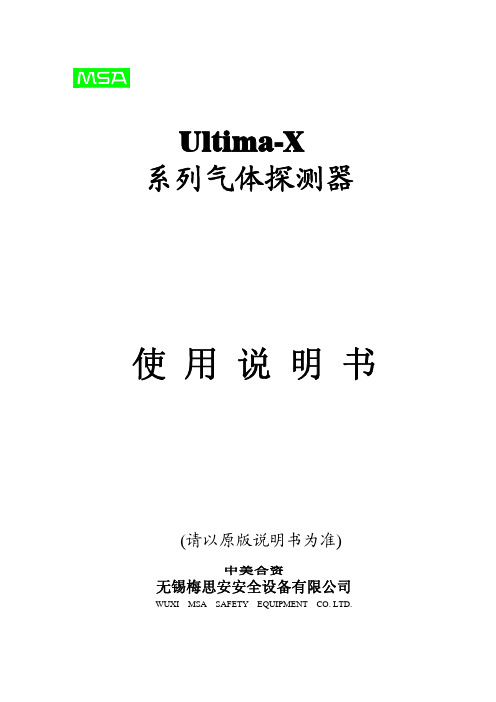
Ultima-X系列气体探测器使用说明书(请以原版说明书为准)中美合资无锡梅思安安全设备有限公司WUXI MSA SAFETY EQUIPMENT CO. LTD.重要的警告本说明书只是对该类仪表作简要的介绍,具体使用说明请按原版英文说明书为准。
任何负责或将要负责安装、使用或维修本产品的人员都必须仔细阅读本说明书。
象任何复杂的设备一样,只有按照制造厂家的说明与要求去安装、使用及维修,才能使本仪表按设计的性能要求去年工作,否则,仪表将不能正常工作而致使依靠此仪表来保障安全的愿望无法实现,甚至发生更为严重的伤亡事故。
如果不按照本手册的说明去安装、使用及维修本仪表,无锡梅思安公司对本产品所作的保证将是无效的。
因此,请遵守本手册说明以保障你本人及员工的安全,欢迎用户在使用本产品之前写信或打电话来询问有关使用或维修方面的信息。
1注意事项1、本手册所叙述的变送器应按照产品标签、注意事项、警告等项说明(并仅限在指明的范围内)去安装、操作和维修保养。
2、为防止在危险环境下引燃起爆,当接通电源时探测器的防爆盒盖务必密闭。
如需打开盒盖维修或标定,先要确认环境空气中无可燃性气体存在,直至关上盒盖。
3、探测器设计用来检测空气中的可燃性气体、毒气、氧气或其蒸汽浓度,而不能测定水汽中或惰性气体中或严重缺氧环境中的可燃性气体与蒸汽浓度。
4、探测器探头探测器隔爆片上不能被粘污或涂漆。
如在安放探测器的场所进行喷漆,须注意确保探测器入口处的粉末冶金隔爆片上不能粘有漆,否则,漆会阻碍被监测的气体扩散进入探测器。
安装时探测器朝下并离地面至少0.3M,以方便检修及标定,要杜绝雨水的滴入和地面水的溅入。
5、确保探测器正常工作的唯一方法是用已知浓度的气体对探测器进行标定检查,因此标定检查应作为此系统日常检查工作的一部分。
6、探测器的电源电压为7~30VDC,推荐工作电压为24VDC。
超过30VDC的电压将导致仪表的永久性损坏!7、在进行本手册所介绍的操作和保养时,只可以使用真正无锡梅思安公司的配件,否则,可能会严重影响仪表性能。
- 1、下载文档前请自行甄别文档内容的完整性,平台不提供额外的编辑、内容补充、找答案等附加服务。
- 2、"仅部分预览"的文档,不可在线预览部分如存在完整性等问题,可反馈申请退款(可完整预览的文档不适用该条件!)。
- 3、如文档侵犯您的权益,请联系客服反馈,我们会尽快为您处理(人工客服工作时间:9:00-18:30)。
现场操作说明; 现场设置··操作
开 向 按 钮 ·· 菜 单 反 阅 ·· 参 数
选择旋钮
点按··反回上级菜单 模式停机 长按··进入下一级菜单
远程控
关向按钮··菜单翻阅··参数减 图2
设定值并保存
在显示第二级菜单时,长按“MODE”按钮即可进入设定级。以显示第二级菜单“F1.1 TORQUE_O”时 为例,长按“MODE”时可进入开向停机力矩设定,菜单显示当前百份比力矩值和“TORQUE_O”,且数字闪 烁,此时用“↑”和“↓”按钮可以调整开向力矩值。达到调整值后,短按“MODE”按钮,如力矩设定
5、输出附加电源; 24V DC/50mA 最大
6、电机控制;
变频调速恒力矩控制 (无刷直流调速选项)
7、工作模式;
S4-25%-1400 次/h
8、额定调节力矩; 最大仃机力矩的 60%
9、环境温度湿度; -25℃~+70℃ 湿度≤95% (可选增加除湿器,避免水气凝结现象)
10、抗干扰性能; 按 GB/T 17626.4-1998 电磁兼容试验标准
16、安 装 位 置; 任意位置安装
4、菜单结构和基本参数设定
Biaoteng 产品采用多层树状菜单,操作简单,维护方便。
第一级菜单中除“F0”外,均含有第二级子菜单。
LOCAL O/S
REMOTE
F0 LANGUAGE
F1 SETUP
F2 PARAMETR F3 SERVICE
F4 DLAG
F5 ACT-DATA F6 PASSWORD
浙江金华自动化仪表有限公司
Zhejiang Jinhua Automatic Instrument CO.,Ltd
1
智能 Biaoteng JAXME600、500 系列 S4-25%- 1200c/h
9/2008-1.02 CN
目录
1、适用范围…………………………………………………………………………2 2、安全注意事项………………………………………………………………… .2 3、技术参数……………………………………………………………………… .2 4、菜单结构和基本参数设定………………………………………………………2 5、电气连接原理图…………………………………………………………………8 6、通讯接口…………………………………………………………………………9 7、故障与意外情况处理………………………………………………………… 11 8、隔爆产品注意事项…………………………………………………………… 13 9、JAXME600d 系列输出扭矩参数表………………………………………… 14~15
量程长度超过最小允许量程长度,屏幕上面一行将显示“□□□□”。到达希望的“0%位置”后,放开“↑”
或“↓”按钮,执行器停止转动。短按“MODE”按钮,屏幕出现“SAVE”闪烁,再短按“SAVE”按钮对
当前的“0%位置”进行保存。
设定量程结束后,退出菜单,此时可见屏幕显示当前量程。切换工作状态至“LOCAL”,按“↑”按
钮,则执行器开向运行,按“↓”按钮,则执行器关向运行。
在行程设定运行,按下“↓”或“↑”按钮的同时按下“MODE”按钮则为高速运行。
P2 的二级菜单-工作方式
F2.1 OPER_KEY 就 地 面 板 操 作 “ 点 动 ” (INCHMODE) 方 式 或 自 保 持(HOLDMODE) 连 续 运 行 INCHMODE
附图),避免执行机构运行时润滑室产生的压力造成的漏油。
取下油螺栓
换上换气阀
3、技术参数
1、模拟量控制; 4~20mA DC 电隔离,输入阻抗 500Ω;
2、开关量控制; 通过组态可实现开关量控制
3、阀位反馈信号; 4~20mA DC 输出 最大负载 500Ω电隔离
4、电源电压:
三相 380V AC 或 220V AC -15% +10 (定货时可选)
2.2 在本上安装电气时,应尊守安全方面的法律法规,对本电气部件进行拆卸工作之前,严禁带电拆
卸,必须先断电后再拆卸,在接线时应有明鲜的警告标指“严禁合闸”避免危险的发生。
2.3 为了不适宣的目的,硬的迫使执行机构动作,将会对阀门造成有害的,也是对操作人员不安全的。
2.4 在执行机构安装完毕后,执行机构的上端的油塞螺栓,换成随机附件“桔红”色的换气阀,换上(见
态
第一级菜单
图1
出厂默认值
3
附图
智能 Biaoteng JAXME600、500 系列 S4-25%- 1200c/h
9/2008-1.02 CN
工作状态 接通三相电后,拨动拨盘可切换“REMOTE”、“O/S”和“LOCAL”工作状态。 执行器处于“REMOTE”状态时,接受远程控制或者现场总线信号进行动作,此时本地操作可观察各
10、JAXME600d 系列产品安装尺寸基本参数表…………………………… .16-17 11、JAXME500d 系列输出推力参数表…………………………………………18~20
12.JAXME500d 系列产品安装尺寸基本参数表…………………………… 21-22 13、产品型号命名及附言………………………………………………………….23
40% 40% 40% 40%
TRAVEL-D 100%
TRAVEL-D 0%
第二级菜单
设置说明
图3
出厂默认值
用户可参考执行器的实际工作情况和与执行器配合的减速箱选型数据来调整开关向停机力矩和速
度。F1.6 和 F1.8 的量程限定值只有在对应的 F1.5 和 F1.7 停机方式选择为量程停机时才有效。
·本电动执行器结构坚固耐用,适用于操纵终端 ·控制元件,广泛应用于能源、化工、石油与天然气、水与污水处理等行业。 ·附加的齿轮传动装置(用于有限转角、直线运动)能与各种类型的阀门相互匹配使用。 ·智能型多转式执行器具有多种扩展功能,大大地简化了调试工作并可加快工程进度。 ·ME600 系列执行器可以通过使用方便的通讯接口或任选的总线接口进行通讯。 ·模块式结构,规格精简,降低用户备品备件库存量 ·辅助的速度控制能确保在微偏差调节中获得很高的定位精度
■ 主要部件
· 坚固的,采用油润滑的蜗轮传动机构 · 变频调速或无刷直流电机 · 微处理器控制的调速、恒力矩控制器 · 带 LCD 的现场操作面板 · ISO 5210 标准连接法兰 · 模拟量输入模块,或开关量输入模块
·■ 应现用场总线通讯模块
· 防爆型结构,符合 dⅡBT4 隔爆型
■ 技术特点
· DC 4~20mA 给定信号或开关量调节 · 变频调速、恒转矩、起动转矩大 · 在额定电压 +10%~-15%范围内正常工作 · 通过数字通讯或现场控制盘进行组态 · 能进行电子式速度和力矩设定 · 采用高技术传感技术,调试极其简单 · 广泛的监视与自诊断功能 · 防护等级 IP67 或 68 水下型
F2.2 DIG_INP 开 关 开 关 控 制 “ 点 动 ” (INCHMODE) 方 式 或 自 保 持(HOLDMODE) 连 续 运 行 INCHMODE
F1.2 TORQUE_C
F1.3 SPEED_O
F1.4 SPEED_C
F1 SETUP
F1.5 CUTOFF_O F1.6 LLMIT_O
F1.7 CUTOFF_C
F1.8 LLMIT_C
F1.9 ADJUST_O
F1.10 ADJUST_C
开 向 停 机 力 矩 10%步距 , 可 调 范 围 40%~ 100% 关 向 停 机 力 矩 10%步距 , 可 调 范 围 40%~ 100% 开 向速 度 步 距 5%步 , 可 调 范 围 40%~ 100% 关 向速 度 步 距 5%步 , 可 调 范 围 40%~ 100% TRAVEL-D 开 向 行 程 限 位 , 或 TORQUE-D 开 向 停 机 力 矩 设 置 开 向 行 程 限 位 设 置 值 , 步 距 1%, 可 设 范 围 55%~ 100% TRAVEL-D 关 向 行 程 限 位 , 或 TORQUE-D 开 向 停 机 力 矩 设 置 关 向 行程 限 位 设 置 值 , 步 距 1%, 可 设 范 围 0%~ 45% 开 向行 程 终 点 设 置 “ 满 位 ” 关 向行 程 终 点 设 置 “ 零 位 ”
11、电 子 辐 射; 按 GB/T17626.3-1998 电磁兼容试验标准
12、控制器死区; 0.5~10%可调
13、脉 冲 控 制; 最短 50mS
14、外 壳 喷 涂; 环氧搪瓷涂层 RAL9005 黑色,外露螺钉为不锈钢(放油螺塞镀铬) 15、外壳防护等级; IP67(IP68 增选项)储存及运输为 IP55
状态运行参数,但无法修改参数,也无法通过本地操作驱动执行器。 执行器处于“O/S”状态时,不接受任何驱动信号,但可通过本地操作观察各运行参数,此为出厂预
设状态。 执行器处于“LOCAL”状态时,可进行本地操作驱动执行器,并可进行产品运行参数修改。 在初始状态(显示“LOCAL”、“REMOTE”或者“O/S”)时,长按“MODE”按钮即可进入第一级菜单。
智能 Biaoteng JAXME600、500 系列
智能 Biaoteng
S4-25%- 1200c/h
JAXME600 系列、JAXME500 系列、JAX-DHZ500 系列
多转式变频智能电动执行机构
操作使用说明
9/2008-1.02 CN
JAXME500 直行程系列
JAXME600 角行程系列
2
智能 Biaoteng JAXME600、500 系列 S4-25%- 1200c/h
9/2008-1.02 CN
1. 本操作说明书适用范围