多丝切割机加工过程与钢丝振动
机械加工过程中机械振动的原因及对策分析
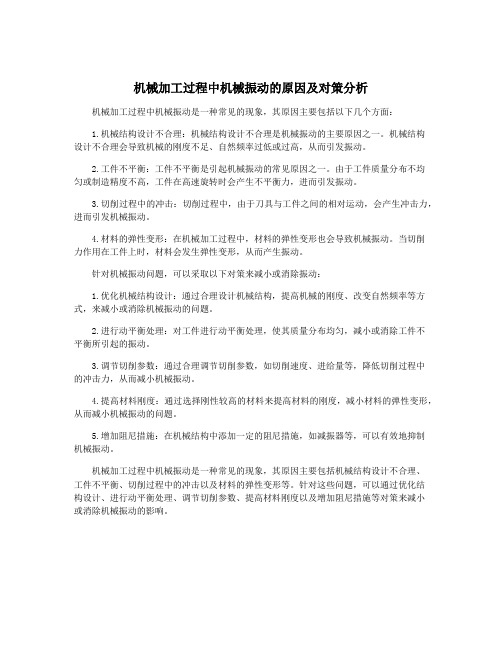
机械加工过程中机械振动的原因及对策分析机械加工过程中机械振动是一种常见的现象,其原因主要包括以下几个方面:1.机械结构设计不合理:机械结构设计不合理是机械振动的主要原因之一。
机械结构设计不合理会导致机械的刚度不足、自然频率过低或过高,从而引发振动。
2.工件不平衡:工件不平衡是引起机械振动的常见原因之一。
由于工件质量分布不均匀或制造精度不高,工件在高速旋转时会产生不平衡力,进而引发振动。
3.切削过程中的冲击:切削过程中,由于刀具与工件之间的相对运动,会产生冲击力,进而引发机械振动。
4.材料的弹性变形:在机械加工过程中,材料的弹性变形也会导致机械振动。
当切削力作用在工件上时,材料会发生弹性变形,从而产生振动。
针对机械振动问题,可以采取以下对策来减小或消除振动:1.优化机械结构设计:通过合理设计机械结构,提高机械的刚度、改变自然频率等方式,来减小或消除机械振动的问题。
2.进行动平衡处理:对工件进行动平衡处理,使其质量分布均匀,减小或消除工件不平衡所引起的振动。
3.调节切削参数:通过合理调节切削参数,如切削速度、进给量等,降低切削过程中的冲击力,从而减小机械振动。
4.提高材料刚度:通过选择刚性较高的材料来提高材料的刚度,减小材料的弹性变形,从而减小机械振动的问题。
5.增加阻尼措施:在机械结构中添加一定的阻尼措施,如减振器等,可以有效地抑制机械振动。
机械加工过程中机械振动是一种常见的现象,其原因主要包括机械结构设计不合理、工件不平衡、切削过程中的冲击以及材料的弹性变形等。
针对这些问题,可以通过优化结构设计、进行动平衡处理、调节切削参数、提高材料刚度以及增加阻尼措施等对策来减小或消除机械振动的影响。
机械加工过程中机械振动的原因及对策分析

机械加工过程中机械振动的原因及对策分析机械振动在机械加工过程中是一种常见的现象,它由多种原因引起。
机械振动不仅会影响加工精度和加工质量,还会对机床和工具设备造成损坏,因此需要采取相应的对策来减小机械振动。
机械振动的原因可以归结为以下几点:1. 切削力导致的机械振动:在机械加工过程中,切削力是产生振动的主要原因之一。
加工过程中的突然切削力、不平衡切削力以及刀具的不良使用等都会导致机械振动的产生。
2. 构件的材质和形状对机械振动的影响:构件的材质和形状也会对机械振动产生一定的影响。
如果构件的刚度不够,容易产生共振现象,进而引起机械振动。
3. 机床刚度不足:机床刚度不足也是机械振动的原因之一。
如果机床的刚度不够,加工过程中的力量无法得到有效的传递,会引起机械振动现象。
针对机械振动的原因,可以采取以下对策来减小机械振动:1. 优化刀具的设计和选择:合理选择刀具并进行刀具的定期检查和更换,以保证刀具的质量和使用寿命。
还可以根据具体的加工需求,优化刀具的设计,减小切削力的大小。
2. 提高机床的刚度:增加机床的刚度,可以有效地减小机床振动。
可以采取增加机床整体重量、加强机械结构的刚度,以及增加机床的支撑点等方法来提高机床的刚度。
3. 选用减振材料:在机床的结构中采用减振材料,如橡胶减振垫、弹簧减振装置等,可以有效地减小机械振动。
4. 控制切削参数:合理调整切削参数,如切削速度、进给量和切削深度等,可以降低切削力的大小,进而减小机械振动。
5. 加强工件固定:在加工过程中,合理固定工件,以减小工件的共振现象,从而减小机械振动。
机械振动是机械加工过程中常见的问题,但通过优化刀具的设计和选择、提高机床的刚度、选用减振材料、控制切削参数以及加强工件的固定等措施,可以有效地减小机械振动的发生,提高加工精度和加工质量。
机械加工过程中机械振动的原因及措施

机械加工过程中机械振动的原因及措施作者:王波涛来源:《科技信息·上旬刊》2017年第05期摘要:机械加工当中最为常见的现象之一就是机械振动,因为机械振动,导致机械加工生产效率降低,同时导致加工产品表面质量不符合标准,加速了机械工具的过渡消耗磨损和噪音污染等一系列问题的出现。
文中重点对机械加工过程中,机械振动产生的原因进行了分析,同时对怎样解决机械振动提出了对应的措施。
关键词:机械加工;机械振动;原因;措施引言:伴随着我国科学技术水平的不断提高,现代企业生产加工流程中广泛使用机械加工。
机械加工能够带来高效快捷精准的效果,减少劳动强度,将生产效率提高。
现实的机械加工当中,因为加工零件和刀具一直处在转动的状态下,经过长时间的转动,振动形成,导致零部件加工精准度无法保证,直接对机械加工质量有影响。
所以,要十分重视机械加工当中出现的振动现象,需要有关工作者深入分析机械加工当中出现的振动原因,利用对应的措施,保证降低机械振动。
一、机械振动的介绍作为一种特殊运动形式的振动,主要是物体在平衡位置进行的往复运动。
不论进行哪种机械加工生产,再加工过程中机械设备都会出现各种各样的振动。
因为振动的物体是机械结构,所以就叫做机械振动。
此种振动具备周期性特征,切割的流程中,加工机械设备当中,刀具切割工件出现的相对运动。
有很多人认为,切削用量低,就能够利用降低摩擦来减少机械振动。
这样导致机械加工基本工作无法得到保证,还会削弱刀具和设备耐用性,降低使用寿命,生成噪声。
二、机械加工过程中机械振动的原因2.1自由振动进行零部件加工生产过程中,机械因为自身原因,总是出现振动,就是所谓的自由振动问题,另外,导致自由振动的原因非常简单。
机械自由振动产生的主要原因就是在利用机械零部件生产加工流程中,因为存在一定的切削力,受到外力的作用,将导致振动出现,此外,可能进行零部件加工生产流程中,受到人为因素的影响,从而出现自由振动现象。
浅析机械加工过程中机械振动的成因及处理方法

浅析机械加工过程中机械振动的成因及处理方法一、机械振动的分类机械加工过程中,工艺系统常常会发生振动,即在工件和刀具的切削刃之间,除了名义上的切削运动外,还会出现一种周期性的相对运动。
产生振动时,工艺系统的正常切削过程便受到干扰和破坏,从而使零件加工表面出现振纹,降低了零件的加工精度和表面质量,频率低时产生波度,频率高时产生微观不平度。
强烈的振动会使切削过程无法进行,甚至造成刀具“崩刃”。
为此,常被迫降低切削用量,致使机床、刀具的工作性能得不到充分的发挥,限制了生产率的提高。
振动还影响刀具的耐用度和机床的寿命,发出噪声,恶化工作环境,影响工人健康。
振动按其产生的原因来分类有三种:自由振动、受迫振动和自激振动。
受迫振动和自激振动都是不能自然衰减而且危害较大的振动。
下面就这两种振动形式进行简单的分析。
二、机械加工中的受迫振动(一)受迫振动产生的原因机械加工中的受迫振功,是一种由工艺系统内部或外部周期交变的激振力(即振源)作用下引起的振动。
机械加工中引起工艺系统受迫振动的激振力,主要来自以下几方面1.机床上高速回转零件的不平衡机床上高速回转的零件较多,如电动机转子、带轮、主轴、卡盘和工件、磨床的砂轮等,由于不平衡而产生激振力F(即离心惯性力)。
2.机床传动系统中的误差机床传动系统中的齿轮,由于制造和装配误差而产生周期性的激振力。
此外,皮带接缝、轴承滚动体尺寸差和液压传动中油液脉动等各种因素均可能引起工艺系统受迫振动。
3.切削过程本身的不均匀性切削过程的间歇特性,如铣削、拉削及车削带有键槽的断续表面等,由于间歇切削而引起切削力的周期性变化,从而激起振动。
4.外部振源由邻近设备(如冲压设备、龙门刨等)工作时的强烈振动通过地基传来,使工艺系统产生相同(或整倍数)频率的受迫振动。
(二)减少受迫振动的途径受迫振动是由于外界周期性干扰力引起的,因此为了消除受迫振动,应先找出振源,然后采取适应的措施加以控制。
1.减小或消除振源的激振力对转速在600r/min以上的零件必须经过平衡,特别是高速旋转的零件,如砂轮,因其本身砂粒的分布不均匀和工作时表面磨损不均匀等原因,容易造成主轴的振动,因此对于新换的砂轮必须进行修整前和修整后的两次平衡。
钢丝振动的原理

钢丝振动的原理钢丝振动的原理是指钢丝在受到外部力量作用下发生的周期性振动现象。
钢丝是一种具有弹性的材料,当受到外力作用时,可以产生弹性形变,并在脱离外力作用后,恢复到原始形态。
这种弹性特性使得钢丝可以在受到外部扰动时产生振动。
钢丝振动的原理可以用简单的弹簧振子模型来解释。
当一根钢丝受到外力拉扯时,会产生张力,使得钢丝形成一定的弹性形变。
如果在这个状态下受到外部的扰动,比如捶打或者摆动,钢丝就会开始振动。
这是因为外部扰动改变了钢丝的原始平衡位置,使其产生了弹性能量,并且在外力作用下产生周期性的来回振动。
这种振动的周期与钢丝的弹性系数、质量和外力大小有关。
除了弹簧振子模型,钢丝振动的原理还可以通过波动理论来解释。
当钢丝受到外力作用时,会在重力和张力的作用下产生一定的波动,即机械波。
当外部力量作用消失后,波动会继续传播,并且在传播的过程中产生反射和干涉现象,最终形成周期性的振动。
这种振动的频率和波速与钢丝的材质、张力和外力的频率有关。
另外,钢丝振动的原理也可以从能量转化角度来解释。
当钢丝受到外部扰动时,外力对钢丝做功,使得钢丝产生了一定的动能。
而在外力消失后,钢丝会持续振动并逐渐失去能量,最终停止振动。
这是因为钢丝的动能被逐渐转化为热能和声能,并且在阻尼的作用下,振动逐渐衰减直至停止。
因此,钢丝振动的原理也可以通过能量守恒和能量转化来解释。
总的来说,钢丝振动的原理涉及到了弹性形变、波动理论和能量转化等多个方面。
钢丝受到外力作用后,产生了周期性的振动,其振动的频率、幅度和衰减速度与钢丝的物理特性和外力特性有关。
因此,通过对钢丝振动的原理进行综合分析和理解,可以更好地控制和利用钢丝振动的特性,从而应用于各种领域,如音乐乐器、工程结构和科学实验等。
多线切割中切割线振动作用研究

应用与研 究 ・
・
电 子 工 业 毫 用 设 备
■
在 本 文 中 我 们 主 要讨 论 了砂 浆 在 进 入 切 割 晶 锭 工 作 区域 后 的运 动 作 用 对 切 割 晶片 质 量 产 生 的 影 响 ,特 别 是 多线 切 割 机 应 用 较 细 切 割 线 时 砂 浆
对 切 割效 果 的影 响 。通 过 使 用 高 速相 机 记 录 下砂
5 nl 0m '
l5m ' 2 n l
、
■目衄
砂 浆
ቤተ መጻሕፍቲ ባይዱ
浆 在 切 割 线 上 的 粘 着 状 态 及 在 切 割 中 起 到 的 作 用 ,而 且 也 描述 出 切 割线 在 高速 往 复 中会 有 一 个 低 频 率 的 振 动 ,这 种 振 动 提 高 了切 割 线 在 携 带 砂
参数 。讨论 了切割 线在 运 动 中的 振 动效 果 以及 对切 割 产 生 的影 响 , 通过 试 验及 对 高速 摄 像机 拍
摄 照 片 的分析 . 出不 同砂 浆 携 带方 式极 其 在 工作 中的振 动会 直 接 影 响到 切割 出晶 片几 何参 数 得
的 结论 。
关键 词 : 多线切 割 : 线振 动 ; 砂浆 作 用
o wae . d t e p o e sn e h n s o mu t wi a b l t d e . f f r An r c s i g m c a im f h l - r s w e as s i d i e o u Ke wo d : u t wi a F e u n y v b a i n S u r c in y r s M l — r s w; r q e c i r t ; l ry a t s i e o o
机械加工中机械振动的原因解析与应对
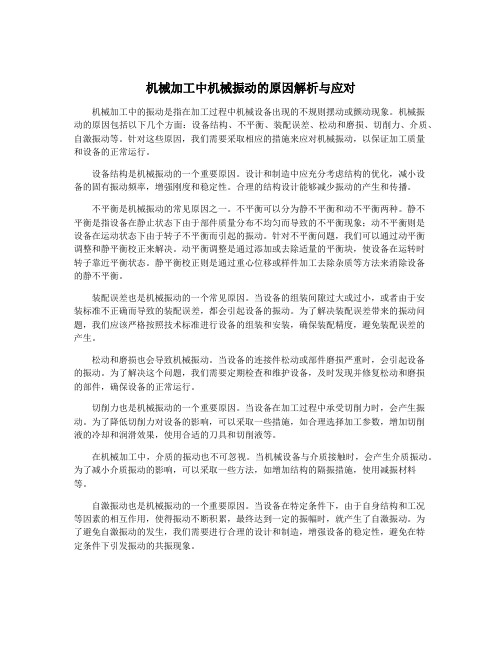
机械加工中机械振动的原因解析与应对机械加工中的振动是指在加工过程中机械设备出现的不规则摆动或颤动现象。
机械振动的原因包括以下几个方面:设备结构、不平衡、装配误差、松动和磨损、切削力、介质、自激振动等。
针对这些原因,我们需要采取相应的措施来应对机械振动,以保证加工质量和设备的正常运行。
设备结构是机械振动的一个重要原因。
设计和制造中应充分考虑结构的优化,减小设备的固有振动频率,增强刚度和稳定性。
合理的结构设计能够减少振动的产生和传播。
不平衡是机械振动的常见原因之一。
不平衡可以分为静不平衡和动不平衡两种。
静不平衡是指设备在静止状态下由于部件质量分布不均匀而导致的不平衡现象;动不平衡则是设备在运动状态下由于转子不平衡而引起的振动。
针对不平衡问题,我们可以通过动平衡调整和静平衡校正来解决。
动平衡调整是通过添加或去除适量的平衡块,使设备在运转时转子靠近平衡状态。
静平衡校正则是通过重心位移或样件加工去除杂质等方法来消除设备的静不平衡。
装配误差也是机械振动的一个常见原因。
当设备的组装间隙过大或过小,或者由于安装标准不正确而导致的装配误差,都会引起设备的振动。
为了解决装配误差带来的振动问题,我们应该严格按照技术标准进行设备的组装和安装,确保装配精度,避免装配误差的产生。
松动和磨损也会导致机械振动。
当设备的连接件松动或部件磨损严重时,会引起设备的振动。
为了解决这个问题,我们需要定期检查和维护设备,及时发现并修复松动和磨损的部件,确保设备的正常运行。
切削力也是机械振动的一个重要原因。
当设备在加工过程中承受切削力时,会产生振动。
为了降低切削力对设备的影响,可以采取一些措施,如合理选择加工参数,增加切削液的冷却和润滑效果,使用合适的刀具和切削液等。
在机械加工中,介质的振动也不可忽视。
当机械设备与介质接触时,会产生介质振动。
为了减小介质振动的影响,可以采取一些方法,如增加结构的隔振措施,使用减振材料等。
自激振动也是机械振动的一个重要原因。
机械加工过程中机械振动的原因及对策分析
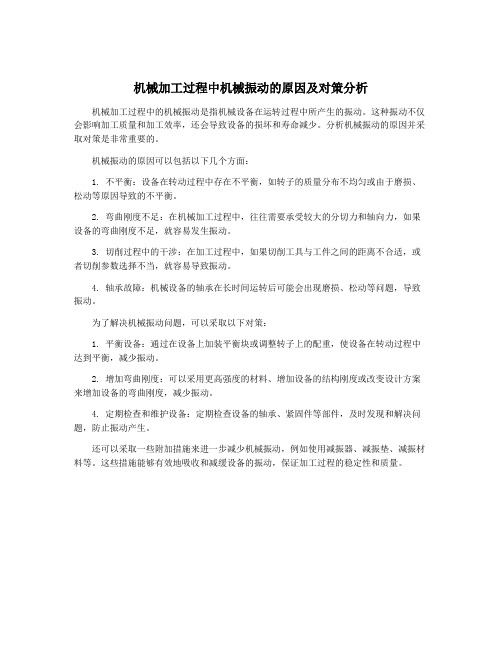
机械加工过程中机械振动的原因及对策分析
机械加工过程中的机械振动是指机械设备在运转过程中所产生的振动。
这种振动不仅会影响加工质量和加工效率,还会导致设备的损坏和寿命减少。
分析机械振动的原因并采取对策是非常重要的。
机械振动的原因可以包括以下几个方面:
1. 不平衡:设备在转动过程中存在不平衡,如转子的质量分布不均匀或由于磨损、松动等原因导致的不平衡。
2. 弯曲刚度不足:在机械加工过程中,往往需要承受较大的分切力和轴向力,如果设备的弯曲刚度不足,就容易发生振动。
3. 切削过程中的干涉:在加工过程中,如果切削工具与工件之间的距离不合适,或者切削参数选择不当,就容易导致振动。
4. 轴承故障:机械设备的轴承在长时间运转后可能会出现磨损、松动等问题,导致振动。
为了解决机械振动问题,可以采取以下对策:
1. 平衡设备:通过在设备上加装平衡块或调整转子上的配重,使设备在转动过程中达到平衡,减少振动。
2. 增加弯曲刚度:可以采用更高强度的材料、增加设备的结构刚度或改变设计方案来增加设备的弯曲刚度,减少振动。
4. 定期检查和维护设备:定期检查设备的轴承、紧固件等部件,及时发现和解决问题,防止振动产生。
还可以采取一些附加措施来进一步减少机械振动,例如使用减振器、减振垫、减振材料等。
这些措施能够有效地吸收和减缓设备的振动,保证加工过程的稳定性和质量。
机械加工过程中机械振动的原因及对策分析

机械加工过程中机械振动的原因及对策分析机械加工过程中,机械振动是一个普遍存在的问题,因为它不仅会导致精度降低,还会加速机器零件的磨损,甚至损坏设备。
因此,对于机械振动问题的解决非常关键。
本文就对机械振动的原因及对策进行分析。
一、机械振动的原因1、切削过程产生的振动切削过程中弯刀和工件之间的相互作用会产生振动。
机械加工时,刀具切削力的幅度和方向会发生变化,从而在机床或工件上形成振动。
2、结构共振机床和工件都是复杂的机械结构,当机床和工件的自然频率与加工中形成的激振频率相同时,就会产生结构共振现象。
3、加工质量问题如果切削刀具使用时间过长,切削的表面质量不佳,磨损过大等问题,就会导致加工过程中的振动。
4、材料变形在对某些材料进行加工时,因材料本身特性的影响,能量的传递不完善,自然会产生振动。
1、切削后处理切削后,工件表面存在不平整现象,如果直接进行下一步加工,就会产生新一轮的振动。
因此,在切削后应采取必要的光洁磨削或光洁加工处理,以减轻振动产生的影响。
2、提高刀具和夹具的刚性和刚度刀具和夹具的刚性和刚度直接影响到机械加工的质量和效率。
因此,加强刀具和夹具的刚度、抵抗自由度,可以减少振动的产生,并提高精度。
3、控制机床的机械系统误差机床的机械系统误差对机械振动产生了很大的影响。
因此,通过对机床的检修和调整,及时发现和排除机械系统误差,可以降低机械振动产生的风险。
4、选择适当的加工策略不同工件的加工策略会对机械振动产生不同的影响。
正确选择加工策略,调整加工参数,减少工件变形现象,避免产生振动。
三、总结在机械加工过程中,振动是一种常见的问题。
要想避免机械振动,就要在生产过程中采取正确的措施,改进机床、刀具等设备的刚性和刚度,控制机械系统误差,选择适当的加工策略等。
这样,就能高效地完成加工,保证加工精度和效率,进而提高生产效益。
机械加工过程中机械振动的成因及解决措施吴岩,王昌,王敬凡

机械加工过程中机械振动的成因及解决措施吴岩,王昌,王敬凡发布时间:2021-09-20T10:15:50.566Z 来源:《教学与研究》2021年9月中作者:吴岩,王昌,王敬凡[导读] 在机械加工过程中,经常会出现机械振动的情况,影响到加工效率和质量,而且有可能导致切削刀具受损,引发噪音污染。
因此,找出机械加工过程中引发机械振动的原因,并提出对应的控制措施已经成为机械加工行业需要解决的关键问题。
鉴于这种情况,文章首先细致分析了当今社会机械加工过程中机械振动出现的原因,然后后提出了几点解决建议,希望可以为机械加工生产的顺利展开起到一定参考作用。
辽宁兴启电工材料有限责任公司吴岩,王昌,王敬凡辽宁省辽阳市 111000摘要:在机械加工过程中,经常会出现机械振动的情况,影响到加工效率和质量,而且有可能导致切削刀具受损,引发噪音污染。
因此,找出机械加工过程中引发机械振动的原因,并提出对应的控制措施已经成为机械加工行业需要解决的关键问题。
鉴于这种情况,文章首先细致分析了当今社会机械加工过程中机械振动出现的原因,然后后提出了几点解决建议,希望可以为机械加工生产的顺利展开起到一定参考作用。
关键词:机械加工;机械振动;成因;解决措施在现实生活当中,会对机械加工效率和质量造成影响的因素非常多,机械振动就是其中之一,而且是比较常见的因素,常见的机械振动主要有自由振动、自激振动与强迫振动三种。
同时,机械振动不仅仅会导致加工效率与质量下滑,还会使设备使用寿命下降,造成生产成本增加。
所以,在机械生产加工过程中,相关工作人员应该准确把握自由振动、自激振动与强迫振动发生的原因,并找出针对性解决策略,这样才可以保证机械生产安全高效展开,提升机械加工质量,取得更加令人满意的加工成果。
一、机械加工过程中机械振动的成因分析(一)自由振动成因在机械生产加工过程中,出现自由振动的原因主要有两种。
首先,如果刀具反复运动速度过快,会致使切削力增加,进而引发自由振动;其次,如果在加工过程中,设备因为受外界环境影响出现冲击力,这也会给机械加工设备造成影响,使加工刀具出现自由振动,导致加工效率和质量下降。
多丝切割机加工过程与钢丝振动

加 工谩 差 、 研磨 颗 粒 的撞 击 、主 轴 瞬 时 速 度 差 等 。 昕 以振
崆稿 日期 :2 0 —0 — 1 06 2 3
维普资讯
机 床
2 O a 金 属 丝 直 径 D = .6 m , 金 属 丝 线 密 度 p: O GP , O1r a
0 0 1 1k/ . 0 6 5 g m ,作 用 于 金 属 丝 的 张 力 T 2 N, 因 而 计 算 0 =5 可 得 , 金 属 丝 的 纵 向 波 速 远 远 大 于 横 向 波 速 。 基 于 此 情
3加 工 区域 受 力 分 析
圈 1 多丝切 割示意 圈
.
很 多 涉 及 恒 张 力 控 制 系 统 的 文 献 : 提 出 _很 多 张 ,都 r
5金属 丝 .
加 工辊
2研磨剂 疃嘴
3硅碇
4工作台
控 制 的 方 法 和 建 议 ,但 是 究 其结 果 来 说 .其 只能 控 制 如
— —
金属丝的加速度 ;
L 图2
一
一
. 一
—
—
金 属 丝 的平 移 速 度 ;
张 力控 制 原 理 图
叮 —— 硅 片 对 金 属 丝 的 正 压 力 ;
一
金 属 丝所 受 张 力 。
从 以上 方 程 可 以看 出 。在 加 工 过 程 中 ,金 属 丝 的横 向
位 移 的 大 小 、频 率 与 金 属 丝 的 密 度 、平 移 速 度 、加 速 度 、 所 受 张 力 以及 加 工 过 程 中 工件 对 金 属 丝 的作 用 力 有 关 。所
机械加工过程中机械振动的成因及解决措施_0

机械加工过程中机械振动的成因及解决措施机械加工在日常生活中应用较为广泛,并且人们对机械加工出的工件质量要求越来越高,而在机械加工工程中,振动现象将对加工件质量造成不良影响。
本文围绕机械加工过程中产生振动的原因及其特征、降低机械振动的措施两个方面展开讨论,从而降低机械加工过程中的振动现象,减少加工过程的噪音影响,并能保证加工件的质量。
标签:机械加工;自由振动;强迫振动0 前言随着社会的发展,对加工件的质量要求越来越高,而日常生活中通常应用到的工具都是有机械加工来实现的。
在机械加工过程中,加工件和刀具之间会发生摩擦,因此不可避免的发生振动现象,将降低了加工件的精准度,从而不利于加工件在生活中的实际应用。
因此应该加强对机械加工过程中振动产生的原因进行研究,并采取相应的解决措施。
1 机械加工过程中产生振动的原因及其特征1.1 自由振动产生的原因在机械加工过程中,自由振动是最简单也是最容易产生的振动,引起自由振动的原因主要包括以下几个方面:第一,在机械加工的过程中,刀具的往复运动会施加给加工件切削力的作用,而在切削力发生改变时,机械加工过程中产生振动现象;第二,在进行机械加工时,机械设备可能受到外界力的作用,从而对机械设备造成一定的冲击,引起自由振动。
机械加工过程中的自由振动现象的发生一般是由于力的作用,而在自由振动的过程中不存在外力的增加,因此自由振动现象会由于阻力的存在而逐渐减弱。
由此可见,自由振动对机械加工过程造成的影响较小并且容易消除,但是自由振动是引起自激振动的一个原因,在一定的条件下机械加工过程中会出现自激振动现象,对加工件的质量有不利影响[1]。
1.2 强迫振动产生的原因产生强迫振动的原因包括以下两方面:第一,由于离心惯性力的影响。
在机械加工过程中,转轴、皮带轮以及一些回转工件在加工过程中会由于机械加工速率较快,导致这些部件出现不平衡的现象,从而将产生离心力,而离心力的产生是造成强迫振动发生的重要原因,振动的频率与受到向心力作用的工件的转速大致相同;第二,如果机械设备本身存在缺陷,会导致强迫振动现象的发生,主要与机械设备中的旋转零件有关,当旋转零件出现尺寸误差的时候,将导致各零件之间结合不紧密,从而零件在加工过程中失去平衡,受到离心力的作用,进而引起强迫振动。
机械加工过程中机械振动的原因及对策分析
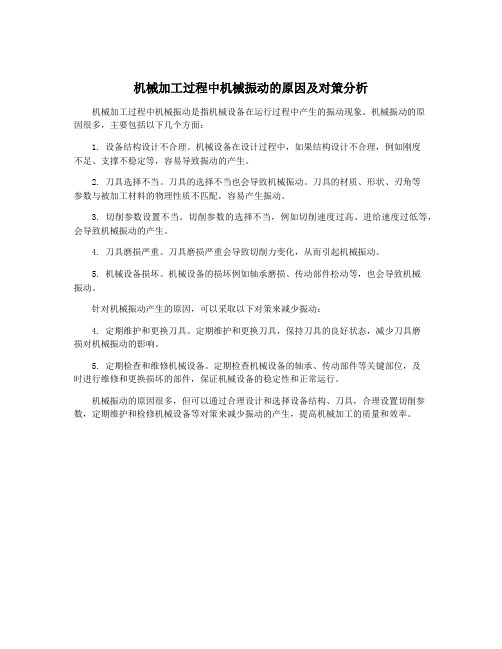
机械加工过程中机械振动的原因及对策分析
机械加工过程中机械振动是指机械设备在运行过程中产生的振动现象。
机械振动的原
因很多,主要包括以下几个方面:
1. 设备结构设计不合理。
机械设备在设计过程中,如果结构设计不合理,例如刚度
不足、支撑不稳定等,容易导致振动的产生。
2. 刀具选择不当。
刀具的选择不当也会导致机械振动。
刀具的材质、形状、刃角等
参数与被加工材料的物理性质不匹配,容易产生振动。
3. 切削参数设置不当。
切削参数的选择不当,例如切削速度过高、进给速度过低等,会导致机械振动的产生。
4. 刀具磨损严重。
刀具磨损严重会导致切削力变化,从而引起机械振动。
5. 机械设备损坏。
机械设备的损坏例如轴承磨损、传动部件松动等,也会导致机械
振动。
针对机械振动产生的原因,可以采取以下对策来减少振动:
4. 定期维护和更换刀具。
定期维护和更换刀具,保持刀具的良好状态,减少刀具磨
损对机械振动的影响。
5. 定期检查和维修机械设备。
定期检查机械设备的轴承、传动部件等关键部位,及
时进行维修和更换损坏的部件,保证机械设备的稳定性和正常运行。
机械振动的原因很多,但可以通过合理设计和选择设备结构、刀具,合理设置切削参数,定期维护和检修机械设备等对策来减少振动的产生,提高机械加工的质量和效率。
机械加工过程中机械振动的原因及对策分析
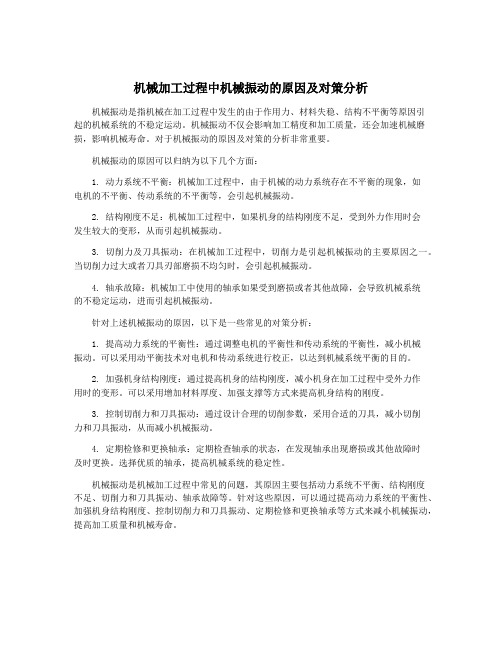
机械加工过程中机械振动的原因及对策分析机械振动是指机械在加工过程中发生的由于作用力、材料失稳、结构不平衡等原因引起的机械系统的不稳定运动。
机械振动不仅会影响加工精度和加工质量,还会加速机械磨损,影响机械寿命。
对于机械振动的原因及对策的分析非常重要。
机械振动的原因可以归纳为以下几个方面:1. 动力系统不平衡:机械加工过程中,由于机械的动力系统存在不平衡的现象,如电机的不平衡、传动系统的不平衡等,会引起机械振动。
2. 结构刚度不足:机械加工过程中,如果机身的结构刚度不足,受到外力作用时会发生较大的变形,从而引起机械振动。
3. 切削力及刀具振动:在机械加工过程中,切削力是引起机械振动的主要原因之一。
当切削力过大或者刀具刃部磨损不均匀时,会引起机械振动。
4. 轴承故障:机械加工中使用的轴承如果受到磨损或者其他故障,会导致机械系统的不稳定运动,进而引起机械振动。
针对上述机械振动的原因,以下是一些常见的对策分析:1. 提高动力系统的平衡性:通过调整电机的平衡性和传动系统的平衡性,减小机械振动。
可以采用动平衡技术对电机和传动系统进行校正,以达到机械系统平衡的目的。
2. 加强机身结构刚度:通过提高机身的结构刚度,减小机身在加工过程中受外力作用时的变形。
可以采用增加材料厚度、加强支撑等方式来提高机身结构的刚度。
3. 控制切削力和刀具振动:通过设计合理的切削参数,采用合适的刀具,减小切削力和刀具振动,从而减小机械振动。
4. 定期检修和更换轴承:定期检查轴承的状态,在发现轴承出现磨损或其他故障时及时更换。
选择优质的轴承,提高机械系统的稳定性。
机械振动是机械加工过程中常见的问题,其原因主要包括动力系统不平衡、结构刚度不足、切削力和刀具振动、轴承故障等。
针对这些原因,可以通过提高动力系统的平衡性、加强机身结构刚度、控制切削力和刀具振动、定期检修和更换轴承等方式来减小机械振动,提高加工质量和机械寿命。
机械加工过程中机械振动的成因及解决措施_1

机械加工过程中机械振动的成因及解决措施随着我国经济发展速度的不断加快,加工生产的需求量在不断增多,这对机械加工的要求也就逐渐提高。
本文将从机械设备加工的过程中产生具体的机械振动出发,根据其形成的原因对解决的措施进行合理思考,从而为我国机械行业发展提供有力参考。
标签:机械加工;机械振动;成因;解决措施0 引言经济生产的过程中离不开各种原料和设备,而且所有的过程都需要进行加工,随着我国机械加工的先进程度不断提高,效率得到了保证,经济效益也逐渐提高,为其他领域发展奠定了基础。
但是我们不能忽视当前机械在加工的过程中还有一定的问题,尤其是产生的振动,这对生产的产品和加工的机械设备都有不利的影响,而且还会造成严重的声音污染,不符合当代社会对加工行业的要求,而且造成设备的过早损坏也浪费了资源,所以国家和相关部门应该重点研究解决措施,这需要先明确产生振动的原因。
1 机械在加工的过程中产生振动的具体概括机械设备需要连电,那么从物理学科的内容来看,在运转的过程中必然会产生一定的振动,但是当前我国的机械设备在总体上还比较落后,所以产生的振动幅度过大,综合分析有两个具体的表现。
第一,被迫的振动,这主要就是在一定的时间内,机械的某一个零部件在运转的过程中造成其他零部件的振动,从而导致设备所在的区域振动,而且只要机械停止加工的操作,振动也会停止,但是会造成设备零部件的磨损,尤其是机床;第二,自激的振动,这主要就是在设备运行的过程中,由于自身整体产生的振动导致本身一直处于振动的环境中,不受外界的干扰,而且如果机械设备自身的功能性差,那么振动的幅度会增大。
2 机械设备加工的过程中产生振动的原因探究2.1 被迫的振动产生的原因机械加工的过程中,产生被迫的振动主要有以下三点主要原因:第一,加工的机床没有在水平的平面上,那么发生了偏移,所有零部件在运转的过程也就不在水平线上,产生的力过大,造成振动;第二,机械设备本身比较落后,或者运转速度快、频率高的零件破损或者性能差,那么在反复运转的过程中,会产生严重的振动,导致被迫的振动,如零件与设备接触不良,那么在运转的过程中偏移的空间大,产生被迫的振动;第三,加工过程中的切、片和削的过程中原料受力不平均,往往也会造成强迫的振动,而且设备所处的环境不适宜也会造成强迫的振动,最普遍的就是地面不平,而且是由于地基不稳固造成的,这样的情况下会造成振动,那么地面上的物品自然会产生被迫的振动[1]。
机械加工过程中机械振动的成因及解决措施

机械加工过程中机械振动的成因及解决措施摘要:机械振动对机械加工质量有很大的影响,因此在进行机械加工时,必须采取有效的控制措施,减少机械振动。
本文介绍了机械加工过程中产生振动的原因及特点,以其能采取更有效的方法解决机械振动问题,以更好地推动机械加工工业的发展。
关键词:机械加工;机械振动;成因;解决措施引言:在传统机械加工中,振动现象频繁发生,严重影响了加工精准度和精细度。
机械加工中的振动会使加工刀具在加工的过程中出现位置偏移,从而使加工产品出现瑕疵,影响了加工产品的质量。
同时,机械振动也会引起刀具磨损,降低刀具使用寿命,并影响整个机床系统,使得加工系统在振动作用下难以正常工作。
在机械加工过程中,机械振动现象往往来自于机械设备使用不当,这使得机械技术人员的设备操作无法满足相应的规范特征,使得机械振动现象严重影响了机械加工。
在进行机械加工时,应提高操作规范,有效地改善机械振动现象。
1在机械加工时发生振动的原因和对应特点1.1 自由振动在进行机械加工时,经常会出现零件自由振动的现象。
在机械加工零件时,经常会引起操作波动,从而引起系统自振。
同时,自由振动现象的产生也受到外部各种力因素的影响,外力通过作用于振动力,使得振动力以自由振动的形式逐渐减弱,从而保证了机械振动过程中机器的正常运行,使得机械加工自由振动作业能得到更好的发展。
自由振动发生后,由于缺少外力补充,经过一定的时间后,自由振动会自动消失。
因此,自由振动对加工过程的整体影响很小。
但施工人员在进行机械加工时,也应注意控制自由振动,防止产生自激振动。
1.2 强迫振动在进行机械加工时,往往受外界干扰力的作用而产生强迫振动,所以在实施强制振动消振时,必须采取一定的技术手段,以消除受迫振动。
因为机械系统本身并不影响干扰力的产生,所以通常情况下,强迫振动与加工本身并没有太大的关系,需要相关人员采取有效的措施来消除外部扰动力。
其次,在进行干扰力消减时,需研究强迫振动频率,以确定外扰力周期,使机械振动产生较大幅值。
切割过程中是否会产生振动?

切割过程中是否会产生振动?导言:在工业生产领域中,切割是一项常见且重要的工艺过程。
然而,切割过程中是否会产生振动一直以来都是人们关注的问题。
本文将从多个角度探讨这一问题,并介绍振动对切割过程的影响。
一、切割过程中的振动现象切割过程中的振动是由多种因素共同作用引起的。
首先,切割设备自身的振动是主要因素之一。
例如,切割刀具在高速旋转时,由于不均匀磨损或者失衡等原因,会产生振动。
此外,切割材料的性质也会影响振动的产生,如硬度、密度等。
最后,切割操作者的技术水平以及设备稳定性也会直接影响振动的程度。
1.1 切割设备自身振动切割设备自身振动是导致切割过程中振动的重要原因之一。
在高速旋转的切割过程中,切割刀具的不均匀磨损或失衡会导致振动的产生。
这种振动不仅会影响切割效果,还会对切割设备的寿命和运行稳定性造成一定的影响。
1.2 切割材料性质对振动的影响切割材料的硬度、密度等性质也会对振动产生影响。
一般来说,较硬、较密的材料更容易产生振动。
这是因为在切割过程中,硬、密的材料对切割刀具的阻力更大,切割切面质量更差,从而引发了更强的振动。
1.3 操作者技术水平和设备稳定性切割操作者的技术水平以及设备的稳定性也会直接影响振动的程度。
技术熟练的操作者能够更好地控制切割过程,减少振动的发生。
而设备的稳定性则决定了切割过程中的振动程度。
如果设备本身不稳定,那么振动的产生将更为严重。
二、振动对切割过程的影响振动对切割过程有着重要的影响,主要表现在以下几个方面。
2.1 切割效果振动会直接影响切割效果。
由于振动的存在,切割刀具与材料接触的时间和力度不均匀,导致切割切面不平整、毛刺严重等问题。
从而影响切割质量。
2.2 设备寿命振动会加速切割设备的磨损,缩短设备的寿命。
特别是切割刀具,由于不均匀振动引起的失衡,会加速切割刀具的磨损,降低切割效率,增加维修和更换的成本。
2.3 操作者健康安全振动也对操作者的健康安全产生潜在影响。
长期接触振动环境可能导致工人出现手臂震颤、麻木等问题,严重的甚至会引发相关疾病,如尘肺病等。
机械加工过程中机械振动的成因及解决措施探讨
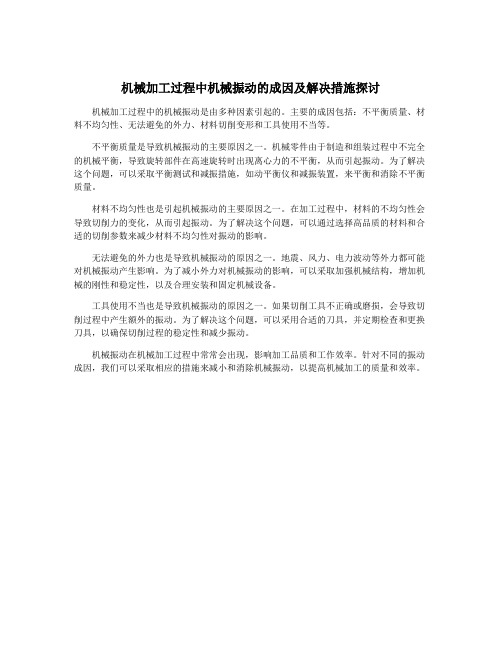
机械加工过程中机械振动的成因及解决措施探讨
机械加工过程中的机械振动是由多种因素引起的。
主要的成因包括:不平衡质量、材料不均匀性、无法避免的外力、材料切削变形和工具使用不当等。
不平衡质量是导致机械振动的主要原因之一。
机械零件由于制造和组装过程中不完全的机械平衡,导致旋转部件在高速旋转时出现离心力的不平衡,从而引起振动。
为了解决这个问题,可以采取平衡测试和减振措施,如动平衡仪和减振装置,来平衡和消除不平衡质量。
材料不均匀性也是引起机械振动的主要原因之一。
在加工过程中,材料的不均匀性会导致切削力的变化,从而引起振动。
为了解决这个问题,可以通过选择高品质的材料和合适的切削参数来减少材料不均匀性对振动的影响。
无法避免的外力也是导致机械振动的原因之一。
地震、风力、电力波动等外力都可能对机械振动产生影响。
为了减小外力对机械振动的影响,可以采取加强机械结构,增加机械的刚性和稳定性,以及合理安装和固定机械设备。
工具使用不当也是导致机械振动的原因之一。
如果切削工具不正确或磨损,会导致切削过程中产生额外的振动。
为了解决这个问题,可以采用合适的刀具,并定期检查和更换刀具,以确保切削过程的稳定性和减少振动。
机械振动在机械加工过程中常常会出现,影响加工品质和工作效率。
针对不同的振动成因,我们可以采取相应的措施来减小和消除机械振动,以提高机械加工的质量和效率。
机械加工过程中机械振动的成因及解决措施 李拓宇

首先,在机械加工进程中,道具反复运动会增加加工件切削力效果,在其出现转变时,机械加工进程中出现振动情况。其次,在实施机械加工时,相关设施被外力所左右,进而为其带来不小冲击,导致自由振动。机械加工进程中自由振动情况的出现通常是因为力效果,但在自由振动进程中并未增强外力,所以这一情况会因为阻力出现而渐渐削弱。不难发现,自由振动为机械加工进程制造的干扰不易去除,但其确是引发自激振动的一个核心因素,在相应条件中加工进程会发生自激振动情况,严重影响加工件品质。
结束语
通过前面的分析和讨论,我们可以得出结论,在加工过程中产生机械振动主要有两种方式。受迫振动和自激振动,机械振动对于机器质量的影响是十分巨大的,他可能影响到设备的损耗程度甚至说产品的质量以及生产速度和生产效率等等,这就要求我们及时找出原因,采取一系列措施解决问题。
参考文献
[1]王平.机械加工过程中机械振动的成因及解决措施[J].南方农机.2018(20).
3.1.3降低激振力
对于激振力出现原因来说,是因为机械加工进程中出现不均衡情况导致的。降低激振力的重中之重,是要杜绝体系中不均衡情况。所以,要在体系中装置相应自主均衡装备,使用动态或者静态均衡手段。另外,为提升传动体系可靠性,必须要确保设施质量且提升装置精细度。并且,相应技术人员在机械加工开始前与实施进程中要对元件展开均衡协调,这同样是降低激振力的良好措施。
2.3自激振动出现成因
这一情况出现频率较多而且是一种十分猛烈的振动。引发自激振动出现的因素有很多。比如:加工材质硬度散布不均衡,加工余量转变等要素导致体系振动,而在此基础上还会致使道具和加工件间地点发生迁移,进而形成切削力,出现自激振动。
3机械加工过程中机械振动的解决措施
3.1强迫Leabharlann 动控制措施机械体系出现强迫振动主要在于有着连续的外力影响。预防强迫振动,要综合常见振源、振动展现规律等等率先明确振源类别。此种振动振源普遍源于外部,因此可利用环境实验、空转实验、现场拾振等形式展开判断。对于现场拾振来讲,其是运用力、速度传感器等搜集已有条件中机械加工进程出现的振动讯号展开频谱剖析,依据剖析结果明确具体振动频次。环境实验则是采用已经确定体系外部环境里出现的振源,选在停机情况下对振动讯号展开搜集与剖析,从而挖掘影响源频率成分且清楚其由来。对于空转实验来说,其是依据加工需求的运动指数运作没有加工件的机械设施展开振动讯号搜集和剖析,且和具体加工进程中频谱图展开比较。确定出现强迫振动振源以后,可使用下列手段:
机械加工过程中机械振动的成因及解决措施

机械加工过程中机械振动的成因及解决措施发布时间:2022-06-08T10:31:40.676Z 来源:《福光技术》2022年12期作者:梁晋宝张超盟吉秀平[导读] 在技术和工艺发展的过程中,原料和设备开展高精度的加工是重要的基础。
在传统的机械加工和数字化加工中,工件和刀具之间需要进行往复运动,系统通常会出现振动问题。
山西汾西重工有限责任公司山西太原 030027摘要:在技术和工艺发展的过程中,原料和设备开展高精度的加工是重要的基础。
在传统的机械加工和数字化加工中,工件和刀具之间需要进行往复运动,系统通常会出现振动问题。
振动的类型和程度不同,对机械加工进度有着不同的影响。
随着车间生产对机械加工精度要求的提高,降低机械加工环节中的振动现象,能够有效提高机械加工精度。
通过分析机械加工振动的原因,采取科学合理的规避和消除措施,有效提高机械生产的效率和质量。
本文就此展开了论述,以供参阅。
关键词:机械加工;机械振动;成因;解决措施引言随着公司新产品的不断研发制造,数控技术在机械生产过程中得到了非常广泛的应用,大大提高了加工效率,使公司的发展提供了便利的条件。
然而机械加工过程中机械振动的问题需要解决,因为机械振动频率会造成加工产品的精度和效率及加工成本。
因此针对机械加工中的振动现象必须引起足够的重视,提高产品加工的精度,减少机械加工过程中机械的振动频率是机械加工作业需要解决的主要问题之一。
1机械加工中的机械振动成因 1.1机械加工中的自由振动成因其一,机械加工中,机械设备上的刀具的反复运动,使得加工件增加了切削力效果,当切削力发生转变,就会产生振动。
其二,机械加工的过程中,受到外力的作用有冲击力产生,就会产生自由振动。
机械加工中自由振动是不可避免的,主要是由于力的作用下产生的。
但是,如果自由振动中没有增强外力,就说明有阻力存在,使得振动逐渐削弱。
由于各种外在因素干扰导致的自由振动是不容易被消除的。
因此,找到导致自由振动的主要因素,就需要采取措施解决,否则会对加工件品质造成影响。
- 1、下载文档前请自行甄别文档内容的完整性,平台不提供额外的编辑、内容补充、找答案等附加服务。
- 2、"仅部分预览"的文档,不可在线预览部分如存在完整性等问题,可反馈申请退款(可完整预览的文档不适用该条件!)。
- 3、如文档侵犯您的权益,请联系客服反馈,我们会尽快为您处理(人工客服工作时间:9:00-18:30)。
收稿日期: !""# — "! — 3$
5"
机电工程技术 !""# 年第 $% 卷第 # 期
机床设 备
!""789 , 金 属 丝 直 径 3 3",+#:: , 金 属 丝 线 密 度 ! 3 ","""+#+%;< 6 :$, 作 用 于 金 属 丝 的 张 力 ! 3!%& , 因 而 计 算
机 床设备
机电工程技术 !""# 年第 $% 卷第 # 期
多丝切割机加工过程与钢丝振动
钱宏峰,林财兴,赵懿峰
(上海大学机械工程与自动化学院, 上海
!"""&! )
摘要:本文从振动对多丝切割机切割硅片的质量影响出发,对加工区域内的受力进行了一定的分析,同时基于对系统的分析,采 用 ’()*+,-. 原则进行系统建模,并且利用有限元方法对系统求解,得出了不同系统参数对系统固有特性的影响。并提出了系统参 数的一般设置,达到了预期的效果。 关键词:振动;张力;有限元 中图分类号: /0##1 文献标识码: 2 文章编号: 3""14151! 6!""#7 "#4""5"4"$
可得,金属丝的纵向波速远远大于横向波速。基于此情 况,可以认为该金属丝的横向运动处于一个准静态情况。 根据 (9:=>?@: 原则,并忽略系统的纵向振动,得到横 向振动运动方程:
7 4582!) 458*2) !4588) A!4588A, 3" ! (4562)
式中: —— 4—金属丝的加速度; —— 9 —金属丝的平移速度;
参考文献: [* ]王 琮 + 半 导 体 材 料 加 工 设 备 的 新 秀 —多 —— 线 切 割 机 [,] + 电 子工业专用设备, !""- , (- ) : #$.#%+ [! ]吴明明,周 兆 忠 , 巫 少 龙 + 单 晶 硅 片 的 制 造 技 术 [,] + 新 技 术新工艺, !""- , (% ) : /.*"+ [ $ ] 01 2345 645+ 789:;<:; .8)9:= >:594?5 @::=8)&A &?5>;?B C4>3 [- ] T:5F U4)DE)?B? , V1@>1F G45)5+ W;4&>4?5 45=1&:= >;)59<:;9: <4X 图# (& ) !’!%( 不同张力时金属丝中间点的振动图形
(8 ) !’!"(
% 结论
从以上分析可知, 由 于 现 有 的 张 力 控 制 系 统 只 能 对 加 工区域外围进行一定的张力调 节 , 而 不 能 对 加 工 区 域 进 行 实时调整。所以为了避免加工 过 程 中 由 于 研 磨 颗 粒 等 的 激 励而引起的共振现象的发生,张力应尽可能设为较高值。 一 般 为 !%( 左 右 为 宜 , 通 过 试 验 在 样 机 上 取 得 了 较 好 的 效果。
-+
机 床设备
机电工程技术 !""# 年第 $% 卷第 # 期
时,由于研磨颗粒的增多, 其 对 金 属 丝 的 作 用 也 越 来 越 频 繁,当达到其固有频率时候 , 振 幅 将 明 显 变 大 。 从 表 ! 中 可以看出,金属丝的固有频 率 随 着 张 力 的 增 大 而 增 大 。 与 表 * 比较,我们可以很明显地看出, 张 力 ! 对 固 有 频 率 的 影响程度明显大于速度。 另外,从图 % 可知,固频随 ! 的 变 化 率 先 大 后 小 。 由 上面分析可知,张力 ! 随 " 有类似周期变化,故一定的 !!
3 引言
多丝切割
[3]
动不可避免地存在于加工区 域 中 , 并 且 从 多 方 面 影 响 着 加 是一种通过金属丝的高速运动把磨料带 工质量。 、翘曲度 ( 3 ) 振 动 会 影 响 硅 片 的 弯 曲 度 ( 89:) 、 平 行 度 ( /2<=; ) 、 总 厚 度 公 差 ( //> ) 、切口 ( :2;<) 切割损耗、表面损伤层厚度、晶片表面粗糙度等; (! )由于振动的存 在 , 切 割 槽 加 宽 影 响 到 单 位 长 度 硅 锭硅片的产出量 (?(@AB C D) ) ,单位长度里所有硅片总的厚 度 ( D) C D) ) 及 单 位 质 量 材 料 加 工 出 来 的 所 有 硅 片 的 总 的 ; 表面积 ()! C EF ) ($ )由于振动的作 用 , 使 切 削 液 的 中 研 磨 颗 粒 进 一 步 均匀分散,悬浮性能提高, 不 发 生 凝 结 , 同 时 使 其 在 金 属 丝上的分布不同,也导致了加工效率等的问题; (5 )由于金属丝的 振 动 , 使 研 磨 液 更 加 容 易 进 入 待 加 工区域,切削正压力增大,进一步提高了加工效率。
) (: 6 B)
频率 (())
" ---,-
% ---,+
+" --$,#
+% --!,/
表!
张力与固有频率的关系
! (&)
频率 ’()*
+ ++$,-
% $$+,.
+% %-!,.
!" #!/,$
!% /"+,#
$" /#0,/
!01 6 ! , 横 向 波 速 为 / 2 3 !! 6 ! 。 由 于 弹 性 模 量 0 3
@;4&>4?5 )5= 45:;>4) &?DE:59)>4?5F 2?5>;?B GH9>:D9 I:&35?B?JH
[ ,] + KLLL I;)59)&>4?59 ?5F M?B1D: **F
K991: *F
,)5+
!""$ N)J: O9P Q*"R.**S+
梁 O编辑:
玉P
-!
#$ %& ’()*+%,%-$. /01+-2*%03!4454. 6*7+18 !"#$%&’$( 9+ +%:;1, (,()#:7) 0<=(##7+- ;1)*7+(=. #*( <:%)(== <1:1;(#(:= >(:( )%+=#1+# 1+? )%0,? +%# @( )%+#:%,,(? %+,7+(A 9+ #*7= <1<(: 1 +(> )%;<0#(: )%+#:%,,(? (,()#:7) 0<=(##7+- =$=#(; 7= 7+#:%?0)(?A B1=(? %+ 1+1,$=7= %& ;17+ <:%)(== <1:1;(#(:= =0)* 1= 0<=(##7+- C(,%)7#7(=. *(1#7+- )0::(+#. 0<=(##7+- <:(==0:(= (#)A. #*( %<#7;0; )%+#:%, =$=#(; %& <:%)(== <1:1;(#(:= 7= ?(#(:D ;7+(?A ’*( )%+#:%, %@E()# 7= #*( %<#7;0; &%:;7+- #(;<(:1#0:( 1+? 7# 7= :(1,72(? @$ )%+#:%,,7+- &%:;7+- <:(==0:(A )*+ ,-%.#( <:%)(== <1:1;(#(:=F ;(#1, ?(&%:;F (,()#:7) 0<=(#D #7+-F %<#7;0; )%+#:%, !!"#!$#%! &’()*++,-. /-0 1,’* 2,3’/4,(- ,- 5674,#8,’* 9/8 /0!1 2-3456*347 801 9&:5;:347 <2!= >:56*34 GH)*%%, %& I()*1+7)1, J K,()#:%+7) K+-7+((:7+- 1+? L0#%;1#7%+. H*1+-*17 M+7C(:=7#$. H*1+-*17N444O4. 6*7+18 !"#$%&’$( 9+ #*7= <1<(:. #*( 10#*%: &7:=# <:(=(+#= #*( P01,7#$ 7;<1)# %& C7@:1#7%+ %+ ;0,#7 >7:( =1> 0=(? #% )0# =7,7)%+. 1+? 1+1,$2(= =%;( &%:)(= 7+ #*( <:%)(==7+- 1:(1=A B1=(? #*( 1+1,$=7= %& #*( =$=#(;. #*( 10#*%: ;%?(,= #*( =$=#(; >7#* Q1;7,#%+ <:7+)7&l