合成氨的生产工艺的现状及发展趋势
合成氨工艺技术的现状及其发展趋势
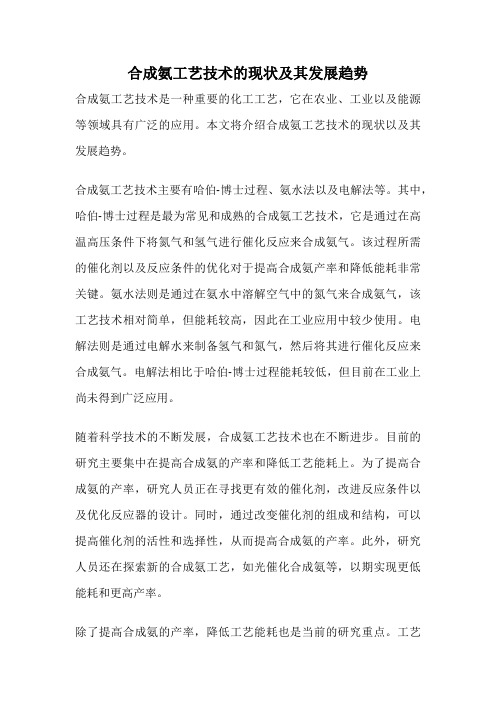
合成氨工艺技术的现状及其发展趋势合成氨工艺技术是一种重要的化工工艺,它在农业、工业以及能源等领域具有广泛的应用。
本文将介绍合成氨工艺技术的现状以及其发展趋势。
合成氨工艺技术主要有哈伯-博士过程、氨水法以及电解法等。
其中,哈伯-博士过程是最为常见和成熟的合成氨工艺技术,它是通过在高温高压条件下将氮气和氢气进行催化反应来合成氨气。
该过程所需的催化剂以及反应条件的优化对于提高合成氨产率和降低能耗非常关键。
氨水法则是通过在氨水中溶解空气中的氮气来合成氨气,该工艺技术相对简单,但能耗较高,因此在工业应用中较少使用。
电解法则是通过电解水来制备氢气和氮气,然后将其进行催化反应来合成氨气。
电解法相比于哈伯-博士过程能耗较低,但目前在工业上尚未得到广泛应用。
随着科学技术的不断发展,合成氨工艺技术也在不断进步。
目前的研究主要集中在提高合成氨的产率和降低工艺能耗上。
为了提高合成氨的产率,研究人员正在寻找更有效的催化剂,改进反应条件以及优化反应器的设计。
同时,通过改变催化剂的组成和结构,可以提高催化剂的活性和选择性,从而提高合成氨的产率。
此外,研究人员还在探索新的合成氨工艺,如光催化合成氨等,以期实现更低能耗和更高产率。
除了提高合成氨的产率,降低工艺能耗也是当前的研究重点。
工艺能耗的降低可以通过改进反应条件、优化反应器的设计以及改良催化剂等手段来实现。
此外,研究人员还在探索利用可再生能源和废弃物资源来替代传统的氢气制备方法,以进一步降低工艺能耗。
在未来,合成氨工艺技术的发展趋势将主要集中在以下几个方面。
首先,随着对环境保护意识的提高,研究人员将更加注重合成氨工艺的环境友好性,努力开发低碳排放的合成氨工艺。
其次,研究人员将继续探索新的催化剂和反应条件,以提高合成氨的产率和选择性。
最后,随着能源资源的日益紧缺,研究人员将更加关注合成氨工艺的能耗问题,努力寻找新的能源替代品,以降低工艺能耗。
合成氨工艺技术是一项重要的化工工艺,它在农业、工业以及能源等领域具有广泛应用。
中国合成氨行业发展现状及趋势分析
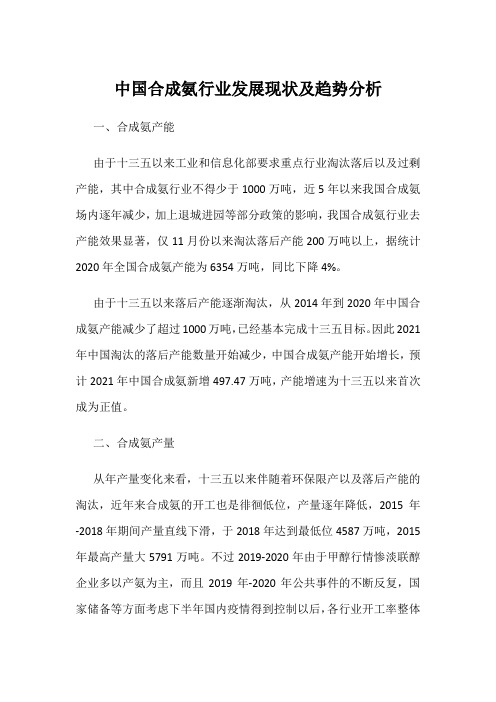
中国合成氨行业发展现状及趋势分析一、合成氨产能由于十三五以来工业和信息化部要求重点行业淘汰落后以及过剩产能,其中合成氨行业不得少于1000万吨,近5年以来我国合成氨场内逐年减少,加上退城进园等部分政策的影响,我国合成氨行业去产能效果显著,仅11月份以来淘汰落后产能200万吨以上,据统计2020年全国合成氨产能为6354万吨,同比下降4%。
由于十三五以来落后产能逐渐淘汰,从2014年到2020年中国合成氨产能减少了超过1000万吨,已经基本完成十三五目标。
因此2021年中国淘汰的落后产能数量开始减少,中国合成氨产能开始增长,预计2021年中国合成氨新增497.47万吨,产能增速为十三五以来首次成为正值。
二、合成氨产量从年产量变化来看,十三五以来伴随着环保限产以及落后产能的淘汰,近年来合成氨的开工也是徘徊低位,产量逐年降低,2015年-2018年期间产量直线下滑,于2018年达到最低位4587万吨,2015年最高产量大5791万吨。
不过2019-2020年由于甲醇行情惨淡联醇企业多以产氨为主,而且2019年-2020年公共事件的不断反复,国家储备等方面考虑下半年国内疫情得到控制以后,各行业开工率整体高位及置换产能等的释放,2020年合成氨行业开工整体偏高,产量也出现增长。
2020年中国合成氨产量第一的企业为云天化集团有限责任公司,第二为中国石油天然气股份有限公司,第三为湖北宜化集团有限责任公司。
三、合成氨消费2018年,合成氨消费总量为5694吨,相比2017年下降0.3%,近5年年均下降1.8%左右。
合成氨下游消费量整体呈现“减肥增化”的转型趋势,故合成氨消费量下降速度较缓,低于尿素3.3%的5年年均降速。
市场对合成氨的需求主要来自农业和工业两大方面,农业消费量近年呈逐年下降的趋势,2018年占合成氨消费量比例为70%,相比于2010年的90%左右下降了近20%。
农业消费领域中下降最快的两大产品是尿素和碳酸氢铵,近5年的年均降幅分别为9%和21%。
合成氨工业发展现状及重要性

合成氨工业发展现状及重要性首先,合成氨工业的发展现状。
合成氨工业在全球范围内具有广泛的应用和重要性。
目前,世界上最常用的合成氨工业方法是哈伯-波仑法。
该法利用铁钼催化剂,以高温高压条件下,将氮气和氢气进行催化反应,生成氨气。
这种方法具有产量高、工艺简单等优点,被广泛应用于全球各地的合成氨厂。
然而,合成氨工业也面临一些挑战。
首先,合成氨是高能耗产业,需要大量的氢气和氮气作为原料。
氢气的制备主要依赖于化石燃料,会产生大量的二氧化碳排放,给环境带来负面影响。
其次,合成氨的催化剂需要高温高压条件下操作,会对设备和工艺提出较高的要求。
此外,合成氨产业还面临市场需求波动和价格波动等风险。
其次,合成氨工业的重要性。
合成氨是化肥的主要原料,化肥在农业生产中具有重要的作用。
据统计,全球85%的合成氨用于制造化肥,其中又以尿素为主要产品。
化肥的使用可以提高土壤肥力,促进植物生长,提高农作物产量,对解决粮食安全和人类生存问题具有重要意义。
合成氨工业的发展对农业生产具有重要支撑作用。
此外,合成氨还广泛应用于其他领域。
合成氨可以用作制造塑料、化纤、橡胶等合成材料的原料,具有重要的工业应用。
合成氨还可以用于制造染料、颜料、医药中间体、炸药等化工产品。
合成氨工业的发展对推动其他化工行业的发展也具有重要影响。
综上所述,合成氨工业在全球范围内具有广泛的应用和重要性。
合成氨作为化肥的主要原料,在农业生产中具有重要作用。
合成氨工业的发展还对其他化工行业和工业生产有着重要推动作用。
然而,合成氨工业仍面临一些挑战,包括能源消耗、环境影响等问题。
因此,未来合成氨工业需要进一步推动技术创新,减少能源消耗和环境污染,实现可持续发展。
中国合成氨行业的现状和发展趋势

中国合成氨行业的现状和发展趋势中国的合成氨行业是化学工业的重要组成部分,广泛应用于农用化肥、化工原料、塑料制品等领域。
本文将从现状和发展趋势两个方面对中国合成氨行业进行分析。
一、现状1.产能和生产规模:中国合成氨行业的产能和生产规模在全球处于领先地位。
数据显示,目前中国的合成氨年产能已超过5000万吨,占全球总产能的40%以上。
2.技术水平:中国合成氨行业在技术水平方面也有显著进步。
早期,中国合成氨主要采用卡夫实验室氨合成工艺,但现在已逐渐发展成为以煤炭、天然气为原料的大型化工企业,采用国际先进的合成氨技术,如哈贝法等。
3.国内市场需求:中国作为农业大国,农用合成氨需求量巨大。
由于农业机械化和现代化水平的提高,以及土壤肥力的下降,中国对合成氨的需求将会持续增长。
二、发展趋势1.生产技术:中国合成氨行业将继续提高生产技术水平,加大对新型合成氨工艺的研究和开发,努力降低生产成本,提高产品质量。
2.环境友好型:合成氨是传统化工产品,对环境的影响比较大。
随着环保意识的增强,中国合成氨行业将更加注重环保问题,推动绿色生产,减少污染物的排放。
3.产业升级:合成氨行业将向高端产品和高附加值链条延伸。
除了农用化肥,合成氨还可用于生产尿素、合成氨甲酸等有机化工产品。
同时,合成氨在新能源、新材料等领域也有广阔的应用前景。
4.供给侧:中国合成氨行业将加速供给侧结构性,通过淘汰落后产能、整合资源,推动行业集中度的提高。
同时,政府还鼓励产业园区的建设,提供更好的产业环境和政策支持。
总之,中国合成氨行业在稳步发展的同时,也面临着挑战和机遇。
只有加强科技创新,推动绿色发展,进一步提高产品质量和技术水平,才能在国际市场上保持竞争优势。
合成氨工艺技术的现状及发展趋势
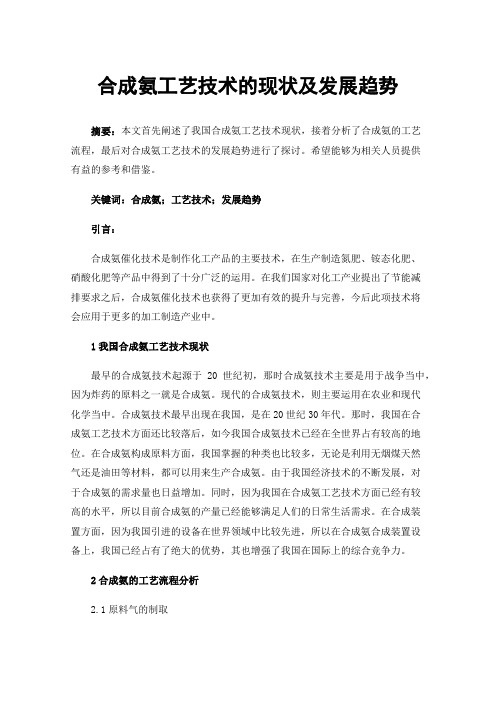
合成氨工艺技术的现状及发展趋势摘要:本文首先阐述了我国合成氨工艺技术现状,接着分析了合成氨的工艺流程,最后对合成氨工艺技术的发展趋势进行了探讨。
希望能够为相关人员提供有益的参考和借鉴。
关键词:合成氨;工艺技术;发展趋势引言:合成氨催化技术是制作化工产品的主要技术,在生产制造氮肥、铵态化肥、硝酸化肥等产品中得到了十分广泛的运用。
在我们国家对化工产业提出了节能减排要求之后,合成氨催化技术也获得了更加有效的提升与完善,今后此项技术将会应用于更多的加工制造产业中。
1我国合成氨工艺技术现状最早的合成氨技术起源于20世纪初,那时合成氨技术主要是用于战争当中,因为炸药的原料之一就是合成氨。
现代的合成氨技术,则主要运用在农业和现代化学当中。
合成氨技术最早出现在我国,是在20世纪30年代。
那时,我国在合成氨工艺技术方面还比较落后,如今我国合成氨技术已经在全世界占有较高的地位。
在合成氨构成原料方面,我国掌握的种类也比较多,无论是利用无烟煤天然气还是油田等材料,都可以用来生产合成氨。
由于我国经济技术的不断发展,对于合成氨的需求量也日益增加。
同时,因为我国在合成氨工艺技术方面已经有较高的水平,所以目前合成氨的产量已经能够满足人们的日常生活需求。
在合成装置方面,因为我国引进的设备在世界领域中比较先进,所以在合成氨合成装置设备上,我国已经占有了绝大的优势,其也增强了我国在国际上的综合竞争力。
2合成氨的工艺流程分析2.1原料气的制取制作合成氨的原材料主要是天然气、重油、石脑油等。
不管是哪一种原材料都可以用来代表。
这些原材料在水蒸气和高温下形成将一氧化碳与氢作为主体的合成氨原材料气。
我们国家制作合成氨原料气的主要方式为煤气化法。
这种方法主要是利用氧、蒸汽以及其他汽化剂高温处理煤,促使其转变成一氧化碳和氢等可以燃烧的气体。
对气态烃类,工业中通常使用二段蒸汽转化法加工制造合成气。
重油部分的氧化法主要是将重油作为原材料,而气态烃类主要是不完全燃烧氧气,促使烃类在高温的作用下出现燃烧和裂解现象,出现的二氧化碳和水蒸气在高温的作用下和甲烷发生转化反应,进而取得将氧化碳和氢气作为主要原料的合成气。
我国合成氨生产工艺技术现状
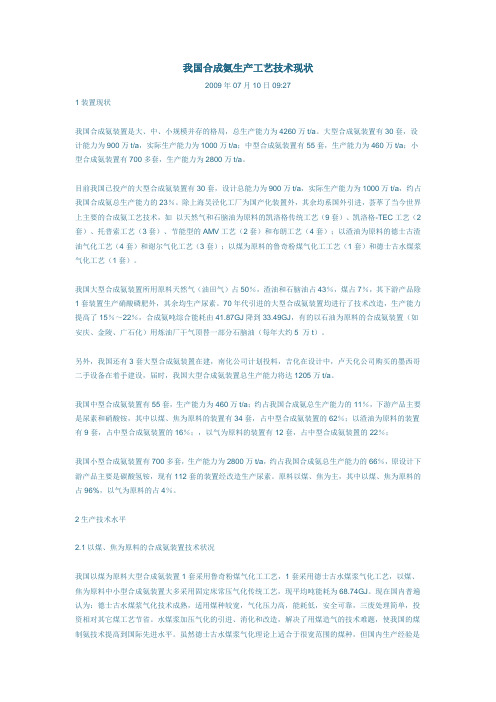
我国合成氨生产工艺技术现状2009年07月10日09:271装置现状我国合成氨装置是大、中、小规模并存的格局,总生产能力为4260万t/a。
大型合成氨装置有30套,设计能力为900万t/a,实际生产能力为1000万t/a;中型合成氨装置有55套,生产能力为460万t/a;小型合成氨装置有700多套,生产能力为2800万t/a。
目前我国已投产的大型合成氨装置有30套,设计总能力为900万t/a,实际生产能力为1000万t/a,约占我国合成氨总生产能力的23%。
除上海吴泾化工厂为国产化装置外,其余均系国外引进,荟萃了当今世界上主要的合成氨工艺技术,如以天然气和石脑油为原料的凯洛格传统工艺(9套)、凯洛格-TEC工艺(2套)、托普索工艺(3套)、节能型的AMV工艺(2套)和布朗工艺(4套);以渣油为原料的德士古渣油气化工艺(4套)和谢尔气化工艺(3套);以煤为原料的鲁奇粉煤气化工工艺(1套)和德士古水煤浆气化工艺(1套)。
我国大型合成氨装置所用原料天然气(油田气)占50%,渣油和石脑油占43%,煤占7%,其下游产品除1套装置生产硝酸磷肥外,其余均生产尿素。
70年代引进的大型合成氨装置均进行了技术改造,生产能力提高了15%~22%,合成氨吨综合能耗由41.87GJ降到33.49GJ,有的以石油为原料的合成氨装置(如安庆、金陵、广石化)用炼油厂干气顶替一部分石脑油(每年大约5 万t)。
另外,我国还有3套大型合成氨装置在建,南化公司计划投料,吉化在设计中,卢天化公司购买的墨西哥二手设备在着手建设,届时,我国大型合成氨装置总生产能力将达1205万t/a。
我国中型合成氨装置有55套,生产能力为460万t/a;约占我国合成氨总生产能力的11%,下游产品主要是尿素和硝酸铵,其中以煤、焦为原料的装置有34套,占中型合成氨装置的62%;以渣油为原料的装置有9套,占中型合成氨装置的16%;,以气为原料的装置有12套,占中型合成氨装置的22%;我国小型合成氨装置有700多套,生产能力为2800万t/a,约占我国合成氨总生产能力的66%,原设计下游产品主要是碳酸氢铵,现有112套的装置经改造生产尿素。
合成氨工业发展现状及重要性
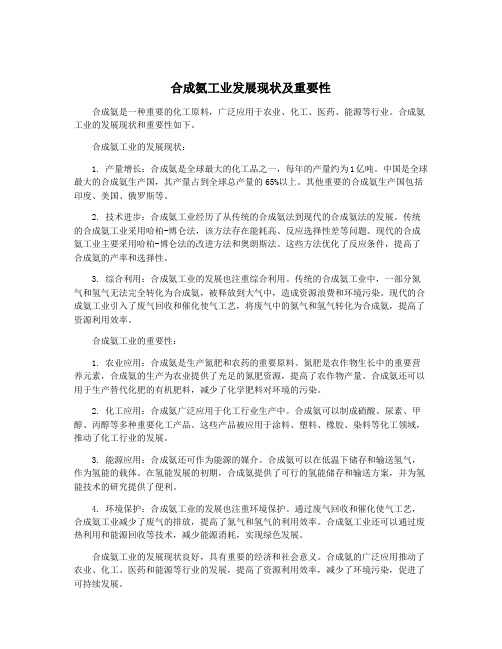
合成氨工业发展现状及重要性合成氨是一种重要的化工原料,广泛应用于农业、化工、医药、能源等行业。
合成氨工业的发展现状和重要性如下。
合成氨工业的发展现状:1. 产量增长:合成氨是全球最大的化工品之一,每年的产量约为1亿吨。
中国是全球最大的合成氨生产国,其产量占到全球总产量的65%以上。
其他重要的合成氨生产国包括印度、美国、俄罗斯等。
2. 技术进步:合成氨工业经历了从传统的合成氨法到现代的合成氨法的发展。
传统的合成氨工业采用哈柏-博仑法,该方法存在能耗高、反应选择性差等问题。
现代的合成氨工业主要采用哈柏-博仑法的改进方法和奥朗斯法。
这些方法优化了反应条件,提高了合成氨的产率和选择性。
3. 综合利用:合成氨工业的发展也注重综合利用。
传统的合成氨工业中,一部分氮气和氢气无法完全转化为合成氨,被释放到大气中,造成资源浪费和环境污染。
现代的合成氨工业引入了废气回收和催化使气工艺,将废气中的氮气和氢气转化为合成氨,提高了资源利用效率。
合成氨工业的重要性:1. 农业应用:合成氨是生产氮肥和农药的重要原料。
氮肥是农作物生长中的重要营养元素,合成氨的生产为农业提供了充足的氮肥资源,提高了农作物产量。
合成氨还可以用于生产替代化肥的有机肥料,减少了化学肥料对环境的污染。
2. 化工应用:合成氨广泛应用于化工行业生产中。
合成氨可以制成硝酸、尿素、甲醇、丙醇等多种重要化工产品。
这些产品被应用于涂料、塑料、橡胶、染料等化工领域,推动了化工行业的发展。
3. 能源应用:合成氨还可作为能源的媒介。
合成氨可以在低温下储存和输送氢气,作为氢能的载体。
在氢能发展的初期,合成氨提供了可行的氢能储存和输送方案,并为氢能技术的研究提供了便利。
4. 环境保护:合成氨工业的发展也注重环境保护。
通过废气回收和催化使气工艺,合成氨工业减少了废气的排放,提高了氮气和氢气的利用效率。
合成氨工业还可以通过废热利用和能源回收等技术,减少能源消耗,实现绿色发展。
合成氨工业的发展现状良好,具有重要的经济和社会意义。
合成氨工业发展现状及重要性

合成氨工业发展现状及重要性1. 引言1.1 合成氨工业发展现状及重要性合成氨是一种重要的化工原料,被广泛应用于农业、化肥、医药、塑料等领域。
合成氨工业的发展现状及重要性备受关注,因为它直接关系到国家经济发展和人民生活水平。
合成氨工业在全球范围内具有重要地位,影响着世界各国的经济和产业结构。
我国作为世界上最大的合成氨生产国之一,合成氨工业的发展现状更是备受瞩目。
合成氨的生产过程涉及到许多技术和工艺,其发展也不断受到技术进步和市场需求的影响。
合成氨工业概况显示,全球合成氨生产规模逐年增加,市场需求也在不断扩大。
我国合成氨工业现状分析表明,我国的合成氨产量居世界前列,但仍面临许多挑战和问题,如资源利用、环境保护等方面存在一定的困难。
加强合成氨工业的技术研发和产业升级至关重要。
合成氨的重要性不容忽视,它不仅是农业生产的重要化肥原料,也是医药、塑料等产业的基础原料。
合成氨工业的发展趋势表明,随着科技进步和市场需求的变化,合成氨行业将迎来新的机遇和挑战。
合成氨工业的未来发展前景广阔,对我国经济发展具有重要意义。
加强合成氨工业的发展不仅能保障国家粮食安全,还能促进产业结构调整和经济增长。
合成氨工业的可持续发展策略是未来发展的重要方向,只有不断创新提高技术水平,才能确保合成氨工业的稳步发展。
2. 正文2.1 全球合成氨产业概况合成氨是一种非常重要的化工原料,广泛应用于农业、化肥、医药、塑料等领域。
据统计,全球合成氨产业目前已经成为化工行业的重要组成部分,且呈现出快速发展的趋势。
在全球范围内,合成氨的主要生产国家包括中国、印度、美国、俄罗斯等。
中国是全球最大的合成氨生产国,年产量占据了全球总产量的相当大比例。
印度虽然合成氨产量较高,但仍属于进口依赖型国家。
美国和俄罗斯的合成氨产业也比较发达,拥有先进的生产技术和设备。
全球合成氨产业存在一定的竞争与合作关系。
各国之间通过技术交流、合作开发新技术,提高生产效率和产品质量。
国内外合成氨工艺技术现状及其发展
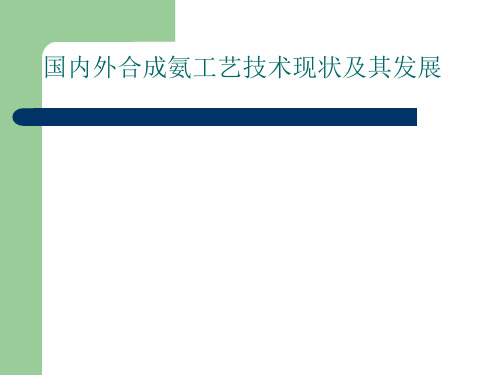
较先进的技术。
上世纪七八十年代引进的装置,经过节能和增产技术改造,产能、消
耗、质量、环保等仍处于国内领先水平;主要技术经济指标仍可跟踪 上世界先进工艺技术的水平。
以油为原料的装置在结构调整中,引入洁净煤气化技术提升了原料多
元化进的技术水平。
大型合成氨生产技术荟萃了当今世界上主要的先进工艺技术,是世界
2584.88
201
3954.67
321
1094.84
522
5049.51
占全国 (%)
9.16 29.45 51.19 78.32 21.68 100.00
1.4 原料以煤为主,适合中国资源特点
合成氨原料结构占产能的比例(%)
年份
2000
2006
2007
2008
天然气
14
21.3
20.2
20.1
2007
ቤተ መጻሕፍቲ ባይዱ
年份
2008
全球总计 中国总计 大型装置
1.1 产能快速增长
中国现有合成氨生产企业 522个,2008年合成氨总产能约5700万吨,2009年 底预计达到6000万吨以上。
产能增加主要是新建装置和部分装置扩能改造的贡献。
合成氨的生产工艺的现状及发展趋势的探讨
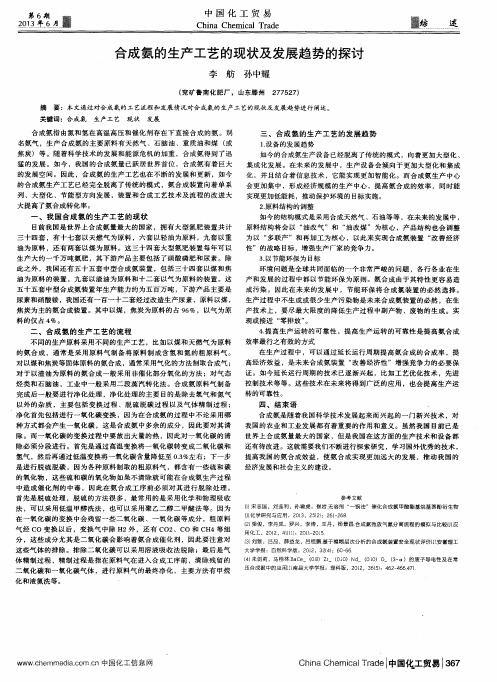
的 合成 氨生 产工 艺 已经 完全 脱 离 了传统 的模式 ,氨合 成 装置 向着 单 系
列 、大 型化 、节能 型 方 向发展 ,装 置 和合 成工 艺 技术 及 流程 的改 进 大
会更 加集 中 ,形 成经 济规 模 的生产 中心 ,提 高氨 合成 的效 率 ,同时 能 实现更 加低 能耗 ,推动保 护环境 的 目 标 实施 。
焦 炭) 等 。随 着科 学 技术 的发 展 和能 源 危机 的加 重 ,合 成氨 得 到 了迅 猛 的发 展 。如 今 ,我 国 的合 成氨 量 已跃 居世 界首 位 ,合 成氨 有着 巨大 的 发展 空 间 。因此 ,合成 氨 的生产 工 艺也 在 不断 的发 展 和更 新 ,如 今
三 、合成氨 的生产 工艺的 发展趋 势
烃 类 和 石脑 油 ,工 业 中一般 采 用二 段蒸 汽 转化 法 。合 成氨 原料 气 制 备 完成 后 一般 要 进行 净化 处理 ,净化 处理 的主要 目的是 除 去氢 气和 氮 气 以外 的 杂质 ,主要 包 括 变换 过 程 、脱 硫 脱 碳 过程 以及 气体 精 制 过 程 ; 净 化 首先 包括 进 行 一氧 化碳 变换 ,因为 在合 成 氨 的过程 中不论 采 用 哪 种 方 式 都会 产生 一 氧化 碳 ,这 是合 成氨 中多余 的成 分 ,因此要 对 其 清 除 。而一 氧化 碳 的变 换 过程 中要 放 出大 量 的热 ,因此对 ・ 氧化 碳 的清 除 必须 分 段 进行 。首 先 是通 过 高温 变换 将一 氧化 碳 转变 成 二氧 化碳 和 氢 气 ,然 后再 通过 低温变 换将 一 氧化 碳含 量降 低至 0 . 3 %左右 ;下 一步 是 进行 脱 硫脱 碳 ,因为 各种 原料 制 取的 粗原 料 气 ,都含 有 一些 硫和 碳 的氧化 物 ,这 些 硫和 碳 的氧 化 物如 果不 清除 就 可能 在合 成 氨生 产过 程
合成氨工业发展现状及重要性
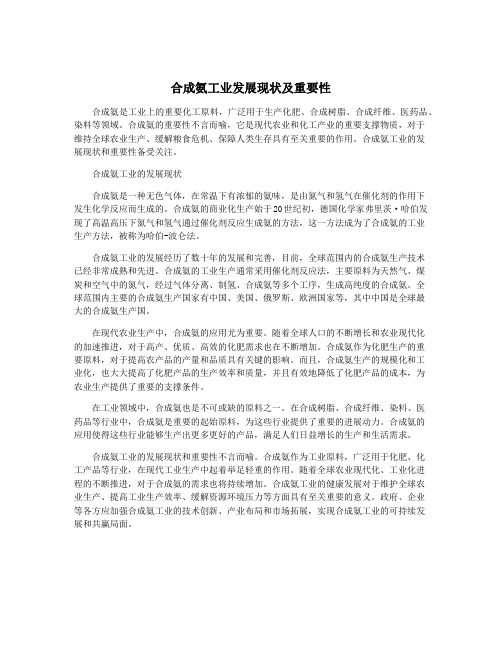
合成氨工业发展现状及重要性合成氨是工业上的重要化工原料,广泛用于生产化肥、合成树脂、合成纤维、医药品、染料等领域。
合成氨的重要性不言而喻,它是现代农业和化工产业的重要支撑物质,对于维持全球农业生产、缓解粮食危机、保障人类生存具有至关重要的作用。
合成氨工业的发展现状和重要性备受关注。
合成氨工业的发展现状合成氨是一种无色气体,在常温下有浓郁的氨味,是由氮气和氢气在催化剂的作用下发生化学反应而生成的。
合成氨的商业化生产始于20世纪初,德国化学家弗里茨·哈伯发现了高温高压下氮气和氢气通过催化剂反应生成氨的方法,这一方法成为了合成氨的工业生产方法,被称为哈伯-波仑法。
合成氨工业的发展经历了数十年的发展和完善,目前,全球范围内的合成氨生产技术已经非常成熟和先进。
合成氨的工业生产通常采用催化剂反应法,主要原料为天然气、煤炭和空气中的氮气,经过气体分离、制氢、合成氨等多个工序,生成高纯度的合成氨。
全球范围内主要的合成氨生产国家有中国、美国、俄罗斯、欧洲国家等,其中中国是全球最大的合成氨生产国。
在现代农业生产中,合成氨的应用尤为重要。
随着全球人口的不断增长和农业现代化的加速推进,对于高产、优质、高效的化肥需求也在不断增加。
合成氨作为化肥生产的重要原料,对于提高农产品的产量和品质具有关键的影响。
而且,合成氨生产的规模化和工业化,也大大提高了化肥产品的生产效率和质量,并且有效地降低了化肥产品的成本,为农业生产提供了重要的支撑条件。
在工业领域中,合成氨也是不可或缺的原料之一。
在合成树脂、合成纤维、染料、医药品等行业中,合成氨是重要的起始原料,为这些行业提供了重要的进展动力。
合成氨的应用使得这些行业能够生产出更多更好的产品,满足人们日益增长的生产和生活需求。
合成氨工业的发展现状和重要性不言而喻。
合成氨作为工业原料,广泛用于化肥、化工产品等行业,在现代工业生产中起着举足轻重的作用。
随着全球农业现代化、工业化进程的不断推进,对于合成氨的需求也将持续增加。
合成氨工艺技术的现状及发展趋势

合成氨工艺技术的现状及发展趋势摘要:在我国不断发展的过程当中,市场对于化工产品的需求量也在不断增大,再加上我国的科学技术开始不断进步,对于化工产品的使用量还在不断提高。
合成氨是化工领域的侧重产品,其产出过程使得能源的消耗量增加,所以如何通过对合成氨工艺技术进行科学的改革,进而改善合成氨现有状态的产出流程,对于我国的化工发展具有促进作用。
合成氨工艺技术的发展必将紧跟我国可持续发展战略,有效的降低对能源的消耗量。
本文将简要介绍氨以及氨工艺的重要作用,指出当下合成氨工艺技术应用的现状,并且对合成氨工艺技术的发展趋势进行分析。
关键词:合成氨工艺技术装置设备低能耗标准引言:氨是我国最重要的基础化工产品之一,所以每年的产量都很高,在研究人员的不断实验之下,合成氨已经大面积的应用在农业产业当中,成为了安徽工业生产的基础原料。
氨本身就是重要的氮素肥料,所以在无机化学和有机化学作为基础原料的时候,也可以被应用在工业领域当中,从社会的发展来看合成氨工艺技术的进步,将会促进我国社会生产效率的提高。
社会生产对安的需求量不断增大,使得合成氨工艺技术的应用范围不断扩张,在新型技术的发展之下,合成氨工艺技术必将会向着大型化、低能耗以及结构完整的目标进行发展。
合成氨的工艺技术在未来的发展过程当中,可以充分的利用高油价下合成氨原料结构的变化模式,再与相关的技术进行结合,对现阶段的合成氨工艺进行调整。
一、合成氨工艺技术应用的现状(一)由传统型蒸汽转化为制氨工艺阶段在我国的工艺技术不断革新的过程当中,合成氨工艺装置的使用也在不断的发生着变化,美国合成氨工艺技术研究部门提出,将天然气作为原料的应用模式,使得合成氨工艺技术对能源的消耗量大大降低。
并且根据不断的实践经验得出,经过改革之后的合成氨工艺技术,还可以有效的提高工艺加工的进度以及产量。
在传统的合成氨工艺当中合成安装制需要运用到离心式的压缩机,进而利用压缩机的原理,将公益系统与动力系统结合起来,最终实现大规模生产的目标,离心式的压缩机装置具有一大优势,其属于单系列的大型化模式,所以可以被应用在众多生产加工使用当中,并且生产效率较高。
我国合成氨工业的现状及发展趋势

我国合成氨工业的现状及发展趋势合成氨工业的现状及发展趋势一、我国合成氨工业已走过了五十多年的路程,从小到大从弱到强,从3000吨/年——5000吨/年到45万吨/年,从碳铵到尿素。
根据中国氮肥协会统计2019年合成氨产量5864.1万吨/年,位居世界第一,其中88%用来生产化肥;30万吨/年工厂有74家约占49.4%,8万吨/年上以工厂有223家占82.4%,合成氨工业由3000吨/年发展到今天40万吨/年(单系列),全国从1000个厂到今只有300个厂,然而总产量不但没有下降,反而有所增加,尿素2019年出口355.95万吨,从而保证了粮食生产连年丰收。
(据农业部门反映一吨尿素可增产粮食几吨),我国粮食为什么连年丰收增产,一是靠国家支农、惠农、护农政策,二是靠优良品种,三是靠化肥支撑。
因此对于我们这样一个有13.4亿人的大国,如果粮食生产不能稳定,那是不堪设想的。
因此合成氨工业是国家发展的需要,也是人民生活的需要。
二、我国合成氨工业发展趋势由于我国人多地少,粮食需求量大,因此合成氨工业必须由小变大,向大型化、现代化发展,过去小规模用块煤的技术已远远不能满足国民经济发展需要,发展趋势主要是:1. 由小变大,扶大压小;2. 由块煤变粉煤;3. 由低压向中压、高压气化发展;具体有以下几点:1. 中压、高压造气不管用水煤浆气化炉、干粉煤气化炉,还是块煤炉,流化床气化炉都要向中压、高压发展,现在有的气化炉已做到8.7Map ,一般都在4.0Map 左右。
透平压缩这样可以省电3%左右。
2. 低压合成氨。
过去为了追求产量合成氨压力由低压向高压发展,现在从降低能耗的角度又能向低压,目前已成功运用15Map ,10Map 即正在试验中,这样可以做到电耗最低。
3. 高度净化,为了保证催化剂长周期运行气体净化已达到PPM 级,甚至PPb 级。
4. 消灭三废,最少做到达标排放,最终做到零排放。
三、合成氨工业发展对空分的要求,由于合成氨工业向大型化发展,因此对空分也提出了由小向大型发展的要求,从几千米3/时到几万米3/时,同时O2纯度N2纯度也提出了更高的要求。
世界合成氨的工业生产现状分析

世界合成氨的工业生产现状分析提示:一、用途合成氨是生产尿素、磷酸铵、硝酸铵等化学肥料的主要原料,工业生产过程是以天然气或煤炭为原料通过水蒸气重整工艺制得氢气,然后与氮气进行高压合成制得合成氨。
目前世界上合成氨主要专利供应商有丹麦哈德尔-托普索、美国KELLOGGBROWN & ROOT和德国伍德公司。
二、生产现状据统计,世界合成氨产能已超过1.76亿吨/年,主要生产能力分布情况:美国1000万吨/年、加拿大520万吨/年、墨西哥291万吨/年、南美地区856万吨/年(其中特立尼达453万吨/年)、西欧1218万吨/年、东欧3333.4万吨/年、中东/非洲1560.2万吨/年、亚太地区8720万吨/年。
合成氨按终端用途来分,约85%-90%的合成氨用作化肥:液态氨、硝酸铵、尿素或其他衍生物,仅13%用于其他商品市场。
三、价格情况美国:257美元/吨C&F TAMPA;270美元/短吨FOB,新奥尔良欧洲: 208-212美元/吨FOB,黑海亚太地区: 250-$270美元/吨C&F,东北亚四、前景展望据美国SRI咨询公司指出,2000-2003年间部分产能关闭使世界合成氨供需平衡得到稳固。
由于美国天然气价格持续居高位使合成氨行业盈利困难,美国一些公司均关闭了产能。
总部位于纽约的J.P.MORGAN公司咨询师DAVIDSILVER指出,世界合成工业已经走出困境,仍在复苏之中,由于需求强劲增长,加上产能增加很少推进复苏,另外北美产能关闭使得全球合成氨开工率维持在85%以上,并使生产商有条件抬高价格。
由于北美地区天然气原料价格走高,过去5年美国有相当数量的合成氨产能被永久关闭,合成氨生产正向天然气低价格地区转移,将集中在中东、北非和特立尼达。
随着天然气价格不断上涨,欧洲已成为世界上生产成本最高地区,相当数量的产能也正经受考验。
据英国FERTECON公司预测,未来4年世界合成氨产量将以3.5%/年增速继续增长,2010年将达到2亿吨,合成氨将主要用于下游尿素的生产。
合成氨
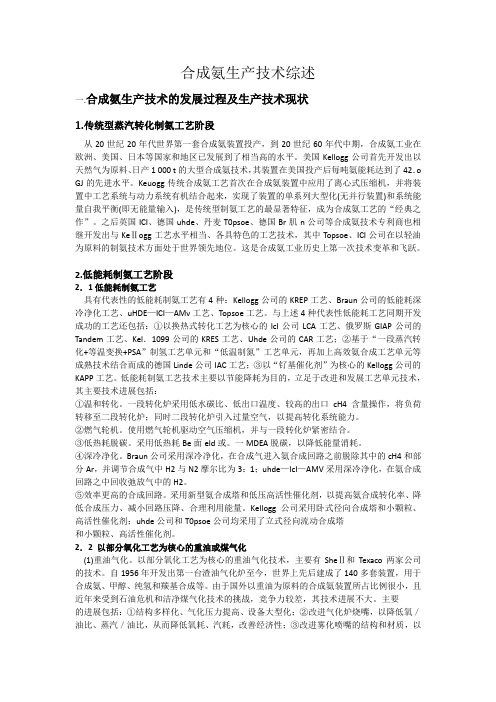
合成氨生产技术综述一.合成氨生产技术的发展过程及生产技术现状1.传统型蒸汽转化制氨工艺阶段从20世纪20年代世界第一套合成氨装置投产,到20世纪60年代中期,合成氨工业在欧洲、美国、日本等国家和地区已发展到了相当高的水平。
美国Kellogg公司首先开发出以天然气为原料、日产1 000 t的大型合成氨技术,其装置在美国投产后每吨氨能耗达到了42.o GJ的先进水平。
Keuogg传统合成氨工艺首次在合成氨装置中应用了离心式压缩机,并将装置中工艺系统与动力系统有机结合起来,实现了装置的单系列大型化(无并行装置)和系统能量自我平衡(即无能量输入),是传统型制氨工艺的最显著特征,成为合成氨工艺的“经典之作”。
之后英国ICI、德国uhde、丹麦T0psoe、德国Br肌n公司等合成氨技术专利商也相继开发出与KeⅡogg工艺水平相当、各具特色的工艺技术,其中Topsoe、ICI公司在以轻油为原料的制氨技术方面处于世界领先地位。
这是合成氨工业历史上第一次技术变革和飞跃。
2.低能耗制氨工艺阶段2.1低能耗制氨工艺具有代表性的低能耗制氨工艺有4种:Kellogg公司的KREP工艺、Braun公司的低能耗深冷净化工艺、uHDE—ICI—AMv工艺、Topsoe工艺。
与上述4种代表性低能耗工艺同期开发成功的工艺还包括:①以换热式转化工艺为核心的IcI公司LCA工艺、俄罗斯GIAP公司的Tandem工艺、Kel.1099公司的KRES工艺、Uhde公司的CAR工艺;②基于“一段蒸汽转化+等温变换+PSA”制氢工艺单元和“低温制氮”工艺单元,再加上高效氨合成工艺单元等成熟技术结合而成的德国Linde公司IAC工艺;③以“钌基催化剂”为核心的Kellogg公司的KAPP工艺。
低能耗制氨工艺技术主要以节能降耗为目的,立足于改进和发展工艺单元技术,其主要技术进展包括:①温和转化。
一段转化炉采用低水碳比、低出口温度、较高的出口cH4含量操作,将负荷转移至二段转化炉;同时二段转化炉引入过量空气,以提高转化系统能力。
论我国合成氨工业的现状及节能减排的措施
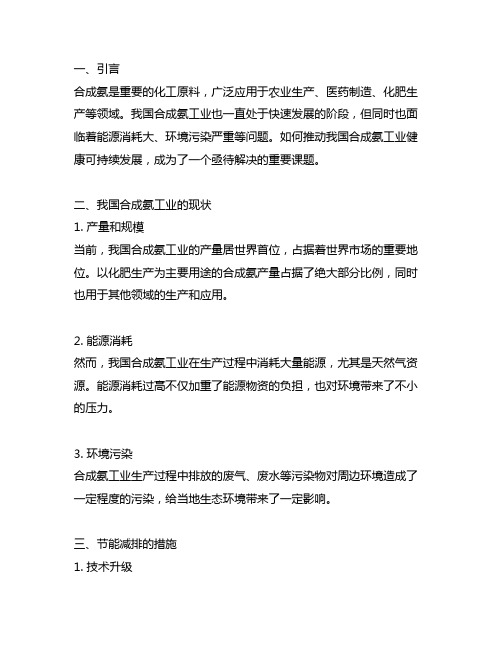
一、引言合成氨是重要的化工原料,广泛应用于农业生产、医药制造、化肥生产等领域。
我国合成氨工业也一直处于快速发展的阶段,但同时也面临着能源消耗大、环境污染严重等问题。
如何推动我国合成氨工业健康可持续发展,成为了一个亟待解决的重要课题。
二、我国合成氨工业的现状1. 产量和规模当前,我国合成氨工业的产量居世界首位,占据着世界市场的重要地位。
以化肥生产为主要用途的合成氨产量占据了绝大部分比例,同时也用于其他领域的生产和应用。
2. 能源消耗然而,我国合成氨工业在生产过程中消耗大量能源,尤其是天然气资源。
能源消耗过高不仅加重了能源物资的负担,也对环境带来了不小的压力。
3. 环境污染合成氨工业生产过程中排放的废气、废水等污染物对周边环境造成了一定程度的污染,给当地生态环境带来了一定影响。
三、节能减排的措施1. 技术升级通过技术创新和设备升级,减少生产过程中的能源消耗,提高合成氨的生产效率,降低生产成本。
2. 资源综合利用利用余热余能,开展能量综合利用,提高资源利用效率,减少对能源的依赖,降低生产过程中的废物排放。
3. 环保设施建设增加环保设施投入,加强废气、废水的处理和治理,降低对环境的影响。
4. 产业结构调整优化产业结构,降低传统合成氨生产的比重,逐渐转向绿色、环保型生产方式,推动我国合成氨工业向高质量、可持续发展的方向迈进。
四、个人观点和理解在我看来,我国合成氨工业正处在改革升级的关键时期。
提高能源利用效率、降低产业对环境的影响,是当前合成氨工业亟需解决的问题。
通过实施节能减排措施,可以不断提升合成氨工业的可持续发展能力,为我国的国民经济和环境保护作出积极贡献。
五、总结回顾我国合成氨工业虽然取得了长足发展,但面临能源消耗大、环境污染等问题。
为了实现合成氨工业的健康可持续发展,需要采取一系列的节能减排措施,以提高能源利用效率,减少对环境的影响,推动工业向绿色、环保方向发展。
相信在政府的政策支持和行业的共同努力下,我国合成氨工业一定能够迎来更加美好的明天。
合成氨工业现状和未来发展趋势
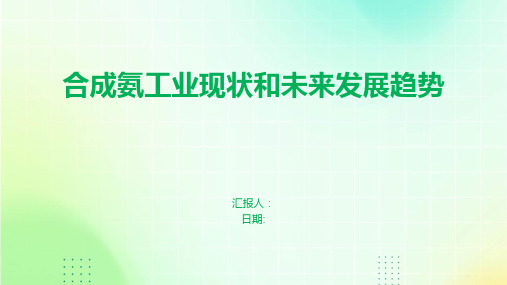
市场风险与应对策略
要点一
市场风险
合成氨市场的供求关系变化和价格波动对行业的发展带来 一定的市场风险。在供过于求的情况下,合成氨企业可能 面临销售困难和价格下跌的压力。同时,全球经济形势的 变化也会对合成氨市场产生影响。
要点二
应对策略
合成氨企业需要密切关注市场供求变化和价格走势,制定 灵活的市场策略,积极调整生产和销售计划。同时,加强 与上下游企业的合作,实现产业链的协同发展,降低市场 风险。
01 02
路径选择
随着环保和能源消耗问题的日益严重,合成氨工业需要进行产业转型和 升级,以实现可持续发展。可以通过提高生产效率、降低能源消耗和环 境污染等方面进行改进。
技术创新
加强技术创新是实现产业转型和升级的关键,可以通过引进和自主研发 新的生产技术和设备来实现。
03
绿色发展
加强环保管理,提高资源利用效率,实现绿色发展是合成氨工业的重要
先进工艺
包括天然气蒸汽转化、氮化物循环和膜分离等新兴技术,提高效率和产量。
行业规模与产能
全球合成氨产能已超过1.5亿吨/年,其中中国是全球最大的合成氨生产国。
行业产能过剩,需要不断提高效率和降低成本以保持竞争力。
市场供需情况
全球合成氨消费量约为1.2亿吨/年, 主要消费领域为农业肥料、工业原料 和燃料。
THANKS
感谢观看
自动化生产
通过自动化设备和机器人等手段,实现生产过程的自动化操作和控制,提高生产效率和降低成本。
市场竞争与合作
市场竞争
随着全球经济的不断发展和市场竞争的 加剧,合成氨工业将面临更加激烈的市 场竞争,企业需要不断提高自身的竞争 力以获得更大的市场份额。
VS
- 1、下载文档前请自行甄别文档内容的完整性,平台不提供额外的编辑、内容补充、找答案等附加服务。
- 2、"仅部分预览"的文档,不可在线预览部分如存在完整性等问题,可反馈申请退款(可完整预览的文档不适用该条件!)。
- 3、如文档侵犯您的权益,请联系客服反馈,我们会尽快为您处理(人工客服工作时间:9:00-18:30)。
合成氨的生产工艺的现状及发展趋势
作者:孙俊龙
来源:《中国化工贸易》2013年第02期
摘要:本文主要介绍了合成氨技术发展历程和基本状况,分析了生产过程中采用的典型工艺及其技术特点与经济性,指出了合成氨技术可能的发展趋势。
介绍了高油价下合成氨的原料结构变化及相关技术进展,认为未来合成氨技术进展的主要趋势是大型化、低能耗、结构调整、清洁生产、长周期运行。
关键词:合成氨工艺技术现状发展趋势
一、现状与发展概述
随着合成氨技术的逐步发展,氨合成的装置也逐渐向单系列、大型化、节能型方向发展。
在基础化工产品中,氨是比较重要的。
它的产量高,在各种化工产品中居首位;同时能源消耗也是最高的。
合成氨在农业上得到广泛应用,合成氨是氮肥工业的基础,同时氨也是无机化学和有机化学工业基础原料。
最近几年,国内外在传统生产工艺的基础上,又研发了节能氨合成工艺技术及流程,其主要是通过增加氨合成转化率、降低合成的压力、减小合成回路压降、合理利用能源等技术,我国现有大型合成氨装置30多套,其中氯合成塔也是国际上广泛使用的工艺设备,目前我国大部分中小型氮肥生产企业,基本采用国产设备,因此十分希望生产优化,但由于设备改造以及优先控制实施的费用过高,在这种情况下就需要挖掘自身潜力,结合现有装置设备特点,对当前操作过程进行合理调节,以实现生产系统与装置的最优搭配。
二、我国合成氨技术的基本情况
1.大型氮肥装置
我国目前的型合成氨装置共计34套,年生产能力1000万吨,其中除1套装置生产硝酸磷肥之外,其他均生产尿素。
按照所使用的原料类型划分,以天燃气为原料的设备17套,以轻油为原料的设备6套,以重油为原料的设备9套,以煤为原料的设备2套。
2.中、小型氮肥装置
目前有中型合成氨装置55套,年生产能力约为500万吨,主要是生产尿素和硝酸铵,其中以煤、焦为原料的装置有34套,以渣油为原料的装置有9套,以天然气为原料的装置有12套,目前有小型合成氨装置700多套,年生产能力约为3000万吨,主要生产碳酸氢铵,如今有112套经过设备改造后生产尿素,原料以煤,焦为主,其中以煤,焦为原料的占96%,以气为原料的仅占4%。
三、合成氨装置的结构调整
合成氨装置的技术调整主要体现在以下四个方面:
1.“油改气” 使用天然气合成氨的装置一般采用蒸汽转化的技术,但采用此技术有它的局限性,采用天然气部分氧化技术较之更为合理。
采用天然气部分氧化技术,不仅可以利用现有的气化炉调整操作工艺,进行烧嘴改造,而且改造难度小,投资少,改造周期短,具有明显的经济效益。
另外,天然气部分氧化技术易于向大型化发展,此项技术逐渐被同行业所认同。
2.“油改煤”煤气化技术相关的改造内容包括新建煤气化和新建合成气净化两部分。
煤气化技术逐步走向市场化奠定了合成氨装置的原料结构调整的主要技术基础。
3.“煤气化” 煤气化工艺技术日益成熟与完善,具有大型的专利工厂。
水煤浆气化工艺生产的粗合成气已逐渐用于循环联合发电,化肥,甲醇等行业的生产,粉煤气化工艺仅用于循环联合发电,两者都发挥了各自的作用并且各具特色。
4.“合成气净化” 这个生产环节的关键问题在于CO的变换工艺,如何脱除酸性气体,气体精制等工序的合理工艺流程。
其中CO变换工艺主要选择合成气净化工艺技术,CO变换工艺技术全为非硫,由于CO具有含量高,分压大的特点,因此要根据变换气的工艺条件,比较适合采用物理吸收法进行变换。
四、合成氨的工艺流程
1.原料气制备
首先将煤和天然气等原料制成含氢和氮的粗原料气,通常采用气化的方法对固体原料煤和焦炭加工制取合成气;渣油可通过非催化部分氧化的方法获得合成气;现代工业中利用二段蒸汽转化法对气态烃类和石脑油提炼制取合成氮。
2.净化
对粗原料进行净化处理,除去氢气和氮气以外的杂质,也是一项重要的工艺。
其操作主要是變换的过程。
①一氧化碳变换过程。
在合成氨生产过程中,很多方法制取的原料气都含有CO。
其体积分数一般为12~40%。
合成氮需要的两种成分是H和N,因此操作过程中就需要除去合成气中的CO②脱硫脱碳过程。
制成的粗原料气,多少都含有一些硫和碳的氧化物,在合成氨生产过程中,可以引起催化剂的中毒,所以必须在氨合成工序操作前加以脱除。
③气体精制过程。
为了防止对氨合成催化剂的毒害,规定CO和CO2,总量不得大于10CM3/M3(体积分数)。
因此,原料气必须进行最终净化才可以在进入合成工序,即精制过程。
3.氨合成
将纯净的氢,氮混合气进行高压压缩,在催化剂的作用下合成氨。
氨的合成是整个合成氨生产过程的核心工艺。
五、工艺技术改造
新建的煤气化生产线,生产合成气主要采用煤气化主流工艺。
新建了空气分离工序。
本工序采用全低压,内压缩空气工艺技术,主要提供煤气化工艺所需要的工艺氧气和高,中、低压氮气。
增建的耐硫变换工序。
采用三段耐硫变换工艺,进行合成气的高浓度CO变换。
增建脱除酸性气体的工序,采有低温甲醇洗净化工艺手段,净化变换气的脱硫脱碳的工序,使变换气中的H2S,COS,CO2成功脱除,并配合两级克劳斯脱硫+SCOT工艺,处理低温甲醇洗工序的H2S产生的尾气,改造和利用甲烷化工序完成整个操作过程。
六、合成氨技术的发展趋势
1.低能耗与生产环境将是未来合成氨装置技术未来发展的主流方向。
其生产设备向大型化、集成化、自动化方向发展。
2.以“油改气”和“油改煤”为主的原料结构调整和以产品再加工为核心的结构的调整,是企业增强竞争力的最有效途径之一。
3.清洁生产是未来合成氯装置发展的必然的,也是惟一的途径。
在生产过程中不生成或减少副产物,废物。
实现或接近“零排放”。
清洁生产已经成为未来工业产业重视的问题。
国内外企业都将清洁生产作为企业发展的一个重要目标。
4.提高生产运转的可靠性,使生产技术日趋成熟。
延长运行周期是未来合成氨装置在市场竞争中的重要保证。
其中可以“提高装置生产运转率”,延长生产运转周期,生产工艺优化的新技术和越来越先进的控制技术等将越来越受到国内外企业的重视。
参考文献
[1]蒋德军.[J].大氮肥,1997,(5):297-300.
[2]亢万忠,蒋德军.[J].大氮肥,1997,(6):372-376.
[3]蒋德军.[J].现代化工,2002,22(6):39-48.
[4]王庭富.[J].化工进展,2001,20(8),6-8.。