国际油漆涂装资料
涂装技术手册(PPG公司)
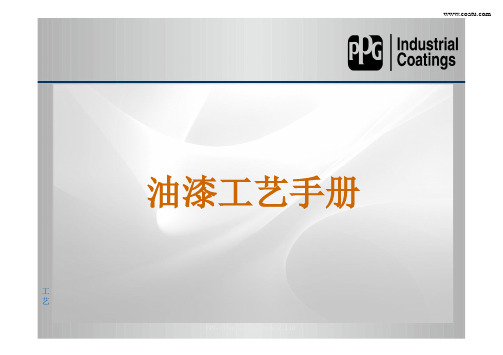
溶剂气泡:在刚刚喷涂的漆膜表面呈现出很多直径在1mm以 溶剂气泡:在刚刚喷涂的漆膜表面呈现出很多直径在 以 下的顶部裂开的小气泡
原因: 因
1、喷涂雾化空气压力太低 喷涂雾化空气压力太低。
2、清漆膜厚太高 清漆膜厚太高。 3、流平时间不足 流平时间不足。 4、涂装环境温度太高 涂装环境温度太高。 5、使用稀释剂挥发速度太快 使用稀释剂挥发速度太快。 1、按照涂装工艺卡,设置雾化空气流量 设置雾化空气流量 2、降低清漆喷涂流量 降低清漆喷涂流量,调整喷涂程序。 3、按照涂装工艺卡正确设定流平时间 按照涂装工艺卡正确设定流平时间。 4、确保喷涂环境温度在涂装工艺卡规定的范围内 确保喷涂环境温度在涂装工艺卡规定的范围内。 5、按照调漆工艺卡调配油漆 按照调漆工艺卡调配油漆,必要时加入慢干剂。 1、 采用1000 1000目的砂纸对缺陷处砂磨 目的砂纸对缺陷处砂磨,再用抛光机进行抛光。 2、情况严重时 情况严重时,用800目砂皮将表面磨平后重新喷
原因: 原因
损。 1、油漆受到污染(含有丝状物 含有丝状物)。 2、喷房、流平间 流平间、烘箱顶棉纤维丝含量过高或滤网受 3、机械手防护服饰 机械手防护服饰、臂套存在纤维丝。 4、喷涂过程风向不符合要求 喷涂过程风向不符合要求。 5、进出喷房工作人员防护服饰存在纤维丝 进出喷房工作人员防护服饰存在纤维丝。 1、进货检验对油漆进行过滤 进货检验对油漆进行过滤,检测油漆内是否含有丝状物。 2、按照清洗保养计划 按照清洗保养计划,定期检查滤网使用状况。 3、机械手防护服饰 机械手防护服饰、臂套等应由不含纤维丝原材料制 成。 4、对喷涂过程各关键点的风向定期监督 对喷涂过程各关键点的风向定期监督。 5、操作员进入喷房必须有相应的防护措施 操作员进入喷房必须有相应的防护措施,防尘服应
国际油漆产品及配套
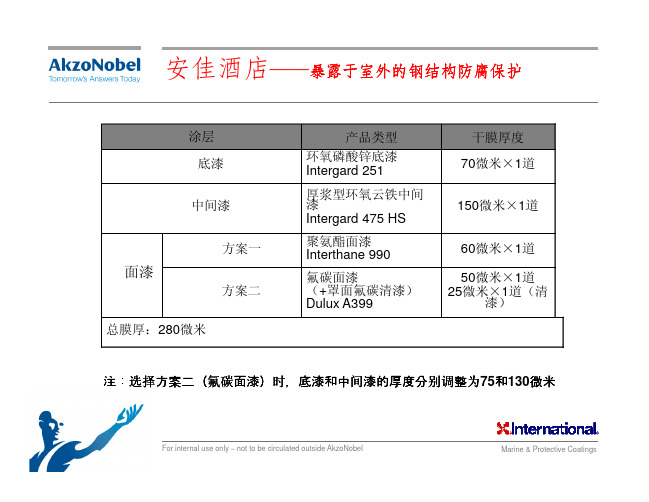
环氧磷酸锌底钝化作用
面漆 中间漆 磷酸锌底漆 钢铁基材
For internal use only – not to be circulated outside AkzoNobel
Marine & Protective Coatings
环氧云铁中间漆的防腐蚀机理
潮湿气、 潮湿气、电解质等
粘结剂与颜料相结合使得外界 的潮气、湿气和电解质进入的 路径变得曲折、困难。
2-3
280
For internal use only – not to be circulated outside AkzoNobel
Marine & Protective Coatings
配套特点
3) 选择高固体份含量产品 例如:环氧云铁中间漆 Intergard 475HS 体积固体份 80%
安佳酒店——暴露于室外的钢结构防腐保护
涂层 底漆 中间漆 方案一 产品类型 环氧磷酸锌底漆 Intergard 251 厚浆型环氧云铁中间 漆 Intergard 475 HS 聚氨酯面漆 Interthane 990 氟碳面漆 (+罩面氟碳清漆) Dulux A399 干膜厚度 70微米×1道 150微米×1道 60微米×1道 50微米×1道 25微米×1道(清 漆)
Marine & Protective Coatings
预定用途-埋设结构物( 预定用途-埋设结构物( Im3 )
• 优异的抗机械损伤性能以及与阴极保护系统的相容性,使Interzone 278可用于埋设在地下的结构件上 • 一般用于埋设管道和储罐外部
For internal use only – not to be circulated outside AkzoNobel
Intergard269
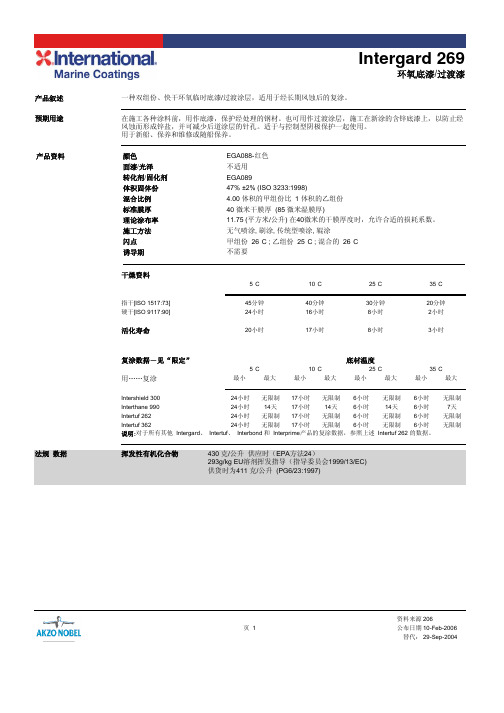
干燥资料
指干[ISO 1517:73] 硬干[ISO 9117:90]
活化寿命
5°C
45分钟 24小时
20小时
10°C
40分钟 16小时
17小时
25°C
30分钟 8小时
8小时
35°C
20分钟 2小时
3小时
复涂数据-见“限定” 用……复涂
5°C
最小
最大
10°C
最小
最大
底材温
最小
作为临时底漆,用于压载水舱。 浸水使用: 磨光所有焊接处、锐边和凸出部分,使其光滑圆润,并在进行喷砂清理前除去所有焊渣。 采用磨料喷砂清理至 Sa2.5 (ISO 8501-1:1988)标准。如果在喷砂和施工 Intergard 269 之间已发生氧化,表面 则应再行喷砂至规定的图片标准。 喷砂清理过程中暴露出来的表面缺陷,应打磨、嵌填或采用合适的方法进行处理。 小区域可通过动力工具处理至Pt3 (JSRA SPSS:1984)。 作为临时底漆,用于压载舱以外的其他区域。 磨料喷砂清理至Sa2.5 (ISO 8501-1:1988)标准。如果在喷砂和施工Intergard 269之间已发生氧化,表面应再行喷 砂处理至规定的图片标准。喷砂清理过程中暴露出来的表面缺陷,应打磨、嵌填或采用合适的方法进行处理。 Intergard 269 可施工在处理至 “国际油漆 (International Paint)水力喷砂标准 HB2”标准的表面上,会出现闪 锈,对于水下船壳/水线区域不比HB2L 差,或对于水上区域则不比HB2M差。 小区域可通过动力工具处理至Pt3 (JSRA SPSS:1984)。 作为过渡涂层,用于含锌底漆上。 底漆表面应清洁、干燥且无任何污染物,破损、损坏等区域应处理至规定的标准 (例如: Sa2.5 (ISO 85011:1988) 。应在规定的复涂间隔时间内采用Intergard 269 进行复涂(请查阅相关的产品数据手册)。 为避免在涂有含锌底漆的表面出现针孔,Intergard 269应用国际牌GTA220进行15-25%的稀释。
SSPC油漆标准(中文译稿)
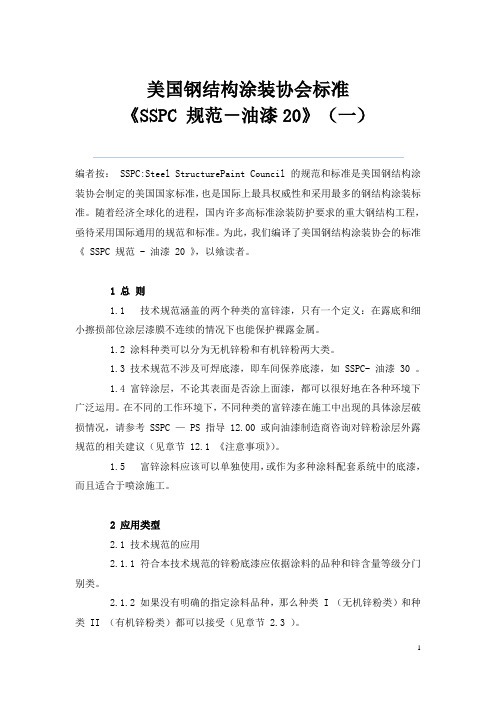
美国钢结构涂装协会标准《SSPC 规范-油漆20》(一)编者按: SSPC:Steel StructurePaint Council 的规范和标准是美国钢结构涂装协会制定的美国国家标准,也是国际上最具权威性和采用最多的钢结构涂装标准。
随着经济全球化的进程,国内许多高标准涂装防护要求的重大钢结构工程,亟待采用国际通用的规范和标准。
为此,我们编译了美国钢结构涂装协会的标准《 SSPC 规范 - 油漆 20 》,以飨读者。
1 总则1.1 技术规范涵盖的两个种类的富锌漆,只有一个定义:在露底和细小擦损部位涂层漆膜不连续的情况下也能保护裸露金属。
1.2 涂料种类可以分为无机锌粉和有机锌粉两大类。
1.3 技术规范不涉及可焊底漆,即车间保养底漆,如 SSPC- 油漆 30 。
1.4 富锌涂层,不论其表面是否涂上面漆,都可以很好地在各种环境下广泛运用。
在不同的工作环境下,不同种类的富锌漆在施工中出现的具体涂层破损情况,请参考 SSPC — PS 指导 12.00 或向油漆制造商咨询对锌粉涂层外露规范的相关建议(见章节 12.1 《注意事项》)。
1.5 富锌涂料应该可以单独使用,或作为多种涂料配套系统中的底漆,而且适合于喷涂施工。
2 应用类型2.1 技术规范的应用2.1.1 符合本技术规范的锌粉底漆应依据涂料的品种和锌含量等级分门别类。
2.1.2 如果没有明确的指定涂料品种,那么种类 I (无机锌粉类)和种类 II (有机锌粉类)都可以接受(见章节 2.3 )。
2.1.3 如果没有明确规定具体的锌含量,那么锌粉含量等级 1 、 2 和 3 都是可以接受的(见章节 2.3 )。
该种类锌粉底漆可以由 (1 ~ 3) 种成分构成。
2.2 组成本技术规范所述的富锌涂料,一般含有金属锌粉、功能性添加剂(助剂),以及有机或无机的油漆主剂和相应的溶剂(见章节 12.2 《注意事项》)。
2.3 油漆主剂的类型2.3.1 种类 I-A : 2 次硬化类无机锌粉涂料 / 水溶性无机锌粉。
Interprime 198

Interprime 198不适合作为防护涂料,用来为老化的氧化橡胶漆和乙烯漆升级。
如果用于海洋环境中,可能要调整漆料配套方案和重涂间隔。有Inteperime 198成分的配套涂料不适 用于水下设备。
Interprime 198通常用于喷射清理或者人工/动力处理的钢材表面。但是,它也适合涂覆在下列底漆 上,并可以作为补漆,用于原有的可转换涂料。
涂覆方法
无气喷涂、空气喷涂、刷涂、滚涂
干燥时间
推荐面漆
重涂间隔
温度
表干
硬干
最小
最大
5℃(41°F) 15℃(59°F) 25℃(77°F) 40(104°F )
3小时 90分钟 60分钟 30分钟
8小时 3小时 2小时 1小时
6小时 3小时 2小时 1小时
无限制* 无限制* 无限制* 无限制*
*参见国际油漆公司工业防护漆部门的《定义与缩略语》
混合
本产品是单组份涂料,每次涂覆之前都必须用动力搅拌器彻底搅 拌。
混合比例
不适用
混合使用寿命
不适用
无气喷涂
推荐使用
-喷嘴直径0.43-0.53毫米(17-21毫英寸) -喷嘴处油漆压力不低于176千克/平方厘米
空气喷涂
(带压力罐)
推荐使用
喷枪 空气量 喷嘴
DeVilbiss MBC或JGA 704或765 E
维修保养与现场修补 本产品用于处理至St2(ISO 8501-1:2007)或者SSPC-SP2标准的表面。使用动力工具时,应该注意避 免对表面进行抛光。本产品也适合经过扫砂清理、达到Sa1(ISO 8501-1:2007) SSPC-SP7标准的表 面。在不良表面,用涂刷方式涂覆可提高涂层性能。 Interprime 198适合在大多数老化涂层上涂覆。疏松或剥落的涂层应该刮除,直至牢固的漆层暴露为 止。光滑的环氧树脂和聚氨酯涂层需要进行拉毛处理。
阿克苏诺贝尔 国际油漆 产品说明书Interchar 973

Copyright © AkzoNobel, 2010
以及‘国际’一词是商标。
混合
本涂料是单组份涂料,施工前采用电动搅拌器彻底搅拌。
混合比例
不适用
混合使用寿命
不适用
无气喷涂
推荐使用
-喷涂直径0.48-0.58毫米(19-23毫英寸) -喷嘴处的输出流体总压力不低于246公斤/平方厘米
空气喷涂
(带压力罐)
刷涂
滚涂
不推荐使用 适用-仅限小面积区域 不推荐使用
厚度一般可达到200-400微米 (8.0-16密耳)
干燥时间 温度
表干#
硬干#
采用Interchar973进行自身
复涂时的复涂间隔时间
最小
最大
25℃(77°F)
2小时
24小时
40℃(104°F)
1小时
20小时
参见国际油漆公司工业防护漆部门的《定义与缩略语》
24小时 20小时
无限制* 无限制*
下列底漆经过核准可与Interchar 973一起使用:
Intergard 251
产品特性 系统配套性
Interchar® 973
丙烯酸膨胀型防火涂料
使用前应参考Interchar 973的施工工艺。
采用无气喷涂方法进行施工,可获得最佳结果,一道涂层即达到最高膜厚。采用无气喷涂以外的其它 方法进行施工。未必能达到所要求的膜厚。在低温或高温等情况下,为了达地到最高膜厚,可能需要 特殊的施工方法.Interchar 973的过度施工会延长最短复涂间隔时间及搬运时间。
Interchar 973的干燥时间与施工膜厚、湿度和通风速率相关。
国际牌油漆部分介绍

Intergard 740环氧面漆产品叙述一种双组份环氧面漆。
预期用途一种装饰面漆,用于水线以上区域。
用于新船、保养和维修或随船保养。
产品资料颜色ECB000-白色, ECK724-风暴灰, ECL274-红色, ECL549-标志绿, ECY999-黑色和多种颜色面漆/光泽高光泽转化剂/固化剂ECA914体积固体份51% ±3% (ISO 3233:1998)混合比例 4.00 体积的甲组份比 1 体积的乙组份标准膜厚50 微米干膜厚 (98 微米湿膜厚)理论涂布率10.20 (平方米/公升) 在40微米的干膜厚度、51%的体积固体份时,允许合适的损耗系数。
施工方法无气喷涂, 刷涂, 传统型喷涂, 辊涂闪点甲组份27°C ; 乙组份29°C ; 混合的28°C诱导期温度低于25°C时,30分钟干燥资料5°C 10°C 25°C 35°C指干[ISO 1517:73] 16小时12小时3小时2小时硬干[ISO 9117:90] 54小时40小时16小时12小时活化寿命12小时11小时8小时3小时复涂数据-见“限定”底材温度5°C 10°C 25°C 35°C用……复涂最小最大最小最大最小最大最小最大Intergard 740 54小时无限制 40小时无限制 16小时无限制 12小时无限制法规数据挥发性有机化合物420 克/公升供应时(EPA方法24)344g/kg EU溶剂挥发指导(指导委员会1999/13/EC)页 1资料来源196公布日期3-Sep-2004替代Intergard 423环氧防锈漆产品叙述一种不含沥青、淡色环氧涂料,可在温度低至-5°C (23°F)的冬天使用。
预期用途作为防锈漆适用于压载舱,隔离舱和空舱,适用于控制型阴极保护。
Interthane 990
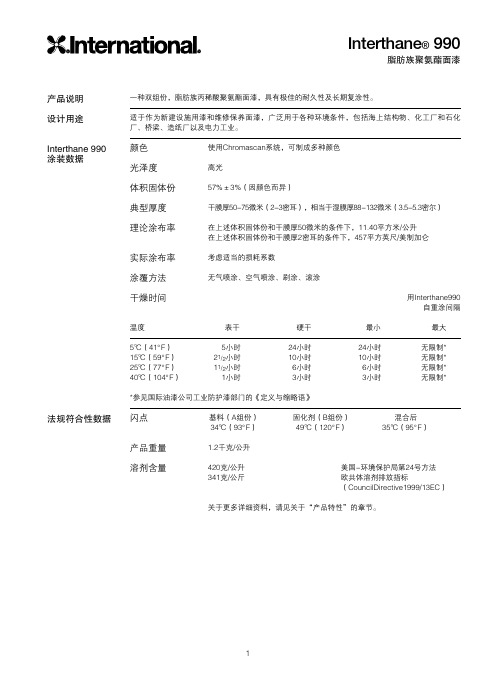
使用Chromascan系统,可制成多种颜色 高光 57%±3%(因颜色而异) 干膜厚50-75微米(2-3密耳),相当于湿膜厚88-132微米(3.5-5.3密尔) 在上述体积固体份和干膜厚50微米的条件下,11.40平方米/公升 在上述体积固体份和干膜厚2密耳的条件下,457平方英尺/美制加仑 考虑适当的损耗系数 无气喷涂、空气喷涂、刷涂、滚涂 用Interthane990 自重涂间隔 表干 5小时 21/2小时 11/2小时 1小时 硬干 24小时 10小时 6小时 3小时 最小 24小时 10小时 6小时 3小时 最大 无限制* 无限制* 无限制* 无限制*
施工
混合
本产品分两罐装,组成一个单元。每次都必须按规定的配比,成 对一次性混合,并在规定的混合使用期限内用完。 (1)用动力搅拌器搅拌基料(A) (2)将全部的固化剂(B)和基料(A)调和在一起,用动力搅拌器彻底 搅拌。 体积比6:1 -5℃(23° F) 5℃(41° F) 26小时 12小时 推荐使用 推荐使用 推荐使用 适合 适合
清洗
Interthane® 990
脂肪族聚氨酯面漆 产品特性
Interthane 990可制成多种金属色,详情请查询Interthane 990金属面漆建议。尽可能避免多种涂覆方法混用。采用传统式空气喷涂法,可 以获得最佳的光泽和外观。 采用刷涂和滚涂时,以及使用某些颜色时,可能需要涂覆两道Interthane 990才能保证颜色一致。用 Interthane 990涂覆于深色底漆以及使用某些无铅的鲜艳颜色(如黄色和橙色)时,尤其如此。最好 是在Interthane 990下面先涂一层颜色相容的中间漆或防腐漆。 风化或老化后重涂时,务必彻底处理原有涂层,去除表面的污染物,如油脂、盐晶、道路烟尘等,然 后再重涂Interthane 990。 涂覆于老化过的Interthane 990的涂层间附着力有所下降,但是仍可满足规定用途的需要。 本产品必须用推荐使用的Interantonal稀释剂稀释。如果使用其它稀释剂,尤其是含乙醇的稀释剂, 会严重影响涂层的固化机制。 表面温度必须始终保持在露点以上至少3℃( 5° F) 。 在封闭空间内使用Interthane 990时,必须确保良好的通风。 涂覆过程中或刚刚涂覆完表面就发生水汽冷凝,会使表面失去光泽,膜质变差。 未完全固化时碰到积水会导致变色,深色和低温条件下尤其如此。 本产品不适用于水下。如果漆膜需耐化学品或溶剂可能发生的严重飞溅,请与国际油漆公司工业防护 漆部门联系,索取有关适用性的资料。 为了提高可操作性,一种Interthane 990的改性品种,已经用于韩国市场。 备注:VOC数值是基于该产品的最大可能值给出的,该数值可能因为颜色不同和一般生产容差的不 同而有所差异。 虽然低分子量的反应性助剂在正常环境条件下固化会成为漆膜的一部分,但是通过采用EPA Method24检测分析发现,它也会影响VOC值。
国际油漆船舶涂料指南说明书

Marine Paint GuideUpdated: 16/12/141. Definitions and abbreviationsTOLERANCESThe numerical information quoted on marine product datasheets has been derived from laboratory test data obtained under controlled conditions for the products described. Whilst every effort has been made to ensure accuracy, this information will be subject to minor variations obtained in normal manufacturing tolerances, and any fluctuations in ambient conditions during the application and curing periods.GLOSS LEVELTypical gloss values have been determined in accordance with ISO2813:1994/ Corr 1:1997 using a 60° gloss head or, for North America,ASTM-D-523. The categories used in the data sheet are:Finish (sheen)Gloss (60°) headMatt0-15Eggshell16-30Semi-gloss31-60Gloss61-85High gloss>85In practice, the level of sheen and surface finish will be dependent upon a number of factors, including application and the condition of the surface to be overcoated.DRY FILM THICKNESS(DFT)The measured thickness of the final dried film applied to the substrate.WET FILM THICKNESS (WFT)The initial thickness of the wet coating applied to the substrate.VOLUME SOLIDSThe volume solids figure given on the product data sheet is the percentage of the wet film, which remains as the dry film, and is obtained from a given wet film thickness under specified application method and conditions. These figures have been determined under laboratory conditions using a modification of the test method described in ISO 3233:1998/Corr 1:1999 –Determination of Volume Solids by Measurement of Dry Film Density. The modification is technically equivalent involving the use of slightly smaller glass slides. For North America, volume solids are measured by ASTM-D-2697 (1986) which determines the volume solids of a coating using the recommended dry film thickness of the coating quoted on the product data sheet, and a specified drying schedule at ambient temperature, i.e. 7 days at 25°C + 1°C.DRYING TIMEThe drying times quoted in the product data sheet have beendetermined in the laboratory using a typical dry film thickness, the ambient temperature quoted in the relevant product data sheet, and the appropriate testmethod, i.e.Touch Dry (ISO 1517 - 1973) - The surface drying state of a coating when Ballotini (small glass spheres) can be lightly brushed away without damaging the surface of the coating.Hard Dry (ISO 9117-1990) - The condition of the film in which it is dry throughout its thickness, as opposed to that condition in which the surface of the film is dry but the bulk of the coating is still mobile.This through drying state is determined by the use of a “mechanical thumb” device “in situ”at the temperature quoted.In North America the Touch Dry, Hard Dry and Re-coat times are determined in accordance with ASTM-D-1680 (1995) using sections7.5, 7.7 and 7.8 respectively.The drying times achieved in practice may show some slight fluctuation,particularly in climatic conditions where the substrate temperature differs significantly from the ambient air temperature and because of variations in practical dry film thickness.OVERCOATING INTERVALThe product data sheet gives both a “minimum” and a “maximum”overcoating interval and the figures quoted at the various temperatures are intended as guidelines, consistent with good painting practices.Certain terms require elaboration as follows:MinimumThe “minimum overcoating time” quoted is an indication of the time required for the coating to attain the necessary state of dryness and hardness to allow the application of a further coat of paint without the development of any film irregularities such as lifting or loss of adhesion of the first coat (ASTM-D-1640). It assumes:(i)the coating has been applied at the normal recommended thickness.(ii)environmental conditions both during and after application were as recommended forthat particular coating, especially in respect of temperature, relative humidity andventilation.(iii)the paint used for overcoating is suitable for that purpose.(iv)an understanding of the “method of application”. For example, if a coating can be applied by both brush and spray it is expected that overcoating may be carried outmore rapidly if sprayed and it is the “lowest” figure that is quoted.If the above conditions are not met, the quoted minimum overcoating times are liable to variation and will invariably have to be extended.MaximumThe “maximum overcoating time” indicates the allowable time period within which overcoating should take place in order to ensure acceptable intercoat adhesion is achieved.ExtendedWhere an “extended” overcoating time is stated, the anticipated level of intercoat adhesion can only be achieved if:(i) the coating has been applied in accordance with good painting practices and at the specified film thickness.(ii) the aged coating has the “intended” surface characteristics required for long term overcoatability. For example, an over- applied epoxy MIO may not have its usual “textured”surface and will no longer be overcoatable after ageing unless it is abraded.(iii) the coating to be overcoated must be intact, tightly adherent, clean, dry and free from all contaminants. For example, the leached layer on an antifouling coating is usually porous and friable and must be removed to provide the necessary surface for overcoating.(iv) coatings having a glossy surface which could have a detrimental effect on the adhesion of subsequent coats should be treated by light surface abrasion, sweep blasting, or other suitable processes which will not cut through or detract from the performance of the underlying coating.(v) in some situations, and with specific products, it may be necessary to high pressure fresh water wash prior to overcoating.It should be recognised that the level of intercoat adhesion obtained is also dependent upon the chemistry of the “topcoat”. By their nature,primers or undercoats will have inherently better adhesion than finish coats.The measurement of ultimate “adhesion strength” can often be a difficult process, and interpretation of results can be subjective. Excellent adhesion does not necessarily mean good performance, nor does relatively poor adhesion necessarily mean poor performance.Although the adhesion of coatings applied to aged / cured coatings may be deemed satisfactory for the specified end use, actual numerical values obtained for adhesion may be less than with coatings applied within“minimum / short” overcoating intervals.FLASH POINTThe minimum temperature at which a product, when confined in a Setaflash closed cup, must be heated for the vapours emitted to ignite momentarily in the presence of aflame (ISO 3679:1983). In North America Flash Point is determined in accordance with ASTM-D-3278(1996).VOLATILE ORGANIC COMPOUND (VOC)VOC content is the weight of volatile organic compounds which participate in atmospheric photochemical reactions for litre of paint.Legislative requirements differ from country to country, and from region to region, and are constantly being reviewed. Values quoted for VOC on the product data sheet are calculated from the product formulation or have been determined practically in the laboratory using one of the following published test methods:-UK-PG6/23(92), Appendix 3This test method was published in February 1992, by the UK Department of the Environment as part of the Secretary of State’s Guidance Note(PG6/23(92)), issued as a guide to local authorities on the appropriate techniques to control air pollution, in order to achieve the objectives laid down in the Environmental Protection Act 1990. The method described in Appendix 3 includes guidance on the method of meeting VOC of coatings, as applied to demonstrate compliance with Clause 19 of the Guidance Note.USA - EPA Federal Reference Method 24The Environmental Protection Agency (EPA), published procedures for demonstration of compliance with VOC limits under Federal Reference Method 24 “The Determination of Volatile Matter Content, Density,Volume Solids and Weight Solids of Surface Coatings”. This method was originally published in the Federal Register in October 1980, and coded40 CFR, Part 60, Appendix A, and amended in 1992 to incorporate instructions for dealing with multi-component systems, and a procedure for the quantitative determination of VOC exempt solvent.It is recommended that users check with local agencies for details of current VOC regulations, to ensure compliance with any local legislative requirements when proposing the use of any coating.EU Council Directive 1999/13/ECThe purpose of this directive is to prevent or reduce the direct and indirect effects of the emission of volatile organic compounds into the environment, mainly into air, and the potential risks to human health. In essence the directive sets emission limits for coatings users(installations), these differ by application and for old/new installations. For the purpose of the Directive a Volatile Organic Compound (VOC) is defined as:“Any organic compound having at 293.15 K a vapour pressure of 0.01kPa or more, or having a corresponding volatility under the particular conditions of use.”WORKING POT LIFEThe maximum time during which the product supplied as separate components should be used after they have been mixed together at the specified temperature.The values quoted have been obtained from a combination of laboratory tests, and application trials, and refer to the time periods under which satisfactory coating performance will be achieved.Application of any product after the working pot life has been exceeded will lead to inferior product performance, and must NOT be attempted,even if the material in question appears liquid in the can.SHIPPING WEIGHTThe shipping weights quoted are typical values and refer to the total weight of the product supplied plus the weight of the can and are for guidance only. They will vary according to the specific colour. These weights are quoted for individual components and do not take into account any additional packaging weight attributable to cartons, etc. Factory supplied material will show differences to the figures quoted on the product Technical Data Sheet.SHELF LIFEThe shelf life quoted on the product datasheets is generally a conservative value, and it is probable that the coating can be applied without any deterioration in performance after this period has elapsed.Exceeding the shelf life of a product does not necessarily render it unusable. However, if the specified shelf life has been exceeded, it is recommended that the condition of the material is checked before any large scale application is undertaken using materials beyond the quoted shelf life. If this occurs, contact International for advice on how to progress.。
国际通用表面处理标准对比
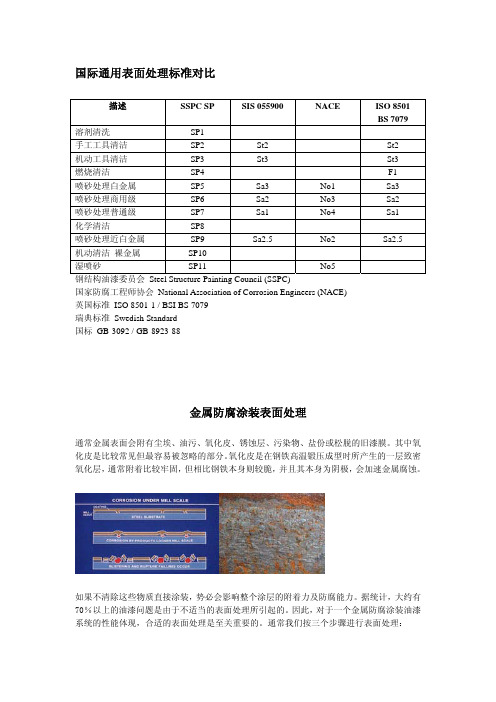
国际通用表面处理标准对比描述SSPC SP SIS 055900 NACE ISO 8501BS 7079溶剂清洗 SP1手工工具清洁SP2 St2 St2机动工具清洁SP3 St3 St3燃烧清洁 SP4 F1 喷砂处理白金属SP5 Sa3 No1 Sa3喷砂处理商用级SP6 Sa2 No3 Sa2喷砂处理普通级SP7 Sa1 No4 Sa1化学清洁 SP8喷砂处理近白金属SP9 Sa2.5 No2 Sa2.5机动清洁裸金属 SP10湿喷砂 SP11 No5钢结构油漆委员会Steel Structure Painting Council (SSPC)国家防腐工程师协会National Association of Corrosion Engineers (NACE)英国标准ISO 8501-1 / BSI BS 7079瑞典标准 Swedish Standard国标GB-3092 / GB-8923-88金属防腐涂装表面处理通常金属表面会附有尘埃、油污、氧化皮、锈蚀层、污染物、盐份或松脱的旧漆膜。
其中氧化皮是比较常见但最容易被忽略的部分。
氧化皮是在钢铁高温锻压成型时所产生的一层致密氧化层,通常附着比较牢固,但相比钢铁本身则较脆,并且其本身为阴极,会加速金属腐蚀。
如果不清除这些物质直接涂装,势必会影响整个涂层的附着力及防腐能力。
据统计,大约有70%以上的油漆问题是由于不适当的表面处理所引起的。
因此,对于一个金属防腐涂装油漆系统的性能体现,合适的表面处理是至关重要的。
通常我们按三个步骤进行表面处理:a) 铲除各种松脱物质;b) 溶剂清洗除去油脂;c) 使用各种手工或电动工具或喷砂等方法处理表面至上漆标准。
在附录A中,列出了SSPC表面处理标准。
在决定表面处理等级标准前,还需界定表面锈蚀等级。
在附录B中,我们列出了各锈蚀等级及喷砂处理后的图片。
在附录C中,还列出了各不同国际组织表面处理标准的相关联系。
Interdur 8800环氧油漆产品说明书
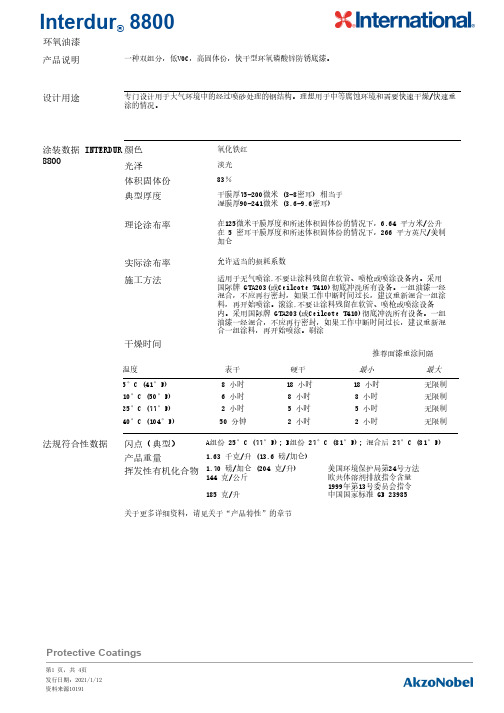
一种双组分,低VOC,高固体份,快干型环氧磷酸锌防锈底漆。
产品说明专门设计用于大气环境中的经过喷砂处理的钢结构。
理想用于中等腐蚀环境和需要快速干燥/快速重涂的情况。
设计用途氧化铁红淡光83%干膜厚75-200微米 (3-8密耳) 相当于 湿膜厚90-241微米 (3.6-9.6密耳)在125微米干膜厚度和所述体积固体份的情况下,6.64 平方米/公升在 5 密耳干膜厚度和所述体积固体份的情况下,266 平方英尺/美制加仑允许适当的损耗系数适用于无气喷涂,不要让涂料残留在软管、喷枪或喷涂设备内。
采用国际牌 GTA203(或Ceilcote T410)彻底冲洗所有设备。
一组油漆一经混合,不应再行密封,如果工作中断时间过长,建议重新混合一组涂料,再开始喷涂。
滚涂,不要让涂料残留在软管、喷枪或喷涂设备内。
采用国际牌 GTA203(或Ceilcote T410)彻底冲洗所有设备。
一组油漆一经混合,不应再行密封,如果工作中断时间过长,建议重新混合一组涂料,再开始喷涂。
刷涂涂装数据 INTERDUR 8800颜色光泽体积固体份典型厚度理论涂布率实际涂布率施工方法干燥时间温度表干硬干最小最大推荐面漆重涂间隔5°C (41°F) 8 小时18 小时18 小时 无限制10°C (50°F) 6 小时8 小时8 小时 无限制25°C (77°F) 2 小时 5 小时 5 小时 无限制40°C (104°F)50 分钟2 小时2 小时无限制A组份 25°C (77°F); B组份 27°C (81°F); 混合后 27°C (81°F)1.63 千克/升 (13.6 磅/加仑)法规符合性数据闪点(典型)产品重量挥发性有机化合物关于更多详细资料,请见关于“产品特性”的章节1.70 磅/加仑 (204 克/升)美国环境保护局第24号方法144 克/公斤欧共体溶剂排放指令含量1999年第13号委员会指令185 克/升中国国家标准 GB 23985第1 页,共 4页资料来源10191发行日期:2021/1/12Protective Coatings这个产品的性能取决于表面处理的等级。
涂料涂装相关标准与规范
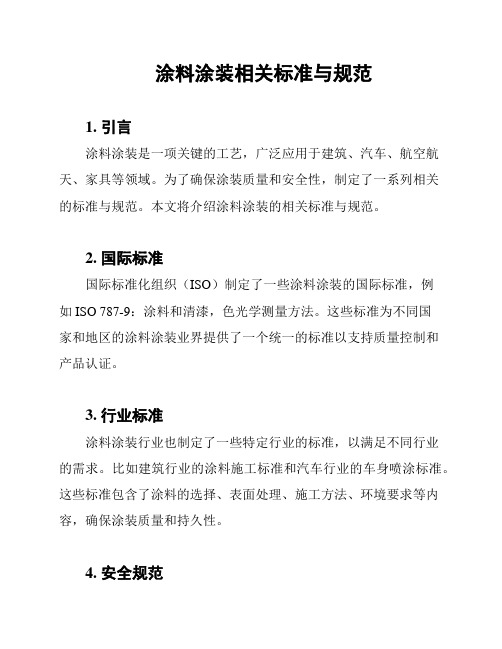
涂料涂装相关标准与规范1. 引言涂料涂装是一项关键的工艺,广泛应用于建筑、汽车、航空航天、家具等领域。
为了确保涂装质量和安全性,制定了一系列相关的标准与规范。
本文将介绍涂料涂装的相关标准与规范。
2. 国际标准国际标准化组织(ISO)制定了一些涂料涂装的国际标准,例如 ISO 787-9:涂料和清漆,色光学测量方法。
这些标准为不同国家和地区的涂料涂装业界提供了一个统一的标准以支持质量控制和产品认证。
3. 行业标准涂料涂装行业也制定了一些特定行业的标准,以满足不同行业的需求。
比如建筑行业的涂料施工标准和汽车行业的车身喷涂标准。
这些标准包含了涂料的选择、表面处理、施工方法、环境要求等内容,确保涂装质量和持久性。
4. 安全规范涂料涂装涉及到化学物质和工艺操作,因此安全是非常重要的。
相关的安全规范包括涂料成分的限制、工人的防护措施、作业环境的要求等。
这些规范旨在保护工人的健康和安全,并防止环境污染。
5. 质量控制为了确保涂料涂装的质量,需要进行严格的质量控制。
检测涂料的物理性能、化学成分和色彩稳定性等是质量控制的关键环节。
标准化的测试方法和设备可以保证测试结果的准确性和可比性。
6. 环境要求涂料涂装对于环境的影响也被重视。
涂料的生产和使用过程中需要遵守环境保护的法规和标准。
例如,一些国家规定涂料必须符合低VOC(挥发性有机物)的要求,以减少空气污染和温室气体排放。
7. 总结涂料涂装相关的标准与规范是为了确保涂装质量、安全性和环境保护而制定的。
行业从业者应熟悉并遵守这些标准与规范,以提高涂料涂装的质量、效率和可持续发展。
以上就是涂料涂装相关标准与规范的简要介绍,希望对您有所帮助。
SSPC规范_油漆20
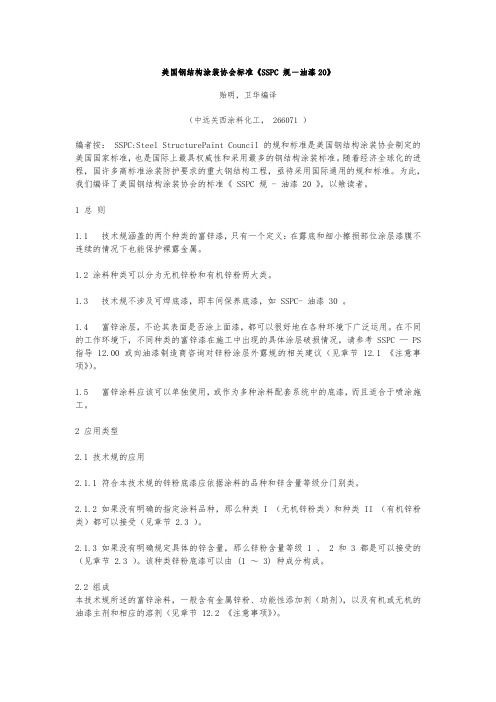
美国钢结构涂装协会标准《SSPC 规-油漆20》贻明,卫华编译(中远关西涂料化工, 266071 )编者按: SSPC:Steel StructurePaint Council 的规和标准是美国钢结构涂装协会制定的美国国家标准,也是国际上最具权威性和采用最多的钢结构涂装标准。
随着经济全球化的进程,国许多高标准涂装防护要求的重大钢结构工程,亟待采用国际通用的规和标准。
为此,我们编译了美国钢结构涂装协会的标准《 SSPC 规 - 油漆 20 》,以飨读者。
1 总则1.1 技术规涵盖的两个种类的富锌漆,只有一个定义:在露底和细小擦损部位涂层漆膜不连续的情况下也能保护裸露金属。
1.2 涂料种类可以分为无机锌粉和有机锌粉两大类。
1.3 技术规不涉及可焊底漆,即车间保养底漆,如 SSPC- 油漆 30 。
1.4 富锌涂层,不论其表面是否涂上面漆,都可以很好地在各种环境下广泛运用。
在不同的工作环境下,不同种类的富锌漆在施工中出现的具体涂层破损情况,请参考 SSPC — PS 指导 12.00 或向油漆制造商咨询对锌粉涂层外露规的相关建议(见章节 12.1 《注意事项》)。
1.5 富锌涂料应该可以单独使用,或作为多种涂料配套系统中的底漆,而且适合于喷涂施工。
2 应用类型2.1 技术规的应用2.1.1 符合本技术规的锌粉底漆应依据涂料的品种和锌含量等级分门别类。
2.1.2 如果没有明确的指定涂料品种,那么种类 I (无机锌粉类)和种类 II (有机锌粉类)都可以接受(见章节 2.3 )。
2.1.3 如果没有明确规定具体的锌含量,那么锌粉含量等级 1 、 2 和 3 都是可以接受的(见章节 2.3 )。
该种类锌粉底漆可以由 (1 ~ 3) 种成分构成。
2.2 组成本技术规所述的富锌涂料,一般含有金属锌粉、功能性添加剂(助剂),以及有机或无机的油漆主剂和相应的溶剂(见章节 12.2 《注意事项》)。
2.3 油漆主剂的类型2.3.1 种类 I-A : 2 次硬化类无机锌粉涂料 / 水溶性无机锌粉。
国际油漆资料

• 绿色建筑涂料需求增长,如低VOC、环保型涂料 • 建筑外墙涂料市场需求增长,如高性能、耐候性涂料
汽车涂料市场需求及趋势
市场需求
• 2020年全球汽车涂料市场规模达到300亿美元 • 2021年全球汽车涂料市场规模预计将达到320亿美元 • 2022年全球汽车涂料市场规模预计将达到340亿美元
环保型油漆研发
• 低VOC、低污染涂料 • 水性涂料 • 高固含量涂料
应用领域
• 建筑涂料 • 汽车涂料 • 工业涂料
智能化油漆的生产与推广
智能化油漆生产
• 自动化生产线 • 机器人技术 • 大数据分析
推广领域
• 建筑涂料 • 汽车涂料 • 工业涂料
多功能油漆的研发与市场前景
多功能油漆研发
• 耐候性涂料 • 防腐性涂料 •规模达到100亿美元 • 2021年全球聚酯树脂市场规模预计将达到110亿美元 • 2022年全球聚酯树脂市场规模预计将达到120亿美元
发展趋势
• 聚酯树脂产品差异化竞争,提高产品附加值 • 聚酯树脂绿色化发展,降低环境污染
04
国际油漆技术创新与发展方向
环保型油漆的研发与应用
市场前景
• 建筑涂料 • 汽车涂料 • 工业涂料
05
国际油漆市场发展前景及建议
全球油漆市场发展机遇与挑战
发展机遇
• 绿色建筑涂料需求增长 • 汽车涂料智能化生产 • 工业涂料高性能化
挑战
• 环保法规日益严格 • 原材料价格波动 • 市场竞争加剧
国际油漆市场发展战略及建议
发展战略
• 产品差异化竞争 • 绿色化发展 • 智能化生产
THANK YOU FOR WATCHING
谢谢观看
国际油漆697说明书

国际油漆697说明书国际油漆697说明书导语:国际油漆697是一种高性能涂料,在各类工业、建筑和船舶领域有广泛应用。
本文将从产品概述、使用范围、涂装方法、喷涂参数和注意事项等多个方面进行介绍,以帮助大家更好地了解和使用该产品。
一、产品概述国际油漆697是由环氧树脂、氨基树脂、活性填料和有机溶剂等原料制成的涂料。
该产品具有耐磨、耐腐蚀、耐化学品、耐水、耐静电等特点,具有广泛的应用前景。
二、使用范围国际油漆697适用于船舶、海洋工程、桥梁、钢水槽、炼油、化工、发电、食品等领域的保护和装饰涂装。
特别是在海洋环境中,其抗腐蚀性能得到了广泛认可,成为海洋工业中的首选涂料。
三、涂装方法国际油漆697可采用刷涂、辊涂、喷涂等多种涂装方式,可以单层或多层涂装。
在船舶领域中,通常采用喷涂方式涂装,可节约时间和人工成本,并且能够有效地防止涂膜出现气泡和起皮等缺陷。
四、喷涂参数在喷涂国际油漆697时,需要注意喷涂机的选用、压力的控制、喷嘴的选择、干燥时间的掌握等因素。
建议使用无气喷涂机进行喷涂,压力控制在0.3~0.5MPa之间,喷嘴的大小与涂膜厚度相对应,干燥时间为25℃下12小时。
五、注意事项在使用国际油漆697时,需要注意以下事项:1.在涂装过程中,应注意工作环境的湿度、温度等因素,以避免出现涂膜发白、粘度过高或过低等问题。
2.涂装前应对基材进行处理,去除表面油渍、锈迹和腐蚀物,以提高涂膜附着力和防腐性能。
3.在涂装过程中,应注意防止涂膜出现气泡、起皮等缺陷,以保证涂膜质量。
4.涂装后应对涂层进行检查和测试,以确保涂层质量符合要求。
结论:国际油漆697是一种性能优异的涂料,具有广泛的应用范围和市场前景。
在涂装过程中,需要遵循相应的涂装方法和注意事项,以确保涂膜质量和涂层效果的稳定性。
涂装材料的相关标准

常用标准主要内容
涂装材料的相关标准
ISO12944-7 色漆和清漆涂装涂层腐蚀防护系统第7部分涂装的实施和监督
4作业用涂料
4.1 作业用涂料的供应
所供作业用涂料必须满足在订货时已经说明的欲采用涂装方法的要求。
涂料生产商应该提供其施工时依照的具体施工规定和技术数据资料,其中应该包括有关用涂料的所有详细资料。
如果要在涂漆前对作业用涂料做测试,都必须事先说明将使用的测试方法。
如何对用涂料取样以及如何处理取样等问题都应该依照ISO1512号标准和ISO1513号标准处理。
作业用涂料生产厂商还必须以其他的方式说明:任何可能影响用涂料应用条件和最终施工质量的细节问题(如在技术数据资料中未说明)。
4.2 作业用涂料的储存
作业用涂料生产厂商应该在包装上明示有效期。
除非在生产厂商的提供的产品说明书中(或在其他资料中)另有说明,作业用涂料应在零上3摄氏度至零上30度的温度条件下保存。
特别要指出的是,液态的涂料决不能结冰。
一旦结冰,即使再解冻也无法使用。
作业用涂料和任何其他作业用材料(比如溶剂,、稀释剂等)必须妥善保存在安全的地点。
作业用涂料必须保持密封状态,要到实际使用前方可开启包装。
已经开启却没有用完的,应该重新密封起来,并在容器上明确标记加以区分。
待需要再次使用时再重新开启。
(除非作业用涂料生产厂商在其提供的技术数据资料中另有说明)。
HG 4077-2009防腐蚀涂层涂装技术规范
JT/ T 733-2008港口机械钢结构表面防腐涂层技术条件。
涂装培训资料(doc5)(1).doc
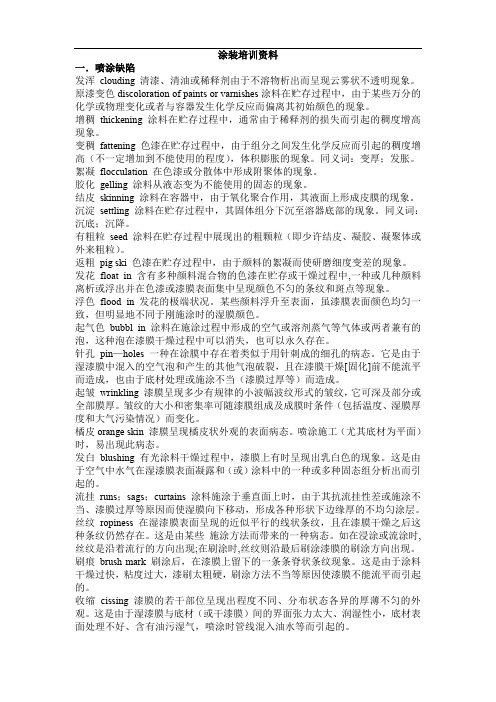
涂装培训资料一.喷涂缺陷发浑clouding 清漆、清油或稀释剂由于不溶物析出而呈现云雾状不透明现象。
原漆变色discoloration of paints or varnishes涂料在贮存过程中,由于某些万分的化学或物理变化或者与容器发生化学反应而偏离其初始颜色的现象。
增稠thickening 涂料在贮存过程中,通常由于稀释剂的损失而引起的稠度增高现象。
变稠fattening 色漆在贮存过程中,由于组分之间发生化学反应而引起的稠度增高(不一定增加到不能使用的程度),体积膨胀的现象。
同义词:变厚;发胀。
絮凝flocculation 在色漆或分散体中形成附聚体的现象。
胶化gelling 涂料从液态变为不能使用的固态的现象。
结皮skinning 涂料在容器中,由于氧化聚合作用,其液面上形成皮膜的现象。
沉淀settling 涂料在贮存过程中,其固体组分下沉至溶器底部的现象。
同义词:沉底;沉降。
有粗粒seed 涂料在贮存过程中展现出的粗颗粒(即少许结皮、凝胶、凝聚体或外来粗粒)。
返粗pig ski 色漆在贮存过程中,由于颜料的絮凝而使研磨细度变差的现象。
发花float in 含有多种颜料混合物的色漆在贮存或干燥过程中,一种或几种颜料离析或浮出并在色漆或漆膜表面集中呈现颜色不匀的条纹和斑点等现象。
浮色flood in 发花的极端状况。
某些颜料浮升至表面,虽漆膜表面颜色均匀一致,但明显地不同于刚施涂时的湿膜颜色。
起气色bubbl in 涂料在施涂过程中形成的空气或溶剂蒸气等气体或两者兼有的泡,这种泡在漆膜干燥过程中可以消失,也可以永久存在。
针孔pin—holes 一种在涂膜中存在着类似于用针刺成的细孔的病态。
它是由于湿漆膜中混入的空气泡和产生的其他气泡破裂,且在漆膜干燥[固化]前不能流平而造成,也由于底材处理或施涂不当(漆膜过厚等)而造成。
起皱wrinkling 漆膜呈现多少有规律的小波幅波纹形式的皱纹,它可深及部分或全部膜厚。
- 1、下载文档前请自行甄别文档内容的完整性,平台不提供额外的编辑、内容补充、找答案等附加服务。
- 2、"仅部分预览"的文档,不可在线预览部分如存在完整性等问题,可反馈申请退款(可完整预览的文档不适用该条件!)。
- 3、如文档侵犯您的权益,请联系客服反馈,我们会尽快为您处理(人工客服工作时间:9:00-18:30)。
(三)预热
预热是为了抛丸前将钢板升温,除去表面水分、部分油污,使钢板升温 达到喷漆后的干燥。 一般预热设备有电热丝加热、中频感应加热、液化石油加热和水加热等。 不论采用何种方式加热,均应使钢板温度保持在40℃ 左右,温度太低, 不利于除去水份、油污,后道喷涂底漆的干燥,温度太高,多耗能量,造成抛丸处理后的钢表面需要立即喷涂车间底漆。
• • • •
喷涂设备为国产长江9 ℃高压无气喷漆泵,压力比为1:32 喷嘴一般为 19~350、19~400、17~350、17~400左右。 喷涂车间底漆时搅拌机不停地缓慢搅拌直至用完为止。 喷枪与钢板之间距离通常为300mm左右,下喷枪距离应略小于上喷枪 的距离。 • 油漆喷覆为50%。
二、钢板抛丸预处理流水线过程
在国内造船、集装箱、大型机械行业中,一般用钢材预处理的方法有抛 射磨料处理、喷射磨料处理和酸洗处理三种方式。其中要获得高效率、高质 量的自动流水作业,目前还只有抛丸处理方式。 抛丸处理是利用抛丸机的叶轮在高速旋转时所产生的离心力将磨料(钢 丸、钢丝段、棱角钢砂等)以很高的速度射向待处理的钢材表面,产生打击 和磨削作用,除去钢表面氧化皮和锈,让钢铁表面露出金属本色并且呈现一 定的粗糙度,以利于涂料的粘附。 抛丸预处理流水线,总体上有两种类型:一是钢板预处理流水线,另一 种则是型钢预处理流水线,两者工作原理是一致的,现造船厂、集装箱、大 型港机厂采用第一种方法,一般性钢结构厂产用第二种方法,两种方法目的 一致都是为了保证涂装质量。
喷砂清理
喷砂清理
喷砂清理
喷砂清理
喷砂清理
喷砂清理
喷砂清理
喷砂清理
喷砂清理
• 真空喷砂的优点是不污染环境,但速度很慢,一般大型船厂和大型机械构
件,无法使用。 • 酸洗方法 除油 —>热水浸洗 —> 酸洗处理 —>冷水浸洗 —> 中和 —>冷 水浸洗 —> 磷化处理 —> 涂装 • 湿喷砂方法 水和磨料进行喷射,达到水喷射的标准后涂装。
钢板抛丸预处理流水线的工艺流程图
除尘器 粉 尘 钢板 校平机 预加热
漆雾过滤器 漆 雾 自动涂漆机 起吊
排风
溶 剂 后加热器 辊道运输
抛丸室
(一)钢板校平
钢板运输过程中或经过长期的堆放后,会产生变形,在工件制作中,影 响加工精度,所以应对钢板进行校平处理。经过校平可以将钢板表面氧化皮 松散部分脱落,对后道抛丸有很大好处,同时校平机能力各有不同一般5mm — 30mm为宜。 另外也有把钢板校平机放在流水线后面,这对车间底漆的性能是一种考 验。
良好的焊接性和切割性 良好的干性(在23 ℃ 时5分钟干燥) 良好的耐溶剂性,能与各种防锈漆配套。 防腐为3个月至6个月。 良好的耐热性,减小受热破坏。 良好的机加工性。 良好的低毒性。(有卫生指标) 良好的耐电位性,适合船舶的阴极保护。
— 焊缝的成型和内在质量不受影响 — 焊缝的机械强度不受影响 — 切割的速度不受影响 — 切割的光洁度不受影响 同时选用的车间底漆必须获得船级社的认可。 车间底漆的特点:含锌,具有电化学保护作用,但有锌盐产生,热加工时,锌蒸汽产生 小,适用于阴极保护,而高温(400-600 ℃ ),热影响区较小,膜厚为20-25微米时, 防锈期一般为九个月。
粗糙度与漆膜厚度的关系
光滑试板 20微米 25微米
R2=40微米 15 20
R2=75微米 12 15
试板 试板 试板
将抹布摩擦50次来回:抹布无锌粉表示已固化;抹布上锌粉很多表示没有固化。 处理方法:进一步固化和重新喷砂。
(十)无机硅酸锌车间底漆性能介绍 Interplate 317(NQA311/NQA317) • • • • • • • •
表面处理的标准
为了正确评定表面处理的质量,许多国家都制订了表面处理质量评定标 准。其中最为著名的是瑞典工业标准SIS055900:1967,目前在世界上被广泛 采用。 国际标准化组织色漆和清漆技术委员会涂装前钢材表面处理分会也制订 了国际标准ISO8501-1.1988其它如日本、美国、英国、澳大利亚、中国(GB 8932)与瑞典,ISO标准相同。 国际标准ISO8501-1:1988将未涂装过的钢材表面原始程度按氧化皮覆盖 程度和锈蚀程度分为四个等级,分别以A、B、C、D表示,并有相应的照片 对照。 A. 全面覆盖氧化皮,表面几乎没有锈蚀钢表面。 B. 氧化皮已开始剥落。 C. 氧化皮大面积剥落,开始麻点。 D. 氧化皮全部剥落,有较多麻点。
(四)抛丸器
•
•
• • •
抛丸器由叶轮、护罩、定向套、分丸轮、轴承座及电动机组成,叶轮由电动 机带动作高速旋转(2200~2600转/min)产生强大的离心力,磨料经进丸管 吸入分丸轮中时,在离心力作用下向叶片长度方向以加速运动60~80米/秒的 速度抛出,抛出的磨料成扇形流速将钢板表面氧化皮和锈蚀除去。 一般抛头4个~16个不等,抛头离钢板间距大约为300~400mm,并且要调整 工件与抛头的角度、方向,控制好每个抛头量。 6mm以下钢板扁钢、型钢不适合钢板预处理,因太薄会变形。 控制好抛丸速度。 选好合适的抛丸钢丸及棱角砂。
在涂装前钢板的表面处理分两个阶段
钢板进厂后,在加工以前对钢材的原材料先进行处理,除去表面的氧 化皮和锈蚀,达到除锈标准后涂上临时保护车间底漆,以确保钢材在加工 制造构件过程中不会再继续腐蚀,这一阶段的钢板处理我们称之为钢材的 表面预处理,其优点是施工方便、保证涂装质量、节约人力财力、缩短后 期涂装的施工周期。 另一阶段处理则是在钢材加工成工件后合拢成整体时,要进行涂装所 作的钢材表面处理,称之为“二次除锈”,但一般不采纳此种方法。
(二)钢板运输
钢板上料后,各工序的传送由辊道完成。 辊道通常为圆柱形,两端有轴承座,辊道间距为500~750mm,在喷涂工 作完成之后,为了防止与辊道接触一面的油漆受到破坏,对辊道的结构形式 有特殊的要求,所以一般辊道与钢板接触部位不会产生大面积的车间底漆损 伤,受到影响很小。 为了保证钢板在抛丸处理时不变形,抛丸机内辊道间距不应小于500mm。
动力工具
铲锤和铲磷锤 钢丝刷和旋转 钢丝刷
针枪和针铲
动力工具
磨片
盘式打磨机
砂轮
旋转铲
活塞铲
动力工具除锈处理的工艺要点 • • • • • • • • • 观察打磨作业环境,做好脚手架、夜晚照明等辅助工作,准备好打磨工具、 风管及接头、个人劳动保护用品。 清理周围环境(箱体内垃圾、杂物及水) 以上打磨工具主要对焊缝区、火工烧损区、自然锈蚀区作彻底打磨至呈现金 属本色,打磨作业应先里后外,先难后易,先下后上的原则。 对完好车间底漆部位作轻度打磨,除取表面的锌盐或表面老化层(对不含车 间底漆而言) 对于区域二次除锈来说,应将焊缝两侧和烧损区,自然锈蚀区的周围涂层打 成坡度,以利于修补涂层附着力及平整。 碗型或碟型钢丝刷对焊缝、磨点锈蚀,除去细孔内的黄锈。 直柄砂轮机装上笔型钢丝刷对角焊缝、小孔,难以到达的部位进行施刷,除 取黄锈。 用风铲将焊缝周围零星锈块和少量焊缝灰渣去除。 清除垃圾和积灰。
•
• • • •
表面处理 •
超高压淡水清洗(一般船上使用) * 去除盐份 * 去除海生物 * 松动的旧涂层 * 去除锈 * 氧化皮 手工和动力工具 手工:拷铲榔头、铲刀、刮刀、钢丝刷、手工砂皮纸。
•
动力工具 • 风动打锈锥(梅花锥) • 直柄砂轮机Ø25 -150的各种砂轮,及可装上笔型钢丝刷用于狭 小角落内部构件、边角和小孔的除锈。 • 端型平面砂磨机Ø100 –180各种型号,可装盆形钢丝刷砂纸盘来 进行二次除锈代表性工具。
二次表面处理
表面处理的三个目的
•
结构处理:对于底材本身必须进行一定的处理,如锐边的打磨、侧角的 磨圆、飞溅的去除、焊孔的补焊和磨平,这些问题对于涂层的完整性, 附着力有很大影响,所以必须在除锈前要进行处理。 表面清理:除去表面上对涂料有损害的物质,特别是氧化皮、铁锈、可 溶性盐、油脂、水分等,如果表面处理不彻底,残留杂质污物将影响涂 层的保护效果。 表面粗糙度:表面粗糙度增大了对涂层接触表面,并有机械接合作用, 提高涂层对底材附着力,但粗糙度不能过大,否则在波峰处往往会引起 油漆膜度不足,引起早期点蚀,而且在较深的凹坑里截留气泡,成为涂 层鼓泡根源。
•
•
表面处理的对象
• • • • •
结构的准备 除油脂 除盐份 氧化皮、铁锈物、旧漆膜及其它污物的清除 表面清理
表面处理的程序
• • •
根据不同的对象,所采取的方法也有区别: 氧化皮 — 在水和氧气的作用下,很容易产生氢氧化物,加上外界温度的变化、机械作 用等,氧化皮很容易脱落,这对涂层极为不利,而且还会引起钢材的电化学腐蚀,除 去氧化皮的最好方法是喷砂处理。 铁锈 — 铁锈是一种较松散物质,往往因为湿气、氧气的影响就会形成钢表面锈蚀物, 并且经常含有可溶性盐,可采用手工、动力工具打磨、喷砂等方法去除锈蚀。 锌盐 — 随着富锌漆的大量使用,锌盐(也称白锈)也构成对涂层的危害,这种松散的 锌的腐蚀产物也影响着涂层附着力,可以高压淡水冲洗,另外用打磨和硬刷子除去。 油脂 — 一般性油漆碰到油脂就会引起漆膜缩孔、附着力差的问题,而越是高性能的涂 料如环氧、聚胺酯涂料就不是常规的油性涂料。首先将大量的油脂要刮去,而后用溶 剂擦洗,反复几次,每次用干净抹布擦过才有效,尽量不要让油脂表面扩大。 焊烟 — 对涂层附着力极为不利,一般用手工砂皮纸磨掉及溶剂擦洗。 各种记号 — 粉笔记号和油漆记号对涂层结合力准确性有很大的影响,一般是无油性记 号笔作为记号,唯一方法采用打磨方式清理记号痕迹。 旧涂层 — 松散涂层必须清除,对后道涂层影响的涂层,要喷涂一道封闭漆,并且可以 除去所有旧涂层,用高压淡水冲洗漆膜表面上的盐份、灰尘并除取油脂。 灰尘 — 一般在钢表面处理后和油漆表面清理后都有不同的灰尘、杂物等,首先将这些 灰尘用无油的压缩空气吹干净。使用真空吸尘机是最理想的方法。