液体模塑成型
三种液态成形方法
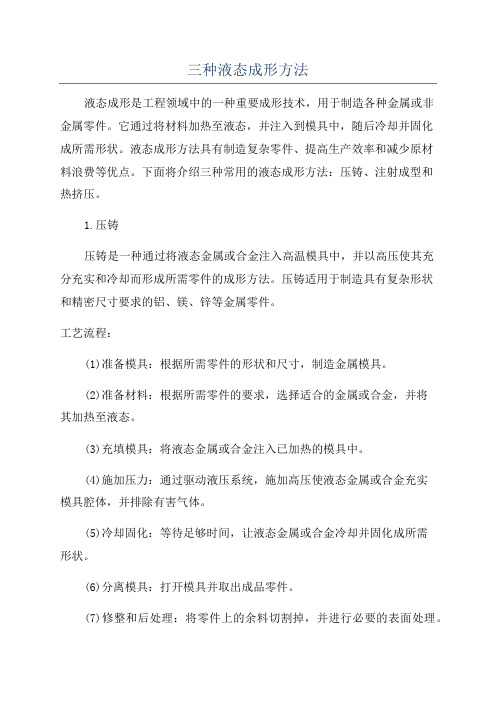
三种液态成形方法液态成形是工程领域中的一种重要成形技术,用于制造各种金属或非金属零件。
它通过将材料加热至液态,并注入到模具中,随后冷却并固化成所需形状。
液态成形方法具有制造复杂零件、提高生产效率和减少原材料浪费等优点。
下面将介绍三种常用的液态成形方法:压铸、注射成型和热挤压。
1.压铸压铸是一种通过将液态金属或合金注入高温模具中,并以高压使其充分充实和冷却而形成所需零件的成形方法。
压铸适用于制造具有复杂形状和精密尺寸要求的铝、镁、锌等金属零件。
工艺流程:(1)准备模具:根据所需零件的形状和尺寸,制造金属模具。
(2)准备材料:根据所需零件的要求,选择适合的金属或合金,并将其加热至液态。
(3)充填模具:将液态金属或合金注入已加热的模具中。
(4)施加压力:通过驱动液压系统,施加高压使液态金属或合金充实模具腔体,并排除有害气体。
(5)冷却固化:等待足够时间,让液态金属或合金冷却并固化成所需形状。
(6)分离模具:打开模具并取出成品零件。
(7)修整和后处理:将零件上的余料切割掉,并进行必要的表面处理。
2.注射成型注射成型是一种通过将液态或半液态塑料材料注入模具中,并在成型温度下固化成所需形状的成形方法。
注射成型适用于制造塑料零件,广泛应用于电子、汽车、日用品等领域。
工艺流程:(1)准备模具:根据所需零件的形状和尺寸,制造塑料模具。
(2)准备材料:选择适合注射成型的塑料树脂,并将其加热至液态或半液态。
(3)充填模具:将液态或半液态塑料注入已加热的模具中。
(4)冷却固化:等待足够时间,让塑料在模具中冷却并固化成所需形状。
(5)分离模具:打开模具并取出成品零件。
(6)修整和后处理:将零件上的余料切割掉,并进行必要的表面处理。
3.热挤压热挤压是一种通过将液态金属在高温和高压下通过模孔挤压成型的成形方法。
热挤压适用于制造具有长直形截面或复杂截面的杆、管和型材等零件。
工艺流程:(1)准备模具:根据所需零件的形状和尺寸,制造高温合金模具。
RTM成型工艺及分类介绍

RTM成型工艺及分类介绍1、RTM成型工艺与分类RTM是指低粘度树脂在闭合模具中流动、浸润增强材料并固化成形的一种工艺技术,属于复合材料的液体成形或结构液体成形技术范畴。
其具体方法是在设计好的模具中,预先放入经合理设计、剪裁或经机械化预成形的增强材料,模具需有周边密封和紧固,并保证树脂流动顺畅;闭模后注入定量树脂,待树脂固化后即可脱模得到所期望产品。
SMC、BMC模压、注射成型、RTM、VEC技术都属闭模成型工艺。
由于环境法的制定和对产品要求的提高使敞模成型复合材料日益受到限制,促使了闭模成型技术的应用,近年来尤其促进了RTM技术的革新和发展。
2、RTM的类型RTM工艺起始于上世纪50年代,目前,RTM成型工艺己广泛应用于建筑、交通、电讯、卫生、航天航空等领域。
下面介绍几种RTM技术。
01、RTM,树脂传递模塑。
该技术源自聚氨酯技术,成型时关闭模具,向预制件中注入树脂,玻纤含量低,约20-45%。
02、VARIT,真空辅助树脂传递注塑。
该技术利用真空把树脂吸入预制件中,同时也可压入树脂,真空度约10-28英寸汞柱。
03、VARTM,真空辅助树脂传递注塑。
制品孔隙一般较少,玻纤含量可增高。
04、VRTM,真空树脂传递模塑。
05、VIP,真空浸渍法。
06、VIMP,可变浸渍塑法。
树脂借助真空或自重移动,压实浸渍。
07、TERTM,热膨胀RTM。
在预制件中插入芯材,让树脂浸渍并对模具与成形品加热。
芯材受热膨胀,压实铺层。
利用这种压实作用,结合表面加压成型。
08、RARTM,橡胶辅助RTM。
在TERTM方法中不用芯材而用橡胶代之。
橡胶模具压紧成型品,使孔隙大大减少,玻纤含量可高达60-70%。
09、RIRM,树脂注射循环模塑。
真空与加压结合,向多个模具交替注入树脂,使树脂循环,直至预制件被充分浸透。
10、CIRTM,Co-Injection RTM。
共注射RTM,可注入几种不同的树脂,也可使用几种预制件,可利用真空袋和柔性表面的模具。
液态模锻成型设计讲解

液态模锻主要内容:液态模锻也称为挤压铸造、锻打铸造以及熔汤锻造等,是一种锻铸结合的工艺方法。
该方法采用铸造工艺将金属熔化、精炼,并用定量浇勺将金属液浇入模具型腔,随后利用锻造工艺的加压方式,使金属液在模具型腔中流动充型,并在较大的静压力下结晶凝固,且伴有小量塑性变形,从而获得力学性能接近纯锻造锻件而优于纯铸造件的毛坯或零件。
目前,采用这种工艺生产的单件质量可达300kg以上,其材料包括有色金属及其合金、铸铁、碳钢和不锈钢等。
采用此工艺可制造大型铝合金活塞、镍黄铜高压阀体、气动单元组件的仪表外壳,铜合金蜗轮等产品。
关键词:液态模锻,特种塑性成形,模锻工艺流程。
液态模锻工艺划分为金属液和模具准备、浇注、合模施压以及开模取件四个步骤,具体如图9-5所示。
图1液态模锻工艺流程.1 工艺分类液态模锻的工艺过程是把一定量的金属液浇入下模型腔中,当溶液还处于熔融或半熔融状态时施加压力,迫使金属充满型腔形成工件。
在整个凝固过程中,对工件保持压力,以便消除金属凝固时在工件内部产生的缺陷,并使其产生塑性变形,工件凝固及塑性变形,借助顶杆或其它方法将其推出,为下一次操作做好准备。
液态模锻工艺按加压方式可以分为如下三种形式:凸模加压凝固法。
如图9-6所示,熔化的金属浇入凹模1中,凸模2下行与凹模形成封闭型腔,待熔融的金属逐渐凝固时加压使其成形,这种方法适用于铸锭或形状简单的厚壁件,在凸模压力作用下液态金属不产生向上移动。
直接液态模锻法。
如图9-7所示,熔融的金属浇入凹模1,凸模2下行与凹模形成封闭型腔,同时将液态金属压成一定形状。
型腔中的液态金属在一定压力的作用下向上流动,中间冷却凝固。
如果没有使多余金属溶液溢出的措施,则凸模的最终位置便由注入溶液的量来决定,并在工件底部和顶部厚度的变化上反映出来。
杯状和空心的法兰状工件常采用直接液态模锻法加工。
间接液态模锻法。
如图9-8所示,熔融的金属浇入下模2中,上模1先与下模2组成部分型腔,待凸模3下行时将液态金属挤出形成一定的形状。
复合材料树脂渗透成型工艺(详细)
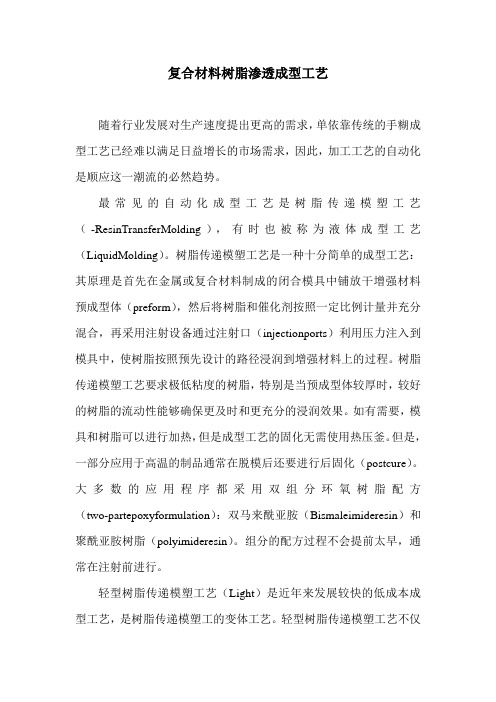
复合材料树脂渗透成型工艺随着行业发展对生产速度提出更高的需求,单依靠传统的手糊成型工艺已经难以满足日益增长的市场需求,因此,加工工艺的自动化是顺应这一潮流的必然趋势。
最常见的自动化成型工艺是树脂传递模塑工艺(-ResinTransferMolding),有时也被称为液体成型工艺(LiquidMolding)。
树脂传递模塑工艺是一种十分简单的成型工艺:其原理是首先在金属或复合材料制成的闭合模具中铺放干增强材料预成型体(preform),然后将树脂和催化剂按照一定比例计量并充分混合,再采用注射设备通过注射口(injectionports)利用压力注入到模具中,使树脂按照预先设计的路径浸润到增强材料上的过程。
树脂传递模塑工艺要求极低粘度的树脂,特别是当预成型体较厚时,较好的树脂的流动性能够确保更及时和更充分的浸润效果。
如有需要,模具和树脂可以进行加热,但是成型工艺的固化无需使用热压釜。
但是,一部分应用于高温的制品通常在脱模后还要进行后固化(postcure)。
大多数的应用程序都采用双组分环氧树脂配方(two-partepoxyformulation):双马来酰亚胺(Bismaleimideresin)和聚酰亚胺树脂(polyimideresin)。
组分的配方过程不会提前太早,通常在注射前进行。
轻型树脂传递模塑工艺(Light)是近年来发展较快的低成本成型工艺,是树脂传递模塑工的变体工艺。
轻型树脂传递模塑工艺不仅具备工艺的所有特点,还降低了成型工艺对一系列指标的要求,例如,注射压力,真空耦合(coupledwithvacuum),和模具的造价和刚性指标。
树脂传递模塑工艺具有许多显著的优点。
一般来说,在树脂传递模塑工艺过程中所使用的干预成型体和树脂材料的价格都比预浸料便宜,而且还可以在室温下存放。
利用这种工艺可以生产较厚的净成形零件,同时免去许多后续加工程序。
该工艺还能帮助生产尺寸精确,表面工艺精湛的复杂零件。
液态成形工艺知识点总结

液态成形工艺知识点总结液态成形工艺的主要特点是能够将液态材料通过模具加工成所需的零件、产品,具有成形周期短、生产效率高、成形精度高、批量生产能力强等优点。
其成型材料包括热塑性塑料、热固性塑料、金属合金等,广泛应用于各种制造工艺中。
注塑成形是将热塑性塑料通过加热并加压的方式,使其溶解成为流动状态,然后通过注射机将其注入模具中进行成型。
注塑成形工艺主要包括原料预处理、注塑机操作、模具设计、成型工艺参数控制等多个方面。
在注塑成形工艺中,模具设计是至关重要的,其质量直接影响到成型产品的质量和生产效率。
同时,成型工艺参数的控制也非常重要,包括注塑温度、注射速度、模具温度、冷却时间等参数的控制都会影响到成型产品的质量。
压铸成形是将金属合金通过加热并加压的方式,使其溶解成为流动状态,然后通过压铸机将其注入模具中进行成型。
压铸成形工艺主要包括原料预处理、压铸机操作、模具设计、成型工艺参数控制等多个方面。
在压铸成形工艺中,原料的质量和成分控制是至关重要的,影响到成型产品的力学性能和表面质量。
同时,模具设计和成型工艺参数的控制也非常重要,直接影响到成型产品的形状精度和表面粗糙度。
吹塑成形是将热塑性塑料通过加热并加压的方式,使其溶解成为流动状态,然后通过气流将其吹入模具中进行成型。
吹塑成形工艺主要包括原料预处理、吹塑机操作、模具设计、成型工艺参数控制等多个方面。
在吹塑成形工艺中,原料的质量和成分控制同样非常重要,直接影响到成型产品的力学性能和表面质量。
模具设计和成型工艺参数的控制也是影响成型产品质量的重要因素。
挤塑成形是将热塑性塑料通过加热并压力的方式,使其在挤出机中形成带状截面的坯料,然后通过挤出头模具进行成型。
挤塑成形工艺主要包括原料预处理、挤出机操作、模具设计、成型工艺参数控制等多个方面。
在挤塑成形工艺中,原料的质量和成分控制同样非常重要,直接影响到成型产品的力学性能和表面质量。
同时,模具设计和成型工艺参数的控制也是影响成型产品质量的重要因素。
复合材料液体成型分类

复合材料液体成型分类
复合材料液体成型是一种制备复合材料的方法,液体成型可以
根据不同的工艺和原理进行分类。
主要的液体成型方法包括压模注
射成型(RTM)、真空辅助树脂浸渍成型(VARTM)、压模挤出成型(RTM)等。
首先,压模注射成型(RTM)是一种常见的液体成型方法,其工
艺流程是将预先切割好的纤维预形状放置在模具中,然后通过模具
封闭,注入树脂,树脂充满整个模具,最后经过固化,得到成型件。
其次,真空辅助树脂浸渍成型(VARTM)是一种利用真空辅助进
行树脂浸渍的液体成型方法,其工艺流程是在放置纤维预形状后,
利用真空将模具内的空气抽出,然后注入树脂,树脂在真空作用下
充满整个模具,最后经过固化,得到成型件。
此外,压模挤出成型(RTM)是一种将纤维和树脂预浸料放置在
模具中,然后通过挤出机将材料挤出,经过模具成型,最后经过固化,得到成型件。
除了上述三种常见的液体成型方法外,还有其他液体成型方法,
如真空压力成型(VIP)、真空注射成型(VIM)等,它们都是根据不同的工艺和原理进行分类的。
总的来说,液体成型方法是一种制备复合材料的重要工艺,不同的液体成型方法在工艺流程、成型效果和适用范围等方面有所不同,可以根据具体的需求选择合适的液体成型方法。
液态成形工艺技术

液态成形工艺技术液态成形工艺技术是一种将液体材料注入模具中,通过各种方式使其固化成形的技术。
液态成形工艺技术包括压铸、注塑、压力真空成型等。
这些技术广泛应用于工业生产中,能够生产高精度、高性能的零部件和产品。
液态成形工艺技术的基本原理是通过将液体材料注入模具中,并施加一定的压力,使其充满整个模腔。
在一定的温度和时间下,液体材料会逐渐固化,从而得到所需的成品。
压铸是一种常见的液态成形工艺技术。
在压铸中,液态金属被注入到模具中,并经过高压力的作用,使其充满整个模腔,然后在一定的时间内进行冷却固化。
最终,通过打开模具,可以得到精确的金属零部件。
注塑是另一种常见的液态成形工艺技术。
在注塑中,熔融的塑料被注入到模具中,并且根据模具的形状和尺寸,塑料材料会逐渐固化。
注塑工艺技术可以生产各种塑料制品,如塑料壳体、包装材料等。
注塑工艺技术具有生产效率高、成本低等优点,因此在工业生产中得到广泛应用。
压力真空成型是一种利用压力和真空力来注入液态材料进行成形的技术。
在压力真空成型中,将液态材料放入模具中,并在一定的压力和真空条件下,使其充满整个模腔,并在固化过程中保持形状。
压力真空成型技术适用于各种不同材料的成形,如橡胶、塑料、陶瓷等。
液态成形工艺技术具有许多优点。
首先,液态成形工艺技术可以生产高精度的零部件和产品,尺寸和形状的精准度较高。
其次,液态成形工艺技术可以实现大规模的生产,生产效率较高。
此外,液态成形工艺技术具有良好的表面质量和产品性能,可以生产出高质量的产品。
然而,液态成形工艺技术也存在一些局限性。
首先,液态成形工艺技术对模具的要求较高,模具制造成本较高。
其次,对液态材料的选择和控制有一定的技术要求,不同的液态材料需要不同的成形工艺。
此外,液态成形工艺技术在处理高温材料和特殊材料时存在一定的困难。
总之,液态成形工艺技术是一种重要的加工技术,能够生产出高精度、高性能的零部件和产品。
随着材料和工艺的不断创新,液态成形工艺技术将在工业生产中发挥越来越重要的作用。
充液成形原理
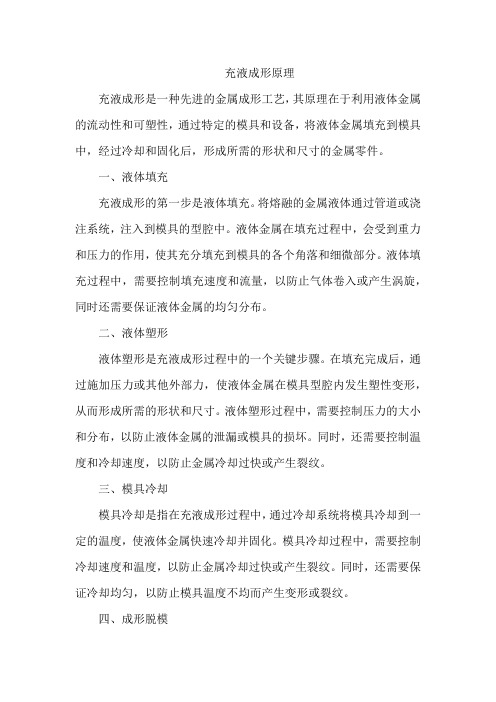
充液成形原理充液成形是一种先进的金属成形工艺,其原理在于利用液体金属的流动性和可塑性,通过特定的模具和设备,将液体金属填充到模具中,经过冷却和固化后,形成所需的形状和尺寸的金属零件。
一、液体填充充液成形的第一步是液体填充。
将熔融的金属液体通过管道或浇注系统,注入到模具的型腔中。
液体金属在填充过程中,会受到重力和压力的作用,使其充分填充到模具的各个角落和细微部分。
液体填充过程中,需要控制填充速度和流量,以防止气体卷入或产生涡旋,同时还需要保证液体金属的均匀分布。
二、液体塑形液体塑形是充液成形过程中的一个关键步骤。
在填充完成后,通过施加压力或其他外部力,使液体金属在模具型腔内发生塑性变形,从而形成所需的形状和尺寸。
液体塑形过程中,需要控制压力的大小和分布,以防止液体金属的泄漏或模具的损坏。
同时,还需要控制温度和冷却速度,以防止金属冷却过快或产生裂纹。
三、模具冷却模具冷却是指在充液成形过程中,通过冷却系统将模具冷却到一定的温度,使液体金属快速冷却并固化。
模具冷却过程中,需要控制冷却速度和温度,以防止金属冷却过快或产生裂纹。
同时,还需要保证冷却均匀,以防止模具温度不均而产生变形或裂纹。
四、成形脱模成形脱模是指在充液成形过程中,将成形的金属零件从模具中脱出。
在脱模过程中,需要保证金属零件的完整性和尺寸精度。
如果脱模不当,可能会导致金属零件的变形或损坏。
因此,在脱模过程中,需要使用专业的脱模工具和技术,以确保金属零件的完整性和精度。
五、液体回流液体回流是指在充液成形过程中,将残留在浇注系统和管道中的液体金属重新回收到熔炼炉中。
液体回流过程中,需要控制回流速度和温度,以防止金属氧化或产生气孔。
同时,还需要对回流的金属进行成分分析和质量检测,以确保其质量和性能符合要求。
总之,充液成形原理是一种高效、高质量的金属成形工艺,具有广泛的应用前景。
在实际生产中,需要根据不同的材料和产品要求,选择合适的工艺参数和技术设备,以实现最优的成形效果和质量。
复合材料液体成型工艺的发展及应用

玻璃钢2019年第1期复合材料液体成型工艺的发展及应用徐竹(西安航空职业技术学院,陕西西安710089)复合材料液体成型工艺也称液体模塑成型技术(Liquid Composite Molding,简称LCM)是指将液态树脂注入铺有纤维预成型体的闭合模腔中,或加热熔化预先放入模腔内的树脂 膜,液态树脂在流动充满模腔的同时完成纤维/树脂的浸润并经固化脱模后成为复合材料制 品的一种成型工艺。
与其他纤维复合材料制造技术相比,LC M技术可生产的构件范围广,可按结构要求定向 铺放纤维,一步浸渍成型带有夹芯、加筋、预埋件等的大型构件。
LC M可以实现复合材料设 计、制备的一体化;既可制备大型整体复合材料制件,又可制备各种小型精密复合材料制件;既能显著缩短制件生产周期,又可保证制件的整体质量。
20世纪80年代后,随着飞行器的 承力构件及次承力构件、国防应用、汽车结构件以及高性能体育用品等的开发,RTM工艺取 得了显著的进展,并且在此基础上开发了 VARTM、SCRIMP、RFI、SRIM等这些先进的L C M工 艺技术。
1树脂传递模塑(RTM)成型工艺树脂传递模塑成型简称RTM(Resin Transfer Molding),是一种闭模成型技术,可以生 产出两面光的制品。
它的基本原理是先在模腔内预先铺放增强材料预成型体、芯材和预埋件,然后在压力或真空作用下将树脂注入闭合模腔,浸润纤维,经固化、脱模、后加工而成制品 的工艺。
随着材料技术和工艺的不断发展,R TM工艺制品已经在航空航天、交通运输、体育 用品、船舶、建筑等领域得到了广泛应用。
RTM在航空航天和军事领域的应用主要体现大型 结构部件的整体成型方面,国外R T M成型技术在航空航天领域的应用主要有雷达罩、螺旋桨、隔舱门、直升机的方向舵、整体机舱、飞机的机翼等。
R T M成型技术在舰船和装甲车辆上的 应用主要有舰船的防护板、船舶结构件及装甲战车的车体等部件。
液体硅胶不同成型方式方法介绍

液体硅胶不同成型方式方法介绍液体硅胶是一种高性能的材料,具有优异的耐热性、耐寒性、耐臭氧、抗紫外线、电绝缘性能等优点。
因此,在工业生产和日常生活中,液体硅胶被广泛地应用于模具制造、电子元件封装、食品加工、医疗器械、家具制造等领域。
液体硅胶成型方式有很多种,下面我们来介绍几种比较常见的成型方式。
一、压模模压成型压模模压成型是液体硅胶制造模具常用的成型方式。
它适用于制作成型精度高、细节复杂的模具,如模具表面呈现的花纹、图案等。
该成型方式要求模具表面光滑,无油污,且需要在涂布模具分离剂之后加工。
具体操作过程如下:1. 选用合适的模具,涂布分离剂。
2. 混合液体硅胶A、B组分。
3. 将混合后的液体硅胶注入模具中,通过压模机施加压力,整个成型过程在常温下完成。
4. 成型完成后,从模具中取出成品,进行下一步的后处理。
二、注塑成型注塑成型是将液体硅胶注入注射成型机中,在高温和高压条件下形成作为成型物的一种成型方式。
该成型方式适用于生产精度高、尺寸规范的硅胶制品,在医疗器械、汽车零配件等领域得到广泛应用。
具体操作过程如下:1. 选用适量的液体硅胶A、B组分,并混合。
2. 料筒预热至适宜的温度,将混合后的液体硅胶注入料筒中。
3. 利用注塑机进行加热和注塑操作,机器将加热后的液体硅胶注入模具中,成形制品。
4. 成品冷却卸模,进行下一步的后处理。
三、流水线工艺流水线工艺是将液体硅胶连续注入成型模具中,通过高温固化、挤出切割等方式,快速、高效地进行生产制品。
该成型方式在食品加工、医疗器械等领域得到广泛应用。
具体操作过程如下:1. 设计制造合适的成型模具。
2. 确定流水线生产过程,制定生产流程的控制方案。
3. 在流水线上设置不同的工位,在工位之间连贯衔接,并对成型过程进行自动化控制和监控。
4. 混合液体硅胶A、B组分,根据生产需要连续注入模具中,进行加热、冷却、切割等操作,在生产线上形成合格的硅胶制品。
液体硅胶不同成型方式各有特点,具体应用需要结合生产需要、技术要求、成本控制等因素进行选择。
传递模塑工艺

树脂传递模塑工艺(树脂压铸成型)属于复合材料的液体成型工艺
(Liquid composite molding)。
它是在20世纪70年代发展起来的复合材料成型新工艺,也有资料认为它是由20世纪30年代的浇铸冷模工艺演变而来的,在西欧RTM工艺也称"树脂注射"工艺。
RTM 工艺的基本原理示意如图-1(a)所示,在一定的温度、压力下,低黏度的液体树脂被注人铺有预成型坯(增强材料)的模具中,注人树脂,固化成型,然后脱模。
工艺过程图解如图- 1 (10所示,包括预成型坯的加工与树脂的注入和固化两步。
由于这两步可分开进行,所以说RTM工艺具有髙度的灵活性和组合性,便于实现"材料设计",同时使操作工艺简单。
图-1RTM成型工艺
RTM工艺的注射操作一般要求在1/4 ~ 1/2树脂凝胶时间内完成,传递时间为2~15min,传递压力为0.3~0.7MPa。
为脱除模腔内的气泡,促进树脂的流动和改善浸渍性,还发展了一种在注入树脂的同时抽真空的新工艺——真空辅助RTM工艺。
复合材料液体模塑成型工艺研究现状
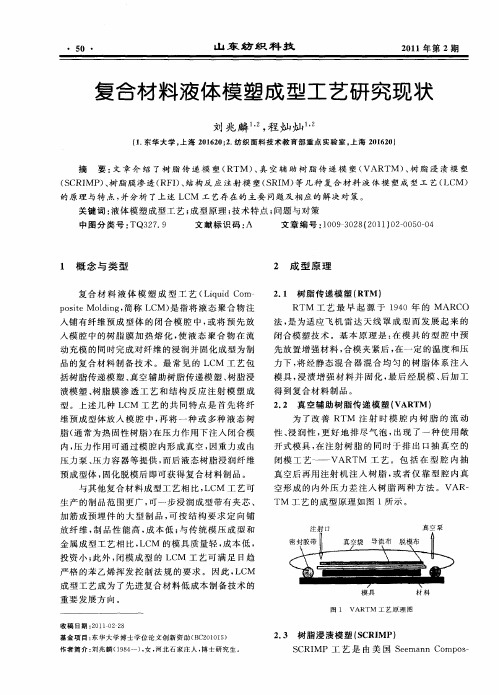
真空后 再用注 射机 注 人树 脂 , 者仅 靠 型腔 内真 或
空 形 成 的 内外 压 力 差 注 入 树 脂 两 种 方 法 。 VAR —
TM 工 艺 的 成 型 原 理 如 图 1所 示 。
加筋 或预埋件 的 大型 制 品 , 按 结 构要 求 定 向铺 可 放纤 维 , 品性 能高 , 制 成本 低 ; 与传 统模 压 成 型和 金属 成型工艺 相 比 , C 的模具 质量轻 , L M 成本 低 , 投资小 ; 此外 , 闭模 成 型 的 L M 工艺 可满 足 日趋 C 严 格 的苯 乙烯 挥发 控制 法规 的要 求 。 因此 , C L M 成型 工艺成 为了先进 复合材 料低成本 制备技 术 的
摘 要 : 章 介 绍 了 树 脂 传 递 模 塑 ( TM ) 真 空 辅 助 树 脂 传 递 模 塑 ( 文 R 、 VAR M ) 树 脂 浸 渍 模 塑 T 、 (C I )树 脂膜渗透 ( F) 结构反 应 注射模 塑( R M) 几种 复合 材料 液体模 塑 成 型工 艺 ( C ) S R MP 、 R I、 S I 等 L M 的 原 理 与 特 点 , 分 析 了上 述 L M 工 艺 存 在 的 主 要 问 题 及 相 应 的 解 决 对 策 。 并 C
重要发展 方 向 。
图 1 VAR TM 工 艺 原 理 图
收稿 日期 : 0 10 —8 2 1 2 2
模 具
材 料
基金项 目: 东华 大学 博 士 学位 论 文 创 新 资 助 ( C 0 0 5 B 211)
2 3 树脂浸 渍模塑 (C I . S R MP) S R MP 工 艺 是 由 美 国 S e n o o C 工艺 ; 成型原 理 ; 技术 特点 ; 问题 与对策
三种液态成形方法
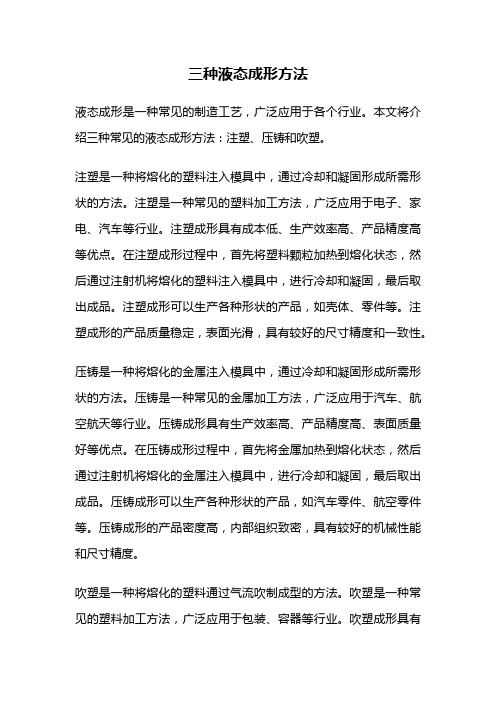
三种液态成形方法液态成形是一种常见的制造工艺,广泛应用于各个行业。
本文将介绍三种常见的液态成形方法:注塑、压铸和吹塑。
注塑是一种将熔化的塑料注入模具中,通过冷却和凝固形成所需形状的方法。
注塑是一种常见的塑料加工方法,广泛应用于电子、家电、汽车等行业。
注塑成形具有成本低、生产效率高、产品精度高等优点。
在注塑成形过程中,首先将塑料颗粒加热到熔化状态,然后通过注射机将熔化的塑料注入模具中,进行冷却和凝固,最后取出成品。
注塑成形可以生产各种形状的产品,如壳体、零件等。
注塑成形的产品质量稳定,表面光滑,具有较好的尺寸精度和一致性。
压铸是一种将熔化的金属注入模具中,通过冷却和凝固形成所需形状的方法。
压铸是一种常见的金属加工方法,广泛应用于汽车、航空航天等行业。
压铸成形具有生产效率高、产品精度高、表面质量好等优点。
在压铸成形过程中,首先将金属加热到熔化状态,然后通过注射机将熔化的金属注入模具中,进行冷却和凝固,最后取出成品。
压铸成形可以生产各种形状的产品,如汽车零件、航空零件等。
压铸成形的产品密度高,内部组织致密,具有较好的机械性能和尺寸精度。
吹塑是一种将熔化的塑料通过气流吹制成型的方法。
吹塑是一种常见的塑料加工方法,广泛应用于包装、容器等行业。
吹塑成形具有生产效率高、产品质量好、成本低等优点。
在吹塑成形过程中,首先将塑料颗粒加热到熔化状态,然后将熔化的塑料注入吹塑机中,通过气流吹制成型,最后取出成品。
吹塑成形可以生产各种形状的产品,如瓶子、容器等。
吹塑成形的产品具有一定的韧性和透明度,可以满足不同行业的需求。
以上三种液态成形方法在工业生产中得到广泛应用,为各行各业提供了丰富的产品。
注塑、压铸和吹塑成形方法各有特点,适用于不同的材料和产品。
在实际应用中,需要根据具体情况选择合适的成形方法,以满足产品的需求。
液态成形技术的不断发展和创新,将为制造业带来更多的机遇和挑战,推动行业的进步和发展。
复合材料液体模塑成型技术(中文版)
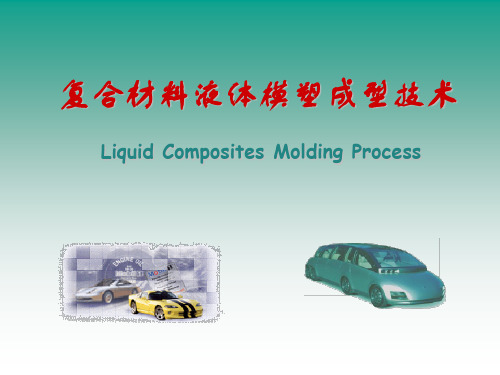
Liquid Composites Molding Process
复合材料液体模塑成型技术
液体模塑成型技术 织物与预成型 工艺监测与控制 液体模塑成型技术的应用
液体模塑成型技术
树脂传递模塑 Resin Transfer Molding (RTM)
结构反应注射模塑Structural Reaction Injection Molding (SRIM)
性能 低
高
工艺操作性 易
难
成本
应用
低 汽车, 军事
汽车, 军事
汽车, 军事
汽车, 军事
航空
航空
高
树脂传递模塑成型技术
注射口 预成型体
预催化树脂
排气孔
热流
充模与固化
脱模
适合于RTM的树脂体系
粘度 适用期 固化温度 固化时间 后固化
< 200 cps > 2 hours < 175 °C 取决于应用情况,一般 < 1 hour 尽可能避免
- 反应速率 - 比热焓
热传递模型
- 分子量 - 粘度
工艺周期
液体模塑成型技术的应用
复合材料在汽车工业上的应用
高性能复合材料客车
复合材料在航空领域的应用
复合材料在航海领域的应用
复合材料在基础设施上的应用
复合材料芯材横截面
复合材料在运动器材上的应用
织物结构的选择
工艺性能 渗透率 (X、Y和Z轴) 压缩性能 铺覆性能
使用性能 模量、强度等 耐久性 压缩性能
预成型体
一般指实际结构的骨架 根据结构与树脂注射要求设计 设计时需特别注意如下几点:
液态成型工艺课程设计
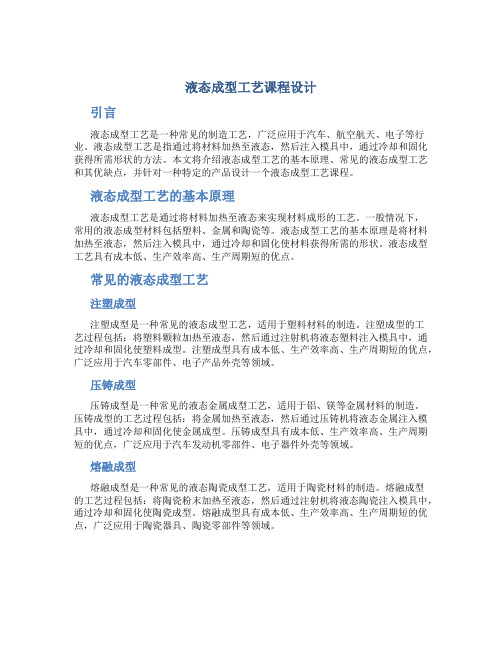
液态成型工艺课程设计引言液态成型工艺是一种常见的制造工艺,广泛应用于汽车、航空航天、电子等行业。
液态成型工艺是指通过将材料加热至液态,然后注入模具中,通过冷却和固化获得所需形状的方法。
本文将介绍液态成型工艺的基本原理、常见的液态成型工艺和其优缺点,并针对一种特定的产品设计一个液态成型工艺课程。
液态成型工艺的基本原理液态成型工艺是通过将材料加热至液态来实现材料成形的工艺。
一般情况下,常用的液态成型材料包括塑料、金属和陶瓷等。
液态成型工艺的基本原理是将材料加热至液态,然后注入模具中,通过冷却和固化使材料获得所需的形状。
液态成型工艺具有成本低、生产效率高、生产周期短的优点。
常见的液态成型工艺注塑成型注塑成型是一种常见的液态成型工艺,适用于塑料材料的制造。
注塑成型的工艺过程包括:将塑料颗粒加热至液态,然后通过注射机将液态塑料注入模具中,通过冷却和固化使塑料成型。
注塑成型具有成本低、生产效率高、生产周期短的优点,广泛应用于汽车零部件、电子产品外壳等领域。
压铸成型压铸成型是一种常见的液态金属成型工艺,适用于铝、镁等金属材料的制造。
压铸成型的工艺过程包括:将金属加热至液态,然后通过压铸机将液态金属注入模具中,通过冷却和固化使金属成型。
压铸成型具有成本低、生产效率高、生产周期短的优点,广泛应用于汽车发动机零部件、电子器件外壳等领域。
熔融成型熔融成型是一种常见的液态陶瓷成型工艺,适用于陶瓷材料的制造。
熔融成型的工艺过程包括:将陶瓷粉末加热至液态,然后通过注射机将液态陶瓷注入模具中,通过冷却和固化使陶瓷成型。
熔融成型具有成本低、生产效率高、生产周期短的优点,广泛应用于陶瓷器具、陶瓷零部件等领域。
液态成型工艺课程设计课程目标本液态成型工艺课程的目标是培养学生对液态成型工艺的基本原理和常见工艺的了解,以及掌握液态成型工艺在产品设计和制造中的应用能力。
通过本课程的学习,学生将能够独立完成一个液态成型产品的设计和制造。
课程内容第一章:液态成型工艺概述•液态成型工艺的定义和分类•液态成型工艺的优缺点及应用领域•液态成型工艺与传统加工方法的比较第二章:注塑成型工艺•注塑成型工艺的基本原理和流程•注塑成型机的结构和工作原理•注塑成型工艺中的关键技术和操作要点第三章:压铸成型工艺•压铸成型工艺的基本原理和流程•压铸机的结构和工作原理•压铸成型工艺中的关键技术和操作要点第四章:熔融成型工艺•熔融成型工艺的基本原理和流程•熔融成型机的结构和工作原理•熔融成型工艺中的关键技术和操作要点第五章:液态成型工艺在产品设计中的应用•液态成型工艺在产品设计中的优势和局限性•液态成型工艺与产品设计的关系•液态成型工艺在不同行业的实际应用案例课程教学方法本液态成型工艺课程采用理论教学与实践教学相结合的教学方法。
复合材料液体模塑成型技术
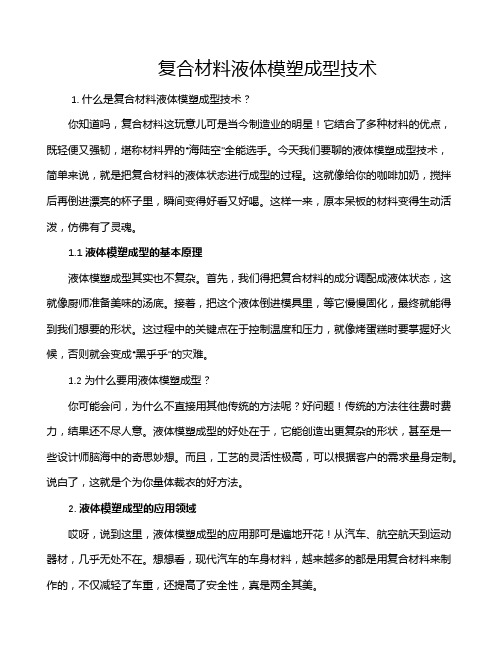
复合材料液体模塑成型技术1. 什么是复合材料液体模塑成型技术?你知道吗,复合材料这玩意儿可是当今制造业的明星!它结合了多种材料的优点,既轻便又强韧,堪称材料界的“海陆空”全能选手。
今天我们要聊的液体模塑成型技术,简单来说,就是把复合材料的液体状态进行成型的过程。
这就像给你的咖啡加奶,搅拌后再倒进漂亮的杯子里,瞬间变得好看又好喝。
这样一来,原本呆板的材料变得生动活泼,仿佛有了灵魂。
1.1 液体模塑成型的基本原理液体模塑成型其实也不复杂。
首先,我们得把复合材料的成分调配成液体状态,这就像厨师准备美味的汤底。
接着,把这个液体倒进模具里,等它慢慢固化,最终就能得到我们想要的形状。
这过程中的关键点在于控制温度和压力,就像烤蛋糕时要掌握好火候,否则就会变成“黑乎乎”的灾难。
1.2 为什么要用液体模塑成型?你可能会问,为什么不直接用其他传统的方法呢?好问题!传统的方法往往费时费力,结果还不尽人意。
液体模塑成型的好处在于,它能创造出更复杂的形状,甚至是一些设计师脑海中的奇思妙想。
而且,工艺的灵活性极高,可以根据客户的需求量身定制。
说白了,这就是个为你量体裁衣的好方法。
2. 液体模塑成型的应用领域哎呀,说到这里,液体模塑成型的应用那可是遍地开花!从汽车、航空航天到运动器材,几乎无处不在。
想想看,现代汽车的车身材料,越来越多的都是用复合材料来制作的,不仅减轻了车重,还提高了安全性,真是两全其美。
2.1 在汽车工业中的应用在汽车工业中,复合材料的使用可谓如鱼得水。
那些轻巧的车身,不仅能提高燃油经济性,还能在碰撞时保护乘客的安全。
想想当年那些笨重的金属车身,现在的车就像是现代版的“轻骑兵”,既灵活又强悍。
对于车主来说,油费省下来的钱可够吃几顿大餐了!2.2 在航空航天领域的应用而在航空航天领域,复合材料更是大显身手。
飞行器的外壳一般都采用复合材料,这样不仅能降低重量,还能提高飞行效率。
谁能想到,空中的巨无霸也是用这么轻便的材料打造的呢?这就像给飞行器穿上了一件“隐形斗篷”,在空中飞得更快更稳,真是太酷了!3. 未来的发展趋势未来,复合材料液体模塑成型技术可谓大有可为!随着科技的发展,材料的性能会越来越好,模塑工艺也会更加精细。
成型水是什么
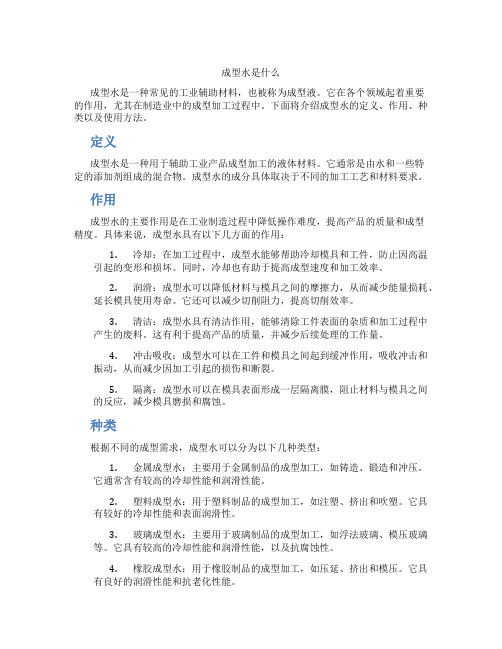
成型水是什么成型水是一种常见的工业辅助材料,也被称为成型液。
它在各个领域起着重要的作用,尤其在制造业中的成型加工过程中。
下面将介绍成型水的定义、作用、种类以及使用方法。
定义成型水是一种用于辅助工业产品成型加工的液体材料。
它通常是由水和一些特定的添加剂组成的混合物。
成型水的成分具体取决于不同的加工工艺和材料要求。
作用成型水的主要作用是在工业制造过程中降低操作难度,提高产品的质量和成型精度。
具体来说,成型水具有以下几方面的作用:1.冷却:在加工过程中,成型水能够帮助冷却模具和工件,防止因高温引起的变形和损坏。
同时,冷却也有助于提高成型速度和加工效率。
2.润滑:成型水可以降低材料与模具之间的摩擦力,从而减少能量损耗、延长模具使用寿命。
它还可以减少切削阻力,提高切削效率。
3.清洁:成型水具有清洁作用,能够清除工件表面的杂质和加工过程中产生的废料。
这有利于提高产品的质量,并减少后续处理的工作量。
4.冲击吸收:成型水可以在工件和模具之间起到缓冲作用,吸收冲击和振动,从而减少因加工引起的损伤和断裂。
5.隔离:成型水可以在模具表面形成一层隔离膜,阻止材料与模具之间的反应,减少模具磨损和腐蚀。
种类根据不同的成型需求,成型水可以分为以下几种类型:1.金属成型水:主要用于金属制品的成型加工,如铸造、锻造和冲压。
它通常含有较高的冷却性能和润滑性能。
2.塑料成型水:用于塑料制品的成型加工,如注塑、挤出和吹塑。
它具有较好的冷却性能和表面润滑性。
3.玻璃成型水:主要用于玻璃制品的成型加工,如浮法玻璃、模压玻璃等。
它具有较高的冷却性能和润滑性能,以及抗腐蚀性。
4.橡胶成型水:用于橡胶制品的成型加工,如压延、挤出和模压。
它具有良好的润滑性能和抗老化性能。
使用方法使用成型水需要根据具体的加工过程和要求进行操作。
一般来说,以下几个步骤是常见的:1.配制成型水:根据加工要求,将成型水配制好。
具体的配比和添加剂可以根据实际情况进行调整。
成型水怎么做
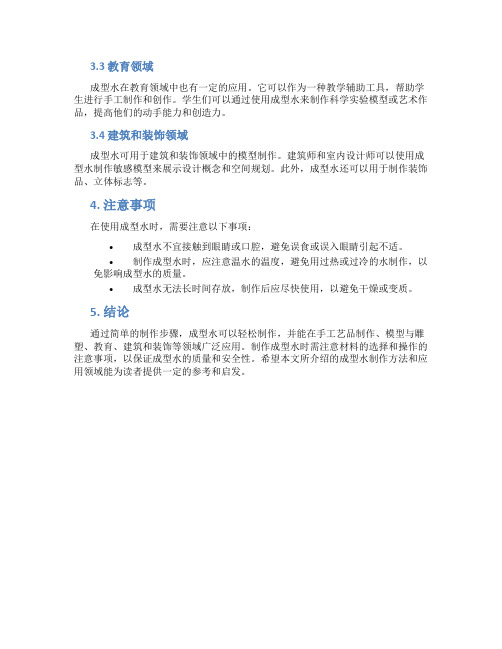
成型水的制作方法与应用1. 导言成型水是一种具有一定流动性和可塑性的液体,常用于制作各种手工艺品、模型、雕塑等。
它可以通过简单的制作方法和常见的材料来制作,同时在多个领域有广泛的应用。
本文将介绍一种简单易行的成型水制作方法,并分析其应用领域。
2. 成型水的制作方法2.1 材料准备制作成型水所需的材料主要有以下几种:•白色胶水:可在文具店、工艺品店等地方购买。
•液体淀粉:一般为食品级淀粉,可在超市等地方购买。
•温水:适量。
2.2 制作步骤以下是制作成型水的步骤:1.取一个容器,将适量的白色胶水倒入容器中。
2.慢慢地往胶水中加入温水,同时用搅拌棒或勺子搅拌均匀,直到胶水完全溶解在水中。
3.慢慢地往溶解的胶水中加入液体淀粉,边加入边搅拌,直到溶液呈现出适当的浑浊度和黏稠度,即成型水的制作完成。
3. 成型水的应用领域成型水作为一种具有可塑性的液体,被广泛应用于以下领域:3.1 手工艺品制作成型水可以用于制作各种手工艺品,如石膏模具、塑料玩具、假花等。
只需要将成型水注入模具中,待其干燥成型后,即可得到精致的手工艺品。
3.2 制作模型和雕塑成型水可以用作模型和雕塑的原料。
它的可塑性使得制作过程更加方便,可以根据需要进行调整和修改。
制作模型和雕塑时,只需将成型水按照设计要求进行塑造和造型,然后等待其干燥成型即可。
3.3 教育领域成型水在教育领域中也有一定的应用。
它可以作为一种教学辅助工具,帮助学生进行手工制作和创作。
学生们可以通过使用成型水来制作科学实验模型或艺术作品,提高他们的动手能力和创造力。
3.4 建筑和装饰领域成型水可用于建筑和装饰领域中的模型制作。
建筑师和室内设计师可以使用成型水制作敏感模型来展示设计概念和空间规划。
此外,成型水还可以用于制作装饰品、立体标志等。
4. 注意事项在使用成型水时,需要注意以下事项:•成型水不宜接触到眼睛或口腔,避免误食或误入眼睛引起不适。
•制作成型水时,应注意温水的温度,避免用过热或过冷的水制作,以免影响成型水的质量。
molding工艺

molding工艺
Molding工艺是一种广泛应用于工业制造和消费品生产的技术,它可以以有序、高效且低成本的方式制造出许多不同形状和材料的产品。
Molding工艺是把液体和固体材料经过特定的模具进行压力成型的过程,从而制造出具有精确的大小和外观的产品。
Molding工艺可以分为几种不同类型,其中最常见的是压力成型,这一工艺在一般消费品制造中得到了广泛的应用。
压力成型工艺广泛应用于制作各种大小和形状的塑料制品。
该工艺中,模具将熔融的塑料材料挤压入其内以形成所需的外观和形状。
除了常见的压力模塑外,还有其他一些被称为逆流熔模塑的技术,它们可以用于制作一些特殊的产品,如精密模块和内部复杂结构的产品。
其工作原理是将熔融的材料注入模具的内部,然后由外部的发泡剂器产生压力以形成所需的形状。
另一种Molding工艺是吹塑成型,它通常用于制作一些比较大的塑料制品。
该工艺中,塑料柔软的片材将被熔融,然后利用蒸汽压力形成所要求的形状。
在通过吹塑技术进行加工后,这些塑料制品具有高度的强度及耐磨性,可以满足大多数工业应用的要求。
Molding工艺也可以用于制作一些特殊的塑料制品,如真空成型和密封成型。
真空成型工艺是使用特殊的技术将熔融的塑料材料灌注到被真空处理的模具中,利用空气压力而形成几种不同的复杂几何图形。
而密封成型工艺则是在真空成型之后,利用压力将塑料固化成所需要的外观和尺寸。
综上所述,Molding工艺是一种用于制造各种形状和材料的工业技术,可以有效地减少制造成本,提升制造效率,同时可以实现精确的尺寸和外观要求。
可以说,Molding工艺在工业制造和消费品生产中发挥着重要的作用。
- 1、下载文档前请自行甄别文档内容的完整性,平台不提供额外的编辑、内容补充、找答案等附加服务。
- 2、"仅部分预览"的文档,不可在线预览部分如存在完整性等问题,可反馈申请退款(可完整预览的文档不适用该条件!)。
- 3、如文档侵犯您的权益,请联系客服反馈,我们会尽快为您处理(人工客服工作时间:9:00-18:30)。
将两种或两种以上的组分在混合区低压(0.5MPa)混合后,即在低压 (0.5-1.5MPa)下注射到闭模中反应成型(例如,组分一为多元醇, 一为异氰酸酯,则反应生成聚氨酯)。直接在一种组分内加入磨碎 玻纤原丝和(或)填料,亦可在注射前,将长纤维增强材料(如连续 纤维毡、织物、复合毡、短切原丝等的预成型物等)预先置模具。
真空袋
树脂注射口
真空管
真空管
真空辅助树脂注射
Vacuum Assisted Resin Transfer Molding
Seeman’s Composite Resin Injection Molding Process
西曼复合材料公司树脂渗透成型法(SCRIMP)
真空过下面的关系进行估算
工 艺 监 测 与 控 制
树脂固化过程
化学反应 热反应 挥发 粘度增加 凝胶 玻璃化
液 态
固 态
热辐射
固化是树脂通过化学反应改变其性能的过程
加工成型工艺模型流程图
材料 - 热传递 - 比热 热动力学模型 - 反应速率 - 比热焓 热传递模型 - 分子量 - 粘度
真空管
真空管
autoclave: Apply Vacuum Pressure and Heat in an oven which can be 5 feet to 300 feet long
液体模塑成型的优点
成本低
表观质量佳
工艺灵活 可成型大型复杂制品 可加筋、加芯及插入物 整体成型 适合多种树脂体系
低投入 低污染 树脂系统
反应速率 放热曲线 低收缩 高机械性能 复合引发体系
高效率
高品质
混合系统
特殊性能
流动通过多孔介质 (流体动力学)
真空口 真空口 注射口 非稳态 热传导 (热力学) 非等温 化学反应 (反应动力学) 等效渗透 织物结构、层合结构
纤维预成形
Structural Reaction Injection Molding (SRIM)
渗 透 率
渗透率(K)是用来表征流体通过预成型体的 难易性,主要与下面两点有关
预成型体的结构
树脂的粘度
渗透率可决定一些关键的工艺参数 充模时间 注射压力
对于各向同性预成型体,渗透率仅需用一个值来表征
K = Kxx = Kyy = Kzz
对于各向异性预成型体,渗透率有三个值 Kxx, Kyy, Kzz
性 能
模量 强度 使用寿命 使用温度
成 本
常用树脂类型
类型 聚酯树脂 乙烯基酯树脂 酚醛树脂 聚氨酯 环氧树脂 双马来酰亚胺 热塑性塑料 高 难 高 性 能 低 工艺操作性 易 成本 低 应 用 汽车, 军事 汽车, 军事 汽车, 军事 汽车, 军事 航空 航空
树脂传递模塑成型技术
注射口
预催化树脂
预成型体 排气孔 热流
脱模 充模与固化
适合于RTM的树脂体系
粘 度
< 200 cps
适用期
固化温度 固化时间 后固化
> 2 hours
< 175 °C 取决于应用情况,一般 < 1 hour 尽可能避免
RTM 技术的综合性能
预成型体
模 具
注 射
预成型体类型 预成型体结构
固 化
模具设计 模具材料 渗透性 模具设计 渗透性 树脂反应动力学 模具温度 热传递 充模时间 树脂反应动力学 模具温度
预 成 型 体
一般指实际结构的骨架 根据结构与树脂注射要求设计 设计时需特别注意如下几点:
• 泡沫芯材 • 金属嵌入物 • 多层预成型体
随机毡
二维机织物
编 织 机
环 形 编 织 机
三 维 编 织 机
通 用 预 成 型 技 术
剪切-铺放预成型
纤维取向预成型
热成型材料冲压预成型
二维环形编织 插入物预成型
预成型体取向
渗透性
脱 模
模具温度
树脂粘度
热传递
织 物 与 预 成 型
织 物 类 型
双向平纹
三向平纹
缝 编
多轴多层经向针织
三维柱状
三维编织
三维直交织物
角度互锁结构
织 物 结 构 的 选 择
工艺性能 渗透率 (X、Y和Z轴) 压缩性能 铺覆性能
使用性能 模量、强度等 耐久性 压缩性能
复合材料液体模塑成型技术
Liquid Composites Molding Process
复合材料液体模塑成型技术
液体模塑成型技术 织物与预成型 工艺监测与控制 液体模塑成型技术的应用
液体模塑成型技术
树脂传递模塑
Resin Transfer Molding (RTM)
结构反应注射模塑
工艺周期
液体模塑成型技术的应用
复合材料在汽车工业上的应用
高性能复合材料客车
复合材料在航空领域的应用
复合材料在航海领域的应用
复合材料在基础设施上的应用
复合材料芯材横截面
复合材料在运动器材上的应用
液体模塑成型的主要研究内容
注射模塑 部 件 的 复 杂 性 RTM (液体模塑)
压缩模塑
微 结 构 控 制
增强材料的选择
模塑件的力学性能要求 模塑件的使用环境要求 经济效益
常用增强材料
碳纤维 玻璃纤维 芳纶纤维 纤维纱
树脂体系的要求
工 艺
时间-温度-粘度 固化周期 后固化 适用期
Structural Reaction Injection Molding (SRIM)
真空辅助树脂注射
Vacuum-Assisted Resin Injection(VARI)
SCRIMP成型 Seeman’s Composite Resin Injection Molding Process
复合材料液体模塑成型工艺原理示意图