塑料管材挤出模具设计
挤出模具设计
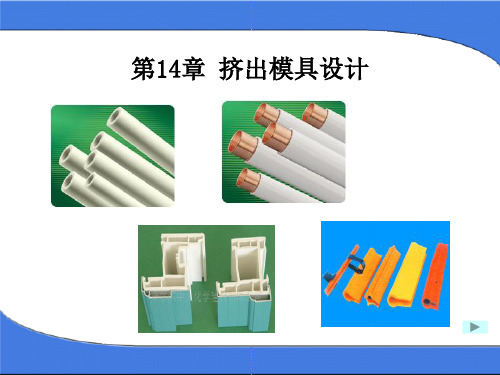
(5)过滤网和过滤板
ⅰ过滤杂质 ⅱ将熔体的螺旋运动 直线运动
(6)加热器 (7)璧厚均匀调节装置 (8)定型模
异型材定型模的型腔截面 1.上型板 2.镶条 3.下型板
二、挤出机头的分类
1、按挤出的塑件分类
ⅰ管机头 ⅱ棒机头 ⅲ异型材机头等
2、按挤出塑件的出口方向分类
ⅰ直通机头(直向机头) ⅱ角式机(横向机头)
三、挤出成型工艺参数
1、温度:
包括加料段、压缩段、均化段、机头及口模段温度。
※加料段的温度不宜过高,压缩段和均化段的温度可高一些。 ※机头的温度控制在塑料热分解温度以下
• 2、压力
• 克服料流的阻力、过虑板、过虑网、口模等产生的阻力。 • 合理控制螺杆转速,保证温控系统的精度,以减小压力波动。
• 3、挤出速度
• 将熔融的塑料自模具内以挤压的方式往外推出,而得到与模口 相同几何形状的流体,冷却固化后,得到所要的零件。
二、挤出成型工艺过程
(动画) 1.原料准备:干燥、去杂质处理
2.挤出成型:
挤出机预热——加入塑料——熔融塑化——由机头挤出成型
• 3.定型和冷却
• 4.牵引和切割
• 在冷却得同时,连续均匀地将塑件引出。
第14章 挤出模具设计
14.1 挤出模具的机构杆之分,包括加料段、压缩段、均化段
附机: 模具(机头口模、定型装置)、冷却装置、
牵引装置、切割机或卷取装置等
控制系统
3、挤出成型特点
生产连续、效率高;质量稳定,适应性强。
• 一、挤出成型原理及其特点
1、挤出原理:塑化——成型——定型
真空定径装置(续)
定径装置与多个冷却槽的组合应用
• (1)口模和型芯 ——可形成稳定段(定型区)
挤出成型的类型
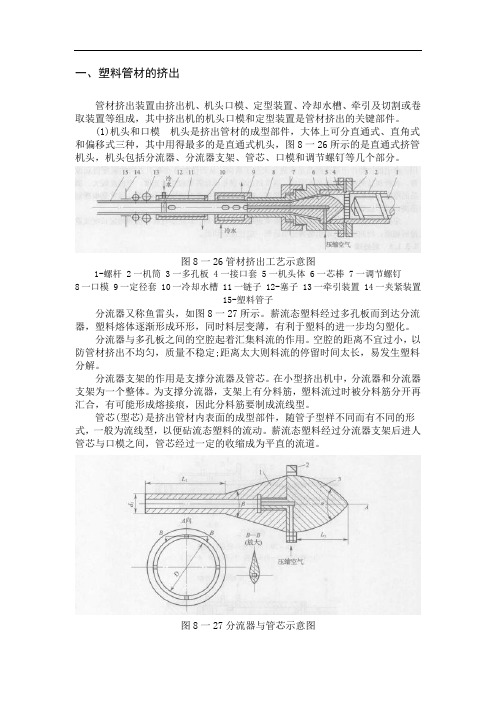
一、塑料管材的挤出管材挤出装置由挤出机、机头口模、定型装置、冷却水槽、牵引及切割或卷取装置等组成,其中挤出机的机头口模和定型装置是管材挤出的关键部件。
(1)机头和口模机头是挤出管材的成型部件,大体上可分直通式、直角式和偏移式三种,其中用得最多的是直通式机头,图8一26所示的是直通式挤管机头,机头包括分流器、分流器支架、管芯、口模和调节螺钉等几个部分。
图8一26管材挤出工艺示意图1-螺杆 2一机筒 3一多孔板 4一接口套 5一机头体 6一芯棒 7一调节螺钉8一口模 9一定径套 10一冷却水槽 11一链子 12-塞子 13一牵引装置 14一夹紧装置15-塑料管子分流器又称鱼雷头,如图8一27所示。
薪流态塑料经过多孔板而到达分流器,塑料熔体逐渐形成环形,同时料层变薄,有利于塑料的进一步均匀塑化。
分流器与多孔板之间的空腔起着汇集料流的作用。
空腔的距离不宜过小,以防管材挤出不均匀,质量不稳定;距离太大则料流的停留时间太长,易发生塑料分解。
分流器支架的作用是支撑分流器及管芯。
在小型挤出机中,分流器和分流器支架为一个整体。
为支撑分流器,支架上有分料筋,塑料流过时被分料筋分开再汇合,有可能形成熔接痕,因此分料筋要制成流线型。
管芯(型芯)是挤出管材内表面的成型部件,随管子型样不同而有不同的形式,一般为流线型,以便砧流态塑料的流动。
薪流态塑料经过分流器支架后进人管芯与口模之间,管芯经过一定的收缩成为平直的流道。
图8一27分流器与管芯示意图1一芯棒 2一分流器支架 3一分流器在管材挤出过程中,机头压缩比表示豁流态塑料被压缩的程度。
机头压缩比是分流器支架出口处流道环形面积与口模及管芯之间的环形截面积之比。
压缩比太小不能保证挤出管材的密实,也不利于消除分料筋所造成的熔接痕;压缩比太大则料流阻力增加。
机头压缩比按塑料性质在3一10的范围内变化。
口模结构如图8一28所示。
口模的平直部分与管芯的平直部分构成管子的成型部件,这个部分的长短影响管材的质量。
典型的挤出模具设计

典型的挤出模具设计挤出模具是一种常用于橡塑制品加工的模具,通过材料在模具中连续挤出,使其形成具有一定形状和尺寸的产品。
挤出模具广泛应用于塑料、橡胶、硅胶、硬质泡沫等各种材料的生产中,能够制造出各种管材、板材、条材、异型材等产品。
典型的挤出模具设计需要考虑材料特性、产品形状和尺寸等多个因素。
首先,挤出模具设计需要根据材料的特性来确定模具的结构和参数。
不同材料具有不同的流动性、熔体温度和粘度,对模具的设计产生不同的要求。
例如,一些材料具有较高的熔体温度和较高的黏度,需要采用加热设备和较大的流道截面积来确保材料能够顺利挤出。
而一些材料具有较低的流动性,需要增加收缩率和壁厚等参数来避免产品出现瑕疵。
因此,设计师需要了解材料的特性,合理确定模具的结构和参数。
其次,挤出模具设计需要考虑产品的形状和尺寸。
不同的产品形状对模具的设计产生不同的要求。
例如,圆形管材的模具需要设计圆形的出模口和流道,以保证挤出的产品具有良好的圆度和尺寸一致性。
而异型材的模具需要根据产品的形状和结构设计复杂的挤出口和流道,以确保产品能够顺利挤出,并且具有良好的表面质量和尺寸精度。
因此,设计师需要根据产品的形状和尺寸,合理确定模具的结构和参数。
再次,挤出模具设计需要考虑模具的制造和使用成本。
模具的制造和使用成本直接影响到产品的竞争力和市场占有率,因此设计师需要在满足产品形状和质量要求的前提下,尽量减少模具的制造和使用成本。
一方面,可以通过合理设计模具的结构和参数,减少模具的复杂度和制造难度。
另一方面,可以选择合适的材料和加工工艺,提高模具的耐磨性和使用寿命,降低维护和更换的频率。
因此,设计师需要综合考虑多个因素,合理选择模具的结构、材料和加工工艺,以实现最佳的经济效益。
最后,挤出模具设计还需要考虑产品的生产效率和质量稳定性。
生产效率和质量稳定性是企业提高竞争力和降低成本的关键。
模具的设计应充分考虑产品的生产工艺和生产效率,提高生产效率和降低不良品率。
挤出成型工艺及模具设计课件
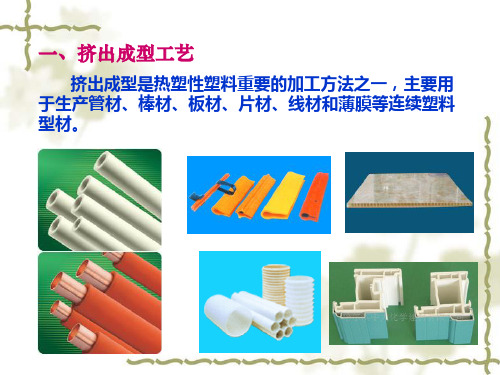
• 直通式挤管机头工艺参数的确定
• (1) 口模
① 口模内径D ❖经验公式: D = d /K
d——管材外径 K——补偿系数
❖按拉伸比确定
② 定型段长度L
❖ 按管材外径:L=(0.5~3)d ❖ 按管材壁厚:L=nt
(2) 芯捧(芯模)
芯棒与分流器之间通过螺纹连接,其中心孔用来通入压 缩空气,以便对管材产生内压,实现外径定径。
适用:内径尺寸要求准确、圆度要求高的情况。
1-管材 2-定径芯模 3-芯棒 4-回水流道 5-进水管 6-排水管 7-进水嘴
定径芯长度:与管材壁厚及牵引速度有关,一般取80~ 300mm,牵引速度和壁厚大时,取大值。反之,取小值。
定径芯直径:一般比管材内径直径大2%~4%,始端比终端 直径大,锥度为0.6:100~1.0:100。
面,芯棒用来成型塑件的内表面。通过调节螺钉5,可
调节口模和芯棒之间的间隙,从而控制塑件的壁厚。
口模实物图片 返回
芯 棒 实 物 图 片
返回
过滤网和过滤板
使从挤出机出来的塑料熔体由旋转流动变为平直流 动,且沿螺杆方向形成挤出压力,增加塑料的塑化均匀 度。
机头体 机头的主体,相当于模架,用来组装并支撑机头的
挤出机:挤出系统、传动系统、加热冷却系统、机身
辅机: 机头、定型装置、冷却装置、牵引装置、切割
装置、卷取装置 控制系统
2. 挤出成型工艺过程
原材料准备
塑化
挤出成型
冷却定型
塑件的牵引、 卷曲、切割
挤塑生产线
3. 挤出成型工艺参数
• 温度
❖ 加料段的温度不宜过高,压缩段和均化段的温度可高一些 ❖ 机头的温度控制在塑料热分解温度以下 ❖ 口模的温度比机头温度可稍低一些,但要保证塑料有良
塑料挤出成型工艺及模具设计教学

其他质量问题的原因与解决方案
06
塑料挤出成型工艺实例分析
管材挤出成型工艺主要包括原料准备、模具设计、挤出成型、冷却定型和牵引切割等步骤。
工艺流程
关键技术
应用领域
管材挤出成型的关键技术包括温度控制、压力调节、模具设计和材料选择等。
管材挤出成型广泛应用于建筑、给排水、农业灌溉等领域。
塑料挤出成型工艺及模具设计教学
目录
contents
挤出成型工艺简介 塑料挤出成型设备 塑料挤出成型模具设计 塑料挤出成型工艺参数控制 塑料挤出成型质量问题及解决方案 塑料挤出成型工艺实例分析
01
挤出成型工艺简介
挤出成型工艺是一种塑料加工技术,通过螺杆旋转加压,使塑料从挤出机机筒中连续挤出,经过模具定型后形成所需的制品形状和尺寸。
详细描述
04
塑料挤出成型工艺参数控制
温度参数控制是塑料挤出成型工艺中的重要环节,它直接影响着产品的质量和生产效率。
温度参数控制包括机筒温度、模具温度和塑料温度的控制。机筒温度的设置要根据塑料的特性和工艺要求来确定,以保证塑料在机筒内能够充分塑化。模具温度则影响着塑料的流动和成型,其设定要根据产品的大小、形状和材料特性来决定。塑料温度的控制也十分重要,合适的塑料温度可以保证塑料在挤出过程中保持稳定的流动状态。
常见的冷却定型设备包括冷却水槽、冷却隧道等。
这些设备通常配有强力的风扇,以加速冷却过程。
其他辅助设备
除了上述主要设备外,挤出成型工艺还需要其他辅助设备,如切粒机、振动筛、上料机等。
这些设备在生产过程中起到各自的作用,如切粒机用于将挤出的塑料切成一定长度的小颗粒,振动筛则用于筛选出不合格的塑料颗粒。
挤出成型原理及其特点

3. 挤出成型的特点与应用
生产效率高; 模具结构简单; 成型质量稳定; 适应性强;
ቤተ መጻሕፍቲ ባይዱ
挤出成型的应用: 挤出成型的塑件均为具有恒定截面形
状的连续型材,除氟塑料外,几乎所有的 热塑性塑料都可采用挤出成型,可成型的 制品包括管、棒、板、丝、薄板、电缆电 线的包覆以及各种截面形状的异型材。
塑料成型工艺与模具设计
挤出成型原理及其特点
1.挤出成型原理 借助于螺杆或柱塞得挤压作用,使塑
化均匀的塑料强行通过模口而成为具有恒 定截面的连续制品。
挤出机有螺杆式和柱塞式两种:
SJ-65型单螺杆挤出机
SJSZ-65型 锥形双螺杆塑料挤出机
ZS-65柱塞式挤出机
热塑性塑料的挤出成型原理如图4.1所 示(以管材的挤出为例)。
图4.1 1.挤出机料筒; 2.机头 ;3.定型装置;4.冷却装置
5.牵引装置;6.制品;7.切割装置
由挤出的成型的定义可看出,挤出过程实 际上分为两个阶段: ➢第一阶段:成型材料的塑化和赋形阶段。 ➢第二阶段:挤出的连续体的定型阶段。
2.挤出成型分类 挤出成型按照成材料的塑化方式不同,
可分为干法挤出和湿法挤出。
塑料成型工艺与模具设计
➢ 干法挤出一般在螺杆式挤出机上进行, 成型材料的塑化是通过加热达到的。
➢ 湿法挤出一般采用柱塞式挤出机,材料 的塑化是借助溶剂使其变为可流动态的。
根据挤出时加压方式的不同,可分为 连续式和间歇式两种。 (1)连续式挤出采用螺杆式挤出机,加压是
通过螺杆进行的。 (2)间歇式挤出采用柱塞式挤出机进行,借
塑料挤出成型模具设计
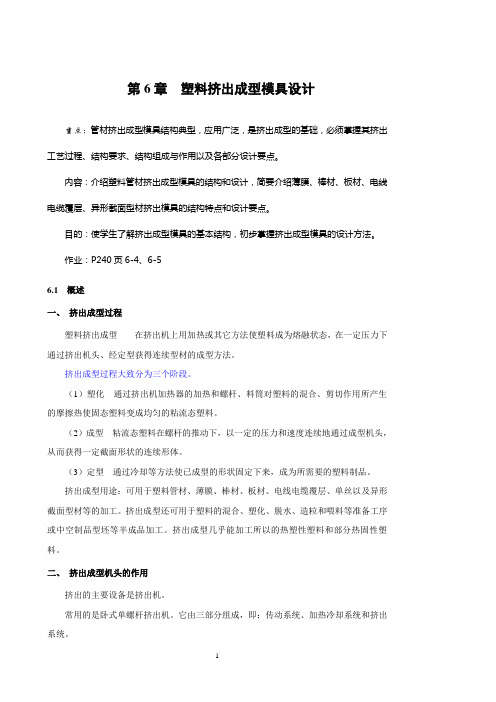
第6章塑料挤出成型模具设计重点:管材挤出成型模具结构典型,应用广泛,是挤出成型的基础,必须掌握其挤出工艺过程、结构要求、结构组成与作用以及各部分设计要点。
内容:介绍塑料管材挤出成型模具的结构和设计,简要介绍薄膜、棒材、板材、电线电缆覆层、异形截面型材挤出模具的结构特点和设计要点。
目的:使学生了解挤出成型模具的基本结构,初步掌握挤出成型模具的设计方法。
作业:P240页6-4、6-56.1 概述一、挤出成型过程塑料挤出成型------在挤出机上用加热或其它方法使塑料成为熔融状态,在一定压力下通过挤出机头、经定型获得连续型材的成型方法。
挤出成型过程大致分为三个阶段。
(1)塑化通过挤出机加热器的加热和螺杆、料筒对塑料的混合、剪切作用所产生的摩擦热使固态塑料变成均匀的粘流态塑料。
(2)成型粘流态塑料在螺杆的推动下,以一定的压力和速度连续地通过成型机头,从而获得一定截面形状的连续形体。
(3)定型通过冷却等方法使已成型的形状固定下来,成为所需要的塑料制品。
挤出成型用途:可用于塑料管材、薄膜、棒材、板材、电线电缆覆层、单丝以及异形截面型材等的加工。
挤出成型还可用于塑料的混合、塑化、脱水、造粒和喂料等准备工序或中空制品型坯等半成品加工。
挤出成型几乎能加工所以的热塑性塑料和部分热固性塑料。
二、挤出成型机头的作用挤出的主要设备是挤出机。
常用的是卧式单螺杆挤出机。
它由三部分组成,即:传动系统、加热冷却系统和挤出系统。
挤出系统包括螺杆、机头和口模。
通常把机头以及装于机头上的口模合并起来,统称为机头。
螺杆的作用是把原料从粉状或粒状经过料筒外的加热和螺杆转动时的摩擦生热把原料熔化并通过螺杆的压缩和推进使熔体在压力下流入机头。
机头是挤出模的主要部件,有如下四个方面的作用:(1)熔体由螺旋运动转变为直线运动;(2)产生必要的成型压力,保证挤出制品密实;(3)熔体在机头内进一步塑化。
(4)熔体通过口模成型,获得所需截面形状的制品。
塑料管材挤出模具可重构设计

2 1 模 具 的 快 速 更 换 .
寻求最 佳 可重构范 围。从 而 为塑料 管材挤 出模 具 的 设计 、 制造 、 用 和维护 提供新 的思 路 。 使
1 可 重构 管材挤 出模具 1 1 管材挤 出机 头的 重构 .
现 今 通用 的管材 挤 出模 具 设计 中 , 用 功 能结 共
机头 重构 的基本 原则是 最大 限度地 共用 功能结 构, 或者说 尽量少 地更换 零 件 。一 般来说 , 一组 不 同
7 0
工程塑料应用
21 , 3 0 0年 第 8卷 , 9期 第
分析 , 即作到科 学 合 理地 进 行 产 品分 组 。分 组 一经 确定 , 具方 案随 之而定 , 模 并且是 相对 固定 的 。
重构 管材挤 出模 具进 行 特 性 分 析 和关 键参 数分 析 ,
系列 的多个 规格 的管材 制 品进 行模 具设计 。在对 全
体被设 计对 象 的几何参 数和性 能参 数进行 综合分 析
的前提 下 , 理利 用取值 范 围进 行统 一设计 , 合 在最 佳 可重构 范 围内 以期 最 大 限 度地 共 用 功 能结 构 , 到 达 高效率 、 低成 本设计 、 造 、 制 使用 和维 护模具 的 目的 。
丁 晚景 , : 料 管 材挤 出模 具 可 重 构 设 计 等 塑
6 9
塑料 管材 挤 出模 具 可 重构 设 计 术
丁 晚 景 刘 蘩 孙 '
(. 石理工学院, 石 1黄 黄
川
407 ) 3 0 4
4 5 0 ; 2 华 中科 技 大 学 , 汉 30 3 . 武
摘要
为 大 幅度 地 降低 模 具 生 产 成 本 , 高模 具 利 用 率及 生产 效 率 , 出 了塑 料 管 材 挤 出模 具 的 可 重 构 设 计 思 提 提
塑料管材挤出模具设计
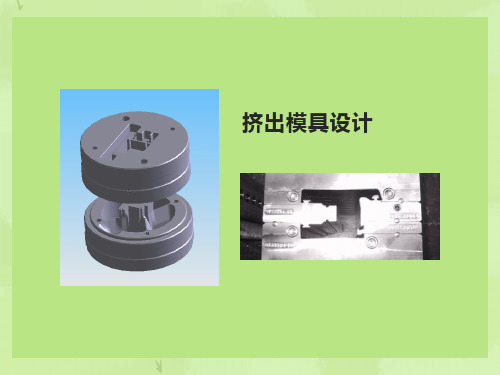
(直径<80mm)硬管挤出模具
下图所示是成型管材直径小于80mm用成型模具结构。采用内压法定径,定径套外腔是带有能通冷却循环水的环形套,冷却管坯;生产时,通过分流锥支架肋上的小孔,把压缩空气输入管坯内,管坯前端装有气堵,防止管内压缩空气逸出。分流锥、支架和芯轴也是用螺纹连接成一体,依靠分流锥支架外圆与模具体内圆紧密配合定位。保证分流锥、支架和芯轴与模具体装配后的同心精度。
PP
1.0.~1.2
HDPE
1.1~1.2
LDPE
1.2~1.5
口模定型段长度L1,与塑料性质、管材的形状、壁厚、直径大小及牵引速度有关。其值可按管材外径或管材壁厚来确定:
单击此处添加小标题
1
口模结构尺寸从图中可 以看到,主要是平直段 长度、内径和压缩角。 平直段(也叫定型段) 长度L1=(0.5~3)D 内径 d1= D/k 式中D —管材外径( mm) k—系数,k=1. 01~1.06。 压缩角α取14 °~50 °之间。
(4)结构紧凑
(5)选材要合理
02
01
03
04
05
常见的挤出机头有:
2典型挤出机头及设计
管材挤出机头、
异型材挤出机头
电线电缆包覆机头
1.管材挤出机头的结构形式
常见的管材挤出机头结构形式有以下三种: 直管式机头 图示为直管式机头。其结构 简单,具有分流器支架,芯模加热困难,定型长度较长:适用于PVC、PA、PC、PE、PP等塑 料的薄壁小口径的管材挤出。是挤出成型塑料 管材应用最广泛的一种模具结构
口模内径不等于塑料管材外
挤出成型模具设计

4.2.2 定型模的作用
定型模的作用是使用定径装置将从机 头挤出的具备了既定形状的制品进行冷却 和定型,从而获得能满足使用要求的正确 尺寸、几何形状及表面质量。通常采用冷 却、加压或抽真空的方法,将从口模中挤 出的塑料的既定形状稳定下来,并对其进 行精整,从而获得截面尺寸更为精确、表 面更为光亮的塑料制件。
挤出成型工艺过程可分为四个阶段: (1) 塑化阶段 (2)挤出成型阶段 (3)冷却定型阶段 (4)塑件的牵引、卷取和切割
4.1.3 挤出成型工艺参数及其选择
挤出成型的工艺参数主要包括温度、 压力、挤出速度、牵引速度等 。
1. 温度
温度是挤出过程得以顺利进行的重要条件 之一。温度主要指塑料熔体的温度,该温 度在很大程度上取决于料筒和螺杆的温度。 因为塑料熔体的热量除一部分来源于料筒 中混合时产生的摩擦热外,大部分是料筒 外部的加热器所提供的。所以,在实际生 产中经常用料筒温度近似表示成型温度。 常用塑料挤出成型管材、片材和薄膜时的 温度参数见表4.1。
低黏度塑料: β=45~60; 高黏度塑料: β=30~50;
3. 分流器和分流器支架
(1)分流器的扩张角α: 对于低黏度塑料: α=45~80; 对于高黏度塑料: α=30~60;
(2)分流器长度L3:L3=(1~1.5)D
(3)分流器尖角处圆弧半径R: R=0.5~2 mm
(4)分流器表面粗糙度:Ra<0.4~0.2
4.3.2 棒材挤出机头的典型结构
棒材主要指实心的具有一定规则形状 的型材,如圆形、方形、三角形、菱形和 多边形等。棒材挤出机头结构比较简单, 机头流道光滑呈流线型,一般流道中不必 有分流措施。棒材挤出机头的典型结构如 图4.5所示。
图4.5 棒材挤出机头的典型结构 1—口模; 2—连接套; 3—加热圈; 4—机头体; 5—多孔板;
挤出机头口模设计-PPT

3.模具的吊装
2.吊装方式 1)水平尺寸大于拉杆水平距离时,采用侧面滑
入(中小型模具) 2)模具厚度小于拉杆水平间距,将模具长方向
平行拉杆轴线方向,吊入后再旋转90度。 3)整体吊装: 4)分体吊装:起重设备受限时,可采用;先定
筛孔直径 1-2.5mm
熔体压力损失小、结构紧凑,易于装拆、清理 适于流动性好和热稳定性好的聚烯烃类大口径管 材。
螺旋供料机头
星形螺旋供料机头 环形螺旋供料机头
槽深变浅 芯模与外壁间距增大,保证流速一致,均匀 无芯棒支架,无熔接痕。
复式机头
三管机头
小型薄壁管
2.管材挤出机头参数确定
1.成型段长度 口模平直部分长度L1 作用:增加料流阻力,使管材更密实;使 料流稳定均匀,消除熔接痕 L1=(0.5-3.0)ds, L1=nt
成型段长度:棒材直径的4-15倍
无分流锥棒材机头
有强力冷却作 用的定型模
定型模
绝热垫
• 机头压缩角影响表面粗 糙度а=30-60°,出口扩
张角β =45°以下。
• 机头口模定型长度 L= (4-10)d,太短,会挤
出胀大明显,太长,阻
力过大卡滞
大家应该也有点累了,稍作休息
大家有疑问的,可以询问和交流 ‹#›
3)内定径 管材与定径棒直接接触,冷却定径 ,内应力均匀,保证尺寸精度和表面粗糙度
3.管材定型装置
(2)定径模尺寸
长度:管材尺寸、塑料性能、挤出速度、冷 却效果、热传导性能有关
过长—牵引阻力大;过短—冷却不 足易变形
RPVC ds300内,3-6ds, 35mm10ds; PO2-5ds 直径:外定径大0.8-1.2%;内定径大2-4% 锥度:出口直径略小于入口
塑料管材挤出模具设计
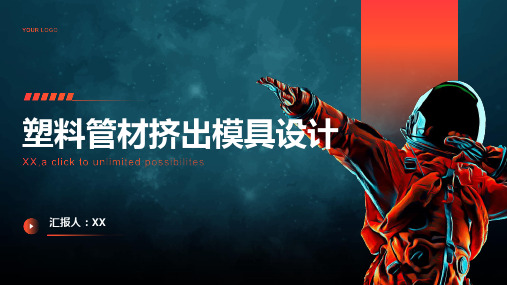
实例分析:对 PVC管材挤出模 具设计实例进行 深入分析,包括 设计要点、难点 及解决方案
经验总结:总结 PVC管材挤出模 具设计的经验教 训,提出优化建 议和未来发展方 向
实例二:PE管材挤出模具设计
模具结构:采用分流器、定 径套、机头等部件
模具温度控制:加热和冷却 系统对管材成型至关重要
模具材料:选择高强度、耐 磨性好的钢材
模具设计的原则和流程
模具设计应满足生产塑料管材的工艺要求,确保管材质量、尺寸和外观符合标准。 模具设计应考虑到生产效率、成本和安全性,以提高生产效益。 模具设计应遵循“一模多腔”的原则,以提高生产效率。 模具设计应注重冷却系统的设计,确保模具温度控制合理,提高管材质量。
塑料管材挤出模具设计要点
模具流道设计
数字化与信息化 技术:优化设计 流程,提高设计 精度
3D打印技术:个 性化定制,缩短 产品上市时间
绿色环保设计:降低能耗和减少废弃物排放的措施
采用新型材料:选择 可再生、可降解或环 保的材料,降低对环 境的污染。
优化结构设计:通过 改进模具结构,减少 生产过程中的能耗和 废弃物排放。
引入智能化技术:利 用先进的控制技术, 实现生产过程的自动 化和智能化,降低能棒加热,确保温度均匀分布,提高塑料管材的塑化效果 冷却系统:采用循环水冷却,快速降低模具温度,提高生产效率 温控系统:精确控制加热和冷却温度,保证产品质量和生产稳定性 安全保护:设置温度过高、过低自动报警和保护功能,确保生产安全
模具排气和溢料设计
模具排气:设计时需考虑模具的排气口位置和大小, 以确保在挤出过程中气体能够顺利排出。
产。
新型材料应用: 采用高强度、耐 高温、耐腐蚀等 新型材料,提高 模具的使用寿命
挤出模结构及分类

挤出模结构及分类挤出成型是目前比较普遍的塑料成型方法之一,适用于所有的热塑性塑料及部分热固性塑料,可以成型各种塑料管材,棒材,板材、电线电缆及异形截面型材等,还可以用于塑料的着色、造料和共混等。
挤出型材的质量取决于挤出模具,挤出模具主要是由机头和定型装置两部分组成,其结构设计的合理性是保证塑件成型质量的决定性因素。
1 挤出模的结构组成挤出模具主要由机头和定型装置(定型套)两部分组成。
下面以管材挤出成型机头为例,介绍机头的结构组成,如图8-1所示。
图8-1管材挤出成型机头l-管材;2-定径套;3-口模;4-芯棒;5-调节螺钉;6-分流器;7-分流器支架;8-机头体;9-过滤网;10-加热器1.1机头机头又称机头体,是成型塑件的关键部分,它的作用是将挤出机挤出的熔融塑料由螺旋运动变为直线运动,并使熔融塑料进一步塑化,产生必要的成型压力,保证塑件密实,通过机头获得所需要的塑件。
机头主要由以下几部分组成:(1)口模口模是成型塑件外表面的零件(图8-1所示的件3)。
(2)芯棒芯棒是成型塑件内表面的零件(图8-1所示的件4)。
(3)过滤网和过滤板过滤网(图8-1所示的件9)的作用是改变料流的方向和速度,将塑料熔体的螺旋运动转变为直线运动,过滤杂质,形成一定的压力。
过滤板又称多孔板,起支承过滤网的作用。
(4)分流器和分流器支架分流器俗称鱼雷头(图8-1所示的件6),其作用是使通过它的塑料熔体分流变成薄环状平稳地进入成型区,同时进一步加热和塑化。
分流器支架(图8-1所示的件7)主要用来支承分流器及芯棒,同时也能对分流后的塑料熔体起加强剪切的混合作用(但有时会产生熔接痕而影响塑件强度),小型机头的分流器与其支架可设计成整体式结构。
(5)机头体机头体(图8-1所示的件8)相当于模架,用来组装并支承机头的各零部件,并且与挤出机料筒相连。
(6)温度调节系统为了保证塑料熔体在机头中正常流动和挤出成型质量,机头上一般设有温度调节系统(图8-1所示的件10)。
塑料挤出模具设计
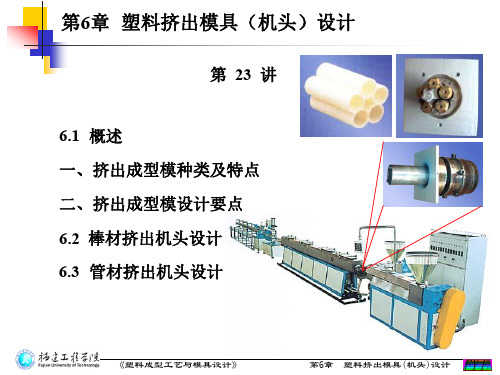
一、棒材挤出机头结构设计
棒材机头口模与定径套之间需用绝热垫圈隔热。
《塑料成型工艺与模具设计》
第6章 塑料挤出模具(机头)设计
一、棒材挤出机头结构设计
定径套:直径很小( φ 5mm以内)的棒材挤出可以不设定 径套;当棒材直径较大时,必须使用定径套。
《塑料成型工艺与模具设计》
第6章 塑料挤出模具(机头)设计
二、水冷定径套结构设计
水冷定径套关键尺寸:内径和长度。
• 内径:由棒材直径决定,需考虑成型收缩率的影响;
• 长度:应保证棒材离开定径套后不因自重作用而变形,并 能保持一定的表面质量。
棒材挤出成型收缩率
材料 PA1010 PA66 ABS
PC
POM 氯化聚醚 聚砜
收缩率/% 2.5~5 3~6 1~2.5 1~2.5 2.5~4 1.5~3.5 1~2
第6章 塑料挤出模具(机头)设计
6.2 棒材挤出机头设计
棒材规格:几毫米~几百毫米不等,它可比挤出螺杆直径 还大。
挤出速度:为使中心的塑料熔体全部冻结,挤出速度有时 控制得很慢(如φ 45mm挤出机挤φ 60mm尼龙棒时,速度为 2.5m/h,挤φ 200mm棒材时,挤出速度为0.5m/h)。
《塑料成型工艺与模具设计》
第6章 塑料挤出模具(机头)设计
6.3 管材挤出机头设计
一、管材挤出机头结构设计 1、管材挤出机头结构组成
适用于挤RPVC小管
《塑料成型工艺与模具设计》
第6章 塑料挤出模具(机头)设计
一、管材挤出机头结构设计
2、管材挤出机头分类 按管材挤出方向与挤出机轴线之间的关系分: • 直管式机头 • 直角式机头 • 旁侧式机头等
特点:挤出管材轴线与挤出机 螺杆轴线成直角,便于进气、 芯模的加热,以及芯线、复合 管的导入包覆。